
8 minute read
Stabilising Seismic Activity
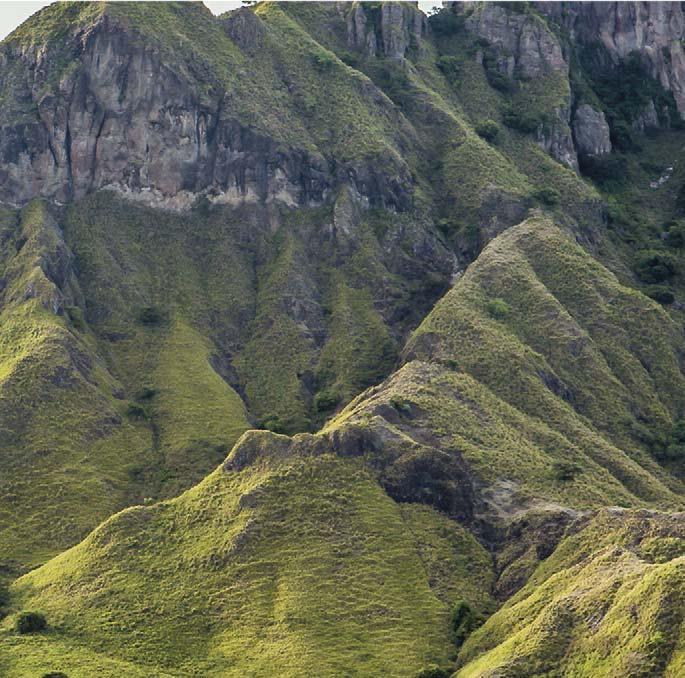
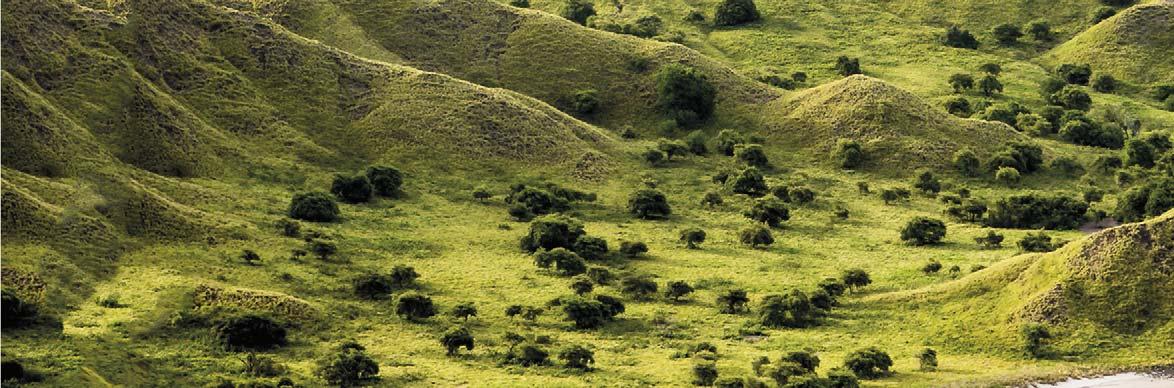
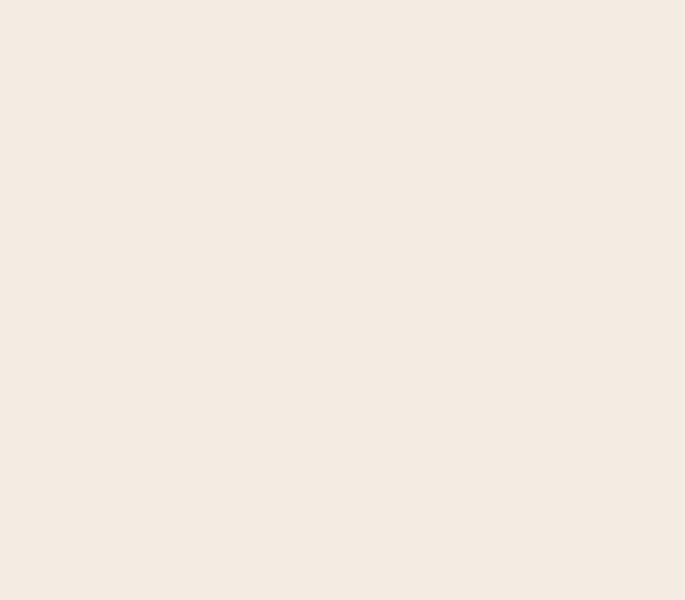
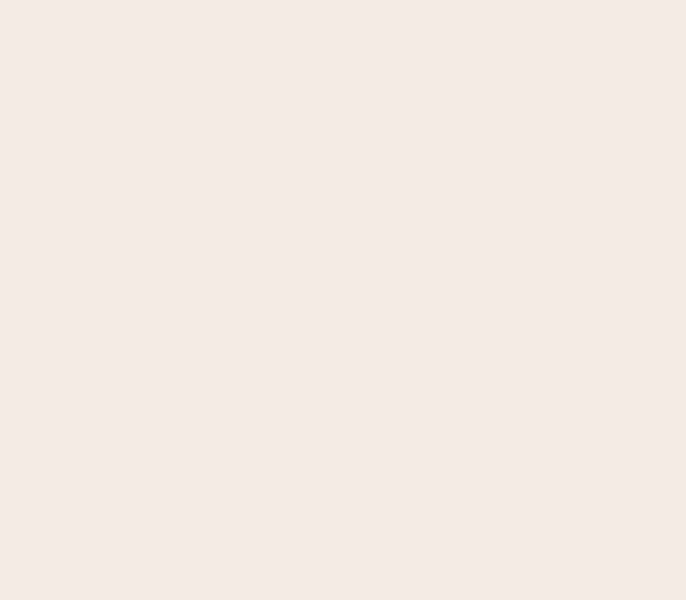
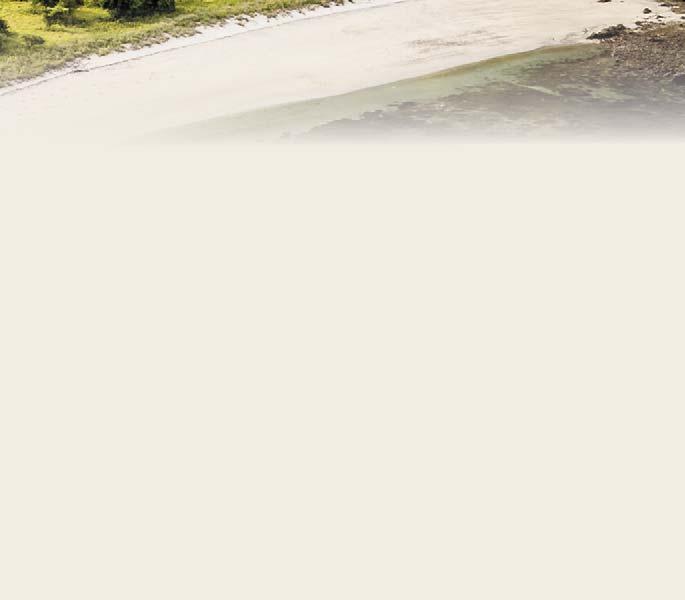

Kevin Slemko, Major Drilling Group International Inc., Canada, outlines the process of supporting the delivery and ramp up of a new hydrofracking programme for Freeport Indonesia at the Deep Mill Level Zone mine.
Located in the highlands of New Guinea and in the Indonesian Province of Papua is Freeport Indonesia’s Deep Mill Level Zone (DMLZ) underground mine. Known as one of the world’s largest copper and gold deposits, DMLZ is found below the Deep Ore Zone (DOZ) mine where 2021 production rates are expected to average approximately 60 000 tpd of ore from several production blocks. In 2022, an increased 80 000 tpd of ore is expected.1
It is here that Major Drilling has partnered with Freeport, using specialised drilling techniques to support hydrofracking and mitigate mine-induced seismic activity in the DMLZ. Major Drilling provides block cave preconditioning services and equipment to help mitigate the mining-induced seismic responses from mining in the DMLZ (Figure 1).
As caving operations have progressed in the DMLZ, mine induced seismic responses have increased, leading to several changes, including the use of hydrofracking to help mitigate issues.
The project
Undercutting began in August 2015 and progressed until the seismic response to the caving process began to increase. Those initial seismic events caused damage to tunnels at the mine, mainly around the extraction and undercut levels. Realising the
rock mass being caved was more massive and competent than originally planned, Freeport teams determined that a hydrofracking programme to precondition the rock mass would be beneficial in mitigating the seismic response, primarily due to a series of seismic events between August 2015 and March 2019.2
In block caving, companies rely on the rock breaking along natural fractures once a certain span is achieved. When this natural breaking did not happen as expected in the DMLZ, Freeport began seeing higher stresses in the supporting rock until the rock could not take it anymore, resulting in a sudden release of stress or mine-induced seismicity.3
Freeport teams responded with a rapid redesign of the DMLZ mining process, in order to improve the response to the actual ground conditions being encountered. Several diff erent initiatives were applied, including pre-conditioning the rock mass using hydrofracking. Major Drilling joined the project to help support the drilling and fracking initiative.
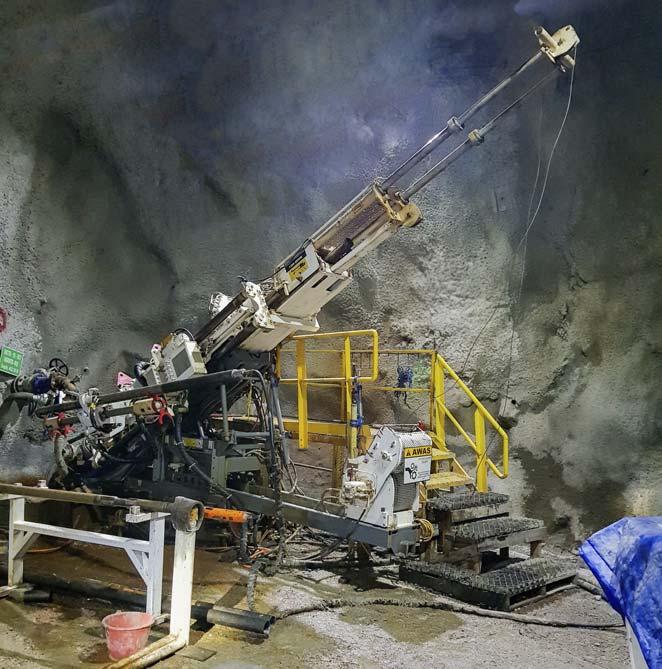
Figure 1. Major Drilling’s LM drill is used in underground hydrofracking and block cave work.
Figure 2. Packer system for hydrofracking used in block cave pre-conditioning detail.
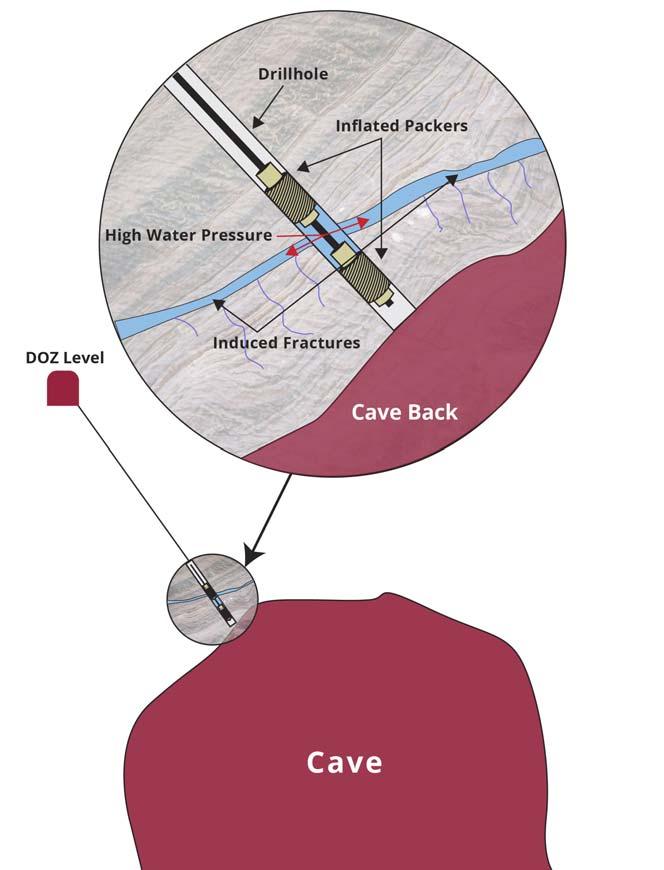
The process/solution
At the DMLZ, teams continue to use a block caving method for extraction, a mining system that involves undercutting an ore body and then allowing it to collapse under its own weight. Block caving is a cost-eff ective method of mining large mineral deposits. The DMLZ’s dominant rock type is diorite, a very strong and generally competent rock mass.
Challenges that come with block caving can include: stalling of progressive caving, draw-point blockage, reliable prediction of orebody caveability, cave propagation, and ore flow management. One solution is hydrofracking to precondition the block cave.
Block caving preconditioning benefits underground projects as it: Increases caveability. Reduces the size of rock fragments during caving. Reduces the risk of mine-induced seismic events.
Working together with Major Drilling teams, Freeport Indonesia has been able to eff ectively reduce mine-induced seismic damage at the mine, with the help of sophisticated monitoring equipment, pumps, and packer systems.
Equipment and expertise
The Major Drilling team at the DMLZ is responsible for operating and maintaining the equipment associated with the specialised drilling process, along with communicating to Freeport engineers the progression of fracs, as per Freeport’s instructions. These eff orts result in teams: identifying ideal fracture sizing; finding out how long fractures will take to form; discovering the necessary pressure to form a fracture; and determining water needs to produce a fracture.
Drill holes made by a Major Drilling LM underground drill make way for packer installation (Figure 2). Once the packers reach the designated location, a balloon on either end of each packer inflates air up to 13 000 psi, remotely sealing in the centre of the tool. Then, pumps move high-pressure water, averaging 3000 – 7000 psi, into the drill rods and out of the centre of the tool. Once the water pressure is higher than the natural pressure of the rock, the ore body cracks, and the fracture forms.
The high-pressure water interacts with the geology to break up rock and this hydrofrack reaps the desired results. Major Drilling supports and operates underground diamond drills, coupled with three complete hydrofracking setups, in the mine to drill and frack holes in accordance with project management.
From among the 14 LM underground core drills Major Drilling provides at Freeport Indonesia, seven are
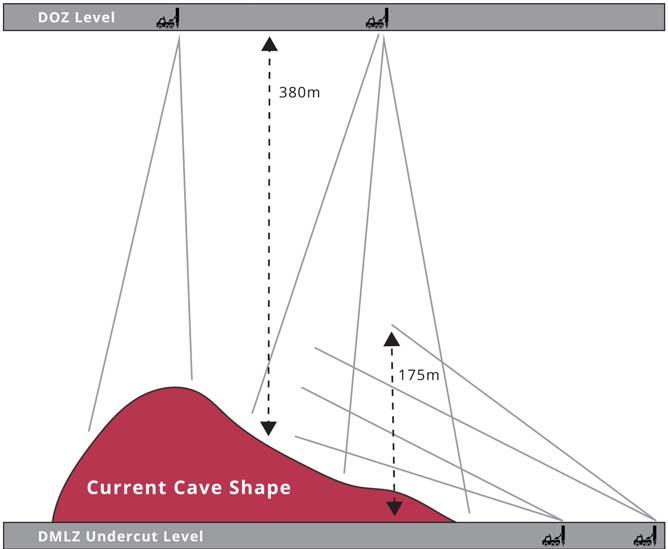
dedicated to supporting the hydrofracking project. Drillers also operate three hydrofracking pump systems. Two pumps were set up at the DOZ level for the sub-vertical holes, and the other was deployed on the DMLZ undercut level in the drilling of sub-horizontal holes from outside the abutment. Freeport Indonesia project managers added a fourth, spare pump in 2020.
Pumps on the DOZ level focus on the area above the existing undercut. This promotes cave propagation. The main goal of preconditioning the rock mass using hydrofracking is to help reduce the seismic response around the edges of the caved area or abutment zone. The hydrofracking holes at the DMLZ are long and very challenging. Two drills are stationed with each pump – an approach designed to increase the hydrofracking eff iciency (Figure 3).
Teams perform fracking procedures in a controlled environment. They clear, barricade, and monitor all pressurising areas. From the secured control room, where all systems are monitored and controlled, teams receive measurements of water pressure and flow, multiple pump pressures, injection pressure, and packer pressure.
Major Drilling teams use the following equipment and methods at the site: Underground core drills. Fracking pumps. Mixing tanks. Blending and gel tanks (when required). Electrical and control room. High pressure treating iron. High pressure purpose-made drill pipe. Holes are surveyed and viewed by an in-the-hole camera. Holes may be cemented and drilled out if required to have a smooth contact for the packers.
Safety is always considered first when embarking on projects, and crews are well trained in safety protocols. Major Drilling enacts safety programmes as part of every operation, including risk assessment of critical tasks as part of a safety management programme.
Figure 3. Hydrofracking drill holes are illustrated between the DOZ and DMLZ mine levels. Source: Freeport Indonesia.
Figure 4. Fracking, production mucking, and underground core blasting from 2015 to 2019 improved production levels aft er the hydrofracking programme commenced in August 2019. Source: Freeport Indonesia.2
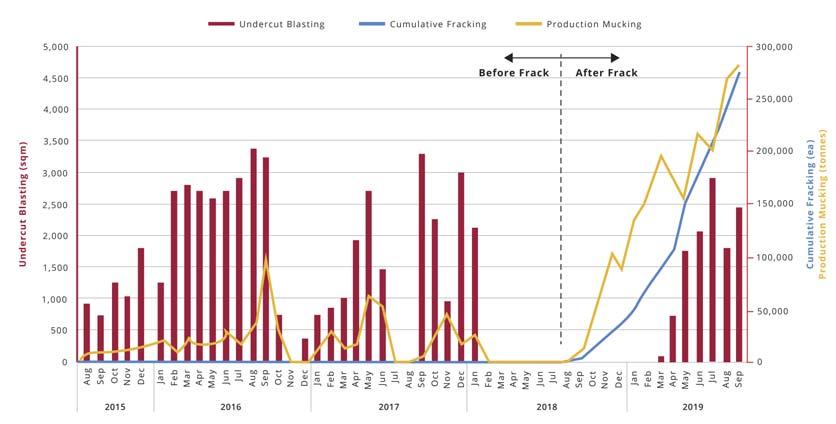
Results
The application of hydrofracking, as well as other initiatives, allowed the DMLZ mine to advance caving and production activities. The DMLZ mine started hydrofracking in September 2018. The project restarted undercutting in March 2019.2
By September 2019, the DMLZ mine had completed over 4500 fracks in 49 holes that supported undercutting and drawbell development, which led to an increase in production (Figure 4).
The application of hydrofracking and other initiatives has resulted in an overall reduction in damage from seismicity.
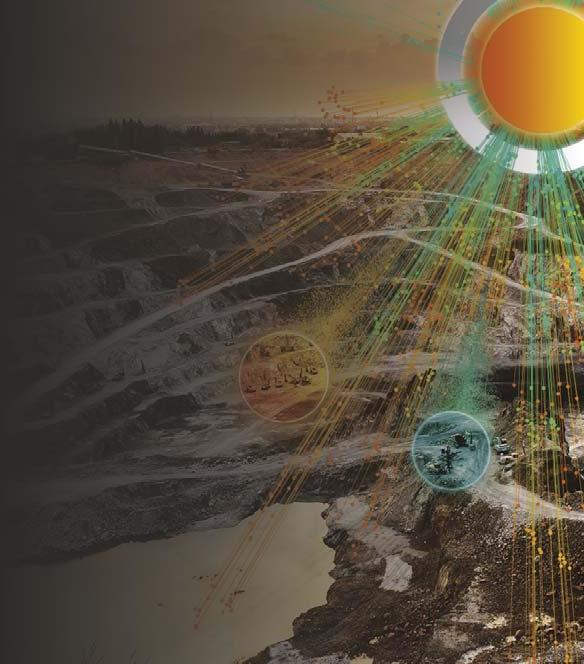
UNLOCKING THE POWER OF YOUR DATA
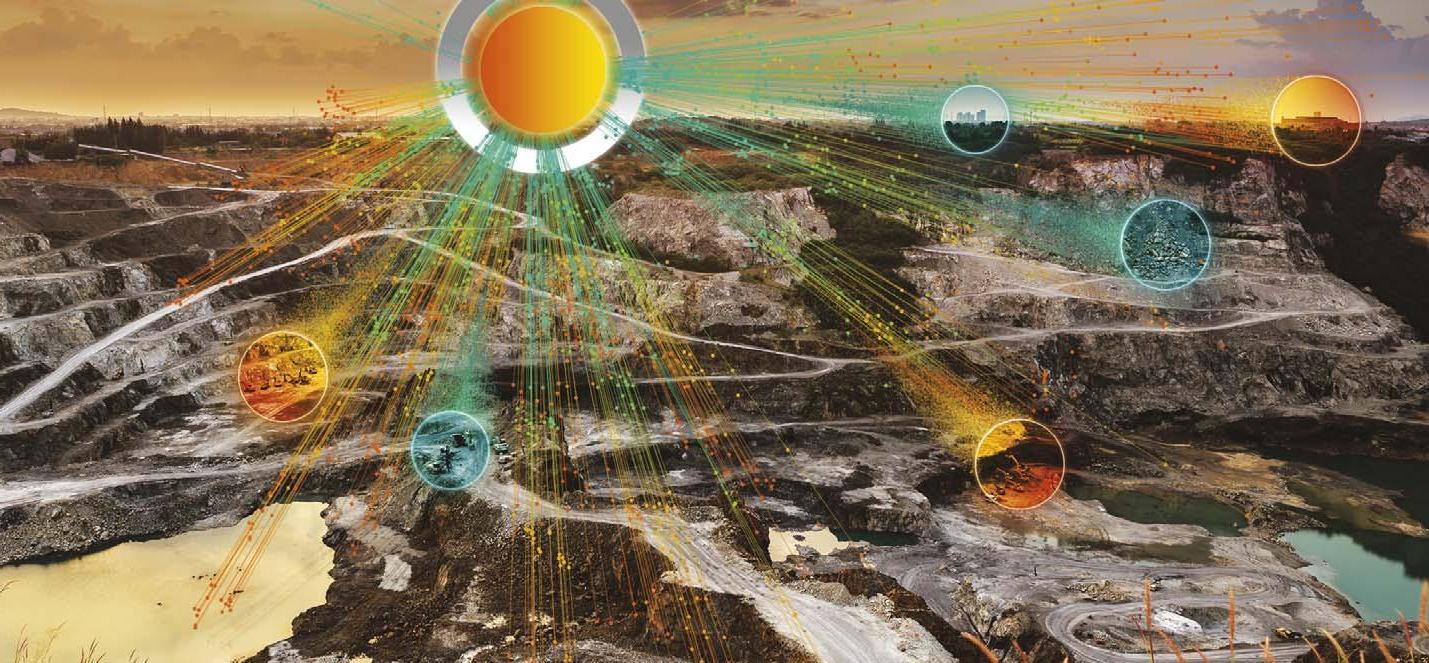
References
1. 'Deep Mill Level Zone (DMLZ) Mine (Grasberg Complex)', Mining Data Online, (2021), miningdataonline.com/ property/3329/Deep-Mill-Level-Zone-(DMLZ)-Mine.aspx 2. NUGRAHA, N., BASTIAWARMAN, R. and EDGAR, I., 'Initial setup of hydraulic fracturing in Deep Mill Level Zone (DMLZ) underground mine, PT Freeport Indonesia, Papua, Indonesia', MASSMIN 2020 Conference and Exhibition on Mass Mining, (2020). 3. 'Hydrofracking Yielding Promising Results at PTFI’s Deep MLZ Mine' E-BeritaKita Monthly Bulletin, (30 November 2018), ebk.ptfi.co.id/highlight-news/ hydrofracking-yielding-promising-results-at-ptfi-s-deepmlz-mine Figure 5. Results of seismic damage events pre and post-hydrofracking at the 4. 'PSM Evaluation – HF and Damage Correlation Report', Freeport Indonesia DMLZ mine.4 Freeport Indonesia Report R4-R5 Damage Occurrence, (19 November 2020). Additionally, the rate of damaging seismic events has been significantly reduced since control measures including 5. 'Defining Reads: Block Cave Pre-conditioning Yielding Promising Results in Indonesia', Major Drilling, https://www.majordrilling.com/promising-results-in-indonesia hydrofracking were implemented at the DMLZ (Figure 5).
The results desired by both Major Drilling and Note Freeport Indonesia were realised and delivered, and the drilling The Major Drilling Indonesia Branch thanks the teams grew their working knowledge of the systems required to Freeport Indonesia Engineering and Operations teams and the safely frack and further strengthen the partnership between the Geotech and Monitoring groups for guidance in ramping up companies.5 drilling equipment and staff for the hydrofracking contractor partnership at DMLZ. Conclusion Special thanks to Freeport Indonesia staff Nico Nugraha, Hydrofracking has proven an eff ective way to mitigate Superintendent of Underground Engineering; mine-induced seismic activity at the DMLZ, resulting in impactful Rifki Bastiawarman, Engineering Manager at DOZ and improvements that have helped stabilise the seismic impacts DMLZ Mine; and Ian Edgar, VP of Engineering, for contributing to through block cave preconditioning. the case study content in this article.
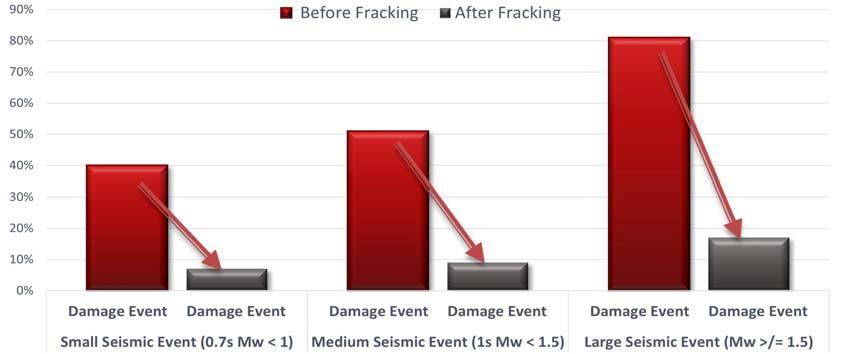