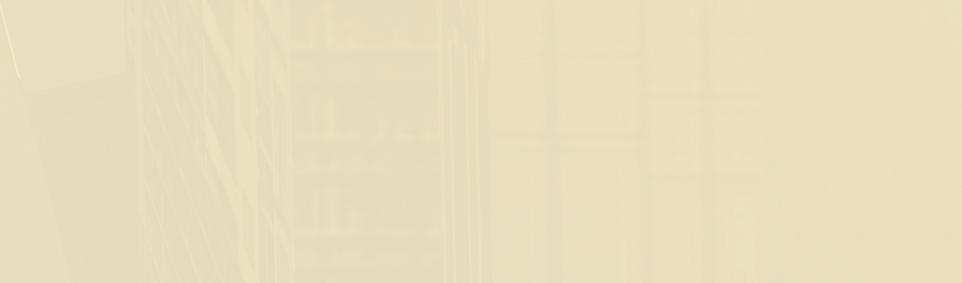
8 minute read
A Bridge To The Future
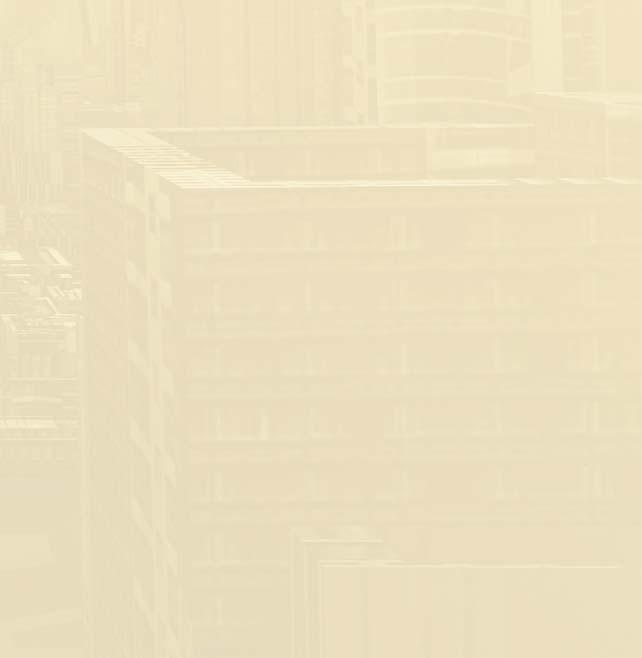

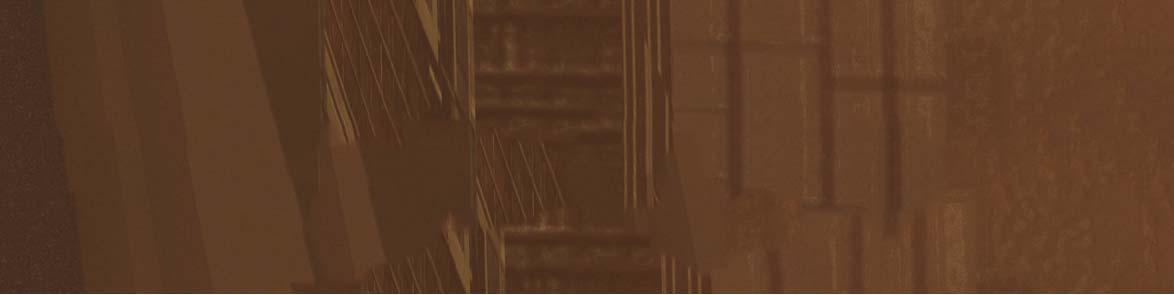


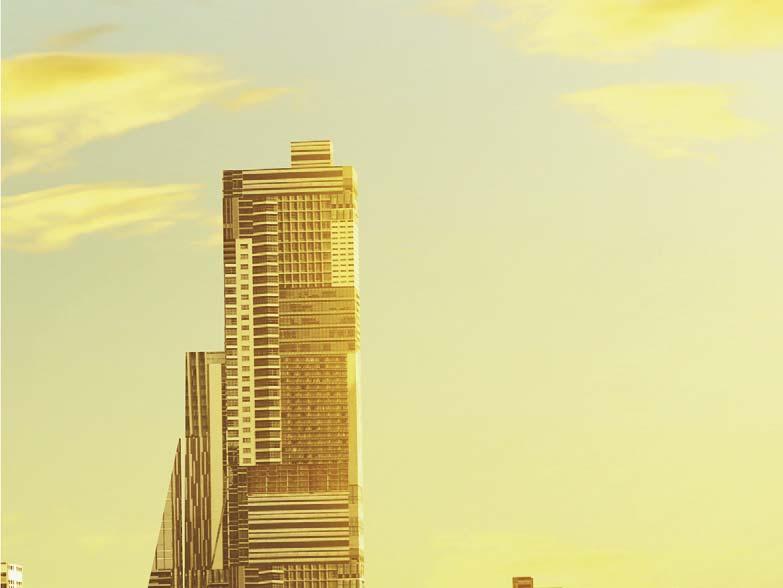
Thiru Veeraraghavan, A.W. Chesterton Co., USA, provides insight into how using the Internet of Things for preventative maintenance can thwart pump and valve failures in aluminium processing.
Acritical aspect of mining and producing aluminium is processing bauxite. This process, which goes by the term ‘The Bayer Process,’ was invented more than 100 years ago by Austrian scientist, Karl Josef Bayer. During the procedure, aluminium hydrate is extracted from bauxite ores to produce 1 t of aluminium for every 2 – 3 t of bauxite.
Case study: North American aluminium processing plant
At a global mining company's extensive aluminium processing plant in North America, over 1 million tpy of aluminium is produced using this process. Although oft en overlooked, this facility, like every other aluminium processing facility, counts
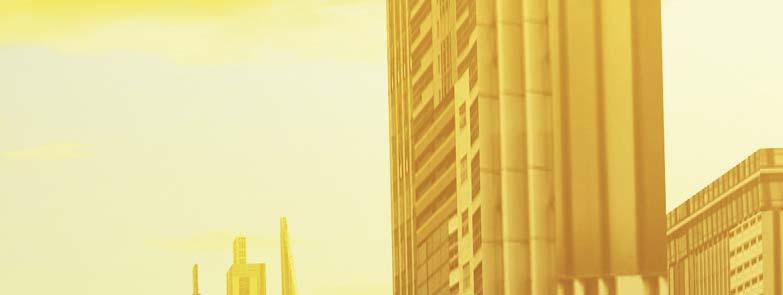
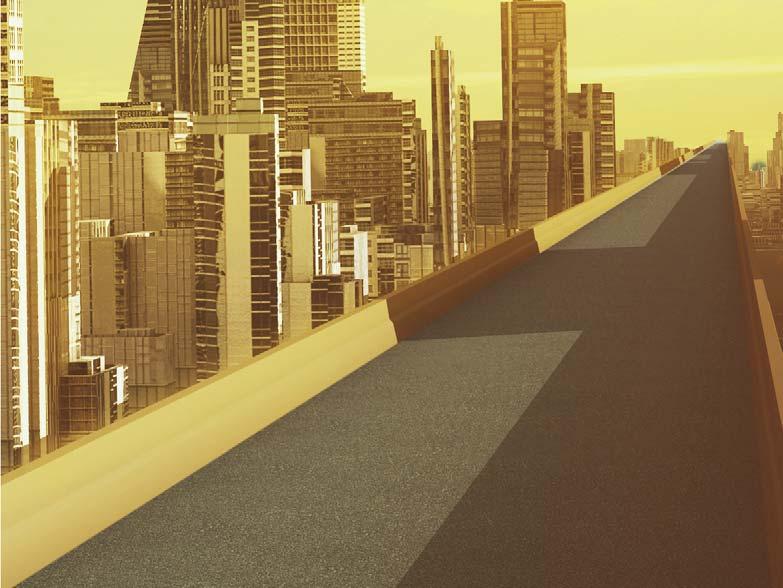
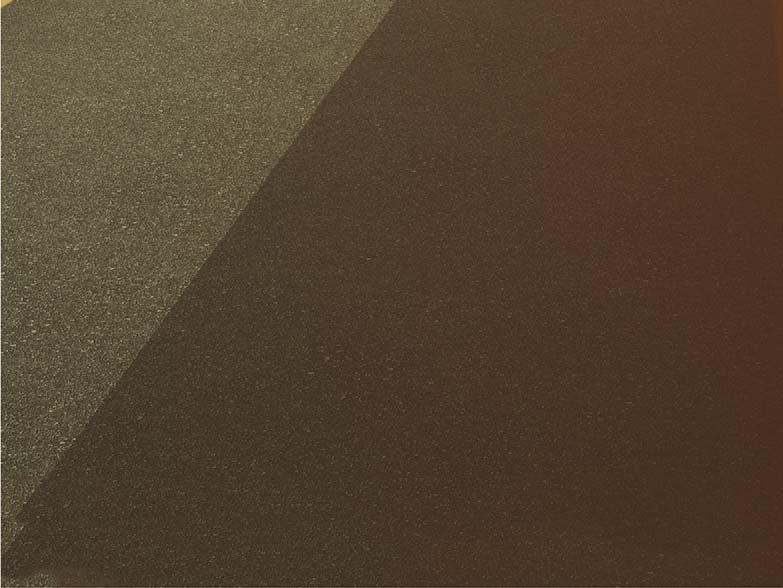


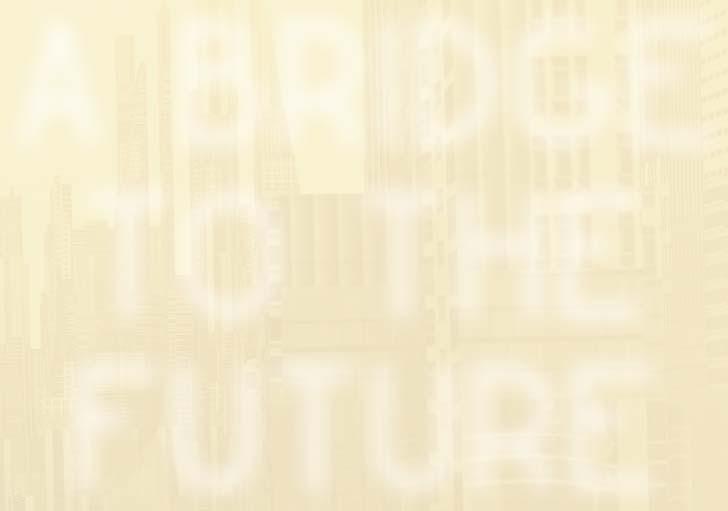
on the reliability of pumps and valves, in various stages of the process, to minimise downtime and avoid catastrophic failures.
For decades, this North American plant has relied on the support of the A.W. Chesterton Co.’s hydraulic sealing solutions to ensure pump and valve reliability and extend the hours of operation between maintenance intervals, in order to increase overall asset life. In addition to mechanical seals and valve packings, Chesterton provides industrial gaskets and specialty industrial lubricants, as well as advanced wear and corrosion protection composites. The company is a knowledge provider with strong technical support and hands-on local service.
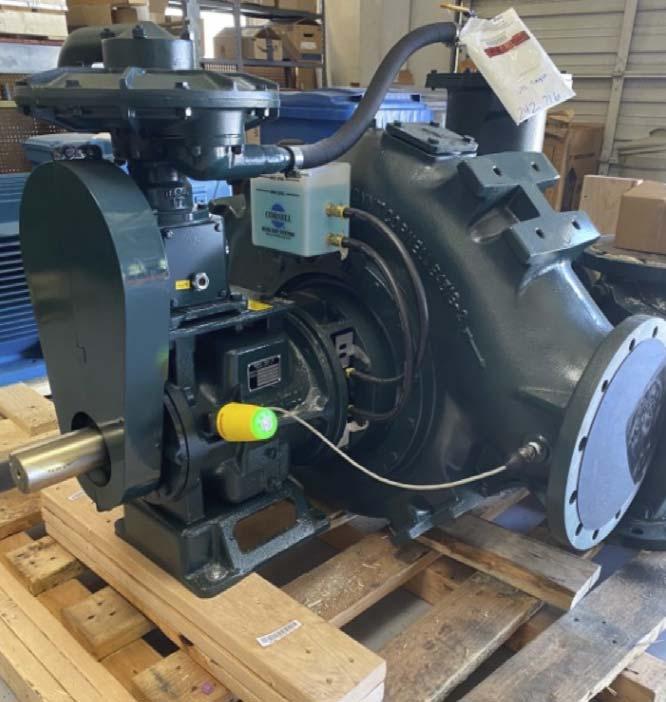
Figure 1. Chesterton Connect Internet of Things (IoT) hardware in use on a pump.
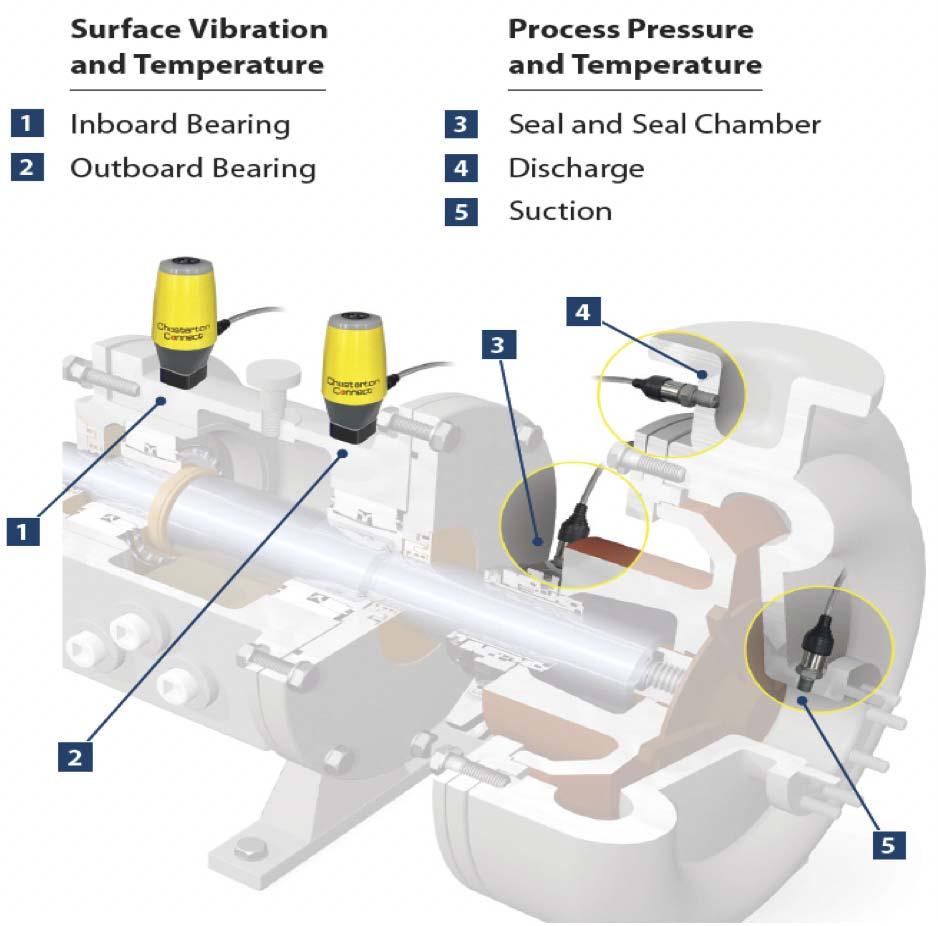
Figure 2. Illustration of Chesterton Connect being used on a pump to detect surface vibration, temperature, and process pressure. Pump vibration challenge leads to initial Internet of Things sensor implementation
In early 2020, the plant’s operators approached Chesterton regarding a vibration problem with a pump that plays a significant role within the aluminium production process. They noticed that the hydrate pump – one of the most critical pumps in the entire plant – would infrequently but aggressively vibrate when it was turned on and ramped up to 1200 rpm. Given the erratic vibrations would occur for only 5 – 10 minutes during the pump's activation, the service team could not pinpoint the root cause of the problem.
By the time servicing crews arrived with a point-in-time vibration monitoring device, it was too late to catch the vibrations. Nevertheless, the issue still needed to be addressed, as vibration can signal imbalance, misalignment, looseness, and late-stage bearing wear – all early warning signs of impending failure. Without addressing the fault, plant operators would risk needing to replace a US$40 000 pump.
To solve the problem, Chesterton suggested installing Chesterton Connect, a simple, Bluetooth-enabled Internet of Things (IoT) solution, developed in collaboration with Preddio Technologies, for 24/7 condition monitoring to pinpoint the time and area where the vibration was occurring. The plant operators agreed to adopt the approach and quickly set up a single Chesterton Connect sensor on the pump.
Diagnostic vibration information from the pump was relayed to maintenance, which allowed the customer to spot the issues that were causing the vibrations. When the pump was started, the vibration insights extracted from the sensor spotlighted a clogged impeller as the root of the problem – product had settled down inside the pump housing, causing increased vibration.
As a result of the findings, maintenance workers now know when the pump is shut down for more than 24 hours, it needs to be cleaned out before starting up again. These changes mean they can avoid doing damage to a critical piece of equipment. More importantly, from a business continuity perspective, they eliminated potential downtime and production waste, which could have run up to US$100 000/hr.
In addition to detecting irregularities in equipment performance, Chesterton Connect was also able to identify instances when the pump and valve equipment used was not the right equipment for the job. On one occasion, aft er further analysis of a similar pump valve using data extracted from the sensor, maintenance workers found that the pump valve used was the incorrect size – they would need a completely diff erent type of pump valve. These insights allowed the plant's team to take action and make slight changes to their operations, without needing to replace the US$40 000 pump fully.
The ability to easily install Chesterton Connect and identify the cause of the vibration problem on the hydrate pump (and similar pumps) highlighted the potential to facility operators for using the solution across the plant for preventative maintenance. Rather than relying on a set schedule to service a piece of equipment every month or quarter to prevent future failures, the sensor provided condition monitoring that could better dictate the need for maintenance in real-time.
In that sense, Chesterton Connect makes preventative maintenance a responsive process. Furthermore, unlike other IoT solutions that the plant had tried and failed to implement in the past, it was installed for a fraction of the cost of other solutions. Before using the sensor, the plant had tried standalone vibration sensors connected to a newly installed WiFi roof antenna. However, this solution proved costly and the plant saw its spending reach into the six-figure range. Additionally, the soft ware was not user-friendly, and the sensor proved to be unreliable. Maintenance staff found that the physical sensor was frequently knocked off of equipment by routine machine movement or inadvertent worker contact.
What started as a finite issue – installing a Chesterton Connect sensor to monitor a single pump – has resulted in over 50 Chesterton Connect devices being deployed within the facility. Furthermore, the global mining company has also deployed the solution within its other plants. The ease of deployment has been a significant reason why the install base has expanded so quickly. Plant staff can now quickly move between various equipment when new use cases arrive.
In addition, as the use of the sensors scaled throughout the facility, the plant service team worked with Chesterton to install an even more user-friendly IoT gateway, so that service workers no longer need to walk to all 50 sensors. Chesterton Connect devices still use Bluetooth connectivity, but the sensors communicate with the gateway to send data to the cloud. Now, maintenance workers can utilise the gateway to enable remote monitoring from nearly any device and at any location, via a cloud dashboard.
Both plant service managers and Chesterton executives now monitor equipment throughout the plant, analysing vibrations, surface temperatures, process temperatures, and process pressure. As such, teamwork between the global mining company’s plants and Chesterton continues to produce further savings, since condition monitoring ensures that maintenance tasks are performed when warranted, rather than with a rote or time-based plan.
For example, before establishing Chesterton Connect within another one of the company’s plants, maintenance workers were having an issue determining the pressure within a particular stuff ing box. Although there are a handful of calculations one can use to determine the stuff ing box pressure, the results are never the exact amount – rather a ballpark estimate. Aft er collaborating with the plant and the outside engineering team that built the facility, the teams figured if the flush water pump could correctly pressurise the seal to prevent product backup, they could gain more visibility into the stuff ing box's pressure by installing the sensor within the pump itself.
The process was straightforward, with an adapter set-up behind the seal and a port and sensor attached inside the device. Aft er even just one 20-minute cycle with Chesterton Connect collecting data in the background, the plant can now obtain a more accurate pressure percentage inside the stuff ing box.
With 50+ IoT sensors installed within its plants, the global mining company expects to increase the use of Chesterton Connect across its mining operations. IoT applications have common themes across industries, regardless of the segment. Predictive analysis, improved eff iciency, increased safety, and optimised productivity strategies can be used separately or in tandem, in order to drive deployment in most commercial or industrial applications.
As such, the Chesterton Connect IoT solution can be utilised across all types of mining and refining processes to detect and monitor any pressure, such: as air, liquid, and gas. The global mining company’s maintenance workers in this case benefitted from having a monitoring solution that continuously analyses air pressure.
Physical asset performance analysis, including condition monitoring and failure prediction, are the keys to improved outcomes. Today’s industry primarily operates on a simple model: if the asset is broken, then fix it; otherwise, check on it periodically. This traditional practice is ineff icient. Alternatively, using IoT to predict failures before they occur, while learning what is needed to prevent a repeat failure, has proven to be a better approach. A single equipment failure can oft en pay for the IoT system many times over.
Conclusion
Improving overall equipment eff ectiveness is also essential to take into consideration. By leveraging the power of cloud computing and IoT, it is possible to deliver exceptional returns. Industry 4.0, powered by IoT, broadly represents many emerging methods in the mining and broader manufacturing industries, all focused on improving productivity and reliability. Productivity use cases can deliver the highest returns on investment. Transitioning mining operations into Industry 4.0 is no easy task – especially in the age of many mining facilities – but simplified and cost-eff ective IoT solutions are finally off ering forward-thinking mining operators a bridge to the future.
The worldwide leader in specialized drilling.


