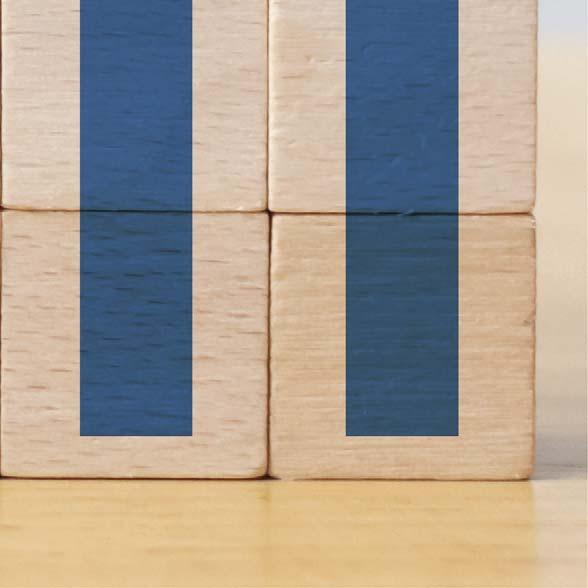
7 minute read
Managing Productivity
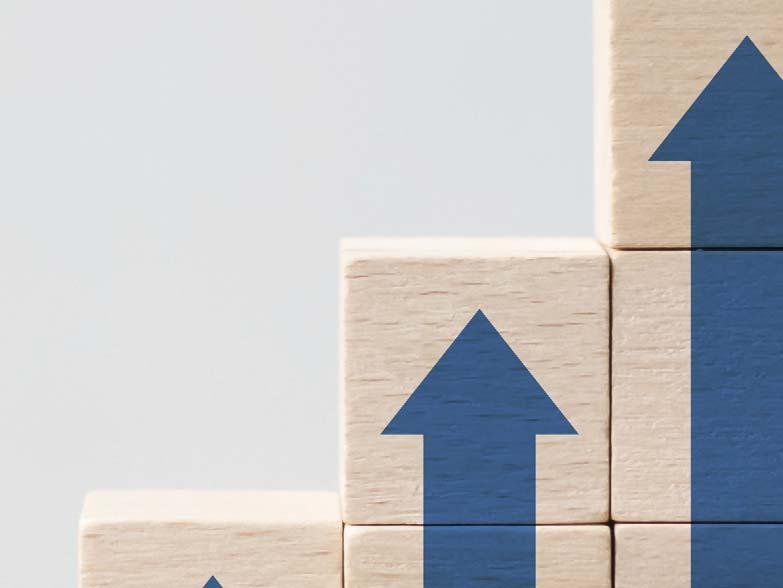
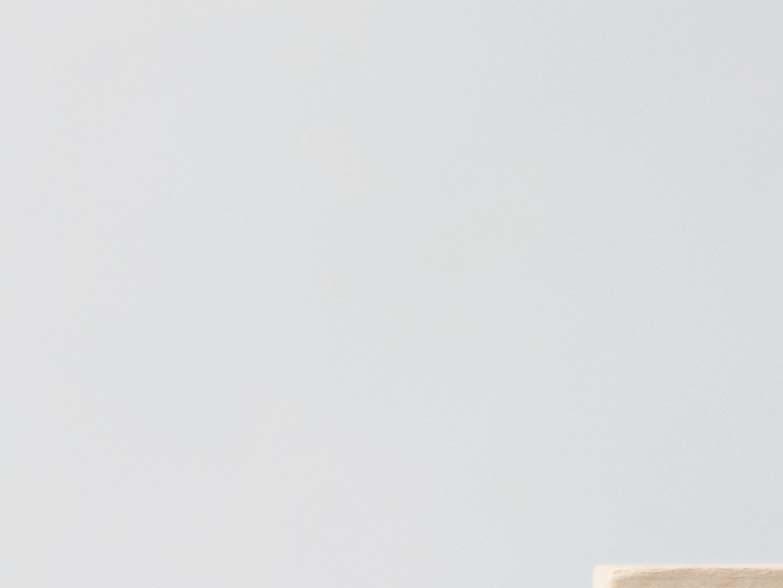
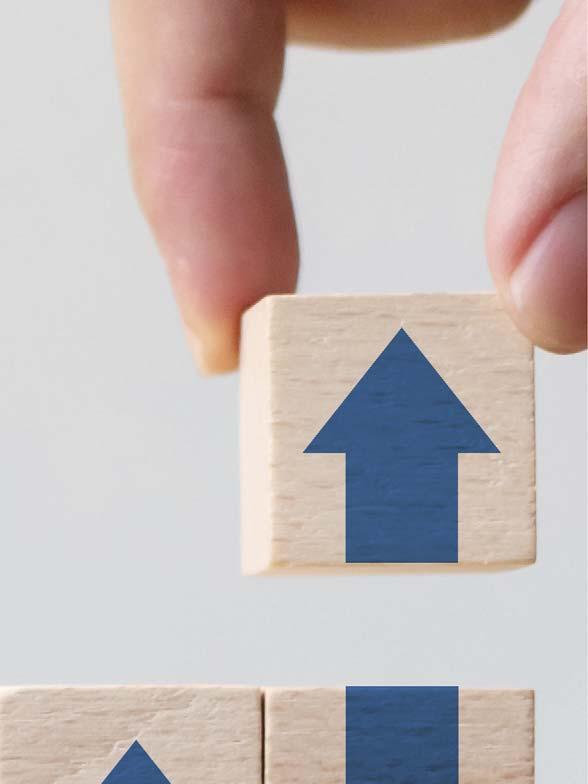
Peter Malmberg, Epiroc, Sweden,
explains how inventory management can increase productivity.
Productivity, safety, and sustainability are all key factors for drillers looking to increase eff iciency and profitability. The quality of the rock drilling tool is essential for getting the most out of a business. A premium quality drill bit provides more drilled metres per bit, minimises operator contact with the bit, and reduces raw material consumption in production, as well as transport.
These advantages can be further enhanced through smart inventory management. By monitoring stock levels and consumption in real time, a driller has a far better view of how a certain drill rig and operator is performing. It also helps reduce inventory requirements, since the need for excess stock to buff er against uncertainty is eliminated.
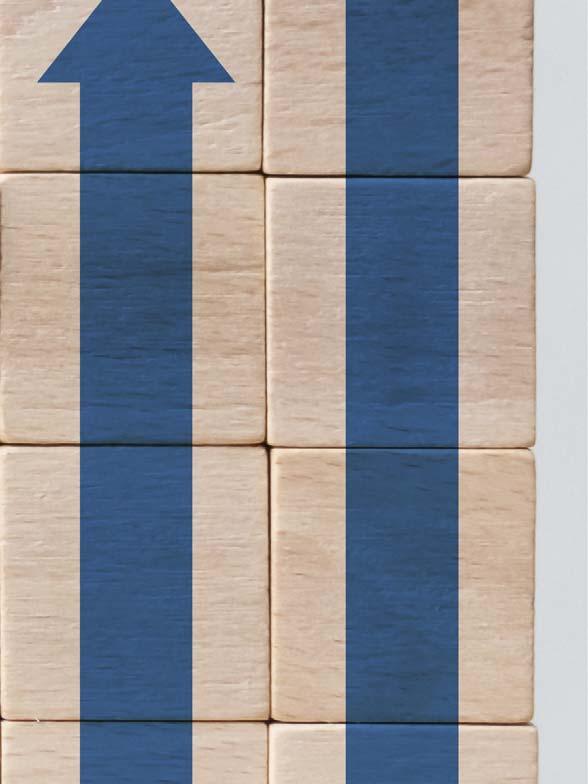
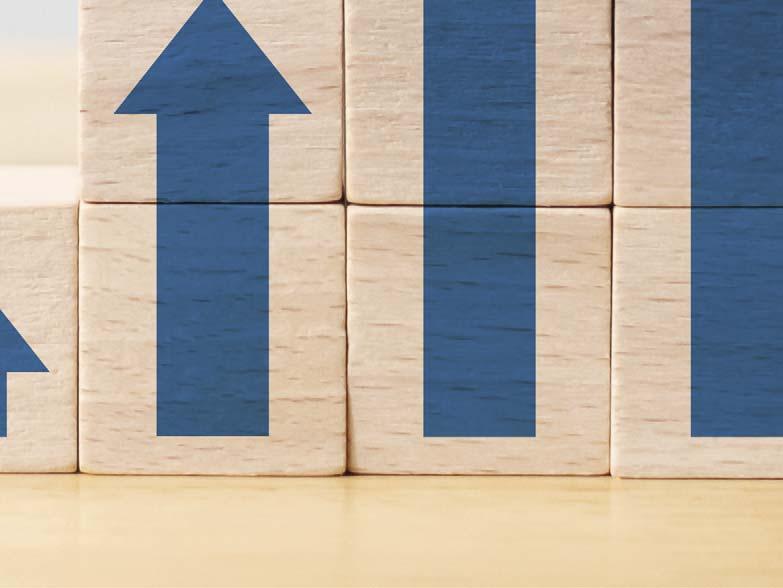
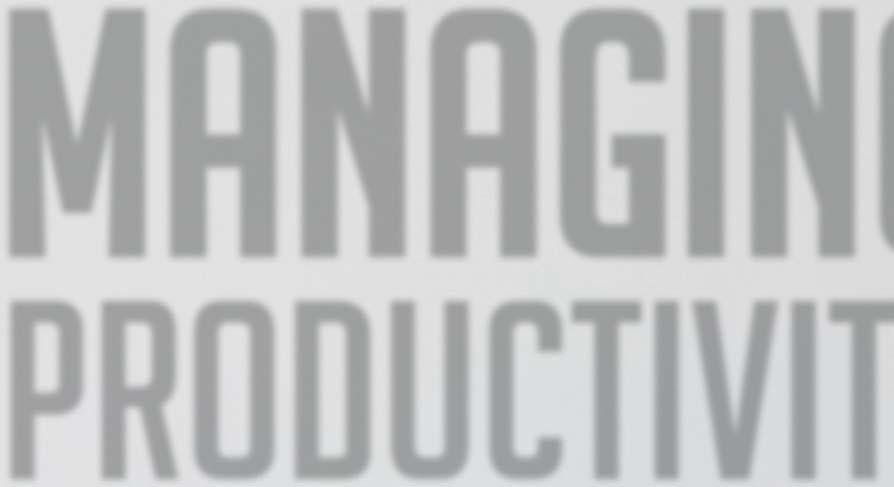
Inventory applications
Swedish company, Epiroc, has developed the Smart Inventory Management (SIM) application to perform just this. The objective when developing the application was to increase efficiency related to the management of inventory located at a customer’s site. The SIM application also gives insight to consumption per piece of equipment and/or operator, and is therefore a tool to support performance monitoring. The overall objective is to create a ‘real time total cost per measure’ reporting system.
The company’s push to develop solutions in automation and digitalisation has culminated in a concept called the 6th Sense. The 6th Sense offering is a complete solution with which Epiroc provides diverse, but closely intertwined, products and technologies to simplify and streamline customer operations.
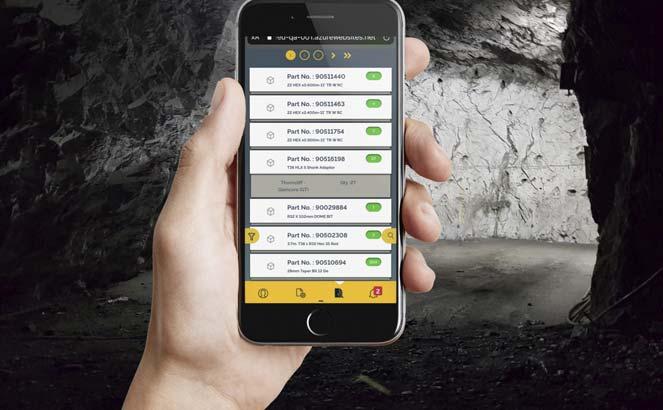
Figure 1. The Smart Inventory Management (SIM) application provides an eff icient overview of drilling tools inventory.
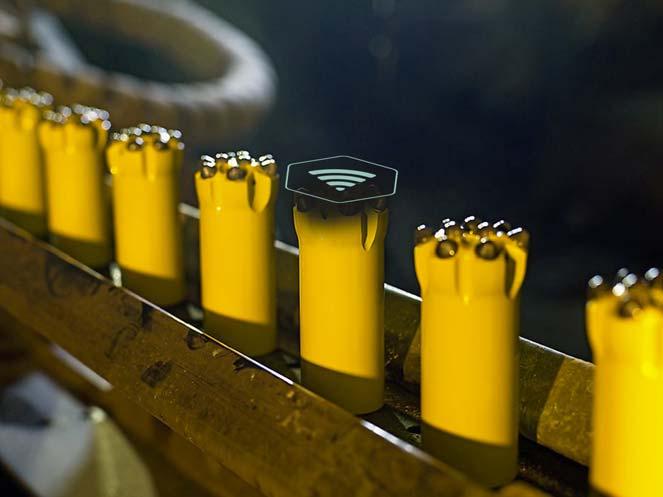
Figure 2. By using digitalised inventory management, the need for excess stock to buff er against uncertainty is eliminated.
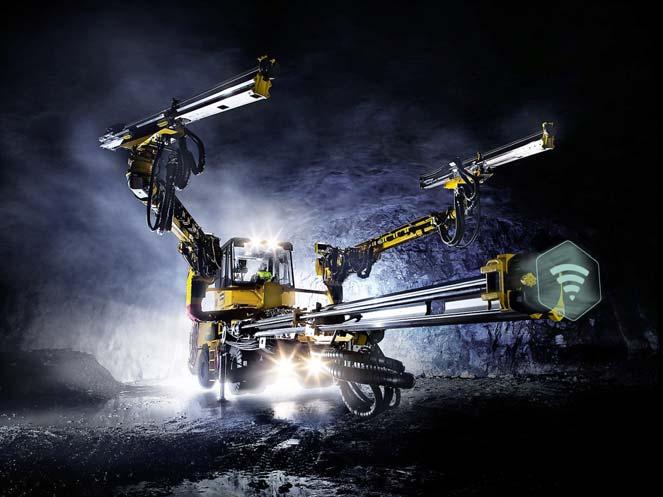
Figure 3. The SIM application can help drillers get information regarding how a certain drill rig and operator is performing.
The need for a digital solution
Inventory management for stock located far out in the supply chain, typically in remote mining areas, is time consuming and commonly conducted with low frequency, resulting in late responses. Transactions are typically noted with pen and paper, using a template to make sure that the required information is collected. Consumption is difficult to monitor, often resulting in either too high or too low stock levels. It can also result in obsolete inventory, as supply struggles to keep up with actual swings in demand. It is clear that there is a lot to gain by having improved supply chain visibility and that the development of the SIM application is a step in the right direction towards digitalisation in rock drilling tools.
At the outset of the project, three major benefits were targeted: Improved customer service by receiving timely information when goods are withdrawn – thereby suppliers can better respond to customers’ inventory needs, in terms of both quantity and location. Minimised demand uncertainty by constantly monitoring customers’ inventory and demand stream – lowering the need for large, unexpected inventory orders. Reduced inventory requirements by knowing exactly how much inventory a customer is carrying – allowing for the supplier’s own inventory requirements to be lower, since the need for excess stock to buffer against uncertainty is eliminated.
Given these objectives, the need for a digital solution that would automate processes for efficient inventory management, report stock movement in real time or near real time basis, and pass information immediately to an enterprise resource planning (ERP) system for execution was identified. The ideal system would provide integrated management of primary business processes, in real time, mediated by software and technology.
Connectivity
The SIM application is designed to work while connected to the internet above ground, and offline while underground. This is made possible by storing data locally on a device and then uploading it once the user is re-connected. Epiroc aims for its SIM application to support all devices, having built it using progressive web applications (PWA) architecture. Today, it supports integrations with Epiroc ERP systems, but in the future it
will be possible even to connect to external ERP systems, if the customer require this support.
When a user registers information in the application, the application will then send the data to an integration layer. The reason for using an integration layer is to enable other ERPs to integrate without changing anything in the application. The integration layer will then forward the data to the assigned ERP system, which will then save the data and in turn send it forward to the Global Inventory Management system (GIM), which is the system used by the supply chain for monitoring stock levels and consumption. The GIM will then analyse the consumption and suggest purchasing orders to replenish the consignment. If the device is offline, the information will be cached on a phone and automatically sent to the ERP when the device is connected
If a warehouse is not replenished via a GIM, the administrator can still analyse the GIM suggestion and place orders based on the information. The ERP will then push data back to the application via the integration layer making sure that that stock levels will be always synchronised. The application provides the appointed administrator with the transaction history, specifying which items were taken, in what quantities, and to which machine and operator the items were assigned. This will enable the administrator to effectively investigate the reasons for potential discrepancies and enable a faster reaction time on swings in consumption.
The SIM application is now being rolled out to selected customers and the benefits are being shown, with reduced administration and improved quality of master data. The system installation is executed in a controlled manner, including mapping and analysis of the logistic process. Actual results vary with the complexity of the existing process, but there is typically a process improvement in place aft er implementation. These are all improvements that already justify the SIM application, while the true value related to data driven actions from having real time insights will take a bit more time to confirm.
Conclusion
Keeping track of drilling tool inventory has long been a challenge for most companies in the industry. Relying on experience has been one way, but that comes with varying degrees of accuracy. Not knowing how the drilling operation performs means that drilling tools may be changed too early or too late, creating inefficiency in the drilling operations. In the worst case scenario, the machines stand still due to empty inventory, affecting profitability. For very remote sites it is even more critical to have an accurate inventory calculation, as the delivery times can be very long. From a sustainability standpoint, actual knowledge of how the drilling rigs and tools are performing enables more accurate predictions of how much inventory will be needed, which reduces the risk of having to place additional orders. This leads to fewer transports and a reduced environmental footprint.
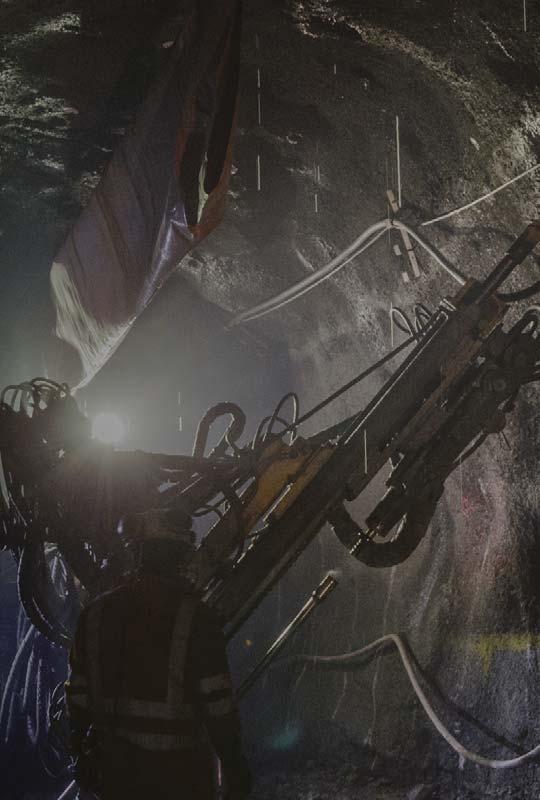
SECURING MINING TOGETHER.
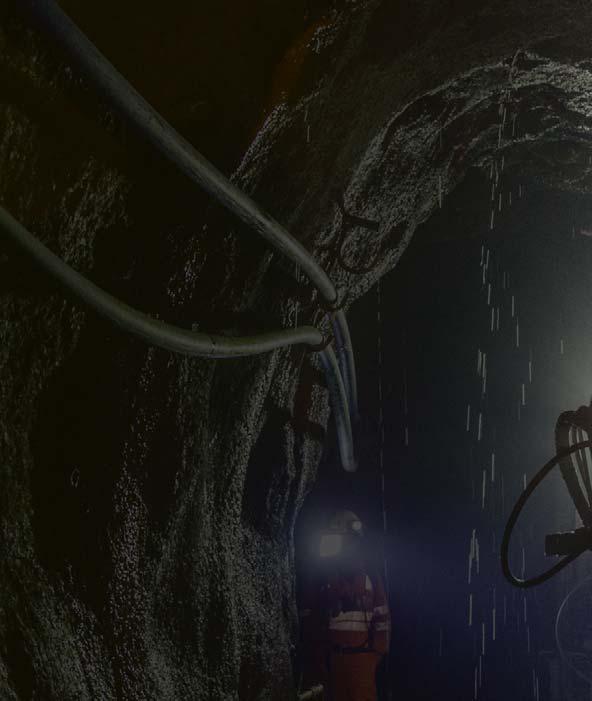
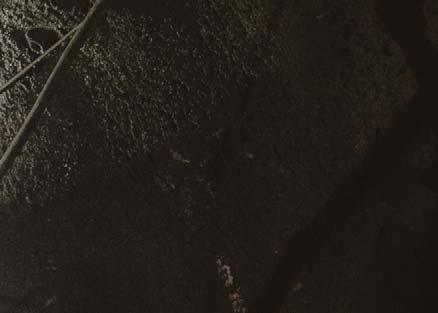
HARD ROCK & COAL SOLUTIONS
Minova is a leader in developing innovative bolts, resins and grouting solutions for underground rock support, covering even the most challenging environments.
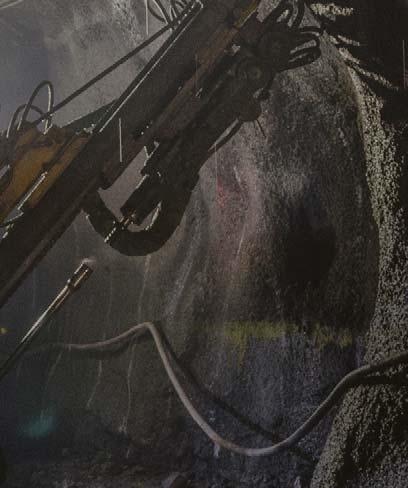
We know the importance of continued safety and improved installation efficiency. Our products are used in a variety of applications across the development and production areas of the metalliferous and coal mining industries, including ground support, water stopping, void filling and ventilation.
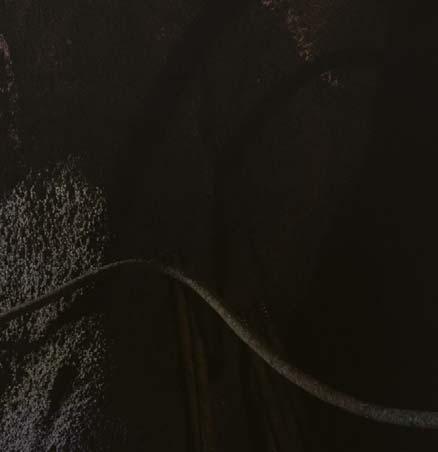
> STEEL AND GFRP BOLTS & ACCESSORIES
> RESIN & CEMENT CAPSULES
> INJECTION CHEMICALS
> PUMPABLE GROUTS
> SPRAYED MEMBRANES & COATINGS
> EQUIPMENT > TECHNICAL SUPPORT
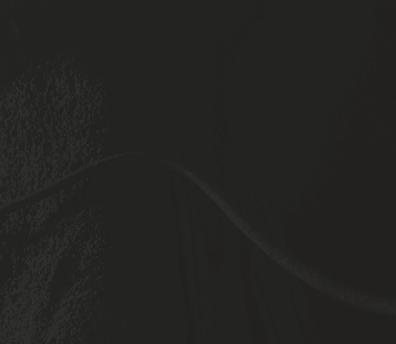
ground support, water stopping, void filling and ventilation.

See our product portfolio at See our product portfolio at www.minovaglobal.com www.minovaglobal.com
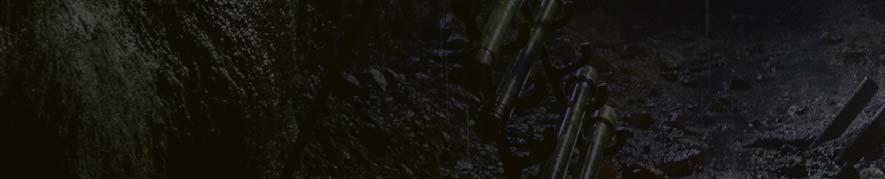
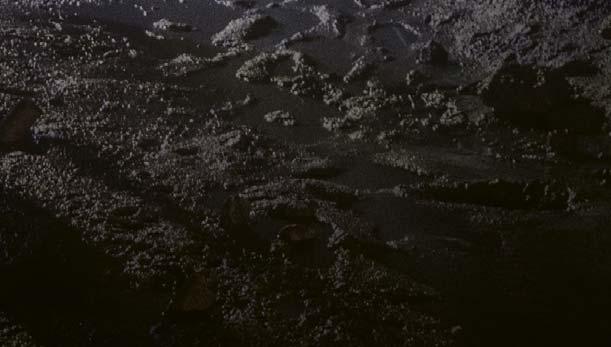
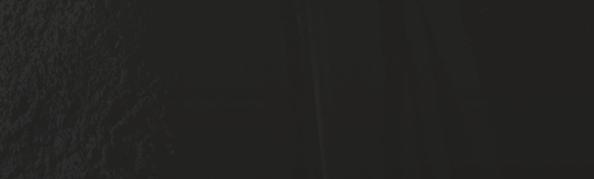
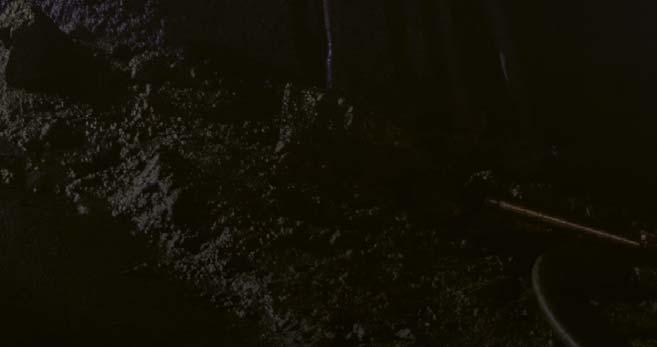
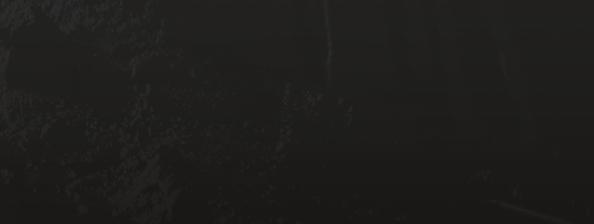
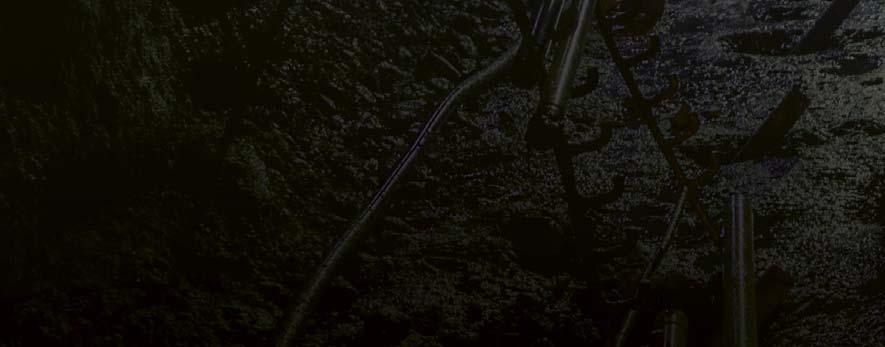