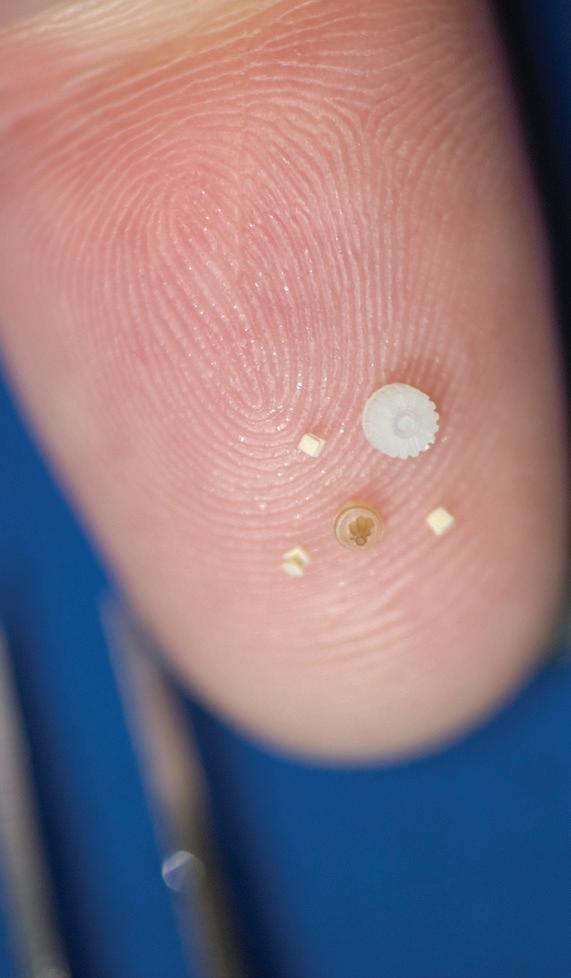
4 minute read
Cover story
from MPN NA Issue 17
by MPN Magazine
Micromanufacturing by numbers
ENGAGEMENT WITH A MICROMOLDER FOR A MEDICAL DEVICE PRODUCT DEVELOPMENT PROCESS WILL ULTIMATELY RESULT IN THE NEED TO MANUFACTURE PARTS, OFTEN AT VERY HIGH VOLUMES. MICROMOLDERS NEED TO EXCEL AT EVERY STAGE OF PRODUCT DEVELOPMENT, BUT, AS AARON JOHNSON, VP OF MARKETING AND CUSTOMER STRATEGY, ACCUMOLD, HIGHLIGHTS, THERE ARE PARTICULAR CONTINGENCIES THAT SURROUND VOLUME MANUFACTURING THAT MAKES SUPPLIER SELECTION ESPECIALLY IMPORTANT.
Micromolding typically requires the achievement of truly exacting and sometimes almost impossibly tight tolerances. In many instances the demand is for tiny parts or slightly larger parts with submicron feature sizes. When micron tolerances matter, the customer and micromolding provider must enter into a close partnership in product development, and it becomes hugely important that the micromolder owns, manages, develops, and innovates in every aspect of the supply chain. The “get it right the first time” headline over every activity plays to the vital importance of vertical integration, which enhances the quality, compliance, and conformance to design intent. Micromolders need to understand the critical to quality (CTQ) characteristics to manufacture parts successfully; these characteristics — including molding, assembly, and packaging — are important to the functionality of the product with regard to end-user experience.
In basic terms, the longer the value stream, the more disconnected the value stream, and the more variables can be introduced causing customer issues. Vertical integration supports a shorter value stream reducing silos and suboptimized processes.
VOLUME MANUFACTURING
Variability is the enemy of high-volume micromanufacturing, and so focus needs to be maintained on implementing process controls that drive repeatability all the way from cutting micro tool steel to measurement and validation methods.
Typically, medical device OEMs want the highest quality products at the lowest possible cost. Product quality requirements are driven by the Voice of the Customer (VOC), which enables good micromolders to identify critical medical product characteristics which need to be verified during production. Cost, however, is more than just the price charged to mold a part; it also includes the time it takes to get a product to market, whether defects make it to market, and the levels of supply consistency. Micromolders should strive to supply the highest quality products, through validated processes, with short timelines to market. Realistically, this can only really be accomplished through vertically integrated processes and utilizing process validation.
When short-listing potential micromolding suppliers, from a production perspective there are some key questions that medical device OEMs need to ask to ensure the micromolder is equipped to achieve often exacting objectives. First, do you design, build, and maintain your molds? Second, what measurement capabilities do you have on site? Third, what are your methods of validation (DOE, IQ, OQ and PQ)? Finally, what resins do you have experience with in production?
The successful manufacture of micromolded medical products is almost entirely down to the VOC. But it is important to realize that the end user isn’t the only customer — there are customers throughout the entire value
stream. The shorter and more centrally located the value stream the quicker concerns can be raised and resolved.
ASSEMBLY
When dealing with miniaturized plastic medical parts and components, the assembly stage of the product development process must be discussed and considered early in the design cycle, demanding a collaborative and pragmatic relationship between medical device OEM and micromolder. When dealing with microscale parts and components, the cost of manual assembly is prohibitive and often requires levels of precision when dealing with submicron tolerances that are impossible to achieve. Automated assembly is, therefore, a must in most micromolding scenarios, requiring that medical device OEMs select a micromolding partner that is able to understand the methodology of micro assembly and achieve the extreme positional accuracy required.
The demand is for a laser-like focus on design for micromanufacturing (DfMM), which crucially influences the success of every part of the overall product development process, including assembly. The importance of considering assembly at the design stage of a micromolding product development process is huge, and is an important factor for any project. Micromolding just adds more variables that need to be controlled than a standardsized product for which there are many different manufacturing solution partners in the marketplace. Micromolded parts can be difficult to feed, inspect, and manipulate without causing damage. Capturing a micromolded part as it comes out of the mold is often difficult, as is orienting a micro part after molding. Capturing a part at mold ejection and immediately assembling is often the only route to efficient assembly with low waste.
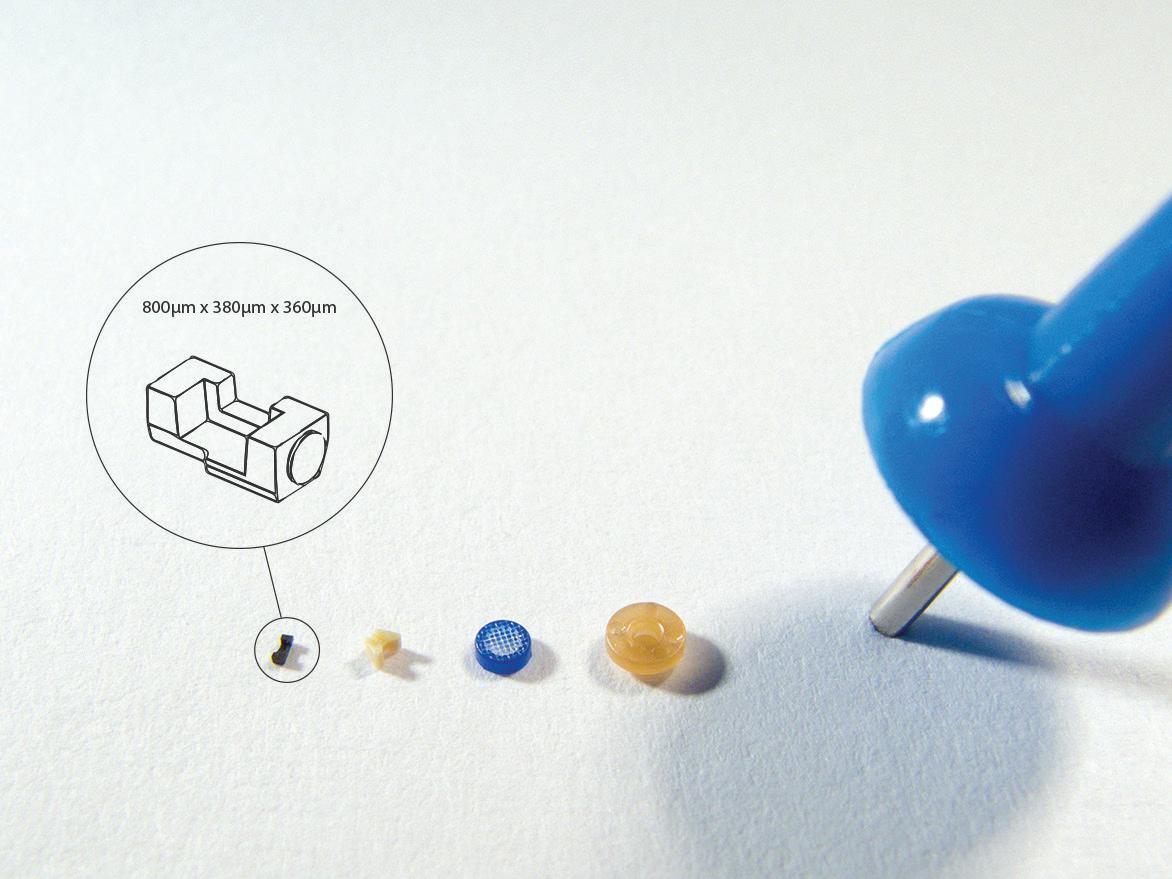
All such considerations should be bottomed-out at the design stage to keep costs under control so a medical device OEM can maintain margins and provide a product to the marketplace at an acceptable price.
SUMMARY
Before embarking on a micromolding project, medical device OEMs should focus on the mold design, mold build, and quality measuring capabilities of the vendor they are engaging to mold their parts. If molders lack the ability to design, build, and measure high-quality molds to extremely tight tolerances they will struggle to produce consistently high quality parts to tight tolerances at high volume. Producing products to specifications that only allow microns of variations to a specification is much more challenging than producing a product with significantly larger variation allowances. A poorly designed and built tool can eat up your entire variation before you even mold a part, essentially killing the project. So, when micron tolerances matter, informed supplier selection is the absolute key to high volume manufacturing success.