
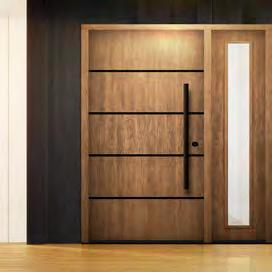
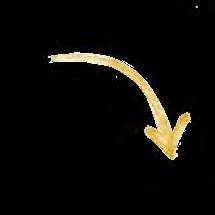
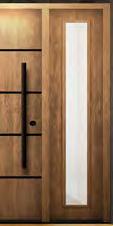
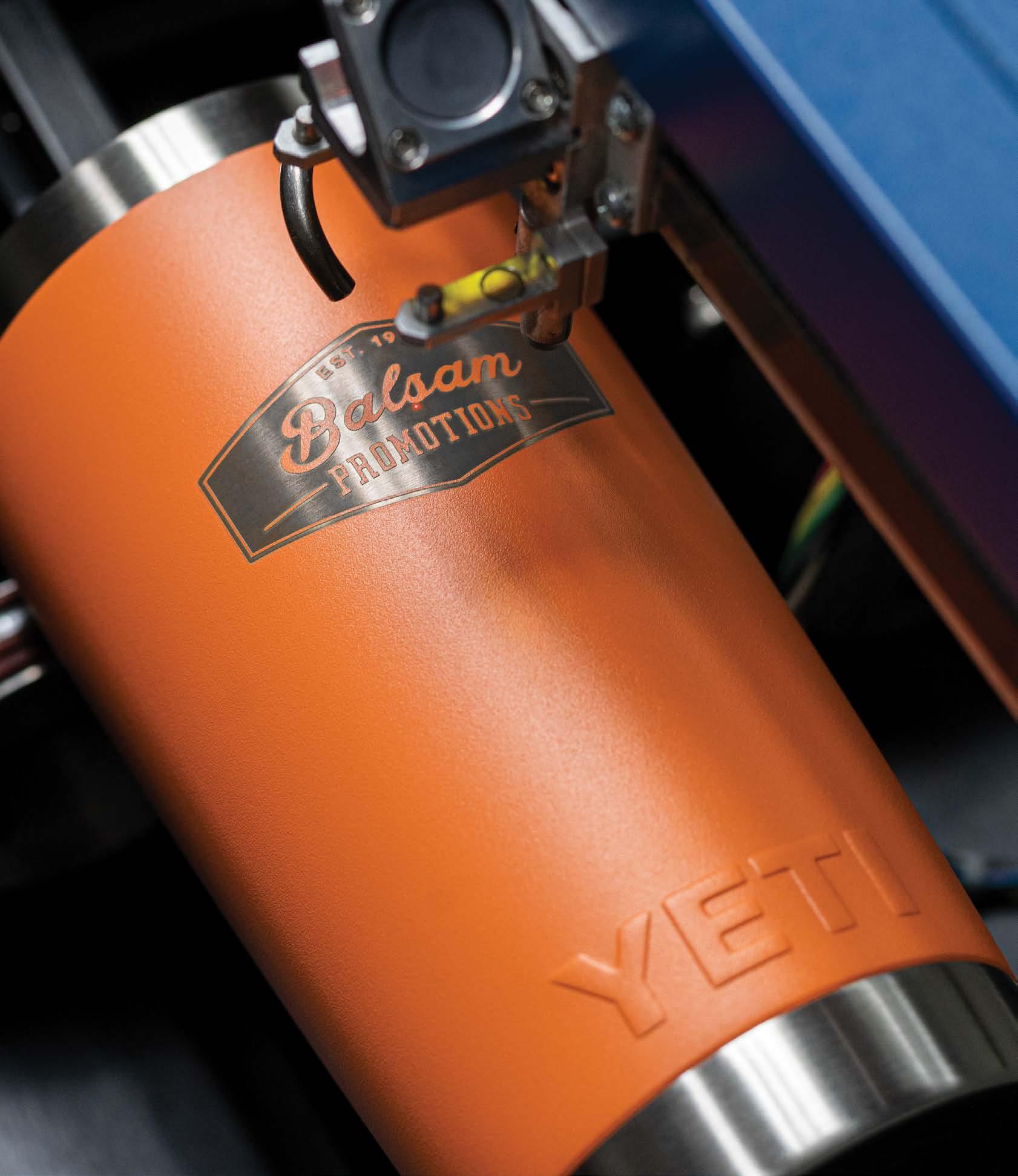
Servicing the residential building community for 40 years. Contact: Adam Zaretsky 905-761-2471
azaretszky@appliancecanada.com
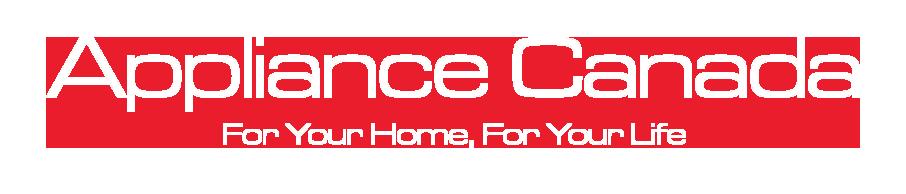
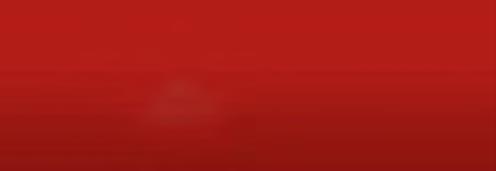
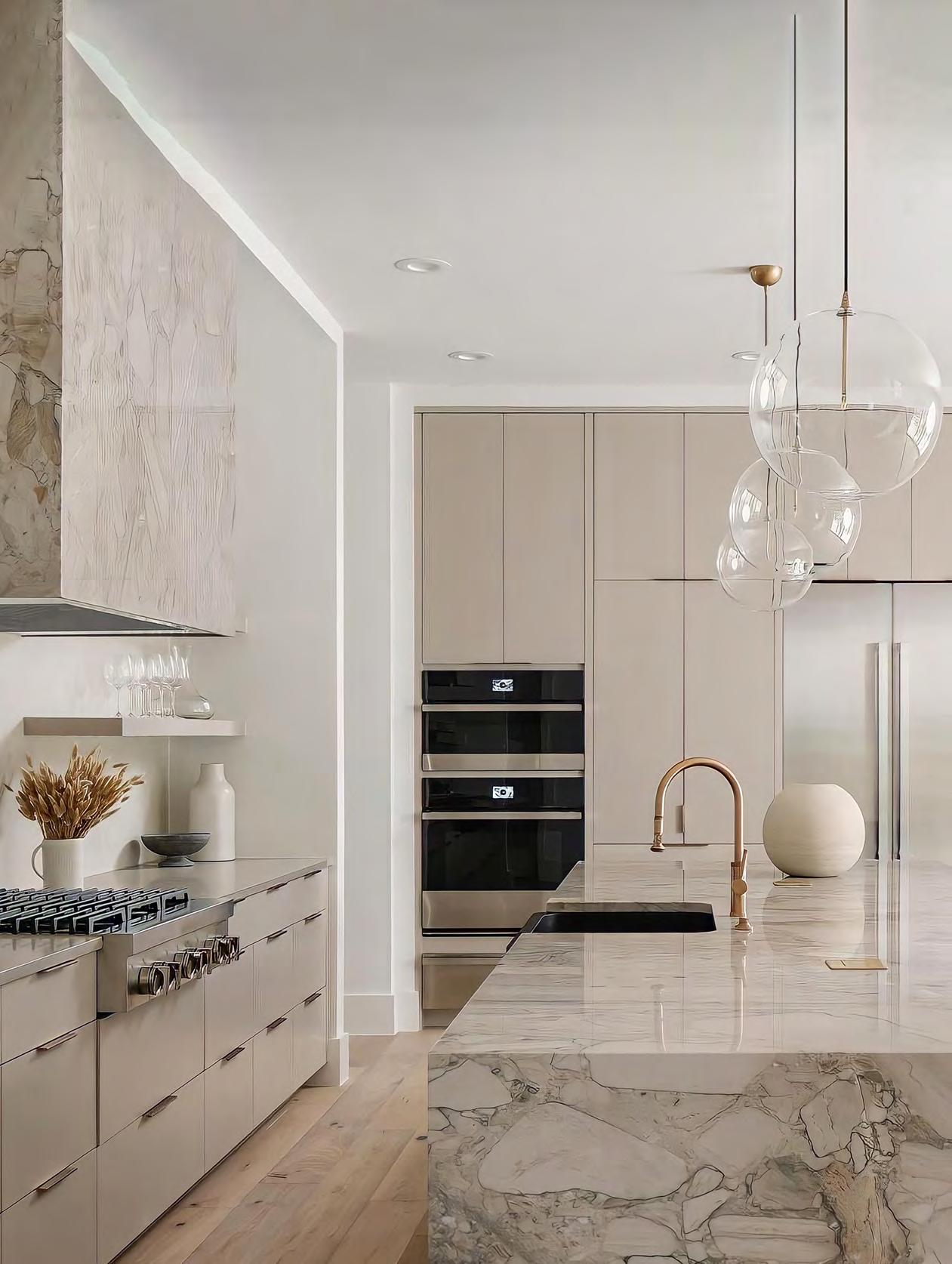
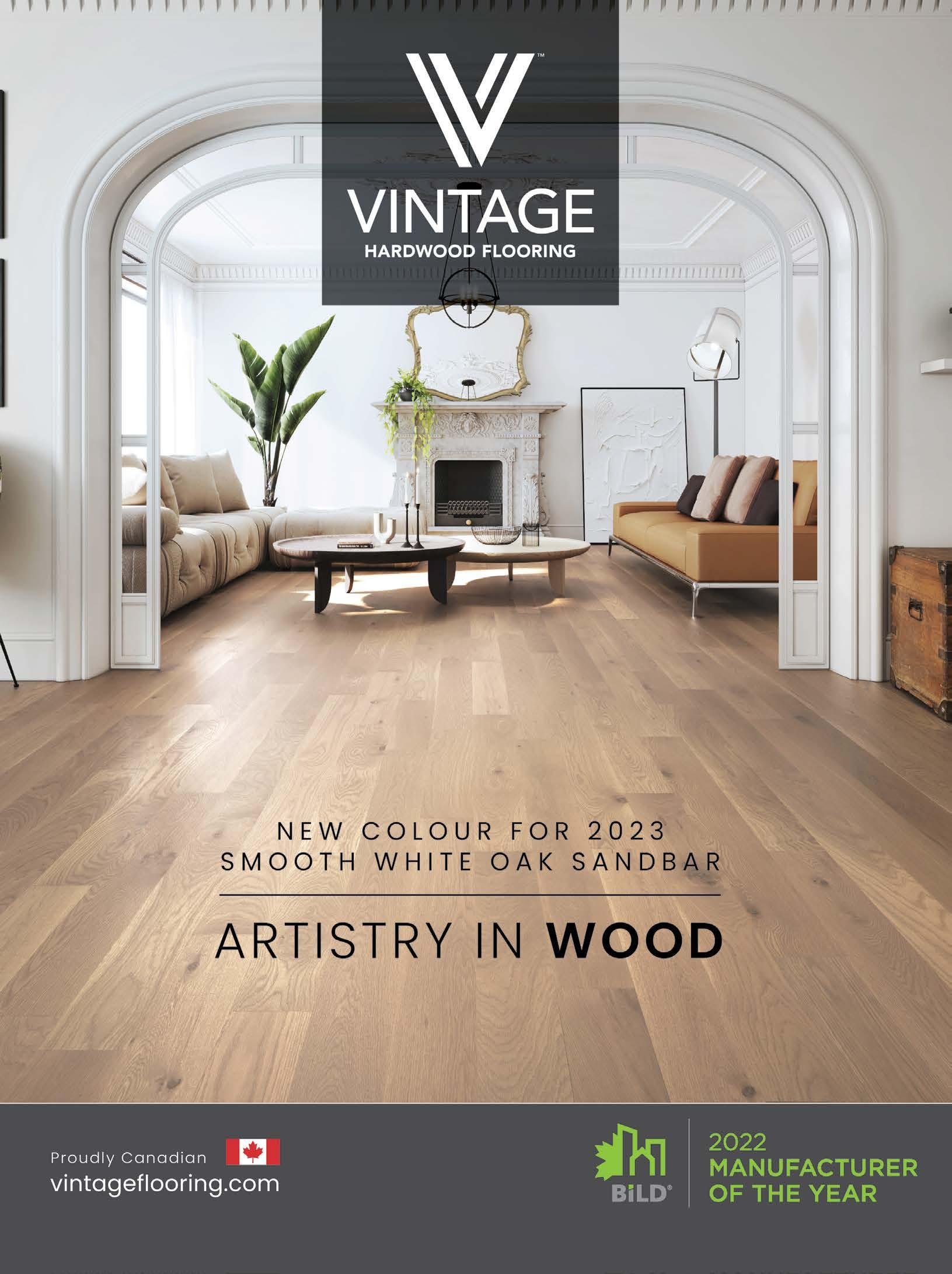
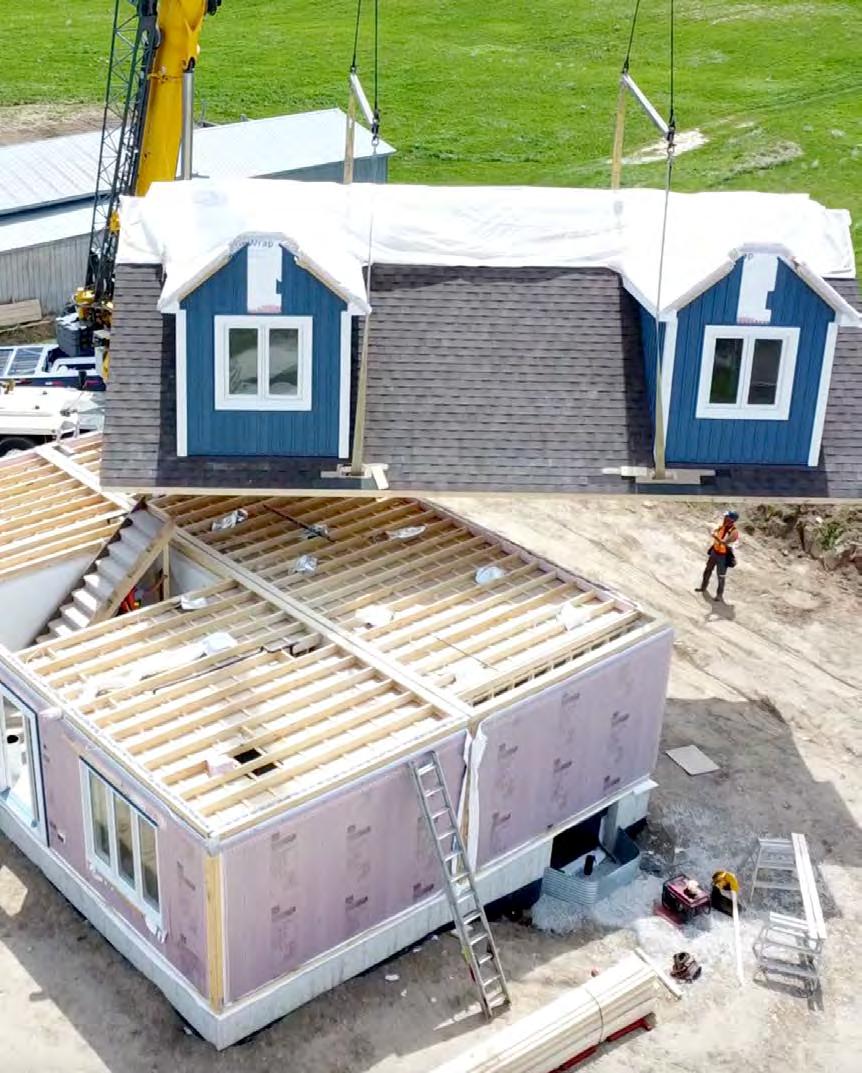
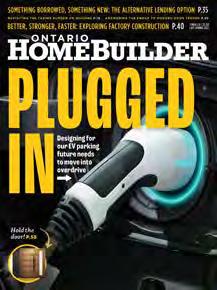
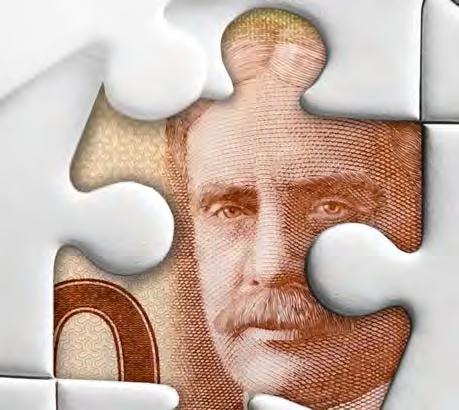
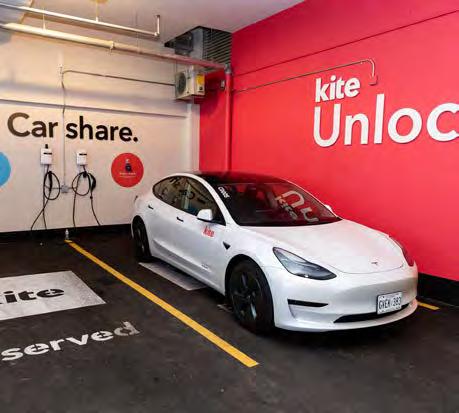
Servicing the residential building community for 40 years. Contact: Adam Zaretsky 905-761-2471
azaretszky@appliancecanada.com
The official publication of the Ontario Home Builders’ Association
Late Spring 2023| Vol.
EDITOR
Ted McIntyre ted@laureloak.ca
ART DIRECTOR Ian Sullivan Cant
COPY EDITOR
Barbara Chambers
CONTRIBUTORS
Tracy Hanes, Soumya Ghosh
ADVERTISING
Cindy Kaye, ext. 232 cindy@laureloak.ca
DIRECTOR NEW BUSINESS
Paul McNair paul@laureloak.ca
PUBLISHER
Sheryl Humphreys, ext. 245 sheryl@laureloak.ca
PRESIDENT Wayne Narciso
PUBLISHED BY Laurel Oak Publishing laureloak.ca ohba.ca Take
Ontario Home Builder is published six times per year (Winter, Early Spring, Late Spring, Summer, Fall, Awards).
All rights reserved. No part of this magazine may be reproduced without the written consent of the publisher. © 2023
For address corrections please email info@laureloak.ca or phone: (905) 333-9432.
Single copy price is $6.00
Subscription Rates: Canada $14.95 + HST per year, USA $29.95 USD Order online at https://www.laureloak.ca/subscribe.
The model on which the Ontario Home Builders’ Association is constituted, funded and governed needs to change to adapt to our new political environment. The way we conduct advocacy, while improving over the past year, needs a refresh.
We want to be the powerful, authoritative voice for housing and the first choice on housing policy matters for decision-makers and policymakers. Right now, though, we are simply one of many stakeholders in a crowded space.
Under previous governments our approach has been defensive. We measured success by being included in meetings, rather than by influencing outcomes. We focused on what didn’t happen, rather than what could have happened. We accepted policies that constrained land supply, drove up costs and created a narrative that labelled our members as “greedy, rich developers.” And we watched as members were publicly shamed by the very people who created the problem in the first place.
This approach left a void that begged the question: “Who will advocate for our industry?” More important, this void remained at a time when the government was transitioning to one
that actually sympathized with our industry’s challenges.
I was hired as CEO of OHBA to reposition the association as a fierce advocate, and to be primary voice of the home building industry in Ontario. Together we have made positive strides since, including: helping the government create and implement Bill 3, Bill 23, Bill 39 and Bill 97; employing a province-wide advocacy campaign that was pulled together in five days; achieving changes in the interest rate treatment for deposits under the Condominium Act ; and helping expand urban boundaries in Hamilton, Ottawa, Waterloo and other regions in the face of incredible opposition. We achieved comprehensive changes to development charge regimes, ended site plan requirements for sites of 10 units or less, froze parkland rates on the date that zoning bylaw or site plan application is filed and eliminated frivolous public meetings on subdivision draft plans.
Further, we worked with the government to allow for three residential units “as of right” on most land zoned for residential development without a municipal bylaw amendment. We
worked with Tarion to establish the Industry Relations Team. A resource dedicated to provide one-on-one guidance, support and education on Tarion’s builder processes and obligations. We secured major additional funding for our Job Ready Program, which focuses on bringing young people into the skilled trades. And recently, through Bill 97, we landed groundbreaking changes into the provincial policy statement and eliminated the Growth Plan.
We achieved all of this, among other things, by working in a different, more efficient and collaborative way with our locals. But the changes necessary to achieve this progress have been difficult, dividing those clamoring for change with those who are content with the status quo.
So, on the eve of my first anniversary as CEO of OHBA, I am signalling to the membership that the debate on housing supply and affordability is entering its next phase, a phase that may prove to be even more difficult than it has been thus far. We are three years away from the next provincial election. While it is our hope—and highly likely—that the current policy direction continues, there may come a time when that will not be the case.
We have taken only small steps toward creating the association our industry needs and deserves. We must build a modern, professional, effective association, focused on servicing one member with one voice. We need to build an association that can deliver meaningful change, but that can also effectively defend the industry against the changes in political direction—and do so with all levels of government.
We need to be an association that uses members’ and staff resources effectively, removing duplication at the local level. We need an association model that uses the best of our people, knowledge, resources and influence. We need to build an association that celebrates where appropriate but prioritizes delivering tangible results for members.
This is the type of association the current situation demands and that our members want. I look forward to leading this association as we work towards delivering it and building a new OHBA. OHB
OHBA needs to change if it wants to be the authoritative voice for Ontario housingOHBA CEO Luca Bucci didn’t mince words at the Industry Leaders’ Dinner.
For more information on the OHBA Job Ready program visit OHBAJobReady.ca
On Monday, April 24, OHBA welcomed leaders from across the province for a day of association collaboration and an evening of industry celebrations.
The day began with association business at the Board of Directors meeting, bringing together representation from across the provincial HBA network, including OHBA board members, chapter presidents and executive officers.
In the afternoon, this leadership team took part in two engaging sessions. The first, “Developing Your GR Capacity,” led by OHBA Manager of Government Relations, Alex Piccini. This panel featured OHBA CEO Luca Bucci, along with the CEOs from OHBA’s four largest chapters: BILD, Greater Ottawa, London and West End. This discussion provided insights into the advocacy process, including lobbying requirements and how policy is developed and implemented at the municipal and provincial levels, and also provided regional case studies to demonstrate effective advocacy.
The afternoon continued with “Building Better Associations,” a session on board governance. This training provided valuable insights and tools to strengthen OHBA’s governance practices and to position local chapters and the provincial association
for sustained growth.
After a full day of programming, leaders from across the residential construction sector gathered at the OHBA Industry Leaders’ Dinner. The program began with a keynote address from the Honourable Monte McNaughton, Minister of Labour, Immigration, Training and Skills Development. During his remarks, Minister McNaughton announced a monumental reinvestment into the OHBA Job Ready Program. Through the Ontario Skills Development Fund, this funding will provide indemand residential construction training to a new cohort of unemployed and underemployed job seekers to shrink the skilled trades gap in the province.
OHBA was honoured to welcome representation from all three levels of government, with attendees from the Government of Ontario including the Hon. Caroline Mulroney, Minister of Transportation; the Hon. David Piccini, Minister of the Environment, Conservation and Parks; the Hon. Kaleed Rasheed, Minister of Public and Business Service Delivery; Matt Rae, Parliamentary Assistant to the Minister of Municipal Affairs and Housing; and Deepak Anand, Parliamentary Assistant to the Minister of Labour, Immigration,
Training and Skills Development. Municipal representation included Mississauga Mayor Bonnie Crombie and Subdury Mayor Paul Lefebvre. OHBA also received virtual greetings from the Hon. Ahmed Hussen, Canada’s Minister of Housing and Diversity and Inclusion. This significant representation of elected officials demonstrates OHBA’s reach and relationships with government at all levels and the impact of our industry on communities big and small.
OHBA CEO Luca Bucci addressed the roomful of leaders, discussing the future moving forward for the association, one focused on the needs of the membership and to advancing the goals of the industry.
The program concluded with association honours and the presentation of the inaugural OHBA Leader of the Year award, established by President Louie Zagordo to recognize individuals who have demonstrated exceptional leadership skills and made significant contributions to the association through participation on the OHBA Board of Directors. The 2023 OHBA Leader of the Year award was presented to Southwest Region Co-Chairs Heather Galloway of Perth-Huron HBA and Jon Rumble of Chatham-Kent HBA. OHB
ALIGN Composite Cladding has it all: the high-end look of real wood your customers want –and the lower total installed cost you need.
REMARKABLY REALISTIC CEDAR MILL TEXTURE
You’ll have to touch it to tell the difference.
TRADE-FRIENDLY
Strong, lightweight construction is easier and quicker to install than fiber cement; no skilled labor, special tools or respirators needed.
(GP)2 TECHNOLOGY®
Ensures lower expansion and greater structural integrity.
FASTER TURNAROUND TIME, LESS LABOR
No sealing, touching up, joint flashing or caulking.
us a part of your home.
1001 Corporate Drive Burlington, ON L7L 5V5 gentek.ca MakeIn March, Ontario Minister of Finance Peter Bethlenfalvy delivered the 2023 Provincial Budget. Entitled Building a Strong Ontario, this provincial budget signalled that the government is focused on investing in the future of our province’s workforce, while finding new ways to increase housing attainability. As part of Budget 2023, the provincial government invested an additional $75 million in the Skills Development Fund (SDF), which will make it easier for our province to build the skilled workforce of tomorrow. OHBA’s highly successful Job Ready program, which helps introduce young people to rewarding careers in the skilled trades, has been supported by the SDF in the past and we will continue to push for this support in the future. Furthermore, an investment of over $20 billion dollars towards vital highway, transportation and infrastructure projects such as Highway 413 and the Bradford Bypass will also create new links throughout our province, help connect people and underpin more housing options. Finally, we are pleased to hear the provincial government is continuing conversations with the federal government on exempting the GST/HST on new housing and rentals.
In the months leading up to the budget, OHBA actively participated in the pre-budget consultation process from late 2022 into 2023 and provided a comprehensive submission to government on key industry priorities that will enable our sector to build the housing choice and supply that Ontarians are counting on. This budget builds upon the provincial government’s latest Housing Supply Action Plan (the More Homes Built Faster Act) and advances important priorities called for by industry to support new-home buyers.
Whether it is the millennial first-time home buyer, working adult, young family or retiree, Ontarians need more attainable housing. Without the right mix of homeownership, including rental options, Ontario risks economic damage, as opportunities, investments and businesses will leave in search of jurisdictions that provide greater housing choice and supply. Significantly increasing housing supply and variety is critical to ensuring Ontario can remain the economic engine of Canada. We will continue to champion investments and initiatives that increase housing supply and choice so that more Ontarians can find a place where they can live, work and raise a family. OHB
It has been just over seven months since Louie Zagordo assumed the role of OHBA president. During the first leg of his presidency, Louie has been zig-zagging his way across the province, speaking with Chapter HBAs about the power of membership in the association. From research and reporting to education and events, HBA membership offers resources and benefits to grow members’ skills, knowledge and business.
One such benefit is the critical advocacy work being done on behalf of the membership. During his time as president, Louie’s advocacy focus has been on the challenge posed by illegal building and renovations in Ontario. While regulations are in place to ensure that homes are constructed safely and with respect to the environment, not everyone complies with these guidelines.
Illegally built homes may not meet building code and efficiency standards or perform as advertised, potentially leaving the homebuyer in a difficult position without any warranty. In fact, it is estimated that each year, millions of dollars in claims are paid out in warranty backstop, resulting from defects with illegally built homes. Put simply, illegal building in Ontario poses a significant risk to the collective reputation of the new-home construction and renovation industry. It erodes public confidence and puts potential homebuyers and owners at risk.
As Louie heads into the second half of his presidency, he is dedicated to raising awareness about the dangers of illegal buildings and renovations in Ontario. He will continue to engage with Chapter HBAs, gathering direct feedback from members to develop and articulate potential solutions. OHB
7 best better
WAYS THE SELLING CONDENSING TANKLESS* JUST GOT EVEN
NAVIEN NPE-2 TANKLESS WATER HEATERS
1 2
EZNavTM multi-line control with built-in intuitive software
Easy whole home recirculation with optional NaviCircTM recirc valve
4 5 6 7 3
High efficiency up to 0.96 UEF allows for BIG savings when designing via performance path
To learn more visit Navieninc.com
Exclusive ComfortFlow®
NPE-A2 internal buffer tank and recirc pump
CSA P.9-11 rated with multiple air handler options
Dual stainless steel heat exchangers and 2” PVC venting up to 75
NPE-2 tankless is great for most programs, such as Energy Star, Net Zero Ready and more!
Endless hot water comfort is just one of many reasons to go tankless with Navien
On Thursday, April 27, the St. Catharines-based Niagara Children’s Centre launched its Help Kids Shine campaign, one of the organization’s largest annual fundraising initiatives to support new programs and equipment and to make improvements to the facility. The campaign runs throughout the entire month of May and involves various fundraising initiatives.
Niagara HBA CEO Chuck McShane serves as Chair of the 2023 Help Kids Shine Committee, with Executive Officer Alicia Dimitrov-Lawrence serving her second year on the cabinet.
“The NHBA is proud to support such an impactful organization within our community,” says NHBA President Richard Lawrence. “Children and their families rely on these services and therapy programs, and we are honoured to lend our support in order for this life-changing work to continue throughout our region.”
Through the generosity of NHBA members, as of the end of April, over $35,000 had been raised for the Niagara Children’s Centre Help Kids Shine campaign.
The COVID pandemic financially impacted many notfor-profits across the region. In 2021, the Niagara Home
Builders’ Association and its members partnered with the Niagara Children’s Centre in order to assist them in reaching their Help Kids Shine campaign goals.
The Niagara Children’s Centre is recognized throughout the Niagara Region as the provider of rehabilitation and support services to children and youth with physical, developmental and communicative delays and disabilities. Core services include physiotherapy, occupational therapy, speech and language services, augmentative and alternative communication, family services and therapeutic recreation. The family-centred programs aim to help each child achieve his or her own unique potential so that they can participate in all activities at home, school and in the community. The centre provides therapy and supports to over 6,000 children and their families every year, and in 2023 officially launched two satellite centres in Welland and Grimsby in partnership with the local YMCA.
Anyone who may be interested in donating to the Niagara Children’s Centre or would like additional information can reach out to info@nhba.ca or Marla.Smith@niagarachildrenscentre.com . OHB
IMPROVE HOME COMFORT ALL YEAR ROUND WITH ENERGY-EFFICIENT WINDOWS
DURABLE CONSTRUCTION TO KEEP WINDOWS AND DOORS LOOKING AS GOOD AS THE DAY THEY WERE INSTALLED
JELD-WEN® windows and doors offer both performance and style, making them the perfect choice for any planned upgrades and renovations. Homeowners can choose from a broad selection of ENERGY-STAR® certified products—including the revolutionary Northern Tri-Pane Collection™—that help better regulate indoor temperatures, lower heating and cooling bills, and even qualify for provincial and federal rebates, such as the Canada Greener Homes Grant. Industry-leading efficiency is complemented by multiple style and customization options that let imaginations run wild. Choosing JELD-WEN is a win-win!
CONTROL UNWANTED SOUND TRANSMISSION
REDUCE ENERGY BILLS AND QUALIFY FOR UP TO $5,600
DREAM RENOVATIONS
START HERE:
inspiration.jeld-wen.ca/bgp
ARCHITECTURAL DESIGN
1. Production Built Home (One Storey)
2. Production Built Home (Two Storeys up to 2500 SF)
3. Production Built Home (Two –Three Storeys 2501 SF and over)
4. Attached Multi-Unit Home
5. Stacked or Back to Back Townhome
6. Custom Home (Up to 3000 SF)
7. Custom Home (3001 – 5000 SF)
8. Mid-Rise Building (4 – 10 Storeys)
9. High-Rise Building (11+ Storeys)
10. High or Mid-Rise Condo Suite (up to 800 SF)
11. High or Mid-Rise Condo Suite (801 SF and over)
12. Lobby Entrance
13. NEW Low-Rise Green Building (1-3 Storeys)
14. NEW High or Mid-Rise Green Building (4+ Storeys)
15. Home Renovation / Addition (Actual Retail Value up to $250,000)
16. Home Renovation / Addition (Actual Retail Value between $250,001 - $500,000)
17. Home
over $500,001)
IN 2010, the Harmonized Sales Tax was implemented in Ontario, raising the tax on multiple goods and services from 5% (GST) to 13%. That included new homes. Thankfully, purchasers were able to recoup some of those taxes through the New Housing Rebate, which was instituted simultaneously, offering new-home buyers 36% of the GST tax portion up to a maximum of $6,300, and 75% of the provincial sales tax total up to $24,000 ($16,080 if you didn’t pay HST on the land the property sits upon).
The $24,000 cap on the PST portion effectively meant the rebate topped out once the home’s after-tax price got to $450,000. That seemed fair enough back in January 2010, when the average price of a GTA home was $409,000. But as of last month that average GTA residence stood
at $1,108,606. That means that the Province is reaping nearly triple the income on every new-home sale than it did 13 years ago.
It’s high time we revisit the HST burden on new home sales, suggests OHBA Chief Executive Officer Luca Bucci, and to better align the New Housing Rebate with today’s market.
LUCA BUCCI: “We have to accept that HST on new home sales is something that happened in the industry and that it’s best to manage it through the rebate. But the realities of the housing market have changed, while the policies have remained consistent. There needs to be a rethink around it. It’s something that we
advocated for in our last provincial budget submission and that the government listened to. They said that they’re going to start a conversation with the federal government to look at the HST policy with respect to new homes. That was a big win for our organization and something we were very happy about.”
“I actually don’t, because it’s an embedded cost, like gas at the pump, and you lose sight of what you’re actually paying for and how much the taxes are. But I don’t think people are aware of the land transfer taxes that are embedded in the closing cost either. So I think there’s an opportunity here to bring about some consumer awareness as to how much tax they’re paying on new homes and, more important, where that money is going, considering how big a political issue that housing is right now.
“When it comes to financial issues concerning new home building, we want to work with the CHBA, be more active in federal government politics and put an advocacy strategy together with regard to a lot of the monetary issues—everything from the way banks finance new home construction projects to the way that interest rates play into decisions around mortgages, including HST with new homes.”
“I think it has to be proportional to the increase of the value of a new home since 2010. We will have to consult with our members over it, but if the market has gone up by a factor of 125%, that rebate increase should be in proportion. How we advocate for a change and what percentage makes the most sense is something we’re going to put in front of our members. We’ll have a hard time advocating for something beyond market value, though.
“Scrapping the provincial tax on new homes is not realistic. While it wasn’t through OHBA, there have been conversations with the Ontario government on taxes around new home construction and home purchases concerning the land transfer tax. The Province wasn’t going to budge on that, because the reality of the situation is that governments are revenue-restricted, so won’t willingly part with a significant source of revenue.”
WOULD TAXING RESALE HOMES BE AN OPTION TO HELP INCREASE THE HST REBATE?
“I don’t think so. Our focus is going to be on new home construction. The price of a resale home similarly impacts the market price of a new home, and embedding that tax in a resale home will have the same impact on market conditions. But we are getting to a very dangerous point where the cost of construction of a new home is becoming a little more than the market can bear, so trying to eliminate or offset some of those costs by focusing on things like HST on new homes is a step in the right direction.”
WITH AN ESTIMATED NEED OF 5.8 MILLION NEW HOMES IN CANADA BY 2030, YOU MUST SEE SUCH FEDERAL INCENTIVES FOR HOMEBUYERS AS VITAL?
“Making the price of a new home more affordable seems to be the focus of every level of government, and I think the entire association has benefitted from having a provincial government that understands a lot of the challenges we face at getting new homes into market and what that means for people who are looking to buy homes for the first time. The Ontario government has shown that it is willing to make tough decisions to address the housing issue. Their focus to date has been more process oriented with issues of land development and construction, as opposed to what provincial tools they have to address the financing and taxation of new homes. But now we’re at a point where they can look at the next frontier, which is the monetary
aspect of the new home transaction.
“The reality, though, is that a lot of those financial tools rest within the jurisdiction of the federal government. So the best the Province can do is help the federal government understand the need to change policies to reflect the interest of the new-home buyer, because a lot of these policies reflect the market conditions and incomes of 20 to 30 years ago. Things like HST on a new home and the way we allow banks to both finance new-home construction projects and to mortgage the cost of a new home need to be rethought from the perspective of a first-time homebuyer. For example, I can go down to the U.S. and get a mortgage locked in at a specific interest rate for 30 years, which will allow me to have a significant amount of certainty in my cost of financing a new home on a month-to-month basis. Here, even if a mortgage is amortized over 30 years, that interest rate certainty only lasts maybe five years at the most.
“What we’re seeing now is the impact of that policy on a whole segment of first-time homebuyers, who are renewing a mortgage rate that is four to five times higher, and what they calculated as an affordable home payment four or five years ago is no longer affordable, and it’s going to severely affect their lives.”
“It’s unclear. Now that we have gone through Bill 97 (the Helping Homebuyers, Protecting Tenants Act), we anticipate that there will be another piece of legislation in September. Even though the provincial government has limited legislative tools to deal with the financial situation, there is always a narrative component to a piece of legislation that we can help influence. I think that’s a natural progression for our advocacy efforts. With the help of our partners at the CHBA and some of our more active locals in Ontario, we can put forth a pretty compelling narrative to the federal government so that we can start seeing changes perhaps as early as the next federal government budget.” OHB
P.24
German-engineered nobilia, the world’s largest manufacturer of European kitchen furniture, has added to its nature-inspired palette with its Easytouch 964 model in mineral green. This nature-inspired new soft green is ideal for combining minimalism with a natural look. The Easytouch system integrates a host of intelligent features for more efficiency, comfort and options— including clean no-handle looks. The innovative surface coating of Easytouch’s velvety matte kitchen fronts, meanwhile, says goodbye to annoying finger smudges. NOBILIA.DE/EN
Looking for a way to say thanks to your clients? Balsam Promotions offers a hot closing gift with the Ember Mug. Custom laser-engraved with your logo, it allows you to set a precise drinking temperature directly on the mug or by using the Ember app—so that your coffee is never too hot or too cold. A built-in auto-sleep function senses when to turn the mug on and off.
BALSAMPROMOTIONS.COM
Uponor’s Smatrix Pulse solution offers the precise wireless comfort control of radiant heating and cooling, along with forced-air heating and cooling, in multiple zones throughout a structure. The system provides faster, easier installations for professionals with the app’s Installation Wizard, which requires no internet, while wireless thermostats eliminate the time, cost and hassles of running wires. Smatrix connects to a smarthome assistant and can also be controlled remotely via an app. UPONOR.COM/SMATRIXPULSECONTROL
Bigfoot’s newest plastic tube, the BFT12, delivers a simple, yet dependable way to build footings, including for underwater dock piers. With groundwater, wet soil or moisture posing no threat, the BFT12 meets or exceeds all local and national building codes when used with a Bigfoot Systems footing form. Measuring 12” wide and 4’-tall, it can be used with either the BF28 or BF36 models, and can be installed and backfilled, then filled with concrete at a later date. BIGFOOTSYSTEMS.COM
Thor Kitchen’s 36-Inch Professional
French Door Refrigerator with Freezer Drawers (TRF3602) features a counterdepth design to maximize kitchen space. Its generous 22 cubic feet of space includes humidity-controlled crisper drawers, six one-gallon door bins for large containers like milk and juice, as well as adjustable shelves designed to provide a variety of configurations. Its SuperFreezing and Cooling function accelerates a temperature drop to the coldest setting within just 24 hours. THORKITCHEN.COM
A first-of-its-kind product, Hilti’s new Kwik-X Dual Action anchor system cuts installation time by up to 70%, while saving up to 20% in installation cost of high-performance anchoring of steel to concrete. Comprised of the convenient Kwik-X pre-portioned adhesive capsule and Kwik HUS-EZ screw anchor, the system provides the performance for safetycritical applications, while reducing the number of steps, such as hole cleaning, curing time and dispensing/eliminating adhesive waste. HILTI.COM/KWIKX
Measuring 66” x 34” x 24”, BainUltra’s luxurious Libra Aurora tub features softly sloped interior walls while providing restful lounging space for two bathers. Hand-finished, the tub’s upper rim creates a halo-like effect and frames the top with an elegant accent. Choose from the luxurious soaker tub or the Thermomasseur version, with its hydro-therapy massage via 40 adjustable air jets, heated backrest and Geysair hot air system. Options include armrests, coloured lights for an elevated sensory experience, and heating zones inside the bath’s inner shell. BAINULTRA.COM
The new lüft long-term radon and indoor air quality monitor makes a great value-added for builders and renovators. Monitoring radon gas, toxic chemicals (VOCs), carbon dioxide, humidity and air pressure, the sleek lüft plugs into an indoor outlet and connects to existing wifi. Apart from providing a convenient status light to indicate current indoor air quality, it connects to a mobile app to allow homeowners to view their air quality in real time. RADONCORP.COM
Innovative and design-forward, Napoleon’s new Stylus Cara Elite electric fireplace enables voice control through Google Home and Alexa devices. Installation is simple and inexpensive, and the wall-mount design will complement any living space. The heat level, flame colour and ember bed colour are fully customizable through the newly introduced Napoleon Home mobile application. Plus, the fireplace has a display that communicates the time and date, along with the indoor and outdoor weather conditions through a wifi connection. NAPOLEON.COM
revolutionizing the Industry yet again AND THIS TIME IT IS
Individually, electric vehicles can sneak up from behind you like a ninja in the night, but their collective advance into the marketplace sounds more like a marching band. How loud is the message? According to Statistics Canada, 34,313 new zero-emission vehicles (ZEVs) were registered in the third quarter of 2022, comprising 8.7% of total new motor vehicle registrations—up 43.2% year over year. Battery electric vehicles (BEVs) made up the bulk (85.6%) of new ZEVs, while plug-in hybrid electric vehicles (PHEVs) comprised the other 14.4%. But that doesn’t tell the whole story. Year over year, BEVs were up a whopping 85.4% across the country, while PHEV sales actually dropped. In other words, when it comes to electric vehicle adoption, the trend is to go all in. Further, the 2021 CHBA/ Avid Ratings Canada Homebuyer Preferences study indicated that 36% of new-home buyers actively looked for a pre-installed EV charger. That was two years ago. It’s bordering on an expected feature today.
Much of the momentum is driven by government, with the transition to EVs being a key piece of Canada’s emission reduction plan. “The signature piece of this plan is a mandate to have every vehicle sold in Canada by 2035 be a ZEV, with benchmarks along the way to have ZEVs hit 20% of sales in 2026 and 60% by 2030,” reminds Kevin Lisso, co-founder and CEO of Toronto-based EnerSavings, which offers sustainable and tailored energy-saving solutions for clients in the commercial, institutional and multiresidential sectors. “According to an analysis by Bloomberg, once EV sales hit 5% of the total market, it starts a tsunami in the marketplace. Both Canada and the U.S. hit that 5% threshold in 2022.”
As part of preparing the landscape, the Canada Infrastructure Bank (CIB) and FLO, a leading North American EV charging network operator and smart charging solutions provider, have announced a plan to bring more than 2,000 public fast-charging ports online across Canada by 2027. A $220 million loan commitment from CIB represents the first investment under its
Charging and Hydrogen Refuelling Infrastructure initiative, which is focused on expanding the private sector’s rollout of large-scale charging infrastructure.
The installations will nearly double the number of total universal public fast-charging ports currently available in the country.
Quebec-based FLO has been in the market for 14 years. “As with any new trending industry, there are a lot of new entrants, sometimes with questionable quality and reliability. It’s great to have a charger, but it needs to be reliably operational,” stresses Julien Deschamps, FLO’s regional sales director for Eastern Canada. “We’re recognized as having the chargers with the highest uptime. The reliability component and robustness of the units is critical. Ours are designed and assembled in Canada for our changing weather, so the elements are not a concern.”
Northwinds Corp. services Ontario clients for FLO, including Application Engineers who will work with architects and engineering firms to optimize EV plans.
There are no regulations currently in the National Building Code that require multi-unit residential buildings (MURBs) to offer EV charging, but independent news platform Electric Autonomy Canada identifies some regions as being more driven than others. “B.C. is, by far, Canada’s most advanced province in terms of having mandates for EV charging access in condos, apartment buildings, strata or townhomes, with 20 cities with modified building codes to stipulate EV-readiness requirements and one city in the process of implementing them,” with some of those local bylaws dating back five years.
Ontario waded into the pool in 2017, when the Kathleen Wynne Liberal government amended the Ontario Building Code to require 20% of parking spaces in a new single-unit, semi-detached and townhouse buildings to feature EV charging, making Ontario the lone province at the time to mandate EV charging. But the policy was repealed in 2018 after the Conservative party took power.
Since then, the issue has been punted to local governments. Toronto is among the few to take charge. According to the Zoning Bylaw 569-2013, which was amended in December 2021, and Toronto Green Standard Version 4’s EV infrastructure standards, which came into effect in May 2022, “all residential parking spaces provided for dwelling units located in an apartment building, mixed-use building, multiple dwelling unit building, excluding visitor parking spaces, must include an energized outlet capable of providing Level 2 charging or higher.”
In Mississauga, an amendment to zone bylaw 0225-2007 passed last June requires EV-ready parking spaces “for the construction of new buildings or portions thereof, effective June 8, 2023.” A minimum of 20% of multi-residential residents’ parking spaces must be EV-ready; 10% for visitors lots, the amendment cites. Other cities, Hamilton and Sarnia among them, currently have staff looking into EV requirements.
Some builders are already plugged in. Amexon’s Central Park community beside Leslie subway station in North York will be the first large-scale project of its
kind in Canada to include electric vehicle charging stations in each one of its 1,500+ parking spots, the developer notes.
One of the most innovative approaches to EV parking belongs to EVE Park in London, Ontario. Equipped with smart charging systems, each of the project’s four buildings will feature a pair of EV-ready parking towers—one that can hold up to 14 sedan vehicles and the other up to 12 SUVs. The low-footprint tower designs allow for multiple electric vehicles to park in the same land space as two surface lot parking spots, increasing land efficiency by up to 700%, according to developer s2e Technologies. EVE-Car, meanwhile, is the development’s EV car share program, with four plans to choose from that offer Tesla Model 3s or the latest Model Ys for lease, be it by the hour or for a family trip.
Tridel has also entered the carsharing market. Its Bianca condo in Toronto’s Annex neighbourhood was the first MURB in Toronto to feature sustainable ride sharing, thanks to partnerships last year with Canadian cleantech companies Kite Mobility and Swtch Energy. Bianca residents can book one of two Tesla Model 3’s, a Nissan Leaf
Tridel’s innovative program shares electric vehicles as well as e-bikes with residents at its Bianca condos, but can also feed energy back to the building.
# BY
* Statistics Canada
or eight e-bikes through a mobile app. Depending upon demand, additional vehicles (and corresponding parking spots with charging stations) will be added. The payas-you-go (or monthly subscription) arrangement helps users avoid vehicle upkeep costs, while contributing to clean transportation.
Kite, whose other recent developer partners have included Collecdev, Broccolini, Madison Group, Vandyk Properties and Distrikt, estimates it can reduce 10 automobiles per building for every car share program. “In Vancouver, where electric mobility uptake is higher, developer Canderel is currently removing a whole parking level of 450 spots in a new building through a Kite partnership,” notes REMI Network.
There is an added power management component to the Bianca Condos innovation, though—a pilot project with Kite and Switch Energy that’s part of the Government of Canada’s i.d.e.a innovation fund. “We were the first—maybe even globally—to combine vehicleto-grid charging with electric vehicles and an electric vehicle car-share service,” says Graeme Armster, Director of Innovation
THE NUMBERS 35%+ Annual growth rate for electric vehicles (past five years).
and Sustainability at Tridel. “The idea is to give people affordable and green mobility solutions right at home, but then when those cars aren’t being used, to have the ability to unload that energy during down periods for other uses, like bringing down peak demand in the building. So now you’re getting multiple bang for your buck in terms of it being both a mobility solution and also a load-management solution.
“Ultimately, I think the solution is for every building to have access to multiple charging tools—Level 1, Level 2, Level 3 and V-to-G (vehicle-to-grid). And then the question should be, ‘How do we use those different charging tools, and in what quantity?”
The Ontario Energy Board is addressing the demand on electricity that growing EV numbers will entail with a new ultra-low overnight rate. At 2.4 cents per kilowatt hour from 11 p.m. to 7 a.m., it is 67% lower than the standard offpeak rate. (If customers choose that plan, though, it will be in exchange for a higher on-peak rate.)
“That special rate presents some interesting opportunities for leveraging technology on the energy management side, particularly if we can expect a steady increase in residents returning home from work in the evening and plugging in their vehicles at a similar time,” explains Armster. “You could say, ‘OK charging station, I’m plugged in, but don’t turn on and charge my car until after 11 p.m.’
“Of course, if you’ve got 400 cars in a garage and they all need power at the same time, maybe you run into a new peak in the building, and the utility may start adjusting the rate structure,” Armster notes. “From that perspective, you want to make sure from an infrastructure standpoint that you’re set up and malleable enough to address that in the future. As the industry transitions to a lower carbon economy centred around electrification, we want to ensure that the properties we’re developing will never be at risk of not
Choose your charging stations carefully, advises FLO EV Charging.
#
BY THE NUMBERS100% New vehicle sales in Canada mandated to be zeroemission by 2035.
* Transport Canada 80% Amount of electric vehicle charging done at the home.
* Forbes Magazine
having access to enough power, and will be resilient to that, where all the peaks and valleys are technologically managed on the building side—batteries or even renewables, and even feeding back to the grid. That’s where I think things will go. But the key question is, ‘Do you have the infrastructure in place so that you can manage what you have right now in terms of at least just shifting charging times so that you’re paying the lowest rates?’”
One company immersed in the power management field is Toronto-based EVdirect. Designed, developed and built in North America, with a key manufacturing facility in Mississauga, the company’s Evolute product is a smart multi-user electric vehicle charging system that addresses the unique challenges associated with deploying EV supply equipment in both new and existing MURBs, office towers and fleets.
“Currently, the main challenges facing this sector are limited capacity, remote control, billing and consumer freedom. The Evolute is the only system that addresses all four,” says EVdirect founder and Chief Visionary Officer David Ackermann. “Its advantage over the others is its agnostic charging
station compatibility and multiple billing options, providing consumers with full freedom of choice. The software includes a cloud-based dashboard for administrators and management, with tools for remote control, monitoring, billing and account management.”
EVdirect’s partnership with multinational power management giant Eaton Corporation has also helped attract developers, included Trulife Developments (8188 Yonge St. in Thornhill) and Broccolini (River & Fifth Condos in Toronto). “Eaton is the panel builder, while we designed the software,” says Ackermann, a master electrician himself.
Ackermann believes builders should “stay out of the appliance game” when it comes to installing chargers. “The charging station is a small appliance in your condo—it’s your toaster, your microwave,” he says. “It’s something that every end-user should be able to choose and upgrade when they like, and match to what their auto manufacturer suggests, if they want.
When you’re building in 2023 and occupancy is going to be 2026, why would you spec a charging station today for occupancy in three years?
Just like cell phones, they’re going to change multiple times by the
time you get to occupancy. Even the way we charge is going to change, such as wireless charging, etc. The proper way to do it is to give everybody power in their spots and manage that power in an efficient way to make sure that everybody wakes up in the morning and is charged.”
And there’s money to be made, if builders recognize it, Ackermann says. “Our system without a charging station—just the actual infrastructure, with a Level 2 receptacle—is about $1,000 a drop. That doesn’t include the pipe and wire from the system to the particular parking spot or the charging station, which could be another $2,000. But it’s $1,000 for that basic infrastructure, where they’re going to now flip it for anywhere from $5,000-$10,000 more than a traditional spot, which I’ve heard going from $40,000 to beyond $70,000.
“But I see too many builders not looking at the future to what drivers are going to want and expect. They’re trying to do the least expensive solution and not seeing the upcharge value of it. There are all these buildings that have maybe a dedicated panel for EVs, but there’s no metering, no power sharing and no way to expand the system past the initial uptake of whatever they designed it for. And that really has to change, because a retrofit condo across the street that might be 10 or 15 years old is doing proper upgrades. You’re either going to lose potential owners, or there’s going to be blowback afterward from unit owners.”
With the implementation of any new technology, there are bound to be learning curves, and there were two right off the bat for Tridel.
“First, just because you put an EV station in doesn’t mean someone is going to use it right away,” Armster cautions. “The numbers we’re seeing right now from our sales and marketing team is the demand for about 30% of the parking spots to have charging stations in each new development. After a project is
completed, though, I’ll usually go back and walk through the parking garage to inspect things. Over the past couple of years, I’ve seen tons of parking spots with charging stations but with an internal combustion engine parked in it. That tells me that someone’s future-proofing their spot and planning on making the jump to an EV eventually. But the issue there is that the utility has assumed a fixed timeline on payback for the investment they made in expanding the local electricity infrastructure to serve the new development. Payback is achieved through forecasted revenue that is generated from the electricity ratepayers for that development. When assumptions are off, which is often, the developer has to make up the revenue shortfalls that the utility receives. This will continue to be difficult for developers and utility providers to manage as more and more people look to future-proof their parking spots.”
Getting the numbers right is also important, given the expense associated with being EV-ready. EnerSavings, which has ‘futureproofed’ 250 buildings across the country, estimates that the added builder cost to installing an EV-ready versus standard parking space is approximately $2,000 per stall. This cost includes rough-in and running conduit and wiring during construction so that other equipment such as transformers, electrical panels, metering and charging stations may be added easily in the future. If you wanted to move beyond EV-ready and select a fully wired EV charger at your parking spot, Armster notes that the cost, including the associated infrastructure, would be about $10,000 to $15,000 extra per parking spot.
“The second learning curve was making sure that in the condo documents there is a clear process for expansion,” Armster says. “We’ve seen examples where people have
#
BY THE NUMBERS
71% Canadians considering an EV as their next vehicle.
* KPMG
“I see too many builders not looking at the future to what drivers are going to want and expect. They’re trying to do the least expensive solution and not seeing the upcharge value of it.”
told their condo corporation, ‘Hey, I want to add a charging station to my parking spot,’ and the condo corp. says, ‘OK, let’s price this out.’ They get an engineer, a design and price, and after adding a transformer, panel and all the associated wiring to introduce EV charging to the condo, it could be $150,000 for the resident. If economies of scale come into play, you could get one at maybe $10,000 to $15,000, but they’d have to find 9-14 other residents or so to make it all work.
“It’s also not as simple as saying a person should be able to just plug their vehicle into the outlet that’s there; there should be a process in terms of the breaker being off for that plug, and the person requesting that they want power turned on now,” Armster advises. “Developers should have a process in their condo docs that lays out the obligations of the condo corp. to support this service and for growth and expansion. But they must also identify the responsibilities of the parking spot owner, and consider that those who don’t have spots should not have to contribute maintenance fees for the upkeep of those spots.”
Armster also worries whether the amount of mining required to meet the demand for both lithium batteries and copper wiring might offset any potential gains from the move to EVs. But there are other reasons why this might environmentally motivated upgrade isn’t
THE NUMBERSso straightforward. “Will all the EV spots we’re installing get used in the future?” Armster wonders. “Will fewer people even need to own a car because autonomous vehicles have taken off and the infrastructure around transportation has changed in Toronto? Will they figure out hydrogen cars in the next five years? Everyone has the same goal right now. We want to address climate change and reduce carbon emissions, and we have to act quickly. But I think sometimes we have to just take a second longer to think about what we’re doing to make sure that we’re not over-vectoring, and in trying to solve one problem creating another.”
Insurance companies will also be watching closely, since EV batteries produce an entirely different type of fire, burning longer and hotter and requiring a different fire extinguishing approach. Automotive news site MotorBiscuit reported on a Germany parking garage that banned EV and hybrid vehicles altogether, since the underground car park ceilings were not high enough to allow for heavy equipment to pull out burning cars. “Since lithium-ion fires are a chemical reaction, they can only be cooled not extinguished,” it noted. “They end up burning for several days in some cases. In that
case, damage to the parking structure would be extensive.”
“Ontario has prescriptively prohibited the installation of lead-acid or lithium-ion batteries for energy storage solutions below grade or above 23 metres in a building. Interestingly, this hasn’t been fully addressed with regard to electric vehicles, as that would technically be a battery that would be parked below grade,” Armster says. “But our industry may see changes in the near future as building codes catch up. It could be driven by insurance companies. It could be driven by safety authorities. But the City is not quite there just yet.”
We also might not be quite there with respect to federal and provincial funding for EV’s evolution. “Many incentives are currently going to people who were going to buy EVs anyway,” says Steve Boccadoro, president of Eaton Canada. “In terms of funding, investment and incentives, we have to make sure we’re directing it to the overall hurdle of EV charging infrastructure. The government needs to incentivize the private sector to draw them in.”
Ackermann agrees. “The rebate system and the NRCan grants just don’t talk about infrastructure. If builders could get some infrastructure rebates or some other incentives instead of these programs focusing on charging stations, that would be a huge boost.” OHB
The Daikin Fit hybrid (gas/electric) heat pump system is a side discharge, smart HVAC system that won’t compromise on comfort and connects to traditional ductwork.
The lightweight, low profile, and quiet outdoor unit o ers solutions when a traditional cube style cannot. In addition, the Daikin Fit unit includes an inverter (variable-speed) swing compressor that supports ideal indoor comfort and e ciency.
* Complete warranty details available from your local dealer/contractor or at www.daikincomfort.com. To receive the 12-Year Unit Replacement Limited Warranty and 12-Year Parts Limited Warranty, online registration must be completed within 60 days of installation. Additional requirements for annual maintenance are required for the Unit Replacement Limited Warranty. Online registration and some of the additional requirements are not required in California or Québec. The duration of warranty coverages in Texas di ers in some cases.
For more info visit daikinfit.com
s the real estate market has cooled dramatically and interest rates increased, not only homebuyers are finding it more difficult to arrange financing. Already plagued by the increased cost of materials and labour, developers and builders are also finding the traditional lending environment challenging when it comes to securing financing for land and construction.
Brian Dorr, founder of Dorr Capital Corporation, a commercial real estate mortgage lender and broker that focuses on the Greater Toronto Area and Greater Golden Horseshoe, says until recently there was a lot of capital chasing a lot of builders, but the reverse is now true. “Lenders don’t feel that compelled to lend to builders. They are very risk-averse,” says Dorr, noting that traditional lenders are not opening their relationships beyond the developers they have a history with.
Consequently, the current lending climate has many developers and builders looking at other options. That’s why alternative lenders, who have played a role in the development and building industry for decades, are seeing a rush of new business.
“The tightening of traditional financing parameters has pushed some developers/builders into the alternative lending space for the first time, as they may require more flexibility in their deal structures,” says Michael Carragher, V.P., Mortgage Investments, at Firm Capital Corporation, a nonbank lender that has been providing real estate funding to small, medium and large builders and developers in Ontario for more than 35 years.
Land financing is particularly challenging. “In today’s market, it’s very difficult to get money. A lot of lenders who were doing land have put a pause on that financing,” says Rena Malkah, president of CYR Funding Inc. Her firm represents institutional lenders such as pension funds, insurance companies, banks, credit unions and more than 2,000 private lenders that supply capital for land purchase, construction financing and income-producing properties.
Land money is scarce, but Malkah says it was typically financed by private lenders anyway. “Only big builders would get land money from typical lenders. Land may be agricultural property that has to be rezoned. Then when it’s rezoned, its value goes up, then again after the Official Plan amendment, and then after the site plan approval. After each stage, as the land value goes up, it becomes more desirable for a lender to finance.”
“Land financing is very tight in today’s marketplace,” concurs Riccardo Plati, executive V.P. of Dorr Capital. “Construction loans are getting tighter for less experienced builders.”
Malkah says a lot of financial institutions are more cautious
due to the rising costs of building and the drop in home sale prices.
“That reduces the profitability of a project. In some cases, deals aren’t making sense anymore.” If a builder is plausible and the borrower has a strong record, Malkah says they may still be able to go to a lending institution. “However, if the borrower doesn’t have a strong net worth, lenders are concerned about cost overruns and that the borrower doesn’t have deep enough pockets.” In that case, it would have to be a private deal— including for first projects, even if a builder has experience.
Alternative lenders are expe riencing a bump in business not just because clients are finding it harder to source funding the traditional way, but because they have the ability to structure loans to meet each client’s unique needs, explains Carragher. “Unlike traditional lenders, we do not need to fit a transaction into a specific lending box or set of parameters.” For example, due to the current slower pace of sales, a builder may need a more flexible pre-sale structure.
Carragher says there is also comfort for clients using alternative lenders such as Firm Capital Corp., as they know they can call and speak directly to the decision makers throughout every step of the financing process. Even established builders with good relationships with traditional lenders often opt to use private lenders, says Malkah. Time is money and the quicker they can get a project started, the better. Construction funds are advanced in draws, based on an inspection and report by a cost consultant to a lender. And while a bank may take a couple of weeks to provide an advance, it can take only three or four days with a private lender.
Interest rates at the time of publication ranged from 9-12% on land financing and 8.5-10% on construction financing, plus fees, says Malkah. While banks may offer slightly lower rates by a
$ Low-rise housing will continue to be in demand, especially for units priced less than $1 million.
$ High-rise condo units by transit lines will continue to sell well.
$ Some builders and developers are looking at projects smaller in scope than they normally would, as this allows for shorter project timelines, the ability to better match project revenues and costs, and a clearer exit strategy.
$ There is still demand in some smaller communities beyond the Greenbelt, but it makes it even tougher to secure financing.
$ Big banks are not willing to deal with medium-sized developers at this time (according to information gleaned from the RealCapital conference in February).
$ Listen to lenders and be very patient.
$ Have a strategy mapped out to discuss with lenders, including market analysis and risk assessment. For example, can you secure zoning and permits, and do you have a financing plan in place if costs change or there are delivery delays?
$ Have budgets locked down.
$ Make sure presales are solid.
$ Be prepared to add more equity.
$ For land purchases, see if the land seller will hold a vendor take-back mortgage until construction is ready to start, at terms favourable for the buyer and seller.
percentage point or two, as well as slightly lower fees, there is more red tape and most banks have paused on taking on new builder/ developer clients.
Alternative lenders play a big role in projects of all types across the province. Firm Capital has provided construction financing to Ontario builders and developers for 35 years for infill, low-rise, mid-rise and high-rise condominium projects, site servicing, land financing, inventory financing and mezzanine/equity capital. Loan amounts range from $1 million to $50 million.
Firm Capital treats every real estate project, whether small or large, as unique. To understand the needs of the project, Firm holds a face-to-face meeting or call with the builder or developer. When considering an application, Carragher says his company wants to see that the scale of the project fits with the builder’s (or developer’s) track record, skill set and experience. Firm’s business is lending and it does not get involved in managing projects, but does keep tabs on their progress. Following a meeting with a borrower, it will present a financing structure within 24 to 48 hours to a client. If that’s accepted, they’ll move ahead with a financing commitment and funding date required by the borrower.
“We have the ability to react quickly, given our collective industry experience and the fact we are a direct lender with proprietary capital,” says Carragher.
Dorr Capital operates in the private debt market and has placed $2.2 billion in loans with private and institutional investors over the past decade. Dorr Capital’s business has grown significantly since it was launched 13 years ago, with the average loan size nearly
$19 million in 2021, with some deals close to $200 million.
Dorr, who is also president/ CEO of RealAlt Investments, started his career as a default analyst at CMHC and saw deals go bad because customers didn’t have great exit strategies. The credit crisis of 2008/2009 created a huge gap in the market for development and land financing. He subsequently started Dorr Capital as a broker, tacked on loan administration, then six years ago started syndicated mortgages from private individuals. Two years ago, RealAlt was created, a mortgage fund that spreads out risk by investing in multiple loans in land, and new multi-family home developments.
Dorr Capital works with developers that are typically building 10 to 500 units annually, providing financial advice and assistance through every stage of a project. It has recently provided a loan ($30,720,000) for construction of 36 townhomes in Richmond Hill. Dorr’s underwriting process is stringent, as it wants to be assured that developers can get the necessary approvals. It does thorough market research on aspects such as location and demographics, using its own internal resources as well as thirdparty consultants. This involves budget review, in addition to timing, cost escalation and risk assessment to determine whether a developer or builder has the necessary experience to carry out a project and handle the scale.
As most lenders will not lend 100% of the cost of a project, developers or builders have to come up with either their own capital in equity or seek a source of equity funding. That’s where companies such as Harbour Equity Capital Corp come in.
It is a private equity company that raises pools of capital, then invests in and owns a portion of the projects, generally on a joint venture basis with developers.
“We invest with the developer at the time of land acquisition, as well as later stages, but we generally provide capital from day one,” says Harbour President and Principal Ari Silverberg. Harbour Equity provides development partners with the time and resources required to facilitate the completion of the project and helps ensure that the joint venture maximizes project profit. The company acts as an advisory partner to help mitigate any issues and facilitates the progress of development, while the developer provides the day-to-day management of the project.
Harbour deals with everything from land development to condo developments, but mainly focuses on low- to mid-rise infill projects that include single-family homes, townhomes and stacked townhouses, as well as urban and suburban condo and rental buildings. With rental projects, Silverberg says the goal is to get in and out—to sell and not hold those buildings long-term.
The majority of Harbour Equity’s projects are in Ontario, typically valued at $40 million to $120 million. “Our focus is Southwest Ontario (London, Kitchener-Waterloo, Cambridge, Hamilton, Guelph, etc.), although we have projects as far east as Clarington and north to Barrie,” says Silverberg.
Harbour bases its investments on the quality of developer, their experience and the value they see in the land. “We look at a developer’s reputation for sure, we look at past experience,” Silverberg notes. “We generally make decisions reasonably quickly and are pretty transparent.”
Partnering on equity financing with Harbour allows developers to leverage their equity and do more deals than they would otherwise with their own capital, says Silverberg. They pay market management fees, but Harbour adds value in terms of financing and strategy. Some developers are facing situations where units were sold some time ago and costs have gone up, so Harbour works through those situations with its partners to find solutions, expedite
projects and attain profitability.
Currently, Harbour has $60 million in equity capital that it intends to deploy over the course of the next year. It has invested in more than 65 projects since 2011, which on completion will comprise more than $2.5 billion in real estate assets, including for-sale residential, purpose-built rental and industrial developments.
“Banks appreciate that we’re not registered on title in second position on these projects, that our interest in the property is through our joint venture and having title to the property,” says Silverberg. Thus, builders that Harbour deals with are able to borrow from ‘A’ lenders such as banks and credit unions. “Lenders also appreciate that we are required to help with cost overruns through our joint venture agreements, providing them comfort that our projects will be completed and they will be repaid.”
Harbour has invested $140 million for its investors over the past two years, and Silverberg believes the push from the Ontario legislature to reduce red
tape and approvals challenges at the municipal level will continue to make the real estate market an attractive place to invest.
Some examples of recent projects include committing $20.80 million for a 50% interest in the community of Courtice, with 500 low- and mediumrise residential units to be developed on a 58.8 acre site. Harbour Equity, as fund manager, committed $10.97 million for a 26.4% interest in the project, while coinvestors committed to $9.83 million for a 23.6% interest. It also provided $7.80 million for a 50% interest in a 1.1 acre site to be developed into a 30-storey, 250,000 sq. ft. mixed-use condo tower in Toronto.
But while alternative lenders offer builder and developer clients many advantages over traditional banking, there can be a few disadvantages. “There is a flight to quality and part of that flight is to get large, large loans,” says Dorr. “I suppose the Achilles heel of alternative lenders is loans of $50 million or more. That’s still the domain of banks.” OHB
“Land financing is very tight in today’s marketplace.
Construction loans are getting tighter for less experienced builders.”
Off-site construction and lowering modules into place via crane allows for minimal neighbourhood and site disruption
Factory construction can offer a way past some of builders’ biggest impediments
BY TED M c INTYRE (Photo: Triple M Housing)f you like surprises, this probably isn’t for you. Consistency, after all, is a hallmark of modular construction, whereby a building is constructed off-site, under controlled factory conditions, using the same materials and designing at least to the same codes and standards as conventionally built facilities.
It’s topical at the moment, but hardly a novel concept. Online publishing platform Medium.com notes that the first documented prefabricated home was created in the 1830s “by London carpenter John Manning for his son, who was moving from England to Australia. Manning built a prefabricated house in pieces, then shipped it to the Land Down Under for easy assembly.”
An ad in the May 1, 1922 edition of MacLean’s magazine, meanwhile, promotes a ready-built summer cottage from Brantford’s Schultz Brothers measuring 16’ x 32’, with five rooms and a verandah—all for $699.95, including hardware, windows and doors.
A century later, the merits of manufacturing in a controlled, efficient, predictable and virtually error-free environment has been the theme of Working with Modular, an ongoing six-part webinar series hosted by the Canadian Home Builders’ Association over the past year. The content is designed to inform builders and developers, code officials, government departments, lenders, warranty providers, municipal planners and housing specialists, as well as other stakeholders engaged in the residential construction industry.
As of 2019, the modular sector included 216 factories certified to Canadian standards, 181 of which were located in Canada. They serve the range of residential occupancy from garden suites and singlefamily homes to multi-storey projects, employing 30,000 full-time workers, with $6 billion in economic activity.
“Factory-built construction is catching on as builders look for solutions to address the skilled labour shortage, improve productivity and to maximize much-needed housing supply to provide more homes to people at a price they can afford,” says webinar series co-host Frank
Lohmann, CHBA’s Director of Building Science and a 23-year veteran of the National Building Council before joining CHBA in 2020. “CHBA is seeing a growing interest in the high level of environmental performance and full range of singleand multi-family design options achieved with modular construction. That’s most recently evidenced by the very high participation in our webinar series.”
That included more than 300 registrants from throughout the industry for the December webinar alone, which addressed the factory-built process. Those tuning in identified an even distribution of interests, ranging from sustainable construction to cost savings and scheduling.
Alberta’s Triple M Housing was front and centre in the December webinar. Its sprawling Lethbridge site spans 31 acres, the main factory of which measures 192,1000 square feet, along with a separate 12,000 sq. ft. saw shop and a welding facility. The company employs more than 400, including staff for customer support and warrantees, with both day and night shifts.
Inside the factory are 21 workstations and 12 drywall stations, churning out floor sizes up to 30’ x 76’, with each home requiring 10-21 days to complete.
Triple M’s step-by-step factory tour and assembly line-like automation served as a reminder of the amount of work that can be done before the finished product is shipped to site, including mechanical installations, such as prewiring and electrical panels, plumbing lines and vents, and even appliances, cabinetry and surfaces. And it all comes in a nicely sealed package.
“One of the tremendous advantages of factory-built construction is that it lends itself to creating an airtight building,” notes Triple M’s V.P. of Manufacturing and CHBA Modular Construction Council committee member Simarjit Bains. “Each wall, each floor, each storey is built from the inside out, which provides for easy and effective installation of insulation. There are no gaps in corners, behind electrical outlets or other hard-to-reach areas.
“Once the wall and floor panels have been put together to create volumetric models, they get finished really much the same way as on-site construction,
except that this happens in a dry, warm environment with the help of cranes, and in some cases utilizing much larger material sizes for higher efficiency and fewer cut-offs,” Bains adds. “The safety railing system above and the flat firm factory working surface makes scaffolds easy to use and safe, leading to fewer accidents. And waste removal and recycling are simple and quick.”
Finished modules and sections can travel on the road or rail, as well as by air and water (Canadian provinces also export modules overseas), before being assembled on site.
The ability to work on the site foundation and the construction of the
superstructure simultaneously accounts for most of the time savings, which are significant, as evidenced in the North Ridge CO2 Analysis Report, prepared by Dr. Mohamed Al-Hussein, PhD and Associate Professor of Construction Engineering and Management at the University of Alberta. The report, which analyzed the 42-suite, four-storey North Ridge residential building in St. Albert, Alberta, concluded that modular construction resulted in a 43% reduction in CO2 emissions and a 55% scheduling savings, with an overall construction time of 6.3 months compared to the 14.25 months of traditional on-site construction.
Alberta’s Landmark Homes, which used conventional stick-built construction from 1977-2005, before moving to automated panelized construction in 2005, provides Dr. Al-Hussein with another illuminating case study. “First off, the cycle time of panelized construction will decrease about 97 days—from 247 days to 145 days per house—with a corresponding 40% increase in production rate,” Al-Hussein says.
Factors contributing to the reduction included fewer uncertainties related to handing off to different trades, a smoother turnover from house to house and higher predictability.
The number of superintendents required to inspect those finished products was
reduced from 46 to 27, resulting in a 41% decrease in superintendent salary payment. It also led to a roughly 40% reduction of pickup truck use, which correspondingly reduced fuel consumption by 22,682 litres/year, leading to 52.46 fewer tons of annual CO2 emissions.
Then there’s the huge reduction of permits and inspection costs for things like HVAC, plumbing and gas, electrical and building codes, Dr. Al-Hussein indicated. “With stick-build construction, there’s an average of two additional inspections for each area, or eight total, for an additional cost of $2,160. With panelized construction, no additional inspections are required.”
The savings extend right down to the number of invoices and the time to process each. Another dramatic cost savings was associated with the shrinking of required office space, which dropped by 76%—from to 33,798 sq. ft. in 2005 to 7,956 sq. ft. in 2020.
Bains highlights the heightened degree of quality control that factory production provides, from every cut and measurement to the stability of materials
“First off, the cycle time of panelized construction will decrease about 97 days—from 247 days to 145 days per house—with a corresponding 40% increase in production rate.”
in a climate-controlled environment—a far cry from traditional sites exposed to the whims of Mother Nature. Each component is checked and documented at every stage, Bains notes, with a travel log accompanying the factory checklist for all homes/modules, with each unit having a unique serial number.
All new buildings, whether site- or factory-built, must comply with the local building codes and regulations. However, for compliance of the work completed away from the building site, the administrative provisions of Division C of the National Building Code permit an off-site review to determine compliance with this code. Off-site review is done through certifying the entire factory construction process to the CSA A277 standard, which covers the factory’s quality program, auditing and in-plant inspections. So if a factoryconstructed building in Canada bears the label of an accredited certification body (CSA, Intertek, Quality Assurance International, etc.), that body guarantees that the work completed in a factory meets the requirements of the local codes and regulations in effect at the installation site. That then provides local inspectors with assurance that concealed components that they cannot inspect, as well as other factory-built parts of the home, do not require re-inspection on this site. Further, the CSA A277 standard also sets requirements for personnel, their qualifications, schedules for inspection, labelling requirements and compliance procedures.
An added bonus is that modules also tend to exceed the wind resistance requirements of conventionally built homes, since they must be code-compliant to handle the potential stresses and high winds associated with road travel to the home site.
As local codes go, though, “municipal bylaws still need to be reviewed, as they set restrictions for factory-built housing in the context of architectural styles,” Lohmann says. “In addition to code compliance, we also often stress to municipalities that factory-built housing can easily meet the same architectural design guidelines as site-built. And some municipalities may also not realize that factory-constructed housing solutions can also help them meet
Factory-type construction doesn’t have to always be done in a factory. At the Buildings Show in Toronto this past winter, Stubbe’s Precast rolled out its Fast Track Modular Precast system. Partnering with Toronto’s BIM Studio, Stubbe’s is helping speed up the process of development and construction of residential midrise by pre-designing modules tailored to its total-precast production.
The new process provides standardized units that have been fully designed with input from all stakeholders, while providing trade-specific drawings. The integration of building information modelling (BIM) ensures faster design times, apart from a myriad of data acquisition.
“Total precast has been pretty common in the industry to speed up construction. We’ve probably done over 100 buildings in Ontario using precast,” says Stubbe’s Managing Director Jason Stubbe. “But then we wondered, ‘How can we standardize this to make the building cheaper while also reducing the time from when we start design to on-site construction?’ So we’ve come up with predesigned one- and two-bedroom units, and one-bedroom-plus-den units—all of varying sizes. Basically, we’ve made this building efficient for precast. We have four sample elevations and 26 different units and are working on more.
“We’ve had multiple developers go through the units and weigh in on how they would want to set up the unit,” continues Stubbe, whose company has worked extensively with OHBA members such as Reid’s Heritage Homes and Melloul Blamey Construction. “And we had architects look at it to make sure it flows for accessibility, etc. Then we hired a mechanical electrical engineer. and they pre-designed all the electrical mechanical for these units. So basically a customer calls and says, ‘Hey, I’ve got this property that can handle 100 units. I want 50% one-bedroom and 50% twobedroom units. We plug together these modulars into our BIM program and can have drawings for
you in five days. Within two months we can have building permit-ready drawings, whereas the traditional process could be a year. And once that’s done, we can tell you exactly how many square feet of drywall, studs, electrical wire per unit, per floor—however you want it broken up.
“There are mistakes found with every design in traditional construction,” Stubbe says. “But one advantage of standardized units is that if a design error is discovered in this new process, it’s fixed for all projects moving forward, which also helps us bring down cost.”
The model consciously addresses the shortage of skilled labour by providing “better information from these 3D models for trades on site,” says BIM Studio’s Joris Raaijmaakers. “Normally, the drawings being provided to trades are working documents that only show the end result of the building, whereas we give them an IKEA-style breakdown. For example, the framer gets a framing drawing that only shows framing—what they need to know to get their jobs done. But it’s also in combination with HVAC, plumbing, etc., because that’s usually where it goes wrong—when it turns out to be different than what the buyer thought they were getting—just because they were not able to make it work between the different trades. So we’re figuring things out ahead of time, rather than them having to figure things out on site.”
“We developed something that we saw most software vendors were not supplying,” Raaijmaakers adds. “That includes how much brick or siding or runs of HVAC pipe you’ll need. We can analyze how much ‘X’ is being sold, as well as the most popular home elevation style. There are many applications.”
“We don’t necessarily believe in full modular built-in-factory, ship-to-site—we don’t think it’s cost-competitive yet,” Stubbe says. “We believe in standardizing the hell out of it. I call this Total Precast 2.0.”
many of their policies, such as affordable housing, age-friendly housing, secondary suites and garden units or, in general, sustainable design.”
Arguably the most high-profile modular construction project in the province of Ontario is currently EVE Park in London, Ontario’s Riverbend community. Ellis-Don is constructing four buildings in two phases, using modular components produced by TRS Components Ltd. from the nearby town of Thornbury. “Each panel is manufactured off-site to fit precisely where it needs to go before being officially assembled. Faster, cleaner, stronger and with generally better quality,” the project’s website explains. A total of 84 units will
be divided equally across the four buildings, with August occupancy planned for Building A, and October for Building B. Occupancy dates for Phase 2 (Buildings C and D) have not been released.
“This is our first modular project in Canada,” says project lead Ashley Hammerbacher from the San Francisco office of St. Jacob’s, Ontario-based s2e Technologies. “We chose panelized modular construction because we believed that it would save time, reduce in-field mistakes, reduce material waste and improve quality.”
Royal Homes is well aware of the advantages, even touting that it “revolutionized the local building industry by blending traditional craftsmanship with modern technology to produce high quality custom homes that are built better and faster than outdoor-built homes.” Founded in 1971, Royal’s headquarters and 110,000 sq. ft. factory are located in the North Huron community
of Wingham. The company is seeing increased traffic through its doors, with recent projects varying from handsome 1,155 sq. ft. bungalows to sprawling luxury lakeside cottage country residences.
“On average, our homes are completed turnkey in as little as six to nine months after signing,” says Royal’s Matt Steffler, whose company is noted for its design centres and wealth of options for prospective homebuyers. Its 250point inspection is similarly as detailed. Further, Royal extends the seven-year Tarion-backed structural warranty three additional years, including a five-year no-leak foundation warranty.
On the renovation side, Toronto-based Modular Homes Additions has completed over 1,000 construction projects since its founding in 2000 and is taking advantage of its ability to do big things in restricted areas. “In the city, the best way to put an addition is to go up, since the lots are usually quite narrow and
“On average, our homes are completed turnkey in as little as six to nine months after signing.”
do not allow for ground additions. The modular addition system was developed so that bungalows can be topped up within three to five days,” says Bole Cirovic, director of sales and marketing at Modular, which has its own factory in East York. Although its construction process is not automated, “it is done in modules off-site in our climate-controlled facility,” Cirovic notes. “Another key advantage is convenience. Our clients can stay in the house during the construction, and installation of the shell is done quickly and without much mess on the site, meaning less hassle for both owners and neighbours.”
Through CreateTO, the City of Toronto has also been capitalizing on modular construction for supportive housing projects such as 11 Macey Avenue, a 56-unit, three-storey apartment building with a dining room and common rooms that opened in December 2020—just eight months after being approved by City Council, and 321 Dovercourt Rd. (three storeys with 44 units and similar added facilities), which opened nine months after approval.
Another plus is occurring on the job front, Lohmann explains. “While factory construction provides reliable access to skilled labour, it also broadens the labour pool in two ways. Number one, it can require other types of skilled workers, like machine operators or robotics specialists. And some modular construction workers may work at single stations and may be able to work on a narrower scope of their work, and therefore may not need the same breadth of skills that tradesmen on the traditional site would require. These two features reduce the dependency on the same labour and skills as on-site construction.
“To be clear though, it’s not necessarily less labour to build modular houses,” Lohmann says. “But where a shortage of labour exists, panelized modular construction may add capacity to supplement on-site builders.
“I think there needs to be more information about these kinds of benefits, and the webinar series is the first step,” Lohmann adds. “Hopefully each of the participants have conversations in their area of practice to incorporate some of these ideas. That’s how we can scale this faster.” OHB
demographics. Year after year, the most requested information is for the top features of homes in Canada. Storage remains a key priority for Canadians, with closet and garage space among the top spots. Energy efficiency features continue to show strongly as well, accounting for four of the 10. Large windows dropped out of the top 10 this year into 11th place. Not far behind were hardwood or wood-look floors in the kitchen and wifi thermostats.
The top 10 in order were: 1. Walk-in closets (primary suite); 2. Kitchen island; 3. Energy-efficient appliances; 4. Overall energy-efficient home; 5. High efficiency windows; 6. Walk-in closets (interior of home); 7. Two-car garage; 8. HRV/ERV air exchange system; 9. Linen closets; and 10. Openconcept kitchen.
The eighth annual edition of the CHBA Homebuyer Preferences study has been released. A total of 74 home builders participated in 2022, and over 20,000 new homebuyers were surveyed, with data collected from 1,390 respondents across six provinces.
The study enables industry professionals to dynamically drill down on data that matters most to their organizations. For example, data sets can be narrowed to a specific age cohort, revealing the preferences for that demographic. The response data can also be filtered by various local regions, buyer type, home type, home
price and other key fields.
“With the pandemic, we saw an accelerated shift towards preferences for digital resources when making home-purchasing decisions. In the home features section of the study, there was an increase in importance for ‘rooms’ and a decrease in the desire to be close to work and amenities,” the study notes. “Time will tell how many of those preferences are here to stay.”
The survey asked recent homebuyers for their opinions on more than 50 in-depth areas of home design, building features, buying preferences and
When asked what they’d be willing to sacrifice in order to make their current home more affordable, the most popular response again this year was a smaller home (21.4%), followed by being located farther from work and amenities (19.1%), neither of which have changed significantly since the study began.
Survey participants were also asked what they would spend an extra $10,000 on if they had the funds available. Interior finishes/ options continue to trend down but still rank first at 24.4%. Energy efficiency is the next most selected option at 16.3%. Notably, the agingin-place features category, first introduced as an option last year, has gone up this year, with 9.4% of respondents saying they’d put more money behind those features. That number goes up to 25% for Boomers and Pre-Boomers.
To check out this year’s survey, visit: Chba.ca/CHBADocs/CHBA/ Publications/2023-CHBA-CanadianHome-Buyer-Preferences.pdf.
After years of research and development, Minto Communities GTA unveiled the first production Net Zero home last month in Markham’s Union Village master-planned community. Developed in partnership with Metropia, the Net Zero home is both the first in Markham as well as Minto Communities’ first in the GTA.
Designed to produce as much energy as it consumes over a one-year period, its trade partners who helped design and construct the Net Zero home included Building Knowledge, Aerobarrier, RN Design and Bluewater Energy. Minto sees this as a milestone representing the future of development where more efficient and sustainable homes will be essential to cut greenhouse gas emissions for a healthier future.
A better building envelope with more insulation, triple-pane windows, improved airtightness, a dual-fuel airsource heat pump system and multizoned HVAC are just a selection of the features that improve the overall efficiency of the home and contribute to the home being certified under CHBA’s Net Zero Home Labelling Program. This first Net Zero home is designed to reduce energy consumption by 60%
and carbon emissions by 36%. In addition to comfort and efficiency, Net Zero homes can protect homeowners from future increases in energy prices.
“Sustainable design has always defined Minto’s core values and continues to gain momentum through our Corporate ESG Strategy,” says Carl Pawlowski, Senior Manager, Sustainability, Minto Communities GTA. “Our work on Net Zero is also a stepping stone to stay ahead of upcoming regulatory shifts towards reducing carbon emissions.”
Net Zero home upgrades were introduced to Union Village in the second phase of sales in April 2022, which contributed to the project’s reception and sold-out success. Due to the reception of the Net Zero upgrade packages, Minto Communities included this offering for The Heights of Harmony master-planned community in Oshawa where there has been steady interest as well.
The Union Village master-planned community is currently under construction. As of the end of April, 215 homes had been constructed and occupied. A total of 22 Net Zero Ready Homes will be constructed as part of phase 2.
TECHNOLOGYWhat’s the overlap between digital technology and running a home-building, construction or renovation business? Forward-thinking business owners in the residential real estate industry recognize it and can spot opportunities for digital tools to increase revenue and create efficiencies.
To stimulate digital transformation across the Canadian economy, the federal government has created the Canadian Digital Adoption Program (or CDAP) to offset the costs of digital investment for small and mid-sized businesses. CDAP enables your business to step back, assess your technological needs and opportunities, and then build a digital transformation plan and roadmap—at essentially no cost. Through the Boost Your Business Technology Grant, one of CDAP’s funding programs, your cost of completing this formal digital assessment with the help of a third-party advisor is offset by 90%.
After the assessment phase, you can receive an interest-free loan of up to $100,000 to execute the plan you created. Those funds can be used to purchase software and hardware, train employees and hire an outside advisor to facilitate your implementation of new technology.
CDAP presents an opportunity to expand your business sustainably. You can unlock all the potential of digital transformation to enhance your operations and boost revenue, while drastically reducing the financial risks.
Why invest in digital transformation? If you’re a builder, you’ve seen how economic challenges like rising costs and supply constraints impact your bottom line. No single digital solution can make those pains disappear, but a prudent
digital strategy can help alleviate them. Digital tools can support your business along the entire value chain. Whether you’re investing in workplace safety or simply getting your invoices paid on time, technology can lead to more efficiency. In the back office, there are the following opportunities:
CLIENT RETENTION AND FOLLOW-UP: As digital customer relationship management (CRM) tools become smarter, you can use them to drive higher profitability and sales volumes through optimized client communica tion and follow-up.
PAYROLL: You can automate routine payroll tasks and enable your staff to focus on more specialized tasks, with the help of digital tools and robotic process automation (RPA).
DATA ANALYTICS: Your business is collecting a pile of data that you might not even be aware of. Smart data analytics tools can help you anticipate financial impacts on your business before they happen, estimate job costs more accurately and much more.
BID MANAGEMENT: Certain software can create bid packages and standardize the process on a single platform, as well as search for the best bids and convert them into contracts with ease.
On the jobsite:
REDUCE WASTE: Waste takes many forms, from time and energy as employees move around the jobsite, to materials that get thrown away. Technologies for tracking movement and spotting inefficient processes will reduce costs and improve margins.
WORKPLACE SAFETY: Consider the impact of technologies like augmented reality (AR) or virtual reality (VR) to help train employees without exposing them to real dangers, or sensors that track noise levels, airborne particles or temperature on the jobsite.
AUTOMATION: No digital tool replaces top talent when it comes to producing quality work, but technologies like 3D printing and drones can automate certain time-consuming tasks.
—Soumya Ghosh is a director at MNP Digital
Life in the kitchen has never been so good
Building Knowledge Canada has welcomed Mark Rosen, Troy Tilbury and the Building Energy Inc. team into the BKC family.
For more than eight years, BKC and BEInc have worked together supporting common home builders and other professional clients throughout Ontario, Canada and the U.S. The amalgamation brings a deeper level of support to their clientele, notes Building Knowledge President Gord Cooke.
“I am so excited to be working with Mark and Troy,” Cooke says. “I had the pleasure of experiencing the vision and professionalism of (BEInc. founder) Bruce Gough as he brought ‘Energy Star for New Homes’ to Canada. Then watching as Mark continued that legacy of helping the building industry advance its performance goals—it seemed inevitable we would work together. This is the perfect time to make that happen, as our builder clients drive towards the 2030 zeroenergy challenge.”
Rosen, a noted professional architect, Registered Energy Advisor and building science consultant, will become a partner with BKC and take on the senior role of Director of Building Science, Building Knowledge Canada. Tilbury, an experienced Registered Energy Advisor, architectural technologist and building science technician, has supported some of Canada’s largest home builders in developing sustainability programs and meeting new energy codes. He will take on the role of Senior Project Manager, Greater Ottawa Area, Building Knowledge Canada.
The Professional Home Builders Institute is offering programs to specifically fit your unique business needs, with in-house Customized Training for your employees. Its team of industry experts works with you to tailor the content, resulting in a meaningful and highly relevant training experience.
Personalized education means you can focus on specific educational areas, while learning from proven industry experts and instructors. Companies can determine their class size (minimum of 10 students), addressing scenarios specific to your building style, sales challenges or construction scenarios.
The program also allows you to reduce travel expenses since the instructors will come to you.
For further information, contact PHBI’s admissions team at (888) 325-9999 or admissions@phbi.ca, or visit phbi.ca/on.
Neolith has launched a new global positioning campaign entitled “Sustainable Beauty,” which encapsulates its vision of the world as one of its primary objectives. “In essence, the company has elevated sustainability to be paramount and tantamount to success on the same level and nothing less,” Neolith notes.
Recent statistics back up the claim: zero waste, 100% water being recycled, fewer raw materials, 100% natural, 6,500+ solar panels, 100% renewable energy, up to 98% of content recycled and more. The new campaign features a new symbol, the dragonfly. OHB
We are a specialized pre-construction brokerage with a custom project approach. We know that one sales model does not fit all builders or projects. Instead, we listen to our clients to learn their individual needs, which ensures each project they launch sets a new benchmark for success.
Our services extend beyond what you see on the sales floor to include floorplan design, APS review, marketing, and achieving maximum revenue for our clients.
Simply put, we see and sell your vision.
IT CAN BE as plain as the nose on your face. Or a home’s facing anyway.
Whether part of a custom build or a simple upgrade for clients looking for an inexpensive reno, changing out the front door can have a quick and dramatic impact on curb appeal.
“Over the years, consumers didn’t necessarily pay a lot of attention to the front door. That trend is definitely shifting,” says Paul Commisso of Concord-based MasterGrain. “They are paying attention not just to the
aesthetics, but durability and energy efficiency as well. We get a lot more questions, especially with respect to government-funded programs like the Greener Homes grant.
Beyond the simple eye test, clients also want to feel safer these days, and technology is at the fore, Commisso says. “Smart locks that use a fingerprint, biometric scan or even ocular scans are becoming more popular. And mobile automation is increasingly prevalent as far as how the lock opens
and closes without a key. It works great for landlords and people who are renting properties like Airbnbs, because it gives them an opportunity to get rid of keys and manage who gets access to a home. And prices have come down considerably.”
But style is becoming more important too, says Commisso, whose company is noted for its innovative moldmanufacturing capablility, allowing it to accurately replicate virtually any texture or grain. “We are seeing the
door moving from ‘status quo’ to ‘status symbol. In a recent survey, about 50% of our customers were looking at what they could customize for their doors, whether it’s engraved designs, adding inlays or how they use hardware or glass.”
On the style front, MasterGrain is addressing a shift in the market toward more contemporary designs with its new Esperanza, Morgan, Thomas and Madelaine models. Esperanza is a smooth panel cherry door—almost Spanish Colonial in style—with added stainless steel inlays with gold finishes. The Morgan uses the same cherry slab
as the Esperanza, but with horizontal inlays that give it a more modern feel. “These doors can be stained any colour the customer desires, but it also gives us opportunities to start the conversation about what level of customization they want to see, since those inlays could be gold, black, silver‚—whatever,” says Commisso.
The Thomas door features a smooth fibreglass panel, with an engraved herringbone pattern that calling to mind the Art Deco era. It can also be stained or painted in any colour. The Madeline, meanwhile, is more of a transitional door. Lending itself to a modern
farmhouse style, it can be paired with minimalist barn lights and rattan furniture for a completely curated entryway. “But as soon as you paint that door black, it goes instantly contemporary,” Commisso notes. “And you can use door pulls or lockset hardware on it to entirely change up the look.”
Size matters too. With contemporary home design commanding ceiling heights of 10 feet or higher, “it’s driving a taller door, because you don’t want to 6’8” door with 10’ ceilings,” Commisso says. “So we’re seeing these entranceways getting larger and the desire for nine- or 10-foot doors picking up. And when you go with a taller door, proportions also change from a width perspective—so 42 inches wide, or wider, is becoming more sought after, especially within custom home design and construction.”
Beyond customization, where can the general builder make a big impact for a value-priced product? “If you look at the performance of a well-made fibreglass door, over time it performs
better than steel,” Commisso says. “It stands up to dings and scratches better than steel. And energy-performance-wise, it’s a better product if installed correctly. We’re definitely seeing a little bit of a shift in the marketplace towards fibreglass.”
Are homeowners surrendering any security if moving from steel to fibreglass? “Absolutely not, especially if you’re installing a fibreglass door with a multipoint lock system,” Commisso assures. “And a lot of our components are reinforced with steel on the interior. It makes it a much better door and much more difficult to break in.”
Kitchener’s Strassburger Windows and Doors is also leading the fibreglass door trend with its new Solution Series and shaker models.
“Thoughtful, clean lines, simple design and peace of mind,” are the principles behind the Solution Series, says Strassburger sales manager Dean Elvidge. “It comes with a selection of glass textures and sizes. The minimalistic style of the low-profile frame allows the glass in the door to feature prominently. The frame is built to resist warping and melting in highheat areas, so it can be used with any colour finish. And the frame is available in both smooth and textured.”
On the shaker side, the Plastpro Craftsman series pulls design inspiration from 19th and 20th-century architecture, featuring flat panels and traditional styles. It combines modern and classic elements with a selection of ovolo (rounded convex molding) profiles, simple shaker profiles and sleek direct-glazed options. Grain options in this series are Fir and Smooth.
“Fibreglass doors are still more expensive than steel, but when you factor in the ease of finishing, dent resistance, composite stiles and rails, and numerous glass and grill options, it isn’t surprising that their popularity continues to grow across all markets,” Elvidge says.
“We are seeing a trend towards
Even garage doors are getting a contemporary makeover, suggests Chris Garden, owner of Vaughan-based Highbury Doors, a one-stopshop for selecting, installing and servicing residential garage door, entry door and window needs.
“A newish trend is for long slim windows across the top. And now we’re seeing slim windows going down the side. But it’s more of a modern sleek look with tinted windows,” says Garden, who has worked with such OHBA members as Pratt Hansen, Calibrex Developments, Hallett Homes and Huron Creek, as well as a number of custom builders.
While that tint—black satin or frosted are common—add a measure of privacy, it also allows clients to modernize the home’s look, Garden notes.
Being versatile is obviously key when it comes to customization, Garden stresses. “We just finished a project in Barrie that were all modern towns with flush black doors with no windows. We’re doing a build in Cambridge that has a flush look with frosted glass windows on the side. We’ve got custom builders going with a traditional look and others building a more modern edge into it. That’s why we deal with a lot of different suppliers, each of whom offers something different.
Since 1974, TRS has o ered builders a single source supply network of wall panels, roof trusses, oor panels. Our supply and install expertise will make your next job faster, easier and more e cient.
clean, simple lines, reflecting the architectural design of today,” he adds. “We offer options for many designs, including Modern Farmhouse, Contemporary, Craftsman and Traditional. Demand for custom paint finishes along with requests for our many standard paint and stain finishes is increasingly popular too.”
And customers want to see a tight fit, Elvidge says. “There’s a growing demand for these entrance systems to be equipped with multipoint hardware to provide the utmost in security while ensuring a tight seal to minimize air infiltration.”
Citing it as an easy way to add personality to a client’s home without going through a major reno, Kitchener’s Golden Windows is seeing an uptick
in statement-making colours for front doors. “In 2023, we’re going to see a major shift to brightly coloured doors in a variety of eye-catching shades, ranging from bright and sunny yellows to soothing blues and teals,” the company predicts.
Expect further advancement in glass elements as well, Golden says. “In past years, traditional homes typically donned a standard solid wood door. In some cases, a small window would sit at the top, primarily to let in the natural light. This year, glass is making a bigger statement. In some cases, glass is used to frame the door itself, with panelling on each side of the door— and in many instances, on top of the door frame. Modern homes may favour a more geometric style, with large glass panes cascading down the door. Those looking to add glass without sacrificing
privacy will benefit from an etched or frosted glass designs.
Golden also expects to see more natural wood elements being incorporated into front entry doors this year. “A natural stain is a great way to make a statement without changing the aesthetic of the home drastically.”
And look for more innovation and unique designs inside the home, including glass sliding doors, pocket doors, arched interior doors, modern pivot doors and textured doors.
The stylish search for natural light continues in 2023, says Jeld-Wen, be it from the addition of glass inserts in an entry door or patio door. But it can all be had with a little help from the government. Following the criteria established by Natural Resources Canada, windows and sliding patio doors may certify as an Energy Star Most Efficient model and qualify for $250 per rough opening, under the Greener Homes program. Any hinged steel or fibreglass door can only meet the Energy Star Certified criteria, but that still qualifies for $125 per rough opening, the company reminds.
Jeld-Wen’s ProCore the Quiet Door construction offers a solid-core design that helps with sound reduction while also improving fire ratings when compared to hollow-core models.
As far as the colour equation goes, Jeld-Wen sees nature-inspired shades with a hint (or more) of pink making big inroads as the year progresses. Supporting the biophilic design trend are four soothing shades this year: paint brand Dunn-Edwards’ Terra Rossa (a rosy pink tone with a touch of terracotta); Raspberry Blush (a bold redorange); Sherwin Williams’ Colour of the Year, Redend Point (an earthy “soulful blush-beige” from the company’s Terra collection); and Glidden’s 2023 Colour of the Year, Vining Ivy, an aqua-emerald.
Those natural tones serve to catch the eye of passers-by, but also to calm the nerves of residents looking outward. OHB
THE DESIGNS of future homes will pose several challenges. They will have to be functional and address new lifestyle trends, be comfortable to live in, be cost- and energy-efficient, as well as sustainable in their construction and operation.
This seems to be a tall order from a designer, builder and homebuyer standpoint. Yet it offers an opportunity to be creative and address issues that in the past were considered marginal, such as adaptability.
The need to make homes adaptable to a wide range of occupants involves a conceptual approach to make any space look larger to begin with. Traditionally, the proportions of a dwelling’s footprint can be either square or rectangular. The interior of a home with a square plan is likely to be easier to subdivide. When the unit is detached, there will also be greater flexibility in the placement of rooms next to windows.
One of the distinguishing features of adaptable design is the option for homebuyers to purchase the type and “quantity” of residence that they need and can afford. This option is made possible by designing a threestorey structure that can be built, sold and inhabited as a single-family house, a duplex or a triplex; thereby
contributing to a healthy mix of user types in the same development.
For example, in the case of a singlefamily house for a couple with one child, the ground floor can accommodate a living room, dining area, washroom, laundry room and kitchen, with plenty of storage, leaving the second level for three bedrooms and a complete washroom with a bathtub. The semi-basement can be used as a garage, home office or workshop. Therefore, considering the same family 20 years later, the original buyers may decide to rent their semi-basement as an independent unit with a kitchen, living/ dining area, bedroom and washroom.
Woodview Mews is the first application of Geraghty Taylor Architects’ LivinHome typology, located in London, U.K. The design focuses on providing flexibility through layout and facade choices that can reflect its owners’ lifestyles.
The LivinHome concept consists of three standard plans on open floor plates. One is an open-plan living space, another contains only bedrooms and the third encompasses one- or twobedroom apartments. The service zone of each layout is placed at the same location, which facilitates a change in plan when needed.
At Woodview Mews, the six townhomes are organized into 11 units of various densities: townhouses, duplexes and apartments. The first floor features a recessed entryway, while the second and third floors have balconies.
A couple purchasing a townhouse may live in a duplex and rent out an apartment or live in an apartment and rent out two. When they decide to start a family, the townhouse can be reorganized to become their home. After the children grow up, the parents may rent out apartment floors to their children. They may also transform the first floor into an office or shop. As they age, they may choose to enclose the balcony space to make room for an elevator. Using this method, aging in place is possible with minimal disturbance to the buildings and to neighbours.
Woodview Mews practices sustainability first by offering interior flexibility that encourages homeowners to stay with their current home. This increases the lifespan of the development, which also saves owners money by avoiding the costs of moving to a larger home. OHB
Avi Friedman IS AN ARCHITECT, PROFESSOR, AUTHOR AND SOCIAL OBSERVER. AVI.FRIEDMAN@MCGILL.CA