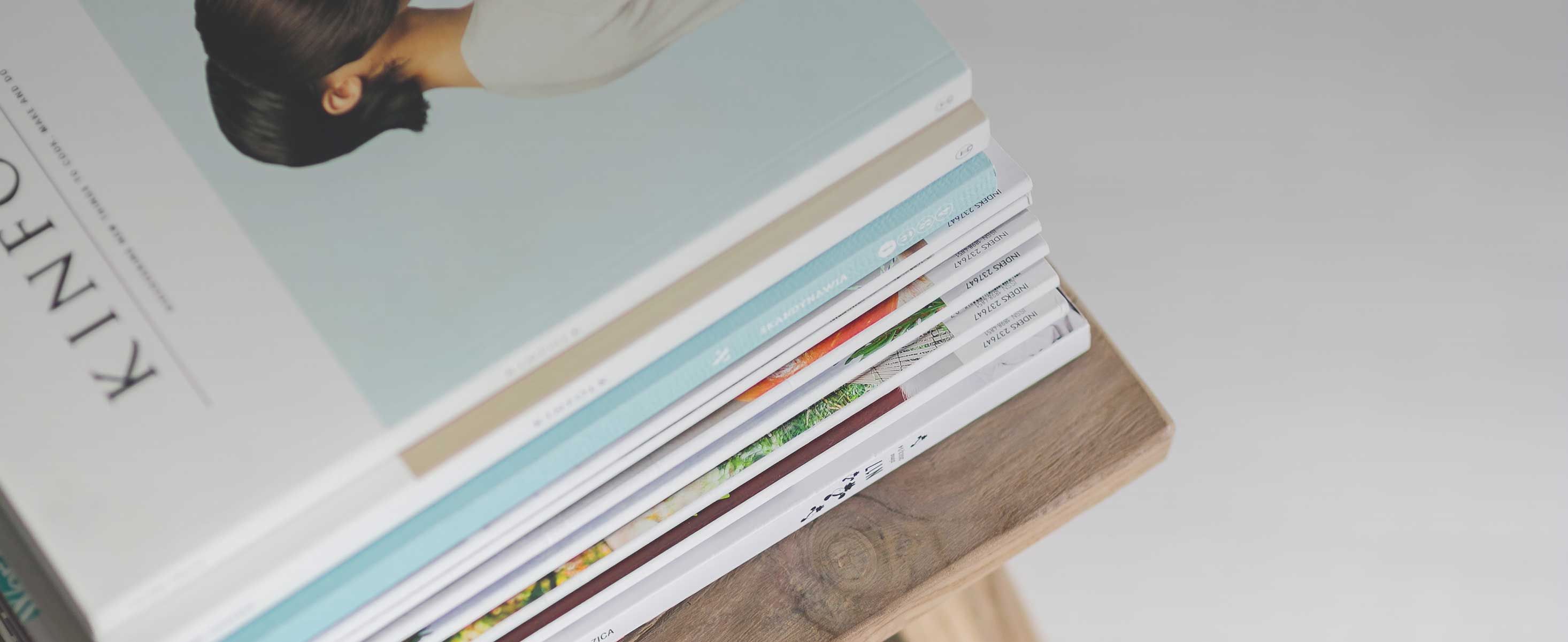
5 minute read
Tubing: The eight-point path to design enlightenment
from MPN NA Issue 17
by MPN Magazine
The eight-point path to design enlightenment
CARL GOUNDRY, PRODUCT MANAGER, TEKNI-PLEX, DISCUSSES EIGHT KEY FACTORS MEDICAL DEVICE INNOVATORS SHOULD CONSIDER WHEN ENGINEERING TUBING SOLUTIONS FOR EMERGING APPLICATIONS.
Medical device companies are innovating at an exponential rate, but they must consider the following eight factors to ensure a successful product development design process.
INTRICACY OF DESIGN
Improvements in patient safety and procedural efficiencies are driving innovative design technologies that require more complex components to ensure product performance. Demands on product specifications are tighter and quality standards more stringent. There is increased pressure to ensure fit, form, and function are right first time. Device design engineers are constantly seeking to partner with organizations that can push boundaries and work collaboratively towards meeting new product innovation requirements.
Aligning with a well-experienced team — skilled on all aspects of the design journey, from conception to commercialization — is vital to ensure the correct decisions are made at every stage of the development process. Early engagement on design, material selection, conversion, and assembly with the right partner is invaluable towards the success of new product development and launch.
INCREASING PRECISION
Demands are increasing for even higher levels of surgical procedural precision, putting advances in material and tubing technology at the forefront for device innovation. Comfort, speed and minimally invasive procedures are all attributes that positively affect health and wellbeing. Working with a solution provider that can engineer tubing with these desirable attributes is critical to procedure success.
For example, surgeons are relying on robots to perform surgical procedures that would previously have been impossible; pills with cameras are replacing endoscopes; tiny catheters can be used to access every vessel in the body. These technologies have been designed to minimize trauma and improve patient recovery rates. This need for miniaturization is driving more demanding and tighter tolerances. The end result is more pressure on medical device engineers and further pushing of the boundaries of material science.
AFFORDABILITY FOCUS
People worldwide are living longer, primarily because of access to better healthcare and the advances in medicine during the past 20 years. People are, therefore, more likely to go through an increasing number of medical procedures during their lifetime.
This added cost pressure on the healthcare system requires control of cost to allow device manufacturers to keep pace with ever-growing demand volumes which allows equal access for all. Efficiency of design and material selection are critical elements in this regard and as such must be afforded a great deal of consideration to ensure a device remains viable during its expected lifetime.
REGULATORY EXPERTISE
Being aware of, and compliant with, ever-changing regulatory requirements around the world is critical for any medical device manufacturer. The latest medical device regulations (MDR) in Europe, for example, have different requirements than those found in the US and China. Suppliers to medical device companies must be well versed and up to date with these stipulations, including approved ingredients, toxicity testing, validation steps, labeling requirements, and registration documentation and recording.
Your medical tubing partner should exhibit proficiency in best-in-practice manufacturing processes, as well as quality systems optimized for medical device products. Look for companies with decades of experience supporting its customers throughout the regulatory submission phase, regardless of geography.
SPEED-TO-MARKET
Working with a tubing supplier who knows how to remove weeks and months from the development timeline is an important asset to meeting project milestones. For example, suppliers heavily focused on R&D can help you to reach your end goal quicker, while at the same time meeting critical performance and commercial criteria.
Rapid turnaround on material/formulation changes, customized trial runs and prototype sampling are essential for delivering shorter development times. These capabilities, therefore, are an important ask of any supply partner. The greater the depth of expertise in material science and processing technology, the greater the rate of success.
PLAN FOR THE FUTURE
As conception, design, development, validation, and final commercialization of a medical device can take years to complete, medical device companies do well to work with tubing suppliers who can support their long-term vision and aspirations. Need for change may arise at any stage, and every effort should be taken to limit the impact of such a change.
The three most common reasons that we have encountered necessitating a change are transfer of manufacturing site (localization or globalization), obsolescence of a raw material (more and more common nowadays), and engineered change (usually an efficiency improvement or cost-saving initiative). Partnering with companies specializing in the medical sector will proactively address all three. When evaluating options look for global reach and high levels of raw material/formulation design control and integration.
VISION FOR SUSTAINABILITY
There is a global spotlight on sustainability, whatever the product or market segment. Medical devices are not exempt, particularly as more disposable devices enter the marketplace. Ensuring the world has access to medical devices that are both safe and sustainable requires a high level of know-how combined with a commitment towards social accountability.
Responsible companies should look to associate themselves with like-minded parties that share the same environmental values and are willing to work collaboratively, with passion and urgency, towards a common goal. Innovations in material science are likely to play a big part in this arena in the coming years; it is important to act early, or risk being left behind.
MEDICAL SECTOR EXPERIENCE
Now, more than ever, it is essential to align with a tubing manufacturer that is fully ensconced in the medical sector. Supply partnerships with skilled companies that are proven experts in the medical arena need to be nurtured to ensure all aspects of new product development are covered.
By doing so, you will help to mitigate potential problems/ risks in quality, regulatory failures (or product recalls), bridge technology gaps and prevent shelf-life problems — all of which can stem from a lack of in-depth understanding of the demands placed on the medical device sector.