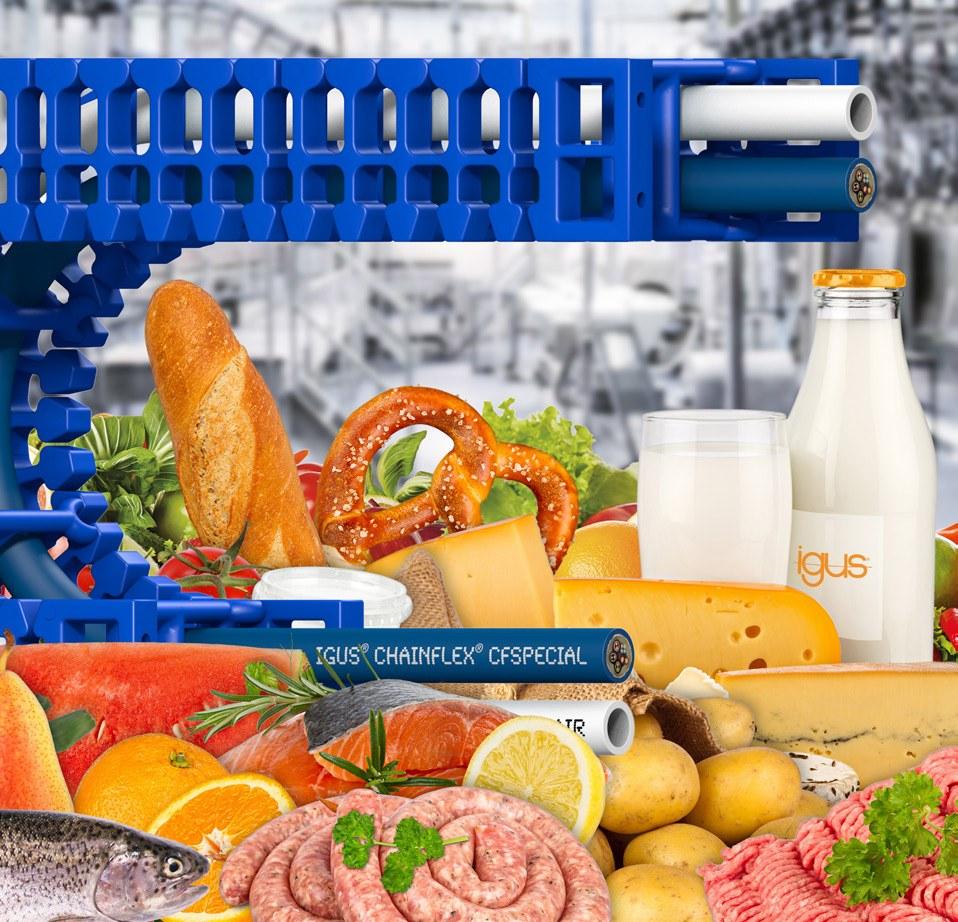
4 minute read
Farm to fork
How igus takes our country from farm to fork
The Farm to Fork Strategy aims to accelerate the transition to a more sustainable food system that should have a neutral or positive environmental impact. It is one of the reasons why lubrication-free tribopolymer bearings are quickly displacing their traditional metallic counterparts in farming equipment, through to food processing and packaging machines. Robert Dumayne, drytech Director at igus, provides an overview of how igus bearings play a vital role in removing the risk of lubricant contamination.
Advertisement
Automating manual tasks to increase productivity and throughput is a given in high-volume manufacturing, such as the automotive industry. Today, modular, low-cost automation is enabling other industries to automate manual tasks with a good return on investment – this is particularly so in the food production sector with vertical farming as well as traditional agriculture. This is driven by environmental
considerations, such as the requirement for the elimination of external lubricant and the necessity of low energy production.
iglidur bearings and liners are based on thermoplastic polymers that ensure good basic resistance to wear. Fibres and filling materials increase the bearing’s mechanical load-carrying capacity. Most importantly, they do not require any external lubrication as solid lubricants form part of the homogenous structure made up of millions of microscopic particles. The plain bearings release tiny amounts of solid lubricants during movement to lubricate the immediate surrounding area sufficiently.
iglidur A160 and iglidur A181 are blue materials that are visually detectable to comply with EU regulation 10/2011 and the requirements of the FDA. Both materials have high wear-resistance, low moisture absorption and resistance to chemicals. iglidur A160 has good chemical resistance, which also makes it resistant to aggressive cleaning agents. iglidur A181, on the other hand, is suitable for use on stainless steel shafts and in applications involving pivoting and rotating movements.
Developed specifically for food contact, iglidur FC 180 and igumid FC materials are also visually detectable by their blue colour, as well as by metal detectors. In case of damage, broken pieces can be quickly detected and removed. Even the smallest fragments of 0.0139g (iglidur FC180) or 0.015g (igumid FC) can still be identified on a conveyor belt when passing through a metal detector.
With the use of intelligent technology called isense – a monitoring system which accurately measures wear and reports back to a master controller – igus can offer predictive maintenance. Having a system that can predict any required maintenance before failure helps reduce unscheduled maintenance and downtime. This capability is especially useful in areas with minimal direct human operation. It also creates more efficient production and maximises productivity by minimising downtime, allowing companies to remain competitive and keep costs down. The isense bearing range comprises a number of materials, including iglidur A180, as well as the heavy-duty bearing iglidur Q2E for use in agricultural engineering, the all-rounder iglidur G, the endurance runner iglidur J and iglidur P210 for pivoting and rolling applications.
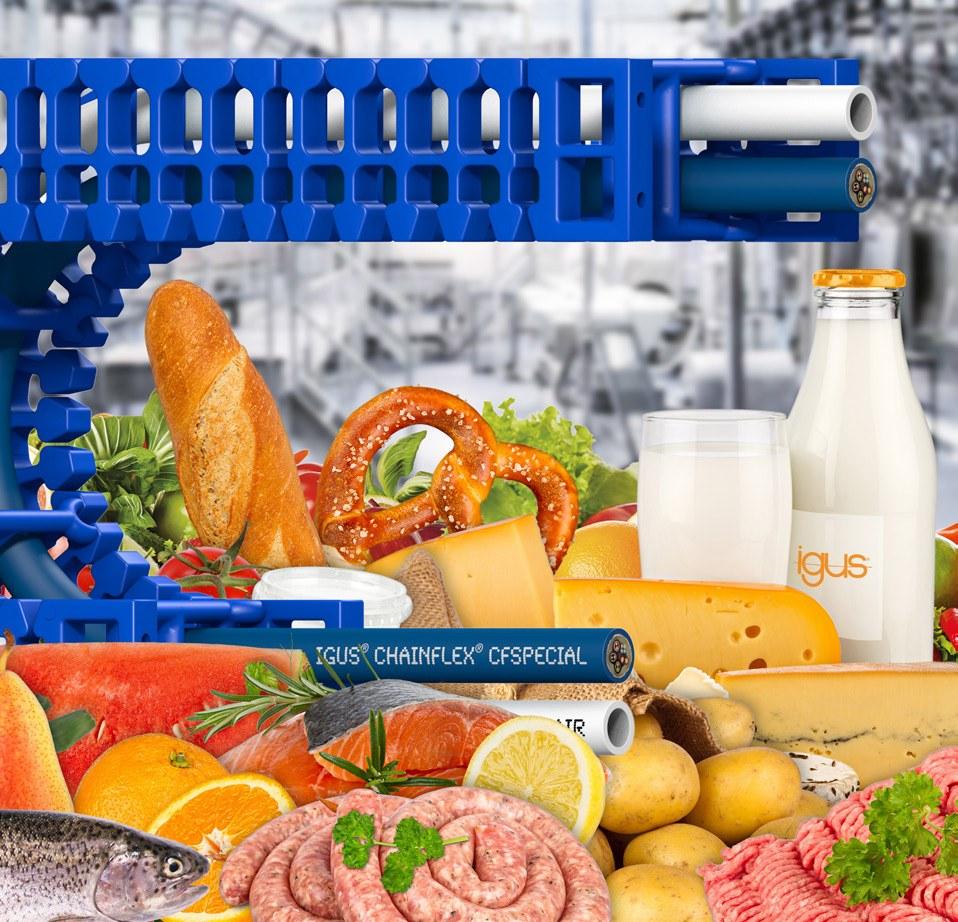
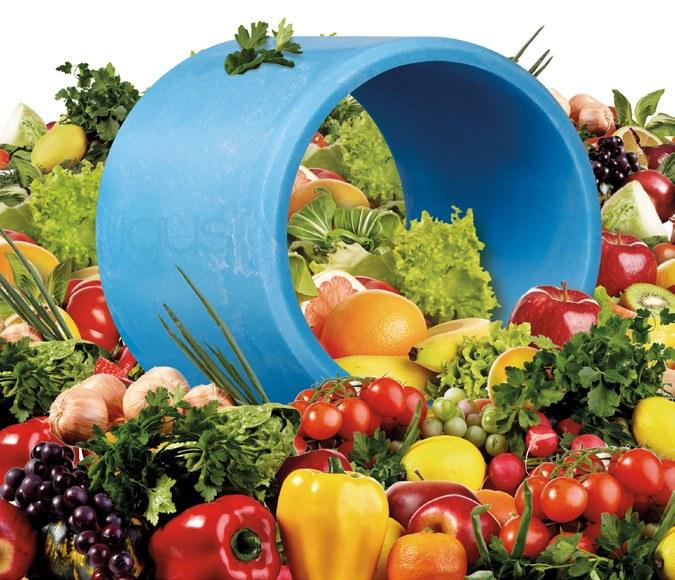
In the field, where there is always a lot of dust, igus linear gantries (which feature iglidur bearings) are used in automated planting, picking, weeding and sowing. The fact that the bearings are resistant to media and require no maintenance ensures maximum uptime all year round. On food assembly lines, igus linear robots are used for the automated application of metered products, such as mayonnaise or tomato sauce. This not only maintains product consistency, but it also minimises product cost. In food production machines, bottling lines, packaging systems and knifeedge conveyors iglidur materials are used as the roller bearing. On conveyor tables, xiros bearings made from iglidur B180 are used in the ball transfer units. Stainless steel balls inside allow smooth running and absorb loads of up to 500N.
Aside from bearings, the TH3 series of hygienic design energy chains are deployed on food processing and packaging machines. They feature rounded corners and simple, threadless connections to prevent dead spaces where debris and germs can build-up. Its design avoids surfaces lying on top of each other, which prevents plastic on plastic abrasion and material wear. The blue material is also highly resistant to aggressive cleaning agents and chemicals.
Every year, igus also carries out not only 1,000 customer-specific tests in its test laboratory but also more than 4,000 tests of its energy chains and over 12,000 tests of its plain bearing products. The results of all tests are fed into a database and, as a result, igus provides its customers with around 40 different web tools, such as the online product finder and the service life calculator. Therefore, users are always able to find the most suitable solution that improves the technical performance of their equipment while reducing costs. They can rely on tested and safe components in their machines and systems.
www.igus.co.uk/food
About the author:
Rob Dumayne is dry-tech Director at igus, responsible for the development and management of the drytech technology roadmap in the UK. Disciplined in Mechanical Engineering, responsibilities during his 21-year career with igus started in internal technical sales, which developed into project engineering and systems, and then design work, including new product development and testing.