
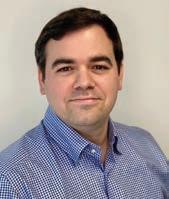
Across radar, EW bands, and beyond, Analog Devices provides broad and narrow-band GaN power amplifier MMICs for your next-gen phased array and communication systems.
analog.com/gan
Editor’s Perspective
5 Speeding up DoD acquisition By John M. McHale III
Mil Tech Insider
7 CJADC2 interoperability: AI-/ML-based sensor fusion at the edge By Dominic Perez
Guest Blogs
40 The U.S. Marine Corps’ new approach to asset management and data precision By Carlos Peña and Robert Droppa, DT Research
41 Driving the future of defense technology By Pragati Pathrotkar, Transparency Market Research
42 How the DoD can win the AI race By Logan Schraeder, FirePoint Innovations
Defense Tech Wire
8 By Dan Taylor
Editor’s Choice Products
44 By Military Embedded Systems Staff
Connecting with Military Embedded
46 By Lisa Daigle
SPECIAL REPORT: Tech for navigating GPS-denied environments
12 Beyond GPS: How the defense industry is building smarter navigation By Dan Taylor, Technology Editor
16 Optimizing MEMS IMU data coherence and timing in navigation systems By Mark Looney, Analog Devices, Inc. (ADI)
20 New security standards for electronic device detection: Are military and federal facilities ready? By Dr. Brett Walkenhorst, Bastille
MIL TECH TRENDS: Military power supplies
22 The real-time battlefield: The revolutionary tech connecting the front line By Rob Mather, IFS
26 Mobile energy: powering the future battlefield By Gary Dannar, Dannar
INDUSTRY SPOTLIGHT:
Open standards for embedded systems: FACE, SOSA, CMOSS, VPX, and more
30 Autonomous engine systems for helicopters depend on standards-based controls By Richard Jaenicke, Green Hills Software
36 Navigating the heat: Advanced cooling strategies for high-performance military computing By Matthew Tarney, nVent SCHROFF
To
ON THE COVER:
U.S. Space Force Tech. Sgt. Vince Couch, 527th Space Aggressor Squadron (SAS), right, uses an azimuth compass to ensure the proper positioning of a GPS electromagnetic attack system during a GPS electromagnetic interference training session at Schriever Space Force Base, Colorado. The 527th SAS’s mission is to know, teach, and replicate modern, emerging, and integrated space threats in order to prepare service, joint, and coalition forces to fight in and through contested or denied environments. U.S. Space Force photo by Ethan Johnson.
https://www.linkedin.com/groups/1864255/
By John M. McHale III
President-elect Donald Trump says he is looking to disrupt government and eliminate waste and no department will go untouched, especially the U.S. Department of Defense (DoD). Aligning with billionaire and well-known cost-cutter Elon Musk, along with entrepreneur and erstwhile presidential candidate Vivek Ramaswamy, he is forming the Department of Government Efficiency, what is planned to be a presidential advisory commission, to enact this promise.
As I write this, Trump has also named Pete Hegseth, a retired Army major and television presenter, to head the DoD and carry out many reforms to the behemoth government agency. Hegseth, with his decorated warfighter background, cares deeply about those in uniform, but he has limited experience running a bureaucracy this size and will have challenges enacting change in such a behemoth.
During an interview with the Shawn Ryan Show on youtube. com, he told the show host he wants to purge what he called woke generals, reform military training, and return the DoD to being a more lethal force by speeding up procurement. All of that hinges on his confirmation, which is no guarantee.
Lethality is greatly aided by technology and by getting the best commercial, high-performance weapons, sensors, and armor to the warfighter as fast as possible. Speeding up the tech-development-to-tech-deployment chain is a change just begging for acquisition reform.
Speeding up acquisition – a topic we’ve covered many times in this space – flavored conversations I had with readers and advertisers in Washington at the annual Association of the U.S. Army (AUSA) Annual Meeting in October. Most of those conversations started with discussions of what the MOSA –modular open systems approach – mandate actually means for the acquisition process.
I was told that flag officers are saying they want MOSA: They see it as a way to get tech deployed more quickly. All have seen the success of quickly deployed autonomous solutions in the war in Ukraine and want the DoD to be able to move that quickly. However, there is an upfront cost to MOSA initiatives and it’s not for every system. It’s not a panacea to improve capability, but rather a way to lower long-term life cycle costs and a way to leverage commercial tech early in a system development cycle.
And there’s the rub: How do you get the DoD to speed up, break through bureaucratic walls, and grab the innovation?
John.McHale@opensysmedia.com
In 2018, Ken Peterman, then president of Viasat’s Government Systems division, told me there is a certain amount of inertia in acquisition policy. “For 50 to 60 years the government has been an inventor of technology,” he said. “It doesn’t know how to buy a turnkey service. Its model is based on breaking down an ecosystem into parts such as waveforms, modems, etc. This encourages long developmental cycles and higher costs. By leveraging commercial solutions, the government is able to do the opposite; because by purchasing a service the government can access a complete, functioning system all at the same time, with no risk and no delays. Early adoption of these … technologies can help solve warfighter problems now.”
Six years later the inertia is still there. The DoD acquisition process continues to be glacial. Many people thought the DoD’s 1994 commercial off-the-shelf (COTS) technology mandate would speed up acquisition and lower costs of technology. Today, many think that MOSA strategies will finally enable both. These strategies will do that to some extent and will also bring new companies into the DoD orbit with new innovations, but they are not a complete overhaul of acquisition practices.
It has been my experience covering the DoD that efforts to replace or eliminate government-acquisition processes often end in failure or do not change anything in the long run. Eliminating whole departments and drastically reducing the workforce, as Trump’s appointees promise to do, could accomplish that. We’ll see if Musk, himself a defense contractor, can help break down those bureaucratic walls.
In recent years, to get around the slow acquisition process, the U.S. government created new processes and dusted off old ones to test, develop, and procure technology and get it more quickly into the hands of warfighters.
Rapid-acquisition offices, increases in Other Transactional Authorities (OTAs), and the Defense Innovation Unit’s developmental offshoots like the Air Force’s AFWERX and Special Operations Command’s SOFWERX are examples of efforts to prototype technology and leverage commercial innovation and small business. Of all of these the Space Development Agency has the most funding and momentum, aiming to launch viable products every two years.
The obstacles to reform are not few in number and will only increase. Hegseth told Ryan the U.S. is a decade behind in weapons procurement. However, as SecDef he may only have two years to catch up, as the 2026 midterms may bring Democrat control back to Congress.
ADVERTISER/AD TITLE
32 AirBorn – Introducing Power Blade 2300W+ VPX power module
2 Analog Devices, Inc. –Amplify your spectral dominance with the GaN edge
3 Annapolis Micro Systems –64 GS/s Direct RF is at hand!
25 Behlman Electronics, Inc. –No one powers the Army like Behlman
38 Dawn VME Products –Dawn single slot OpenVPX development backplanes
27 Elma Electronic –Accelerate development to deliver performance to the warfighter
34 embedded world –Save the date! 11-13.3.2025 Nuremburg, Germany
48 GMS – X9 Spider – the world's smallest ultra-rugged battlefield A.I.
24 Interface Concept –Elevating your embedded experience
39 Phoenix International –Phalanx II: The ultimate NAS
13 PICO Electronics Inc –DC-DC converters, transformers & inductors
18 Rantec Power Systems Inc. –Global leader in power supplies designed in alignment with the SOSA Technical Standard
28 Sealevel Systems, Inc. –Advancing architecture for the next generation of command & control
Association of Old Crows International Symposium & Convention (AOC 2024) December 11-13, 2024
National Harbor, MD https://aoc2024.crows.org/
SPIE Photonics West
January 25-30, 2025
San Francisco, CA
https://spie.org/conferences-and-exhibitions/ photonics-west#_=_
WEST 2025 (AFCEA West)
January 28-30, 2025
San Diego, CA
https://www.westconference.org/West25/ Public/enter.aspx
embedded world 2025
March 11-13, 2025
Nuremberg, Germany https://www.embedded-world.de/en
GROUP EDITORIAL DIRECTOR John McHale john.mchale@opensysmedia.com
ASSISTANT MANAGING EDITOR Lisa Daigle lisa.daigle@opensysmedia.com
TECHNOLOGY EDITOR – WASHINGTON BUREAU Dan Taylor dan.taylor@opensysmedia.com
CREATIVE DIRECTOR Stephanie Sweet stephanie.sweet@opensysmedia.com
WEB DEVELOPER Paul Nelson paul.nelson@opensysmedia.com
EMAIL MARKETING SPECIALIST Drew Kaufman drew.kaufman@opensysmedia.com
WEBCAST MANAGER Marvin Augustyn marvin.augustyn@opensysmedia.com
VITA EDITORIAL DIRECTOR Jerry Gipper jerry.gipper@opensysmedia.com
DIRECTOR OF SALES Tom Varcie tom.varcie@opensysmedia.com (734) 748-9660
STRATEGIC ACCOUNT MANAGER Rebecca Barker rebecca.barker@opensysmedia.com (281) 724-8021
STRATEGIC ACCOUNT MANAGER Bill Barron bill.barron@opensysmedia.com (516) 376-9838
EAST COAST SALES MANAGER Bill Baumann bill.baumann@opensysmedia.com (609) 610-5400
SOUTHERN CAL REGIONAL SALES MANAGER Len Pettek len.pettek@opensysmedia.com (805) 231-9582
DIRECTOR OF SALES ENABLEMENT Barbara Quinlan barbara.quinlan@opensysmedia.com AND PRODUCT MARKETING (480) 236-8818
INSIDE SALES Amy Russell amy.russell@opensysmedia.com
STRATEGIC ACCOUNT MANAGER Lesley Harmoning lesley.harmoning@opensysmedia.com
EUROPEAN ACCOUNT MANAGER Jill Thibert jill.thibert@opensysmedia.com
TAIWAN SALES ACCOUNT MANAGER Patty Wu patty.wu@opensysmedia.com
CHINA SALES ACCOUNT MANAGER Judy Wang judywang2000@vip.126.com
PRESIDENT Patrick Hopper patrick.hopper@opensysmedia.com
EXECUTIVE VICE PRESIDENT John McHale john.mchale@opensysmedia.com
EXECUTIVE VICE PRESIDENT AND ECD BRAND DIRECTOR Rich Nass rich.nass@opensysmedia.com
DIRECTOR OF OPERATIONS AND CUSTOMER SUCCESS Gina Peter gina.peter@opensysmedia.com
GRAPHIC DESIGNER Kaitlyn Bellerson kaitlyn.bellerson@opensysmedia.com
FINANCIAL ASSISTANT Emily Verhoeks emily.verhoeks@opensysmedia.com
SUBSCRIPTION MANAGER subscriptions@opensysmedia.com
By Dominic Perez
The U.S. Department of Defense (DoD) Coalition Joint All-Domain Command and Control (CJADC2) system is revolutionizing modern military operations by integrating data across all military domains: land, air, sea, space, and cyberspace. For effective multidomain operations, sensor data needs to be processed rapidly and shared across different military branches. Achieving this level of interoperability requires sophisticated technologies to handle vast and complex data streams in real time, particularly artificial intelligence (AI) and parallel sensor fusion processing at the edge.
AI and machine learning (ML) algorithms, vital enablers in CJADC2, help to automate decision-making by rapidly analyzing diverse data sets from various sensors and sources. These algorithms excel at processing complex sensor data, identifying patterns, generating actionable intelligence, and perhaps most importantly, they do not get tired or distracted as a human operator might. In the CJADC2 environment, information from different systems – whether airborne, space-based, or ground-based sensors – must be harmonized into a common operational picture (COP).
For interoperability, AI serves as a bridge between disparate data systems and protocols. Military platforms and sensors were often developed independently and are not inherently designed to communicate with each other. AI-driven systems can standardize data formats and protocols, transforming raw sensor data into actionable intelligence that can be accessed and used by all branches of the military, our allies, and coalition partners. Generating a COP requires data from multiple sensors to be combined and correlated to create a unified understanding of the environment. For example, radar, video, and infrared sensors may all capture data at the same time, but each sensor offers a different perspective of the same battlefield.
Appropriately configured CJADC2 systems can analyze all sensor inputs concurrently, fusing them into a more detailed operational picture. This ability to analyze real-time sensor data is critical in rapidly changing combat environments, where delays could cost lives. AI algorithms drive sensor fusion by analyzing relationships between data streams and identifying threats or opportunities that individual sensors might miss.
Edge computing is integral to CJADC2 because it enables the processing of sensor data close to where it is collected, rather than relying on a centralized data center. When data travels back to a central command, delays can undermine military operations. While a data center can handle orders of magnitude more processing, edge systems can operate independently in communications-denied environments. This factor is crucial for ensuring real-time actionable information is available to commanders regardless of battlefield dynamics. Processing data at the tactical edge ensures that operators can act immediately based on real-time data.
Edge systems, such as Curtiss-Wright’s PacStar 454 GPU enhanced server, provide the computing power necessary for processing large-scale AI inference and sensor fusion at the tactical edge. These systems can be used in mobile, vehicle-mounted, or remote environments.
AI- and ML-powered sensor fusion at the edge represents the future of CJADC2 interoperability. The military can leverage these technologies to create a seamless, real-time understanding of the battlefield in order to make faster, better-informed decisions. Edge computing platforms are key to this future, enabling real-time
processing of vast amounts of sensor data in austere environments. However, implementing AI and sensor fusion in CJADC2 faces several challenges:
1. Data collection: The old adage “garbage in, garbage out” applies both to AI-based systems and legacy system designs. Data from the battlefield must be collected and added back into datasets used for training/retraining AI models. Ideally, data is stored at the edge and forwarded to a data warehouse when connectivity allows.
2. Data standardization: AI systems must handle different data formats and protocols from various sensors, making it critical to establish standardized formats and labeling systems for sensor data.
3. Security: As AI systems become integral to processing military data, they also become prime targets for cyberattacks. Secure and encrypted communication between sensors and AI systems must be ensured. National Security Agency (NSA) Commercial Solutions for Classified (CSfC)-certified data-at-rest (DAR) solutions provide dual-encrypted data storage solutions.
4. Scalability: As the number of sensors and data streams increase, AI systems must scale effectively, maintaining performance while ensuring interoperability across different military platforms.
These challenges related to data standardization, security, and scalability, must be addressed to fully realize the great potential of CJADC2.
Dominic Perez is the CTO at Curtiss-Wright Defense Solutions and a Curtiss-Wright Technical Fellow.
Curtiss-Wright Defense Solutions https://www.curtisswrightds.com/
By Dan Taylor, Technology Editor
MQ-20 Avenger performs autonomy maneuvers with U.S. Navy controls
General Atomics Aeronautical Systems, Inc. (GA-ASI) used its MQ-20 Avenger uncrewed aerial system (UAS) to execute commanded autonomy maneuvers as part of a demonstration with the U.S. Navy, the company announced. The demonstration used the Navy’s MD-5 Ground Control Station (GCS) equipped with Lockheed Martin’s MDCX autonomy platform to command and control the MQ-20 Avenger via a Proliferated Low Earth Orbit (PLEO) datalink.
The MD-5 GCS operated from Patuxent River, Maryland, while the MQ-20 flew from GA-ASI’s Desert Horizon flight operations facility in El Mirage, California, according to the company. The flight marked the first instance of bidirectional communication between GA-ASI’s MQ-20 and the Navy’s Unmanned Carrier Aviation Mission Control Station (UMCS) operation codes, the company notes, adding that the exercise demonstrated the UMCS’s ability to command various unmanned platforms, including autonomous behaviors, through a common control system.
The U.S. Marine Corps initiated full-rate production of the Amphibious Combat Vehicle 30 mm (ACV-30) program with a $51 million contract won by Kongsberg Defence & Aerospace for long lead items.
According to a Kongsberg statement, the contract, part of a broader framework agreement worth as much as $329 million, includes subcomponents for the 30 mm remote turret manufactured by Kongsberg in Pennsylvania. The ACV-30 features the Medium Caliber Turret 30 (MCT-30), a stabilized, remotely operated system designed to enhance protection and mobility for Marines while maximizing space for troops and mission-critical equipment, according to the company. This contract is a major milestone in the Marine Corps’ ACV-30 program, enabling expedited deliveries for full-rate production, the company says.
The U.S. Navy reported completion of the Preliminary Design Review (PDR) of the substantial improvements for the E-2D Advanced Hawkeye under the Delta System Software Configuration (DSSC)-6 update.
According to the Navy’s announcement, E-2/C-2 Airborne Command & Control Systems Program Office (PMA-231) and industry partner Northrop Grumman wrapped the PDR, which assesses the allocated baseline and authorizes the transition into a detailed design for the E-2D DSSC-6 program upon closure of the review.
The updated configuration is intended to enable avionics infrastructure improvements to flight and mission systems including increasing crew effectiveness, addressing parts obsolescence, adding improved computing and electronic storage, improving connectivity for command and control, and creating a modular open systems environment for future technology insertion. The Navy reports that the first test flight is scheduled for fiscal year 2027.
Sweden, Finland sign military optronics framework agreement with Senop
The Swedish Defence Materiel Administration (FMV), the Finnish Defence Forces Logistics Command, and Senop Oy signed a framework agreement for the procurement of military optronics, according to a joint statement. The agreement aims to streamline and reduce costs for acquiring optronic systems to improve the operational capabilities of the Finnish and Swedish armed forces, the partners say. This procurement collaboration follows an earlier executive agreement between the countries to improve defense resilience and cost efficiency in equipment acquisition, according to the statement. Earlier in 2024, Finland signed a letter of intent with Senop to acquire additional night-vision goggles (NVGs) and new night-vision technologies. Senop specializes in night-vision devices, sensor-based solutions, and critical communication systems for defense and security sectors.
Netherlands orders 12 Airbus H225M helicopters for special forces
Airbus Helicopters won a contract from the Dutch defense ministry for the acquisition of 12 H225M helicopters, along with an initial package of support and services, Airbus announced. The agreement, finalized during the November 2024 Euronaval trade show in Paris, designates the H225M for use by the Royal Netherlands Air Force (RNLAF) 300 special operations squadron, Airbus reports. The H225M was selected following an evaluation process during 2023.
The H225M is equipped for special forces missions, featuring tactical communication systems, upgraded avionics, and an enhanced main gearbox. The helicopter’s maximum takeoff weight has been increased to 11,160 kg (24,604 pounds), and it can be tailored to accommodate mission-specific equipment, Airbus says. The RNLAF currently operates H215M Cougars, and the H225M will expand operational capabilities for special operations, the company says. Airbus Helicopters and the RNLAF intend to collaborate on customization efforts.
Cyber hardening program from DARPA gets RTX BBN Technologies on board
RTX’s BBN Technologies unit won a contract to support the Defense Advanced Research Project Agency (DARPA) Compartmentalization and Privilege Management (CPM) program, which seeks to harden cybersecurity for legacy computing systems. Under the terms of the DARPA contract, BBN Technologies is tasked with developing tools to enhance cyber resilience by automatically subdividing software systems into smaller and more secure compartments, preventing initial breaches from escalating into successful cyberattacks while maintaining system efficiency. RTX reports that under the CPM program, BBN is developing the Analysis and Restructuring for Containment (ARC) tool to thwart unauthorized privilege escalations and lateral movements within software systems. According to the RTX announcement, ARC will be engineered to automatically analyze large code bases and construct smaller, secure compartments. The tool intends to ensure that only the minimum access necessary is granted.
3D-Audio system contract won by Terma for U.S. Air Force F-16s
Aircraft technology company Terma won a $9 million contract to supply its 3D-Audio system for the U.S. Air Force Combat Command’s F-16 fighter aircraft. Under the terms of the contract, the company reports, Terma will provide the 3D-Audio systems as part of an F-16 fleet upgrade over the next two years.
The system is designed to enhance pilot situational awareness by spatially separating audio signals, aligning sound with threat directions, and integrating active noise reduction, according to the company. The 3D-Audio system is compatible with various aircraft and aims to reduce audio clutter, enabling pilots to process critical information more efficiently during missions, the company says.
Gripen E debuts in multinational military exercise
Saab’s F-39E Gripen made its operational debut during the first two weeks of November at CRUZEX 2024, a multinational military exercise hosted by the Brazilian Air Force (FAB). The exercise involved more than 2,000 military personnel and more than 100 combat aircraft from Brazil and 15 other countries across Latin America, Africa, Europe, and the U.S.
The Saab news release about the CRUZEX debut stated that the F-39E Gripen participated in composite air operations (COMAO), which simulate complex scenarios requiring coordinated missions from diverse aircraft to counter adversary defenses. The Gripen E’s combat tasks include offensive counterair (OCA) operations to protect allied forces and defensive counterair (DCA) missions aimed at repelling attacks, according to the Saab statement. The F-39E Gripen also features technologies such as active electronically scanned array (AESA) radar, infrared search and track (IRST) sensor, and advanced human-machine interface with artificial intelligence (AI).
Chinook helicopters to leverage Honeywell auxiliary power unit, generator
Columbia Helicopters chose Honeywell’s 36-150[CH] auxiliary power unit (APU) and 35KVA generator system to upgrade its fleet of Model 234 and CH-47D Chinook helicopters, Honeywell announced in a statement. The upgraded APU will provide a source of ground power for main engine starts and for operating aircraft hydraulic and electric systems, the statement reads. Honeywell claims that the new systems will deliver greater power compared to the currently installed equipment, enhancing operational efficiency for heavy-lift missions.
The 36-150[CH] APU is based on Honeywell’s 36-150 series, which has been deployed globally on military Black Hawk helicopters. Columbia Helicopters, a provider of heavy-lift helicopter services, plans to integrate the new systems to support its mission readiness and expand its capabilities in demanding operational environments, the statement reads. Honeywell has delivered more than 10,000 36-150 APUs since 1983, the company says.
MEDUSA underwater mining system prototype under development for U.S. Navy
General Dynamics Mission Systems (GDMS) won a $15.9 million contract from the U.S. Navy to design, test, and deliver the Mining Expendable Delivery Unmanned Submarine Asset (MEDUSA), a tactical uncrewed underwater vehicle (UUV) for advanced maritime mining operations, the company announced. MEDUSA, an expendable system launched from submarine torpedo tubes, is intended to enhance long-range offensive mining capabilities in clandestine naval missions. The contract covers research and development for the MEDUSA prototype, including its design, fabrication, and testing, with options for further prototype production and support that could raise the contract’s value to $58.1 million, the statement reads. The MEDUSA program will be supported by a team that includes General Dynamics Electric Boat, Applied Physical Sciences, Ordnance and Tactical Systems, EaglePicher, and MIKEL, the company says.
Airbus to supply H135 training helicopters to Canada’s air force
Airbus Helicopters signed a contract with SkyAlyne, a joint venture between CAE and KF Aerospace, to deliver 19 H135 helicopters to the Royal Canadian Air Force (RCAF) for pilot training, the company announced in a statement.
This contract, part of Canada’s Future Aircrew Training (FAcT) program, will be the first time that H135 helicopters have been provided to the Canadian Armed Forces. The twin-engine helicopters will be completed at Airbus’s Fort Erie facility and customized with Canadian-developed modifications to avionics and communications, the statement reads. Deliveries are expected to begin in early 2026. The agreement also includes a support and services package and development of a Ground-Based Training Solution, Airbus says.
Navy electronic warfare antenna arrays designed by Honeywell
Honeywell announced the award of a $16 million U.S. Navy contract for the full build, test, and integration of 25 antenna array panels supporting the Surface Electronic Warfare Improvement Program (SEWIP) Block 2. According to the company’s announcement, SEWIP is an integrated shipboard combat system that provides a full suite of next-generation electronic warfare (EW) capabilities, with Block 2 adding new defensive technologies and functional capabilities that enable enhanced threat detection and situational awareness. The antenna array panels support early detection, analysis, threat warning, and protection from anti-ship missiles, the company said.
The SEWIP antenna array panels are slated to be built at Honeywell’s Lansdale, Pennsylvania location, with the work expected to be completed by August 2027. The latest contract win comes immediately following Honeywell’s $1.9 billion acquisition of CAES Systems Holdings, which was announced in September 2024.
Airbus Helicopters won a contract from the Dutch Ministry of Defence for the acquisition of 12 H225M helicopters, along with an initial package of support and services, Airbus announced in a statement. The agreement, finalized during the Euronaval trade show in Paris, designates the H225M for use by the Royal Netherlands Air Force (RNLAF) 300 Special Operations Squadron, the statement reads. The H225M was selected following an evaluation process in 2023.
The H225M is equipped for special forces missions, featuring tactical communication systems, upgraded avionics, and an enhanced main gearbox. The helicopter’s maximum takeoff weight has been increased to 11,160 kg (24603.5 pounds), Airbus says. The RNLAF currently operates H215M Cougars, and the H225M will expand operational capabilities for special operations, the company says. Airbus Helicopters and the RNLAF will collaborate on customization efforts to align the helicopters with mission requirements.
Gray Eagle STOL UAS makes first ship-to-land
General Atomics Aeronautical Systems, Inc. (GA-ASI) conducted a ship-to-land flight of its Gray Eagle Short Takeoff and Landing (STOL) uncrewed aerial system (UAS) from the South Korean navy’s amphibious landing ship Dokdo to Pohang Navy Airfield, marking a first for this aircraft type, the company announced in a statement.
The mission, conducted in collaboration with South Korea’s Hanwha Aerospace, was intended to demonstrate Gray Eagle STOL’s capability to operate from large-deck warships and land-based short or unimproved airstrips. Gray Eagle STOL is derived from the original Gray Eagle UAS, with modifications including a new engine, wings, control surfaces, and landing gear to enable short takeoff and landing operations.
Air Force ISR, special operations support contract won by Odyssey Systems
Odyssey Systems Consulting Group won a five-year, $531 million contract to provide advisory and assistance services to the U.S. Air Force’s Intelligence, Surveillance, Reconnaissance (ISR) and Special Operations Forces (SOF) Directorate, the company announced in a statement.
Under this contract, Odyssey will support the Program Executive Officer for ISR and SOF by augmenting engineering, technical, and research capabilities, along with acquisition, program, and financial management, the statement reads. The services will aid the development, testing, and deployment of systems within the ISR and SOF portfolio, which includes $22 billion in assets. Odyssey’s work will also support the Air Force Tactical Exploitation of National Capabilities (TENCAP), aimed at accelerating the integration of advanced technologies into operational platforms, according to the company. The effort will help deliver “critical ISR and SOF capabilities,” the statement adds.
Tech for navigating GPS-denied environments
By Dan Taylor
When Russia invaded Ukraine in 2022, GPS jamming quickly emerged as a major problem faced by combatants. Two years later, as jamming technology becomes increasingly sophisticated and widespread, the defense industry is responding with innovations and technology that don’t rely on satellite signals from space.
From camera-based navigation systems that use terrain recognition to artificial intelligence (AI) that fuses data from multiple sensors, new technologies are transforming how military forces navigate in contested environments. The stakes couldn’t be higher: In modern warfare, losing positioning capability means losing the ability to fight effectively.
LEO satellites: a piece of the puzzle
One area that has shown a lot of promise is low-Earth orbit (LEO) satellites. The number of LEO satellites has grown exponentially in recent years, which could provide a big benefit to the sensor-navigation industry. Position, navigation, and timing (PNT) technology that utilizes LEO satellites is in some situations better than GPS, with a more
powerful signal and in some cases more accurate.
However, some industry experts have a measured outlook about their role in military navigation.
“LEO satellites continue to be of interest, but they won’t be a silver bullet,” says Dana Goward, president of the Resilient
Navigation and Timing Foundation in Alexandria, Virginia, a nonprofit a nonprofit organization that promotes resilient navigation and timing worldwide.
He points out that geopolitical realities may limit their effectiveness. “With Russia, China, and perhaps others having the ability to jam or spoof signals from space, the added resilience from a LEO constellation might not satisfy many,” Goward notes.
But the technology itself shows promise. Frank Armstrong, senior product manager at Kymeta (Redmond, Washington), says that providers of LEO satellite constellations want to be able to provide GPS-like capabilities, either through broadcasting timing signals directly or by enabling ground stations to use the satellites as reference points for position tracking. (Figure 1.)
But it would be unwise to ignore the limitations of this tech, says Adam Moya, director of business development for aerospace and defense at Benchmark (Tempe, Arizona). “Its major drawback is that it is not a completely independent, noninterference, nonjammable source, which is driving the base need for GPS-denied solutions,” he explains.
This vulnerability to interference, combined with what Goward describes as a growing desire for “sovereign PNT capability” among nations, suggests that LEO satellites will likely be just one piece of a larger navigation puzzle rather than a complete solution.
The role of artificial intelligence AI and machine learning (ML) could prove to be powerful tools for navigation, particularly in their ability to process and interpret data from multiple sources when GPS signals aren’t available.
“AI’s largest contribution in this front is utilizing sensor fusion and access to alternative signals of opportunity to enhance or replace PNT information in a GPS-denied environment,” Moya says. He notes that researchers are also exploring how AI might “compensate for drift during these outages along with the sensor fusion algorithms.”
This ability to process complex data at the edge of the network is proving valuable for satellite communications companies as well. “AI and machine learning have helped us ... by enabling more complex algorithms at the edge to derive our position from signals of opportunity,” Kymeta’s Armstrong says. “This reduces our reliance on GPS or GNSS [Global Navigation Satellite System] information.”
2V to 10,000 VDC Outputs 1-300 Watt Modules
• MIL/COTS/Industrial Models
• Regulated/Isolated/Adjustable Programmable Standard Models
• New High Input Voltages to 900VDC
• AS9100D Facility/US Manufactured
• Military Upgrades and Custom Modules
• Ultra Miniature Designs
• MIL-PRF 27/MIL-PRF 21308
• DSCC Approved Manufacturing
• Audio/Pulse/Power/EMI Multiplex Models Available
• For Critical Applications/Pico Modules, Over 50 Years’ Experience
While the technology shows promise, it’s still maturing.
“We have seen some initiatives to use AI to interpret a variety of sensors, many of which one doesn’t usually think of in terms of navigation and timing, to determine position and aid navigation,” Goward says. “It still seems to be in the early stages, though as we haven’t seem a lot of application. That could change quickly, though.”
A variety of proposed solutions
This is a relatively new technological challenge, so not surprisingly there are a wide range of proposed solutions, each approaching the problem from a different angle –from image-based systems to hybrid satellite terminals and comprehensive engineering services.
Scientific Systems Co. Inc. (SSCI – Woburn, Massachusetts) has developed a camerabased solution called ImageNav, which has received about $45 million in funding and takes a completely different approach to the problem that doesn’t involve using LEO satellites or AI. Instead, the system uses onboard electro-optical (EO) or infrared (IR) digital cameras and fuses the outputs of three different algorithms: stereo terrain correlation, image-based feature matching, and feature-based velocity estimation, says Tom Frost, vice president at the company’s products division.
Kymeta’s Osprey u8 is a GEO [geosynchronous]-LEO terminal that aims to provide multiorbit capability for mission-critical operations while on the move. The system uses a range of receivers and location technology to ensure continuous operation. (Figure 2.)
Other new approaches in this area are also emerging. Location-software startup Zephr, for instance, tested a solution in Ukraine that networks ordinary cellphones together to detect and potentially locate GPS jammers, according to a recent Defense One report. The system exploits the various sensors already built into phones – such as automatic gain control, Doppler sensors, and carrier phase measurements – to create what company officials describe as one big, distributed antenna.
The U.K. Royal Navy, meanwhile, is going in an entirely different direction and has delved into quantum technology. Working with U.K. startup Aquark Technologies, the United Kingdom’s naval warfare branch is testing a quantum-positioning system that uses laser-cooled atoms to detect minute changes in motion. Unlike traditional
inertial navigation systems that become less precise over time, this quantum approach could potentially maintain accuracy without needing GPS updates, according to a Royal Navy release.
Regardless of the nature of the solution, power management in GPS-denied navigation presents varying obstacles. While some solutions require minimal power adjustments, others demand a lot of processing power to maintain effectiveness.
In the satellite communications sector, power consumption isn’t directly tied to antijamming capabilities. “GPS jamming is unrelated to power consumption in the satcom terminal technology space,” Armstrong notes, adding that the company’s Osprey u8 antenna “performs in a GPS- and GNSS-denied environment which has as one of the lowest SWaP [size, weight, and power profiles] in the industry in its class.”
However, alternative navigation solutions often require more substantial powermanagement considerations. “AltPNT [alternative position, navigation, and timing] solutions such as sensor fusion will require more processing power, which in turn drives a change in power management strategies,” says Benchmark’s Moya. “GPS/GNSS is overall a very-low-power sensor system, but the processing of their input is substantial as in a flightnavigation system.”
Some companies are taking different approaches to the power challenge. SSCI, for example, focuses on optical solutions to reduce power needs.
“We are seeing increased interest in our optical-based ImageNav solution that overcomes electronic jamming in contested environments by using on board cameras,” SSCI’s Frost says. The system “uses inertial navigation system information to match camera imagery, including electro-optical and infrared, against stored georegistered digital terrain elevation data to determine the precise location of a suitable air vehicle or weapon in flight.”
Integrating these new solutions into existing systems presents unique situations. “The challenge will be to adapt the AltPNT solutions to fit into the current systems without significant changes to their certification architecture,” Moya adds.
While the Sensor Open Systems Architecture, or SOSA, Technical Standard and open systems approaches have shown promise in many defense applications, their role in GPS-denied navigation solutions remains uncertain –although they undoubtedly will have an impact in the future.
“We are in favor of standardization,” Anderson asserts. “It drives down systemsdevelopment costs and allows greater interoperability across multiple networks. With the current pace of change it also enables easier upgrades and more flexible system configurations.” However, he does add that they are “not sure how SOSA and open systems architecture will affect GNSS capabilities.”
The potential impact of open standards may be more apparent at the moment in the commercial sector, a path that then often leads to developments in the defense industry.
“This has more of a play in commercial applications looking for a standardized and certifiable approach to AltPNT,” Moya says. The main problem is that while open standards could help develop common alternative navigation solutions, “this solution can be critical IP [intellectual property] in certain situations,” he says.
Any standardization effort would need to be driven by an industry consortium to resolve this issue, he adds. MES
Navigation in GPS-denied environments poses particular challenges for uncrewed systems, with size constraints often limiting the available solutions.
“It depends on the class of aircraft, but GPSdenied is particularly troublesome for smaller aircraft that do not already have terrestrial navigation systems or the payload capabilities to create an independent AltPNT [any source other than GNSS] system,” says Adam Moya, director of business development for aerospace and defense at Benchmark in Tempe, Arizona.
He notes that potential solutions include “a robust, high-integrity data link that could be used to provide external PNT information for the aircraft, and/or AI/ML [artificial intelligence/machine learning] algorithms utilizing
visual and IMU [inertial measurement unit] information within the aircraft.”
The current conflict in Ukraine highlights these vulnerabilities: “Uncrewed systems of all sizes are being affected by evolving jamming capabilities because many were designed to rely on GPS systems that aren’t available in contested environments like Ukraine,” says Tom Frost, vice president at the Scientific Systems Company Inc. (SSCI –Woburn, Massachusetts) products division.
“The difficulties posed by Russian jamming on the battlefield in Ukraine have forced the designers of uncrewed systems to look for solutions beyond celestial magnetic backup options.”
Some solutions are emerging, but many necessarily remain under wraps.
“Unmanned systems are becoming more important, especially in military planning and contingencies,” asserts Dana Goward, president of the Resilient Navigation and Timing Foundation in Alexandria, Virginia. “Yet reliable navigation still appears to be a hurdle. If the military has something, it is likely classified.”
The industry is working on options for uncrewed. Frank Armstrong, senior product manager at Kymeta in Redmond, Washington, notes that the company is “looking at ways to be a provider of some GNSS-type information to these systems from our products but can not elaborate at this time.”
SSCI’s Frost says that the company’s ImageNav system is designed for uncrewed aerial system (UAS) manufacturers looking for a low-cost option. (Sidebar Figure 1.)
Tech for navigating GPS-denied environments
By Mark Looney
Systems developers can use certain techniques to manage the gap between slow/asynchronous computing loops and high-performance data capture and processing in MEMS IMUs [micro-electromechanical system inertial measurement units] (MEMS IMUs >2000 Hz). Quick prototyping that provides time-relevant representation of MEM IMU responses will be an important step for defense-industry autonomous vehicle (AV) developers, who are seeking to manage both expansion of their mission profiles, along with the increasingly serious threats to their existing position, navigation, and timing (PNT) services.
In a recent editorial in GPS World, expert Dana Goward identified society’s overreliance on GPS-provided position, navigation, and timing (PNT) services1 . Faced with a complex set of threats to existing GPS/GNSS [global navigation satellite system] PNT services, many navigation-platform developers must quickly assess emerging technologies, which can help address vulnerabilities to their current PNT strategies. For those that are seeking to assess inertial sensing solutions for the first time, existing computing and I/O resources may limit data rates and synchronization functions, which might impede progress
towards proper, in-situ assessment of sensor capability.
Many autonomous vehicle (AV) developers and operators are facing several challenges that are forcing them to consider adding inertial sensors to their platforms for the first time. For those that are using MEMS inertial measurement units (IMUs) for the first time, establishing data coherence at sample rates that support best-available performance can be a major challenge. Even in early prototyping and preliminary field trials, sample rates and synchronization can make a difference, especially when systems developers are relying on preliminary results to assist their requirements-development process. Therefore, identifying and optimizing key operating attributes (of a MEMS IMU) is an important first step in the development process.
The MEMS IMU
MEMS IMUs typically include triaxial linear acceleration and triaxial angular rate (gyroscopes) sensing, along (and around) three mutually orthogonal axes. Figure 1 provides an illustration of the inertial reference frame, along with each sensor polarity and axis assignments.
Autonomous ground vehicle use case
Figure 2 illustrates a simplified flow chart for the main processing loop of an autonomous ground vehicle (AGV) that uses video, wheel-based odometry, and
GPS for inertial navigation and tracking. The dotted lines also illustrate adding an operation to read the six inertial sensors from the ADIS16576 MEMS IMU into this loop.
For purposes of illustration, the main loop will acquire data from the video and wheel-based odometers at the main loop rate of 50 Hz, while it will update GPS/PNT data at a rate of 10 Hz. The first generation of this AGV provided basic supply-delivery service between buildings at an airbase; in the next generation, the AGV operators must start evaluating additional sensors for managing partial GPS outages (such as only two GPS satellites available) and need to upgrade to guidance navigation control (GNC) to double the velocity over complex, off-road terrains.
The first challenge to address is that the example IMU per-forms best when operating at or near its natural sample rate of 4000 Hz, which is 80 times faster
than the present AGV processing loop. Increasing the processing loop of the GNC system will require major changes, a move that is impractical for the first prototypes and preliminary field trials. What can be done to ensure that the preliminary field trials have the best chance to evaluate the merit of the IMU in this particular use case? The answer lies in optimizing a combination of the following operational attributes: data reduction, time coherence, synchronization, and buffering.
Reducing the data rate can be as simple as acquiring data at a slower rate. However, this approach can undersample the signals, which can introduce errors, especially under conditions at which AGV platforms are most reliant on the MEMS IMU for feedback sensing: that is, highly dynamic motion and environmental profiles. MEMS IMU core sensors (accelerometers, gyroscopes) and signal chains often have bandwidths that are wider than most other AGV sensing platforms. For example, the cutoff frequency is greater than 500 Hz in both linear and angular rate sensors on the ADIS16576. Therefore, reducing the bandwidth needs to be part of any strategy for reducing the data rates in the inertial signals.
One convenient method for managing this vulnerability is through use of digital filtering in the MEM IMU’s signal chain. For example, when adapting the ADIS16576 to the system in Figure 2, setting its Bartlett FIR [finite impulse response] filter to 64 taps per stage will reduce the cutoff frequency to approximately 20 Hz. Setting its decimation filter to average 80 sequential samples for each data update will reduce its output data rate (ODR) to 50 Hz. When employing these filters, the user must make sure that the data widths will support the resultant bit growth. In the case of the ADIS16576, this will require reading 32-bit data widths, through two separate 16-bit registers,
for each inertial sensor. When using a burst-read command with a serial clock of 8 MHz, the communication sequence will require less than 40 μs.
After optimizing the data rates and associated bandwidth, the next opportunity for optimization comes from establishing time coherence between the IMU data sampling and a system clock reference. For purposes of illustration, let’s define the video sync (50 Hz) as the system reference. When operating in its factorydefault configuration, the example IMU will use an internal clock reference, which inevitably will have some mismatch with the video sync. When the IMU’s ODR is lower than the video sync, the consequence will be reading “stale data” on occasion. When the IMU’s ODR is faster than the video sync, the consequence will be missed samples. The frequency of this occurrence will depend on the scale of the mismatch between each clock. Another limitation will be that the
latency of the IMU data will vary by an entire sample cycle (20 ms = 1/50 Hz).
There are two different methods for establishing stronger time coherence. The first method is to use the IMU’s data-ready signal to trigger IMU data collection. Figure 3 is a flow chart that checks for IMU data after two different operations. This approach will eliminate the problem of missing data samples, to establish a time-coherent flow of IMU data, at the main loop rate of 50 Hz. This concept can also expand to check for “new data” in the IMU in-between the GNC processing and video read as well.
Another method for establishing time coherence and precise latency is to use external synchronization features on the MEMS IMU. The ADIS16576 offers two primary options: direct and scaled. Using the scaled sync mode will be the most appropriate mode for the flow chart in Figure 2. Since the system clock is operating at 50 Hz and the ADIS16576 performs best at 4000Hz, the clock scale should be set to a factor of 80. When used in conjunction with the on-board filtering, the outcome will still be a bandwidth of 20 Hz and an ODR, but with a fixed latency, with respect to the system clock reference (video sync).
In cases where AGV architects are evaluating a MEMS IMU for mission profiles that must push for “best-available” response times, they may need to sample rates that are beyond their current loop rates, as soon as practical in their prototyping. Data buffering provides a useful technique in this scenario and can provide flexibility to system processors to read IMU data at different times during their main processing loop. This approach may require the use of a colocated processor or use of an IMU that provides a first-in/first-out (FIFO) buffer function, if the IMU does not include a FIFO function.
Using the same example from Figure 2, while disabling all on-board filtering in the ADIS16576, the on-board FIFO will collect 80 samples during one cycle of the main loop. Since the on-board filters are not in operation, best-available performance is available in the 16-bit data
Inertial States
Inertial Commands
Navigation Control (GNC)
widths. Therefore, the AGV processor can acquire all 80 samples, for all six inertial samples, in less than 4 ms, when using a serial clock of 8 MHz and a stall time of 6 μs, between each 16-bit communication segment.
Getting the most out of a MEMS IMU may drive substantial architectural change. Prior to making large investments in such upgrades, optimizing available digital features can help AGV developers evaluate their use cases and eventually, develop credible requirements for meeting their most important operational objectives. Quick prototyping that provides time-relevant representation of MEMS IMU responses will be an important step for autonomous vehicle developers who are seeking to manage both expansion of their mission profiles and need to counter the increasingly serious threats to existing PNT services. MES
Note
1 Goward, Dana, “U.S. Dangerously Behind, PNT Leadership Needed,” GPS World, July 2024. https://www.gpsworld.com/us-dangerously-behind-pnt-leadership-needed
Mark Looney joined Analog Devices, Inc. (ADI) in 1998 and is currently the Application Engineering Manager for the Inertial Sensing Technology Group. He earned BS and MS degrees in electrical engineering from the University of Nevada. Since joining the industry in 1995, Mark has worked in development, characterization and system-level integration of inertial sensing, high-speed analog-to-digital conversion, clock management, power management, and embedded processing technologies. Prior to joining ADI, Mark was a design engineer for Interpoint Corp. and was a founding member of IMATS, a vehicle fleet and traffic solutions start-up company.
Analog Devices, Inc. (ADI) https://www.analog.com
By Dr. Brett Walkenhorst
Military and government facilities that store or handle classified information must comply with new security requirements aimed at detecting unauthorized electronic devices. Following a June 2023 directive from Secretary of Defense Lloyd Austin, all SCIFs [sensitive compartmented information facilities] and SAPFs [special access program facilities] were instructed to program for electronic device detection and mitigation systems by September 30, 2024.
The growing insider threat
This mandate is part of a larger effort by the U.S. Department of Defense (DoD) to centralize its approach to combating insider threats, a priority heightened after the 2023 arrest and 2024 sentencing of Jack Teixera, a Massachusetts Air National Guard member. Teixeira’s unauthorized sharing of classified military documents regarding Russia and other sensitive issues underscored the potential damage posed by insiders with access to classified information. Following the breach and arrest, a DoD security review revealed the need for more stringent protections against electronic device threats.
Secretary of Defense Austin’s memo emphasizes a comprehensive strategy to secure and audit all access to classified spaces and data. This approach involves a complete inventory of locations where classified work is conducted, strict access controls to ensure thorough audit trails, and detailed control over data on
Attackers now have greater capabilities to exploit these devices, even without the owner’s knowledge. Many devices contain vulnerabilities that enable them to be compromised without the owner’s knowledge. Consequently, even well-intentioned employees with authorized access to classified information can unknowingly record conversations, extract sensitive data, or serve as entry points for malware, all with potentially devastating consequences for national security.
Wireless attacks encompass a variety of techniques, including rogue cell towers, smartphone spyware, physical malware injection, “Evil Twin” or fraudulent Wi-Fi access point attacks, password spraying, denial-of-service (DoS) attacks, session hijacking, man-in-the-middle (MitM) attacks, keystroke injection, credential sniffing/cracking, jamming, and many more. Each of these attacks poses a risk to device integrity and can alter device functionality with some methods potentially introducing malware, transforming the target into a covert surveillance tool for attackers.
All kinds of low-cost COTS [commercial off-the-shelf] devices are readily available and can be used for wireless attacks or to exploit wireless protocols for command, control, and data exfiltration. Examples include Wi-Fi Pineapple, O.MG Cable, USB Ninja, Flipper Zero, and Deauth hacking watch. Other inexpensive devices like narrowband software-defined radios, Wi-Fi dongles, and Bluetooth dongles can also be adapted for various wireless-attack methods.
To address this, SCIFs and SAPFs must implement wireless intrusion detection systems (WIDSs) that continuously monitor for unauthorized devices and suspicious wireless activity. WIDS solutions help organizations detect and prevent data leaks by identifying and locating rogue devices before they can leak or compromise classified information.
Current industry solutions offer a comprehensive and effective wireless detection and localization solution that uses passive (zero transmissions) radio frequency (RF) sensors to provide comprehensive monitoring of secure facilities. Unlike traditional lobby-based detection systems, which are prone to false alarms and often miss critical threats, the most innovative systems provide continuous and robust detection and localization with decoders for multiple protocols, leading to high detection confidence. When decoding a packet, there is no doubt that a wireless device sent it; such systems enable accurate identification of unauthorized devices, whitelisting of approved devices, and zero false alarms for device detection.
The risks of electronic devices in classified areas
Personal electronic devices (PEDs) are ubiquitous and pose increasing risks in high-security environments. Devices capable of emitting signals – such as smartphones, tablets, laptops, and even wearables like smartwatches – can be used for espionage, cyberattacks, or data theft. The widespread availability and low cost of these devices, coupled with easily accessible tools and code repositories for wireless hacking, make them an attractive vector for malicious actors.
Dr. Brett Walkenhorst is the Chief Technology Officer of Bastille. Bastille • https://bastille.net/ on-network devices. Additionally, the memo highlights detection and monitoring of off-network devices that could pose a risk to classified information. Together, these measures aim to establish a centralized framework to address insider threats throughout the DoD.
The central focus of the defense secretary’s memo is the DoD’s comprehensive approach to tackling the issue. The goal seems to be creating a joint capability by integrating systems which would allow the DoD better oversight with coordinated analysis of both on- and off-network activities. For detecting off-network electronic devices (such as through wireless intrusion detection), these capabilities are largely new and will require prioritization, funding, planning, design, deployment, and implementation over time. The DoD has made significant progress in supporting the memo’s directives, addressing the issue based on both risk severity and available resources.
By meeting the SECDEF memo’s requirements, military and federal facilities can ensure they are equipped to handle the evolving landscape of wireless threats, protecting both classified information and national security. MES
By Rob Mather
Personnel on the battlefield need to get real-time information – that’s not negotiable. Whether in the air, on land or water, or now even in space, devices and data streams must be able to provide the exchange of complex data in real time to keep combat zones constantly connected. The simple exchange of real-time data is only the beginning – the real work is what defense organizations do with this data. Turning this data into insights is critical for mission success.
Being connected on the military frontline is vital. Its importance has been recognized through milestone legislation such as the Goldwater-Nichols Department of Defense Reorganization Act1 in 1985, which shifted the focus on military connectivity. Spearheaded by a need for better interservice cooperation, the act
directed plans for intelligence sharing and operational coordination during joint military operations.
Today, military connectivity is very much a reality. State-of-the-art technology on the front line has transformed information and data exchanges in warfare. Whether it’s to monitor equipment condition or soldier health, an interconnected web of devices and data streams is making this information available in real time. Known as force connectivity, it’s the latest technological revolution for the battlefield.
Legislation first, now technology drives connectivity
Fast-forward to now and, rather than regulatory-driven change, we’re moving into an era of technology-driven connectivity. We’re seeing an explosion of asset connectivity that is starting to build a truly connected battlefield on the ground, in the air, at sea, and in space too.
There are five key developments powering the connected battlefield now and into the future:
1. Wearables and biometrics keep a check on every single soldier
A revolutionary and growing area of connectivity on the battlefield is the ability to monitor the health of troops on the field. In most modern fighting forces, almost every soldier now has biometric monitoring devices which use sensors to track
heart rate, body temperature, blood-oxygen levels, and stress levels so commanders can make decisions based on this human data. NATO2, for example, is currently supporting the development of new wearable technology that is “designed to minimize casualties during combat operations. It involves soldiers wearing various body sensors that will help medics collect vital data and determine the extent to which a soldier may be injured more accurately than a field medic would be able to conclude.” Add to this communication transmitter-receivers, GPS devices, night-vision aids, and other comms devices – and there is a huge proliferation of tactical-level data available.
Whether it’s to monitor equipment condition or soldier health, an interconnected web of devices and data streams is making this information available in real time.
Known as force connectivity, it’s the latest technological revolution for the battlefield.
2. Deeper insights with IoMT
The internet of military things (IoMT) is the growing militarization of IoT – whereby IoT-enabled sensors and devices provide a network of data that enables a deeper level of insight into a fighting force than ever before.
IoMT presents widespread opportunities, including enhanced efficiency, real-time decision-making, and improved situational awareness. The Australian Army has published a paper3 looking at IoMT describing it having “much scope for the development of additional capabilities in the future through the integration of sensors, robots, munitions, wearable devices, vehicles, and weapons.”
Successful IoMT deployments take command, control, communications, computers, intelligence, surveillance, and reconnaissance (C4ISR) processes to a higher level by exploiting large volumes of collected data for optimized decision-making. The ability to connect scattered systems and networks with IoMT data feeds into a large integrated network will be a key component in the move to a more-connected battlefield.
3. Welcome to space! The battlefield has changed
The dimensions of the battlefield itself are also changing. What used to be air, land, sea, and time has now become, air, land, sea, and space. It could even be argued this is now air, land, sea, space, plus cyberspace.
While not militarized, advances in communications satellites have become extremely beneficial in recent conflicts – even using technology from the civilian side. For example, when SpaceX Starlink satellites were moved over Ukraine, that showed a flexibility and an adaptability of an infrastructure to quickly move to support an emerging conflict.
Data reach broadens here too. According to a Deloitte study4, the amount of data being sent to and from space will likely grow to more than 500 exabytes of information from 2020 to 2030 (a 14-time increase). On top of this, 98% percent of senior executives surveyed said that demand for space data is increasing as it has broader use and significance across end markets.
4. The power of smart assets to facilitate two-way communication
There is no longer just a one-way flow of info out to the asset from command. Many smart assets are now collecting data and engaging in two-way communication with other assets, and that two-way communication turns them into stakeholders.
A single U.S. Air Force uncrewed aerial system (UAS), as per Deloitte, can generate 70 terabytes of data within an operational span of 14 hours. Multiply that by 1,000 in a drone-swarm scenario and you can start to see the challenge facing commanders today in collecting the vast amounts of data available and distilling that data into actionable insights.
Or consider a scenario where the asset itself, combined with predictive-maintenance solutions, can tell the operator before the machine breaks down that a part is going to fail and alerts the operator, possibly even self-triggering a repair workflow by picking parts and scheduling a technician.
However, getting a total view of asset readiness from this vast dataset can be challenging – and can further complicated by the involvement of defense contractors who may be responsible for performance-based logistics (PBL) agreements to keep assets mission-ready.
5. Assured command-level insights with a data lake
So, we have IoMT plus the asset operators – now add the munitions themselves such as drone swarms and data feeds from space, and now we’re talking about a very sophisticated connected battlefield. Common to all these connected-battlefield advances is the proliferation of data. Militaries must be able to turn this vast pool of data into critical insights that can influence mission success.
But if these developments operate in a decentralized manner, defense forces are not getting the immense value of the real-time aggregation of terabytes and terabytes of data every second in a wartime scenario. All of this data must be received, reviewed,
and sorted for the end user so that they can glean insights and make decisions quickly. This is where a data lake for asset management can provide commandlevel insights on all assets.
The fighting force needs a framework overarching all of this to tie data together in that one single solution with the ability to collect, analyze, and redistribute all of that data to the correct audience in a useful format. Combining forecasting and predictability with a presentation layer drives total asset readiness on a whole new level, giving commanders a clear real-time view of the assets at their disposal, in the context of the mission they need to complete. Mission success will hinge on connectivity infrastructure.
War zones are increasingly becoming more connected, and harnessing the power of the data deluge will be the secret weapon in driving tactical and strategic success on the battlefield. An all-encompassing asset-management solution can allow defense organizations to manage assets and power a comprehensive logistics network. MES
Notes
1 https://www.congress.gov/bill/99thcongress/house-bill/3622
2 https://www.natomultimedia.tv/app/ asset/686707
3 https://cove.army.gov.au/article/internetmilitary-things
4 https://www2.deloitte.com/us/en/insights/ industry/aerospace-defense/future-ofspace-economy.html
• Large range of Ethernet Switches
• 1U enclosure, 3U & 6U VPX
• Managed Layer 2+/3 switches
• 1/10/25/40/100 Gigabit Ethernet
• Aligned with the SOSA™ Technical Standard
• Air-cooled, conduction-cooled, AFT grades
Rob Mather is Vice President, Aerospace and Defense Industries at IFS. He is responsible for leading the IFS global A&D industry marketing strategy and for supporting product development, sales, and partner ecosystem growth. Rob has over 15 years of experience in the A&D sector, starting out in the field and having held a number of strategic R&D, presales, and consulting positions at IFS, Mxi Technologies, and Fugro Aviation.
IFS • https://www.ifs.com/
FIRST UNIVERSAL POWER SUPPLY FOR ALL ARMY CMFF APPLICATIONS
Introducing the VPXtra® 400DW-IQI, Behlman’s first power supply with a wide range DC input that is fully compliant for all platforms in the Army CMFF program. This rugged, highly reliable switch mode 3U VPX unit meets a new standard of adaptability, and is backed by unmatched integration support from the Behlman team.
> Developed in alignment with the SOSA™ Technical Standard and VITA 62.0
> Delivers over 400 watts of DC power via two outputs
> 90% typical efficiency
> Features cutting-edge Tier 3 software
> System management integration via VITA 46.11 compatible IPMC
By Gary Dannar
The modern military’s power needs are growing more complex with each passing year. The rapidly changing dynamics of warfare, driven by technological advancements and evolving operational strategies, are reshaping how power is used, distributed, and sustained on the battlefield. This shift, coupled with federal mandates to reduce reliance on fossil fuels, is placing increased pressure on military leaders to rethink energy and power systems. The challenge is no longer just about generating power; it’s about how to deliver it efficiently, flexibly, and rapidly to dispersed units in the field.
Today’s battlefield requires power for an abundance of new technology and equipment, and this shift will require a combination of grid power, fuel-based generators, and battery-electric energy. We’re not just talking about radios or computers anymore; today’s battlefields involve electric vehicles, drones, broadband connectivity, and even electric vertical takeoff and landing (eVTOL) aircraft, all of which need power, and lots of it. Throw EV [electric vehicle] mandates for nontactical vehicles into the mix and the challenge becomes even more complex, driving greater need for electricity and battery storage to support both installation and operational energy.
Dispersed battlefields require flexible power
As the battlefield continues to evolve, the lines between installation and operational environments are blurring. The modern battlefield is becoming more lethal, and survivability depends on units operating in a more decentralized
manner to avoid detection. While dispersing units and equipment across vast areas can improve operational effectiveness, it creates challenges to the supply chain and causes a new problem: How do you get a reliable supply of energy, in the right form, to these units to keep them functioning?
Imagine a scenario where an electric drone or surveillance system needs to be recharged miles from a forwardoperating base but the installation and fueling to prop up a new microgrid is strategically disadvantageous, either by taking too long to deploy or drawing too much attention to the area. What is the best solution? How will units deploy, operate, reach, recharge, and safeguard electric power assets in the field?
In this new operational landscape, speed, resiliency, and agility will be key. When military units become more mobile and operations more dispersed, energy sys tems must be able to keep up. The advan tage of tactical microgrids is of interest to the military and will require complimen tary technologies that can both support these grids and move power from them to other assets in the field.
That’s where mobile energy is both the problem and the solution. Developing mobile power sources that can move seamlessly with units as they deploy, operate, and reposition is the kind of energy flexibility that will be critical in modern warfare, where all technological advantages can be utilized, and the ability to adapt quickly to changing conditions can be the difference between mission success and failure.
The future of military power is mobile
Knowing all of this, military personnel must consider the following when evaluating mobile energy solutions:
1. Assess mobility and agility needs. Power systems must be quick and easy to deploy, relocate, and adapt to changing battlefield conditions, with rapid setup and takedown capabilities.
2. Evaluate power capacity and compatibility. Solutions should handle diverse needs, from AC power for infrastructure to DC fast charging for EVs and aircraft, with flexibility for various voltages and seamless integration with microgrids.
3. Provide resilience and redundancy. Mobile power must offer reliability under rugged conditions, with battery storage and bidirectional power capabilities that support both backup and primary distribution roles. Look for solutions
As the military looks to the future, energy resilience will be a critical focus. The ability to generate, store, and distribute power across dispersed and mobile units will be crucial to maintaining tactical superiority. The integration of battery-electric solutions, tactical microgrids, and mobile power systems will play a vital role in ensuring that the military’s energy infrastructure is as agile and adaptable as its operational strategies.
can count on Elma to deliver reliable, rugged solutions wherever the mission takes you. We accelerate development and mitigate risk with platforms based open standards such as SOSA™ and OpenVPX. Talk to us about your next project.
with redundant features and robust energy storage to maintain functionality in the face of grid outages, cyberthreats, or physical disruptions.
The future of military power is decentralized, flexible, and increasingly reliant on battery-based technologies that can move as fast as the forces they support.
Bridging the gap between installation and operational energy
Mobile power is definitely on the rise for battlefield use: Large tactical rechargers, hybrid power-generation vehicles, thermophotovoltaic turbines, mobile nuclear power plants, and fuel cells are in use with more under development. One example is the electric Mobile Power Station (MPS) by DANNAR: The MPS is designed to meet the military’s evolving power needs by offering a modular, mobile, and scalable energy solution that is capable of receiving and distributing power. It is being
tested to seamlessly hook into a tactical microgrid to recharge or deliver power and then transport that power to where it’s needed most, supporting a wide range of applications in the field.
While dispersing units and equipment across vast areas can improve operational effectiveness, it creates challenges to the supply chain and causes a new problem: How do you get a reliable supply of energy, in the right form, to these units to keep them functioning?
The MPS can deliver bidirectional power at both military and industrial levels, from 480 three-phase to DC fast charging for electric vehicles, drones, and eVTOL aircraft, and 208 V in development and testing. For installations, the MPS can serve as a reliable backup power source for command centers, field hospitals, or maintenance bays. In the field, it is also a mobile charger capable of recharging vehicles, drones and other electric equipment wherever it is deployed. (Figure 1.)
Additionally, the MPS participated in a U.S. Department of Defense (DoD) Defense Innovation Unit (DIU) test under which DANNAR deployed multiphase units supporting eVTOL operations at two sites held by the Air Force and vehicle-to-grid/vehicle-to-vehicle resilience evaluation efforts at three more sites operated by the Navy and Marine Corps. eVTOL charging has also been tested by experts at AFWERX where the MPS, carrying a half-megawatt of stored energy, both recharged electric aircraft and also powered ground
control computers plus various other power tasks. (Figure 2.)
The challenge for military decisionmakers is to ensure that any energy supply not only meets current needs but is also scalable for future requirements. By integrating versatile, mobile power solutions, the military can ensure that it has the energy resilience needed to operate effectively in any environment. MES
Gary Dannar is the founder and CEO of DANNAR, which focuses on providing heavy-duty work capabilities with gridscale auxiliary power. In addition to his years at Ford Motor Company and New Holland, where he drove sales and business development for heavy equipment, he also led product development for The General and the Alamo Group. He also started and acquired businesses including Little Roadside Management and the Kitselman Pure Energy Park.
DANNAR
https://www.dannar.us.com/
Open standards for embedded systems: FACE, SOSA, CMOSS, VPX, and more
By Richard Jaenicke
More complex combat-helicopter engines require large increases in diagnostic/prognostic capability, which also require a greater number of sensor inputs to the electronic engine controls (EECs.) At the same time, military helicopters face the increased need for resilient cybersecurity. Together, these trends drive the need for multicore processors in the EECs, despite the challenge of ensuring real-time determinism when different processor cores compete for the same shared resources. The foundation for a solution to both challenges is a certified, hardened real-time operating system (RTOS) with multicore interference mitigation. Multicore interference mitigation enforces real-time determinism even when multiple processor cores are vying for access to the same processor resources.
Although fully autonomous aircraft are not likely to get certified for several years, some aircraft systems already operate autonomously. One such system is the full authority
digital engine control (FADEC) found in many airplanes and some helicopters.
FADECs – which have complete autonomous control of the engine without pilot backup – have redundant control channels to provide full flight capability in the event of a failure in one of the channels.
A FADEC is a type of electronic engine control (EEC), and all modern aircraft use some type of EEC to increase engine
performance, efficiency, reliability, and safety while reducing maintenance costs. EECs automatically adjust engine output to compensate for engine temperature, air temperature, altitude, and other sensor inputs as part of normal operations. EECs manage the startup phase to get to a stable idle and continue through the entire operating envelope from idle to full throttle. EECs also automatically keep the engine within safe operating limits for speed and temperature while detecting any failures in the engine. (Figure 1.)
In an airplane, the EEC combines the pilot’s power level position with the environmental sensor readings to calculate the engine operating parameters, such as fuel flow and stator vane position required to achieve the thrust indicated by the pilot. Every power setting at any altitude results in optimum engine performance and maximum fuel efficiency.
In a helicopter, thrust is not provided directly by increasing engine power but by changing the angle of the rotor blades. The power of the turboshaft engine still needs to be adjusted to achieve the goal of a nearly constant rotor RPM, which maximizes stability and control. Achieving constant rotor RPM requires adjusting the engine output based on air pressure and temperature as well as the pitch angle of the rotor blades, which changes the drag. Although those adjustments can be done manually to varying degrees of success, manual control is usually reserved for emergency operations. Under normal operation, those adjustments are made automatically by an EEC.
EECs continuously analyze data inputs from sensors and send commands to effectors, such as fuel meters, to control engine performance while keeping the engine within safe and efficient operating parameters. On a helicopter, the sensors typically include:
› ambient air temperature
› air pressure
› power turbine inlet air temperature
› torque
› rotational speed of the turboshaft inside the combustion chamber
The main output is the command for the fuel-metering system to adjust the fuel flow and thus the engine output. Additional advanced outputs can include variable bleed control, which prevents turbine blade stall at low speeds; and active clearance control for the turbine blades to prevent gas leakage as thermal and mechanical loads change the clearance between the blade tips and the surrounding casing.
EECs provide simplified, hands-off engine starting, much like an electronic ignition in an automobile. The full progression can include automatic engine starting, sequencing ignition, start fuel, and stabilized engine operation at idle.
The controls monitor key engine-operating parameters to automatically keep the engine within safe operating limits for speed and temperature and also detect any failures in the engine. EECs also run built-in tests on themselves to detect internal errors. In each case, the EEC is designed to mitigate such failures through backup functions or by reverting to a safe operating state.
Although early EECs were implemented with analog circuitry to process the inputs and outputs, current EECs use a microprocessor to program the control functions in software digitally. A digital EEC enables much more complex algorithms that achieve higher engine efficiency and performance. A digital EEC includes digital memory that can store not only the engine operating parameters but also engine measurements and any fault logs generated during operation. Such data is essential for prognostics and maintenance activities.
Digital EECs typically utilize a safety-critical real-time operating system (RTOS) to provide the high-assurance software infrastructure to host the various engine control, monitoring, and built-in test applications. For example, the INTEGRITY178 safety-critical RTOS from Green Hills Software has been deployed in EECs since 2003.
Many of the latest EECs are full authority digital engine controls (FADECs), which have complete control of the engine without pilot backup. Although some people and companies use the term “FADEC” interchangeably with “EEC,” “DEC” [digital engine control], and “ECU” [electronic control unit], a true FADEC has no provision for reversion to manual pilot control. FADECs include redundant control channels, a primary and a backup, so that if one channel fails, the other can take over.
Open standards for embedded systems: FACE, SOSA, CMOSS, VPX, and more
The best way to look at a FADEC is at the system level: A FADEC system includes not only the digital EEC for each engine but also all the sensors, effectors, and indicators required for autonomous engine control.
FADEC systems have many advantages. At a high level, they are autonomous and self-monitoring, thereby reducing the pilot’s workload. FADECs also increase safety and reliability through redundancy.
AirBorn’s new VPX Power Module is a VITA 62, Open VPX compliant, 6U system with models for a 270 VDC input IAW MIL-STD-704. Power Blade is a SOSA aligned, conduction cooled, switch mode unit built for highend defense applications.
• Auxiliary DC Output: +3.3V/60A
• Efficiency of >94% Typical above 50% Load
• Input-Output Isolation 2100VDC
• Main DC Output: +12V/180A
• Overvoltage, Overload, & Overtemperature Protection
• Programmable Regulated Current Limit
• VITA 46.11 System Management
Other advantages of FADECs for helicopter engines can include:
› Load sharing between the two engines on a twin-engine aircraft
› Transient load anticipation (using rotor speed and collective pitch rates)
› Transient torque smoothing (using power turbine rates)
› Contingency power capability to meet aircraft demands
› Surge avoidance
› Automatic switch-over to an independent backup control system
› Control system self-test, selfdiagnosis, and fault identification
› Accurate torque matching
Even though an engine is certificated as part of the airplane or rotorcraft, a commercial engine and its controls (EEC or FADEC) first must receive its own Type certificate under Part 33. Advisory circular AC 33.28-3 “Guidance Material For 14 CFR §33.28, Engine Control Systems” states that “Design, implementation, and verification of software as specified in Level A (DO-178C) is normally needed for turbine engines.” Additionally, any helicopter FADEC needs to be at DAL A because its failure would result in the loss of ability to maintain flight.
Even when the EEC software has been designed to RTCA/DO-178B DAL A, the use of a partitioning operation system permits partitions that perform noncritical functions to be developed to lower levels, thereby reducing life cycle costs.
The heart of the FADEC system on the CH-47D/F Chinook tandem-rotor
helicopter consists of an electronic control unit (ECU) and a hydro-mechanical unit (HMU) for each of the two Honeywell T55-714A turboshaft engines1. Both the ECU and HMU are manufactured by Triumph Group (Triumph), and the ECU runs the INTEGRITY-178 RTOS from Green Hills Software.
The ECU for the CH-47D/F is the Triumph EMC-100 dual-channel engine control unit, which consists of two dissimilar, mechanically separated channels operating independently but cooperating with each other. The primary channel provides precise engine power management and rotor speed control throughout the engine’s operational range. The second channel provides full mission capability should a failure occur in the primary channel.
The EMC-100 software is organized in a multipartition architecture, with application-specific control system software running in isolated partitions on the RTOS. The ECU software has been designed to
RTCA/DO-178B DAL A, but the software architecture permits partitions that perform noncritical functions to be developed to lower levels, thereby reducing life cycle costs.
The HMU meters the engine fuel flow as commanded by the ECU in both primary and reversionary mode operation. Additional functions provided by the HMU include electrical power generation, compressor air bleed management, and positive engine shutoff.
The FADEC system includes several additional components to provide information and control, including the master caution/advisory panel, engine-condition levers, increase/decrease RPM switches, thrust control position transducer, and the FADEC control panel. (Figure 2.)
Triumph ECUs are deployed in a wide variety of U.S. military helicopters, including the AH-64D Apache, CH-47D/F and MH-47D/F/G Chinook, UH-60L/M/V Black Hawk, HH-60 Pave Hawk, MH-60 Jayhawk, and SH-60 Sea Hawk. Triumph ECUs are also deployed internationally in commercial Airbus helicopters, including the H130, H135, H160, and H225.
As engine manufacturers strive for lower thrust-specific fuel consumption, lower weight, and higher reliability, EECs will necessarily become more intricate. More complex engines require significant increases in diagnostic/prognostic capability, which will also require a greater number of sensor inputs to the EECs. Together, these trends drive the need for multicore processors in the EECs, despite the challenge of ensuring real-time determinism when different processor cores compete for the same shared resources.
Another trend is the increased need for resilient cybersecurity. As aircraft and their engines share increasing volumes of data over higher bandwidth communications, the opportunity for cyberattacks increases considerably. In addition to being susceptible to interference from high-bandwidth communications such as cellular networks and satellite communications, aircraft systems are also vulnerable from a variety of other sources, such as field-loadable software, maintenance laptops, and wireless aircraft sensor networks. Once any of the subsystems is breached, an attacker can move laterally to other parts of the aircraft, including flight-critical systems.
The foundation for a solution to both challenges is a hardened RTOS with multicore interference mitigation, which enforces real-time determinism even when multiple processor cores are vying for access to the same processor resources. The bandwidth allocation and monitoring (BAM) functionality in the INTEGRITY-178 tuMP RTOS enables a software architect to reserve a specific amount of bandwidth for each processor core to access shared resources. This provides a quality of service that mitigates bandwidth hogs, whether due to application design, unfair hardware arbitration schemes, or malware.
BAM enables system integrators to meet both DO-178C airworthiness objectives and AC 20-193 multicore objectives to DAL A. This RTOS also provides cybersecurity assurance, as it meets both ISO/IEC 15408 Common Criteria to evaluation assurance level (EAL) 6+ and the NSA-defined Separation Kernel Protection Profile (SKPP) to “high robustness.” High robustness provides resilience to attacks from highly motivated and well-funded actors such as hostile nation-states and national laboratories. MES
Note
1 “CH-47D POWER PLANT (714) Student Handout,” U.S. Army Warfighting Center, Fort Rucker, Alabama, Oct. 2006. www.chinookhelicopter.com/standards/Army_D_Model_ AQC_Classes/Engine_714.pdf
Richard Jaenicke is the director of marketing for safetyand security-critical products at Green Hills Software and has over 25 years of experience working with embedded software and systems. Prior to joining Green Hills, he worked at Mercury Systems, where he was responsible for marketing avionics software/hardware and signal-processing systems. Rich holds an MS in computer systems engineering from Rensselaer Polytechnic Institute and a BA in computer science from Dartmouth College.
Green Hills Software https://www.ghs.com/
TECHNOLOGY, TRENDS, AND
Military Embedded Systems focuses on embedded electronics – hardware and software – for military applications through technical coverage of all parts of the design process. The website, Resource Guide, e-mags, newsletters, podcasts, webcasts, and print editions provide insight on embedded tools and strategies including technology insertion, obsolescence management, standards adoption, and many other military-specific technical subjects.
Coverage areas include the latest innovative products, technology, and market trends driving military embedded applications such as radar, electronic warfare, unmanned systems, cybersecurity, AI and machine learning, avionics, and more. Each issue is full of the information readers need to stay connected to the pulse of embedded technology in the military and aerospace industries.
Open standards for embedded systems: FACE, SOSA, CMOSS, VPX, and more
By Matthew Tarney
Advanced computing is revolutionizing defense platforms across all domains. Modern C5ISR [command, control, communications, computers, cyber, intelligence, surveillance, and reconnaissance] and the tactical advantages it brings to the battlespace would not exist without the rapid advancement of compute hardware. However, the ability to deploy this hardware in rugged and extreme edge environments depends heavily on the effectiveness and reliability of cooling systems. Preferred methods of cooling like conduction and forced air are often insufficient to meet the thermal needs of these high-performance computers. Systems designers should be aware of both the advantages and challenges associated with next generation cooling such as air flow-through and liquid flow-through. While each adds some additional complexity and risk to the system they are cooling, they bring enormous advantages in terms of cooling performance. Without implementing these higher-capacity cooling mechanisms, systems in the near future will not be able to take advantage of the latest processing hardware for critical edge applications.
It is hard to overstate the rapid pace at which processing technology has changed in the past five years. Breakthroughs in machine learning and artificial intelligence (AI and ML), coupled with the development and scaling of advanced compute hardware like graphics processing units (GPUs), have transformed computing across almost every industry. While the broad adoption of GPUs enables rapid technological advancements, it also creates significant new demands and challenges. One of the largest obstacles to overcome is managing the power consumption of highperformance chipsets and the resulting heat generated by the processors.
Power consumption of GPUs has increased dramatically since the primary use case
1 | A thermal-analysis image demonstrates how heat builds up at the processor location; it also shows the importance of ensuring the PCB has the right thermal-management tools to protect the processor from overheating.
for GPU processing switched from rendering graphics to handling AI workloads. As recently as 2021 the highest power consumption of any NVIDIA GPU accelerator was 300 watts (W), with most single processors operating in the 100 W to 250 W range. Their latest chipset, the Blackwell B200, has a max power consumption of 1,200 W per chip. This massive increase in power consumption requires new approaches to electronics cooling from the data center to the edge. (Figure 1.)
Until recently high-performance GPUs like those from NVIDIA, AMD, and Intel were found primarily in data centers and research labs. These purpose-built
facilities are designed with cooling in mind, and typically use a combination of cold room air conditioners (CRACs), chillers, and targeted liquid cooling to dissipate heat generated by electronics. Air cooling is often preferred, as it is cheaper and less complex, but as power consumption increases air cooling is often insufficient to handle the heat generated by high-density electronics racks.
More and more data centers are adopting air-to-liquid heat exchangers (Figure 2) or direct liquid cooling as their primary cooling method. Liquid cooling has many advantages over air cooling; it is more efficient than air, produces less noise, and allows for greater electronics density by eliminating the space required for large heatsinks and sufficient air flow to cool them. However, these systems are often more expensive than air cooling, more complex and harder to maintain, and carry the risk of coolant leaks.
As high-performance computing moves out of the data center and to the edge, especially in aerospace and defense, the challenges associated with cooling become more complex. Many issues exist at the edge that aren’t present in
the data center, including environmental extremes, rigorous SWaP requirements, shock, vibration, and motion profiles not encountered in climate-controlled, stationary data center applications. In addition, the critical nature of aerospace and defense applications means systems cannot fail, even when subjected to significant stress. Managing thermal load in such extreme applications is a major challenge for system designers. Thankfully, the VITA 48 standard provides multiple options for cooling rugged embedded electronics.
VITA: multiple options for beating the heat VITA 48 is a standard developed by the VMEbus International Trade Association (VITA) that defines mechanical specifications for ruggedized systems, particularly focusing on cooling methods for embedded systems used in harsh environments. It encompasses a variety of cooling techniques tailored to support high-performance electronics, such as military and aerospace systems, where managing heat dissipation is critical.
The Dawn family of one-slot OpenVPX test station and development backplanes gives engineers the ability to perform compatibility tests and easily reconfigure payload module profiles and slot interoperability to meet custom requirements.
Highly useful as stand alone or in combination with other backplanes, with or without RTM connectors. Multiple units can be topology wired using MERITEC VPX Plus cables.
Open standards for embedded systems: FACE, SOSA, CMOSS, VPX, and more
Key cooling methods outlined in VITA 48 include conduction, forced air, air flowthrough, and liquid flow-through cooling. Each is briefly described below. While cooling capacity is given here as a general reference, please note that actual cooling performance can vary greatly depending on system design and environmental factors.
Cooling (VITA 48.2)
› Method: Transfers heat directly from electronic components to the system’s enclosure, typically through heat frames or wedge-locks.
› Usage: Effective in environments where airflow or liquid cooling is not feasible, such as sealed or rugged systems used in military or space applications.
› Advantages: No reliance on moving parts like fans; highly durable and suited for shock and vibration-heavy environments.
› Cooling capacity: Approximately 80 W to 100 W per slot
› Factors influencing capacity: Thermal interface materials, efficiency of heat conduction paths, and the thermal conductivity of the enclosure play a significant role.
Air Cooling (VITA 48.1)
› Method: Air is circulated over modules or a heatsink using fans, without exposing the electronics directly to the external environment.
› Usage: Effective in rugged, sealed systems where it’s important to protect electronics from dust, moisture, or contaminants, while still benefiting from air cooling.
Available 3U and 6U in VITA 65, VITA 67.1, VITA 67.2, VITA 67.3, Nano-RF, SOSA-aligned and Power Supply slot profiles. Custom configurations available.
Rugged, Reliable and Ready. You need it right. You want Dawn.
› Advantages: Simple and costeffective; fans can easily be added to increase cooling capacity.
› Cooling capacity: Approximately 120 W to 180 W per slot
› Factors influencing capacity: Airflow velocity, fan efficiency, ambient air temperature, and heatsink design.
(VITA 48.5, VITA 48.8)
› Method: Air is directed through a channel or cavity within the modules to cool internal components directly.
› Usage: Used in systems where internal airflow is possible, such as those deployed in less extreme environments or where higher levels of heat dissipation are required.
› Advantages: Higher cooling efficiency than conduction and traditional forced air, resistance through card-loks and chassis less important.
› Cooling capacity: Approximately 200 W per slot, depending on airflow rates and the system’s thermal design.
› Factors influencing capacity: Sealed airflow paths, air channel design, and ambient air temperature.
› Method: Liquid coolant is circulated through a cold plate or channels in the module, which draws heat away from the components.
› Usage: Suitable for systems requiring very high levels of heat dissipation, such as high-power computing or signal processing applications.
› Advantages: Provides superior heat dissipation compared to air or conduction cooling; ideal for extremely high-performance systems.
› Cooling capacity: Approximately 300-plus W per slot.
› Factors influencing capacity: Coolant type (e.g., water/glycol, dielectric fluids), flow rate, and cold plate channel design.
Each cooling method in VITA 48 is tailored to specific operating environments and system requirements, balancing factors like environmental sealing, heat dissipation needs, and mechanical hardening.
An additional benefit of designing VITA 48 compliant cooling solutions is that VITA 48 is one of several open standards integrated into the Sensor Open System Architecture, or SOSA, Technical Standard, which is used to establish command, control, communications, computers, cyber, intelligence, surveillance, and reconnaissance (C5ISR) systems guidelines. The alignment between VITA 48 and SOSA supports the creation of
rugged, high-performance systems that are modular, interoperable, and thermally optimized for harsh environments.
VITA 48’s cooling and mechanical standards provide the critical thermalmanagement infrastructure that SOSA systems rely on to meet performance requirements in military and aerospace applications. By utilizing VITA 48 cooling methods, system designers can create more versatile, efficient, and upgradable systems. MES
Matthew Tarney is the Global Vertical Growth Leader for Aerospace & Defense at nVent SCHROFF. In this role he is focused heavily on finding solutions to the thermal challenges facing electronics in the aerospace and defense space. Readers may email the author at Matthew. Tarney@nvent.com.
nVent SCHROFF
https://schroff.nvent.com/en-us/
McHale Report, by mil-embedded.com
Editorial Director John McHale, covers technology and procurement trends in the defense electronics community.
By Carlos Peña and Robert Droppa, DT Research
In the rapidly evolving world of defense, military organizations must continuously adapt to maintain readiness and effectiveness. To meet these demands, the United States Marine Corps (USMC) has embraced innovative solutions like the Marine Corps Platform Integration (MCPIC) System. This advanced system dramatically enhances the service branch’s ability to manage critical assets while streamlining operations for improved efficiency and control.
The Marine Corps-developed MCPIC system is a net-centric software and hardware solution designed to improve the management of asset visibility, inventory, location verification, and force deployment and distribution. MCPIC enables Marine Corps personnel to quickly perform asset counts and provides real-time location tracking for all assets.
The system’s automatic identification technology (AIT) captures every event that occurs within the system, ensuring total accountability for processes, events, and workflows. This level of transparency and control has been pivotal for improving the Marine Corps’ operational efficiency.
Colonel John S. Sattely, Commanding Officer, BIC & Marine Corps Support Facility, explained, “MCPIC gives us very accurate in-transit asset visibility. It gets us out of the habit of notebooks and using Excel worksheets and building PowerPoints with all the same data. We can see the whole process of off-load to all the nodes it hits before it’s issued out. Not only does it help us with accuracy in terms of where the equipment and supplies are, but it also provides a standard format for the different ops [operations] centers and COCs [combat operations centers] to see what we are looking at is all the same.”
The MCPIC system transmits live data to the program through passive radio-frequency identification (RFID) transactions enabled using DT Research rugged tablets. This capability provides seamless real-time tracking, simplifying the oversight of items in their journey from the warehouse to maintenance facilities and, ultimately, to their final destination.
To ensure that Marine Corps personnel have immediate access to up-to-date information, the system includes an ITRAK function that provides real-time monitoring, visualization, and mapping of inventory operations, offering a comprehensive view of assets and their movements. The experience is maximized by LED-backlit, sunlightreadable touchscreen displays, which allow access to critical data even in difficult lighting conditions.
Deputy Commander Daniel W. Elzie of Marine Force Storage Command described MCPIC as a real time-saver: “MCPIC has been a game-changer for us. What once took us 14 months to do an inventory of military equipment, we can now do in about three hours. We use MCPIC in order to increase our auditability, improve inventory accuracy, and expedite our ability to locate all of our equipment.”
This major reduction in the time required for inventory checks has important implications for readiness and responsiveness, enabling the Marine Corps to maintain a
higher level of operational readiness and respond swiftly to emerging threats or mission requirements.
Playbooks serve as an indispensable component of military operations. Through the Playbook Manager within MCPIC, schedules and executions can be adeptly organized and progress can be systematically tracked throughout the entirety of the asset-management process. This feature introduces an additional layer of control and coordination that ensures operations run smoothly and efficiently.
The ability to adapt and scale operations is critical for the Marine Corps. The MCPIC system supports this requirement by accommodating a near-limitless number of rugged tablets, making it versatile for a wide range of applications and scenarios. This flexibility enables Marine Corps teams to expand operations as needed, fully utilizing the system’s potential.
The MCPIC system has yielded remarkable results in asset management and data accuracy while streamlining processes, enhancing transparency, and largely reducing the time required for critical inventory checks.
This innovative approach shows the Marine Corps’ commitment to harnessing technology to meet the challenges of modern asset management and maintain operational effectiveness in a complex and evolving environment.
Carlos Peña is Director, Navy and Marine Corps, DT Research; and Robert Droppa is VP Government Solutions, DT Research.
DT Research • www.dtresearch.com
By Pragati Pathrotkar, Transparency Market Research
Military embedded systems are pivotal in modern defense operations, ensuring robust, real-time data analysis and secure communication. They play critical roles in air, land, and naval platforms in support of intelligence, surveillance, and reconnaissance (ISR); command-and-control systems; and data acquisition. As the demand for these highly specialized systems grows, so too does the need for technological advances that address operational requirements and cost efficiency.
Embedded systems, essential for defense operations, serve in various applications such as surveillance, communication, and command-and-control systems. The market faces challenges due to increasing design complexity, power management, and the need for compact, reliable solutions. However, continuous innovation is fueling significant growth, with the market projected to reach $128.81 billion by 2026 at a CAGR [combined annual growth rate] of 6.4%.
The rapid evolution of microprocessor and integrated circuit technologies has been a catalyst for market expansion. These advances have reduced production costs, making complex embedded systems more affordable and accessible to defense sectors globally. High-performance blade servers are increasingly utilized for their scalability and ability to manage high data throughput in network-centric applications.
Additionally, Ethernet technology has revolutionized the way data is transmitted across embedded systems. The convergence of data from different sources into a unified network has simplified processes and improved operational efficiency. These integrated networks can handle a wide range of data types, from real-time video and audio feeds to sensor outputs, crucial for military applications.
Despite positive market trends, designing military embedded systems comes with challenges. Embedded components must perform parallel operations with reduced power consumption while remaining compact, lightweight, and high-performance.
These systems must also be durable enough to operate in extreme environmental conditions, from high heat to sub-zero temperatures. Achieving this resilience without increasing system size or weight demands leveraging cutting-edge materials science and engineering ingenuity. Developers must also anticipate ongoing technological upgrades to ensure long-term system compatibility, which piles on another layer of design complexity.
The market is responding to these challenges with innovative solutions. Multicore processors and GPGPUs [general-purpose
graphics processing units] have become staples in the design of military embedded systems, enabling substantial computing power while conserving energy. Rugged systems, which are resistant to environmental stress, have seen heightened demand as defense missions extend into varied and harsh terrains.
The introduction of artificial intelligence and machine learning (AI and ML) capabilities into military embedded systems is another noteworthy trend. These technologies facilitate more dynamic data processing, enabling real-time decision-making support. AI-driven analysis enhances situational awareness, enabling military personnel to react faster and more accurately to evolving battlefield scenarios.
High-speed data transfer solutions are also critical: New powermanagement technologies are ensuring embedded systems maintain operational longevity without excessive energy consumption. Modular and scalable designs, which can be upgraded or expanded without complete system overhauls, are gaining traction for their cost-effectiveness and flexibility.
The versatility of military embedded systems is evident in their applications across various platforms. On land, embedded systems are integrated into armored vehicles to support communication, control, and surveillance functions. In the air, they are used in uncrewed aerial systems (UASs) and fighter jets for tasks such as reconnaissance and secure data transmission. Naval platforms employ these systems for radar operation, navigation, and complex sensor fusion. The global rise in demand for mobile command units and the expanded use of uncrewed vehicles have been major growth drivers.
Market opportunities
The military embedded systems market is poised for sustained growth, as governments worldwide modernize and invest in state-of-the-art technology. This trend supports the previously mentioned growth forecast of a 6.4% CAGR through 2026.
Opportunities lie in the development of more energy-efficient, AI-integrated, and resilient systems that can adapt to new defense requirements. The integration of cloud-based solutions and advanced wireless technology within military applications promises further growth, enabling more flexible and scalable military operations.
Pragati Pathrotkar is a data/marketing and editorial expert with Transparency Market Research.
Transparency Market Research www.transparencymarketresearch.com/
By Logan Schraeder, FirePoint Innovations
Despite the recent surge in military spending on artificial intelligence (AI), the U.S. Department of Defense (DoD) is still falling behind its adversaries in leveraging this groundbreaking capability for national defense. Not only is China beginning to outpace the U.S. in both AI investment and innovation, but the DoD is also struggling to compete with the private sector in the war for talent.
With the DoD spending $4.3 billion on AI – causing AI spending by all other agencies to become what a recent Brookings Institution report called “a rounding error” – it’s not the lack of financial investment that’s holding the U.S. back. Instead, we risk losing the edge in AI because we don’t have the personnel infrastructure or the culture to make the most of the technology once we have it.
To successfully compete in the AI space, the DoD must shift away from the legacy culture and infrastructure that stymies agility and innovation. Following are five strategies for a winning DoD AI strategy that have more to do with culture than technology.
› Revamp the talent infrastructure. While there’s no doubt the DoD should do all it can to develop AI talent, it must also figure out how to receive the talent that’s already emerging. Enrollment in AI training programs is rising, but there’s no clear career pathway for an AI or machine learning (ML) specialist to bring that skill to the defense sector either as a uniformed soldier or civil servant; there’s simply no job classification for it in the current taxonomy. The Army Futures Command has developed an Additional Skill Identifier (ASI) to highlight these specialized skills, but it has yet to be embraced by the larger Army and the Joint Force, and that must become a priority. Even if we recruit the best AI talent in the world, it will be for naught if there’s nowhere for them to really apply their skills.
› Prioritize continuing education. Nearly a third of federal defense leaders said in a survey that workforce challenges are a stumbling block for adopting new technologies. In fact, military enlistment has been declining; with high demand for AI talent in private-sector tech companies, the DoD must continue to evolve in order to compete. That evolution means prioritizing education benefits, continuing education, and a meaningful path forward for service members after their enlistment ends. Professional development is a priority for today’s job seekers, but tuition assistance is often one of the first line items to get cut from the DoD budget every year. In order to attract and retain AI talent, the DoD must adapt its policies, organizational politics, and mission requirements to provide meaningful upskilling, education vouchers, and continuing education opportunities.
› Upgrade legacy systems. Across the DoD, Industrial Age infrastructure is trying to adapt to Information Age demands. The current platforms are a severe disappointment to most young recruits who already use more advanced technology to do their homework. So much DoD hardware is antiquated, which makes compatibility with new solutions sometimes impossible – you’d be pressed to develop a meaningful AI model on the typical military standard-issue Toughbook. The DoD desperately needs upgraded, agile technology on par with what’s available in the commercial sector in order to integrate these new tools much faster and attract people who want to work on the latest systems. While DoD’s acquisition systems are improving with Other Transaction Authority (OTA) contracts and other methods, these improvements should be part of a continual evolution, not the end of the line.
› Accelerate tech transfer. AI development is booming in the private sector with unprecedented new capabilities being brought to market with incredible potential in DoD applications. But technology transfer can be extremely slow, with complex hurdles preventing agile startups from connecting with government procurement systems. Upstart companies that do strive for DoD contracts often get mired in the red tape and end up wasting resources they could be spending to secure commercial partnerships with faster ROI. The
DoD must prioritize participation in networked innovation programs like the Great Plains Mission Acceleration Center (MAC), MAC National Network, and Defense Innovation Unit (DIU) On-Ramp Hubs and do better leveraging organizations across the joint modernization ecosystem – like Army Futures Command and the Office of Naval Research – to form strategic partnerships between civilian innovators and the DoD. These collaborations will help lower the barrier to entry and get prototypes into the field faster.
› Teach the teachers. A GovTech report says that more than 70% of K-12 educators do not have the training and resources to teach their students how to use AI effectively. Often there’s a good chance their students are more advanced than the instructors are in using it, but likely also lack knowledge of AI’s
risks, nuances, and limitations. The country as a whole has an opportunity to invest in raising the next generation of AI experts by teaching their teachers how to integrate AI into their classrooms, instruct students about its caveats and responsible use, and begin exploring applications and career opportunities, including military service.
There’s no doubt AI provides a greatly expanded tool set for the modern warfighter. The ability to receive, interpret, and make intelligent decisions is among the most decisive factors in war throughout history, and AI has the ability to help the military do that at a level never seen before. But while having the right technology is vital, it also needs the right people, approach, and culture to make it a seamless and meaningful part of U.S. strategic defense capabilities.
Today’s incoming service members are growing up with Amazon Alexa at home and using ChatGPT for their homework, and we have yet to see what the Future Force’s recruits will grow up with. In the same way we outfitted GWOT [Global War on Terror]-era explosive ordnance disposal units with Xbox controllers to create an intuitive interface for operators, the DoD must now adapt its systems to meet today’s enlistee expectations. That reality means modernizing not only the technology it uses but also shifting its culture to welcome ground-up innovation, troop-level input, and battlefield improvisation.
Logan Schraeder is Research Manager – FVL & Autonomy at FirePoint Innovations.
FirePoint Innovations https://www.firepoint.info/
Powered by Military Embedded Systems
Sponsored by Abaco, Aitech, Curtiss-Wright, Elma, Mercury, RTI, and Wind River
The CJADC2 At The Edge Virtual Summit drives awareness and thought leadership around CJADC2 concepts and requirements and studies how AI, high-performance computing, cyber operations, signal-processing solutions, and other embedded technologies will impact system designs. (This is an archived event.)
Watch this webcast: https://tinyurl.com/ycaewe8z
Microchip Technology’s 101765 line of voltage-controlled SAW [surface acoustic wave] oscillators (VCSOs) delivers ultra-low phase noise for mission-critical applications such as radar and test and measurement systems. Available in frequencies of 320 MHz (pictured) and 400 MHz, the devices achieve phase noise performance of -166 dBc/Hz at a 10 kHz offset and a noise floor of -182 dBc/Hz, which enhances detection capabilities in radar systems, including those using active electronically scanned array (AESA) technology. Designed to operate efficiently with supply voltages ranging from 4.75V to 15.75V and a current draw of 111 mA, the VCSOs come in a compact, hermetic Kovar package measuring 1 inch by 1 inch, meeting lower size, weight, power, and cost (SWaP-C) requirements.
The 101765 VCSO family also offers MIL-PRF-38534 screening for aerospace and defense customers requiring high reliability in harsh environments. Supporting a broad frequency range from 30 MHz to 2.7 GHz, these oscillators address ITAR and EAR exportcontrol compliance requirements and can be integrated with other Microchip products, including FPGA/RF [field-programmable gate array/radio-frequency] components. Development tools such as the 101765 test boards enable design-phase evaluation, ensuring suitability for applications requiring precise frequency control and robust performance in military and aerospace systems.
Microchip | www.microchip.com
Haivision’s Play ISR software application is a free, cross-platform tool designed to provide low-latency playback of live video streams with embedded key length value (KLV) metadata for intelligence, surveillance, and reconnaissance (ISR) applications. Compatible with Windows, Mac OS, and Linux, it supports video encoded in H.264/AVC and H.265/HEVC, with streaming over UDP and SRT video protocols. Developed specifically for defense professionals, Play ISR integrates real-time video with geospatial metadata, enabling users to visualize and analyze mission-critical situations with context-enhanced clarity.
Play ISR is positioned as a major component of Haivision’s ISR ecosystem, pairing with its Makito video encoder and Kraken processing platform to support the entire ISR workflow. The software ensures ultra-low latency for real-time situational awareness, providing an efficient tool for rapid decision-making in the field or command centers. It decodes MISB/STANAG (digital video standards) -compliant metadata, enabling users to overlay or display geospatial information alongside video for enhanced operational context. The interface is designed to minimize setup time and learning curves, making it accessible for professionals across various defense sectors, in large part by enabling free access and compatibility across major operating systems.
Haivision | www.haivision.com
Review Display Systems (RDS) introduces AMT Resistive Multi-Touch (RMT) panels, designed for environments where precision and reliability are critical. These panels combine the dependability of resistive touch technology with multi-point touch and gesture support, ensuring uninterrupted functionality in challenging conditions. Their construction is designed to be robust in order to resist contamination from water, saline, or other fluids, making them ideal for applications such as industrial control systems and mission-critical environments. The panels are designed to offer precise input accuracy, excellent linearity, and compatibility with gloved hands or styluses, making them versatile for diverse operational needs.
Available in sizes up to 21.5 inches, AMT RMT panels can be customized with features like low-reflective sunlight-readable designs, glass-film-glass (GFG) structures, or combined GFG LR options for enhanced durability and visibility. These panels also include electrostatic discharge (ESD) resistance, meeting standards of 15 kV for air discharge and 8 kV for contact discharge. For applications requiring enhanced electromagnetic interference (EMI) performance, an integrated fine mesh film is available. AMT RMT panels can be used in industrial human-machine interfaces (HMIs) or aerospace systems, and are intended to deliver reliable, noise-immune operation tailored to meet the exacting requirements of critical-use equipment.
Review Display
Holt Integrated Circuits’ ADK-1592 development kit evaluates the HI-1592 radiation-hardened MIL-STD-1553 transceiver. The HI-1592 transceiver can withstand total ionizing doses up to 100 krad(Si) and single-event upsets with linear energy transfer (LET) values of at least 67.7 MeV-cm²/mg, making it suitable for space, high-altitude aircraft, and low-earth orbit satellite applications. The transceiver supports digital I/O levels of 1.8V, 2.5V, and 3.3V, enabling compatibility with a wide range of FPGAs and controllers.
The kit connects to external MIL-STD 1553 controller boards via an industry-standard PMOD [peripheral module interface] port and provides alternative connectors for signals such as Rx Enable and Tx Inhibit. It includes DIP switches configured for PMOD usage by default and supports both direct and transformer-coupled connections to a MIL-STD-1553 bus through on-board triaxial connectors. The kit facilitates evaluation and software development by enabling the digital transmit signals to loop back to the controller. The modular design of the development kit makes it flexible enough for integration into various testing setups. The easy connection to interface with MIL-STD-1553 systems means that the ADK-1592 development kit simplifies prototyping and testing for demanding applications. This dev kit is tailored for avionics, defense, and space-grade systems that require robust communication performance and ease of use during the development phase.
The StreamCaster LITE 5200 (SL5200) from Silvus Technologies is a MANET [mobile ad hoc network] radio module designed for unmanned systems requiring ultra-low size, weight, and power (SWaP). It weighs in at 52 grams (1.83 ounces) and delivers as much as 2 W of native output power and 4 W effective power through transmit Eigen-beamforming, a technique used in multiple-input/multipleoutput (MIMO) systems to improve signal quality and system performance. The module supports data rates up to 100 Mbits/sec and features the Silvus MN-MIMO waveform, enabling scalable mesh networking for hundreds of nodes. This capability makes the SL5200 suitable for multidomain operations, linking different types of uncrewed platforms, sensors, personnel, and other platforms into a cohesive network.
Designed for Group 1 unmanned systems (very small) while providing Group 2-level (medium-sized) performance, the SL5200 integrates into a variety of tactical platforms and accommodates multiple I/O interface options. Advanced features include AES256 and FIPS 140-3 encryption, as well as low probability of intercept/detection (LPI/LPD) and antijamming capabilities, supporting secure operations in contested environments. The SL5200 is interoperable with the Silvus 4000-series StreamCaster radios, ensuring seamless integration across applications. By unifying command-and-control, sensor, and telemetry data, the SL5200 aims to provide an efficient solution for real-time communication and operational awareness in constrained environments.
Silvus Technologies | www.silvustechnologies.com
The QPA0015 from Qorvo is a gallium nitride (GaN) power amplifier designed for satellite communications, radar, and data link applications. Operating within the 13.75 to 14.5 GHz frequency range, it provides an output power of 39 dBm (8 W), a gain of 35 dB, and a power-added efficiency (PAE) of 32%. The amplifier features an input return loss of 15 dB and an output return loss of 6 dB, with an intermodulation distortion (IM3) of -25 dBc. Its construction uses Qorvo’s 0.15 μm GaN-on-SiC [silicon carbide] process (QGaN15) and includes on-chip blocking capacitors connected to the DC grounds on the input and output ports.
The QPA0015 requires a 24 V DC power supply and consumes 195 mA of current. It is packaged in a compact surface-mount form factor measuring 7.0 by 4.5 by 2.45 mm, making it suitable for integration into space-constrained systems. Designed to operate in environments with temperatures ranging from -40 °C to +85 °C, it is suited for high-performance communication and sensing systems in commercial and defense applications. The amplifier meets RoHS standards (standards that limit the use of hazardous substances) and enables consistent, reliable performance across a variety of mission-critical scenarios and applications requiring reliable performance in demanding environments. Qorvo | www.qorvo.com
Each issue, the editorial staff of Military Embedded Systems will highlight a different organization that benefits the military, veterans, and their families. We are honored to cover the technology that protects those who protect us every day.
By Editorial Staff
This issue we are highlighting The Battle Within, a 501(c)(3) nonprofit organization that was inspired by U.S. Army veteran and Purple Heart recipient Justin Hoover. Hoover returned from a deployment in Iraq after being injured in combat. As he returned home to a new career and caring for family, unresolved traumas eventually resurfaced, catalyzing a pivotal journey towards healing, guided by the support of his family.
The organization was eventually founded in 2018 by Hoover and more than 100 fellow veterans, first responders, and community leaders with the stated mission of helping military personnel, veterans, and first responders deal with the psychological challenges of their past service and professions.
The Battle Within – with headquarters in Kansas but serving the entire U.S. – offers a number of services and outreach opportunities. An initial contact may be what it calls the “Revenant Journey,” which is a free five-day program designed to give participants a way to identify their burdens, confront them in a secure environment, and obtain the necessary tools to overcome them, with the result that they can acquire new skills and start to work on long-term healing. The organization also offers structured therapy support and immediate access to behavioral and mental-health resources.
One of the Battle Within’s major programs is Dogs 4 Valor, which pairs retired veterans and first responders with service dogs; the organization says that the service-dog program focuses on partnership and a way out of isolation for the returning serviceperson. For additional information, visit https://www.thebattlewithin.org/.
SOSA in use: Radar, Electronic Warfare, Communications Applications
Sponsored by Epiq Solutions, New Wave DV, and Wolf Advanced Technology
It’s been two years since the Sensor Open Systems Architecture, or SOSA, Technical Standard revision 1.0 was ratified. Military applications are already requiring SOSA aligned products in systems for radar, electronic warfare, communications, and more. Open architecture approaches like SOSA have changed the way defense electronics designers build tomorrow’s military platforms.
In this webcast, several members of the SOSA Consortium discuss in detail how SOSA aligned products can make a major impact on how companies and engineers design and specify critical defense platforms. (This is an archived event.)
Watch this webcast: https://tinyurl.com/jbukd9bx
Watch more webcasts: https://militaryembedded.com/webcasts/
MOSA e-Book: Leading editorial on MOSA strategies for military applications
Sponsored by Precise Systems
Backed by a 2019 U.S. Department of Defense (DoD) memo from the leaders of the Air Force, Army, and Navy man dating the use of a modular open systems approach (MOSA) in new programs and upgrades, MOSA strategies are part of most conversations at U.S. defense industry events. From design engineers to four-star flag officers, MOSA strategies are in demand. The momentum behind MOSA is growing as MOSA strategies become part of program requirements. That industry excitement is why we have compiled this MOSA e-Book to bring you exclusive MOSA content from the pages of Military Embedded Systems, the SOSA Special Edition, and the FACE Special Edition on how MOSA is changing the way the DoD procures and develops technology.
Download the MOSA e-Book: https://tinyurl.com/4zmb9tw2
Get more white papers and e-Books: https://militaryembedded.com/whitepapers
Military Embedded Systems focuses on embedded electronics – hardware and software – for military applications through technical coverage of all parts of the design process. The website, e-mags, newsletters, podcasts, virtual events, annual Resource Guide, and print editions cover topics including radar and electronic warfare, artificial intelligence/machine learning, uncrewed systems, C5ISR, avionics, and cybersecurity. Don’t miss any of it!
Military Embedded Systems is also the largest source for coverage of the Sensor Open Systems Architecture, or SOSA, Technical Standard and the Future Airborne Capability Environment, or FACE, Technical Standard. We exclusively produce the once-yearly SOSA Special Edition and FACE Special Edition. militaryembedded.com