
3 minute read
Residual stress systems
Stress relief pre-heat treatment vs. straighten/ flatten post-heat treatment
Most engineering components have a residual stress system. Such systems are inherent in bar stock, plates, and, to some extent, in forgings and castings. While the residual stress system can be modified by removal of material, further forming of the raw material, and heat treatment processes, modification invariably leads to distortion or cracking.
Advertisement
“Distortion may be rectified by straightening or flattening operations. However, there is always a risk of breakage or cracking with such operations,” cautions Roger Haw, Managing Director of Flame Hardeners Ltd.
Problems associated with changes of residual stress systems are often found in the heat treatment of rollers, shafts, and pins – together with items such as gear rings, bearing rings, guide bars, machine tool beds and press brake tools.
Modern machining techniques have led to increased rates of metal removal and, in many cases, use of bar stock to produce complex machined parts from which 50 percent or more of the original material volume has been removed.
“Cases have been seen where, for the benefit of expedient delivery of cylindrical items, such as rollers and piston rods, available bar stock has been used which can be 20 percent greater than the diameter required. Gear shafts, which may have been made from forgings some years ago, are now manufactured from bar stock and diameters of the length of a shaft can vary by as much as 200 percent,” Haw elaborates. Problems arising from distortion during treatment can be minimised by stressrelieving at intermediate machining stages, and correct jigging during heat treatment. This can eliminate the requirement for straightening after heat treatment. It’s a relatively low-cost heat treatment operation, undertaken under controlled parameters and often giving a predictable response, whereas straightening and flattening are risky operations due to the high risk of cracking or breakage.
“Economically, the cost of stress-relieving can be easily estimated and included in the overall estimate of cost for the component,” continues Haw. “The cost of straightening is not easily estimated as the degree of any distortion to be corrected cannot be easily assessed.”

For larger diameters of rollers, piston rods, guide bars etc., warm straightening is the most desirable process, as this makes actual straightening easier and minimises the risk of cracking. It is necessary to heat the component to a temperature in the range of 180-250°C and to keep it at such a temperature for as long as possible. Larger objects may require several reheats during the straightening operation.
“Over many years of processing components that may distort, we have reached the conclusion that it is far more economical to stress-relieve at an intermediate machining stage prior to heat treatment to minimise or eliminate distortion than it is to straighten or flatten following heat treatment. A component that cannot be straightened or flattened is just a piece of scrap – and often a very expensive piece of scrap,” Haw concludes.
Your specialist heat treatment contractor can often assist you at the design stage by recommending suitable treatment routes.
Drinking Water Analysis simplified.
Type 8905 packs up to six sensors in one compact casing, and up to sixty on one customised panel! This saves space, time and money – during installation, operation and maintenance. The online analysis system can be modularly fitted with miniaturized analysis cubes – during operations with hot swap functionality. Each transmitter cube registers itself on the system through auto-addressing and transmits reliable measurement data
even with minimal sample water flow.
Not sure if this is the right solution for your application? Contact us with a view to trialling our Type 8905 and to see for yourself why water municipalities around the world are choosing this compact, modular, and repeatable system for their process and water quality monitoring.
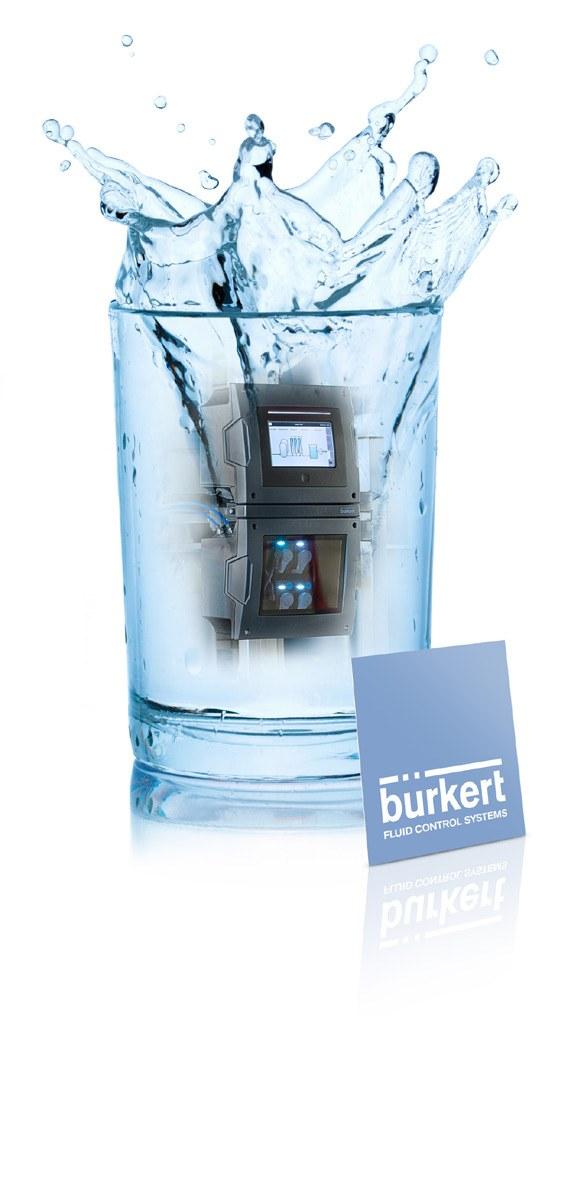
We make ideas flow.
Get in touch Call us at +44 (0) 1285 648720 or email sales.uk@burkert.com
