
3 minute read
Pre-Commercialized Innovation: Ardagh Group
Our inaugural Pre-Commercialized Innovation award went to Ardagh Group for its innovative method for giving new life to glass that is rejected during the recycling process. We spoke to Brendan O’Meara, Cullet Process Engineer for Glass Europe, Ardagh Group.
PE: Firstly, congratulations on winning the award! What does this mean for you?
BoM: We’re absolutely thrilled and proud to win the Sustainability Award for our glass briquette project, particularly with such strong competition. As this is a pre-commercialized innovation, our next step is to build the plant that will manufacture the briquettes, allowing us to recover 100% of recycled glass for remelt. Thanks to the judges for recognizing this achievement, and to Packaging Europe for organizing the competition and the professional virtual Sustainability Awards event – it was thoroughly enjoyed by all.
PE: Could you please introduce your successful entry and what’s innovative about it?
BoM: Ardagh Group has developed a method to produce briquettes from the fine particle glass rejected during the recycling process, allowing 100% of recycled glass to be remelted into new bottles and jars.
The goal of the project was to maximize cullet recovery for remelt, focusing on the small particles of glass breakage, or ‘fines’, caused during collection or produced during the recycling process itself.
These fines make up 10% of glass collected for recycling and are currently unusable in glass manufacture, because they contain excessive amounts of Loose Organics and CSP (ceramic, stone, and porcelain) which can create problems if they enter the furnace for remelt, causing blistering and inclusions in new containers.
Fines are typically diverted into road aggregate production or lost to landfill and will never be recovered for remelt: a ‘cradle to grave’ scenario.
Our research and development has culminated in the design of a processing plant to close the recycling loop by creating briquettes using 100% of recycled glass containers recovered through the various collection systems across the UK. The plant will be the first commercial type in the world.
PE: What are the environmental challenges in packaging that your entry addresses, and what impact do you hope it will make?
BoM: The whole glass packaging value chain is continually developing ways to reduce the emissions and environmental impact of glass manufacture. Using the briquettes to increase the cullet ratio in the glass batch recipe will reduce the need for raw materials, reducing energy consumption and CO2 emissions in the furnace, improving the circularity and thus the environmental impact of glass packaging.
The additional cullet available as briquettes will help to achieve the ultimate objective of 95% cullet and 5% raw materials within the glass batch.
PE: ‘Sustainability’ in packaging is multi-dimensional – both in terms of objectives and challenges. Could you comment on the most important roadblocks you identify from your position in the value chain, and the kinds of solutions you would like to see addressing them?
BoM: Industry-wide collaboration projects, such as the hybrid, oxy-fuel Furnace of the Future, are vital: sharing expertise and resources to replace fossil-fuel energy sources and cut CO2 emissions, to make glass production more sustainable throughout the world.
We would like to see more switching to renewable energy and improved energy efficiency of existing glass melting furnaces, processes, and plants as a whole, and more process innovation. Waste heat recovery through innovative technology such as Organic Rankine Cycle Engines is an important step in saving energy in the furnace by preheating the batch.
As a member of the container glass federation, FEVE, Ardagh is fully behind the ’Close the Glass Loop’ campaign, which aims to increase the amount of recycled glass collection from 76% to 90% across Europe which, again, will increase the glass cullet available for remelt, reducing energy and emissions in the furnace. n
©Ardagh Group
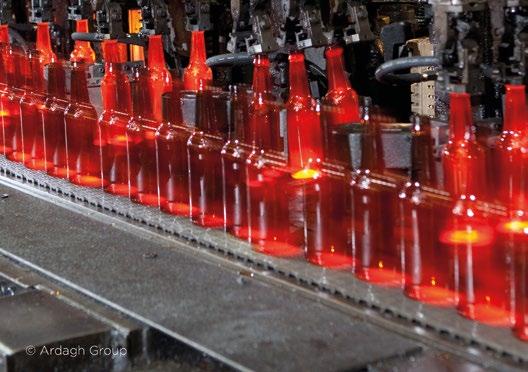

