
6 minute read
How to extend switchgear life and improve system reliability
SOLUTIONS
ELECTRICAL SYSTEM RELIABILITY
Advertisement
By Jeff Brittain and Andrew Kaster
How to extend switchgear life and improve system reliability
Improve system reliability of switchgear with protective relay upgrade projects
Figure 1: Before and after the protection relay upgrade. Courtesy: High Voltage Maintenance N ot long ago, a telephone had a specific purpose: making phone calls. In the early 2000s, cell phone manufacturers took advantage of new technologies to enable users to not only make phone calls from anywhere, but also take photos, play games, identify the species of trees in the backyard, get a weather forecast and so on. The possibilities of applications for modern smartphones extend as far as the imagination can go.
During the smartphone revolution, electrical protection and control system technology also advanced considerably. With the advent of microprocessor-based protection relays, the modern relay can do much more than protect a circuit. They now can perform communications on multiple protocols, system monitoring, alarms and self-alarms, arc flash mitigation, controls, time delay and remote breaker operations, event reporting, increased safety and more.
As facility electrical systems age, the demand for production is not slowing down. Plant facilities and maintenance personnel are asked to maintain a wellfunctioning electrical system and minimize system outages. While complete replacement of original electrical distribution switchboards and switchgear is a possibility, the cost and outage time required do not align well with facility budgets and production demands. An alternative to a complete replacement is extending the life of the existing switchgear and increasing system reliability by performing a protective relay upgrade project.
Protective relay upgrade projects
These projects provide microprocessor relays that have many advantages for the overall power system. Even in situations where the protection relays have been maintained and are fully functional, the benefits of upgrading to modern relays can justify the expense. Once the decision to upgrade has been made, performing this as a turnkey project offers many benefits. A workflow of a turnkey relay upgrade can be broken into several distinct phases: Engineering, procurement, bench testing, installation, field testing and startup.
Consider the following use case while keeping in mind these phases are applicable to any protection scheme upgrade.
A semiconductor manufacturing facility was experiencing challenges with its switchgear control system. The facility had two medium-voltage utility feeds. The original switchgear, which dated back to the 1970s, contained an auto throwover (ATO) control scheme to operate the main-tie/main breaker and maintain power to the switchgear if one of the utility sources is lost. The vintage ATO was comprised of control relays, voltage relays, timers, resistors, capacitors and a significant amount of wiring. The parts for this vintage system are now obsolete and no longer supported by the manufacturer, thus a repair to the system would be difficult and slow, resulting in an extended and possibly unplanned outage (see Figure 1).
The High Voltage Maintenance (HVM) team performed an engineering evaluation to assess the system and make recommendations for a path forward. The protection relays were an original electromechanical overcurrent relay style, and even though they had been properly maintained throughout the years, HVM developed a solution that would use the relays in conjunction with a logic processor to act as the new ATO control system. This design took advantage of the communications, individual relay element functions and configurable internal logic within the relays to work in tandem with a separate logic controller to function as the ATO. The new relays also took over the circuit protection role.
The project was performed as a turnkey solution. As a manufacturing facility with production at full
capacity, operations required a maximum outage time of 36 hours. To accommodate this requirement, the phases of the project were designed with this outage requirement in mind.
Engineering.The engineering phase typically consists of data collection, field observations, measurements, review of existing drawings and an analysis of the existing system functionality. Once the data collection is complete, the engineering work can begin. Since the system was not a complete replacement and much of the existing wiring was to remain, the original drawings were revised according to the new system design. The original drawings were only available in hard copy, so they first had to be recreated in AutoCAD. Once there was a working set of AutoCAD drawings, HVM created three sets: one each for demolition, construction and installation. The installation team used the demolition set to remove devices, components and a circuit that was not needed in the new design. The installation drawings showed each applicable item color-coded with the required action. For example, devices or wires to be removed were highlighted in green, wires to be relocated in purple and items to remain did not have any highlight. Being able to also deliver a final set of construction drawings to the client ensures proper documentation of the completed installation and a record should future modifications be needed.
Procurement and bench testing. After the engineering was complete, procurement and bench testing were implemented for the more advanced electrical components of the project. This phase incorporated protective relays, panel/door prefabrication and any ancillary components such as relay test switches, wiring and the like, required to make the system fully functional. Once the prefabrication panel/door modifications were complete, panel/door mounted equipment along with any interconnect to and from the devices were installed. Relay settings (provided by the engineering phase of the project) were then downloaded and the relays were bench tested on the programmed setting. Having all this work completed offsite saved valuable time during the outage at the client’s facility.
Field Installation, functional testing and startup.
Once delivered to the site, the field wiring and components required for field installation are completed according to the installation drawings. All wires are marked at the terminal strips. Any field-installed component testing was then completed along with point-to-point wire checks. A functional test plan was developed, and the complete system was tested against the plan to ensure proper operation (see Figure 2). The last phase of the project required the lead test technician to be onsite during startup to verify phasing, download advanced relay waveforms, set event parameters, and so on, and everything is documented on the final project report.
Final thoughts
Protective relay upgrade projects with advanced style relays provide many ways to improve system operation, reliability and safety. These relays provide enhanced protection and control features that bring old infrastructure into the 21st Century and extend power system equipment lifecycle. Partnering with a company that can provide a complete turnkey solution also provides the added advantages of consistent engineering throughout the project, prefabrication with offsite testing, quality installation and thorough testing to ensure a fully functional and well documented project. Proper project phasing enables the project to be completed during a limited onsite outage and offers improved facility reliability and uptime, which saves the client valuable budget dollars. PE
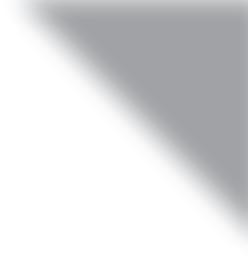
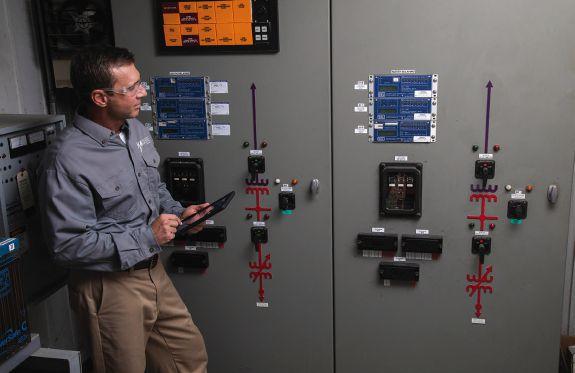
Figure 2: A functional test plan was developed, and the complete system was tested against the plan to ensure proper operation. Courtesy: High Voltage Maintenance
Jeff Brittain is Midwest region sales manager at High Voltage Maintenance (HVM). Since joining HVM, Brittain’s focus has been on improving generation, transmission and distribution system reliability, uptime and safety for critical power customers. Throughout his career, he has worked in various operations and sales roles while promoting a reliability-centered maintenance approach that meets the customer’s needs and budget. With more than 25 years in the industry, Brittain has amassed great knowledge of power system electrical testing, maintenance and engineering.
Andrew Kaster, EE, PE, NETA IV, is manager of systems integration at Electrical Reliability Services (ERS). Kaster has more than 15 years of experience in design, testing and commissioning generation, transmission and distribution systems from 208 V through 500 kV.