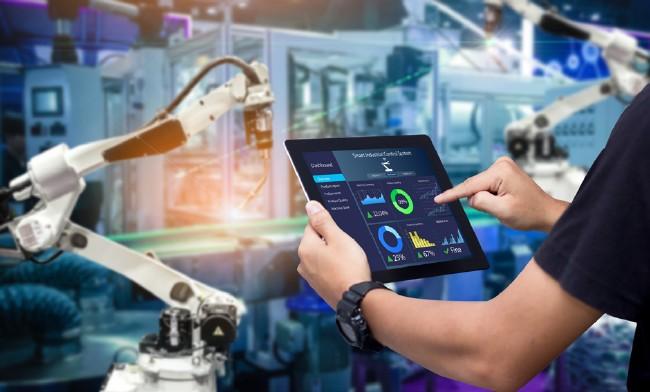
12 minute read
Choosing an MES solution that will evolve with your needs
TAKING YOUR MES WITH YOU
When looking for the right MES solution system today, manufacturers need to consider the ability of an MES to evolve with them, argues Francisco Almada.
Advertisement
Systems controlling plant floor operations are changing rapidly. The whole premise of Industry 4.0 is to bring physical production and its operations technology (OT) together with information technology (IT) solutions to provide a holistic view of production, supply chain and wider business goals. It aims to break down silos and create an integrated ecosystem where production efficiency, quality, and business agility all thrive. But, how do you know you are picking the right system for the future?
Manufacturing execution systems (MES) have long been the backbone of plant floor operations. Historically, however, they have evolved with narrow requirements – with specific functionality and features to fit specific types of processes – making it difficult to apply them in different industries. More recent MES offerings have instead focussed on flexibility and configurability of systems so they can adapt to a wide variety of different processes. Today’s MES solutions can create more flexible, configurable out-of-the-box solutions, and, when different possibilities of working within the bounds of configuration are exhausted, additional options for extending the core functionality.
Choosing the right MES
An MES needs to allow a company to evolve, grow and innovate. To this end, a system that has highly flexible configuration and allows for extension of core functionality is needed. The option for extreme configuration is preferred because a severely customised system makes upgrades, integration, backwards compatibility, and futureproofing much harder – but areas of both configuration and customisation for the future need to be considered in the design of forwardthinking solutions.
An MES should give guidance, enforce manufacturing rules and processes, and collect information. In addition, it also now needs to go beyond the boundaries of manufacturing areas. Modern manufacturing models require integration business related processes, such as maintenance, quality, and engineering, and the ability to expand into the entire supply chain and integrate areas such as warehouse management, supply chain management and Product Lifecycle Management (PLM).
Another important aspect of a future ready MES is its analytical capability. Traditionally, an MES would collect data for traceability and for some key performance indicators (KPIs).The Industrial Internet of Things (IIoT) has introduced new solutions, such as stream processing and machine learning (ML), to help derive insights. To enable tight control and execution, data needs to be collected in real time and the benefits of deeper analytics can only be achieved with deep integration between MES and IoT data platform.
In the cloud
Another consideration is where should the MES reside? Some manufacturers want it on premises, some on the cloud, some a combination of the two, some want ‘Software-as-a-Service’, some want ‘Platform-as-a-Service’. If on the cloud, should it be a private cloud? An MES needs to allow for all these options and this is possible if MES deployment is based on ‘containers’ to provide an abstraction layer for easy deployment in any environment.
The way users interact with an MES is also changing. Augmented reality (AR) and virtual reality (VR) solutions are all entering the manufacturing landscape, making interactions with the system as reactive, intelligent, intuitive, adaptive and personalised to real circumstances as possible.
An MES solution requires a long-term commitment. History has shown that these systems can reside in a business for up to 20 or even 30 years. So, it is important to understand the roadmap and future plans for MES systems to ensure you do not get stuck with a solution that will not evolve with the business. To this end, a system should allow extreme customisation and personalisation without compromising the upgrade path for the future and consider development paths of all areas, including execution, automation and analytics.
As plant floor operations evolve, different solutions, such as IoT, MES and automation, begin to occupy the same spaces and the boundaries between them blur. As these ‘systems’ become increasingly integrated, a solution that employs the features of each of these entities, and which allows different types of customisation and expansion by utilising a framework architecture, will be one that a business can thrive on for decades to come. plus-circle
Francisco Almada Lobo is CEO at Critical Manufacturing.
A NEW PATH TO OPERATIONS VISUALISATION
Find out why touch technology won’t eliminate physical controls.
For nearly all enterprises, the rise of Industry 4.0 and IIoT has transformed automation, leading to a global intelligent manufacturing revolution that shifts the paradigm from ‘automation’ to ‘intelligent automation.’
Industrial human machine interfaces (HMIs) that can handle bulk data exchanges are essential for field data visualisation. Thus, in order to better visualize the equipment status and production workflow, HMIs must evolve to become more intelligent.
With the advantages of a growing computer and electronics industry and the continually declining cost of developing new technologies, HMI design is entering a new stage. Each upgrade enables users to better operate machines and control applications using ever-more simple and accurate methods, thereby improving productivity.
Despite the recent advancements of industrial HMIs, including expanded displays, accelerated communication speeds, and other powerful features, their designs and interactivity can still be improved to better satisfy consumer demands. So, what types of HMI designs and functionalities do consumers require/ are likely to become mainstream? And what are the reasons they will become mainstream? These issues will be discussed in the downloadable white paper to provide a projection of future market trends.
The history of industrial HMIs
HMIs, as an interface that allows users to interact with the system and exchange information, are widely used in today’s society. In fact, HMIs have become indispensable to the development of many industries, such as the automobile, entertainment, electronics, medical equipment, banking, and service industries, which have long been major markets for HMIs.
HMIs typically comprise hardware integrated with software. Just like other HMI applications, industrial applications of HMIs have matured. Their primary functions are real-time information exchanges between humans and production equipment via programmable logic controllers (PLCs), variable-frequency drives. (VFDs), and meters, displaying data and providing visual feedback, and executing operating commands via an input unit (such as a touchscreen, keyboard, or mouse).
Following the infiltration of IIoT into factory floors, HMI technology has become essential to the fulfilment of intelligent production and the integration of system functions. To better display machine performance parameters and production workflow, over the past three decades computer technology has continually evolved to match ever-changing production requirements. This has also driven improvements in HMI designs to maintain pace with the development of intelligent manufacturing.
As early as three or four decades ago, when PC-based HMIs had not yet emerged, screen-based interfaces played a minor role in automation. At that time, most HMI products were controlled using physical features such as buttons, knobs, and indicators and connected via serial ports or proprietary protocols. However, their control capabilities were rather limited, often only allowing users to start or stop machine operations or implement certain settings or adjustments.
With the introduction of the Microsoft Windows operating system, HMIs started to go through drastic changes in visual functions: industrial technology experts combined graphics with data acquisition features and created a new breed of automation software to be implemented on the Windows platform. Accordingly, more advanced PC-based HMI terminals started to pervade factories. Compared to earlier solutions, PC-based HMIs deliver greater value as they support additional functions such as data processing and programming at production lines, which optimizes the flexibility of the machines. However, with the ever-increasing machine functions and rapid development of IoT technology, HMIs must be upgraded and enhanced.
In response to trends in the consumer electronics market, most of the industrial sector has begun equipping traditional control equipment with touchscreen technology to better integrate HMIs into the control workflow. And the realisation of intelligence continues to evolve. In a number of high-end industrial sectors, cutting-edge AR and VR technologies have been integrated into the manufacturing process to enable remote monitoring and machine control through virtual operations.
Although emerging technologies like AR and VR have endless potential for industrial applications, to optimize and streamline the processing workflow, most factories still prefer using HMIs with physical control units for human-machine interaction. plus-circle
The whitepaper can be downloaded at: https://bit.ly/3qrM7Ma www.advantech.eu
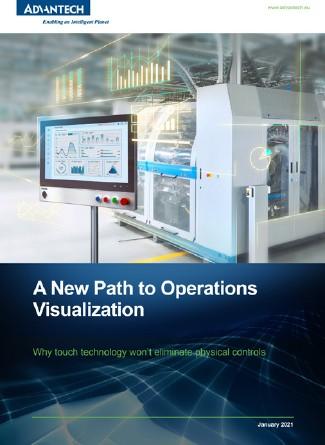
EIGHT TIPS FOR PROCESS AUTOMATION SUCCESS
Process automation projects are complex and can go through many challenges before completion. Remaining open, honest and demanding high expectations from everyone can help ensure the project will succeed, argues Robbie Peoples.
Complex integration projects can present a level of ambiguity even for seasoned project managers. Keeping a close watch on budget and schedule is critical for success, but is not enough to ensure the project is successful in the eyes of a client. Maintaining client satisfaction can be the most challenging aspect when managing an integration project.
A client’s perception of satisfaction goes through transition cycles just like projects do. The client’s view of the performance of the integration team is a complex element that can be difficult to measure accurately. Effectively managing perceptions and expectations can be challenging. To succeed, one must understand and relate to the client’s pain points.
As projects progress through their lifecycle, the number of interactions and exchanges of data between stakeholders fluctuates. On a typical project, the time and effort of the definition and planning phases exceed that of the execution phase.
Generally speaking, more interaction is needed with clients on the front- and back-end of project phases. The planning stage also requires accurate and timely delivery of data from the client in order to progress into the execution stages. These demands put pressure on clients to produce information and can be a bottleneck for the entire project. In many cases, clients do not have the expertise and/or available bandwidth to spend the time to produce the information needed for execution.
The following eight points are derived from real-world experiences of managing complex automation projects and identify key attributes to help manage the process.
1. Don’t underestimate the demands:
To ensure project demands can be met, it is recommended to evaluate the workload requirements for all stakeholders prior to the execution of a large project. If the company does not have large project execution experience, it is highly recommended to talk with knowledgeable professionals to define the requirements. A common misconception is that the current work responsibilities can be maintained while taking on additional project loading activities as well. Another common oversight is underestimating the detailed knowledge required to provide accurate data or review/approvals required. These oversights can be detrimental to success and all work loading should be properly planned and staffed for success.
2. Engage with stakeholders early:
It is important to have a solid working relationship between stakeholders. It is recommended that time is dedicated at the front-end of the project to establish a solid foundation based on ethical business practices. Face-to-face meetings always are recommended over video or conference calls. It is important to discuss the interactions between groups and define scope boundaries.
Define the expectations of how requests, submittals, deadlines and out-of-scope requests will be
handled. Doing business is easy when the project is within schedule and budget. However, when deadlines are looming and stakes are high, so it is always better to understand how to work together to address issues and concerns prior to a high-stress situation. Overcommunicate the expectation from all stakeholders to ensure everyone understands. 3. Request feedback often: Embrace feedback as an important aspect of continuous improvement. That is, stakeholders should check in their ego at the door, humble themselves and ask for direct honest feedback.
Positive feedback is great but the only way to improve is to define the negative aspects. This is a two-way street, however, and both client and contractor should have an open discussion because both have responsibilities to deliver. Depending on the project size, milestone reviews can be performed on a periodic basis. All issues and actions should be published and followedup for each feedback session. 4. Get management involved: Involving upper management on a periodic basis shows a commitment to the responsibilities of the project. This cultivates an open-door policy to help clarify current issues at hand and provide primary decision makers with first-hand information. These meetings should be more strategic than tactical. Identify roadblocks or critical-path items but keep the topics at a level that everyone can follow and do not allow conversations to get into the weeds,

DTE selected the Siemens Simatic PCS 7 distributed control system (DCS) to modernize its control system using redundant AS400H controllers for the updated project configuration, including the combustion control (blue I/O) and process safety/burner management applications (yellow I/O). The system was integrated into new cabinets by Cross Company. Courtesy: Cross Co. via Siemens
which might make the management team lose interest. Review meetings should not be the standard weekly or bi-weekly meeting attendees.
Identify a separate time to review the key issues to keep management aware of the project status.
5. Hold stakeholders accountable:
Stakeholders should be held accountable to deliver the associated data and/or information needed to move the project forward.
Always assign specific deadlines for delivery and do not allow generic time frames to be assigned. If items are delayed then the successive items will be delayed as well. All deliverables and deadlines should be reviewed at every meeting to ensure everyone fully understands and accepts the responsibilities.
Collective synergy and commitment from all stakeholders will result in project success. 6. Follow the process: Partnering with a professional group with a defined and qualified process of implementation can be the difference between success and failure. Do not allow a custom
approach or unproven strategies to creep into the project. Cutting a new path or reinventing the wheel only invokes a level of uncertainty to the outcome. The only way to predict the future is to understand the past. When schedules become tight, most people search for ways to cut corners. Be sure to fully evaluate the impact or potential impact of all actions and trust the proven process to lead to success. 7. Do the right thing: Mistakes will happen, but what is important is to be honest and admit the mistake, identify how to correct the situation and provide a solution to prevent that mistake from happening again. Honest, fair and open communications with stakeholders is the best policy. Always act in the best interest of the client and lead by example.
8. Remain persistent and open:
Common attributes of successful projects are acceptance and upholding responsibilities from stakeholders. Successful projects have hardships throughout the project lifecycle. However, persistence to work through those issues establishes a level of trust and understanding that builds healthy relationships. An open culture of continuous improvement and dedication to success are critical to forming a close partnership.
Dedication to those relationships means fair practices solutions are identified together and decisions are not one-sided. It is a good idea to keep management involved, solidifying the commitment. Be sure to communicate openly and honestly with realistic expectations while adhering to the most ethical business practices. Doing these things surely will bring success to the project. plus-circle
Robbie Peoples is integration manager at Cross Company.
This article originally appeared on www.controleng.com