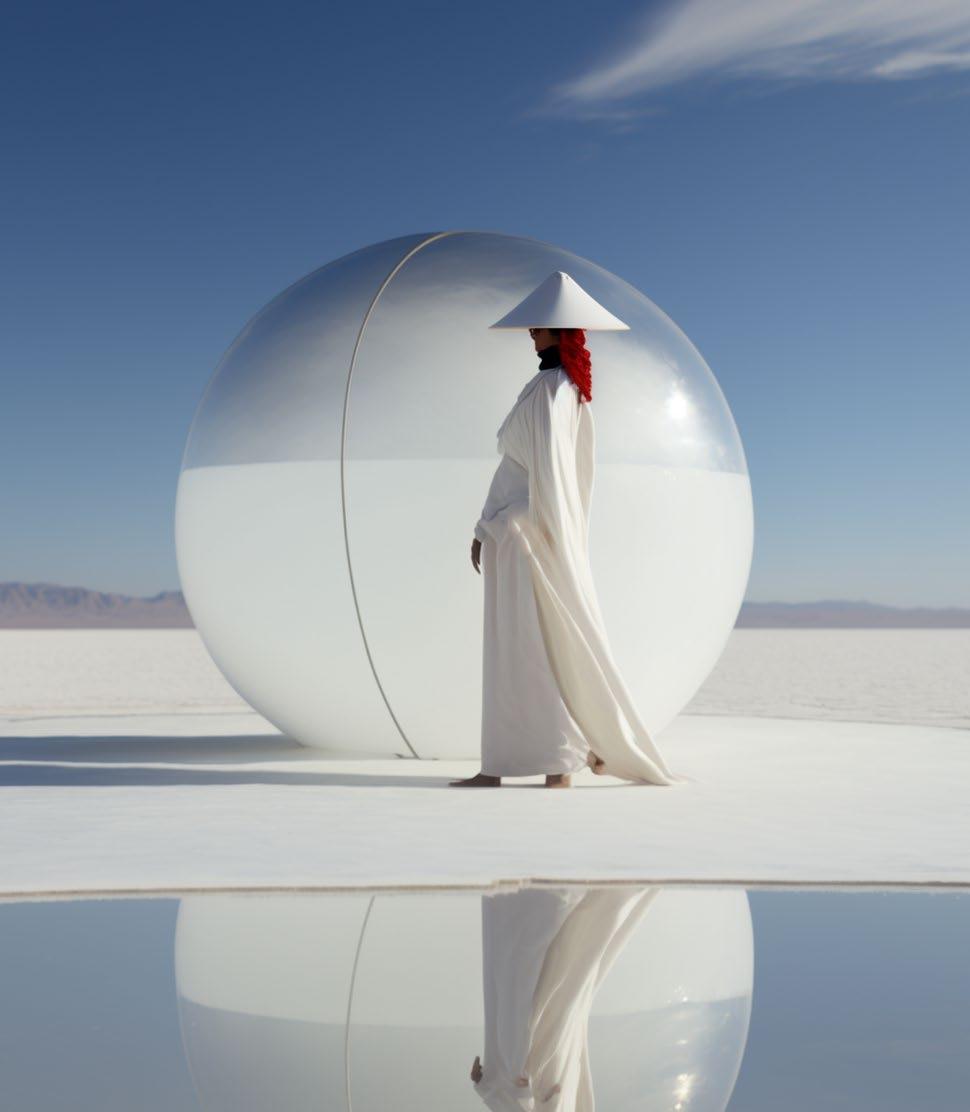
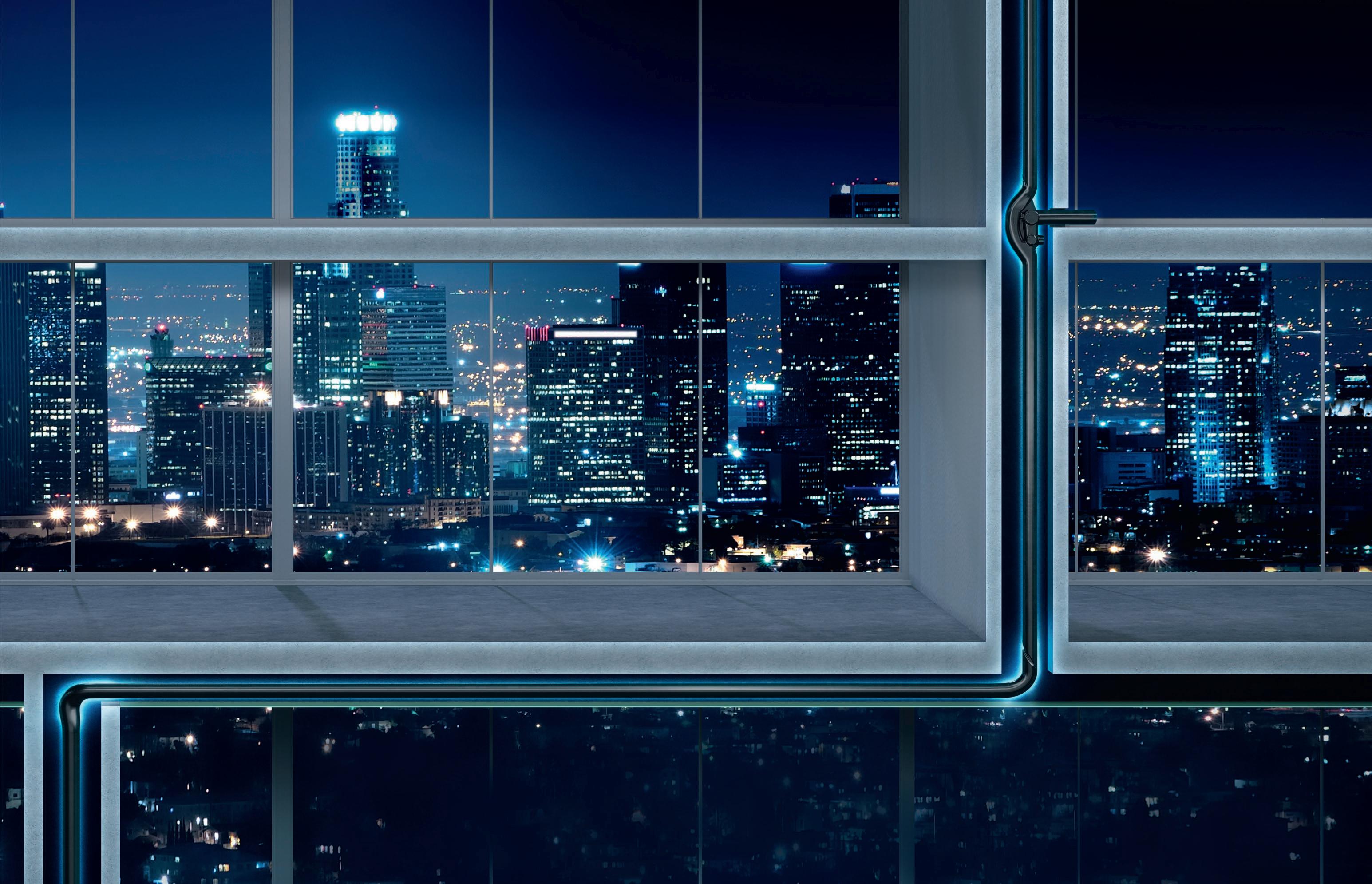
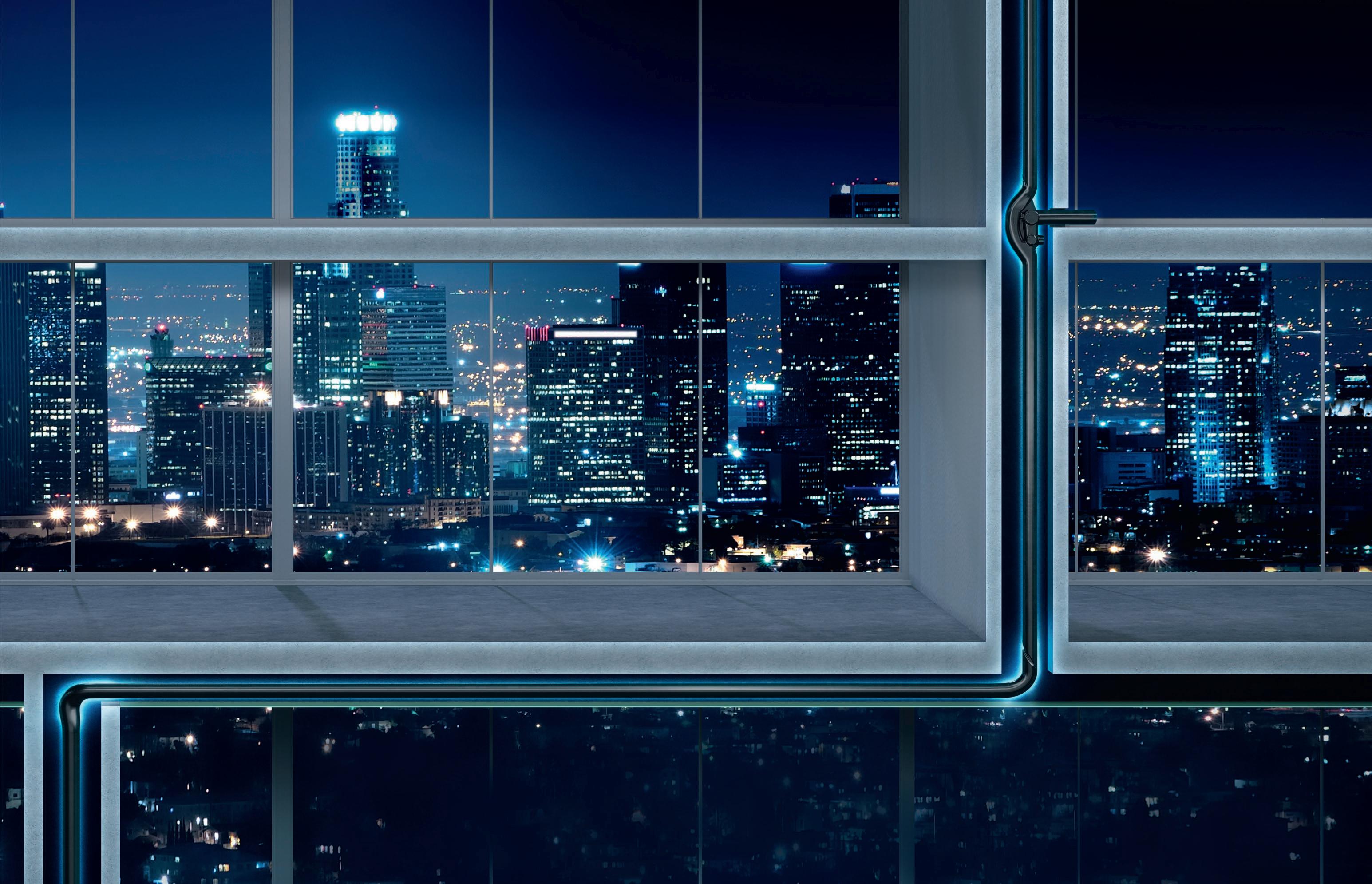
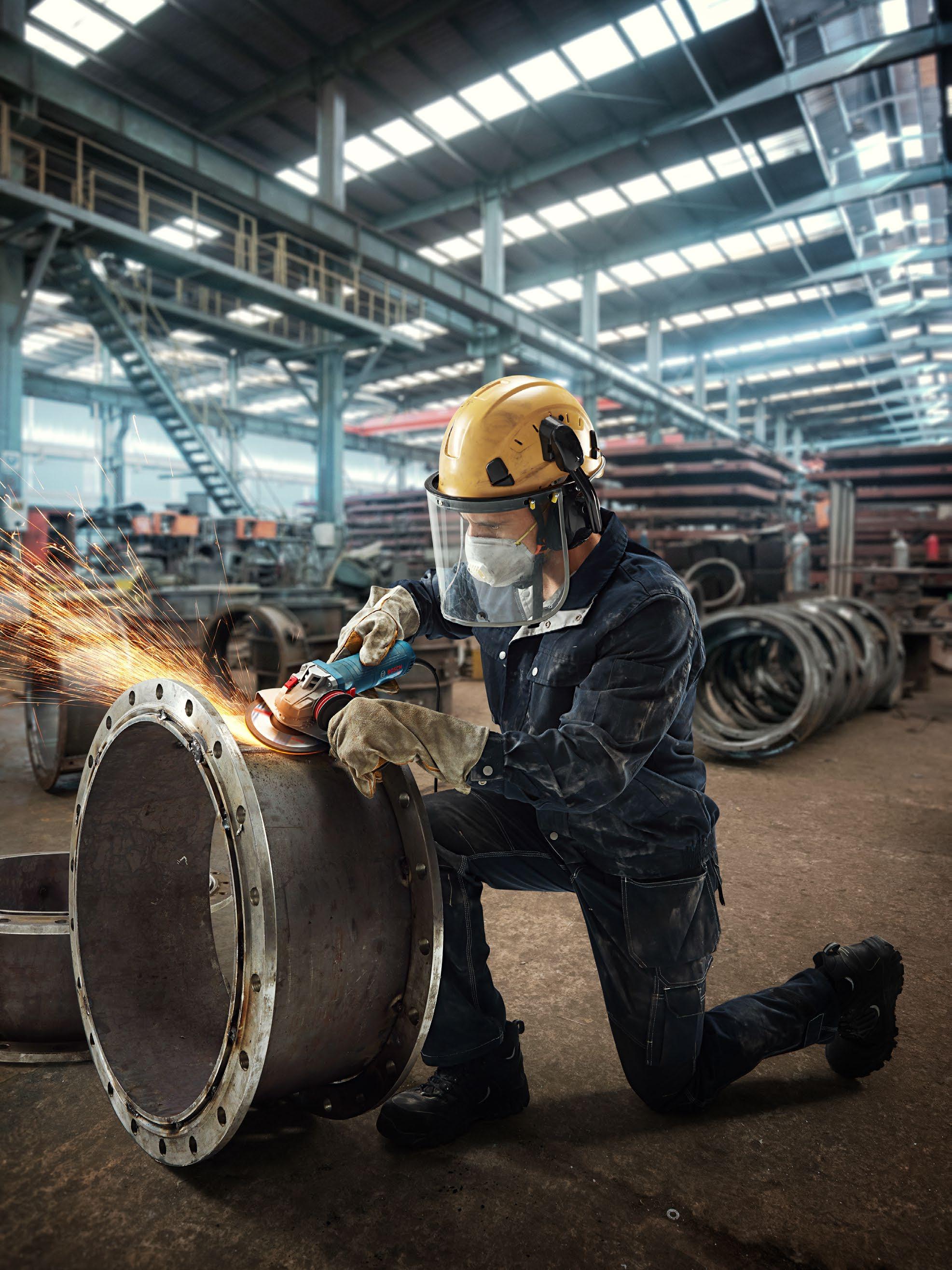
With
KEY BENEFITS
APPLICATIONS
SPECIFICATIONS
For over 50 years, MiTek has provided innovative solutions to the construction industry, helping to reduce overheads and improve the building process. MiTek offers advanced planning and design software, team extension services, collaboration with component manufacturers for off-site solutions, and trusted engineered connections and systems to help you overcome whatever the market brings.
MiTek's Design-Make-Build™ methodology transforms the traditional design/build model with software and automationenabled collaboration tools. This approach uses innovative off-site construction methods to deliver significant parts of the building to be installed during the build phase. By identifying the ideal off-site building methods as part of the concept and design phase, MiTek can ensure optimal efficiency and savings.
Optimise building plans for off-site construction with software and services that enable collaboration across the supply chain.
Leverage off-site automation technologies to get highquality components that compress your schedule, reduce waste, and improve the build quality.
Use componentised roof trusses, advanced wall panels, and floor joists that arrive on-site ready to install, reducing on-site resources, waste, and time.
Today, the building industry faces significant challenges, including shortages of skilled labour and materials, resulting in wasted time, materials, and energy. To meet the growing demand for affordable, sustainable, and resilient homes and buildings, traditional building methods must evolve. MiTek's Design-Make-Build™ approach reduces waste and increases value by optimising both on-site and off-site processes, moving decisions from the physical to the virtual world, resulting in more efficient, cost-effective, and sustainable building.
MiTek is committed to transforming the building industry by championing better building methods through collaboration across the industry. Their innovative and integrated solutions empower partners to transform the way they design, make, and build. Join MiTek in creating transformational breakthroughs in design and construction and build a better future together.
It’s no secret that materials are arguably the most important piece in the infrastructure puzzle. Materials can set the tone for a building or landscape's overall aesthetic, determine its durability, and influence its environmental impact. Therefore, choosing the right ‘genetic makeup’ can make all the difference in creating a structure that is not only visually stunning but also functional and sustainable for both people and planet. Whether you’re a designer, a build professional, or tasked with maintaining a site, one thing is certain: materials matter!
In an industry heavily reliant on materials, our shift in recent decades has been towards experimenting with new and exciting products that lower our footprint, celebrate innovation, and champion better buildings. So, it should come as no surprise that we’ve decided to dedicate an entire issue to materials, as we look to future-proof our cities and suburbs!
In this issue, we showcase some of the most remarkable materials being used in modern architecture. Our expert contributors share their insights and experiences working with these materials and highlight some of the unique properties and benefits they offer. From Spatial Activists to urban mining and special plaster recipes, designers are breaking the boundaries of traditional construction conventions and thinking outside the box with eco-friendly alternatives. We explore how materials like timber and strawbales are being transformed into sleek and modern designs, and investigate the potential of emerging materials, such as mycelium and bioplastics, to revolutionise the industry.
Although we don’t feature anything made of shells, the world is your oyster! The only limit is our imagination. May you find your material muse. Until next month, when we bring you our May issue titled The Giants.
Veld Architects | Wolf + Wolf Architects | studioMAS | Paul Elliot Architects | dhk Architects | SVA International | Bone Interior Design Studio | Ebesa Architects | Gregory Katz, Gregory Katz Architecture | Ashleigh Killa and Maximillian Melvill, the MAAK | Pieter Mathews, Mathews + Associates Architects | Ruth Manda, GREENinc | Andrew Horn, Eco Design Architects and Consultants | Stephen Hitchcock and Dave Long, Stretch Architects | Nicholas Plewman Architects + Associates | GREENinc Landscape Architecture + Urbanism | Local Studio
Cover image: NEOCOSMOS - Take Me to the Sun, a cosmic exhibition by HOMMÉS Studio and TAPIS Studio for Milan Design Week, 18-23 April.
Architecture is not just about design; it's about selecting the right materials to bring those designs to life for generations to come. We've gathered a group of visionaries who are using everything from cork to stone to repurposed tyres to create functional and stunning structures that will stand the test of time. Let’s step inside the projects of the people who are making it happen.
Constructing with earthen materials is one of the oldest traditional technologies, and is a sustainable building practice that works hand in hand with nature. We used rammed earth in our project Soil & Serenity — a material that brings character to buildings through its textures.
Rammed earth has a low carbon footprint that promotes a cost-effective home with the use of local materials that will be stringent for years to come. It can be directly sourced on site, can be repurposed, supports local workmanship and techniques, requires none to minimal maintenance, and contributes to excellent thermal comfort due to its high density.
Too often, the natural landscape of a building is only considered in hindsight, losing the powerful connection that exists between a building, the landscape, and the user. To preserve this link with nature, the excavated soil from the site was repurposed and interwoven into the building in layers of rammed earth walls. These unique feature walls subtly yet intentionally mimic the surrounding Magaliesberg mountains and create a main entrance axis that guides users through the home. This beautifully practical construction method pays homage to the client’s profession as a geologist. Simple durable and honest, it reduces the design to the point of elemental poetry.
Of all the plant fibres used in construction, hemp is superior from both the ecological perspective as well as the economic one. With most conventional wall construction techniques, you can expect to find multiple layers of different materials each performing only one specific function. For example, a steel framed structure with a composite wall system requires an insulation layer, vapour barrier layer, breather membrane, sheathing layer, and finishing cladding, to name a few. A hempcrete wall can perform all of these functions, and due to the reduced number of connection points between these materials, a more air-tight envelope can be achieved.
As a lightweight, breathable, vapour-permeable building envelope, it regulates internal relative humidity, eliminating condensation on internal faces. It has excellent thermal insulation values and good thermal mass well above regulation standard, leading to substantial energy savings compared with conventional building technologies. Hemp walls also have excellent acoustic insulation, blocking out external noise and dampening the transfer of sound through walls.
It is microbe, insect, mould, and rot resistant — one square metre of hemp can absorb up to 14 litres of water. Hempcrete is also a carbon negative material, meaning it sequesters CO2 from the atmosphere. About 108 kg of CO2 can be locked away as biomass per cubic metre of hempcrete for the lifespan of the building. The material is 100% biodegradable as it is fully organic, and has the potential to be a zero-waste material, as previously used hempcrete can be reused and added to new mixes or composted. Another significant performance benefit of hemp is a high fire rating — a single skin wall (110 mm) built with hemp blocks is certified for a two-hour fire rating.
In our South African context, industrial hemp can be cultivated and harvested in abundance with relative ease. It grows quickly, requires little water, and its farming can be completely toxin-free. In fact, it can even contribute to the phyto-purification of previously contaminated soils. Plus, it has the potential to create a whole new industry and job pool, which is particularly relevant in our country.
An impressive and completely unique engineered timber-pleated façade warmly clads Deloitte’s Cape Town offices. The exterior, executed using XLAM’s Cross Laminated Timber (CLT), gives the building its distinct identity. The site, which was previously a parking lot, is rectangular and orientated at a slight diagonal from north to south. Therefore, the sawtooth angled façade’s job was to correct this by folding the timber or glazing onto a direct north-south to assist with the sun control strategy.
The carbon savings involved in the use of CLT are significant. It is local, renewable, and highly durable. It requires no additional finishes to interior or exterior, no insulation, is a room temperature material, and ultimately allows the timber façade to improve with time as it weathers and ages.
House Elliott is a cork-clad, mass timber house built on a relatively inaccessible site — the subdivided portion of a house designed by Julian Elliott.
Mass timber was chosen as the structural building material for its carbon neutral credentials, ease of erection, and health benefits. Due to the location’s inaccessibility, the cross-laminate timber floor, wall, and roof panels were lifted over the existing house using a crane.
Cork was chosen as the cladding material as it is water-repellant, UV and mould resistant, and has excellent insulation and acoustic properties. Used to clad the walls and the roof, it gives the house a monolithic appearance.
www.paulelliottarchitects.co.za
35 Lower Long, an elegant 86-metre glass-clad office tower designed by dhk Architects, is characterised by a singular sculpted massing with dynamic glazed planes that extend seamlessly over the office and parking levels. The two main corners of the building are chamfered towards the roofline and soar upwards, forming a striking wing-like effect, resulting in a distinctive, non-orthogonal addition to Cape Town’s skyline. By extending the façade screens beyond the roof level with parapet sloping, the appearance of soaring shards is created, opposed to an abrupt utilitarian termination.
In terms of materiality, a glazed façade was selected due to its flush and sculpted reflective form, which is able to conceal both the parking levels and solid spandrels. Not only does glass facilitate an exciting play of light, but it allows for an expressive articulation of the building mass in the screen and shard-like elements.
The introduction of pixilation on the portions fronting the parking levels, ceiling voids, structure, and internal desk height upstands, allows the building to avoid overbearing horizontal bands. The glazed façade allows for unencumbered floorto-ceiling vistas, further enhanced by mullions at 2.4-metre-wide centres. This required a high-performance, double-glazed specification with increased internal cill height raised to desk height — reducing both solar gain and radiant heat, which significantly lowered HVAC requirements.
PIERRE SWANEPOEL Partner dhk Architects www.dhk.co.zaThere is a long tradition of architects building bespoke structures for their own use. Freed from the responsibility and constraints of designing for a client, these projects are an opportunity to innovate, to take risks, and to experiment.
Gregory Katz’s ‘Armadillo Studio’ is one such project. Built in just three months by the architect and a pair of skilled carpenters, this 80 m² duplex box was designed to house Greg’s practice on the upper story and his wife Caryn’s voice coaching studio below. A number of advanced materials and building technologies were used in the build.
The structure is made from balloon-framed light gauge galvanized steel, supplied by MiTek Industries, wrapped in a black ‘raincoat’ of asphalt shingles from Owens Corning. The unusual application of shingles on all surfaces including vertical ones (shingles are traditionally used only as a roofing material), gives the block-like form its striking, homogenous, sleek appearance. It’s a wonderfully versatile solution: it’s light-weight, waterproof, and UV stable, and it’s flexible enough to form flashings at the corners, eaves, and lintols. Both materials are fully recyclable — although this durable little studio is built for keeps!
Dotting the urban landscape of Eastgate Shopping Centre is Batley Partners’ solar tree family: a self-reliant live installation that provides shade, shelter, containment, and a sense of place to the piazza. The trees harness the sun to provide a source of renewable energy to the centre, whilst increasing the public’s awareness of sustainable green methods.
Inspired by the Baines’ baobabs in the Botswana Nxai Pan National Park, which have been captivating people for centuries as Africa’s ‘tree of life’, these solar trees are designed to encourage community-driven experiences and facilitate social and storytelling culture, just like the baobabs.
To make the trio look as natural as possible (the tallest tree stands at 13.5 metres), each tree consists of three primary parts: the steel tubular ‘trunk’ and ‘branches’, which allow electrical cables to run through them without being seen, the stainless-steel netting called Jakob Webnet procured in Switzerland, and the solar panel ‘leaves’ that have a life-span of 10 years and can easily be replaced. The hollow steel sections are the most cost-effective components to use, as they offer a good strengthto-weight ratio and are extremely flexible in terms of ‘bendability’. They are also easy to ‘splice’ or join, and can be divided up into components for transportation and installation. In fact, being so large, the trees had to be constructed off-site before being assembled.
They come alive at night through an intricate array of LED lights that automatously and gradually illuminate based on the diurnal rhythm and energy generation of the day. This system of transferred energy into an autonomous LED feature had not been done before; therefore, much research and testing went into the development of a customised electrical and lighting system.
JOHANNESBURGThe concept around this bathroom design in a residential refurb was to ground the space with a piece of artwork. A bath to hold the room.
The decision to use sandstone for this custom bath, titled Gres, was obvious in the stone’s healing benefits as well as being the most durable stone that requires no maintenance. The stone’s thermal mass also makes it a good heat insulator, ensuring bathwater stays at the optimum temperature. We selected the original raw block of Namibian sandstone from the stoneyard — a level of faith required that the inside of the rock would be as beautiful as the outside.
Chiselled, hand-carved, moulded, and sanded to a smooth ellipse, the hundreds of hours required to perfect this piece of sculpture, and the crane needed to transport it through the house’s large pane windows, warrant its exclusivity. It is a true element of art.
Established 33 years ago, Victorian Bathrooms is immensely proud to have built our biggest and best showroom yet. We are thrilled to re-introduce Johannesburg to the brand through a space where our customers can make their dream bathroom a reality. This showroom offers a bigger space with inspirational settings, extensive product libraries, and a cosy corner to sit down, enjoy a coffee, and discuss your next exciting bathroom project. We have created a fresh space that we are confident will inspire all who visit.
After 22 incredible years at the prestigious Hyde Park Corner Shopping Centre, the time came for us to offer our beloved clients the true ‘VB Experience’ our Cape Town customers have come to appreciate. Now Kramerville, considered South Africa’s premiere design district, is the new neighbourhood for our showroom — rubbing shoulders with the best in décor and design.
A range of fresh colours, textures, exotic smells, and calm displays await you. Not only have we created several bathroom settings — from retro to modern classic to loft-lifestyle and safari-chic — we have also included select international products exclusive to Victorian Bathrooms and only available by special order, helping you create one-of-a-kind bathrooms.
Clients can expect to find everything you need to complete and uplift a bathroom. From our popular accessories, mirrors, lights, and towels, to our quintessential fragrances, soaps, and lotions that everyone had grown to love in our Hyde Park Shop.
This exciting new showroom is centred around design and collaboration. We have created an inspirations room with product samples and various customisation options, where architects, designers, and clients can meet around the table and discuss their projects. Our knowledgeable team is always on hand to assist with product selection, design input, as well as special requests for unique projects and specifications.
www.victorianbathrooms.co.za
@victorianbathrooms
Ebesa Architects was appointed to design and construct a new educational facility for City of Cape Town at Helderberg Nature Reserve. The goal was to integrate the building into the landscape by using environmentally-sustainable construction methods and materials.
Aided by the Natural Building Collective, the inner curved wall and foundations were constructed using rammed earth and repurposed building rubble, and the outer curved retaining wall was constructed from repurposed tyres. This massively reduced the amount of cement needed for construction. A total of 830 recycled truck tyres were used for the tyre wall, which is approximately 40 metres long and 3.4 metres high. Building rubble, sand from other construction sites, and ecobricks (made from plastic bottles filled and compacted with plastic waste), were used to fill the tyres and the internal wall. Natural cob — an environmentally-friendly plaster mix — was also used to cover the ecobricks instead of conventional cement-based plaster. In addition, approximately 176 cubic metres of earth and recycled building rubble were used for the rammed earth walls and foundations.
This façade-favourite by SVA International is another fantastic addition to the academic honour roll of Nelson Mandela University. The extension to South Africa’s first dedicated Ocean Sciences Campus is wrapped in an aluminium composite curtain wall, giving this sunny Eastern Cape seascape a beautiful effect as sunlight dances through the patterned façade.
The building is conceptualised as a large internal veranda space articulated as a triple-volume, multi-layered foyer that links the main circulation spine with the more private spaces within. A three-dimensional sun-screen layer further articulates the main building façade while simultaneously defining a unique internal aesthetic through the ever-changing shadow patterns throughout the day. The building structure acts as a stereometric composition between exposed concrete and structural steel, distinctly evident within the main foyer space to create a clear rhythm along the main circulation spine.
OCEAN SCIENCES CAMPUS EXTENSION SUMMERSTRAND, GQEBERHA
HSN’s Sky Blue Pool Tiles were first used in Thailand by a daring customer who took our word that the stone would come alive underwater and in full sunlight. Soon after, Cafe del Sol on the magical island of Koh Phangan gained a well-deserved reputation for its outstanding pool. The pool dazzles during the day, showing unending variations while clouds drift overhead. In the evening, small ripples are created by the wind, causing the water surface to mesmerise even further.
Sky Blue is a natural stone, so there is a slight colour variation between tiles — a unique property that you won't find in artificially-produced tiles. When the stone is mined, our quality assurance and quality control system ensures that the variation is within a reasonable colour range to prevent large patches of different colours within a pool.
When dry, our Sky Blue tiles actually appear light grey, but when they are submerged in water, they reveal striking shades of blue. This property is mainly due to the small reflective surfaces that were created through metamorphism (slight recrystallisation) of the original protolith. The depth of the water also plays a role in how the tiles appear. The deeper the water, the more refraction of light takes place, and the bluer the tiles look. This makes for a nice transition from grey to blue-grey to brilliant blue from the steps in a pool down to its deep end. Lastly, the overhead cloud/sky conditions and your position relative to the angle of the sun's rays create variations in how the tiles look throughout the day.
For pool interiors we use a stone size of 100 x 100 x 10 mm, to better follow the curvature of pools than large tiles would. This also provides more reflective edges for the shimmering effect under water.
We not only take into consideration the aesthetics of our tiles, but we also think about the practicality of where they will be installed. Our Sky Blue pool and coping tiles, for example, come in a sanded finish to make it less slippery when wet.
At resorts with large Olympic-sized pools, some of our clients have made use of our darker pool tiles to indicate the swimming lanes. These lines never have to be repainted like conventional swimming lane indicators. Our tiles don't need to be sealed and have zero maintenance after installation.
We look for stones that are chemically suitable for both chlorine and salt water pools.
You’d have to travel far and wide to find a range of decorative flooring solutions more unique, durable, or aesthetically pleasing than that offered by Technical Finishes.
Fortunately, you don’t have to! To experience and evaluate our remarkable tailor-made floors first-hand and in situ, you need only step into some of our country’s top international airports, most luxurious resorts, and foremost fine-dining restaurants.
Ready to design a jaw-dropping fingerprint floor? Simply join forces with one of our friendly and knowledgeable experts, and take inspiration from our vast array of colours, textural finishes, and protective materials.
If you can imagine it, we can achieve it.
Africa’s leading supplier and manufacturer of tailor-made, specialist epoxy and polyurethane flooring solutions for the industrial, commercial, and residential flooring markets nationwide, launched a new flagship concept store in George, in partnership with a local entrepreneur from Wess Turnkey Residential and Commercial Projects.
The city of George on the Garden Route, previously a safe haven for retirees, has in recent years become increasingly attractive for younger families who are semigrating to the Cape from Gauteng, KZN, and the northern provinces. The close proximity to a Category Eight airport enables these families to enjoy a slower-paced lifestyle with added security for their families.
The commercial and industrial markets have seen significant growth in new business ventures and professional practices started by many of these semigrants, boosting the local economy. Our customers are often at the forefront of finishes and decorative trends, and being in the position to offer them such a vast range of industry-leading products will no doubt simplify their bulk ordering and contribute to their ongoing success.
At Wess, you will find a full range of our industry leading epoxy and polyurethane flooring products all under one roof, including some of our flagship products such as Polyscreed GHF Terrazzo, NanoScreed, Liquid Stone, and the highly decorative Metallo. These unique flooring systems deliver value beyond the aesthetics, and are a smarter alternative to mundane cement floors and costly tiles.
From the high-traffic floors of food and beverage facilities, hospitals, warehouses, and shopping centres, to the stylish floors of modern lifestyle estates and contemporary living spaces, we surface them all. And you’ll find our extensive range of corrosion protection and composite solutions hard at work in mines, factories, and construction environments.
www.technicalfinishes.com
@technicalfinishes
FLXfinish+ technology on Colorado printers allows you to produce premium quality prints that feature a soft, velvety matte finish suitable for interior décor applications, or a dazzling glossy finish that's perfect for displays and packaging. Moreover, you can now print both matte and glossy finishes simultaneously in a single print at no additional cost.
With FLXfinish+ on Colorado printers, you can print high-quality applications with a velvety matte finish for interior décor applications or a brilliant glossy finish for displays and packaging. You can now also print matt and glossy in a single print job at no extra cost.
https://canon.sm/flxfinishplus
BREAKTHROUGH TECHNOLOGY
• Print matte and gloss together in one print
• No need for an extra varnish channel and printhead
AUTOMATION
• Unattended printing
Breakthrough technology
• Reliable industrial quality with remote monitoring app
• Print matte and gloss together in one print
• Perfect registration (same pass printing)
• No need for an extra varnish channel and printhead
IMPROVE YOUR BOTTOM-LINE
• Top high margin applications
• Unattended printing
• Easy file preparation, simple workflow
• Reliable industrial quality with remote monitoring app
• Standard on Colorado 1650, optional for Colorado 1630, upgradable for existing customers
Improve your bottom-line
• Perfect registration (same pass printing)
• Easy file preparation, simple workflow
WIDE APPLICATION RANGE
• Add the wow effect in interior decoration
• Top high margin applications
Standard on Colorado 1650,
• optional for Colorado 1630, upgradable for existing customers
• No costs or maintenance for special printheads or special substrates
• substrates
No costs or maintenance for special printheads or special
• Maximize your unboxing experience with mindblowing packaging
Wide application range
• Add the wow e ect in interior decoration
• Make your brand stand out from the crowd in retail
• Maximize your unboxing experience with mind-blowing packaging
Make your brand stand out
• from the crowd in retail
As a practising architect, I am interested in making. Making architecture is a complex, large-scale, drawn-out, and highly collaborative process, and perhaps for these reasons — i.e. architecture’s un-immediacy and mediatedness — architects tend not to think of themselves as ‘makers’. And yet, architects are makers. Making informs unique ways of thinking; for makers, the value of making is less about problem-solving than problem-finding. Makers learn through making. Making is research. How buildings are made, get made, and could be made, are questions central to that research.
Architects are in constant dialogue with the materials and processes of making. Materials and processes are never neutral; they’re bound up in economics, culture, and politics. A given material, say a brick or thatch, may take on a new nuanced meaning in each different context where it’s employed. How we build says something about who we are. Architecture produces culture.
Architects are generalists — we know a little about lots. Material science, craft, and engineering are key elements in making architecture. But whilst our creations rely on the rigours of the sciences, we are, at best, amateurs in these disciplines. Architects consult with specialists for expertise, but a degree of naivety is not necessarily a drawback — it serves us in some ways, allowing for speculative leaps unencumbered by the tyrannies of empiricism. Sci-fi is often a precursor to science.
Creative dialogue — exchanging ideas, asking ‘What if?’, courageous listening — gives us powerful tools for social transformation. Architects have a unique ability to imagine realities beyond the constraints of the present. We are society’s imagination engine. We are skilled collaborators, good at navigating the complex conversations of multiple stakeholders, able to reconcile the big picture with the details. Architects (worthy of the title) are Spatial Activists.Corner Fox, Johannesburg. Photograph courtesy of Dave Southwood Great Primary Shapes House, Johannesburg
Taking a walk around our city, one notices many building products previously manufactured in South Africa that are no longer available. From reeded glass and clay breezeblocks, to channel glass, terrazzo stair treads, linoleum flooring, lightweight concrete mouldings, trowelled-on renders, and asphalt shingles — for one reason or another these are no longer made here. Product ranges have shrunk. There is an epidemic of homogenisation in our built environment. Perhaps cut-and-paste laziness, perhaps sheepish convention, perhaps faddish biases have led architects to unwittingly contribute to the worrying atrophy in the range of materials available to us. As the specifiers of materials, as influencers of taste, architects must shoulder part of the blame.
The market is Darwinian — demand determines supply. Specify or it will die. The aesthetic enrichment of our built environment notwithstanding, there’s an obvious economic growth and employment angle here too. How to reverse this depressing trend? We desperately need to reenergise the country’s ailing manufacturing sectors — who better to inject a boost of innovation moxie than architects? My own practice is heavily engaged with local manufacturers on product development ideas. (And I encourage my students at the Graduate School of Architecture at the University of Johannesburg, where I teach a unit titled ‘Methods and Materials’, to do the same.)
These are the broad interests of my own architecture practice; we experiment with emergent building methods and materials. We encourage brave, imaginative leaps into future tectonic and spatial possibilities. We tease out subtle twists in traditional techniques and forgotten technologies. We borrow and adapt from other making disciplines. We learn through making.
GREGORY KATZ Director and Professional Architectwww.gregorykatz.co.za
@gregorykatzarch
material as a PROCESS, not a PRODUCT
Architects seem obsessed with building new. On the other hand, it’s no secret that the most sustainable way to build is not to build. With this knowledge, as an industry, we have a responsibility to invent new methods of making that shift our thinking around why we build, how, and with what.
What would happen if our material choices were governed by foraging instead of fabrication, and by what is available instead of what we can afford? Could we throw away the catalogues and off-the-shelf schedules and instead look to invention, creation, and craft as the means to shape a new and more sustainable future for our built environment? For the last six years, we have dedicated a third of our studio practice to try and find out.
Fresh out of university in 2016, the MAAK opened shop with an experimental design+build agenda. From day one, we were adamant on forging a new space in our industry for explorative thinking and alternative architectural outcomes. We wanted to promote and create:
• A return to making, where materials are given as much agency as the architect.
• A space free from convention and the numbing worry of ‘consequence’.
• An opportunity to make mistakes while ‘learning-through-making’.
All of this energy was channelled into our annual design+build programme called ‘Follies in the Veld’ (FITV). Each year we collaborate with willing participants (architects, doctors, farmers, food activists, etc.) to explore the spatial potential of alternative building materials. Without a handbook or any precedent to follow, FITV is a testing ground for the studio to explore new means of architectural pedagogy and new ways of making. ‘Design-roulette’, ‘smell chambers’, ‘wild cards’, and ‘charrettes’ are the order of the day, as we fundamentally ask ourselves:
‘What do materials want to be?’The Futuro Pronto pavilion (in collaboration with Space Saloon) in the context of the industrial shipyard it was born from. Fano, Italy.
In the pursuit of uncovering unique material intuition, we explore the idea of ‘The Thinking Hand’ and prioritise play and prototyping over computer programmes. Over the years, the studio has birthed a vibrant collection of hands-on spatial experiments that have helped us to see the value of engaging with material as a process rather than a product.
Seven years ago, we built a top-hung building that considered whether the experience and form of a space could be shaped by the elements (i.e. sun, shadow, wind, etc). In 2017, ‘Hanging Delight’ explored the untapped potential of Agave as a lightweight timber resource. 2018 saw us build with hundreds of locally sourced (within a twokilometre radius) glass bottles and mud harvested from a nearby riverbed. And in 2019, we worked with Tetra Pak overruns to give new life to an unused public space in Langa, Cape Town. Although all of these explorations were short-lived in physical form, they provoked thoughts and lessons that are still very much alive in our studio today.
A hands-on approach to architecture has made us question widespread (and outdated?) material conventions, and kept us curious about new ones. More recently we have teamed up with the international design studio Space Saloon with this as a focus. Last year (2022), our two studios were invited to Fano, Italy, to imagine new architectural narratives for its rapidly changing port area (which is becoming less industrial and more social/pedestrian).
"INSTEAD OF SOURCING NEW MATERIAL FROM CATALOGUES, WE USED A METHOD OF URBAN MINING TO HARNESS THE RICHNESS OF FORMS, TEXTURES, AND INTELLIGENCE ALREADY PRESENT ON SITE."FITV (in collaboration with Our Workshop and Amy Rusch). Close-up detail of Tetra Pak tensile structure and building components, Langa, Cape Town. Photograph courtesy of Elena Balestri
Instead of sourcing new material from catalogues, we used a method of urban mining to harness the richness of forms, textures, and intelligence already present on site. We gathered materials that were on hold, surplus stock, and found objects (all within walking distance from our site), and used them to inform unique building components and new material gestures. These contributed to an explorative pavilion structure we titled ‘Futuro Pronto’ (meaning ‘The Future, Now’), which stands as a provocation towards the potential of hyper-contextual building aesthetics and the value of simply building with what you’ve got.
ASHLEIGH
KILLA AND MAXIMILLIAN MELVILL Co-Founderswww.themaak.co.za
@the.maak
Both FITV and ‘Futuro Pronto’ form part of an evolving body of work that advocates for rethinking the role of resources and agency in architectural production. It prompts us to re-learn an architecture of availability that looks at found objects and building rubble in the same light as milled timber or standardised steel. It ultimately asks, if the materials around us have shaped the form of ancient vernaculars, how can today’s found materials (including waste) help invent new ones?
Futuro Pronto (in collaboration with Space Saloon). Assembling building components out of found materials, Fano, Italy. Photograph courtesy of Danny WillsClay brick is nature’s solar battery, keeping indoor temperatures comfortable without air-conditioning or heating. With timeless appeal, impressive strength and maximum fi re resistance, clay brick complements all architectural styles and materials, creating eco-friendly, long-lasting, low maintenance homes.
CBASA represents clay brick & paver manufacturers across Southern Africa. We drive inclusive, sustainable practices in the industry while supporting our local producers, builders and architects.
BUILDING TOWARDS AN ARCHITECTURE OF EXPLORATIVE DIVERGENCE
NOT JUST ANOTHER BRICK IN THE WALL
The School of Architecture at the University of the Free State introduced a new practice-based PhD with specialisation in design in 2018; a first for South Africa and the continent. What differentiates this programme from a conventional PhD, is that the candidate must demonstrate findings discovered in their oeuvre, distil the essence of their work to transform their practices, whilst crowning the research with an exhibition. In my case, three core divergencies (curation, sculpture, and cinematic architectural choreography) were the lenses used as practical application of explorative divergence (E-D). The theories of narrative depth and propositional density buttressed the study.
Whilst walking to work one morning and questioning why I was pursuing my PhD, the infamous lyric written by architecture dropout Roger Waters of Pink Floyd popped into my head: ‘We don’t need no education’. When the song was released in 1979, it was banned in South Africa under the strict censorship laws of the time. My friends and I, however, obtained pirated cassettes and listened to the line ‘We don’t need no thought control’ on loop. While the first few lyrics were of no help (albeit explorative divergence is open-ended), my ‘Aha!’ moment was sparked by the title. This catalytic thought made me take a closer look at the brick: can a mundane brick or brick composition articulate our work?
Bricks curated as metaphors for recurring themes in our work include:
The following example illustrates (1) the curation of in-between spaces, (2) the notion of randomness, and (3) the composition of facades, of buildings designed for art, and of building complexes.
Mathews + Associates Architects
www.maaa.co.za
@mathews_associates_architects
When one considers the brick as (1) building block, (2) door stop, (3) paper weight, (4) protest weapon, etc., its propositional density becomes quite high. We aim to increase propositional density in our designs. E.g. a retaining wall can simultaneously act as a podium, planter, stairs, seating, and much more. What if a brick is placed on a pedestal and curated as part of an exhibition? Louis Kahn supposedly remarked, ‘Even a brick wants to be something.’ My thesis topic, explorative divergence, led me to the epiphany: my exhibition would be more than ‘just another brick in the wall’.
The collection I identified and categorised three types of bricks for the exhibition: autoethnographic, theoretical (narrative depth and propositional density), and interpretative. This specific interpretative brick represents and alludes to the sculptural quality of our work.
Clay brick compositions became metaphors illustrating the recurring themes discovered in the oeuvre of Mathews and Associates Architects. These themes were extracted from my three selected core competencies: curation, sculpture, and cinematic architectural choreography. These divergencies show how tacit knowledge has informed our oeuvre and opened a way towards an architecture of explorative divergence.
The serendipity in this discovery is that I collected bricks on all my travels and even collected sculptures referencing bricks, not to mention that bricks were ubiquitous during my walk, surrounding me on all sides on route to the office. The brick exhibition made perfect sense, as it was adhocist to the core.
A reverse touchstone
The purpose of this object or light is to summarise the exhibition with one object.
During our raw-brick carving workshop
I created a lamp that encompasses several of the theoretical concepts and divergencies as well as the core competencies explored in this study. The brick lamp was designed to be a functional object and sculpture in one, fulfilling the notions of narrative depth and propositional density. The unfired bricks were supplied and fired afterwards by Corobrik.
EMERGING BIO-BASED MATERIALS
It goes without saying that with rising global environmental awareness, more scrutiny has been placed on industries to utilise sustainable practices. Within the construction industry alone, there is an increased emphasis to utilise alternatives materials that have a lower environmental impact than traditional materials, such as the ubiquitous concrete.
Emerging bio-based materials have garnered much attention, spurred on by this heightened sustainability focus — particularly the need to reduce global CO₂ emissions. Unlike conventional bio-based materials, such as wood, emerging bio-based materials are contemporary materials that are partly or wholly made from substances derived from living organisms, and typically undergo bio-catalysis (the use of living systems or their parts to speed up chemical reactions). These materials are active subjects of current research and development, and breakthroughs in their possible applications are regularly occurring.
At the forefront of emerging bio-based materials is mycelium — the thin, root-like fibres of fungi found in and on soil and other substrates. Mycelium acts as a ‘glue’ using a complex web of fibres to bind substrates such as sawdust, ground wood, straw, agricultural residues, or similar substances that might otherwise be discarded. Mycelium-based blocks are made by combining mycelium and a chosen substrate into a solution that is transferred into moulds. The solution is left to grow in favourable conditions (adequate temperature, humidity, and light) for about five days before it solidifies into a sturdy material. It is subsequently removed from the mould and placed in an oven to terminate any living microorganisms and prevent any further growth.
Depending on the mycelium strain, growing conditions, and the composition and structure of the substrate used, the final mixture can be moulded to produce insulation panels, furniture, accessories, fabrics, packaging material, and blocks. The physical characteristics of mycelium-based material are similar to polystyrene, but with improved biodegradability. These blocks exhibit good thermal and acoustic properties as well as water, mould, and fire resistance.
Then there is hemp. Hemp is a cultivated variety of Cannabis sativa and has a negligible amount of tetrahydrocannabinol (THC) — the substance responsible for feeling 'high' when inhaled or consumed. The misinformed, negative association with the very high THC content of ‘marijuana’ has hindered the adoption of hemp into mainstream industries. But as public opinion around cannabis softens and countries around the world, including South Africa, review and loosen their legislation, hemp and its many possibilities are being explored with fervour. Hempcrete is one of these possibilities. It is made from the woody inner parts of the actual hemp stalk called the ‘hemp hurds’. This is broken into fragments, removed of impurities, and mixed with a lime-based binder and water. This mixture can either be cast in situ or placed in a mould, where it is left to harden into a lightweight block or sheet. Like mycelium-based material, hemp-based material is biodegradable, has good thermal and acoustic properties, and is water, mould, and fire resistant. Furthermore, it is carbon negative as it removes and stores more carbon from the atmosphere over its lifetime than was used in its production and use. Cape Town will soon boast the tallest building in the world made with hempcrete: the 12-storey Hemp Hotel on 84 Harrington Street.
Despite the promising developments within emerging bio-based materials, greater economic incentive is still required for their wide-spread use in our cost-driven society. Conventional building materials such as clay bricks and concrete are still cheaper in comparison. Moreover, emerging bio-based materials usually have load-bearing limitations, and therefore a conventional frame (using conventional materials) for structures is still required. Then there’s also the questions around the scalability and regulation of such novel materials within the construction industry.
Looking ahead, we’re in for an exciting decade where emerging bio-based materials are constantly being researched, tested, and implemented, which includes explorations with banana fibre, cork, and straw (just to name a few). What started off experimental is gradually shifting into the viable, common use of environmentally conscious construction materials.
RUTH MANDA Landscape Architect www.greeninc.co.za @greeninc.laOSRAM LED DAYLIGHT SENSOR LAMP
ENERGY SAVING, LONG LIFE TIME
• Energy efficient with automatic switch off at daylight function
• Security function with automatic switch-on at night
• Very long lifetime of up to 25,000 hours
• Low energy consumption
Earth and lime plasters have historically been used for thousands of years in ancient China, India, Mesoamerica, Greece, and Rome. Locally, in Southern Africa, earthen plasters are still widely applied in many rural communities, and cow dung is often added to reduce cracking, add strength, and provide waterproofing.
Lime was traditionally used to plaster the early European settler buildings, when available. Otherwise, earthen plasters were simply limewashed on a regular basis. That said, earthen plasters, while easily replenished, are less durable, and therefore prone to increased maintenance. So, depending on availability and affordability, lime plasters were used for greater durability.
Recently, lime plasters have come back into fashion after being recognised for their importance in natural building and heritage restoration work. Given their hydroscopic qualities and ability to breathe, respectively helping to regulate moisture and indoor humidity, they are highly recommended for all walls made of unfired earth or straw. For these kinds of projects, particularly heritage buildings, cement-based plasters are far too rigid and tend to crack while trapping moisture inside, causing the walls to disintegrate and the plaster to delaminate.
Lime plasters can be used to create beautiful natural finishes that age gracefully.
Instead of giving a flat even colour, lime plaster finishes are somewhat varied and lively, with an imperfect handmade quality, which can be highly aesthetically pleasing. The result is that they can handle a hand mark or scuff here and there without much notice, and therefore require less maintenance than conventional finishes, which tend to look dirty much more quickly, and, in the case of schools, can look like they need a new coat of paint the day after opening.
Lime production requires less industrial processing and energy to produce than cement. And unlike cement plaster, any wastage or leftover mix can simply be covered and used the next day, which reduces waste and mitigates the environmental impact of construction.
A setback with using lime is that, while it will continue to harden over time, it is initially much softer than cement and takes three times longer to cure. Therefore, its use requires careful site programming and provision for initial added protection. Furthermore, lime tends to be fussier to work with and tends to crack and weaken more easily with exposure to sun and wind during construction. For this reason, one often finds that various additives are included in lime plaster recipes to improve the mixture's workability and ensure proper curing.
‘Lime dung plaster’ is a very specific mix that I learned from an old builder, Herbert Arense, who was taught by his grandfather (also a builder). I’ve since gone on to use it successfully in many projects, both for natural buildings and conventional clay fired brick walls.
The recipe originates from Mamre, the site where I worked on a heritage revitalisation project and one of the earliest settlements in South Africa. The majority of the town’s original old mud brick buildings are plastered with a lime-sand mix, including a small amount of clay and fresh cow dung. Cow dung naturally contains both fine fibres as well as casein, which react with the lime and improve both its quality and workability — the reason why cow dung is considered one of the best additives to use.
Straw is an annually renewable agricultural by-product that is often laid to waste and sometimes even burnt by grain farmers. Historically it has been used as a building material for thousands of years, typically used to make cob, moulded into bricks and baked in the sun, or added to mud plasters to increase strength and reduce cracking.
Due to its highly insulative properties, builders in colder parts of the world use mostly straw and only a little bit of earth to bind it together. Known as Light Clay Straw it is used non-structurally as an in-fill material where it is usually mixed on site, poured between shutters, and then lightly tamped around a lightweight timber frame structure. It can be used for both internal and external walls as well as for ceilings.
Since the industrial age and the advent of the baling machine, people started building with straw bales, which can be used for load bearing or as an in-fill material to make beautiful, thick, super insulated walls (R value = 6-7 K.m²/W).
Building with straw is relatively easy to learn and lends itself to self-builders and community involvement. Straw offers extremely high levels of both thermal and acoustic insulation, even for relatively thin light clay straw walls.
Due to its exceptional insulation and compacted manner, it’s highly fire resistant as it prevents the spread of heat and doesn’t have enough oxygen to support combustion.
While one can build with bales as a load bearing material, this is less common and typically frowned upon by local authorities. Therefore, bales are mostly used non-structurally as an in-fill material, which typically requires the use of more timber.
Bales are fast to build with, but the light clay straw mixture panels, once cast, usually take at least two months to cure properly, and so this needs careful programming on site. Unlike conventional materials, which generate large amounts of construction and demolition waste, straw can simply be mulched for landscaping purposes.
Straw is susceptible to moisture, making it crucial to use breathable plasters and finishes so as to not trap moisture inside the walls. It also requires a good overhanging roof to provide protection from above, and a raised masonry plinth to lift the walls away from the ground, as well as meticulous detailing, particularly around openings.
Despite international building codes and countless local building council approvals, our banks still require an NHBRC building registration for any new homes or homes that are less than five years old that do not accept these highly promising building methods. This forces homeowners to go the cash build route or limits the material’s use to non-residential buildings.
Historically, planted roof structures were common in the extreme climates of Scandinavia, where their thermal stability helped to provide much-needed insulation. More recently, they have become very fashionable with environmentally conscious design, and in countries like Germany it is now compulsory for all public buildings to either have solar or planted roofs.
Planted roofs are visually unobtrusive and can be highly aesthetic, helping to integrate buildings within their landscapes while providing habitat for nature that would otherwise be lost to the site with conventional roofing material. They also help reduce the carbon footprint of construction by maintaining the carbon sink of the site and its topsoil.
At the urban level, they are very effective at reducing the urban heat island effect of developments, making them ideal for hotter climates. Green roofs help to clean and cool the incoming air, thereby reducing the air conditioning load on buildings. They also reduce the pressure on storm water systems by slowly absorbing and releasing water, proving a great asset for flood control.
Roof pitches are typically quite shallow, though they can be built steeper depending on how they are detailed. In order to build lighter, thinner roofs, we use shallow, rooted local species of bulbs and succulents, which are also extremely hardy and require minimal maintenance once established.
Locally, planted roofs help with long-term maintenance by reducing the heat load on the roof, eliminating the temperature extremes, and preventing the continual movement that roofs are normally subjected to, whilst protecting the waterproofing layer from harmful UV rays.
Plants also absorb pollutants, cleaning and revitalising the air around buildings with beneficial negatively charged ions. And, together with the ‘biophilic’ effect, they help to promote healthy building environments.
Being heavier than conventional roofing material, one often sees planted roofs supported on a waterproofed concrete roof structure. However, traditionally these roofs were always built on timber roof structures, and from an ecological building perspective, it is far more sustainable to build with timber, which is how we have built all our new planted roof structures. This simply requires waterproofing, a timber boarded roof deck, and some meticulous construction detailing.
ANDREW HORN Director and Principal Architect www.ecodesignarchitects.co.za @ecodesignarchitectsInternal cabin size: 40 m²
Deck size: 22 m²
Completed: 2022
Location: Hoekwil, Wilderness, Garden Route
Escape to Nima Lodge’s enchanting Sand Cabins, a trio of timber hideouts in the heart of the Garden Route. These undulating cabins are a testament to sustainable design, crafted from locally sourced materials to create a harmonious balance between modern luxury and the raw beauty of the natural world. With comfort at the fore of every contoured slope, the rhythm of this verdant land is the only soundtrack you'll ever need.
Environmental focus
Wilderness and the greater Knysna area have a rich history of timber construction. We wanted to respect this tradition, and therefore decided to construct the three new cabins out of similar locally sourced materials, such as South African pine. Since it’s local, the material has a low travel carbon footprint. It is beautiful, grows fast, is a renewable resource, lightweight, and easy to work with, meaning the builders are less in danger of injury during construction. Timber can easily be recycled or reused, minimising wastage and preventing the material from ending up in landfill.
The cabins were built on timber poles (with reduced concrete and steel as foundations), allowing them to float above the landscape causing minimal interference to the existing vegetation. Just like we all will, the timber exterior of the cabins will gently age over time to become a beautiful silvery dark grey.
The Nima Lodge cabins, at once contextually relevant yet reinterpreted, are the first buildings Stretch Architects did entirely out of timber; therefore, we needed to find the perfect contractor for the job. If it was not for Knysna Timber Homes’ knowledge and experience, the project would never have turned out the way it did. This project again proves the importance of collaboration.
Architect: Stephen Hitchcock and Dave Long, Stretch Architects
Interior designer: Nima Lodge Interiors
Contractor: Knysna Timber Homes
Landscape architect: Honiball Architecture
www.stretcharchitects.com
@stretch_architects
The shape of the Sand Cabins is a direct response to their context and intended use. These timber hideouts are essentially little love nests, and privacy was a big driver in determining the footprint of the cabins. The V shape of the plan does three things: it frames and embraces the endless views and sun towards the north; shelters the cabin and deck from the wind, while also promoting privacy between the units; and makes you feel safe and immersed in your own world.
We wanted the entrance to the cabins to be a bit of a mystery. The door is tucked in between the toilet tower and the bedroom platform, and is purposely designed to be as heavy as possible to emphasise the feeling of safety and retreat once you arrive and close the door behind you. Upon approaching the cabin, guests see nothing but a series of curved timber walls with no windows in them. However, once you open the door and enter, the opposite happens... The solidity of the rear wall is replaced by the transparency of the front, allowing the breathtaking panoramas to rush in to meet you.
The Nima Lodge cabins are designed to celebrate the rituals of everyday life. At its core, the three new Sand Cabins are shaped by the multiple attempts to best marry the incredible natural surroundings with the rhythms of sleeping, reading, bathing, cooking, and so forth.
From the sunken bath to the toilet tower (with one of the best views imaginable), every element brings a touch of ease. The bed, which is raised and elevated above all the other spaces, expresses this concept the best. Despite the cabin’s small square meterage, by creating multiple level changes through ‘stepping each activity to the next’ we created a volume where everything feels like a journey and each space becomes its own little world. For example, transitioning from the kitchen area to the bed, you step down from the bathroom into the shower and into the bath in a convenient flow of movement.
The project took about two years from start to finish. Covid-19 played a big role in shaping the final iteration of these cabins. The tourist industry was on its knees, but this forced us to distil the project down to its essence by including only what was important and necessary to the design. This period gave us time to let the ideas evolve and grow into what they needed to be. It is not often that you have the luxury of time as an architect.
It takes a good client to make a good building. From the beginning the client wanted the cabins to be beautiful (she never compromised on this), and to celebrate and share the incredible location with future guests in the most honest and special way possible. We wanted to create a building that is considerate of place and people, and we think Nima Lodge’s Sand Cabins capture the appeal of both.
South Africa’s largest stockist of speciality timbers. We are proud suppliers to the finest residential, commercial and leisure projects across South Africa and neighbouring countries. We love to get involved early in your project and be on hand to offer expert advice as your vision unfolds.
Size: 650 m²
Completed: December 2022
Location: Elephant Point Private Reserve, Kruger National Park, South Africa
Nestled within the pristine wilderness of Elephant Point private reserve (part of the Legacy Hotel group) alongside the majestic Sabie River, Tembo Tembo Lodge is a stunning architectural masterpiece that seamlessly blends with the natural environment. With its solid rammed earth walls, natural interiors, and unobstructed views of Kruger National Park, this luxurious retreat offers an unforgettable bush experience in true South African safari style.
The site called for a building that would be in harmony with its natural surroundings rather than stand out and overpower the bush. The client’s brief was to create a uniquely architectural lodge that would marry an authentic bush experience with luxury comfort levels and a contemporary design aesthetic. The client wished for us to create a user-friendly space that a family could enjoy as a ‘home away from home’, whilst still being a contemporary experience. As such, we were tasked to create something different from the other offerings in the area.
The lodge is a beautiful rammed earth structure designed by Nicholas Plewman Architects, with interior design by Paris-based Studio Asaï and landscape architecture by GREENinc. The architect conceptually designed the house as a series of solid boxes linked by open, glazed spaces. The solid ‘boxes’ house the more private, retreating spaces (such as the bedrooms, study area, and scullery), while the very lightweight, glazed spaces form the main communal living area (the lounge and open-plan kitchen), finally opening onto the deep terraces.
The main living area is enclosed by large cavity sliders that, when opened, disappear completely into the structure. This allows the house to open up to the outdoors, inviting the bush right into the living room.
The bedrooms, study, and lobby housed in the rammed earth boxes become cool, peaceful spaces sheltered from the intense heat of the area by the thermal massing of the rammed earth. With large sliding doors set in deep reveals, these spaces become almost like viewing hides, allowing guests to peruse the wildlife from the comfort of their own bedroom.
Client: Donald Kramer
Architect: Nicholas Plewman Architects + Associates
Main contractor: Nick Fry Construction
Engineer: RMCE
Rammed earth specialist: Simply Sustainable
Landscape architect: GREENinc Landscape Architecture
Interior designer: Studio Asaï
www.plewmanarchitects.co.za
@nicholasplewmanarchitects
Joinery
D&A Joinery White River
061 061 5268
Custom-made marble Marble Classic
011 392 6700
Granite Objects
0860 353 353
Timber floors Finfloor 011 262 2727
Polished concrete floors
Firmarox 071 213 9443
Lighting Tom Dixon, available at Crema Design
021 448 7775
Ingo Maurer
Pholc, both brands available at European Light and Design Centre
010 594 5131
Furniture Lemon Collection 011 262 4116
Créma Design 021 448 7775
Cassina, available at TRUE Design 021 418 5382
Carl Hansen & Søn 011 262 5257
Artwork
Amatuli Artefacts
011 440 5065
Rammed earth was chosen as the main building material due to both its practical and aesthetic properties. As a natural material, rammed earth speaks to the connection between the house and the surrounding bush. The earth used was sourced from land very near the site, meaning the house is built from the same material it stands on. Evoking pictures of termite mounds, traditional mud building technologies, and slowly eroded river banks, Tembo Tembo is a nod to strong landmarks of the bush.
Furthermore, rammed earth also has a practical function in its effective thermal performance. The walls, which are all at least 350 mm thick, create a thermal massing effect that allows the house to regulate its internal temperature naturally.
As with any building process there were challenges to be faced. The building process was interrupted by the Covid-19 lockdown in 2020, and continued to be disrupted throughout the remainder of the project. This contributed to a particularly long construction period as well as causing budget concerns with sudden increases in building materials.
We also had technical challenges to overcome. Tembo Tembo Lodge aimed to achieve a meticulous level of detail and finish, involving some elements of great technicality and precision. Rammed earth, being a completely natural material, has a certain level of unpredictability. In rammed earth walls, there will often be slight variations in thickness and straightness, especially in longer sections of wall. While this is the beauty of rammed earth, we had challenges in marrying this technology with some of the more precision elements, such as the large-scale cavity sliders.
Overall, the project construction was a challenging process, but one we were able to learn a lot from. We had an amazing team to work with who were all eager to find solutions and work together to create a building that is completely unique and pushes the boundaries of the rammed earth materials in its level of precision and detailing.
The landscape is subtle and restrained. Using locally indigenous plants only — mainly large container-grown trees and carefully-selected grasses, but also some bulbs and flowering plants — the landscape nestles the lodge comfortably into the surrounding bushveld. Polished concrete steps were designed to lead to the front door, matching the interior floors, while sand was used for the driveway and pathways for low impact, both visually and environmentally.
Geberit SuperTube is the innovative technical know-how for hydraulically optimised drains in high-rise buildings. Ingenious, flow-optimised technology creates a continuous column of air in the discharge pipe, meaning a parallel ventilation pipe is no longer necessary. What’s more, the horizontal pipelines can be laid to a length of up to six metres without a slope, giving you more usable, uninterrupted floor space.
Everything an efficient drainage system needs
With its maximum discharge capacity of 12 l/s and a consistent pipe diameter of 110 mm, Geberit SuperTube offers a comparable performance to a conventional system with considerable reductions in space and material requirements.
Next-level HDPE Sovent fitting
The Sovent fitting offers a space-saving solution for high-rise buildings by making it possible to do away with a parallel ventilation pipe. The Geberit SuperTube technology takes this concept one step further by eliminating the need for an additional ventilation pipe previously required for changes in direction.
Space saving installation
Geberit SuperTube saves space in every direction. The ability to do without the additional ventilation pipe reduces spatial requirements in both the vertical stack and in horizontal pipelines (with an offset or collector pipe, for example). This makes it possible to install ceiling suspensions extremely close to the concrete ceiling at an offset.
Fittings that put a whole new spin on things
Geberit SuperTube technology facilitates a consistent discharge pipe with a single pipe dimension. The technology is based on the perfect interplay between four system components. Three clever fittings, coupled with the high load-bearing, tried-andtested Geberit HDPE discharge pipe, create an innovative hydraulic solution. These components are permanently welded to ensure a tight connection in the long run.
www.geberit.co.za
Size: 1500 m²
Completed: 2022
Location: Vereeniging, Gauteng
From unstable soil to the Vaal’s scenic surrounds, this industrial plant is made from the very materials it manufactures. Read along to find out why this project by Local Studio has us singing, ‘Clay Sera, Sera!’
Site context
The National Ceramic Industries South Africa (NCISA) industrial plant is located in Vereeniging, within a cultivated nature reserve on the eastern portion of the site. However, this picturesque site had highly unstable soil conditions, made worse by an adjacent dam. Therefore, the new building replaced a previous building that was condemned due to excessive structural cracking.
Building brief
NCISA is the largest ceramic tile manufacturer in South Africa and one of the largest in the world, forming part of Italtile Ltd. (which is listed on the Johannesburg Stock Exchange). The brief called for a new exhibition area to display the various products that are produced at the factory, as well as new offices and meeting rooms for administrative and executive personnel.
The client required that the building should incorporate as many products as possible that were produced or supplied by the broader Italtile Ltd. Group, which includes CTM, Italtile, U-Light, Eezeetile, and Easylife Kitchens. The brief also called for an extensive landscape design, including a new meandering footpath connecting a series of pause spaces around the perimeter of the building.
Overcoming obstacles
The most challenging aspect of the project by far was the requirement to grant local business forums important finishing packages, such as tiling and paving. Local labour procurement remains the biggest challenge we face on building sites in South Africa.
Material selection
Most material specifications happened collaboratively with the client. The most striking aspect of this collaboration is the porcelain tile cladding on the southern wall of the building, which was produced in a factory on site.
The site was an important design informant in the project, allowing us to orient the building to maximise the best natural light and ventilation while optimising views of the dam and mountains beyond. The client allowed for a substantial landscaping budget, which we made use of to create a number of paths and pause areas around the building. The new pathways also function as stormwater channels to take water away from the building and to protect the structural foundations.
Architect: Local Studio
Quantity surveyor: Kaofela
Structural engineer: Frik Steynberg
Electrical engineer: Parima
Main contractor: Tristar Construction
Landscape designer: RS Interiors & Exteriors
Landscape contractor: Albert Hoof
Photographer: Dirk Jacobs
Silver birch (Betula alba) trees were added as a vertical visual element, but were kept intentionally close to the building as not to block the view. Frost-resistant and drought-tolerant plants were specifically chosen, as down in the Vaal temperatures can plummet down to -3°C in winter mornings (with severe black frost), and rise to 38°C in summer.
The outdoor space is broken into geometric pockets, all interlinked by walkways to create a collective whole. The pathways were intentionally designed to offer employees and visitors a space to walk and stretch their legs between tea and lunch breaks and to enjoy the beautiful view of the dam and surrounding landscape.
A focal water feature central to the design of the garden was strategically placed just outside the main showroom to be enjoyed by visitors. Additionally, benches, a wooden deck area, and tables and chairs were added to sit down, catch a quick bite, or enjoy a cup of coffee.
Façade and floor tiles
Ceramic Industries
016 930 3600
Facebrick and paving
Corobrik
011 871 8600
Steel structure and sheeting
Fluted Steel Construction 082 556 8376
Lighting
Spazio, available at U-Light 081 011 1972
Aluminium and glass
Julies Glass & Aluminium 016 933 7563
Paint
Eezee Tile Adhesives 011 872 0627
buffer of clean air between fuel charges to purge the system efficiently. Clean air from the transfer ports first enters the combustion chamber when the ports are uncovered by the downward moving piston. This air (oxygen) joins the remainder of the exhaust gas being emitted via the exhaust port, reducing emissions by 60%–80%.
The result is ground-breaking, with high torque over a wide speed range, fuel consumption cut by up to 20%, and exhaust emissions reduced by up to 50% when compared with conventional STIHL two-stroke engines without 2-MIX technology.
Add reliability and the trusted STIHL brand name, and it makes perfect sense to use STIHL machines with 2-MIX technology...
STIHL’s revolutionary 2-Mix technology ensures that fuel is used in a highly effective way, delivering more power with reduced emissions — kinder for the user and better for the environment. It also offers savings on fuel — always a win!
A proven example of the fuel-saving benefits of 2-Mix technology is the new STIHL FS 235 brushcutter. Designed to cut thick grass, weeds, and vegetation, this professional-grade, high-powered 1.55 kW model is impressively light on fuel.
Duncan Fryer of STIHL SA says, ‘If you consider that a standard machine with a conventional two-stroke engine could consume on average five litres of fuel daily, while the FS 235 would potentially only consume four litres of fuel for the same amount of work, that’s a saving of around a litre of fuel every day. For professional users, that makes a significant difference!’
The STIHL two-stroke power unit with 2-MIX technology offers impressively high engine power plus excellent power-to-weight ratio and outstanding torque development over a wide speed range for high cutting performance. Despite its powerful action, engine emissions are very low and comply with the strict limits of the EU Emissions Directive.
A 2-MIX engine is a two-stroke engine that replaces unburned fuel, which would have been emitted via the exhaust during the transfer process, with fresh air. To achieve this, an additional ‘fresh air’ port is added on both sides of the inlet manifold, between it and the transfer ports. Essentially, the air induction system introduces a
www.stihl.co.za