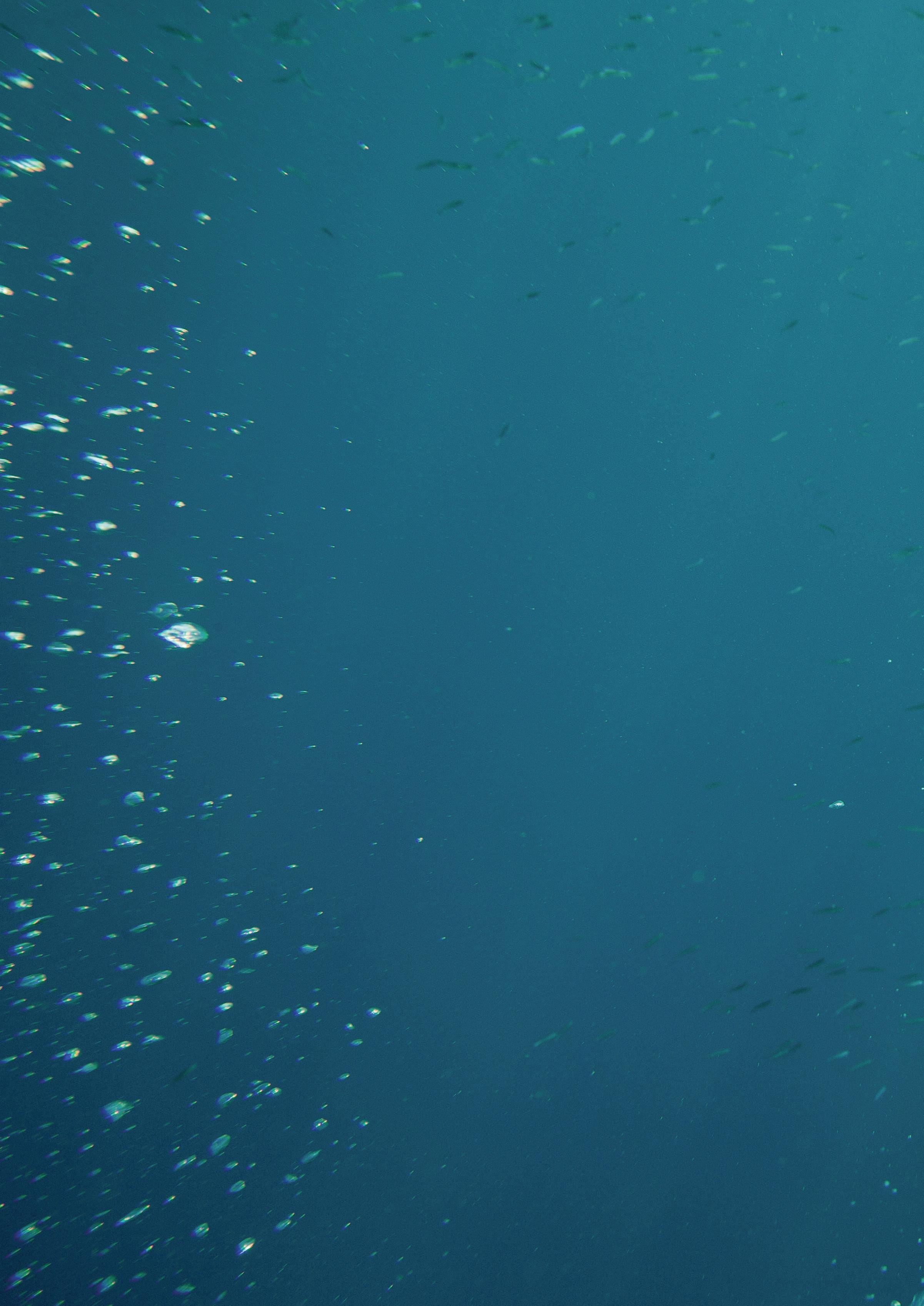
6 minute read
New heights below sea level
Alexandre de Rougemont, MAN Energy Solutions, Switzerland,
shows how new subsea compression systems are facilitating more sustainable and efficient production from deepwater gas fields.
Subsea compression is helping oil and gas operators reduce energy use, increase efficiency and become more sustainable. The shift away from topside solutions reduces safety risks as well as the OPEX and CAPEX needed for the traditional manned production platforms. As a provider of compression technology solutions, MAN Energy Solutions is working on future subsea projects, safe in the knowledge that the world’s first subsea compressor system, at Equinor’s Åsgard gas field, has run for over 100 000 operating hours. 300 m beneath the surface of the North Sea, approximately 175 km west of Karmøy in Norway, the company’s subsea compression system is pushing gas and condensate from a wellhead to a semi-submersible processing platform some 40 km away. Operated by Equinor (formerly Statoil), the Åsgard project marked the world’s first deployment of a modular subsea compression technology, which emerged from a collaboration between MAN Energy Solutions and system solution provider Aker Solutions.
Having now achieved well over 100 000 hours of cumulative operation and design performance figures of 99% availability after 6 years, the two subsea compressor systems support production at a significantly lower carbon footprint than a comparable topside installation. The beneficial characteristics of operating close to the wellhead mean the subsea compression
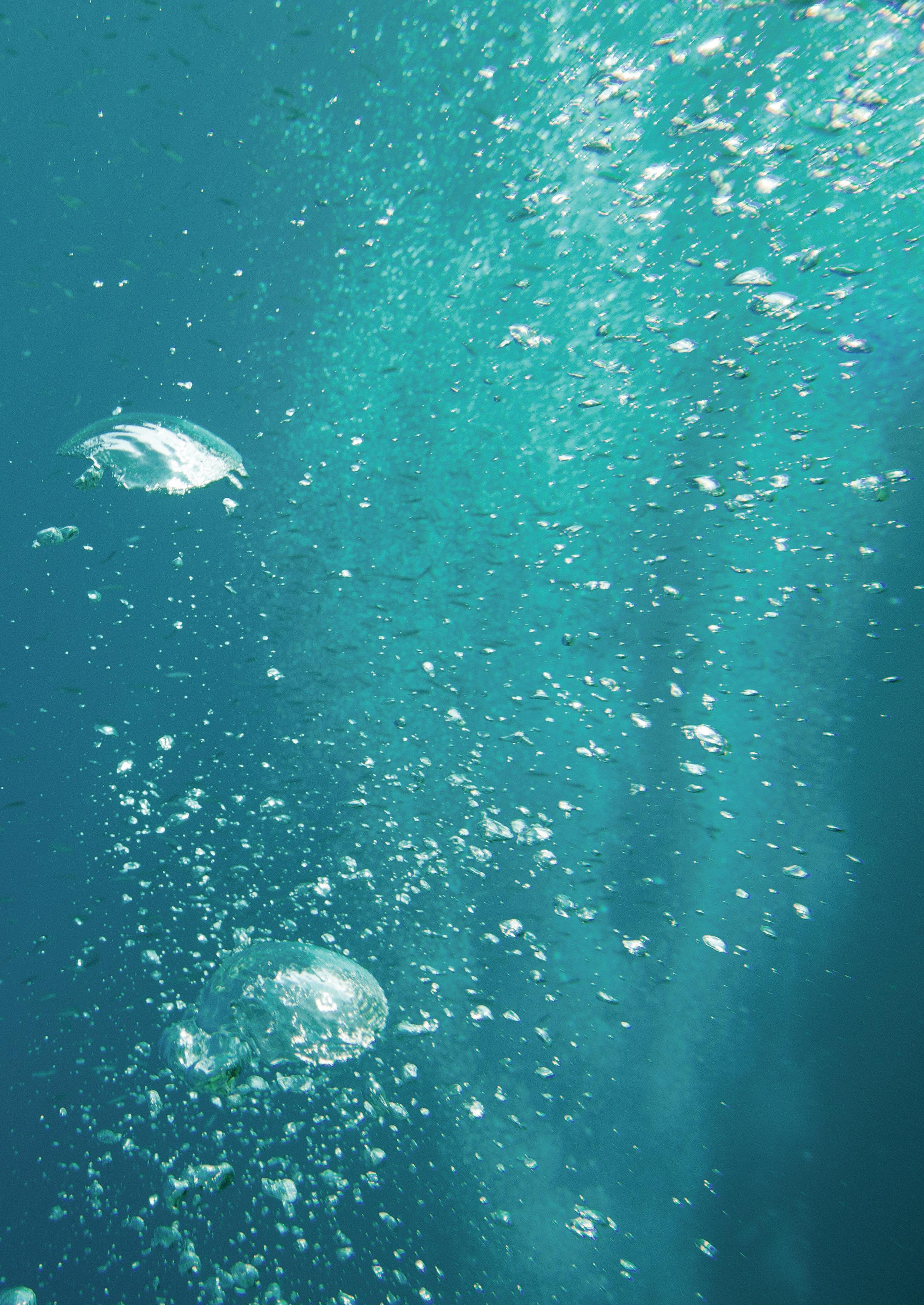
solution is extending the reservoirs’ productive life by another 15 years. This is adding around 306 million boe to the recoverable reserves.
In 2021, Equinor awarded MAN Energy Solutions a new contract to supply an additional subsea compressor unit, which will be deployed at the actively producing field in order to extend its lifetime. The existing compression modules at Åsgard are being upgraded to accommodate a higher compression ratio and thus maintain output and enhance recovery as the pressure in the gas reservoir naturally declines.
The benefits of shifting subsea
Shifting compression technology closer to the wellhead yields significant sustainability benefits through big gains in efficiency. The reductions in power consumption directly result in lower CO2 emissions. Compared with a conventional topside platform, subsea compression installations can achieve emission savings of approximately 60%. The size and weight of the subsea solution is significantly smaller than a platform infrastructure, thereby reducing the requirement for materials such as steel.
In addition, improved production characteristics support enhanced performance and better economics, even at potentially marginal wells. Not only do these conditions equate to higher production and enhanced hydrocarbon recovery, but they also enable significant life extension.
With no maintenance requirements and being completely unmanned, subsea technology also eliminates a wide range of potential costs and safety concerns while coinciding with the growing trend towards de-manning of platforms and shifting control and operations to far lower cost onshore facilities. However, the benefits of using subsea equipment can only be realised through extremely robust engineering and high reliability, as well as key requirements like remote operability.
At the heart of subsea compression
The core technology behind subsea compression is the high-speed compressor that was initially developed 30 years ago by MAN Energy Solutions. In use by the gas transport and storage industries for decades, HOFIM® (High-Speed Oil-Free Integrated Motor-Compressor) machines have been developed and improved to extend their capabilities across a wide range of scenarios. In the oil and gas sector, these include deployment in numerous upstream production applications as well as in subsea environments.
Hermetically sealed and oil-free, the system uses seven axes active magnetic bearings and a high-speed motor. This design means a large number of components – including the gearbox, lubrication oil system, instrumentation and valving – are not required, unlike conventional compressor trains. This improves reliability while simultaneously minimising maintenance.
The core HOFIM compressor unit is integrated into the subsea module architecture with just a few interfaces and therefore can be easily recovered if required. The single casing also reduces complexity while the footprint of the compressor system shrinks by 60%. At the same time, the weight of the compressor is reduced by around a third when compared with conventional designs. Featuring a variable frequency drive, this design offers a number of efficiency advantages during part-load operations. The low starting current also benefits those operators concerned with creating grid disturbances

Figure 1. Subsea HOFIM motor-compressor unit for Equinor’s Åsgard gas field.
when starting under a heavy load. While the Åsgard compression module features two 220 bar compressor trains, a range of capacities is available, with a power range of 3 to 18 MWe and discharge pressures of up to 303 bar (4395 psi).
Strong reliability and performance characteristics were also behind the selection of a single HOFIM unit as the export compressor at the Ivar Aasen topside platform. Pushing gas from Ivar Aasen to the Edvard Grieg platform for further processing and onward export, the compression system is the sole production asset. Clearly, any zero-redundancy strategy will have a significant impact on CAPEX. Furthermore, although the Ivar Aasen platform was designed as a manned installation, controls for the platform are now moving onshore as part of a de-manning policy by the operators. The remote operability of the HOFIM technology is a key enabler of this.
Expanding the boundaries of subsea operations
This shift to subsea technology ties in with the trend towards exploration and production in more challenging waters well over 1000 m below the surface, where the benefits of subsea operations potentially become even more substantial.
In 2021, the company was commissioned to supply five subsea compression units for the Jansz-Io Compression (J-IC) project, located around 200 km off the north-western coast of Western Australia at water depths of approximately 1400 m. Three subsea HOFIM compressor systems will be installed into the subsea modules at the Chevron-operated field, while two more will serve as spare units. The subsea compression stations will boost gas recovery and form a key part of the installation to supply gas to the 15.6 million tpy LNG processing units of the Gorgon project on Barrow Island. Gorgon is one of the world’s largest natural gas developments projects.
The Jansz-Io project marks an important milestone for subsea compression technology, and is the direct result of the technological developments achieved by Subsea Alliance partners Aker Solutions and MAN Energy Solutions.
Next-generation subsea compression
With the latest generation of subsea equipment becoming more standardised, simpler and smaller, HOFIM systems are also being optimised. Current designs feature a further 50% reduction in size and weight and, by reducing the number of modules needed, around 8000 t of CO2 is removed from the construction and installation phases.
Standardised and simpler designs are indicative of lower CAPEX and OPEX, while the modular approach helps to deliver predictable, repeatable quality and accelerated delivery times. The modular configuration also supports operational flexibility, allowing compressor train capacity to change as a field matures and its production characteristics evolve.
In forging long-term partnerships to achieve those essential goals, MAN Energy Solutions and Aker Solutions are advancing next-generation subsea systems. Over time, these subsea compression solutions are becoming smaller, lighter and more cost-effective with improved performance and profitability. Pioneered in Europe, this technology is now forging a path to more sustainable and efficient production for some of the deepest gas fields worldwide.
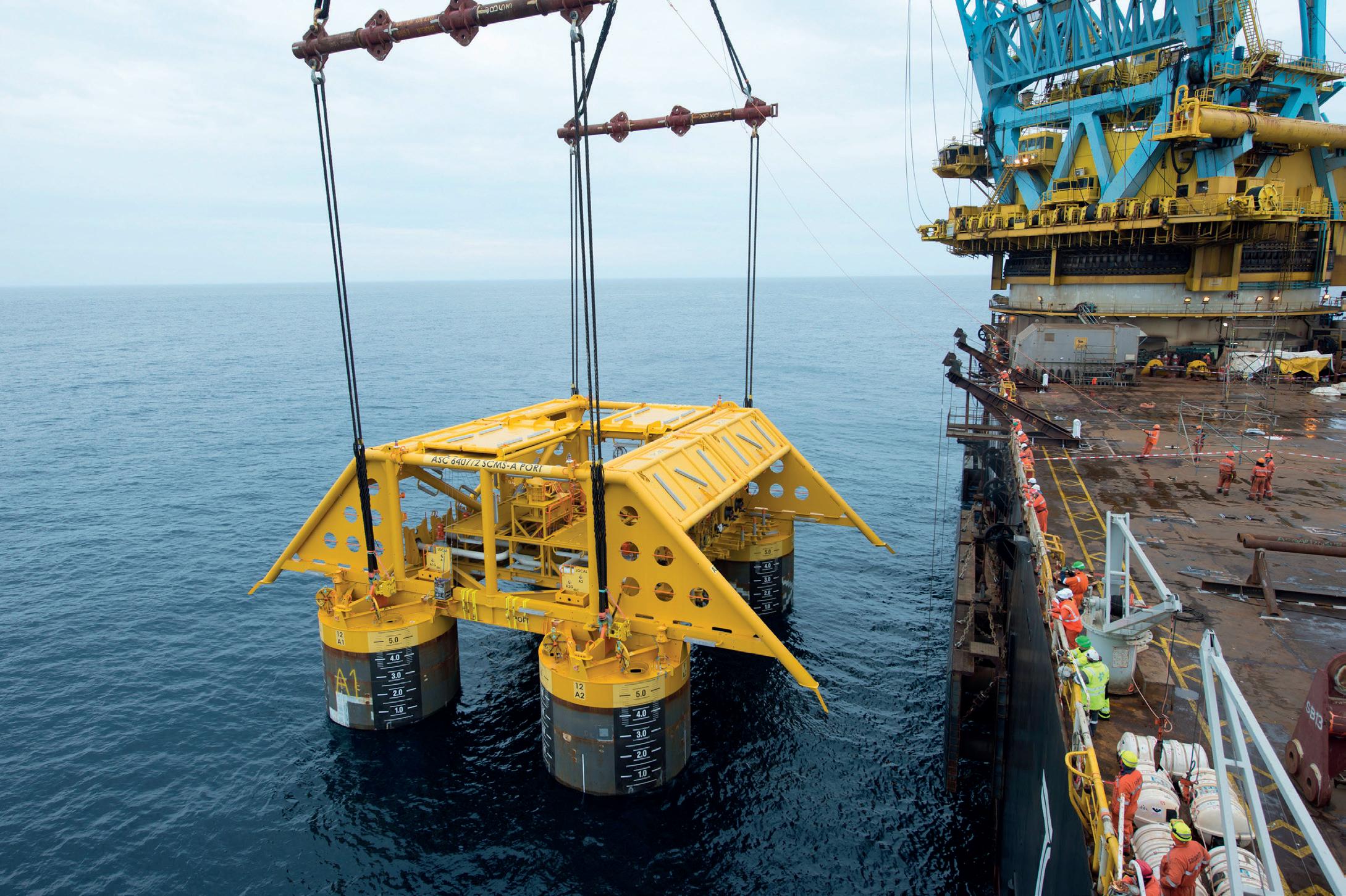
Figure 2. The installation of the world’s first subsea gas compression module at Equinor’s Åsgard gas field. Courtesy of Equinor.