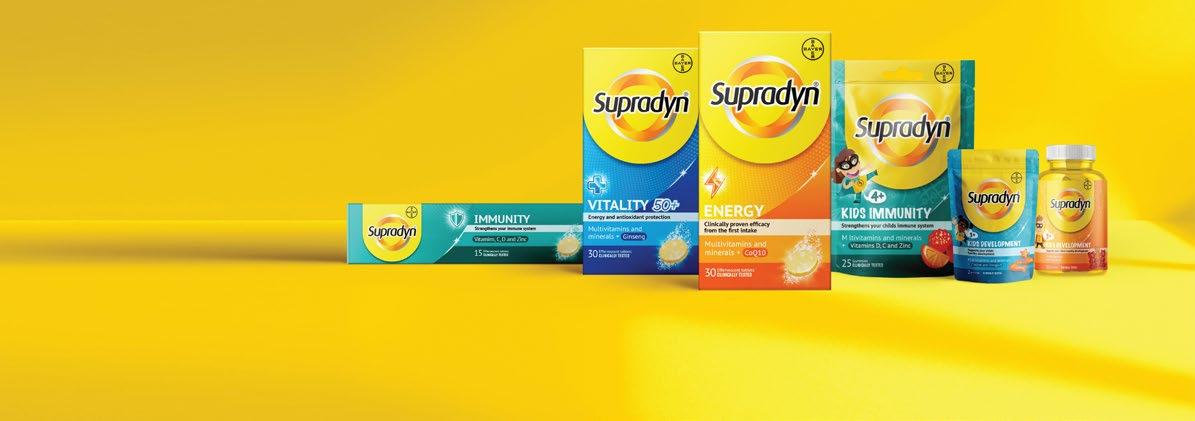
6 minute read
Revitalising vitamin branding
Revitalising vitaminbranding
By Amber Barrow, Account Director, Free The Birds
Advertisement
Design agency Free The Birds has created a new elevated look for Europe’s number one vitamin brand.
upradyn is the number one VMS (vitamins, minerals and supplements) brand in Europe and one of the biggest names in the Bayer Consumer Health portfolio. Established in 1959, the packaging design had become dated over time and was no longer communicating the efficacy consumers had come to expect. The brand’s current architecture was particularly hard for consumers to navigate.
Tasked with revitalising the design, Free The Birds created a simplified architecture and navigable creative system that united the design across all markets.
While we needed a global design approach, within the healthcare sector it is always important to consider the individual regulatory challenges that each market faces. We wanted to enable the brand to flex per market as needed, while retaining a strong and consistent overarching global design framework. The biggest challenge was how to modernise and really move the brand forward, whilst retaining the existing brandmark. It was important that the logo was still easily recognisable on shelf.
There were particular brand elements that were not to be touched. First and foremost, the Supradyn Yellow as the key brand identifier had to remain, as it was important that this primary colour association was not lost by consumers. Core to the Supradyn proposition are the three benefit pillars – our task was to better differentiate between these pillars to aid consumer selection. The new design was brought to life through a refreshed brand logo and engaging ownable brand assets that come to life off-pack. The new logo retains the circular cues; however, the graphic communicates a stronger sense of energy and movement, and the wordmark is hero-ed and proud, breaking through the circular holding shape. Whilst we ultimately reduced the amount of yellow on pack, we were able to create a stronger brand presence with the efficacious power button, positioning the brand yellow at the top of each pack to create a consistent brand block. This also allowed more real estate space for the background colour, enabling us to make the most of the pillar navigation on pack and to introduce graphic patterns to further support differentiation between the core adult and kids ranges.
There was also the perfect opportunity to further elevate the kids products through the creation of our new playful superhero characters, enabling the brand to utilise these assets to engage with kids on pack and digitally, through the brands website, and future campaigns.
What has launched is a bright and confident rebrand that has a clearly defined brand design system that can be flexed as Supradyn continues on its future growth journey.
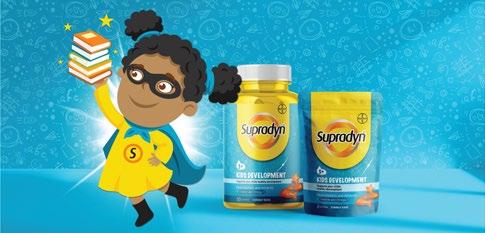
Reliable production support and fully automatic waste disposal
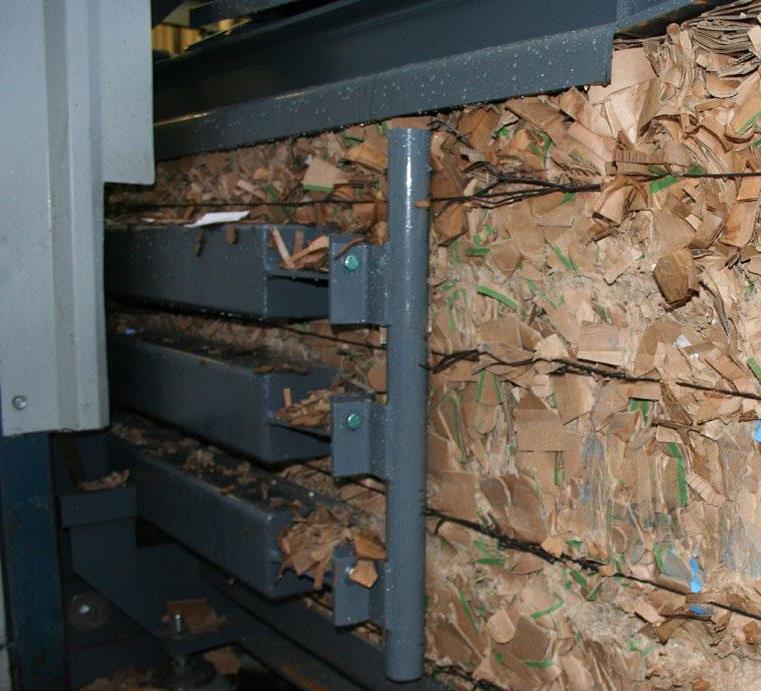
By HSM
WP Packaging is part of GWP Group Ltd, one of the leading and most versatile providers of packaging solutions in Great Britain. Customer specific product and transport packaging made of corrugated cardboard is developed and produced in its sphere of business. Innovative thinking is the central factor behind the work of the packaging specialist from Cricklade, Wiltshire. The most recent investments for the future include an HSM VK 4208 channel baling press from HSM, which fully automatically compresses and bales the waste die cut pieces ready for recycling.
GWP was originally founded in 1990 as The Great Western Packaging Company. The company has now grown to become a key player on the British packaging market and combines, under the umbrella of GWP Group Ltd, the five divisions of GWP Packaging, GWP Protective, GWP Correx, GWP Conductive and GWP Coatings.
GWP Packaging serves customers from the beverages and foodstuffs, medical, automotive and IT and electronics sectors with packaging made of corrugated cardboard, which in terms of design and characteristics is tailored specifically to the product and its application. James Pedley, Operations Manager of the division, explains, “Our task is to design packaging solutions which perfectly showcase the packaged good at the point of sale and protect it from transport damage. The main priorities in the process are cost-efficiency and environmental compatibility.” Priorities which are reflected in the sophisticated corporate processes at GWP Packaging.
Taking production as an example: Die cutting machines play a central role in the automated production process. They die cut cardboard sheets by means of cutting, punching and grooving into finished die cut cartons and fitments. “We design the punching dies so as to save as much material as possible and so that only small amounts of punchings, edge cuts for example, accumulate. We then return these to the recycling loop ,” explains James Pedley.
Since October 2013, this has been achieved with the fully automatic support of the HSM VK 4208 channel baling press from HSM. It replaces a long-serving baling press that could no longer live up to the modern production concept or the increased safety requirements.
Operating efficiency from production to disposal The new HSM VK 4208 has been integrated into the production process and operates by means of air feeding. The waste which occurs at several die cutting machines is extracted by suction while production is ongoing and taken directly to the channel
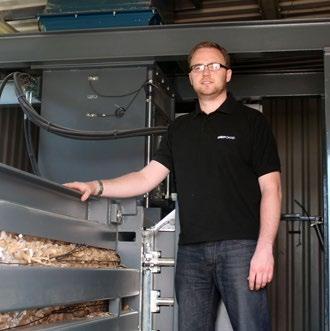
baling press to be shredded with blade ventilators into corrugated cardboard remnants.
According to James Pedley, the reliability of the press has an effect on the efficiency of the entire process. “If it fails, production comes to a standstill for us, so we cannot afford to compromise on technical quality.”
The Operations Manager regards the fully automatic operation of the HSM VK 4208 as another benefit. Where before he had to assign a man full time to operate it, the new channel baling press operates independently, so to speak. If it is full, a light beam triggers a horizontal pressing process.
The collected material is compacted into bales with a specific pressing power of 75 newtons per square metre and is then strapped automatically with wire. The bales weigh up to 420 kilograms. At GWP Packaging they are on average twice as heavy as they were with the old machine. This bale density and weight also impresses the recycling companies: they pay more than they did before for the recyclable waste die cut pieces – around 450 tons every year.
Professionalism from advice to maintenance GWP Packaging didn’t opt for HSM just like that. James Pedley took time to become acquainted with various suppliers across Europe and to compare technical options. Right from the start he was impressed by the professionalism of the advice from HSM as well as the flexibility with which the company could handle customer requirements. The performance and workmanship of the machines were the factors which finally convinced him. “You look at the HSM presses and you can literally see their high quality.” The delivery of the channel baling press in October 2013 confirmed his positive assessment: the narrow time window of a weekend was all that was available for the dismantling of the old machine and the commissioning of the new machine in a difficult to access area. But everything went
smoothly thanks to the excellent collaboration between those involved. The factory’s operations could continue uninterrupted.
“I thought highly of HSM for that”, says Pedley, “and also for the willingness to allow our internal maintenance team itself to carry our preventive maintenance on the press. We would not have been able to achieve this ourselves and only worked because the training in the technology provided by the HSM team was also exemplary.”
The brief was perfectly respected, and the solutions presented were of high quality. The very detailed projects revealed both highly technical aspects and interesting marketing concepts that could be retained by certain brands looking for new ideas.
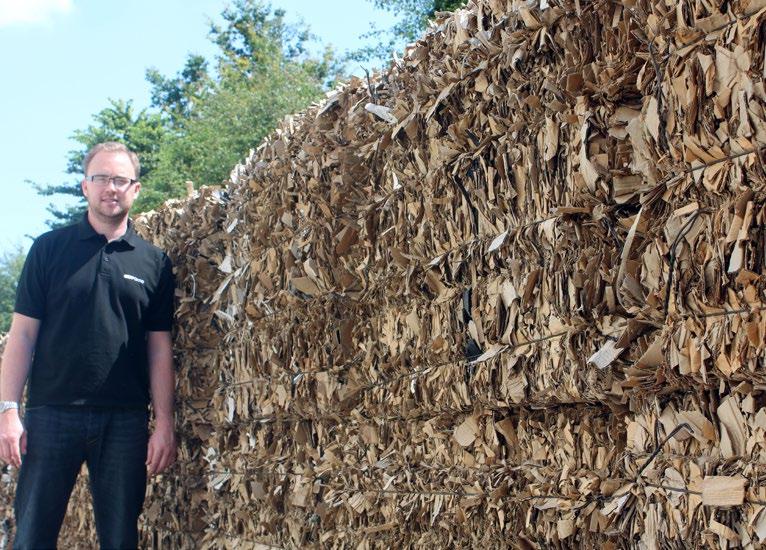
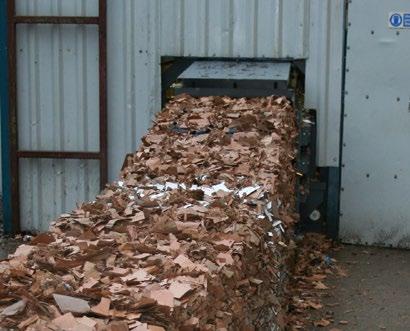
Contact HSM (UK) Ltd 14 Attwood Road / Zone 1 Burntwood Business Park Burntwood, Staffordshire WS7 3GJ Tel +44 1543 272480 Fax +44 1543 272080 sales.uk@hsm.eu www.hsm.eu