
7 minute read
Greener refineries
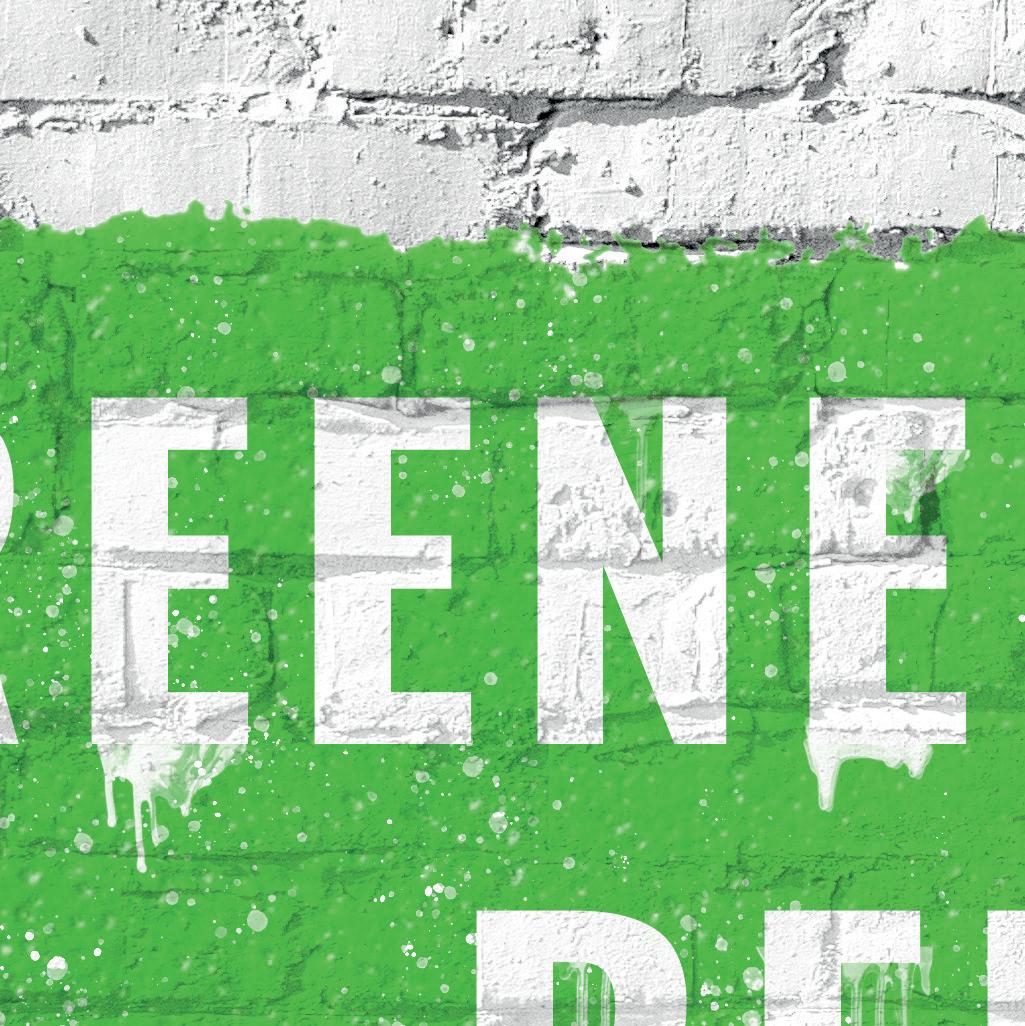
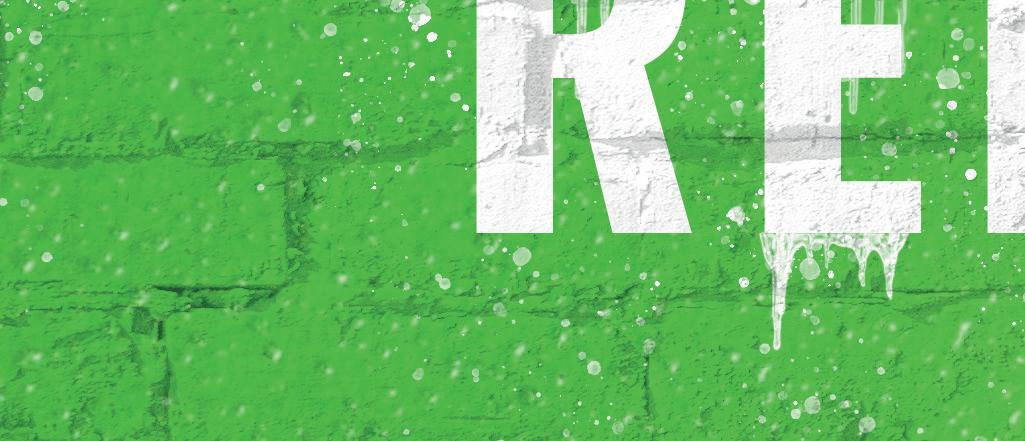
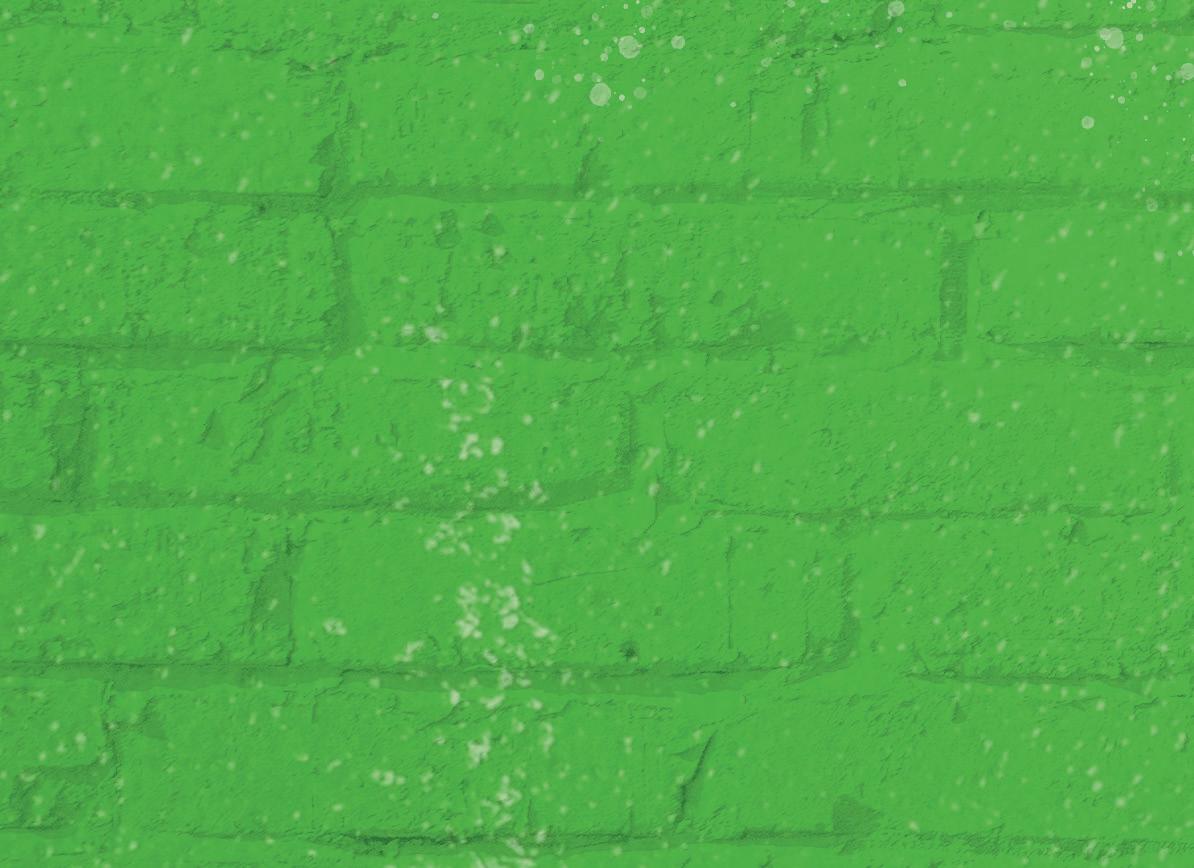
By upgrading their existing plants to utilise renewable resources, edible oil refineries can increase the sustainability of their operations while also opening up new commercial opportunities. Selecting the right mass transfer technology, such as advanced purification units, is crucial to creating highly effective processing facilities. These, in turn, enable refineries to thrive in the alternative fuel marketplace, maximising throughput, product quality, and recovery rates.
The fast-growing demand for alternative fuels obtained from renewable resources, such as plant-based materials, brings with it key opportunities for established businesses in the vegetable oil, renewable fuel or biofuel sectors. In addition, businesses are able to deliver these products by leveraging their existing infrastructures, kick-starting their entry into a highly profitable market, which was valued at over US$141 billion (nearly £103 billion) in 2020.1,2
One such example is bio-based diesel. The market for this renewable fuel is characterised by robust growth and is forecast to develop at an average annual rate of 4.9% through to 2030, when it will reach a global consumption figure of approximately 63 million t.3
Biodiesel also offers a number of advantages over conventional fuels. For example, it yields 93% more energy than the energy invested in its production.4 It also tends to release limited volumes of air pollutants per net energy gain. When looking at the entire life cycle
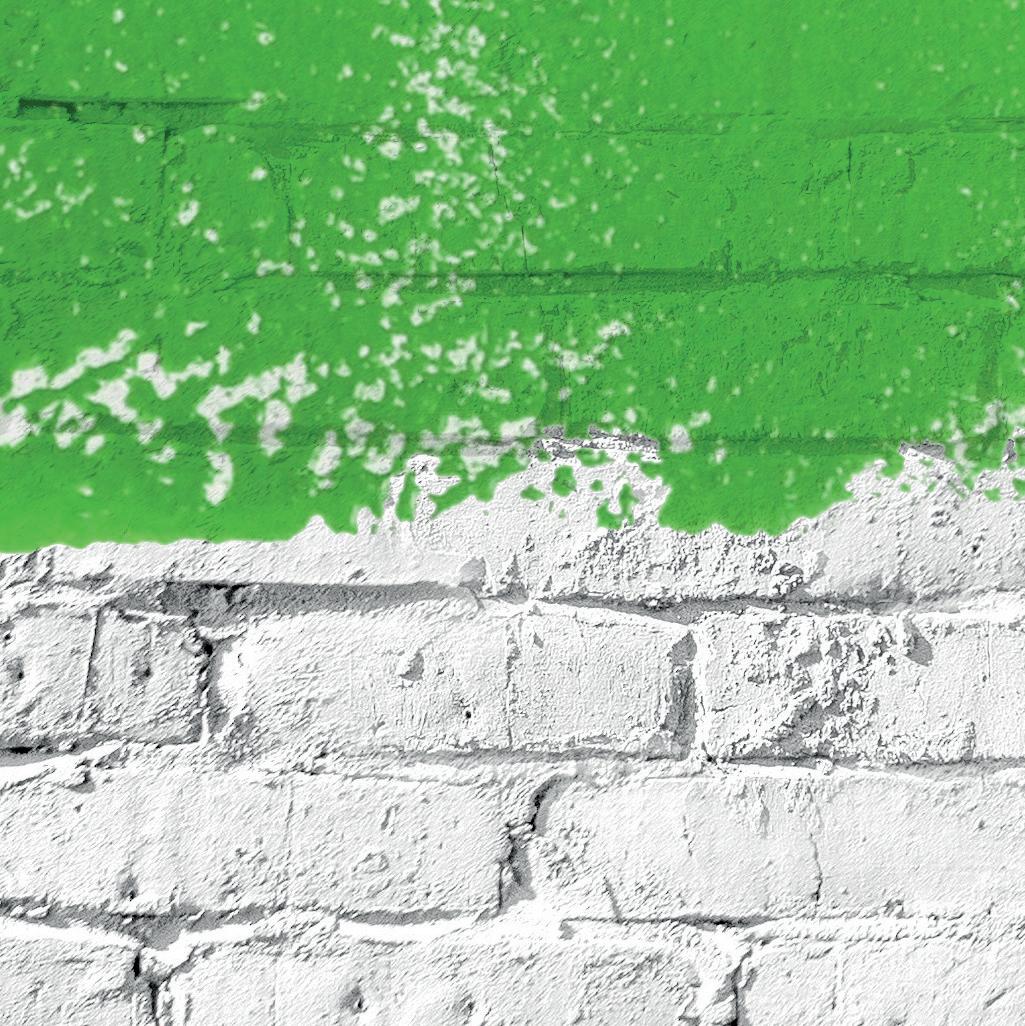
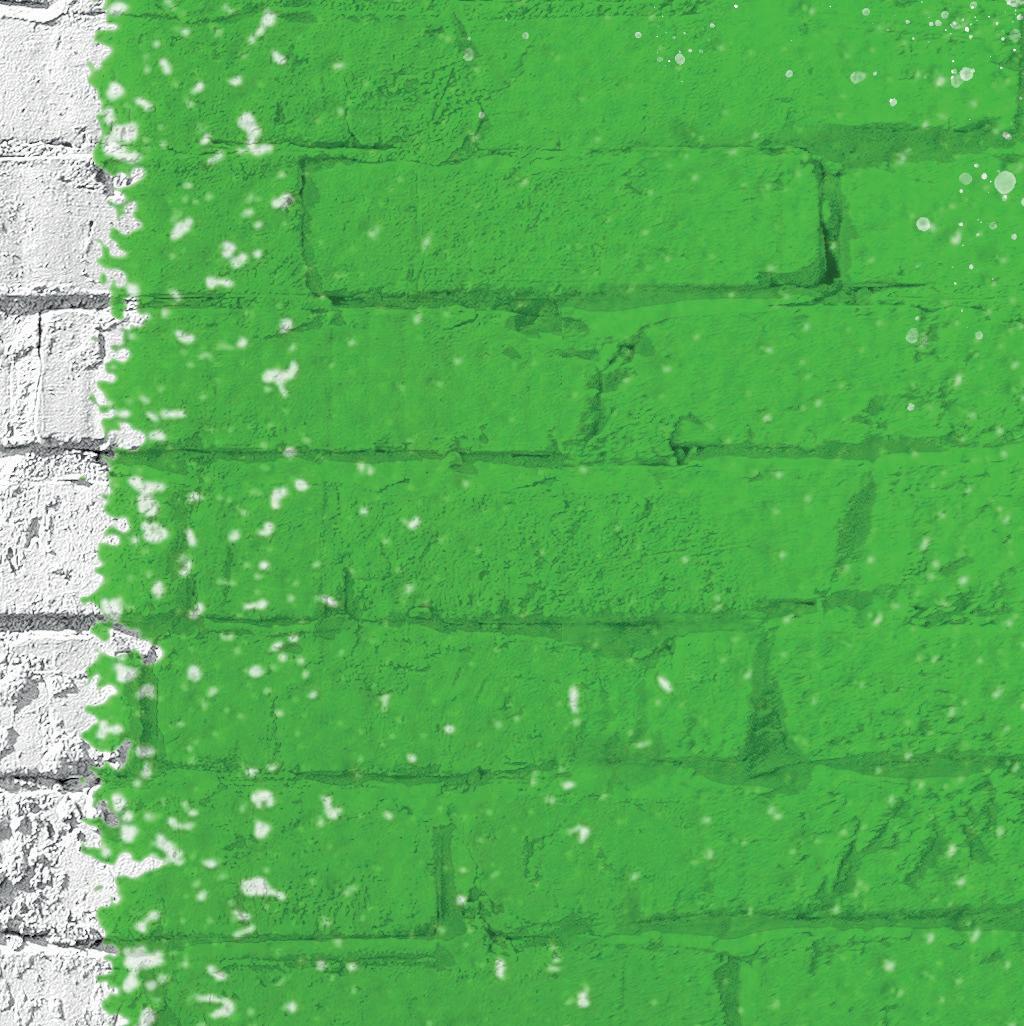
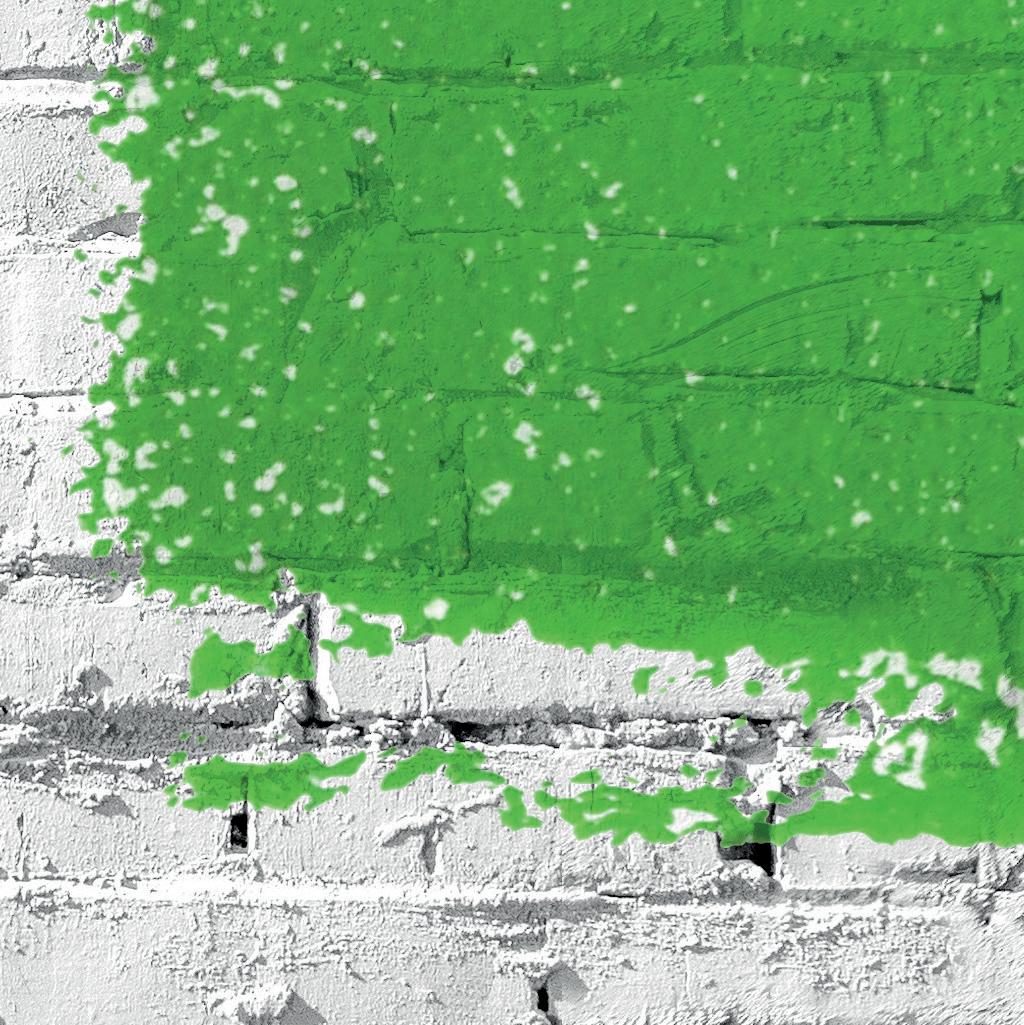
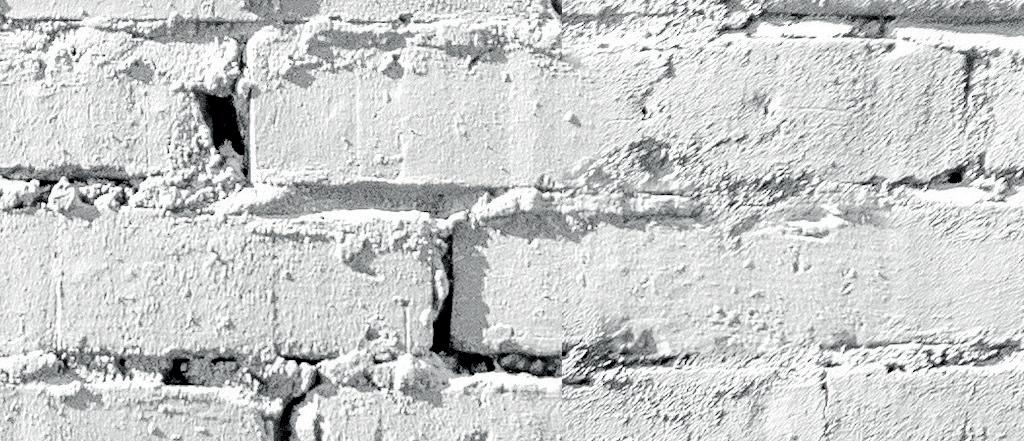
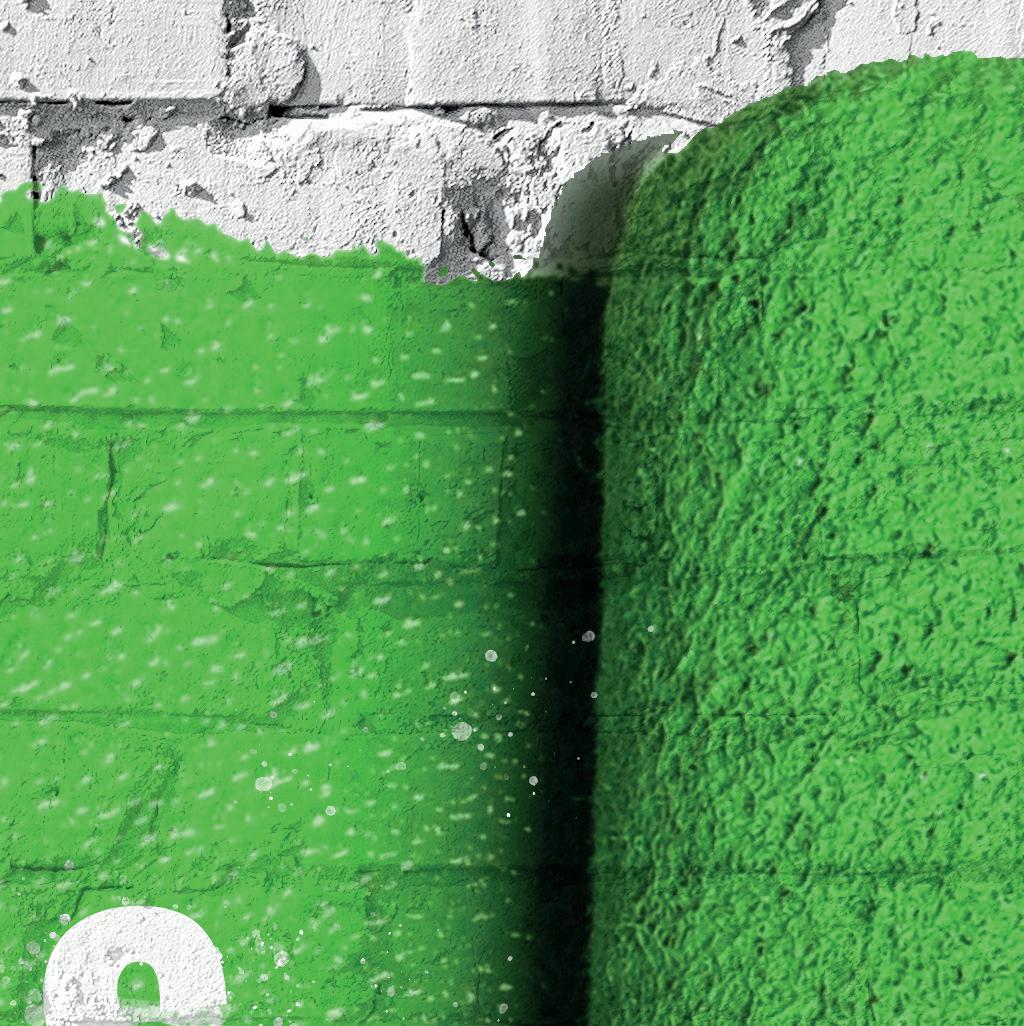
Keen Hoe Lui, Sulzer,
Singapore, looks at how to convert existing biodiesel processing facilities to create sustainable and effective green fuel production plants.

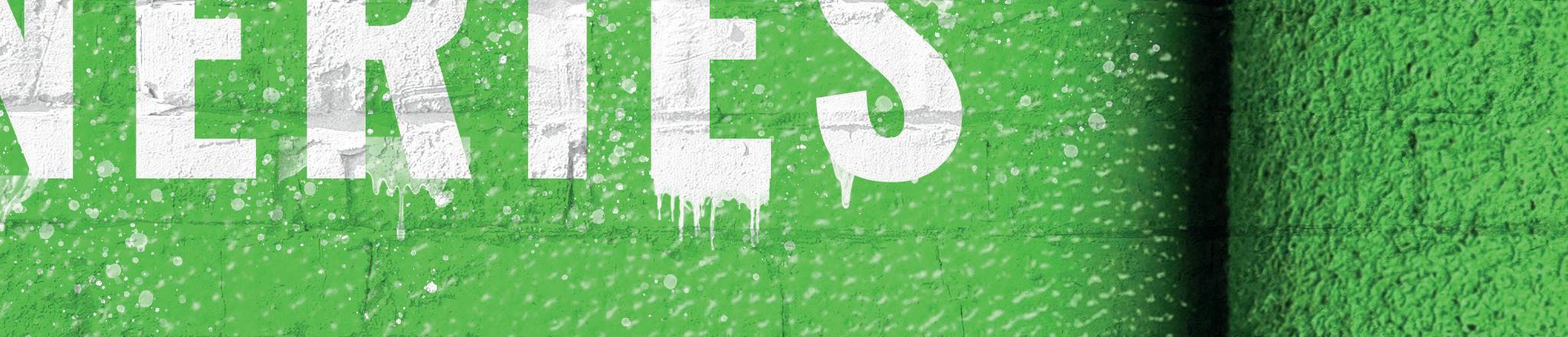
assessment (LCA) of this biofuel, it releases just 1.0%, 8.3%, and 13% of the agricultural nitrogen, phosphorus, and pesticide pollutants, respectively, per net energy gain. Relative to the fossil fuels that are displaced by the use of biodiesel, greenhouse gas emissions are reduced by 41% throughout production and combustion.4
The importance of purified biodiesel

Sustainable biodiesel can be obtained by using a wide range of feedstocks, such as algae, animal fats, vegetable oils, or used cooking oil. These contain triglycerides that undergo catalytic esterification which is facilitated by alcohols, alkaline or acid catalysts, or enzymes. The products of this reaction are fatty acid methyl esters (FAME), i.e. biodiesel.
However, heavier components (heavies) and impurities, such as sulfur and fatty acids – particularly monoglyceride – are also present in varying degrees. These can influence the properties of the biodiesel produced as well as the performance of the engine using it. Therefore, the FAME need to be purified in order to remove these unwanted chemicals and obtain high-quality fuels.
When biodiesel with an elevated purity level is achieved, it has a transparent appearance as well as extremely low cloud and pour points. These features make the product suitable for the most demanding applications, as the fuel can meet even strict winter-grade specifications. This means that it offers a sufficient energy content while


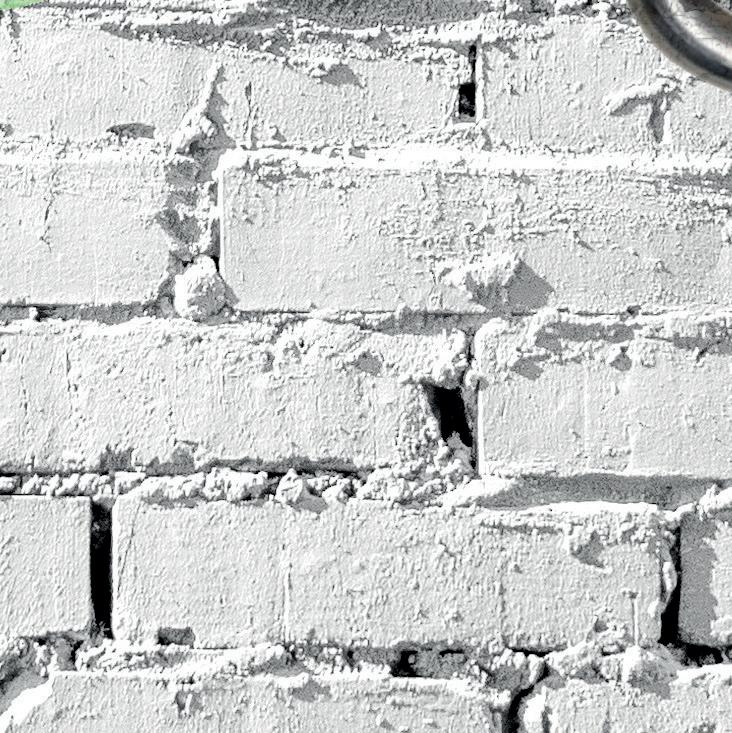
showing a limited tendency to turn into a thickened gel at low temperatures. As a result, users can effectively mix it with conventional diesels to obtain superior fuel blends that can be utilised in colder regions.
Refining process needs
Biodiesel producers that want to supply biodiesel to the European and North American markets, where winterised fuel is often necessary, should therefore make sure that their equipment can deliver a high-quality product at competitive prices. More precisely, the facilities must be able to achieve a high separation performance to successfully remove most of the impurities, especially monoglyceride, and meet or be better than current regulations, such as ASTM D6751 for North America and EN 14214 for Europe.
At the same time, with separation processes being among the most energy-demanding, it is important for purification equipment to be highly efficient. This is key to maintaining low OPEX and, in turn, offering cost-competitive biodiesel. Furthermore, limiting energy usage also helps to improve the sustainability of refining activities, as this reduces the overall carbon footprint of a facility. On top of these considerations, businesses should select solutions that minimise the CAPEX as well as an expanded manufacturing footprint required to repurpose the plant.
Structuring upgraded columns
Ultimately, the solution to address all these challenges lies in selecting a separation technology specialist with an established track record of supporting biofuel production, such as Sulzer Chemtech. In this way, businesses can benefit from proven modifications to create reliable and effective purification systems. The upgrade programme is also likely to include the replacement of column packing and internals to handle different processing conditions and feedstocks.
The most effective set-up to obtain high-purity FAME involves high temperatures and vacuum conditions condensed into a single unit, rather than a separation train. This design of purification tower demonstrates optimised performance, removing most of the monoglyceride and sulfur content, reaching levels below 0.2% w/w and 15 ppm respectively. Also, by employing a single purification unit, businesses can limit their equipment footprint as well as CAPEX.
Columns operating at high temperature and under vacuum are best equipped with structured packing in their beds. This consists of parallel corrugated sheets, gauzes or meshes, in most cases made of metal. Arranged in an open honeycomb structure with vertical flow channels, the design offers low resistance to flow but a relatively high surface area to volume ratio. Thus, it is possible to maximise liquid spreading to facilitate mass transfer while minimising liquid hold-up and residence time. Furthermore, since the packing’s open area is nearly as large as the column’s cross-sectional surface, the pressure drop is limited.
This choice of packing also proves crucial in the challenging separation of FAME from monoglyceride – substances that have similar boiling points. The removal process of such an impurity requires a high number of theoretical stages that only structured packing can accommodate while offering a limited column size.

Figure 1. Oil refineries can play a key role in the global transition towards cleaner energy sources.
Selecting the latest technologies
With the design of structured packing continuously evolving, the most effective solution is the latest fourth-generation design, as used in Sulzer Chemtech’s MellapakPlus™. In effect, when compared to third-generation structured packing, this technology can lead to capacity increases of 30 - 50%.5 Even more, MellapakPlus causes a pressure drop that can be up to three times lower than other solutions with similar specific areas and, under the same conditions, the bottom temperature can be safely lowered while achieving similar separation performance.6 Therefore, facilities can benefit from substantial savings in OPEX.
In addition to advanced separation components, a specialist such as Sulzer Chemtech can provide further support to help biofuel or biodiesel producers maximise profitability. To enhance FAME recovery rates, it can couple the purification unit with a secondary system, such as rising film evaporators or candle evaporators, where the residue is reprocessed to extract any remaining FAME, maximising yield. Also, the company offers steam regenerators to create low-energy, closed-loop heat recovery systems that can lower energy consumption, the associated costs, and ultimately optimise biodiesel production.
By upgrading their existing infrastructures to support more sustainable feedstocks, oil refineries can play a key role in the global transition towards cleaner energy sources. Partnering with a world-leading specialist in separation technology and biodiesel applications, such as Sulzer Chemtech, will ensure that adapted plants benefit from the latest technologies and efficient processes. As a result, biodiesel producers can get ahead of the competition and establish themselves in the biofuel market with high-quality, cost-effective products.
References
1. PRECEDENCE RESEARCH, 2021, ‘Biofuels Market Size, Share & Growth Analysis Report, By Fuel Type (Biodiesel and Ethanol), By Feedstock (Coarse Grain, Sugar Crop, Vegetable Oil, Jatropha, Molasses) - Global Industry Analysis, Trends, Revenue, Segment Forecasts, Regional Outlook 2021 - 2030’. 2. MARKET RESEARCH FUTURE, 2021, ‘Biofuels Market Research Report: Information, by Fuel Type (Biodiesel and Ethanol), by Feedstock Type (First, Second, and Third Generation), and by Region (North America, Europe, Asia-Pacific, the Middle East & Africa, and South America)- Forecast till 2027’. 3. INDEXBOX, 2021, ‘The Global Biodiesel Market Retains Robust Growth Despite the Pandemic and Low Oil Prices.’ Available at: https://www.globaltrademag.com/the-global-biodiesel-marketretains-robust-growth-despite-the-pandemic-and-low-oil-prices/ [Accessed 25 August 2021]. 4. HILL, J., NELSON, E., TILMAN, D., POLASKY, S., and TIFFANY, D., 2006, Environmental, economic, and energetic costs and benefits of biodiesel and ethanol biofuels. Proceedings of the National Academy of sciences, Vol. 103(30), pp.11206-11210. 5. MOSER, F., and KESSLER, A., 2000, ‘MellapakPlus-a new generation of structured packings’, Vakuum in Forschung und Praxis, Vol. 12(2), pp.122-124. 6. SALEM, A., and SHOKRHAR, H., 2008, ‘Effect of Structured Packing Characteristics on Styrene Monomer/Ethylbenzene Distillation Process’, Chemical Engineering & Technology: Industrial Chemistry-Plant Equipment-Process Engineering-Biotechnology, Vol. 31(10), pp.1453-1461.