
4 minute read
Physical Properties of FDM
Physical Properties of FDM (Fused Deposition Modeling )
Injection molding is the most used mass production method for forming thermoplastics into shape. In this process hot liquid thermoplastics are shot into a injection mold and are cooled down before they were released out of the mold. This process besides thermoforming are the best for the physical performance of the produced parts out of thermoplastics.
Advertisement
3d-printing is mostly based on linear extrusion in a XY-matrix and stacked in Zlayers. The adhesion between the extruded lines are in XY-direction as well as in Zdirection based on the overlap between the printed paths. Liquid new material is printed over cooled down already printed paths and they connect to each other but the connection is not as stable as in solid parts made out of injection molding machines.
Researchers found out that 3d-printed parts made with FDM could withstand a force of up to 148 MPa in XY-Direction and in ZDirection as well as in every 2-dimensional overlap up to 40 MPa. Researchers at DMRC generated standard stress-strain curves to compare the stresses of FDM with traditional injection molded parts. They found out that : “The FDM part printed in the X-direction performed equivalently to the injection molded part in stress, but fractured at a much lower strain. “ “The lower strain can most likely be attributed to the internal structure of the parts. Compared to AM processes, injection molding typically has lower porosity and greater homogeneity, leaving fewer imperfections in the structure of the material to encourage crack propagation. “
Research Credit: Matthias Fischer and Stefan Josupeit from DMRC (Direct Manufacturing Research Center)
MULTI-DIRECTIONAL LAYER PRINTING

For 3d-printing an object we have to notice that the printing orientation is crucial for the tensile strength . A side overlap whether its in XY-direction or in Z-direction has less tensile strength than the printing path itself. The solution for the XY-overlap is to rotate the printing paths on the next layer to get a cross-shaped stable compound .

But printing traditionally in 2.5D, that means printing on an XY-Plane and in Z-Layers gives us certain limitations in producing physically comparable objects to injection molded ones. So we are orienting the parts according to the best possible performance of the tensile strength we need for the object we want to produce.
MULTI-PLANE PRINTING
One solution could be to change the printing planes while printing from XY to XZ or YZ to create a crossshaped compound in every possible dimension. A research paper from Ismayuzri Bin Ishak from 2013 is tackling the topic : “Robot FDM Platform for MultiPlane and 3D Lattice Structure Printing “ . He is calling this process Multi-Layer-printing.
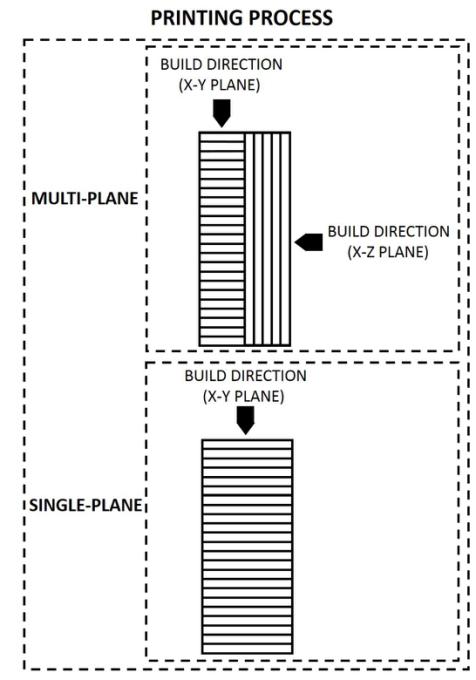
In his research paper he was testing if a multi-plane layer printing could affect the tensile strength of the 3d-printed parts. As conclusion of all of his tests he could increase the tensile strength as well as the yield strength and the modulus of elasticity of his 3dprinted parts .
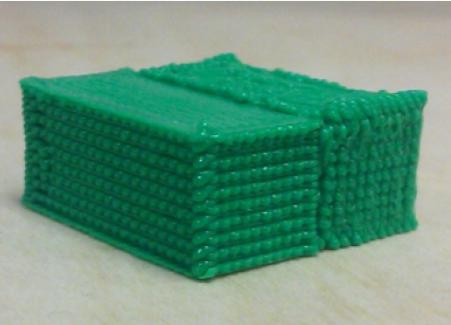
According to the desired mechanical properties of 3dprinted parts multi-layer printing gives a added value getting a step closer to the physical properties of injection molded parts.
For this advanced 3d-printing strategy most of the 3axis based 3d-printers are not working and at least a 4-Axis machine is needed.
MULTI-AXIS PRINTING
The next iteration of 3D-printing strategies following is the translation of printing on a two-dimensional layer in just two axis to a multi-axis printing acting simultaneous in all 3-axis of a 3d-space (XYZ). Instead of dividing every model in planar slices to create the printing layers, we can create layers based on the specified surface of each object. In this method we have to different approaches. We have antigravity printing which works in terms of thermoplastics just until a specified degree of overhang-angle and path-length and in terms of metal with much less restrictions.
This is priority used for lattice structures in a robotic setup for making fast and stable support or formwork structures with thermoplastics as well as with metals.

Curved, double-curved and freeform surfaces could be produced more efficient while the created printing paths are printed surface.
following the particular shapes .
By combining all different printing strategies in a process with the freedom of a robotic arm , 3d-printed structures could

The other method is 3d-printing on a mold or any already existing surface. This shape defines the shape of the be created with good structural behavior , fast and with a novel freedom of fabricating parts .
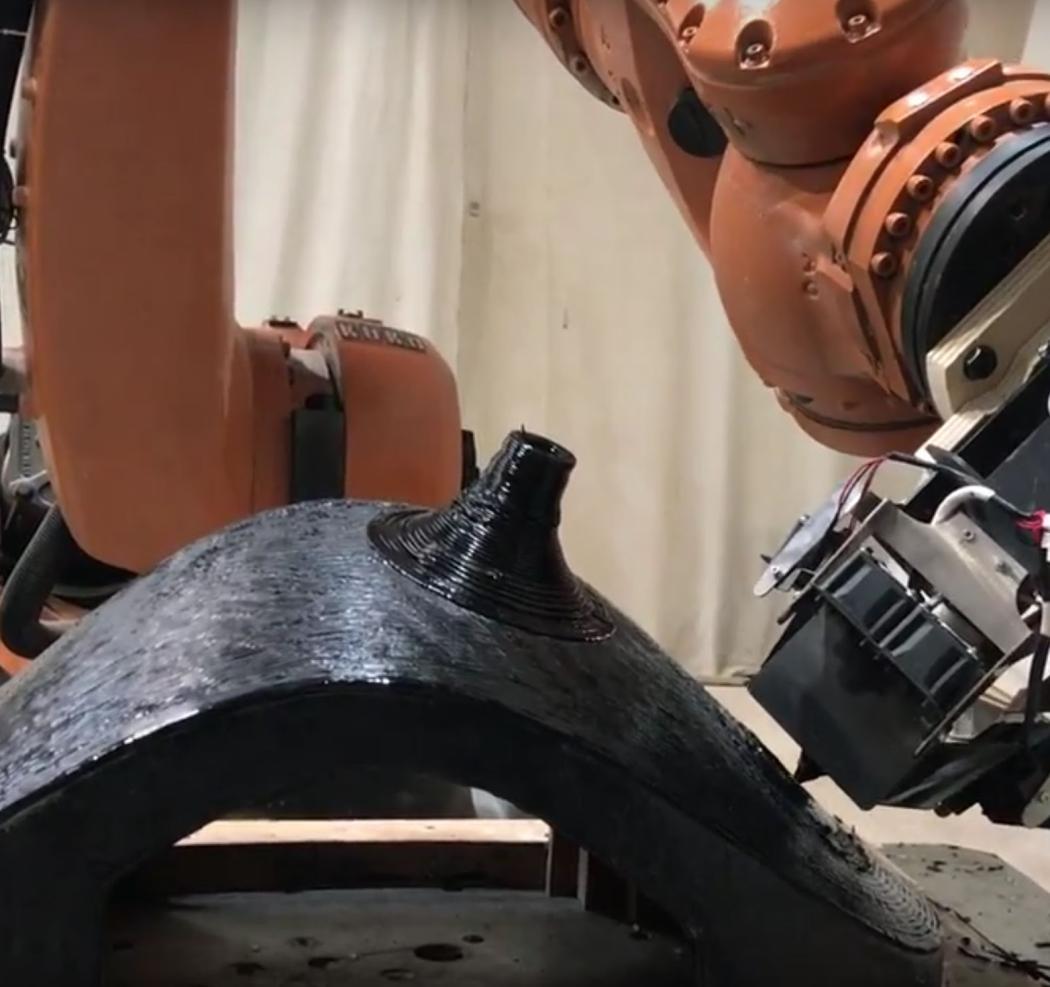
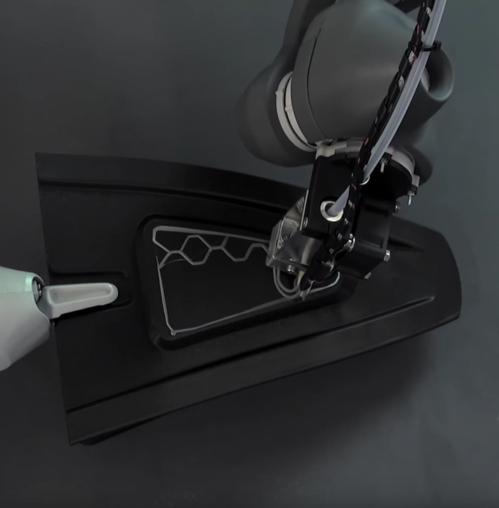