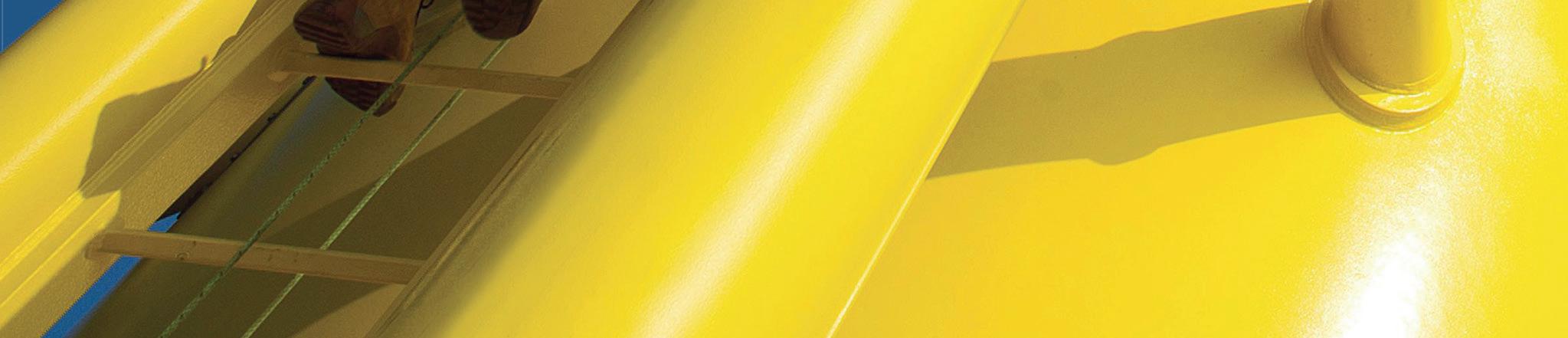
8 minute read
Drivers behind the designs
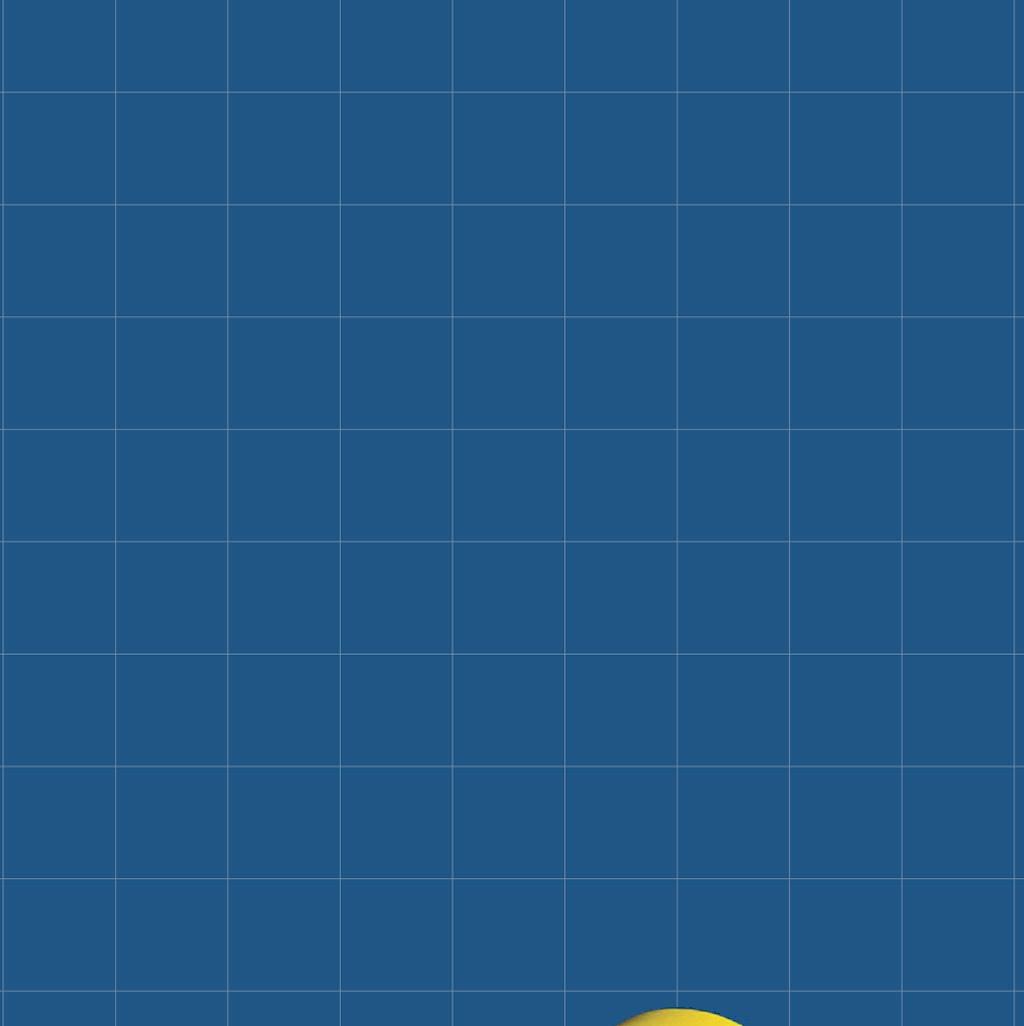
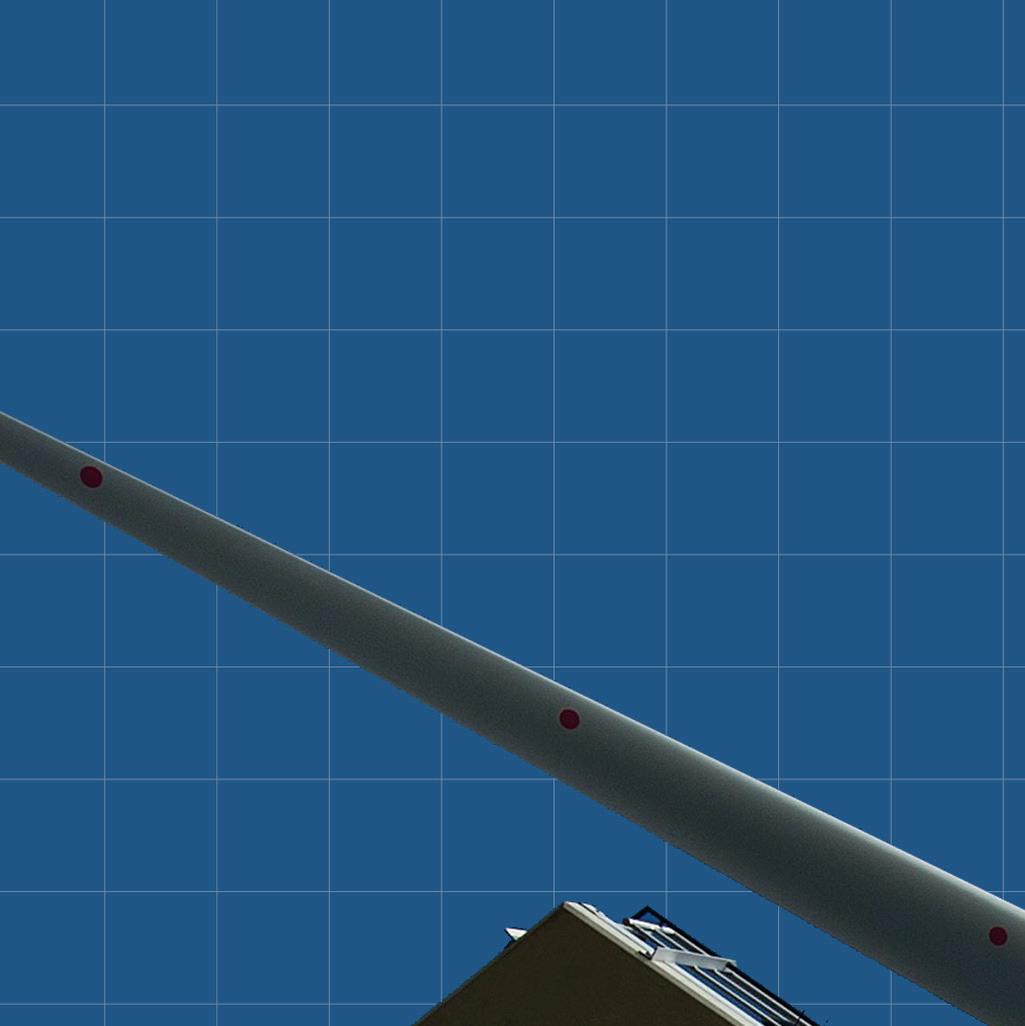

Chris French, freelancer, Wood Thilsted, UK,
details the challenges of offshore wind and how foundation design can overcome these hurdles.
Figure 1. It has been a long climb for offshore wind, but the industry is now all systems go.
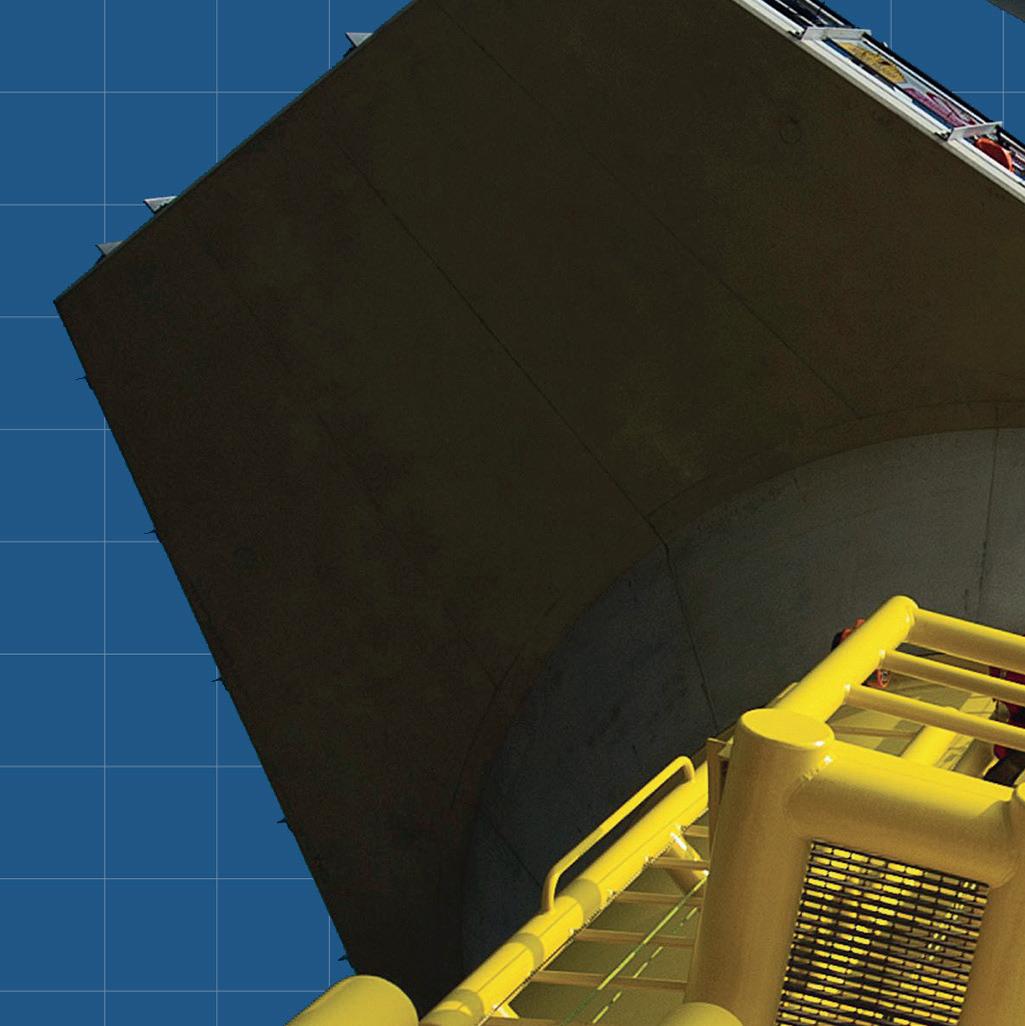
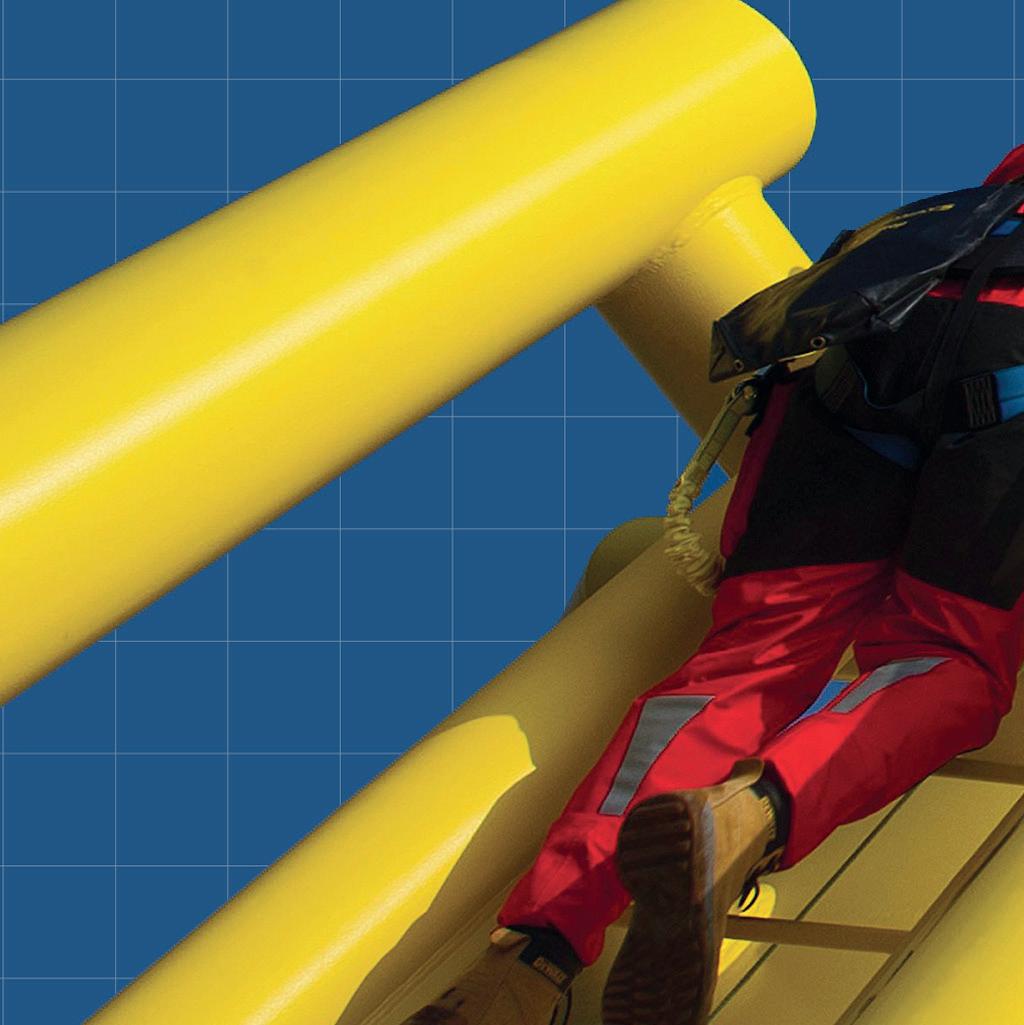
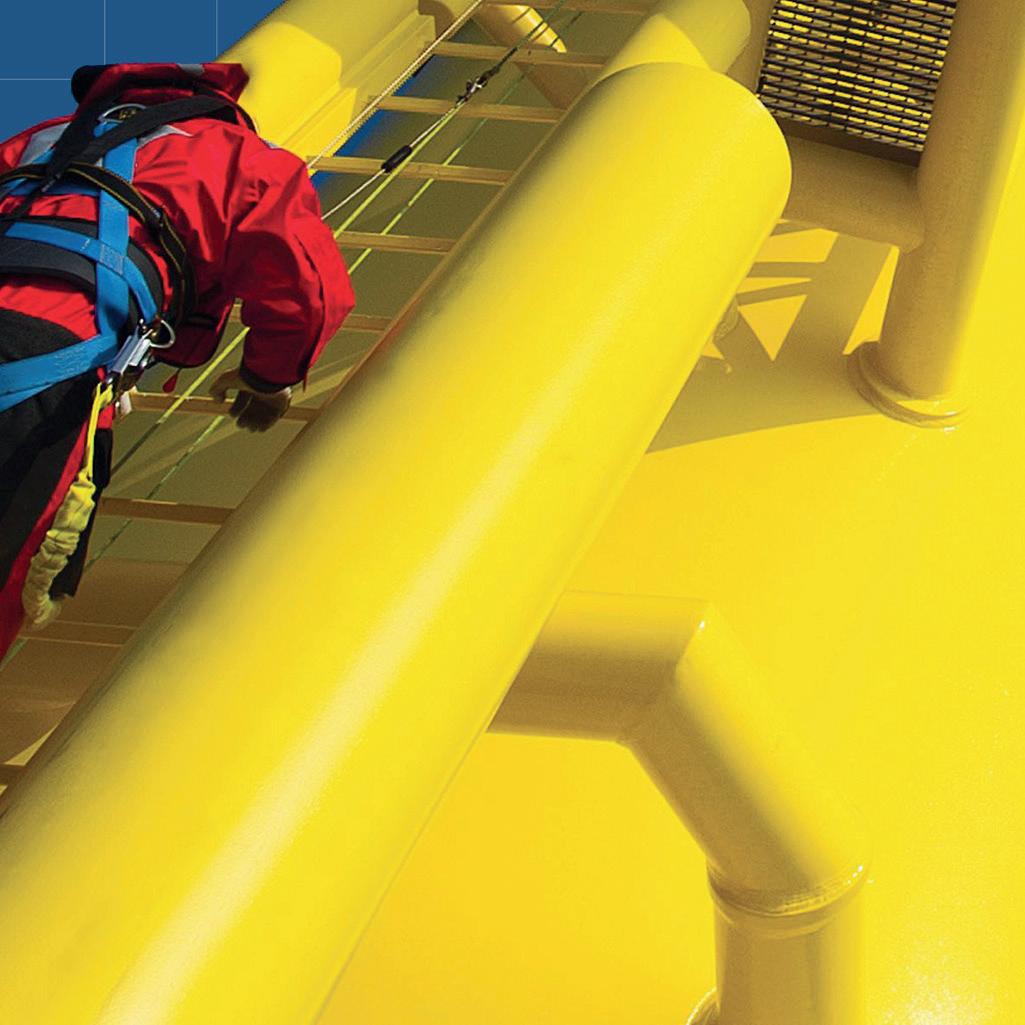
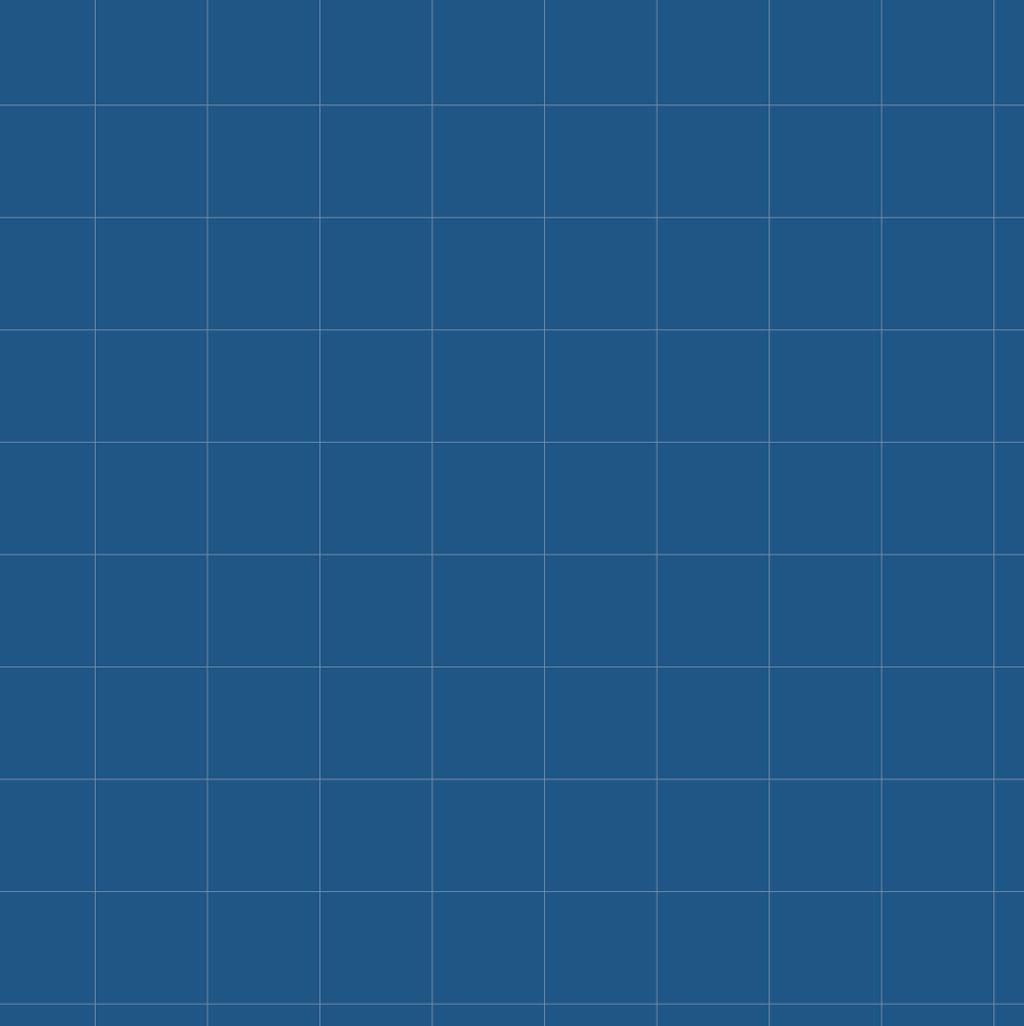
These are suddenly very vigorous and positive times for the offshore wind industry. Announcements about new projects abound – almost too fast to totally digest all of the impressive heights and diameters of structures – as well as the all-important energy generation, and job creation.
Finally, with the political will to fling the doors wide open for a full scale offshore wind revolution, there is no shortage of those who want to share the industry’s bright new spotlight.
But away from the headline figures, what about all the detailed design work that goes into making it happen? Additionally, in this rush to provide utility scale renewable energy, what about those who are trying to make it an affordable, safe, and sustainable way of powering the world?
Christian LeBlanc Thilsted, Co-Founder of Wood Thilsted, expresses his thoughts: “Worldwide, we are making numerous key appointments to ensure that we continue to have the right experts in place. Amid the rush of new projects, making balanced, well-informed decisions for customers is vital for the long-term. Offshore wind is very much part of global net zero targets, but this monumental energy transition must not be ‘at any cost’. The challenges of offshore wind’s levelised cost of energy (LCOE) reduction require a rational, multi-disciplinary approach. Only the highest calibre of engineering will ensure that the right decisions are made and LCOE targets are met.”
He added: “Getting the LCOE right means that offshore wind can take its place in history as an industry that, unlike others, did the right thing. So, even though we are all in top gear to meet demand, let us just pause to remember that ‘the end does not always justify the means’. Our ethos at Wood Thilsted is that we want to see a greener and more sustainable future for the world. In offshore wind, this goes hand in hand with achieving LCOE targets, which help prevent increases in energy bills for already
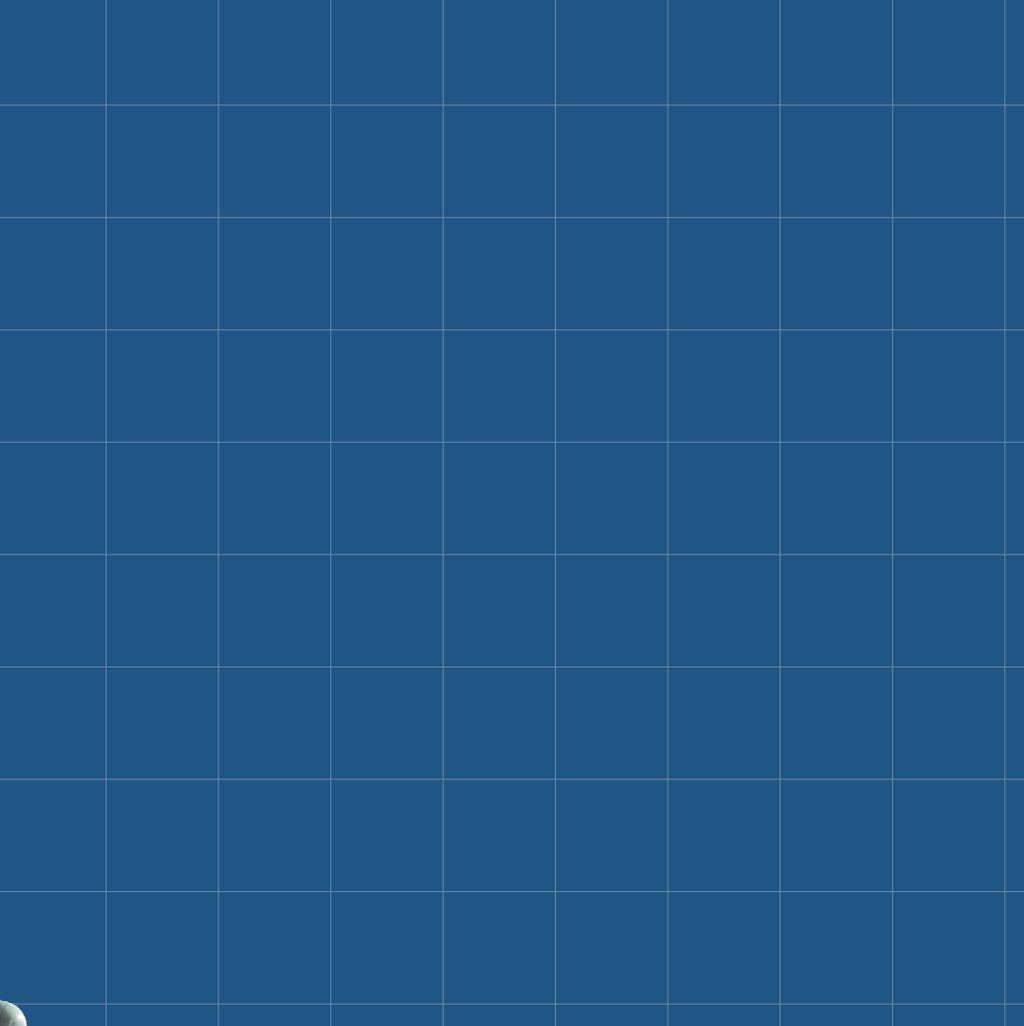
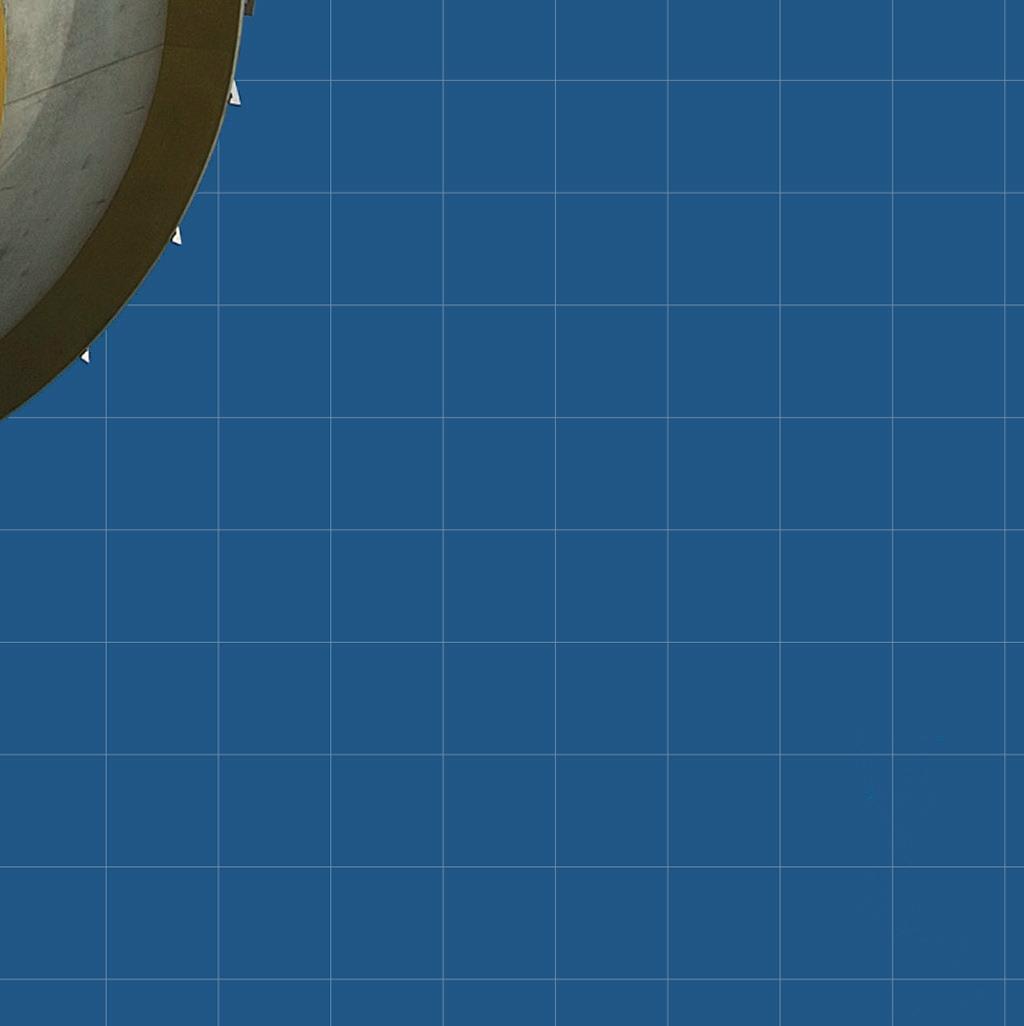

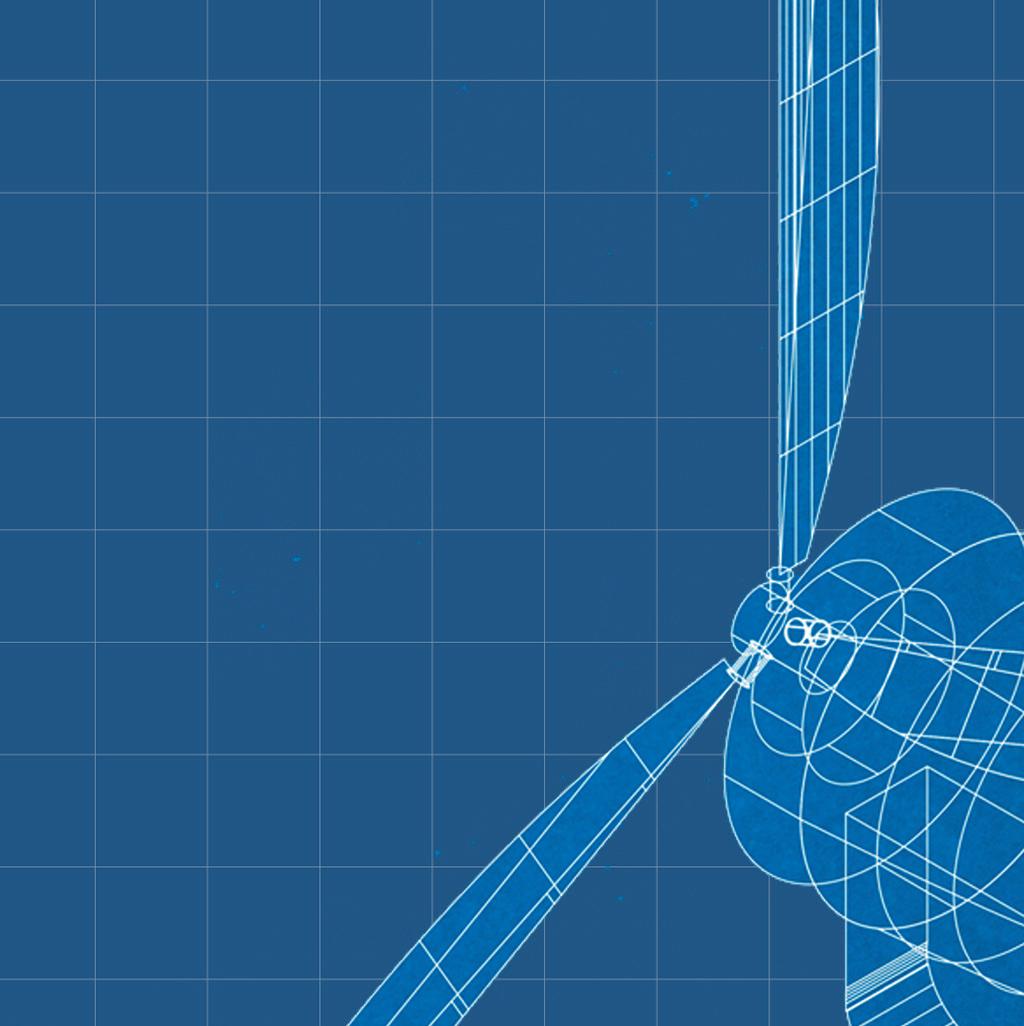

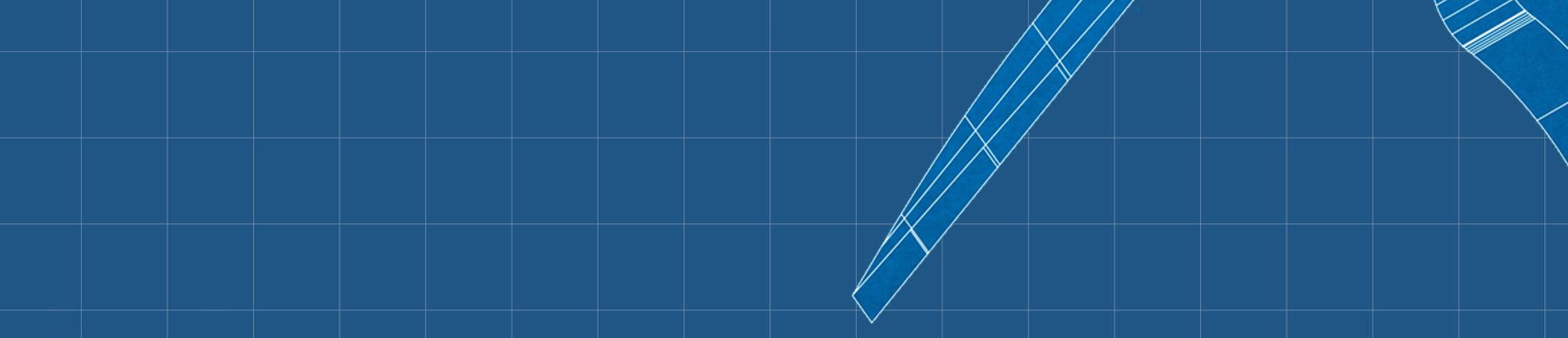
challenged families and communities. We need to keep the debate firmly open about how to best provide that affordable and sustainable way of powering the green world tomorrow.”
The UK leads the world in offshore wind. Between 2016 and 2021 over £19 billion has been invested – and with Scottish Power Renewables’ proposed East Anglia Hub of approximately 2690 next-generation turbines potentially generating up to 3.1 GW, there is no shortage of appetite for growth.
Across the Atlantic, Vineyard Wind is building the US’s first utility scale offshore wind energy project off the coast of Massachusetts – one that will generate clean, renewable, affordable energy for over 400 000 homes and businesses, while also reducing carbon emissions by over 1.6 million tpy.
In what seemed like only moments after President Joe Biden sat at his desk for the first time in the Oval Office, an ambitious goal was announced for the US to deploy 30 GW of offshore wind by 2030. Hitting this target could trigger more than US$12 billion/y in capital investment, creating over 40 000 jobs, plus a further 30 000 or more jobs in communities supported by offshore wind activity. The power created will meet the demand of more than 10 million US homes for a year.
Taiwan has ongoing projects with a combined capacity of 5.5 GW that are due to be completed by 2025, whilst Vietnam is looking to produce over 11 GW of offshore wind energy by 2025.
Three fundamental drivers for the design of offshore wind farms have, for a variety of historical reasons, evolved separately; the marine conditions (metocean), the wind conditions (atmosphere, energy production), and soil conditions (seabed and ground properties). This perhaps results from the way energy production grew with the onshore wind industry, whereas soil and metocean evolved with the coastal engineering and offshore world. There are many synergies between soil, metocean, and the wind world, but until now they have been almost distant cousins. It is the core competence of Wood Thilsted to bring these together to create a universal language.
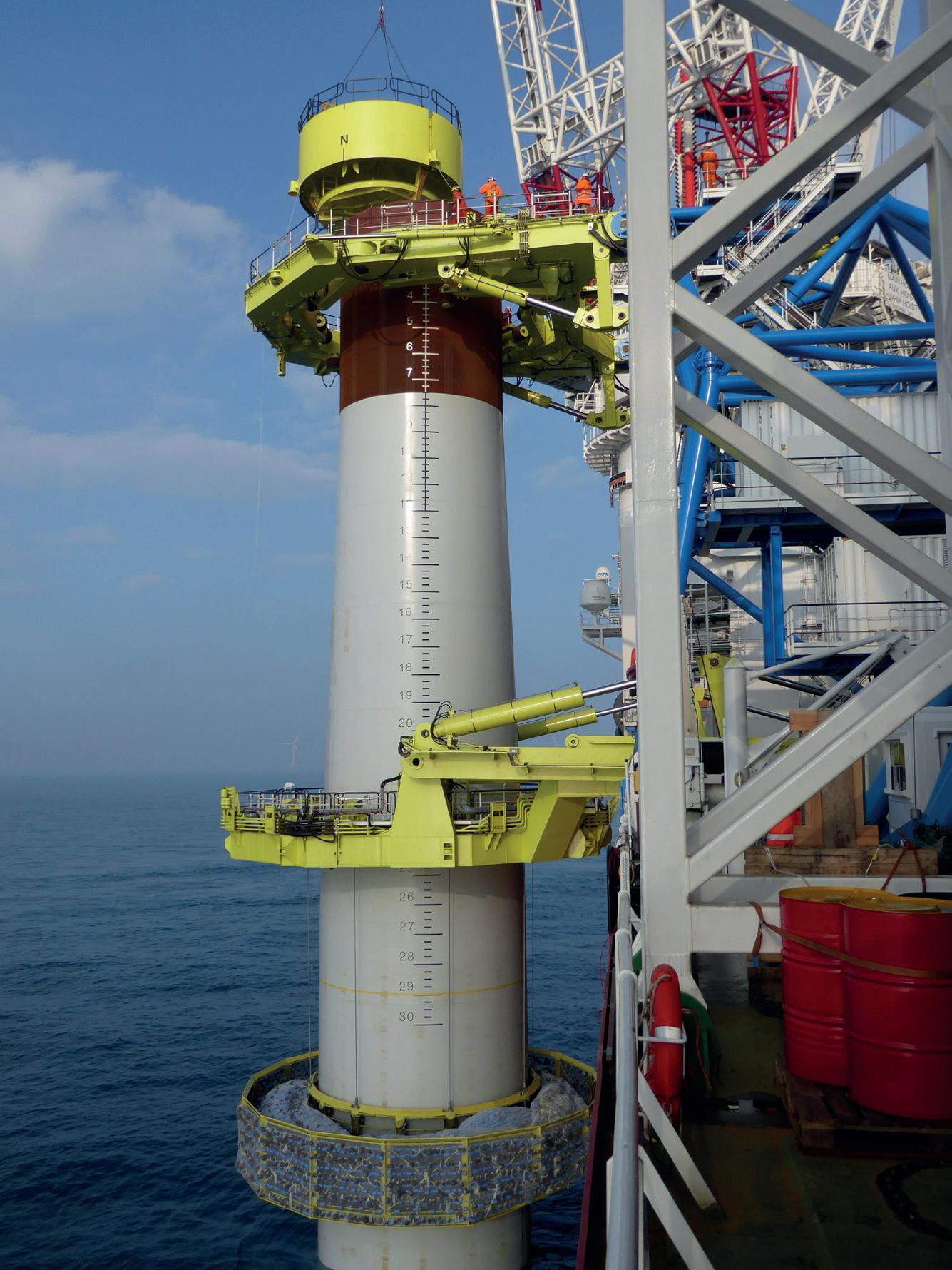
Figure 2. For the most efficient use of steel, monopiles are by far the main choice.
Each site is different and presents its own unique challenges, thus having the combined metocean, wind, and soil expertise is paramount. Wood Thilsted takes on technically challenging areas such as those with tropical cyclones and poor soil conditions in Asia, hurricanes in the US, icing in the Baltic, or common worldwide seismic areas. Armed with the right knowledge, it is then possible to finely balance the design of an offshore wind farm to achieve maximum power production at the expense of the least amount of material and resources.
So, in achieving global net zero, what are the best foundation designs that offshore wind can offer? Is it a straight choice between monopiles, which currently account for over 80% of installations – or jackets and floating foundations, which according to many, will increase in demand as offshore wind projects move to deeper waters, and the turbines increase in size?
Decreasing the LCOE
Decreasing the LCOE is the best service that can be provided for the wind industry and the world at large.
Offshore wind has plenty of room to improve on this. The choice between monopile, jacket, or floating foundations does depend on the location and its conditions – and as detailed designers, there is never any compromise with safety. The actual amount of steel used for a monopile is about the same as a jacket, but jackets have far more in the way of components,
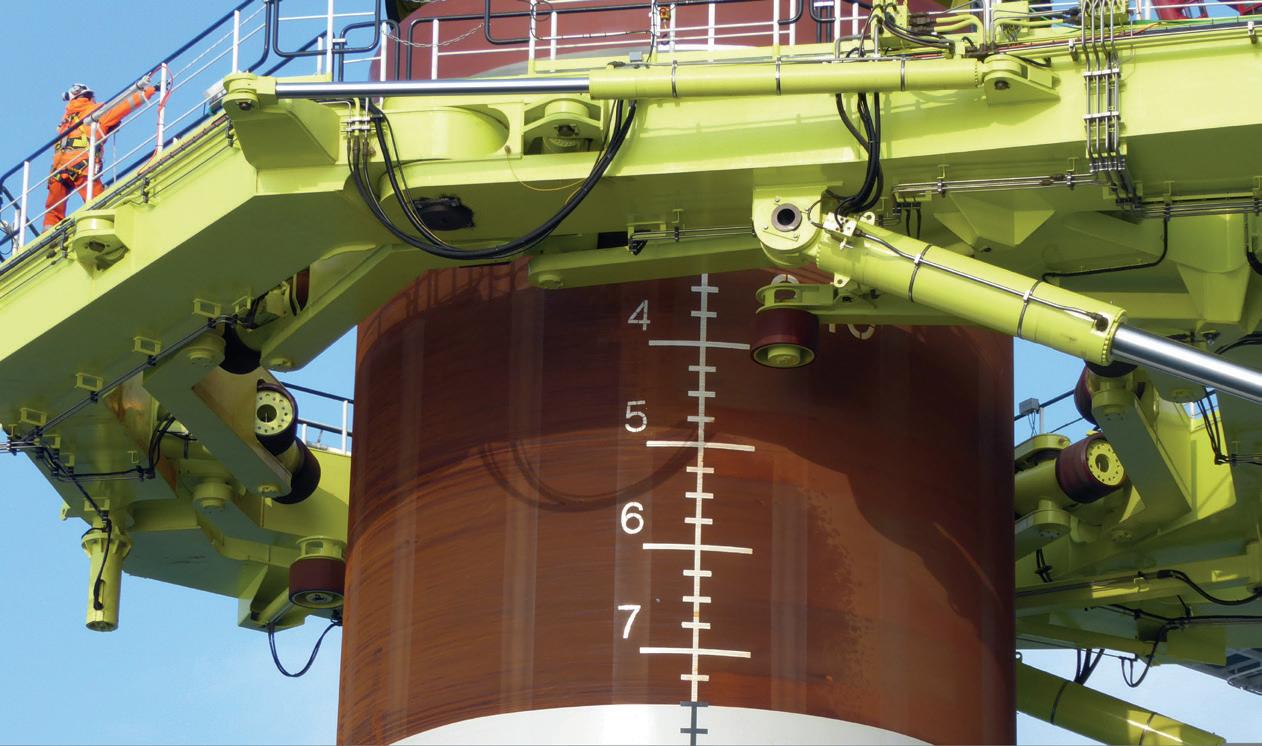
so are far more complicated, with more welding required, so overall, are more expensive.
Over a decade ago, experts were predicting that monopiles would have to be superseded by monopiles for deeper waters and bigger turbines, but that overtake is still to happen. Monopiles continue to prove themselves as superior structures and are very efficient in their use of steel. Importantly, economically, the supply chain is in place, with mass fabrication and the right logistics to move them around. When designing for each site, ideally a custom-made foundation is needed so that an off-the-shelf turbine can be purchased which will fit. In comparison, jackets are more of a jigsaw puzzle.
Putting technical terms aside, LeBlanc Thilsted explains how “with a monopile, you are, in some respects, carefully ramming just one big piece of steel into the ocean floor.”
It is understood that the supply chain needs to keep pace. Previously it has been used to monopiles of 6 - 8 m in diameter, weighing approximately 1000 t. Now, those diameters and weights are going up to 12 m and 3000 t. Talk of ultimate depths is not the ultimate point; it is all about the workable proportions, governed by the loads coming from the turbine. Connection details are also starting to present issues. Current bolt connections are getting so large that they are pushing the envelope on what can be manufactured with the required right tolerances – as a result there are already moves to consider the detail of switching to another type of joint to undertake the job.
As much as a monopile might appear simplistic, it is still all in the detail – and that critical combination at the earliest possible stage of wind, soil, and metocean experts working closely with the structural and loads analysis engineers to ensure accuracy. The difference in 0.1% in construction costs or predicted energy output could mean millions of euros/dollars to a client, so Wood Thilsted ensures it travels to the furthest degree to ensure that it optimises effectively.
Even with these exceptional feats of engineering, the market-related challenges can still be considerable, including the decreasing margins due to fiercely competitive leasing and auction rounds between developers. However, this is the nature of the game in order to become a mainstream and affordable source of energy.
Regulatory certainty, combined with ambitious long-term development goals, will no doubt help deliver the best value to the final energy consumer – and ensure that offshore wind can be safe, affordable, and sustainable.
Wood Thilsted remains fully focused on decreasing the LCOE for the offshore wind industry through optimised
Figure 3. Levelised cost of energy (LCOE) targets can be met using the highest calibre of engineering. Figure 4. Detailed design, that brings together all conditions (marine, wind, and soil) is crucial. designs that improve power production and require fewer resources to produce. Before everyone gets carried away in what to some seems like the next gold rush, it does not hurt to have some words of caution from within the industry. In helping decarbonise the planet, a solid reputation needs to be continued to be built – as a force for good.
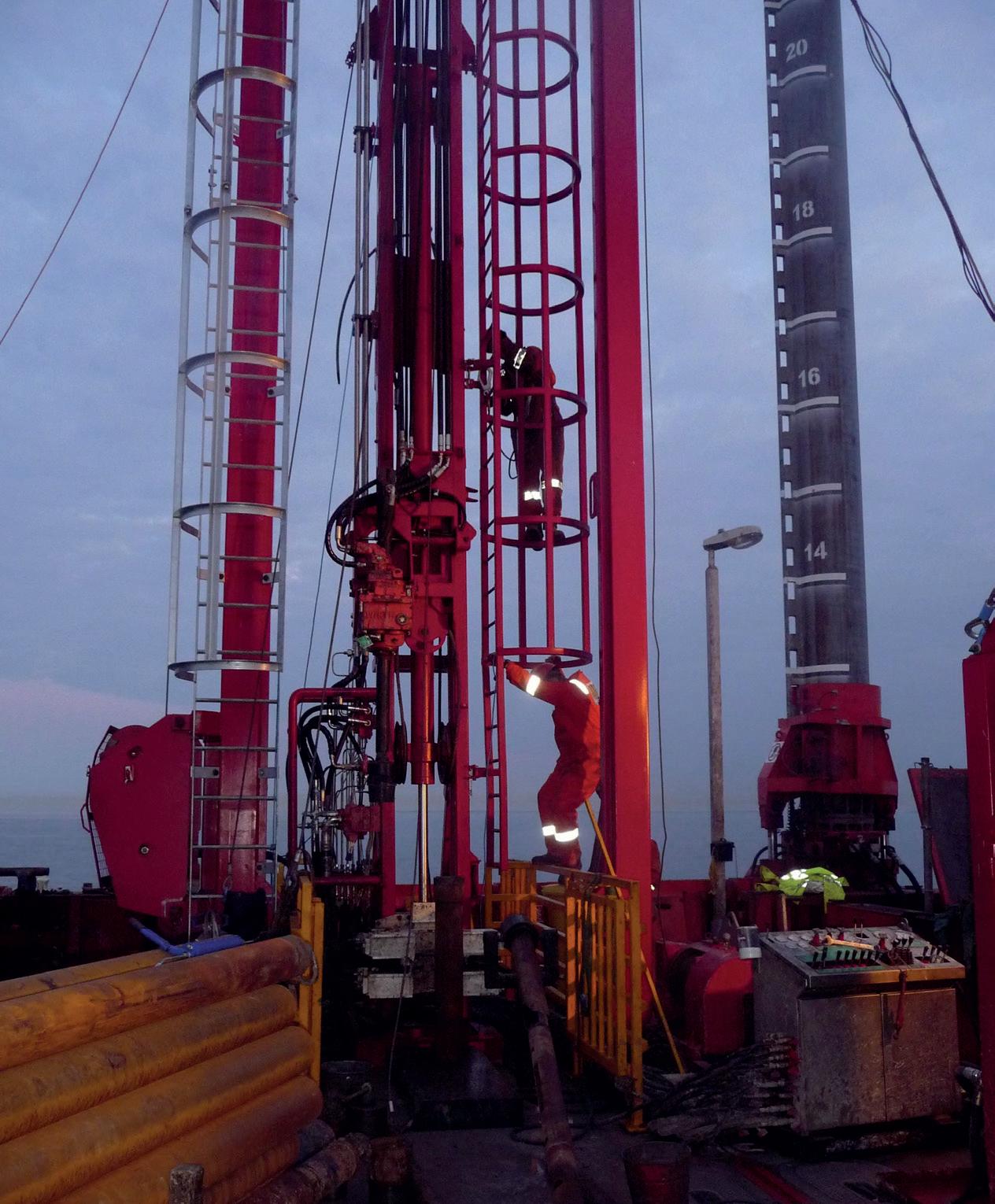