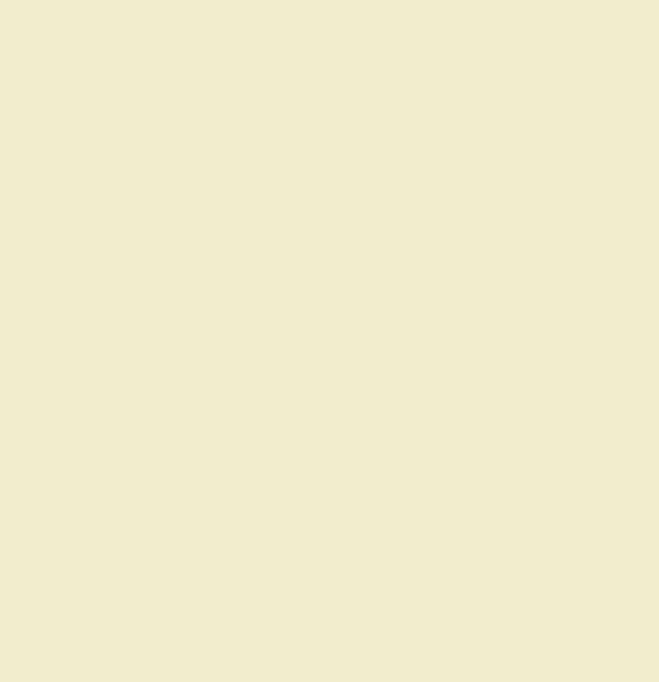
10 minute read
Weighing Up The Options

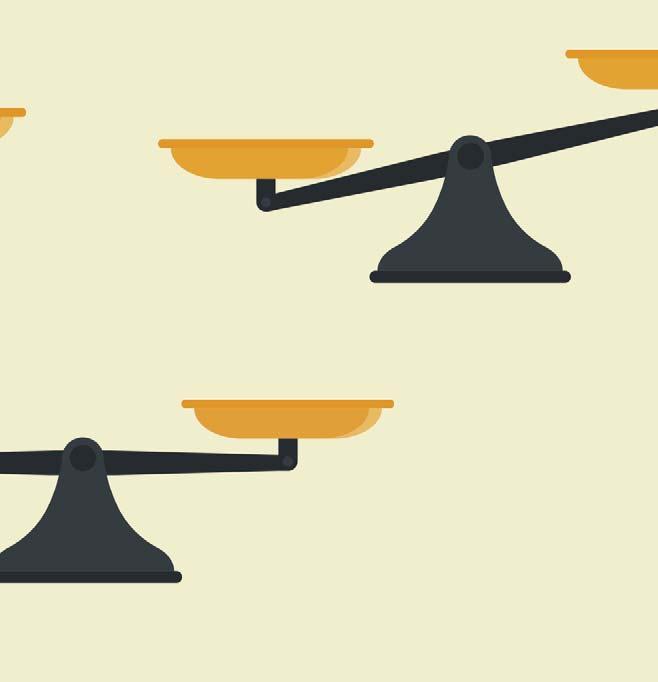
Caleb Tidball, Cardinal Scale, USA, discusses whether analogue or digital trucks scales should be used in coal mining production.
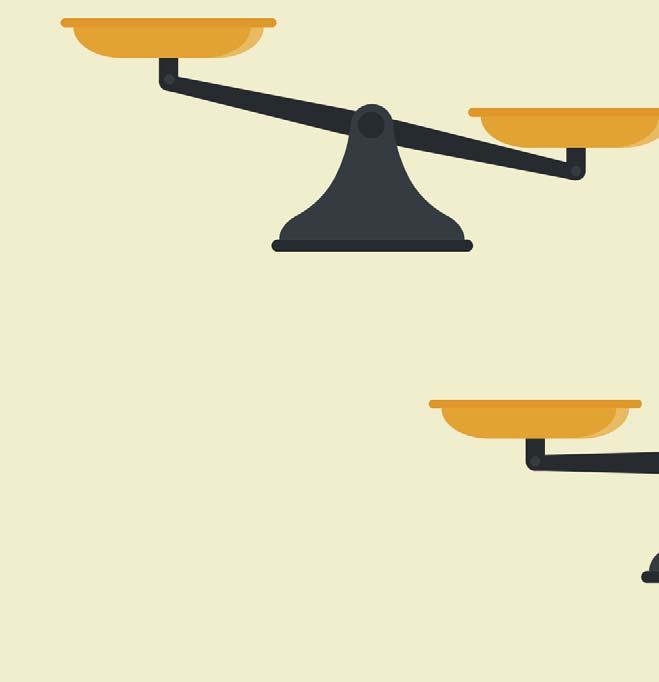
Coal mining is a critical part of meeting the world’s energy demands. The coal industry requires a great deal from its truck scales: accuracy, longevity, and the ability to operate consistently for long periods of time without breaking down.
Meeting increasing energy demands requires high performance from equipment used to weigh coal. Therefore, researching the variations of truck scale types and their respective attributes is an important process, and the diff errent advantages of analogue and digital truck scale systems should be considered.
Analogue truck scales
Analogue truck scales are the most common type of truck scale available on the market. This type of truck scale combines electrical signals from individual analogue strain gauge load cells and sums them in a junction box. These combined signals are then fed from the junction box into an indicator and converted into a digital value displayed for the customer to view. Analogue load cells come in many variations, but the two most common types used in truck scales are the compression load cell and the shear beam load cell.
A truck scale system employing analogue load cells has some distinct advantages. Analogue load cells are inexpensive, have been on the market for a relatively long period, and have a fairly wide range of weight capacities.
However, analogue load cells have many drawbacks. Because of their construction and electrical characteristics, they are especially sensitive to lightning damage. When a 70 ft long piece of
steel (i.e. a truck scale platform used for weighing coal) is placed in an area outside, it becomes a lightning rod that is very susceptible to lightning strikes. Suppression circuitry is added to the overall wiring to divert extreme lightning current from the strain gauges. However, this does not prevent load cells from being destroyed by lightning, which then require replacement by a trained scale service technician.
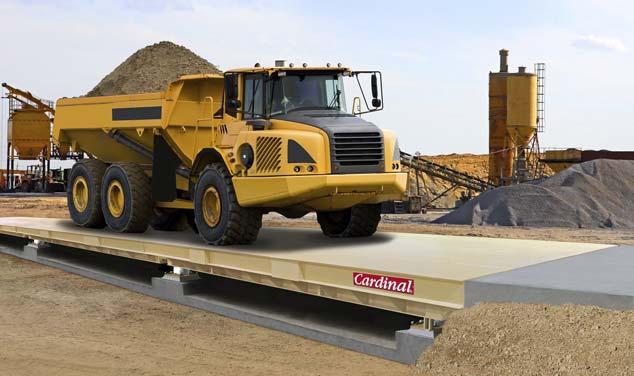
Figure 1. Digital truck scale designs provide a higher level of protection than analogue load cell types in brutal, unforgiving environments.

Figure 2. Weighbridge designs that place load cells up near the top of the scale deck provide maximum protection against sediment and moisture build-up at the foundation, which can aff ect load cell performance.

Figure 3. Steel decks with tighter I-beam concentrations welded side by side in close proximity are engineered to withstand repetitive, heavy truckload weighing more so than steel deck designs that space I-beams further apart.
Digital truck scales
In a digital truck scale system, the load cells perform the analogue-to-digital signal conversion themselves, and produce a native digital output signal. This important distinction precludes signal degradation associated with analogue cells.
Digital load cell systems are also much easier to manage, due to the lack of a junction box and its associated wiring requirements. This decreases the installation time needed for scale service technician wiring – digital load cells can be simply linked to one another in a daisy chain. Sense leads are eliminated since variations in system voltage will not impact the load cell.
Digital truck scale systems, because of their simple design, are very easy to install, maintain, and repair. Since the load cells are more reliable and accurate, costs associated with diagnosis are decreased. Digital truck scale systems have the capability of detecting and diagnosing faults and failures more quickly, eff iciently, and precisely. To help augment this valuable tool, this information can be sent to not only indicators, but to remote locations via a soft ware link. Digital load cells also off er the highest protection against lightning strikes, due to the transient suppression circuitry that is located directly on each individual digital load cell.
Increasing the value and longevity of their businesses are two of the most important aspects coal mine owners and managers should consider. Since mining vehicles tend to be much larger than standard commercial transportation vehicles, there are problems that are compounded when weighing minerals during transport. Overloading and off set loading are going to do much more damage to trucks and scales. Truck scales are more likely to break down due to larger cargo sizes, off set loading and overloading, and repeated heavy usage incurred during their lifespan when used in a coal mining operation.
Analogue vs digital
Effi ciency and operating costs
Two other important points coal mine owners should consider are increasing efficiency and lowering operating costs. Truck scales specifically built for mining operations will provide a hedge against all of the aforementioned difficulties while saving money in multiple facets of a business. Using a tool like a truck scale can increase profit margins by maximising payload, protecting return on investment for transportation vehicles, helping businesses better manage fuel consumption,

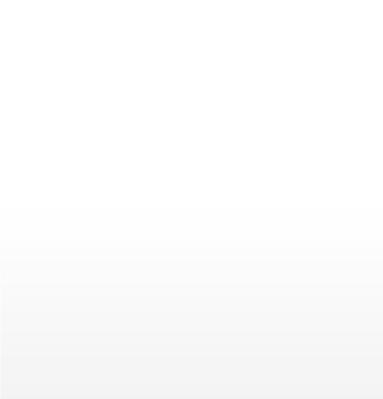
lowering operating costs, and cutting costs related to vehicle maintenance.
Due to the enormity of most mining vehicles, the truck scales that would be most appropriate for such an application would possess a high concentrated load capacity (CLC) rating, have a high maximum capacity, and generally have a wider deck to accommodate heavy-duty off -road vehicles. Scales that possess a tighter I-beam spacing configuration under the scale deck will be more suited to repetitive, heavy loading from large transportation trucks. Structurally, the scale deck will have to be thicker than that of a standard truck scale and have load cells that are also rated for a large capacity. Digital load cells are a good option considering the surroundings and environment that usually accompany a mining operation. In addition, digital load cells can aff ord mine owners, or their scale service company, the luxury of remotely monitoring scale performance and receiving real-time load information. All of these factors provide fail-safes against potential problems that will cost coal mine owners time, money, and valuable resources.
Downtime due to load cell and scale deck failures can be very costly and should be seriously considered before deciding what type of truck scale will be used for an operation. Analogue load cells have the most potential for error due to the vast amount of wiring and junction boxes, and the diagnosis process can vary wildly depending on these factors. They also will be most-susceptible to moisture, fluctuations in weather, and sediment and grime that can get into the wiring and entrances of analogue wiring systems. Digital truck scale systems either mostly or completely eliminate wiring issues that cause expensive downtime and long diagnostic times that can last for days.
Truck scales that feature thinner decks and fewer I-beams under the scale deck are a recipe for potential deck damage. Once a deck has been damaged due to low spots in the scale deck, known simply as ‘dimpling’, the deck is exceedingly diff icult and costly to repair, if it can be salvaged at all. Thicker truck scale decks and more closely-concentrated I-beams provide a more robust structure that is less susceptible to overloading and off set loading that is common in coal mining transportation. Truck scales should also provide I-beam protection that runs the full length of the deck: the ends of the truck scale weighbridge that house load cells might have a pocket with no reinforcement, which increases the probability of weighbridge damage and an inoperable scale. Environment Regarding the environment, it is important to know what limitations are going to be in store for the truck scale in a given application. Sediment and filth are pretty much a given in a coal mining environment, but there are other factors that are just as damaging. Temperatures, either extreme hot or cold, can present unique challenges for truck scales and hardware peripheral equipment. Once again, analogue systems present more challenges due to wiring expanding and contracting, being exposed to moisture, and having more wiring YOUR MINING MACHINE DESERVES THE BEST CHAINS Cincinnati Mine Machinery Company designed and installed the first Dual Sprocket Conveyor Chain. Our unique design utilizes superior metals and a proprietary heat treatment process for unparalleled strength. Our Dual Sprocket Conveyor Chain runs longer and stronger which means less downtime and lower cost per ton. So when it's time to choose, choose the strongest chain under the earth. For over 90 years, Cincinnati Mine Machinery continues to be THE STRONGEST LINK .
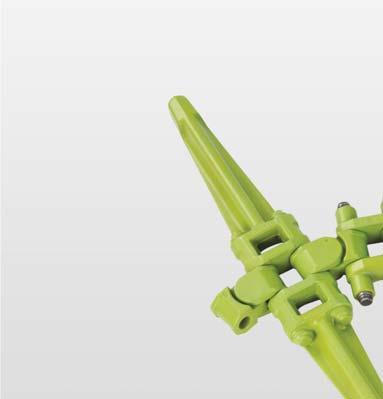
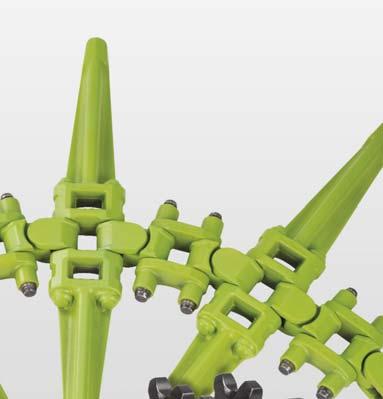

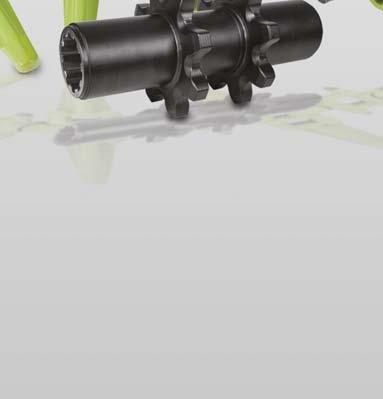
surface area that has the potential to be damaged. Truck decks that protect load cells by keeping them enclosed or elevated from areas that accumulate sediment keep the possibility of load cell damage much lower. Placing load cells in an enclosed area also allows for more protection from damage sustained due to extreme temperatures and moisture. Digital load cells that inject potting into load cell compartments also preclude moisture and sediment ingress from damaging internal components. Truck scale systems that deliver these protections provide more continuous use and prevent load cell and wiring complications.
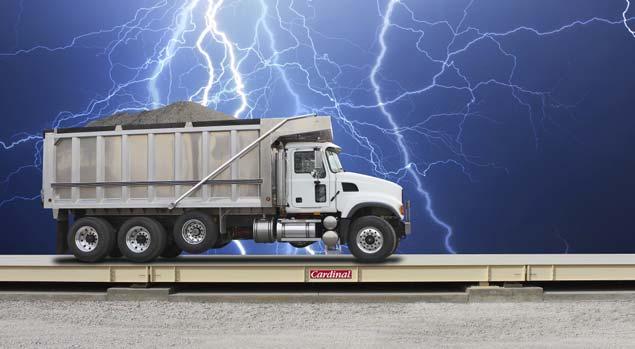
Figure 4. Digital load cells with proper grounding installed provide a more robust defence against the damaging threat of lightning strikes. Lightning strikes can compromise the integrity of the whole weighing system.
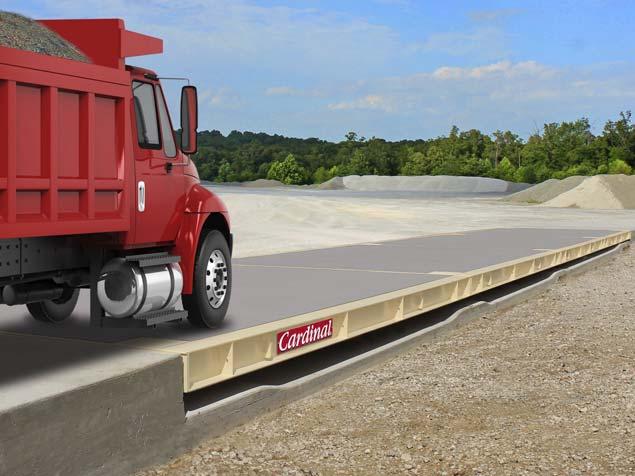
Figure 5. Concrete deck truck scales are especially useful in slippery, wet or cold environments, and many scale service companies feel they provide better tire traction than checkered steel decks. Scale damage
Coal mine owners should also consider scale systems that provide protection against scale damage caused by: truck scale movement spurred on by trucks moving onto the scale, speeds above the recommended limit, overloading, and off set loading. Most analogue truck scale systems, and some digital truck scale systems, utilise bumper bolts, flexures, and check rods; though they are used to restrict deck movement brought on by trucks entering onto a scale platform, they can be damaged themselves or cause damage to the truck scale if ‘jarred’ hard enough. Digital scale systems that allow for passive checking systems that eliminate these pieces of hardware are going to last longer, protect against truck scale damage, and prevent excessive motion. Passive checking systems are much simpler in design and more durable over the life of the digital truck scale – they are also much easier to replace should a load cell or load cell stand become damaged or inoperable.
Digital truck scale systems provide a more informative instrument in comparison to analogue scale systems regarding information quantity and quality. Digital truck scale systems provide more information that can be processed and reported, giving businesses a more accurate depiction of daily, weekly, monthly, and yearly processes. This information can be viewed remotely, and dealers and maintenance personnel have access to this information around the clock. Malfunctions, electrical failures, power issues, and errors of any kind can be easily diagnosed and corrected. The unique advantage of knowing exactly what is not working in a truck scale system gives a coal operation the capability of running a more eff icient, flawless process.

Figure 6.Thicker truck scale decks with superior structural integrity provide a higher concentrated load capacity rating, which will prevent deflection from permanently damaging the weighbridge.
Conclusion
Coal mine owners should consider some of these issues when selecting either analogue or digital options for their operation. The application of their prospective scale, the structural requirements of the scale, the potential costs that might be associated with their application, and the environmental characteristics of the mine where the scale will be operating are good starting points to guide mine owners in the pursuit of finding the scale that will be most-suitable for their business.