
8 minute read
Fight Fire With Functionality
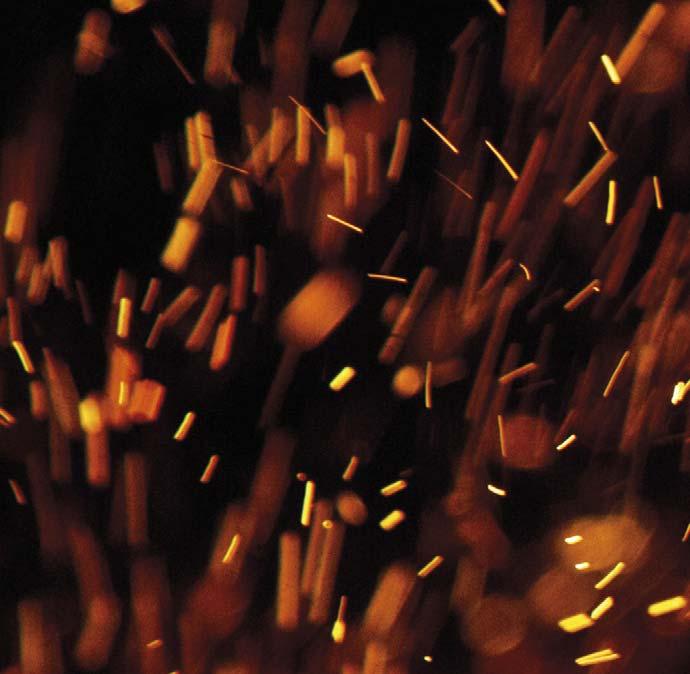
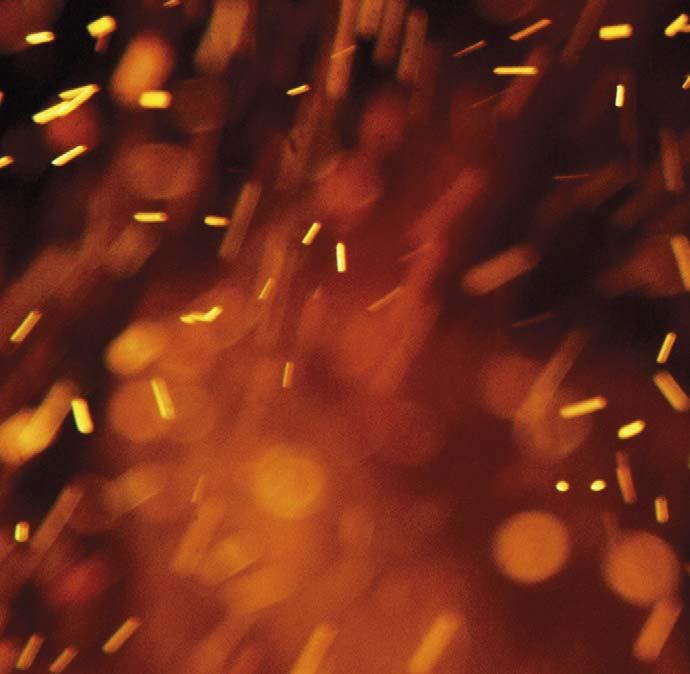
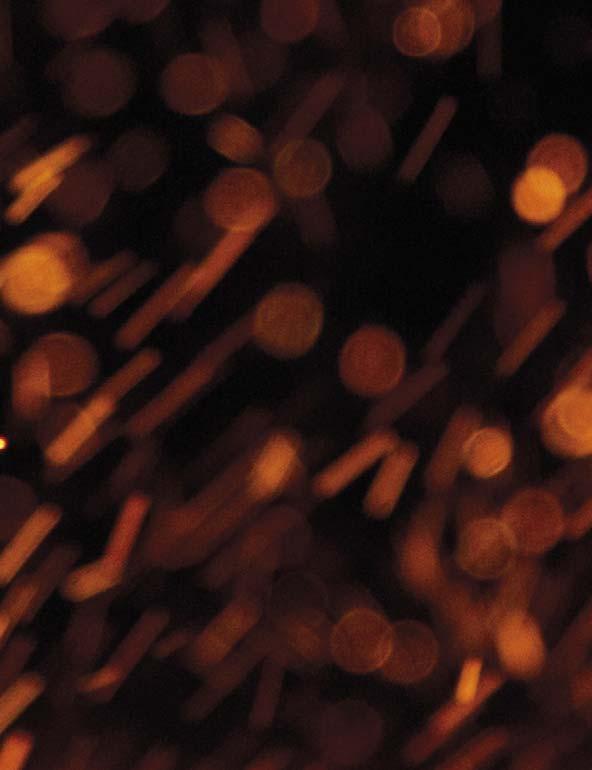
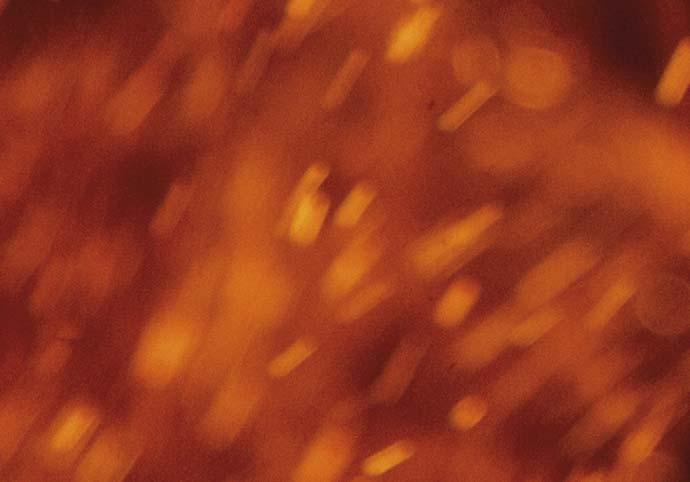





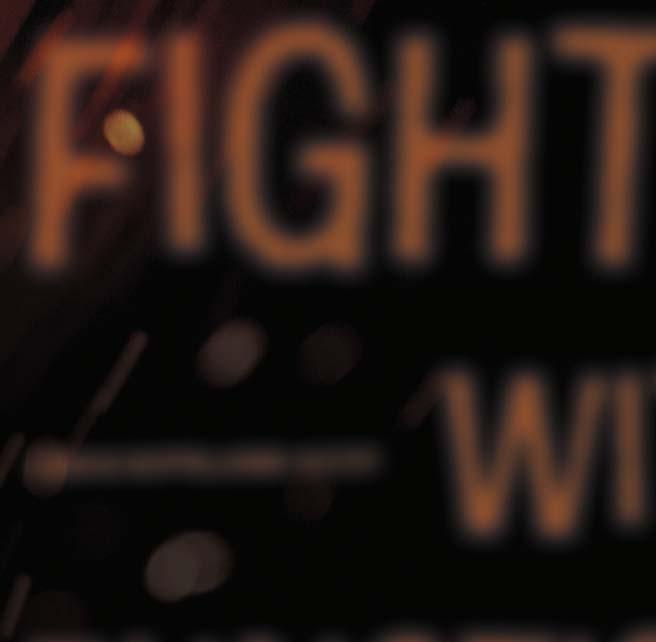

Pierre-Marie Maurice, David Kupiec, and Aimilia Neroutsou, Total, France, review a recent innovation in hydraulic fl uids that is set to provide greater safety to the mining industry without compromising performance.
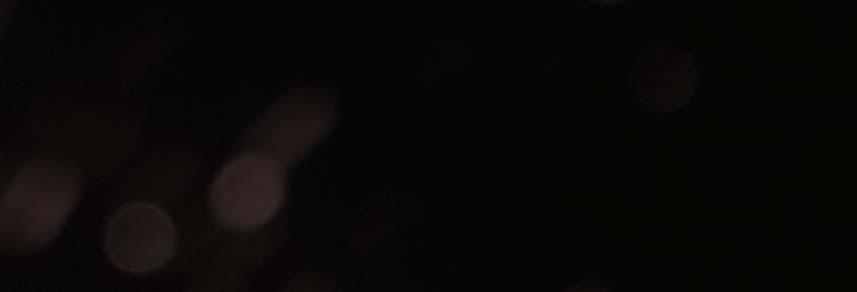
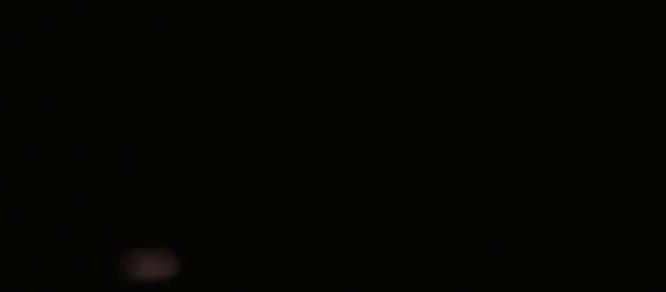
Almost half of all fire incidents in underground mines are caused by hydraulic fluid leakages, making the use of hydraulic mineral lubricants in the underground mining industry a sensitive topic which needs to be addressed, requiring attention and immediate resolution. Underground fires due to hydraulic leakages have been examined by the relevant regulatory bodies, and governments are subsequently seeking to regulate the mining operators to seek a safer resolution.
Up until now, mining operators have faced the difficult challenge of finding a suitable product in the market to fulfill operational requirements. Total is now ready to present its own solution to meet this demand, by offering an innovative technology to Tier 1 mining clients, ensuring a Total core value of keeping safety at the heart of its business, across all sectors, including mining.
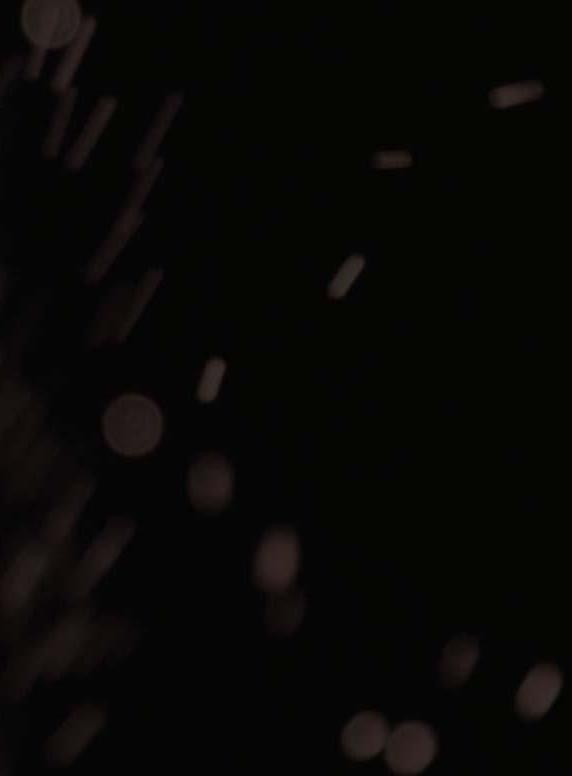
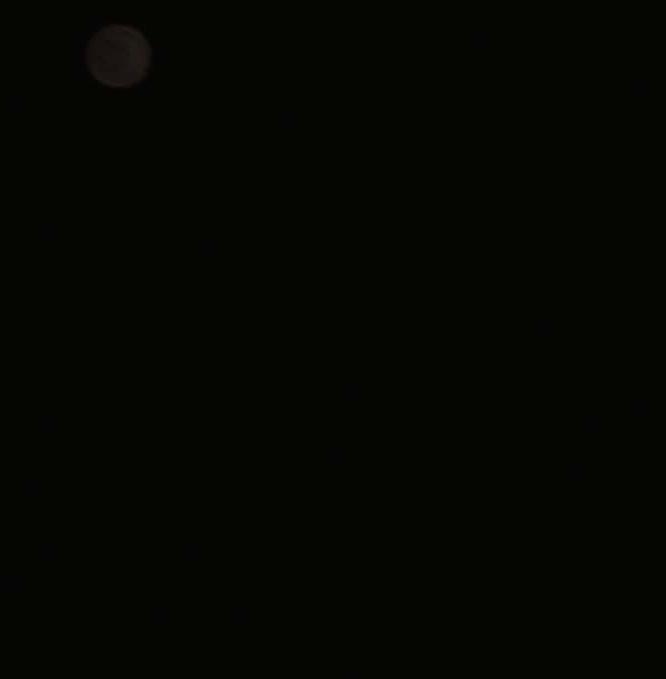
Fire-resistant hydraulic fl uid
Fire-resistant hydraulic fluids have been developed to replace petroleum-based fluids in applications where there is a higher potential ignition source. The types of fire-resistant hydraulic fluids are categorised and defined within the ISO 6743-4:2015 standard. Those with fire-resistant properties within this standard are divided into six categories: HFAE, HFAS, HFB, HFC, HFDR, and HFDU – referring to the types of formulations.
For mobile equipment, HFDU is the only non-water based and is the most common fire-resistant hydraulic fluid used in the mining industry technology (except for HFDR, which is only used in very specific cases), but it has its limitations. This type of fluid is very often based on synthetic esters derived from vegetable oils and has relatively similar mechanical performances compared to mineral oils. However, it is still flammable and the stability of the ester in water can be questionable.

The less flammable technologies are water-based – HFA, HFB, and HFC – but these fluid types typical lack lubricity, and so tend to be found on static equipment with less demanding requirements and derated pumps.
Following the market demands for a water-based technology with superior mechanical performances, comparable to mineral or HFDU fluids, Total has introduced an innovative technology. It combines the fire-resistance performance of water with the equipment protection properties and environmental responsibility that conforms to the highest standards. The HFC-E concept has been launched to make a breakthrough among the existing fire-resistant technologies in the market. Dedicated to delivering the uppermost mechanical performance, and boosted with anti-wear and other relevant additives, the fluid aims to provide optimal equipment assurance and protection.
Figure 1. Hydraulic fluids categories ranking.
Figure 2. Fire resistance characteristics.
Figure 3. Vickers pump test results for Total HYDRANSAFE HFC-E ring and valve weight loss (mg).

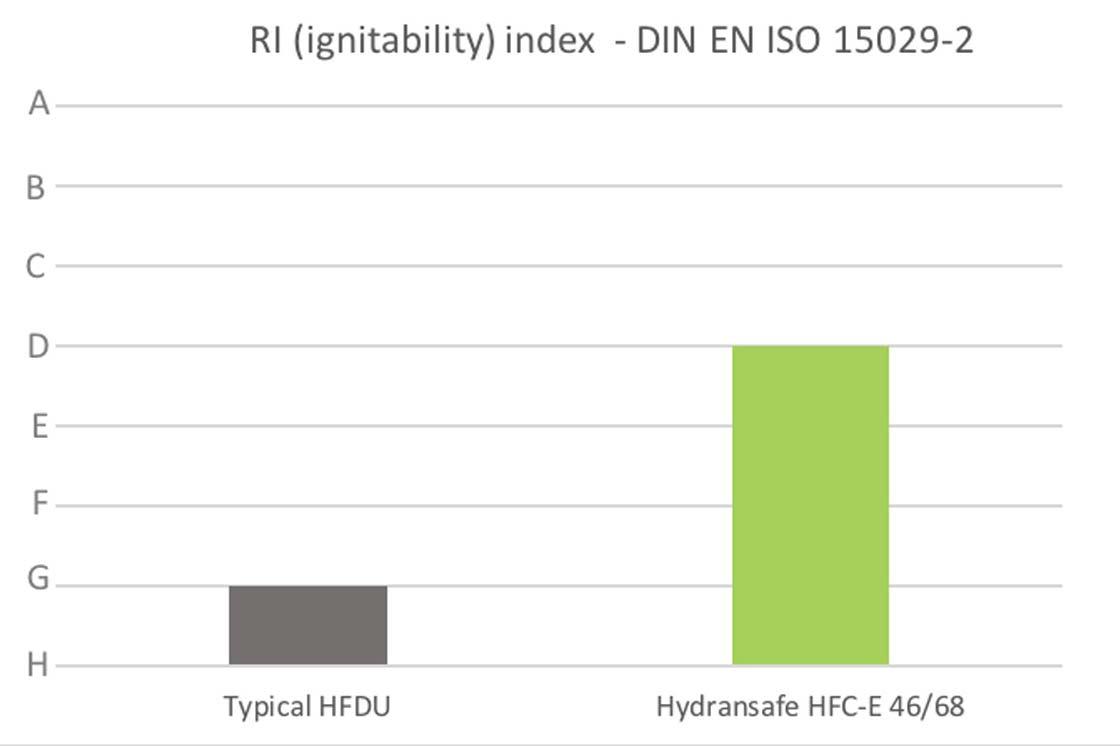
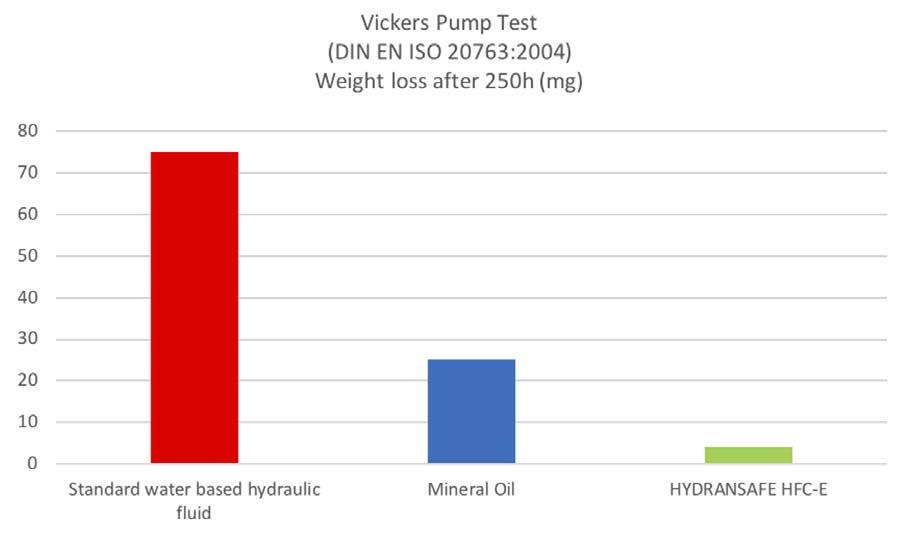
Fire-resistant properties
In general, water-glycols mixtures, water-in-oil emulsions, and synthetic fluids are less hazardous and more fire-resistant hydraulic fluids. Even if fire-resistant fluids have a lower fire hazard than petroleum oil, all have the propensity to ignite under extreme conditions. Although fire-resistant fluids are not fireproof, they significantly reduce the potential fire hazard associated with oil-based fluids.
HFC-E surpasses the fire resistance of prevailing HFDU fluids used in the market. Its RI ignitability index is ‘D’ rated, compared to the ‘G’ classification of HFDU hydraulic oils (according to ISO 15029-2:2018) – ‘A’ represents the most fire-resistant category.
HFC-E fl uid performances
Mobile mining equipment experiences harsher constraints as it is exposed to more severe shocks and vibrations. Hence, higher-ranking mechanical performances are essential for the hydraulic fluid in use in these circumstances.
The current HFC technology has been extensively examined and used as the basis of Total’s new HYDRANSAFE HFC-E, which maintains its fire-resistance characteristics as it is based on a
water-glycol formulation. Nevertheless, its classic water-glycol technology has been enhanced with carefully selected molecules, in order to improve its anti-wear and anti-corrosion performance. This aims to boost equipment’s resistance to the harsh operating conditions that are often associated with work in the mining industry.
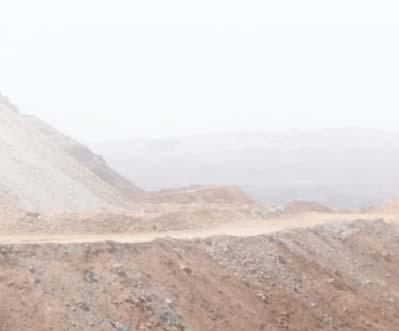
Pump protection

Total has achieved another milestone with the launch of HYDRANSAFE HFC-E, as reflected by a world-renowned original equipment manufacturer (OEM) of pumps issuing a letter of reference, indicating the product’s utilisation in bent axis pumps and motors, without limitations.
In addition to the previously-mentioned attributes, HYDRANSAFE HFC-E provides better cooling to hydraulic circuits than a mineral oil. Indeed, laboratory test results showed an improvement of approximately 12% in the cooling capacity of a hydraulic system using this new fluid type, under specific conditions, compared to a mineral oil. This overall lowering of the system temperature leads to improved equipment reliability and potential energy efficiency.

Field experience

HYDRANSAFE HFC-E has not only demonstrated impressive results in lab scale testing, but also proven its capability in the field, delivering operational performance whilst ensuring fire risk reduction. Thus, RAG, one of the largest mine owners and operators in Germany, has benefitted in reducing operational costs by replacing all HFDU and mineral hydraulic products with HYDRANSAFE HFC-E, attaining an effective total cost of ownership approach.
Similarly, one of Total’s partners in the Asia Pacific region decided to replace the HFDU hydraulic oil which it had utilised for many years with HYDRANSAFE HFC-E. Due to the nature of underground mining, water contamination of hydraulic systems is a common problem resulting in escalation of wear and fluid incompatibility. The application of HYDRANSAFE HFC-E, due to its unique water-based formulation, eliminates the effects of water contamination and associated wear. This is due to the anti-wear and other additive types acting synergistically to deliver optimum equipment protection against wear, corrosion, and other such effects.
Conclusion
Selecting the right fluid is fundamental to increasing equipment reliability, especially in severe mining operations. While the mining sector is a core market for the HFC-E fluids, other sectors that operate in an underground environment, such as tunnelling, also have the potential to benefit from this new development.
RIEGL VZ-i SERIES LASER SCANNERS
FOR MINING
WATCH OUR VIDEO
Mining Apps for Mining Apps for RIEGL VZ-i Series Scanners RIEGL VZ-i Series Scanners
NEW RIEGL MINING APPS FOR REAL TIME ANALYSIS AND PROCESSING
RIEGL VZ-i Series
for highest accuracy and optimal performance: for highest accuracy and optimal performance:
• ranges up to 2500 m, accuracy 5 mm • customized apps written in Python programming language • cloud connectivity for remote operation and data transfer via LAN, Wi-Fi, and 3G/4G LTE
RIEGL Mining Apps
for highest efficiency in the field: for highest efficiency in the field:
• flexible scan data acquisition scheduling • flexible threshold value setting • no extra software required – webserver on scanner for browser-based data and result publication
Monitoring App
data comparison and visualization of differences to the reference data set
Design Compare App
data comparison to a given 3D design model, visualization of undercut and overcut
Slope Angle App
calculation and visualization of local slope angles and the areas above the critical slope angle
Explore the full portfolio of proven RIEGL LiDAR sensors and systems www.riegl.com
newsroom.riegl.international
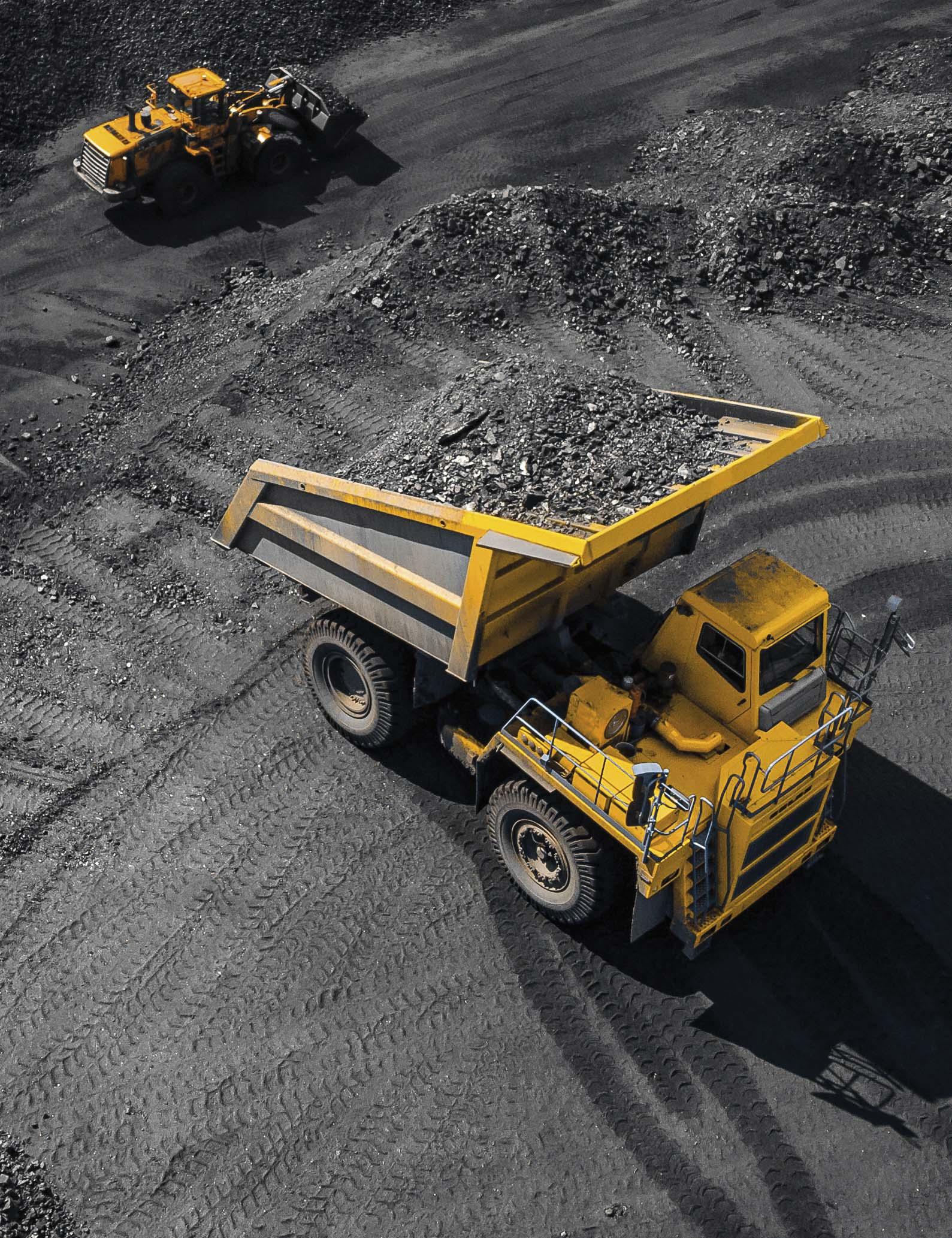

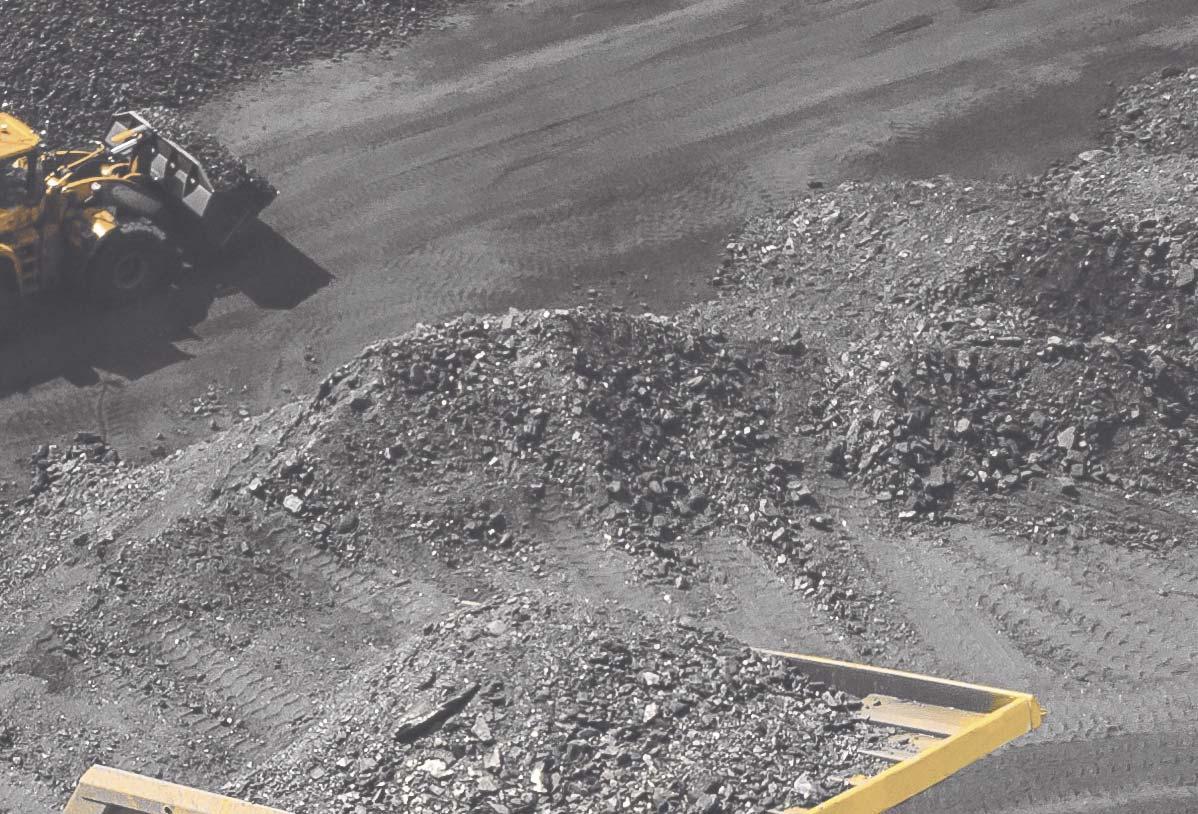
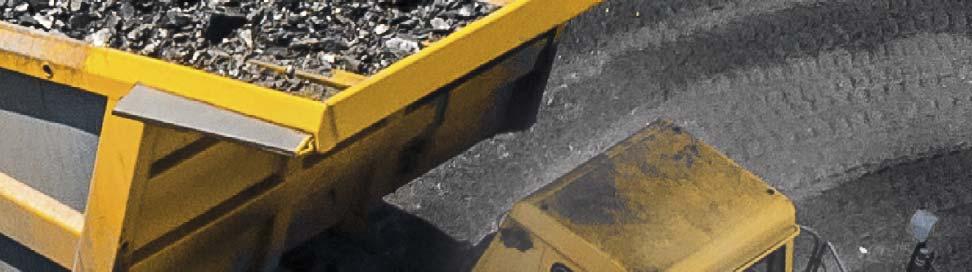

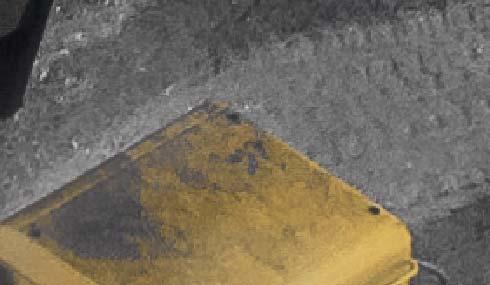
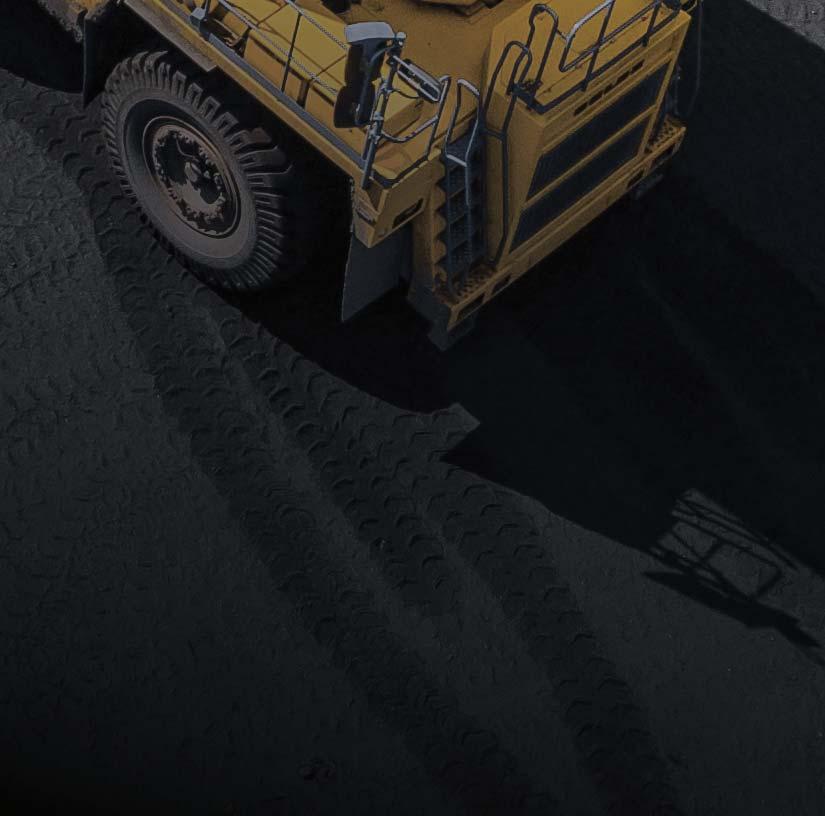
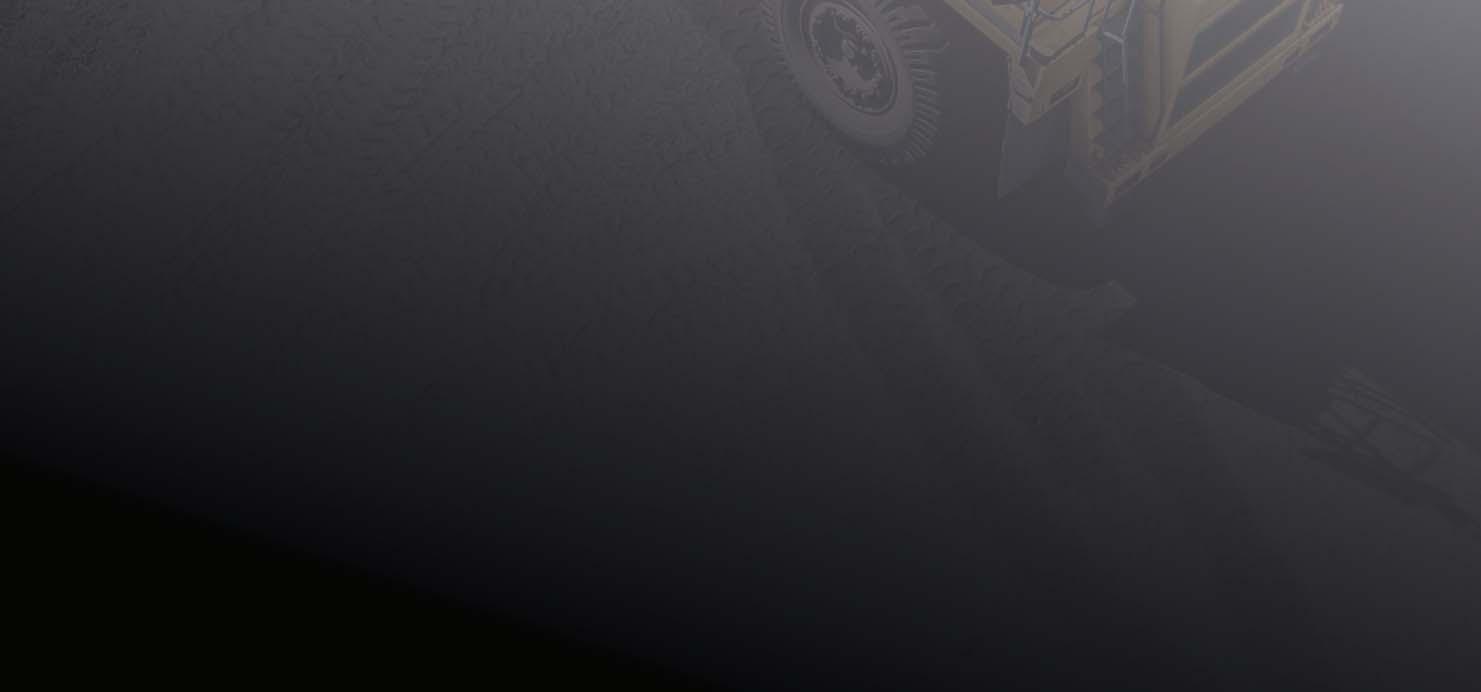
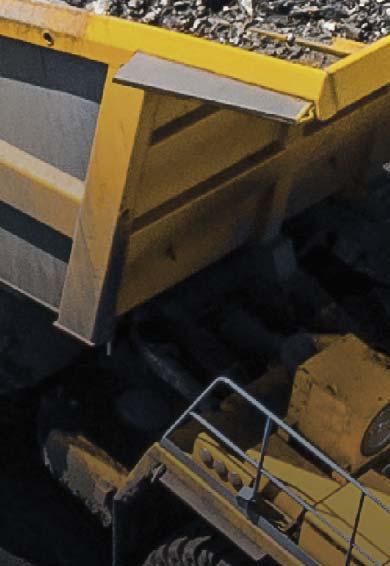

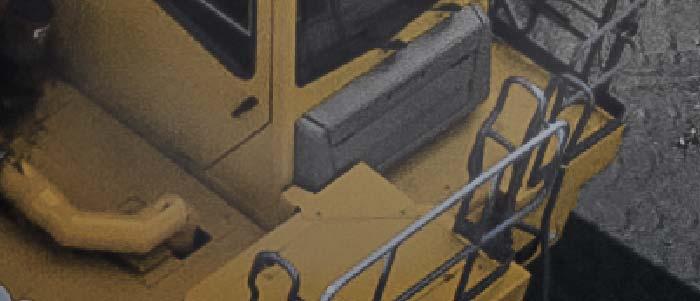




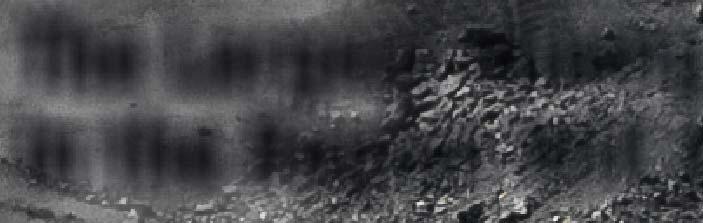
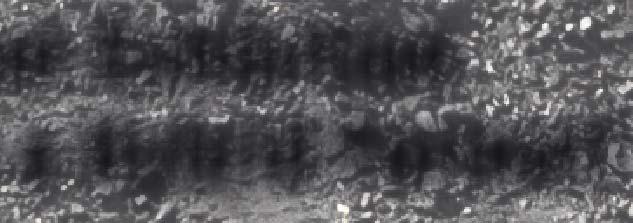


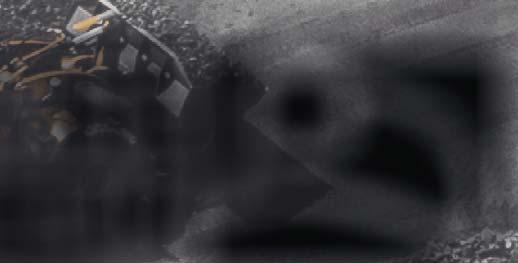