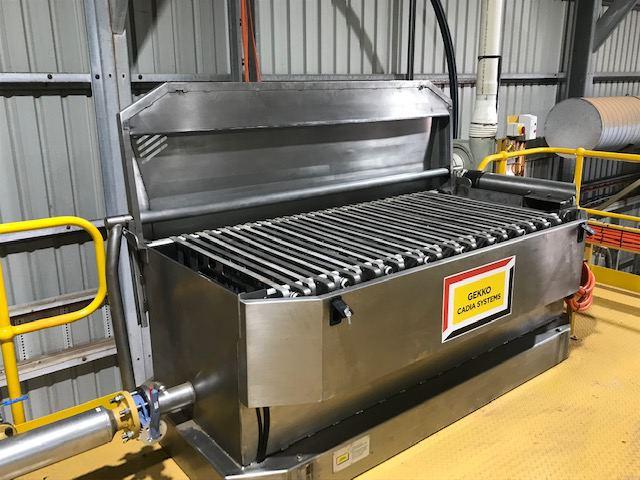
2 minute read
Çlean-in-Place Electrowinning
Çlean-in-Place Electrowinning. It's a concept that when you see it in acon seems obvious. But for years the process used in ADR plant goldrooms in gold mines around the world, has involved the removal of individual cathodes from the electrowinning cell by means of overhead gantry to a dedicated wash-bay for recovery of gold sludges.
“It's me consuming, ergonomically demanding on operators and fraught with the potenal for gold sludges loses to the goldroom floor” says Sean Galvin, Engineering Manager at Cadia Systems – a Perth based mining equipment manufacturer.
Advertisement
Mr. Galvin was, for over a decade, formerly manager and designer at the Equipment Division of Como Engineers – another Perth based Engineering Consultancy and Equipment manufacturer. Having been responsible for design and commissioning of goldroom equipment and modular eluon systems worldwide, he first hand experienced the short comings of cell cleaning - even on the electrowinning cell designs he had been responsible for
Issues common in goldroom cell cleaning acvies include dealing with heavy lids requiring either counter balances for winches to li open, slow movement of overhead gantry cranes when relocang cathodes or anodes, heavy cathodes which were oen man handled in and out during cleaning processes, and problemac connecons of cathodes and anodes to the main busbars.
“I remember commissioning a system for Metso in Finland in 2011 on Christmas day” he states, “they were 800 sized cathodes with 40 cathodes over two split cell designs.”
“Aer moving the first few to the wash-bay using the overhead monorail I just gave up”
Mr Galvin instead proceeded manually hauling the cathodes out of the cell one by one and laying them on top of the remaining anodes and cathodes in the cell. “That was my version of clean-on-top of cell”, he laughs. Cadia Systems specialises in the development of innovave technologies for the gold processing industry. The business has a strong focus on cleanroom style technologies that bring safety improvements for operators. The equipment also has a clear design focus on improving recoveries and opmising performance.
Their proprietary protected EC Clean-in-Place Electrowinning Cell was developed a year aer Mr Galvin started Cadia Systems.
Ulising a novel automated liing mechanism, the cell lis the anodes and cathodes away from the main connecng busbar connecons, allowing the anodes and cathodes to be slid one by one across the cell to provide access to the cathode face for insitu, in-cell washing.
An addional clever addion to the cell designs include a near neutral-pivot, low weight/high rigidity cell lid. The lid simply slides back with a minimal operator pressure to the front of the lid. For larger cells, which can be as large as 1200mm cathodes in size, the lids are also available with automated opening and closing.
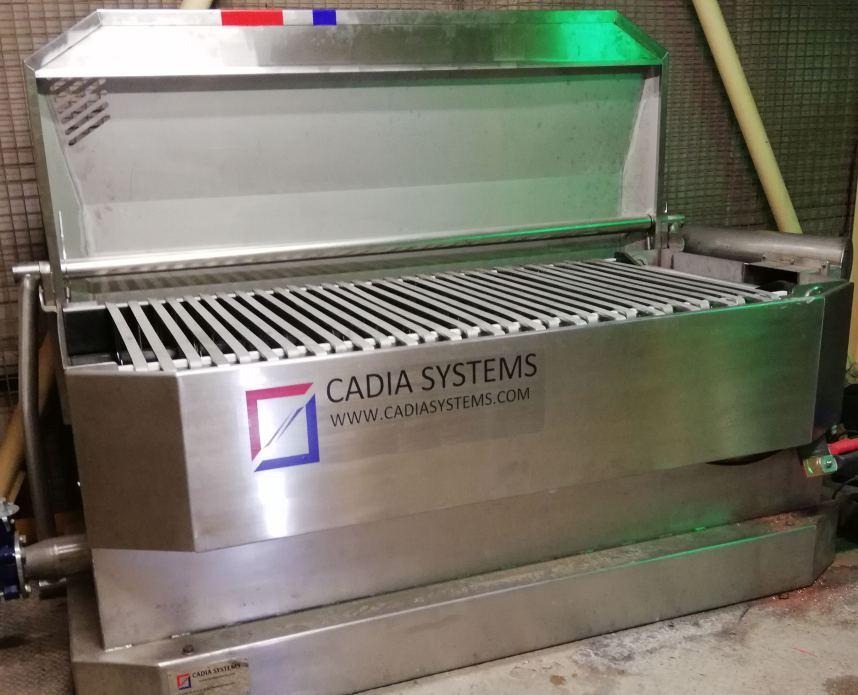
The cells also have front mounted busbars that are located out of the vapour zone to minimise corrosion from ammonia fumes. The busbar contains stud connecons which provide ght inter-busbar connecon ghtness to avoid hot-spot connecons. So no more losing those pesky nuts. A guard protects the busbars when in operaon, but also forms part of an inbuilt keyed locking mechanism for security of the precious metals while in operaon. Anodes are manufactured to provide longer design lifeme, and cathodes can accommodate either mild steel or stainless mesh or more common pre-made pillows.
“The product has really been a great success with clients!” says Mr Galvin, “Goldroom operators love them and site management love the enhanced safety and recovery aspects”.
Cadia Systems has also entered a collaborave arrangement with Gekko Systems for the design and supply of modular eluon systems using Cadia's equipment and design experience and Gekko's world-class engineering, manufacturing and support services.
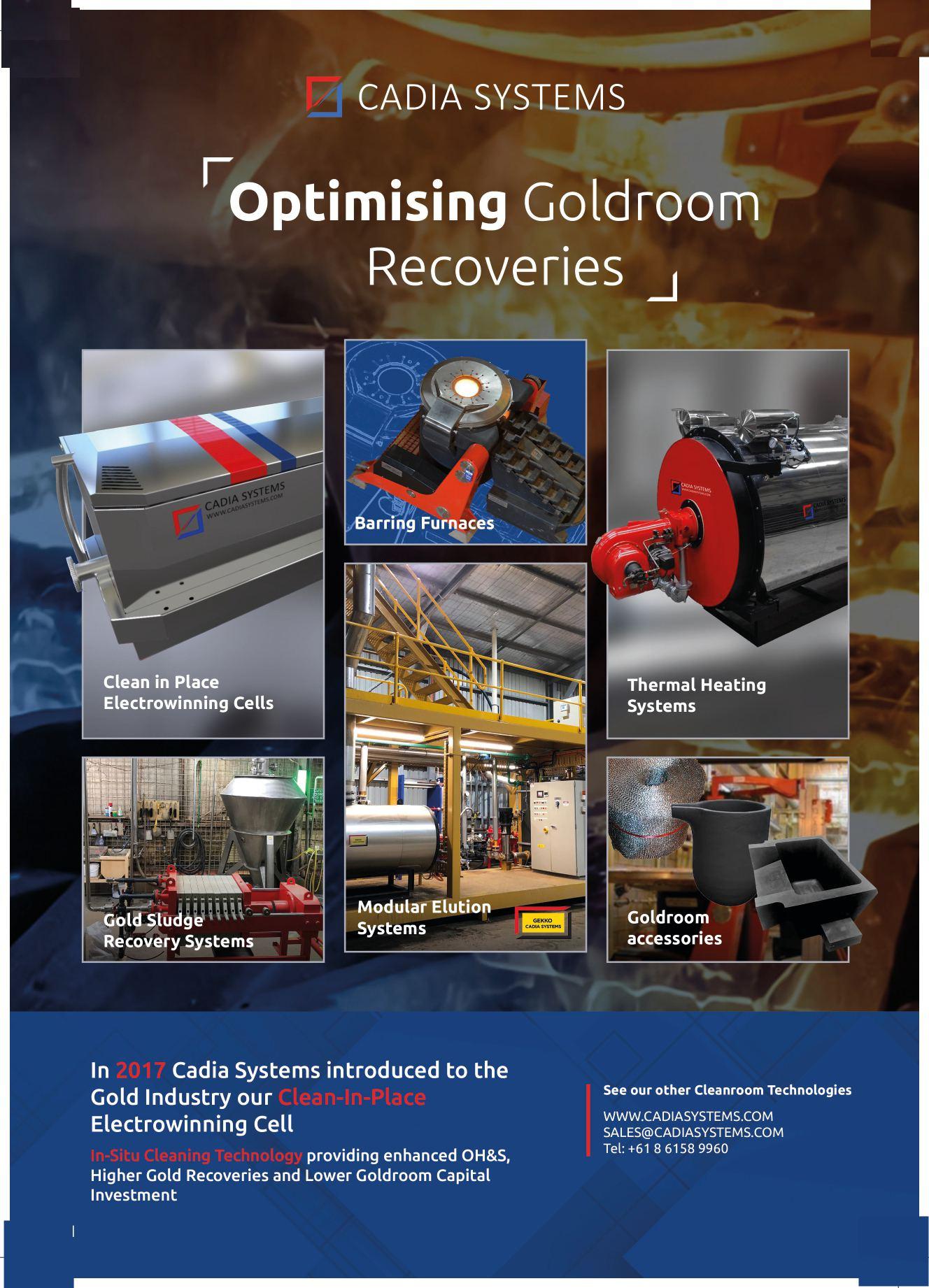