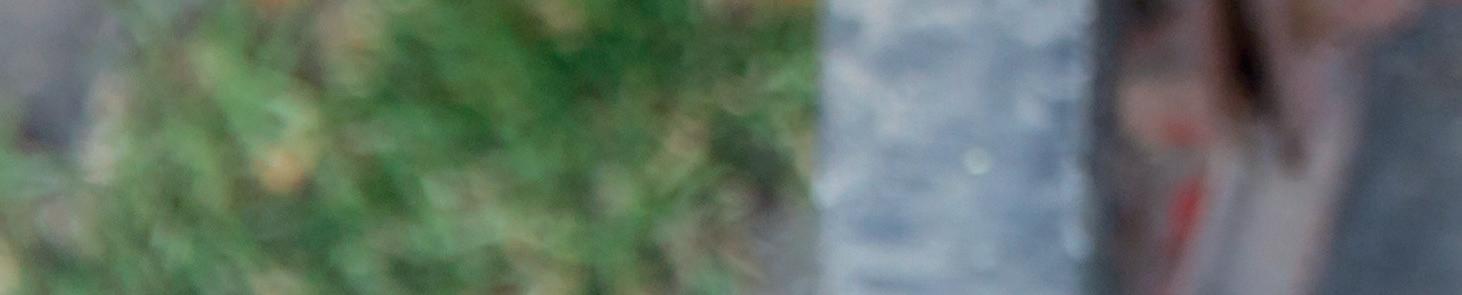
7 minute read
Natural sources for natural power
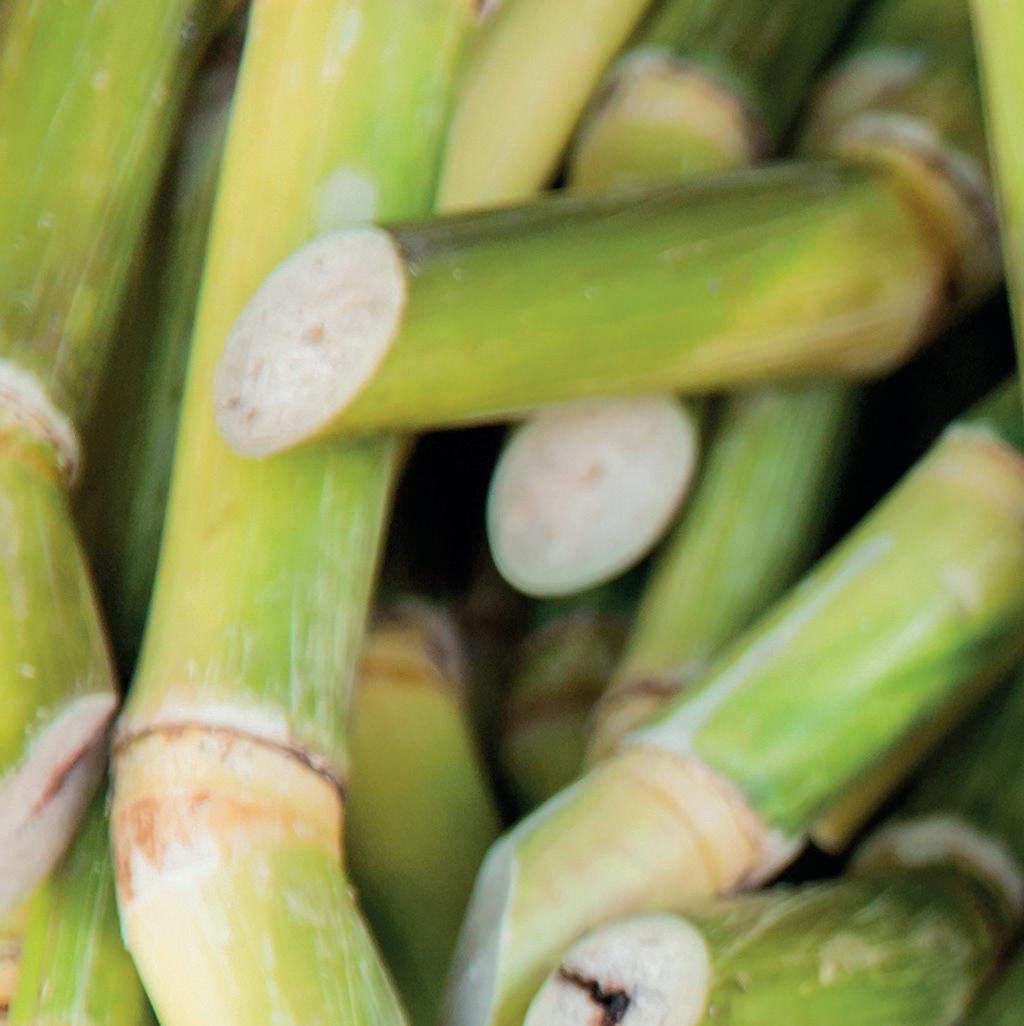
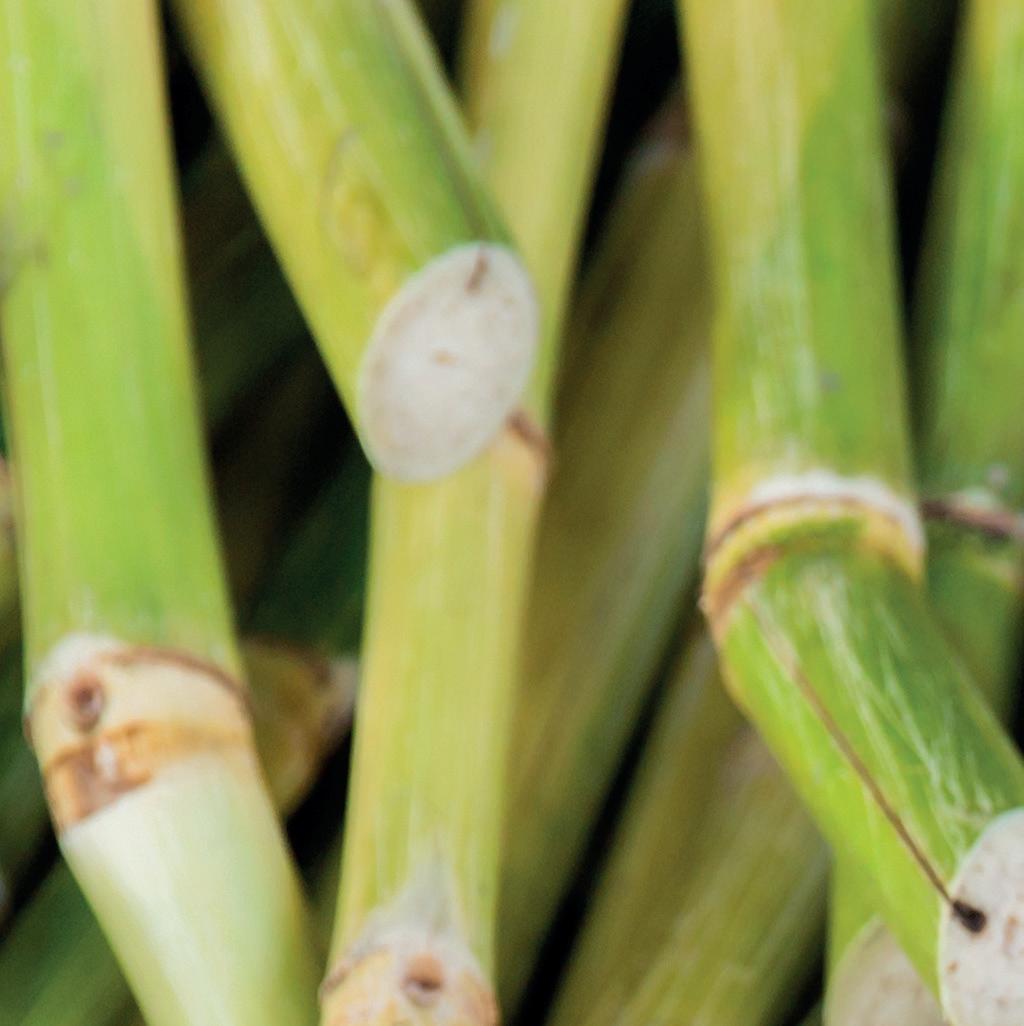
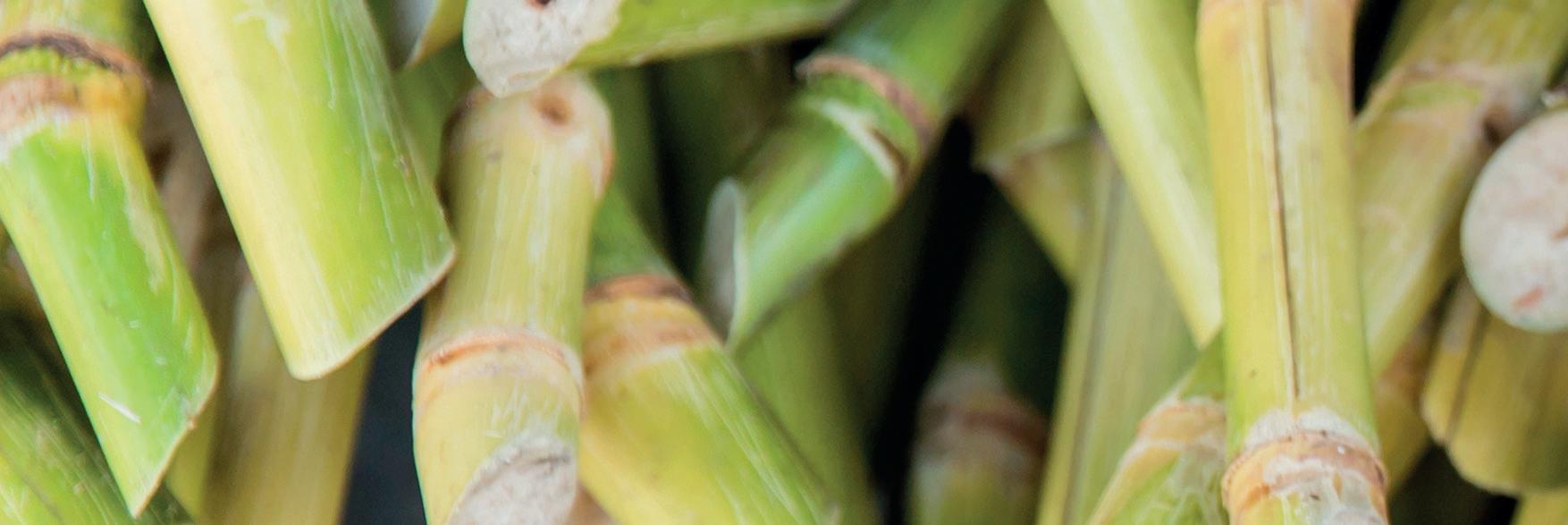

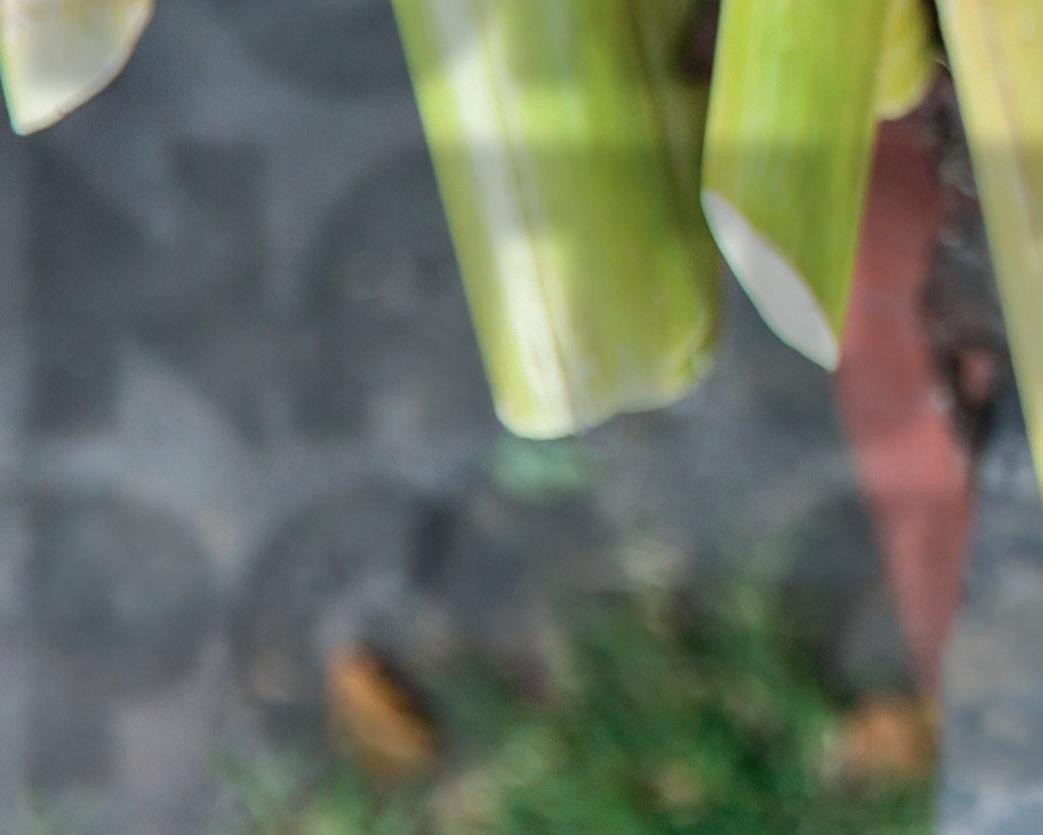

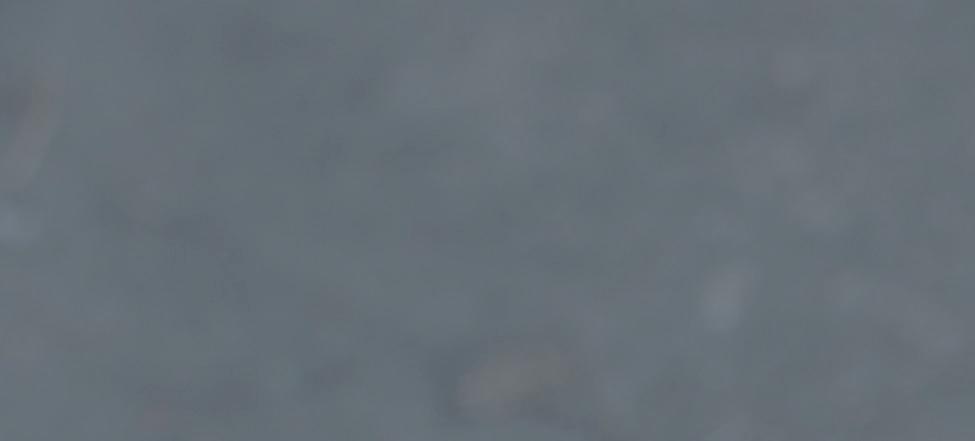
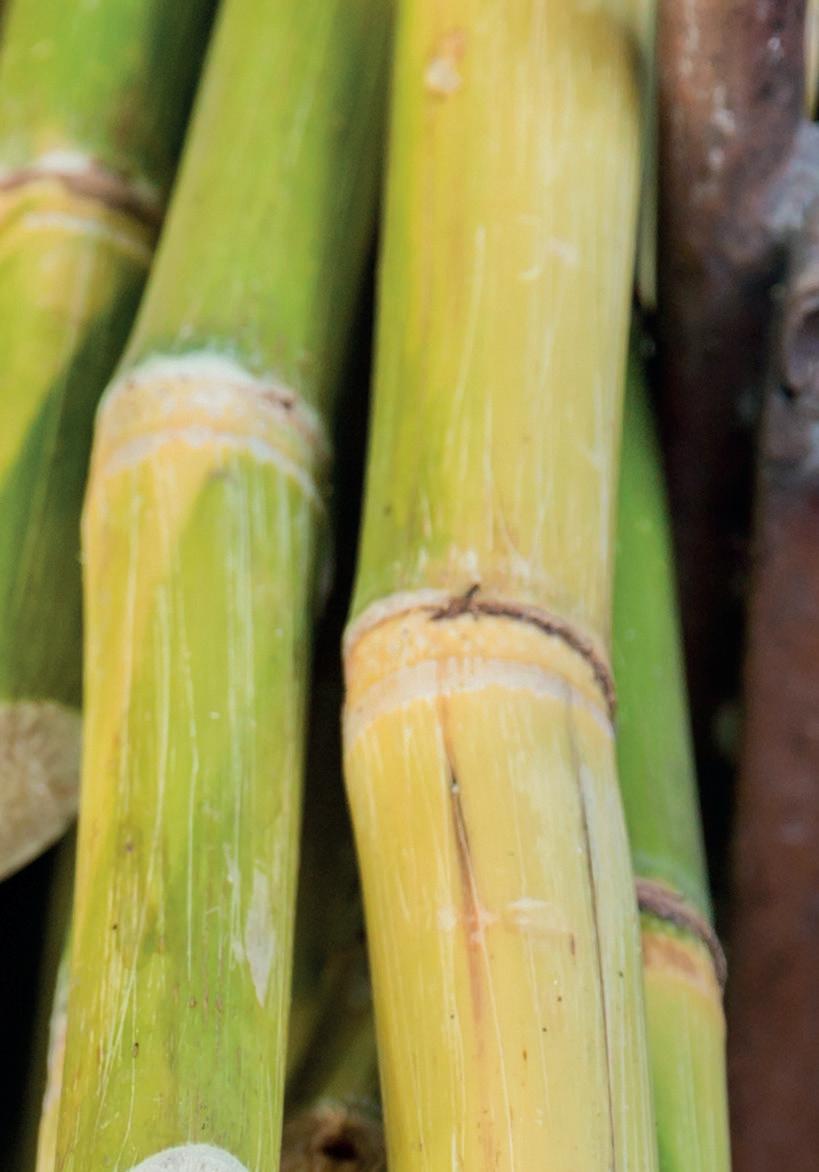
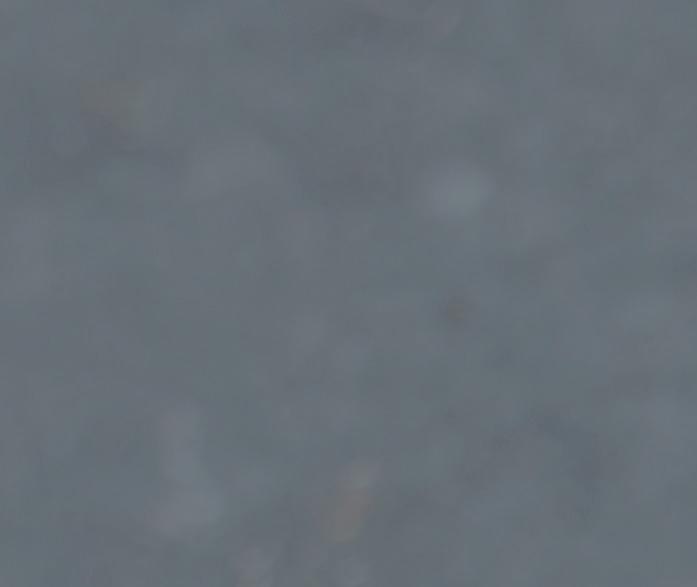

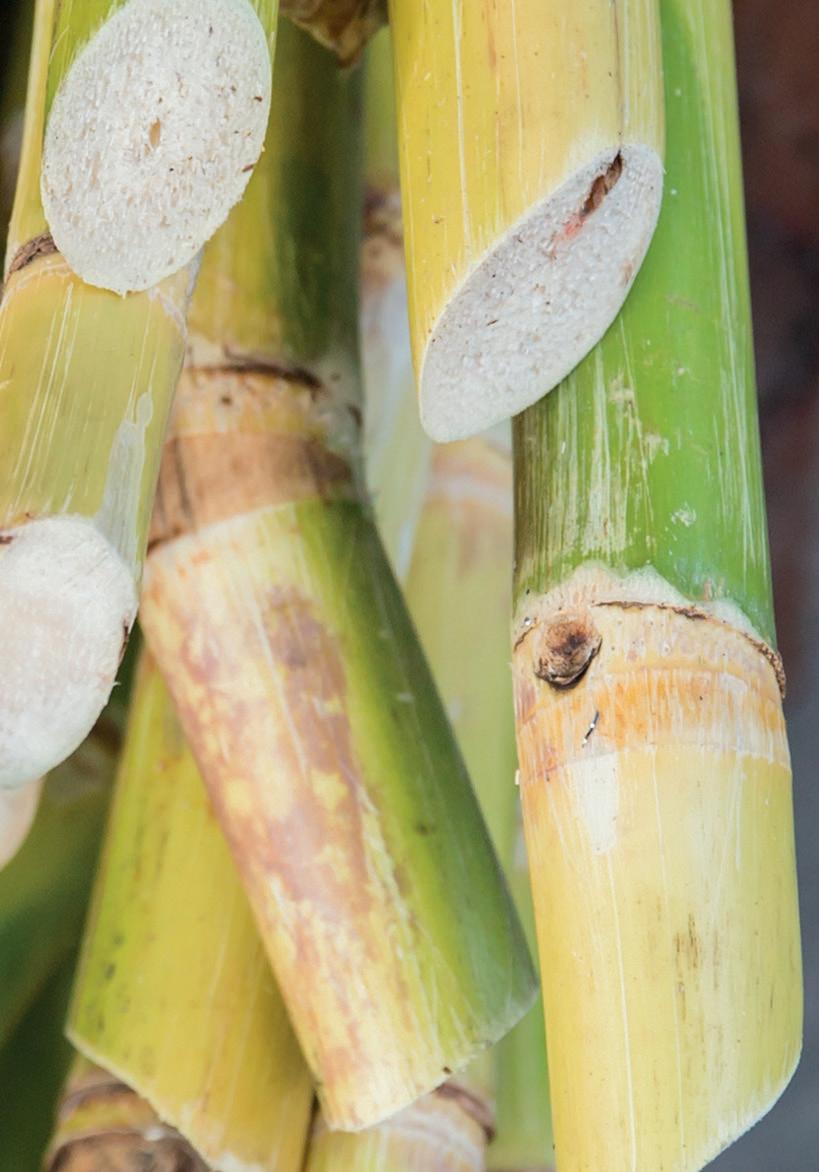
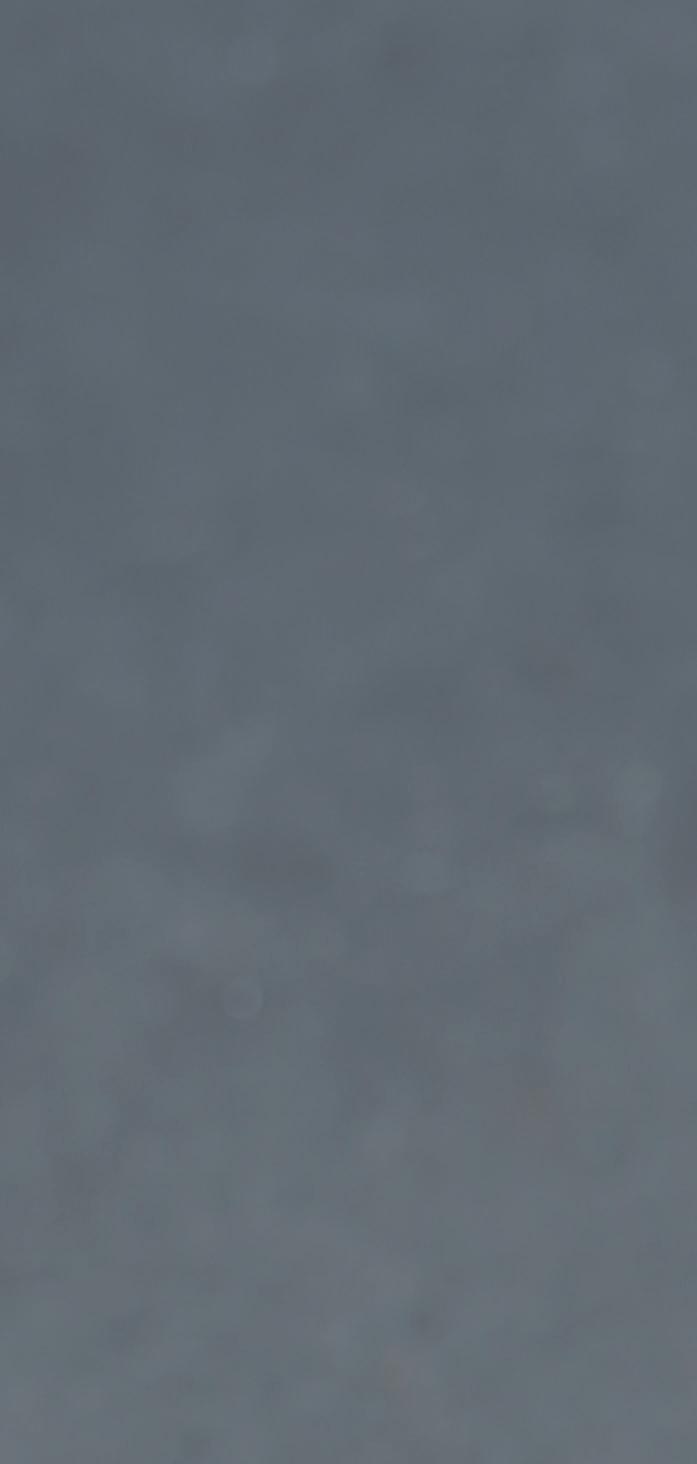
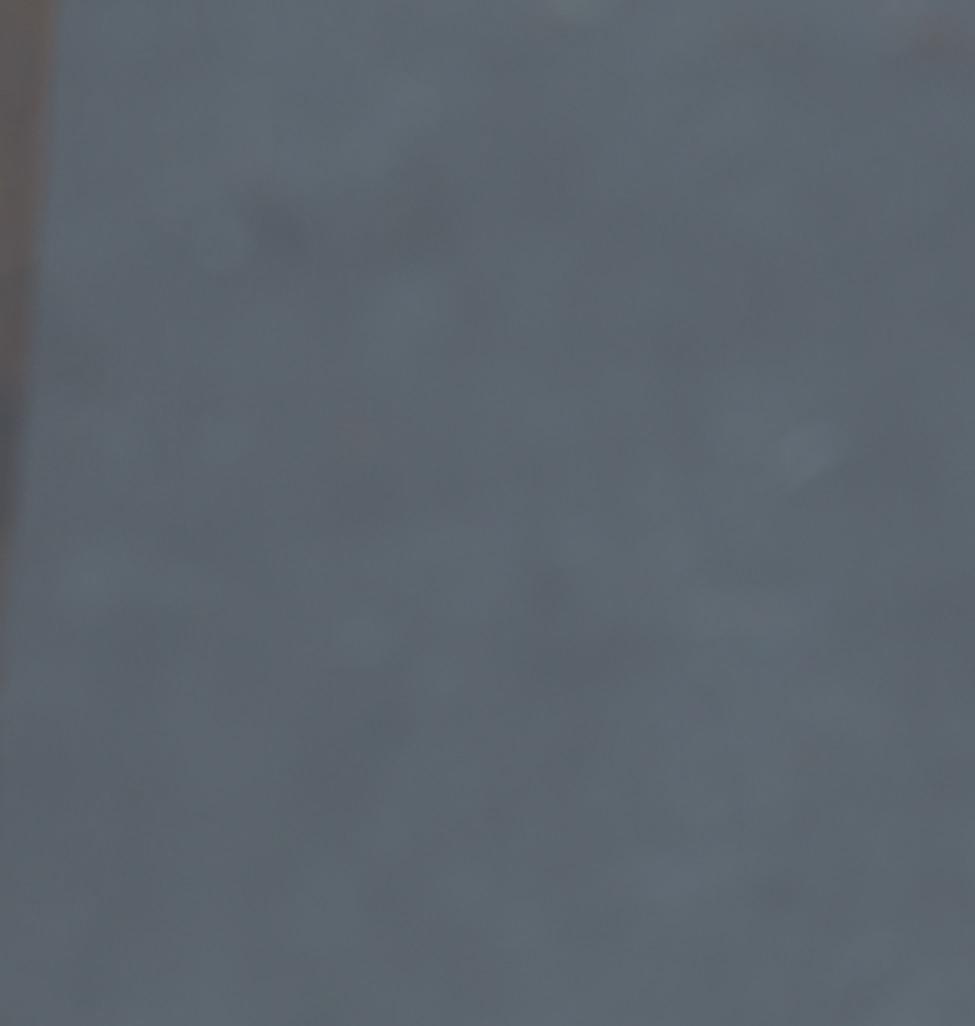
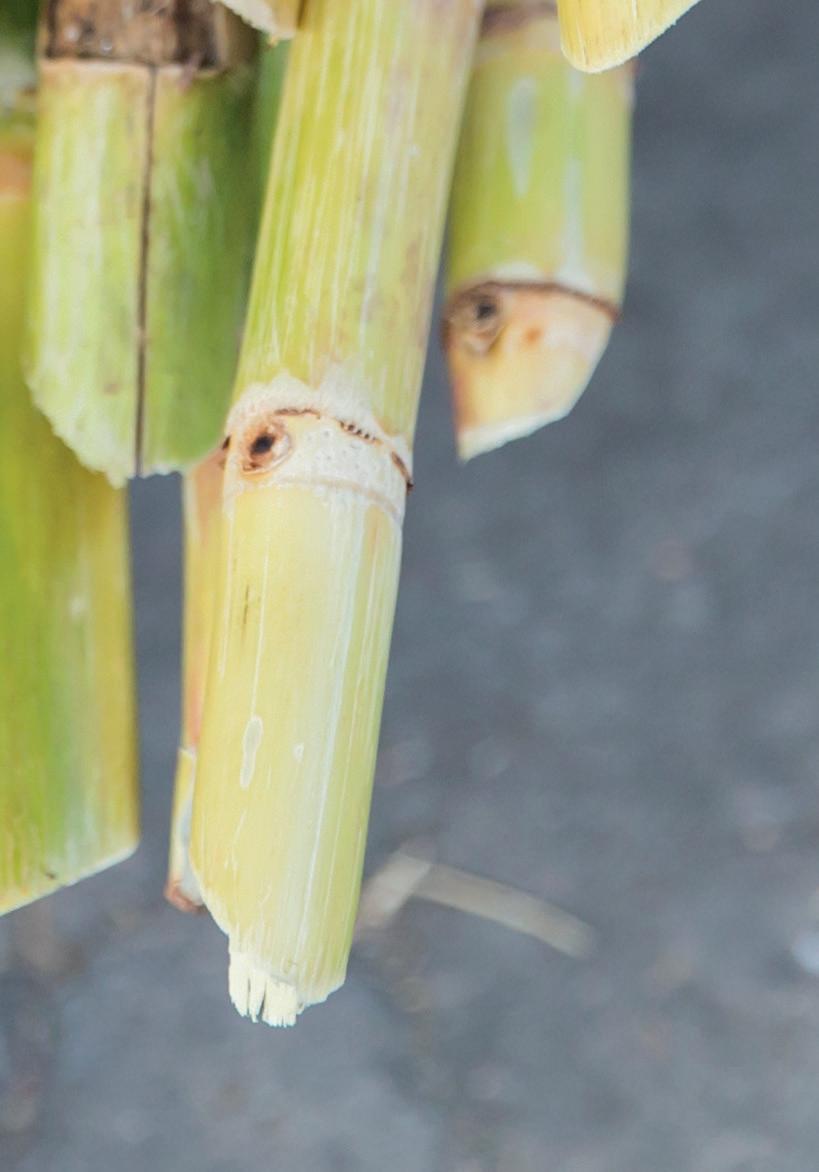
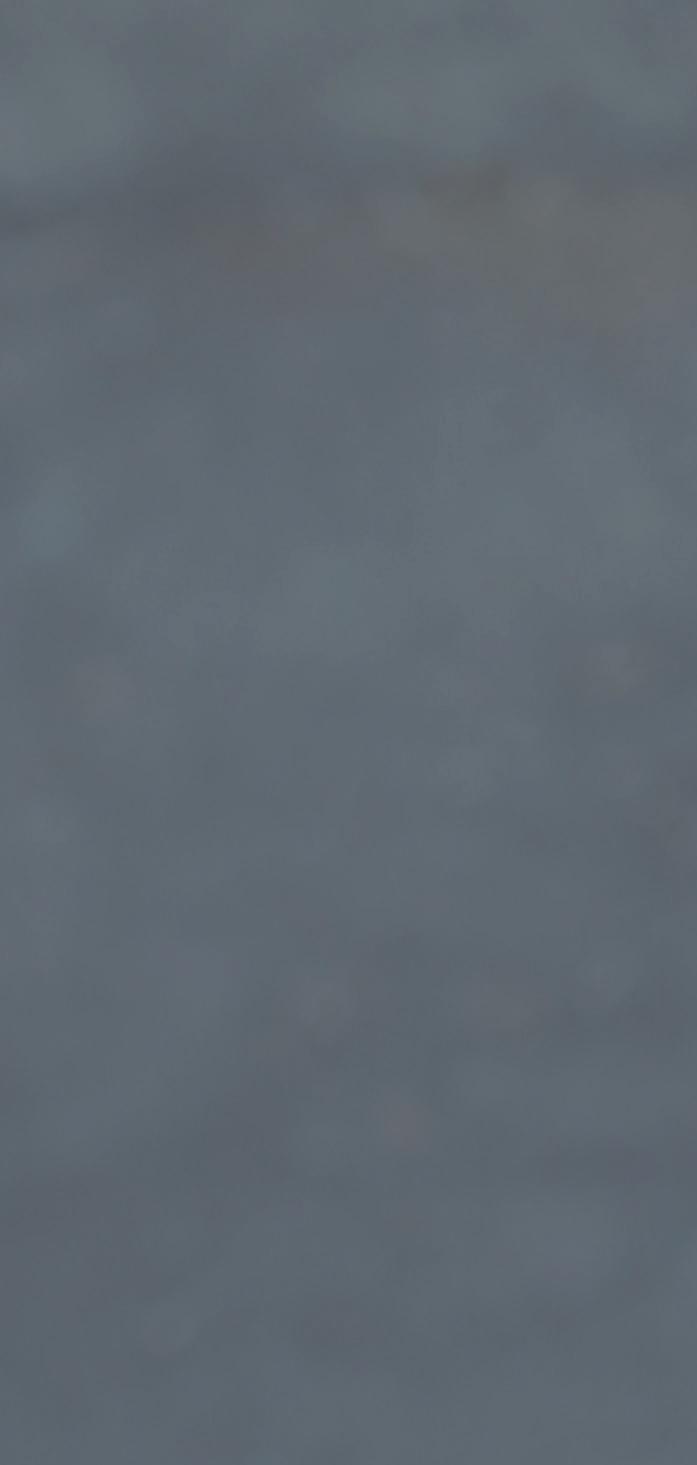
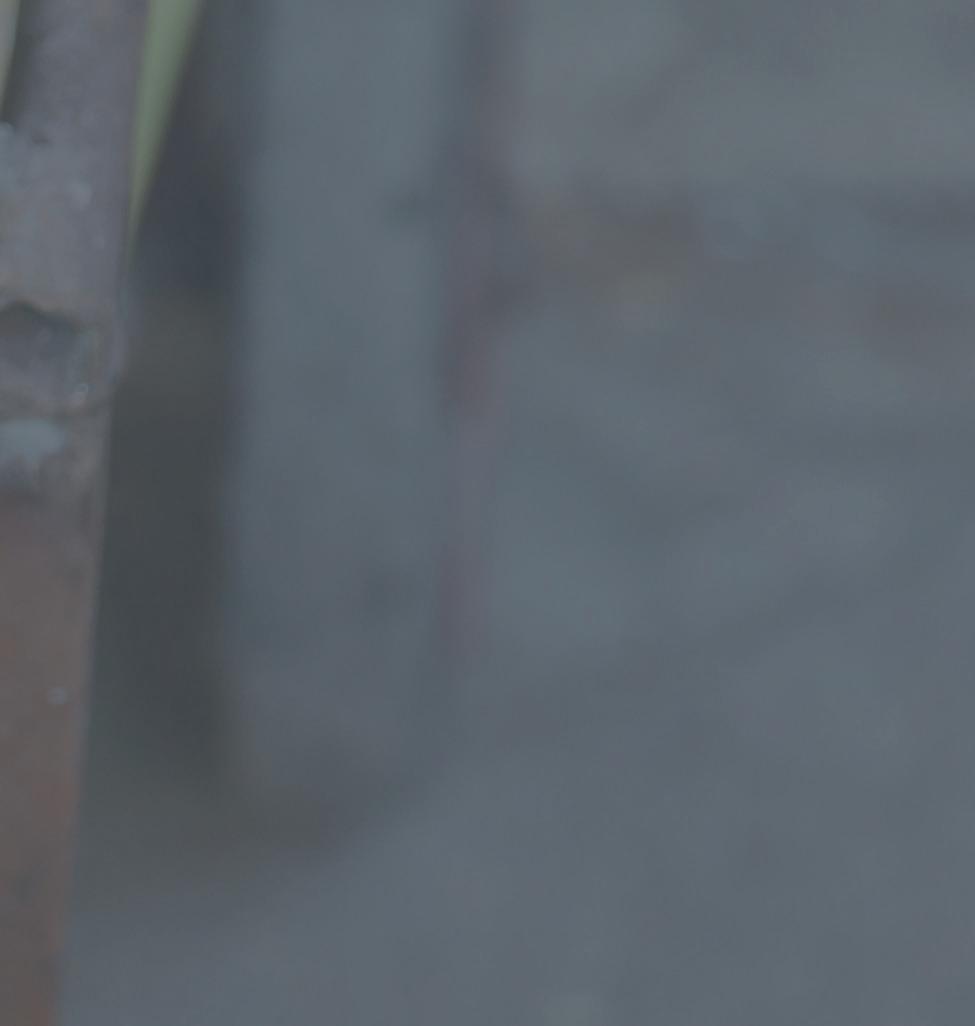
Arun Mote, Triveni Turbines, India, explains how biomass as a fuel helps to generate power in a sustainable manner.
The global power generation industry has been witnessing a major transformation in recent years, which is expected to also continue going forwards. The rapid depletion of fossil fuel reserves and the subsequent environmental impact caused due to carbon dioxide (CO2) emissions have brought sustainable energy sources to the forefront. This resulted in a changing energy generation mix and witnessed the shift from conventional energy sources (fossil fuels such as oil, gas, and coal) to renewable energy sources.
Globally, there is an increasing focus on the replacement of existing coal-fired power plants with clean fuel-fired power plants in order to reduce the carbon footprint. In this context, renewable energy plays a vital role in reducing carbon emissions. It is comprised of non-thermal (such as hydro, solar, and wind) and thermal energy sources.
In the case of thermal energy sources, bioenergy will remain the prime source of fuel going forward. The bioenergy industry turns many potential feedstocks into solid fuels (biomass or wood pellets, sugarcane residues and palm oil residues, etc.), liquid biofuels (ethanol, etc.), and gaseous fuels (biogas, landfill gas), which are then used to produce electricity, heat, and transport fuels.
According to an international report on solid biomass, in early 2020 there were nearly 4200 active biomass-based power plants worldwide, with an installed power generation capacity of approximately 72.5 GW. The installed power generation potential through biomass-based power plants is expected to reach 90.9 GW by the end of 2029, by adding approximately 1250 plants – making the combined total 5450 plants.
The drive to utilise locally available agricultural and forest residues has benefitted power generation closer to the point of consumption that has enabled setting up biomass-based independent power plants (IPPs). The IPPs play a major role in generating the power for sale to the grid or to specific customers. For a majority of the IPPs, a feed-in tariff (FiT) or Power Purchase Agreement (PPA) provides a long-term price guarantee.
Biomass (bagasse and non-bagasse) as fuel helps the CHP/cogeneration system generate power that is sustainable. Industrial use of biomass, particularly from sugar mills, rice mills, and palm oil mills, as well as wood waste from pulp and paper mills, is conducive to the production of power for captive consumption. The pulp and paper industry constantly focuses on improving energy efficiency, which is attained through increased use of non-bagasse based fuel (e.g. wood waste) for power generation, and by appropriate usage of steam.
Today, approximately 70% of biomass power is cogenerated with process heat. For example, the heat sources are being used for district heating in European countries and for industrial process heating application globally.
Triveni Turbines provides steam turbine solutions that use low-pressure steam generated through extraction turbines for a heating application by producing both heat and electric power (CHP). The cost of power generated through this process is 14 - 15% less when compared to the cost of power generated through IPPs – where the customer generates only electric power.
In comparison, solar renewable energy is used as a utility power plant, which means the customer generates effective electric power only during the day. On the other hand, the power that is produced through CHPs benefits the customer throughout the day by addressing the combined heat and power requirements of the plant.
To conclude this section, the rapid increase in electricity consumption, along with growing focus on electricity generation through biomass energy sources, is expected to unleash sustainable power generation through a cost-effective approach by combining both heat and power.
Case study – biomass-based power plant in Turkey
Challenge
Inconsistency in the availability of biomass fuel (forest waste, paddy waste, canola stalk, sunflower stalk, and sweet corn stalk) affects day-to-day operation of the power plant. Due to the variation of fuel input, the boiler load will thus be impacted, which in turn will affect the operation of the steam turbine.
Solution
The turbine internals (rotor and blades) and turbine controls have been designed to operate at lower loads with optimum efficiency and less maintenance. The steam turbine generator (STG) was delivered to the biomass-based power plant in Turkey at a record timeline of seven months and erection and commissioning was completed within 35 days during COVID-19 pandemic conditions.
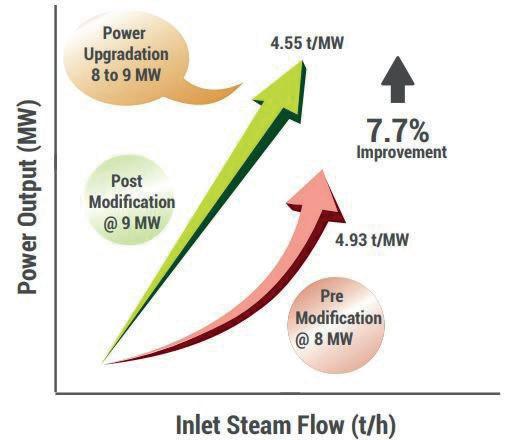
Figure 1. Performance curve indicating actual achieved parameters vs pre modification with a 7.7% efficiency enhancement along with a power upgrade.
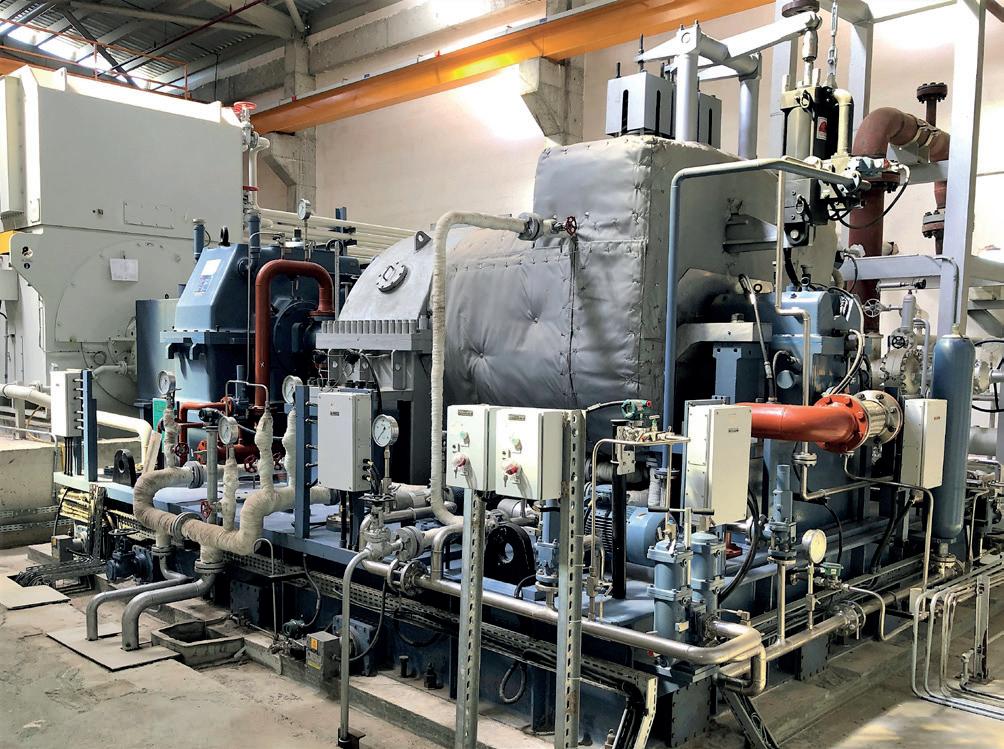
Figure 2. Biomass-based power plant in Turkey, driven by a 16 MW condensing steam turbine with an inlet steam parameter of 42 bar and 450˚C with 0.1 bar exhaust.
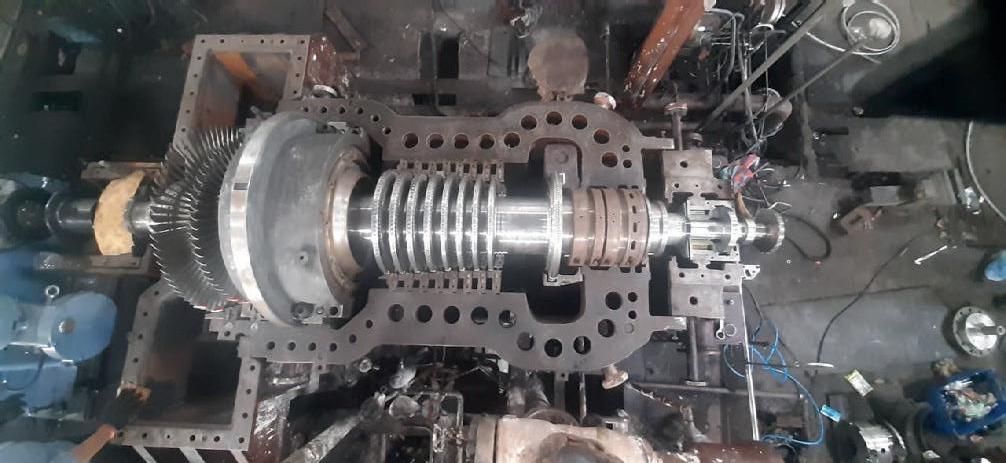
Figure 3. Newly bladed rotor with upgraded steam flown path placed on the existing housing and foundation.
Benefits
The customer is now able to run the power plant in varied fuel conditions by overloading the STG set wherever possible.
To complement this new product portfolio, Triveni’s refurbishment arm – Triveni REFURB – provides an after market solution for the complete range of rotating equipment across the globe. From steam turbines and compressors, to the gas turbine range, the company has adapted itself to ensure that customers find a one stop solution.
With rising costs, operating turbines efficiently is a necessity for cost saving and creating a positive carbon footprint. With age, the turbine becomes inefficient and increases the cost of producing power. The Triveni Turbines team works with the customer to understand the current needs and re-designs the existing turbine to meet the new parameters and ensure the turbine is efficient, thus leading to cost savings. The company’s efficient improvement programme was aimed at existing turbines across all brands by retaining the present housing and civil works. The internals including the rotor, stator, bearings, etc., are replaced with a highly-efficient design and upgraded steam flow path to offer customers the following benefits. > Up to 15% improvement in efficiency. > Upgraded steam flow path. > Re-use existing turbine housing and auxiliaries. > No modification on civil foundation and structures. > Life extension to over 100 000 hours. > ROI under two years resulting in increased profitability of operations.
Case study – natural degradation of turbines
A renowned customer was operating its 8 MW European OEM turbine for more than 15 years, but the turbine had begun to operate inefficiently due to natural degradation. Triveni Turbines reviewed the turbine design and confirmed to the customer that the parameters would be modified as per the current requirements and also ensure availability of 1 MW of extra power.
Triveni REFURB provided a solution to route the additional steam to the existing turbine with an upgraded steam flow path design. By only modifying the turbine internals (rotor with highlyefficient blades, diaphragms, bearings, and gear internals) with the new design, the customer could achieve a power enhancement of 9 MW with lower specific steam consumption than the normal running condition.
The overall project cost was significantly lower as there was no modification to the civil foundation and also the turbine housing was retained. The turbine was commissioned and handed over. With a 1 MW power addition and process stabilisation, the payback period is less than a year.
A strong future for bioenergy
In conclusion, bioenergy will remain the prime source of fuel going forward. Biomass (bagasse and non-bagasse) as fuel helps the CHP/cogeneration system generate power that is sustainable. This bodes well for the global power generation industry to captivate on the needs and requirements of both independent and captive power producers, as the demand for biomass power is expected to grow.