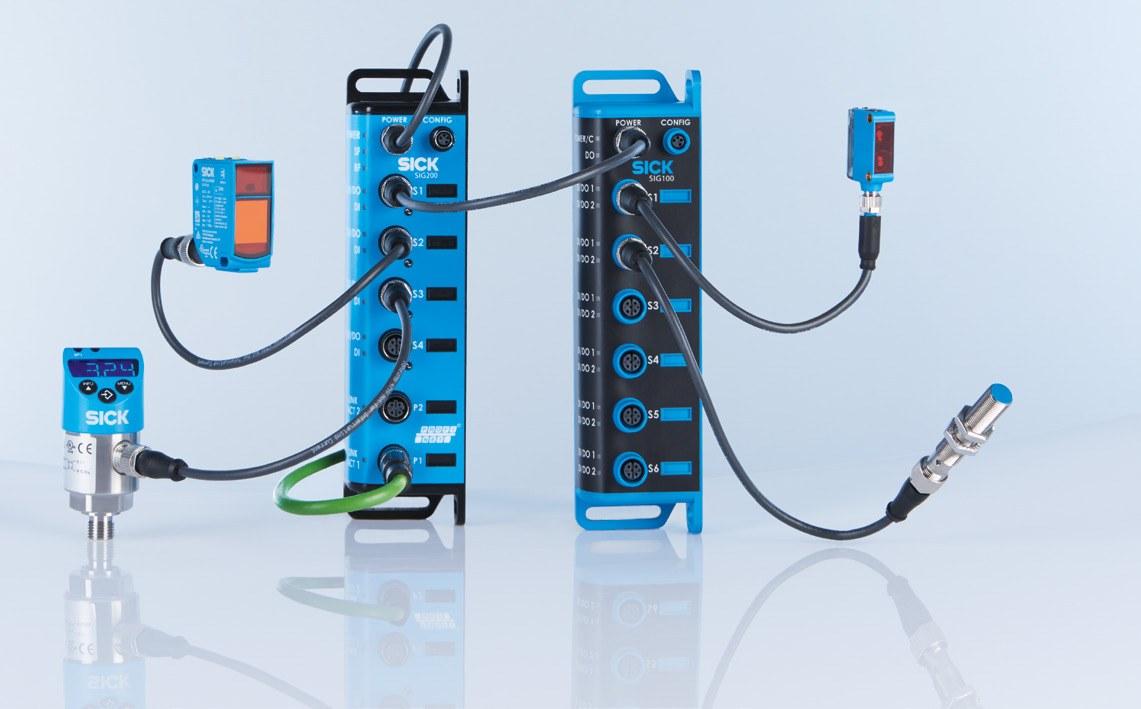
5 minute read
Laser triangulation sensors measure lateral position of rail bogie wheels
Joining the dots with sensor integration devices
There was a time when sensors were simple switches, and their manufacturers just hardware suppliers. All that has changed. Sensors are the ‘eyes and ears’ that collect data on the front line of production and logistics operations. Equipped with ever-smaller microprocessors, they have become intelligent.
Advertisement
With their own decentralised computing power right on board, sensors may no longer need to rely completely on a higher-level or central control system to process and make sense of all the data they produce. They can also provide additional data to the control system via IOLink. Some even process applications, or ‘Smart Tasks’ by themselves. Soon, some will combine multiple functions in a single device, for example, detecting piston position, vibration and angular velocity for end-of-arm tooling.
Integration of hardware takes place at a local level within the systems and control architecture, but the data generated can be shared not just at the machine level, but also via cloud-based systems. First, that data can be monitored and trended on a PC, machine HMI or cloud-based dashboard. It also has the potential to be used in ERP (Enterprise Resource Planning) and MES (Manufacturing Execution System) software; indeed, this is seen as fundamental to the future of Industry 4.0 manufacturing and logistics.
Digitisation, intelligence and networking will increase until, eventually, systems will control and optimise themselves – all using the data from sensors. Data transparency enables trends to be monitored and gives us the ability to understand more about a system. From Overall Equipment Effectiveness (OEE) to Deep Learning, it is the integration of the data that allows a user to become more aware of what is happening within a system.
The key to all this integration lies in the gateways and devices that act as the translators – and, sometimes, as localised controllers – to aggregate and route the data efficiently. They deal with the data at a local level while making it visible globally. Manufacturers like SICK have already begun to roll out a portfolio of devices to facilitate sensor integration into fieldbus environments and higher automation hierarchies.
Sensor integration gateways
To begin with, most people are familiar with IO-Link Masters that sit on a higher-level bus system, such as PROFINET or EtherCAT. They act as a gateway for IO-Link data to be passed on to the PLC or higher-level systems. The SICK SIG200 Sensor Integration Gateway is an IO-Link Master with the addition of an on-board web server that collects, combines, evaluates and transmits signals from IO-Link devices from any manufacturer. It works as both an IO-Link Master and small, distributed logical control system in one. It needs only one cable to communicate simultaneously via the fieldbus with the machine controller and with higher-level enterprise or webbased systems.
To expand this integration, a sensor hub can squeeze the outputs from a number of on/off sensors into one string that can be passed via an IO-Link Master to the PLC. SICK’s SIG100, for example, can be used to bundle up to twelve standard I/Os in a single IO-Link data packet, which can then be communicated to machine controllers and cloud-based systems via the SIG200. A maximum of 52 I/Os can be connected to one SIG200 by using the SICK SIG100.
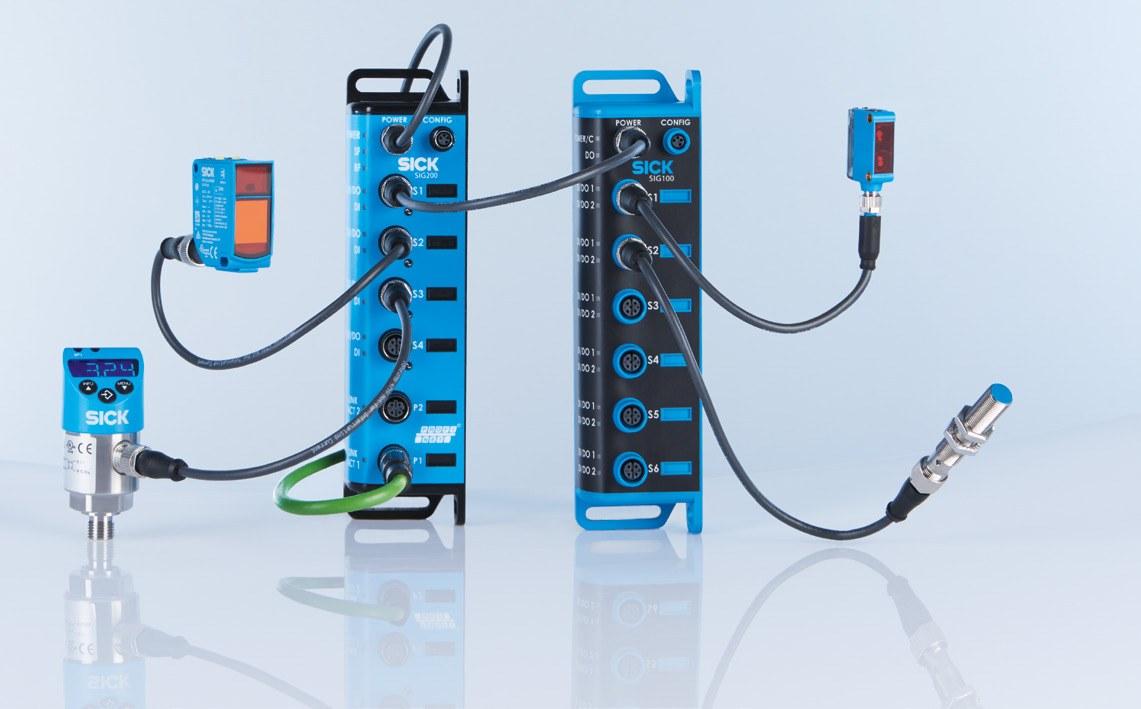
Sensor Integration Machines
Sensor Integration Machines (SIMs) are programmable devices with configurable on-board software, so they can be used to process many different tasks, including more complex machine vision applications. They also include some or all of the functionality of an IO-Link Master.
The SICK SIM1000 and SIM2000 Sensor Integration Machines, for example, collect and evaluate data from multiple sensors working together at the field-level via standard interfaces, including Ethernet, IO-Link, CAN and Serial. With up to four Ethernet ports, they can support interfaces for cameras, lighting, LiDAR scanners, encoders, photoelectric or displacement sensors, as well as to higher-level controls and the Cloud. The multi-sensor outputs, values and results can be used to drive typical industrial automation applications such as camera-based inspection, measurement, or identification of objects.
Gateways
The term ‘gateway’ can mean different things depending on what is using the ‘gate’. In the case of sensor data, it may be the SICK Sensor Integration Gateways. More generally, a cloud gateway is a device that takes all sorts of data and passes it to the next level via the relevant protocol. An example of this would be SICK’s TDC (Telematic Data Collector), used to aid real-time condition monitoring and predictive maintenance.
The SICK TDC collects and processes sensor outputs and data in stationary and mobile machinery, together with GPS localisation information, and enables them to be displayed, monitored, recorded and analysed via a server or cloud system. By transferring data via mobile communications protocol (MQTT), a real-time overview of selected plant and processing parameters can be provided, and SMS text or email alarms can be configured.
The SICK TDC system also enhances system transparency to SICK and third-party sensors compatible with Ethernet, CAN, RS232, RS485, 1-Wire and UART interfaces. Output communications can be via cable, wireless signal or GSM.
The SICK SIG200 can take sensor data and pass it on over REST API to the cloud or fieldbus to the machine controller. The SICK TDC can take data directly or via REST API and pass it to the cloud or a local network storage solution.
Easy data transparency
How can you easily detect all the IO-Link devices in a machine? This is simple using software such as SICK’s FieldEcho. This closes the remaining gaps in integration and makes all IO-Link devices visible, providing direct access to process and service data and enabling the IODD device descriptions to be automatically downloaded. It visualises all configured IO-Link Masters and the IO-Link sensors and actuators and displays their status.
It is networked production and control processes, working in complex machine environments, that will shape our industrial future. The degree of digitisation in future will mean smart factories will organise themselves using huge amounts of up-to-date information to make independent decisions. This information will be provided by smart sensors.
www.sick.co.uk About the author:
Charlie Walker is Product Specialist for Presence Detection at SICK UK. A graduate of Lancaster University, Charlie helped run a factory engineering department before specialising in the application and technical support of sensors. He has particular experience of implementing IO-Link sensor applications and knowledge of their successful integration with many well-known PLC brands. Charlie joined SICK UK in 2017.