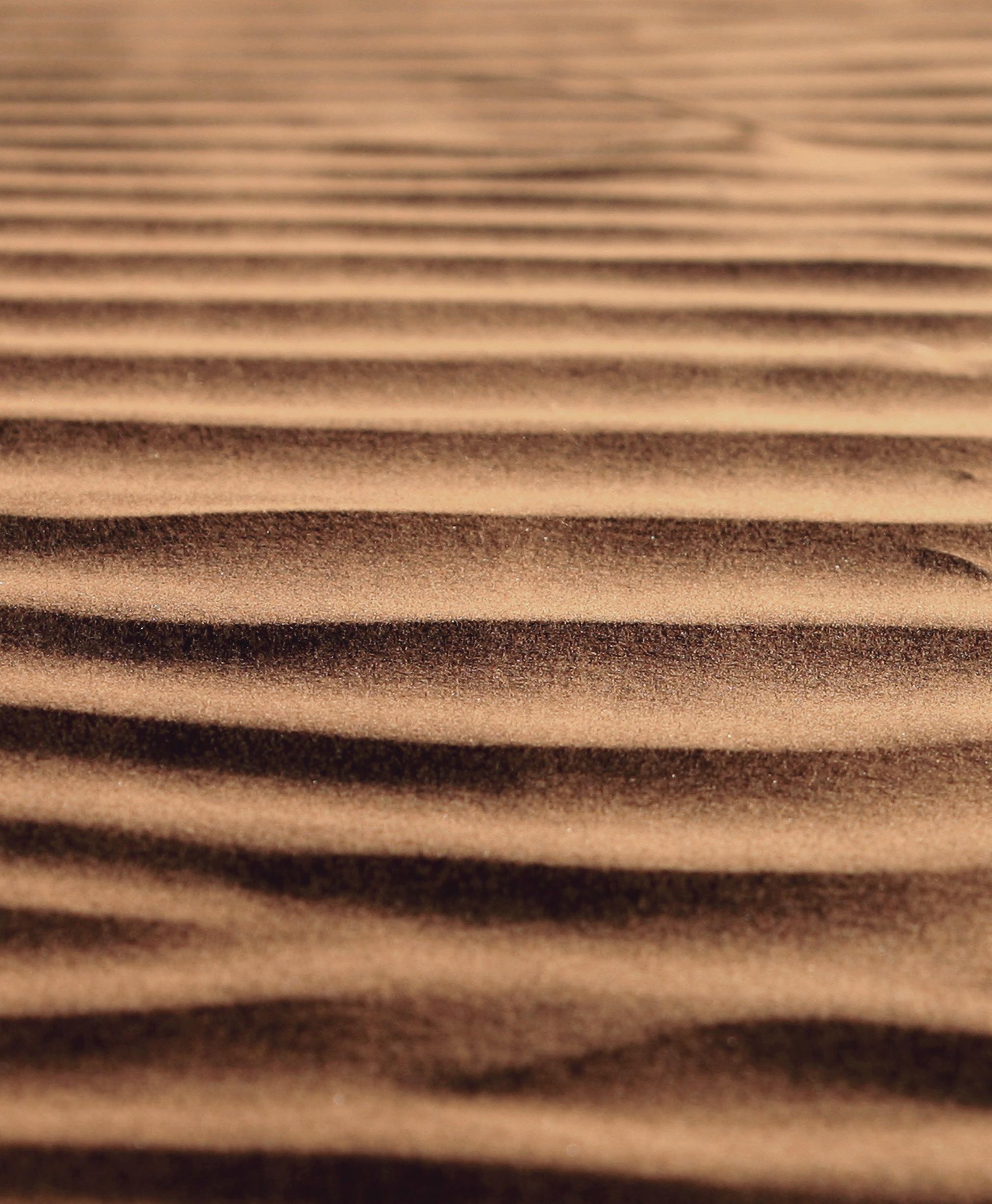
8 minute read
The sands of brine
Far from the mythical Sandman of folklore who brings pleasant sleep and sublime dreams, sand production in oil and gas operations is an all-too-real nightmare that seems to intensify with every improvement in production technique. Finding novel ways to squeeze more hydrocarbons from the formation invariably entails producing not only more water but also more sand – in many cases, a lot more. Not only are sands of finer grain size being used as proppant (further complicating its capture and removal), producers are encountering increasing volumes of sand as operations tap into an ever greater number of ‘soft’ formations, especially in gas fields. And as the demand for natural gas continues to soar with the shift away from coal and other trends, the volumes of sand will naturally track with that upward demand.
Costly geophysics
Sand in the flow stream may be an old problem, but it remains as serious as ever, and it is just as ‘scalable’ as the best modular equipment. Sand can inflict tremendous harm on everything in the wellbore: from the smallest section of tubing to the casing, all the way up to surface equipment and downstream production facilities. It can even compromise wellbore stability and prematurely end the life of a well. If sand-blasting with only moderate pressures can remove layers of rust from metal and carve lines in concrete, imagine what it can do at the high pressures found in wells.
Moreover, the problem is not confined to this or that basin – it is global and prevalent in Africa, North America, South America, Southeast Asia and other regions, both onshore and offshore, particularly in gas fields where reservoir formations are unconsolidated or semi-consolidated. High-flowrate gas wells are especially prone to damaging levels of sand production, where the elevated flow and turbulence exerts drag on the formation, thereby dislodging ever more sand particles, which are then accelerated to erosive velocities that wreak even more havoc on operational infrastructure. Much more than a mere inconvenience, the damage wrought by sand continues to cost companies millions of US dollars every year.
Hydrocyclones: not just spin
Fortunately, and despite the headwinds, the same industry that has for some 170 years fuelled modern living and economic growth continues its long-held tradition of pioneering innovation. Just as recycling flowback and produced water continues to evolve and become the norm, the removal of sand from the flow stream has advanced dramatically in just the past few years.
Brandon S. Mitchell, TETRA Technologies, USA,
says the decisive advance in sand removal technologies in recent years is cause for celebration.
Hydrocyclone technology has now eclipsed passive filter systems and cyclonic sand separators as the favoured means of managing high volumes of fine sand, yielding greater levels of efficiency in removing sand from the flow stream. In fact, one particular advanced hydrocyclone technology has been achieving consistent efficiency rates of 97+% and as much as 100%. Such efficiency rates are gauged by placing separators downstream from the cyclones and measuring the amount of sand they capture, which is now often close to zero.

Centrifugal wizardry
The hydrocyclone is basically a cylindrical-shaped device with a lower conical section, outputs at the top and bottom – called the overflow and underflow, respectively – and an angled feed input on the side near the top. Inside is the vortex finder, a tubular section extending downward a short length from the overflow, and the apex valve adjacent to the underflow.
The core operating principle of the hydrocyclone is centrifugal force, but unlike its cousin, the centrifuge, it has no moving parts. The elegance of the design is that it exploits the velocity of the well’s output to impart centrifugal force on solids as they enter the unit at a tangent to the cylindrical body. The decreasing radius of the conical section increases the centrifugal force, which enhances the separation of the sand and solids from the fluid (this latter term denoting both liquid and/or gas).
Inside, the multiphase content whirls around with enough velocity to force the heavier and denser sand particles outward against the walls of the body, while the vortex finder induces the solids-free fluid to form a vortex column in the centre. The force, described by Bernoulli’s principle, diverts the solids-free vortex upward through the overflow, while gravity forces the sand to funnel down through the apex valve and out the underflow.
Variation in the field
Regarding the application of sand management technologies, and oversimplifying the operational picture to some degree, we could say: all uncomplicated operations are alike; each operation with high sand production is complicated in its own way. That is to say, no two high-volume sand production scenarios are the same; each is unique and requires a solution tailored to the specifics of the reservoir, the well, the flowrate and the sand.
Thus, innovating technologies to address sand production is only half the equation; the technology must also be adapted to accommodate the enormous variation among not just several wells on the same site but also the variations within a single well –
varied pressures, varied volumes of sand, varied particle size, varied flowrates and other potential variables all occurring in the same well. For example, the initial peak flowrate of a well immediately after stimulation is typically much higher than the subsequent normalised, long-term flowrate. When dealing with a high-flowrate gas well, the initial peak could be exceptionally high.
Tailored adaptation to the uniqueness of each job is achieved through meticulous planning (the importance of which cannot be overstated) and having a scalable technology, a technology that lends itself to adaptation in the interests of efficiency, effectiveness and footprint. Depending on the expected well conditions, modular hydrocyclones can be outfitted with one of several inserts, each of which is designed to be efficient through a wide operating range. The inserts can reliably endure the harsh stresses of fast-moving, solids-laden fluids for up to a year, and they are affordable when replacement is necessary.
In terms of scalability, both filter systems and hydrocyclones are scalable, but there is a catch: filter systems can exert significant back-pressure on the flow stream, handicapping production, especially when stacked in series. By contrast, the inherent design of the hydrocyclone minimises back-pressure by not tapering the fluid flow.
Case study
Automated is differentiated
Once a carefully planned and properly sized solution is in place, adding automation greatly amplifies overall operational efficiency. As with water management, an automated sand management system enables TETRA Technologies to reduce the number of personnel needed onsite to operate all the equipment. Instead of, say, four workers constantly changing filters or manually dumping sand from separators, it is now possible to reduce personnel requirements to a single roaming technician performing routine maintenance and ensuring everything runs smoothly.
Meanwhile, automated monitoring and control keeps operations humming along with maximum consistency, reliability and safety, either from a distant control centre or the field technician’s phone or tablet. Adding to its benefits, a ‘smart’ automated system not only provides a host of metrics on efficiency and volumes – invaluable for reports and subsequent job designs – it can also apply algorithms to automatically tweak operations to further optimise performance and efficiency.
In the summer of 2021, a producer operating six gas wells with very high flowrates in Ohio’s Utica Shale Play approached TETRA seeking an efficient, adaptable sand management solution. In addition to the required small footprint due to limited space on the pad site, the system had to accommodate the very high flowrates the region is known for, as well as be adaptable to the variation from the initial peak flowrate immediately after stimulation to the subsequent normative flowrate. In addition to their high output, the wells were unique for their exceptionally long laterals of nearly 20 000 ft (6069 m), whereas most laterals in the region extended no more than 10 000 ft (3048 m). It goes without saying that the longer the lateral, the more opportunities for unwanted sand production.
TETRA engineered an adaptive solution that used the company’s SandStormTM advanced cyclone technology to achieve 99% efficiency in sand removal with a peak flowrate of 255 million ft3/d from the six wells, a yield that surpassed all other well pads in the area. With the SandStorm units operating so efficiently, the value for the operator has been virtual elimination of the risk associated with sand in the flow stream, thereby safeguarding the equipment while enabling a very high rate of production volume.
Finally, a seismic shift
Within the past 5 or so years, as sand removal technologies have advanced so decisively, the industry has seen a lexical shift from “sand control” to “sand management”. While this might seem like a rather trivial semantic distinction, it is actually a telling turn. It signifies less of a piecemeal improvement and more of a clean break from the past, a reorienting from a thoroughly reactive stance of just trying to control the production of sand, with limited success, to a radically proactive stance of managing and overcoming the challenge. This shift is not unlike the digital revolution or the recent advancements in water management, moving from disposing of produced water in saltwater wells to recycling it for use in hydraulic fracturing. Of course, there is no final goal post in the field of industry and technology – there is always room for continuous improvement. Invention is always required, especially given the exponentially rising demand for energy on the planet. But amid today’s disruption and chaos, it is reassuring to pause for a moment to consider how much has been achieved in just the past 5 years, enduring the unpredictable vagaries of the market, politics and pandemics, fired and fuelled by our industry’s Figure 1. TETRA SandStorm advanced cyclone technology captures frac sand and solids with efficiency and insatiable spirit of innovation. minimal pressure differential, without line restrictions or moving parts. That is certainly worth celebrating.

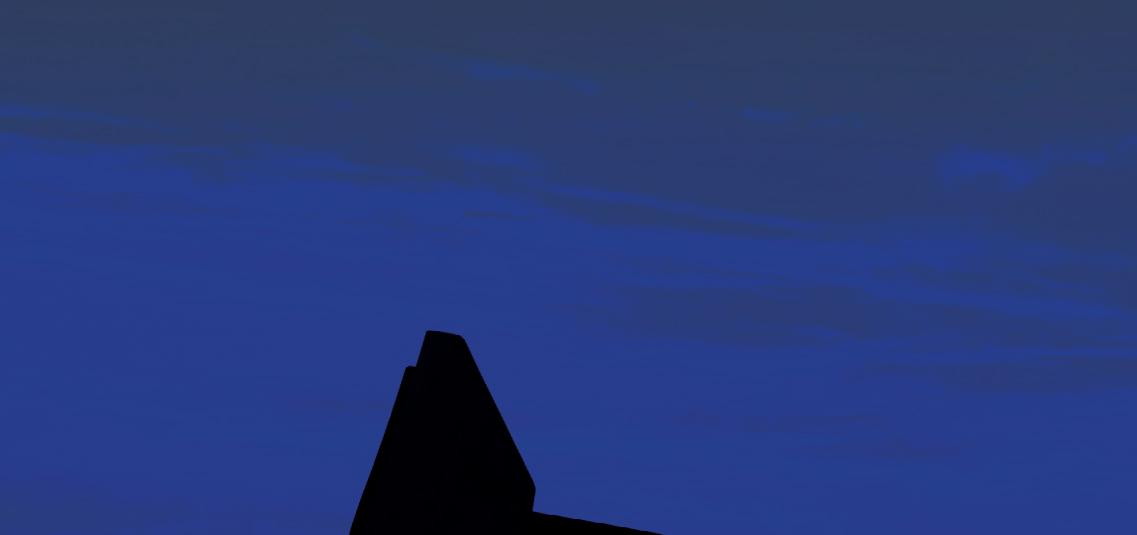
Stay informed
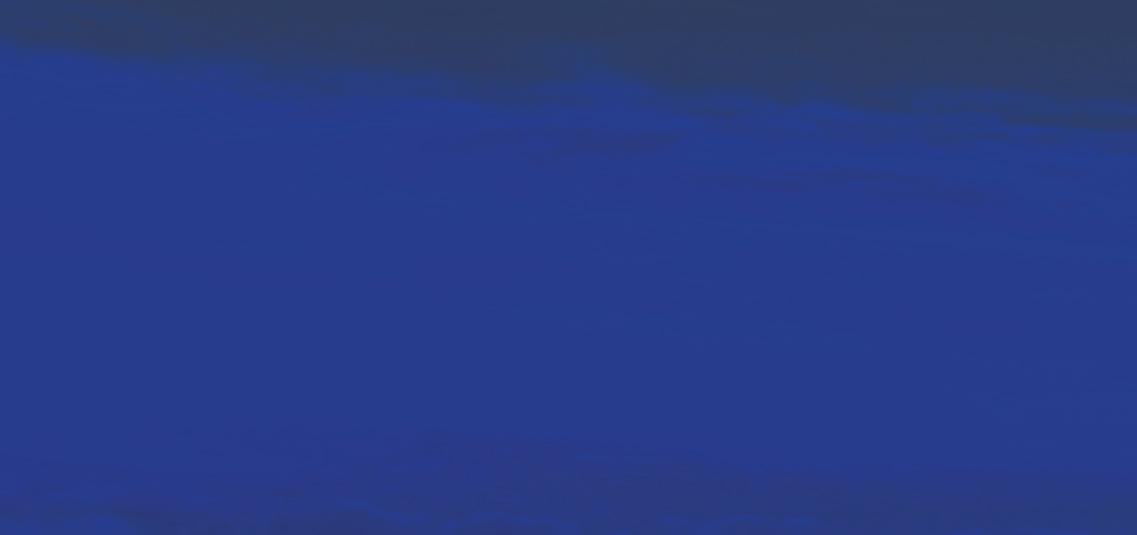
Keep up to date with us to hear the latest in upstream oil and gas news
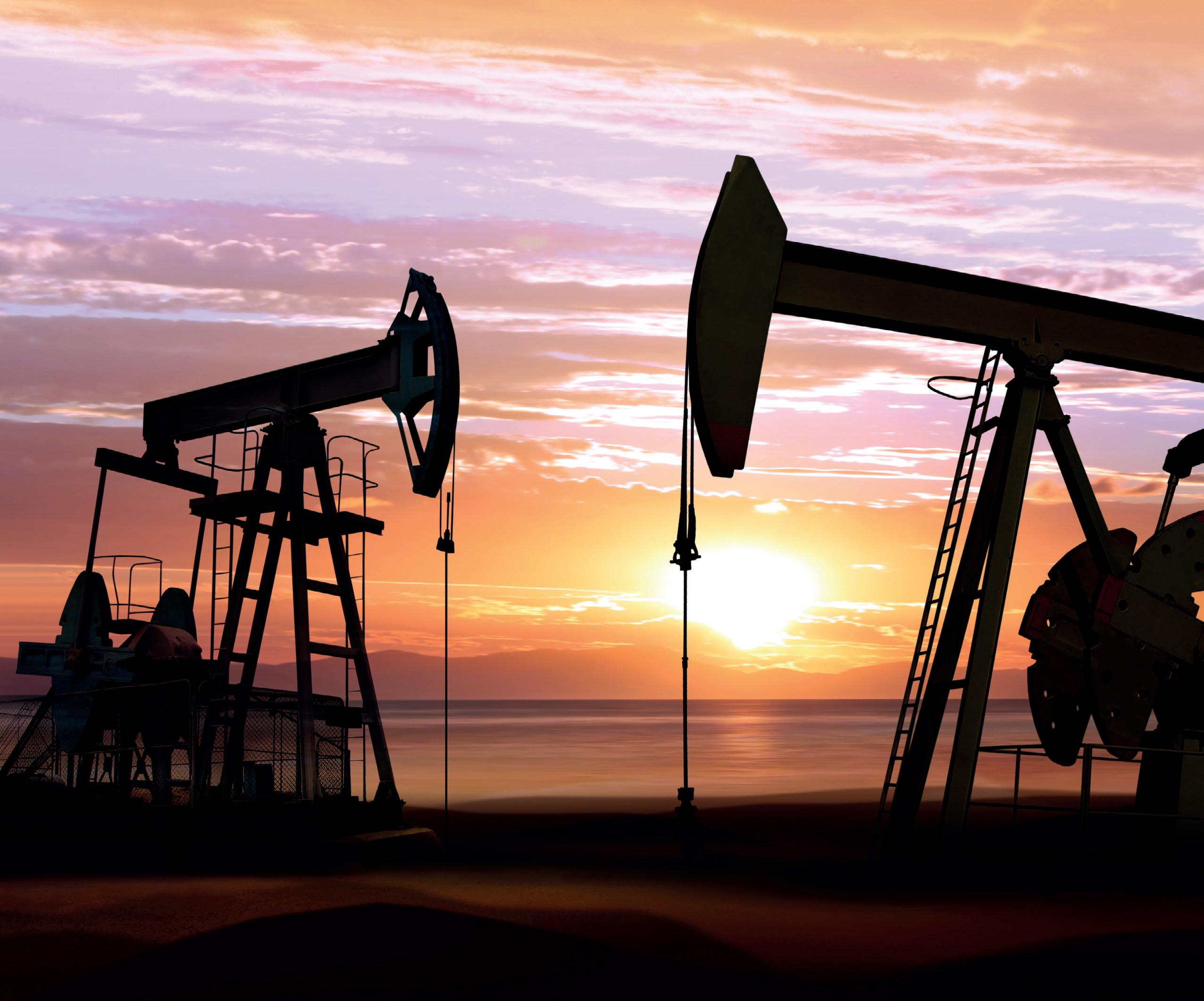
www.oilfi eldtechnology.com
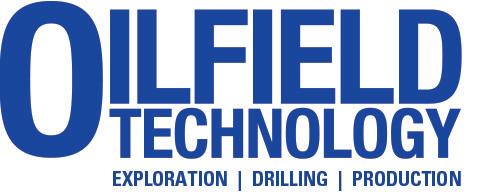