
7 minute read
The Only Way Is Up
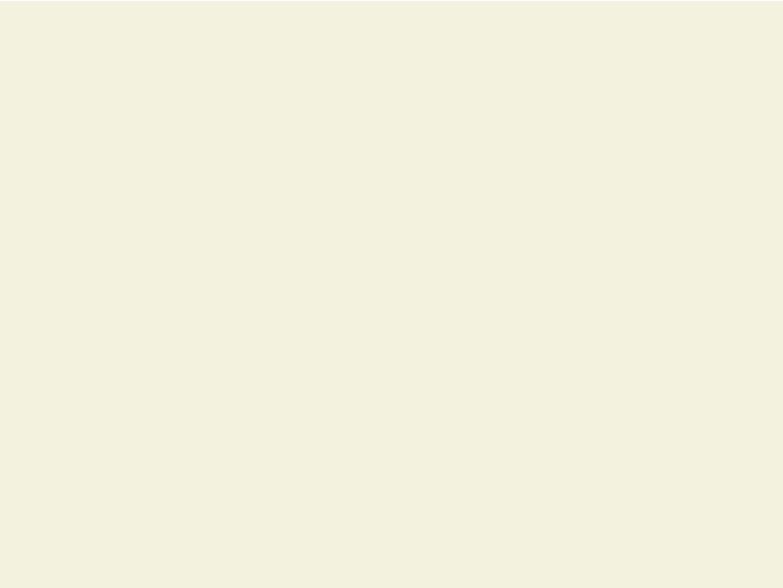
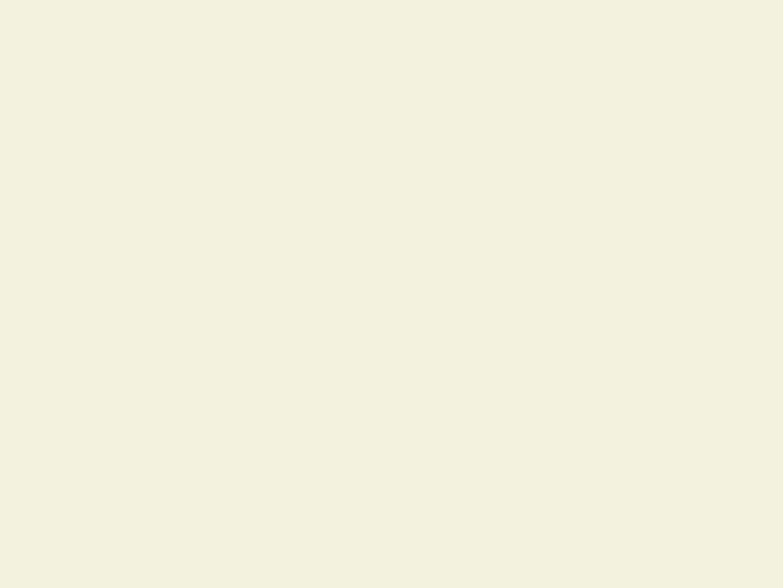
Richard Spaargaren, ESI Eurosilo, the Netherlands,
outlines how fully enclosed coal storage enables future-proof and more sustainable performance of today’s coal fired power plants.
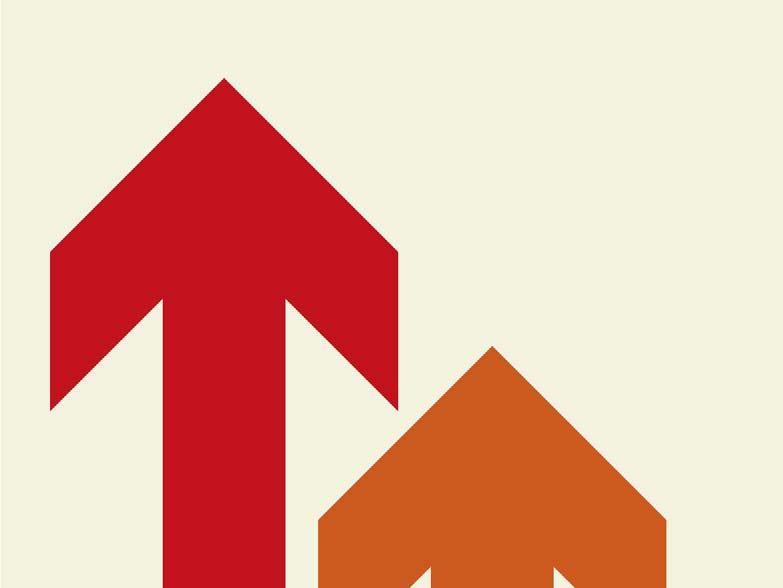
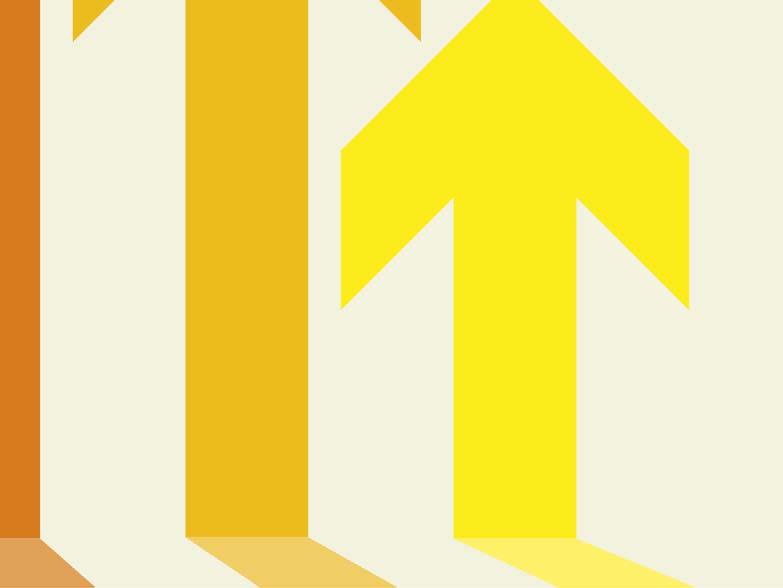
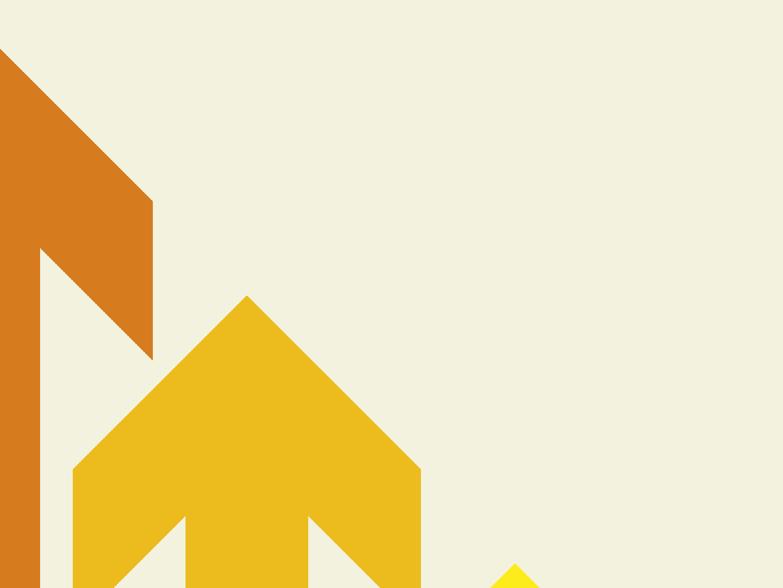
With an abundance of space at power plants built over 40 years ago, the handling and storage of coal was not considered a critical factor. Therefore, when ESI applied fully enclosed storage, originally designed for agri-bulk in the Netherlands, to large scale storage facilities for coal in the early 1980s, it was a revolutionary idea at the time. The early adapters of this system were looking for premium alternatives with high added value, such as the Salmisaari Power Plant in Helsinki, where the complete coal storage moved underground in four connected Eurosilos. Fast forward to 2021, and the world has changed dramatically. Although open stockyards as legacy systems are still common practice, the recent developments show a tipping point towards enclosed storage.
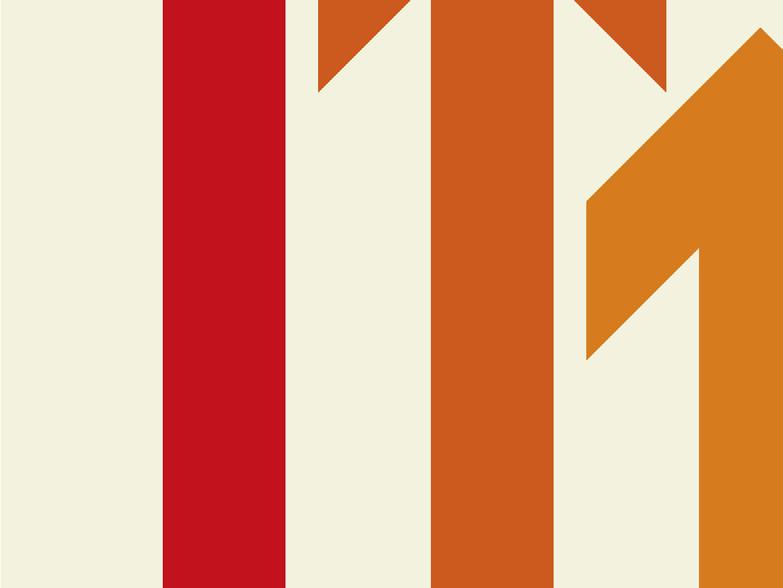
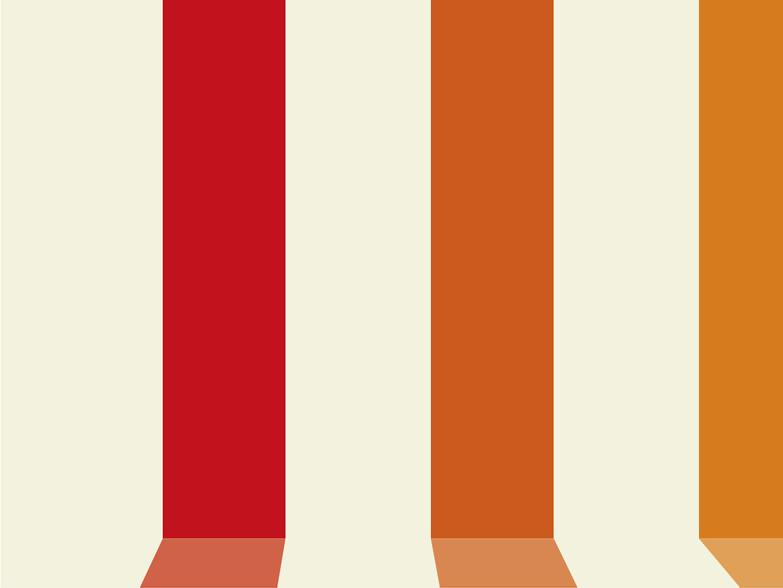
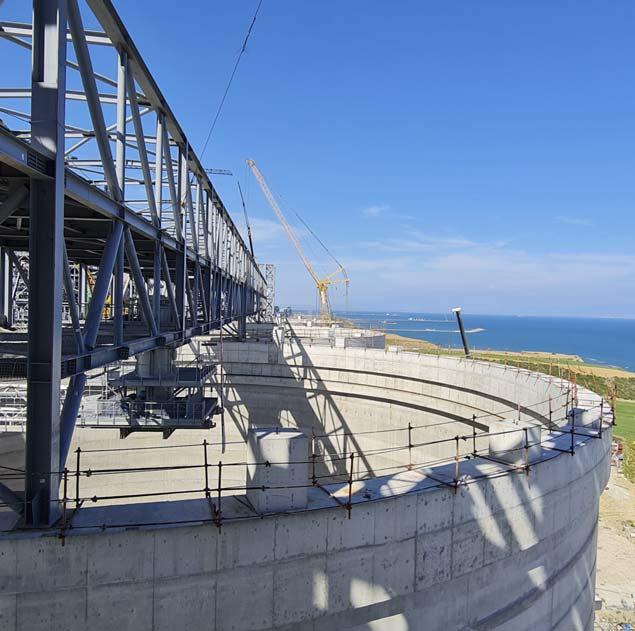
Figure 1. Silo roof construction of Hunutlu plant.
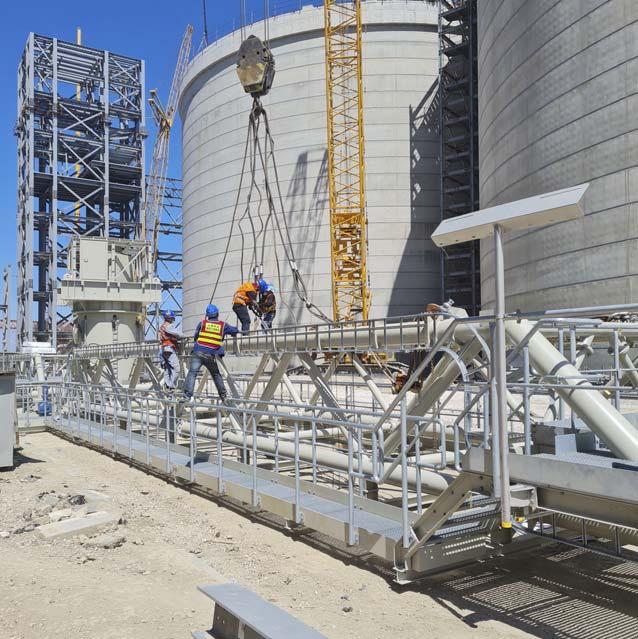
Figure 2. Preparing the slewing bride for the lift at Hunutlu Power Plant.

Figure 3. Eight coal silos at Sin Seocheon Power Plant in South Korea.
More pressing considerations
The main criteria in deciding on silo storage has not really changed since the introduction of the Eurosilo. However, the ever-increasing need for power, due to economic growth, together with an increased and denser world population, have made these considerations more pressing than before.
Space and capacity considerations
Particularly for restricted areas, the volume-to-area storage factor is of major importance. Silos are the most compact form compared to covered storage piles, whether circular or rectangular. The same volume can be stored at a third of the required land space for stockyards.
Environmental considerations
Dust emission, water percolation, and ground pollution have become decisive factors in obtaining permits. With renewables still not in reach in terms of capacity and cost per KW/h, the most viable third way is clean and environmentally safe operation of sophisticated coal fired power plants.
Safety and fi re considerations
Silo storage minimises the intrusion of oxygen in the stored coal. Carbon monoxide-detection systems can detect self-heating spots immediately so that eff ective measures can be taken. The enclosed configuration makes it possible to purge nitrogen into the stored mass, which makes combustion impossible.
High degree of automation
Highly automated filling and reclaim systems reduce labour and health hazards, as well as the need for cranes and shovels. Automated material handling also enables coal blending by reclaiming diff erent grades of coal from diff erent silos and mixing it to an optimal blend.
System operation in detail
The Eurosilo system consists of a slip-formed silo shell, with a 30 – 50 m dia., and a storage height of 30 – 50 m. The silo is mounted on a concrete foundation, including a concrete reclaim tunnel, and is covered by a steel roof that supports the infeed conveyor, which discharges the coal into the silo. In case of a multiple silo system, the coal can be transferred to an adjacent silo by installing a two-way diverting gate.
The coal enters the Eurosilo via a telescopic chute, mounted at the centre of the upper slewing bridge. This slewing bridge is supported by a ridge mounted crane track. The slewing bridge also contains electrical equipment, a slip-ring assembly with electrical and air connection, slewing drive wheel assemblies, and the winches that support and operate the distribution frame. A distribution frame is suspended from the slewing bridge by steel cables and contains the main twin screw system and the lower section of the telescopic chute. The coal is discharged via the infeed conveyor into the telescopic chute and reaches the distribution frame on
the coal surface. In stacking mode, the twin screw system distributes the coal evenly over the area of the silo. Aft er each rotation, the distribution frame is raised by the winches, so the silo is filled layer by layer.
The reclaiming capacity may vary up to 1500 tph. To ensure an uninterrupted output to the day bunkers, each silo has two vibrating reclaimers. Electrically powered counterweights provide the necessary force to induce gravity flow in the centre and to discharge the coal onto the reclaiming conveyors. By withdrawing the coal from the bottom of the silo, a core flow is established. At this point, the distribution frame’s conveyor screws reverse their rotation, directing the coal to the centre of the silo and continuously feeding the formed core. The upper slewing bridge also rotates in the reverse direction, and aft er each complete revolution the distribution frame is lowered.
Dynamic coal blending
Dynamic coal blending is a fuel handling approach whereby the coal quality can be continuously changed – within acceptable limits – in order to meet changing needs in real time. The Fuel Management System (FMS) helps to prepare the right blends at the right time. The FMS soft ware visualises the diff erent grades of coal in diff erent silos and enables the operators to plan the coal blending in the optimal way. The boiler specifications and the coal characteristics are the input data for the FMS solution as well as real-time storage levels. The diff erence with conventional one blend for all conditions can save €1 – €3 million/yr at a 1000 MW power plant.
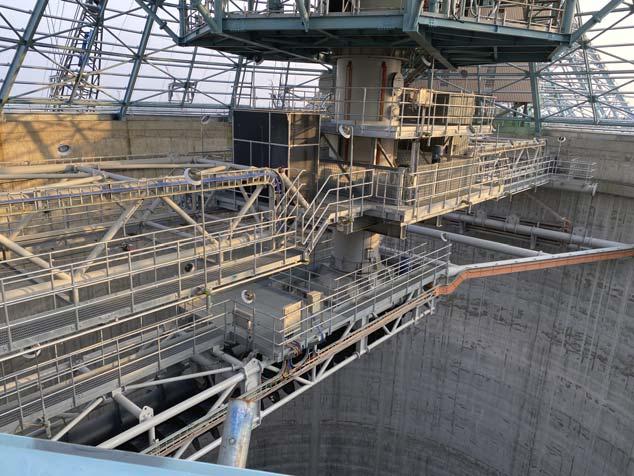
Figure 4. Erection of the coal silo equipment at Sin Seocheon Power Plant.
Figure 5. Silo erection Shi Dong Kou Power Plant (October 2020).
Lowest TCO, short payback period

In order to have an accurate assessment of costs and savings, the total cost of ownership (TCO) over the total life span for diff erent storage methods needs to be examined. Due to its enclosed storage concept and highly automated operation, the Eurosilo system combines a higher CAPEX than conventional stockyard storage, with a much lower OPEX. Dust emissions are eliminated, which can lead to coal savings of several percent. If 2.5% of the coal is blown away, this can easily result in 25 000 tpy for an average 600 MW power station. In order to prevent this, enormous amounts of spraying water are used, which have to be evaporated later on. This decreases the calorific value of the coal mass in the same way as heavy rainfall. On top of that, the cost savings on operational staff and bulk handling material, together with use of optimal coal blends, result in a payback period of just 4 – 5 years. Given a life span of 25 years, it all amounts to the lowest TCO.
Case studies
The global concern for a sustainable future has become more evident than ever. This leads to a demand for innovative technologies that enhance performance and minimise pollution, while being economically viable at the same time.
Turkey
This is why the EMBA Hunutlu Thermal Power Plant in Turkey chose to work with three 100 000 m3 Eurosilos. The Hunutlu Power Plant is located in a precious nature reserve and therefore complies with the highest environmental requirements, taking up as little land space as possible.
South Korea
In South Korea, at the new thermal power plant in Shin SeoCheon, ESI is in the process of building and commissioning no less than eight coal silos.
China
Finally, the Shidonkou First Power Plant in Shanghai ordered two 100 000 m3 coal silos to be built at its existing plant site. With this order, the China Huaneng Group has initiated its shift from open and shed storage to environmentally friendly enclosed coal storage.
Conclusion
When considering the feasibility of a coal silo project an integral estimate of investment, the operating and maintenance costs should be formulated, including costs and savings with regard to environmental protection.