
13 minute read
Fine-Tuning Flotation
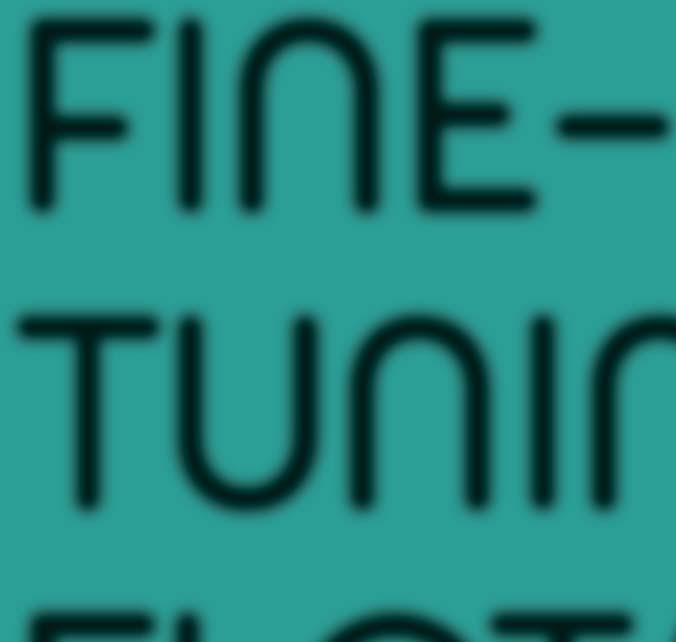
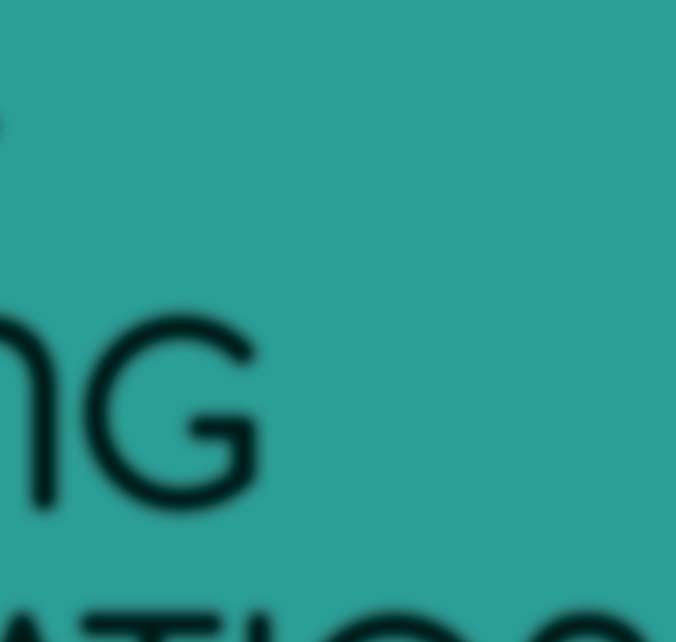

Dr Dariusz Lelinski, FLSmidth, USA, outlines how new approaches to fl otation and froth recovery can cut coarse particle loss and increase effi ciency.
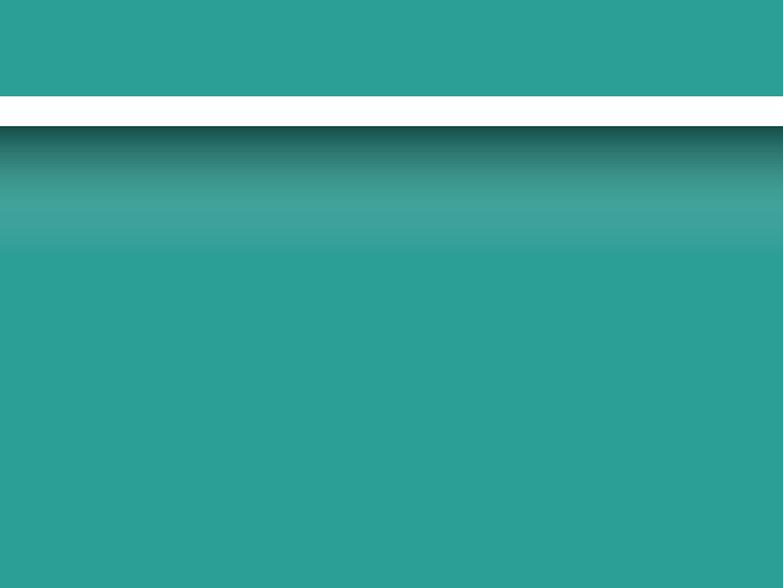
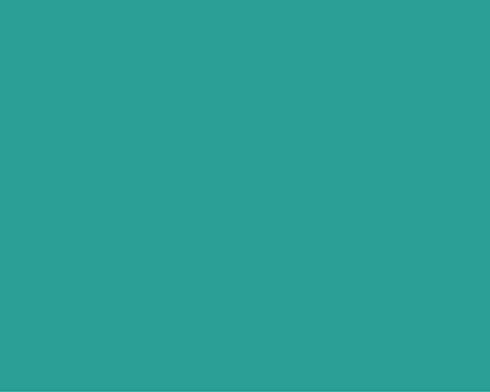
Flotation systems are a vital technology in minerals processing and extraction. But, despite their overall eff ectiveness, particles of valuable ore still get disposed of along with waste material. These can add up, accounting for a significant loss in potential revenue. Additionally, the energy consumption that flotation systems require to function eff ectively is high. So, while flotation systems are necessary when recovering ore, making them more sustainable and energy-eff icient has been a challenge.
One recent approach to optimising flotation has been to divide the flotation process into its two constituent stages: the first part is the formation of the bubble-particle aggregates in the slurry; and the second is the recovery of these aggregates in the froth. Historically, most attention – both from the theoretical and practical point of view – has been given to the first part of this process. However, due to a newly developed instrumentation package, optimising froth recovery rates is now set to deliver real dividends.
It is probably no exaggeration to say that the potential from augmenting froth recovery rates – in terms of what more eff icient control of the level, residence time in froth, and pulling rates could deliver – was only truly recognised a few years ago by the industry.
This is because it was incorrectly assumed that there are no losses during transport from slurry to the launder. It was only a few years ago that it was measured fully, and the results showed that the loses are typically 50% – reaching as high as 90% for coarse particles. What it means is that 50% of particles, averaging across all sizes, must be re-captured aft er becoming detached in the froth phase.
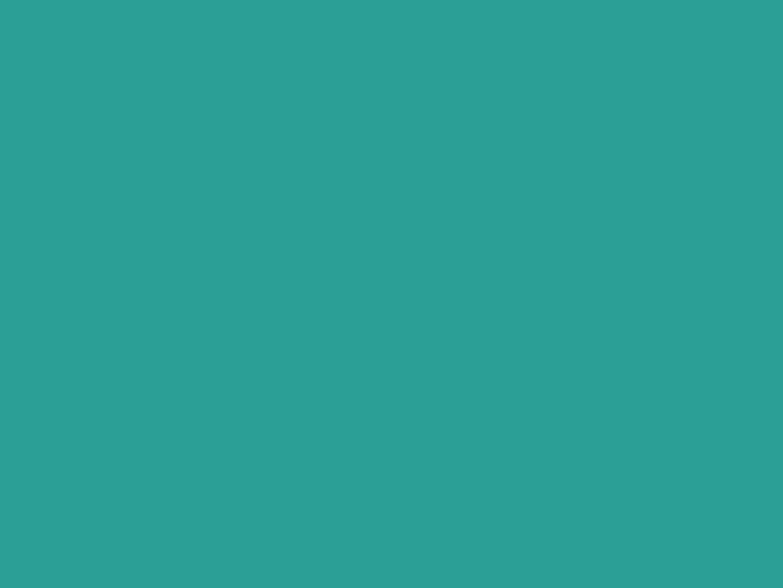
Simplifying a complex solution
What if it were possible to increase the probability of recovery of particles in the froth phase, especially coarse ones? A good idea, but there is no simple way to put it into practice. It would require a combination of instruments and devices, more or less a froth-recovery instrumentation package, flexible enough to achieve this goal in the majority of flotation applications.
A new and practical solution comes from the recognition that the combination of exact slurry level measurement and accurate control of flow using redesigned dart valves and new Festo actuators allows for better control of the froth phase. This in turn results in quicker reactions to flow and slurry density changes, which dramatically improves the performance of flotation machines.
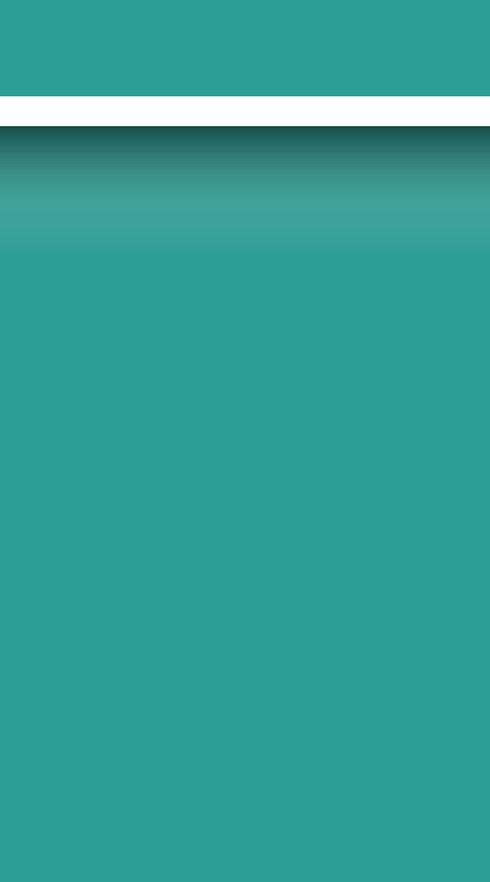
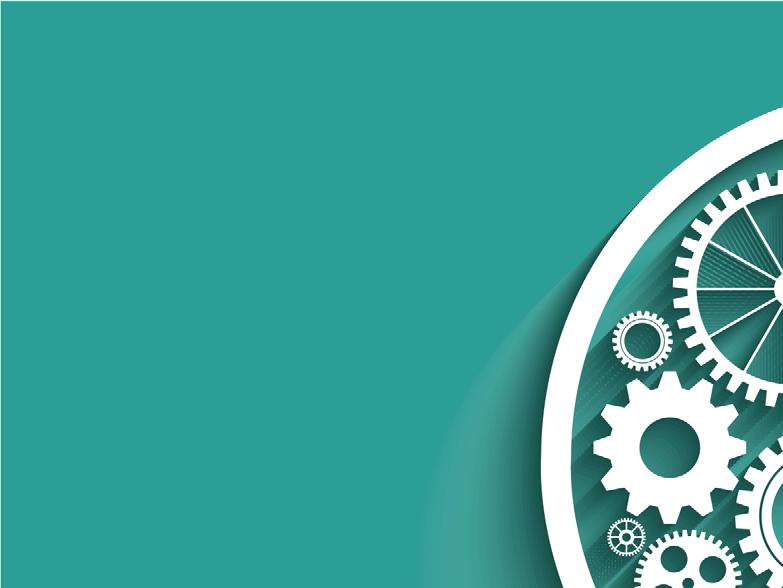
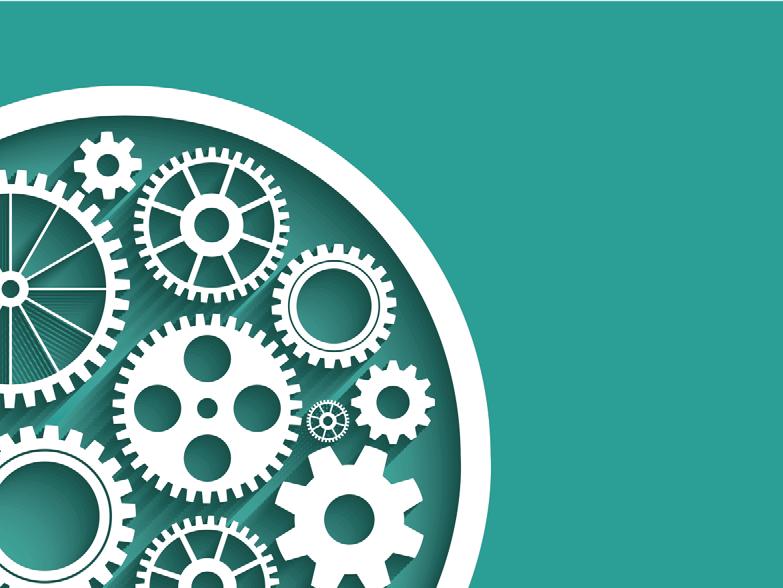
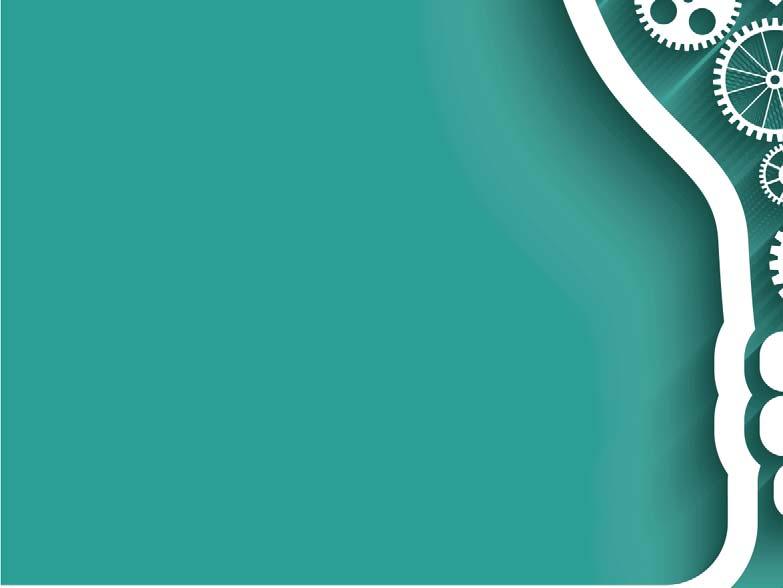
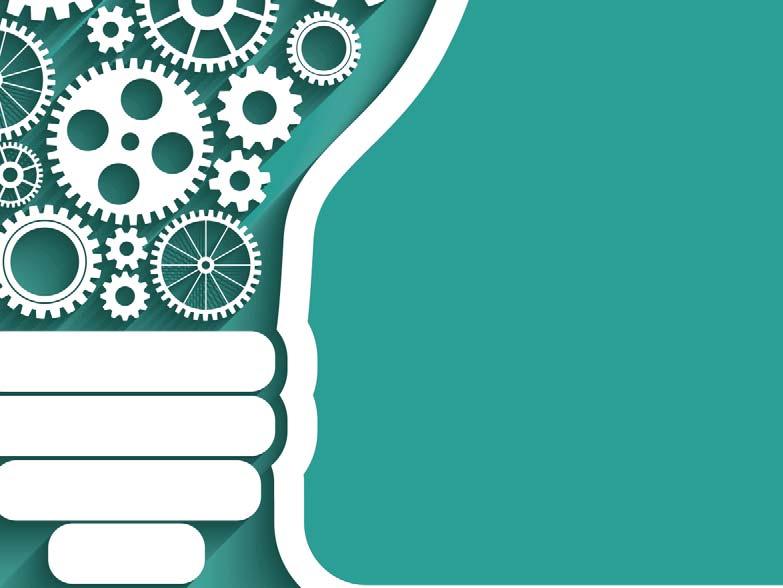
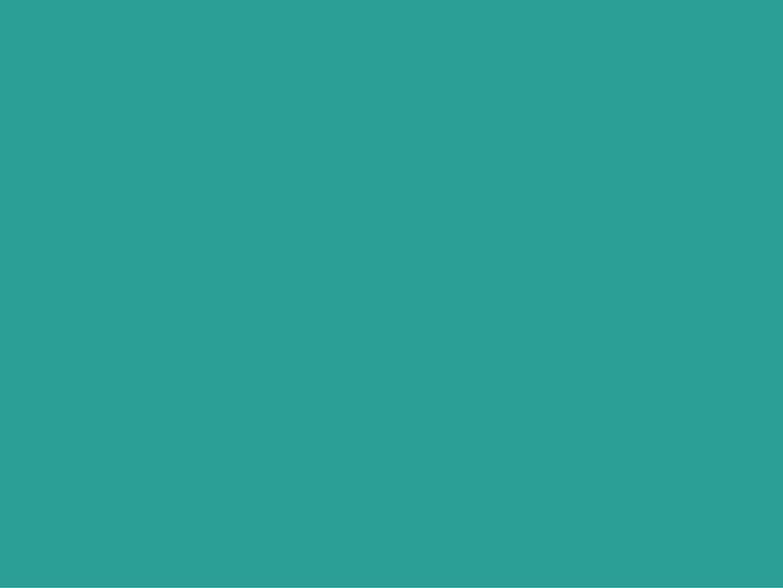
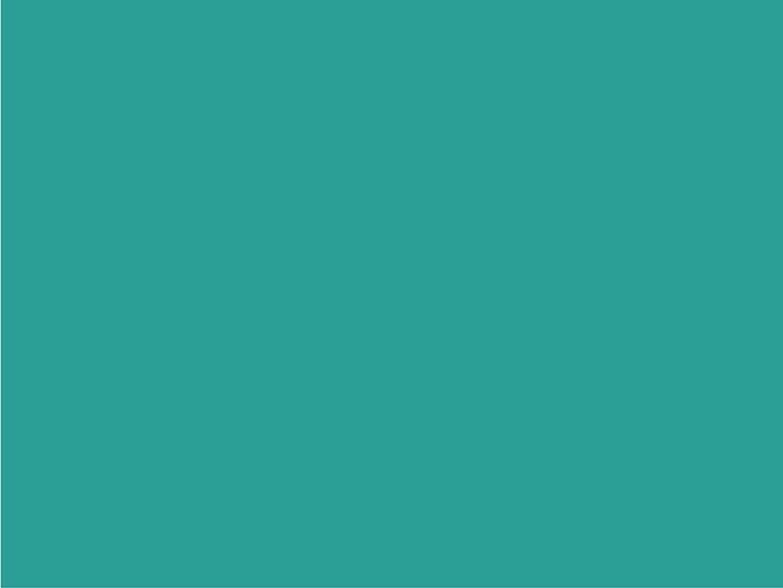
The conventional way to influence froth recovery is a combination of changes to the froth height (improved by new actuators and dart valves), the froth crowding (in the middle of the cell, without the possibility of adjustment aft er installation, and not influencing the most active part of the froth surface), and the number of radial launders.
All these changes are still possible while using a froth recovery package. The most diff icult part is froth recovery at the end of the row, where there is not enough hydrophobic particles to form stable, deep froth, resulting in a large percentage of these particles being left unrecovered. The newly developed solution facilitates not only the recover of these particles, but off ers the control required to balance recovery and grade in this part of the flotation circuit.
Harnessing the combined benefi t of crowders, froth cameras, and actuators
So overall, with the new solution, better results are achieved. Moreover, it also gives another degree of process control, not only during diff iculties of froth formation, but during normal operation. This allows for more flexibility in selecting grade-recovery relationship.
Central to froth recovery packages are adjustable radial froth crowders (ARFCs). ARFCs are mechanical devices that enable an increase of either recovery or grade, regardless of the amount of froth formed at the top of the machine. They allow for much higher pulling rates (recovery) or much deeper froth (grade), which is currently hindered by the top of flotation machine geometry.
In the case of FLSmidth, as well as ARFCs, which the company is capable of producing in-house, advanced froth cameras are provided in cooperation with Stone Three, a market leader in vision equipment. Froth cameras are a flotation instrument of central importance as they allow precise monitoring of the froth phase. By developing these cameras as the second key component of the package, working with a company such as Stone Three, FLSmidth is able to deliver a high quality product to the mining market.
Alongside these elements are improved and redesigned actuators, developed by FLSmidth in cooperation with Festo, and a new and improved level sensor, which monitors both the slurry and froth positions with the MultiSense probe, provided in collaboration with HyControl. The final pieces of the package are redesigned dart valves (typically in a hinged dart valve configuration), which are the result of an in-house, value engineering project.
With all these elements working together in combination with radial froth crowders (RFCs), this package delivers better recovery at the same grade or increased grade at the same recovery, making this package better than the sum of all its parts.
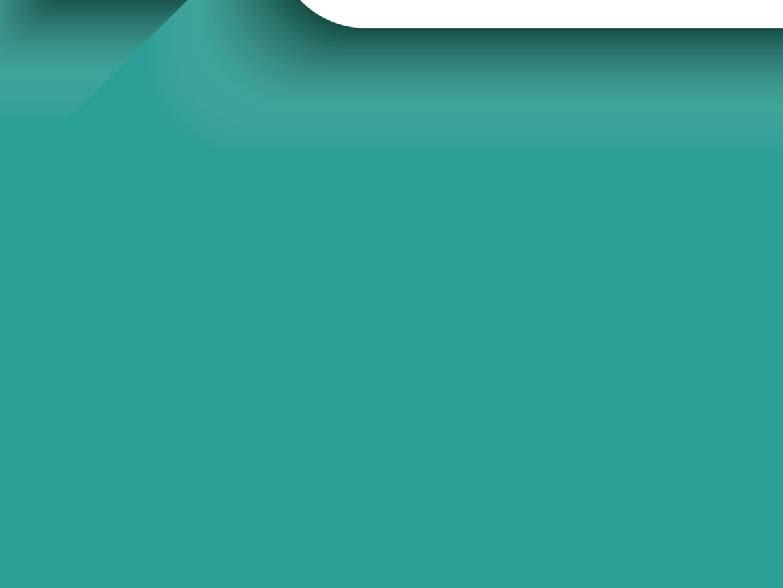
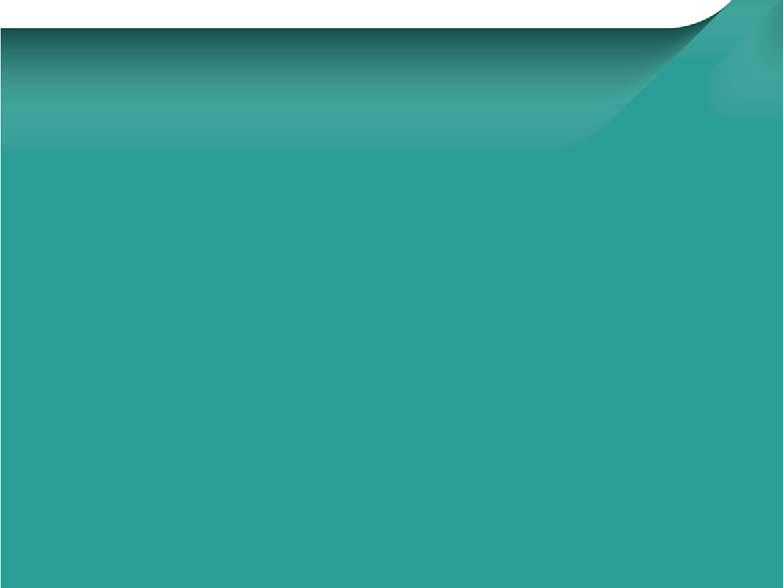
Increased recovery and better grade
The FLSmidth froth recovery package can be retrofitted into existing plants regardless of the type of mechanical cells: forced air or self-aspirated. This means the two major improvements provided by the package – controlled froth depth and the ability to either increase the pulling rate or froth depth with the addition of RFCs – are available to mine operators.
The first improvement can be implemented for both rectangular and cylindrical cells for any type of application, while the second is only for cylindrical cells where the froth pulling rate is low – it does not make sense to install RFCs at the beginning of a row and in high pulling rate applications.
So far, FLSmidth has observed positive results from its new solution. RFCs are a recent addition to its off ering and they have already been installed in two concentrators, while installation in a third has just started. The first two installations have proven that the froth crowders add another process variable in shallow froth situations – they allow for a higher pulling rate, ‘squeezing’ the froth quickly into radial launders, or enabling the building of higher froth depth by reducing the froth area. A high pulling rate increases recovery, while a high froth depth increases concentrate grade.
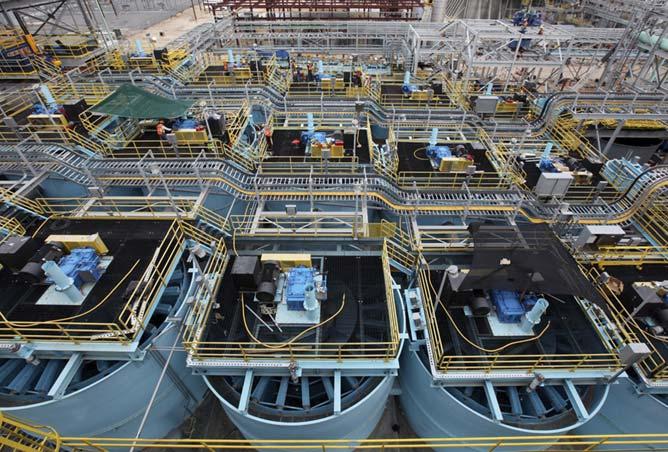
Figure 1. FLSmidth flotation cells at a mine site in South America.
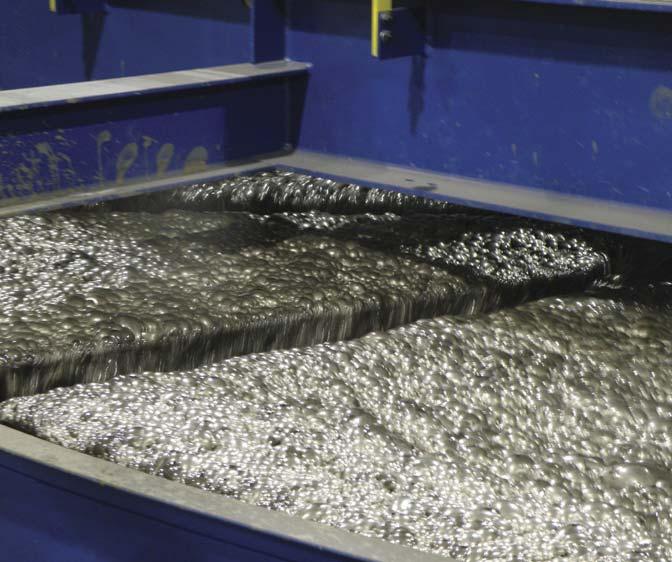
Figure 2. Froth bubbles to the surface as part of the flotation process.
A second separate but signifi cant development
Much in the same manner in which the FLSmidth’s froth recovery upgrade package combines the benefits of diff erent technologies to produce results that are greater than the sum of its parts, mingling two diff erent types of cells – the nextSTEPTM forced air and WEMCO® self-aspirating – also returns dividends in terms of recovery levels. The cell-combination concept came about as the company sought to resolve challenges presented by older flotation systems, as well as ways to boost flotation productivity and reduce environmental footprint. The result was the mixedROWTM Flotation System, launched in late 2020.
The mixedROW Flotation System is the first system of its kind on the market. It works by exploiting the characteristics of two flotation cell technologies at the same time. The nextSTEP machines are placed at the beginning of the row, where it can recover coarse material using the least amount of energy possible. Due to this positioning, the mixedROW lowers energy consumption by between 15 – 40%, and increases recovery by 1 – 3%, depending on the application. This improvement, even if it is not a large number, translates to very large economical gain, in many cases equal to tens of millions of dollars annually.
The WEMCO machines are placed at the end of the row, which increases both coarse and fine particle recovery, as they are capable of treating a wide range of particle sizes. The elevated rotor position built into the machine design also reduces energy consumption, as the froth only has a short distance to travel.
In addition to diff erences in hydrodynamics, absorbed energy and specific energy in the rotor region, both machines have diff erent froth recovery mechanisms: nextSTEP has a very stable froth layer which can be very deep, while WEMCO’s froth is very dynamic (WEMCO wave). These diff erences also influence the type of particles recovered by both types of machines and add to the range of particles recovered by mixedROW. mixedROW also has the lowest head loss on the market, as its carefully engineered system of dart valves allows for eff icient transfer of slurry from one tank to another without significant losses. mixedROW can be configured to suit whatever the customer needs may be. It can be adapted to whatever application it is needed for, making it a highly flexible and eff ective solution.
Although only off icially launched in 2019, there are already quite a number of installations where the mixedROW concept has been successfully applied. The first instillation was at Western Limb in South Africa, where WEMCO was retrofitted into a row of a competitor’s self-aspirated cells. This was followed by the first fully pre-planned and designed nextSTEP-WEMCO mixedROW at Mogalakwena, which, like Western Limb, was also a platinum group minerals (PGM) application. Interest in this solution has continued to grow, and the most recent examples have been: a retrofit at Antapaccay, followed by a mixedROW expansion (copper), and then two mixedROWs added at Toquepala (copper/molybdenum).
Looking to the future of fl otation
In recent years, FLSmidth has participated in targeted collaborations with universities that have process knowledge and capability relevant to flotation. Last year, the company was approached to be the leading industrial partner in an application for an EU funded research project, with the aim of conducting
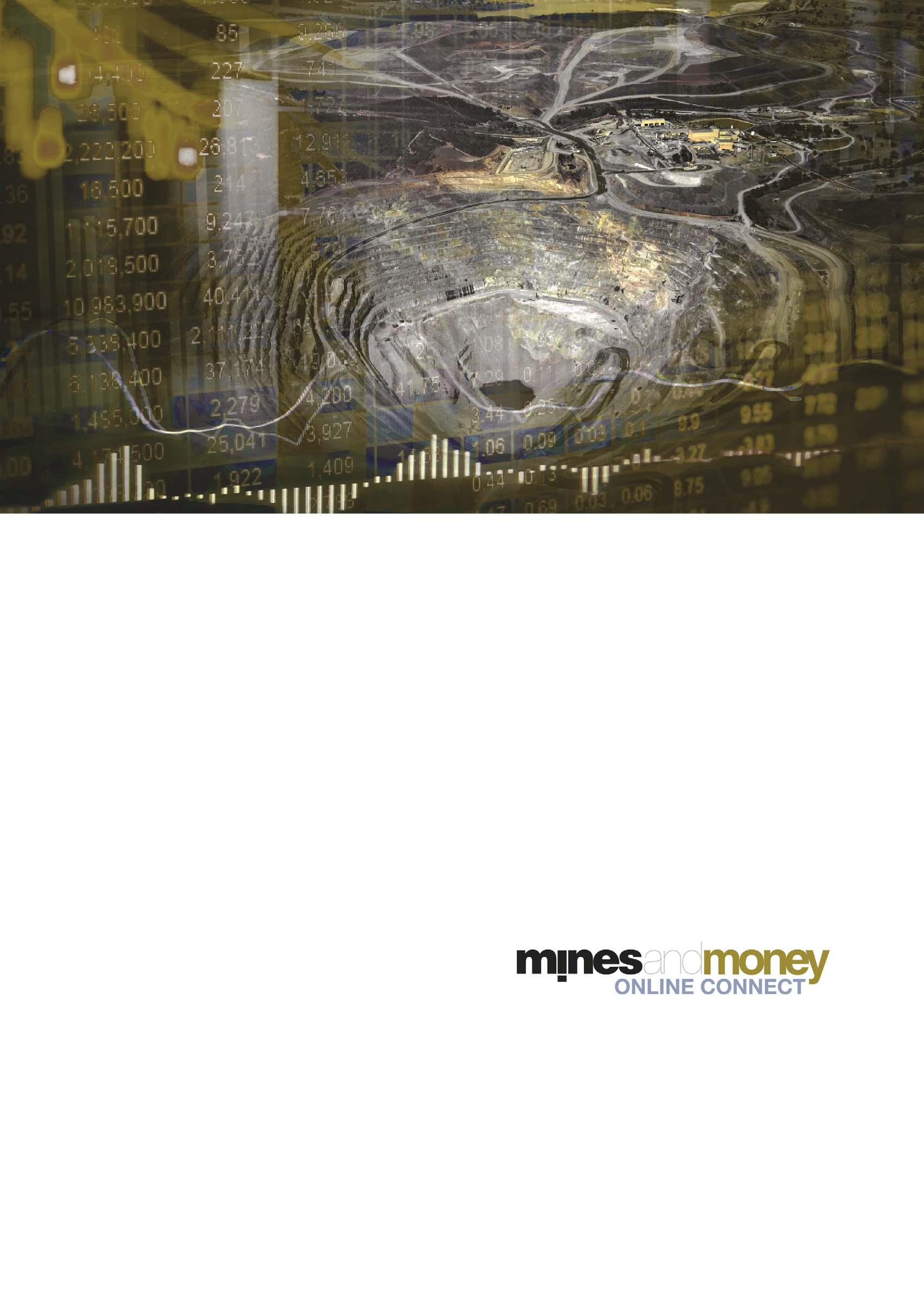
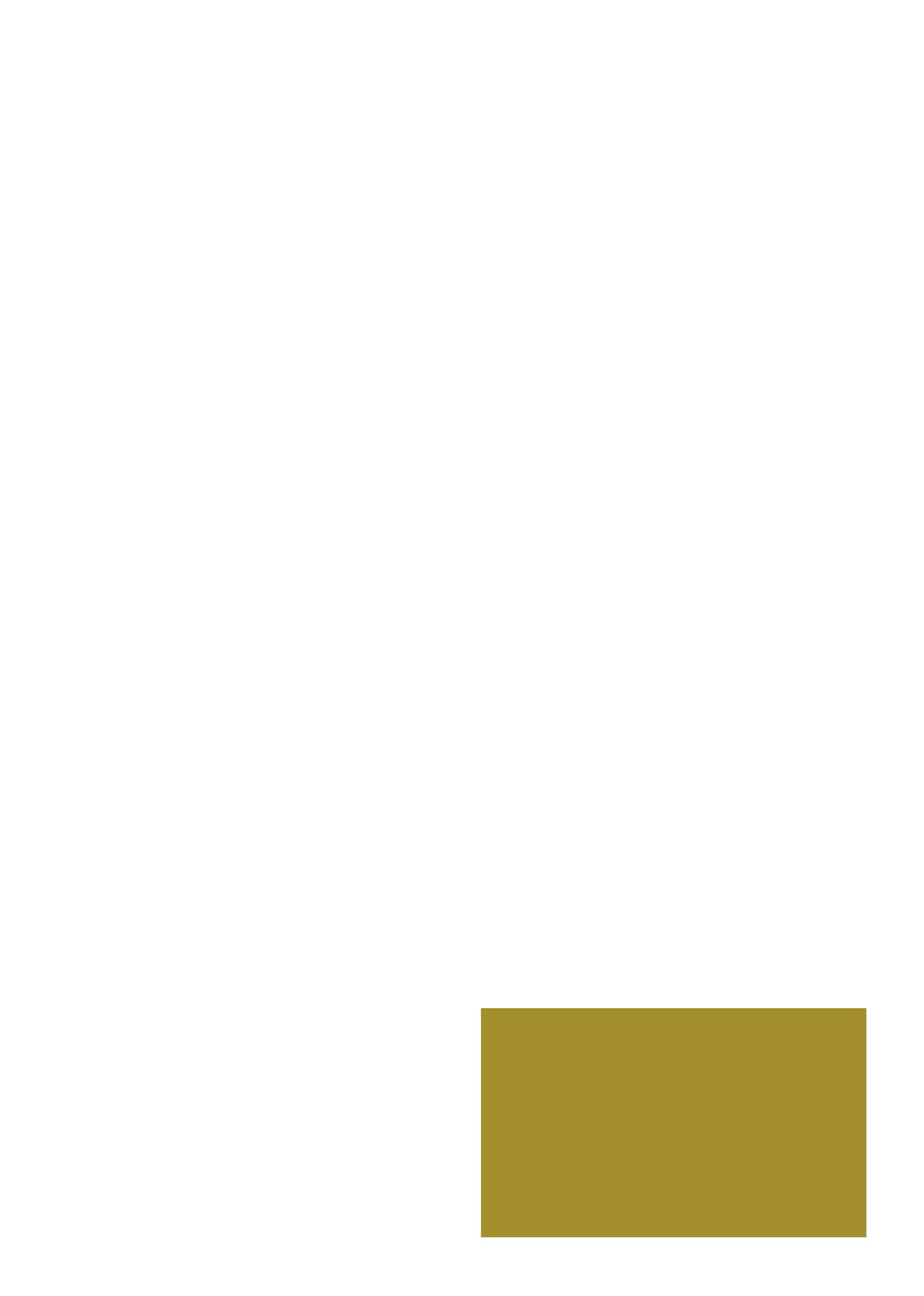
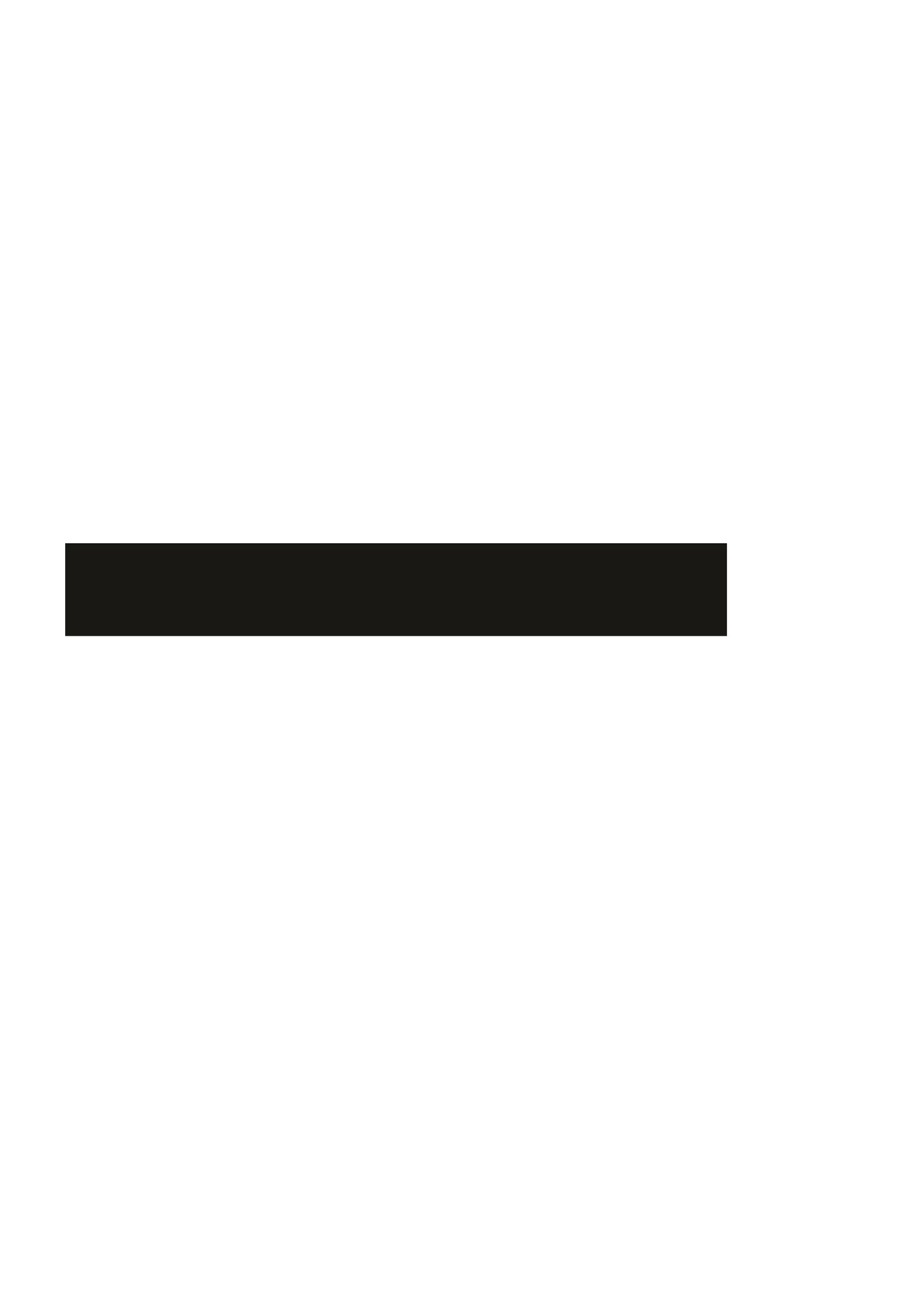
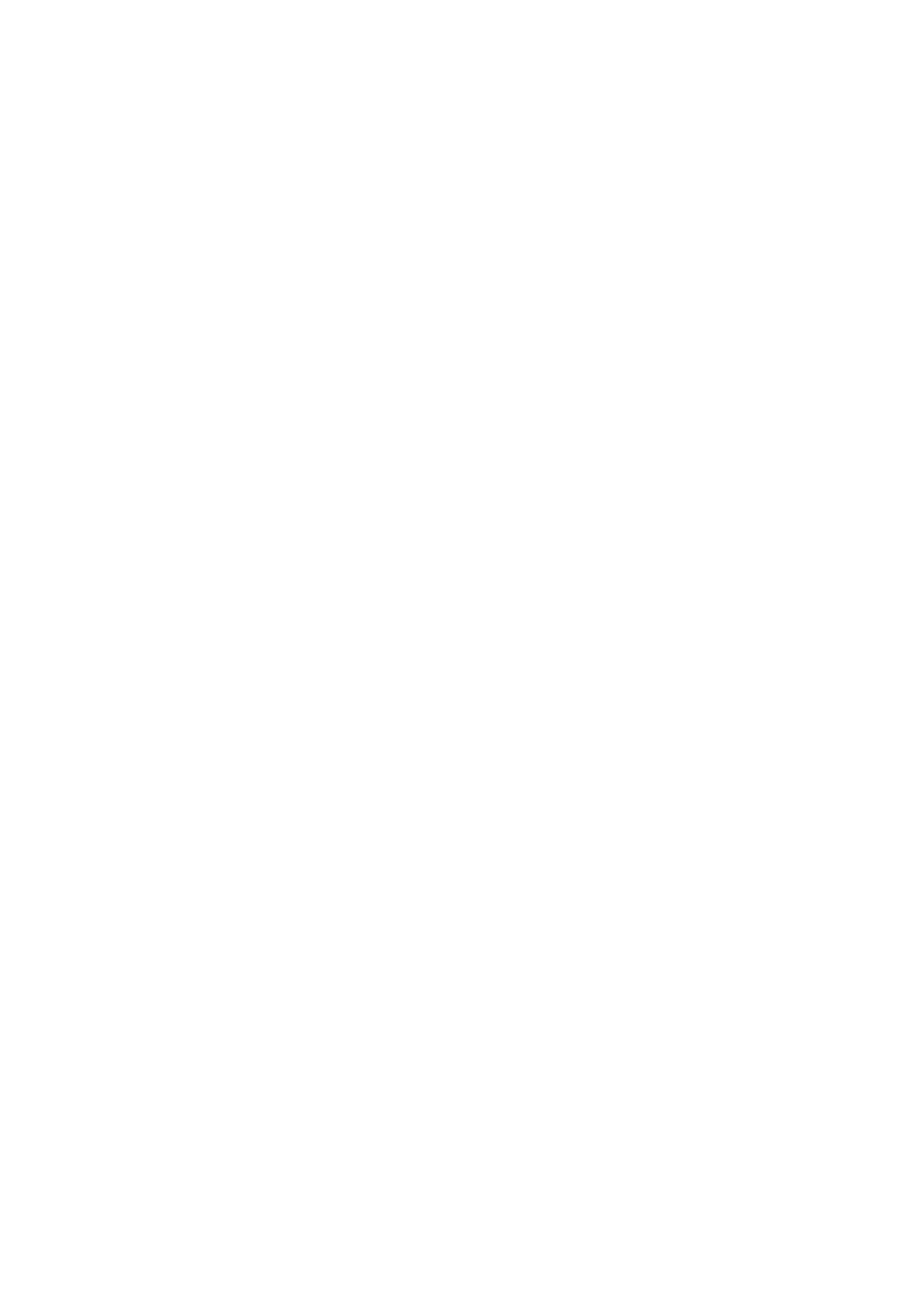

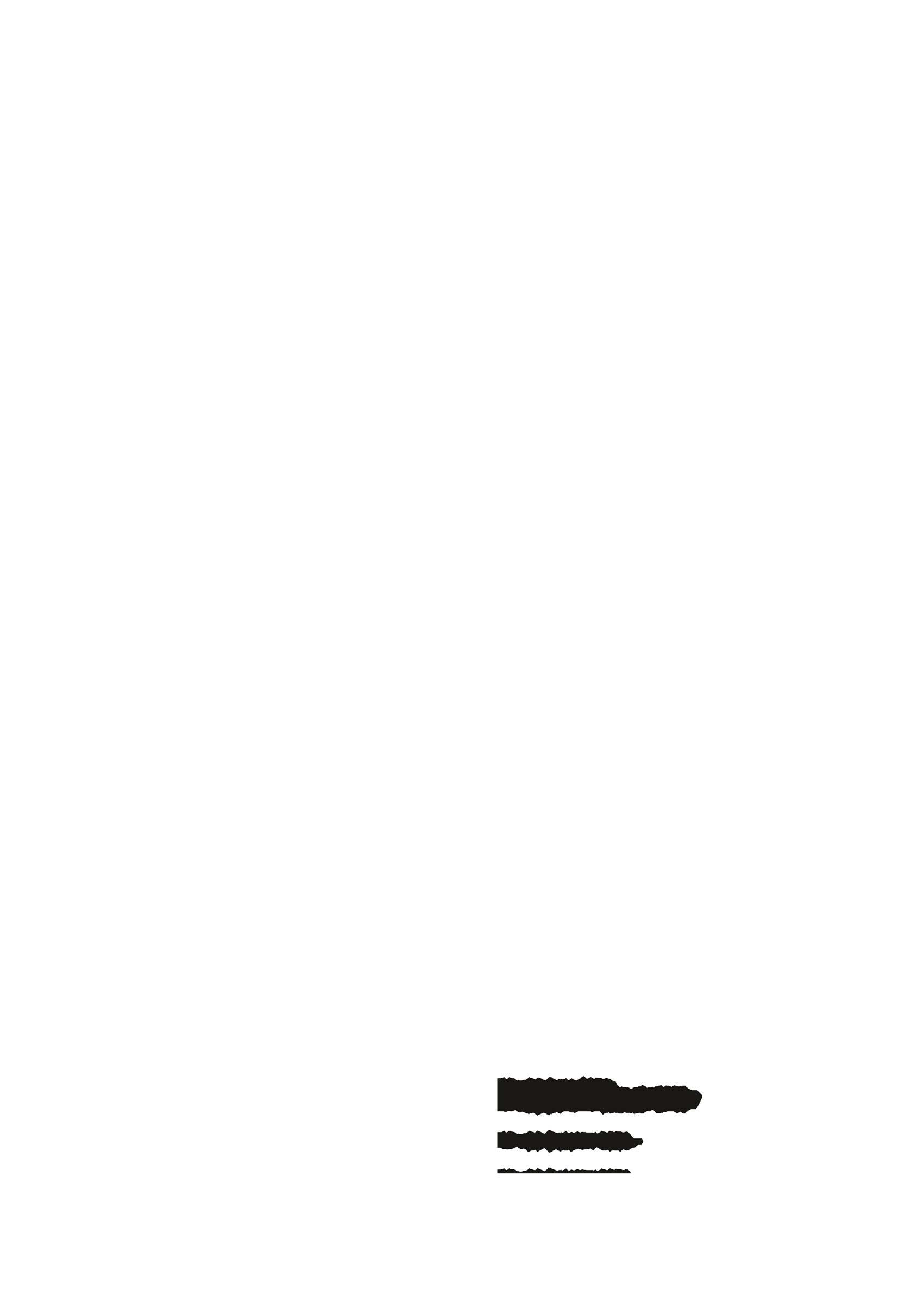
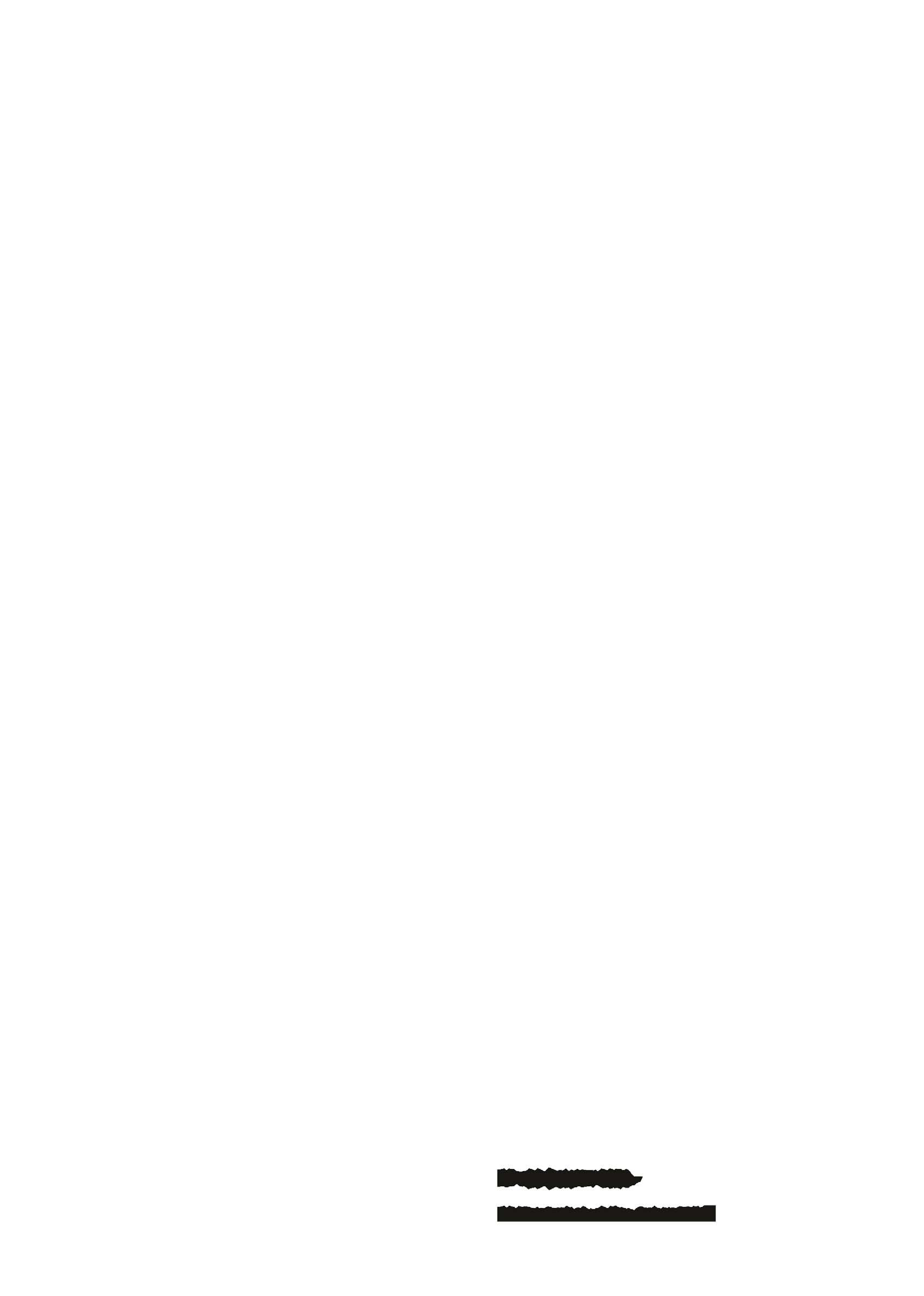
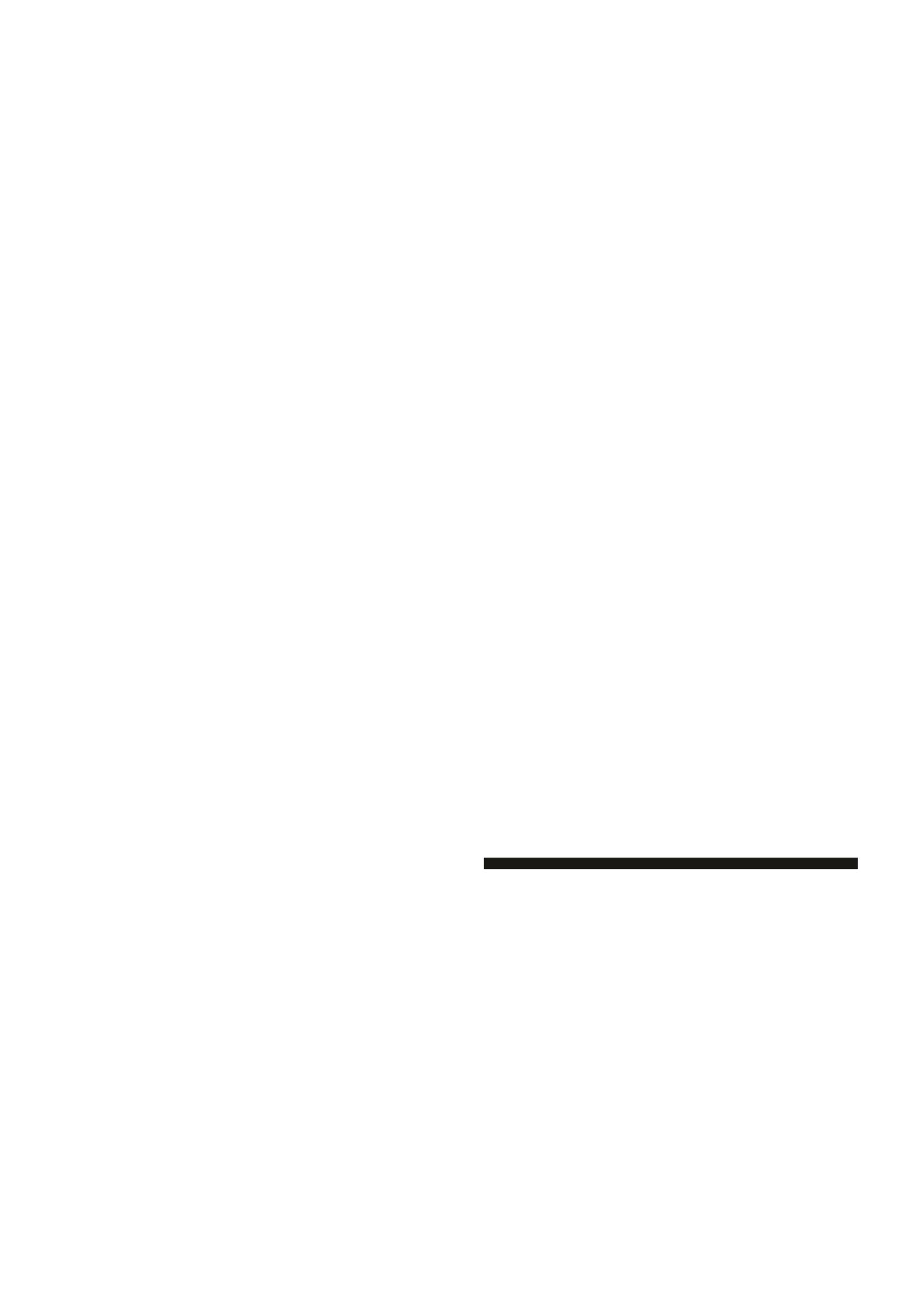
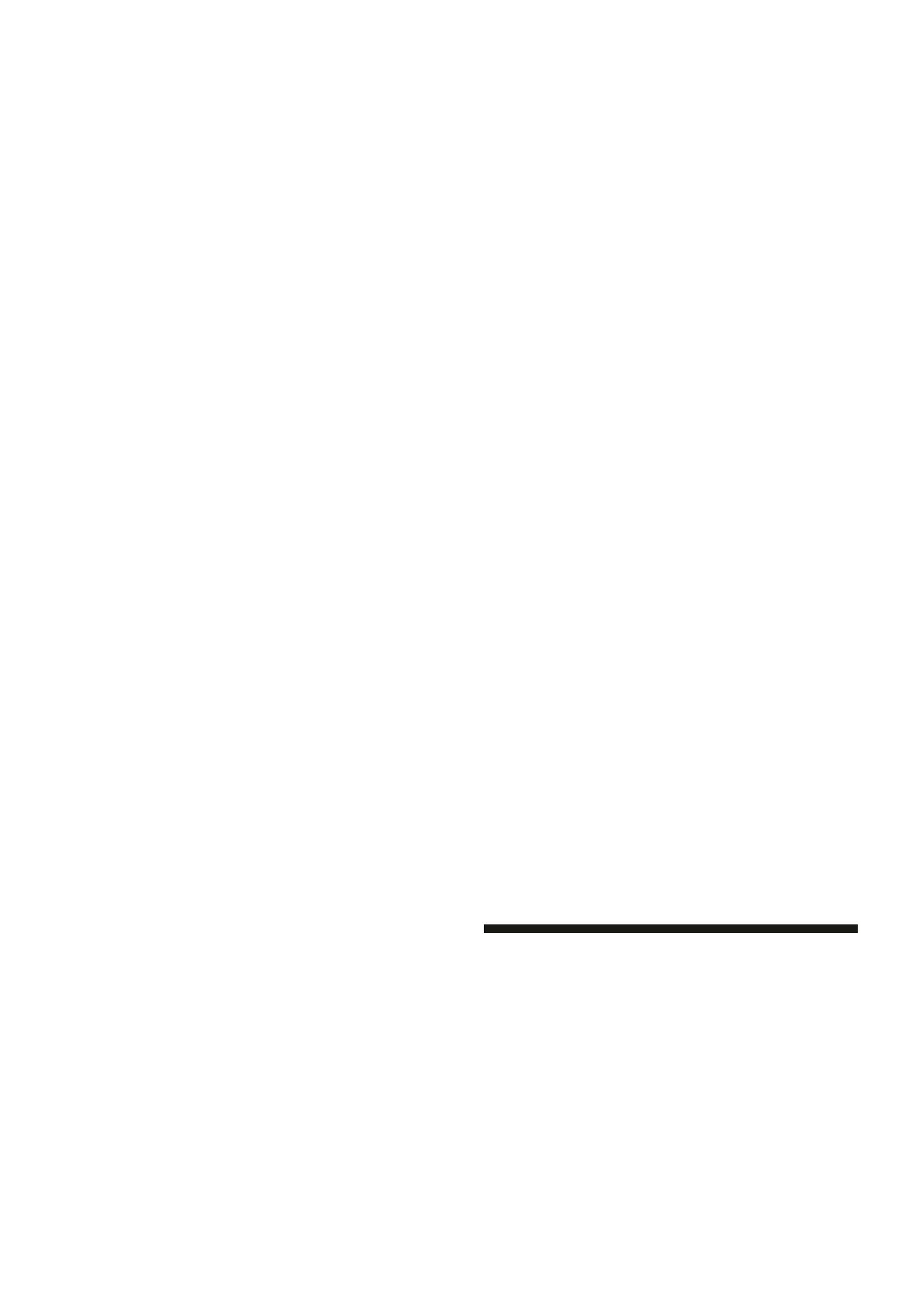
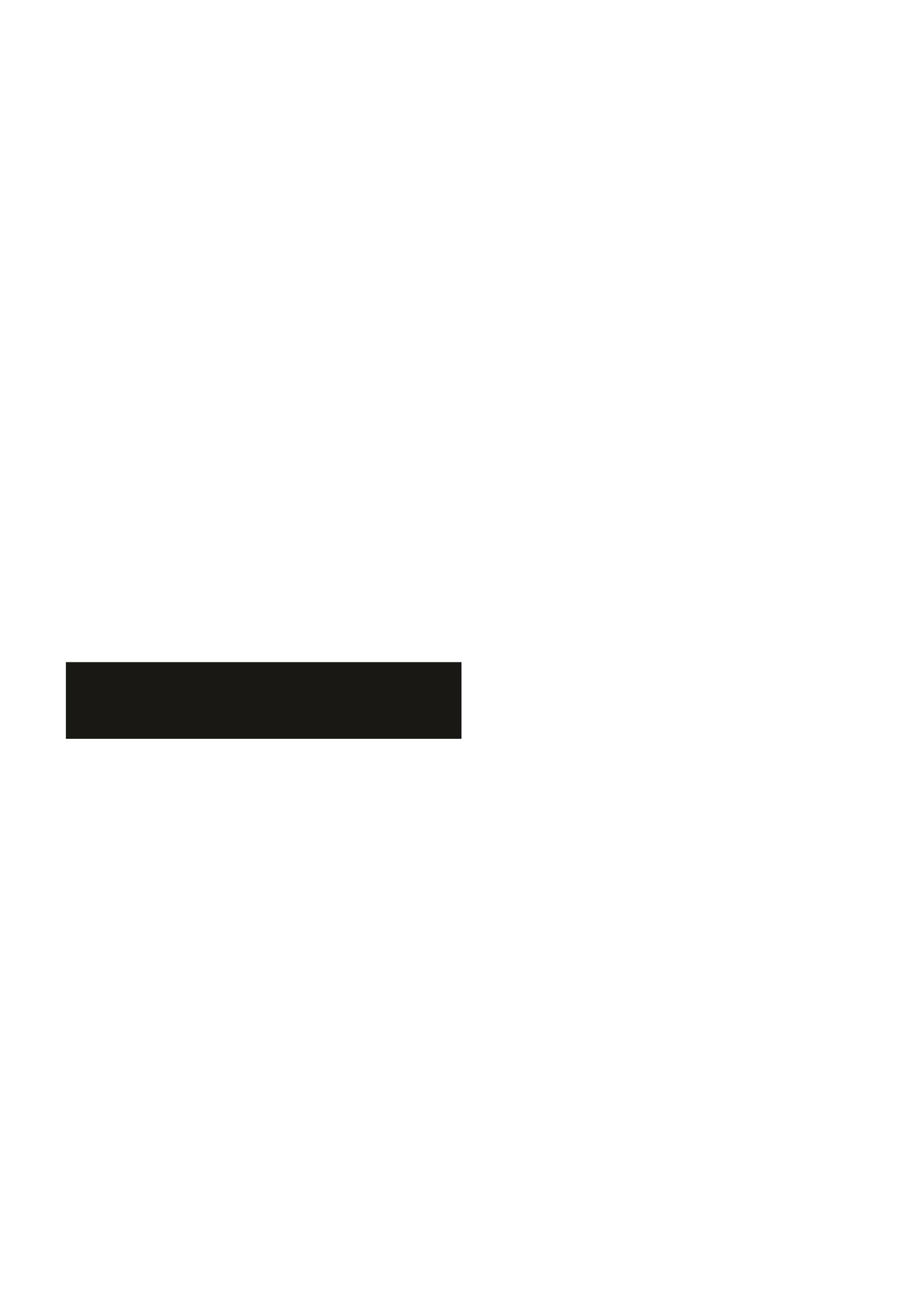
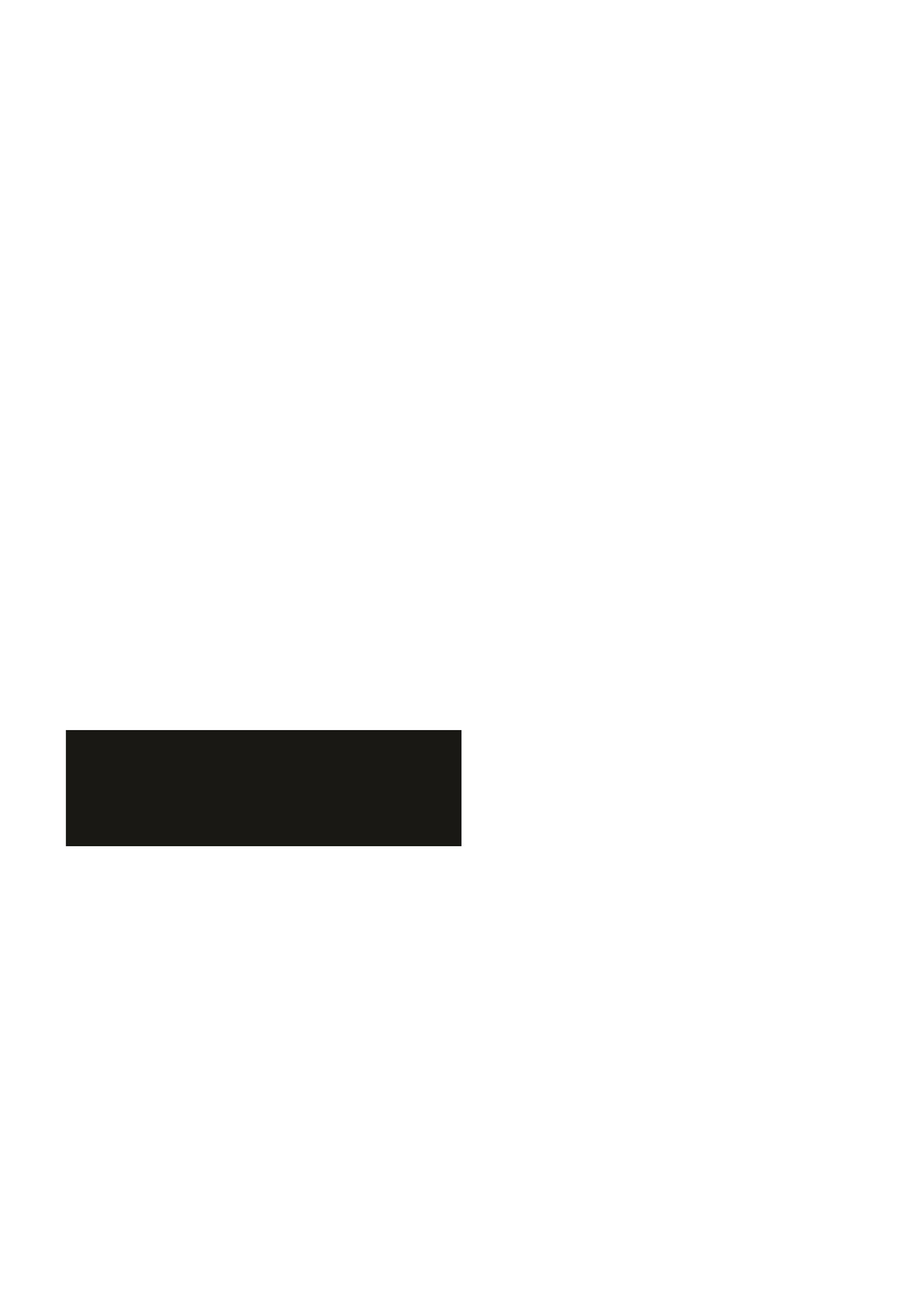
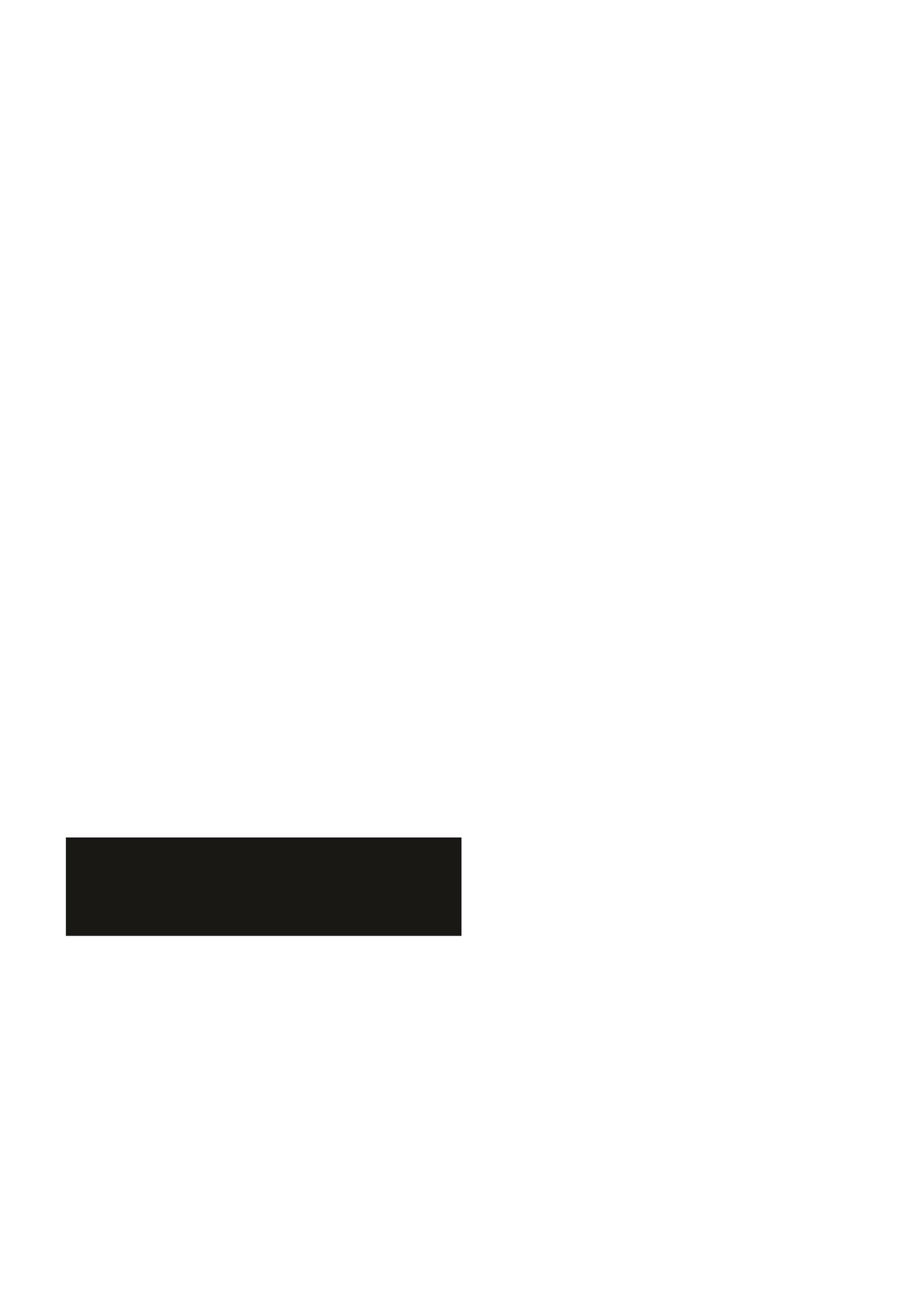
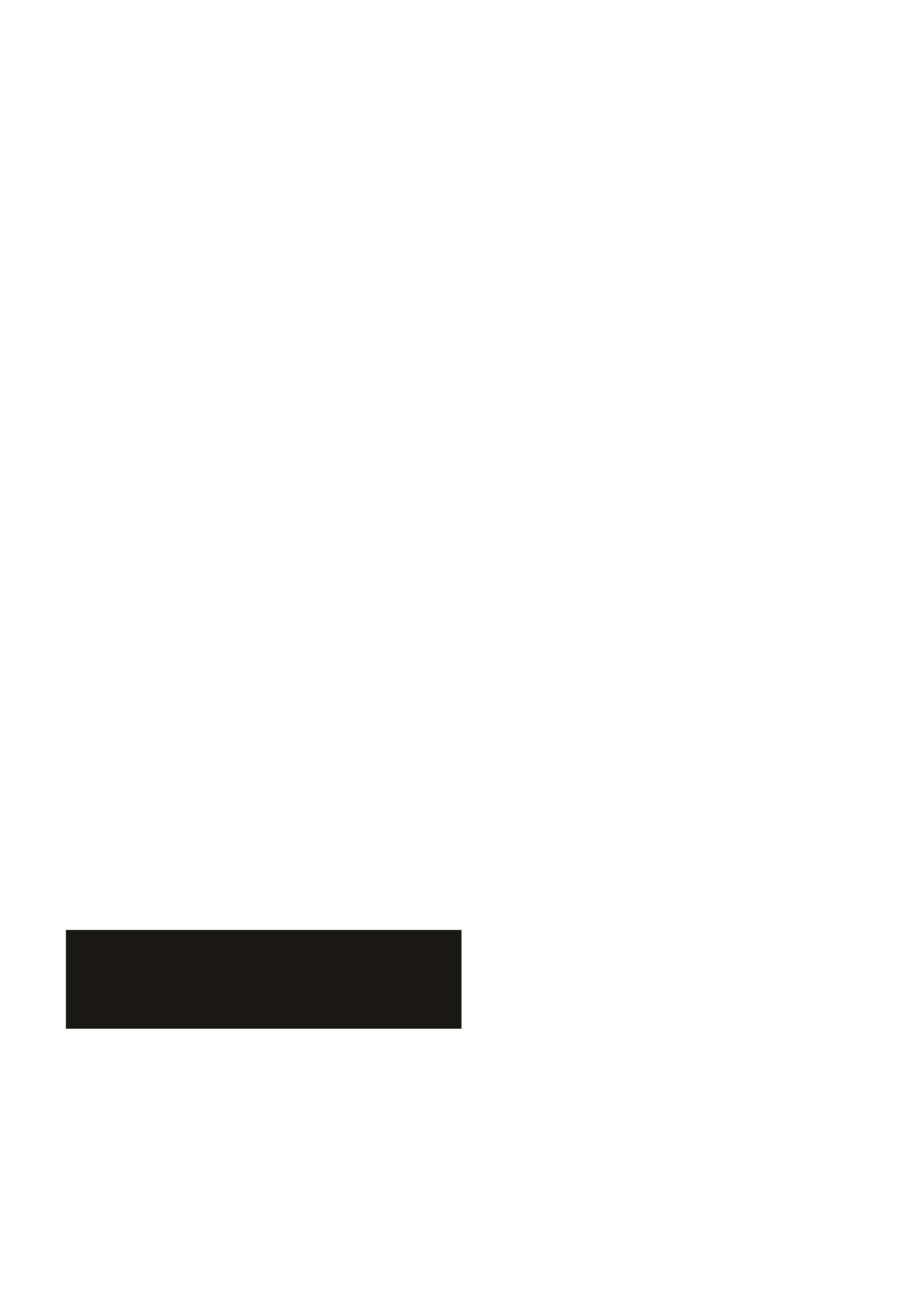
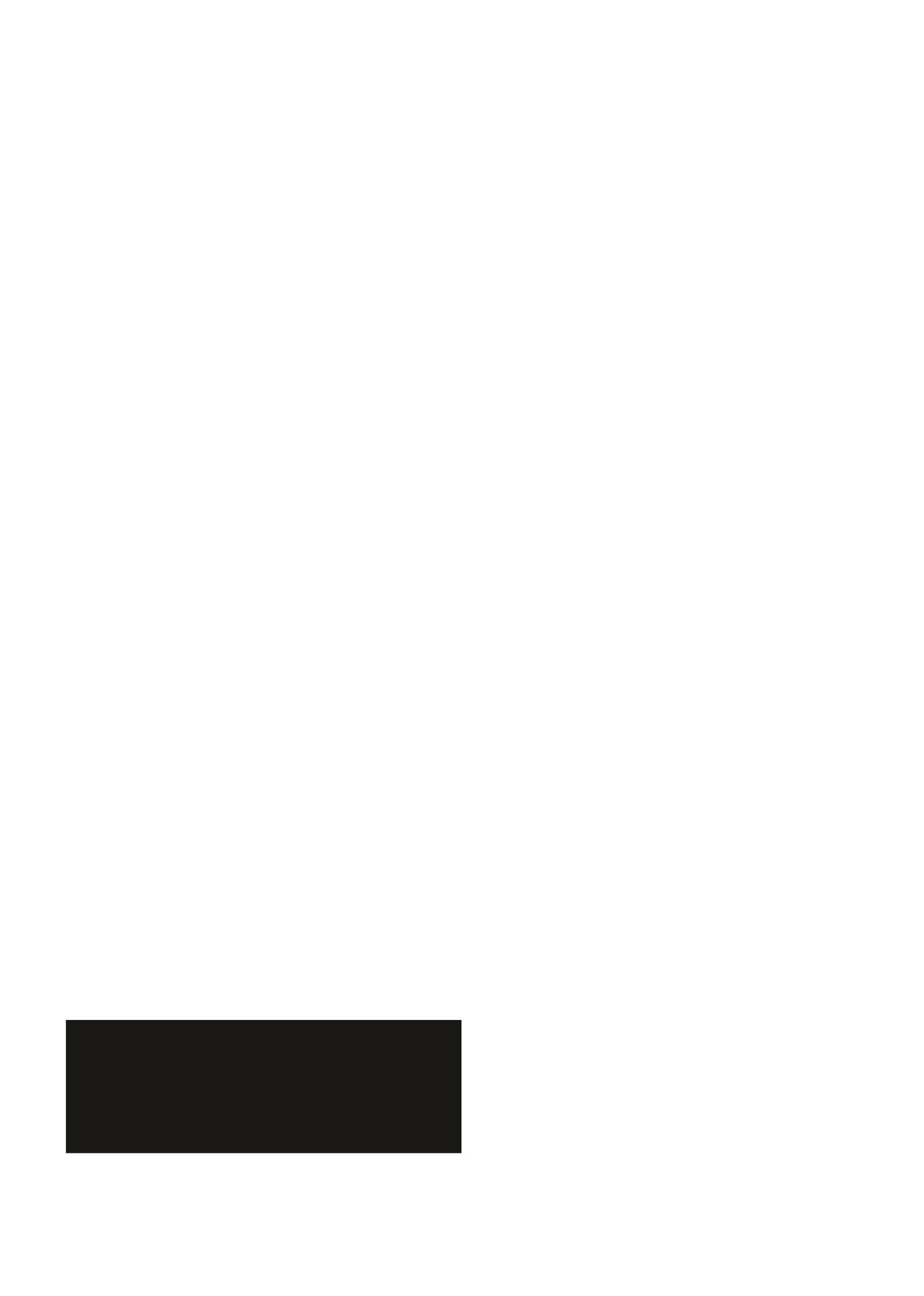
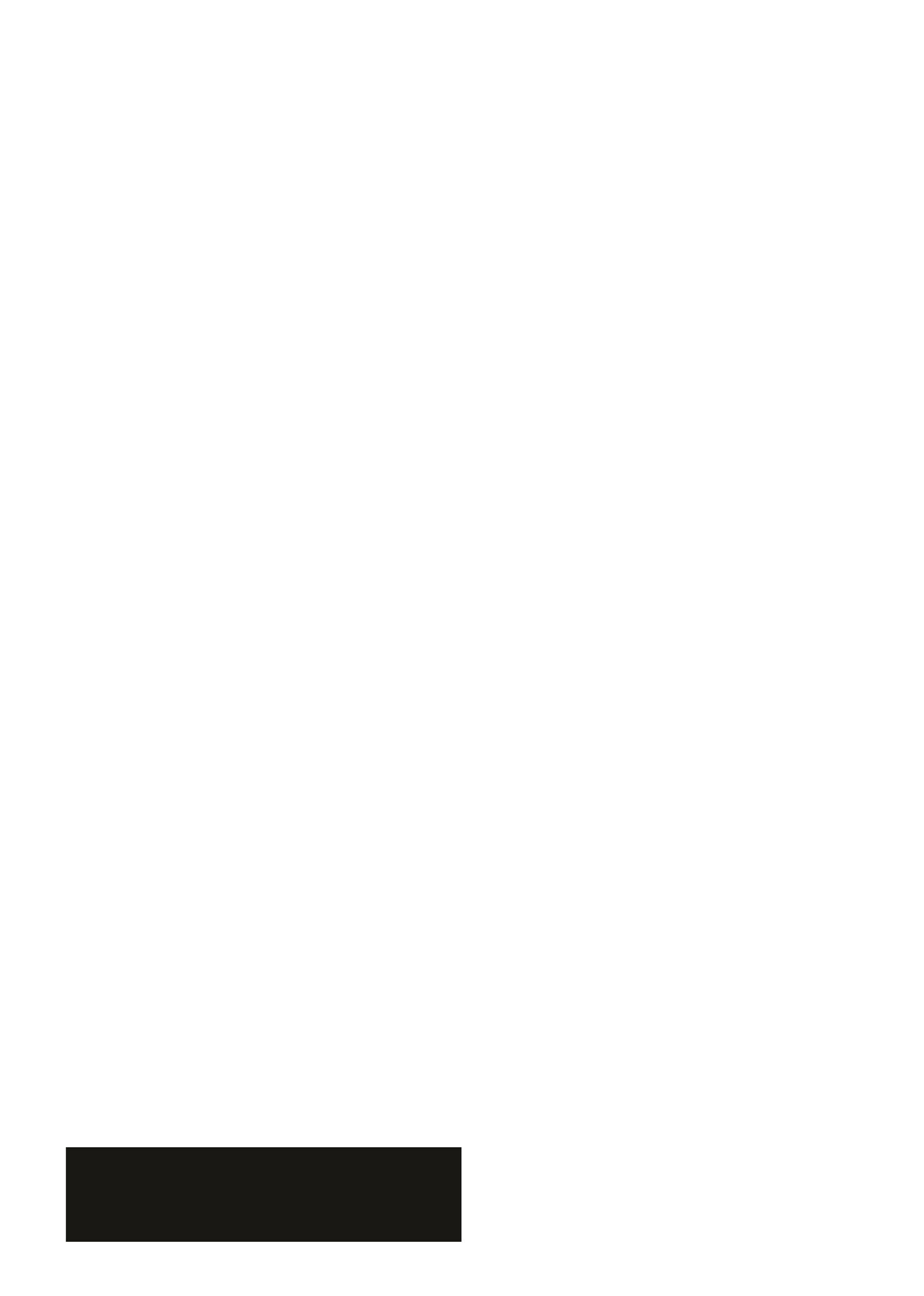
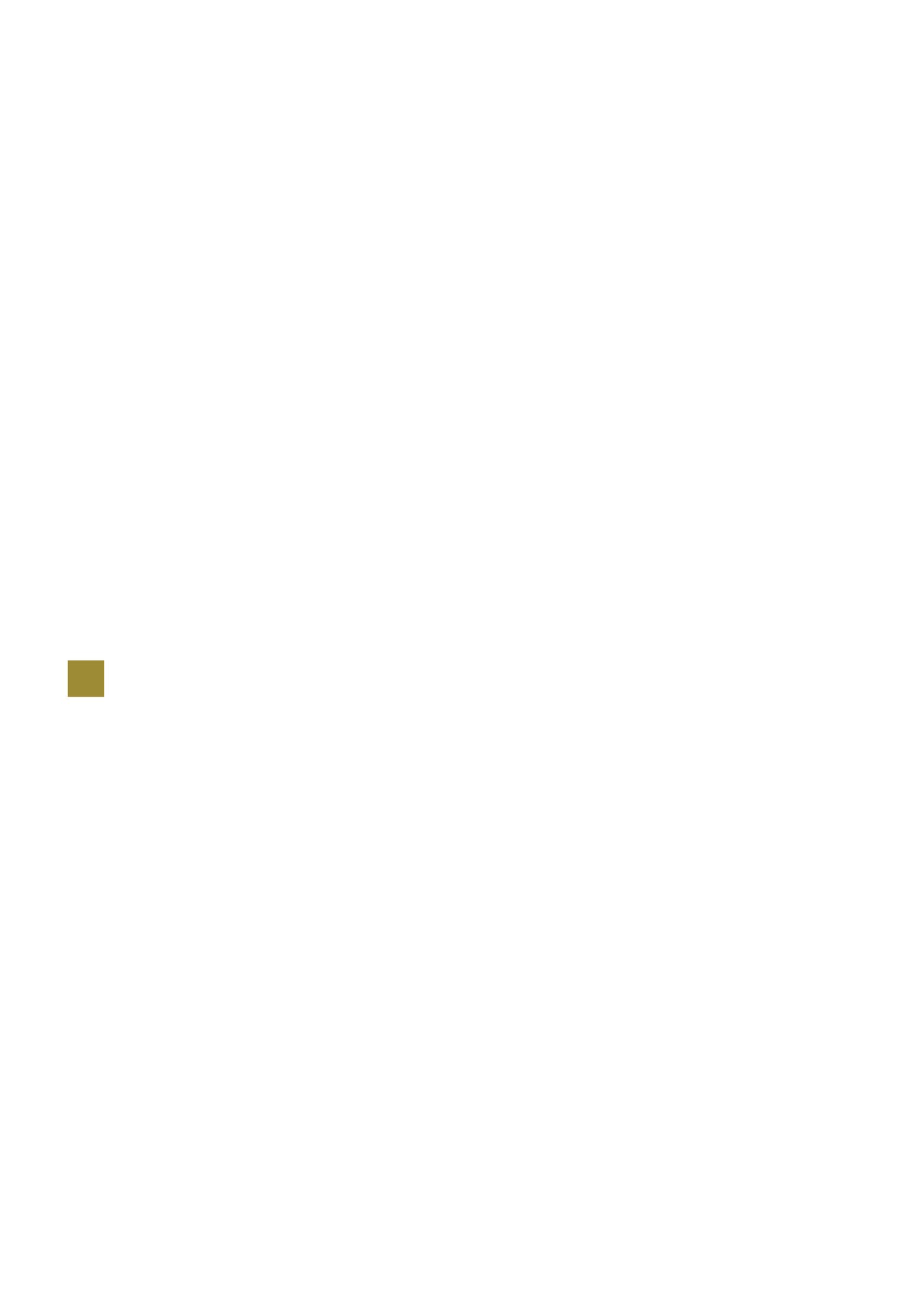
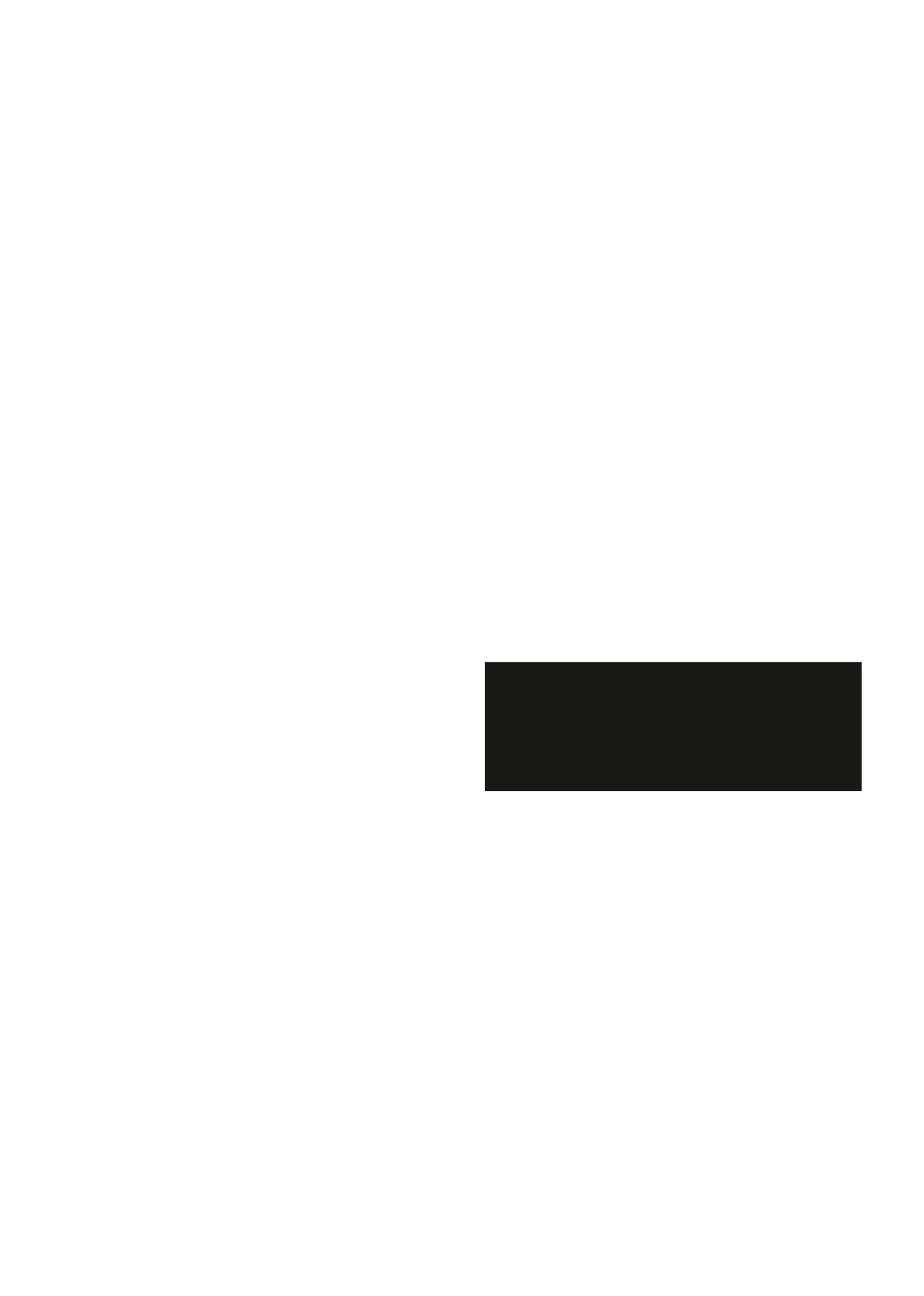
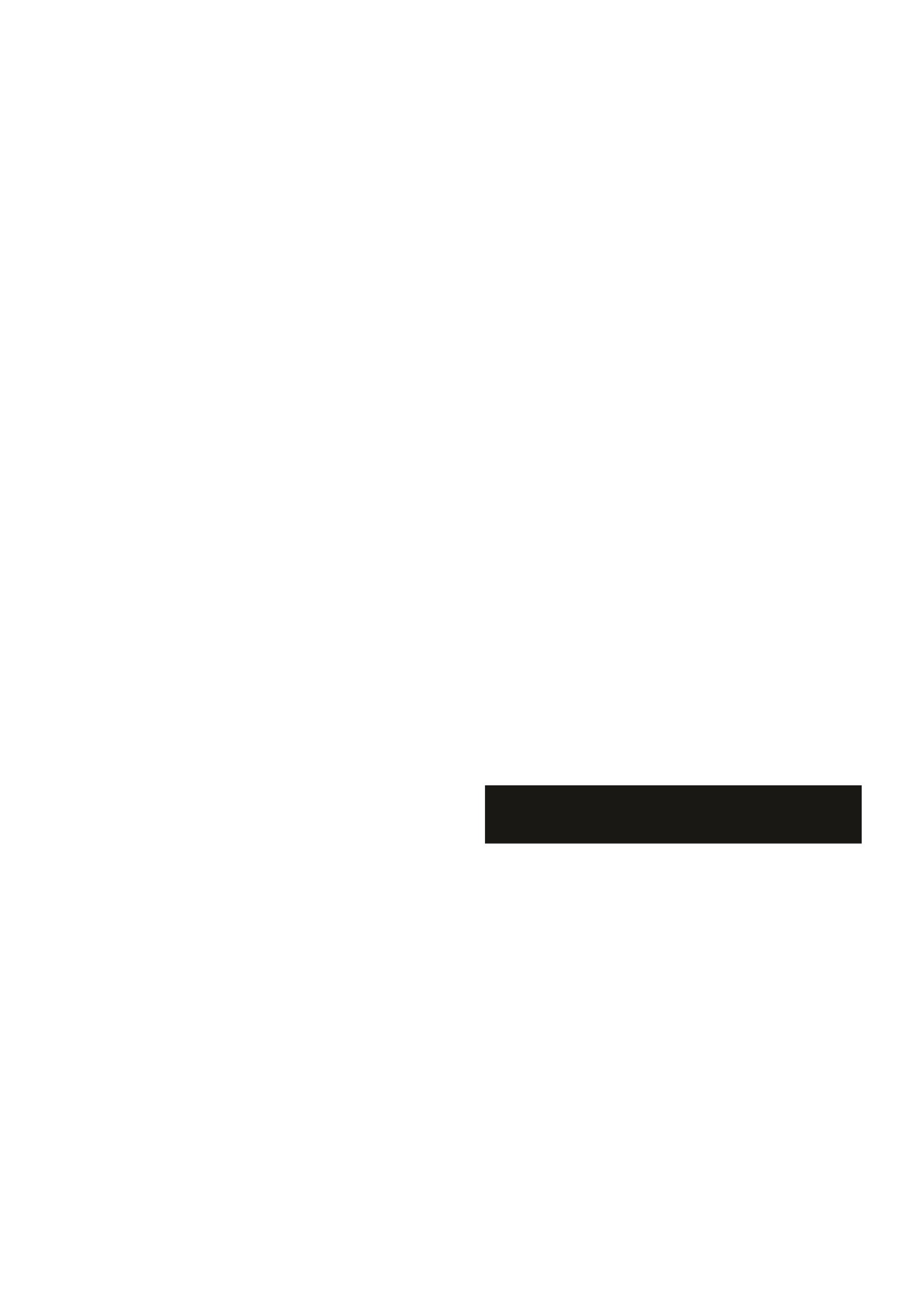
research to gain knowledge and understanding of flotation in mining, while benchmarking various flotation technologies.
Flotation is a key process area with impacts on upstream comminution and downstream dewatering. There is huge potential to save energy and resources through the latest innovations in refining flotation process technology. These environmental benefits also support the FLSmidth MissionZero ambition to reduce emissions from mining towards zero by 2030.
Helmholtz Center Dresden Rossendorf (HZDR) and FLSmidth recently proposed a project named ‘FlotSim’, with the goal of drastically improving the recovery rates of flotation through fundamental flotation analysis, and comparing the industrial state-of-the-art technologies to each other. This project received a 2020 Horizon grant.
This fundamental research, along with strong internal research and development (R&D) eff orts, will advance existing and developing flotation products, including: forced air nextSTEP, naturally aspirated WEMCO, fast flotation REFLUXTM Flotation Cell (RFCTM), and coarse particle coarseAIRTM flotation cells. In addition to furthering fundamental understanding, these eff orts will allow for improved simulation models and, subsequently, optimised equipment selection and flowsheet design.
Improved next generation flotation processes are mandatory to remaining economically competitive and to ensuring sustainable mining for future generations. The FlotSim collaboration with industry and university partners, along with the recruitment of five early stage PhD research candidates, will address some of these important societal challenges.
At the end of 2020, a second grant (the annual EIT RawMaterials KAVA Upscaling Projects grant) was awarded to a consortium of mine sites, chemical companies and universities, led by FLSmidth, to specifically upscale the aforementioned RFC technology.
The goal is to upscale the RFC technology and accelerate commercialisation during the 3-year project. This will involve pilot and full scale testing, as well as eventual sales of full scale equipment for the copper and iron ore industries, among others.
The innovative RFC technology, invented by Professor Kevin Galvin of the University of Newcastle in Australia, has an entirely new internal design compared to traditional flotation methods. The result is much higher throughput with simultaneously improved separation eff iciency.
The RFC is already proving that it can operate successfully outside of the limitations experienced by traditional open tank flotation systems. The technology has potential across various commodities and flotation applications. The opportunity presented by the work packages included in the EIT RawMaterials KAVA grant will accelerate the commercialisation of the technology. It will also allow for further development and optimisation of the RFC, which will further expand FLSmidth's suite of flotation product off erings.
The consortium behind this upscaling project is led by FLSmidth and includes two mine sites (KGHM Polska Miedz Spólka Akcyjna in Poland and Luossavaara-Kiirunavaara AB [LKAB] in Sweden), two universities (Norwegian University of Science and Technology (NTNU) and Helmholtz Helmholtz-Zentrum Dresden-Rossendorf University), the Swedish Environmental Research Institute, and several external advisors. The University of Newcastle in Australia and Professor Kevin Galvin will act as two of the external advisors.
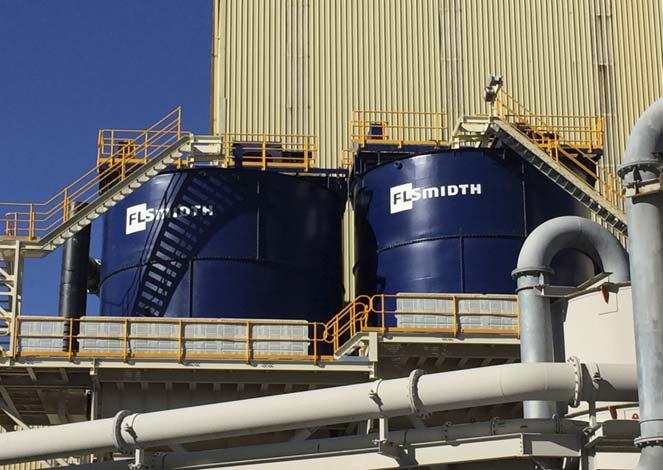
Figure 3. Two FLSmidth flotation cells installed at a mine site.
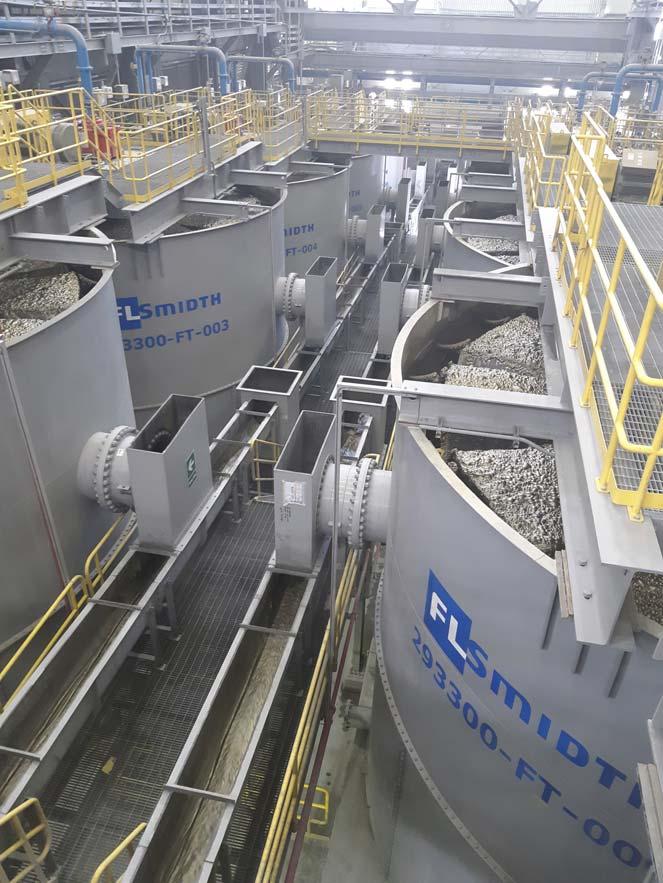
Figure 4. The mixedROW™ Flotation System.
Conclusion
Flotation is a crucial part of the mining process, but it is also one that is resource intensive – using approximately 7% of a mine’s total electrical energy and significant amounts of water. This resource usage means costs for the operator, as well as creating waste that must be managed. As sustainability and a focus on resource usage join eff iciency improvement as priorities for miners, the research and eff ort needed to optimise flotation are becoming increasingly important. Through new innovations, such as those detailed in this article, coupled with a high R&D focus, a more eff icient and higher performing future for flotation seems to be bubbling nicely to the surface.