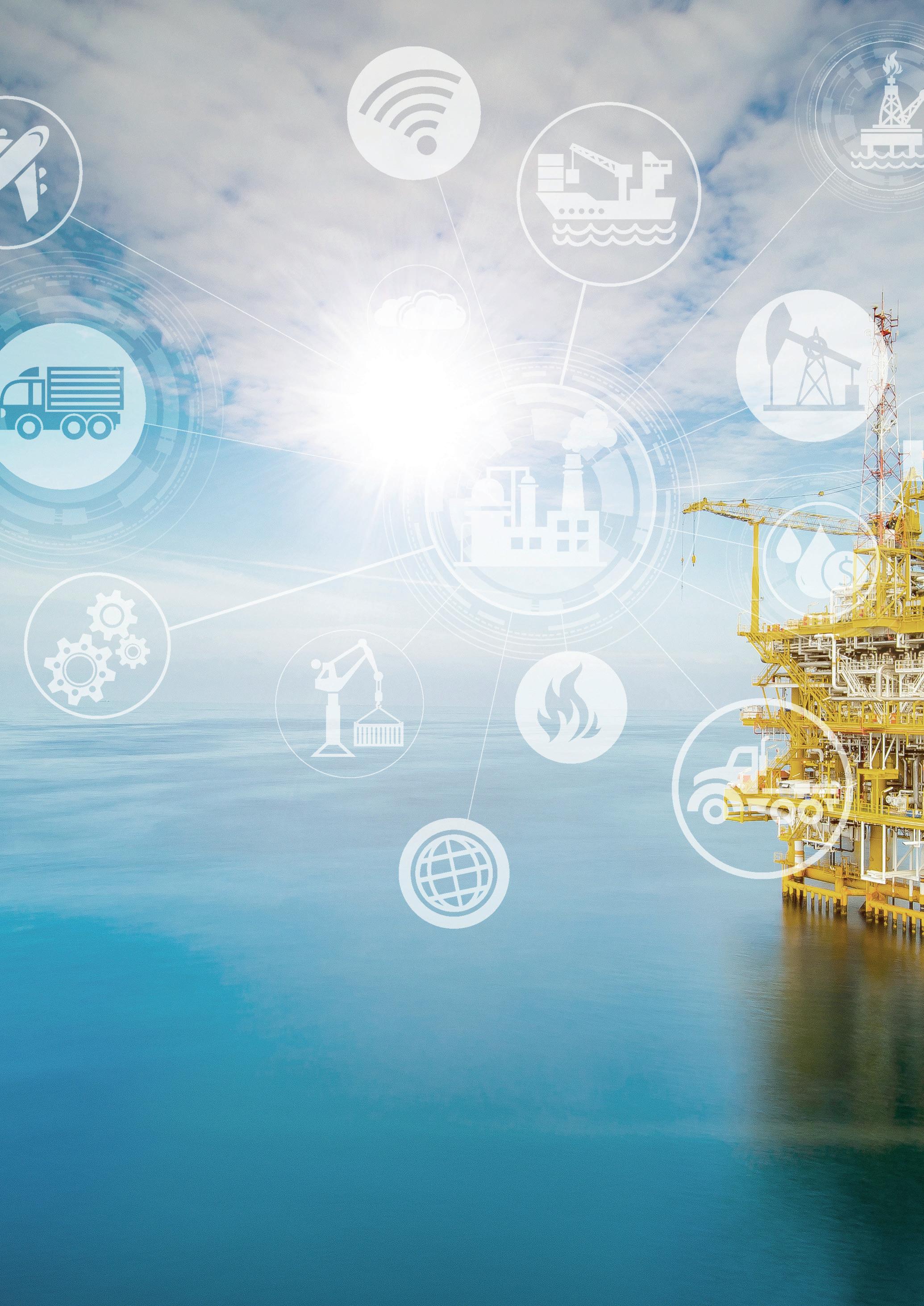
10 minute read
Addressing offshore challenges through digitalisation of operations
The oil and gas industry is known for moving through cycles, and each cycle represents a challenge for the industry. Most experts were worried about the low oil prices during the previous downturn, but no one ever expected the unprecedented outbreak of the COVID-19 pandemic, which has disrupted the balance of demand-supply to levels never seen before. Therefore, maximising production from existing infrastructure and minimising costs for well intervention and well abandonment are key objectives for operators during the current pandemic in order to accelerate the transition of the oil and gas industry to a more sustainable future. With these challenges accentuated even more in the offshore environment, the oil and gas industry has remained resilient with the support of oilfield services companies.
COVID-19 has limited the ability to travel, and many companies struggled especially during the beginning of the COVID-19 emergency to get the required specialists offshore to perform the necessary drilling and well activities. While some operators had focused on integrated operations (IO) before the pandemic, many more have been forced to conduct this type of operation during the pandemic as a contingency measure to keep operations running.
Archer Oiltools has focused on offering solutions where well integrity, reliability and time savings are of the highest importance; to meet these requirements, the company has implemented solutions into their IO to improve operational efficiencies offshore and act upon these challenges, demonstrating how safe, cost-effective operations with high efficiency and minimum staffing can create value for operators.
IO
IO are defined as the integration of people, disciplines, organisations, work processes, information and communication technology to help operators make smarter decisions in real time. Together with oil and gas operators, digital enablers and cutting-edge technology, IO have allowed platform and rig operations to be integrated into a collaborative environment where offshore skills can be augmented with onshore expertise to enhance execution, deliver more complex solutions whilst reducing the rig-based people on board (POB) and reduce risk exposure for employees.
The company has executed IO in the North Sea region for the past decade. Currently, more than half of the temporary and permanent
Andreas Fliss, Elisabeth Norheim and Fernando Zapata-Bermudez,
Archer, Norway, discuss how the COVID-19 pandemic and CO2 emissions have created offshore challenges that are being overcome by technology.
suspension plug operations it has carried out are performed with the IO model. Since the first implementation of IO, the company has conducted more than 1900 remote operations through its IO centres, reducing the POB with the equivalent of 2850 people offshore. That translates into net savings of 92 910 t of CO2 emissions – the same quantity of CO2 emitted by driving a diesel car for 557 million km, according to the industry energy management calculator. Having fewer personnel who are required to travel offshore does not just mean a reduction in helicopter flights from the shore to the offshore location but also a reduction in travel for the personnel from their home location to the onshore location, which is often a long trip crossing perhaps several countries or even continents.
While Archer started with suspension plugs, the company has also recently expanded to other products, such as cementing solutions. Successful IO have been delivered in Azerbaijan, the US Gulf of Mexico, Guyana, Brazil, Malaysia, Australia, Russia and Canada.
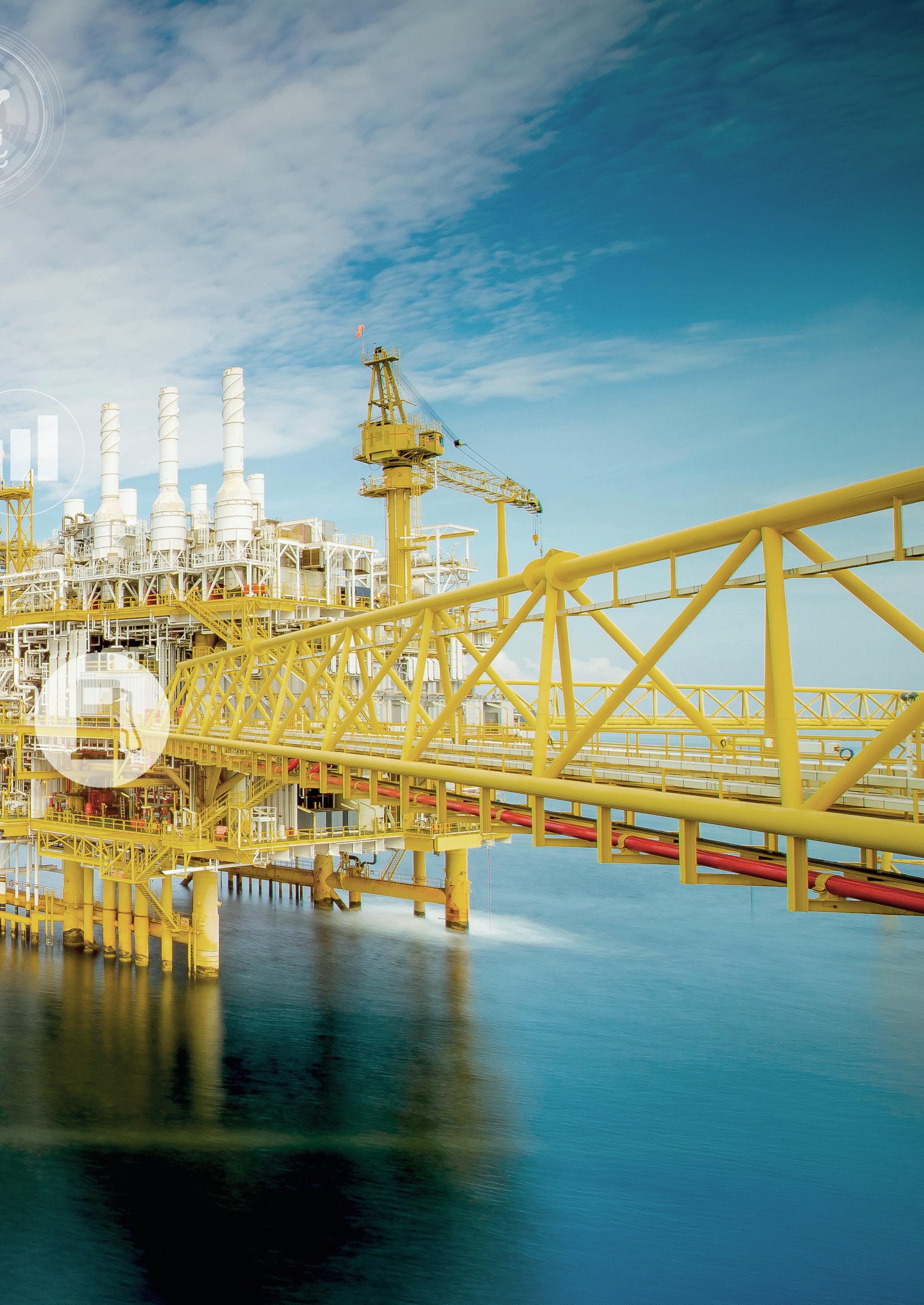
IO value proposition
Archer has demonstrated the integration of their operations through tangible examples from the North Sea, Qatar, Guyana and Canada, where restrictions on field personnel going offshore due to COVID-19 resulted in remote operations taking place. This has reduced the cost of POB, helicopter flights or additional transport costs and lessened risk exposure for personnel, but most importantly enabled the continuation of operations offshore. Due to the implementation of multiskilling programmes across all their operating divisions, reduced field crews are capable of performing multiple operations that follow the standard operating procedures implemented by the company; these include digital workflows, check lists and a competency assurance process which, supported by IO centres located in two different time zones, are ensuring safe and high-quality operations 24/7.
The IO centres receive real-time data from the rig or platform operations using a sophisticated IT enablement digital workflow, with a secure and redundant connectivity to the offshore installation (data latency usually less than 2 seconds) and onshore application software. In addition, the fully operational IO centres provide a real-time enhanced work execution environment for full remote operations (onshore specialist and offshore rig crew) or in a hybrid IO operation (onshore and offshore specialist) for more complex operations.
It is critical that the design of new technologies and equipment is done so as to allow the implementation of more complex IO that are also more sustainable and in harmony with the aims of the energy transition: for example, designing new technologies and implementing solutions that reduce the number of metres with tripping of drill pipe and time spent on P&A operations. When combining these technologies with IO, it becomes the ideal way to operate with less CO2 emissions offshore.
IO reducing the CO2 footprint from operations
For IO to support a reduction in CO2 footprint, it is critical that the entire organisation focuses on supporting and further developing a low carbon agenda whereby the industry is committed to contributing significantly to the ongoing energy transition process. Through continuous development of new technologies and solutions that reduce energy consumption from fossil fuels and with enhanced operating models such as IO, Archer is making an impact on the delivery of low carbon operations. With a broad portfolio of products and services within slot recovery and P&A, the company is in a position to deliver lower carbon solutions to the operators. This is being accomplished through more efficient operations and developing cross synergies between business units, as well as employing complementary service providers that are aligned to the same net zero goals. With this operating model the number of POB in offshore installations is being lowered, reducing rig hours and eliminating multiple trips to the well. This practice directly reduces emissions, reduces carbon footprint and improves industry sustainability in comparison to traditional methods. In brownfield developments, the company is committed to the net zero goals of greenhouse gas (GHG) reductions by supporting the industry with a wide range of technologies that drive short-term operational efficiencies and optimise operational times to generate a much lower volume of emissions into the environment.
The next level of IO
The company’s digital solutions, which today are being used to support the IO model, are moving into the next level of digitalisation by using virtual reality (VR) for more efficient and advanced learning processes in simulated offshore environments. Unlike traditional training methods, VR immerses the learner in the contextual scenarios offshore to help them acquire the experiences needed to respond successfully in a real-world scenario. On the other hand, the use of mixed reality (MR) – where employees are immersed in scenarios that combine physical and virtual environments – is moving offshore operations to the next level through solving more complex tasks and allowing experts to reach offshore operations anywhere and anytime. The MR in the company’s Stavanger and Houston operations delivers an augmented reality experience during offshore remote inspections, equipment verification/troubleshooting and incident management. It is becoming a technical differentiation as the technology addresses the current challenges of cost efficiency and energy transition models. The company is building digital assemblies and maintenance instructions that can be run on MR, can identify the equipment, components and parts, and display 3D models to facilitate all types of maintenance work. Engineering teams in charge of new technologies are launching them with digital 3D operating and maintenance manuals to align with the company’s vision on digital transformation initiatives.
Case study 1: Caspian Sea
Challenge
A major international operator requested the company install two V0-rated barrier plugs in one run to optimise the efficiency of the operation and save rig time. Due to COVID-19 the operator challenged Archer to provide a solution to overcome personnel and travel restrictions, without compromising service quality.

Figure 1. The next level of IO.
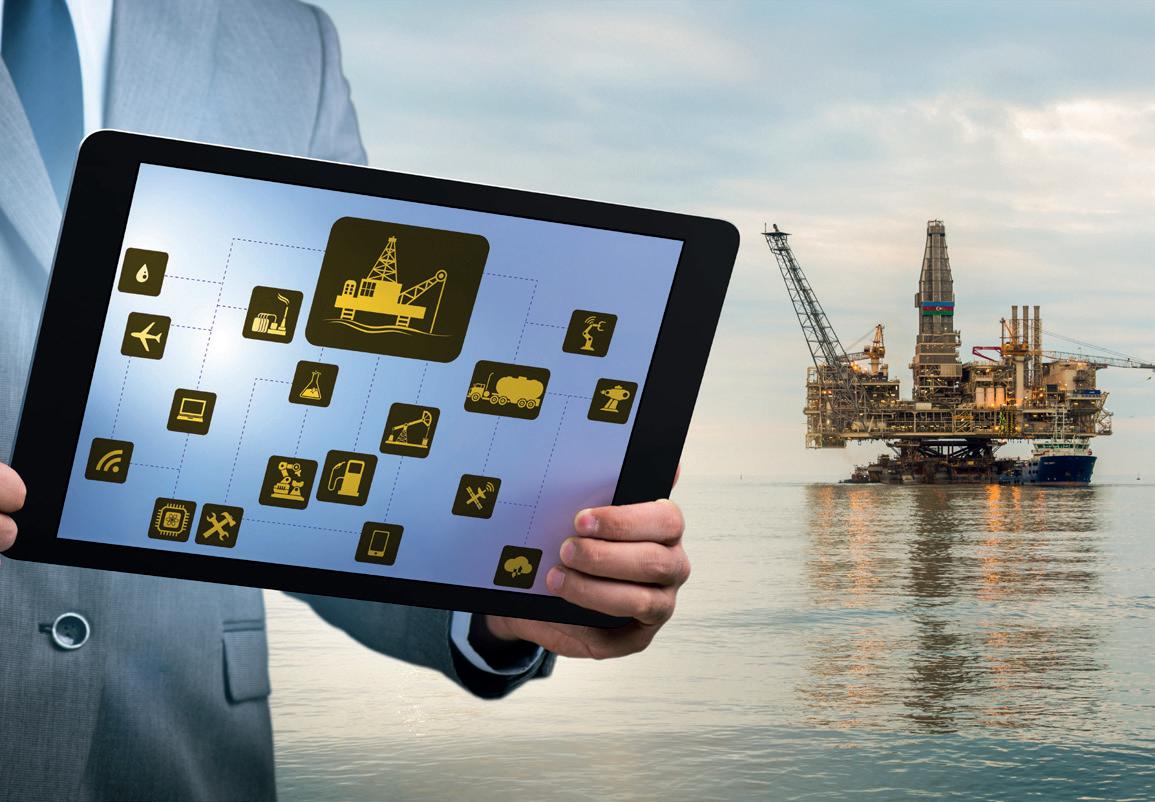
Figure 2. The future is digital in the oil and gas industry. Solution
Archer proposed using the VAULT® dual plug system to set and retrieve two plugs in a single run. Selected for the operation were a 10 in. TIMELOCK® as the deep set and a 9 5/8 in. VAULT as the shallow set plug. In order to meet the barrier suspension criteria, both plugs were pressure-tested. In addition, to overcome travel restrictions on personnel, an IO centre was set up in collaboration with the operator’s remote support centre to receive real-time data from the rig during the operation and communicate directly with the rig team.
Result
A real-time communication link was established between the operating rig and Archer’s remote support centre in Aberdeen. All pre-job checks were completed according to best practice and the VAULT dual plug system was deployed and run to the planned setting target depth. The actual setting operation was closely monitored and supervised from the IO centre. The entire operation was conducted without any issues.
Challenge
A major international operator challenged Archer to provide a solution to overcome personnel and travel restrictions during the COVID-19 pandemic, while delivering a high level of service in the Gulf of Mexico.
Solution
Archer implemented a remote control centre to follow all operational steps in real time and support its operations 24/7.
Result
Using IO in Houston, Archer established communications with the rig. The operator performed offshore checks as per Archer’s guidelines and proceeded to run in hole with the TIMELOCKTM assembly. Upon arriving on the setting depth of 9550 ft, the IO support team was able to oversee and provide real-time support of setting and testing the assembly, resulting in a successful temporary abandonment of the well.
As a result, the customer overcame issues related to: Ì POB. Ì Transport (helicopter flights). Ì Health and safety (HSE) risks. Ì Environmental footprint.
All of the above were achieved without compromising delivery standards.
Case study 3: offshore Eastern Canada
Challenge
Operating in Eastern Canada involves facing harsh weather conditions, including the risk of icebergs and severe storms during the Atlantic hurricane season. A major operator in the Flemish Pass area required temporary well suspension at short notice due to a fast-approaching storm system. In addition, COVID-19 presented a challenge to mobilising personnel.
Solution
Archer’s STORMLOCK®, which delivers V0 gas tight isolation while allowing the option to set without the need of hang off weight or, when needed, the capacity off suspending up to 660k-lbs below, was selected. The V0-rated 13 5/8 in. STORMLOCK was mobilised and prepared to run and set without company personnel on the rig. The operation was planned to be achieved with the assistance of the IO team in Houston monitoring the operation in real time.
Result
The STORMLOCK was run, set, tested and retrieved successfully according to plan, demonstrating its capability by providing the customer with V0 protection in a harsh environment. The operation was delivered efficiently without POB, proving IO capabilities for the first time offshore Eastern Canada.
Conclusion and summary
IO are a proven way to help the oil and gas industry in its transition to a more sustainable future by reducing the number of people required to travel offshore and be subsequently exposed to the offshore environment. This in turn contributes to a significant reduction of CO2 footprint by limiting travel between home locations and offshore locations. Archer has contributed in the last few years with CO2 emission savings of nearly 100 000 t. Looking forwards, the stage is set to enhance further IO processes so that they are able to cover more complex activities and the majority of all operations.
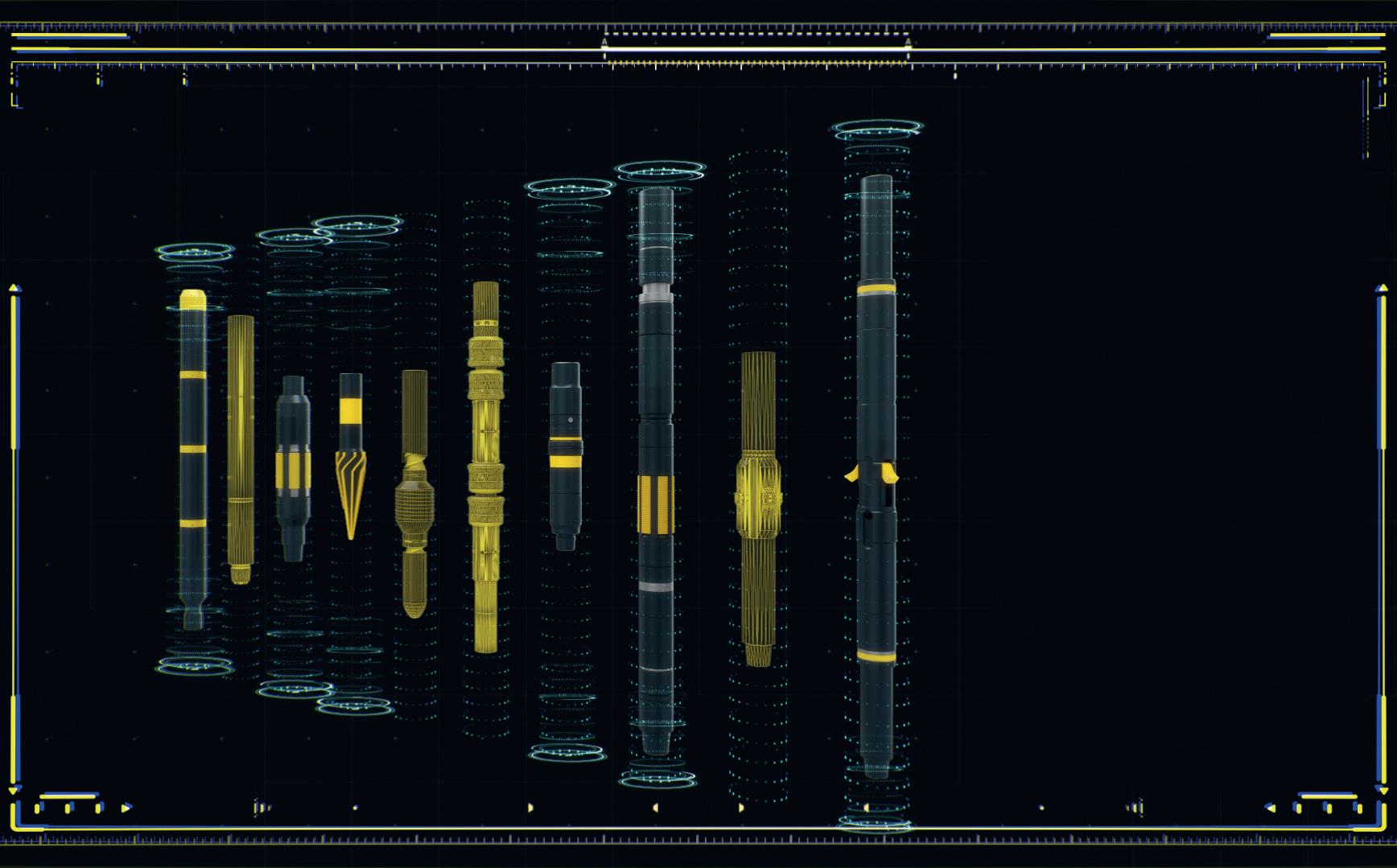
Figure 3. Customised solutions for every well.