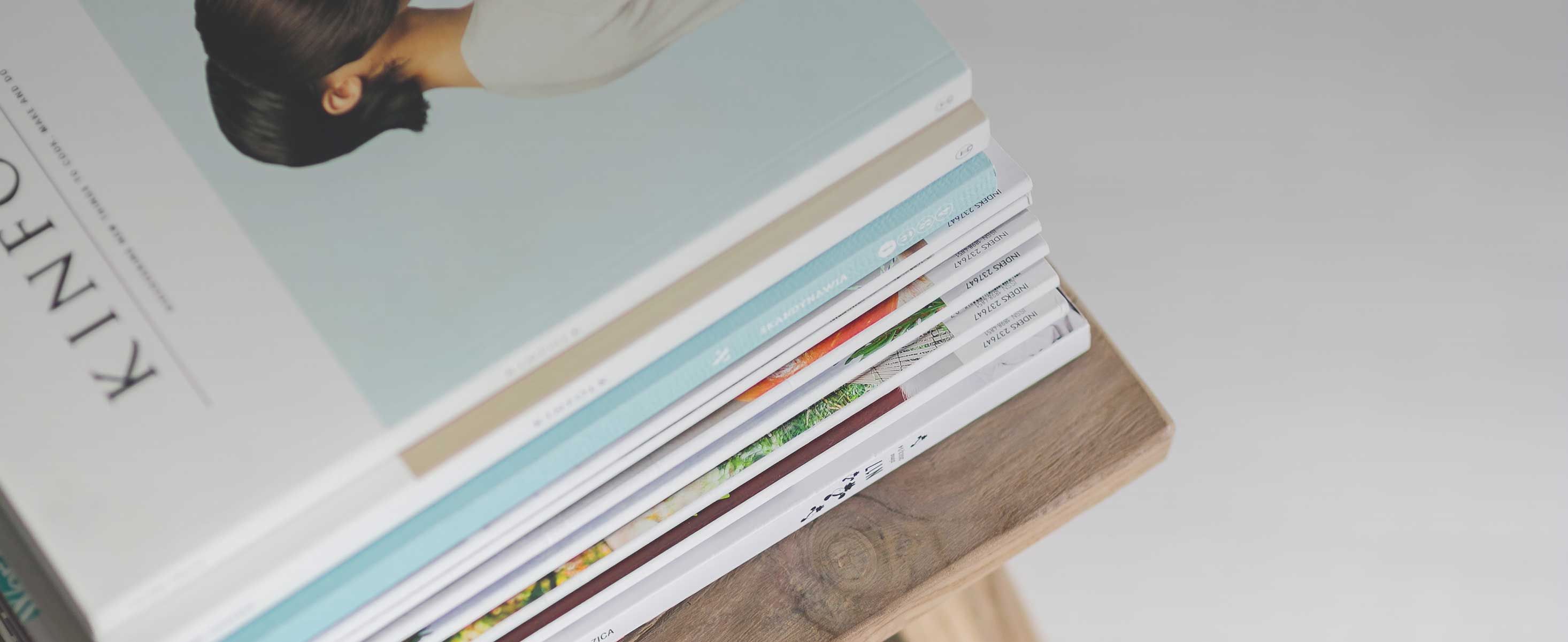
1 minute read
Launch Strategies & Transport
LAUNCH STRATEGIES & TRANSPORT
Dry Docks
Advertisement
Dry-docks allow sea-bound structures to be built feasibly on-land, with the sea close-by. This obviously reduces the cost of transporting the finished product from the place of manufacture to the point of launch, but does impinge on access to vital manufacturing conditions and specialist equipment that may not be available outside of the factory, in a dry-dock. In this case, the concrete would be composed in the factory and transported to the dock via a convoy of cement-mixers, so to speak, and then cast into shape in the dock itself before the final launch. The largest cement mixers available for use in the UK have a capacity of around 14 m3 , meaning that, with a total structural volume of 1662.65 m3, the total concrete requirement for the construction of this tower would demand as many as 120 individual loads.
The Alexandra Dock in Hull, East Yorkshire, is one example of where this could be done.
Factory Construction
The other option that our research disclosed involves constructing the tower in separate panels inside the factory (so that the concrete can be fabricated to the optimum quality in the requisite conditions), and subsequently transporting them by lorry to the dock, where they would be assembled ready for launch. Imagine an enormous, 50 metre tall Lego-set, if you can!
Such that we may work within the constraints of a conventional engineering context, this would limit us to 7m x 7m panels, as this is the largest that could feasibly be transported in view of their exceptional thickness (0.3m). This would give a total mass of 37 tonnes for the denser panels, and 26 tonnes for the lighter ones, which can just be handled within the normal operating capacity of a heavy-duty crane.