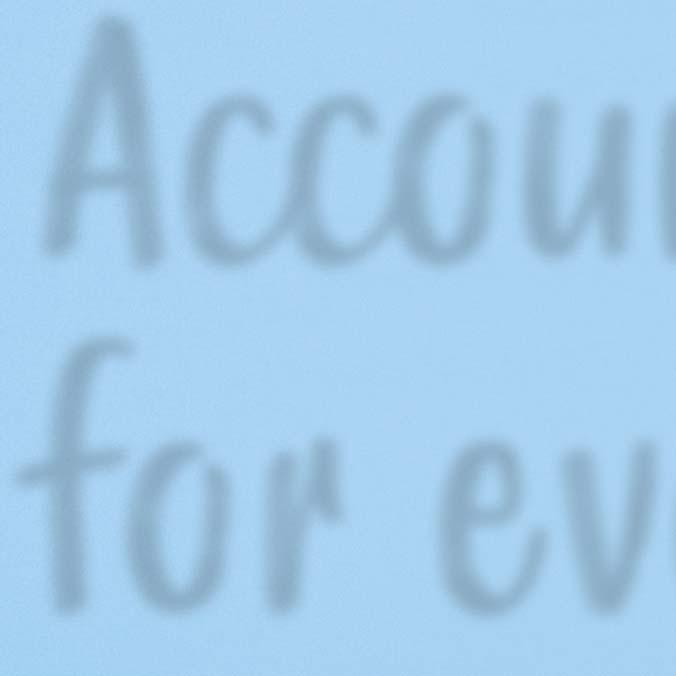
5 minute read
Accounting For Every Step

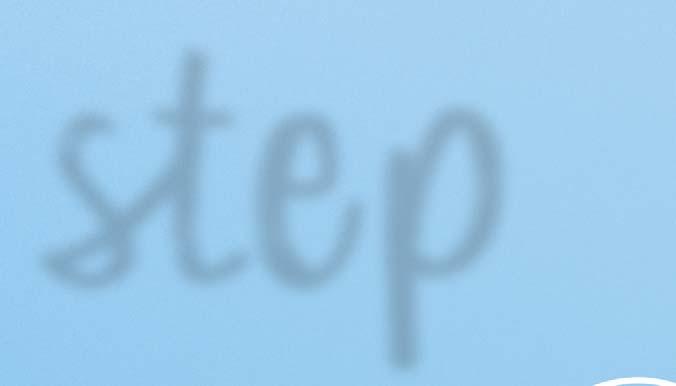
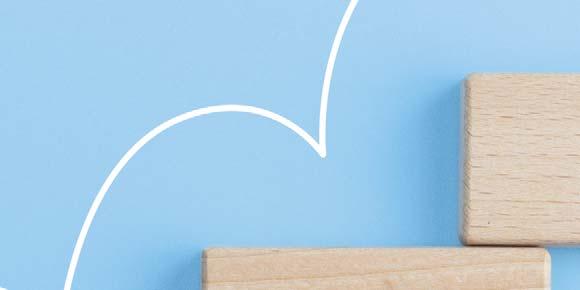
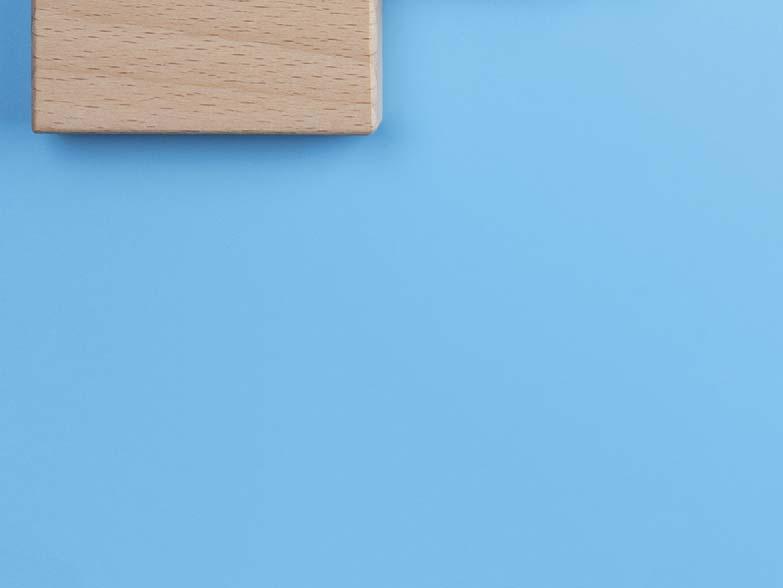
ALLU Finland describes how a single piece of equipment can incorporate the several steps involved in the mining process.
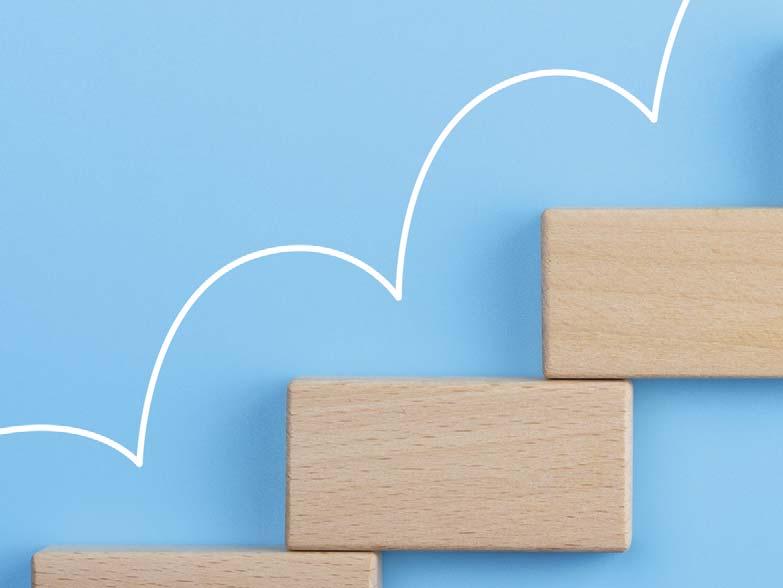
Game-changing technology seems a rarity in the mining industry. It may have moved on from picks and shovels, and opencast mining has been transformed by the use of sophisticated crushing and screening equipment, but mining can still be a relatively labour-intensive undertaking, with advantages accruing to operators in parts of the world where such costs are low.
Much of the equipment required can also be expensive. There are quite a few steps involved in the mining process: blasting of the rock, digging, loading the product onto dump trucks, and transporting it to a location where the material
can be crushed and screened. Sometimes, more than one crushing and screening step will be needed to produce a material ready for shipping.
The possibility that several of these steps might be incorporated in a single piece of equipment seems to have inspired the development of ALLU’s M-series giant crushing bucket. Applicable as a crusher to the full range of soft rock materials – such as oil shale, coal, rock salt, limestone, and gypsum – and as a screener for all materialsm, it performs material processing and loading in a single step.
When the package is mounted onto a 50 – 100 t wheel loader or 60 – 200 t excavator, it turns the vehicle into a mobile processing plant, eliminating much of the requirement for faster transportation between sites. There is also no need for on-site electrics.
The M series buckets can be adjusted to accommodate diff erent sizes of material (typically from 50 – 150 mm) and diff erent crushing forces, and so can be configured to handle any kind of soft rock. The company sees a potentially transformative role with respect to a mineral resource. A typical feedstock might include boulders of up to 500 mm dia. (700 mm 10%), which can be crushed down to 75 mm by the M series bucket for loading directly into dump trucks. Any waste hard rock that is found in the run-of-mine (ROM) is also removed in one simple step – or the majority of it, at least – at source, increasing the quality and the volume of material that can be loaded into the dump truck and improving yields. A similar principle can also be applied in many screening or crushing applications. The ALLU hydraulic attachment can process feedstock down to 50 mm at the source, removing waste material in one simple step, simultaneously, and in such a way that reduces double handling of material, as well as cost. The company has been developing its screening bucket technology for over 30 years, and nowadays, it can be applied to everything from screening municipal waste to detonating anti-personnel mines. Technology such as this can be used to overcome the cost advantages enjoyed by operators in other parts of the world. Margins in coal mining are extremely tight, so if there is the possibility of reducing the cost of production by a few tens of pence per tonne, the potential of the product seems obvious. The company has also designed a smaller version of the M bucket to meet its customer’s needs and requirements. The M3-36 has been designed for agility and work speed for the customers’ requirements, giving them a one-step requirement. The M3-36 is currently being tested with customers and should be available to the wider market soon.
Figure 1. ALLU Transformer M-series processing coal.
Table 1. Cost savings – equipment
Equipment in operation Before Aft er
Processing buckets Three buckets One ALLU Excavators Two units One unit Back-up buckets One bucket Zero buckets Running costs Two units One unit Service cost Three units One unit
Stand-by service personnel One
Bucket service interval Daily
Table 2. Cost savings – material and conditions Zero (equipment maintenance outsourced) Once every two months
Case study
A coal power plant that requires a minimum fuel production of approximately 20 000 tpm got in touch with ALLU regarding the company’s M-series attachment.
Material and conditions Before Aft er
Material mix (slurry/high grade) (%) 25/75 50/50 Received coal slurry Pre-screened Untreated Wet weather conditions Problematic Normal
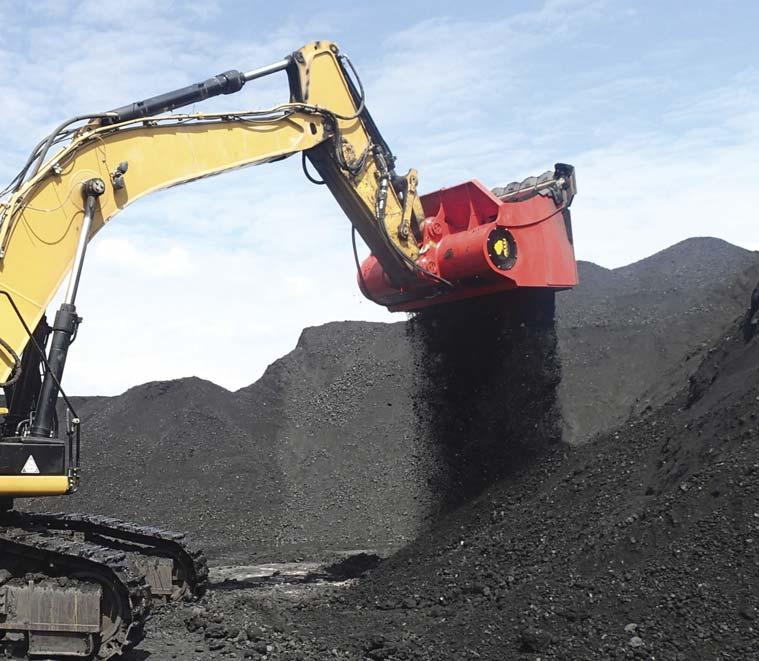
Challenges
The plant had experienced many challenges in the past which had affected fuel production, including: Wet weather conditions, which created sticky material, making it a challenging material to process with small volume buckets. Wet, sticky, low cost coal slurry needed to be mixed and crushed with imported high-grade coal. This possible one third material mix ratio was not optimal for maximum cost efficiency. In the past, a minimum of three-piece standard processing buckets and three-piece excavators were needed. Therefore, a high priority electricity production source that operated 24/7 was required that had a high capacity and continuous fuel flow, so as to help with running costs. Standard processing bucket construction and design did not meet the requirements of equipment durability and service costs.
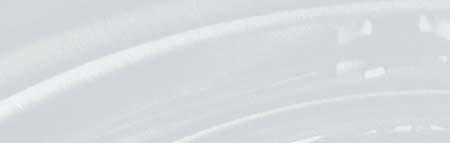
Solution
ALLU suggested using ALLU Transformer M screening buckets for compact base machines. These are also suitable for excavators (maximum 160 t), loaders (90 t), tractors, and backhoe loaders.
The M-series makes for a good attachment for soft rock crushing and mining processes. The attachment reduces the need for buffer storage areas and material transportation. In addition, investment costs are lower than that of stationary processing stations, due to easy and fast transportation from one site to another and the elimination of the need of electrics.
The implementation of the M-series resulted in the following: The big volume bucket and large drum means it is easier to process wet and sticky coal and cope with the wet weather conditions. The high performance makes for a more cost-effective 1:1 fuel mix possible. There is a need for only one unit to achieve the needed capacity, resulting in very low running costs. The equipment is highly durable and has very low service costs.
Conclusion
Whether it is a small mining operation, a contractor working in several mining operations or a large opencast mine, crushing and screening methods using the loader or excavator as the primary or secondary processing machine (such as that from ALLU) can help reduce costs and boosts efficiency. End users such as power plants, storage areas, harbours, and classification sites can also use and benefit from this method.
Visit us! MINExpo, Las Vegas, Nevada, USA September 13– 15, 2021 Central Hall, Stand 8471