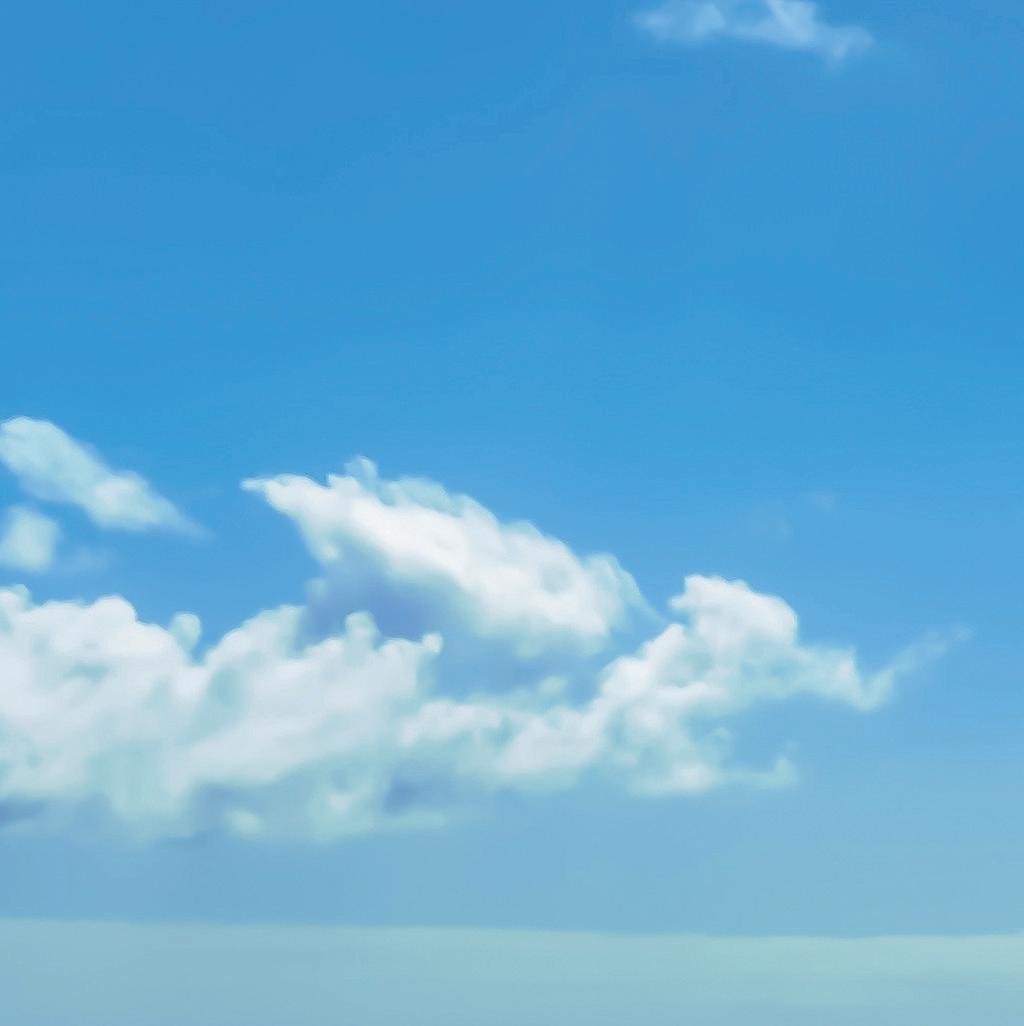
9 minute read
Get ahead of the curve
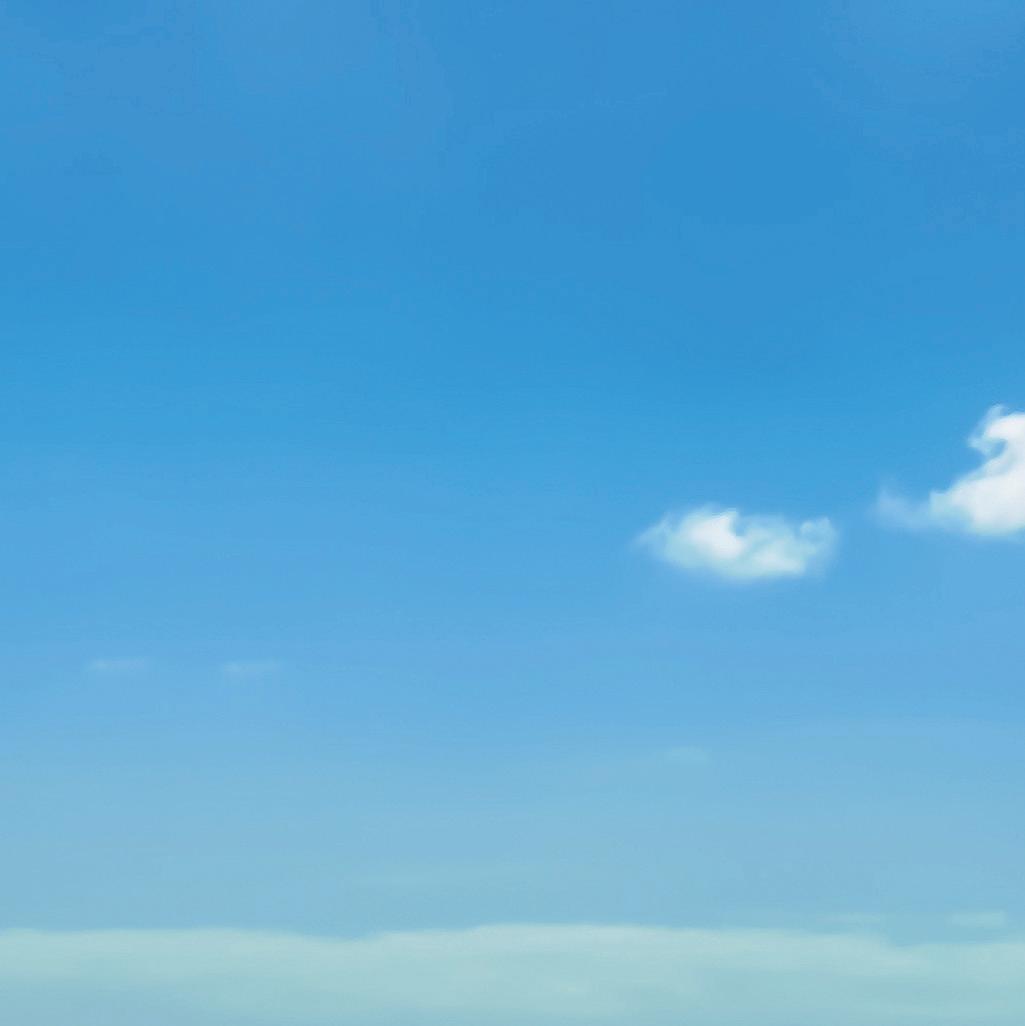
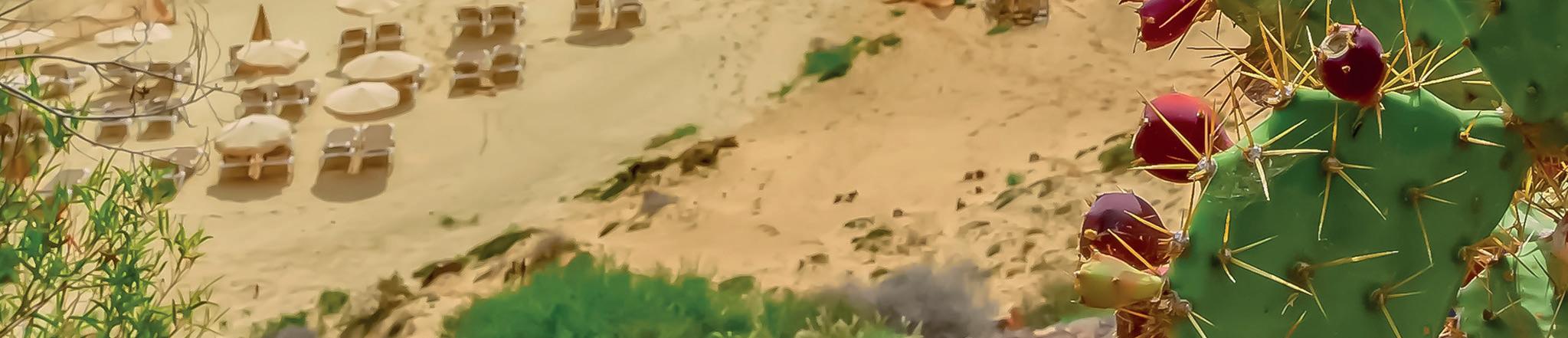
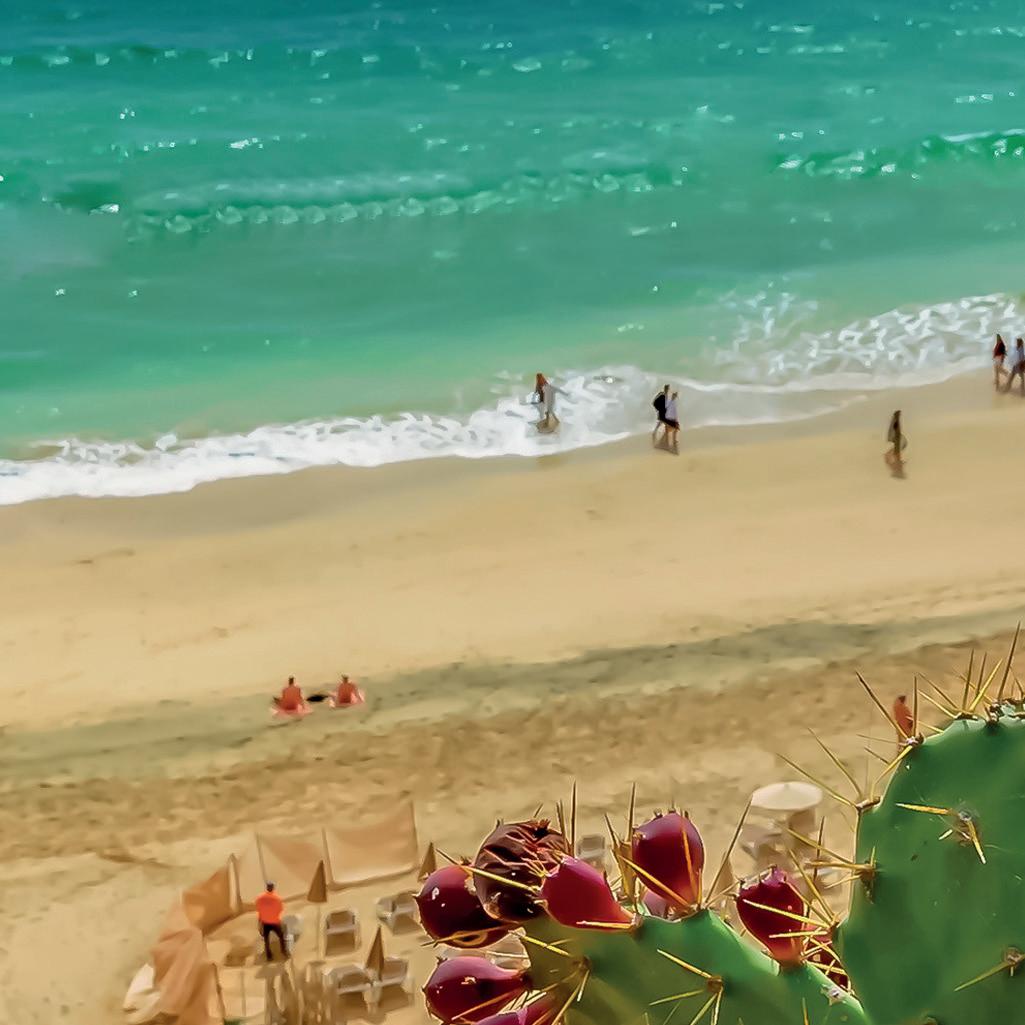
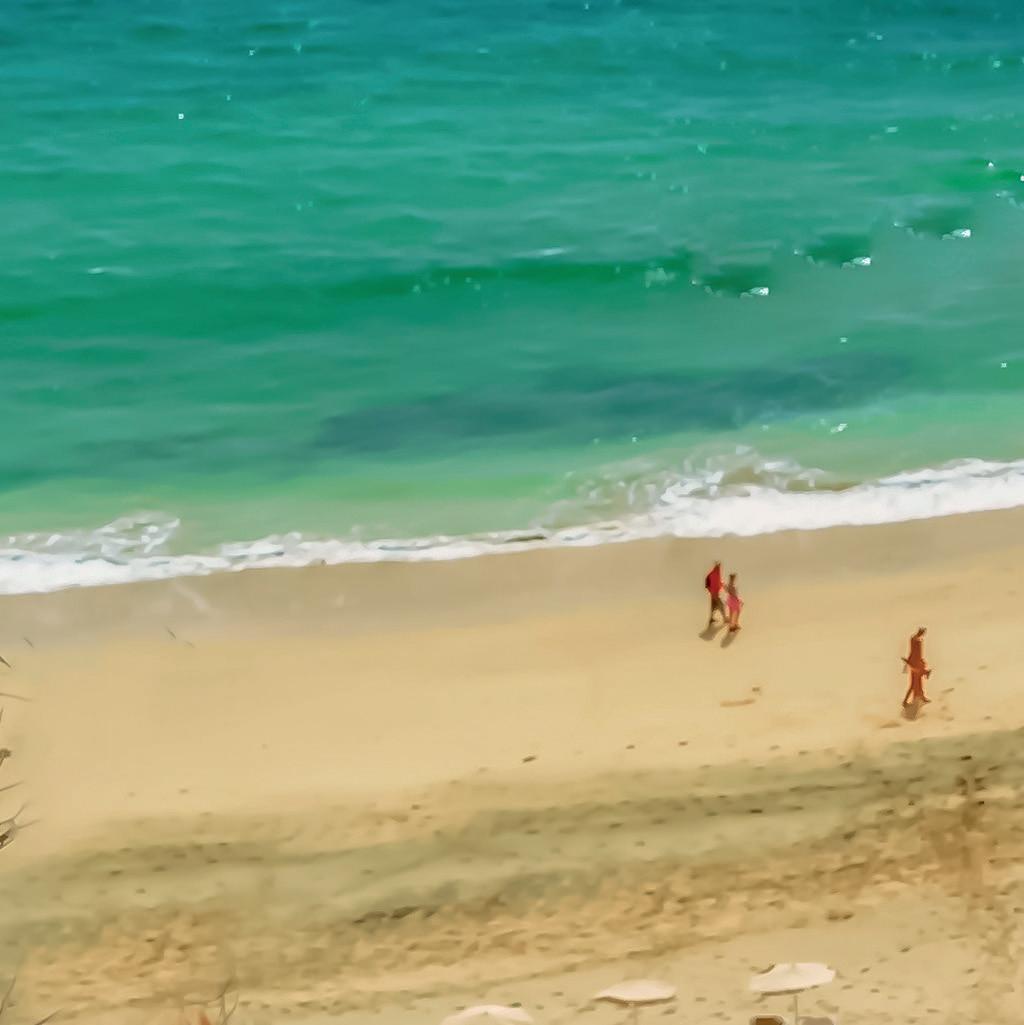
Floating wind technology enables offshore wind turbine installation in deep waters, unsuitable for bottom-fixed systems, opening up large swathes of the planet’s surface to renewable energy generation. Recent pilot projects have shown potential for similar, or even higher energy yields from floating turbines compared to bottom-fixed projects, as they can be situated in locations with higher wind resource.
Recent findings from the Carbon Trust’s Floating Wind joint industry project (JIP) reports predict an estimated 70 GW of floating wind could be installed across the globe by 2040. There is currently approximately 100 MW of floating offshore wind power installed largely in Europe. By the end of 2022, installed capacity could reach 200 - 260 MW.
As confidence in the technology grows, larger projects are becoming more commonplace, and while the majority of the earlier ones may be located in Europe, there is also significant attention in the US and Asia, most notably Japan. There is a now a greater number of international floating wind projects in the pipeline than ever before, aiming to pioneer new technologies and designs. These initiatives also aim to demonstrate supporting infrastructure and component technologies, such as mooring systems and dynamic export and inter-array cables. The results will be essential for securing the future for floating wind across global markets.
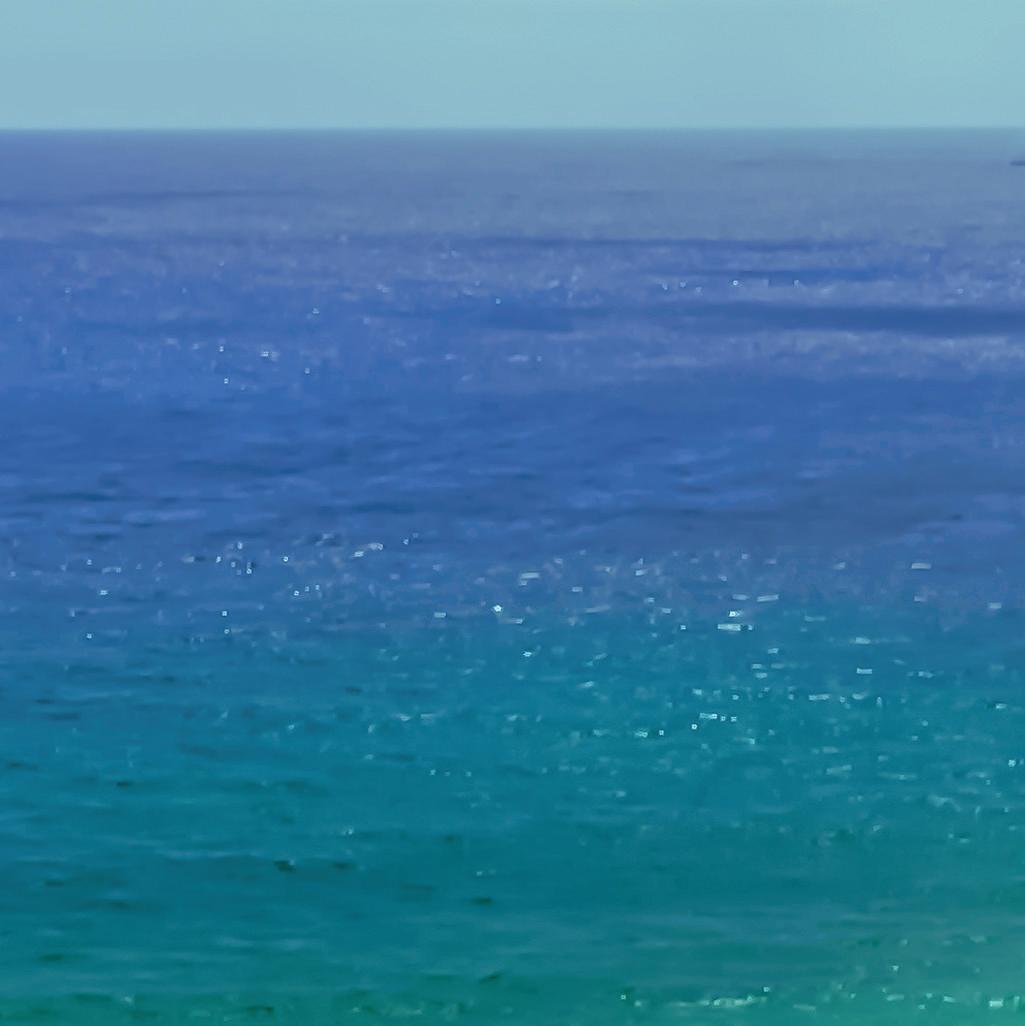
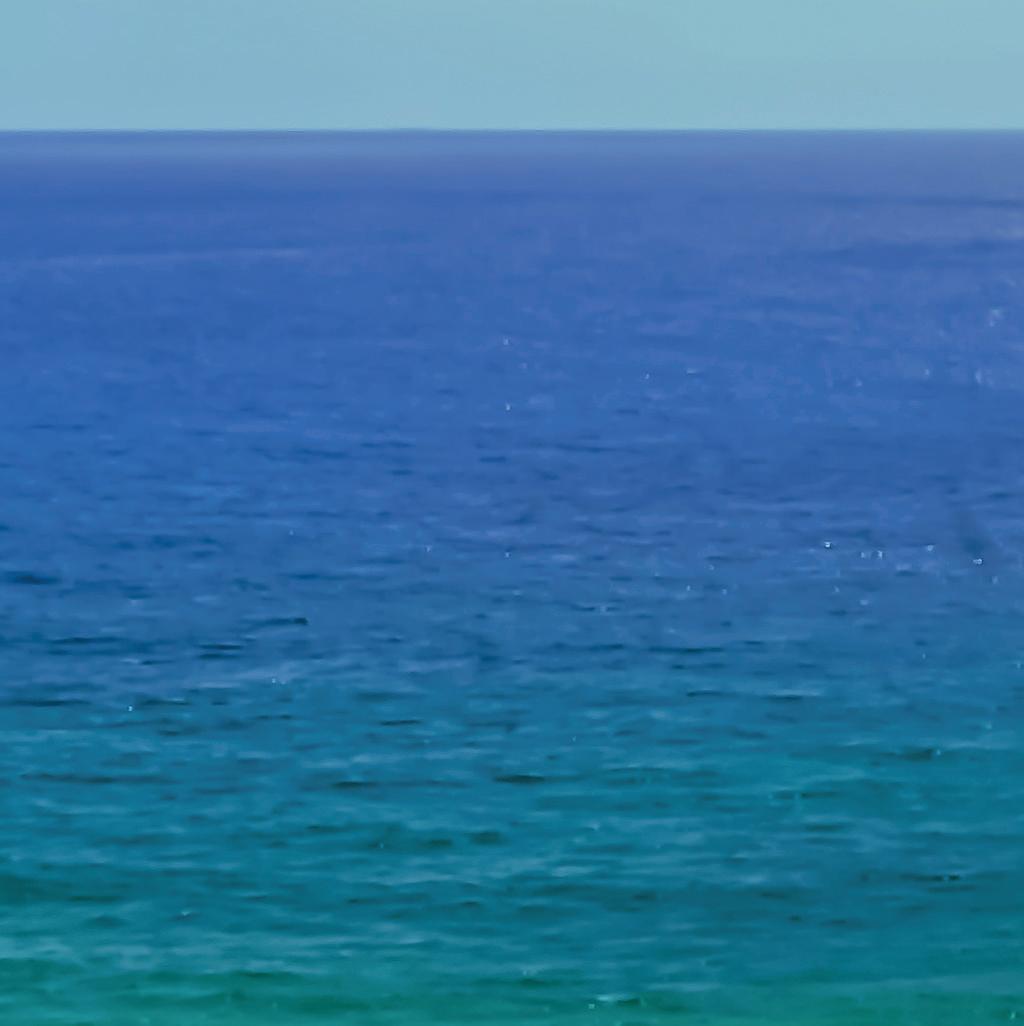
The PivotBuoy concept was initially developed by X1 Wind CTO and Co-founder Carlos Casanovas in 2012, while studying at Massachusetts Institute of Technology (MIT) in the US. He was committed to finding a more efficient structural approach for floating wind than the traditional land-based tower structure – one that would take advantage of the marine environment and reduce the loads on the structure, especially the bending moments at the base of the tower, allowing for a lighter design.
The result is an innovative tripod-like platform design that utilises the best features of a semi-submersible – with a low draft – plus a small footprint and the ability to reach deeper waters provided by a tension leg platform (TLP) mooring system. Furthermore, a single point mooring (SPM), called PivotBuoy, enables the structure to weather-vane and work more efficiently in tension and compression. This significantly reduces the amount of steel required. In order to achieve an optimal structural arrangement and improve alignment with

Alex Raventos, X1 Wind, Spain, looks at the latest floating wind platform tests being carried out in the Canary Islands, at a time where floating wind is rapidly moving from the fringes to the mainstream market.
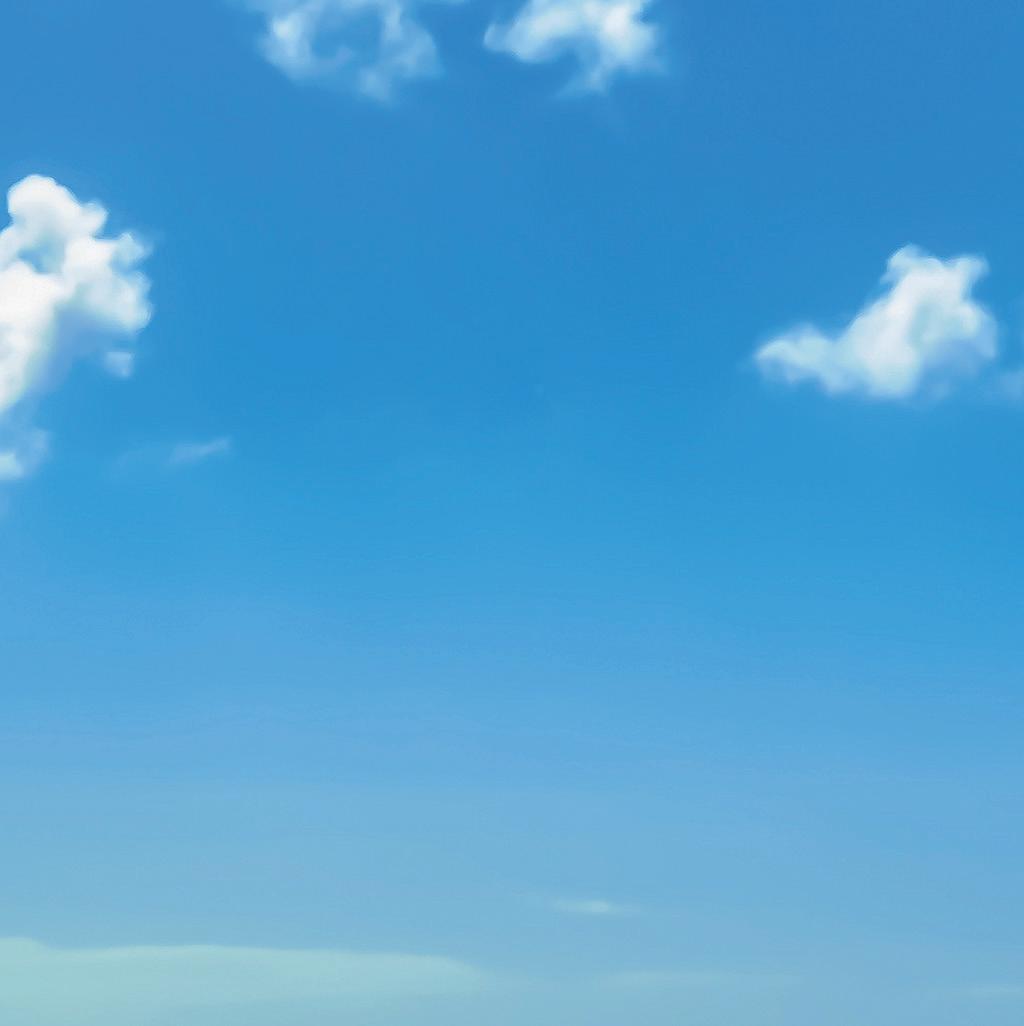

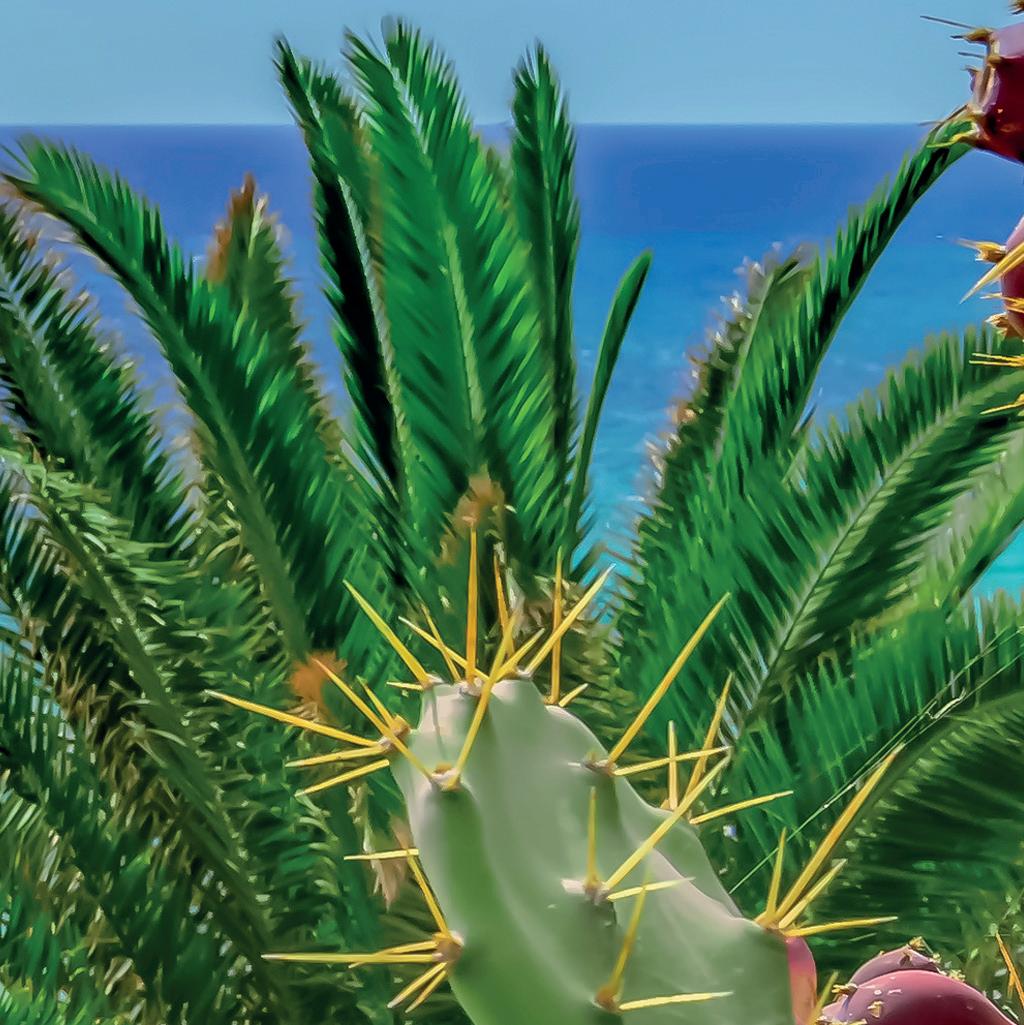
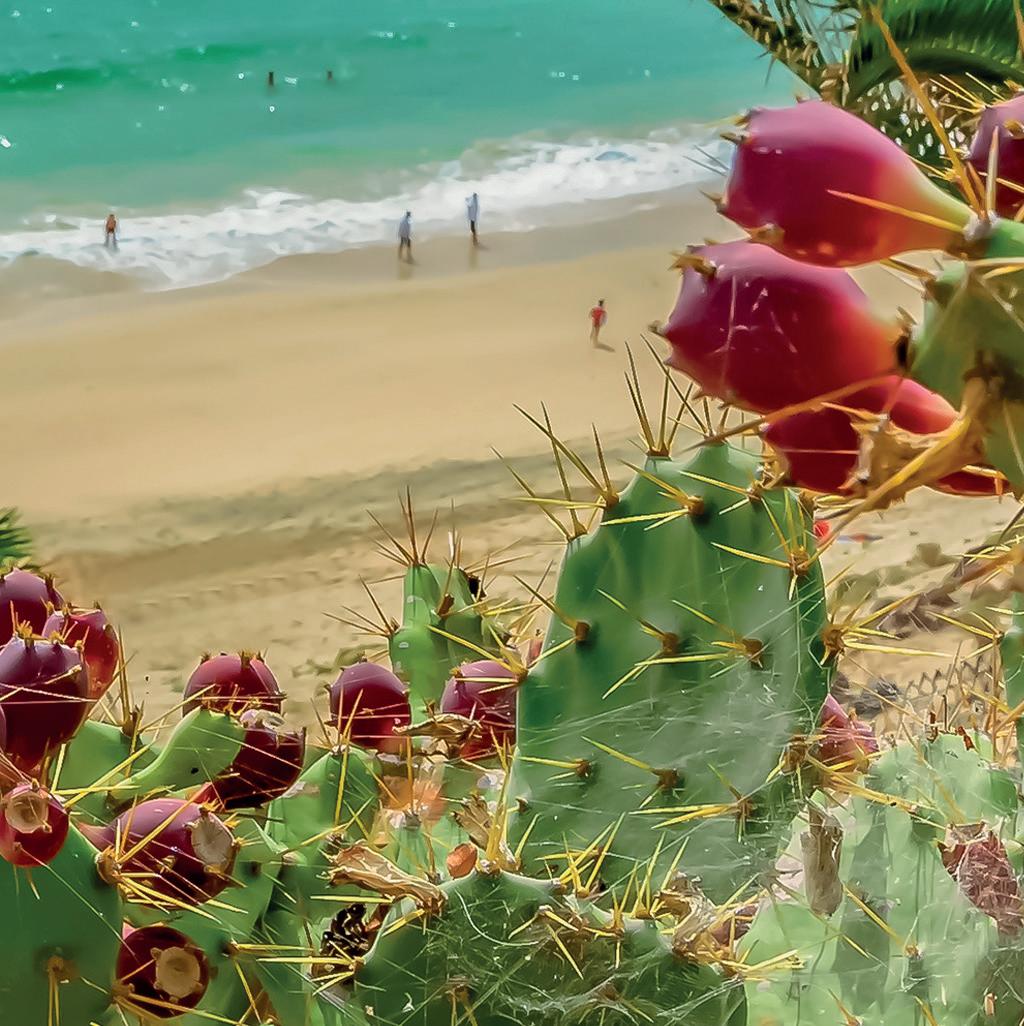
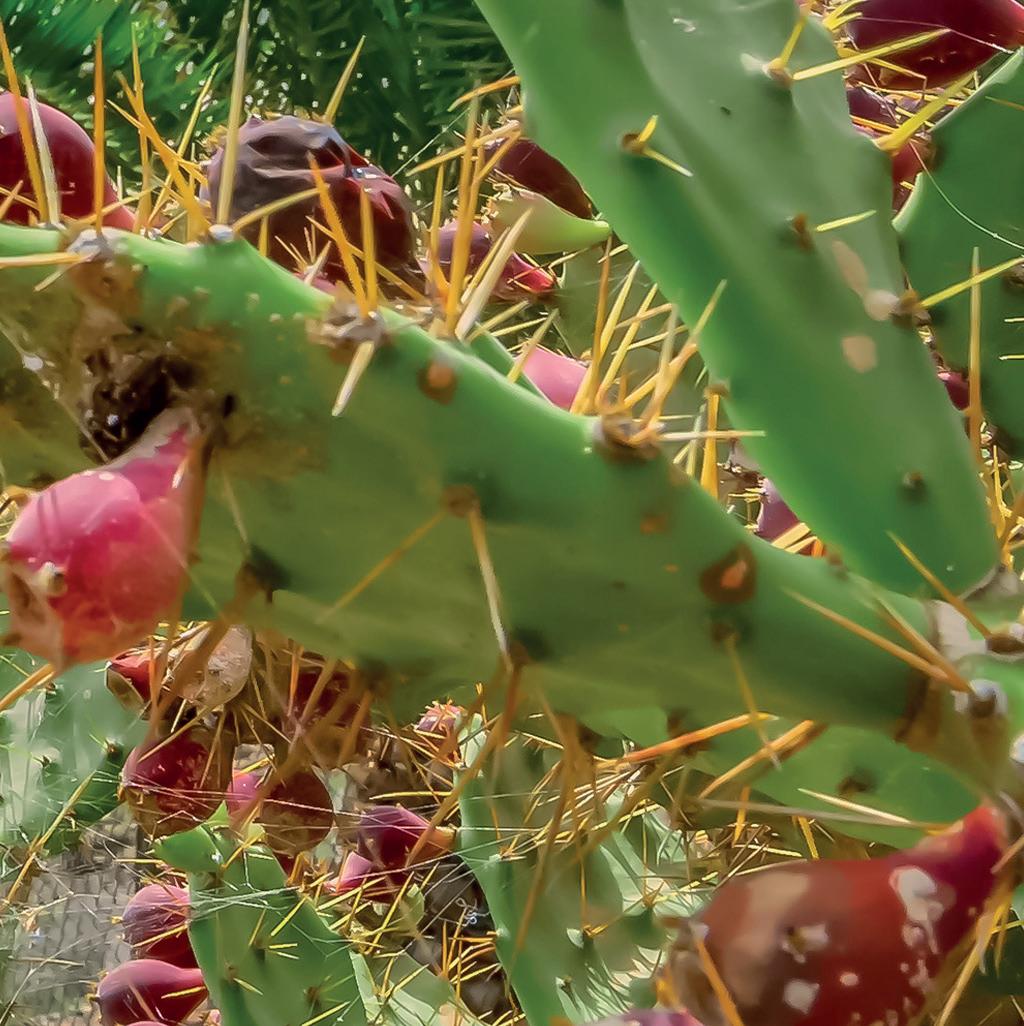
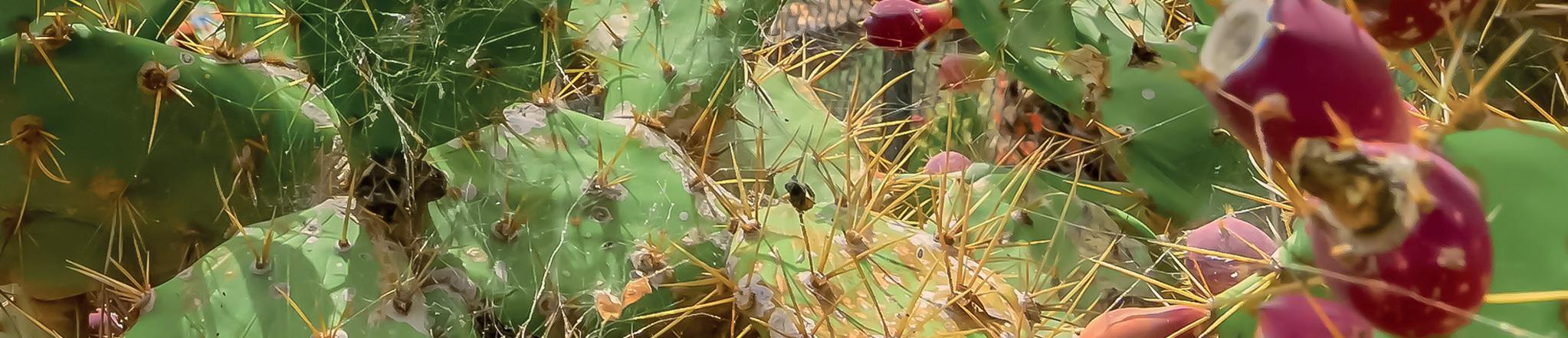
the wind, this structural configuration favours a downwind turbine.
The traditional, industry-wide approach for land-based turbines has developed based on an upwind rotor so as to avoid the tower shadow effect. However, upwind configurations come with a greater risk of tower strikes. This challenge increases as turbine blades get longer. With 100+ m blades becoming more prevalent in offshore environments, these require significant effort to avoid tower strikes by increasing the distance between the blades and tower (overhang margin), applying a tilt and cone angle, and designing costlier pre-bent and stiffer blades. These measures come with an increased complexity, cost, and potential loss of power generation.
Using a downwind configuration greatly reduces the risk of tower strikes, opening up the possibility of using lighter, more flexible, and therefore cheaper large scale wind turbine designs. These are key characteristics which will enable the development of future extreme scale downwind structures, with research already being conducted on 200 m blades and 50 MW power ratings.
Investigations into innovative rotor concepts
The innovative downwind approach was recently given further credence following an investigation led by National Renewable Energy Laboratory (NREL) based in Colorado, US. Its analysis of innovative rotor concepts for the Big Adaptive Rotor (BAR) Project identified the downwind concept as highly efficient in terms of performance.
Funded by the US Department of Energy’s Wind Energy Technologies Office, the BAR Project focused on the research and development of innovative technologies, capable of driving a 10% increase in capacity factor over current large land-based rotors. The purpose was threefold. Firstly, to identify and classify innovative BAR concepts. Secondly, to evaluate the concepts in terms of their potential to impact wind plant levelised cost of electricity (LCOE) and other performance metrics of interest, while identifying science and engineering challenges that would limit the commercialisation of these concepts. Lastly, to quantitatively analyse and compare the BAR concepts.
While capitalising on the advantages of the downwind configuration, X1 Wind technology also aims to solve the challenges pointed out in NREL’s BAR Project, notably the elimination of the tower shadow effect as explained in more detail next.
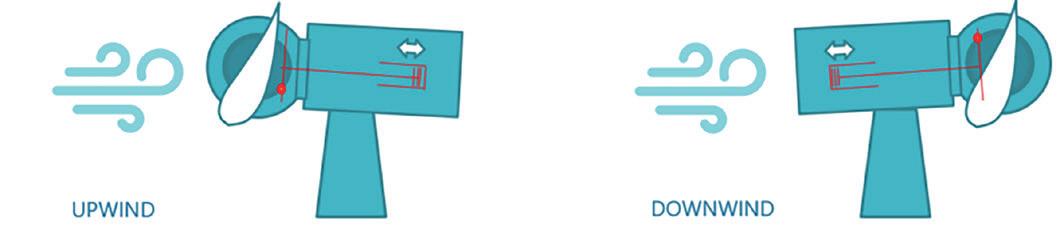
Figure 1. Upwind vs downwind orientation of wind turbines.
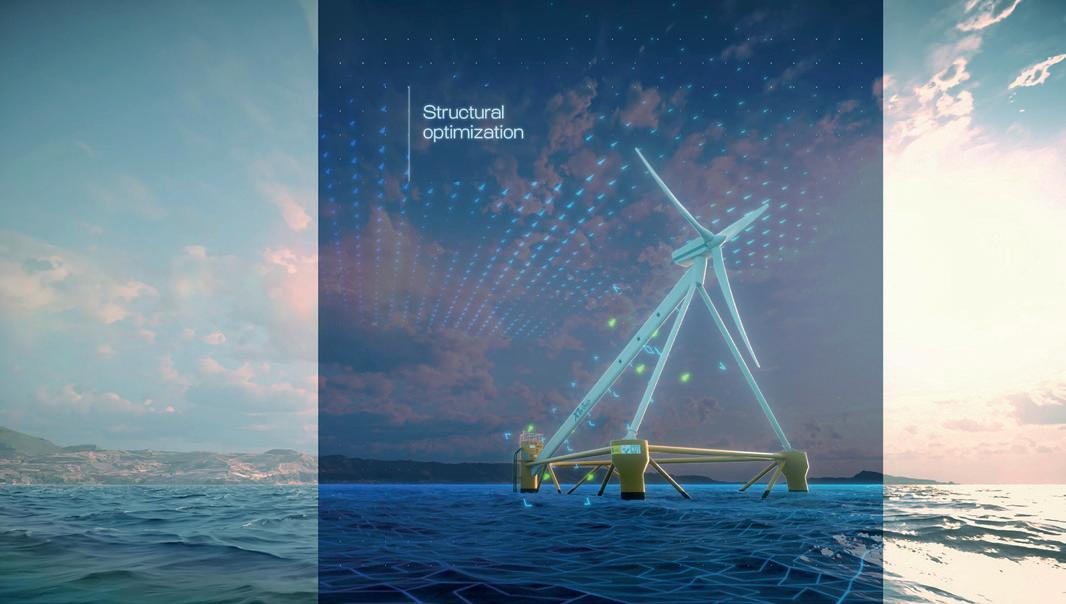
Figure 2. The downwind configuration enables a complete redesign of the floating structure, removing the traditional tower and creating a pyramidal platform that is more efficient in the load transmission.
Advanced simulation tests
In late 2020, X1 Wind completed advanced CFD simulation of its floating platform, working alongside Germany’s worldrenowned Fraunhofer Institute for Wind Energy Systems (IWES). The study included simulations of X1 Wind’s X30 floater integration with a Vestas V29 turbine to better understand the aerodynamic forces acting on the structure and rotor.
Results show significant improvement in velocity deficit compared to downwind turbines using traditional tubular or lattice towers, as well as very low dynamic excitation of rotor blades (3P, 6P) due to the tower shadow effect. This has been achieved by streamlining the shape of the masts and reducing their diameter, which results in much smaller eddies being shed downwind, minimising turbulent inflow into the rotor.
In addition, staggering the position of the rotor axis with respect to the mast apex ensures the blades do not fully enter the side mast’s shadow at any given time. Instead, they move in and out of the shadow gradually, spreading out the 3P excitation over a wider rotation angle – thus making it less impulsive, with minimal effect on torque and thrust. These results are expected to be validated with the installation and operation of the PivotBuoy prototype in the next few months.
Key design innovations
While X1 Wind’s downwind weather-vaning design captures attention, the unique system also delivers a broader range of benefits. FPivotBuoy connection system: An innovative, single point, pre-installed mooring system combines an SPM with a small TLP, allowing for a quick connection and disconnection. This allows the platform to be assembled onshore and then towed to site using local vessels instead of heavy lift vessels, which simplifies offshore operations and reduces installation costs.
FLightweight structure: The combination of the PivotBuoy connection and downwind configuration allows the platform to passively weather-vane and self-orientate.
The downwind configuration enables a complete redesign and more efficient load transmission that results in a substantially lighter platform compared to traditional solutions. As a result of the lower weight, inherent stability, and unique mooring system, the platform can be easily assembled onshore and towed to site using local, low-cost vessels. Being lighter also means reduced emissions at
fabrication and transport, which adds up to the reduced environmental footprint of the TLP on the ocean floor when compared to catenary systems.
F Operations and maintenance: Reliability is a critical issue in offshore operations and the passive systems used within
X1 Wind’s platform, such as the self-orientating system, help minimise maintenance requirements. Additionally, the TLP mooring system minimises the motions of the
PivotBuoy, reducing fatigue on the dynamic cable as well as facilitating maintenance operations.
F Scalability: X1 Wind’s downwind design allows turbine blades to be lighter, longer, and cheaper as they can bend away from the structure, enabling a more efficient transition up to 15+ MW mega turbines. Additionally, unrestricted by water depth, the system can be costeffectively deployed at depths from 40 m to more than 500 m.
F Environmental impact: The SPM system greatly reduces the platform’s footprint on the seabed, compared to the long spread and drag anchors used in catenary systems.
Also, a reduced amount of steel means fewer emissions from manufacturing and enables local manufacturing – by having a low draft – meaning less emissions from transport.
Project details
X1 Wind is currently leading the ground-breaking PivotBuoy Project with a pan-European consortium including leading companies EDP NEW, DNV, INTECSEA, ESM, and DEGIMA, and world-class research centres WavEC, DTU, and PLOCAN. Supported by €4 million from the European Commission H2020 programme, the pioneering project is aiming to substantially reduce the current LCOE of floating wind. It will achieve this by demonstrating the advantages of the PivotBuoy system, namely a reduced floater weight, a faster and cheaper installation process, and a more reliable operation.
Located in the Canary Islands, the PivotBuoy Project will see X1 Wind’s first fully functional prototype exposed to open ocean conditions, to demonstrate the efficiency of its innovative structural design and mooring system. Fitted with a Vestas V29 turbine, the 1:3 scale prototype (X30) will be stationed at a 50 m water depth. The turbine benefits from a re-engineered drivetrain which rotates in the opposite direction in the downwind configuration. Despite the transformation, the rotor will still be spinning clockwise, and the original yaw system will be blocked for operation, since the PivotBuoy system self-aligns with the wind as a result of its weather-vaning ability. This reduces the amount of active systems within the platform, which can bring savings to operation and maintenance during the structure’s lifespan.
Construction of the X30 platform was completed in November 2020 by DEGIMA in Santander, Spain, before being shipped in different segments to the Gran Canarias. Structural assembly was managed entirely onshore at Hidramar shipyard, using regular LTM mobile cranes and local equipment. Earlier in 2021, project partners supervised the successful assembly and load out of the X30 prototype. This is being followed by port-side testing of subsystems, before the installation and connection via a dynamic cable expected in the autumn.
X1 Wind’s approach to mobilising and engaging local supply chains is a key feature of its future fabrication and deployment plan for full scale units. Aside from stimulating local economies and driving job creation, it further reduces transit times, helping reduce costs and carbon emissions for future projects.

Figure 3. The combination of the PivotBuoy connection and downwind configuration allows the platform to passively weather-vane and selforientate.
Figure 4. Traditional upwind rotors require overhang margin, tilt angles, rotor coning, or the use of pre-bent blades to avoid tower strikes.
Figure 5. Using a downwind configuration opens up the possibility of using lighter, more flexible, and therefore cheaper large scale wind turbine designs.
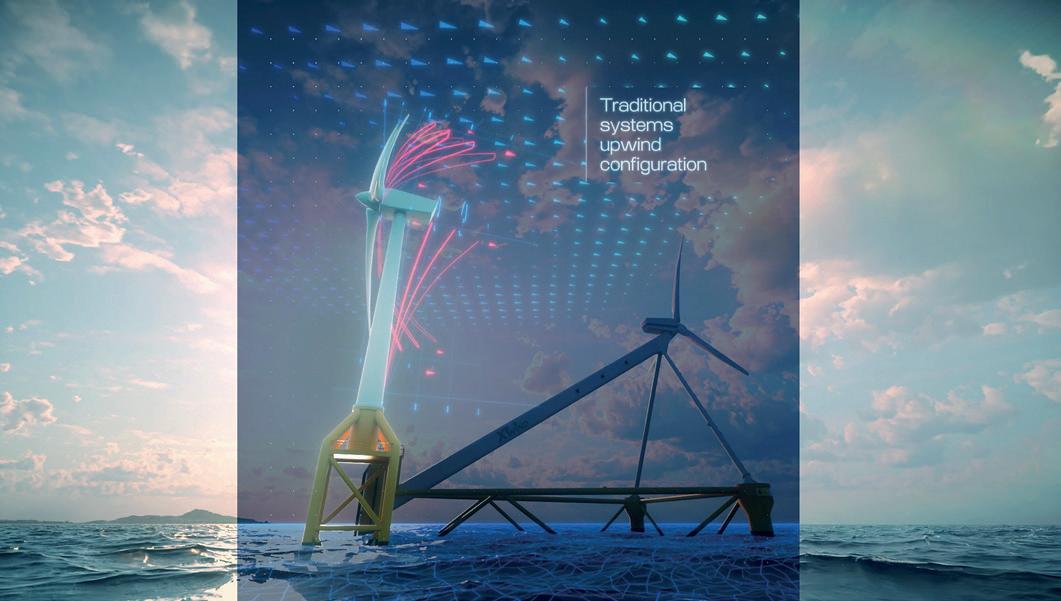
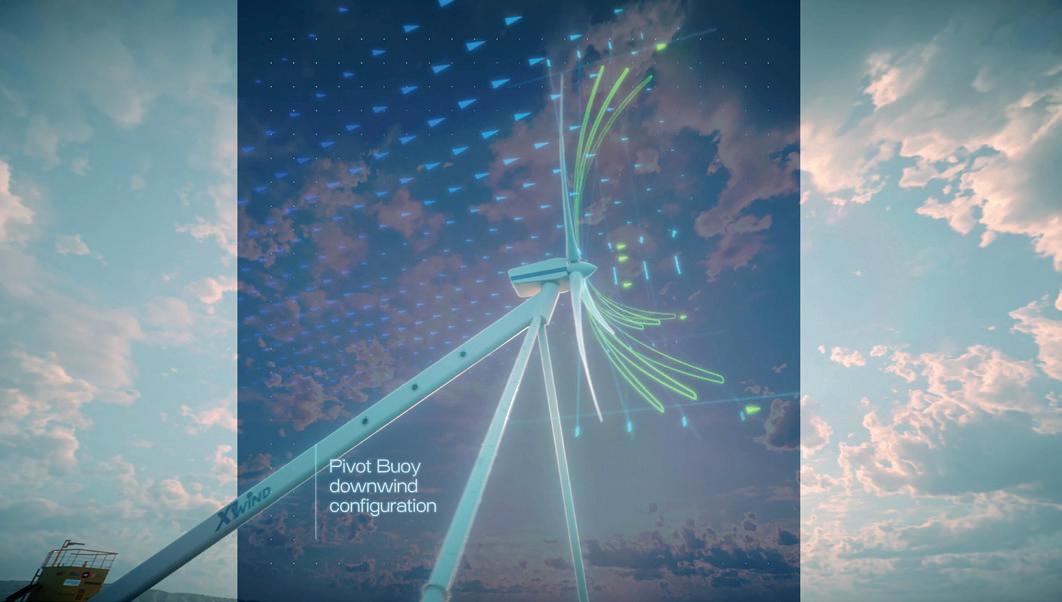