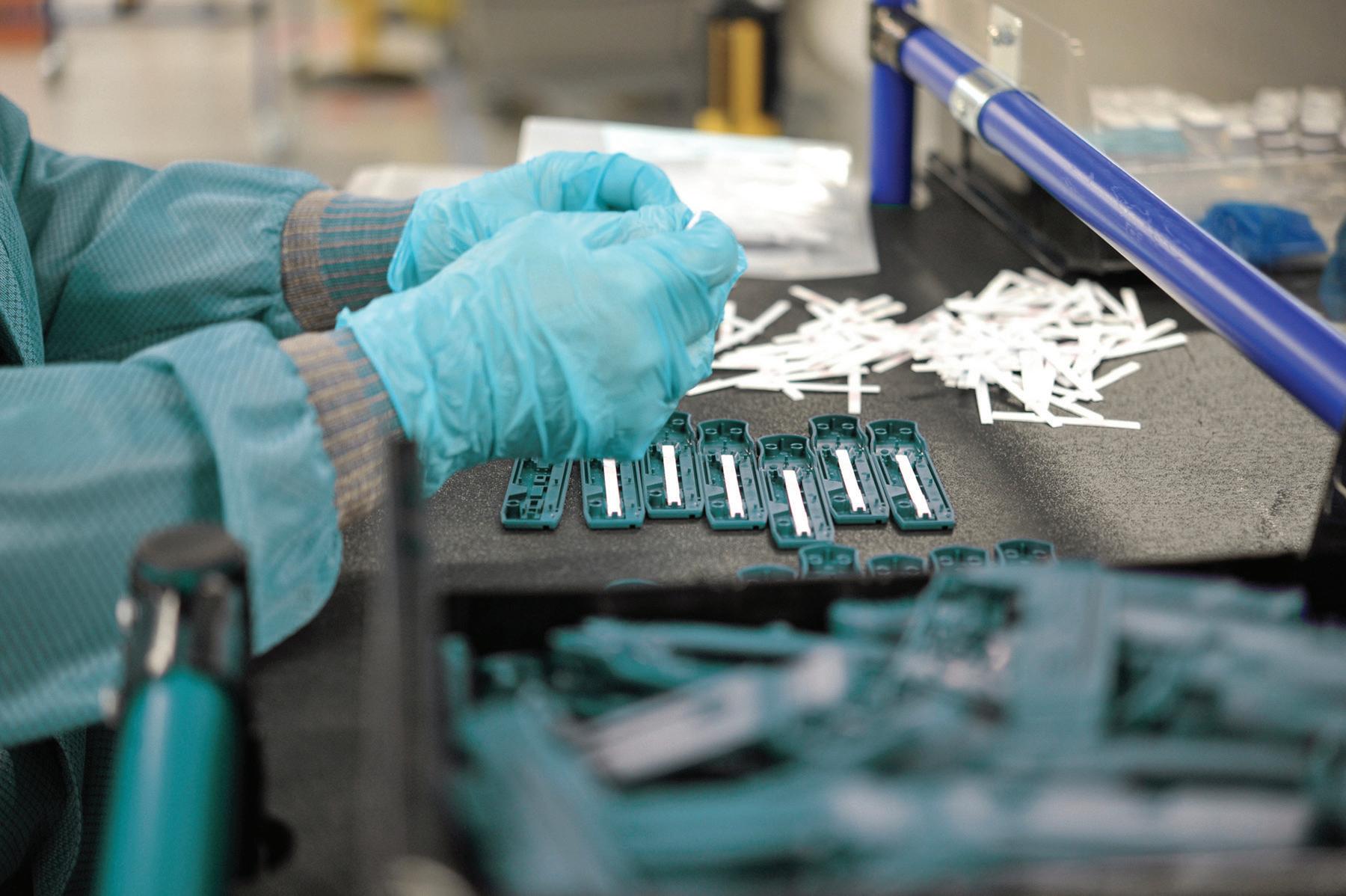
5 minute read
Components & assembly Step up to scaling up
from MPN NA Issue 17
by MPN Magazine
STEP UP TO SCALING UP
ADVANCEMENTS IN DETECTING AND PREVENTING COVID-19 BODE WELL FOR SIMILAR TESTS FOR OTHER MEDICAL CONDITIONS. KEVIN YOUNG, VICE PRESIDENT OF CORPORATE DEVELOPMENT & MEDICAL, WEB INDUSTRIES, INC., EXPLAINS HOW MANUFACTURERS CAN SCALE UP TO KEEP PACE WITH CURRENT AND POST-COVID DEMAND FOR RAPID DIAGNOSTIC TESTS.
In response to COVID-19, medical device OEMs and their suppliers are facing demand for vast quantities of reliable diagnostic tests that yield timely results. The demand will likely outlast the current pandemic and extend well beyond the many tests developed to detect the virus. The widespread distribution of COVID-19 tests, such as lateral flow immunoassay (LFI) antigen tests, is already generating increased interest in rapid tests for other medical conditions. Advancements in COVID-19 detection and prevention will assist in their development.
Scaling up to produce millions of rapid tests often requires manufacturers to make significant operations changes, especially in three categories: • Technology and automation • Supply and infrastructure • Staffing and workforce development.
TECHNOLOGY AND AUTOMATION
Before COVID-19, diagnostic tests were usually made manually and in small quantities (Figure 1). Production took place in separate batches as components moved from one process to the next. This was fine for making thousands or even tens of thousands of test devices per week but inadequate for largescale production.
For large quantities, manufacturers and their suppliers need fully automated and integrated production lines, including those that assemble multiple test device components. Each step of the test-making process must be mechanized, from the preparation of test chemistries to the application and lamination of test formulations to materials. Reel-to-reel (Figure 2) and pickand-place systems are examples of equipment that provide accuracy and speed, with little need for human intervention.
Beyond this, the sheer pace of production necessitates automated camera and vision systems to monitor the process. Such cameras use sensors and software algorithms to produce images and automate visual inspection tasks. They can quickly identify defects and alert operators when problems arise.
Figure 1: Pre-pandemic, LFI diagnostic test manufacturing was a highly manual batch-based process. (Photo courtesy of Web Industries)
SUPPLY AND INFRASTRUCTURE
Manufacturers may need to overhaul their plant infrastructure to house new production lines,
SUBSCRIBE TODAY
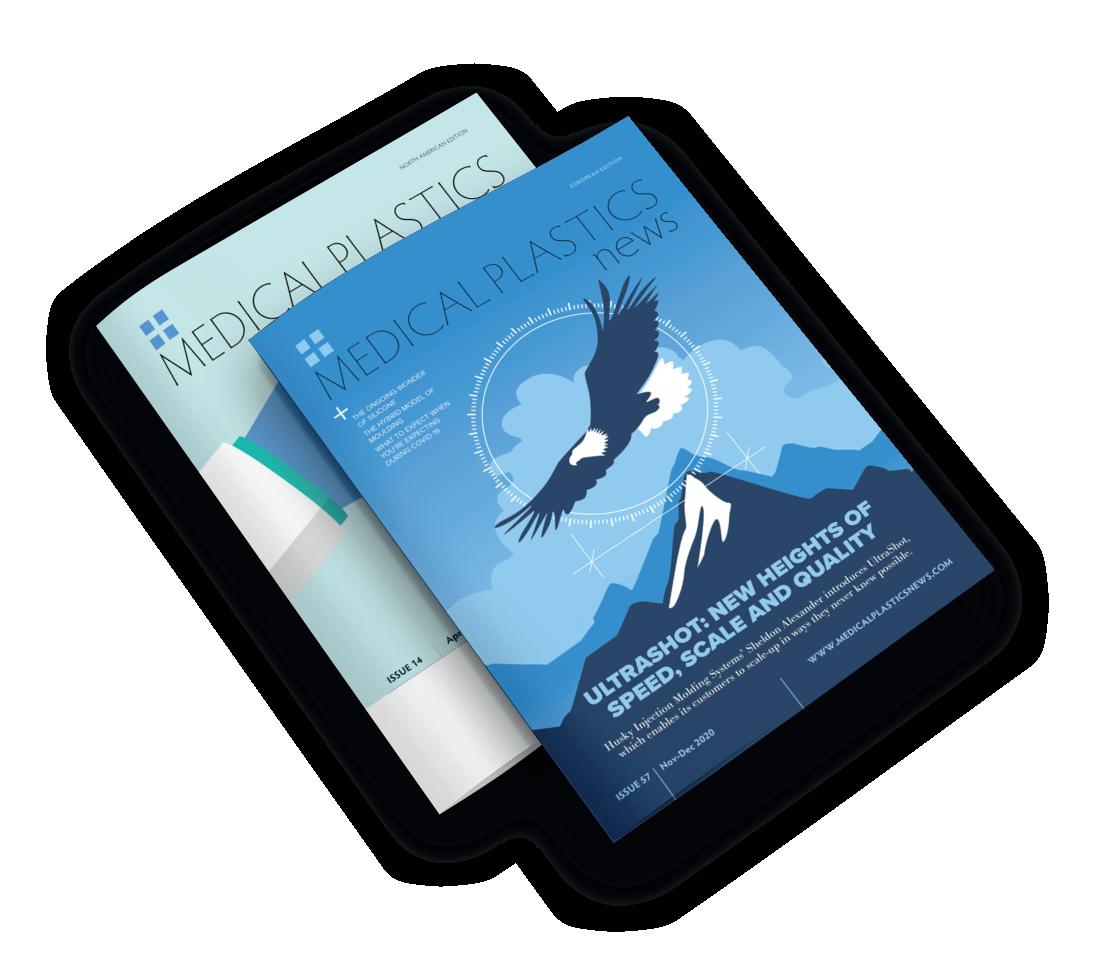
23278 FLL to FLL Connector
13619
Pinch Clamp
80361
Luer-Activated Valve Female Luer Lock Tubing Port
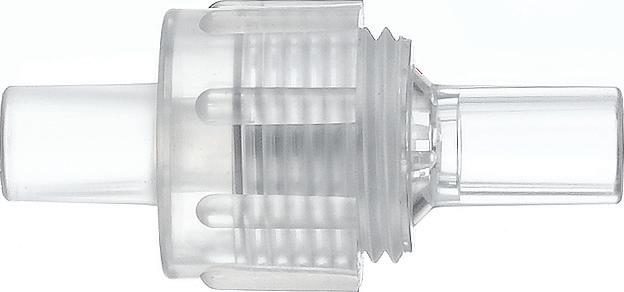
11083 High Flow Check Valve, Adjustable Pressure
61202
Cross Connector Barbed
65515
FLL Connector
11499
Elbow Connector FLL, ML with Spin Lock
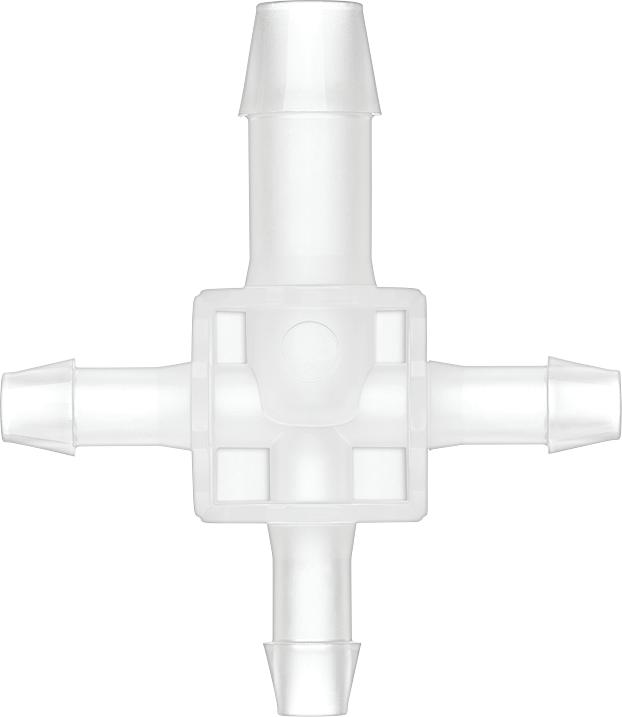
80368 Endoscopic Valve
99780 1-Way Stopcock FLL, MLS
All trademarks and registered trademarks are the property of their respective owners.
97365
Flow Control Switch FLL Inlet MLL Outlet
57030 Flexible Suction Connector
80199 Check Valve Tubing Port Inlet MLL Outlet Coated Stem
28305 Hydrophilic Filter FLL Inlet, MLL Outlet
Log on to qosina.com today to see our full product offering.
Qosina is a leading global supplier of thousands of OEM single-use components to the medical and pharmaceutical industries.
including expanding existing facilities or building new ones. The additional space might accommodate provisions such as dry rooms, which control temperature and humidity and are essential for diagnostic test production. In addition, new warehousing space is frequently needed to store test components and materials.
Scaling up also entails assembling a network of raw material suppliers and production partners to support high volumes. Here, experienced diagnostic test device CMOs can be a central partner. CMOs are often skilled at transferring technology among different production locations and are likely to be expert in flexible materials formatting and converting, and in the precisioncutting needed to manufacture the lateral flow test strips.
STAFFING AND WORKFORCE
Needs for high-volume production usually mandate a corresponding increase in labor and staffing. Workforces in some processes can grow by a factor of more than five. Although full automation eliminates some manual tasks, it creates greater demand for employees with specialized engineering, bioscience, quality assurance, and inventory management skills. Finding experienced workers to fill skill positions might call for training current employees, and new employees for new equipment and processes.
NEW ERA OF RAPID TESTS
Post COVID-19, needs are likely to grow for other diagnostic tests, a coming demand that offers business potential for medical device manufacturers and their suppliers. Many will be available over the counter and prove as easy to use as today’s pregnancy tests. They will be administered outside of clinical settings, be available over the counter at pharmacies, and performed at home. Results will be available in minutes instead of days. Scaling up to produce millions of rapid diagnostic tests will pose technical and organizational challenges like those encountered by producers who have stepped up to make COVID-19 tests. These include technology transfer, automation and human resources — areas where established outside contracting resources are available to smooth the transition.
In early 2020, the pandemic destabilized the aerospace industry, then Web Industries’ dominant business sector, and prompted the company to turn much of its CMO energies to its budding medical market operations in Holliston, Massachusetts. There, the company addressed sample orders from a potential OEM customer for rapid LFI antigen COVID-19 detection kits. Rapid LFI antigen tests recognize proteins on COVID-19’s surface by sampling a nasal or throat swab. Test results appear within 15–30 minutes.
Test devices are packaged in kits. Point-of-care test kits consisted of 30 LFI strips, individually housed in a plastic cassette and pouched in foil, along with a corresponding amount of extraction reagent buffer solution and collection swabs, and positive and negative control swabs. Dividers, a reagent holding tray and an IFU (Instructions for Use) card are also included. At-home tests contain most of the same components but are packaged in a smaller subset, for example, one test device, swab, and extraction reagent.
With the aid of supply partners, the Web Industries’ Holliston plant was soon producing thousands of antigen tests per week, earning approvals from the US FDA and the company’s now-contracted customer. But tens of millions of tests would be needed to satisfy incoming orders. Accordingly, the company accelerated its efforts by fully automating plant operations with pick-and-place and reel-to-reel machines and flow wrappers for automatic packaging. Management also linked reagent deposition, lamination and test strip cutting. By early 2021, the company was producing and shipping several million LFI antigen test devices per week to its OEM customer.
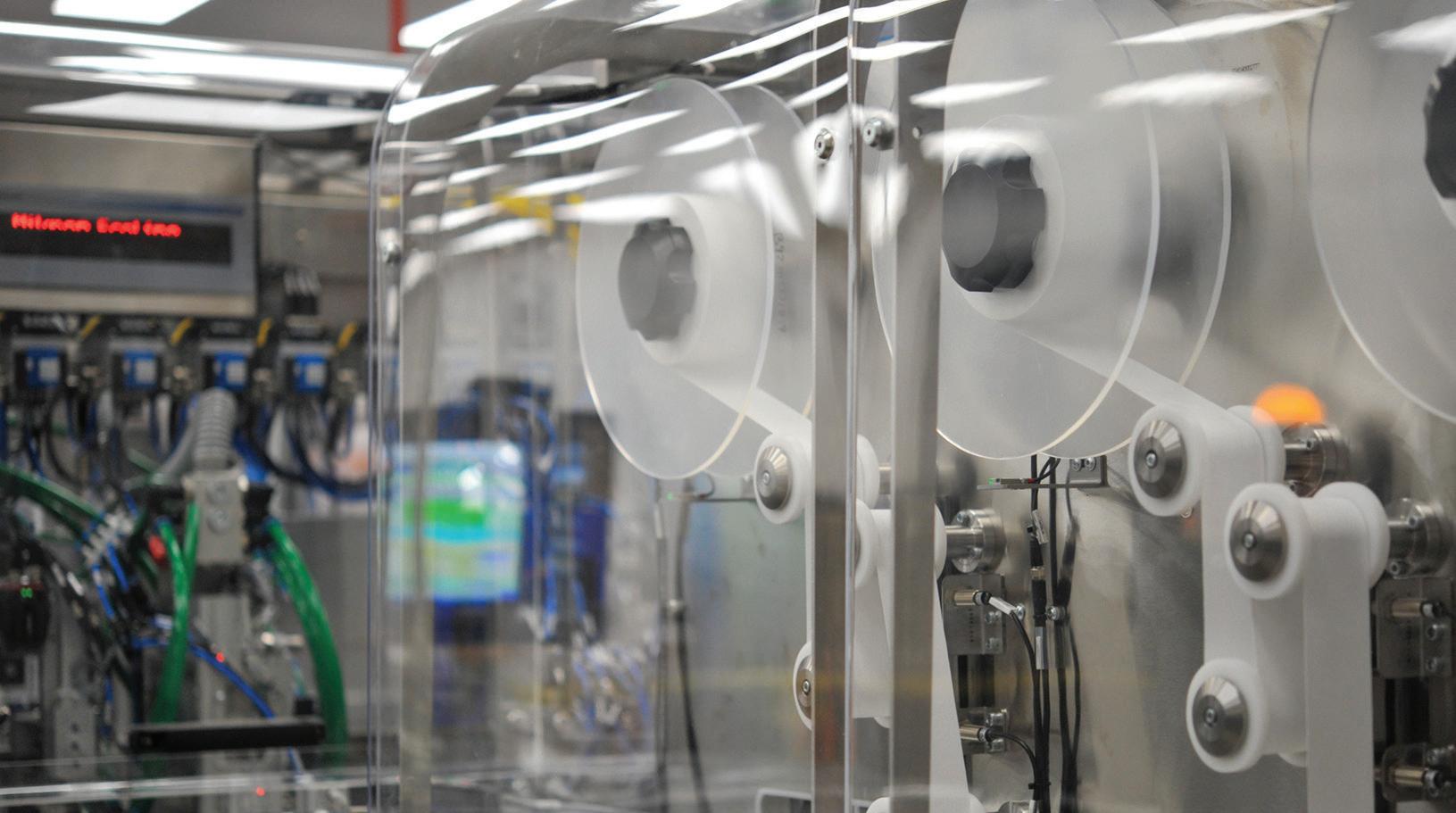
Figure 2: Reel-to-reel assembly and lamination of multi-layer test strips support high-speed manufacturing for large-scale medical testing programs. (Photo courtesy of Web Industries.)