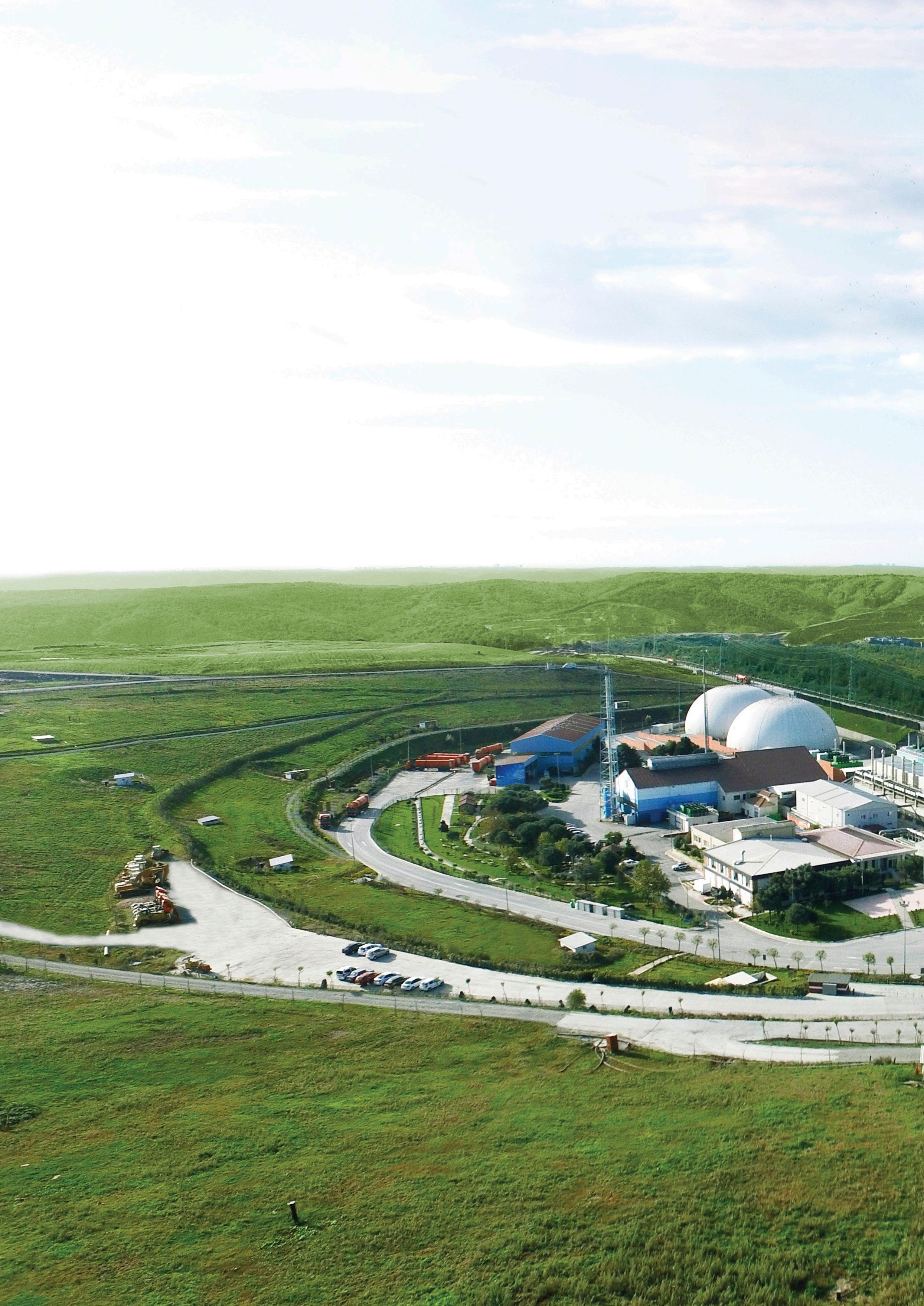
8 minute read
Plants of the future
Filippo Vescovo, Turboden S.p.A., Italy, explores the revolution in the waste-toenergy industry and how Organic Rankine Cycles can help unlock a large potential for smaller, decentralised plants.
Among the mix of power generation plants, waste-toenergy (WtE) plants are likely the only ones in which the generation of energy is not their main duty.
These plants are often considered the last resort for ‘waste’ material that could not be reused, repaired or recycled, thus the waste is disposed and their energy recovered.
Güres: WtE in the Aegean region
This is the case for Güres Energy, a WtE plant located in Manisa, not far from the Aegean coast in Turkey.
Güres is the biggest egg-integrated plant in the country, with more than 4 million chickens. But more than that, this plant produces an average of 350 - 400 tpd of chicken manure: a big challenge for the company since it was dealing with very high costs for the sanitation, elimination of smell, and eventually disposal of the manure.
In 2017, Güres decided to invest in an integrated WtE plant, an ambitious first-of-a-kind project in which the target was to eliminate the chicken manure through its incineration and then to use the heat from combustion to generate 2.3 MW of electric power.
In October 2021, the Güres Energy plant will complete its third year of full activity, being able to eliminate all the manure coming from the company’s chickens and to generate more than 40 GWh of electric power and 150 GWh of useful heat.
A technological innovation
Prior to Güres, there were several examples of industrial plants for the chicken manure incineration, most of which were
Figure 1. The Ortadogu plant in Turkey recovers heat from landfill motor gases.
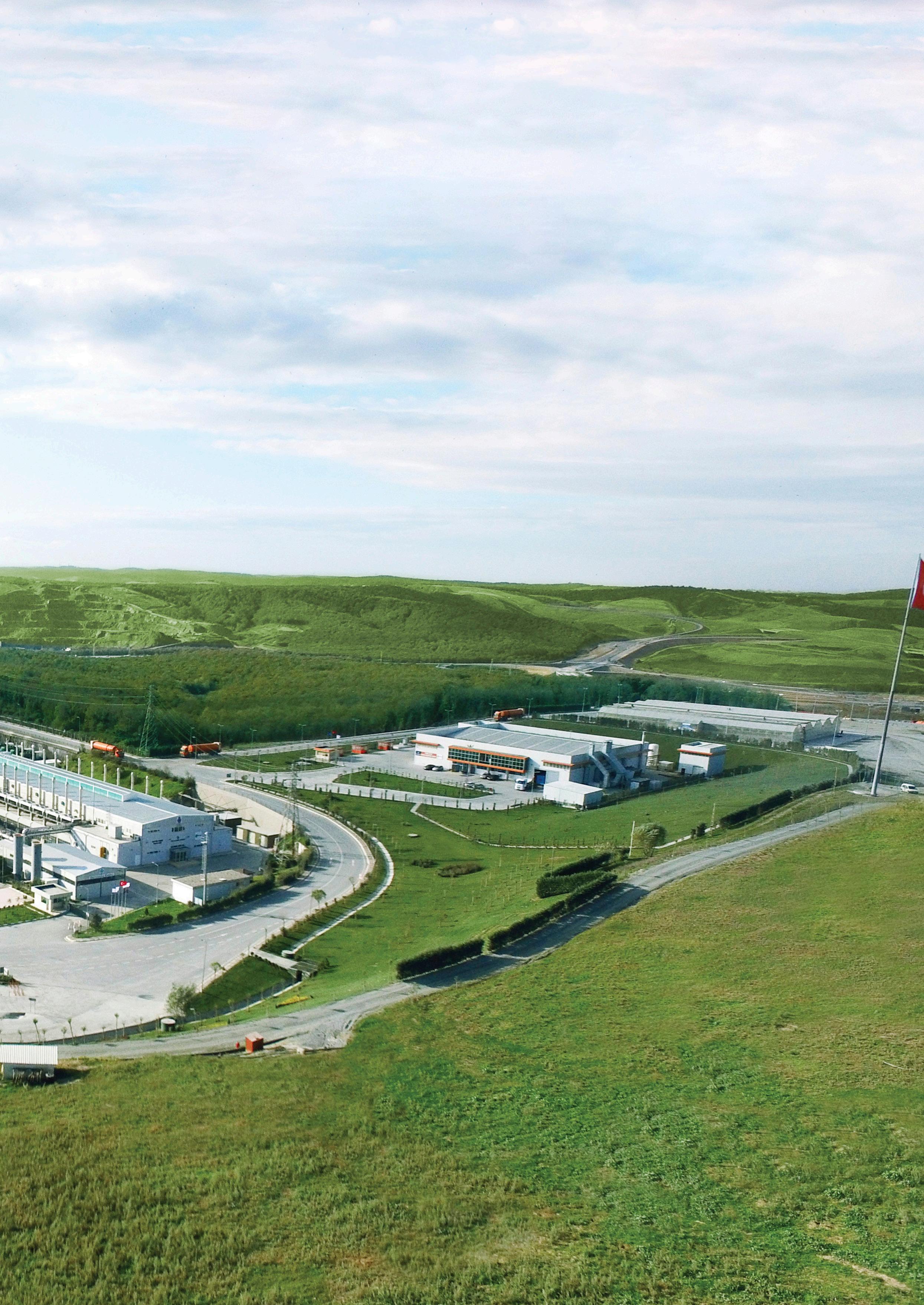
very large scale – such as Foster Wheeler in the US and Eye in the UK. The main challenges for these plants included the aggressive nature of their combustion fumes, their high ash content, and the high investment and operational cost – all of which were common themes for the vast majority of WtE plants.
Güres designed a whole new system to overcome these problems. In an industrial landscape dominated by steam boilers and steam turbines, the Turkish company designed a system based on two different technologies: F A thermal oil heat recovery boiler.
F An Organic Rankine Cycle (ORC) for the power generation part.
Thermal oil heat recovery units
With a waste heat recovery unit (WHRU) it runs similar to a thermal energy plant where the heat of the hot combustion gasses is transferred to a heat carrier fluid that transfers the heat to a user (in Turboden’s case it is a turbine for the conversion to electricity). While the common way is to employ water, Güres chose the opposite route for its plant and decided to proceed with thermal oil.
Thermal oil has various advantages compared to watersteam, such as a lower pressure level, no phase change (from liquid to vapour), and its simplicity of operation and maintenance.
Another key feature is the temperature level of the thermal oil, which at its highest point reaches 300˚C – a level sufficiently low to avoid corrosion problems and expensive practices such as the employment of special materials or the replacement of boiler parts every three to five years.
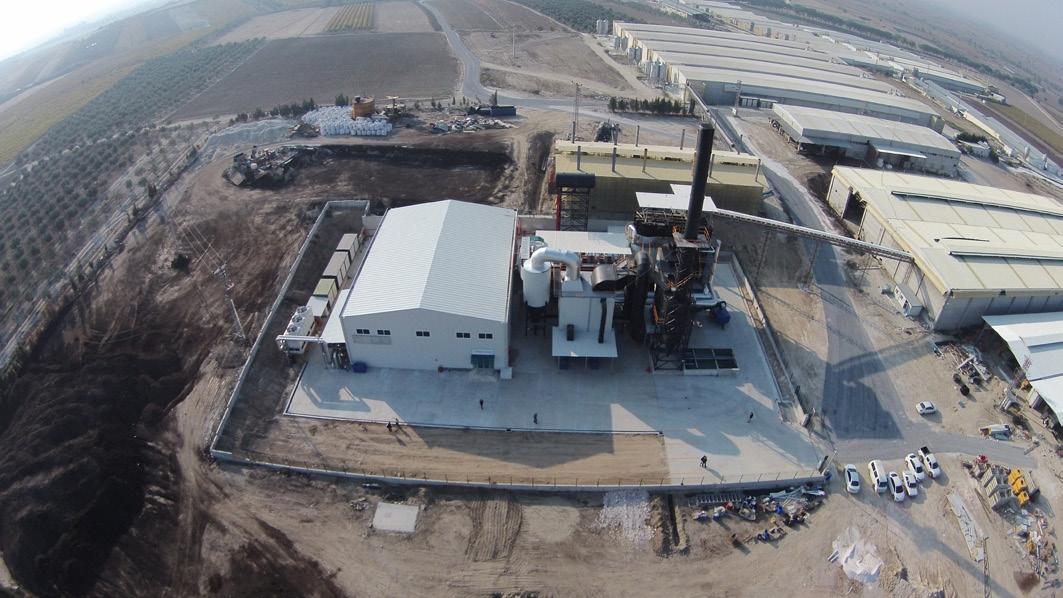
Figure 2. Güres Energy plant in Turkey, an ideal demonstration of Organic Rankine Cycle (ORC) technology in waste-to-energy (WtE) applications.
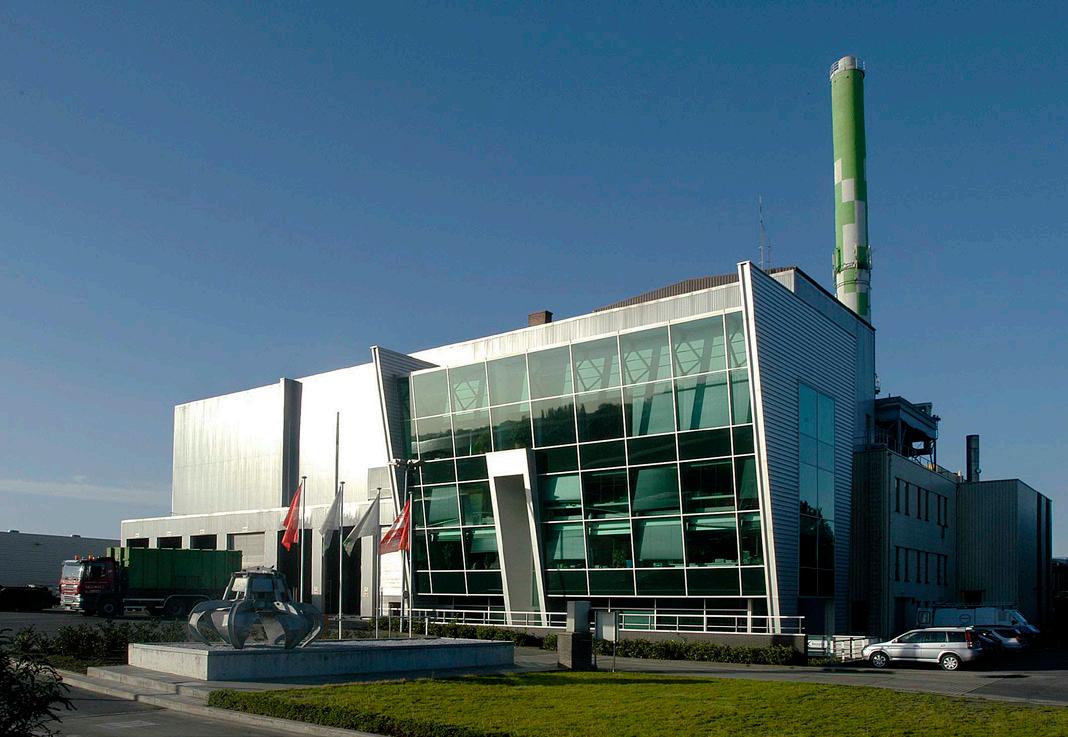
Figure 3. MIROM plant – a 3 MW ORC in Belgium working with MSW – is a good example of power generation and district heating working with different seasonal configurations.
Organic Rankine Cycle
The second main innovation was the selection of the ORC in order to transform the thermal power of the hot oil into electric power and hot water.
ORC is a technology that has been around since the late 19th century, but only saw its diffusion in industrial applications in the 2000s. The principle of electricity generation by means of an ORC process corresponds with the conventional Rankine process: F Pressurisation of the fluid (through a pump).
F Vaporisation of the fluid (in an evaporator) by means of the heat transferred by the hot thermal oil.
F Expansion in the turbine to generate mechanic power, then transformed into electricity by a generator.
F Condensation of the fluid to the liquid form (through a condenser).
The substantial difference lies in the fact that an organic working medium (such as silicon oils, refrigerants, or hydrocarbons) is employed instead of water. Its working principle and the different components of the ORC process are shown in Figure 4.
In the case presented here, Güres decided to purchase a Turboden 22 CHP model – an ORC unit that can directly transform 10.5 MW of heat into 2.3 MW electricity and 8 MW of hot water at 70˚C. Its main features include: F Very high efficiency, >21% electrical and 98% total net CHP efficiency.
F Low operational cost, due to the low pressure employed, with no certified operator needed.
F Low maintenance cost, as a result of the non-corrosive nature of the fluid employed, as well as the low RPM of the turbine and therefore to its direct connection without the need of a reduction gear.
F Very high flexibility of the system – ORC systems can work between 20% - 105% of its nominal load. The Güres plant has been operating its unit at different loads according to the quantity of waste and to the energy consumer, both variable in time.
F No water consumption. ORC systems do not employ water and do not consume water, especially if the condenser
water circuit is a closed-loop like the Güres plant.
Size counts: How ORCs can help out
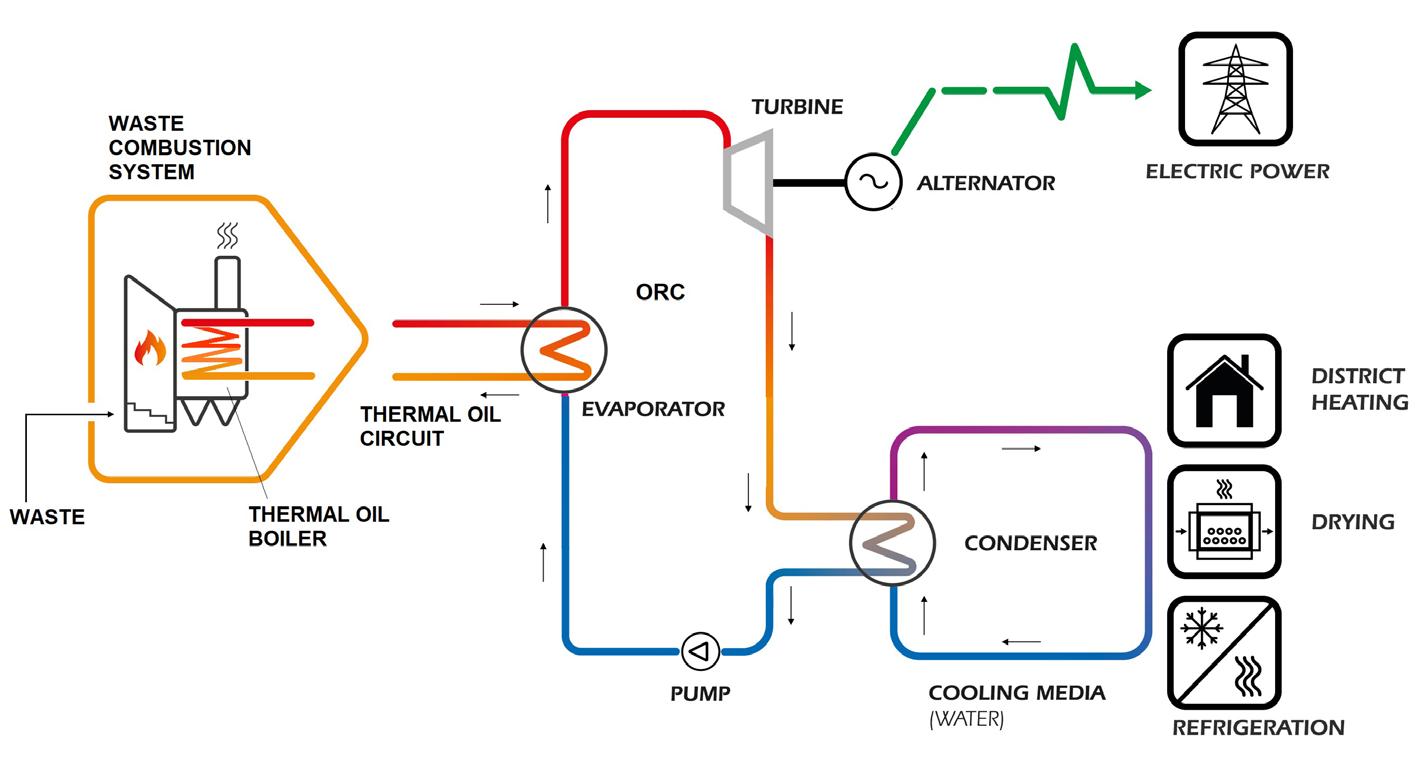
In WtE plants, one of the main challenges is the high operational and investment cost of its equipment, thus for this reason, WtE is often not realised (remaining mere waste incinerators) or their size is incredibly large in order to reduce the specific cost.
An example is the large number of medical waste incinerators in which the thermal power produced (typically from 1 - 5 MW thermal) is not utilised but rather dissipated to the atmosphere, with the further expense of electric power (to run air coolers) or water. This situation is mostly linked to the high operational cost of classic steam cycles such as water treatment and the obligation to have a certified operator on-site.
Case studies such as Güres suggest that these obstacles could be solved by employing thermal oil and ORC systems, in order to create power streams where currently energy is wasted.
In this regard, it may be useful to look back at what happened in the early 2000s in the biomass-to-energy market in the EU, especially Austria, Italy, Germany and Latvia, where Turboden realised more than 200 ORC plants sized between 200 kW and 2 MW.
In these projects, ORC technology was crucial to solve the operational challenges posed by the small size and, on the other hand, to easily find thermal users in order to go with CHP co-generative configurations, where not only the electric power, but also the hot water could be utilised (i.e. drying or district heating).
This was similar to what was achieved at Güres, where the 70˚C water output is employed in the drying of the manure and in the heating of the chicken cages (in winter).
ORC and the quest for decentralised WtE plants
Could the world expect an increase in smaller WtE plants? The example of Güres and many others suggest that figures may work in some specific contexts, and definitely the implementation of thermal oil and ORC systems instead of classic steam cycles (which still remain competitive in larger plants above 10 MWe) can help out.
There are many other criteria to consider, such as the cost of energy, the policies and regulations of the specific country, and the geographical position of the plant (i.e. distance to electrical or thermal user).
The new circular economy principles introduced by the EU are having an impact on the design of next generation waste treatment plants. For instance, there is a clear preference for CHP systems and considerable emphasis is given to proximity. Both those principles together suggest that the waste treated
Figure 4. Simplified scheme of a WtE plant with thermal oil and ORC technology. Figure 5. Turboden ORC systems are designed to contribute to the path towards decarbonisation. should be available locally and plants should be built nearby to heat users for higher total efficiency rates. This would help to reduce the impact of waste logistics on road transport and would make low carbon heat and green power available to local communities. In addition, as separate and selective collection of municipal solid waste should be prioritised, the availability of residual waste will most likely decrease in the future pushing to smaller size. In fact, a small WtE plant is more flexible to cope with waste variations/shortages, which also mitigates financial risk. Turboden has awarded and built 21 ORC plants with a total installed power of approximately 60 MW. This figure covers a variety of installations in various WtE plants including medical, industrial, animal waste, and sludge incinerators. Most of these plants were installed in the past five years, with power installed between 1 - 13 MW. In the near future, Turboden also plans to add some old biomass plants that are being updated in order to receive a fuel mix that includes both biomass and RDF waste (in ratios from 2:1 to 1:1), a trend that may contribute as well to the diffusion of decentralised WtE plants.
