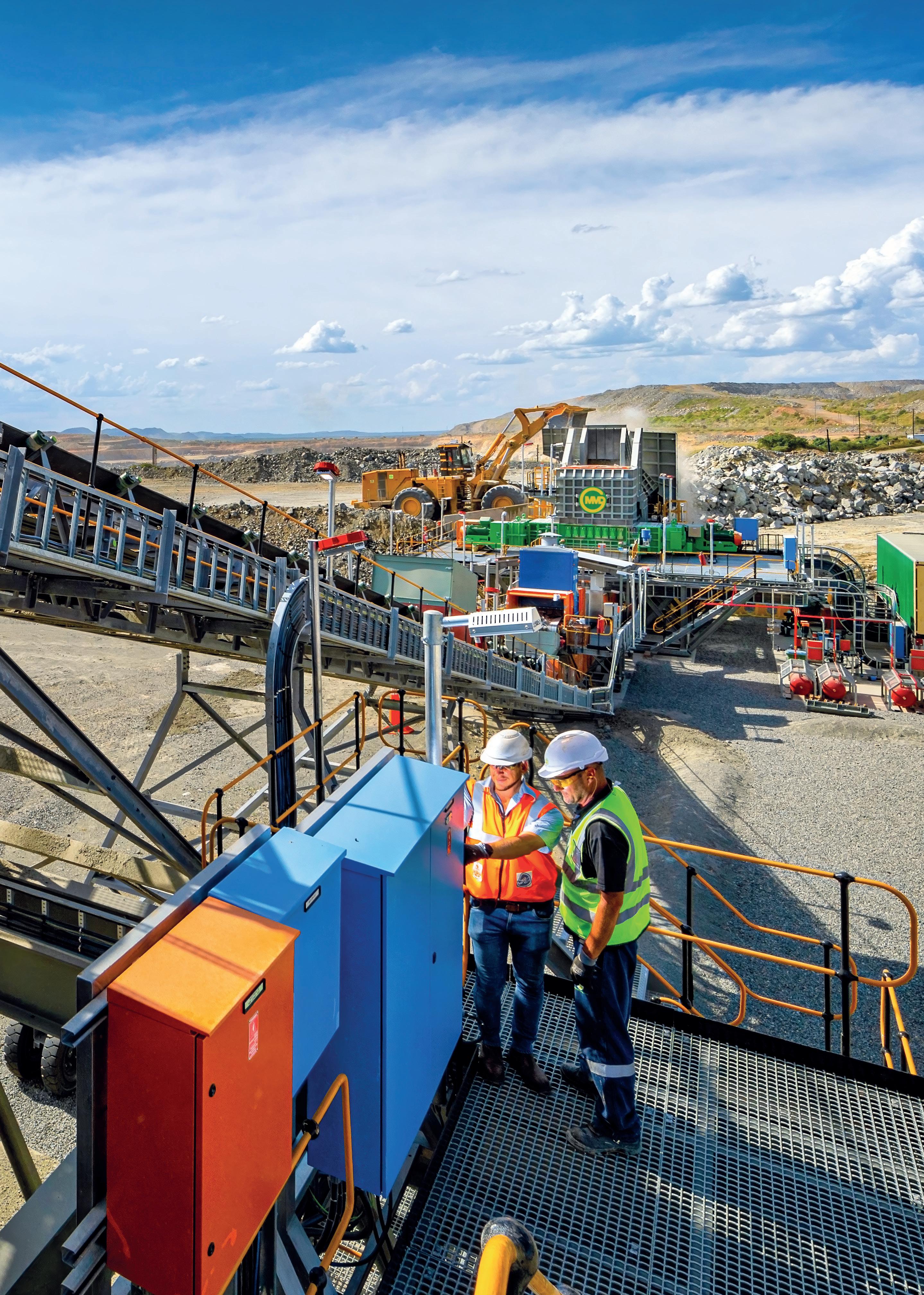
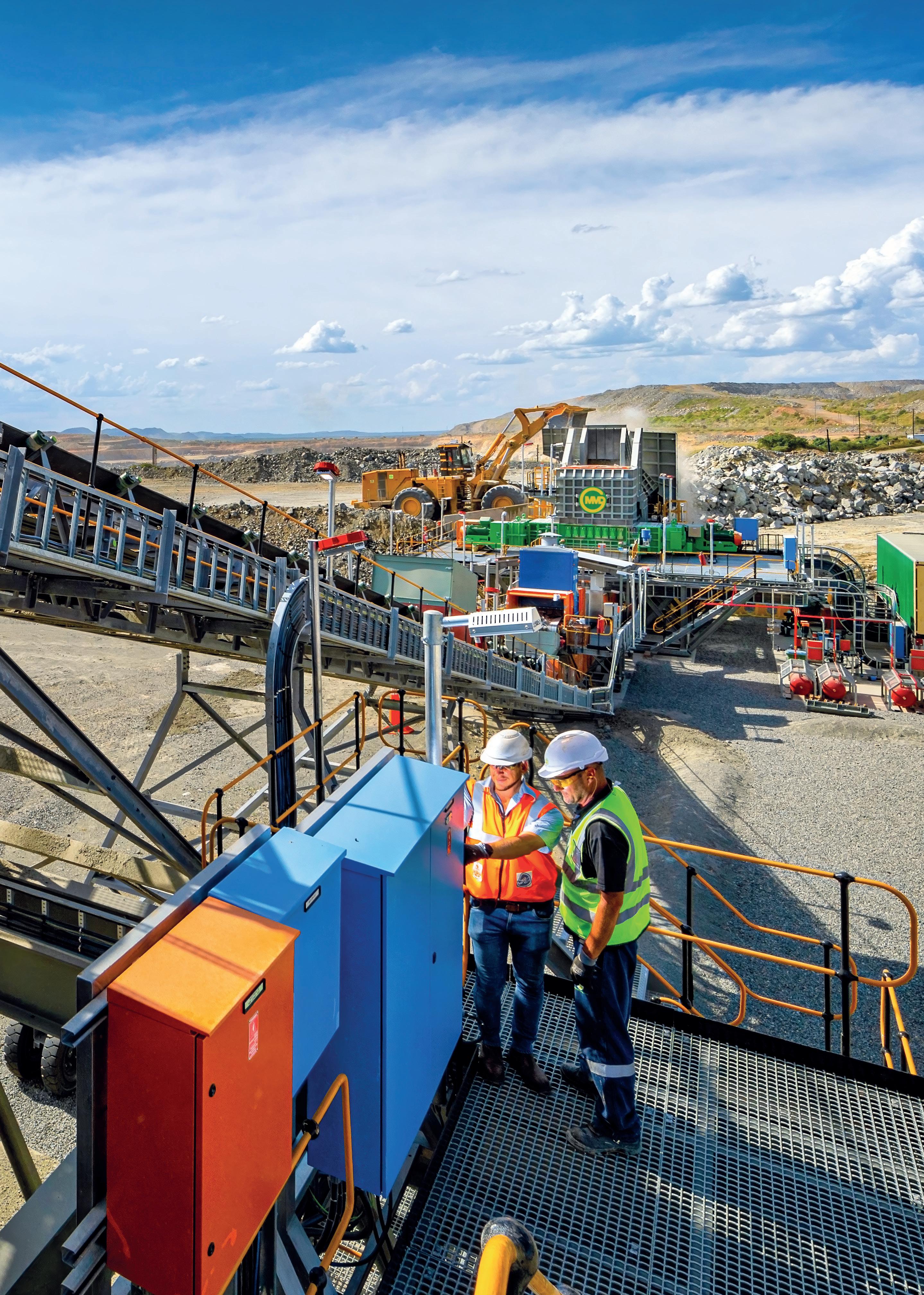
GrizzlyDrive® Drum Motors
Maintenance-Free Conveyor Belt Drives

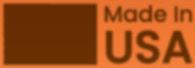
The GrizzlyDrive® Drum Motor, designed for harsh, abrasive, and demanding belt conveyor applications, provides 80,000 hours of continuous operation before maintenance, reducing operational and maintenance costs while increasing throughput.
ELIMINATE external drive components
REDUCE energy consumption
INCREASE workforce safety
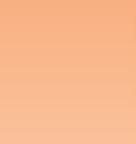
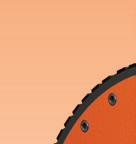
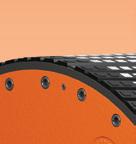
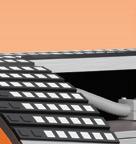
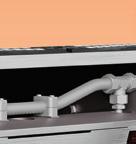
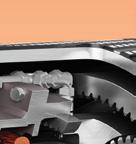
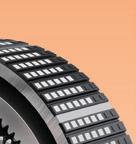
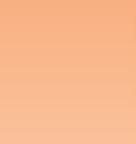
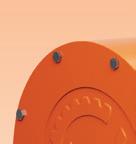
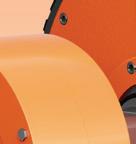
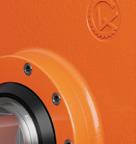
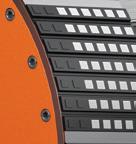
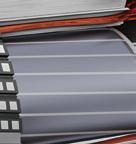
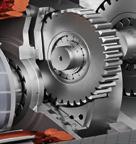
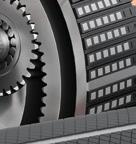
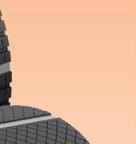
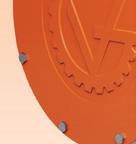
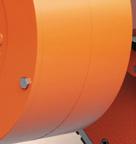
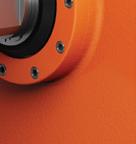
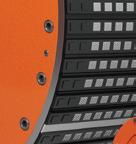
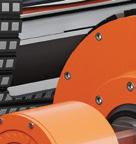
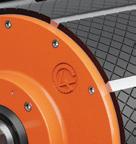
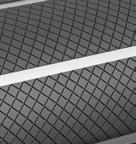
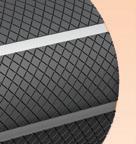
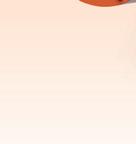
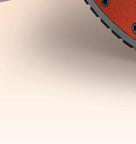
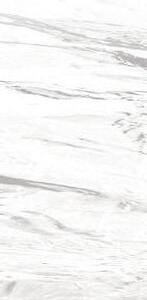
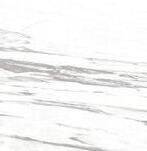

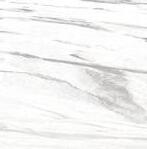
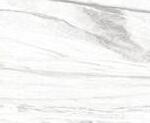
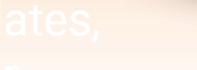
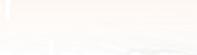
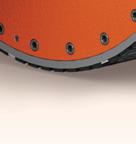
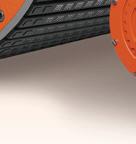
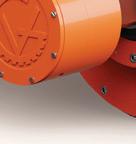
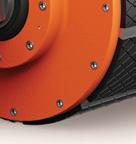
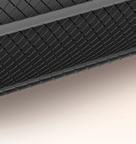
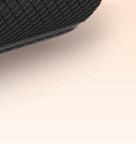

The VDG patented Oil Cooling-Conditioning unit circulates, conditions, and cools the oil inside the drum motor for optimal lubrication and heat dissipation, ensuring a cooler running motor, especially in high-temperature applications, and extending the life of the drive. The Oil Cooling-Conditioning unit is supplied as standard for drum motors 75hp and higher.


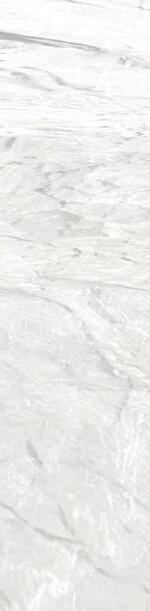
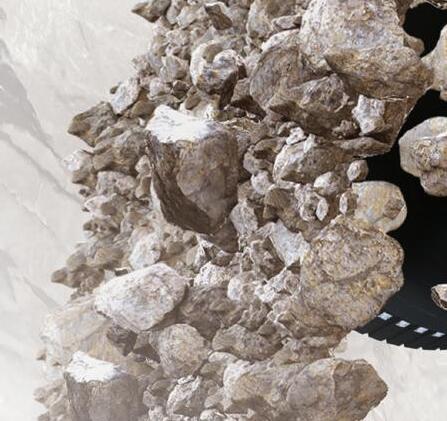
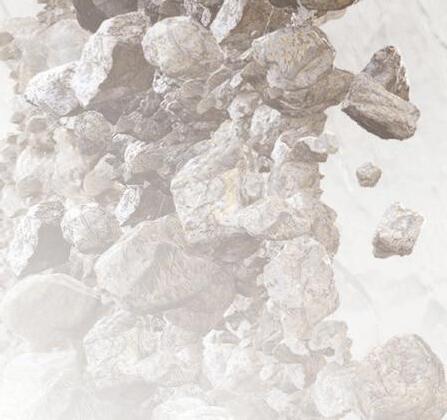
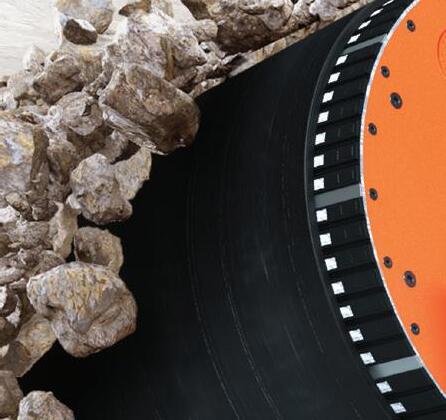
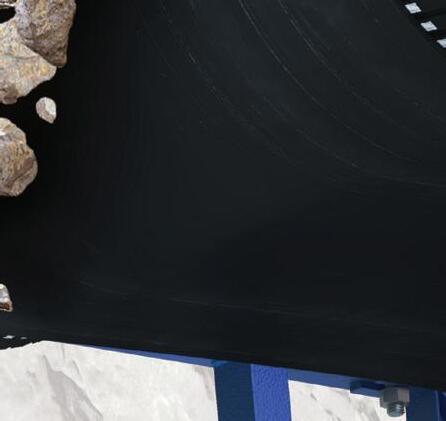
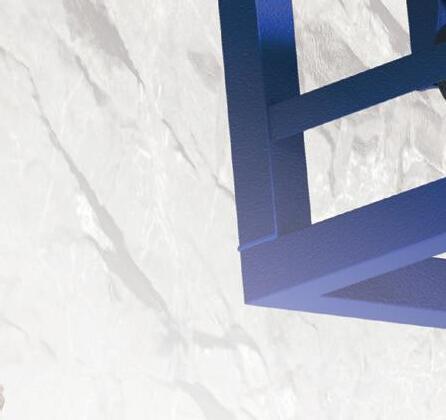
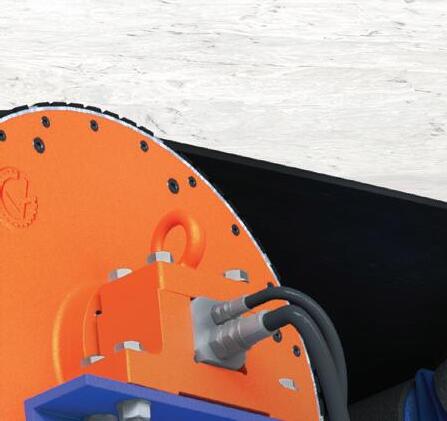

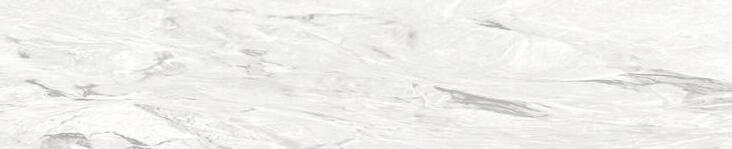
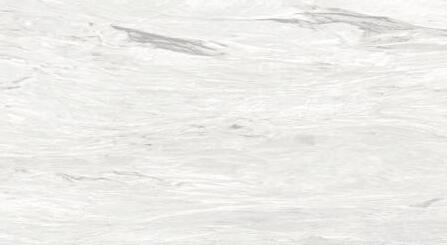
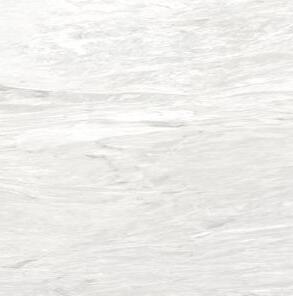
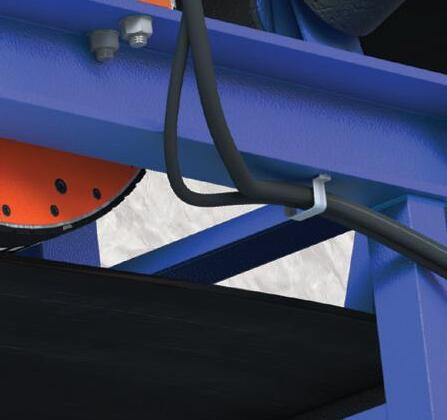
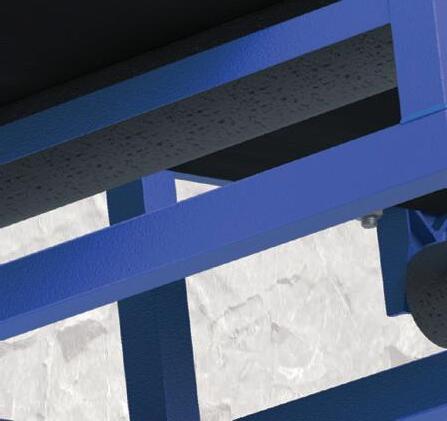

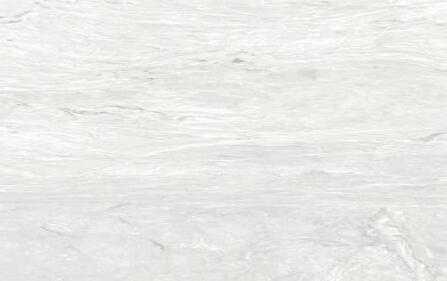
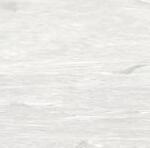
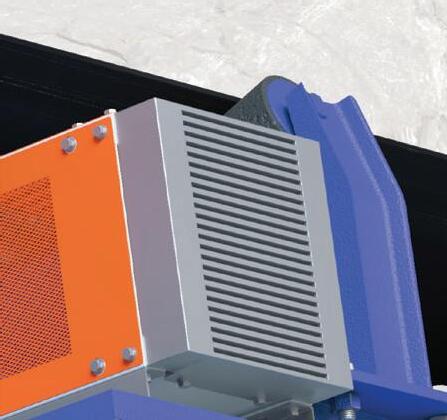
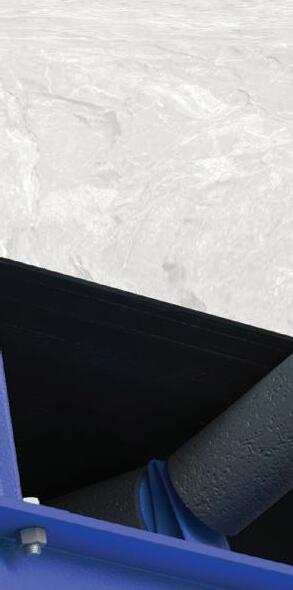
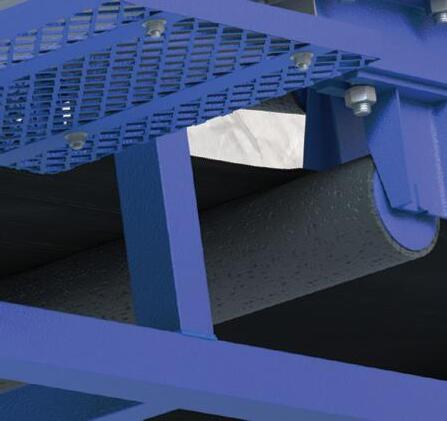
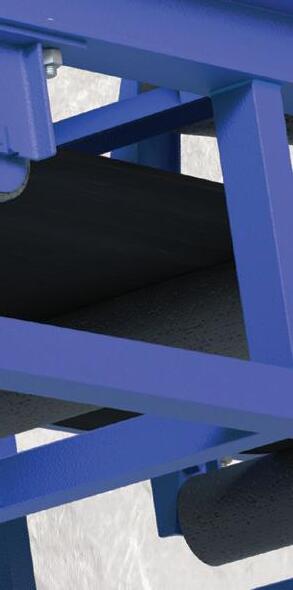
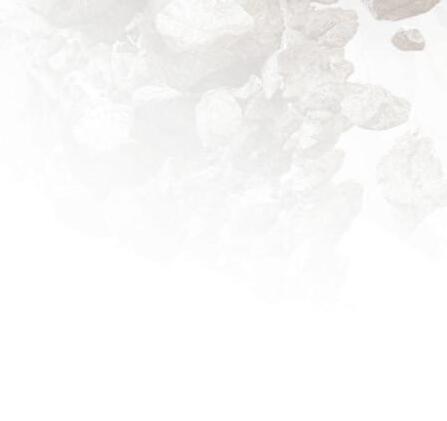
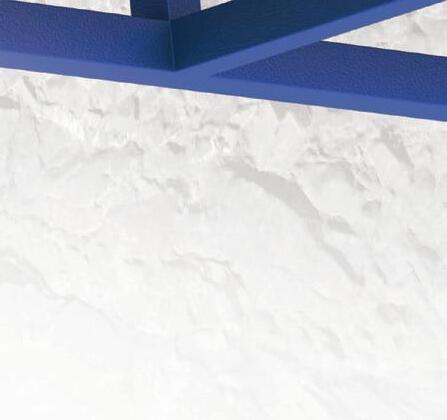
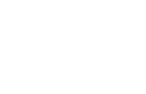
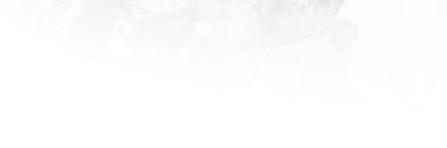
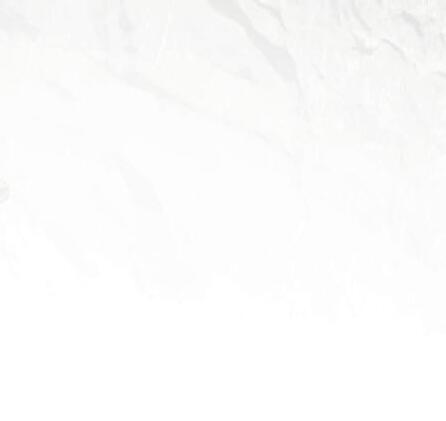
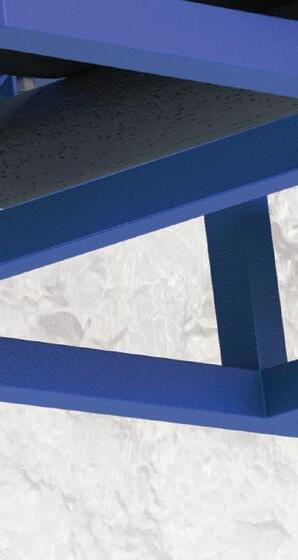
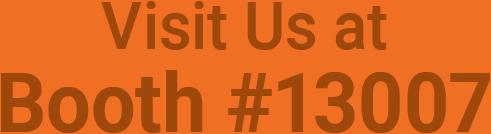
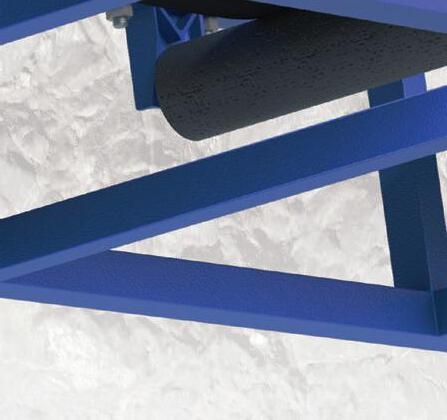
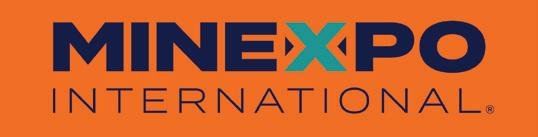
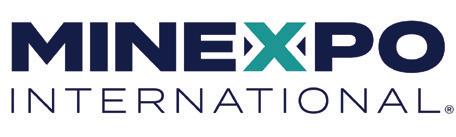
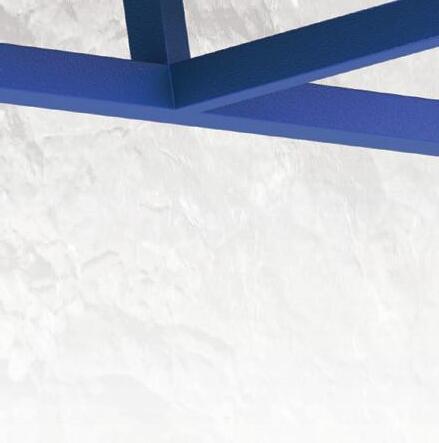
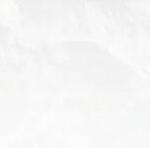
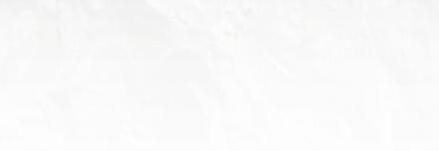
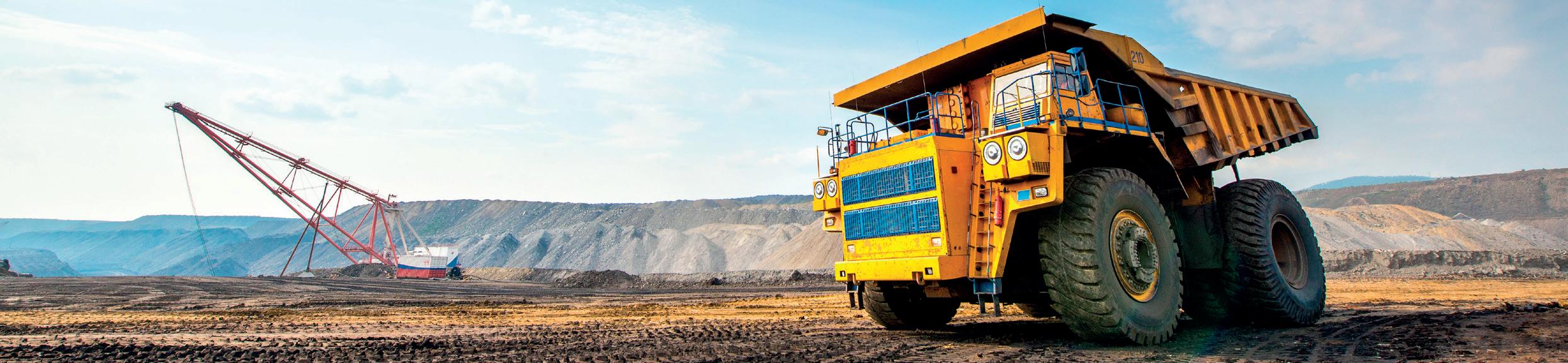
CONTENTS
10 Charting A Sustainable Future For The Copper Industry
Sidhartha Patnaik and Lance Fogtman, ION Commodities, assess the current state of the copper market and consider its future prospects.
16 Future-Proofing Mining Operations
Alireza Oladzadeh, ABB Process Industries, reviews the role of long-term service agreements in gearless mill drive operation and maintenance.
23 Track Shoes In Mining
Giovanni Treleani, BS Track, presents the critical role of track shoes in the mining industry by reviewing some key features, as well as global production trends.
29 Driving Towards A Greener Future
Michael Fleet, Komatsu, USA, outlines the latest loading innovations that can help promote sustainability.
33 Drilling Into The Future
Nellaiappan Subbiah, Sandvik Mining and Rock Solutions, USA, explains why smart miners are saying goodbye to diesel and hello to electricity to revamp drilling, save costs, reduce maintenance interventions, and act more sustainably.
37 Efficient Excavation
Matthias Stöhr and Nicolas Osswald, Herrenknecht AG Business Area Mining, Germany, consider how innovative technologies can ensure safer and more efficient excavation of ore passes and ventilation shafts in underground mines.
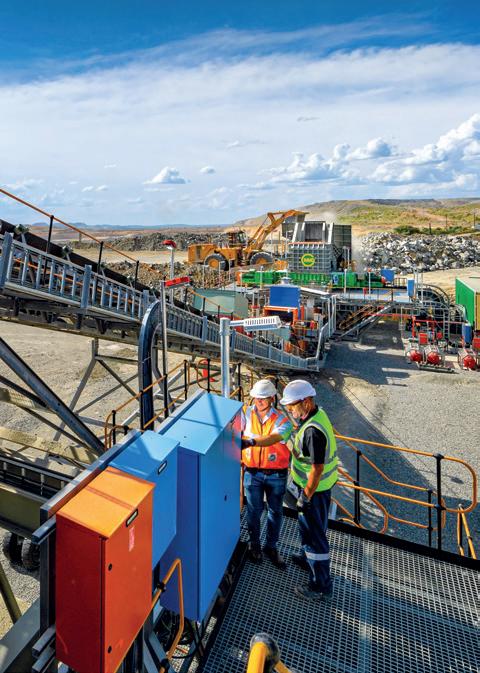


40 Get To Know Your Tyres
Eric Matson, The Goodyear Tyre & Rubber Company, USA, explores how a greater understanding of the technology and construction of tyres can help mine operators optimise performance and lower costs.
45 The Power Of Foam
Anthony Ferrenbach, Weber Mining and Tunnelling, Mexico, highlights how using foam can enhance safety and effectiveness when filling cavities.
48 The Digital Twin Revolution
Richard Clement, Smart Construction, advocates for the adoption of digital twins for brownfield mine sites to aid safety, efficiency, sustainability, decision-making, and resource management.
52 Shaping The Future Of Mining With AI
Mariana Sandin, Seeq Corporation, USA, discusses how AI-augmented advanced analytics platforms can deliver new levels of efficiency in mining operations.
57 Worker Safety And Connected Drones
Jaime Laguna, Oil and Gas Development at Nokia, USA, describes how Mining 4.0 connected drones are helping to pioneer worker safety and productivity in the mining industry.
61 Knowledge Is Power
Dr Graham Howell et al., SRK Consulting, examine the importance of a comprehensive knowledge base through the tailings storage facility lifecycle.
65 Prioritise Pumps
Mikael Hjelm, Atlas Copco Portable Pumps at Atlas Copco Portable Flow, evaluates the importance of dewatering pumps in mine water management.
ON THE COVER
MMD Group provides market leading in-pit solutions and systems tailored for mining operations. Our core Mineral Sizer and Apron Feeder technologies are integral to our In-Pit Sizing and Conveying (IPSC) solutions, Ore Sorting solutions (pictured), and fully mobile Surge Loader® (FMSL®), reducing costs, increasing efficiency and safety, and minimising emissions.
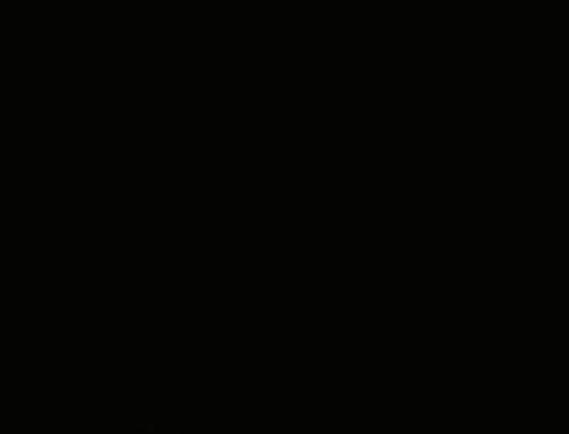
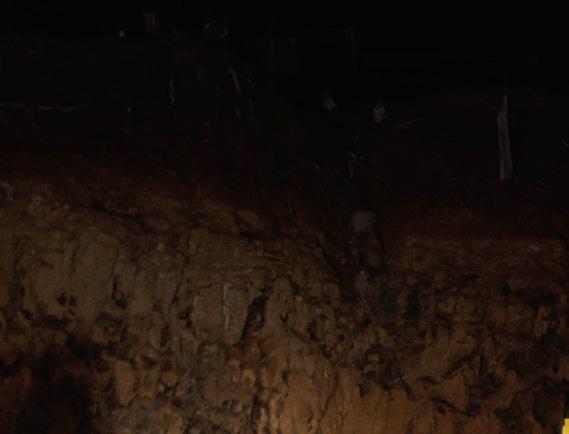
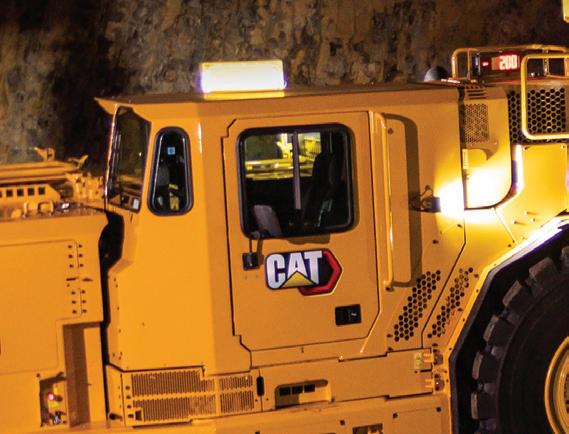
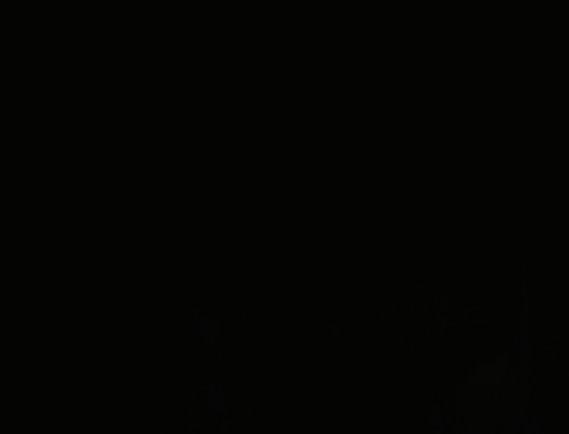
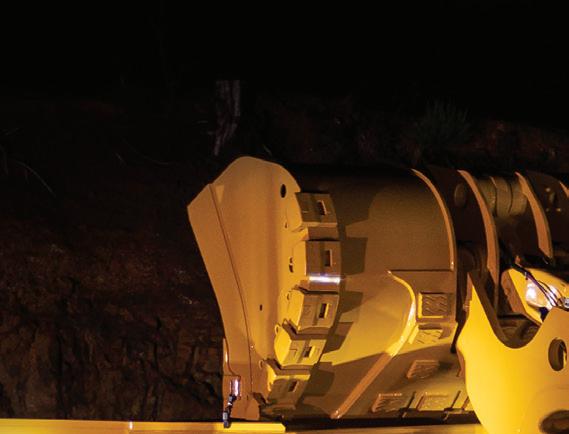
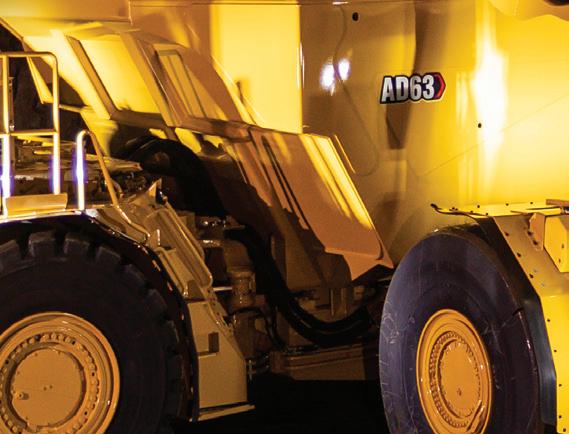
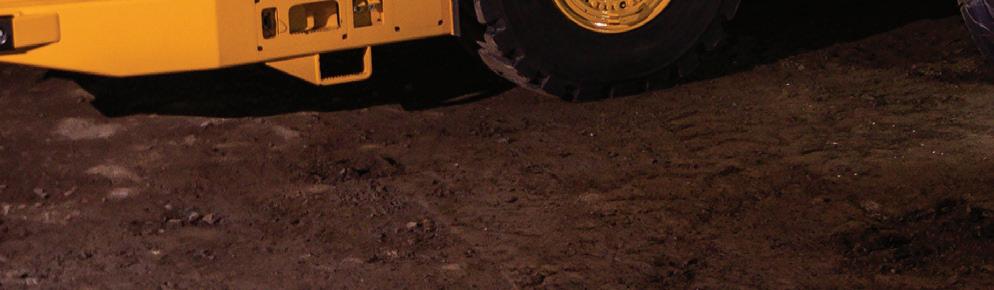
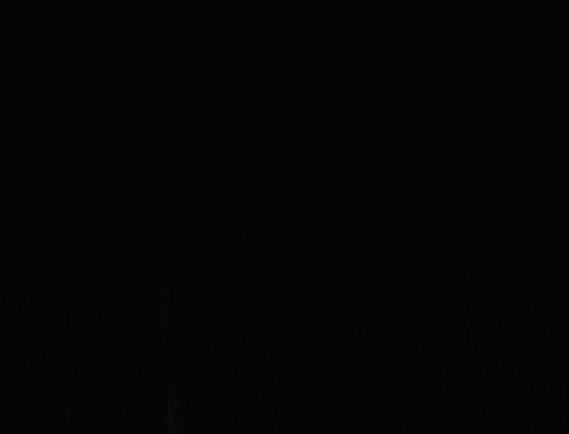
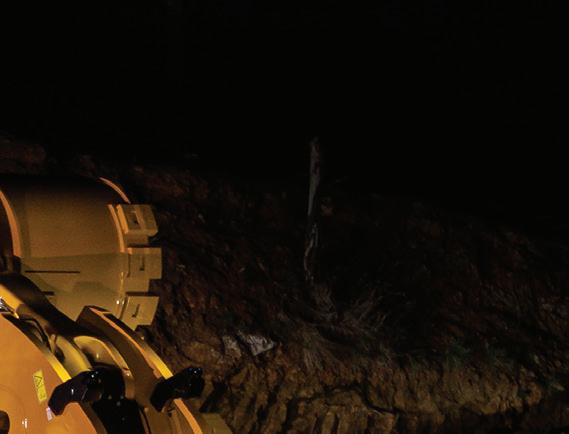
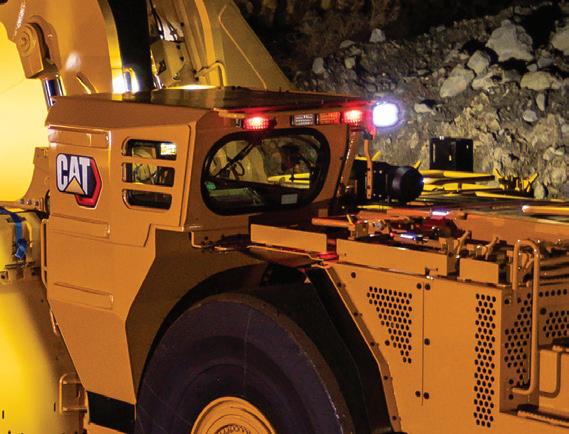
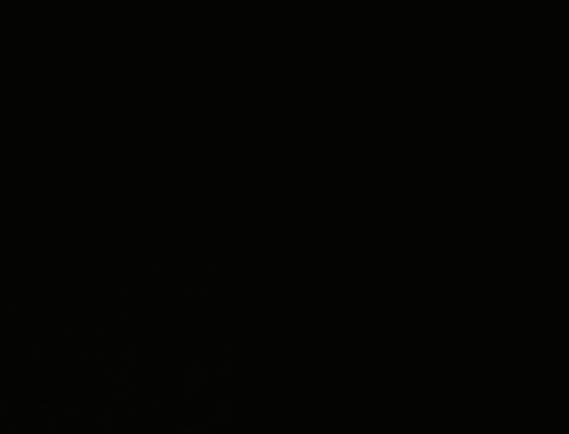
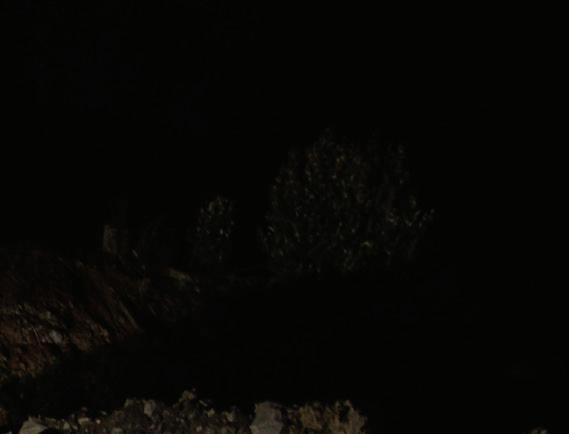
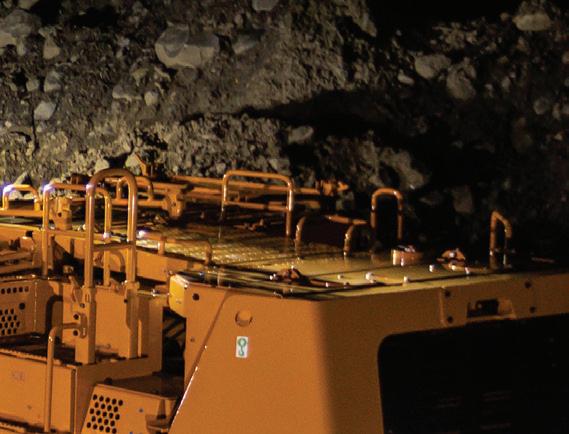
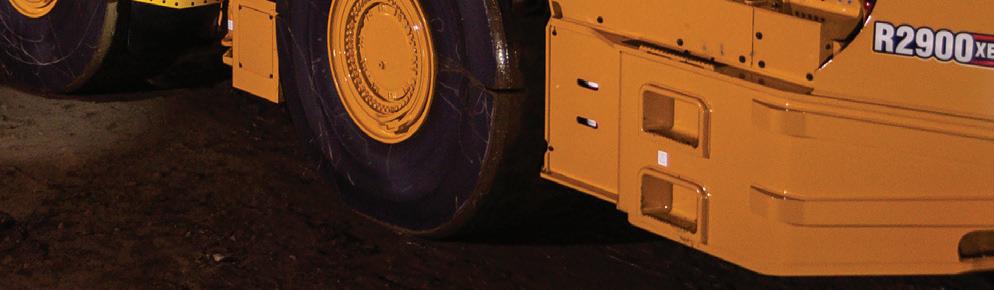
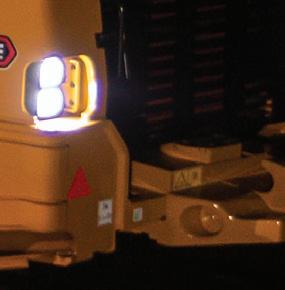
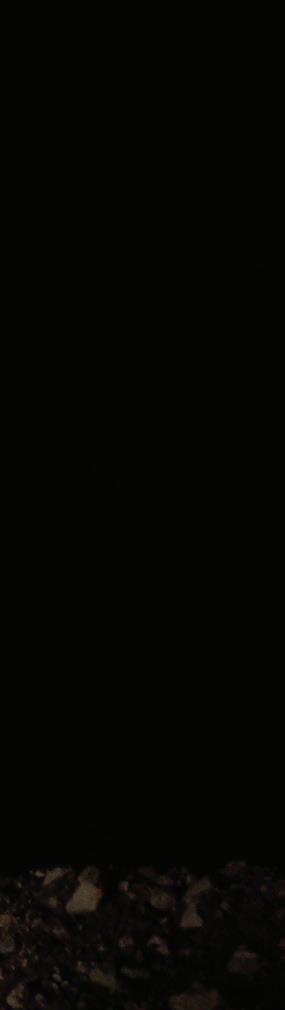
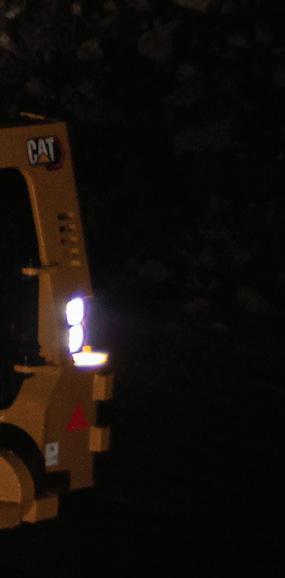
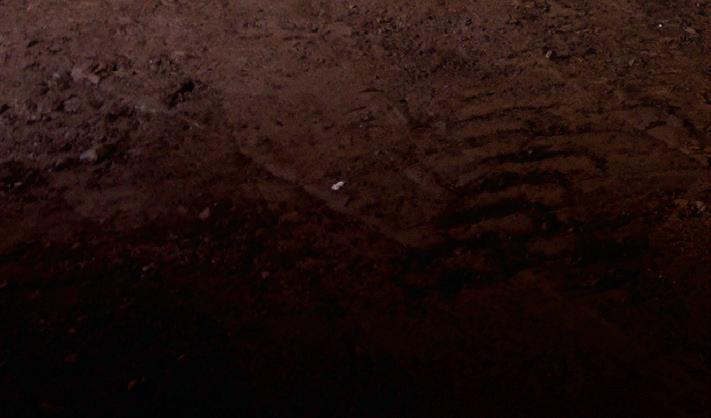
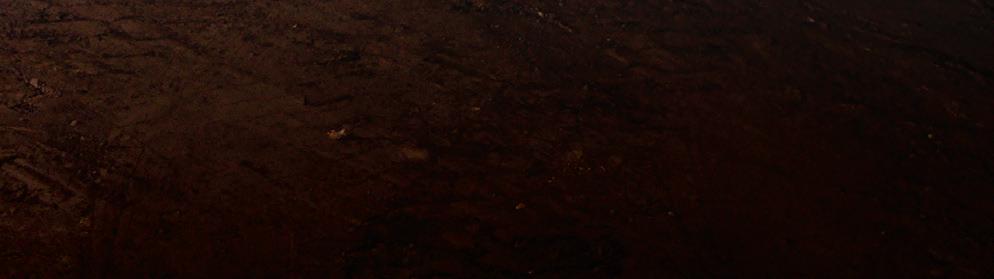
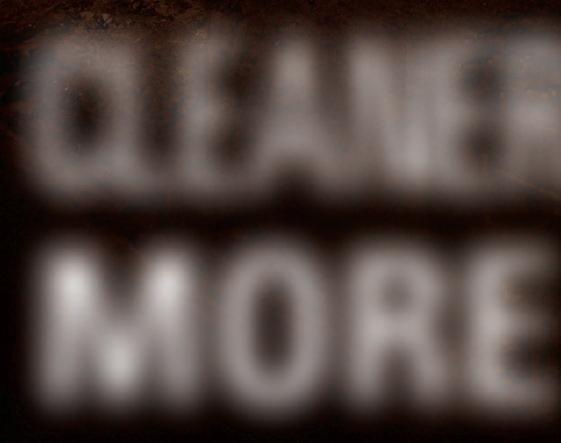

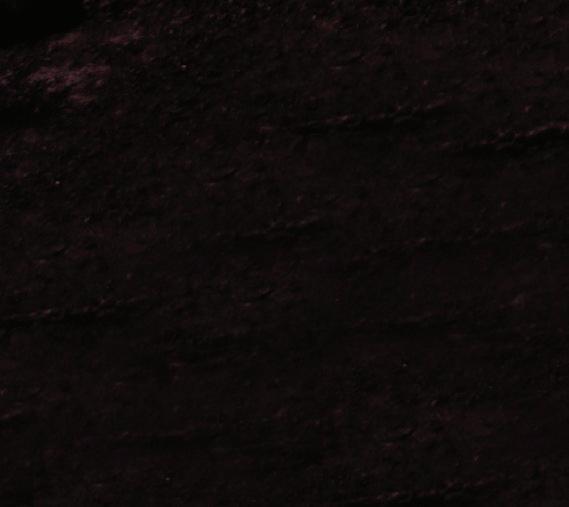
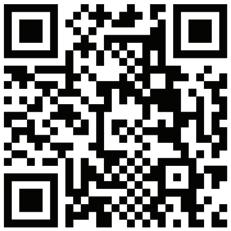
CLEANER. FASTER.
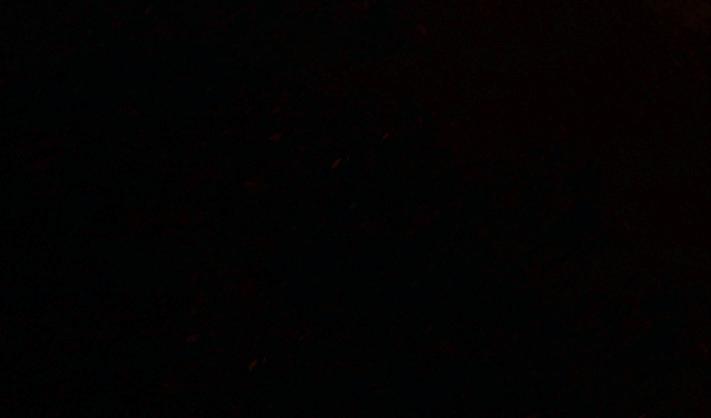
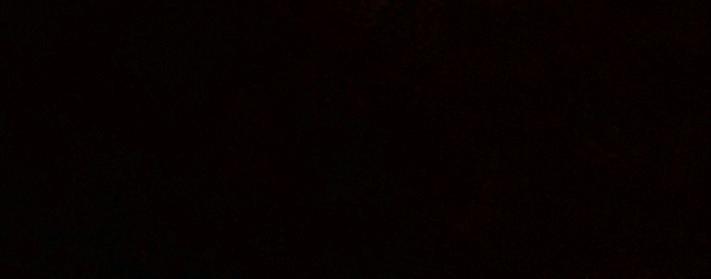
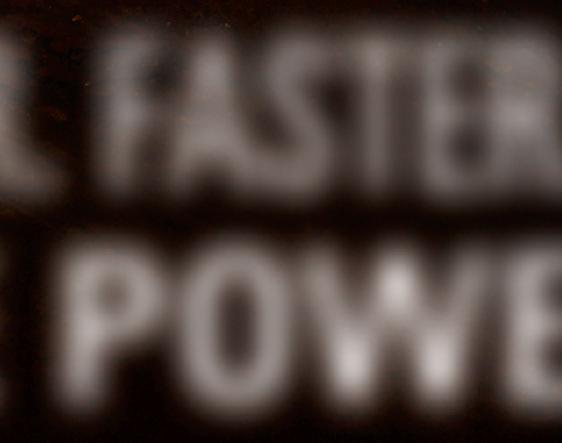
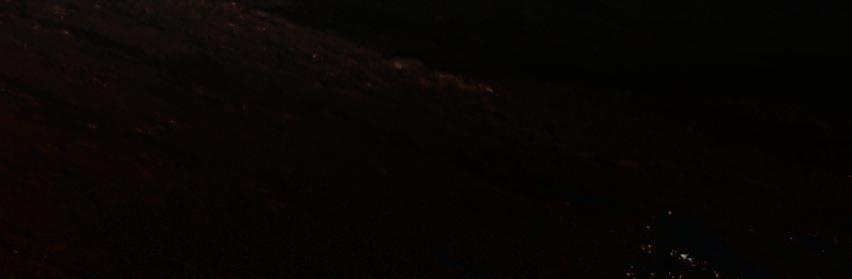
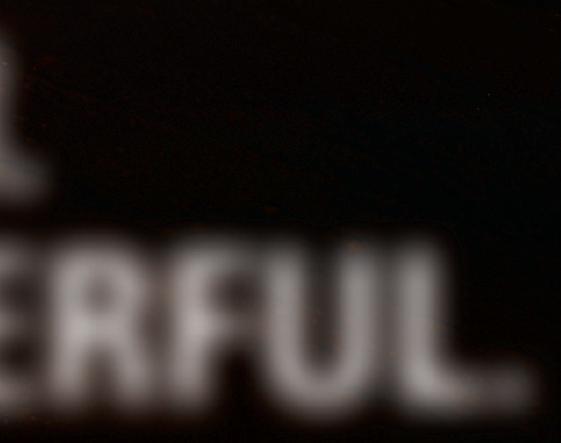

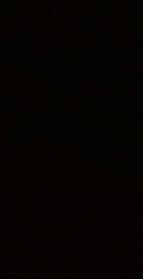
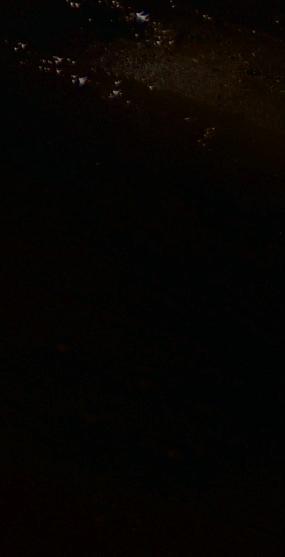
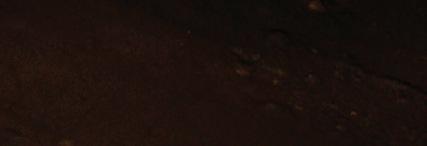
Built on the platform of our most popular underground loaders, the R2900 XE is the first Cat ® diesel electric underground LHD. It’s a productive, powerful, reliable machine built to meet the underground mining industry’s need for bigger payloads, faster loading and reduced emissions. Its powerful engine delivers faster acceleration, instant machine response and higher speed on grade for shorter cycle times, while greater breakout force and higher lifting height make digging and loading faster than ever. And its electric drive components help reduce fuel burn and improve productivity — helping mines reduce exhaust emissions.
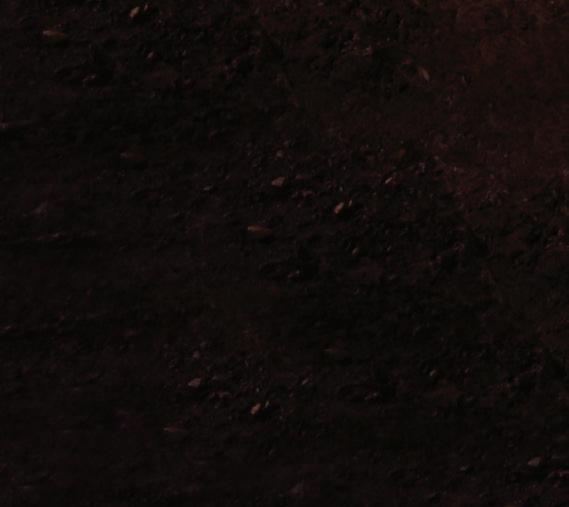
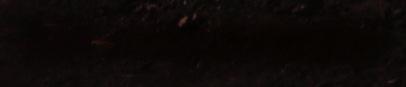
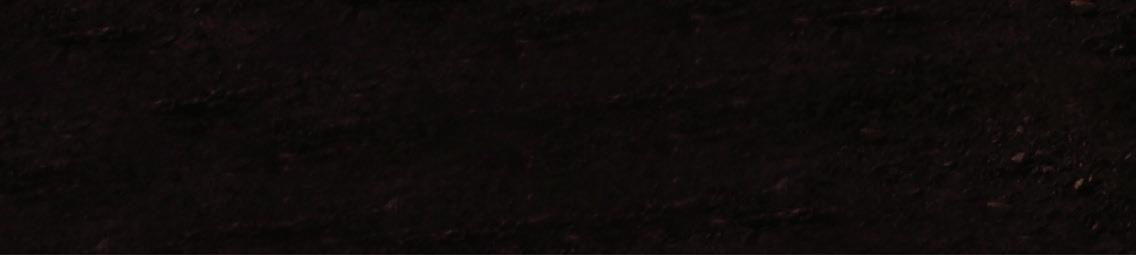
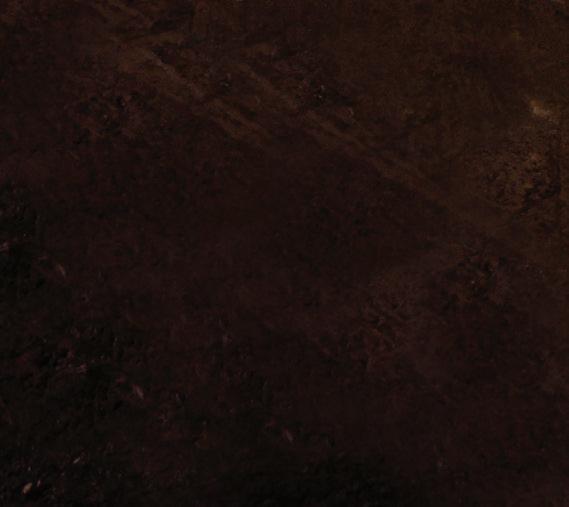
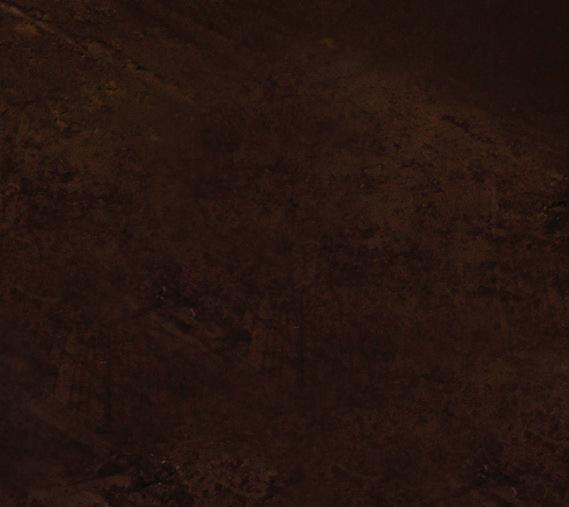
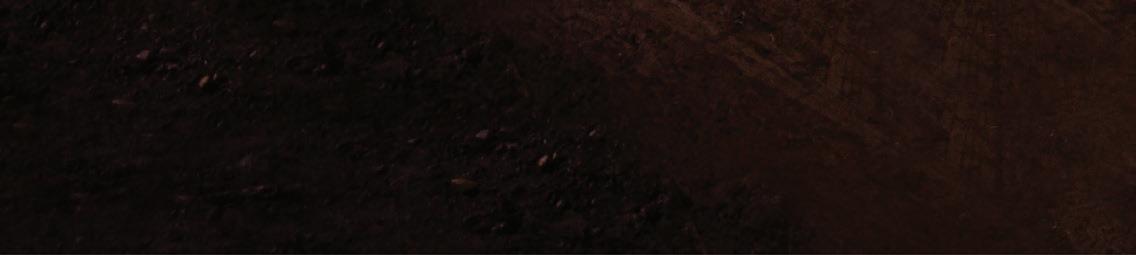
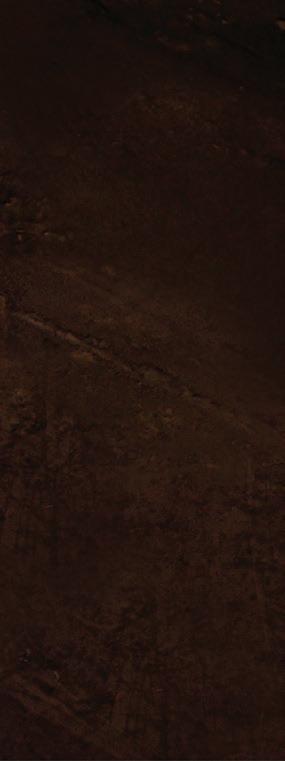

Guest Comment
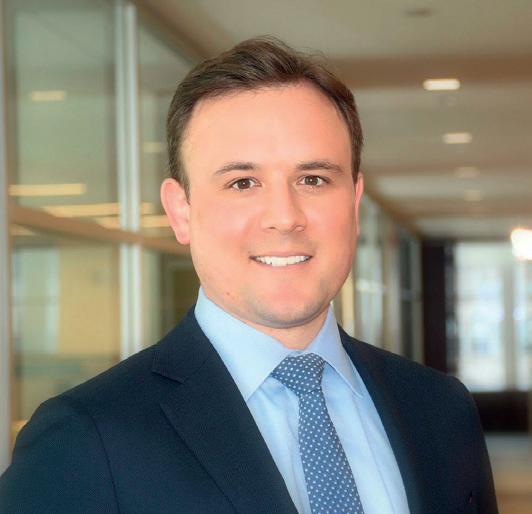
MANAGING EDITOR
James Little
james.little@globalminingreview.com
SENIOR EDITOR
Callum O’Reilly callum.oreilly@globalminingreview.com
EDITOR Will Owen will.owen@globalminingreview.com
EDITORIAL ASSISTANT
Jane Bentham jane.bentham@globalminingreview.com
SALES DIRECTOR
Rod Hardy rod.hardy@globalminingreview.com
SALES MANAGER
Ryan Freeman ryan.freeman@globalminingreview.com
PRODUCTION MANAGER
Kyla Waller kyla.waller@globalminingreview.com
ADMINISTRATION MANAGER
Laura White laura.white@globalminingreview.com
DIGITAL ADMINISTRATOR
Nicole Harman-Smith nicole.harman-smith@ globalminingreview.com
DIGITAL CONTENT ASSISTANT
Kristian Ilasko kristian.ilasko@globalminingreview.com
DIGITAL EVENTS COORDINATOR
Merili Jurivete merili.jurivete@globalminingreview.com
HEAD OF EVENTS
Louise Cameron louise.cameron@globalminingreview.com
Global Mining Review (ISSN No: 2515-2777, USPS No: PENDING) is published 10 times per year by Palladian Publications Ltd., and distributed in the USA by Asendia USA, 701 Ashland Ave, Folcroft, PA. Application to Mail at Periodicals Postage Prices is pending at Philadelphia, PA, and additional mailing offices. POSTMASTER: send address changes to Global Mining Review, 701 Ashland Ave, Folcroft, PA. 19032.
Annual subscription (10 issues) £50 UK including postage, £60 overseas (airmail). Claims for non-receipt must be made within four months of publication of the issue or they will not honoured without charge.
CHRISTIAN KURASEK
CHIEF FINANCIAL OFFICER, PRONTO
The mining industry is often overlooked within the green economy narrative, though it is perhaps the most foundational character in the story. From rare earth elements in high-efficiency solar panels to lithium-based electric car batteries, the global transition to a sustainable energy infrastructure is impossible without the minerals produced by the mining sector.
The energy transition is putting significant pressure on the industry to recruit and retain the skilled workforce necessary to meet the surging mineral demand. This is particularly in the face of an aging workforce that is rapidly retiring, as 50% of American mining workers plan to retire in the next five years.1 Despite strides in environmental and social responsibility efforts, mining still faces perceptions as dangerous and ‘dirty’, hindering recruitment efforts with younger generations.
The digitisation of mining – particularly the rapid adoption of automation that is currently underway – holds the potential to dramatically reshape that dynamic.
The ‘greenest’ mining is autonomous mining
Here at Pronto, we like to say that the ‘greenest’ mining is autonomous mining. Automation delivers a wide range of established ‘green’ benefits to operators, including more efficient use of consumables – such as fuel and tyres – through more controlled driving, adherence to speed limits, etc. Less widely discussed are the even greater potential impacts that autonomy can bring to the industry, via enabling the economics of using smaller haul trucks.
Haul trucks have historically gotten bigger over time, primarily to minimise labour costs – the more material one truck can move, the fewer trucks and drivers required to operate them. But those labour savings come with consequences, including environmental impacts. Bigger trucks need wider roads, which necessitate shallower pit designs, which require more overburden to be removed before productive ore is reached. With a circular pit design, the net impact of every extra foot of haul road width is exponential in terms of tonne-kilometres of unproductive overburden moved to reach the same volume of ore. Fuel efficiency also generally decreases with truck size, contributing to the exponential increase in the carbon footprint of an ore body mined with large haul trucks versus one mined with small haul trucks.
Autonomy eliminates the previously immutable ‘one truck to one driver’ ratio from the haul truck fleet optimisation calculation, which leads to the economics favouring smaller trucks. With smaller autonomous trucks, mines can not only dramatically reduce their carbon footprint, but also reduce their physical footprint. With steeper, smaller diameter pits, less of the environment needs to be disturbed to reach the same ore body.
Upskilling and job creation is happening
As the industry embraces a digital future, the portion of the mining workforce currently dedicated to operating equipment in the field will transition to positions operating and overseeing autonomous technologies from an office. The net impact will be a safer, more highly skilled, more highly paid workforce.
Automation can lead to significant improvements in the efficiency of mining operations – research that we conducted with Whittle Consulting suggests that utilising small autonomous trucks could lead to a 30 – 40% improvement in the net present value of a mine over its lifetime.2 Those kinds of economics can easily support migrating equipment operator jobs into higher-paid technology support positions, while still delivering outsized contributions to the bottom line. We have heard anecdotally from a number of industry participants that to date, with over 1000 autonomous haul trucks deployed around the world, not a single net job has been eliminated by autonomy.
Autonomy promises to transform the mining industry in myriad ways, but one of the most underappreciated and significant is its potential to help solve one of the most intractable problems facing operators – a looming skilled labour shortage. By helping the industry trade higher-risk, manual labour positions in far flung mine sites for safer technology jobs in offices that are foundational to decarbonising the global economy, autonomy is going to be far more central to the future of the mining industry – and mining jobs – than many realise today.
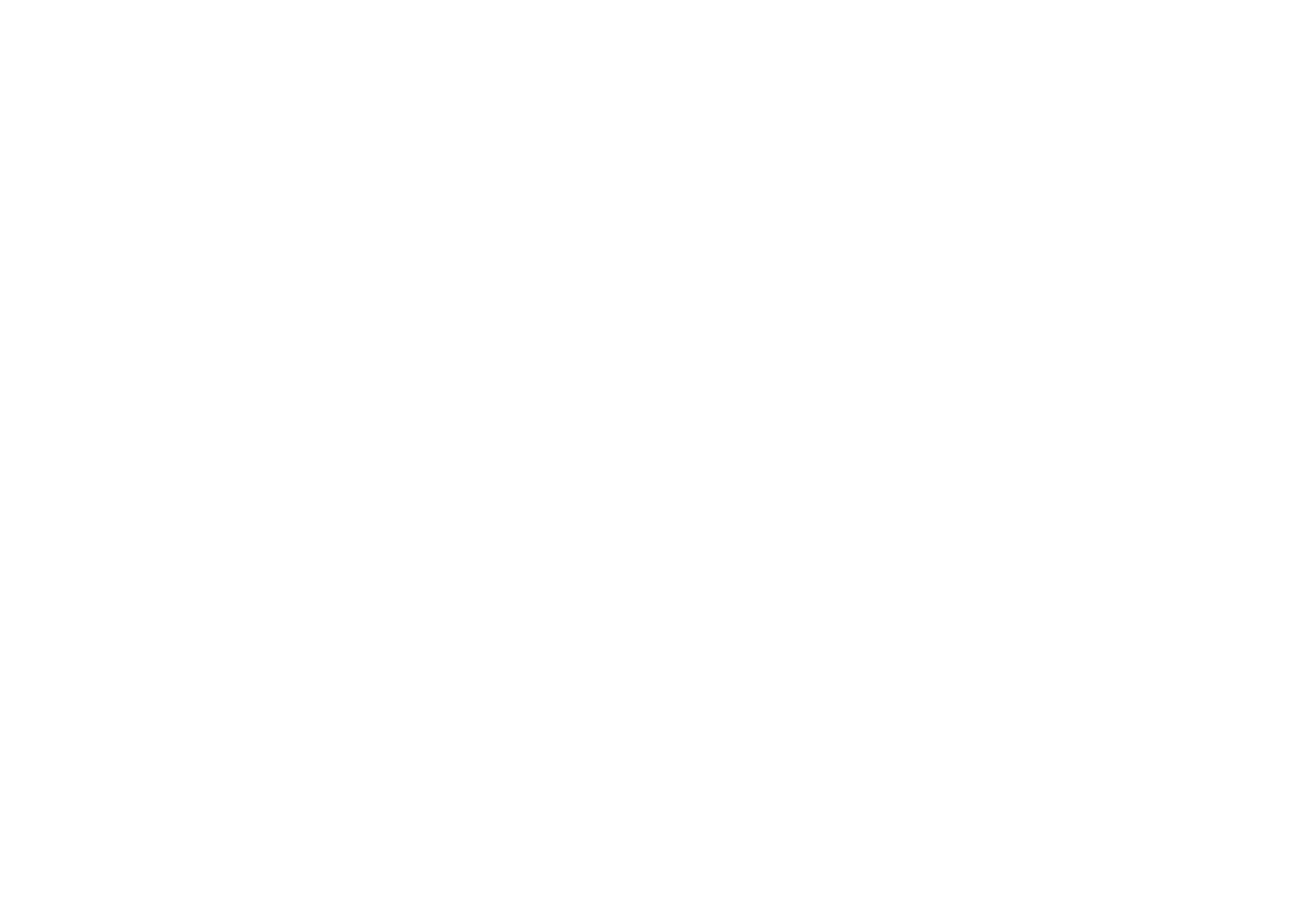
Trust MAAG for unmatched dependability and quality.
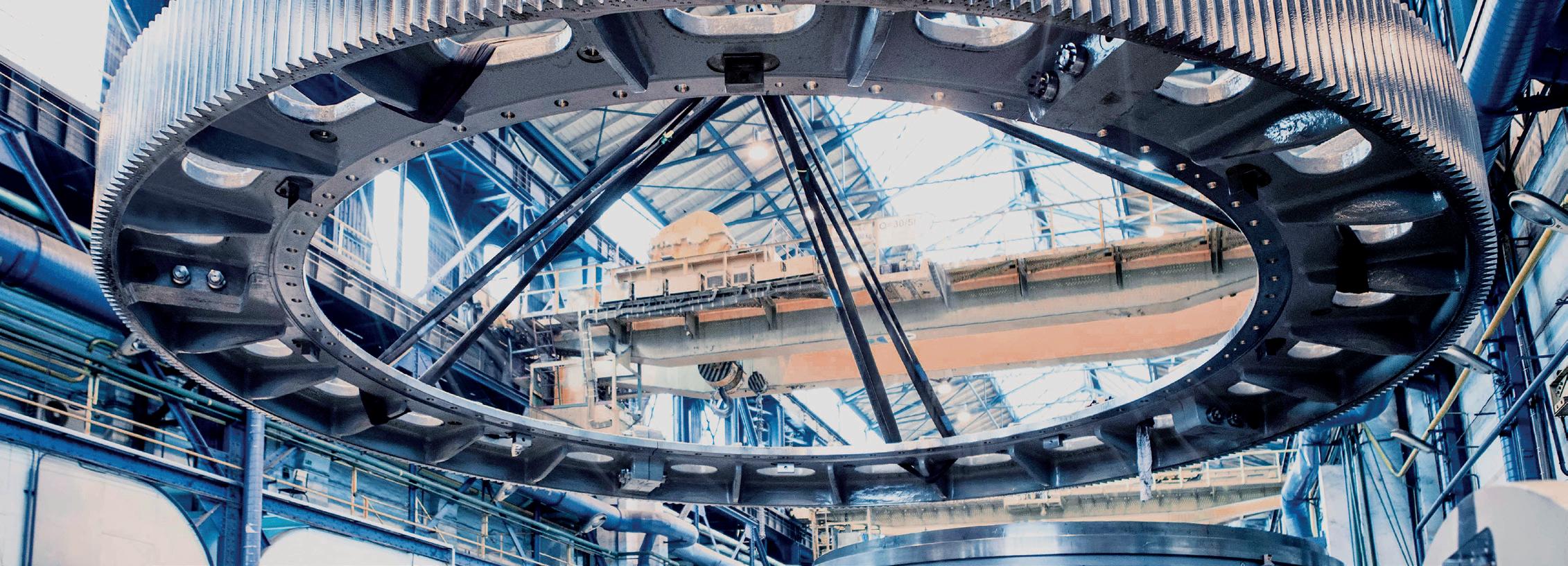
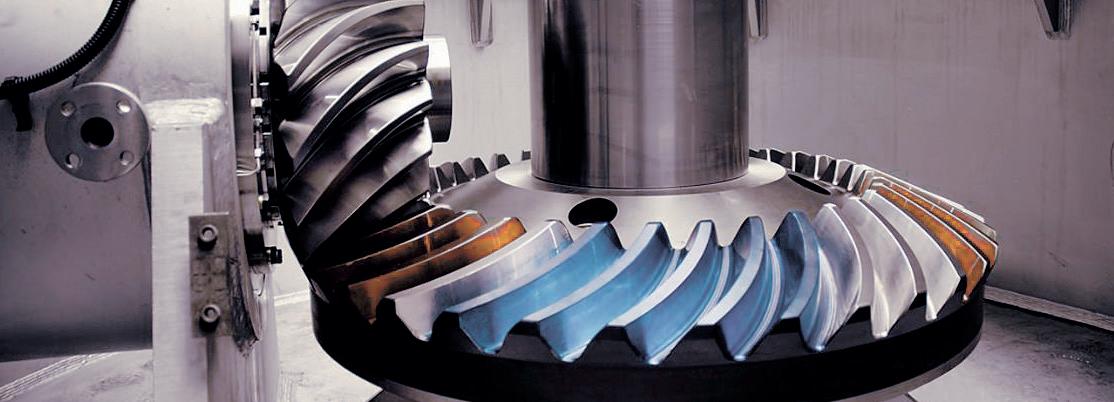
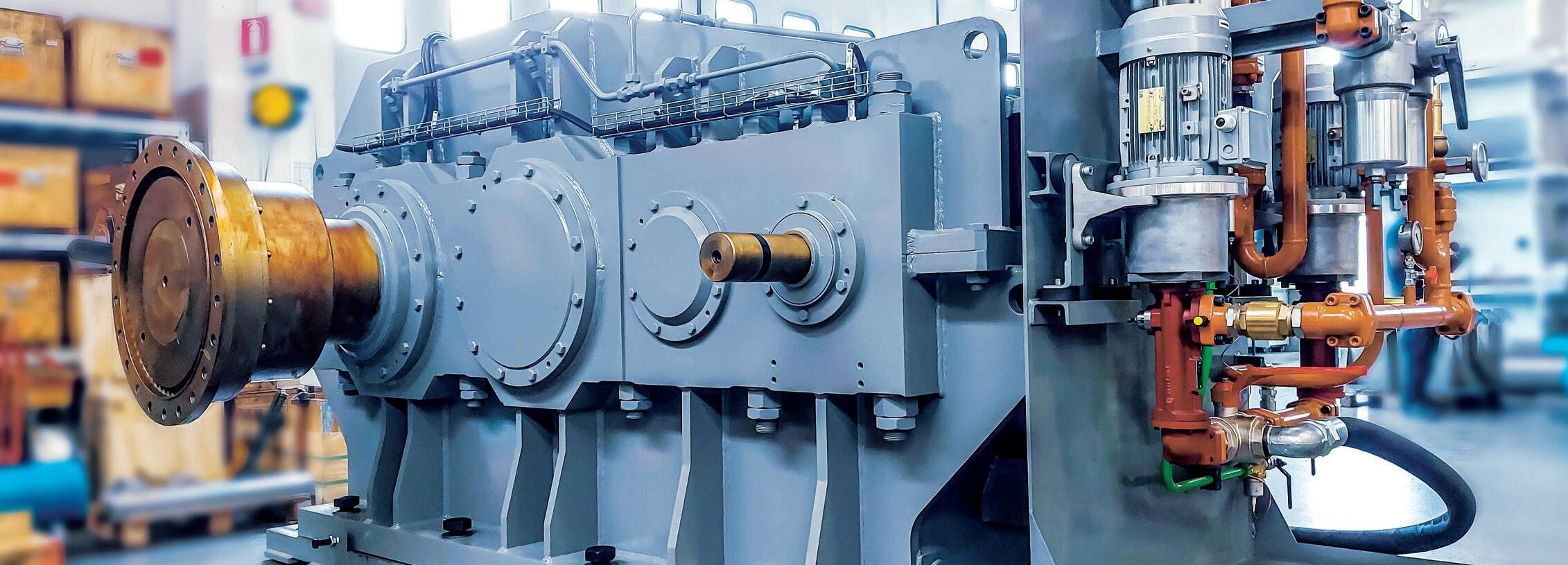
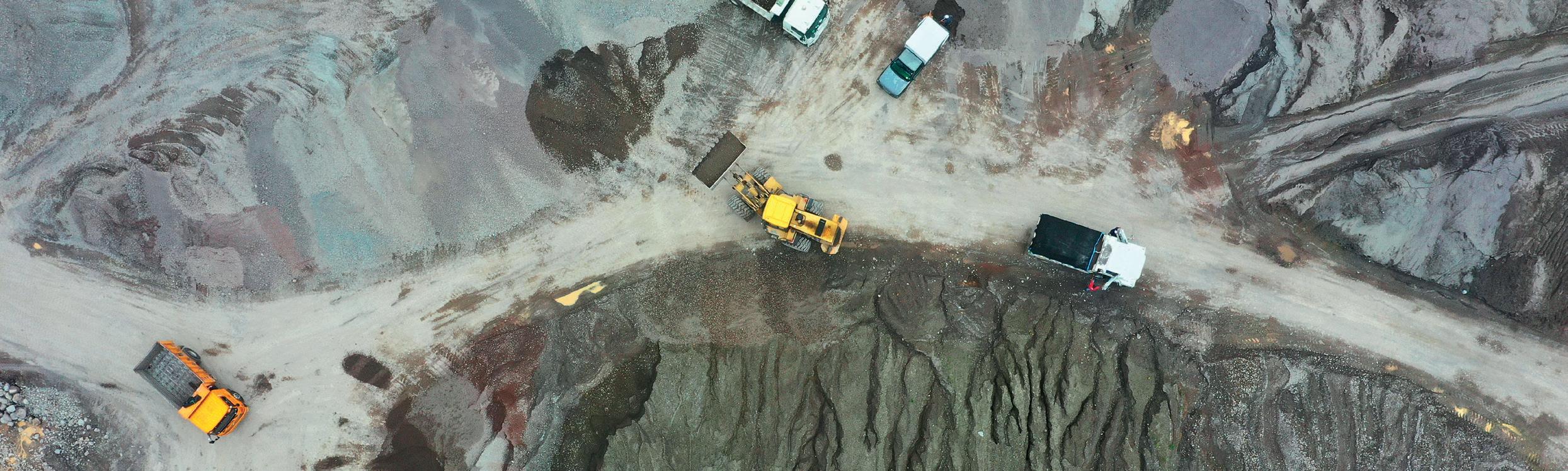
World NEWS
CANADA Orica and De Beers collaborate to reduce nitrate concentrations
Orica has collaborated with De Beers Canada Inc. (DBCI) at its Gahcho Kué site in Canada to improve its drill and blast process and significantly reduce nitrate concentrations under the ‘Building Forever – Protecting the Natural World’ Initiative.
Located in northern Canada’s sub-Arctic region, the Gahcho Kué diamond mine is a joint venture between De Beers Canada Inc. (51%) and Mountain Province Diamonds Inc. (49%). As the operator, De Beers is committed to high safety and sustainability standards, with a deep respect for the land and its surrounding pristine water bodies.
Since the mine’s inception, Orica and De Beers have worked together to mitigate the environmental impact of blasting. The environmental monitoring team at Gahcho Kué noted increasing nitrate levels in mine water, a known issue with bulk mining explosives.
Although nitrate and ammonium levels were within regulatory limits, De Beers proactively sought to reduce nitrate generation.
In 2020, De Beers engaged Orica to review the drill and blast process to align with industry best practices and improve safety and efficiency. Orica applied the nitrate risk reduction (NRR) framework, a three-tiered approach to systematically reduce nitrate contributions from blasting in water. The NRR process identifies nitrate sources from blasting and implements managed changes to reduce them. These changes include minimising bulk explosive waste, maximising detonation reliability and efficiency, and selecting products suited to the mine’s groundwater conditions and sleep time requirements. The site team reinforced best practices on-bench as part of the NRR strategy, introducing i-kon™ III electronic detonators to reduce misfires.
ZAMBIA Hitachi begins trial of the world’s first ultra-large full battery dump truck
Hitachi Construction Machinery Co., Ltd. has announced the commencement of the world’s first technological feasibility trial of an ultra-large full battery rigid frame dump truck by an original equipment manufacturer (OEM) operating at First Quantum Minerals Ltd Kansanshi copper and gold mine in the Republic of Zambia.
The technological feasibility trial, which began in June 2024, is being conducted at First Quantum’s Kansanshi deep opencast copper-gold mine, one of the company’s largest mines in Zambia. The technological feasibility trial aims to verify the basic performance of operations required of a battery-powered dump truck –such as travelling, turning, and stopping – under actual operating loads, as well as the verification of battery charging and discharging cycles.
Hitachi Construction Machinery’s Vice President and Executive Officer, President of Mining Business Unit, Eiji Fukunishi, stated, “Mining companies around
the world are working to reduce emissions. As an OEM, it is our vision to provide solutions that can reduce our customers’ environmental footprint. The battery dump truck represents the future, not only for the Hitachi Construction Machinery Group, but for the mining industry as a whole, and we are pleased to establish this proving ground on an active mine site and work with First Quantum on advancing this zero-emission solution.”
First Quantum’s Director Mining, John Gregory, added, “Battery zero emissions development with little to no impact on payload, production, and fleet size is achievable with Trolley Assist and First Quantum have mastered this technology by working with 2600 V systems of Hitachi Construction Machinery to provide stable platforms with multiple trucks on the overhead line at the same time. This system is an operational, practical, and economically feasible solution that will reduce emissions in mining for many years to come.”

World NEWS
Diary Dates
Electra Mining 02 – 06 September 2024 Johannesburg, South Africa www.electramining.co.za
International Fairs EXPO KATOWICE 04 – 06 September 2024 Katowice, Poland www.expo-katowice.com
Mining Indonesia 11 – 14 September 2024
Jakarta, Indonesia www.mining-indonesia.com
MINExpo INTERNATIONAL®
24 – 26 September 2024 Las Vegas, USA www.minexpo.com
FT Mining Summit
26 – 27 September 2024 London, UK & Online https://mining.live.ft.com
XXXI IMPC-International Mineral Processing Congress (IMPC 2024) 29 September – 03 October 2024 Washington, USA www.smeimpc.org
China Mining Expo
23 – 25 October 2024 Xi’an, China www.chinaminingexpo.com
The International Mining and Resources Conference (IMARC) 29 – 31 October 2024 Sydney, Australia www.imarcglobal.com
Resourcing Tomorrow 03 – 05 November 2024 London, UK www.resourcingtomorrow.com
To stay informed about upcoming industry events, visit Global Mining Review’s events page: www.globalminingreview.com/events
PERU Metso to deliver thickeners and filters to mine water treatment project
Metso has been awarded with a contract to deliver several thickeners and filters to a mine water treatment project in Peru. The value of the order is approximately €15 million, and it has been booked in the Minerals segment’s 2Q24 orders received.
Metso’s scope of delivery includes several high-rate thickeners operating in a high density sludge (HDS) mine water treatment application and automatic EBS Series Liquid Filters with an electric self-cleaning mechanism for ultra-fine filtration. The thickeners, which are part of Metso’s Planet Positive offering, include the Reactorwell™ feed system and are specially designed bolted stainless-steel construction for high corrosion resistance and fast installation.
“We are pleased to continue working with this important customer in Peru to support their needs in mine water treatment with our Planet Positive thickening solutions. The environmentally sound high-rate thickeners will have an important role in ensuring a reliable operation and meeting the customer’s project criteria for high performance, fast installation, and low maintenance”, said Brian Berger, Vice President, Thickening and Clarification at Metso.
NORWAY Public consultation of first licencing round for seabed minerals
Norway’s Ministry of Energy has presented a proposal for the announcement of the first licencing round for seabed minerals on the Norwegian continental shelf for public consultation.
The proposal sets out the areas where companies will be able to apply for exploitation licences, so that exploration and gathering knowledge about whether there is a basis for sustainable mineral exploitation on the Norwegian shelf can begin.
“The world needs minerals for the green transition, and the government wants to explore if it is possible to extract seabed minerals in a sustainable manner from the Norwegian continental shelf. A large majority of the Norwegian Parliament supports the government’s step-by-step approach to the management of seabed minerals. This announcement is an important next step in the management of our seabed mineral resources. Environmental considerations are taken into account in all stages of the activities. Today, we are presenting our proposal for areas to be announced in the first licencing round for seabed minerals for public consultation. We plan to award licences in the first half of 2025”, said Minister of Energy, Terje Aasland.
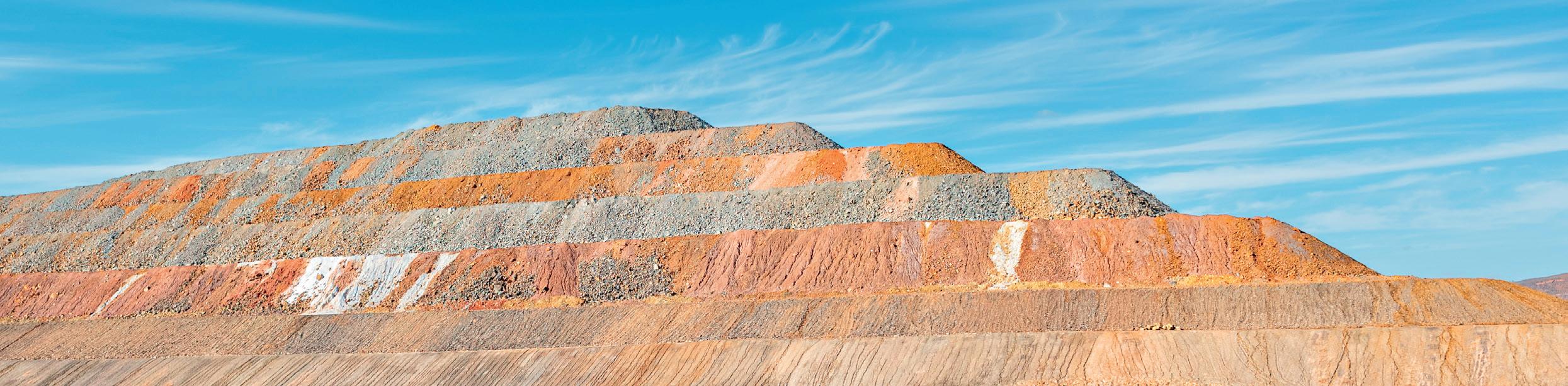
PROdUCT NEWS
As Orica marks its 150th anniversary in 2024, the company is reflecting on one of its innovations that has revolutionised the mining sector: mobile manufacturing units (MMU™s). Since the early days of on-site ANFO delivery, Orica’s MMUs have set an industry standard for bulk delivery systems, continuously evolving to meet the demands of mines worldwide.
The evolution of Orica’s MMUs
Orica’s MMU journey began in the 1960s with the rise of bulk delivery services. In 1968, the Mt Tom Price iron ore mine in Australia’s Pilbara region saw the first bulk ANFO truck loading, marking a significant milestone. Early bulk technology was based on watergel technology as pumped only products. Despite initial criticisms for being costly and slow, these early systems laid the foundation for future innovations.
The move to emulsions through the 1980s saw the development of site mixed emulsion MMU delivery, where emulsion was manufactured on the MMU and was pumped only delivery. With improvements in emulsifier technology, the models changed to the MMU, which were configured to blend emulsion and ammonium nitrate prills and the focus started shifting to productivity and energy. Orica MMUs were configured to deliver Heavy Anfo or Pumped products and were among the first to mix emulsion and prilled ammonium nitrate on site.
Introduction of the Bulkmaster™
The true game-changer came in 1989 with the introduction of the first Bulkmaster MMU. This model optimised on-bench operations and capital efficiencies by delivering ANFO, heavy ANFOs, and pumped blends from a single platform in a single high capacity, high delivery rate platform. The Bulkmaster was the first design to use a flexible bin configuration, adapting to site-specific product mixes.
The Bulkmaster 7, released in 2018, represented a significant leap in productivity with larger payloads and faster delivery rates. Over the past 35 years, the Bulkmaster MMU has not only improved explosive delivery efficiency, but also significantly enhanced safety measures.
Pioneering technological advancements
Orica’s commitment to innovation has continued since the early days of simple
delivery trucks in the 1960s. Its commitment to innovation has led to the development of various MMUs tailored for different markets, including the Flexmaster™, Quarrymaster™, and Handimaster™. The company’s ongoing focus on safety and productivity has resulted in significant advancements. Among these, the 4D™ bulk system stands out as a technology that harnesses Orica’s knowledge in emulsion chemistry, smart MMU capabilities, and process control. This system enables customers to use a wider range of energy-matched explosives in real time across varying blastholes conditions, whether they be wet, dewatered, or dry.
Customer benefits from innovation
The technological progress in Orica’s MMU range now integrates digital and automated systems to allow precision in drill rate measurement and the tailoring of bulk delivery to achieve greater blasting outcomes. Enhanced safety features protect workers and assets, while increased loading efficiencies save time and boost productivity.
Looking forward: Bulkmaster Pro
The forthcoming Bulkmaster Pro, set to launch in 2025 – 2026, will embody the pinnacle of bulk delivery technology. Combining the best features from previous models, the Bulkmaster Pro promises improved loading efficiencies, superior safety features, and cutting-edge integrated technology. This new model will reaffirm Orica’s position as an industry leader in innovation and technology.
As the company celebrates 150 years of innovation, its MMUs remain at the forefront of mining technology, continually evolving to meet the industry’s needs with enhanced efficiency, safety, and productivity.
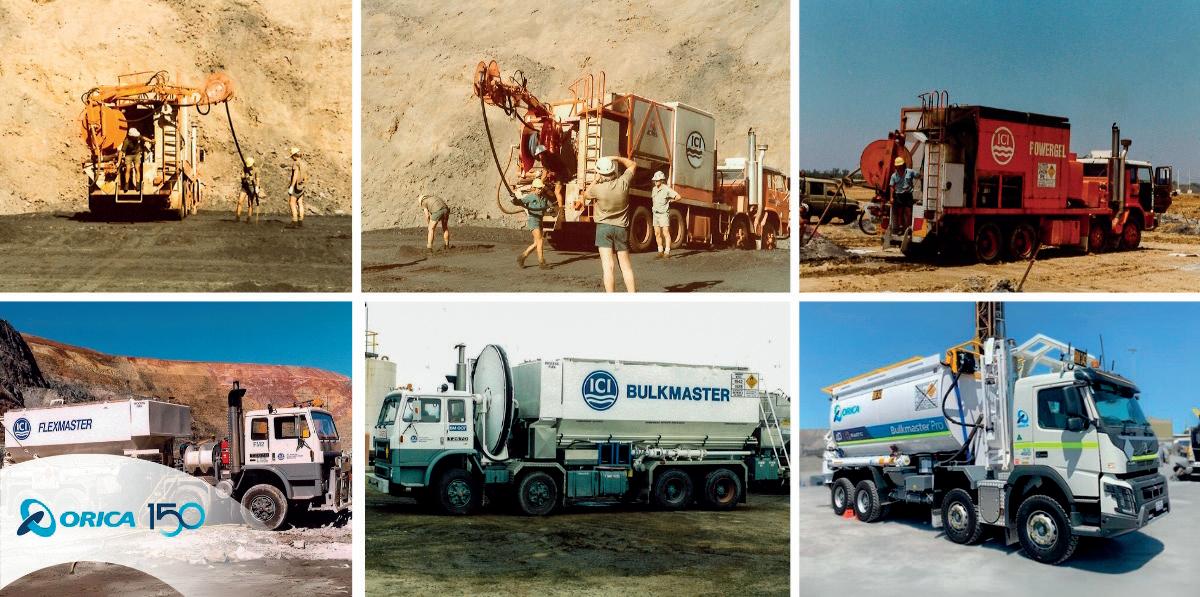
Figure 1. Driven by innovation: Orica’s journey in advancing bulk delivery MMU™ technology.
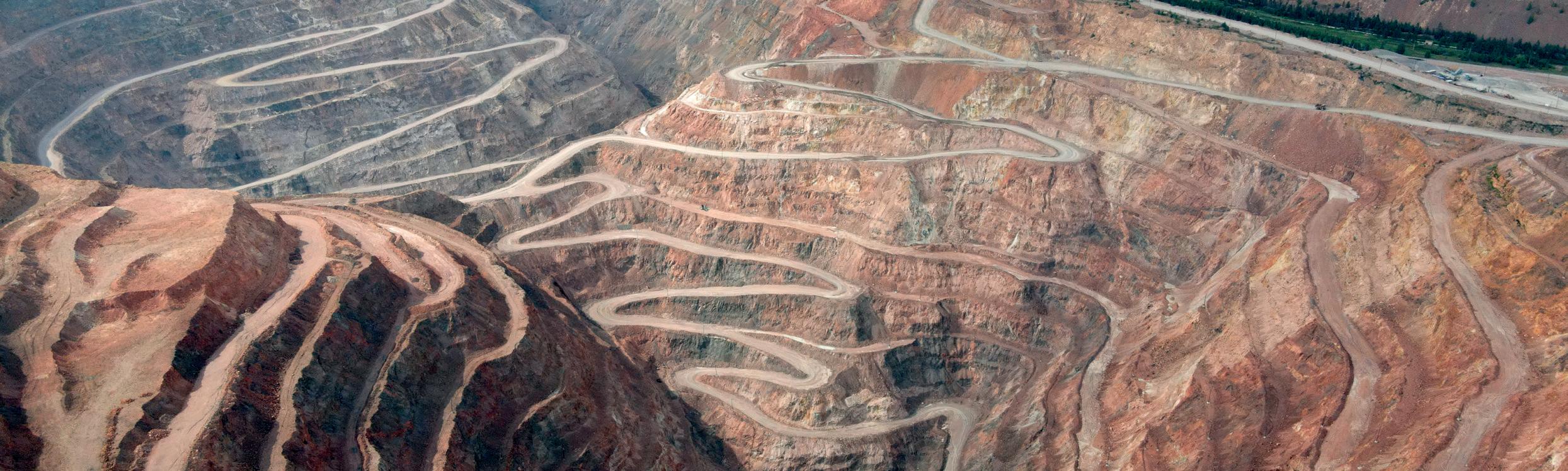
PROdUCT NEWS
As global demand for metal and minerals rises, so does the need for higher capacities – from processing large volumes of low-grade ore with minimal residual moisture, to doubling an operation’s throughput with an existing filter press. In either of these cases, LENSER offers innovative and reliable filter plate solutions to make high capacity operation both possible and profitable.
The filtration process is the key Obviously, external conditions must align to achieve a sustainable filtration process. One way to improve
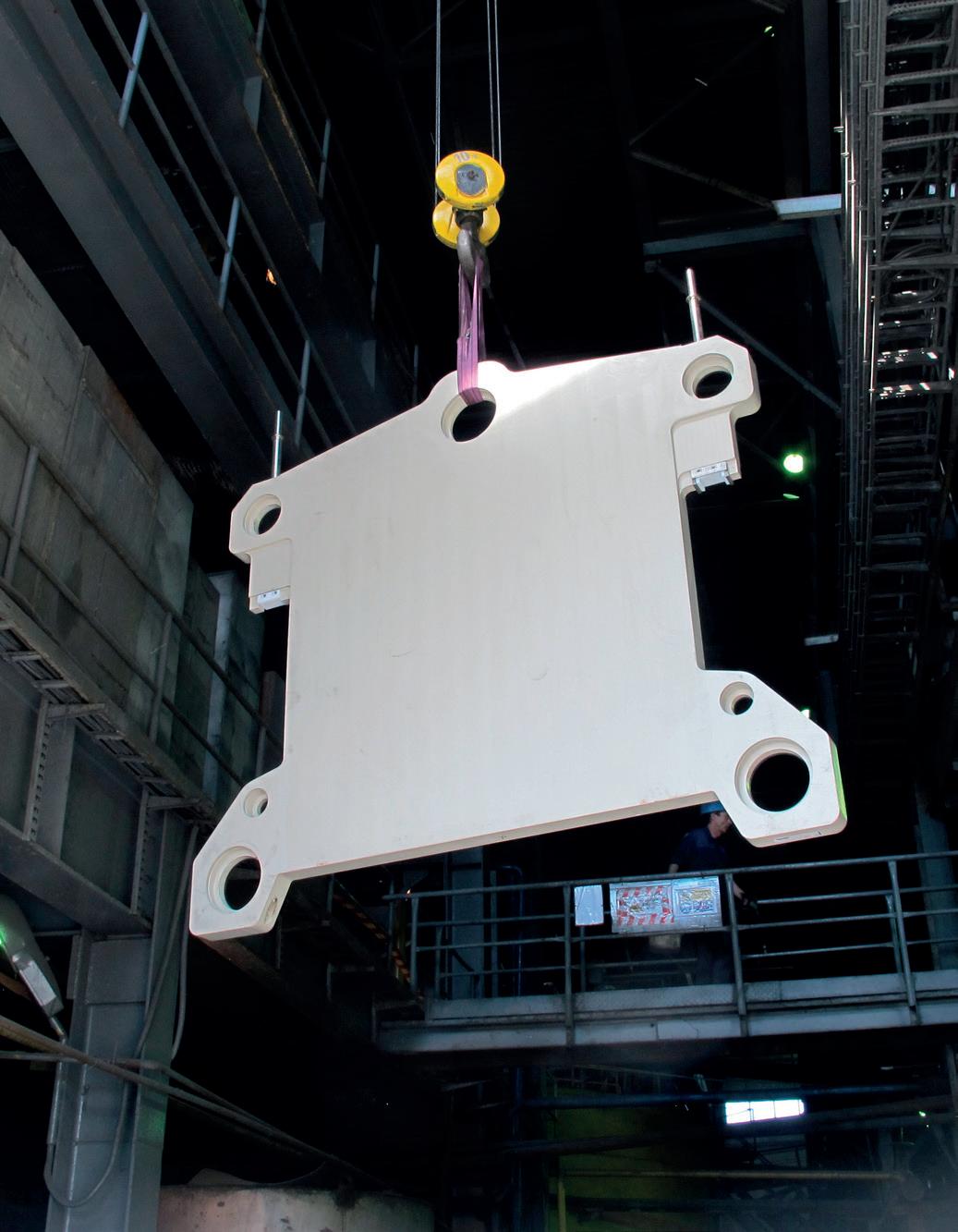
conditions may be the costly purchase of a new filter press. LENSER’s vision, on the other hand, focuses on the inner workings of an existing press – the filter plates and cloths –in order to optimise the filtration process. The company specialises in the production of customised filter plates and strives to find the best possible solution to complement a customer’s given situation. Having the perfect and individualised filter plate enables an outstanding filtration result.
Why have a customised plate?
For the mining industry, there are several purposes that a customised filter plate can serve. This can range from increasing filter press volumes and weights of the cake discharge (due to a higher capacity), to a noticeable reduction of the production costs themselves, lower energy and water consumption, and a noticeable increase of dry solid content of the concentrates or tailings. Furthermore, the filtration cycle time can be reduced, which simultaneously increases the service life of the filter plate. All of this results in a remarkable operating cost reduction.
LENSER Mining Plate
The LENSER Mining Plate is well suited to mining applications, especially for dewatering of concentrates and tailings. It differs from a normal filter plate in a number of ways: maximised drainage area, a large external feed port, a purposeful material selection, and detachable corner ports.
The LENSER Mixed Pack
Always highly recommended as an all-rounder alternative, LENSER also offers a standard product combination that suits every kind of mining or mineral application.
The LENSER Mixed Pack is a mix of recessed chamber and membrane filter elements which features all the advantages of membrane technology – i.e. it provides shorter filtration cycles with higher dry solid contents.
Customers have the choice of various filter plate designs and sizes (up to 2500 mm), and, as always with LENSER, the mixed pack is produced according to specific needs and challenges. The membrane filter plates within the LENSER Mixed Pack can also be made from LENSER Aurum, a newly developed, highly abrasive resistant material.
Figure 1. LENSER Mining Plate in Cooper Mine in Kazakhstan. Results: Cycle time per cycle reduced per 10%, residual moisture shrunk from 9% to 8%, and higher cake weight per cycle (11 t instead of 9 t).
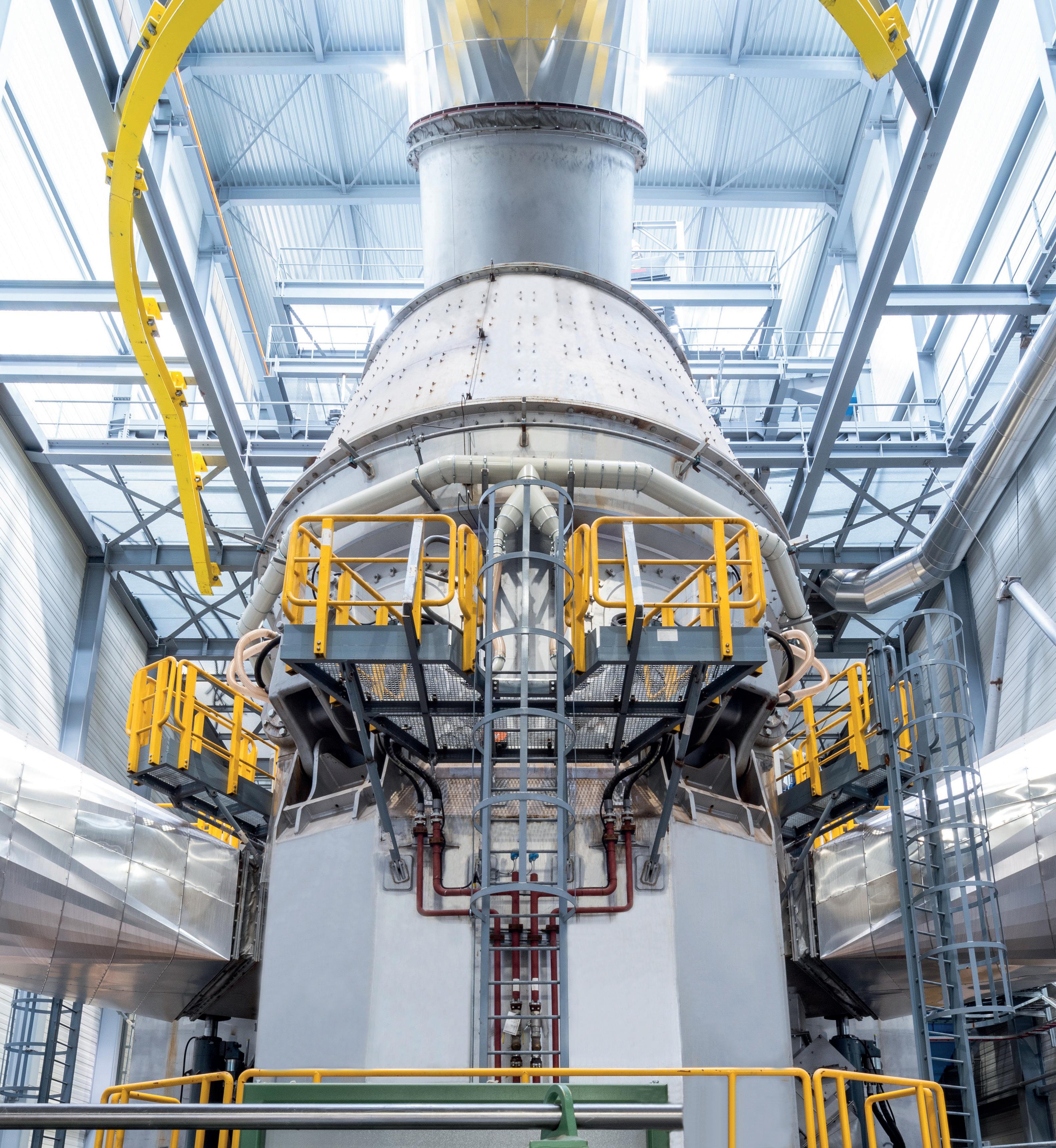
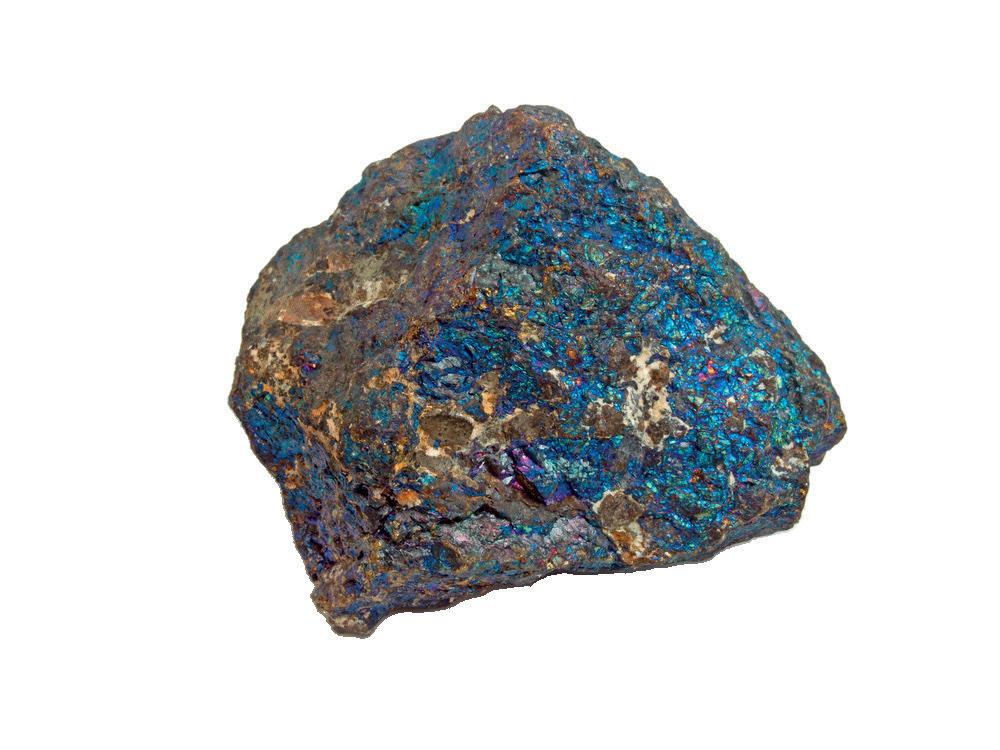
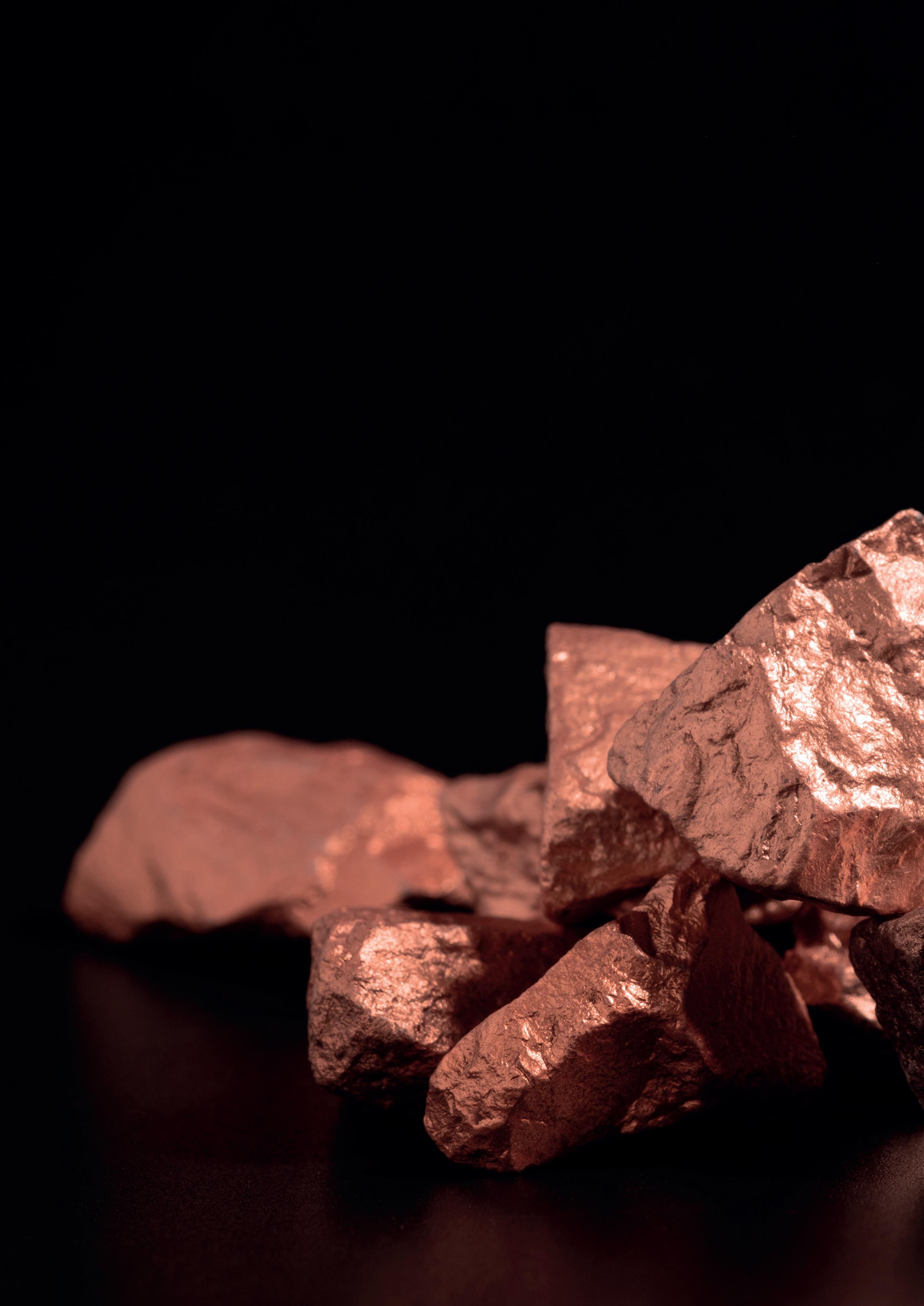
Sidhartha Patnaik and Lance Fogtman, ION Commodities, assess the current state of the copper market and consider its future prospects.
While several commodities are poised for growth in the next decade, few face an evolution as dynamic as copper. 2024’s prices, after hovering around US$8000/t for a good part of the first quarter, have shown a clear breakout and are now above US$10 000/t as of May, with the London Metal Exchange (LME) recording its highest three-month trade volume since June 2022. 1,2 Analysts suspect this bullish trajectory could last for at least the next three years, and some have suggested a new commodities ‘supercycle’ is afoot, led by copper. 3
A combination of short-term factors and structural changes are responsible for the tightness between copper’s high demand and constrained supply. The key question is how well the industry is poised to adapt to the impacts. While opportunities abound for market players to
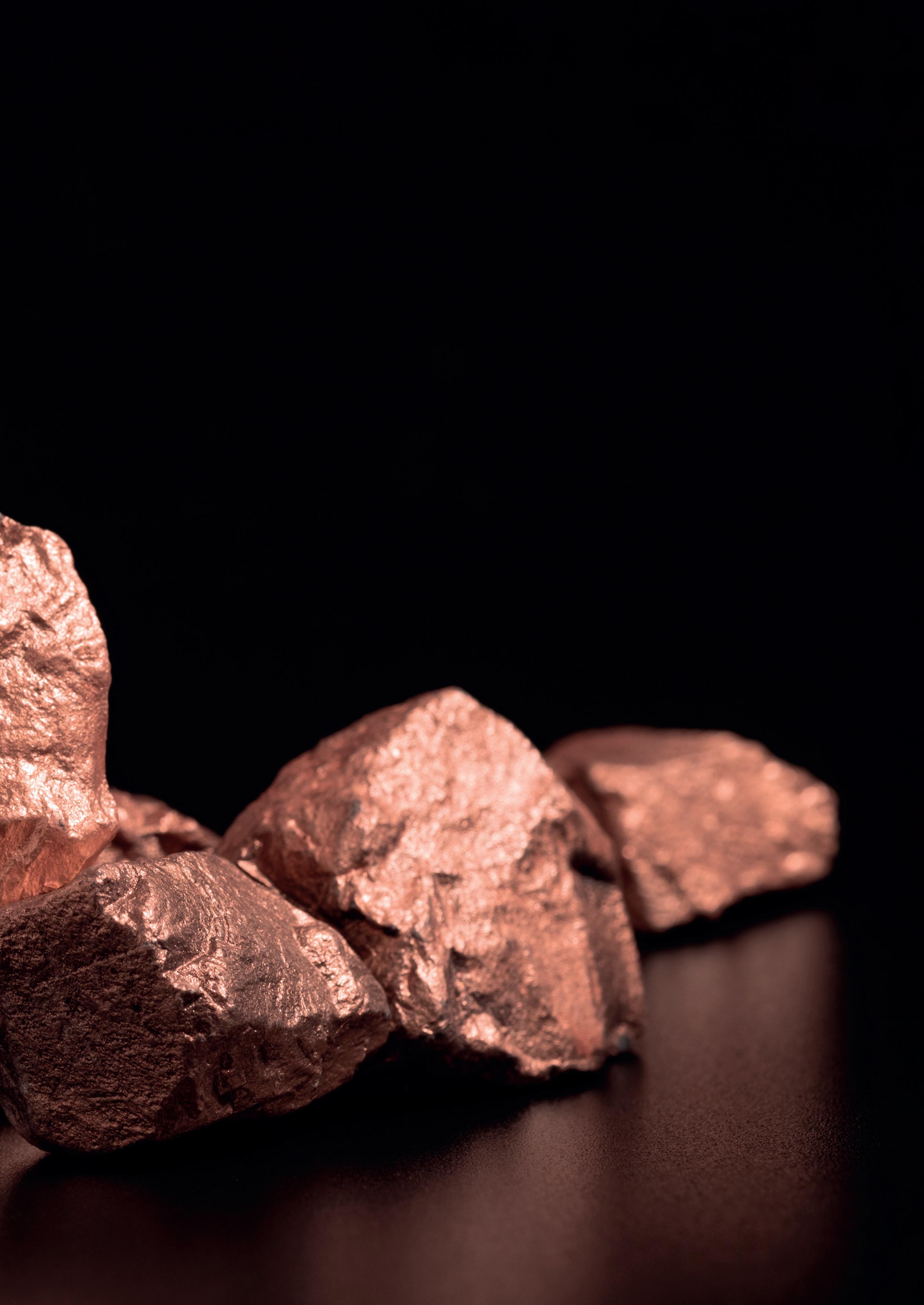
capitalise on these emerging trends, strategic investment is necessary to chart a resilient, sustainable, and prosperous future in this market as it evolves.
Market changes
Exceptionally conductive and malleable, copper is one of the most widely used metals globally. Its applications span power grids and data centres; industrial machinery and construction materials; chip manufacturing; medical devices; and energy transition technologies.
Modern demand for these applications has already driven an international boom, with global copper reserves estimated to be 1 billion t in 2023. 4 However, the last few years have seen a step change in growth and volatility due to more seismic market shifts underway. 5
Energy transition
Copper’s core applications in electrification, technology, and infrastructure make it instrumental to the global energy transition, which is becoming the most significant factor in the gulf between modern supply and demand.
The metal is a vital component in mineral-intensive ‘clean’ infrastructure and technologies – from electric vehicles (EVs) and charging infrastructure, to solar cells, wind turbines, and batteries. Demand for metals including copper has grown at pace amid the impending phase-out of conventional fuel vehicles and the arms race in EVs, with the latter using more than double the quantity of copper per vehicle. 6 Such is the dependency on copper that any supply-side disruption or tightness would now cause a dramatic slowdown in the production of renewable energy infrastructure, battery storage, and the uptake of EVs, with serious consequences for global supply chains.
New demand
Demand remains concentrated in the Eastern Hemisphere, with China alone consuming more than half of all refined copper globally. 7 Demand has typically stemmed from large infrastructure projects and construction, and though recent structural challenges in China’s infrastructure sector and its population decline could temper levels, other developing powers in Southeast Asia will almost certainly pick up the slack.
Consumption levels are naturally accelerating amid new tipping points in energy and technology. In addition to the feedstock demands of the global energy transition, the meteoric rise of electronics and chip manufacturing has bolstered copper’s bull run, especially among the BRICs. India, for instance, recently
pledged over US$15 billion for three semiconductor plants as it vies to compete globally across automobiles and consumer technologies. 8
Tight supply
In tension with demand, the exhaustion of reserves in addition to disruptions amongst producers – frequently linked to geopolitical tensions and conflict – are tightening supply.
The largest global supplier, based in Chile, is still falling short of pre-pandemic output levels due to depleted reserves, while other producers missed annual targets in 2023 amid unexpected closures. 9 One major case is that of the disputed Central American mine, Cobre Panamá, which previously produced around 1% of global output, but was closed by the local outgoing government following protests last year. 10
The situation has worsened with supply chain disruptions to the Panama and Suez transport routes. With the largest production assets some distance from demand sources like Australia and South America, copper will see a high volume of freight movement for the foreseeable future.
Some projects to ease this strain have already been approved. Copper smelters in China recently pledged to curb output, while Adani is set to open a US$1.2 billion copper refinery in Gujarat to boost production. 11,12 Despite this, mine production in 2024 will most likely contract. Together with the ban on Russian copper and other metals from the LME and COMEX this April, a surge in prices is highly likely. 13
Circular economy
A major portion of copper demand is increasingly met through recycled material. Being durable, energy-efficient, and highly recyclable, copper lends itself to the circular economy trend playing out across metals as a way of mitigating resource scarcity, limiting environmental impact, and boosting economic efficiency. Interest in the scrap market is growing amongst trading firms, and this emerging cycle will continually reshape the dynamic between asset owners and asset traders in the years ahead.
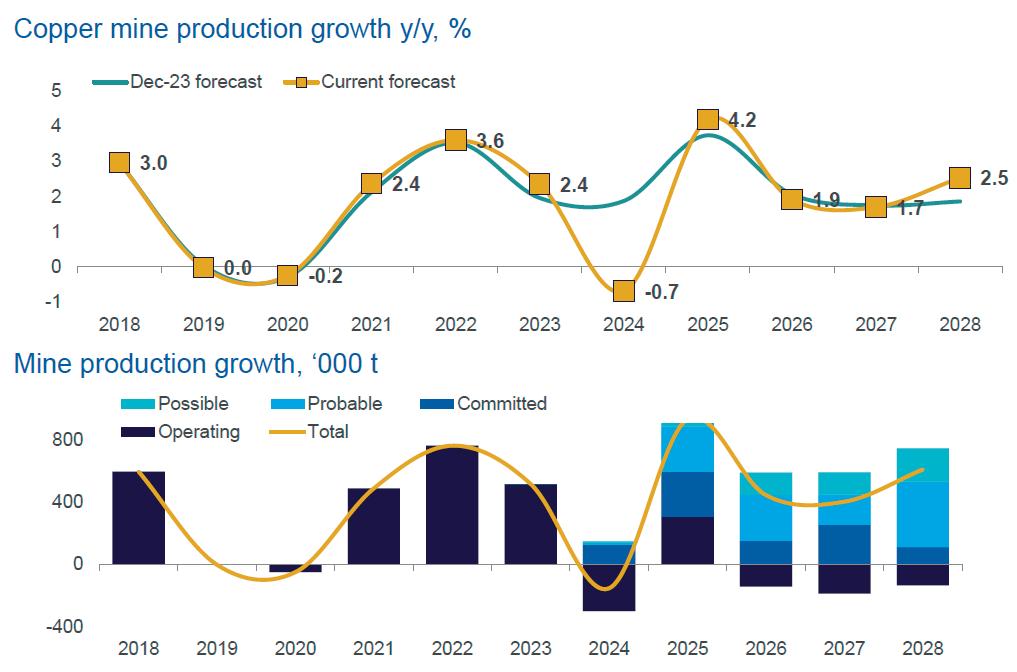
Key implications
All of this demonstrates the level of complexity in copper is constantly growing.
Figure 1. Global copper production has come under pressure in recent years, though forecasts show some signs of growth (Source: CRU Group Copper Market Outlook – March 2024).
Fletcher
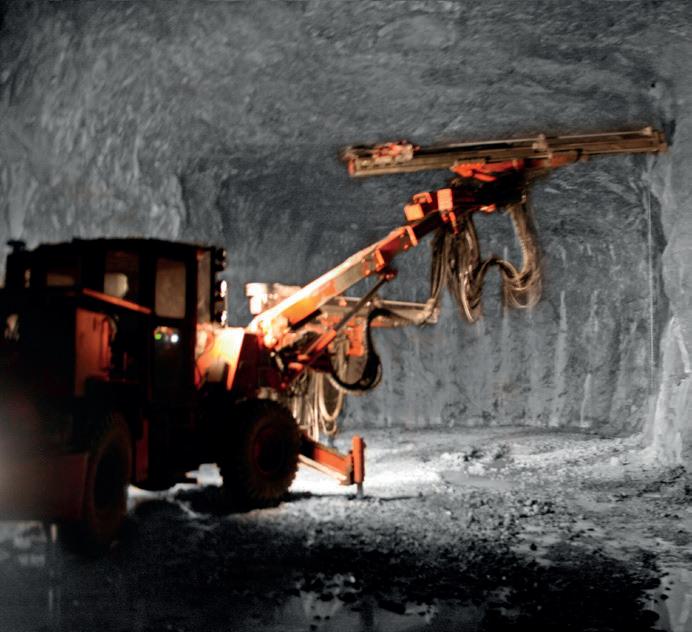




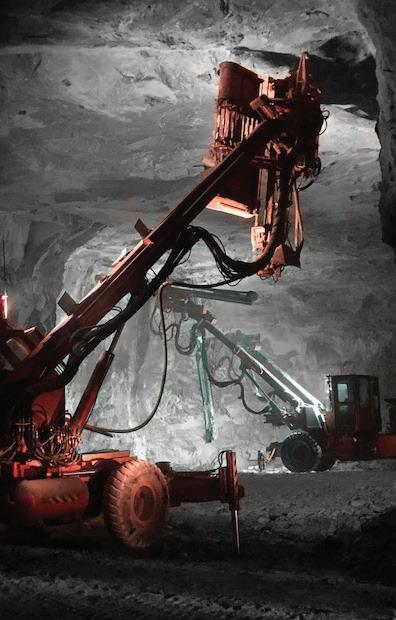
For asset owners, optimising assets and eliminating any idle time is crucial to capitalise on surging demand and secure their business against significant risks.
The key challenge lies in achieving this operational efficiency. Though copper offers liquidity and efficient price discovery on multiple exchanges right now – the LME, COMEX, ShFE – too many businesses fall short of the capacity to take advantage, due to inefficiencies in the way they monitor their positions, profit and loss (P&L) calculations, cashflows, and financing facilities.
Optimising these functions is challenging. A flexible, interoperable technological backbone is the bedrock for simplifying operations, yet the industry has typically deployed technology inconsistently, and there are key gaps in awareness about its value.
Those which have invested in digital transformation face issues too, usually related to operating with siloed platforms that cannot interact or using a local solution to manage an evolved and booming global business. Even the best enterprise technology is limited in its ability to support global trading or offer visibility into positions and operations across borders.
The implications for profitability are huge: it is not unheard of for a trader to lose millions of dollars due to unmonitored trades, without real-time monitoring capabilities installed.
Futureproofing the market
In the race for digital transformation across commodities, metals such as copper lag at least a decade behind power. To narrow this gap, the market must address some specific shortfalls.
Every corner of the market must prioritise risk management more than ever before. Some of the
largest market entrants in recent years have witnessed the threat posed by impaired supply chain visibility at times of volatility and disruption. Moving forward, we should see more investment in real-time risk management capability, moving on from generic solutions.
Related to this is the need to pre-empt the rigorous reporting and compliance procedures that will inevitably emerge as the energy transition progresses. Firms will soon be obligated to track their supply chains and more closely monitor compliance, and public companies face even greater scrutiny from investors. Investing in the tools for a more holistic view of supply chains, risk, sustainability metrics, and more will be a major advantage.
Finally, establishing a base level of interoperable technology across the industry would secure the market more broadly. This is especially true for regions that are critically low on high-quality infrastructure, yet have the means to be globally competitive. Once a broader layer of risk management and operational efficiency has been established, the industry can lean into some of the most sophisticated analytics solutions available to fully optimise assets and trading routes.
Futureproofing copper is doubly critical, given climate risk and uncertainty. A recent PwC analysis recently found that even in an optimistic scenario for 2050, over half the world’s copper mines will be in areas exposed to significant drought risk. 14 While research is nascent and evolving, some of the most significant mines today are already a source of key ESG concerns, such as geopolitical contention, armed conflict, and corruption. Being equipped to mitigate this risk is imperative.
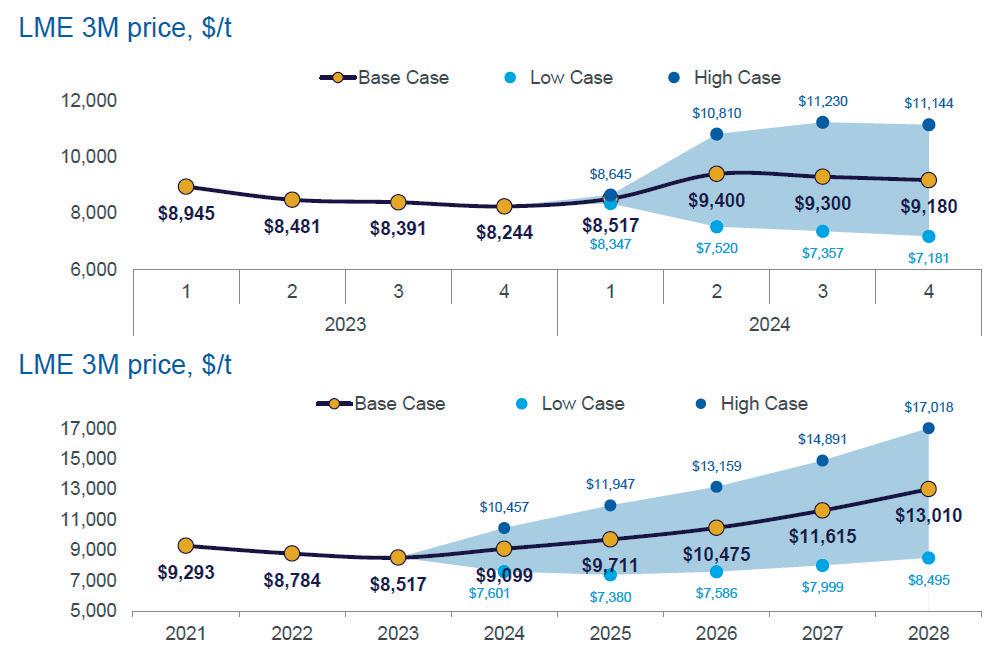
Looking ahead
Investment in operational efficiency and risk management was once a secondary consideration for metal traders. However, the rise of the energy transition and the emergence of complex supply-demand dynamics, fuelling copper’s bullish outlook, show a new approach is needed.
Having the capabilities for rigorous risk management and efficiency combined with a futureproofed, interoperable infrastructure will be a key necessity and differentiator in the turbulent years to come.
References
Available on request.
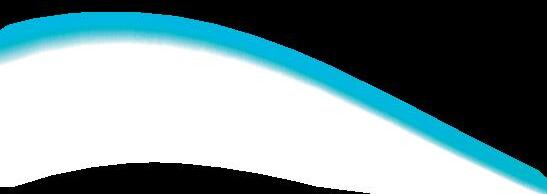
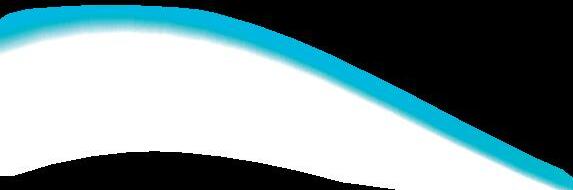
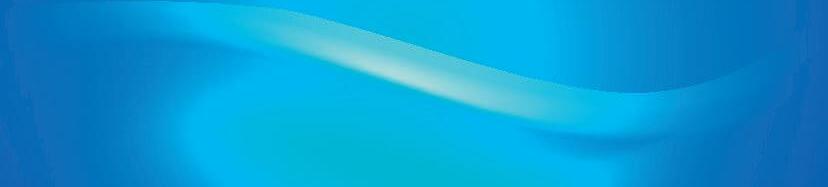
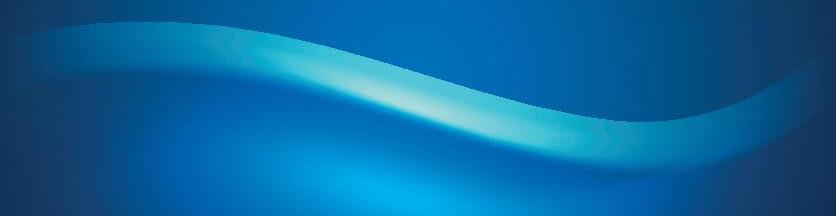
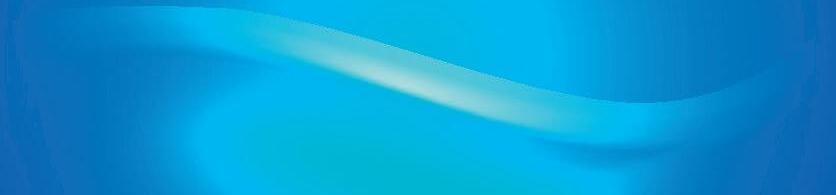
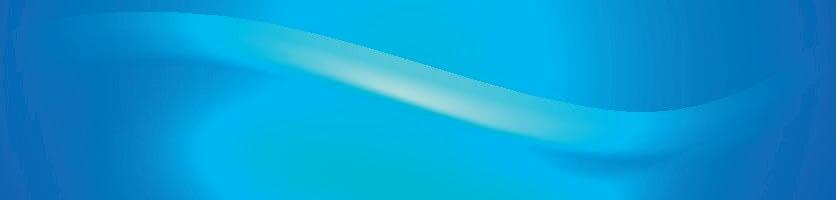
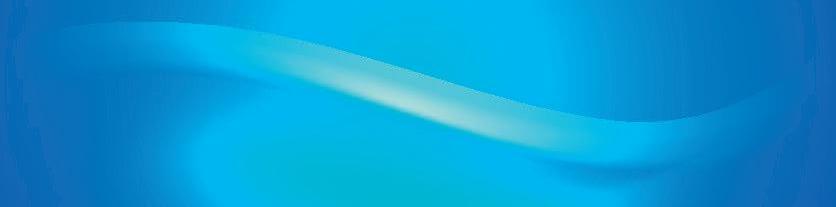
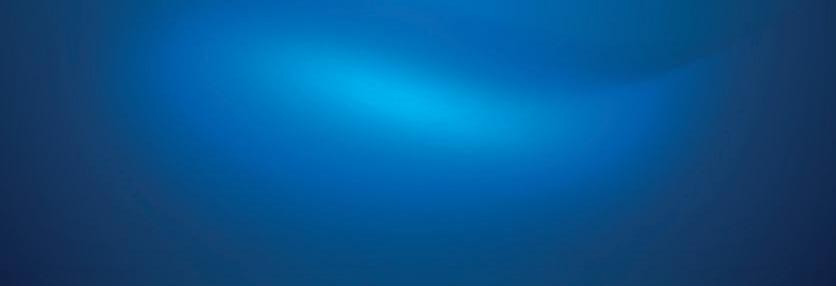
Figure 2. Copper prices recently surged to their highest in years, with the London Metal Exchange (LME) reporting record figures (Source: CRU Group Copper Market Outlook –March 2024).
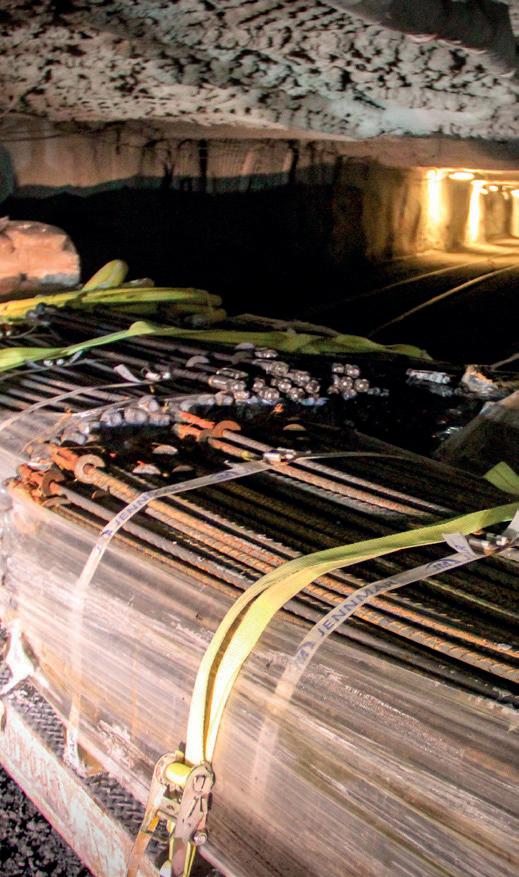



DEMANDING CONDITIONS
DEMAND JENNMAR
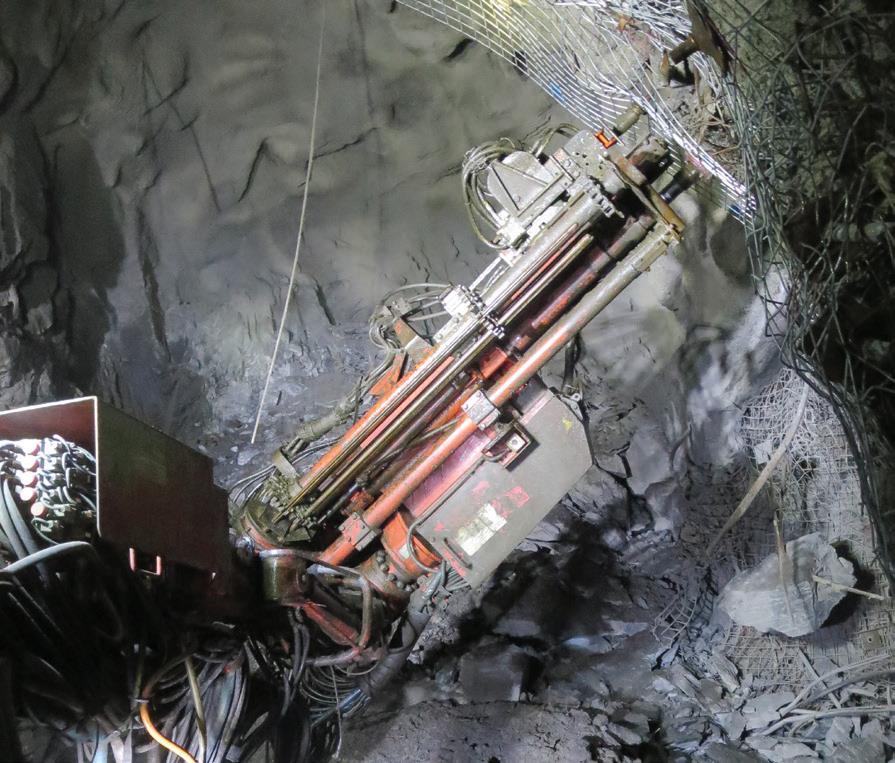
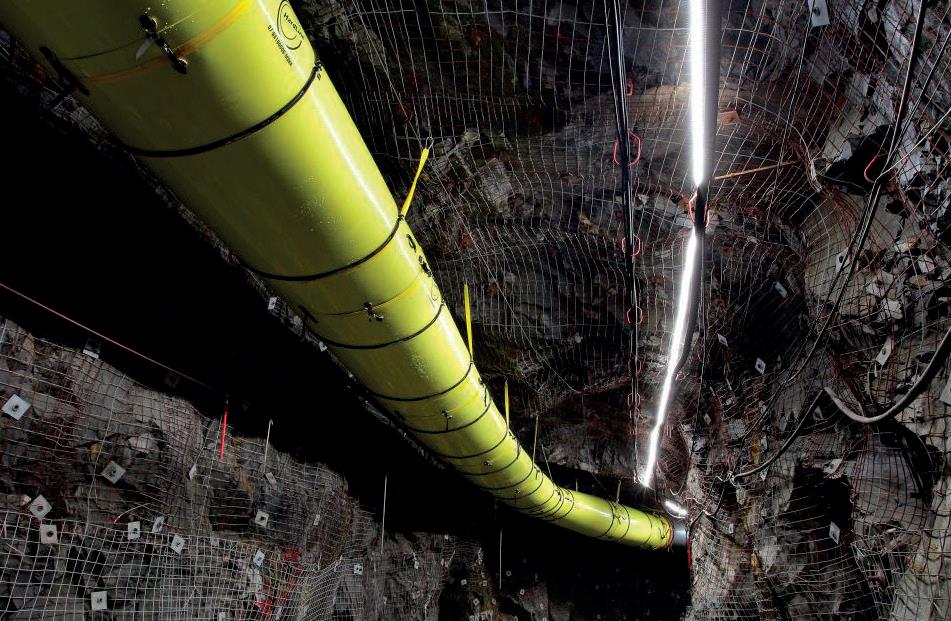
JENNMAR designs and manufactures a wide range of dependable ground control products, from bolts and beams to channels and trusses, resin, rebar, and more. We’re proud to make products that make the mining, tunneling, civil, and construction industries safer and more efficient.
Because we understand the ever-changing and demanding conditions above and below ground we have built the richest portfolio of diverse and complementary brands. JENNMAR sets the bar in every industry we serve and as we continue to grow, our focus will always be on the customer.
We feel it is essential to develop a close working relationship with every customer so we can understand their unique challenges and ensure superior customer service. Our commitment to the customer is guided by three words: SAFETY, SERVICE, and INNOVATION . It’s these words that form the foundation of our business. It’s who we are.
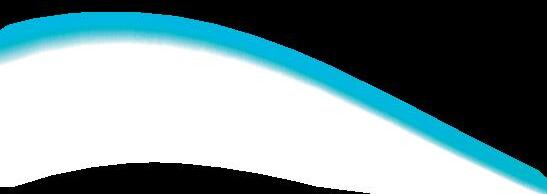
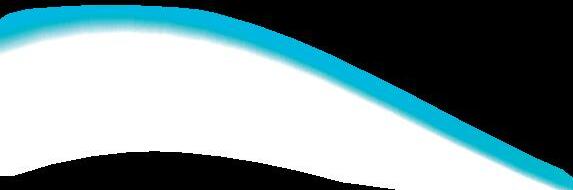




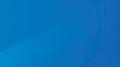
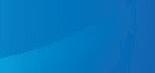
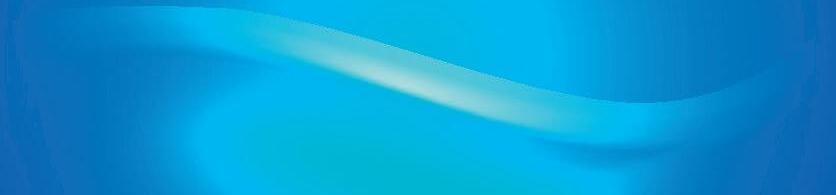
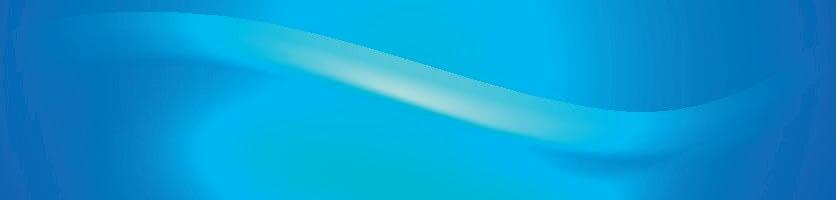
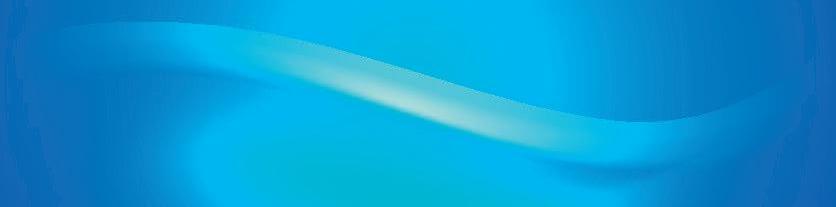
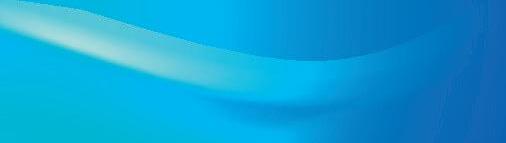
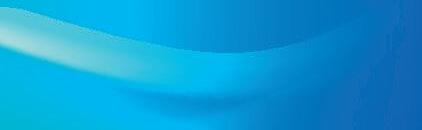
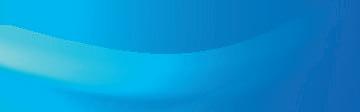
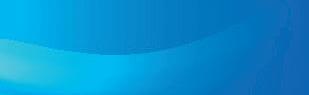

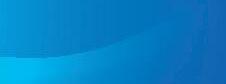
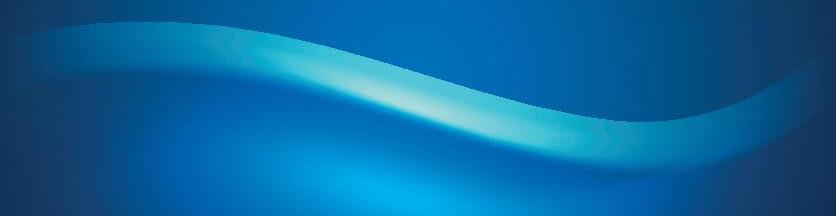

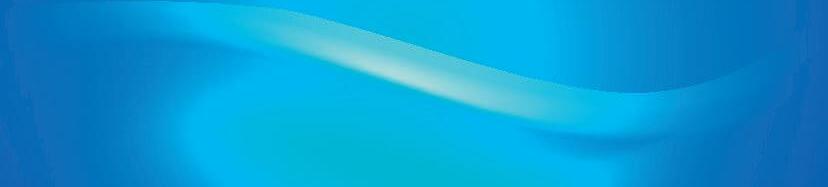
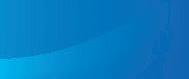
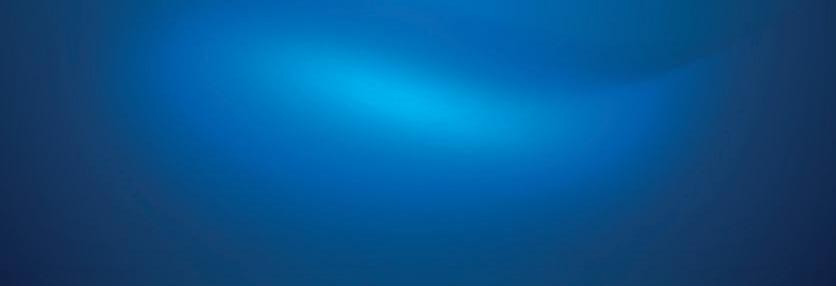



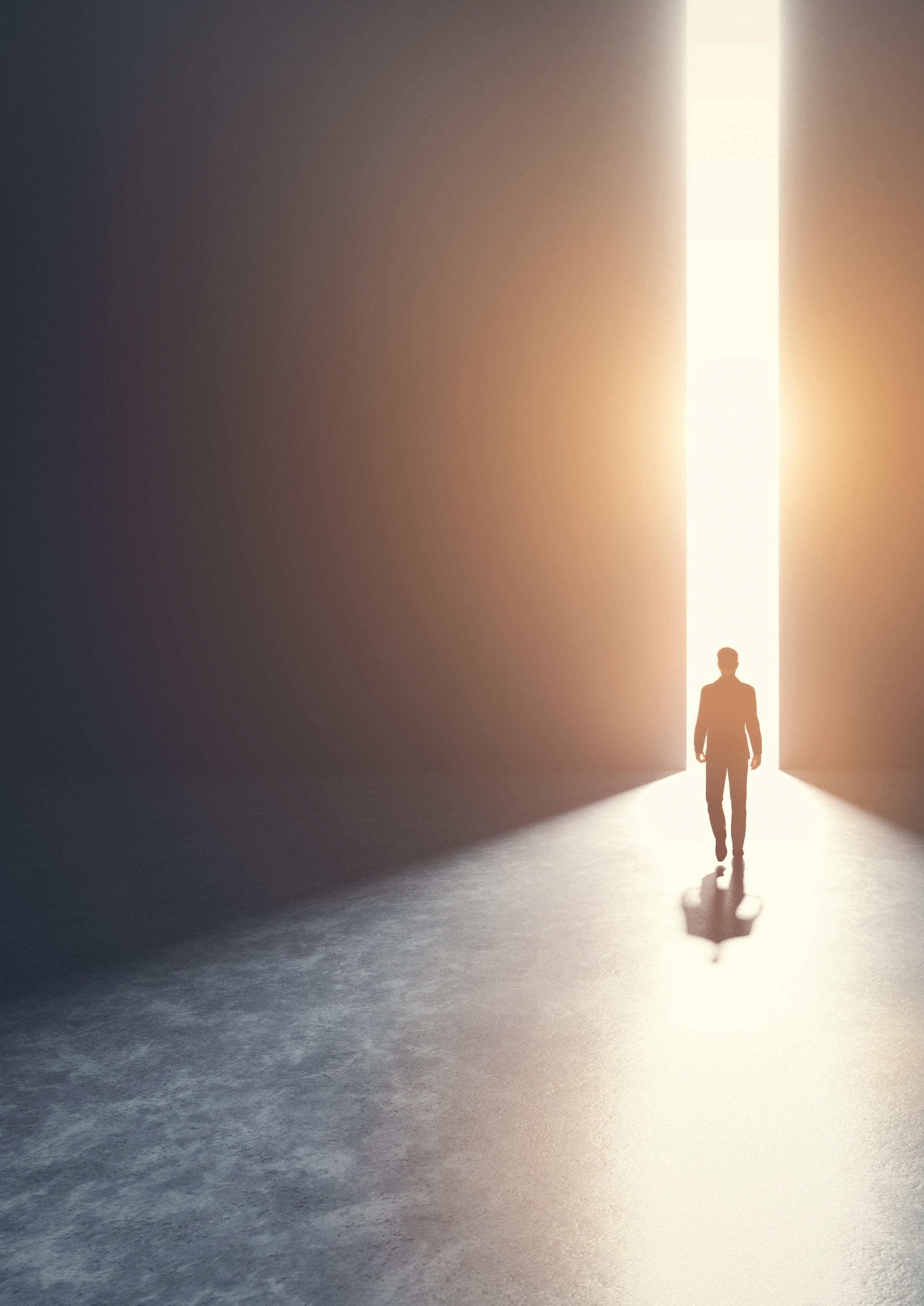
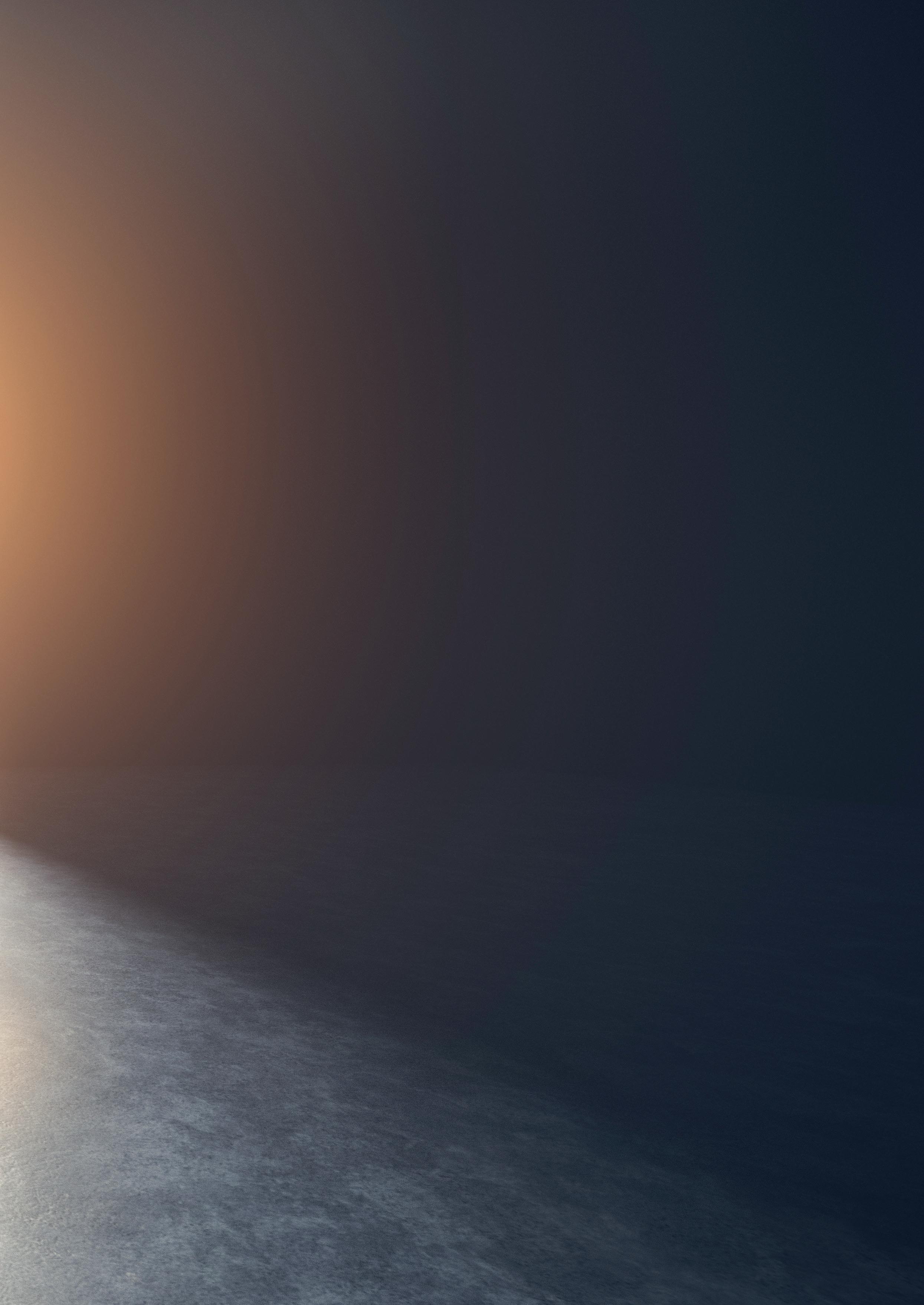
Alireza Oladzadeh, ABB Process Industries, reviews the role of long-term service agreements in gearless mill drive operation and maintenance.
The mining and minerals processing industry is currently navigating a landscape fraught with challenges. Rising exploration costs, volatile market prices, and increasingly remote environments are pushing the industry to evolve. These challenges must be met while protecting the health and safety of workers and adhering to increasingly stringent environmental regulations. Solutions that tackle these issues need to ensure equipment operates efficiently and reliably, with minimal intervention from the operators.
In this context, the upkeep of critical equipment, such as gearless mill drives (GMDs), becomes paramount. GMDs are a foundation for grinding operations at scale in mining, offering enhanced reliability and efficiency. The upkeep of these systems is essential for their longevity and continued productivity. However, maintaining these complex systems requires more than just regular check-ups; it demands a proactive and comprehensive approach to maintenance. This is where long-term service agreements (LTSAs) come into play. Through corrective, preventative, predictive, and prescriptive maintenance strategies, supported by the latest in remote diagnostic services, LTSAs offer a robust framework for tackling industry challenges, while improving health and safety, achieving environmental goals, and reducing costs.
Getting to know gearless mill drives
GMDs are the workhorse of grinding operations within the mining industry. In a GMD, rotor poles are mounted directly onto the mill, meaning the mill itself becomes the rotor of the gearless motor. This eliminates the need for additional mechanical components such as ring-gears, pinions, gearboxes, couplings, and motor shaft bearings, enhancing the reliability and efficiency of the system.
GMDs offer several advantages over alternative mill drives. For example, they can reach higher power levels while reducing overall energy consumption. Furthermore, their overall mechanical infrastructure and the need for fewer components, coupled with greater power, reduce a mine’s footprint by eliminating the need for larger or multiple smaller mills. This reduction in physical footprint translates into a more efficient use of space, particularly in remote areas, and is advantageous for operations in environmentally sensitive areas where minimising land disturbance is crucial.
Unlocking greater performance and reliability
Implementing LTSAs for GMD maintenance offers numerous benefits that enhance reliability and uptime. These agreements provide regular maintenance schedules and predictive maintenance strategies, which help to avoid unplanned downtime. In mining operations, every second counts, and the ability to rapidly address and prevent any unscheduled shut-downs can make a significant difference in productivity and profitability.
Solutions like ABB’s multi-year service agreements embed advanced services that help plan maintenance activities over the long term, extending the lifecycle of equipment and increasing overall equipment effectiveness (OEE). These agreements cover all levels of maintenance strategy, ensuring equipment like GMDs remain operational and efficient.
Streamlining the overall maintenance process, LTSAs ensure that all necessary checks and repairs are conducted in a timely and efficient manner. This not only extends the lifespan of the equipment, but also maintains optimal performance levels. Continuous technical support and access to specialised knowledge further enhance operational efficiency. With experts on hand to manage and troubleshoot complex GMD systems, mining operations can maintain a high level of performance with minimal disruption.
Remote diagnostic services allow engineers to log onto the system regardless of physical location, access cloud-based data, and investigate problems and provide recommendations or immediate resolutions. For example,
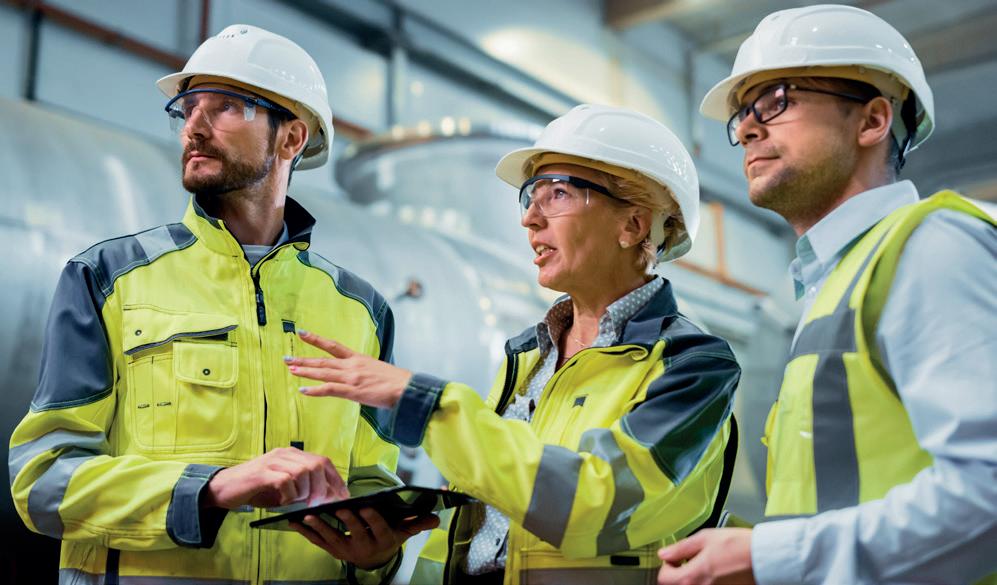
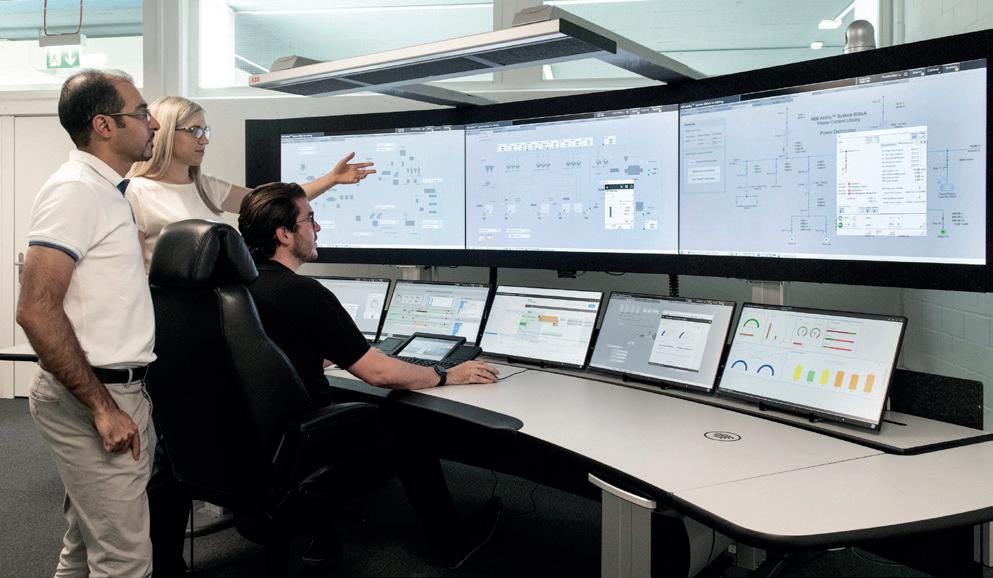
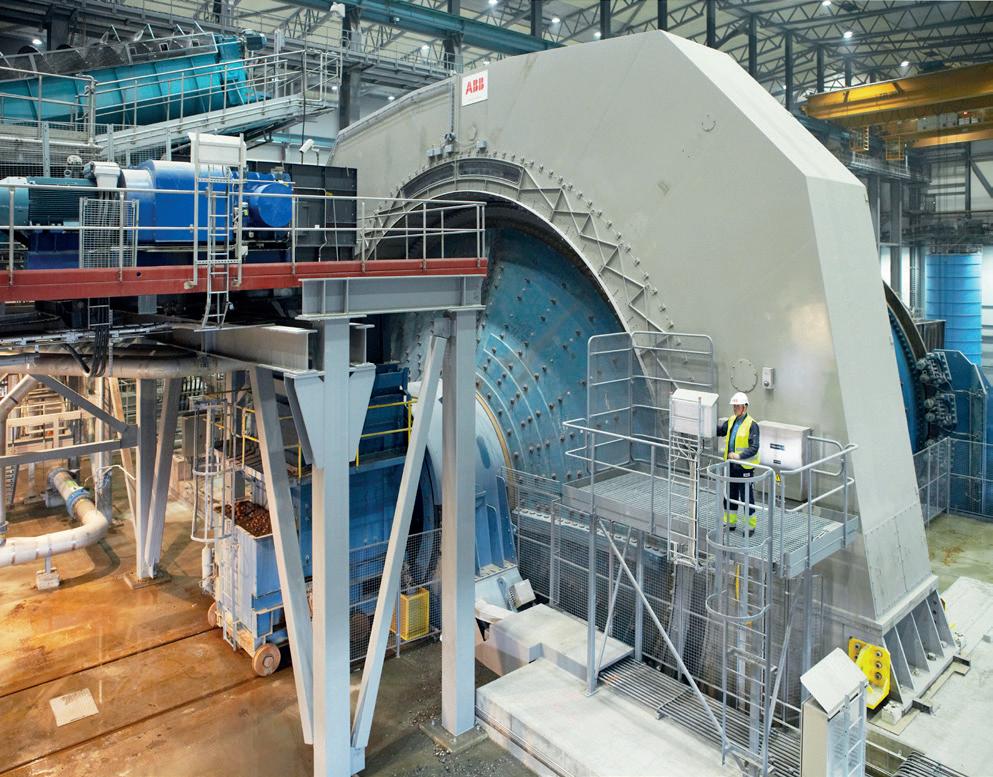
if there is an issue on the machine, engineers are able to quickly diagnose the problem and guide operators on how to resolve it. From support lines (24/7) and remote troubleshooting, to predictive maintenance and condition monitoring, these services are designed to support fundamental, complex systems like GMDs and allow experts to suggest solutions from anywhere in the world.
To further prevent downtime and keep the GMDs running, LTSAs allow for service experts to monitor the system on a regular basis without having to be on site. This minimises the risk of costly, unscheduled breakdowns and optimises process performance. Software is able to predict potential failures based on detailed analysis of historical and current data on the electrical, mechanical, and thermal parameters of the GMD. For instance, the ABB Ability™ Predictive Maintenance for Grinding (Figure 4) monitors the health of crucial assets against pre-defined thresholds utilising this data, and is able to notify operators if an anomaly is detected by the system.
Ongoing health assessments allow operators to take action before failure occurs. Combining these services with the integration of a mobile application, like ABB’s Grinding Connect (Figure 5), allows operators to access status updates and an overview of the equipment from anywhere, at any time.
To provide a full range of maintenance, it is important to provide consistent, detailed condition checks. As such, ABB experts create a number of maintenance reports each year. During structured GMD system assessments, ABB technical experts analyse and evaluate data collected via a secure internet connection. They perform an analysis and deliver these reports which include a summary of findings and recommended preventative and corrective maintenance tasks.
Data is key to corrective, preventive, predictive, and prescriptive maintenance concepts. The ability to collect and analyse data provides accurate visibility into the health of a GMD system. This visibility offers clear advantages to GMD operators, such as the ability to plan maintenance tasks ahead of time or postpone them with confidence based on condition reports and evolving priorities. This targeted decision-making is gaining traction as the advantages become more apparent to mining companies.
The overarching goal of LTSAs aims to help mining companies achieve the most from their investment in critical equipment and ensure that they can predict and plan the resources they need to spend on service. Going beyond short-term success, these maintenance strategies target long-term value creation, helping to identify risks, make qualified decisions, and manage available data to increase the longevity of the systems.
Addressing flexibility and customisation
Flexibility and customisation are key components of effective LTSAs. Mining operations vary greatly in their individual needs and challenges, and a one-size-fits-all approach is rarely feasible. Customised solutions allow for targeted maintenance strategies that maximise efficiency
Figure 2. ABB collaboration Operation Center (CoC).
Figure 3. ABB GMD running in Boliden’s Aitik mine.
Figure 1. ABB service staff.
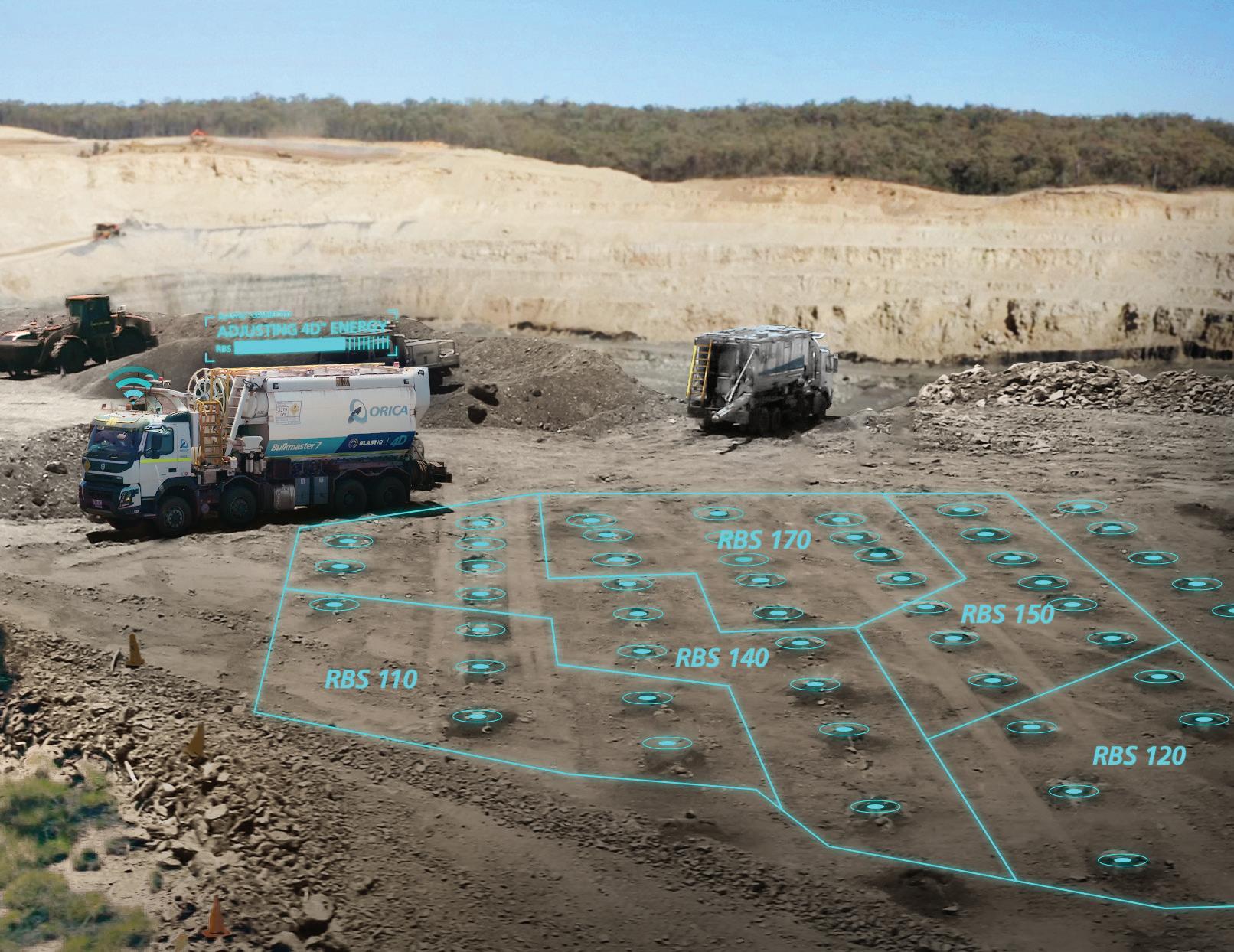
4D™ BULK SYSTEMS
THE NEW DIMENSION IN BLASTING REAL-TIME TAILORING OF ENERGY TO MATCH GEOLOGY AND HOLE CONDITIONS
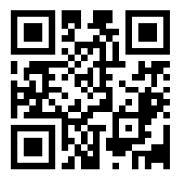
A revolutionary bulk system integrated with cutting-edge technologies.
fume & nitrate leaching
drill & blast costs
To learn more about 4DTM and how it can support your operations today, come and see a 4DTM Bulk Delivery System enabled MMU up close at MINExpo 2024 booth #13901 or visit orica.com/4D
and cost-effectiveness. It is also vital that these services evolve with the technology. Continuous adaptation of service requirements to meet the needs of the system helps to extend the lifecycle of the equipment while reducing associated costs.
Furthermore, having experts with GMD Field Service Certification on hand who are familiar with the intricacies of critical equipment ensures that any issues can be addressed promptly and effectively. Whether remote or on-site, LTSAs help to maximise the availability of service for proactive and reactive assistance contributing to asset performance.
The LTSA, lasting three to five years and including a comprehensive lifecycle management programme, aligns focus on long-term reliable maintenance strategies which will support customer operations and maximise operational equipment effectiveness.
Technology made for tomorrow
The future of mining maintenance is increasingly tied to technological advancements in corrective, preventive, predictive, and prescriptive maintenance. Digitalisation and the integration of the Internet of Things (IoT) are
revolutionising how maintenance is conducted. ABB’s advanced services use data analytics and machine learning to anticipate failures and issues with equipment before they occur or escalate, allowing for proactive interventions that prevent downtime and extend equipment life.
Digital tools and IoT devices enable the real-time monitoring and diagnostics of GMD systems, providing valuable insights into equipment performance and health. This allows for more precise and effective maintenance strategies that can adapt to changing conditions and requirements.
Sustainability and energy efficiency are also becoming increasingly important in maintenance practices. As the mining industry seeks to reduce its environmental impact, strategies that enhance energy efficiency and minimise waste are crucial. LTSAs that incorporate these principles not only contribute to environmental goals, but also offer cost savings through reduced energy consumption and improved operational efficiency.
ABB is currently developing its ‘Meet the Expert’ campaign to further support customer operations with its service solutions, as well as raising awareness of the benefits associated with LTSAs. This involves immersion sessions between experts and mine operators designed to cultivate collaboration and ignite innovation for the future of mining technology.
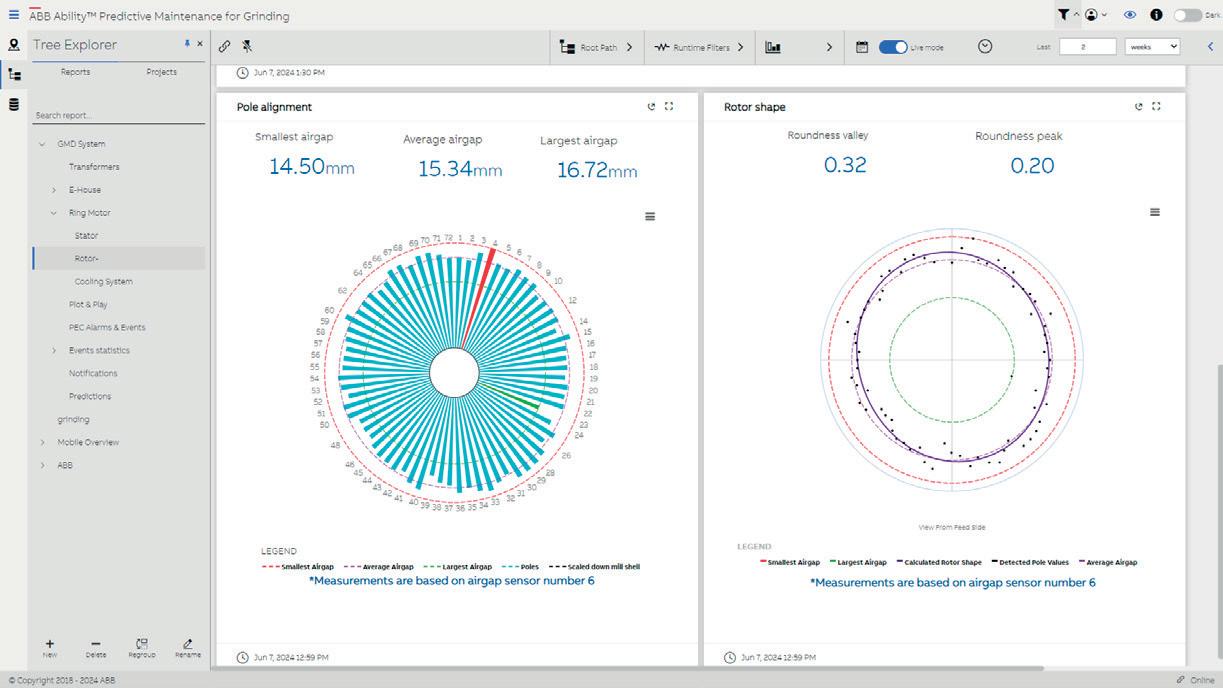

The path to sustainable success
LTSAs play a pivotal role in future-proofing mining operations, particularly in the maintenance of GMDs. The key benefits of LTSAs include enhanced reliability and uptime, streamlined maintenance processes, continuous technical support, and adherence to environmental and safety standards.
Technological advancements in corrective, preventive, predictive, and prescriptive maintenance, driven by digitalisation and IoT integration, are set to further enhance the effectiveness of LTSAs. These advancements, coupled with a growing emphasis on sustainability and energy efficiency, position LTSAs as a strategic imperative for the mining industry.
In summary, the strategic importance of long-term service agreements in the mining industry cannot be overstated. By ensuring the longevity and efficiency of GMDs through a comprehensive service portfolio including maintenance strategies, LTSAs offer a path to overcoming industry challenges while promoting safety, environmental responsibility, and cost-efficiency. As the mining industry continues to evolve, the role of LTSAs in maintaining critical equipment and driving operational excellence will only become more vital.
Figure 4. ABB Ability Predictive Maintenance for Grinding application.
Figure 5. Grinding Connect mobile app.
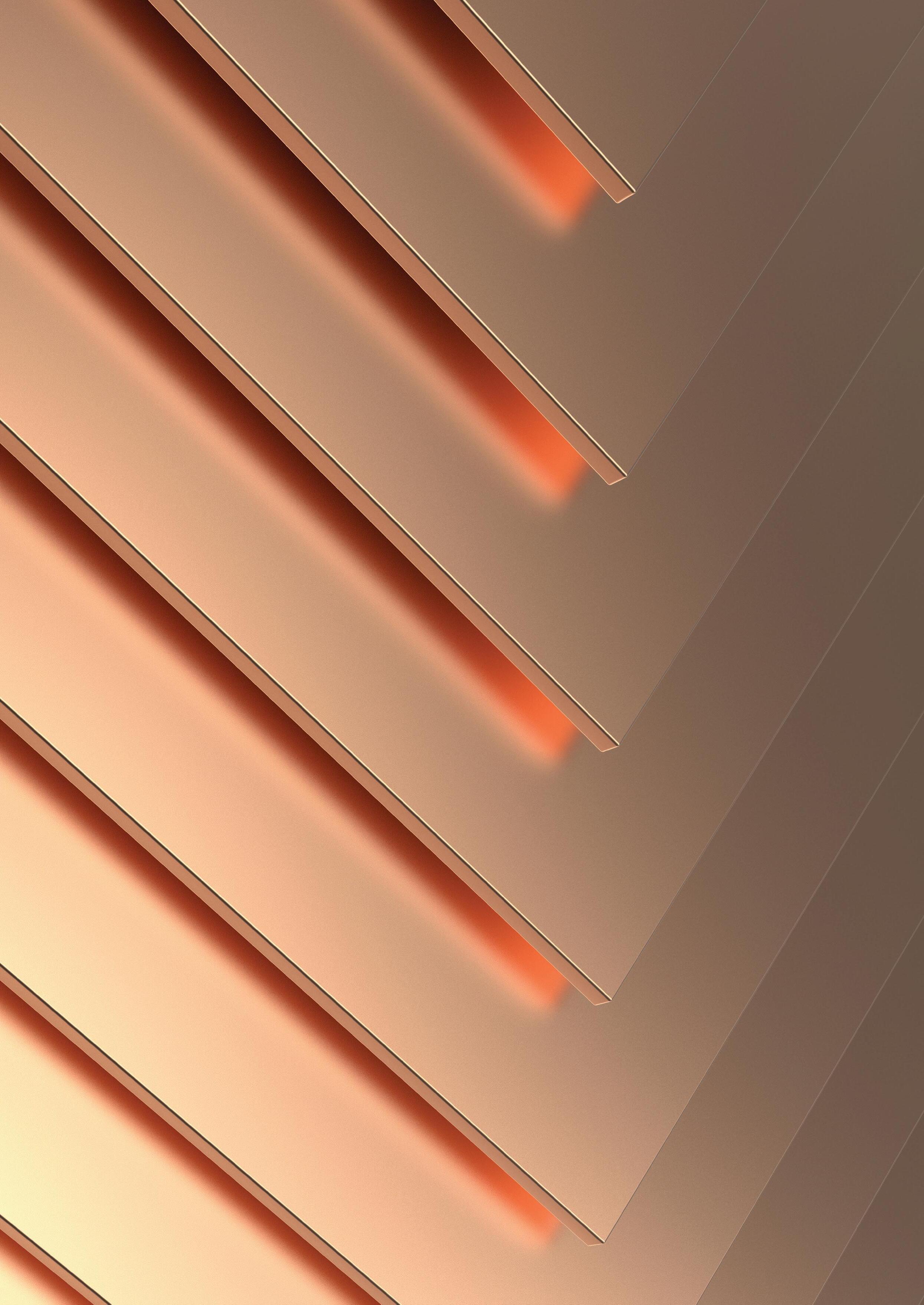
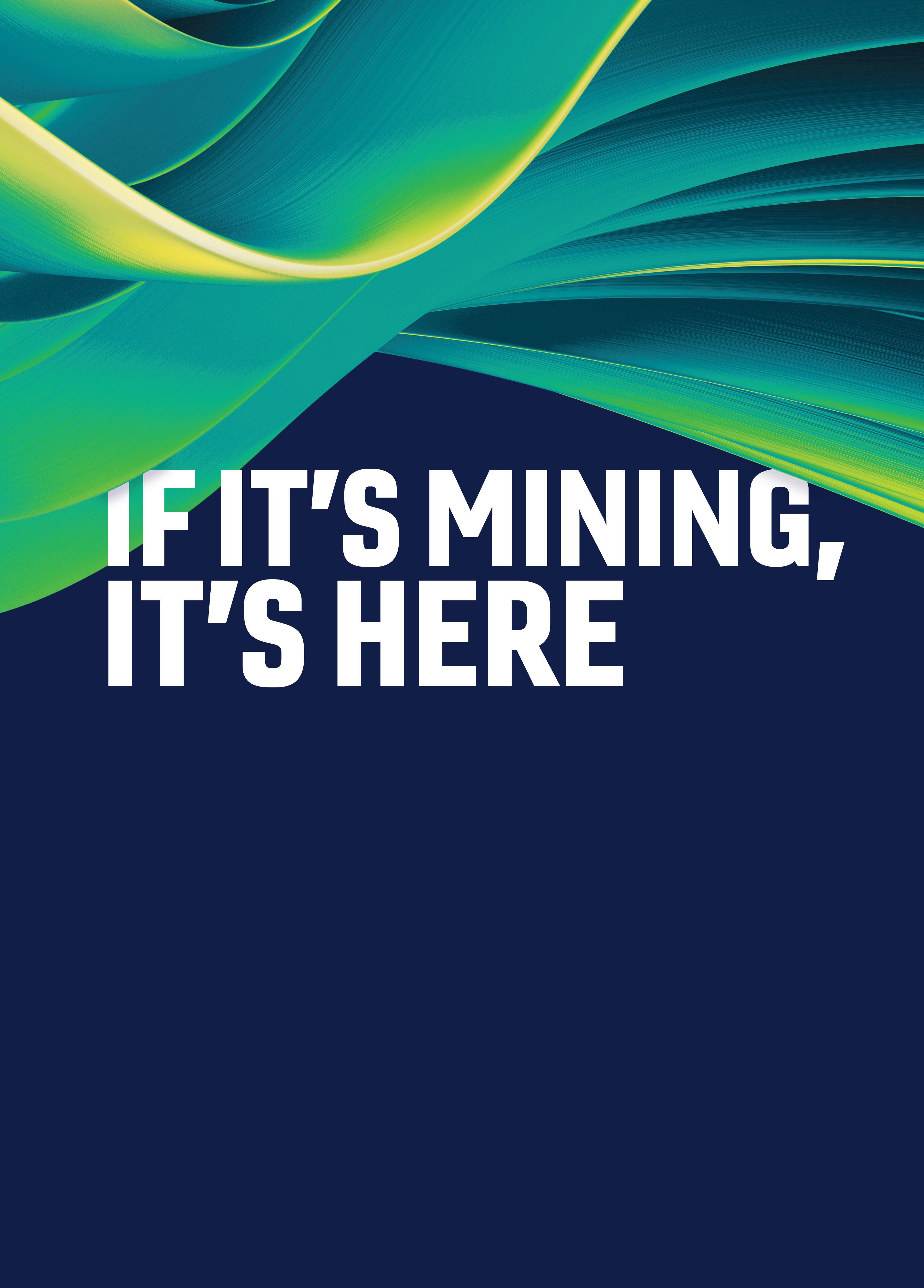
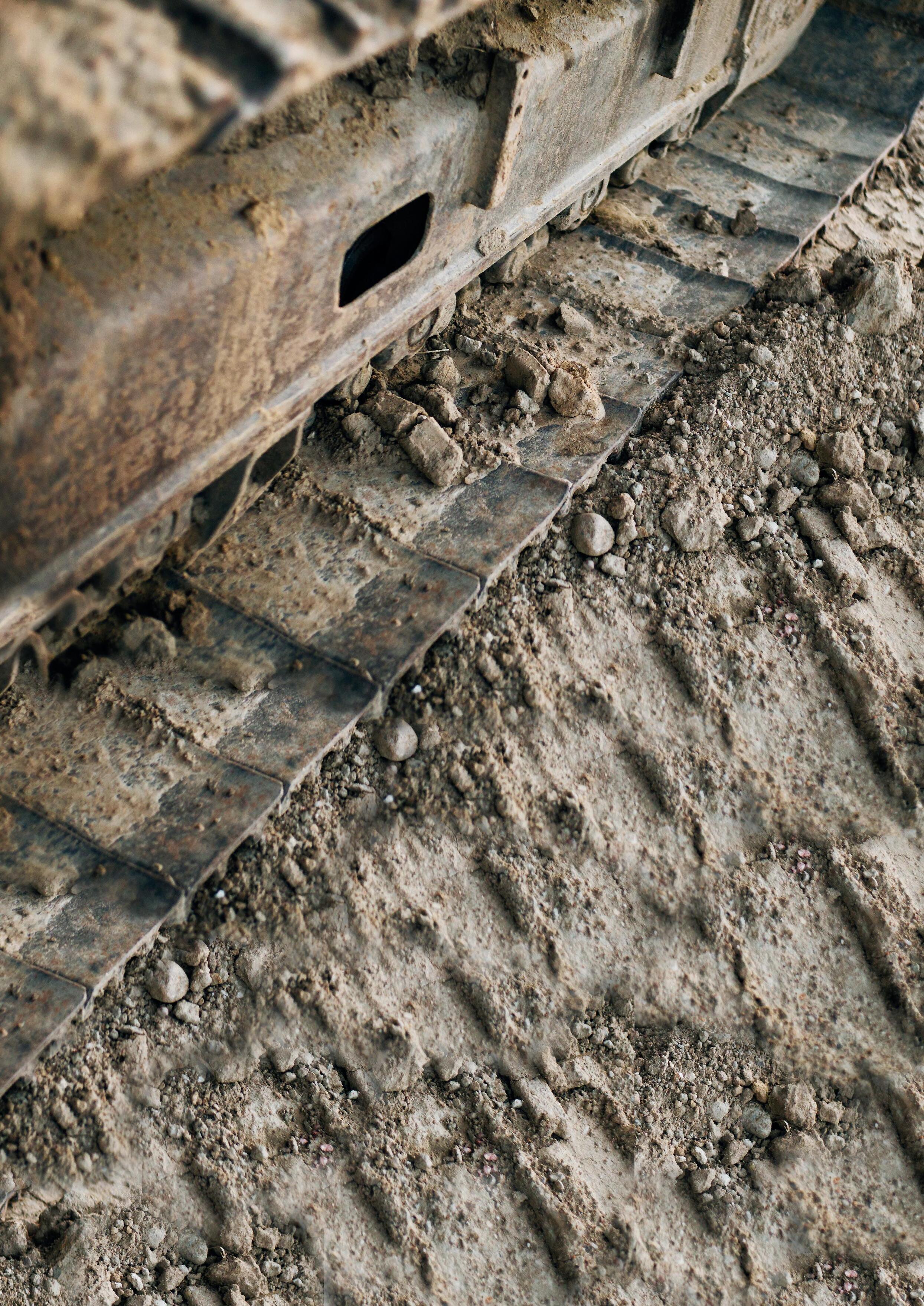
Giovanni Treleani, BS Track, presents the critical role of track shoes in the mining industry by reviewing some key features, as well as global production trends.
In the mining industry, track shoes play a crucial role in moving heavy machinery – such as bulldozers, excavators, loaders, and drilling machineries. These machines often operate in harsh conditions, including rough terrain, abrasive materials, and extreme temperatures. Track shoes are essential components of tracked vehicles, providing traction, stability, and durability to navigate through challenging environments.
Key features of track shoes
Track shoes and undercarriage are critical components of mining machinery, enabling them to operate efficiently and safely in challenging environments. Investing in high-quality track shoes and proper maintenance can help maximise equipment uptime and productivity while minimising downtime and repair costs.
Material
Track shoes are typically made of high-strength steel or other durable materials capable of withstanding heavy loads and abrasive conditions. Some may also have reinforced designs or specialised coatings to enhance wear resistance.
Design
The design of track shoes varies depending on the specific application and terrain. For example, some track shoes feature deep treads or cleats to improve traction in muddy or rocky environments, while others may have a flatter profile for smoother surfaces.
Size and configuration
Track shoes come in various sizes and configurations to fit different types and sizes of tracked machinery. Larger track shoes are often used in mining equipment to distribute weight and reduce ground pressure, which helps prevent machinery sinking into soft ground.
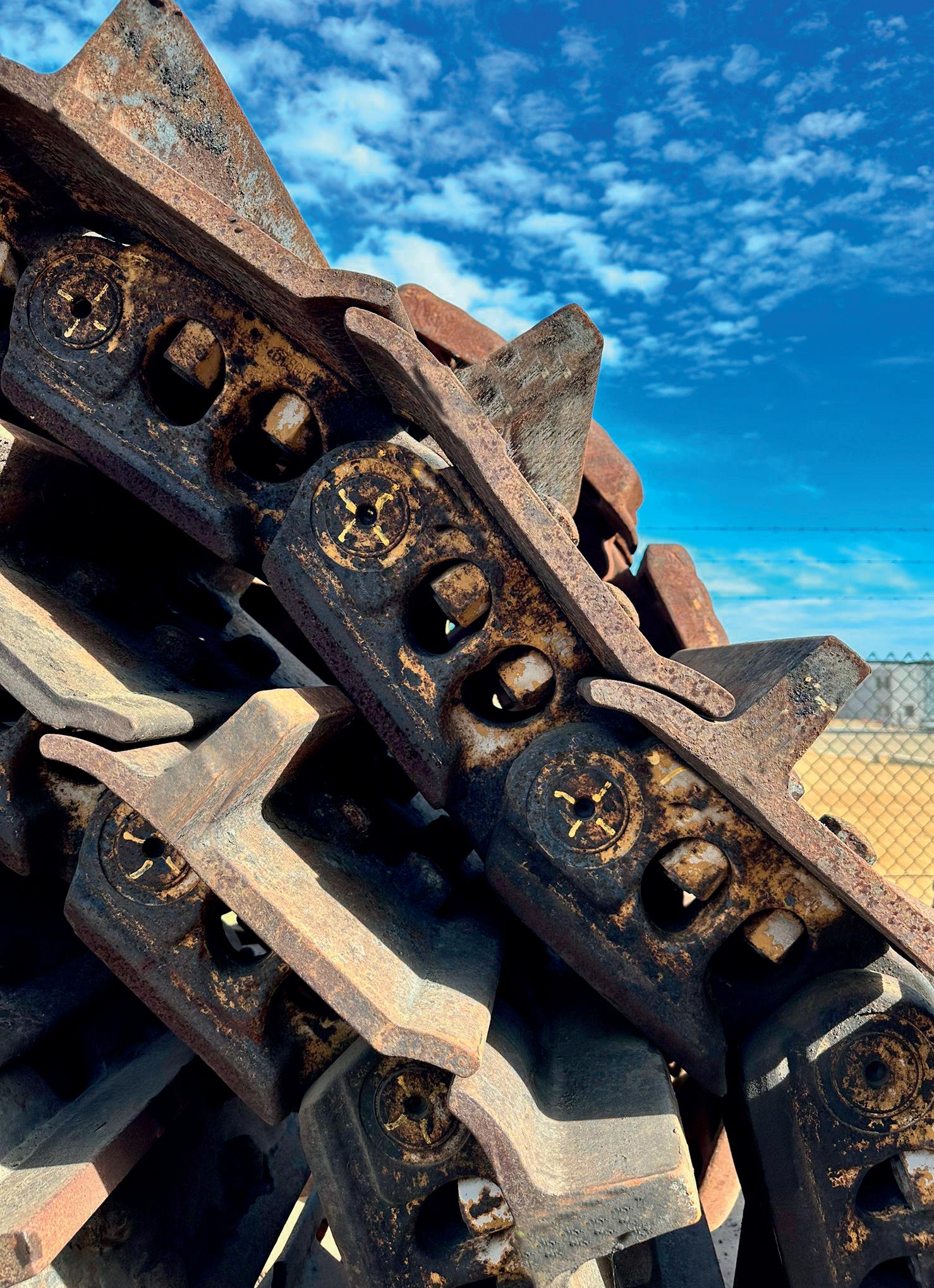
Maintenance
Proper maintenance of track shoes is essential to ensure optimal performance and longevity of mining equipment. This includes regular inspections for signs of wear or damage, timely replacement of worn-out track shoes, and lubrication of moving parts to prevent corrosion and friction.
Specialised applications
In addition to standard track shoes, some mining operations may require specialised types of track shoes, such as those designed for specific types of terrain (e.g. desert, permafrost, etc.) or for use in extreme conditions (e.g. high temperatures, corrosive environments, etc.).
Undercarriage performance in the mining industry is crucial
Undercarriage performance is of fundamental importance in the mining industry due to its impact on equipment stability, terrain adaptability, wear resistance, fuel efficiency, uptime, safety, and asset longevity. Mining companies must prioritise the maintenance and upkeep of undercarriage components to ensure the reliable and efficient operation of their equipment in the demanding conditions of mining environments.
Heavy load support
Mining equipment carries substantial loads, and the undercarriage bears the brunt of this weight. A robust undercarriage design ensures that the machine remains stable and can navigate through rough terrain without the risk of tipping over or becoming stuck.
Terrain adaptability
Mining operations can be found in a range of diverse environments – from rocky landscapes to muddy terrains. An undercarriage’s ability to adapt to different terrains is critical for maintaining traction and manoeuvrability. This adaptability ensures that mining equipment can operate efficiently across various work sites.
Resistance to abrasion and wear
Mining environments are notoriously abrasive, with rocks, gravel, and other debris causing rapid wear on equipment. The undercarriage components – such as tracks, rollers, and sprockets – must be highly durable and resistant to abrasion to withstand the harsh conditions encountered in mining operations.
Optimised fuel efficiency
A well-maintained undercarriage contributes to optimal fuel efficiency by reducing rolling resistance and ensuring smooth operation. Minimising friction between the undercarriage components and the ground reduces the amount of power required to propel the machine, ultimately lowering fuel consumption and operating costs.
Prevention of downtime
Equipment downtime is costly in the mining industry, where every hour of lost productivity translates to significant
Figure 1. The undercarriage must be able to operate and perform a large dozer with a weight of up to 110 000 kg, where downtime is often simply not taken into account.

SMARTER IN-PIT SOLUTIONS
For over 45 years, we have successfully provided pioneering Sizer technology to many industries worldwide. Our tailored mobile, semi-mobile and fixed Sizer stations as well as our latest in-pit innovations, are reliable and efficient answers to reduce the complexity of today’s modern mining challenges.
As a turnkey provider, we have the specialist knowledge and equipment to offer comprehensive services and support. From conceptual planning and design through to manufacture, installation and aftersales service. We are your partner throughout your sustainable journey.
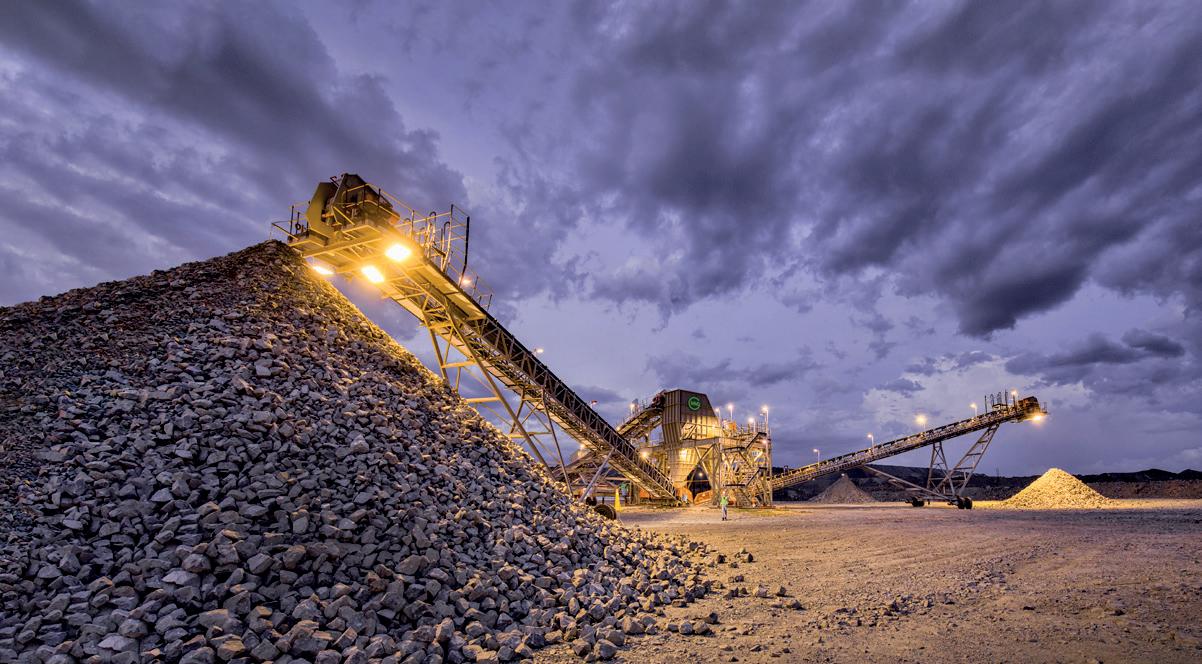
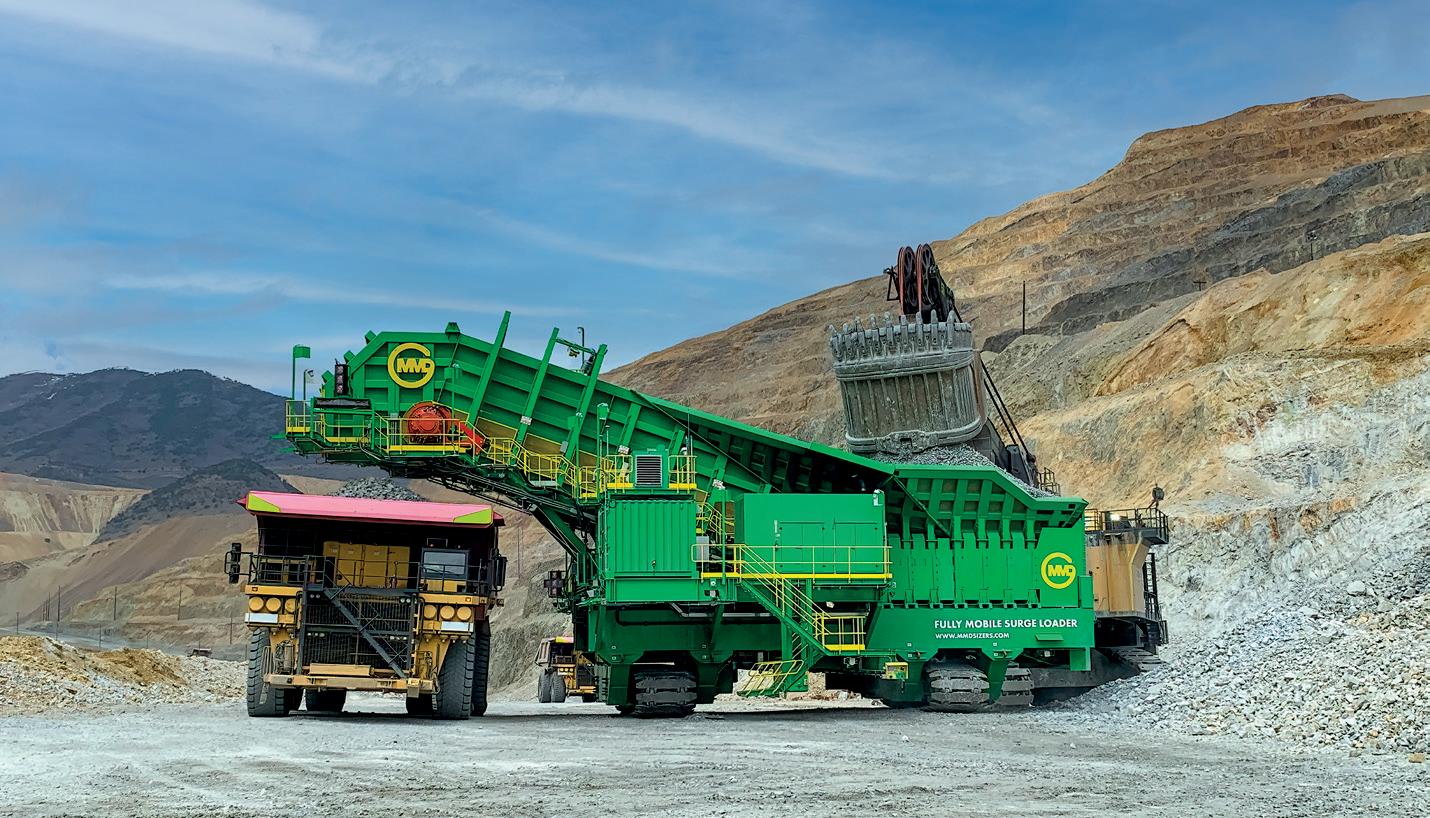
MMD Fully Mobile Surge Loader™
MMD Bulk Ore Sorting
revenue losses. A poorly performing undercarriage increases the risk of breakdowns and unplanned maintenance, leading to costly downtime and delays in production.
Safety
A reliable undercarriage is essential for ensuring the safety of mining personnel. Equipment instability due to


undercarriage failure can result in accidents, injuries, or even fatalities. By maintaining the integrity and performance of the undercarriage, mining companies can create safer working environments for their employees.
Asset longevity
Mining equipment represents a substantial investment for companies, and maximising the lifespan of these assets is crucial for achieving a favourable return on investment. A well-maintained undercarriage extends the lifespan of mining equipment by reducing the frequency of component replacements and major repairs.
Diving a little deeper
While other undercarriage components – such as rollers, idlers, sprockets, and track frames – are also essential, the track shoes stand out for their direct impact on traction, stability, load distribution, wear resistance, terrain adaptability, and propulsion, the key factors that determine the performance and productivity of mining equipment in challenging operating environments.
Traction and stability
Track shoes provide the primary contact between the machine and the ground, offering traction and stability essential for navigating through challenging terrain common in mining environments. Without adequate traction, the equipment may struggle to maintain stability or move efficiently, leading to decreased productivity and increased safety risks.
Load distribution
Tracks distribute the weight of the machine over a larger surface area, reducing ground pressure and minimising soil compaction. Proper load distribution is critical for preserving the integrity of the ground, especially in environmentally sensitive areas where soil disturbance must be minimised.
Wear resistance
Tracks are subjected to significant wear and tear in mining operations due to constant movement over abrasive surfaces like rocks, gravel, and debris. Therefore, they must be made from durable materials and designed to withstand the harsh conditions encountered in mining environments to minimise downtime and maintenance costs.
Terrain adaptability
Tracks come in various designs and configurations to suit different terrains and operating conditions. Whether the terrain is muddy, rocky, or uneven, tracks must adapt to provide optimal traction and manoeuvrability, allowing mining equipment to operate efficiently across diverse work sites.
Drive and propulsion
In tracked machinery, tracks transmit power from the machine’s engine to the ground, propelling it forward, backward, or enabling it to turn. The effectiveness of the drive system depends on the condition and performance of
Figure 2. Leading companies provide a complete list of mechanical tests performed in their laboratories.
Figure 3. The profiles can have different shapes and thicknesses for perfect field application.
the tracks, making them integral to the overall functionality of the equipment.
Global production
Track shoes for heavy machinery, including those used in the mining industry, are manufactured by specialised companies around the world. The manufacturing process typically involves precision engineering, high-quality materials, and advanced fabrication techniques to ensure durability and performance in demanding operating environments. Here are some regions and countries where track shoes are commonly manufactured:
USA
Several companies in the US specialise in manufacturing track shoes for heavy equipment used in industries like mining, construction, and agriculture. States such as Illinois, Wisconsin, and Pennsylvania are home to manufacturers with expertise in producing high-quality track shoes.
Europe
Countries like Germany, Italy, and the UK have a strong manufacturing presence in the heavy machinery sector, including the production of track shoes. European manufacturers are known for their advanced engineering capabilities and emphasis on quality and innovation. For example, BS Track, one of the most recent manufacturers to enter this market, has established its operations in Turkey, and will serve the construction, quarrying, and mining market at a global level with its complete range of products.
China
China is a significant hub for heavy equipment manufacturing, including track shoes. Many Chinese companies produce track shoes for both domestic and international markets.
Japan
Japanese manufacturers are renowned for their precision engineering and high-quality products. Some Japanese companies specialise in producing track shoes for heavy machinery, meeting stringent quality standards for durability and performance.
South Korea
South Korea is another key player in the heavy machinery industry, with companies manufacturing track shoes for various types of construction and mining equipment. South Korean manufacturers are known for their technological advancements and competitive pricing.
India
India has a growing presence in the manufacturing of heavy equipment components, including track shoes. Indian companies often cater to both domestic and international markets, offering a wide range of track shoe options for different applications.
Other regions
Track shoes are also manufactured in other regions, including Australia, Brazil, and Russia, among others. These countries may have companies specialising in the production of track shoes to serve local industries or export markets and are, in most cases, branches from the most notable international companies from the same sector.
Conclusion
Track shoes are vital components in the mining industry, integral to the performance and reliability of heavy machinery – such as bulldozers, excavators, and loaders. Made from high-strength materials and designed to withstand harsh conditions, track shoes provide essential traction, stability, and durability, enabling equipment to operate efficiently across varied and challenging terrains. Proper maintenance and specialised designs further enhance their performance, ensuring safety, fuel efficiency, and minimal downtime.
The global manufacturing landscape for track shoes includes notable hubs in the US, Europe, China, Japan, South Korea, and India, each contributing to the innovation and quality of these critical components.
Ultimately, investing in high-quality track shoes and maintaining the undercarriage systems are crucial for maximising the productivity, longevity, and safety of mining operations.
Global
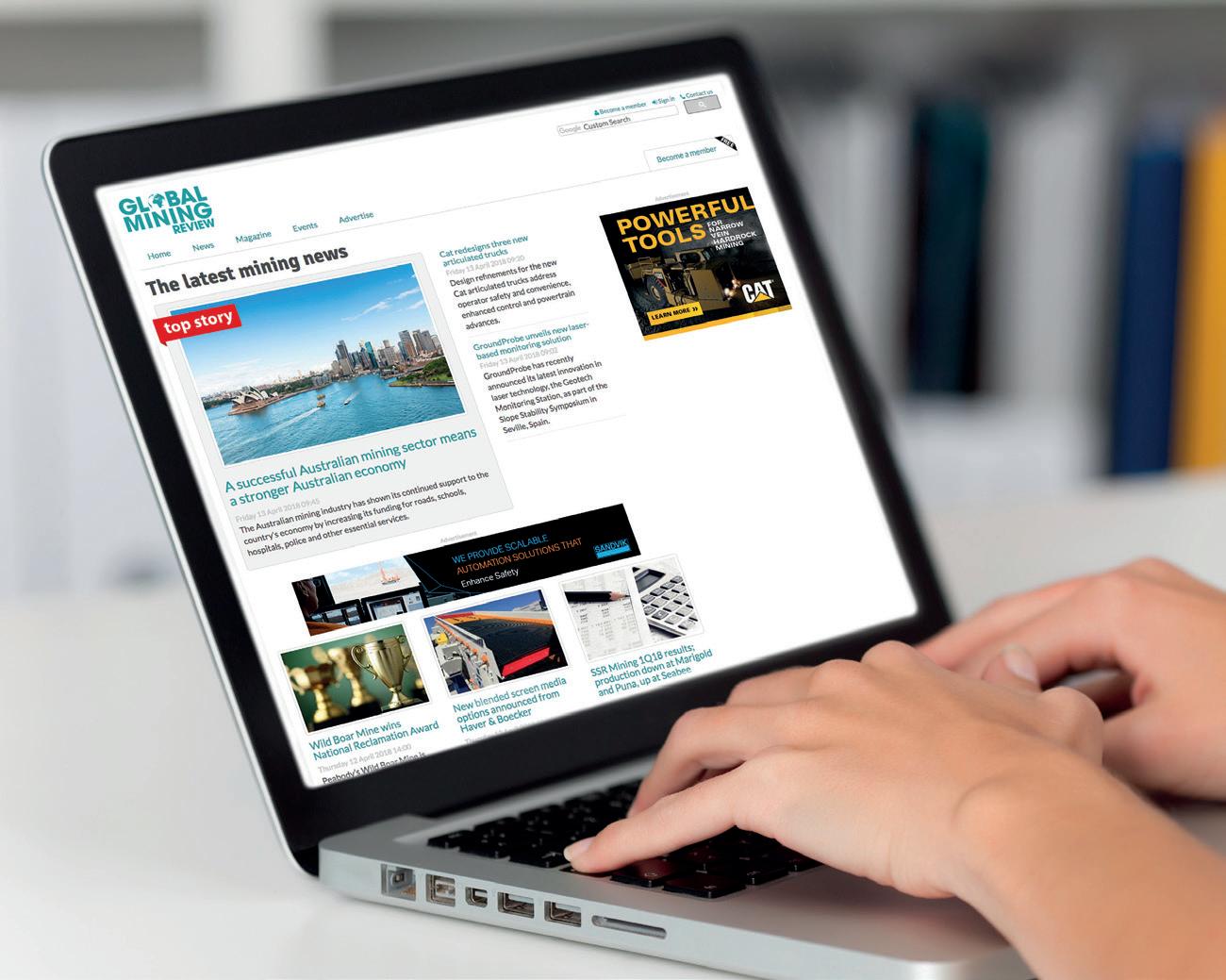
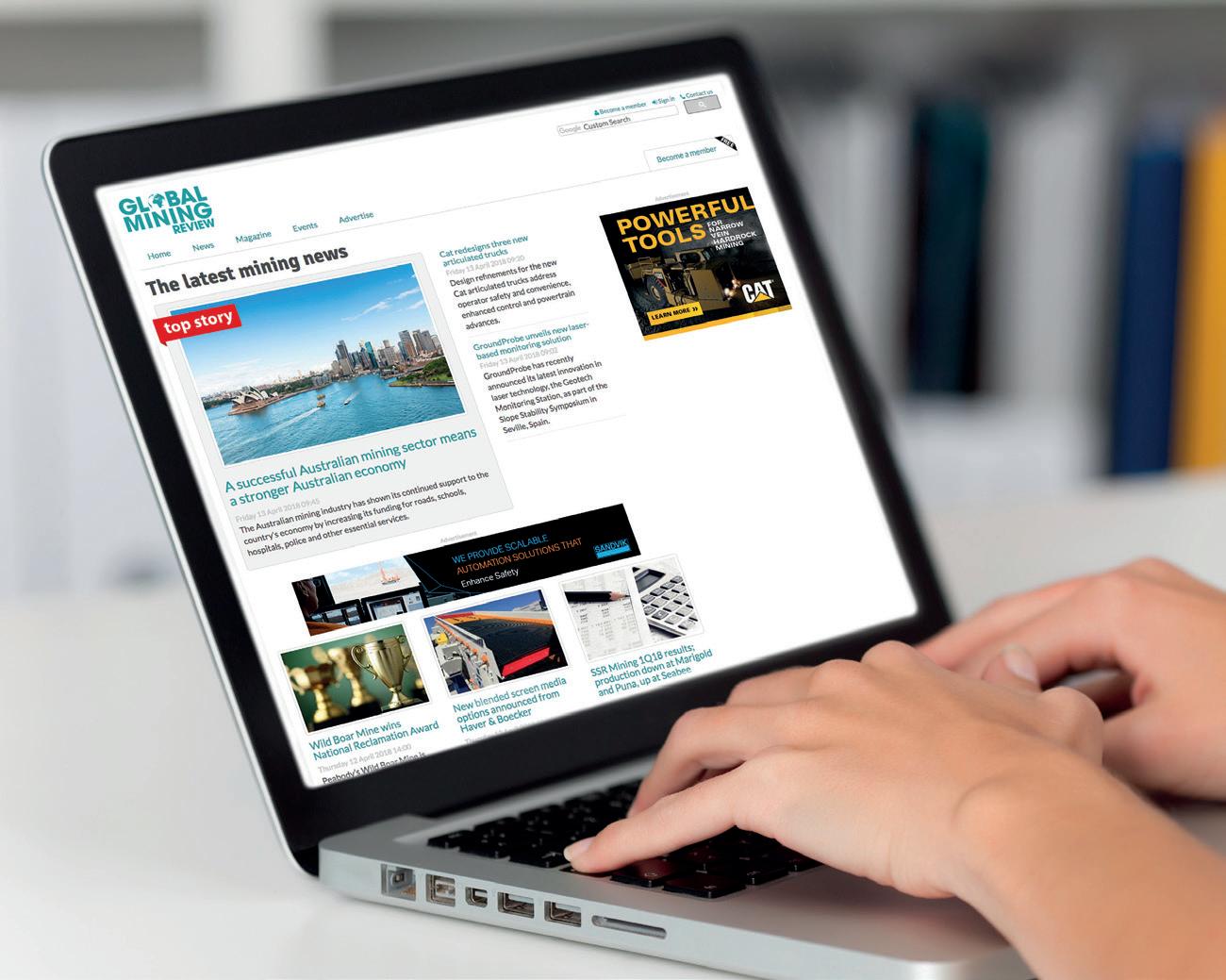
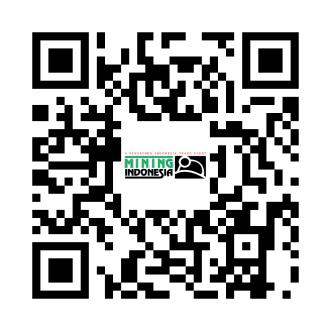
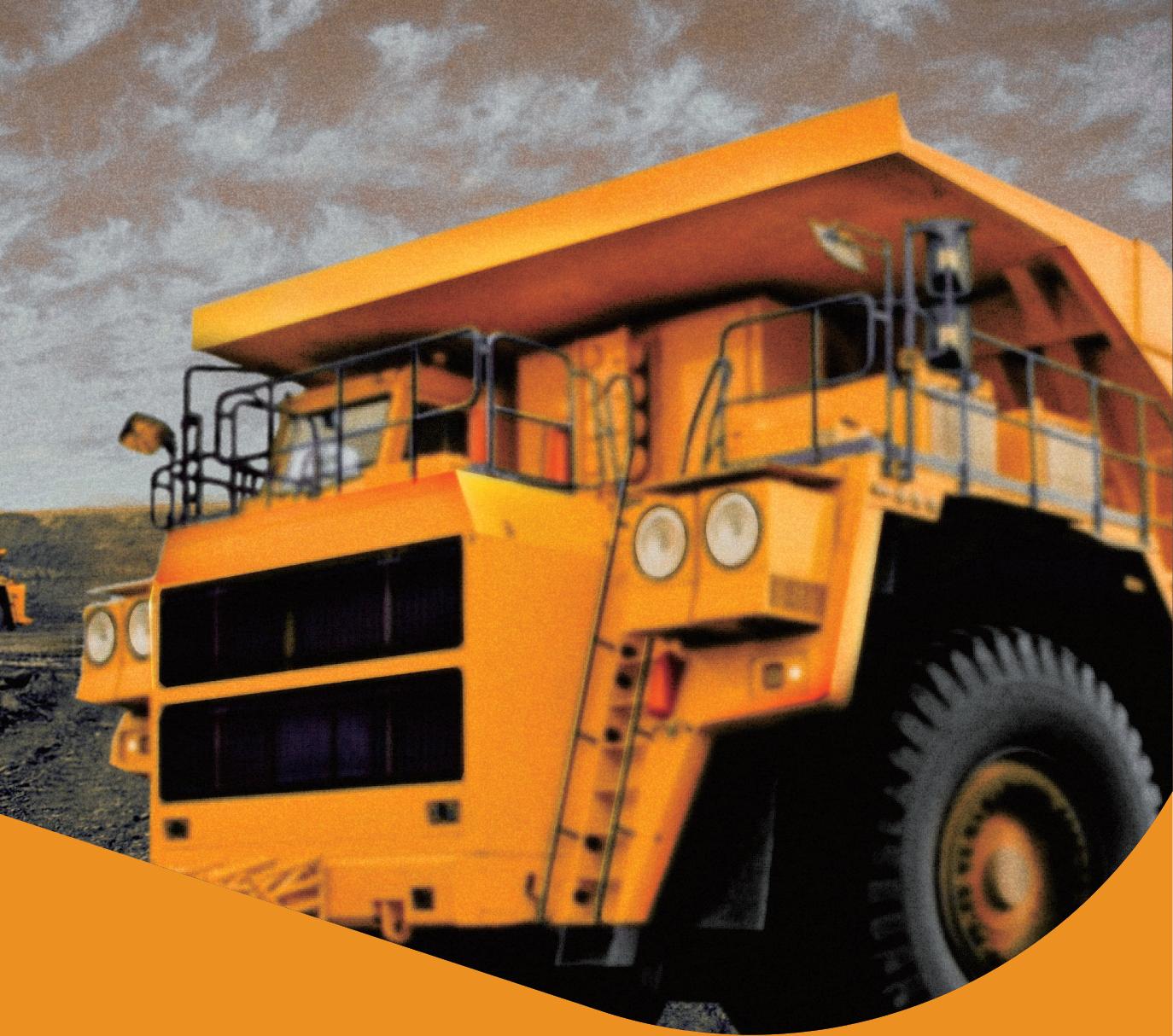
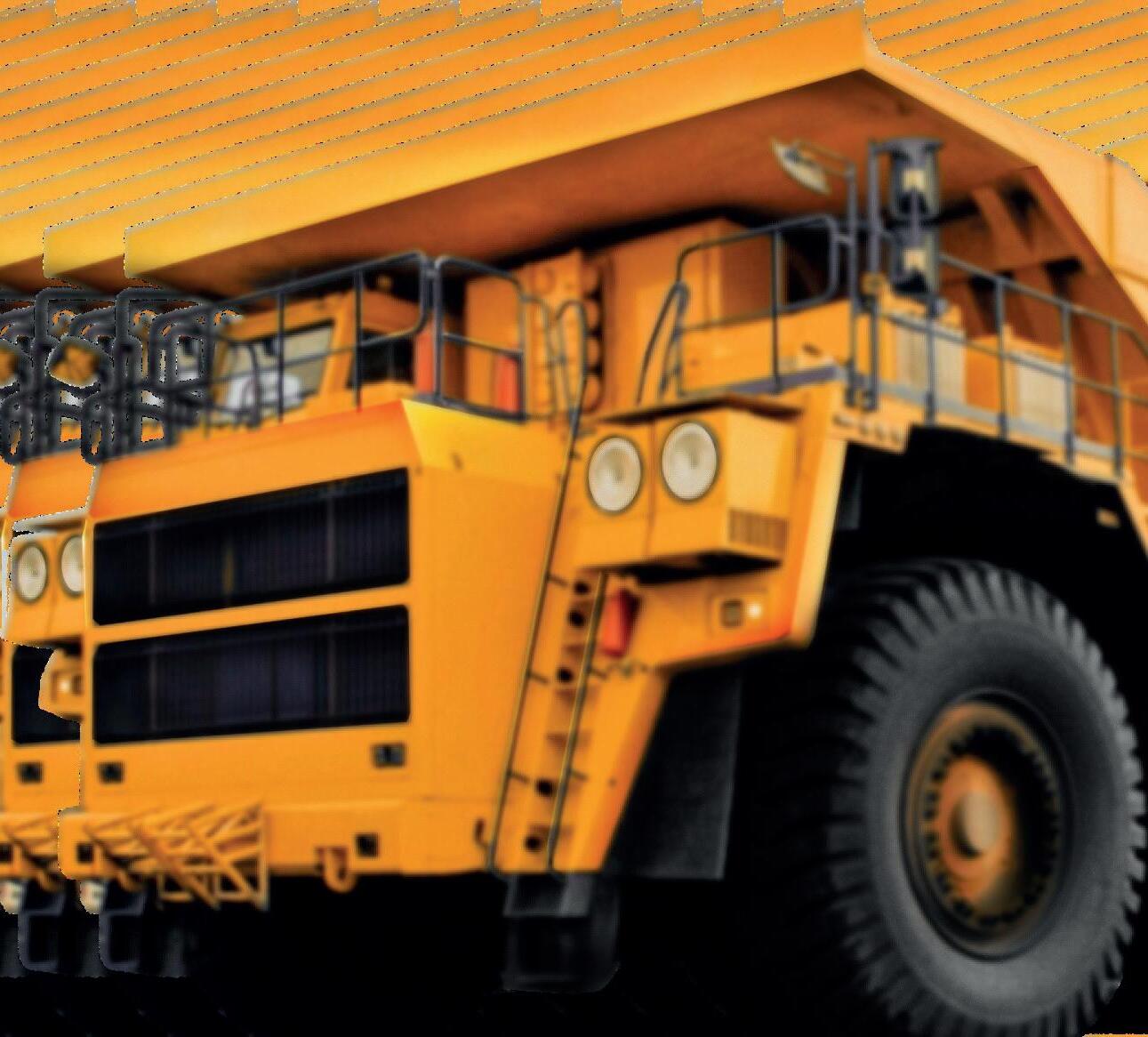

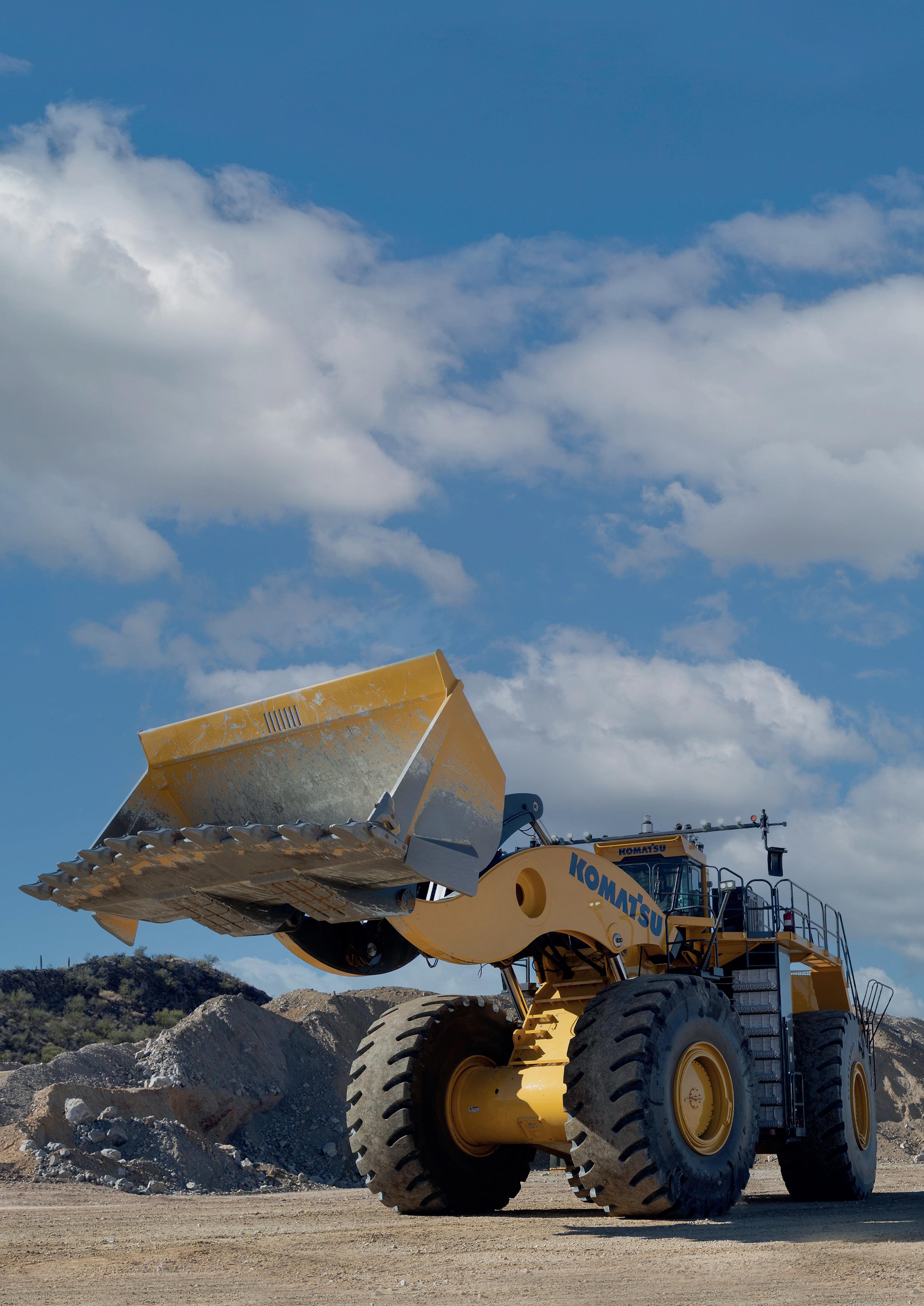
Michael Fleet, Komatsu, USA, outlines the latest loading innovations that can help promote sustainability.
In today’s world, surface mining operations are looking to prioritise being good stewards of the environment. Mining companies that ignore sustainability as a top concern expose themselves to big risks. Overlooking the environmental impact of their surface mining operations can result in regulatory fines, local community backlash, and damage to the company’s reputation.
Of course, it is a huge challenge to balance sustainability and productivity goals. Companies need to produce minerals while doing their best to address environmental concerns.
Like other traditional mining equipment, wheel loaders can be challenging when striking that balance. These immense machines
Figure 1. Wheel loaders and bucket loading technology have advanced and evolved over the years, making loading much more efficient, with fewer emissions.
can be highly productive in moving material, yet older models may produce more CO2 while burning more fuel. The good news is that wheel loader design, technology, and other industry innovations have significantly evolved. Monitoring machine data, telematics, and autonomous and semi-autonomous functions have empowered more efficient operational processes.
Put it all together, and the industry is in the midst of a rapid evolution of hybrid drive wheel loaders. These machines have been designed to facilitate sustainability in mining operations beyond what they were capable of just a few short years ago.
Advancements in haulage wheel loaders
When looking at the most influential sustainability-related innovations for wheel loaders, several factors stand out: regenerative SR hybrid electric driveline, semi-autonomous functions, remote data monitoring, and advancements in operator interface technology are at the forefront.
SR hybrid electric driveline
The electric drive, which R.G. LeTourneau pioneered, is one of those innovations. Electric drive technology was improved in the late 1990s when switched reluctance (SR) technology was first introduced on hybrid wheel loaders.
Through decades of refinements and improvements, some of today’s biggest wheel loaders use a hybrid electric drive. Komatsu’s SR hybrid electric technology has progressed to become an integral technology that powers productivity at mines and construction sites worldwide. Its engineers continue to push the envelope to design for more efficiency out of its SR hybrid electric drive surface loaders. These latest innovations in electric drive technology, which include regenerative capabilities and a unique energy storage system, are engineered to help surface mines achieve their sustainability targets.
Because the Komatsu SR system was specifically designed to improve the efficiencies of mining machines (rather than adopt drives from other applications), the company has developed a system to capture and manage braking horsepower that would normally be lost.
For instance, historically, when a typical electric drive machine brakes, the converted energy from the inertia of the rotating wheels is converted to heat. During electrical
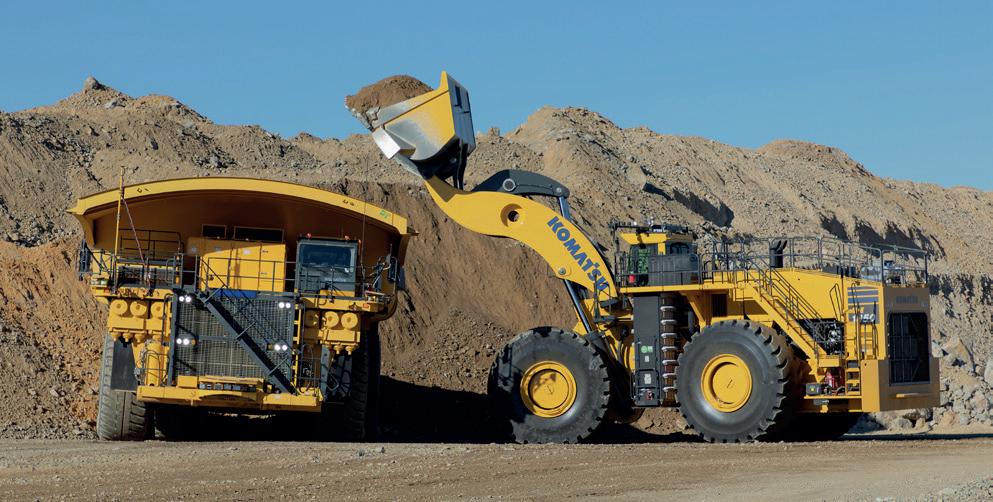
braking (dynamic or retarding), the wheel motors produce power. Komatsu has developed a system that captures the braking energy in the form of an SR device that functions as a motor and a generator.
This device is called a Kinetic Energy Storage System (KESS) unit. During electrical braking, the converted energy is fed into the KESS unit and it acts as a motor. The KESS unit takes the available power and begins to spin at a high rate of speed. As subsequent functions of the loader take place, the KESS unit converts to a generator, providing supplemental electrical horsepower to assist the diesel engine and SR generator in supplying the power needs of the loader.
Combining the hybrid drive system and the KESS unit allows the hydraulic and electrical drive systems to receive full power demand.
With this system, there has been up to 45% less fuel consumption with SR hybrid electric-drive machines than comparably sized mechanical-drive wheel loaders, and loading cycles can become more efficient. Because it is highly productive, the SR hybrid electric drive is designed to strike a productivity-sustainability balance.
Semi-autonomous, remote data monitoring, and operator interface innovations
Automation in wheel loaders continues to evolve, bringing tangible productivity and efficiency benefits. Integrated machine technology provides operators with instantaneous feedback, empowering more efficient loading. The HMI interface on Komatsu wheel loaders also delivers text and visual alerts to operators if they need to take corrective action.
Komatsu’s LINCS II network control system, integrated into its wheel loaders, monitors over 700 data points. It provides virtually instant, real-time feedback, and vital statistics. These metrics include bucket height and angle, total tonnes moved, fuel burn, steering and dump angle, cycle time breakdown, machine health, and more.
Communicating all of these factors to operators can help them adjust to conditions that allow for more efficient loading to promote reductions in fuel burn. This data can also help new or underperforming operators improve their performance. For instance, data from the LINCS system may show an operator spending too much time in the dig space, so tips and guidance can be provided for faster digging.
As an added benefit, personnel can view health monitoring data and other diagnostics remotely via a smartphone or digital device.
Innovations in bucket payload technologies
Bucket payload management is a crucial operational factor that impacts the efficiency of each loading cycle.
Maximising each load can help a mine become more sustainable, as moving more material with each load-and-haul cycle means fewer cycles, which can help decrease overall fuel usage.
Even small improvements in bucket loading can promote tremendous productivity and sustainability benefits. These solutions can help an operation hit the ‘sweet spot’ in loading, realising efficiencies that result in
Figure 2. Today’s loading bucket loading technology optimises efficiency with every haul cycle, which can help mines become more sustainable.
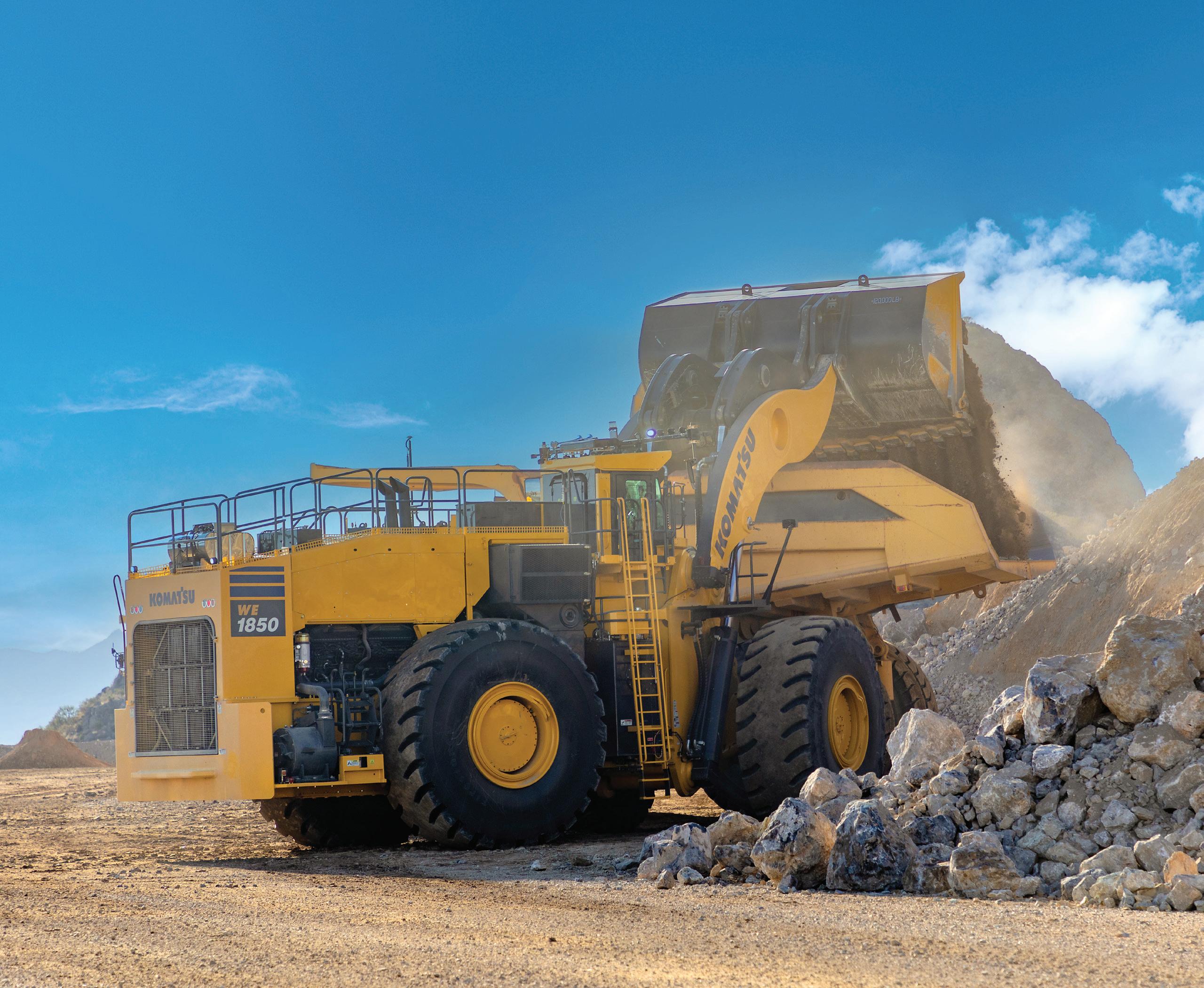
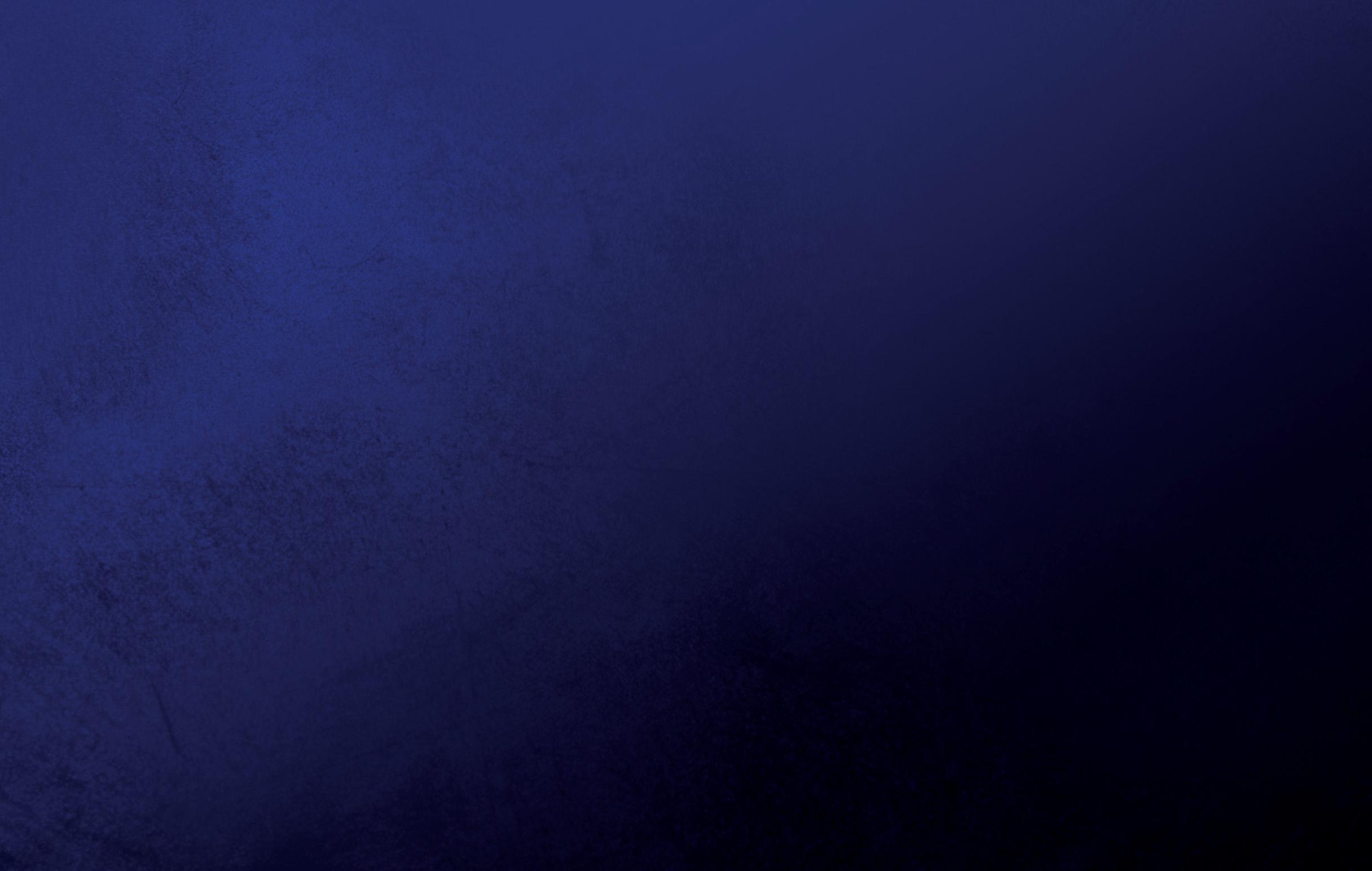
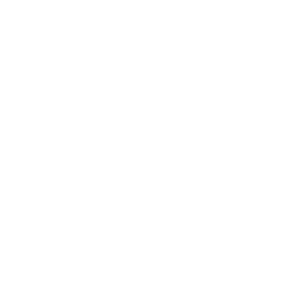
sustainability benefits, such as reductions in fuel consumption and optimised loading.
For instance, Komatsu’s Modular Mining Argus Wheel Loader Monitoring System – an optional aftermarket solution for its machines – can deliver a 3% or more productivity improvement in the total volume of material moved per load cycle.
At the heart of any bucket payload system is data. The actionable insights from data offer many operational benefits. For instance, access to bucket payload data can provide a more holistic view of a mine’s operational performance. It also helps operators do a better job on the surface mine site, while empowering those back at the control centre with robust information to make more informed decisions in real time.
Most payload monitoring systems deliver a host of cycle-by-cycle information that is designed to help enhance a mine’s efficiency. This usually includes bucket payload, cycle time, cycle component time (fill, tram, dump, return, spot), hang time, wait on truck time, time usage modelling, and more. Once all of this information can be accessed, user-friendly data analytics can help operations.
Data analytics generated by a bucket payload solution can have a direct impact on an operation and help companies:
n Control payload range variance and standard deviation.
n Narrow down the payload distribution curve and shift it to targets or the appropriate operating limits for the OEM.
n Empower operators to hit the maximum payload mark while promoting safety and sustainability.
n See how different areas of a mine are connected for a more holistic view and informed operational decisions.
What all of these advancements mean for sustainability
When companies combine the technological advancements in wheel loaders and cutting-edge bucket management solutions, new ways of doing things emerge that can make mining processes more streamlined.
With machines and software communicating with each other, mining control centres can have access to comprehensive dashboards that allow companies to control bottlenecks and make processes more efficient, using the interconnected data and factors with every decision.
With all of these machine advancements and bucket payload solutions, mining operations can become like a choreographed dance – equipment, operators, and the control centre in sync and harmony. The result is a sustainability-focused operation that still can achieve productivity goals while controlling costs.
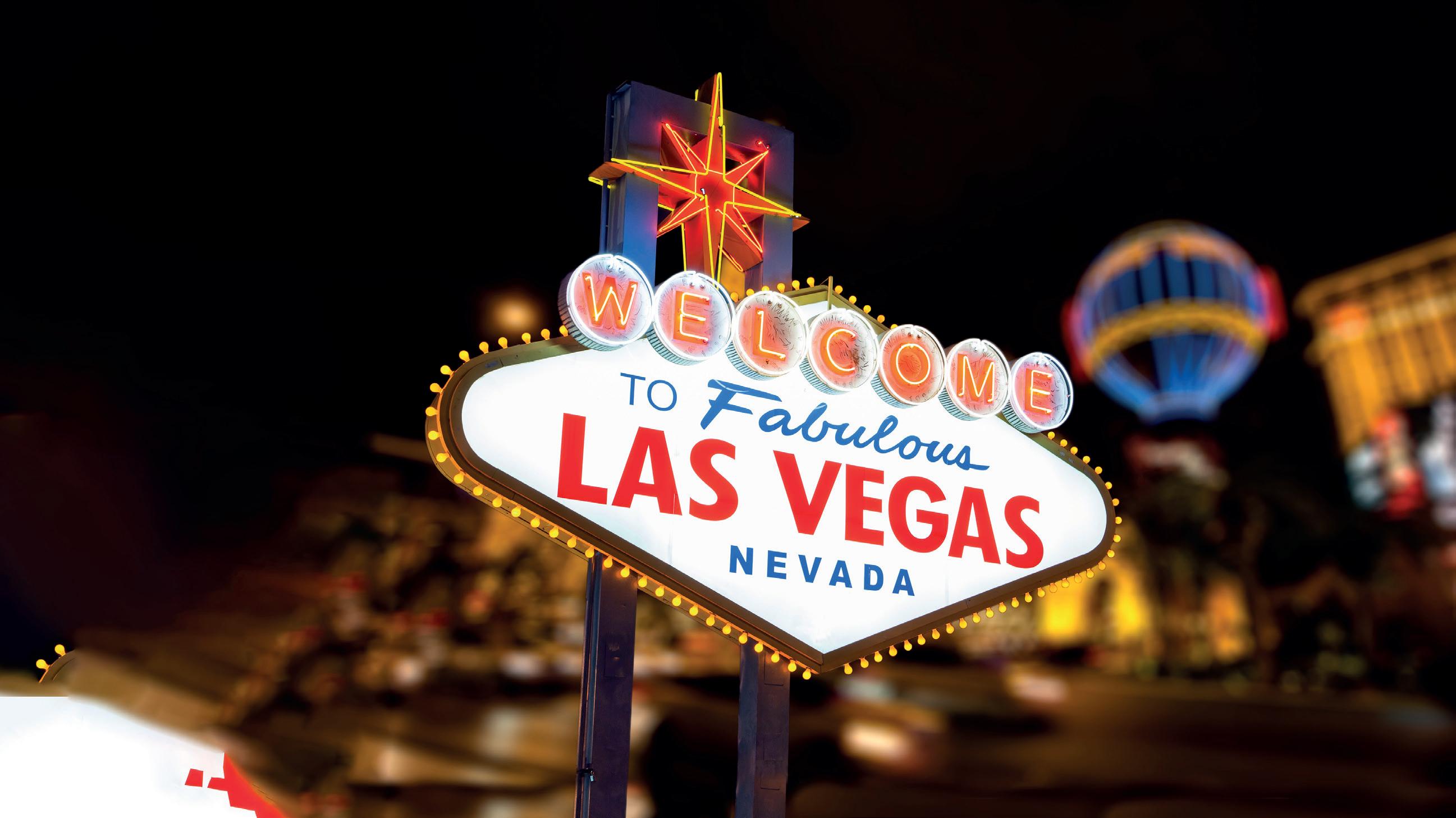
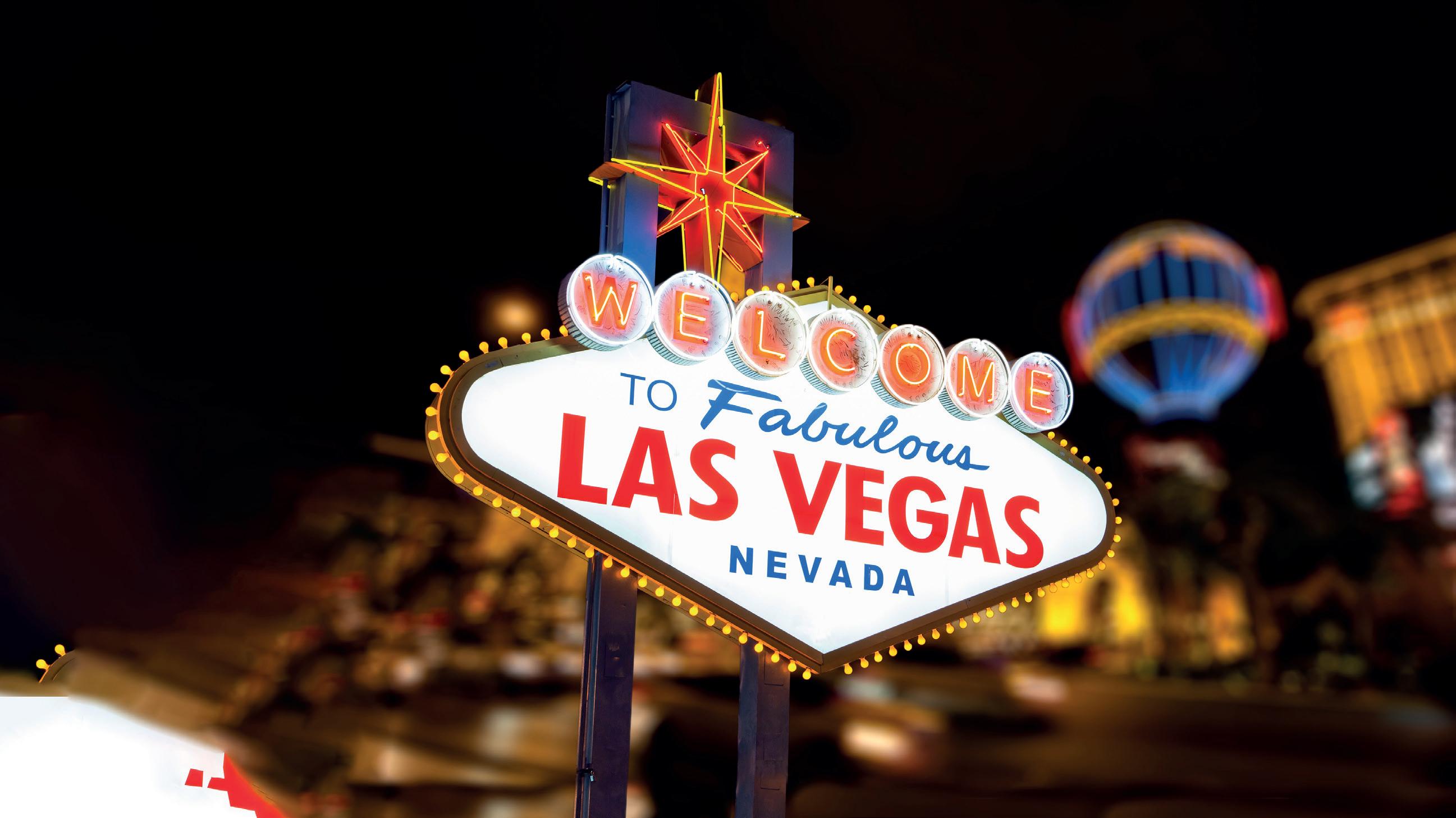
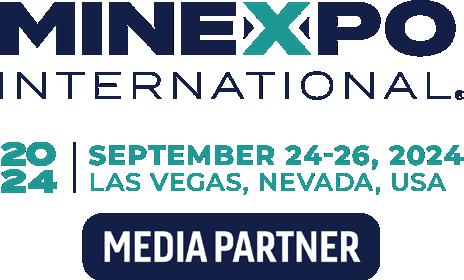
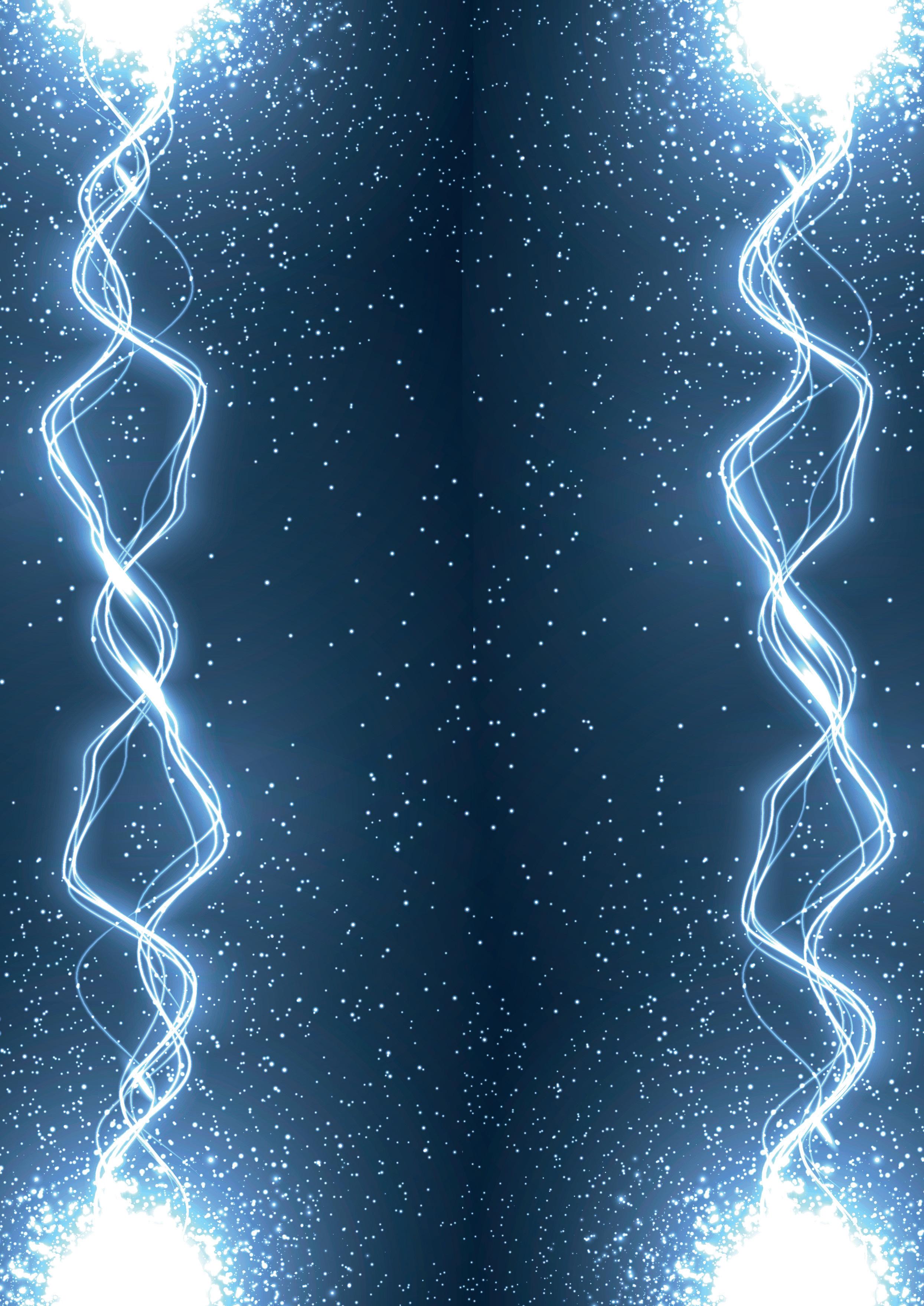
Nellaiappan Subbiah, Sandvik Mining and Rock Solutions, USA, explains why smart miners are saying goodbye to diesel and hello to electricity to revamp drilling, save costs, reduce maintenance interventions, and act more sustainably.
Mining, like every other sector, has a problem. Processes that have been well-grooved by decades of activity need to be re-engineered as mandates and ethics demand investments in sustainability and carbon emissions reductions. This demand does not brook negotiations. Without adherence to prevailing regulations, miners will lose their licences and permissions to operate. Therefore, whether they go into this willingly or unwillingly, miners have to change. And change is what is occurring everywhere across the big mining houses like BHP, Rio Tinto, and Glencore, but also at a panoply of smaller companies.
This need to change is seeing progressive miners of all sizes and specialisations make investments in automation, digitalisation, data analytics, and anything else that can aid their cause. However, where the rubber hits the road, or rather where the drill hits the seam, is the place to start. In drilling, the advent of a massive transition between diesel and electric is clear.
Why electric trumps diesel
Why this change? The simple answer is that for a host of reasons and in a host of ways, electricity beats diesel hands down. These reasons range from lower maintenance thresholds and extended motor lifespans to cooler running, reduced energy demands, and a hugely significant improvement in total cost of ownership (TCO) levels.
Going electric means the wholesale elimination of standard diesel components, such as filters, cooling packages, exhaust systems, and fuel tanks – all of which
carry a significant maintenance burden. Losing them means a lengthier lifespan for drilling products.
Moreover, a diesel engine is only about 30 – 35% efficient in terms of converting chemical energy into mechanical energy, whereas a high-voltage electric motor typically delivers 90 – 95% efficiency.
Electricity also beats diesel when it comes to lifespan. A diesel lifespan will have an expected life of about 20 000 hr, but the same-class horsepower electric motor will have a life of 80 000 – 100 000 hr. This effectively means that an organisation could avoid changing the prime mover throughout the lifetime of the asset itself. This is a huge advantage, especially in harsh and remote locations with extremes of weather, limited accessibility, or high altitudes.
A related improvement is an ability to seamlessly integrate settings controls for automatic drilling and adaptive drill features that optimise energy usage. Electric drilling often goes hand in hand with smart drilling, as miners tap into ways to remotely control and monitor drilling activities. Results are even better if electric drilling is integrated with business infrastructure and workflows, as organisations deploy intelligent energy management systems, automated engine update alerts, and optimised drilling settings.
The motor control cabinet or transformer does not need a lot of maintenance, compared to the complexity of a diesel engine with its exhaust system, fuel system, radiator, charger cooler, and air-intake filters. These and other items typically have high levels of wear and tear, and must be maintained by periodical interventions every 500 – 1000 hr. With an electric-powered machine, these interventions largely go away for what is calculated to be a total maintenance time saving of about 68% compared to diesel.
Safety is another advantage in favour of going electric. Sensors can more easily be deployed to monitor the speed and direction of the rotation of cable reels and the force on the cable. This means that an operator no longer needs to leave their cabin and take remedial actions and
information can be relayed to a remote-control room. More broadly, automation can also be tapped to minimise manual human intervention and lower cycle times between operations, as well as in maintaining minimum distances between cable routings to avoid electromagnetic interference, thus ensuring the design’s reliability and robustness.
Electrification also plays a role in the human factor: how are personnel in operations impacted by their work? Electric machines generate less noise, heat, vibration, and emissions than diesel machines, so operations not only become more environmentally-friendly, but they are also less exhausting for operators and maintenance personnel. The decreased service intervals of the aforementioned prime mover also mean less time is spent on maintenance, so stress and fatigue are reduced. The result is that drill and blast supervisors, or other personnel on the ground, can work in a less hazardous environment. Therefore, clearer thought processes and, ultimately, smarter decisions are evident.
Think carefully when managing change
Swapping out diesel for electricity is highly effective, but it should not be considered as a ‘slam dunk’ or quick win. Change must be managed, and smart miners are making gradual, measured shifts towards electric power and cutting emissions.
First, there is hardware modularity. By designing drills to accept different fuel sources, companies can ensure that original equipment investment is not squandered and there is no ‘rip and replace’ strategy needed.
Second, infrastructure needs to be considered. Organisations (or their providers or service centre partners) can replace diesel engines with electric prime movers that are connected to the mine grid, usually via a substation and trailing cable.
However, introducing electrified components brings challenges too. Layouts and form factors in circuitry and hardware design when converting a machine from diesel to electric are very different. It is also important to ensure that users are adequately trained and collect feedback to ascertain that they feel they are having a positive experience.
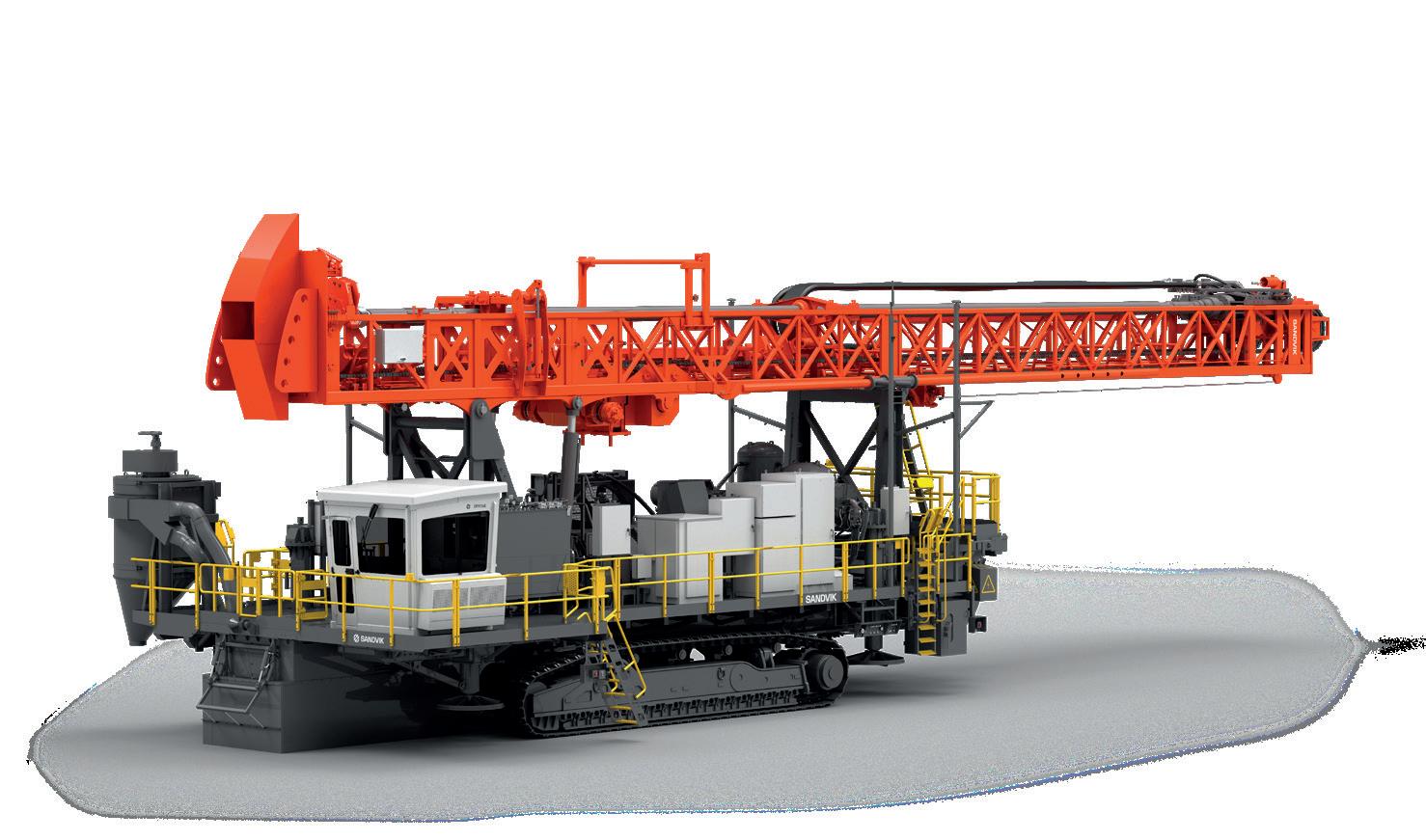
Making the transition and using ‘tailor-made’ equipment
For organisations with unique operational needs, adaptations can be made. Electric motor and diesel power packs should be interchangeable without affecting the machine frame, cab, mast, or
Figure 1. Sandvik DR416iE electric rotary blasthole drill.
Create a large footprint.
While leaving a small one.

Sandvik DR416iE
Ideal for iron ore and copper applications, with a hole diameter range of 270 to 406 millimeters (10.6 to 16 inches) and powered by a robust 1,044 kW (1,400 HP) electric power group designed to meet the demands of high-altitude applications. Sandvik DR416iE boasts a sophisticated electric system that incorporates a soft starter to help reduce the impact on the mine’s power grid, preventing disruptions to other equipment, while the multi-voltage and multi-frequency electric motor offers outstanding flexibility.
The DR416iE - Powering tomorrow, today. Go electric. Go Sandvik.
hydraulic system. Electrical power packs can replace diesel power packs, with changes only being needed for the cooler, plumbing, fans, etc.
In most transformations, it is not just the drill that is electrified, but also the shovel, dragline, or other equipment. However, many organisations will exist in a hybrid environment, combining diesel and electric equipment. Hence the importance of modularity – the ability to extract optimal usage from older equipment and integrate it with the modern aspects of the environment – is clear.
The future is bright
The electrification of what were primarily diesel-powered machines is just one aspect of how the drilling process is changing. Looked at holistically and in the long term, it may best be considered as an interim step. At some point in the future, mining operations could be powered by a blend of alternative and sustainable fuel sources, including batteries, hydrogen, biodiesel, and biogas sources.
However, even today, demand for electric drills is going up and Sandvik’s estimates suggest that these models will soon account for about a third of the total market with the scope to advance to perhaps half of the market in the mid-term. Sandvik’s experience is that a mixture of emissions concerns and related tax benefits
for miners are seeing many take a proactive stance and that this trend is inexorable.
Electric dreams
The advent of electrical drilling marks a radical transformation, but it is also important to have some patience and work through changes. Ground-based controls must still be maintained, because there are situations – such as the loading and unloading of cables, or dealing with some specific or unique obstacles in the field around the pattern – that require those controls.
And, as anyone who has experienced the operation of electric high-voltage electrified equipment will know, there is still a high potential for electromagnetic interference between different circuits. This means companies need to continue to put a lot of effort into making sure that the safety and reliability of the system are world-class.
However, any serious miner knows that radical steps need to be taken to stay relevant in a century that is being defined by attitudes towards power management. Drilling is just one example of how mining is moving away from old, dirty activities towards cleaner, smarter processes. It will be incumbent on everyone in the future of mining to work towards sustainability, reusability, and recycling. If those are watchwords, then the industry will be well-positioned to create a brighter future.

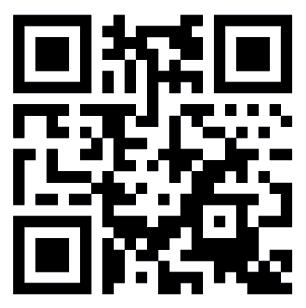

Matthias Stöhr and Nicolas Osswald, Herrenknecht AG Business Area Mining, Germany, consider how innovative technologies can ensure safer and more efficient excavation of ore passes and ventilation shafts in underground mines.
The innovative technology of the Boxhole Backreaming Machine (BBR) and Lining System has been developed by Herrenknecht for the economical and safe excavation of ore passes and ventilation shafts. It allows reaming and lining to be carried out in a single operation. The new technology prevents the collapse of the borehole in unstable rock after reaming and eliminates the rework that would otherwise be required. It also reduces the amount of activity at the production level during initial mine construction and development. The new technology enables mine owners to develop a safer and more efficient mine, resulting in an earlier start to production. A BBR and lowering unit is currently used at El Teniente mine in Chile, where around 300 m of shafts with a final diameter of 3 m were drilled and lined in very challenging geologies.
The BBR
The BBR is a novel, further development of the existing and proven Boxhole Boring Machine (BBM) technologies for creating small-diameter slot holes. Its technology is based on the principle of mechanised pipe jacking widely used in microtunnelling. Herrenknecht has adapted this process for vertical boxhole drilling in mines. In view of the harsh working conditions in underground mines, the safety, productivity, and mobility of the equipment were important design criteria. Proven technology, adapted to the requirements of the situation, has resulted in a machine that creates slot holes faster, safer, and more economically than comparable mechanised methods.
The BBR drills a pilot hole and reams it up to 3.6 m for shaft lengths up to 80 m. In combination with an optional lining lowering unit, shaft lining is carried out simultaneously while reaming.

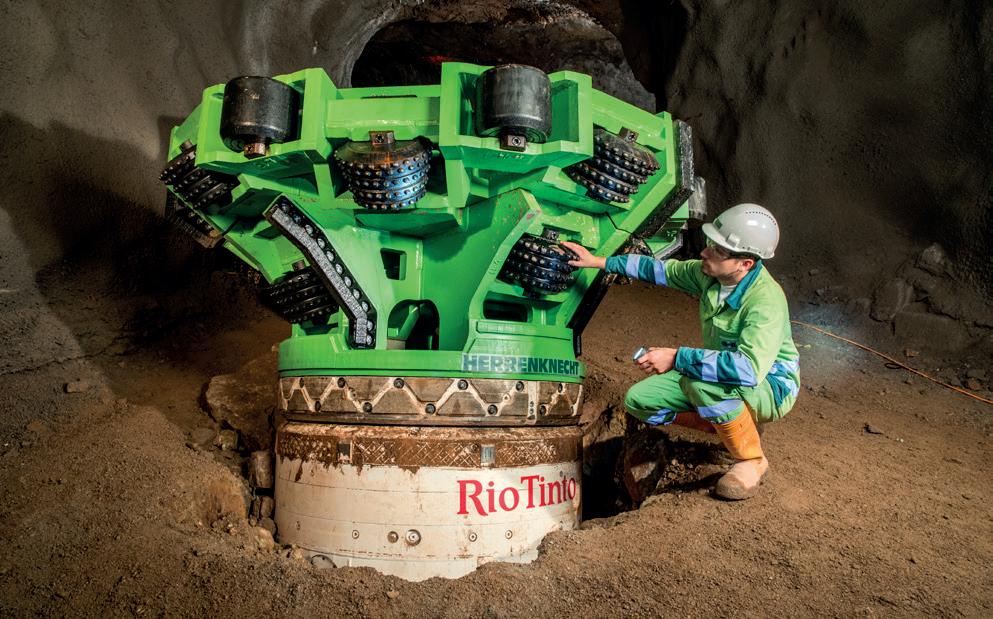

From a jacking frame, a boring unit at the head of the pipe string is pressed upward from the launch point. Additional thrust pipes are installed one after the other and pushed forward, thus increasing the drilling length. The thrust pipes transmit the thrust forces of the jacking frame to the boring unit and handle the controlled removal of the material it excavates.
The cutterhead excavates rock with compressive strengths of up to 250 MPa and with a borehole diameter of 1.5 m. The excavated cuttings fall through the centre of the boring unit due to the force of gravity. The cuttings are transferred to a muck chute at the jacking frame via channels introduced into the thrust pipes. After each jacking stroke, the boring process is stopped for a short time to secure the pipe string and the boring unit. Then, the next thrust pipe can be installed in the jacking frame.
All production steps of the Herrenknecht BBR are remotely controlled, therefore no personnel are required to remain in hazardous areas during operation – improving work safety significantly.
Reaming and lining
After breaking through to the upper level, the cutterhead is removed and replaced by the reamer head. The reamer head expands the bored hole to diameters of up to 3.6 m. The modularity of the reamer head allows the diameter to be adapted to individual requirements. Coordinated with the reaming progress, the thrust pipes are removed one by one by the jacking frame until the reamer head breaks through to the lower level.
Traditionally, a shaft is secured after reaming is complete. This is time-consuming and carries the risk that the excavated shaft may partially collapse before it is secured and require reworking. The newly developed lining lowering unit for the BBR allows the shaft to be lined simultaneously with the reaming, saving time and reducing risk.
The lowering unit is installed on the upper level after the cutterhead has been broken through and the reamer head is mounted. The lowering unit inserts steel lining segments into the shaft one after the other, following the progress of the reamer head. This ensures that the shaft is fully lined and secured when the reamer head breaks through to the lower level. The lowering unit is operated by remote control as well, to improve work safety.
In operation at El Teniente
A Herrenknecht BBR is currently in operation at Codelco’s El Teniente mine in Chile. It is used for shaft development and lining in very complex ground conditions, presenting blocky, fractured, and unstable rock formations and geology prone to over-excavation, which can lead to shaft collapses. This geological context presents challenges to traditional methods such as raise boring, particularly in terms of shaft stability during excavation and until the lining is installed.
In addition to the complexity of the geological context, the high safety standards imposed by Chilean mining regulations, as well as the very strict shaft dimensional specifications required in the mine production level, disqualified standard boring methods.
A unique constraint emerged from the construction method and its sequencing. The final four shaft lining elements are lined
Figure 1. Illustration of the working principle of the BBR (pilot hole drilling).
Figure 2. Reamer head before starting the reaming process.
Figure 3. Top-down lining process and reaming.
with composite rings to enable subsequent blasting in the area of the shaft intended to receive the ore pass’ chute. Consequently, HDPE rings were fabricated and installed in this shaft area using the same lining lowering system as for the steel lining.
To facilitate the lowering process, temporary flat steel casing rings were deployed around the final steel liners, to reduce friction as much as possible. Once these casing rings were removed, the annular space was backfilled with concrete to cement the steel casings rings to the geology.
In this very specific context, the development of a specialised machine and methodology was imperative to completely meet all these requirements. Safety for personnel was a top priority, requiring a procedure that excluded any human presence in the shaft. The BBR minimises the risk of shaft development in areas where conventional operation is not possible and is therefore a viable alternative.
Currently, the BBR is able to complete an entire mine shaft, from equipment positioning to excavation processes and lining installation, in less than six weeks of effective time. The team works in two shifts per day, each shift averaging around six hours of actual work. This is a significant advance over conventional excavation methods, such as conventional shaft sinking and raise drilling, particularly in difficult rock formations.
The BBR was introduced in 2022 at Codelco’s El Teniente mine to construct ore passages connecting the production level to the haulage level. Seven shafts with a diameter of 3.6 m, an average length of 30 – 50 m, and an internal casing diameter
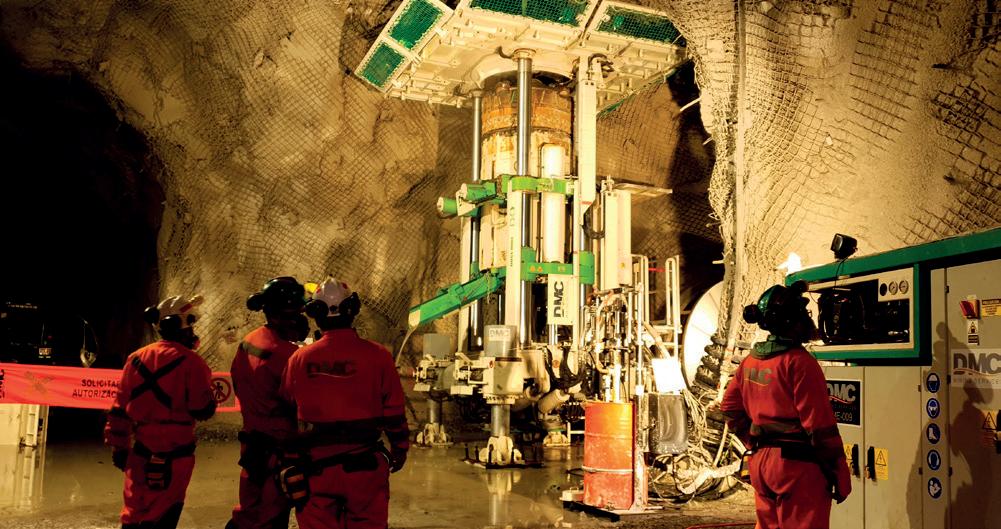
of 3 m – representing a total length of approximately 300 m –were successfully completed.
Outlook
The BBR has proven to be an efficient alternative to other conventional or mechanised methods in excavating ore passes and ventilation shafts. The optional lining unit shows significant advantages, especially in complex geological conditions. The concept and layout of the BBR is constantly advanced, in view of a large demand for mechanised shaft sinking in underground mines. The focus here is to further improve the BBR’s efficiency in terms of excavation rates, as well as adaptions to individual local requirements. A next step will be to extend the possible shaft diameters to 4 m.
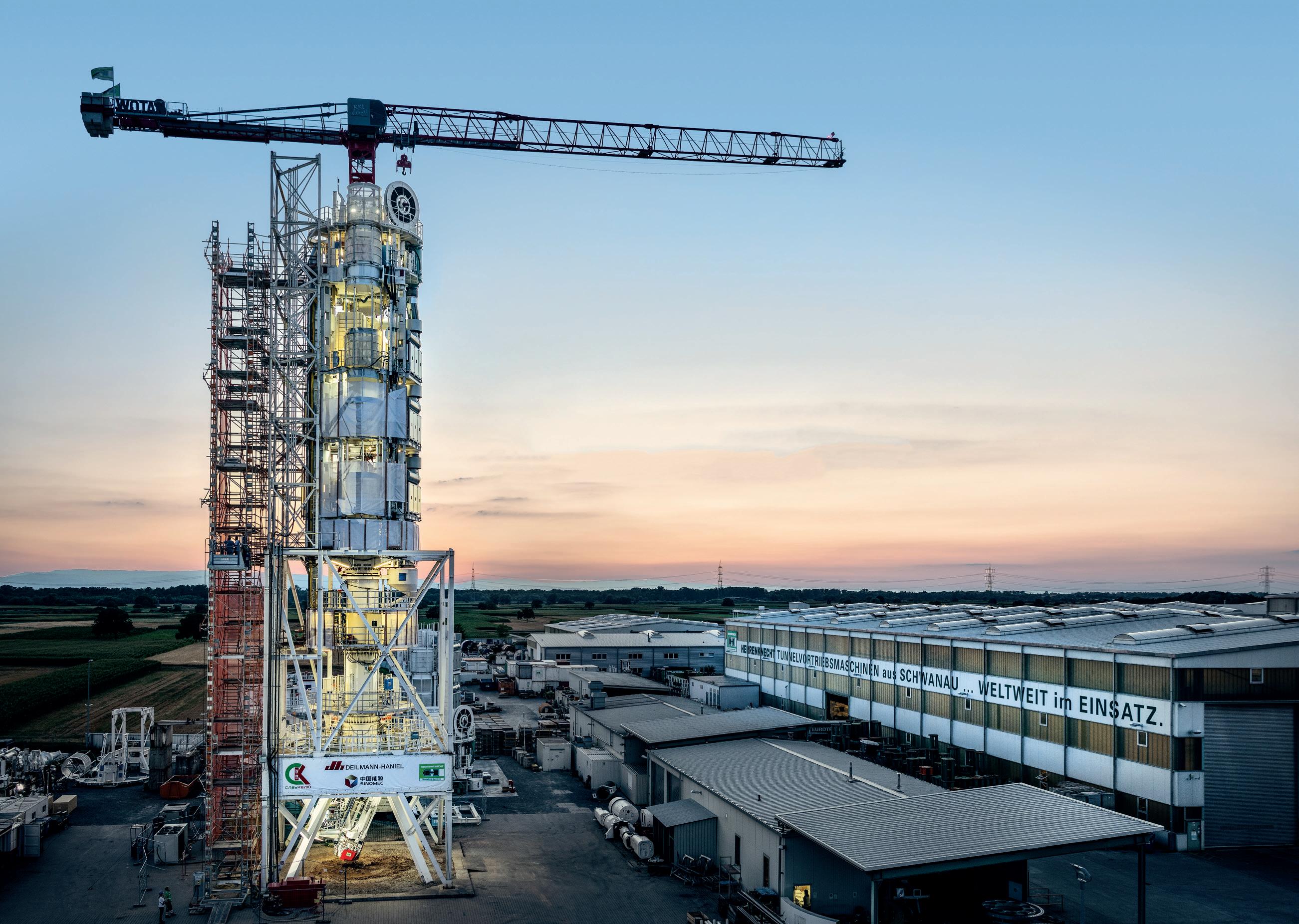

Figure 4. Operation of BBR1500 in El Teniente mine in Chile (Credit: DMC Chile).
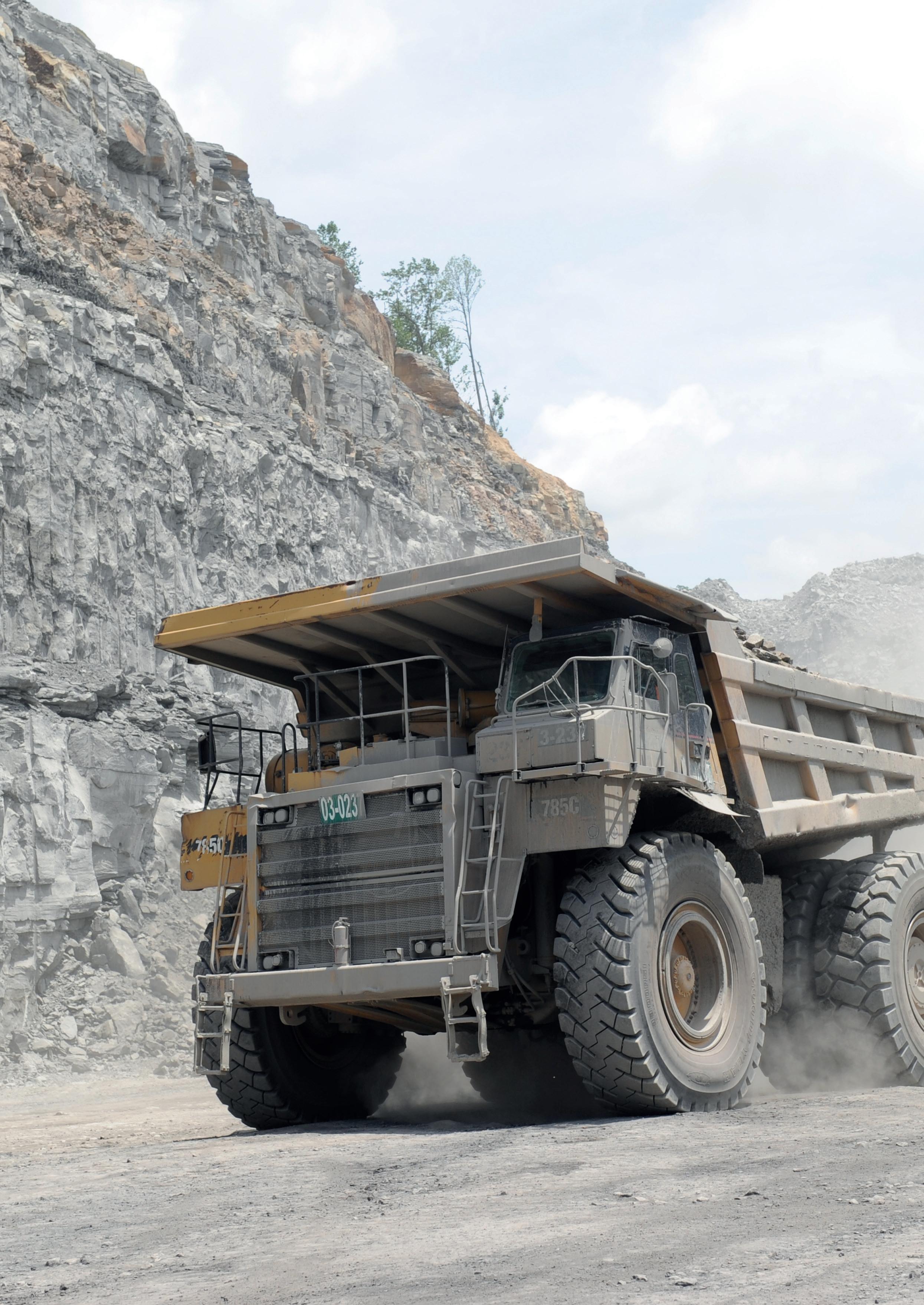
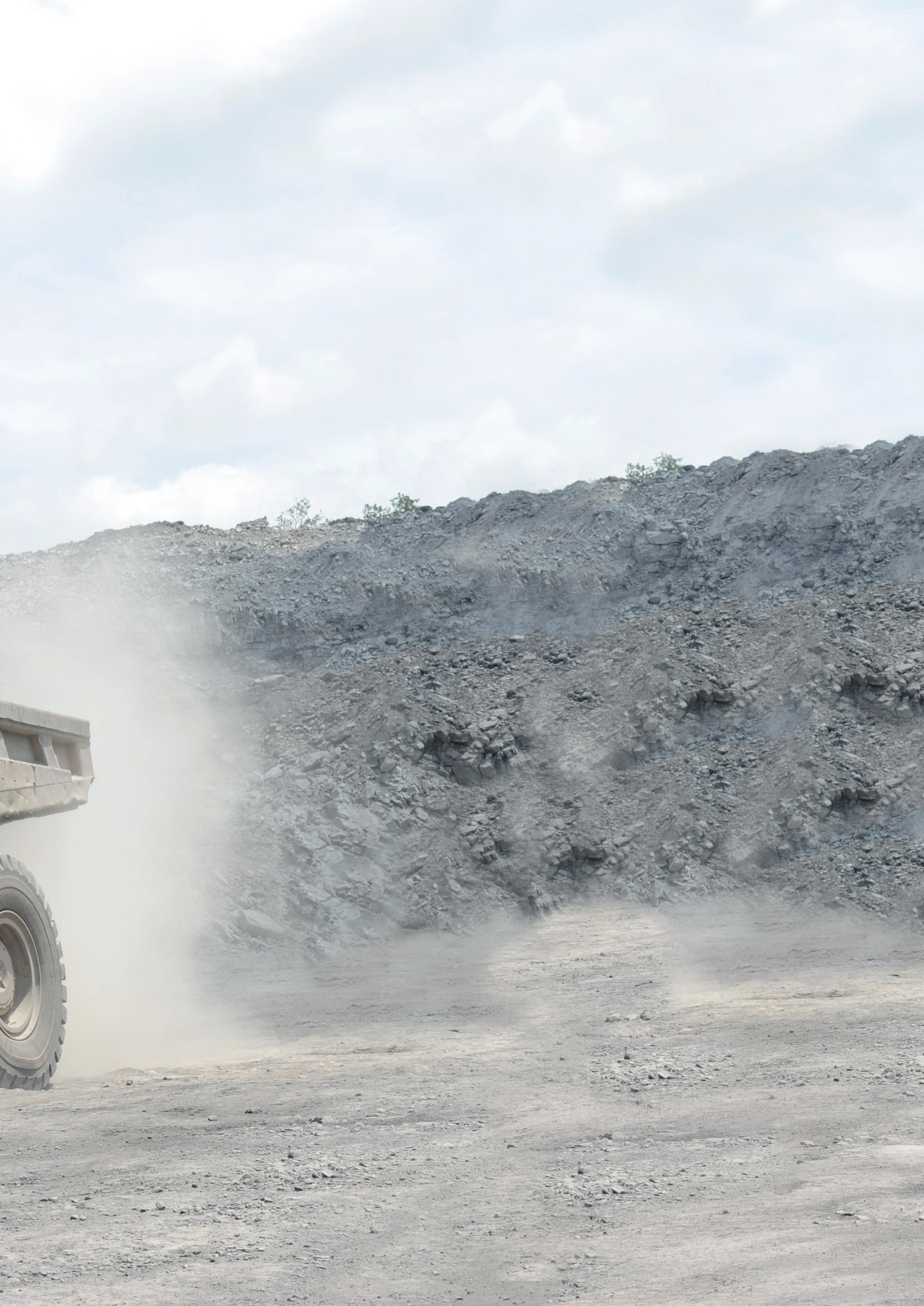
Eric
Matson, The Goodyear Tyre & Rubber Company,
USA, explores how a greater understanding of the technology and construction of tyres can help mine operators optimise performance and lower costs.
Figure 1. By tracking performance and other indicators over time, with tools like Goodyear’s TPMS HD, fleets can make better decisions about tyres in service today and help predict future tyre requirements more accurately.
For some in the mining industry, tyres may be a bit of an enigma. Basic knowledge revolves around what tyres are – round, black, and made of rubber. Many operators forget that tyres are the only point of contact that the vehicle has with the road. They are the connection to a job site and an important part of equipment, no matter the job. Learning about the basic construction and key components in their tyres can help operators make better decisions for their fleet. Leveraging a suite of tyre management solutions that fits a fleet will help improve productivity and efficiency. It is imperative to partner with a trusted advisor to help select the right tyres and technical solutions for the application, in order to get the most out of investment and optimise performance while managing operating costs.
Part 1: Optimised tyre design
First, it is important to get grounded on the key components of OTR tyres and how they can meet the specialised needs of every mine and yard. The design and technology that go into each tyre component help deliver the performance characteristics that a fleet needs. Tyre manufacturers design and build treads, compounds, and sidewalls to deliver toughness and performance for their customers. Combining different technologies in each element can help a tyre do its particular job more effectively. To illustrate the overlapping design and technology of today’s modern mining tyres, one of Goodyear’s premium tyres for large mine haulage, the Goodyear RH-4A+, can be used as an example.
The tread pattern of a tyre should be designed to function optimally in different underfoot conditions. Based on the harsh working conditions in today’s modern mine, tyres like the Goodyear RH-4A+ were designed with an extra-deep E-4+ tread depth with a high net-to-gross pattern to handle the rock and aggregate underfoot conditions. Adjusting the tyre face based on the application can help increase durability and performance. The RH-4A+ uses centerline blading and enhanced shoulder lug pockets, as well as shoulder lug side notches to resist stone drilling and dissipate heat built up on the job site. The special blend of tread design features helps the tyre deliver better traction, improved cut/chip resistance, and longer tread life.
Tyre compounds provide the muscle of a tyre. They add strength and flexibility, and can be adjusted to provide different performance characteristics. In the case of the RH-4A+, there are different compounds built into the tyre. The tread cap, casing, foundational radial layers, and bead construction all have different compounds working together while the tyre is in operation. Extreme conditions mean that the RH-4A+ is made with tread compounds, with the stiffness to deliver high cut resistance and the flexibility to reduce any chipping and cracking, all while staying cool. A tyre’s ability starts with the compounds used, and the right foundation leads to consistent performance and dependable life cycles.
The sidewall of a tyre helps support the vehicle’s load and provides the durability needed to move heavy OTR payloads. Sidewalls play an important role in maintaining equipment stability. Exposure to heavy loads can, over time, expose more of a sidewall’s surface to rocks and other debris. This means that OTR mine tyres need increased thickness and reinforcing
technology to reduce the impact of bending and deflection. The RH-4A+ is made with Goodyear Durawall Technology to improve lateral stiffness and casing durability. This special blend of complementary technologies helps cut down on a tyre’s exposure to
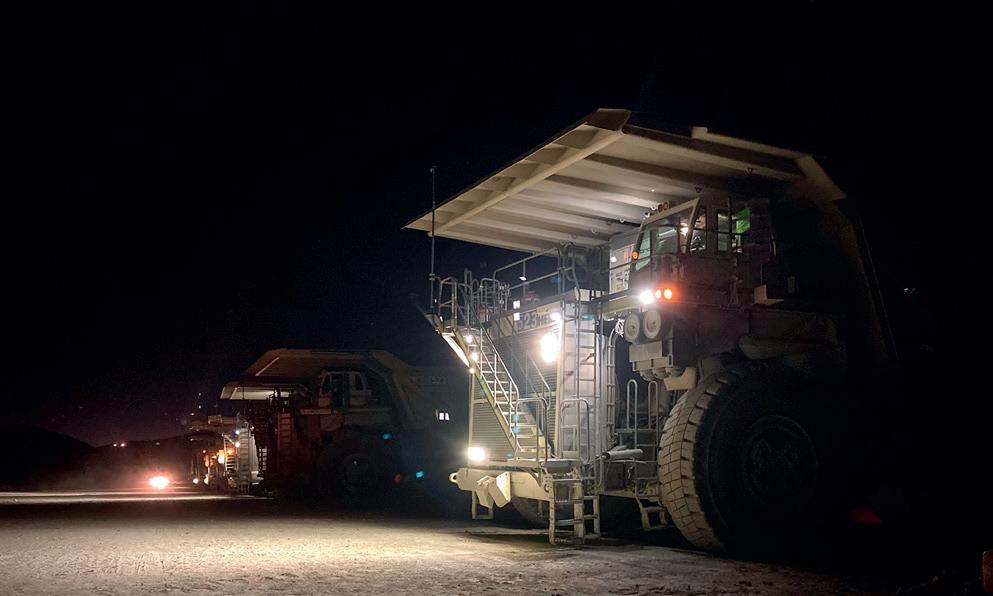

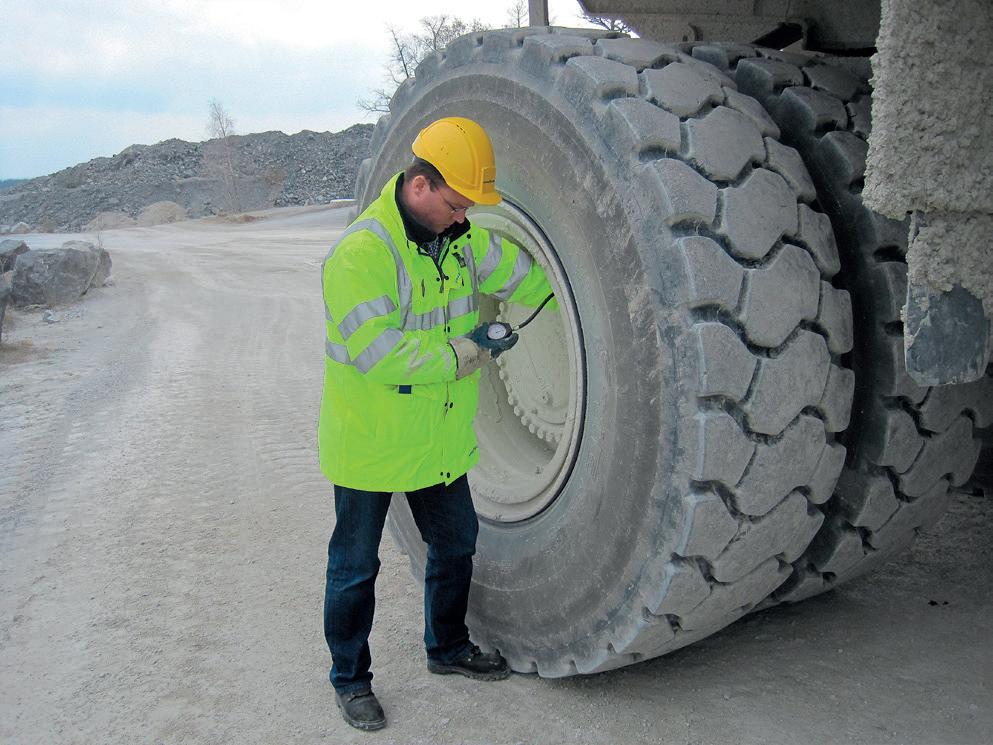
potentially damaging objects it may come across in the line of duty. Tyres like the RH-4A+ are also designed with longevity in mind, with a strong focus on lengthening the overall service life to minimise downtime and maximise the tyre investment.
Blending different technologies in the tread design, compounds, and sidewall structure helps give each tyre the characteristics that allow it to perform and do its job well. The RH-4A+ is a tyre designed to handle the stress and strain of heavy haulage in tough hard rock underfoot conditions. The unique combination of components, working together as a holistic system, helps deliver what Goodyear calls ‘performance power’ and the ability to get the job done. Next time you look at your tyres, look past how they are ‘black and round’ and see the different components working together to do the particular job –whether in the yard, in the mine, or in your driveway.
Part 2: Tyre management by design for optimised performance
With a better understanding of the construction of the tyre, the next step is proper tyre maintenance. With so many moving pieces in a modern mining operation, tyre maintenance may not be top of mind. There are a variety of tools and services on the market today that can help keep vehicles running and maintain investment. The tools utilised and how they are applied is a matter of individual preference, but building a tyre maintenance programme is key to running an efficient and economical operation.
Monitoring and maintaining the air pressure of the tyres is the number one most important task for a tyre maintenance programme. Leveraging connected, data-driven technologies, such as a TPMS, is a good option to monitor tyre pressure and temperature to detect under or over-inflated tyres, air leaks, and mechanical issues that could impact productivity. The benefits of this, and other similar systems on the market, include easier tracking by built-in sensors and user-friendly mobile and web applications to connect teams to their tyre’s performance.
Most of today’s tyre and machine monitoring solutions include sensors attached to the tyres and an on-board telematics unit (TCU). The tyre sensors constantly measure tyre pressure and temperature while driving and are easy to install, maintain, and move to new tyres when needed. The onboard TCU collects data from the sensors in the tyres and loads the inputs to a mobile network. The data can then be ‘mined’ for further analysis to help drive greater efficiencies throughout the entire operation.
Teams specialising in tyre maintenance understand the value of having a clear vision of how their tyre investment is performing today and appreciate a forward-looking view of what to expect in the future – no one likes a bill for new tyres that comes early. Regular reporting on and a survey of tyre and vehicle assets is indispensable for today’s mining business. Using today’s tracking tools allows site managers to track maintenance history, tread depth, tyre damage, machine engine hours and milage, air pressure, rim history, retread performance, and repair history.
There are different tools on the market today, and Goodyear offers EMTrack, an easy and accessible fleet
Figure 3. Today’s mining tyres are optimised and fit for purpose. The special blend of tread features and specialised technology help tyres like the RH-4A+ deliver traction, cut/chip resistance, and long tread life.
Figure 2. The Goodyear RH-4A+ was designed to function in the harsh working conditions in today’s modern mine, with extra-deep E-4+ tread depth and a specially designed tyre face and tread pattern to handle the rock and aggregate underfoot conditions.
Figure 4. Regular inspection of tyre inflation and wear should be the cornerstone of any maintenance programme. The right tools and services will help achieve enhanced tyre performance and longer service life.
survey reporting tool that gathers data and provides valuable reports to site operators and dealers. Using a tool to consistently track cost-per-hour, cost-per-tonne, and other key metrics will help enhance efficiency, reduce operating costs, and improve decision-making. Leveraging different tools available today will help teams improve inventory management, get ahead of maintenance and replacement planning, maximise budget efficiency, and, ultimately, deliver more productivity for their operations.
Part 3: Putting products and data to work
With the proper tyres and the tools and management solutions in place, an enterprising mining operation might think that the job is done. However, in today’s complex and evolving environment, there are still opportunities to unlock and efficiency to harness. The final step to unlocking what Goodyear calls the ‘Total Mobility solution’, is the collaboration with trusted tyre professionals to make sure that plans are executed efficiently, and an operation remains optimised. Goodyear’s field experts use advanced evaluation and survey technologies to understand the needs of a site, and consult and collaborate on ways to get more mileage and uptime out of investments. Working with trusted tyre professionals can help unlock experience that can improve an operation. The first step is a full site evaluation to score and track operating conditions. This process is called ‘doing your homework’, and can help enhance tyre performance in unexpected ways. A thorough site analysis includes understanding the unique needs of individual sites, and fingerprinting of the mines or job sites to explore all opportunities to make an operation more tyre friendly. Consultation with experts can help discover small changes to get better use out of
tyres, vehicles, and sites. Simple things like super elevating curves, finding the right slope for drainage, and examining the rock and aggregates on the floor can help extend tyre life and, by extension, improving overall efficiency.
Conclusion
Understanding more about your tyres and the available solutions, as well as collaborating with trusted tyre professionals, will help optimise investment, performance, and adaptability in today’s complex mining operations. In a day-to-day world that is filled with so many unknowns and unforeseen challenges, it is good to have a plan and network to help put it into practice. Getting to know your tyres might seem like an odd request at first but, as seen time and time again, they are working just as hard as you are to make sure that the job gets done.

we deliver the
cost per ton. For 90 years, Cincinnati has proven to be THE STRONGEST LINK

Cincinnati Dual Sprocket Conveyor Chains are proven to be b etter than other mining chains . Tons better, in fact. Tests confirm our chains deliver 20 percent more strength The result is greater durability, maximum availability and a trouble-free service life. That’s how
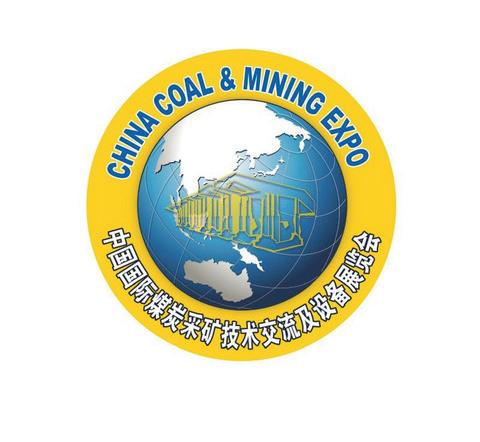
China Mining Expo 2024
Oct 23-25, 2024
Xi an Airport Convention and Exhibition Center
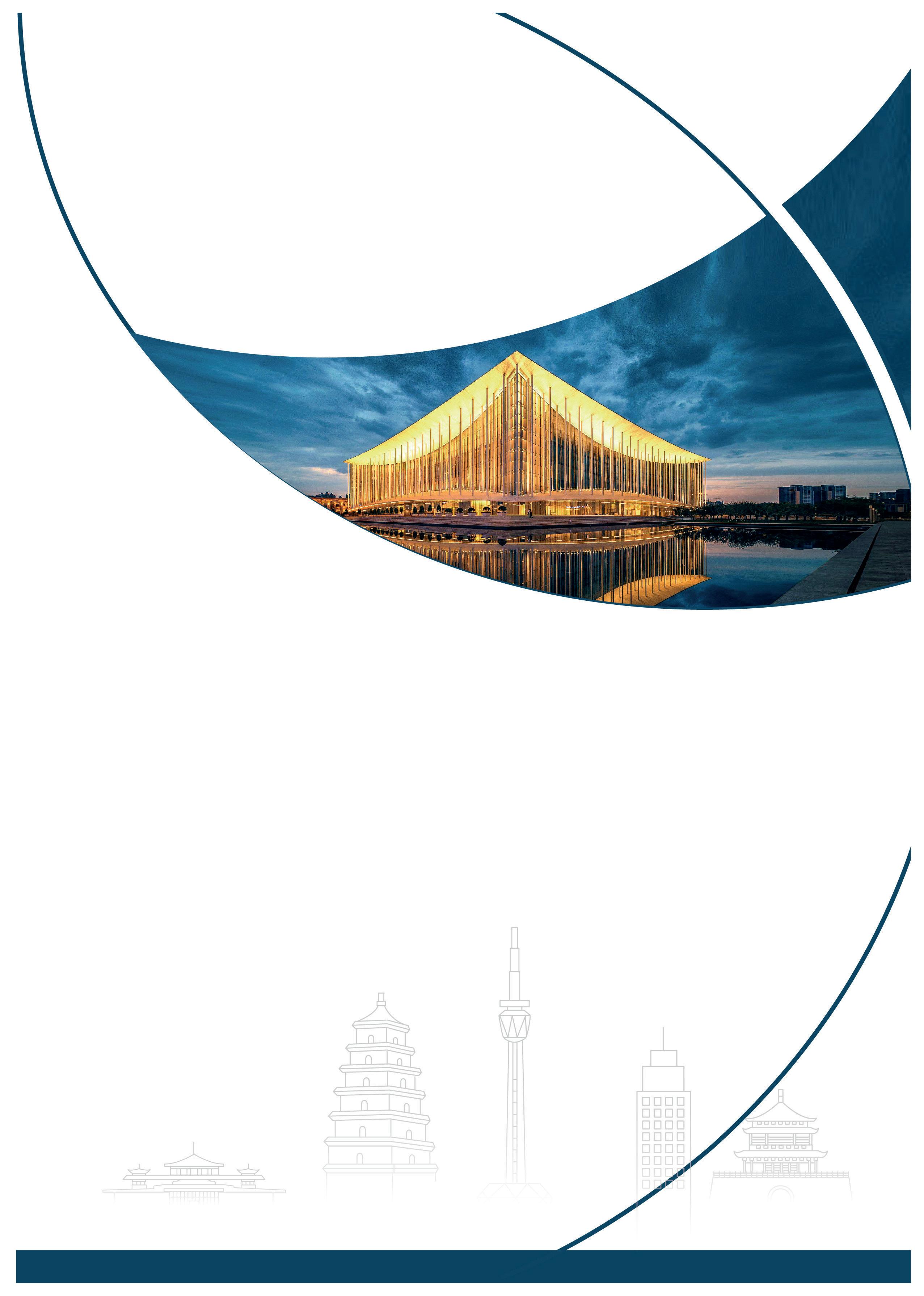
Host:
China National Coal Association
Organizers:
Together Expo Limited
China Coal Consultant International
Co-hosts:
China National Coal Group Corp.
Shaanxi Coal & Chemical Industry Co., Ltd.
Shaanxi Coal Industry Association
Rare opportunity!!! Visit Shaanxi’s mine
Exhibitor will have the opportunity to visit one of the most modern coal mines in the region, the Shaanxi Coal Group Huangling Coal Mine.
First coal mine to get NOSA 5 stars coal mine in China
Annual production capacity is 6 million tons
Field area is 184 square kilometers
Possible reserves are 359 million tons
Recoverable reserves are 281 million tons
WORLDWIDE ENQUIRIES
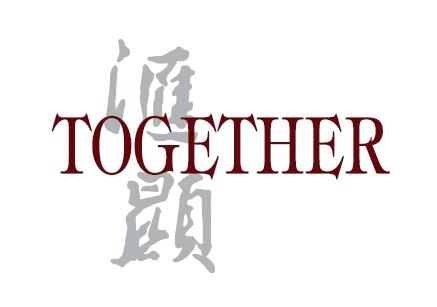
TOGETHER EXPO LIMITED
Hong Kong Head Office:
Room A, 16/F, Eastern Commercial Centre
83 Nam On Street, Shau Kei Wan
Hong Kong
Contact : Ms. Katherine Lee
Tel : +852 2881 5889
Email : katherinelee@together-expo.com
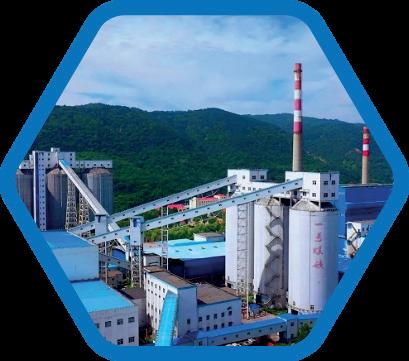
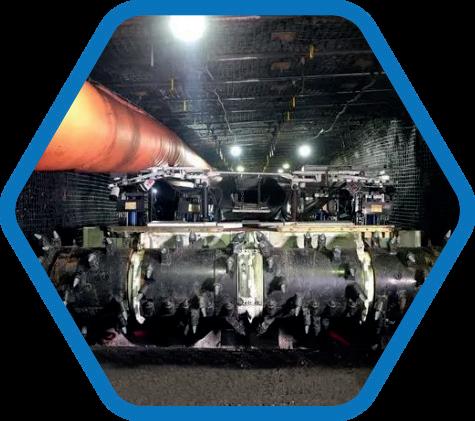
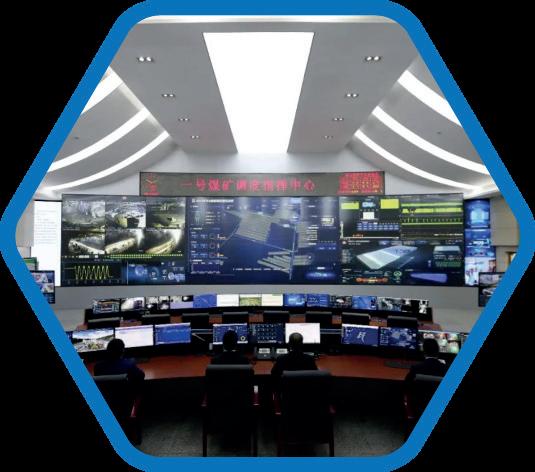
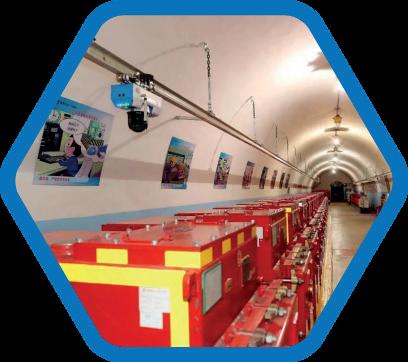
Beijing Office: Room 12A11, Building A, Kunsha Center No 16
Xinyuanli, Chaoyang District
Beijing 100027, P R China
Contact : Ms Zoe Yin
Tel : +86 10 84510286 / 17310285580
Email : zoeyin@together-expo com cn
Anthony Ferrenbach, Weber Mining and Tunnelling, Mexico, highlights how using foam can enhance safety and effectiveness when filling cavities.
Geological conditions related to mining can lead to rockfalls and large-scale collapses, challenging every mining operator. These cavities can cause severe damage to both personnel and mining equipment, and can halt production. To prevent more serious problems, recover the areas with minimal delay, and restore workplace safety, it is necessary to fill these cavities as soon as possible. Some benefits of filling cavities caused by rockfalls include:
n Reduction of transport times to work areas, due to the quantities of Rocsil® foam required to fill large volumes.
n Due to the high expansion rates of Rocsil, complete filling of the cavity is ensured. This allows for the containment of the surrounding walls in exposed cavities, which prevents weathering.
n Increased work safety.
n No waste of material.
n Fire resistance.
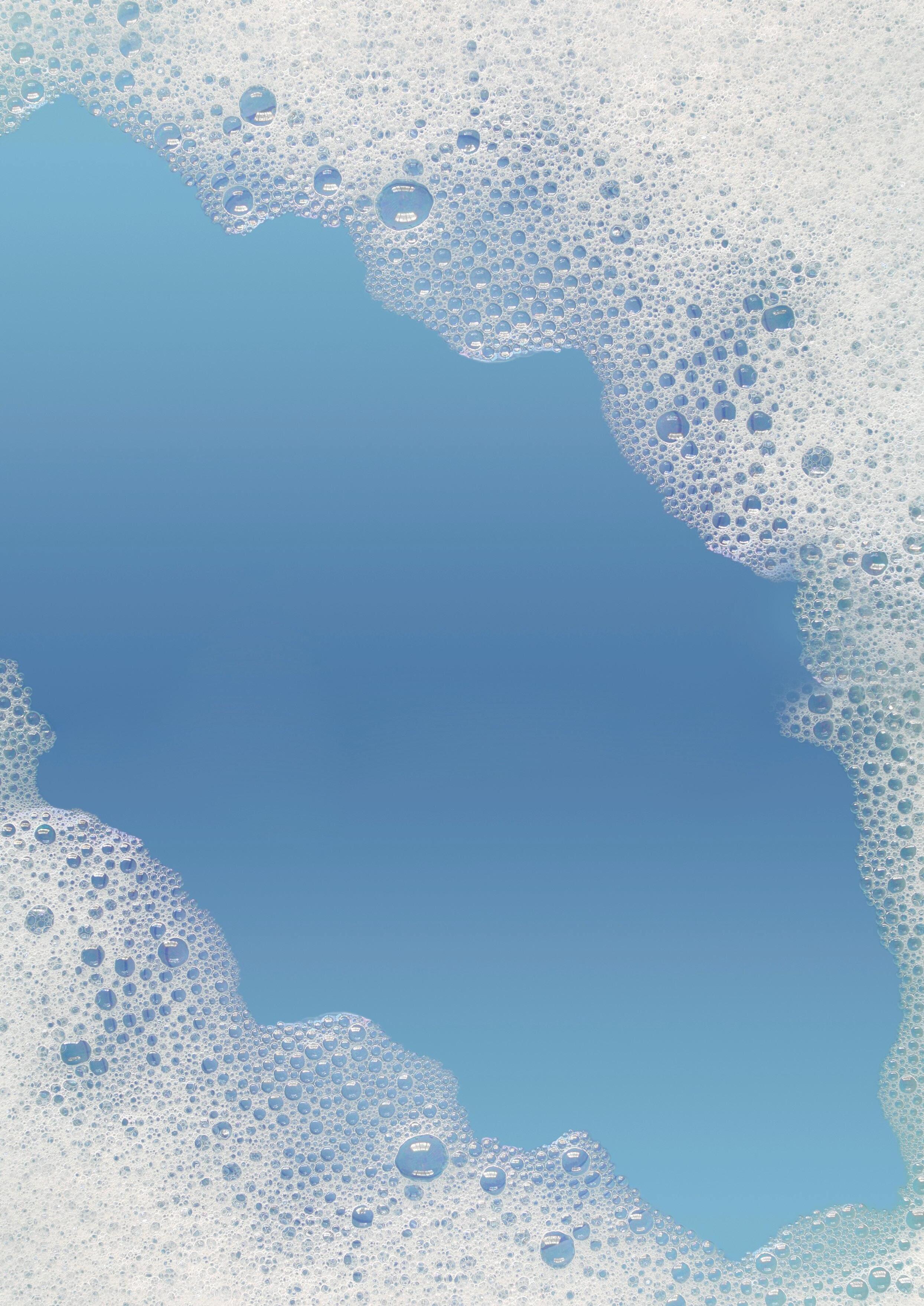
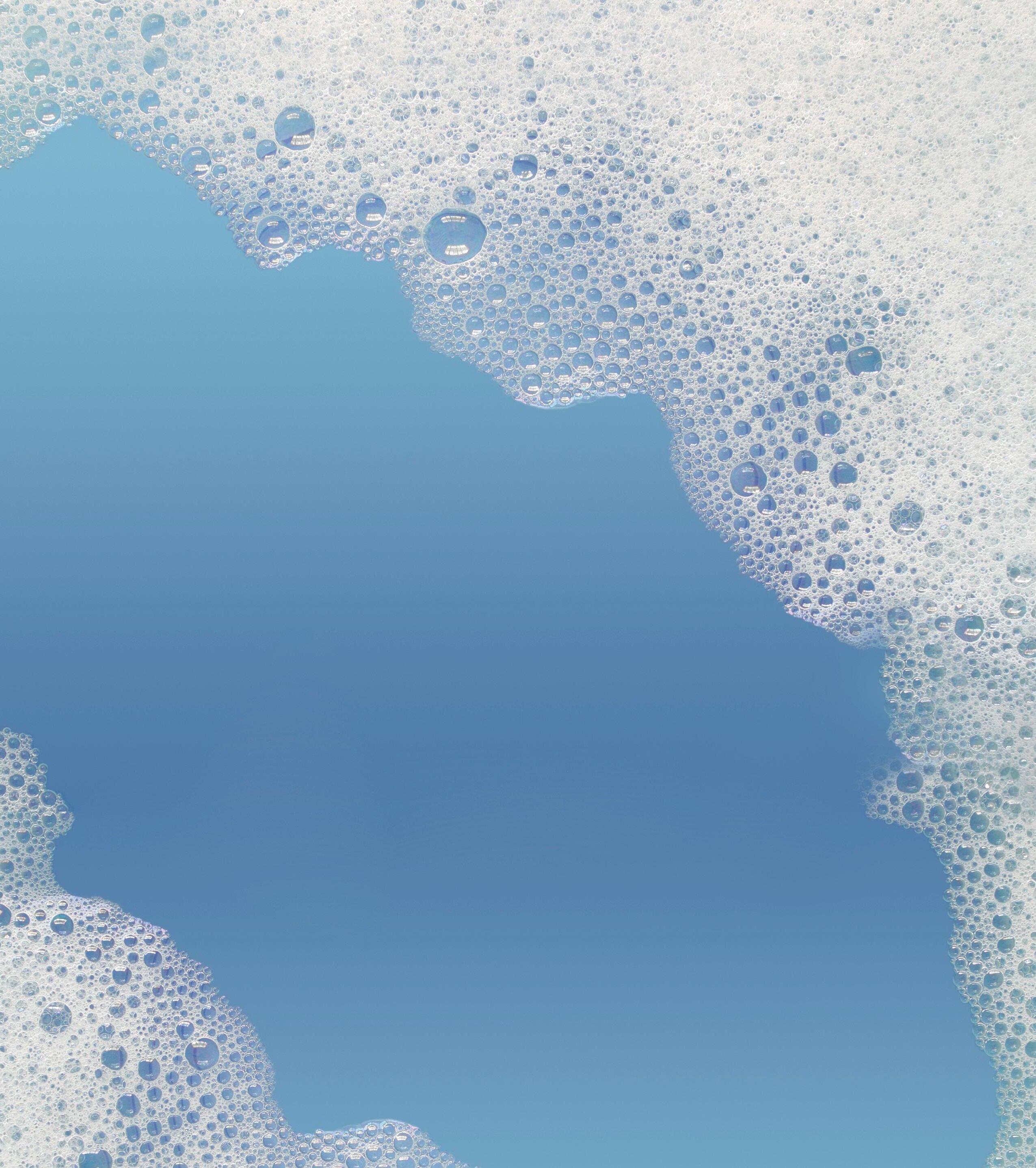
Weber Mining offers phenolic foam and silicate products with different technical characteristics for individual solutions in mining and tunnels. The foam is pumped into the cavity using a pneumatic pump with a pre-established mix ratio of the two components, resin, and catalyst. A mixing gun joins the components shortly before the product exits the pipe and is placed. The foam begins to expand immediately, allowing for efficient filling of the cavity with a minimum use of product.
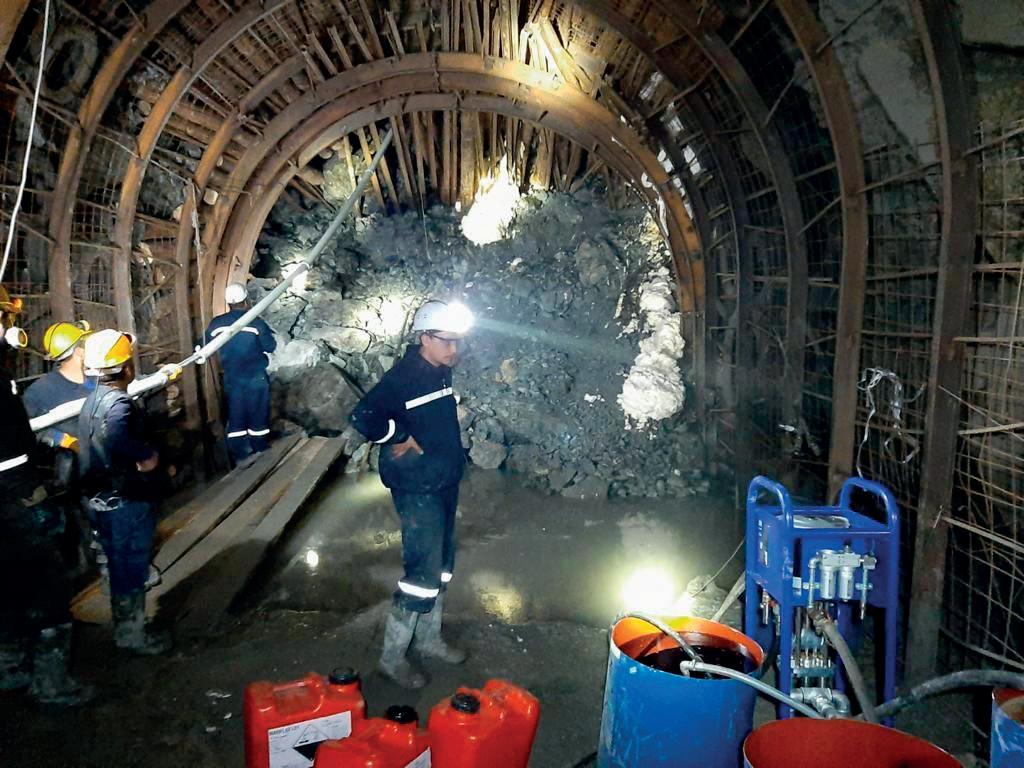
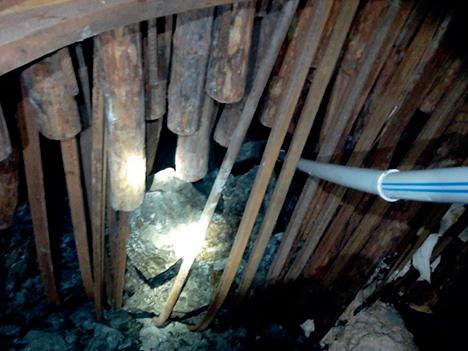
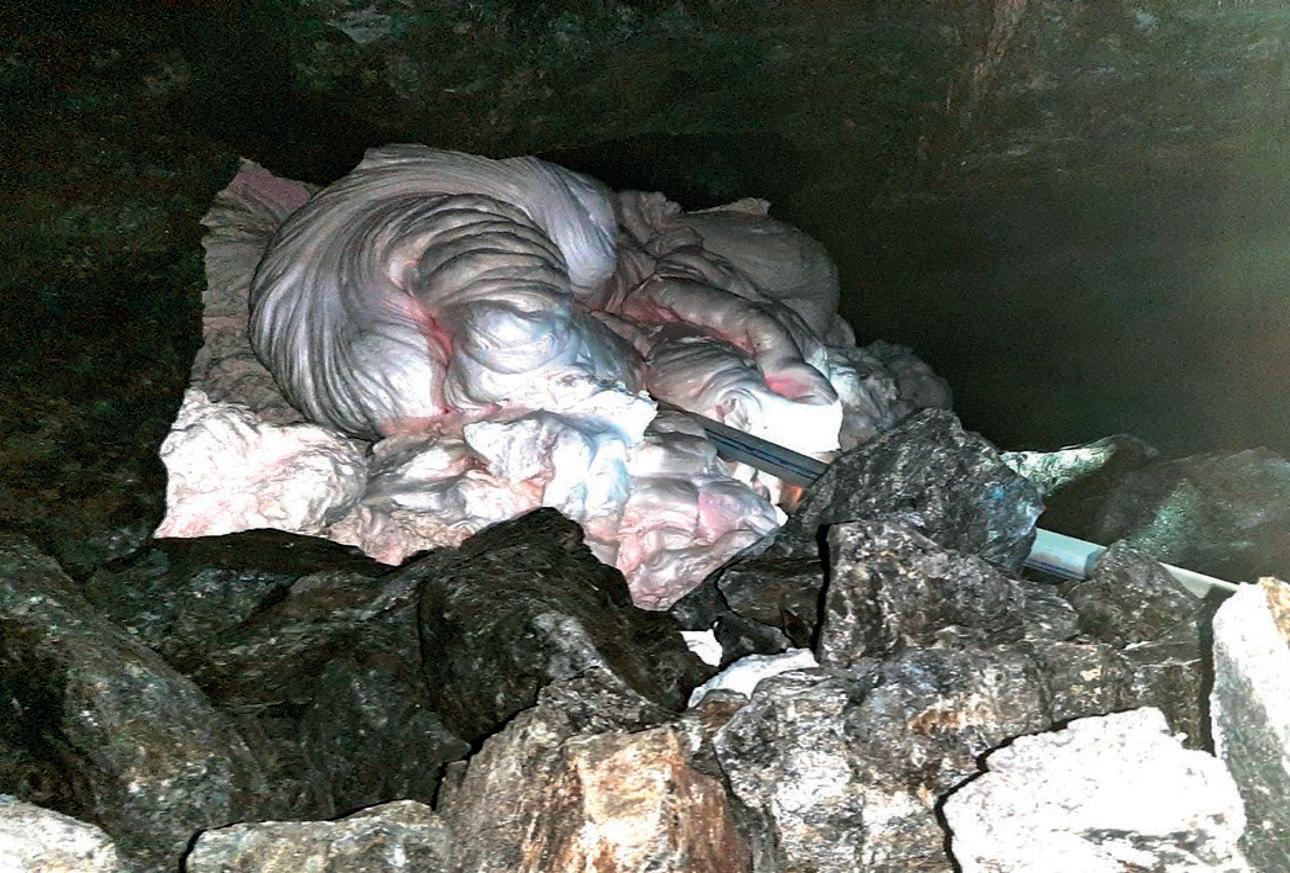
The expansion rate varies according to the desired compressive strength of the final product. Cavity filling foams allow for a cost-effective, time-saving, and safe solution.
Phenolic foams
Phenolic foams are two-component, high-expansion solutions designed to quickly fill gaps and cavities according to their size and morphology. The benefits of this technology include time savings and increased safety compared to traditional filling methods. Designed in the 1980s, especially for filling cavities when the ceiling collapses and with no alternative but to abandon the sites, the technology has been improved with different expansion ratios, safer chemistry, and longer component life. There are 10 different variants available for each specific requirement.
Case study
A mine was developing its gallery in an area of poor rock quality. Therefore, specific fortification methods had been applied, one of them being the installation of frames, continuously at certain distances. However, during the excavation, a large collapse occurred that damaged the previously installed frames. An attempt was made to clear the area; however, since the collapse was ongoing, it was impossible to remove the fallen rocks to facilitate the installation of new frames. Therefore, an alternative method had to be considered to stabilise the cavity and minimise personnel exposure, thereby improving the safety of the operators.
The phenolic foam from Weber Mining was chosen and injected from outside the cavity. This technique has been used with great success in underground works around the world. To ensure the methodology and guarantee the success of the project, Weber Mining’s procedure was employed, with its own equipment and technical team.
Immediately after the start of the collapse, the area was evacuated safely and quickly without incidents or injuries. The Weber Mining team began the injection from a safe distance, 10 m from the collapse, installing a set of injection tubes with different lengths inside the cavity to ensure complete filling. The injection began from the gallery floor, with an initial 8 m injection lance installed within the fallen rocks. Due to the pump flow, the injection lance had a reach of 4 – 5 m, allowing operators to direct the foam where needed. The injection started from the gallery floor, surrounding the loose rocks and filling the empty spaces. As the filling continued and the foam expanded within the cavity, the previously installed injection lances were used, with a better reach upward within the collapse. Weber Mining’s pumps are equipped with pressure gauges that indicate any increase in pressure, signalling that the empty spaces are being filled. The expansion of Rocsil within the cavity in a confined space exerts positive pressure on the cavity walls, allowing the filling to be pressurised. This pressurisation exerts a resultant force on the surrounding walls, preventing self-mining from the ground and providing an active support function. Once the gallery recovery was completed, the Rocsil foam, in addition to protecting the support from possible additional collapses, allowed for better load transfer through the frames. This load distribution optimised the support’s strength once placed.
Figure 1. Cavity filling with expansive resin.
Figure 2. Injection system through the fallen rocks.
Figure 3. Foam inside the cavity.


Due to the size of the cavity, which extended over 10 m, and the instability of the ongoing collapse, it was decided to perform the treatment in stages. Once the first part of the cavity was filled, the mine had to follow a strict excavation process consisting of excavating 1 m of the gallery with fallen rocks and foam, and installing frames before excavating again. This process allowed the mine to quickly recover the gallery without being exposed to further rock collapses, as the ceiling was composed of foam. After 8 m of excavation, Weber Mining personnel continued to fill the rest of the void using the same strategy.
The initial evidence of the filling’s effectiveness came from the readings of the differential pressure gauges and the foam returning to the gallery as the cavity was filled. This was corroborated by direct observation and underground measurements carried out by the mine’s operating teams when they began to excavate the fallen rock onto which Weber Mining injected the foam, and were able to place the frames without difficulty and with a stable foam ceiling.
Another important aspect is that filling the cavity ensured that the new frames were in place, absorbing the energy of falling rocks in case of a possible collapse from the top of the cavity.
Conclusion
The gallery was able to be quickly recovered without incidents, accidents, or injuries of any kind. The entire length of the collapse is now protected by a foam ceiling, providing safe and long-term access for traffic.
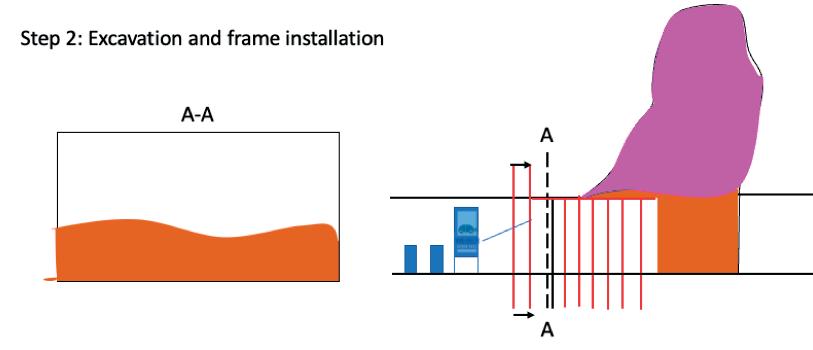
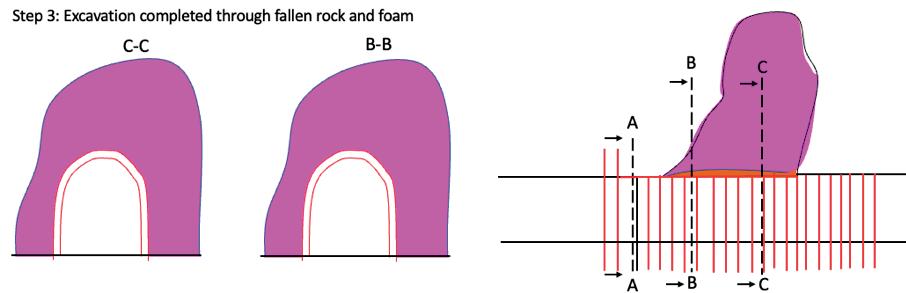
This case study serves as the most appropriate testimony and legacy to the effectiveness of foam as an alternative to traditional cavity filling products. Success was achieved, despite technical adversity. Even though the rockfall continued and the size of the cavity could have blocked access for months and delayed mining operations, adherence to the procedure and methodology employed offered a safe and effective solution.
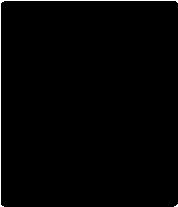
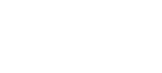
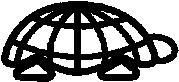









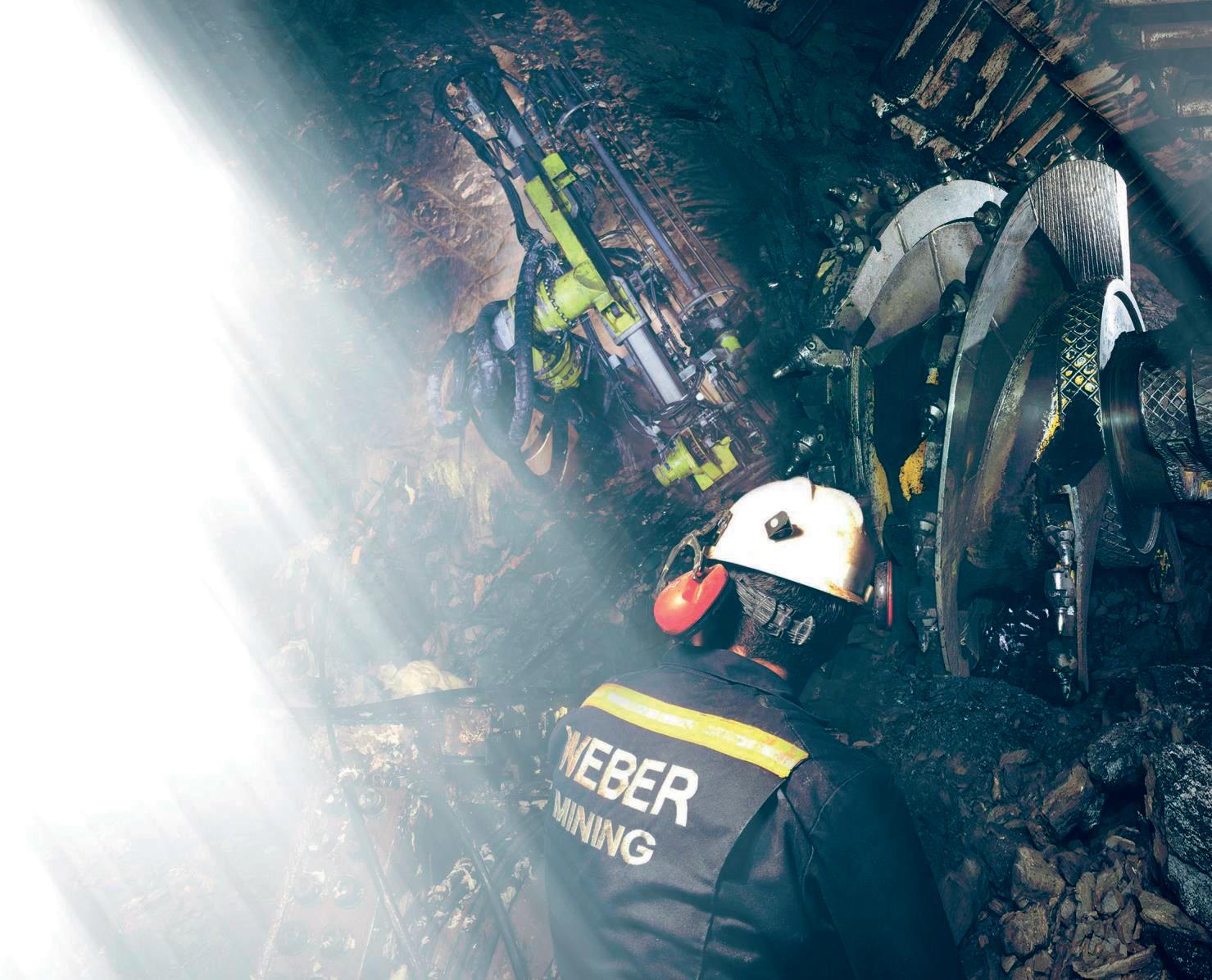


Figure 5. Step 3: Excavation completed through fallen rock and foam.
HARD ROCK MINING – COAL MINING – CIVIL &
Figure 4. Step 2: Excavation and frame installation.
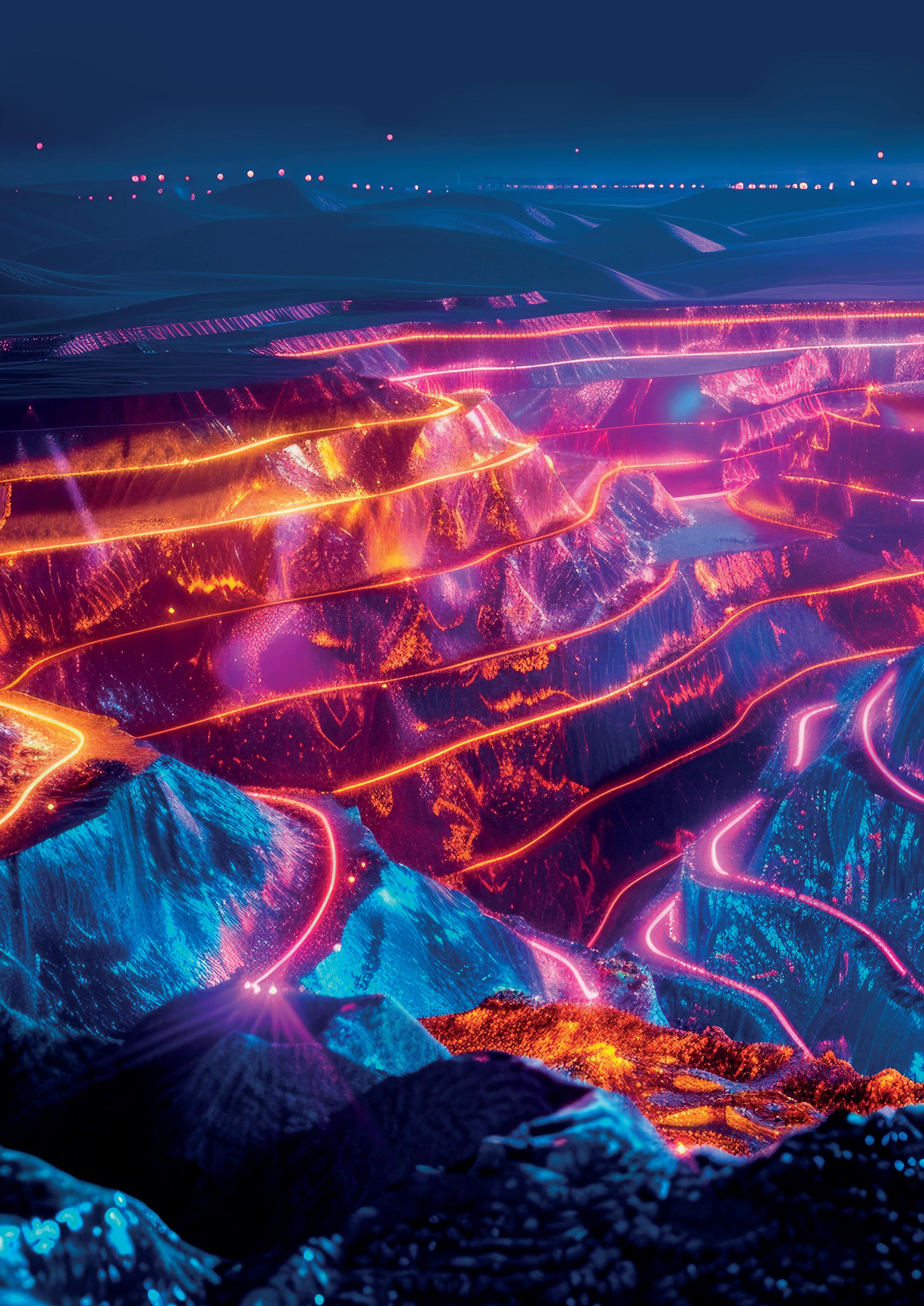
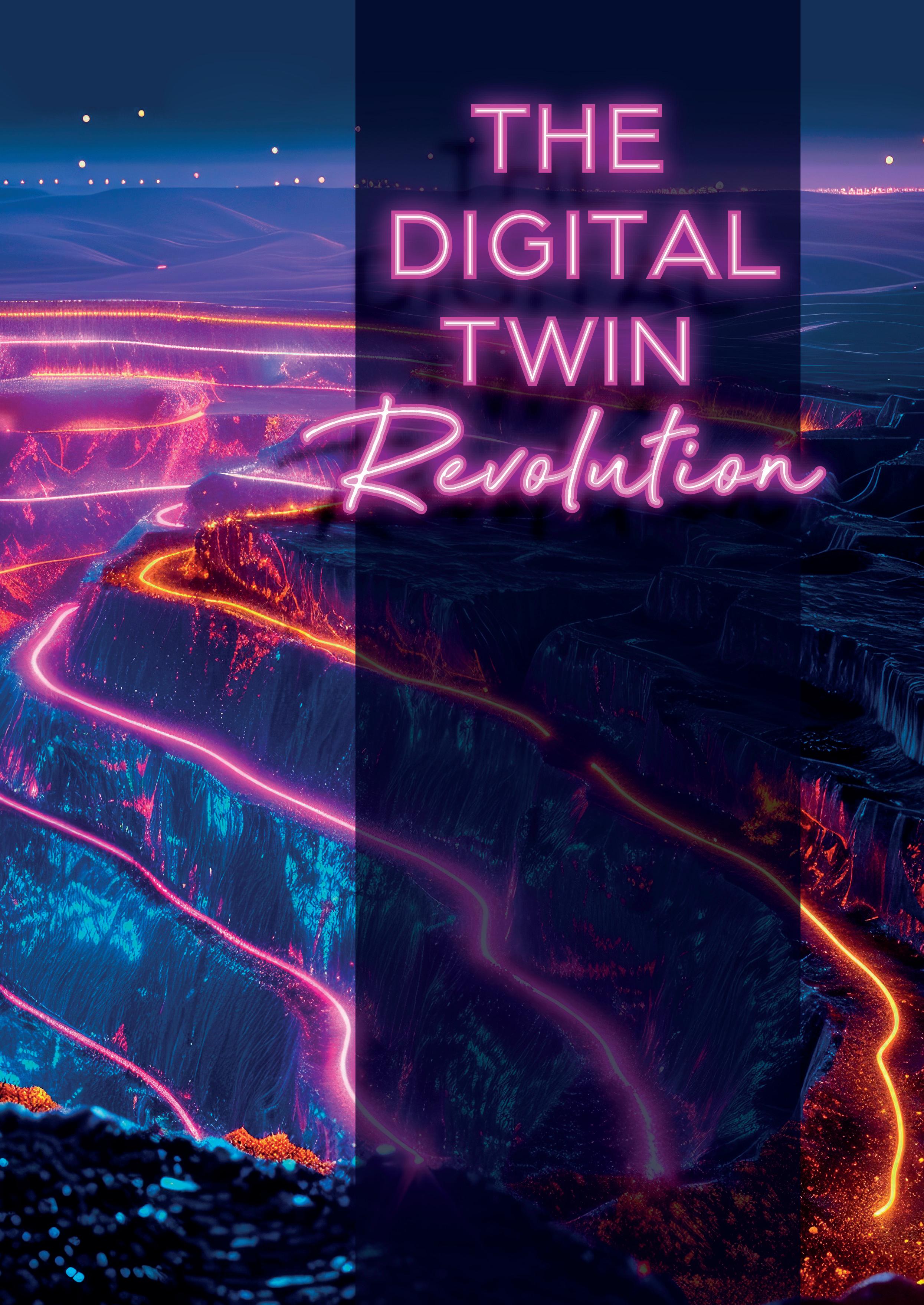
Richard Clement, Smart Construction, advocates for the adoption of digital twins for brownfield mine sites to aid safety, efficiency, sustainability, decision-making, and resource management.
As the mining industry evolves and more sites are converted into brownfield land, companies around the world are turning to digital solutions that will effectively support projects to fill in former active sites. As these projects take place, digital twins are increasingly being viewed as a vital solution to emerging challenges within earthmoving. This comes as part of a larger global push for the utilisation of more technological solutions in day-to-day practices.
In a recent survey, 99% of mining company decision makers said technology and innovation were ‘critical’ to their organisation’s survival.1 As digital tools and technology continue to revolutionise every step in the mining process, this article breaks down how digital twins offer a unique opportunity to the mining industry.
What is a digital twin?
The idea of digital twins has been around for more than two decades, but businesses are now beginning to realise their enormous potential, particularly for innovative enterprises in the mining sector to create brownfield sites at former active mines.
A digital twin is a virtual model that accurately recreates a physical object. They are highly detailed for the purposes of integration, testing, and maintenance, allowing the user to apply hypothetical simulations to the model to examine the outcome. Digital twins have become critical in a number of industries as a method of trial before physical changes are made to a project.
Within the mining industry, digital twins can offer a wealth of benefits. Both real-time monitoring and predictive maintenance are vital, and digital twins enable the ongoing monitoring of mining machinery, which ultimately allows operators to assess performance and prevent possible breakdowns in real time.
Mining is recognised as one of the most hazardous industries to work in. Measures that can improve safety and mitigate risks and hazards play a huge role in improving health and safety for employees. Digital twins are a great example of this, by creating simulations for training, enabling remote equipment operation, and monitoring the movement of workers and vehicles. Digital technology is also used to identify hotspots in advance and reduce critical asset downtime which brings significant financial benefits. Digital twins specifically are able to help managers identify cost-saving opportunities throughout the value chain, directly impacting the profitability of the project.
Building a digital twin for the mining industry
Initially, a digital twin is created using data from various sources, including 2D linework plans, surveys, drone mapping, robotic 3D scanning, Triangular Irregular Network (TIN) geographic data vector development files, photogrammetry, and LIDAR. This collection of information is then used to create a highly accurate and detailed digital model of the physical site and its current, baseline state.
Smart Construction’s Dashboard solution provides the environment to visualise and analyse 3D digital twins quickly and easily, allowing for better communication of construction plans and schedules with everyone involved throughout the project’s lifecycle. Each digital twin is created using IoT tools – such as drones, rovers, and machines – all contributing data to the Dashboard, in order to build a comprehensive view of the site.
Digital twins can be continuously updated as the brownfield project progresses. They are updated using data collected from the site itself and can simulate and monitor the site in real-time, offering the potential to make improvements before something is built and avoiding costly reworks. Dashboard can also work in alignment with Smart Construction’s other products, such as Fleet. Fleet tracks vehicle movement and cycle times, collecting the load count data which can then be fed through to the digital twin.
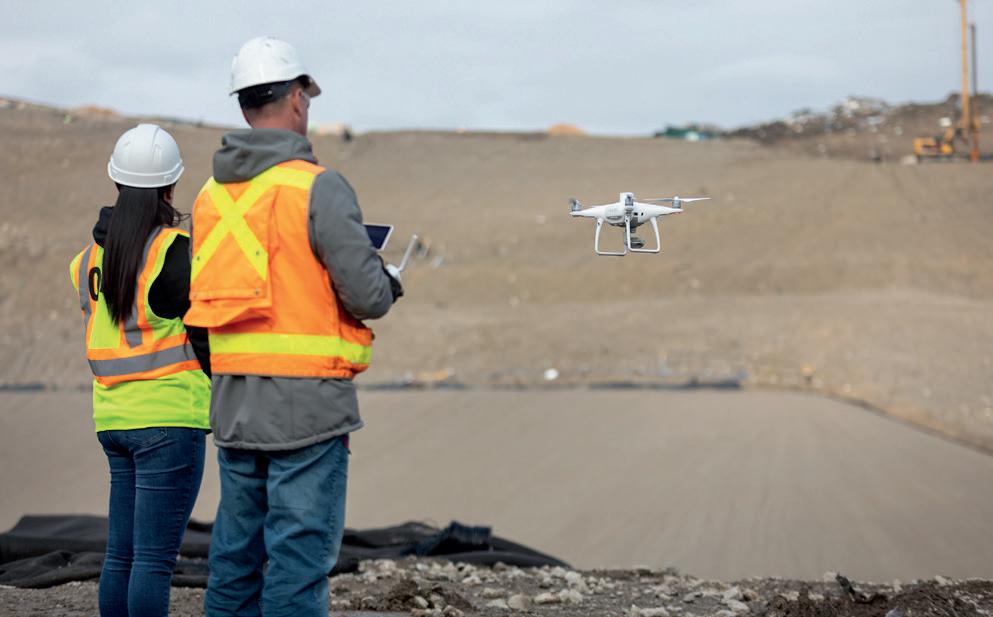
Central to the process of building a digital twin are Smart Construction’s expert advisors. Working directly with clients and partners, each advisor works to ensure the digital twin is optimised for different briefs and challenges.
How can digital twins benefit the mining industry?
Working within mining and on former mines is a high-risk profession, with many safety measures and regulations in place. Digital twins enhance safety and risk mitigation by creating simulations for training and enabling remote equipment operation. Operators can use these virtual models to simulate emergency scenarios in a risk-free virtual environment. These virtual experiences will inform employees about the different dangerous situations within a mine and help them understand how to respond effectively and safely in real-world situations.
Whether it is a machinery failure or a sudden change in conditions, digital twins enable site managers to anticipate and prepare for potential hazards before they occur. This helps mining companies to minimise the risk of costly accidents and injuries while improving worker safety.
Digital twins also have the ability to create a more productive job site by producing a virtual replica of complex processes within the mine. This enables site managers to run various different simulations and scenarios before making any actual changes to the mine site in the physical world. These simulations can optimise mining processes like drilling, blasting, and ore extraction, which not only improves productivity within the mine site, but also reduces waste by virtually testing different parameters.
This technology also enables the real-time monitoring and predictive maintenance of earthmoving equipment –operational delays are costly for companies, but virtual twin models provide predictive maintenance capabilities and enable operators to address equipment issues before they lead to downtime.
Brownfield operations are complex and dynamic. Ensuring the efficient movement of materials and supplies within mines is crucial to efficiency and safety. Digital twins provide real-time tracking of equipment, optimising processes, reducing congestion, and enhancing safety. This efficiency helps save resources and time, which, again, directly impacts the profitability of the mine.
Case study: HEITKAMP
Within a mining site it can be difficult to grasp the latest jobsite developments, as materials are regularly being moved and delivered, machines are constantly running, and site managers are confronted with a flood of data every day.
Located in the renowned mining region of Germany, Saarland, the Maybach mining heap has historically served as the repository for non-coal-bearing waste rock from neighbouring coal mines. The HEITKAMP project involves the delivery of 2 million m3 of soil across 27 ha., over the entire duration of 10 years.
For Sina Motsch, site manager for HEITKAMP Corporate Group, it is crucial that she finds an easy way to make sense of the job site and make use of the information effectively. Drone surveying was the first solution Motsch’s team put in
Figure 1. Smart Construction drone technology at site.
place to efficiently collect high-quality field data for the digital twin, which helped her gain comprehensive terrain insights once every few months. However, the logistical challenge of daily drone flights and the need for more detailed information on specific jobsite areas and material deliveries required them to explore alternative solutions.
By utilising the Smart Construction Dashboard, Motsch was able to transform her site into a digital twin. This enabled her to immediately discover jobsite developments, view which materials were needed, and see where and how much of the mining site had been built.
As the mining industry strives towards becoming more digitised, digital twins can help aid this vision. Embracing the goal of a digital future, companies are feeling the benefits from their investment in technology. Smart Construction Dashboard, paired with Komatsu’s intelligent Machine Control, serves as a robust solution for monitoring jobsite progress, supporting Motsch and her peers around the world by providing efficient, real-time insight into current jobsite conditions.
What does the future look like?
As the mining industry strives towards becoming more sustainable, digital twins can help aid this vision. Embracing the goal of a greener future, mining companies are now looking to minimise their environmental impact while undergoing the change to become a brownfield site. By installing Smart Construction Fleet alongside the implementation of Dashboard, site managers can monitor
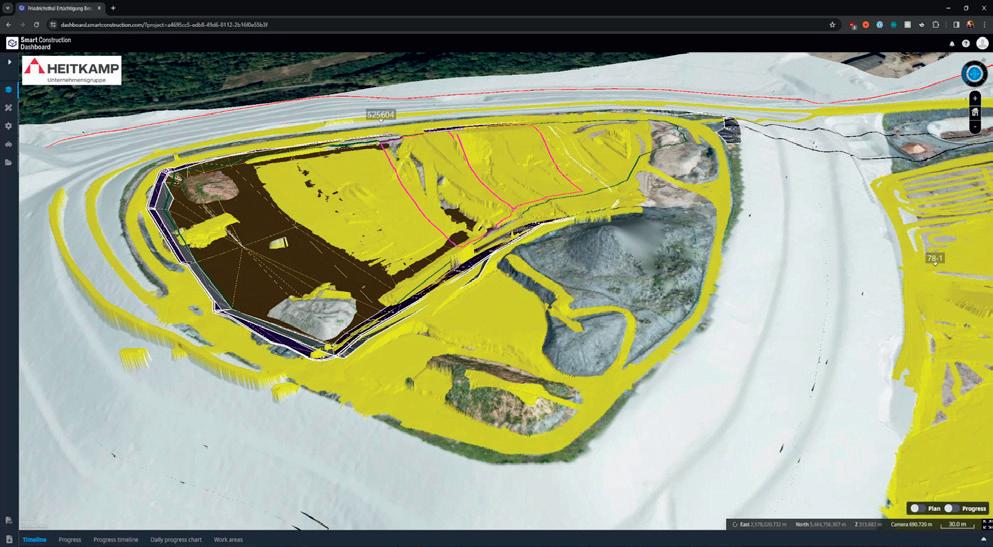
the efficiency of their entire motor fleet remotely. Fewer errors lead to less disruption to the schedule and terrain and digital twins enable straightforward site visualisation which improves decision-making capability, productivity, and effective management of pollutant materials.
Now is the time for the mining industry to optimise the use of resources, make informed decisions in terms of equipment and strategies to account for its impact on the environment, become more profitable, and take steps towards becoming a more sustainable workforce.
References
1. ‘Innovation Forecast 2021: Metals & Mining’, AXORA, (2021), https://assets-global.website-files.com/6491698c2f3d4e71067e4b3f/6 52fab676adae6f5400b37a1_Axora%20Metals%20and%20Mining%20 Innovation%20Forecast%202021.pdf
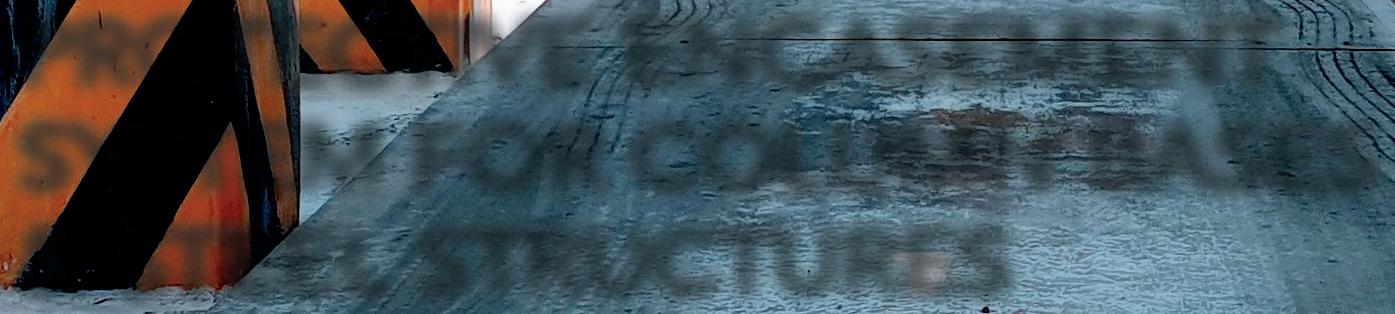
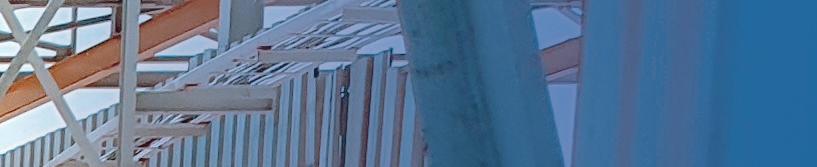

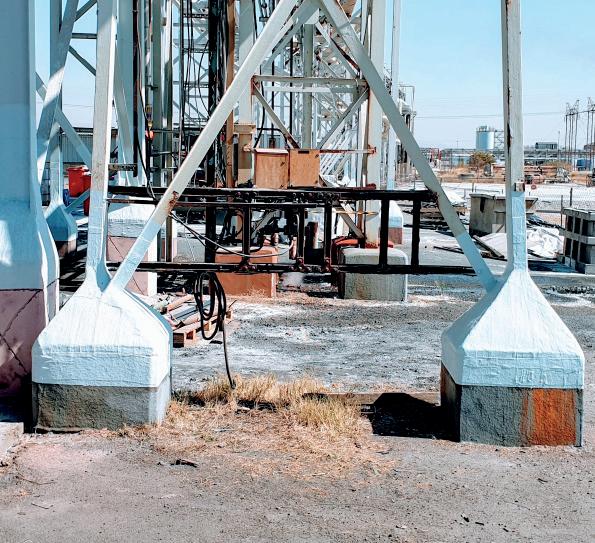
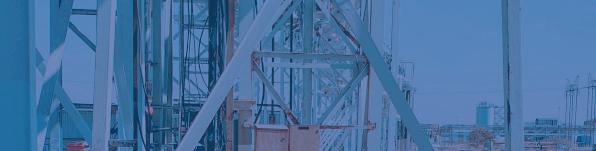

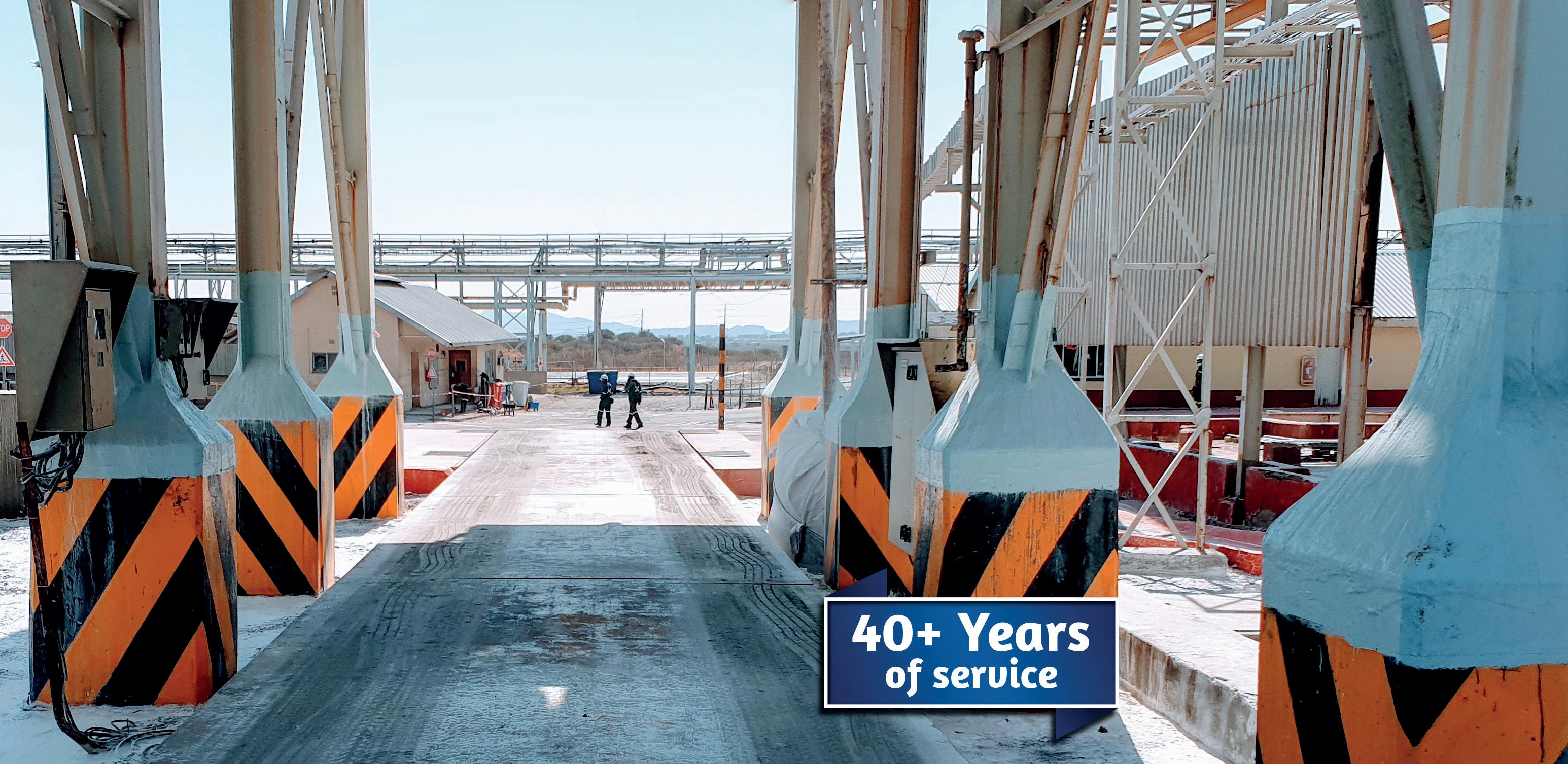
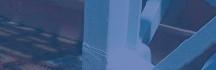
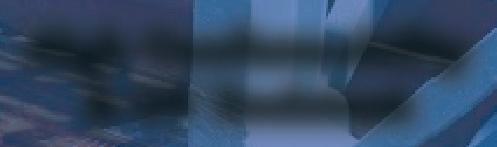


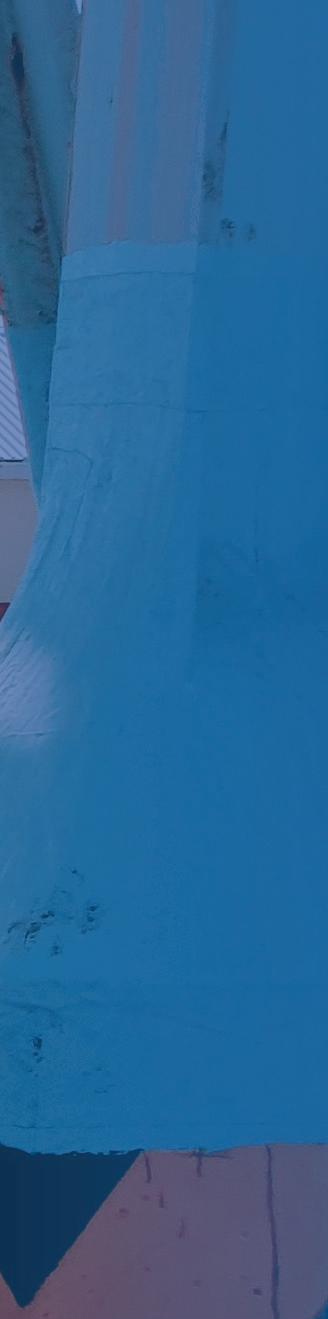
Figure 2. HEITKAMP Smart Construction Dashboard.
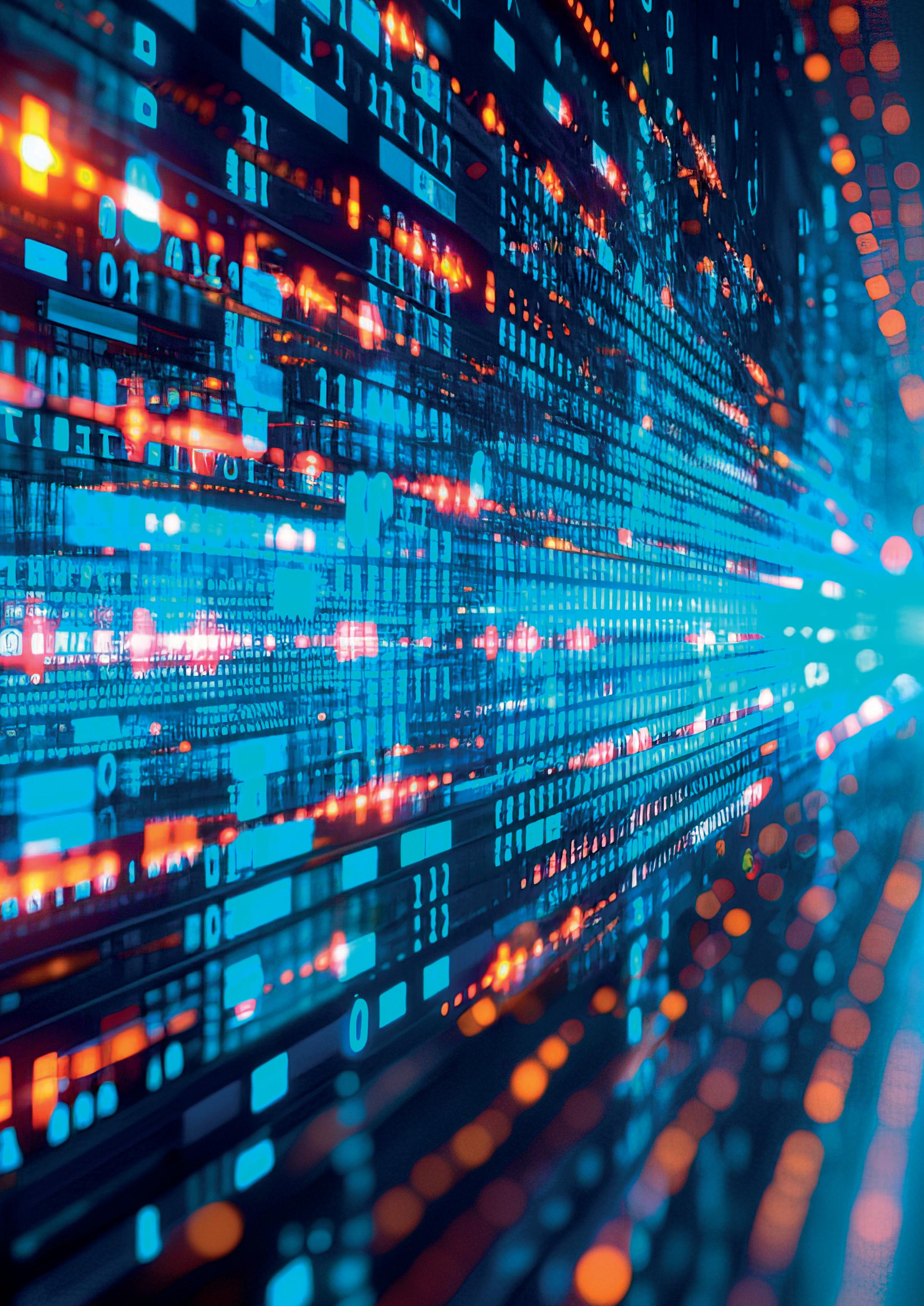
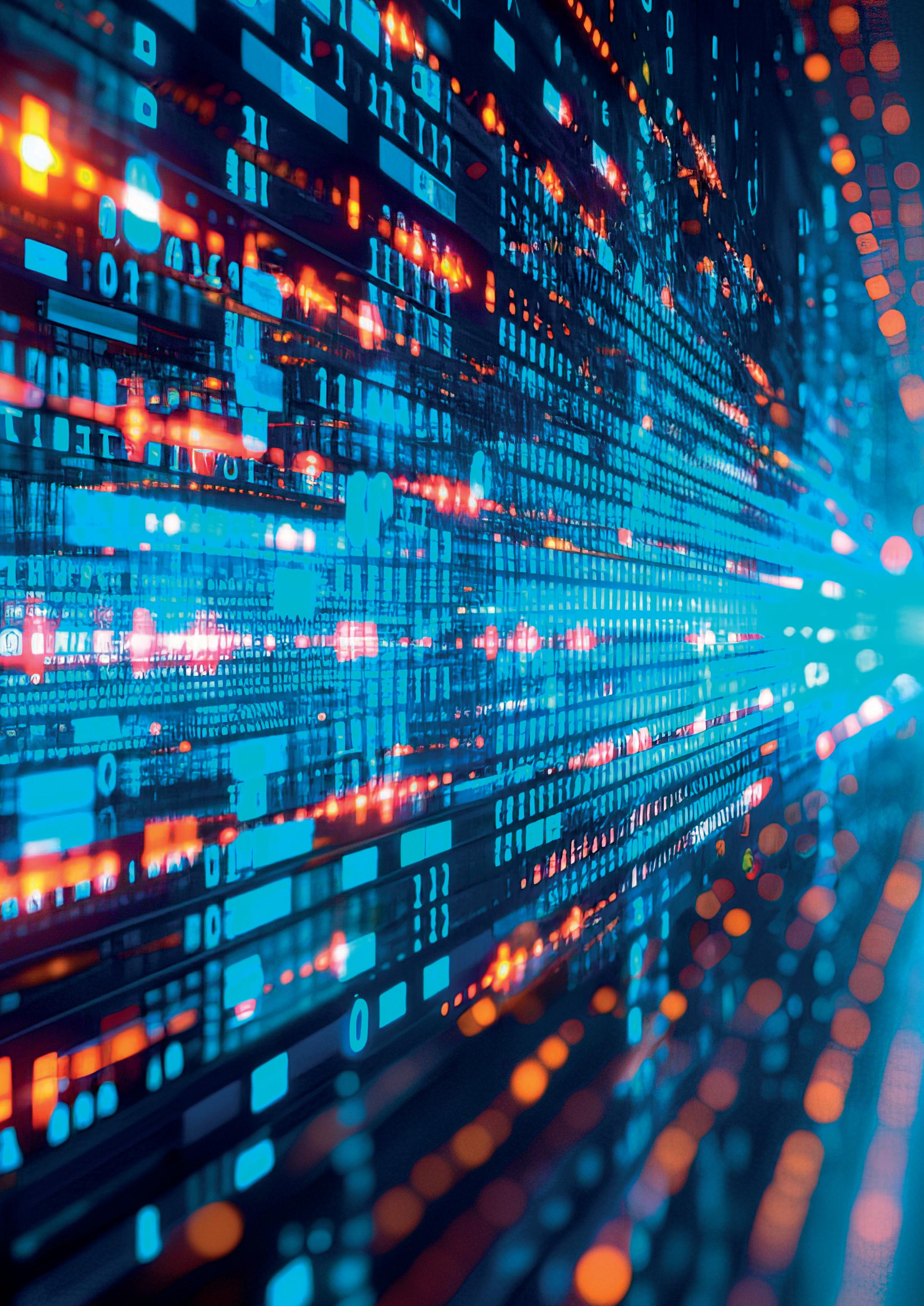
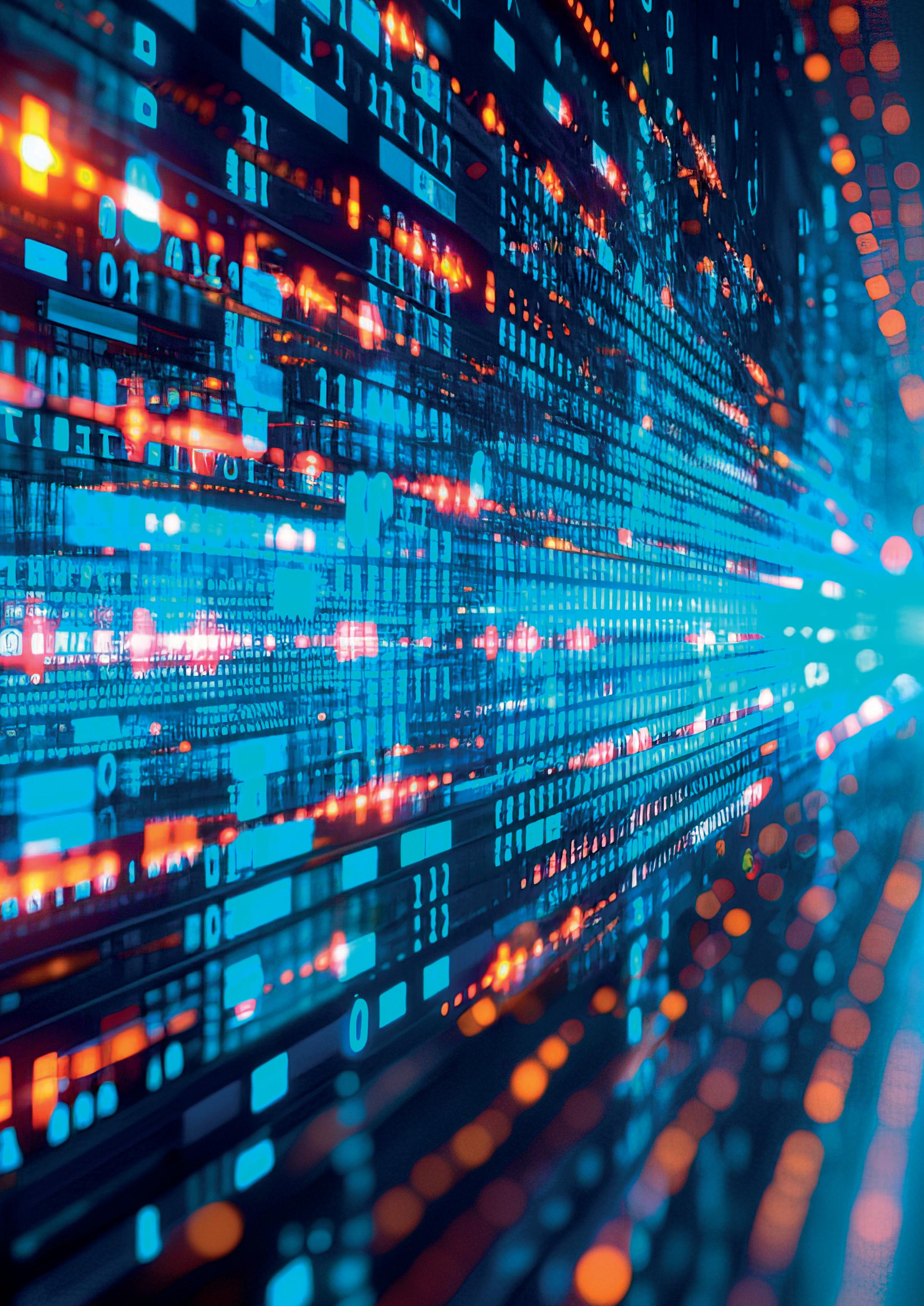
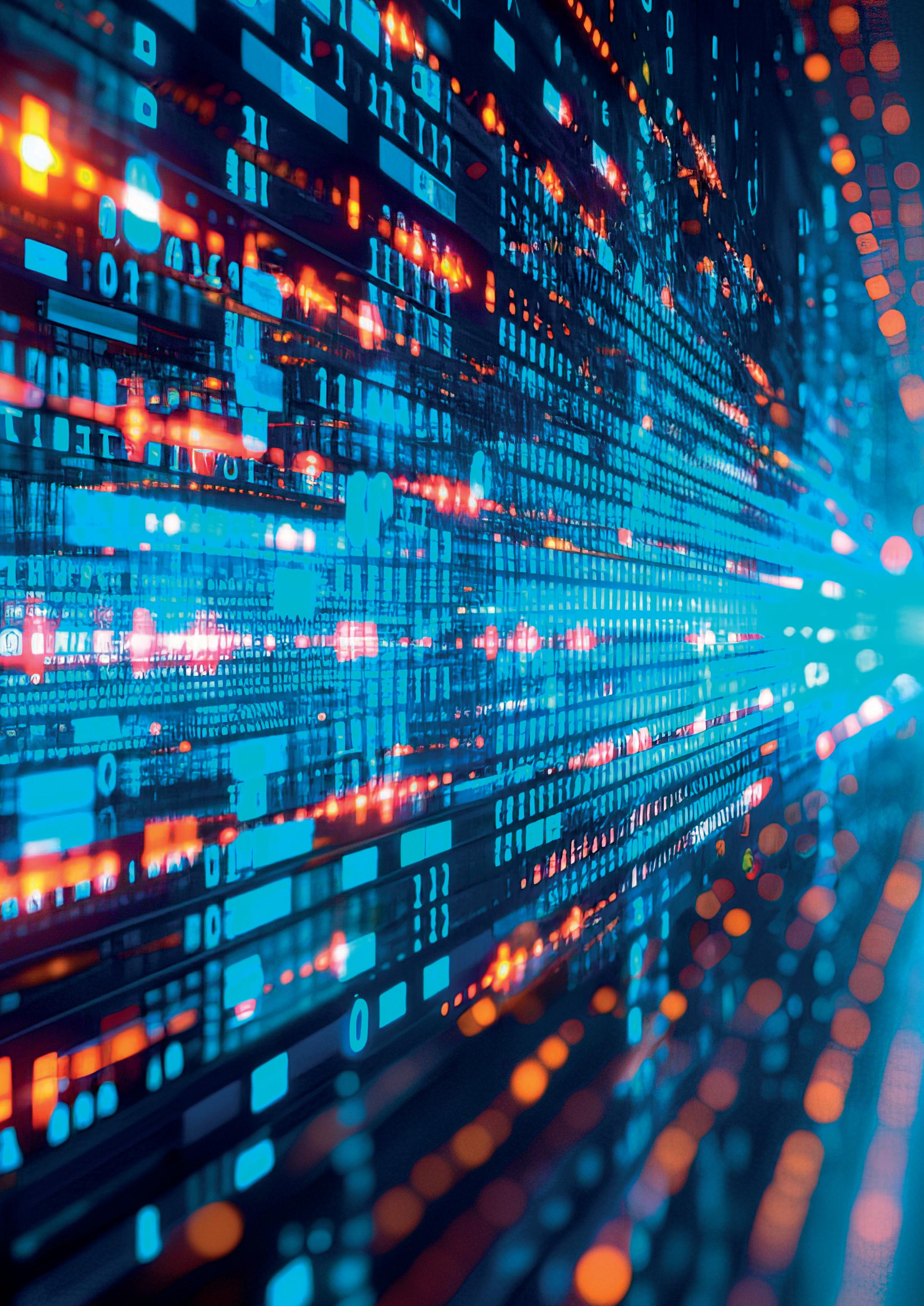
Mariana Sandin, Seeq Corporation, USA, discusses how AI-augmented advanced analytics platforms can deliver new levels of efficiency in mining operations.
A2023 panel titled “The Future of Deployment, Adoption, and Implementation of Technologies in Mining”, focused on how technology is enabling the next generation of miners. One of the more groundbreaking topics discussed was the concept of the augmented engineer, and this highlighted the need to pay close attention to engineers’ ideas about new technologies on the table, especially artificial intelligence (AI).
Nearly 80% of leaders in the industrial trades expect AI to substantially transform their businesses. According to Deloitte, the initial applications of generative AI
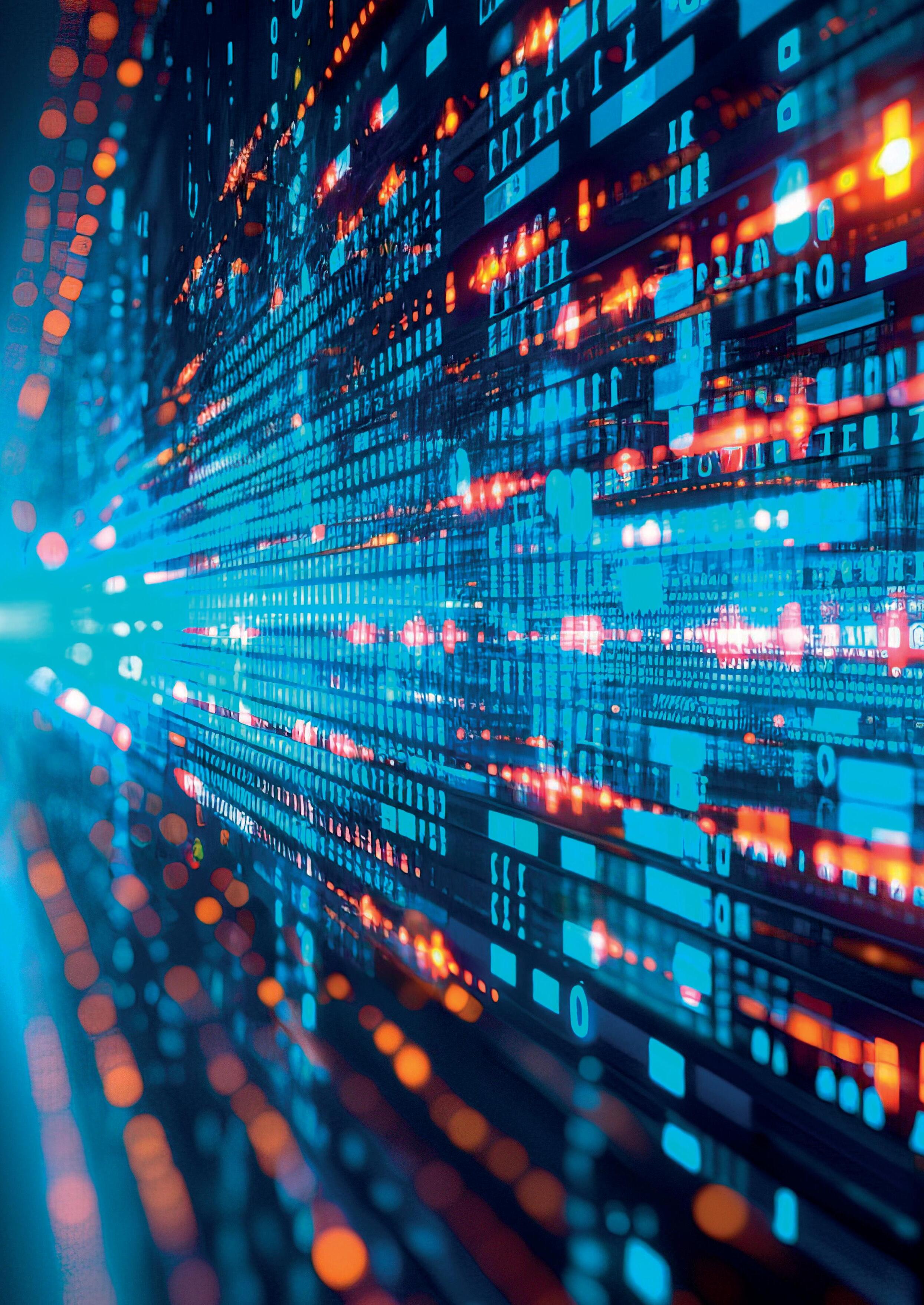
(GenAI) are focused on challenges that will increase bottom line efficiency and productivity, reduce costs, and improve product quality.1
While the AI revolution is exciting, there are many unknown variables and questions regarding ethics, security, and trust that remain unanswered. As industrial organisations prepare to ride the AI wave, setting guardrails is imperative.
Basic AI concepts
A quick internet search – or more likely nowadays, prompting a chatbot – reveals that AI is “the simulation of human intelligence in machines, enabling them to perform tasks that
typically require human cognition, such as learning, problem-solving, and decision-making.”2
Machine learning (ML) was another common industry buzzword just a short while ago. However, in the past two years – since ChatGPT made a splash in the public eye – most companies that were touting their ML, IoT, and digital twin technologies have shifted their moniker to AI as an all-encompassing term for human-like machine intelligence. Although this change in nomenclature for some of the same technologies is correct by definition, it can be misleading.
ML’s focus is on training machines to learn from data and improve in performance over time without being explicitly programmed. Engineers are familiar with the long cycles of preparing data to feed the ML models and the number of iterations necessary for satisfactory model deployment. When applied correctly, ML has proven highly beneficial for industrial organisations – especially in reliability use cases, and in identifying indicators of and helping to prevent pump failure, to name one example. It has also shown value in specific applications, such as metal recovery.
GenAI is the next iteration of operational ML, which facilitates self-machine learning based on patterns in existing data samples. This is the enabler making the ethereal augmented engineer concept a reality by suggesting, answering questions, and explaining how to solve problems, which is accelerating the companionship between human expertise and advanced data analytics.
With 27% of the North American manufacturing workforce set to retire in the next 5 – 10 years, process manufacturers will need to leverage AI to help fill the tacit expertise gap with knowledge derived from operational data. AI is augmenting human capacity to view an everchanging global market and provide solutions to challenges that are not yet visible.
What’s in it for the mining and metals industry?
Global Market Insights estimated that GenAI will grow at a compound annual growth rate of 30.3% over the next 8 years.3 The technology’s primary potential lies in reducing operational costs by 20% and increasing workforce productivity by more than 70%. By 2025, it is projected that over 40% of total cost reductions will be attributed to raw material and energy consumption optimisation, 40% to material movement and logistical enhancements, and 20% to improvements in finished product quality.4 These statistics clearly indicate areas where industrial operations can benefit in the coming years, and AI will play a significant role in transforming the mining, metals, and materials (MMM) industry.
According to the same Deloitte survey, the majority of industrial organisations are more focused on tactical benefits; for example, those related to productivity (56%) and variable cost reductions (35%). Only 29% are applying AI for strategic benefits, such as research and development.
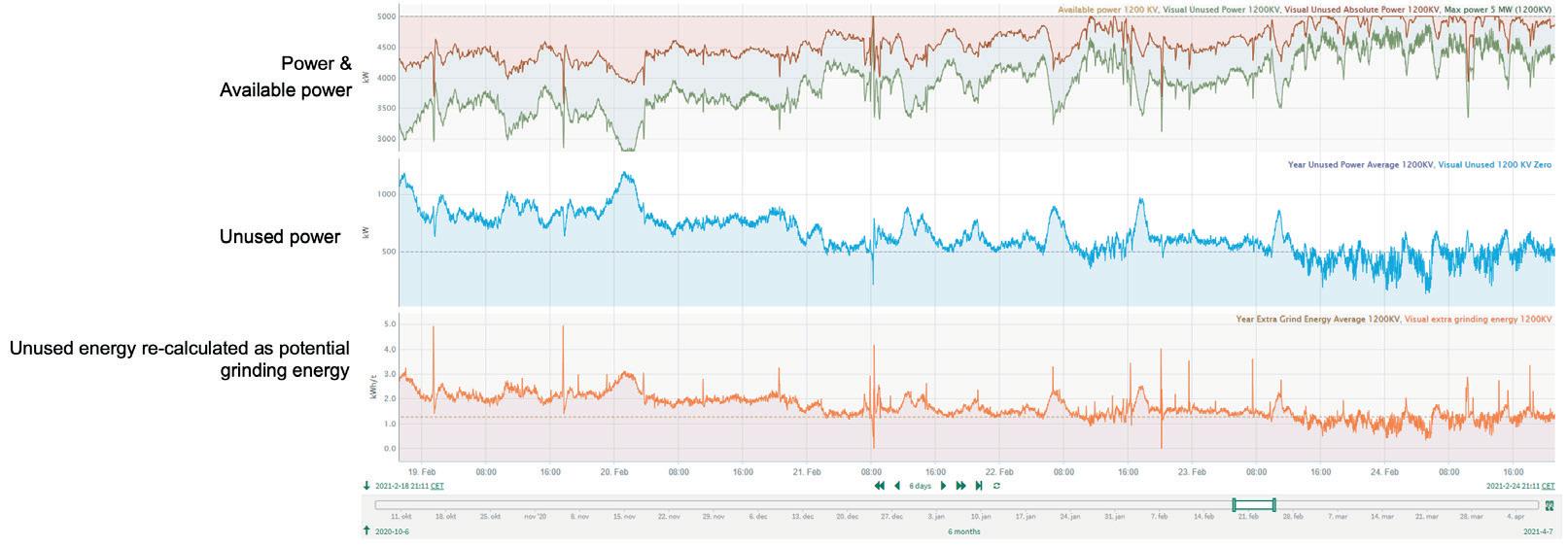
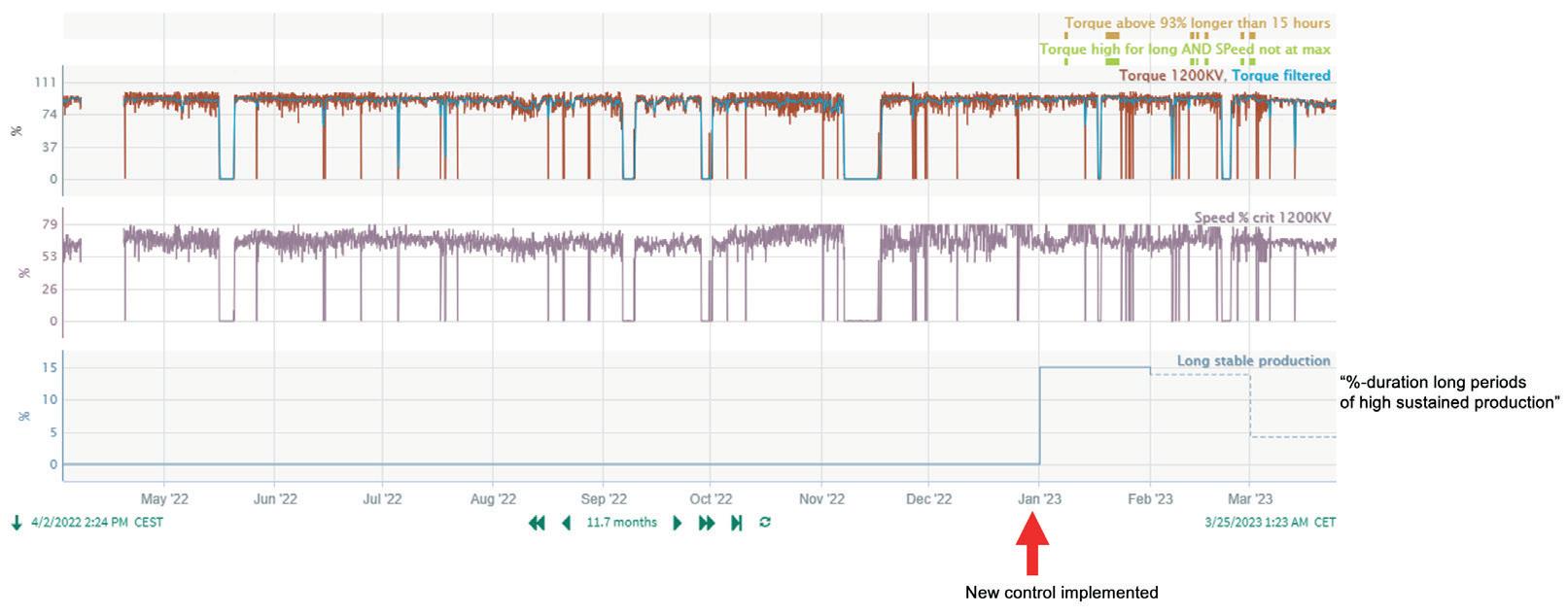
Within the MMM industry, there is an ongoing evolution in analytics and its applications. Implicitly, some operational challenges are more complex than others, and consequently, there is a range of complexity in data analysis necessary to solve different challenges. Next, this article will explore three examples of how different AI subsets are helping organisations within the industry.
Optimising the process at a grinding mill
At Boliden’s Gerpenberg Mill in Sweden, the miner monitored a key performance indicator
Figure 1. Using Seeq, the Boliden Gerpenberg Mill monitored available power in the grinding section to determine the output efficiency impact of changes to the process control system.
Figure 2. Over time, the Boliden team refined the power efficiency analysis, revealing a 15% increase in long, sustained periods of high production.
(KPI) related to energy consumption and torque in the grinding section to pursue a 15% increase in long, sustained periods of high production.
Optimising operations in this semi-autogenous grinding mill is critical because ore grinding is very energy intensive, requiring nearly half of the electric power used for all mineral processing. Ore grinding also dictates the particle size that enters the floatation system, thereby directly impacting mineral recovery efficiency. This procedure is the bottleneck in almost every mineral processing plant, so any improvements to this step are felt in full force at the output stage. For example, increasing ore grinding production by 1% increases overall output by 1%.
The company used Seeq, an AI-augmented advanced analytics platform, to identify ways of increasing sustained periods of high production, which provide a more efficient output-to-energy ratio. The first step was creating and running a simulated model of the grinding process to benchmark current operations against potential changes in the process control system, and to identify scenarios that would increase production. The solution monitored historical data for both absolute and relative power distribution utilisation to calculate available power, the KPI used to determine the effort’s success.
With this KPI available, the Boliden development engineering team was able to quantify the benefits of changes to the advanced process control system (Figure 1).
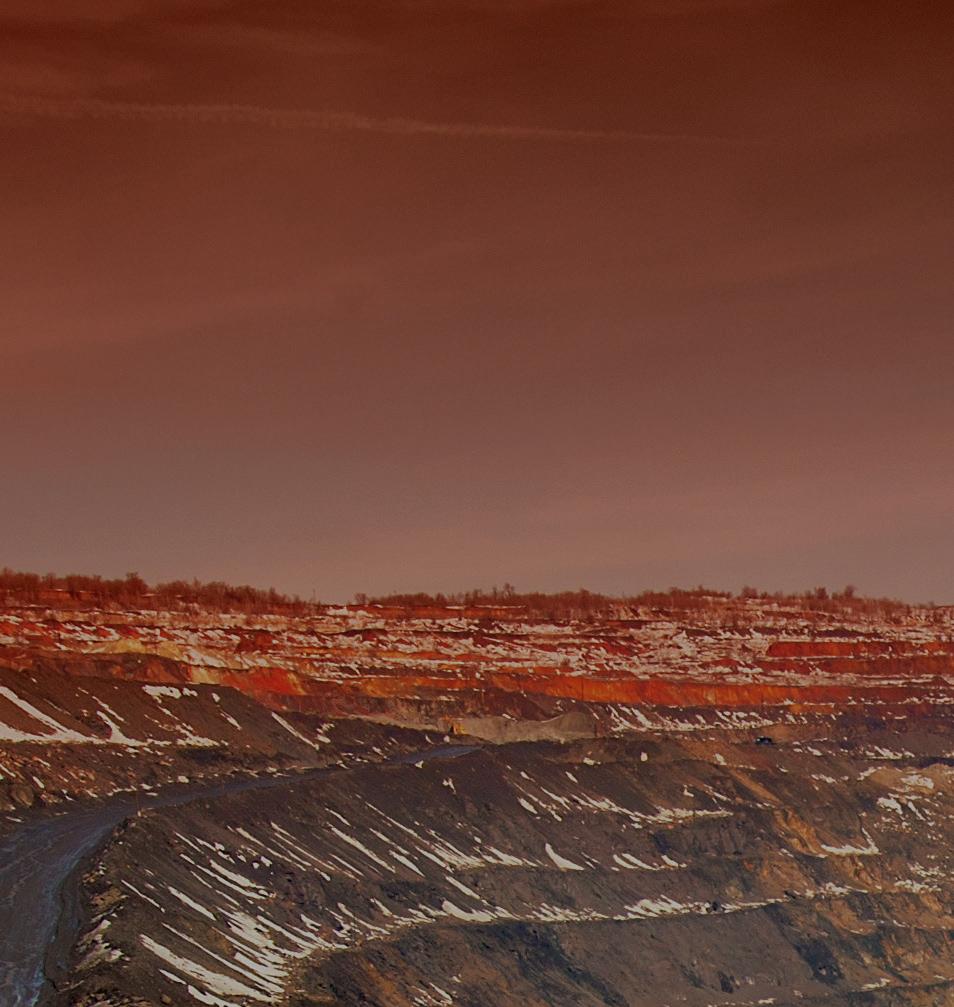
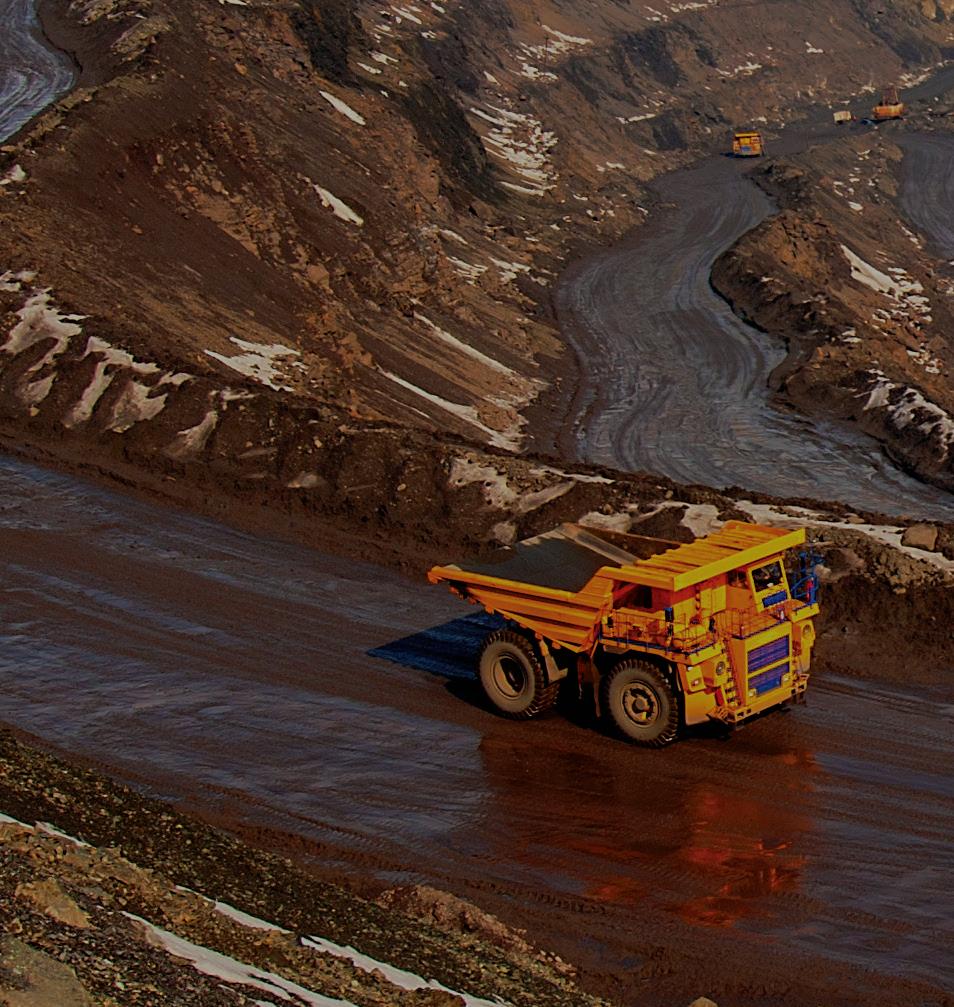
It also enabled the organisation to improve, refine, and add nuance to the analysis, including setting up conditions to determine and correct load limitations for a more accurate evaluation (Figure 2). The data revealed a 15% increase in long, sustained periods of high production.
Increasing water recovery at a copper plant
A copper concentration plant in South America leveraged Seeq with gradient boosting ML to improve solids and water recovery in its processes by 3%.
The quest for improved efficiency began with the assessment and contextualisation of data processed by the advanced analytics solution. Signal preprocessing included correlation validation, dependent variable selection, and a simple regression model to confirm technical feasibility. After establishing these baseline metrics, the team applied a more robust XGBoost model.
This model predicts the percentage of solids in the discharge of tailings thickeners based on prior conditions like grinding speed, treatment, granularity, hydrocyclone pressure, and mineralogy of the plant feed. The percentage directly correlates to water recovery, and the model’s predictions provide approximately two hours of lead time for possible destabilising events in the thickeners, thus increasing water recovery and avoiding a loss in separation efficiency.
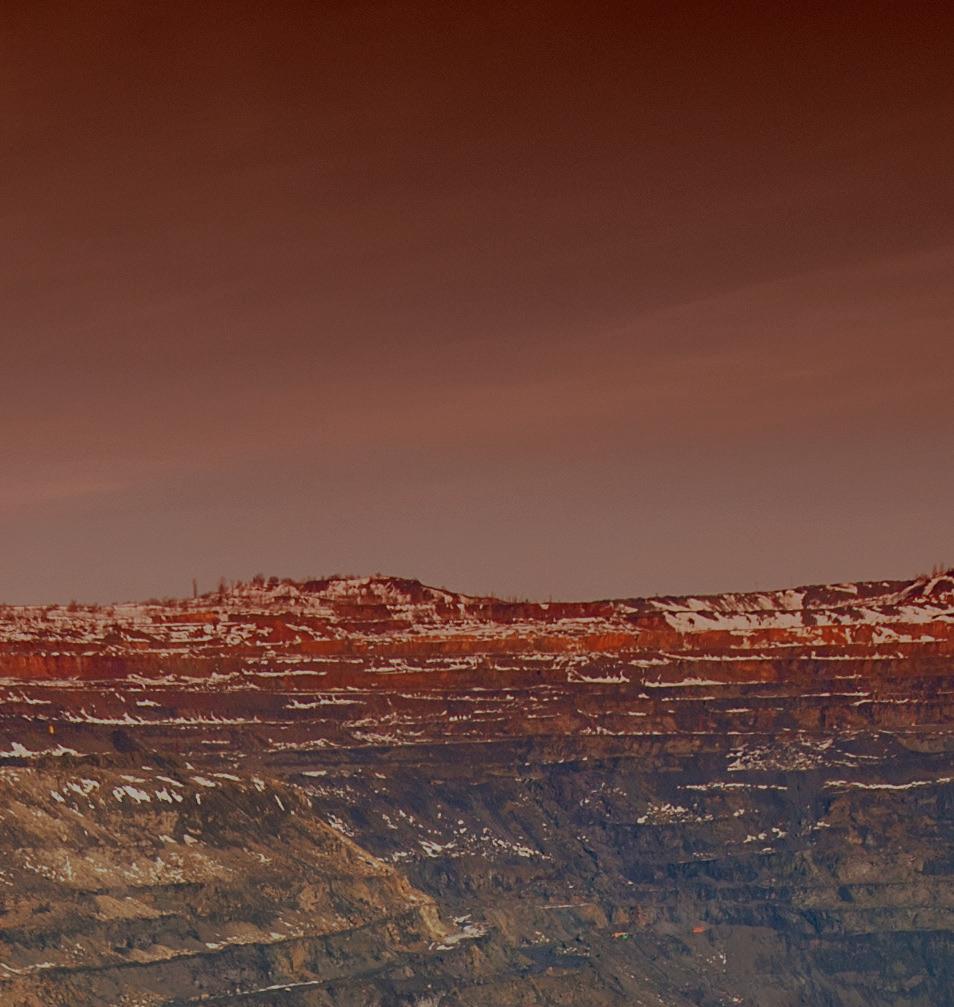
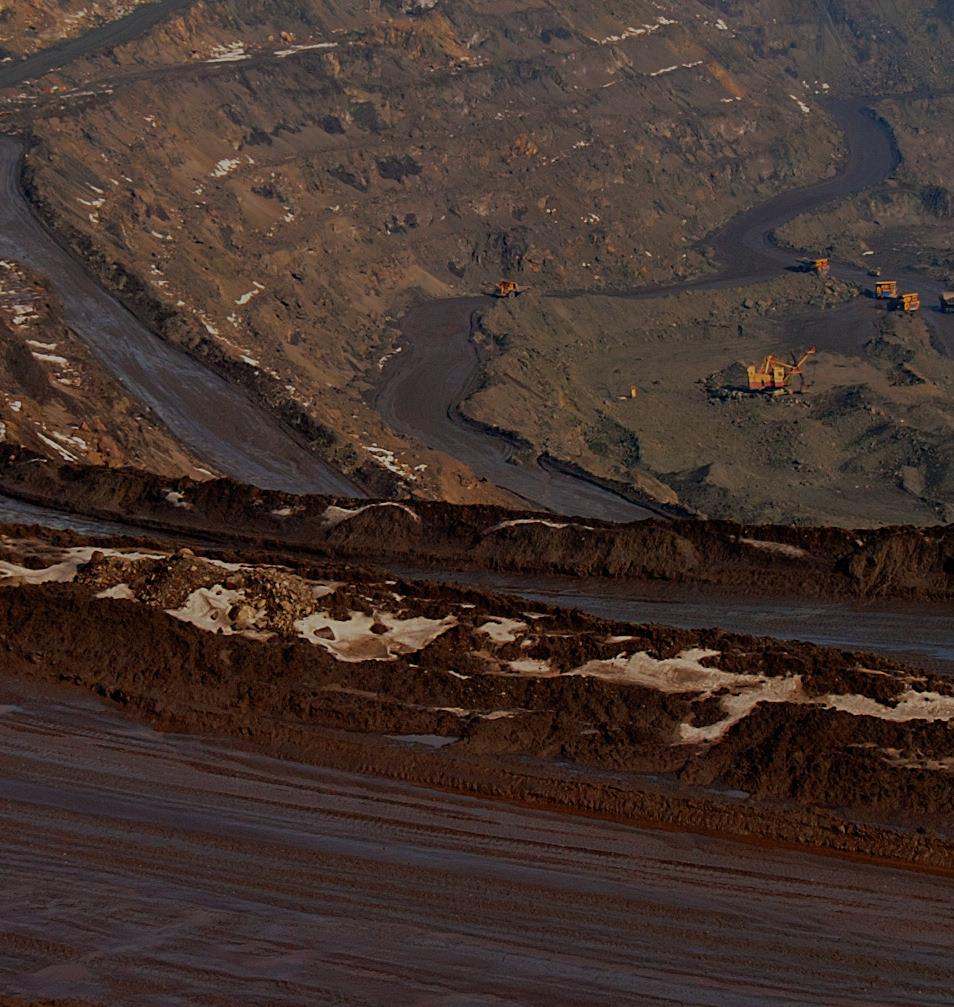

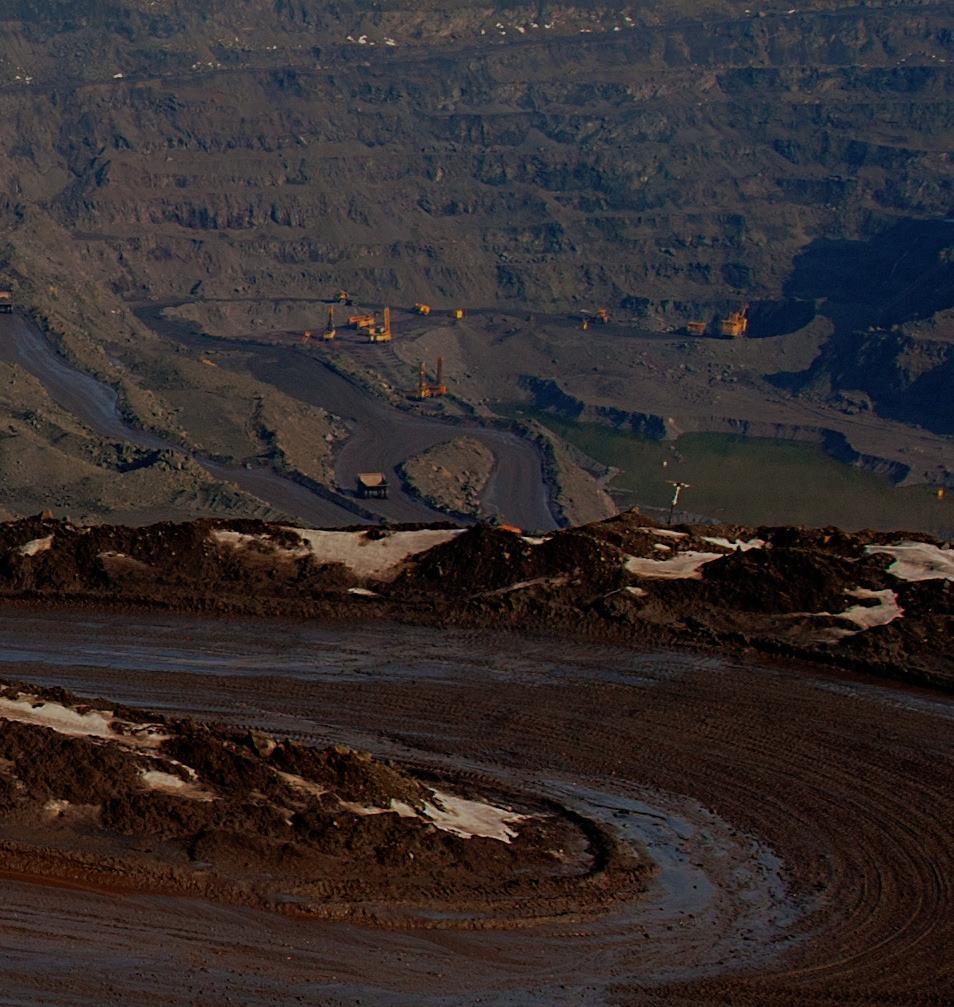

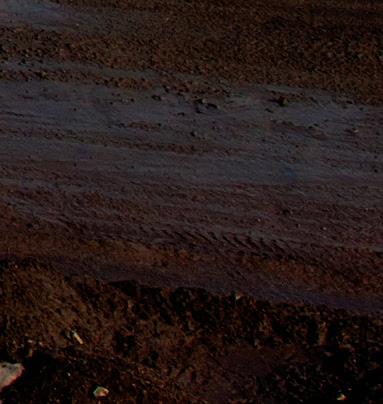
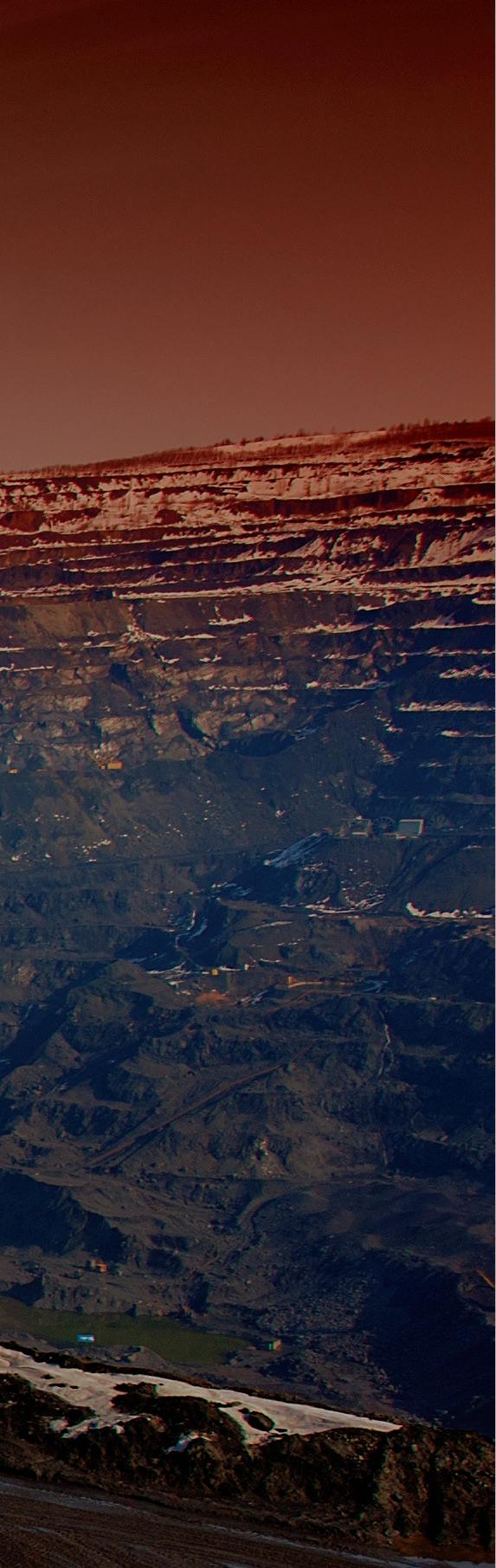
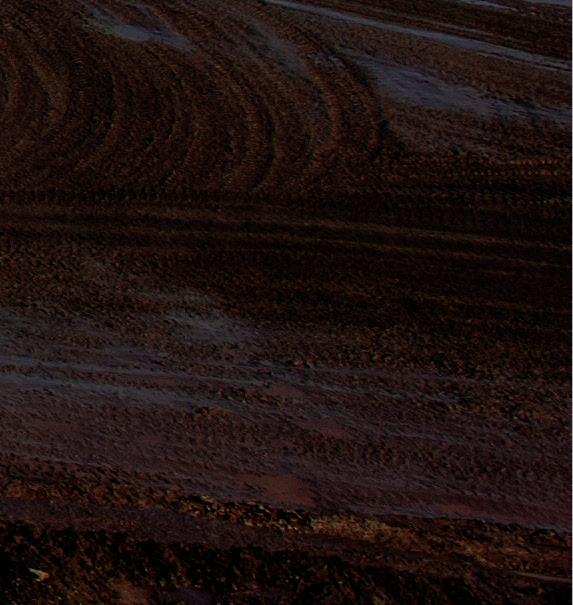
The grinding speeds were also made visible by the advanced analytics solution, and the XGBoost model helped identify controllable variables to stabilise the system, which reduced the need for freshwater makeup in the grinding process. This is a textbook example of plant optimisation’s impact on achieving sustainability targets, such as water reutilisation.
Immortalising knowledge
Many mill product suppliers are exploring methods of incorporating GenAI into their enterprise analytics solutions to make it available for current and new users. The application of large language models (LLMs), which form the base for GenAI, speeds the adoption rate by at least eight times, based on early adopters’ feedback.
One supplier uses an LLM to embed its experts’ knowledge into operational data available in its datastores. With many of its subject matter experts (SMEs) expected to retire in the next two years, several of the supplier’s facilities will lose their full-time, resident SMEs. These experts traditionally performed the analytics necessary to identify deviations in data, and they executed root-cause analyses for abnormal operating conditions.
LLMs are trained in persona, question-asking, and tone, enabling GenAI to answer questions like, “What is wrong with my continuous casting?”. Advanced analytics solutions can then pass along the conditions and properties from time periods of interest to the GenAI application to respond to the prompt (Figure 3).
The AI assistant built into Seeq has access to models, training documentation, and graphs that are woven into prompt responses. For example, when asked about problem sources, the system can quickly display signals that prove violations in the maximum residence time, and extrapolate its repercussions in the daily production target. It can also describe the violation’s leading indicator, such as lower-than-normal feed flow and control valve position setpoints.
Other milling suppliers are taking a more conservative approach, selecting several signals and asking a few leading questions. For instance, this approach can be used
to optimise chemical consumption during washing phases. In these cases, the advanced analytics solution’s AI assistant is expected to respond with known relations between signals in the context of different operational modes, such as idle or running. Following the initial question, SMEs prompt the assistant with additional questions to further refine the process, increase asset efficiency, reduce energy consumption, minimise the use of chemicals, and extend the assets’ life.
By following this method, the LLM is trained to optimise production based on the mode of operation, chemical mix, and product quality. This prescriptive approach then becomes available for others also using the model.
Adopting AI in the mine
Focusing on tactical benefits is an effective strategy to justify the application of AI at scale. Organisations frequently find success employing the ‘think big, start small’ approach, garnering buy-in for new technologies that drive innovation and change. Additionally, this approach helps build both skills and the organisational structure to support strategic efforts in the future.
Hesitations to embrace AI are not unfounded, especially surrounding intellectual property privacy concerns. For this reason, it is crucial for organisations to assess both the benefits and the risks of implementation, and to mitigate the latter. For example, Seeq segregates AI model data by organisation so it cannot be used to train public or general models.5
By combining GenAI with advanced analytics and mindfully integrating this union into their workflows, miners can unlock new levels of efficiency, accuracy, and innovation to stay ahead in an increasingly competitive landscape.
References
1. DUTT, D., AMMANATH, B., PERRICOS, C., and SNIDERMAN, B., ‘Now decides next: Insights from the leading edge of generative AI adoption’, Deloitte, (January 2024), https://www2.deloitte.com/ content/dam/Deloitte/us/Documents/consulting/us-state-of-gen-aireport.pdf
2. ‘What Is Artificial Intelligence (AI)?’, Investopedia, (9 April 2024), https://www.investopedia. com/terms/a/artificialintelligence-ai.asp
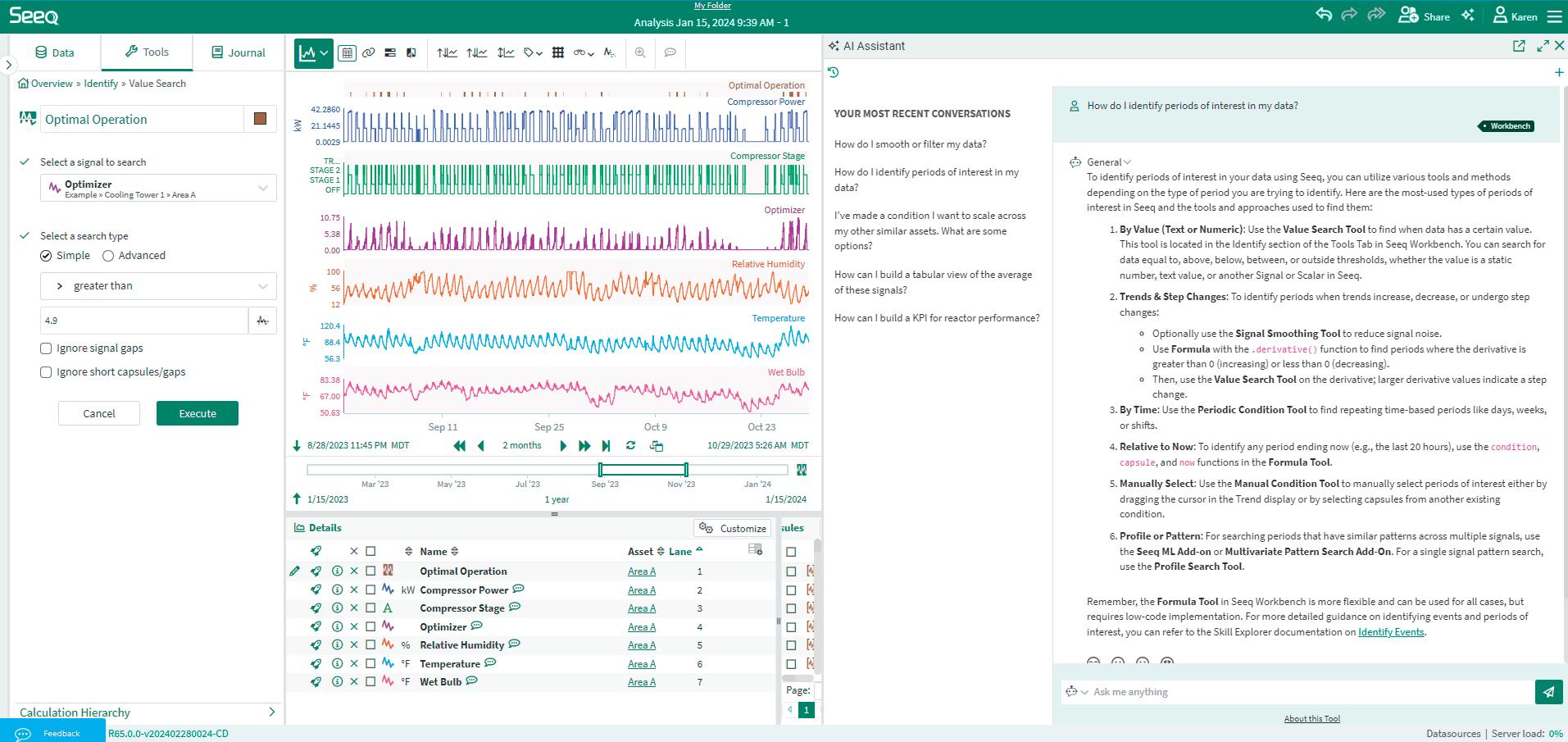
2. WADHWANI P., ‘Generative AI Market Size’, Global Market Insights, (June 2023), https://www.gminsights. com/industry-analysis/ generative-ai-market
3. WADHWANI P., ‘Artificial Intelligence in Manufacturing Market Size’, Global Market Insights, (February 2019), https:// www.gminsights.com/ industry-analysis/ artificial-intelligence-ai-inmanufacturing-market
4. ‘Seeq Drives Innovation With Generative AI’, Seeq, (25 August 2023), https://www. seeq.com/resources/blog/ Seeq-Drives-Innovationwith-Generative-AI/
Figure 3. GenAI built into advanced analytics platforms augments engineering capabilities to extract more value from industrial data.
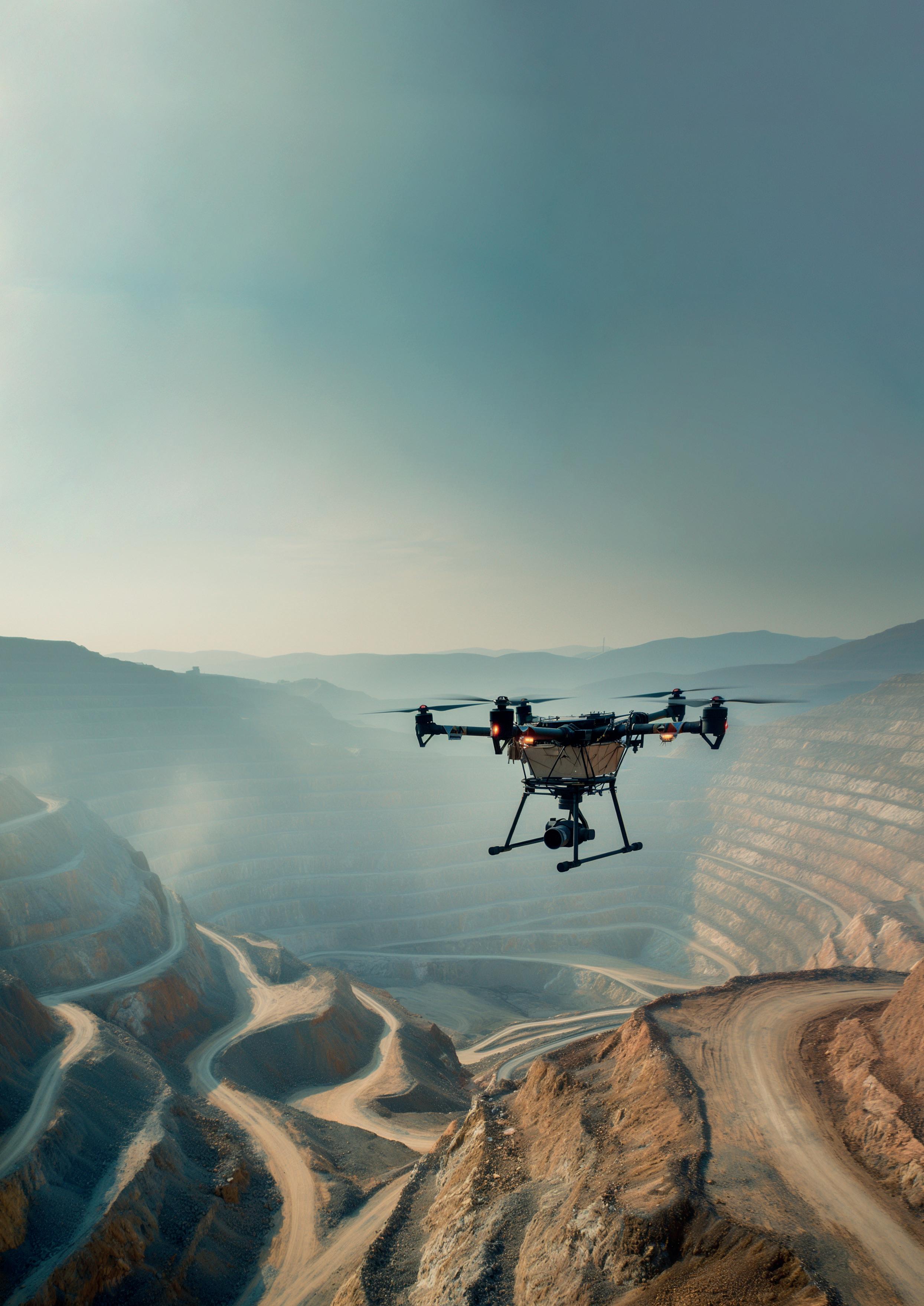
Jaime Laguna, Oil and Gas Development at Nokia, USA, describes how Mining 4.0 connected drones are helping to pioneer worker safety and productivity in the mining industry.
As mines ramp up production levels to meet the needs of a net zero economy, they must also look at their own environmental, social, and governance (ESG) data, finding ways to reduce emissions, enhance worker safety, and protect the environment in which they operate. One example of a technology that can help unlock operational efficiencies, while complying with new regulations, is the connected drone.
Valued at US$1.18 billion in 2023, the global drone for mining market size is expected to reach US$5.54 billion by 2030. 1 Connected drones are just one of the many compelling use cases that the mining industry can benefit from. The digital transformation of mines, also known as Mining 4.0, will allow companies to take advantage of automated and tele-remote operations, remote monitoring of connected IoT devices, and more to achieve their safety, sustainability, and productivity goals.
Connected drones can deliver value for mining companies even before mineral extraction begins. Equipped with a mix of payloads including cameras and sensors, such as magnetometers, drones can be used to accelerate the site survey selection process and mapping, allowing teams to access and use data more quickly, safely, and cost-effectively compared to traditional aerial and ground surveys.
Using Geographic Information Systems (GIS) to process this data, companies can make faster site decisions with a more accurate picture about
mineral deposits. Once construction begins, drones can be used to manage site inspections before being put to work as operations commence.
Increasing worker safety through connected drones at mines
Even with greater safety regulations in place today, mining operations can be perilous. Rockfalls, gas leaks, blasting activities, cave-ins, huge industrial haulage trucks, drills, and other equipment pose hazards for workers.
Inspections play a vital role in alerting teams to these hazards, but traditionally still require humans to manually visit underground caves, blasting areas, tailings, and other areas of a mine to assess if an area is stable for work to continue to maintain regulatory compliance and to identify threats to the environment. Using drones to carry out these inspections drastically reduces risks to the workforce.
Drones can, for example, be deployed to capture images and video underground to determine if caves or pillars should be reinforced following blasting activity, to prevent cave-ins. They can be equipped with thermal feeds and sensors to detect hazardous gases; and/or cameras with video to better assess the condition of pit walls or haulage routes following periods of adverse weather or rockfalls, in order to determine whether it is safe to transport minerals.
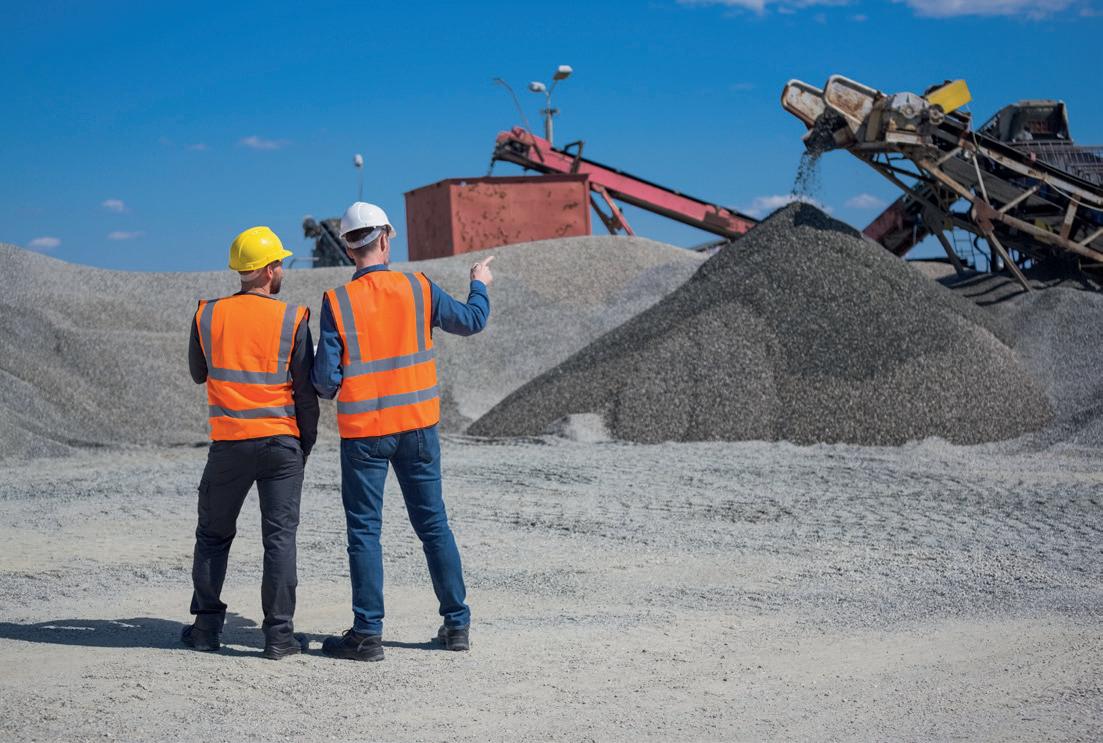

Connected drones deliver more accurate measurements of stockpiles and remove the need for people to navigate these large crumbling structures. They can be dispatched to monitor tailings, as well as water levels, giving companies access to greater amounts of data so that they can more accurately monitor change over time. Critically, they can more rapidly identify the potential for hazardous events, such as flooding, and implement preventative measures.
If an incident occurs, drones can be dispatched to conduct search and rescue missions beyond visual line of sight, helping teams to both identify the locations of injured colleagues and deliver medical equipment more quickly and safely than would be possible by foot or vehicle. They can also be used for safety patrols and surveillance. This allows companies to enhance worker safety and protect others in the vicinity of a mine, allowing them to equip drones with loudspeakers to warn potential trespassers of the hazards ahead.
Increasing productivity through greater data awareness
As well as enhancing safety, the ability to capture multiple images more rapidly across a vast mine site makes it easier to understand scale and calculate stockpile volumes over time, allowing companies to better inform markets about mineral availability. By using drones to monitor the
Figure 1. Mining 4.0, or the digital transformation of mines, enables companies to leverage automated operations, tele-remote systems, and remote monitoring of IoT devices to meet safety, sustainability, and productivity goals.
Figure 2. Implementing technologies like connected drones in mines can optimise operations, reduce emissions, enhance worker safety and protect the environment, streamlining site surveys for quicker, safer, and cost-effective data access and utilisation.
condition of haulage routes as well as inspect conveyor belts, tailings, and dams, teams can make more informed decisions about journey times or the need for predictive maintenance, so that productivity is not impacted by downtime, costly repairs are avoided, and equipment lifecycles are extended.
By taking advantage of drones that can fly beyond visual line of sight (BVLOS), tasks such as volumetric measurement, perimeter patrols, and other monitoring activities can be managed more frequently and efficiently and with less risk to the workforce.
With more data at their fingertips, mining companies can make better informed decisions that do not only positively benefit worker safety and productivity, but that also aid their sustainability journey and goal achievement.
Enhancing ESG reporting
A net zero economy can only be achieved through the adoption of more sustainable power sources and vehicles, and this is creating huge demand for a variety of raw materials including lithium and cobalt. Even as they are being asked to ramp up productivity, mining companies are coming under greater pressure to show stakeholders how they are protecting the Earth’s resources.
Remote monitoring of tailings, dams, streams, caves, and other areas around a mine using drones will allow
teams to better identify trends and more rapidly implement preventative measures to protect the environment. They can be used to monitor wildlife or to scare them from blasting sites and, as previously noted, to prolong the lifecycle of equipment, through remote inspections and the implementation of predictive maintenance activities. Companies can use the data gained from drone flights to aid ESG reporting and show how they are achieving their goals.
Supporting connected drones using the right technology mix
How mining companies choose to implement drones will depend on their unique operational goals, but for maximum impact they should choose solutions that give them the greatest flexibility. Drones that allow companies to use a mixture of applications and payloads will allow them to achieve their goals more rapidly, as will those that operate reliably BVLOS, in the largest radius for the longest flight time. Given the harsh environments and extreme temperatures at many mining sites, it is also imperative that drones and their docking stations are ruggedised and built to withstand those conditions.
For mining companies to leverage the true benefits of drones, they must be supported by the right mix of communications technologies from the outset. Wireless communications networks are vital, and there are many
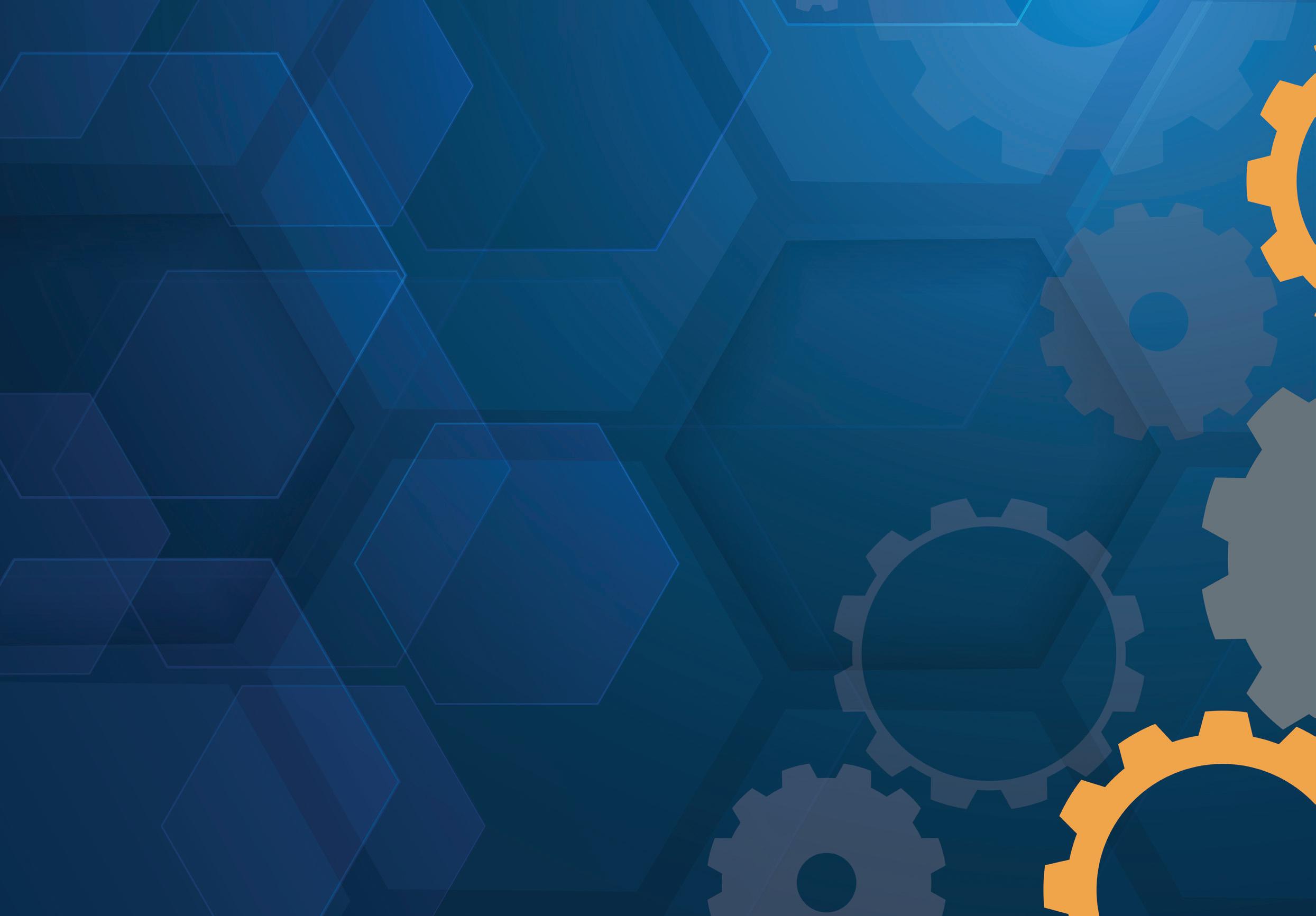
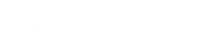
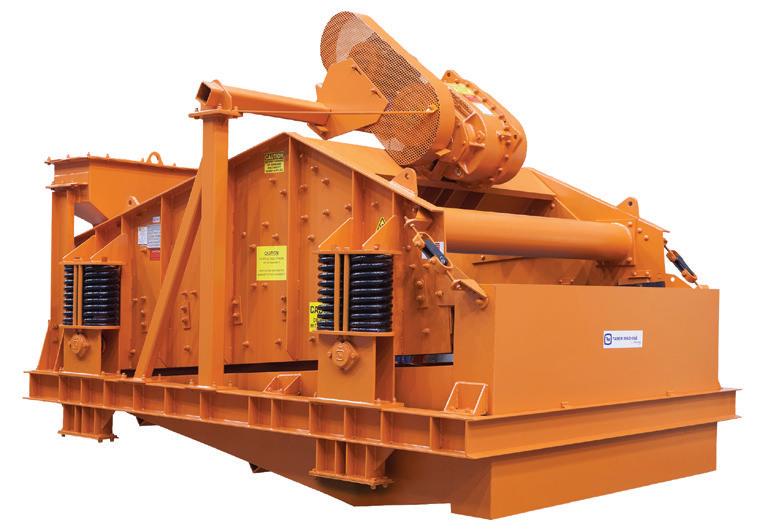
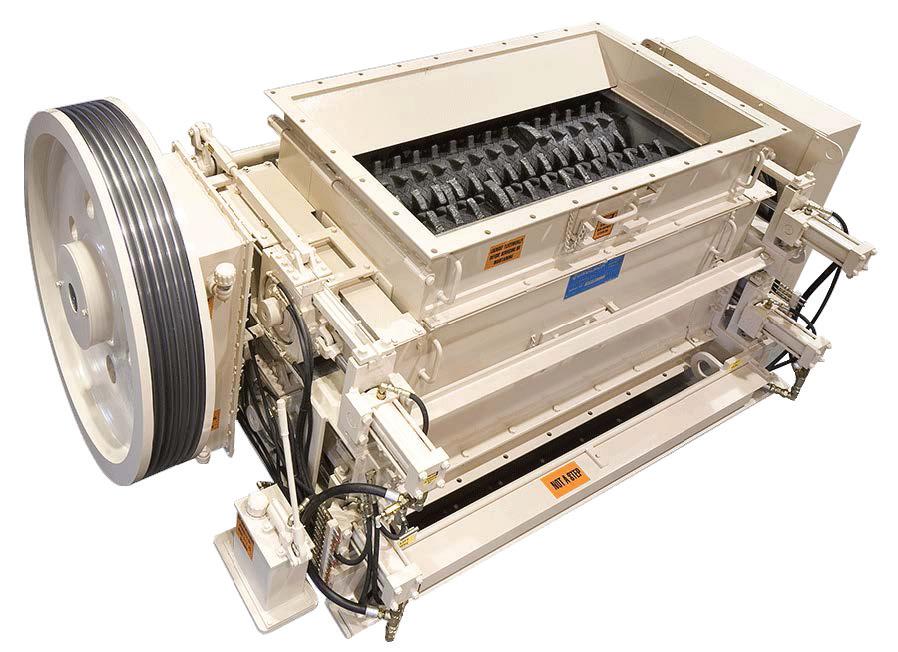

Our OEM spare parts are always a better choice: better value better performance better safety better service and engineering support with every purchase.
reasons why many mining companies are now choosing to implement 4G/LTE and 5G private wireless networks to support their critical infrastructure.
Private 4G/LTE and 5G wireless networks hold significant advantages over technologies such as Wi-Fi, as they are less susceptible to interference from metal structures or blasting activities, ensuring drones remain connected to the network. The superior coverage and capacity offered by 4G/LTE and 5G radios mean fewer radios than Wi-Fi access points are required to connect drones across greater distances. Drones can be operated remotely by users with access to that private wireless network, allowing teams both at the mine and at base sites to operate them and access their data.
Moreover, 4G/LTE and 5G private wireless networks do not just provide robust reliable connectivity for beyond line-of-sight drone flights. Used in conjunction with industrial edge on-site processing, managed closer and closer to the source using micro edges, companies can grow their Mining 4.0 capabilities as their needs evolve; implementing autonomous operations and greater numbers of IoT sensors, while prioritising network resources to ensure mission-critical services are always supported for the greatest safety and operational efficiency.
Additionally, by choosing a private wireless network that also delivers support for Wi-Fi, companies can use resources more efficiently, reserving low latency private
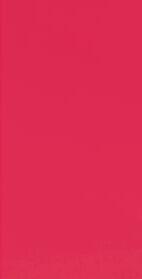
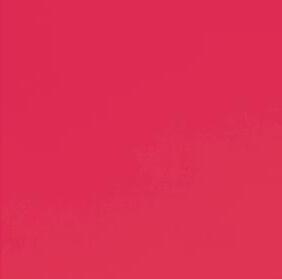
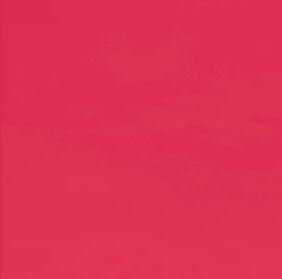
4G/LTE and 5G wireless to support mission-critical OT use cases and running IT services over Wi-Fi.
Accelerate return on investment leveraging a pre-integrated end-to-end drone solution
It is clear that the case for using connected drones to assist mining safety, increase productivity, and make progress toward companies’ ESG goals is a compelling one. To access drones’ full potential, they must be supported by robust, reliable 4G/LTE and 5G private wireless networks and industrial edge processing. By adopting this technology mix in a subscription model or ‘as-a-service’, companies can expand Mining 4.0 use cases as their needs evolve, in the safest, most effective way.
To accelerate the implementation of drones, as well as return on their investment, mining companies should team up with providers that offer end-to-end drone solutions that are pre-tested and pre-integrated with a private wireless platform. Companies that enhance their service offerings with compelling applications will have the most flexibility in achieving their specific safety, productivity, and ESG goals.
References
1. ‘Global Drone for Mining Market By Type (Fixed Wing, Multi-rotor), By Application (Blasting, Measuring), By Geographic Scope And Forecast’, Verified Market Reports, (January 2024), www. verifiedmarketreports.com/product/drone-for-mining-market/
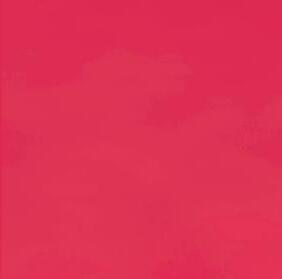
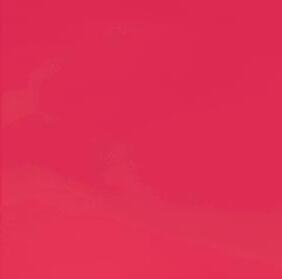
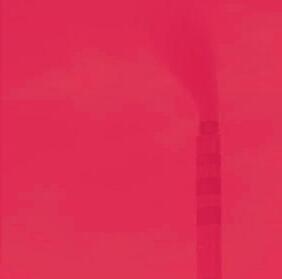
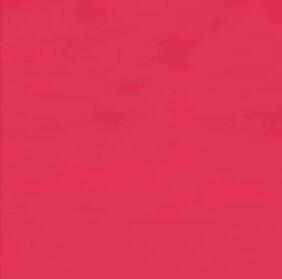
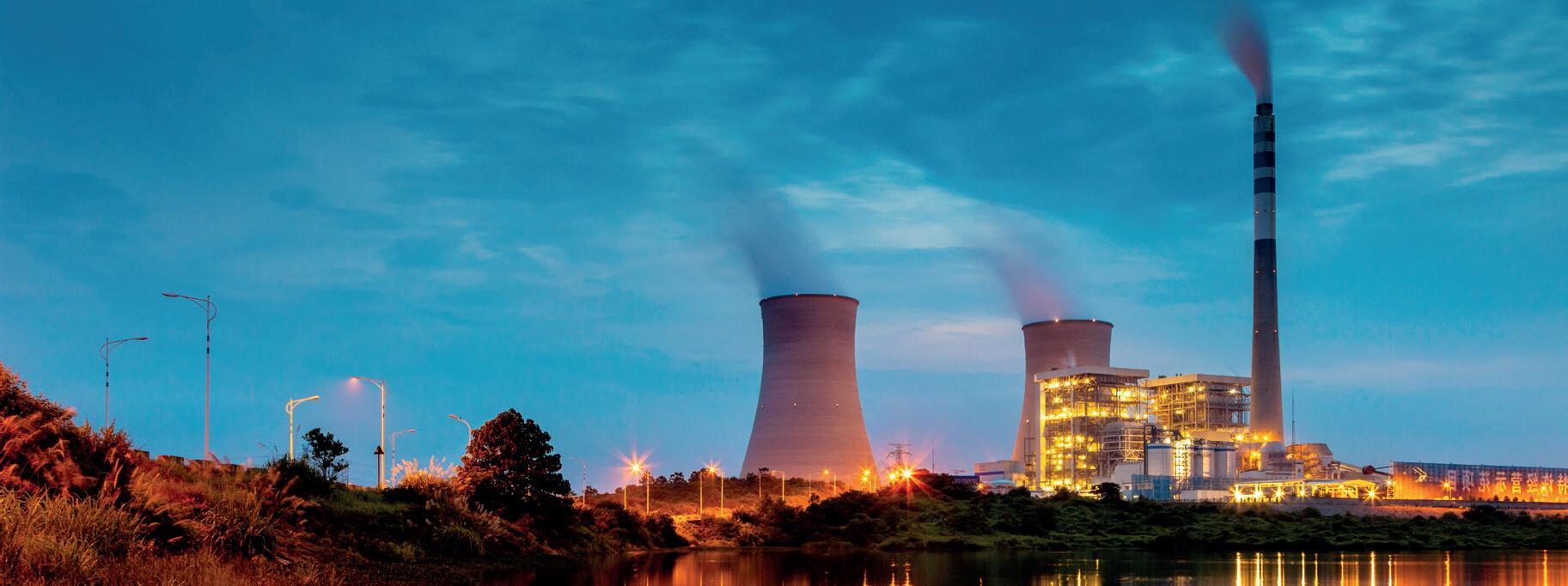

Dr Graham Howell et al., SRK Consulting, examine the importance of a comprehensive knowledge base through the tailings storage facility lifecycle.
As industry standards for tailings storage facilities (TSFs) become more stringent, compliance is requiring an ever-wider breadth of scientific and engineering disciplines to be integrated. It is also demanding a thorough philosophical reassessment of design and analysis processes through the TSF life cycle.
The TSF life cycle involves conceptualisation, preliminary and final design, initial starter construction, deposition (construction), continuous monitoring (surveillance), closure, and post-closure. It is a process that
could cover many decades and is affected by changing conditions that include metallurgical technology, changes in orebody geology, global environmental trends, and legislative amendments.
Interventions such as the Global Industry Standard on Tailings Management (GISTM) emphasise the need for a comprehensive knowledge base for planning and decision-making. Such a base would include a range of fields, from engineering considerations and environmental, social, and governance (ESG) factors, such as climate change, to emergency preparedness and response plans (EPRPs).
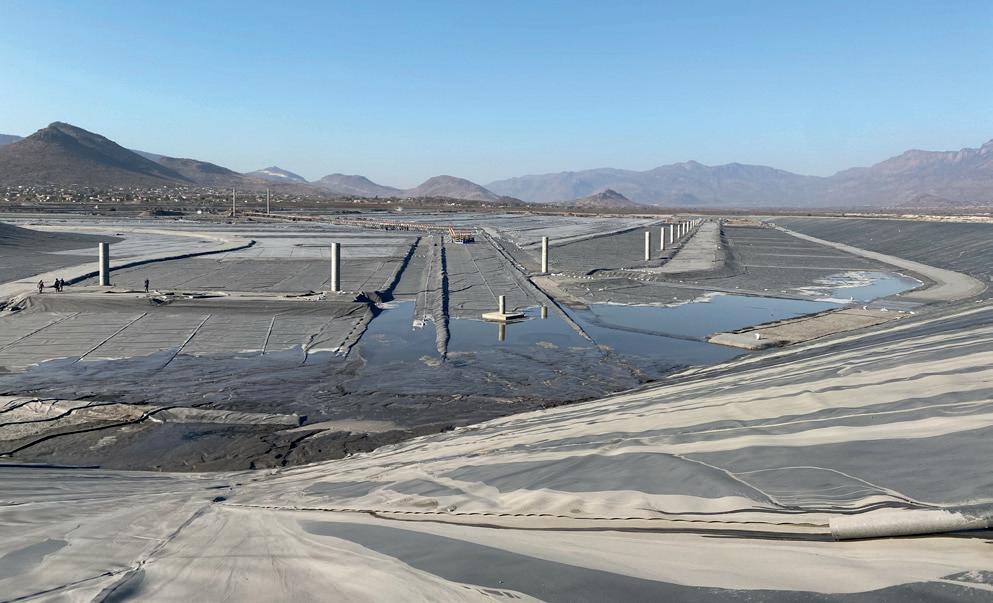
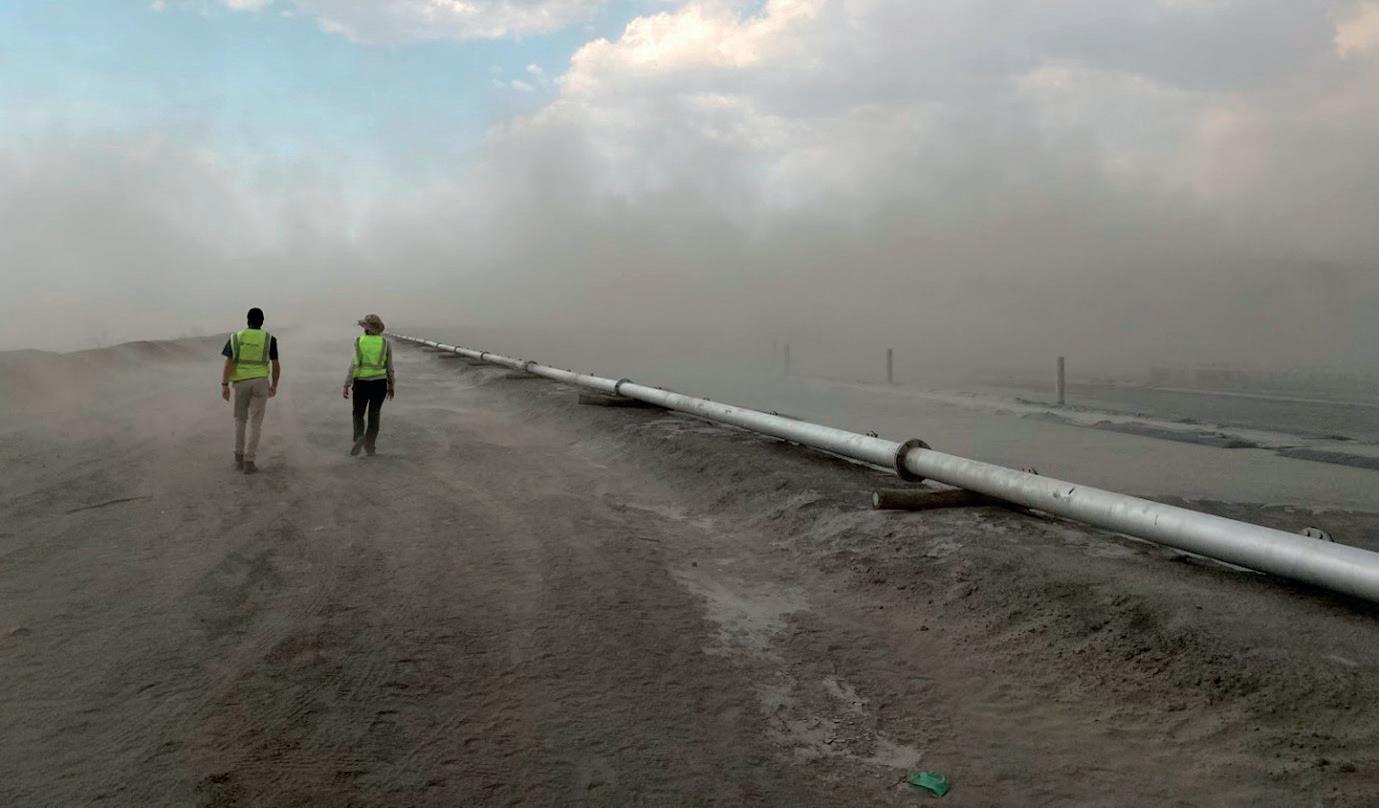
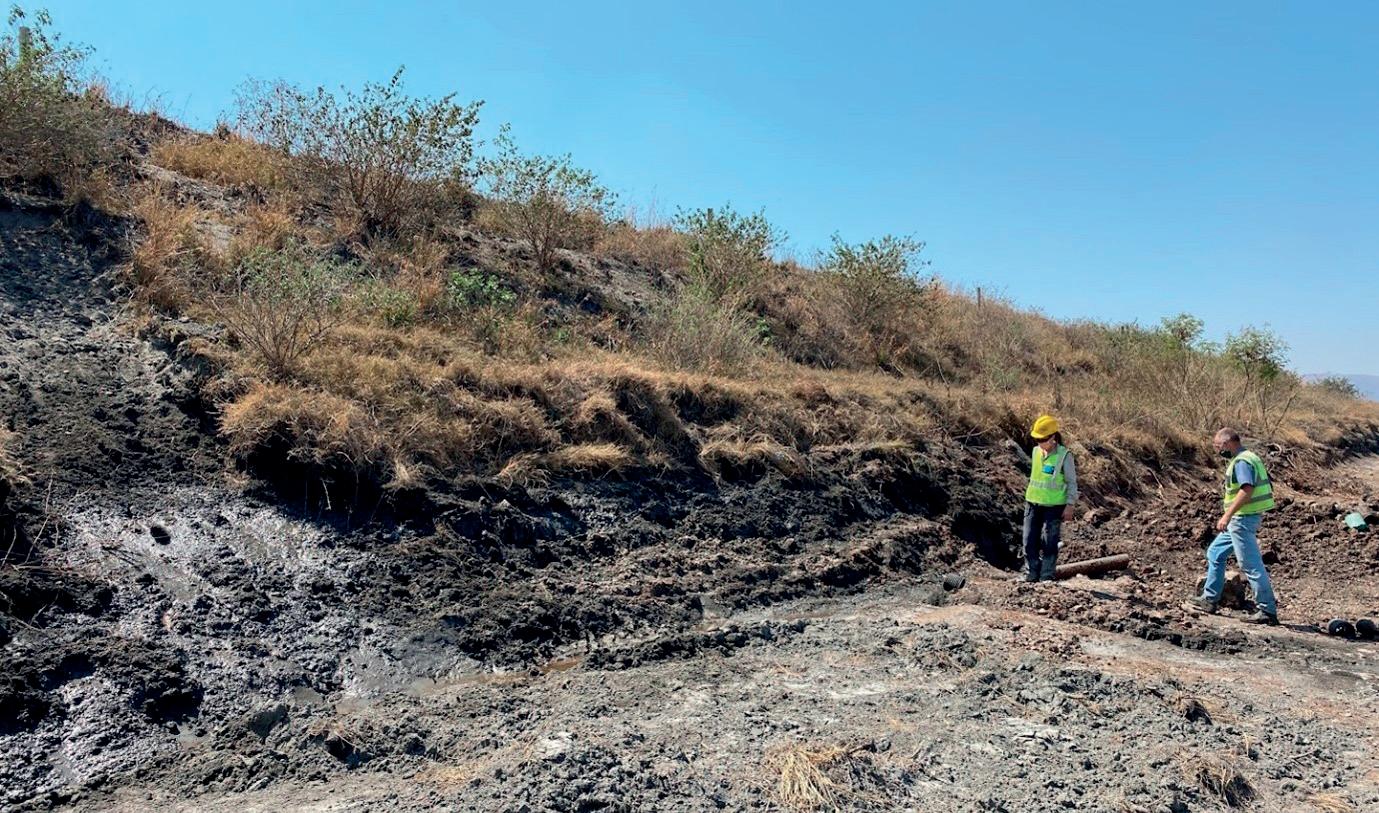
Better decisions
The GISTM requires a breach analysis, for instance, that will model where tailings are likely to flow in the event of a new TSF breach. By predicting the inundation zone, this allows the mine to make better decisions about the location of the TSF, based on the environmental and socio-economic risks associated with the inundation zone.
In existing TSFs, it can support planning in terms of environmental and socio-economic considerations. An important part of quantifying the socio-economic aspects is determining the presence of vulnerable people in the inundation zone. The mine’s stakeholder relations and emergency response teams can then contribute to developing specific plans to support vulnerable groups in case of an emergency.
Such plans also need to be based on an understanding of the environment and number of people potentially affected by a breach – as well as the value of private, public, and community assets in the inundation zone. This information provides a scientific baseline from which mining companies can make informed decisions about tailings design and management.
Addressing uncertainty
The example of breach analysis demonstrates how the knowledge base impacts the assumptions, plans, and costs incurred in TSF design and execution. A poor technical knowledge base invariably raises levels of uncertainty, thereby leading to conservative assumptions, which in turn lead to the larger assumed inundation areas from a hypothetical breach. This means a larger area where people will appear to be at risk, and the need for more comprehensive and extensive emergency preparedness and response planning.
Vital to the value of a knowledge base is the continuous updating that must be done as the TSF evolves over time. This involves the latest information being drawn from assessments, monitoring, observation, and engagement –and from a variety of disciplines. From an engineering perspective, the design of TSFs covers aspects such as geology, hydrology, hydrogeology, material geotechnical characterisation, drainage, geometry, and many others. However, the treatment of the engineering processes in each stage is fundamentally different. The philosophy of design and analysis are both integrated and independent, depending on the stage of the life cycle.
Adding to the knowledge base
In the design stage, the data is only theoretical, being based on pre-existing knowledge, research, investigation, and experience, and could also be based on industry standards. This means they can only represent an ‘a priori’ condition available before the design process begins.
This type of information is used to inform the initial design decisions and to ensure that the project satisfies certain constraints and requirements. However, once the facility is constructed and performance monitoring or surveillance commences, the critical data that was not known initially then represents an ‘a posteriori’ condition.
Figure 1. Engineers, scientists, and environmental experts collaborate to develop an interdisciplinary knowledge base, crucial for tailings compliance and safety.
Figure 2. SRK has been working intensively with clients to forge innovative strategies for meeting the new GISTM requirements.
Figure 3. The GISTM requires a breach analysis, for instance, that will model where tailings are likely to flow in the event of a new TSF breach.
These conditions are those that are discovered from feedback from users, through testing and other experimental results, and ongoing environmental analysis and monitoring during the construction phase of the life cycle. This data may not have been available initially, but becomes part of the knowledge base – being used to refine the operation and make necessary changes to improve performance.
Indeed, TSF design is noteworthy – in the engineering context – for having to rely on relatively limited data sets (the a priori case), with the knowledge that unnecessarily conservative or unreliable designs could waste considerable time and financial resources – as the designer strives to satisfy risk and safety criteria. At the same time, those involved in this process must acknowledge that the design decisions taken with the use of the a priori data sets will be augmented over future decades in the life of the TSF; these design decisions are then likely to be questioned, with the benefit of hindsight.
Bayesian thinking
Here it is valuable to draw on Bayesian theory, which provides a convenient way to improve predictions from new data as it becomes available – which is really like a ‘machine-learning’ algorithm. The use of Bayes’ rule is becoming more accessible to the geotechnical practitioner and will become increasingly valuable to TSF design.
Bayesian theory treats uncertainty as degrees of belief and it allows designers to combine information from
MINE MORE UPTIME
From mechanic trucks and service cranes to tire trucks and manipulators, count on Stellar ® products to keep mining equipment running. Rugged TMAX™ Mechanic Trucks can be configured for your needs, and the available aluminum construction reduces weight for higher payload. Stellar’s Large OTR Tire Trucks and Manipulators deliver the strength and capacity to handle a wide range of tire sizes. The list of Stellar products that maximize uptime for mining operations goes on and on.
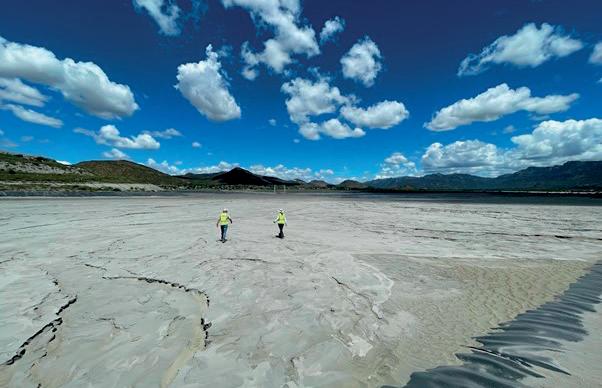
4. Tailings facilities should be designed for mine closure, as true future engineered landforms that will be physically and chemically stable for the long term, says
multiple sources to update prior knowledge given new information. From a geotechnical point of view, the Bayesian method follows the same logic as the observational method and, as a result, it is a powerful basis for inference.
Beyond behavioural observation, Bayesian thinking can also provide a means for drawing strong inferences from weak data, allowing qualitative data to lead to quantitative conclusions. This means that rational inferences can be made on the probabilities of things which have yet to be observed. By allowing the observational method to be placed on a quantitative foundation, it allows data of
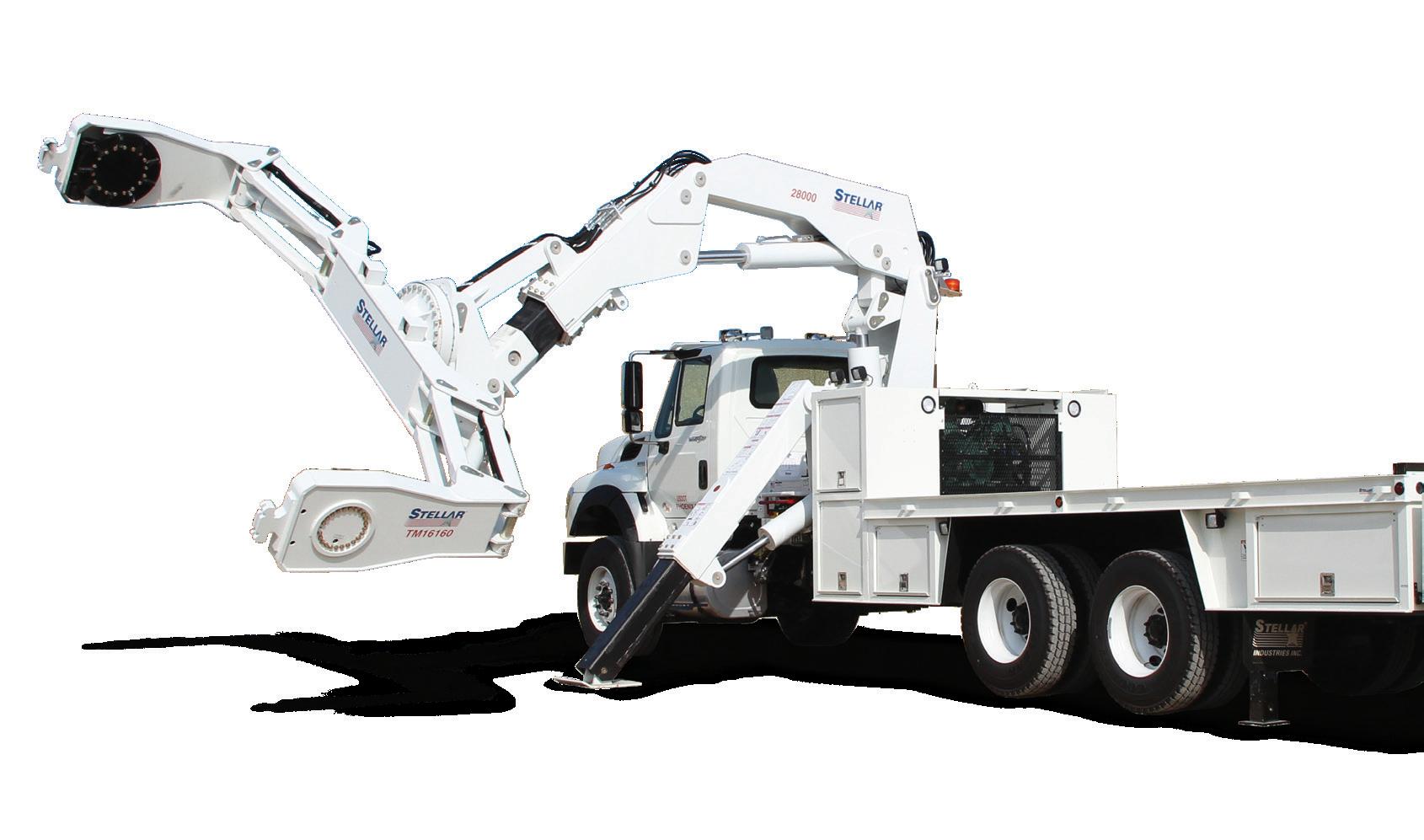
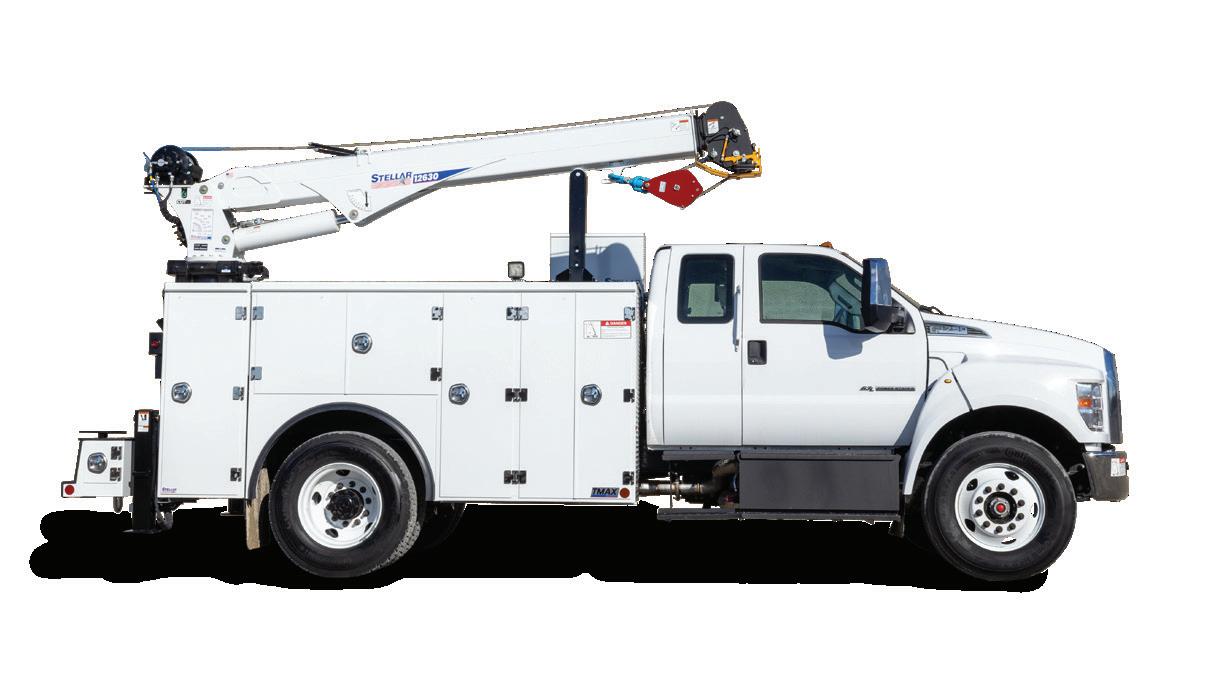
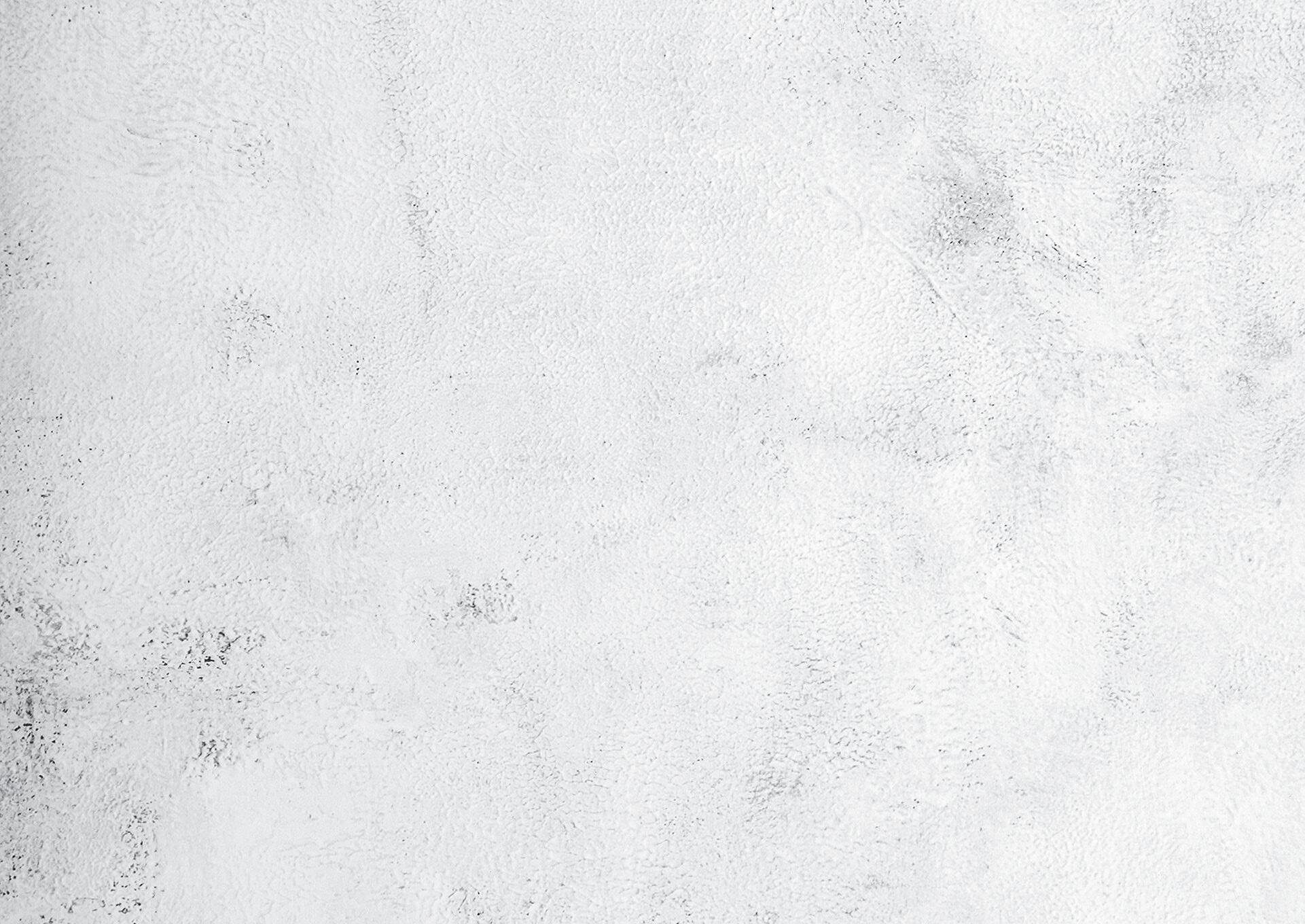
Figure
SRK Consulting.
disparate sorts to be combined into coherent probability statements. An understanding of the reasonably simple mathematics behind Bayesian thinking allows anyone to make much stronger use of data and observations than would otherwise be the case.
Living asset
By strengthening the knowledge base in this way, mines can facilitate improvements to the safety and management of both existing and new tailings dams as they evolve. A thorough knowledge base requires compilation of knowledge at hand, as well as meticulous planning and development to improve the knowledge base – as technical knowledge improvement is time consuming and costly. In this way, the knowledge base becomes a living asset that mines can expand and adapt in line with the developments on and around the mine site.
It is important for the design of a TSF to be conducted with closure in mind, and the GISTM provides valuable additional guidance to achieve this. Applying these standards from the concept stage delivers the best results, especially when there is effective interdisciplinary collaboration to balance engineering, financial, socio-economic, and environmental imperatives.
Iterative steps to reduce risk
From a technical perspective, the GISTM aims to help mines to reduce risk by managing uncertainty. Much of this
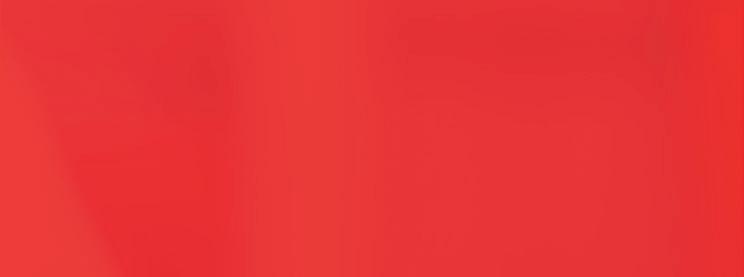
uncertainty resides at the boundaries of disciplines –highlighting the need for better integration. In practice, mining operations often tend to compartmentalise their different on-site functions, which makes integration of knowledge difficult. In these situations, consultants play an important role in helping clients to bridge these disciplinary boundaries on their mines.
In conclusion, the use of the observational method, Bayes’ theorem, and predictive performance modelling will enhance the accuracy with which TSF behaviour can be predicted. This approach provides a mechanism for the results of actual performance to be incorporated into the TSF knowledge base, and used to enhance the subsequent predictive model. The iterative process of predicting TSF behaviour, followed by additional new data to assess and improve predictions of behaviour, risk, and safety, can then continue over the decades of a TSF life cycle.
Contributors
n Dr Graham Howell, Corporate Consultant.
n Grant Macfarlane, Partner Principal Engineering Geologist.
n Franciska Lake, Partner and Principal Environmental Scientist.
n Bruce Engelsman, Partner and Principal Engineer.
n Kavandren Moodley, Senior Environmental Scientist.
n Roanne Sutcliffe, Principal Environmental Engineer.
n Andries Fourie, Senior Technologist.
Dry Bulk Magazine Online
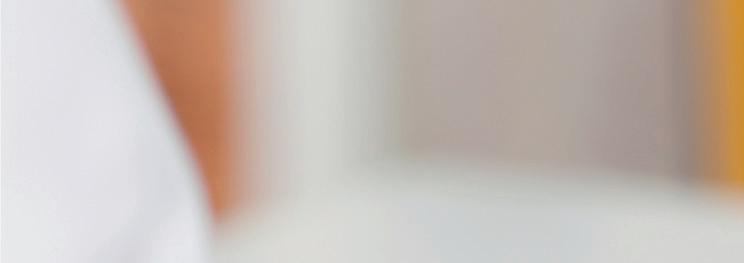

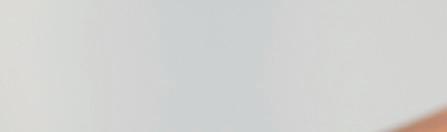
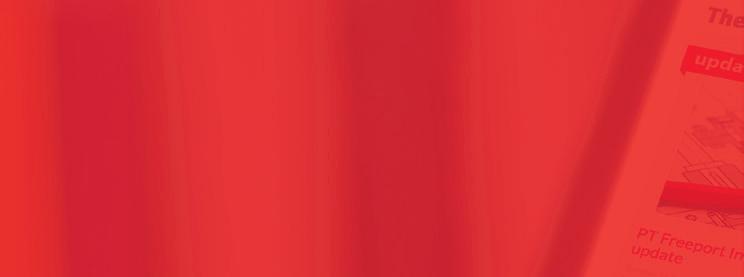
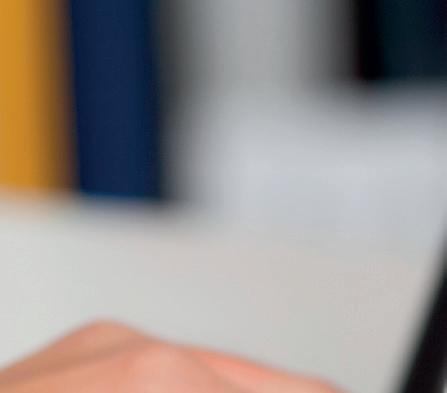
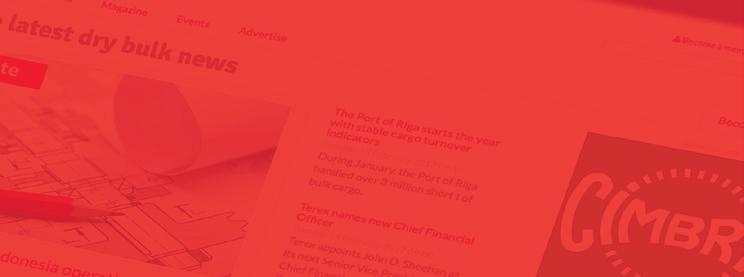
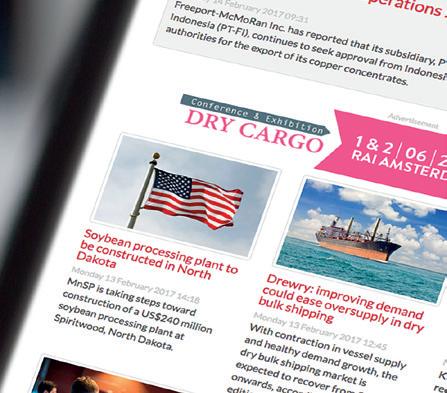
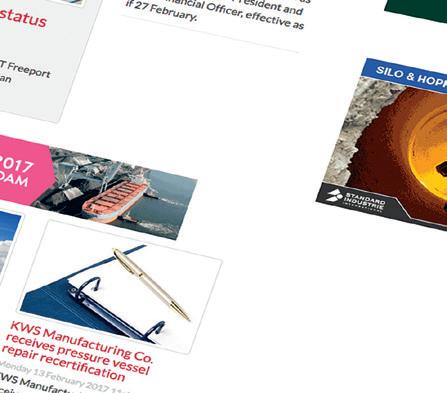
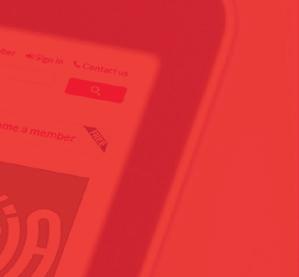
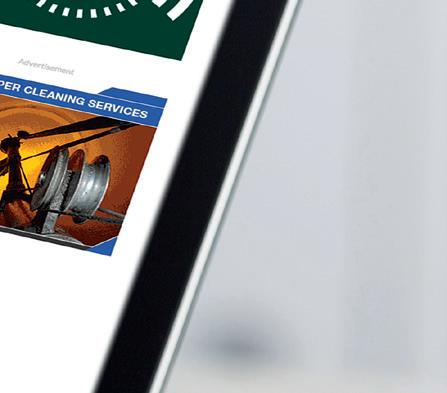


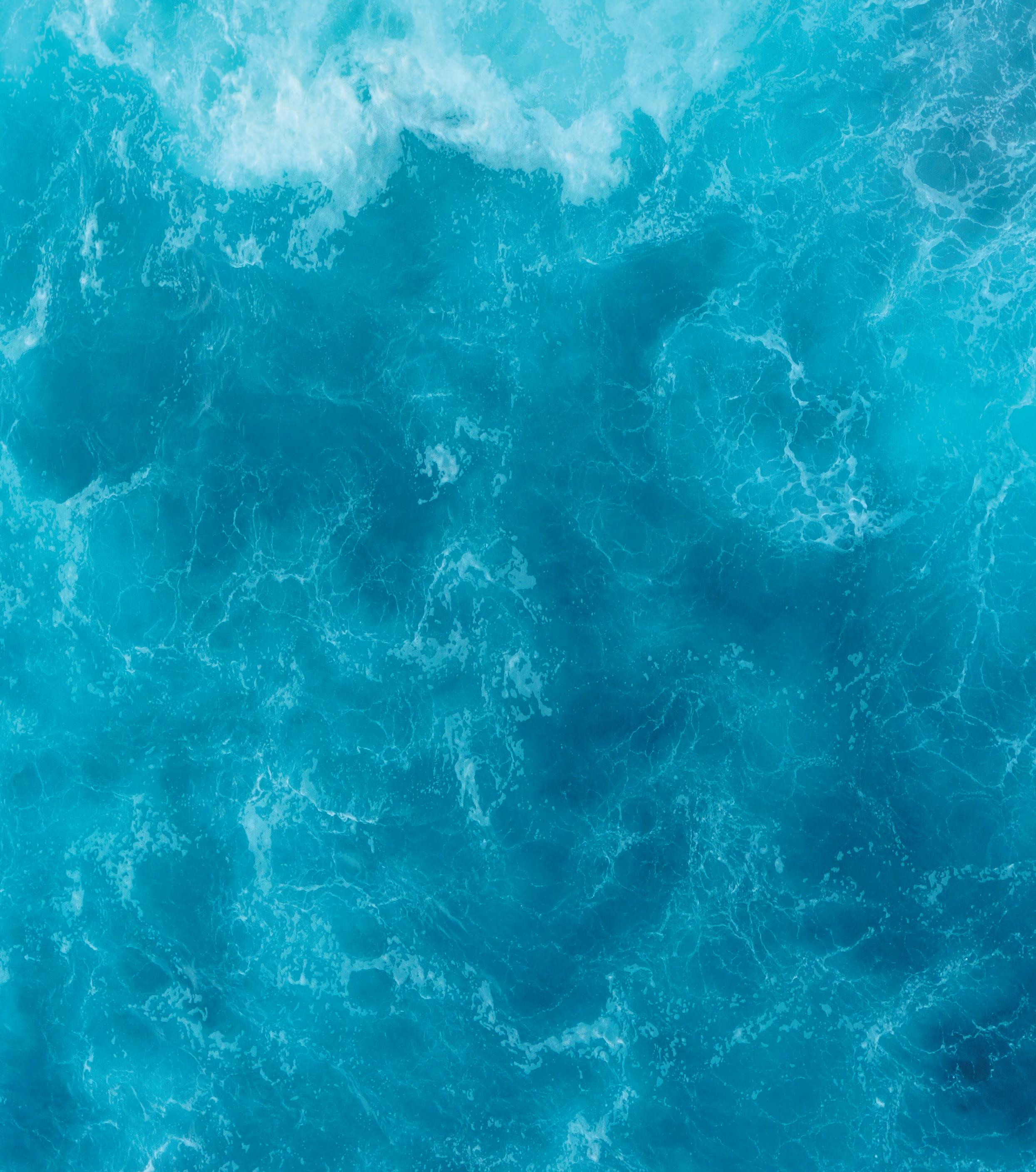
appropriately, with excess water removed. One critical piece of equipment in efficient mine water management is the dewatering pump.
Taking a deeper look
Mine dewatering falls into two categories – active and reactive dewatering. In active dewatering, the water table is proactively lowered to reduce the risk of groundwater entering the mine. Deep wells are drilled at various points around the mine and multistage and submersible borehole pumps are used to remove the water.
Conversely, reactive dewatering is the process of removing water from the working areas of a mine. This water could
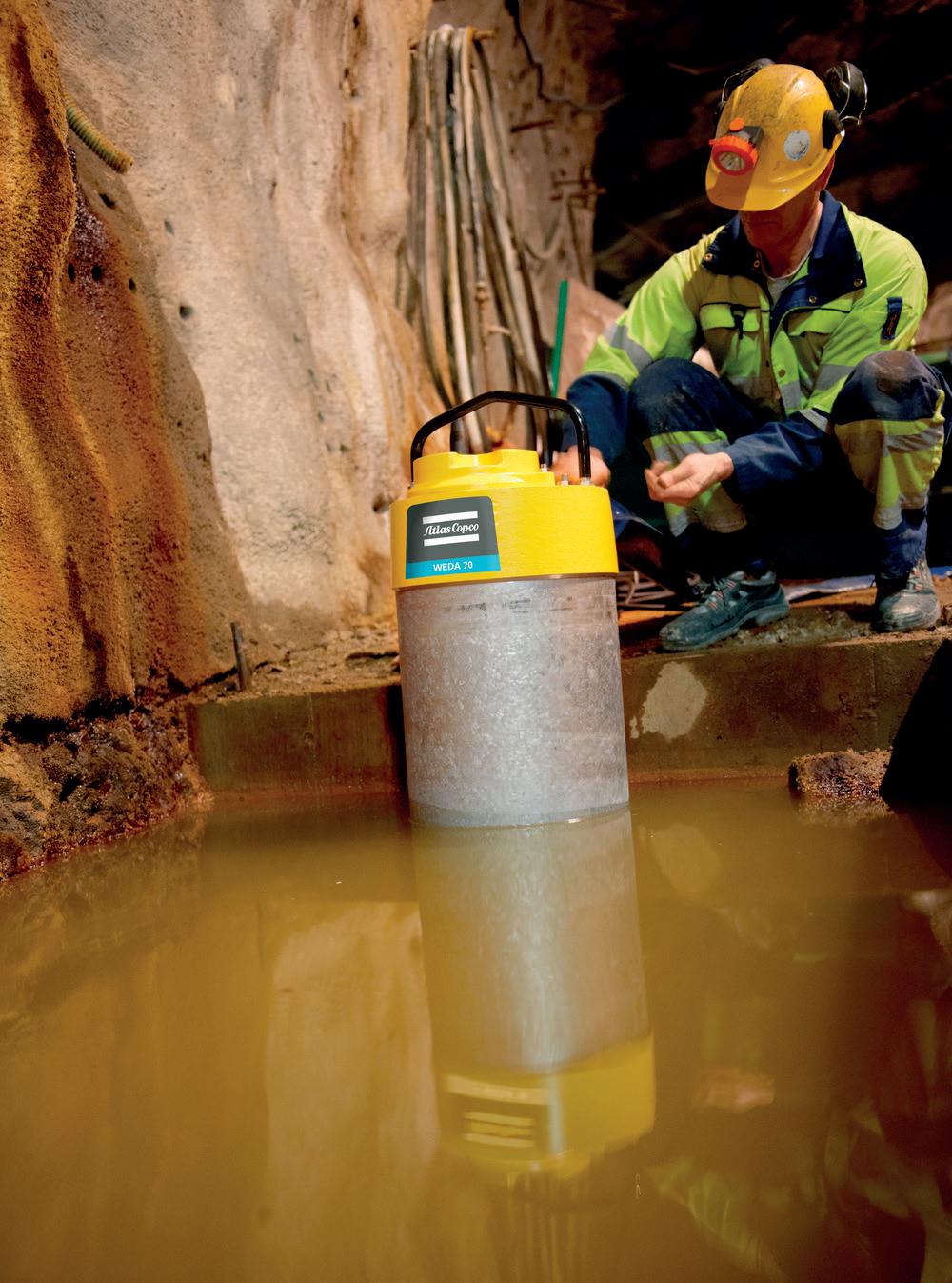
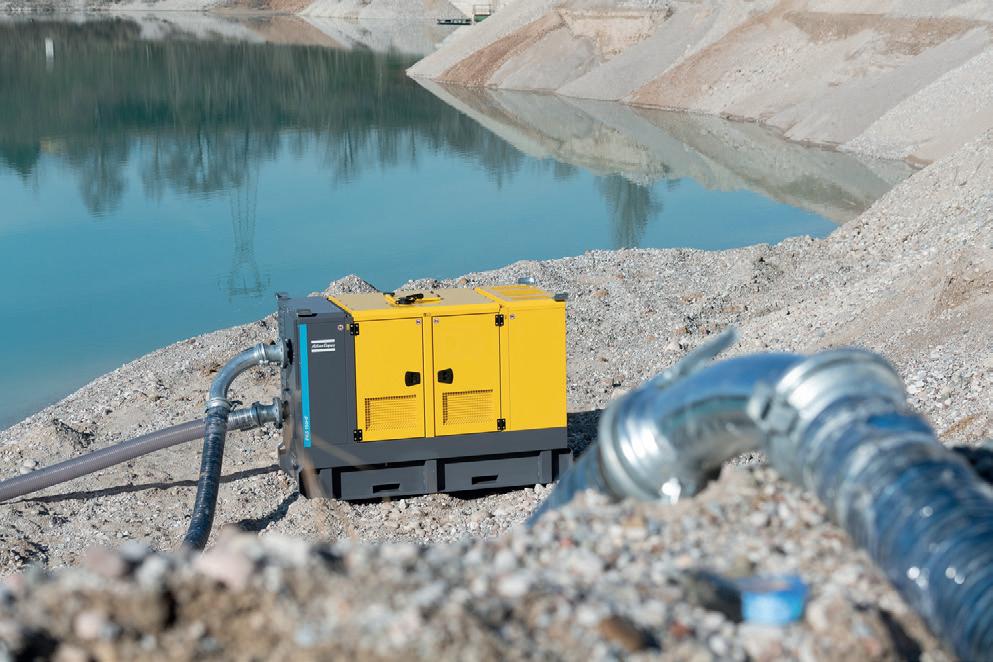
have been introduced through the mining process, or from groundwater, and is collected in sumps along the drifts and at the bottom of the mine.
Pumps are key equipment
Dewatering pumps are essential for draining a mine to prevent waterlogging. Using dewatering pumps also ensures that sites can meet environmental regulations and legislation to manage water properly and prevent run-off and the risk of pollution. There are many types of pumps, such as: small portable pumps, electric submersible pumps, self-priming centrifugal pumps, electric self-priming centrifugal pumps, high-head pumps, and well point surface pumps.
Application requirements
While all mining operations include product extraction, transfer and processing, and disposal and treatment of the waste products, different types of mines have different pumping requirements for dewatering.
Opencast mining
An opencast mine is typically excavated with a series of benches to reach greater depths. In opencast mining, the removal of ore is normally extracted through drilling or blasting. As opencast mines reach greater depths below the water table, and with additional water influence from precipitation and ground water seepage, removal of water becomes essential to continue operating the mine. The type of pumping technologies used depends on whether the mine has access to electric power. This is important, since many opencast mines are in areas without this access. In the event there is no access to electricity, operators can use diesel operated self-priming pumps.
If the mine does have electricity readily available, several types of pumping technologies can be used to remove excess water. For example, deep well borehole pumps are often placed in multiple wells surrounding the mine to lower the groundwater level. Self-priming pumps, electrical submersible pumps, multistage high-head pumps, vertical pumps located on barges, or a combination of these technologies, can be used to remove water in the pits and sumps and for water transportation. If the required pumping heads are high, a serial connection of these pumps could be necessary.
Underground mining
In underground mining applications, water is used at the face of the mine for drilling and blasting. The dirty water at the face is transported to the main sump at the bottom of the mine through several stages. In both face and stage pumping applications, electric submersible pumps are commonly used. To remove the water from the bottom sump in the mine, the type of pumping technology used depends on whether the mine has a clarifier that separates solids from water.
If the mine is equipped with a clarifier, water is typically removed by high-head multistage centrifugal pumps. Water is either pumped in one or several stages from the bottom of the mine to the ground level for further transportation to holding lagoons. If there is no clarifier installed, the dirty
Figure 1. Atlas Copco WEDA submersible pump engaged in harsh underground mining operations.
Figure 2. Atlas Copco self-priming centrifugal pumps keep mines dry and operational.
water containing larger particles is removed by either piston diaphragm pumps (if the mine is deep), or serial connected slurry pumps. Furthermore, drilling equipment and boring machines need a reliable supply of cooling water to operate, which must be recovered and removed, and pumps can contribute to this process by supplying cooling water to the drilling machine prior to blasting.
Metal ore mineral processing
With metal ore mining, a typical operation includes ore extraction, comminution, separation, and thickening, before the product is transported to the refining and finishing process. Once large rocks have been extracted, they go through comminution processes to reduce their size. The preliminary crushing and screening processes are dry, and water is only added when the ore reaches the grinding mills. The finishing processes also often contain corrosive fluids, and so pumps must be able to withstand these harsh conditions. In mineral processing, water is required for different applications. Depending on the fluid characteristics and solid content, either standard process pumps or slurry pumps are used.
Considerations for specifying pumps
Having a full understanding of the application can help operators to ascertain dewatering needs. However, there are several factors and considerations to take into account when selecting the most appropriate pump.
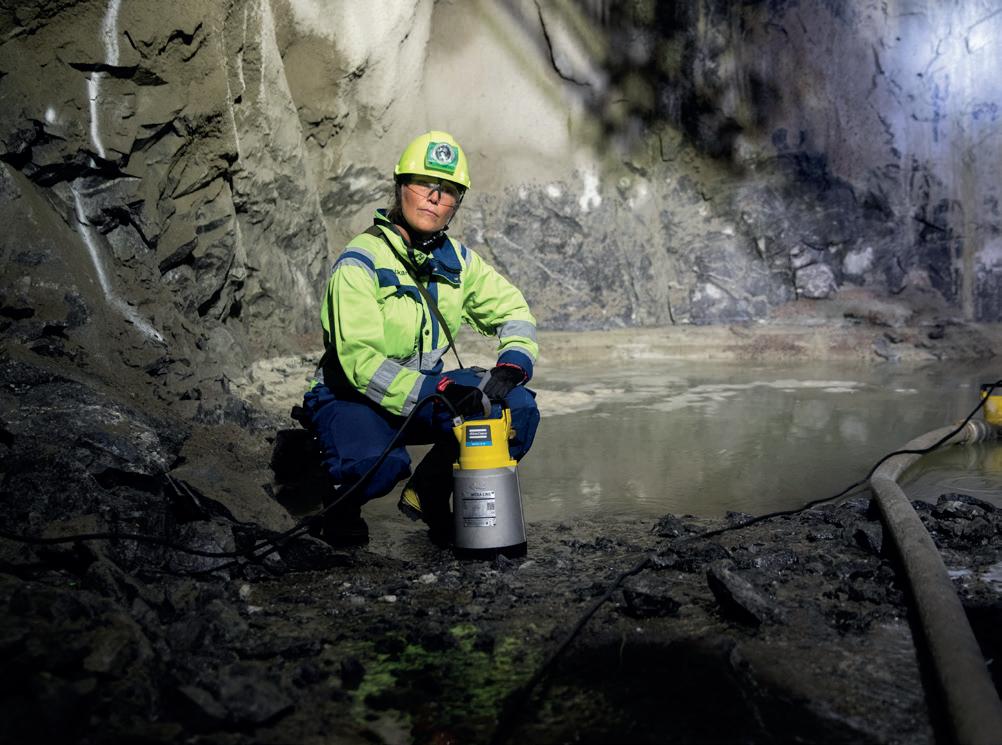
When a mine is set up, the dewatering system should be designed and specified according to the quality and volumes of the water to be handled, as well as the capacity requirements in terms of its size and depth.
The mine’s location is also significant, as seasonal conditions can affect the volume of water that needs to be removed, impacting the pump to be selected. Other
Subsurface exploration requires careful evaluation of the underlying lithology. Accept no substitute; SONIC Drilling is the superior solution.
Terra Sonic Drill Rigs can generate near-in situ core samples of sand and rock with no premature refusal up to 10x faster than non-Sonic drilling methods.
Have Questions? Let us know. www.terrasonicinternational.com/contact
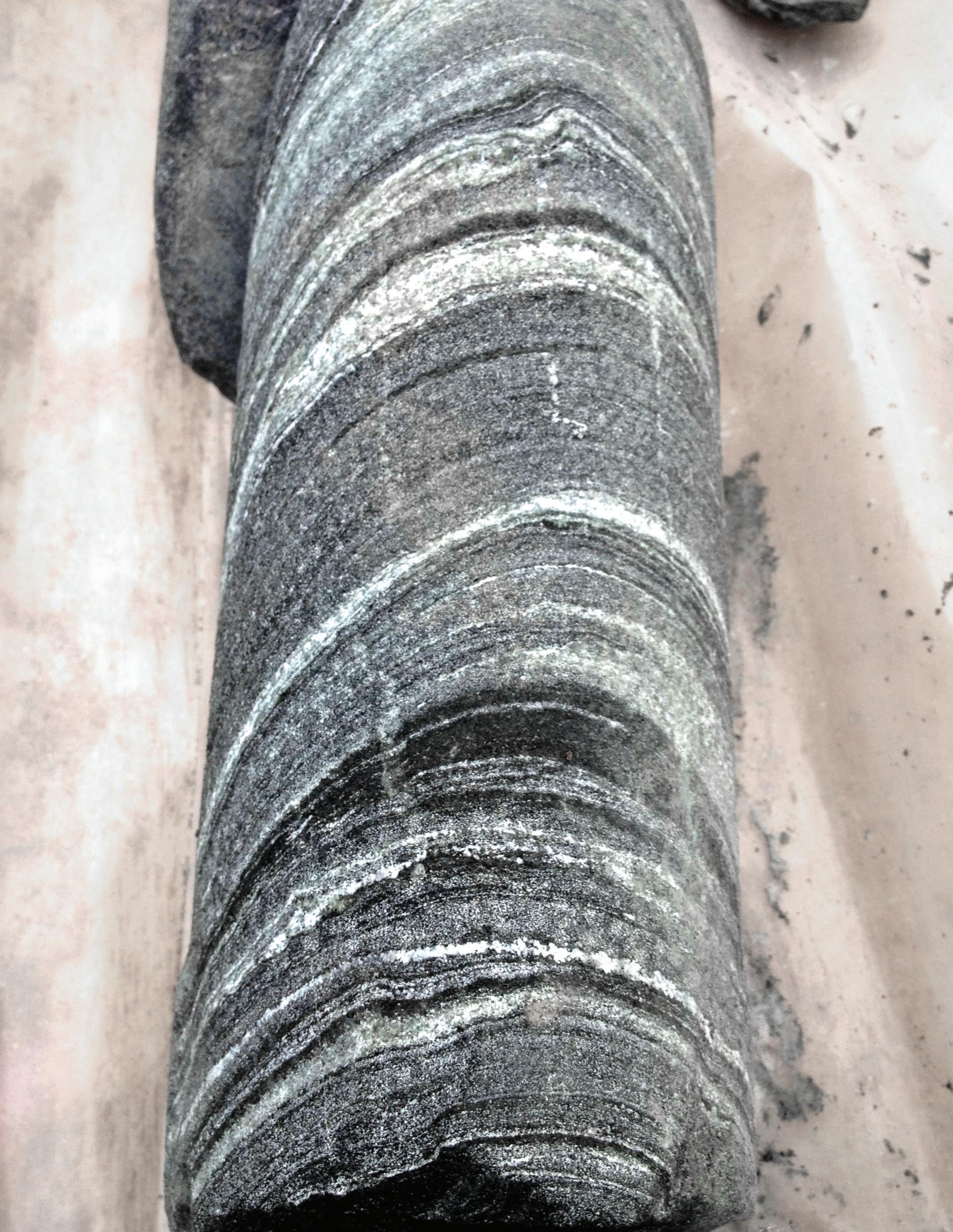
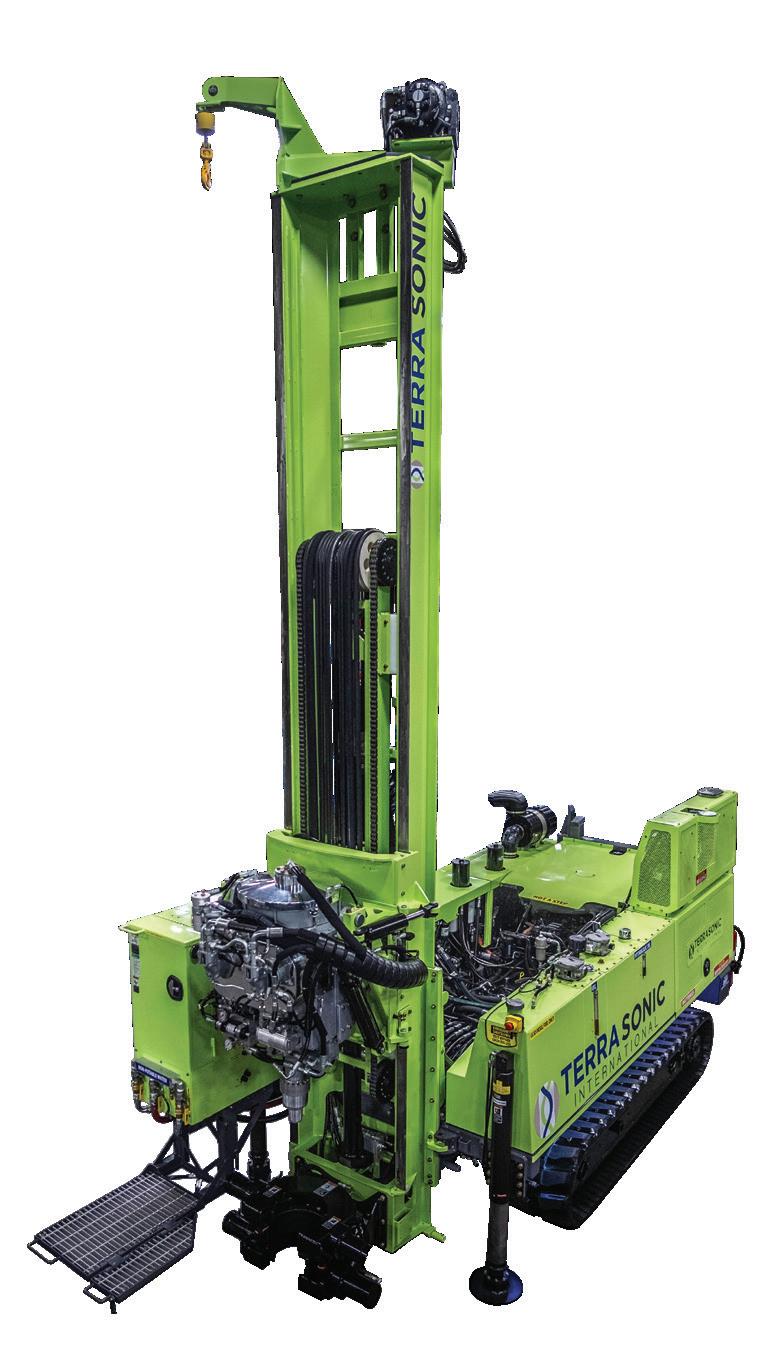
Figure 3. Atlas Copco WEDA electric submersible pump prevents flooding for efficient and safe ore extraction in mines.
electrical power, and how mobile the pumps need to be. Finally, the operational life of the mine also needs to be accounted for to determine whether permanent or temporary pump solutions are needed.
Improving sustainability in the future
Making sure the pump is fit not only for the needs of today, but also for those of tomorrow and the future, also plays a large part in selection. One of the biggest challenges facing water management in mining is how operators can engage in more sustainable pumping operations. Integrating renewable energy sources – such as solar or wind – to power the pumps is one way sustainability can be increased. Electrical pumps will further reduce emissions when powered with fossil-free electricity.
As mines are often remotely located and pump installations are sometimes positioned on deep levels in the mines, reliability and durability are also important factors to consider. Operators must avoid installing pumps that fail prematurely, since the replacement of pumps is both costly and time-consuming.
Sustainability can be improved in the future by installing pumping technologies which offer higher efficiencies and longer service life. For example, the advanced pump portfolio
from Atlas Copco includes WEDA electric submersible pumps, which have innovative features including a high performanceto-weight ratio, hardened high-chrome impellers, and Wear Deflector technology. This advanced technology is designed to minimise wear, ensuring durability for a longer working life.
Also included in the portfolio are Atlas Copco’s versatile range of electric and Stage V compliant diesel automatic self-priming surface dewatering pumps. These units contain the latest technology in telemetry and design innovation, which can reduce the customer’s mean time to repair (MTTR) by up to 35%. The range is suited to many different applications including mining, and offers excellent performance, low cost of ownership, reduced footprint, and unique digital connectivity.
Working with trusted partners
Dewatering pumps are a critical piece of equipment on any mining site and play a central part in mine water management. Working with trusted partners and manufacturers, that can offer expert knowledge and an extensive range of pumps designed to help operators reduce energy consumption and improve the efficiency of their water usage, is key.

Advert Index
Caterpillar 44 China Mining Expo 2024
43 Cincinnati Mine Machinery Co. 51 Denso Inc.
64 Dry Bulk
59 Elgin Equipment Group IBC EXPO KATOWICE 21 Freeport 09 Gebr. Pfeiffer
27, 32 & 36 Global Mining Review
39 Herrenknecht Tunnelling Systems 15 Jennmar
13 J.H. Fletcher 31 Komatsu 04 MAAG Gear 22 MINExpo INTERNATIONAL® 2024 28 Mining Indonesia OFC & 25 MMD GPHC Ltd
Orica 35 Sandvik 55 Stantec
63 Stellar Industries
67 Terra Sonic International
IFC Van der Graaf
47 Weber Mining & Tunnelling OBC Weir
60 World Coal
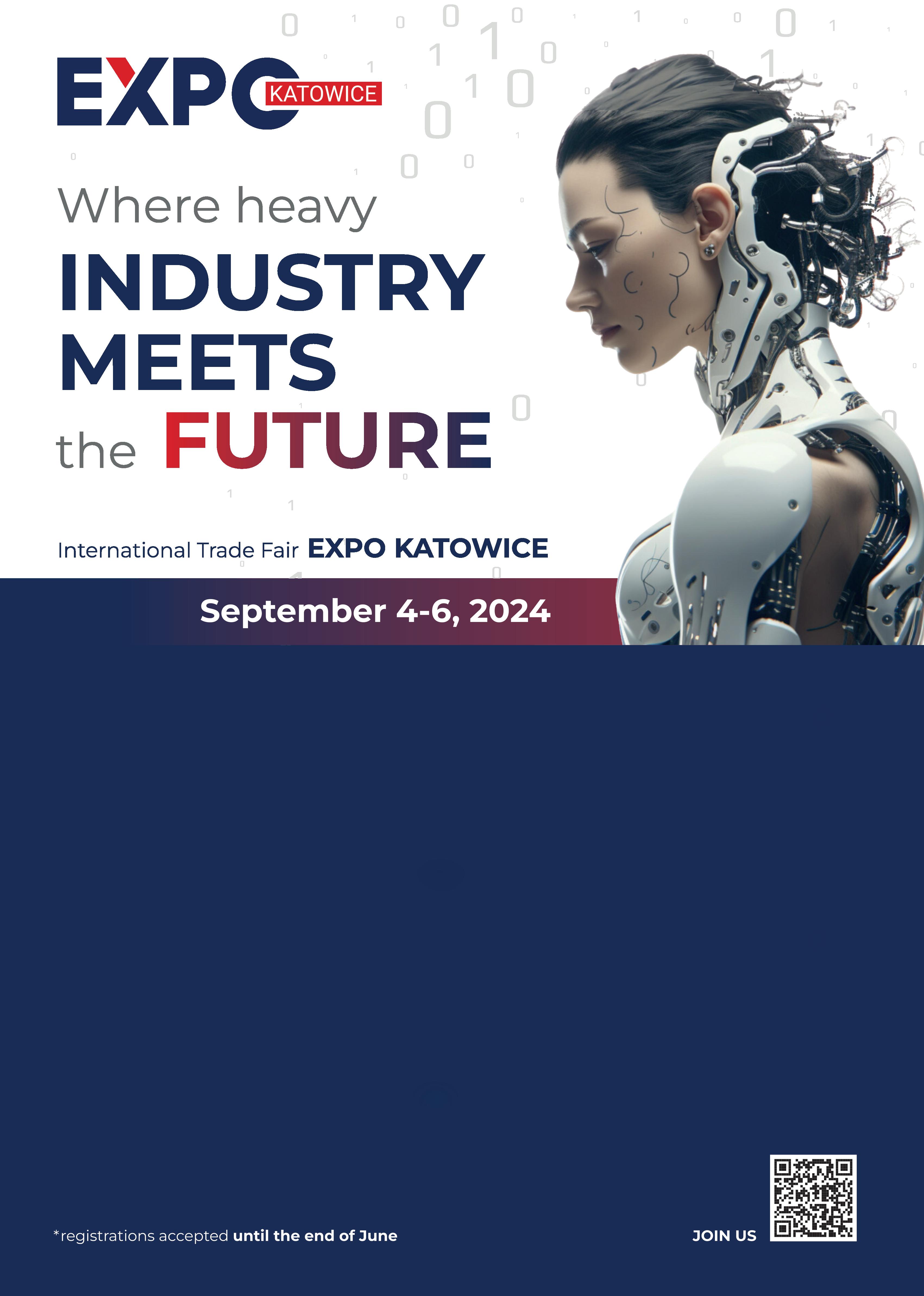
The biggest heavy industry trade fair in Europe! 40 years of experience!
Join us! Showcase your machinery, equipment, and cutting-edge technologies to an international audience.
Enter our prestigious competition! Showcase your products and innovations!
Shape the Future of Industry at EXPO KATOWICE: Embark on a journey of innovation with Dynamic Networking, Growth Opportunities, and the Enlightening Conference “Industry 5.0 - Transformational challenges of industrial sector” - All Under One Roof!
Mark your calendars for September 4-6, 2024, and let EXPO KATOWICE be your gateway to global success.
Reserve your spot by the end of June and unlock your potential with EXPO KATOWICE
Don’t spend more on tailings than you have to.
Weir’s unmatched technology and expertise means you can find a solution that’s built to your operational and site requirements. We’ve reduced customer energy consumption by 51%, average water usage by 76% and lowered TCO all while safely improving the stability of tailings and reducing the tailings footprint. Plus, we can even help re-purpose waste into useful materials for dam wall construction and backfill that saves valuable resources and increases efficiency.
Now it’s your turn to re-think tailings with a Weir tailored solution.
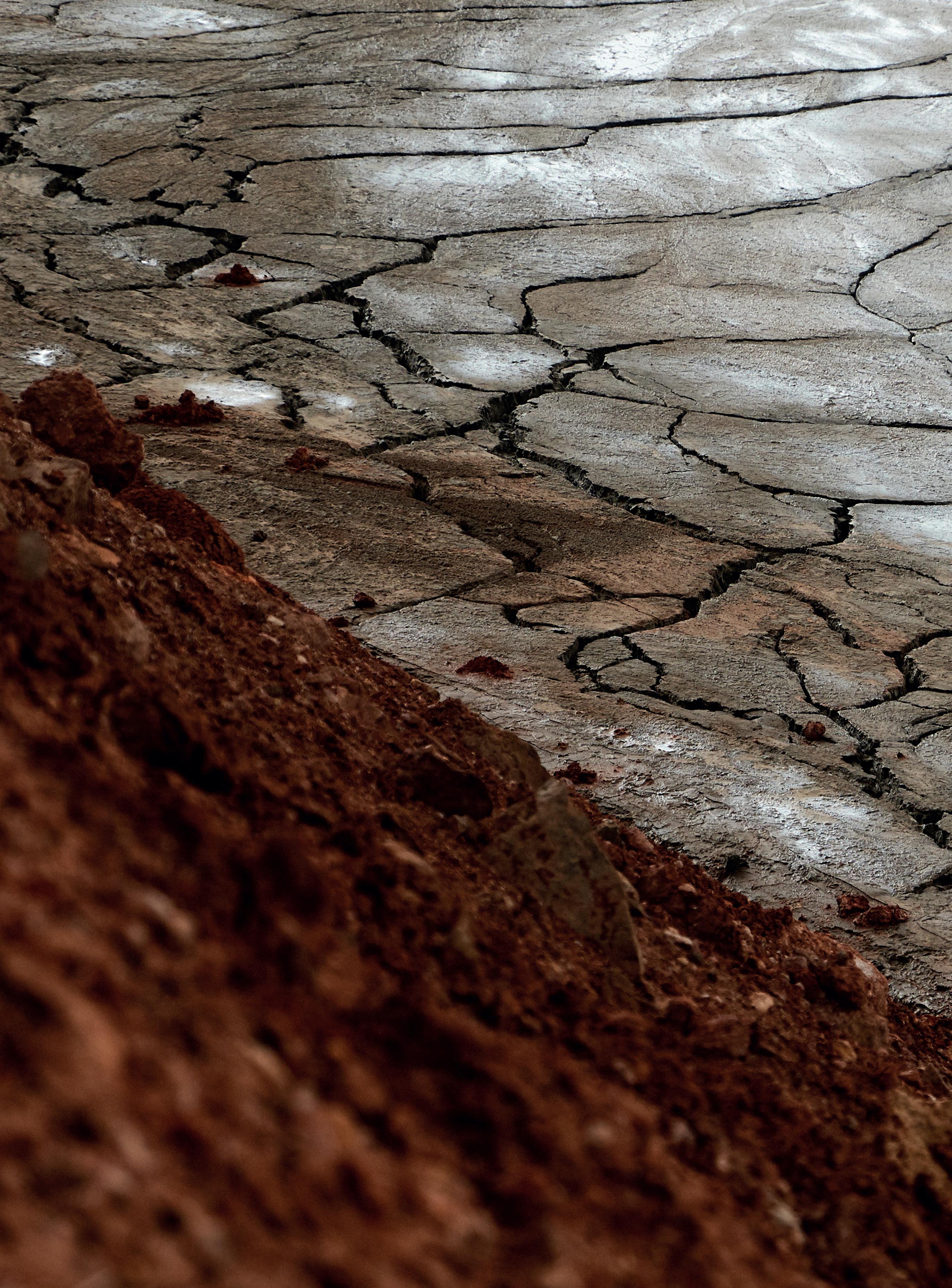
www.global.weir/rethink_tailings