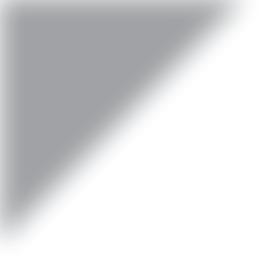
2 minute read
Why commodity casters cause injuries
SOLUTIONS
MATERIAL HANDLING
Advertisement
By Eric Hassen
Why commodity casters cause injuries
Commodity casters are workplace injuries waiting to happen
Failed kingpins and faulty tread materials are among the leading causes of caster failures on material handling equipment and of safety incidents within manufacturing and distribution centers.
Overloaded carts or carts specified with casters with high rolling resistance can cause physical overexertion, the number one cause of workplace injuries. Why are casters such a hidden danger in the workplace?
Cart manufacturers are continually looking for ways to reduce costs, and that may mean skimping on the casters. They may specify a lower cost caster that uses inferior materials and not customized to the application. No frills. Bare bones. The carts may have ideal material-handling functionality but contribute to workplace injuries.
Casters 101
Commodity casters typically feature a kingpin design, the number one failure point on a swivel caster. Typically, commodity casters do not have the correct bearing for the application. The wheel tread is likely an inexpensive and ineffective material option like phenolic or a type of hard plastic (see Figure 1). Combining poor quality construction with incorrect bearings increases the friction forces during manual operation, making the wheels more difficult to rotate. Commodity casters also tend to have a standard swivel lead, the distance from the center of the top plate to that of the axle.
As a result, commodity casters cannot get into the trailing position when trying to pivot. By design, short swivel lead casters are more difficult to turn, which can result in expensive push/pull injuries. The caster fights itself when trying to maneuver into the trailing position. A standard swivel lead has a short distance roughly straight up and down from the center point of the kingpin to the center point of the axle. Applicationspecific casters can come with an extended swivel lead. This added distance enables reduced push-pull forces, improved maneuverability and decreased noise and chatter.
Commodity casters typically have an open raceway design. Their two sets of ball bearings — one on top and one on the bottom — are open to the elements. Dust from the plant environment gets inside the raceway and binds up the grease.
If not greased on a regular basis, the bearings or swivel raceways will create costly caster issues. If an operator tries to push a cart and the wheel doesn’t move, the risk of ergonomic-related injuries increases dramatically.
Think differently about casters
When many purchasing agents choose carts and casters, they are likely looking for the lowest initial cost, thinking, “a caster is a caster.” When maintenance and injury-related costs are calculated, the total cost of ownership becomes the issue. Plant management examining what causes continuous issues with carts and contributes to workforce ergonomic issues should keep these considerations in mind.
Advances in replacement casters provide plant engineering and operations a choice for improving workplace safety while increasing productivity and giving material handling carts an extended useful life. PE
Figure 1: Poor quality commodity casters combined with insufficient maintenance practices can lead to chipped wheels that fall apart and pick up debris, leading to potential pushpull injuries for workers. Courtesy: Caster Connection
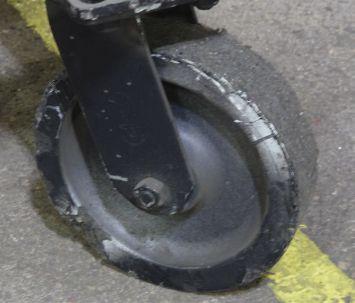
Eric Hassen is director of business development for Caster Connection, a manufacturer and distributor of high-performance casters, wheels and other material handling products based in Columbus, Ohio.