
12 minute read
How to fuel our world
esterification, and is then purified. The key stages of bioethanol production, however, are fermentation, sometimes preceded by pre-treatment to make cellulose more accessible, followed by separation – via distillation or rectification – and dehydration.
For both types of biofuels, separation is essential to purify the end product and meet biofuel specifications, allowing biorefineries to deliver high-octane bioethanol or biodiesel free of water and other impurities. As a result, using top performance separation processes with state-of-the-art equipment that fully addresses specific plant needs is essential.
In contrast to conventional refineries, where the structure of a distillation column and its internals is relatively standardised, the variability in bio-based feedstocks demands that biofuel producers adopt customised distillation set-ups. Therefore, it is crucial for businesses in this sector to choose separation specialists that can clearly identify what the process
Figure 1. Biomass ethanol lifecycle.
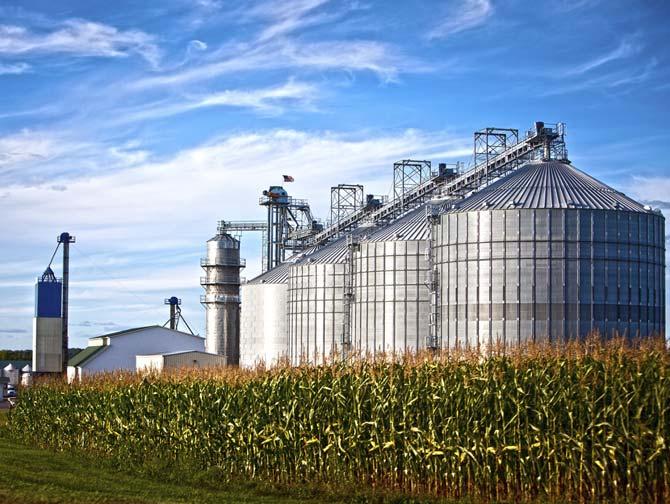
Figure 2. Corn crop and grain silos. requirements are and provide the most suitable system to fulfil them.
Full-service providers that can combine separation and heat integration systems, for example, are extremely beneficial, as they can offer seamless and comprehensive solutions while reducing the number of contractors. Firstgeneration biorefineries can benefit from implementing heat recovery and integration practices, as these are particularly effective in reducing energy consumption – and accordingly environmental impact.
Furthermore, due to separation specialists such as Sulzer, this first wave of greener fuels and energy was extremely successful. In 2013, approximately 86 million t (circa 95 million t) of first-generation biofuels were consumed globally, including 65 million t (nearly 72 t) of bioethanol. 1 At the beginning of 2016, the volume of bioethanol contributed to more than 80% of the 113 billion l of biofuels produced worldwide. 2
An evolving industry
Nonetheless, the global production capacity of biofuels could be increased considerably by using lignocellulosic material as feedstock. In particular, a study from 2016 concluded that North American autochthonous herbaceous crops, such as switchgrass, could help the US produce at least 1 billion tpy of biomass that could be used as feedstock for biofuels. 3
While this would not be able to replace the entire petroleum consumption of the US, it could allow the country to replace up to 30% with biofuels.
This is why second-generation bioethanol plants incorporate the use of plant-based biomass and lignocellulosic residues, such as bagasse. In this way, more businesses can use their resources to deliver green energy and adopt circular bioeconomy approaches. In addition, this expansion in suitable resources can optimise the biofuel/land area ratio, reducing the land demand for crop fuels.
Second-generation plants use different methods to convert biomass into biofuels. Pre-treatment is mandatory to break the hemicellulose-lignin complex cross-links and increase the accessibility of cellulose and hemicellulose. Subsequently, biorefineries can adopt various methods to produce bioethanol.
The first route, commonly referred to as the biomassto-liquid (BTL) conversion process, subjects the biomass to pyrolysis or gasification to produce synthesis gas (syngas), which is purified. This is then reformed to fuels using either a catalytic process, such as Fischer-Tropsch reactions, or by a biological conversion. The second route is similar to the process used in first-generation plants, as it relies on the transformation of sugar polymers present in biomass, i.e. cellulose and hemicellulose to monomeric sugars. These are fermented using microorganisms and purified. The third route is a combination of the other two methods. A chemical intermediate is produced by a biochemical process, transformed into fuels via pyrolysis and purified.
Another possibility is to utilise flue gas, for example, from steel mills, which is converted by micro bacteria into ethanol and then purified in highly heat-integrated distillation and dehydration steps into ethanol fuel.
The challenges of using other types of feedstock
Separation plays a key role in second-generation plants too. However, the process requirements and challenges are dissimilar, resulting in differently engineered mass transfer components. While potentially highly beneficial, the production of biofuels from non-edible forest and crop residues presents some key challenges associated with the higher complexity of the feedstock. If these are not properly addressed, second-generation plants could potentially increase their environmental impact and production costs, reducing the advantages of using renewable resources.
The sugar-rich crops used in first-generation bioethanol production result in almost no degradation products in the substrate. Therefore, ethanol concentrations above 10% are easily achievable, making the distillation process relatively straightforward and economical. The higher volume of impurities in second-generation feedstocks requires even more efficient high-performance separation solutions to make the process economically and environmentally feasible.
To accommodate these needs, columns should feature a high number of theoretical stages while remaining compact in size. In these situations, Sulzer’s AF type trays followed by slit trays are designed with a tray spacing of between 150 - 250 mm, which is half of that generally used. Therefore, it is possible to fit a high number of trays in a limited space, optimising the column’s separation performance.
Another particularly effective solution to address this issue in plants using biochemical routes consists of leveraging pervaporation, or vapour permeation. This is a membranebased separation technology that can efficiently replace conventional energy-intensive dehydration processes. Before the pervaporation step, distillation is generally required to remove components with higher boiling points and microbial cells from the fermentation broth. The distillate then enters in contact with one side of the hydrophilic membrane while a vacuum is imposed on the other side. As a result, the bioethanol is retained while water permeates in a vapour phase through the membrane.
Another key aspect that should be considered when building separation units for second-generation biorefineries is selecting high-performance mass transfer components that are particularly resistant. These pieces of equipment should be able to withstand the harsher operating conditions caused by the contaminants during the process itself. Robust materials are necessary to protect the separation units from fouling, plugging, and corrosion, maximising the equipment’s service life. In this way, plants can reduce their CAPEX and their OPEX costs, as well as downtime associated with repairs and maintenance, and additionally reduce their overall environmental impact.
For high fouling applications, Sulzer’s VG AF TM (V-Grid anti fouling) trays are an example of suitable internals for separation columns in first-generation and second-generation biofuel plants.
The outlet weirs are highly resistant and the trays can also be equipped with extra-large fixed valves, which were developed specifically for severe fouling applications.
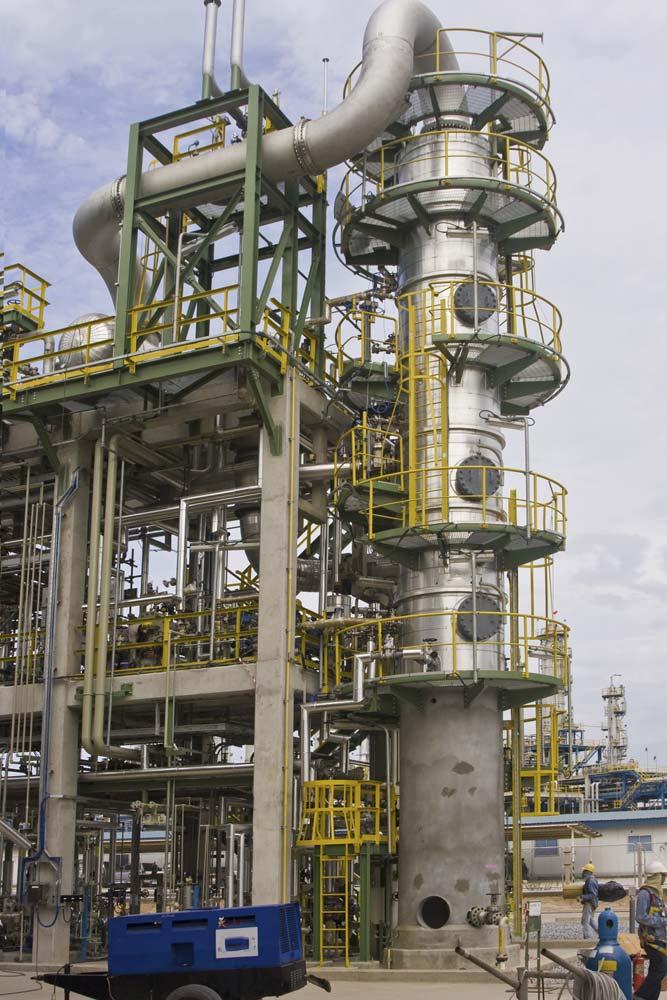
Figure 3. Distillation tower for bioethanol recovery.
Finally, it is essential for second-generation biorefineries to implement heat-integrated process solutions to reduce their energy consumption, operational expenses, and environmental impact. In this way, plants can deliver highly sustainable biofuels. In fact, an elevated use of resources and energy in biofuel production would compromise the sustainability goals of such processes.
More precisely, second-generation biofuel feedstocks typically enter distillation with lower alcohol concentrations, compared to first-generation feedstocks, thereby significantly increasing the specific energy demand. Therefore, it is crucial to minimise energy usage to maintain a low environmental footprint. To achieve this, businesses can utilise heat integration methods, such as multi-effect distillation or compressor/turbo fan technologies.
Third generation and beyond: unlimited possibilities
The quest to find new, green feedstocks has not stopped, and third-generation biorefineries are now starting to be developed. These will utilise algae, which can produce biomass faster and require even less land surface than lignocellulosic feedstocks. In particular, microalgae are able to double their biomass in less than 24 hours. This means that plants could benefit from a 49 - 132-fold reduction in the medium culture
Learn more about our advertising opportunities

• Brand exposure • Lead generation • Premium packages
For more information, please contact: will.pownall@energyglobal.com
time when shifting from canola or soybean feedstocks. 4
While in its early stages of development, it is already clear that third-generation biofuel production, like second-generation solutions, will use a biomass feedstock of high complexity. As a result, it also requires engineered separation equipment, especially in downstream processing, while also presenting new challenges in the initial stages of production. This is also the case for other innovative processes aimed at obtaining fuels from other types of waste streams, such as industrial emissions and non-recyclable plastic. Ultimately, the sky is the limit when developing new biofuel production routes, as long as forward-looking separation specialists are involved to identify and develop suitable purification solutions.

Keeping biofuel plants up-to-date
Choosing the right separation equipment to create successful biofuel plants is key, but it is also important to keep them running at peak performance. Continuous support during operation, in the form of servicing, maintenance, and upgrades is therefore crucial for biorefineries. Field specialists that have extensive expertise in separation processes and technologies, such as Sulzer and its Tower Field Service (TFS) branch, can support these activities.
In addition to performing regular maintenance, it is important for plants to stay up-to-date with the latest processing technology as biofuel production evolves. For example, as new developments in yeast strains allow
Figure 4. A key aspect that should be considered when building separation units for second-generation biorefineries is selecting high-performance mass transfer components that are particularly resistant.
plants to increase their bioethanol yields, the separation units need to keep up with these advances to avoid any process bottlenecks.
Biofuel producers can address this issue by expanding their distillation columns horizontally or vertically, i.e. expanding the column diameter or increasing the number of theoretical stages, as well as by altering or replacing the column internals with state-of-the-art solutions. Defining the most suitable and effective revamp strategy is crucial to completing appropriate modifications to trays, structured packing, and liquid distributors in bioethanol plants. By implementing these changes, biorefineries can potentially increase their column capacity by over 25%.
Conclusion
As the pool of suitable feedstocks for biofuel production expands, a growing number of businesses can utilise their resources, waste, and byproducts to increase their sustainability and generate additional revenue. To achieve this, it is crucial to collaborate with an industry-leading mass transfer specialist. Businesses can benefit from high-quality equipment that fully meets specific processing requirements, turnkey solutions, and even full plants, as well as continuous support via maintenance services, repairs and upgrades.
Sulzer has extensive experience in delivering customised column internals and full plants for separation processes in biofuel production, as well as highly effective services for existing equipment. In addition, the company has supported a number of innovative projects aimed at converting waste into sustainable energy and fuels.
References
1. RULLI, M., BELLOMI, D., CAZZOLI, A., et al., ‘The water-land-food nexus of firstgeneration biofuels’, Scientific Reports 6, 22521 (2016). 2. BERTRAND, E., VANDENBERGHE, L.P.S., SOCCOL, C.R., et al., ‘First Generation
Bioethanol’ Green Fuels Technology, Springer, Cham (2016). 3. LEE, D.K., ABERLE, E., ANDERSON, E.K., et al., ‘Biomass production of herbaceous energy crops in the United States: field trial results and yield potential maps from the multiyear regional feedstock partnership’, Global Change Biology Bioenergy,
Vol. 10, No. 10 (2018), pp. 698-716. 4. PICAZO-ESPINOSA, R., GONZALEZ-LOPEZ, J., MANZANERA, M., ‘Bioresources for
Third-Generation Biofuels’, Biofuel’s Engineering Process Technology, ed. Dos
Santos Bernardes, M.A., IntechOpen (2011).
Joey Broda, FortisBC, Canada, looks at how RNG produced from wood wastes could help decarbonise British Columbia’s natural gas grid.
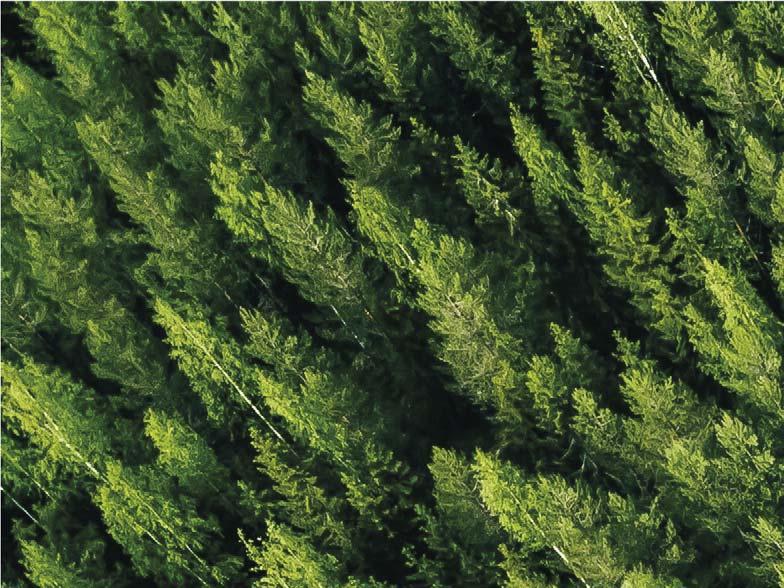
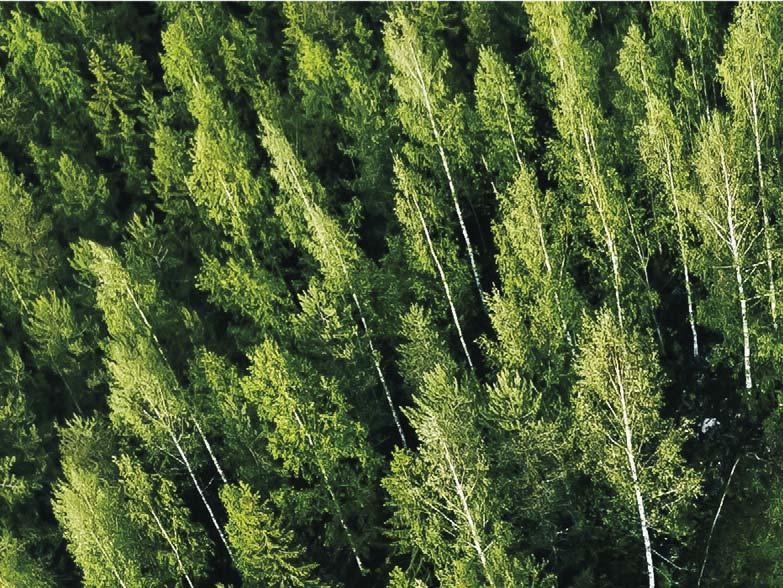
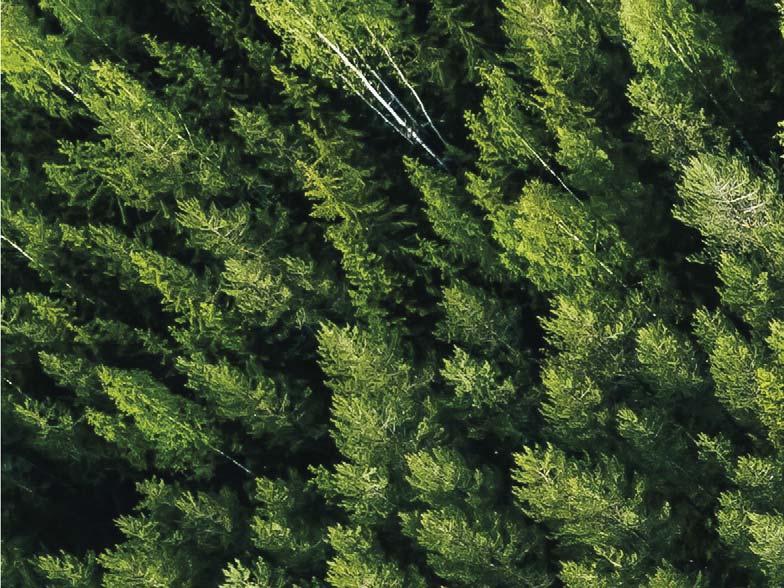
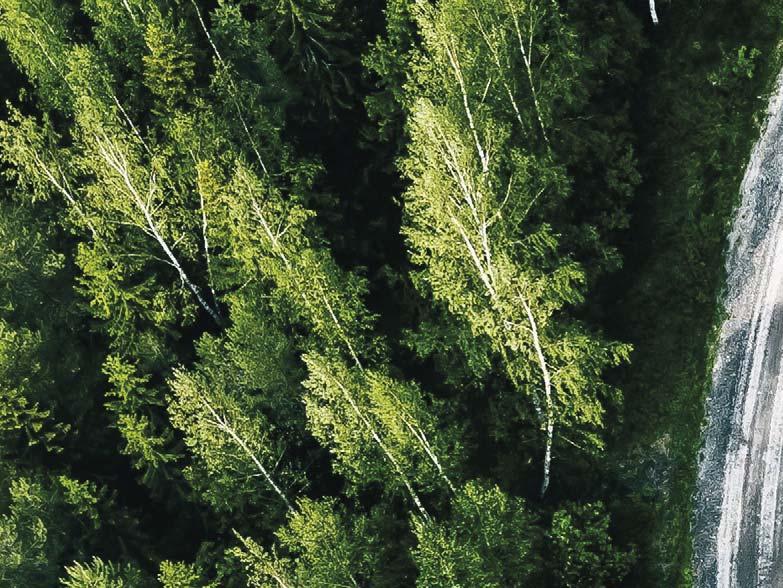



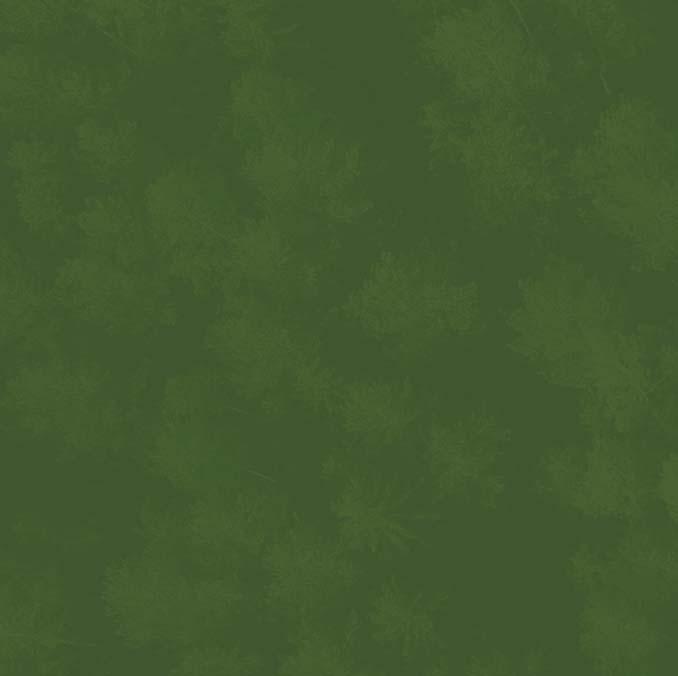
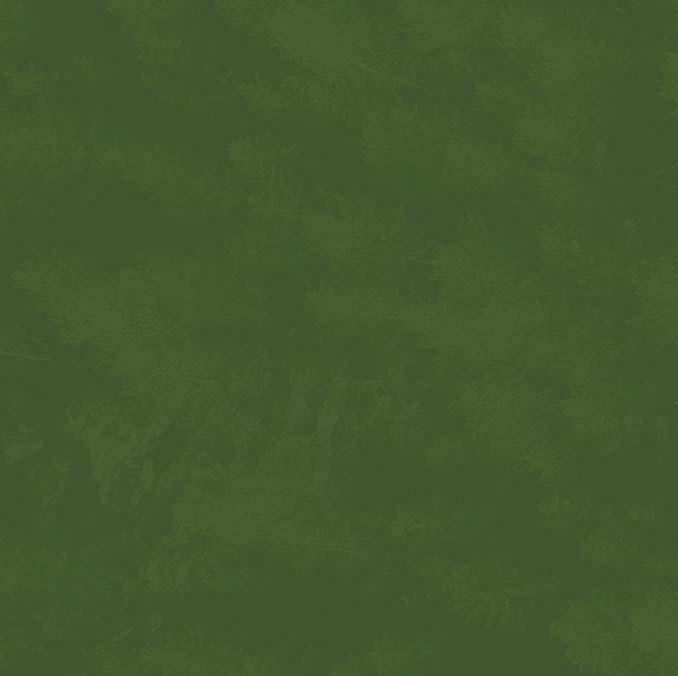

Decarbonisation is one of the foremost scientific and industrial challenges of this era. In some ways, decarbonised energy looks familiar and can be built on the existing backbone of electrical and natural gas infrastructure. However, some parts will be new and unfamiliar.
Renewables are a crucial part of a decarbonised energy system, and often these renewable energy systems will be composed of elements unique to their location. The Canadian province of British Columbia (BC) has a number of local challenges and opportunities distinct from other Canadian and North American regions. While BC already has a largely low-carbon electricity supply, it is a significant producer of natural gas, and has a larger natural gas grid than electricity grid, making it an important region in which to decarbonise natural gas supply. The current primary method of decarbonising natural gas is through producing biomethane from anaerobic digestion. While BC is home to a number of anaerobic digestion operations, its smaller population and fewer agricultural regions limit the ultimate potential of anaerobic digestion. However, there is an opportunity to expand the methods of decarbonising the natural gas supply.
BC is a province of river valleys and mountain ranges. Amongst these valleys is a large supply of lumber that contributes an estimated CAN$14 billion to the local economy. BC’s forestry-related activities directly support over 7000 businesses and employ more than 50 000 people, according to Forestry Innovation Investment. The largest source of biomass for energy is the waste from the processing of this lumber and the slash piles of low-value materials. Getting this energy to market where it can be used to offset fossil fuels is a major priority. A promising option for offsetting fossil fuels is to produce biomethane or renewable natural gas (RNG) from wood waste material. The RNG, which is interchangeable with conventional natural gas, can then be injected into the existing natural gas grid, and many existing forestry-based operations are already connected to this natural gas infrastructure.

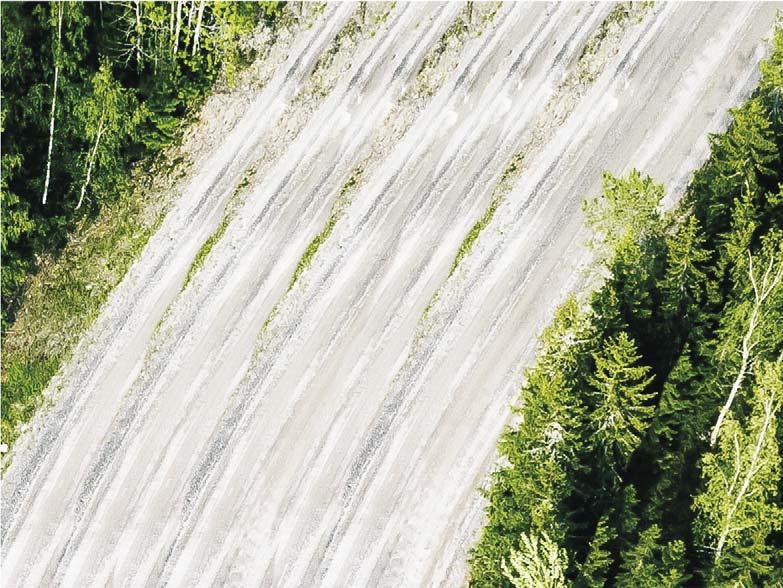
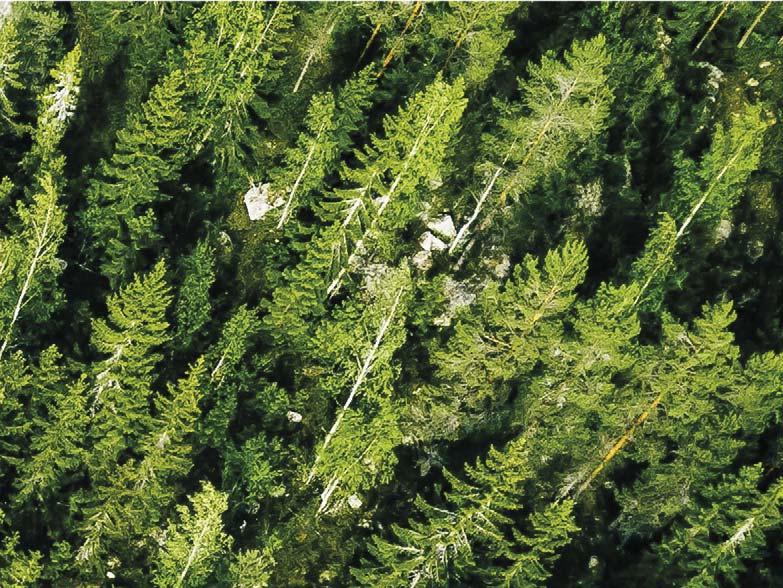
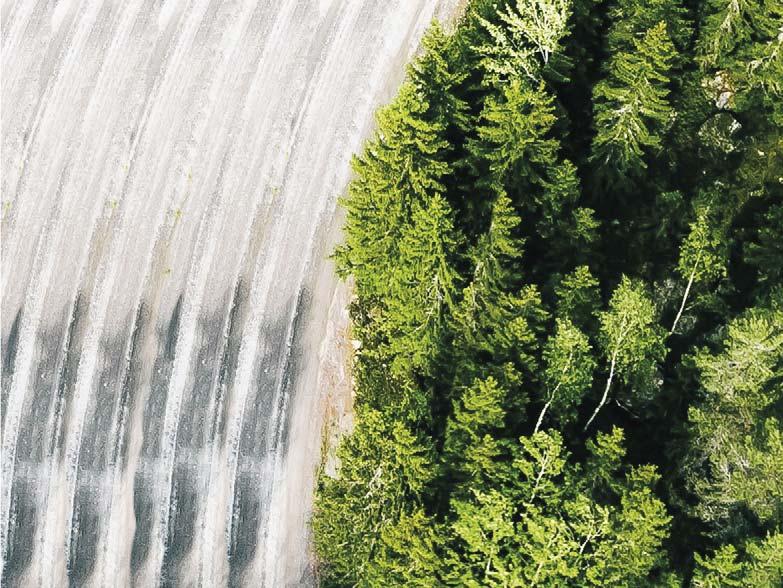
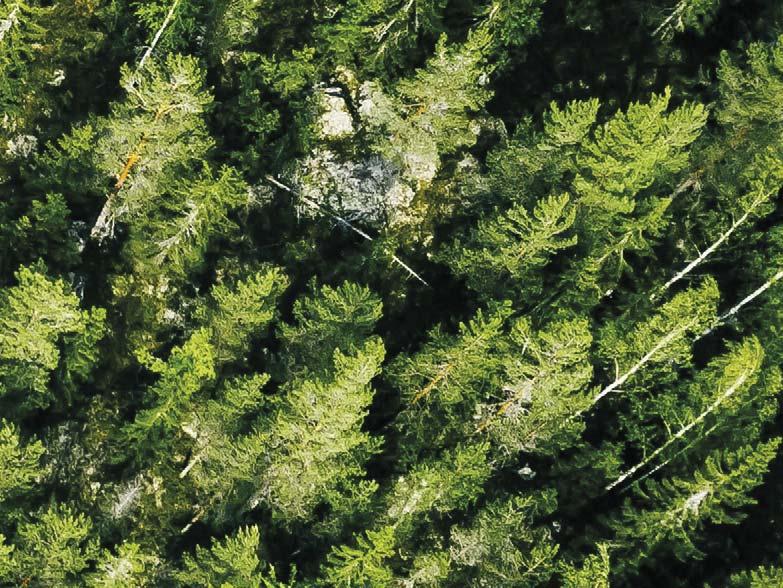
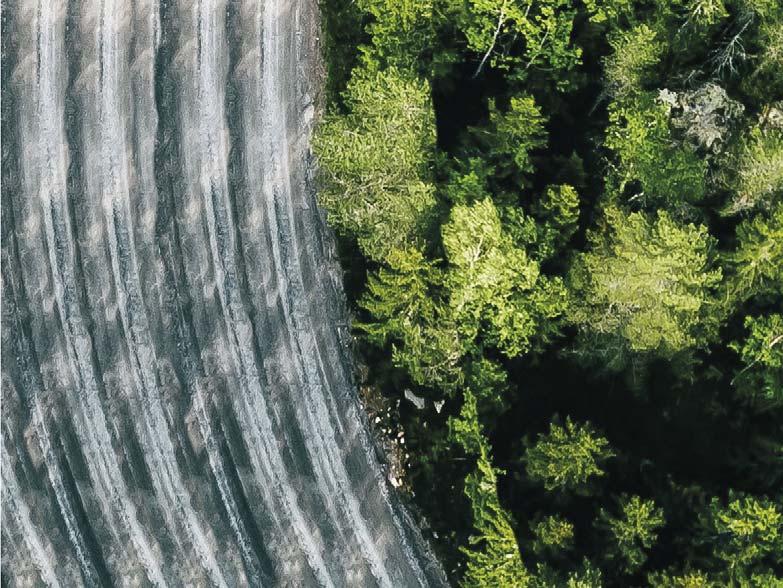
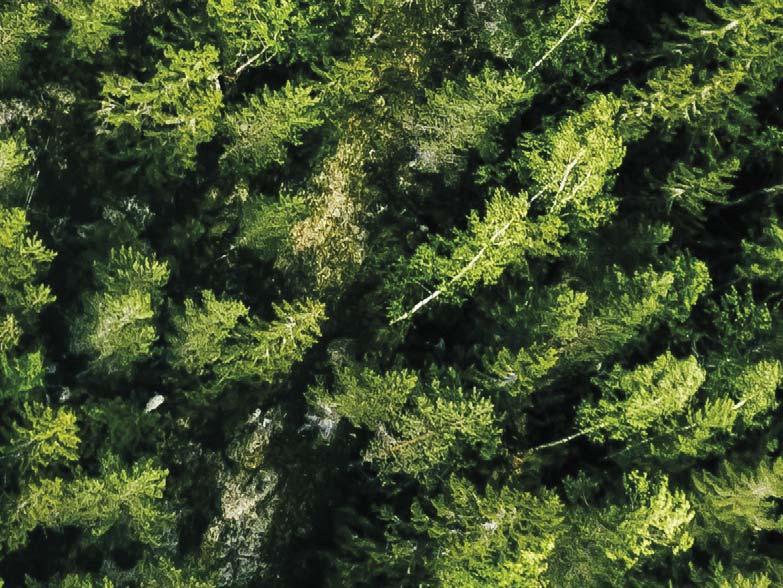
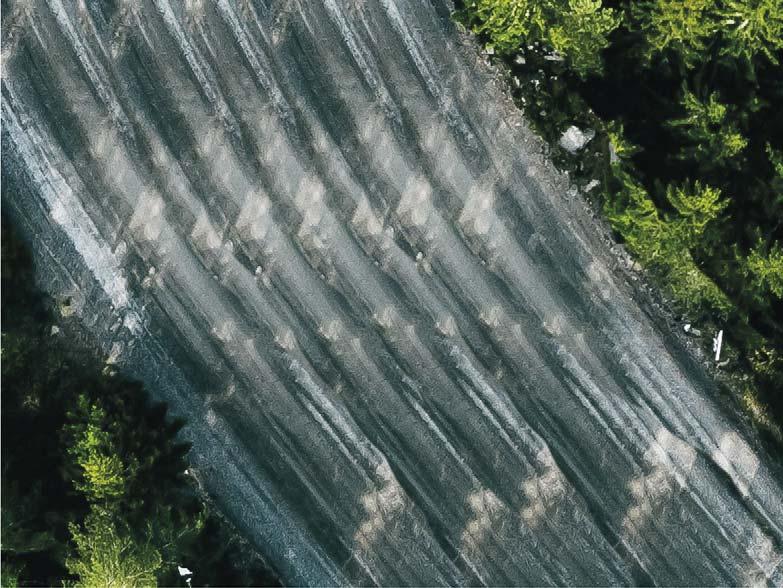
