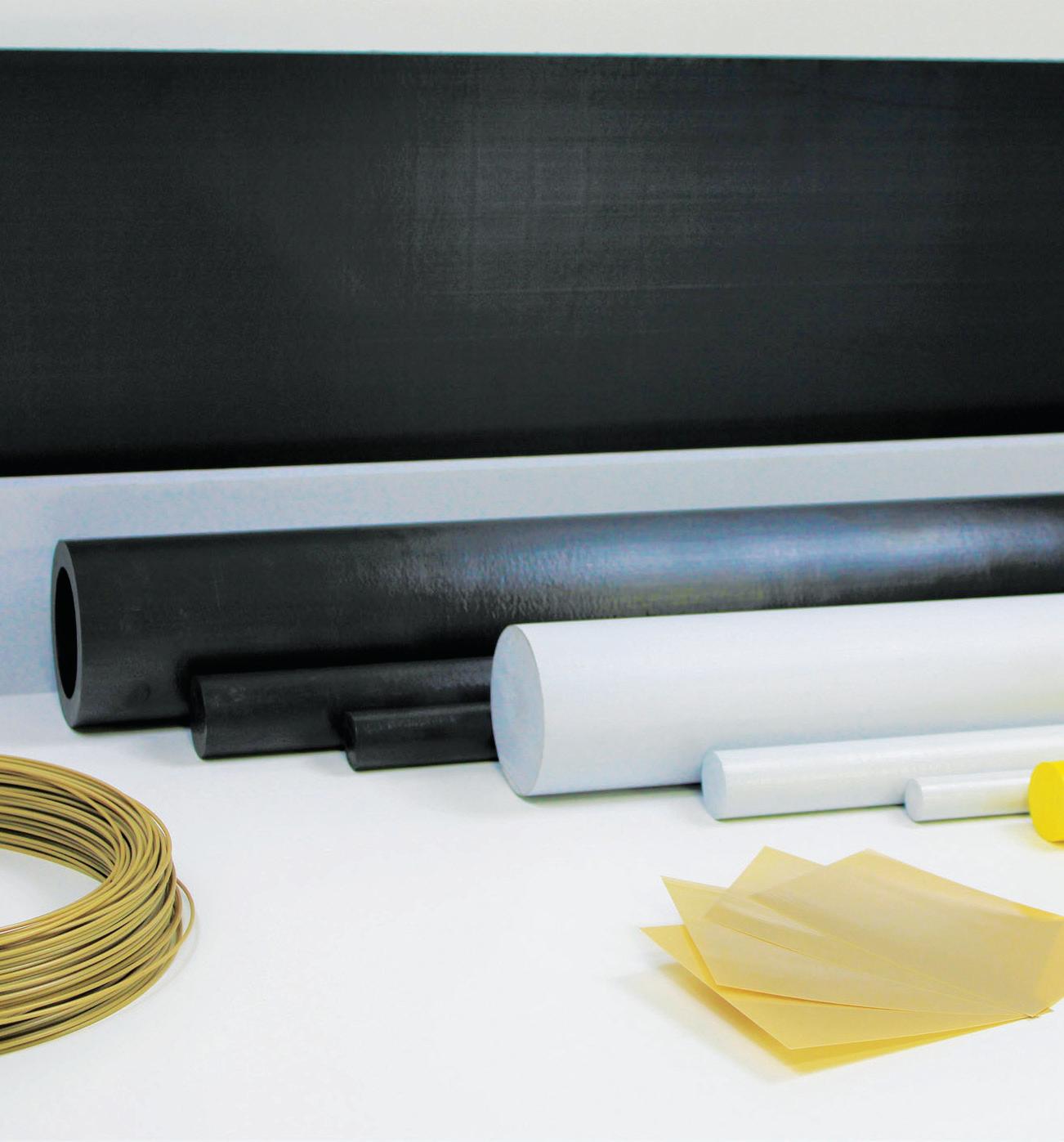
5 minute read
Digital spy
from MPN NA Issue 17
by MPN Magazine
PARTNERSHIP UPDATE
www.fosterpolymers.com www.drakemedicalplastics.com
Foster and Drake Medical Plastics create one-stop shop
Foster Corp., a provider of polymer solutions for medical devices, has signed an exclusive sales agreement with Drake Medical Plastics, a converter of highperformance polymers into stock shapes and precision parts. The agreement streamlines their services to customers in the medical device marketplace globally, and creates a one-stop shop for high performance polymers in the form of machinable shapes.
Based in Cypress, Texas, Drake Medical Plastics provides ‘resin-to-shape’ polymer conversion into rod, plate, and tube for machined components for the medical and life science industries. Stock shapes provide customers with a quick and economical route for prototypes and scaling up to commercial manufacturing. Depending on volume, machined parts can also be a flexible platform for production parts with little to no capital investment.
Currently, Foster provides highly engineered materials and compounds to be used in specialty medical and life sciences applications. With this collaboration, medical compounds including highly filled materials will be available in machinable shapes made from Foster’s full range of polymer compounds.
www.qosina.com
EXPANDED PRODUCT LINE FOR SINGLE-USE BIOPROCESS COMMUNITY
Global supplier of OEM single-use components to the medical and pharmaceutical industries Qosina has extended its product portfolio, developed specifically for the needs of the single-use bioprocess industry.
The company now offers a comprehensive selection of components for the design, development and manufacture of single-use systems.
Scott Herskovitz, Qosina President and CEO, said: “Our experience serving the needs of regulated customers positions us well to expand our products and services for the single-use bioprocess community. We have leveraged this experience and our extensive supply chain to provide a muchneeded resource for bioprocess, vaccine production, and cell and gene therapy.”
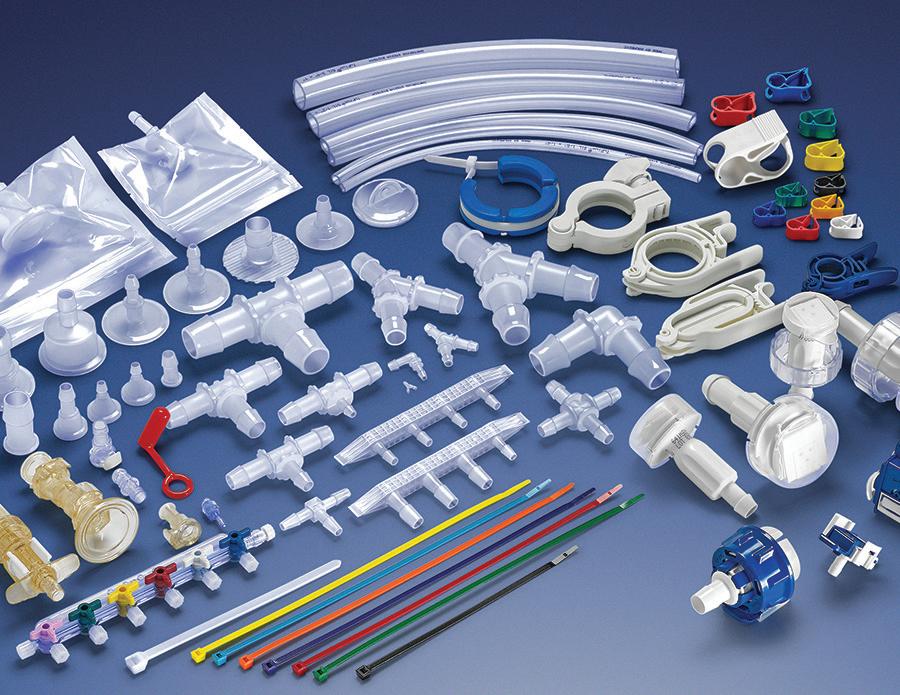
COMPANY UPDATE
www.siigroup.com
SI GROUP INVESTS TO EXPAND THE US CHEMICAL MARKET
Performance additives company SI Group has said it plans to invest more than $50 million across three manufacturing sites in North America to install globally competitive main antioxidant capacity to increase its supply for this important and growing market segment.
This investment will expand the US chemical market, with a focus on supplying strategically located, critical raw materials to key partners in the region. With SI Group’s current extensive antioxidant manufacturing footprint in the US and backward integration, this planned expansion will increase its security of supply by offering a fully integrated portfolio of phenolic antioxidants in the US. 2022. These projects are expected to create short-term construction jobs, followed by permanent manufacturing jobs once construction is complete. With projected growth in the polyolefins market in the US, the expansions will enable SI Group to increase its domestic supply to match growing demand, and further strengthen its position as a key partner to its customers.
www.canadianshieldppe.ca Manufacturer launches new line of PPE for Canada’s frontline
The Canadian Shield, a Waterloo Region-based medical device manufacturer has added a new proprietary PPE solution to its product line. The new attachable eye shield, called the Vizor, is a patent pending piece of PPE designed to be a simple, affordable, and practical solution for personal protection on Canada’s frontline.
Made of 100% recyclable plastic, the Vizor aims to improve patient and worker safety in healthcare settings by offering an easily accessible additional barrier of protection.
The Vizor, which comes flat-packed for easy storage and distribution, attaches to almost any face mask in seconds. This simple, innovative design alleviates a number of issues for frontline workers, including reduced availability of traditional combination masks, and limited space for storage and distribution of PPE. Furthermore, the ability to separate the Vizor from the mask body means that the Vizor can be fully recycled, helping to reduce the costs associated with healthcare waste removal.
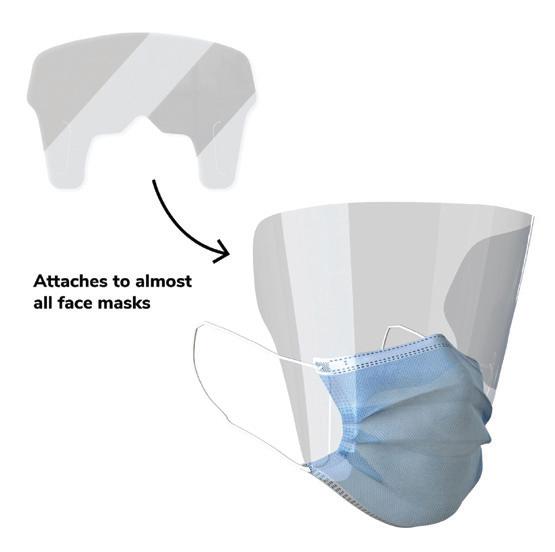
SUSTAINABILITY UPDATE
www.newageindustries.com NEWAGE CELEBRATES A DECADE OF SOLAR ENERGY
Back in the summer of 2010, NewAge Industries made the decision to embrace solar power and reinforced the roof at its headquarters. The construction culminated on June 8, 2011, when a group of the plastic tubing manufacturer’s employees flipped a switch and began using solar energy.
The power system, consisting of 4,082 rooftop solar panels, has the capacity to produce up to one megawatt continuously and has been doing so for the past 10 years.
“It was our most ambitious project to date,” said Ken Baker, the company’s CEO. “As a US manufacturer, we insisted on USmanufactured products — the solar panels, the racking system that holds all the panels, the inverters that convert the electrical current — and it took a lot of research to source everything.”
NewAge, which manufactures single-use molded tubing assemblies used in vaccine production, in addition to plastic tubing, made the switch to solar power in conjunction with several other green initiatives including installing energy-efficient lighting.
The solar energy system originally contributed more than half of the energy needed at NewAge’s headquarters. Expansions at the facility have since increased electricity needs, but the company says it is proud to be harnessing the sun’s energy and putting less pressure on the community’s power grid.
talking POINT
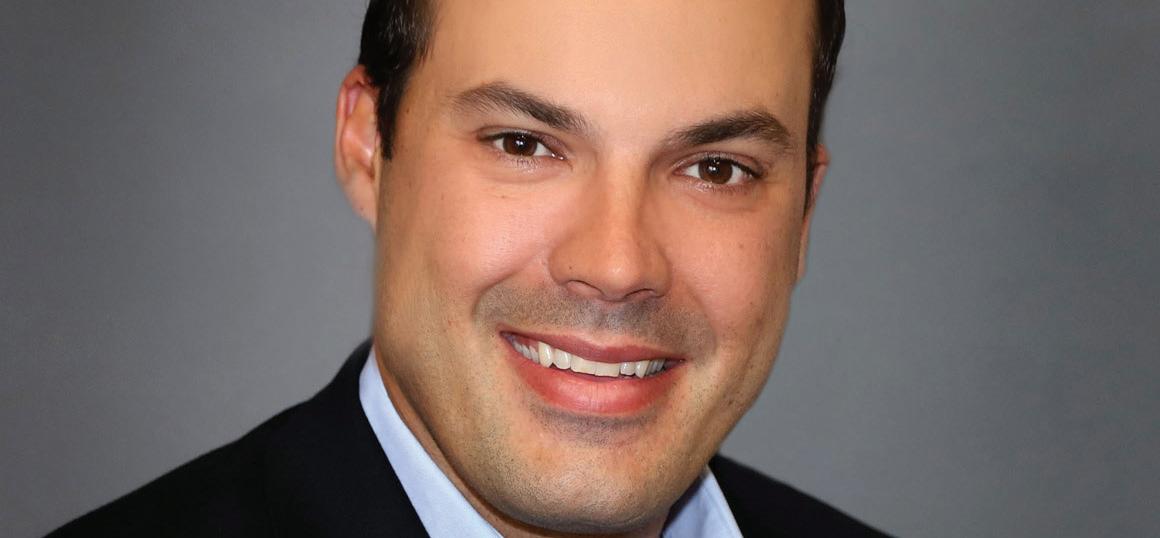
www.materialanddesign.com Andy Jorgensen, CEO of Material & Design Solutions
What was the motivation behind MDS’ recent acquisition of APS Plastics & Manufacturing?
Material & Design Solution’s (MDS) acquired the assets of APS Plastics to have better control in our supply chain as it relates to the machining of tight tolerance thermoplastics components. Having control of the planning of work and scheduling allows MDS to shorten lead times and improve on time delivery to our customers. The acquisition gives MDS milling capabilities beyond that which our suppliers could provide and ensure the demanding quality requirements of the customers we serve.
Does this acquisition represent MDS’ first interaction with the medical plastics sector?
Yes, although John Jorgensen, MDS Chairman, has done business in the field with major players in the US and Europe (while President and CEO of Greene Tweed).
How will medical plastics customers benefit from the acquisition?
All the different industries that MDS serves demand the highest levels of quality. The medical plastics customers’ demands are a good fit with the values and strategic objectives shared by all MDS employees.
What’s your view on the “Made in the US” ethos?
MDS is committed to providing our customers with high-quality manufactured parts, in short lead times with on time delivery. We have a strong preference in sourcing our raw material and other subcomponents with made-in-USA product. Our commitment is to our customers, and if the technology or supply base is unable to support us in meeting those customer requirements, we will source globally.