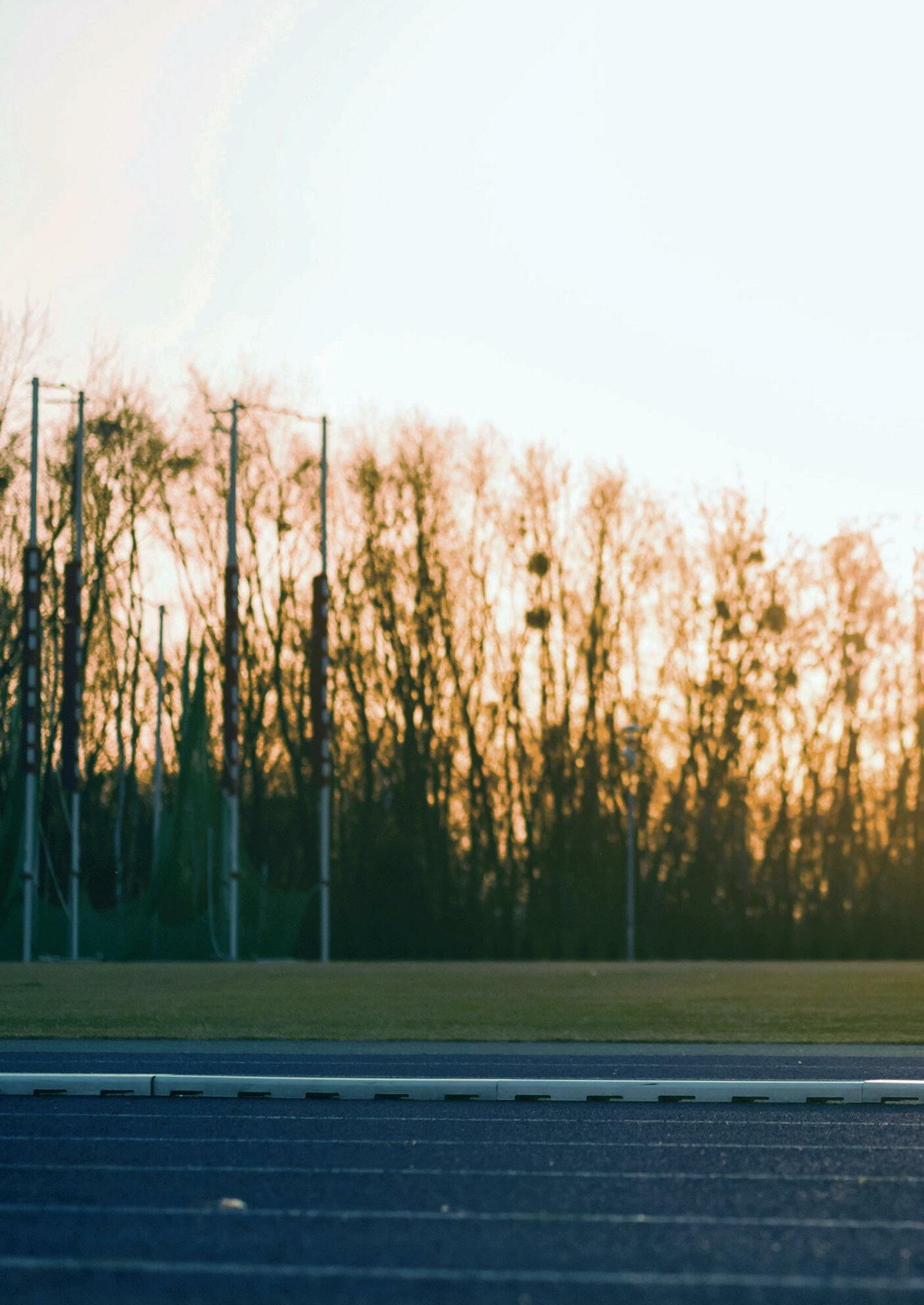
9 minute read
Over the hurdle
Jonathan Rogers, Martin Shumway and Dr Amir Mahmoudkhani, Locus Bio-Energy Solutions, USA,
review the progress that naturally sourced biosurfactants have made in maximising oil recovery in shale wells – for greater profits and a smaller carbon footprint.
Global demand for energy is expected to keep growing – and oil and gas will remain a vital part of the energy mix for decades to come. Even the most conservative clean energy transition scenarios predict that US oil and gas liquids production will need to increase from the 12.24 million bpd average produced in 2019 to 13.3 million bpd by 2030.1,2
Production from shale wells typically declines by 50%+ in the first year. As a result, meeting increased demand requires E&P companies to increase production in cost-effective and sustainable ways to both compensate for these steep decline rates and produce additional crude to meet requirements. Adding to the challenge, producers must address evolving ESG requirements and transition to net zero energy production, even as falling operating costs make it cheaper to produce new barrels of oil. According to Rystad Energy, the average breakeven price for tight oil
was US$37/bbl at the end of 2021, down from US$47/bbl just 3 years prior.3
To boost declining production rates and meet growing domestic energy demand, US operators have traditionally employed conventional enhanced oil recovery (EOR) techniques, such as water flooding, chemical flooding, thermal techniques and gas injection. EOR has a proven history of maximising oil recovery in conventional oil wells, which are drilled into sandstone and carbonate reservoirs with pore sizes ranging from 1 to 100 μm on average. But these same techniques are not as effective or economically viable in many shale reservoirs with pore throat radii in the range of 1 to 200 nanometres (nm). For size comparison 1 μm equals 1000 nm, with human DNA measuring just 2 nm in diameter. 1 nm is equal to 1 millionth of a millimetre.

Class Family
With pressure mounting to extract more production from existing assets and deliver new wells in a more cash-constrained environment, new technologies are required to profitably boost production and meet more stringent ESG criteria.
Glycolipids
Lipopeptides
Phospholipids
Polymeric biosurfactants � � � � Sophorolipids Rhamnolipids Trehalolipids Mannosylerythritol (MEL-A, MEL-B)
� � � � � Surfactin Iturin Fengycin Lichenysin Bacillomycin
�Diphosphatidylglycerol
� � � � Emulsan Liposan Mannoprotein Poly-saccharide protein complexes
Biosurfactants – an innovative alternative technology
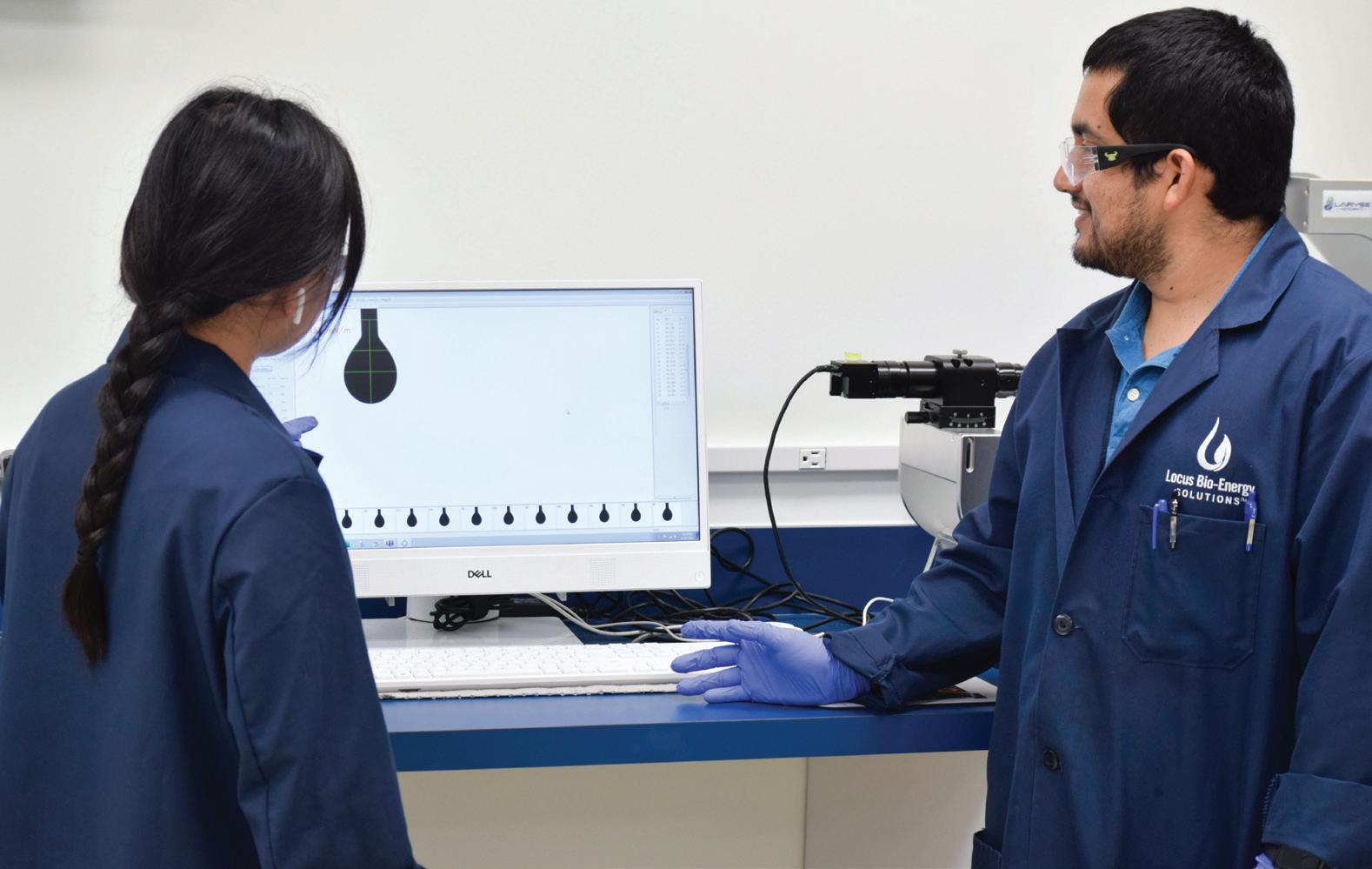
Surfactants synthesised from petroleum feedstocks have been used for decades in a range of oilfield treatment chemicals. In chemical flooding EOR operations, surfactants aid oil recovery by altering the wettability of the formation rock and reducing surface and interfacial tensions – which helps mobilise oil by reducing the drag between oil and the reservoir rock. However, because these surfactants tend to have high usage costs and carbon footprints, the industry has been actively searching for more cost-effective and environmentally sustainable alternatives. Naturally produced, sustainable biosurfactants are a novel technology showing promise in shale EOR and hydraulic fracturing operations. These biosurfactants are amphiphilic molecules produced by living microorganisms and use sustainable raw materials – carbohydrates and natural oils in particular – as carbon sources. Because they are 100% natural, biosurfactants degrade into byproducts that do not negatively impact the environment. Biosurfactants come in a diverse array of chemical structures. Glycolipids are the largest and most diverse class of biosurfactant studied to date, thanks in large part to their higher fermentation yields and application versatility Figure 1. Representative structures of a highly complex biosurfactant (right) with many chemically active sites (Table 1). Significant work has been and a traditional surfactant (left), which contains few active sites linked to a long carbon-chain tail. conducted on these glycolipids, with recent advancements focused on use of sophorolipids in oilfield applications. Biosurfactants have unique structures that typically include multiple chemically active sites – a contrast to the limited number of active sites on traditional surfactants (Figure 1). In both laboratory and field studies, the complex structures of biosurfactants give rise to interfacial properties that allow them to consistently outperform traditional, hydrocarbon-based surfactants in mobilising oil in both conventional and tight/shale formations. Surface/interfacial tension (IFT) reduction is a key measure of surfactant performance. In commonly used force Figure 2. IFT measurements are used to screen and identify the best biosurfactants for well treatment. tensiometer studies, some

high-performing traditional surfactants can reduce the surface tension of water from 72 to 35 mN/m and the IFT of n-hexadecane/water from 40 to 1 mN/m. Studies done by Locus Bio-Energy Solutions have shown that biosurfactants have even greater results, reducing the surface tension of water to 25 mN/m and the IFT of water/hexadecane to < 1 mN/m.
The concentration at which surfactant molecules self-assemble into micelle structures, typically called the critical micelle concentration (CMC), is also a key performance criterion. The CMC value of most biosurfactants ranges from 1 to 200 ppm, a fraction of the CMC of many traditional surfactants. This significantly lower CMC allows biosurfactants to match the performance of many hydrocarbon-based surfactants, but at a fraction of the dosage.
In a typical study conducted by the company, the efficacy of biosurfactants in reducing the IFT of an oil-brine system was evaluated at various dosage rates as a function of time using a drop shape analysis method (Figure 2). The biosurfactants reduced IFT even at concentrations much less than the CMC, a notable property that supports production enhancement longevity. These IFT measurements are used to screen and select the best biosurfactants for specific well applications. The company’s studies have demonstrated that application of biosurfactants at a dosage of only 2 ppm is sufficient to reduce the oil/water IFT and cause oil to mobilise from reservoir rock. Conversely, many synthetic surfactants require dosages of 50 to 100 ppm to achieve the same level of IFT reduction. Further studies have shown that in addition to lower CMCs, the company’s biosurfactants form micelles that are less than 3.1 nm in diameter, significantly smaller than the micelles of their traditional surfactant counterparts. As Figure 3 illustrates, their smaller micelle size and lower dosage requirements allow biosurfactants to penetrate deeper into the smallest nanopores and mobilise oil from even the tightest shale reservoirs. This small micelle size is critical in EOR applications in unconventional tight formations where pore throats are very small. In the Permian Basin’s Wolfcamp Shale, for example, nanopores range from 3 to 18 nm. Another benefit of biosurfactants is their stability. Biosurfactants can be used at high temperatures and pH values ranging from 2 to 10. They also tolerate high salt concentrations of up to 10% (or higher), whereas 2% sodium chloride (NaCl) is enough to render some common synthetic surfactants inactive.
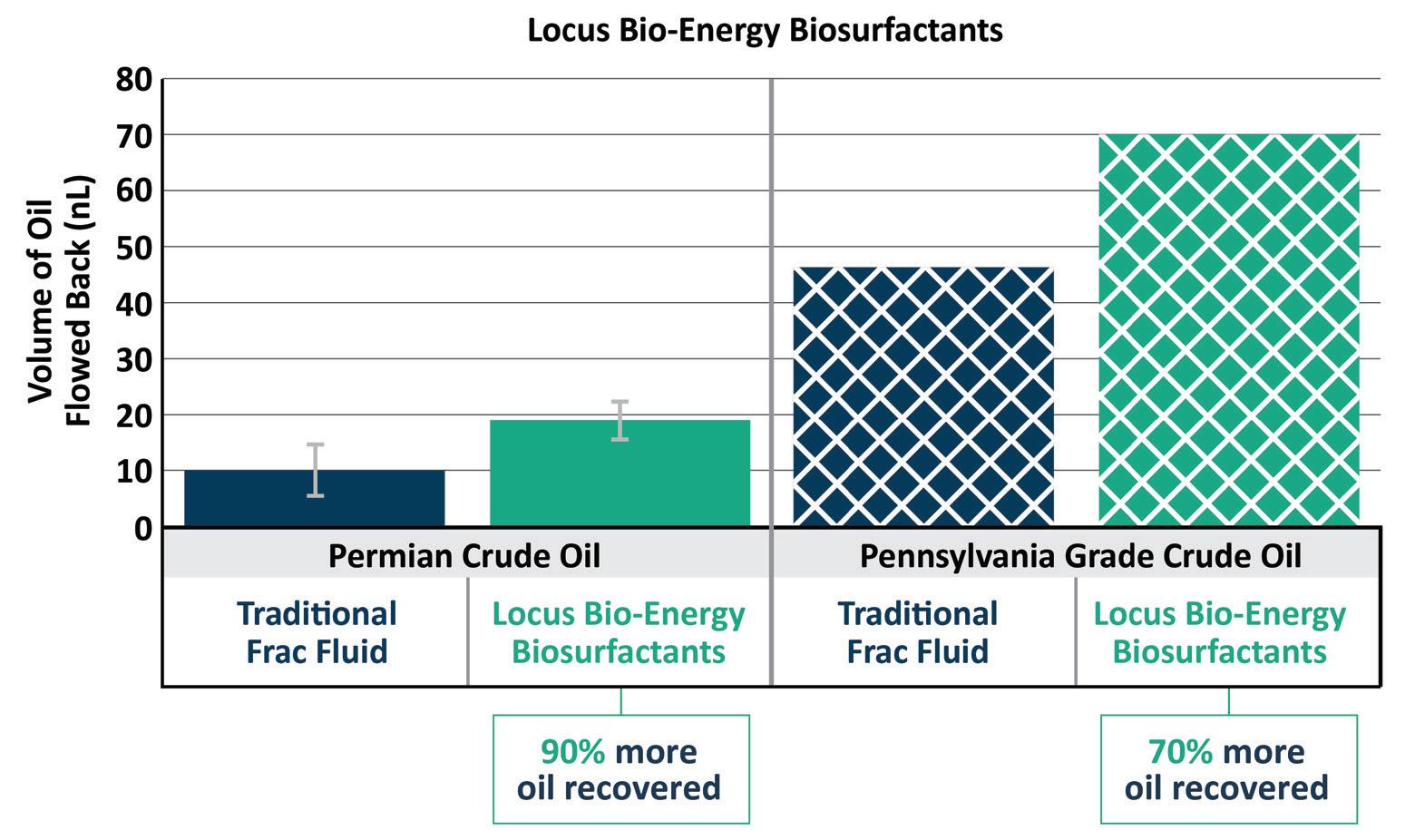
Figure 3. A comparison of micelle size versus depth of penetration in shale rock pores. With an average micelle size of less than 3.1 nm, biosurfactants can penetrate into the smallest nanopores to mobilise oil that typical frac surfactants and nanofluids cannot reach. Figure 4. Microfluidic technology provides a high-resolution simulation of reservoir fluid dynamics. This testing demonstrates that when a biosurfactant is included in the treatment fluids up to 90% more oil can be mobilised. In field applications, the results translate to a reduced need for continued refracking to meet production goals.
Ready for the oilfield
Biosurfactants have found successful application in a number of high-end medical and consumer products, including pharmaceutical drug delivery, skin care formulations and environmentally-friendly household detergents.
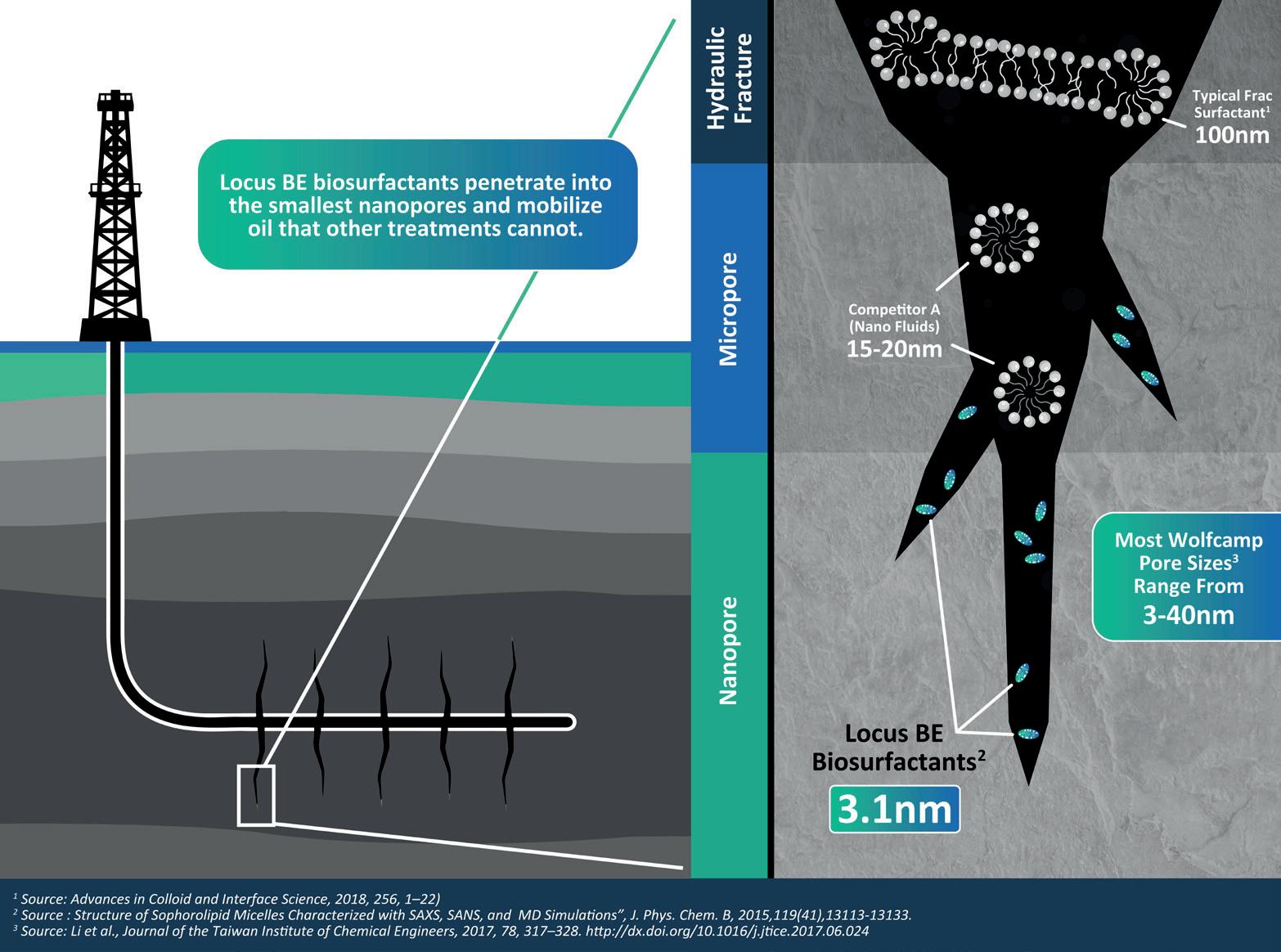
However, the application of biosurfactants in the oilfield has been slow, despite decades of research and promising results.
To be more readily adopted in the oilfield, biosurfactants had to overcome hurdles including high production costs, volume limitations, scalability problems and efficacy challenges. Recent advances in manufacturing technology, championed by Locus Bio-Energy Solutions, are now making biosurfactants commercially available at the price point and volumes required for widespread adoption in oil and gas applications. The solutions have a near-zero carbon footprint and do not contain any nutrients or living cells.
The oil mobilisation performance of these biosurfactants has been confirmed in both laboratory and field deployment. In independent laboratory testing, a microfluidic technique was utilised in which nano-sized pores were etched onto a test chip to replicate the inherent nanoconfined geometries of shale reservoir rock (Figure 4). This template was used to reproduce individual reservoir characteristics and compare the oil mobilisation potential of different chemistries. In tests using a Permian Basin crude oil and Pennsylvania Grade crude oil, the microfluidic technique confirmed that significantly more oil (70 – 90%) can be mobilised when a biosurfactant is included in the frac fluid formulation.
Boosting production in declining wells
Biosurfactants are enhancing oil recovery and removing high molecular weight deposits in reservoirs across major US basins. Analysis on the latest well stimulations carried out in the Delaware and Midland Basins has demonstrated oil production increases ranging from 50% to more than 100%, and increases in gas production ranging from 20% to more than 80%. The results yielded 1.5 to 4 times return on investment (ROI) and treatment cost payback in less than 4 months – with a minimal carbon footprint.
The significant production gains in EOR applications have operators looking at using biosurfactants to build better-designed shale wells with improved performance from the start. In a recent application in the Bakken Shale, the company’s SUSTAIN biosurfactant was used as part of a re-frac operation of a mature well. The biosurfactant’s performance, as measured by cumulative oil produced, was compared with the performance of a hydrocarbon-based surfactant used to re-frac two analogue wells (Figure 5). In the first 75 days after recompletion, the well that was re-fracked with a traditional surfactant produced 21 874 bbl of oil. The well that used a biosurfactant in the completion fluids yielded 25 413 bbl of oil, a 16% increase in production that translated to more than a quarter of a million US dollars of revenue – revenue that would not have been realised without the biosurfactant.
Ensuring higher production from the start
In new well deployments in the Permian Basin, the SUSTAIN biosurfactant helped increase oil production by over 30% in the first 30 days and reach peak oil faster compared to frac jobs with traditional surfactants. The biosurfactant boosted well production by more than 6200 bbl compared to the analogue wells, and at one-third the application rate of hydrocarbonbased surfactants. The treatment paid for itself three times over within the first month.
Conclusion
As the industry continues to embrace new technologies to meet growing global energy demand, biosurfactants are a technology innovation whose time has finally come. By boosting production rates from new and declining wells alike, biosurfactants provide cost-effective solutions to the challenges of optimising production of low-cost, low-carbon barrels and recovering more oil from the reservoir. These low-dosage, robust and ESG-friendly products are gaining recognition as a sustainable way to move the industry forwards in innovation, environmental stewardship, safety and cost.
References
1. U.S. Energy Information Administration, ‘U.S. crude oil production grew 11% in 2019, surpassing 12 million barrels per day’, https://www.eia.gov/ todayinenergy/detail.php?id=43015 (2 March 2020). 2. U.S. Energy Information Administration, ‘Annual Energy Outlook 2022’, https://www.eia.gov/outlooks/aeo/data/browser/#/?id=11-AEO2022&cases=r ef2022&sourcekey=0 3. Rystad Energy, ‘As falling costs make new oil cheaper to produce, climate policies may fail unless they target demand’, https://www.rystadenergy.com/ newsevents/news/press-releases/as-falling-costs-make-new-oil-cheaperto-produce-climate-policies-may-fail-unless-they-target-demand/ (17
November 2021).
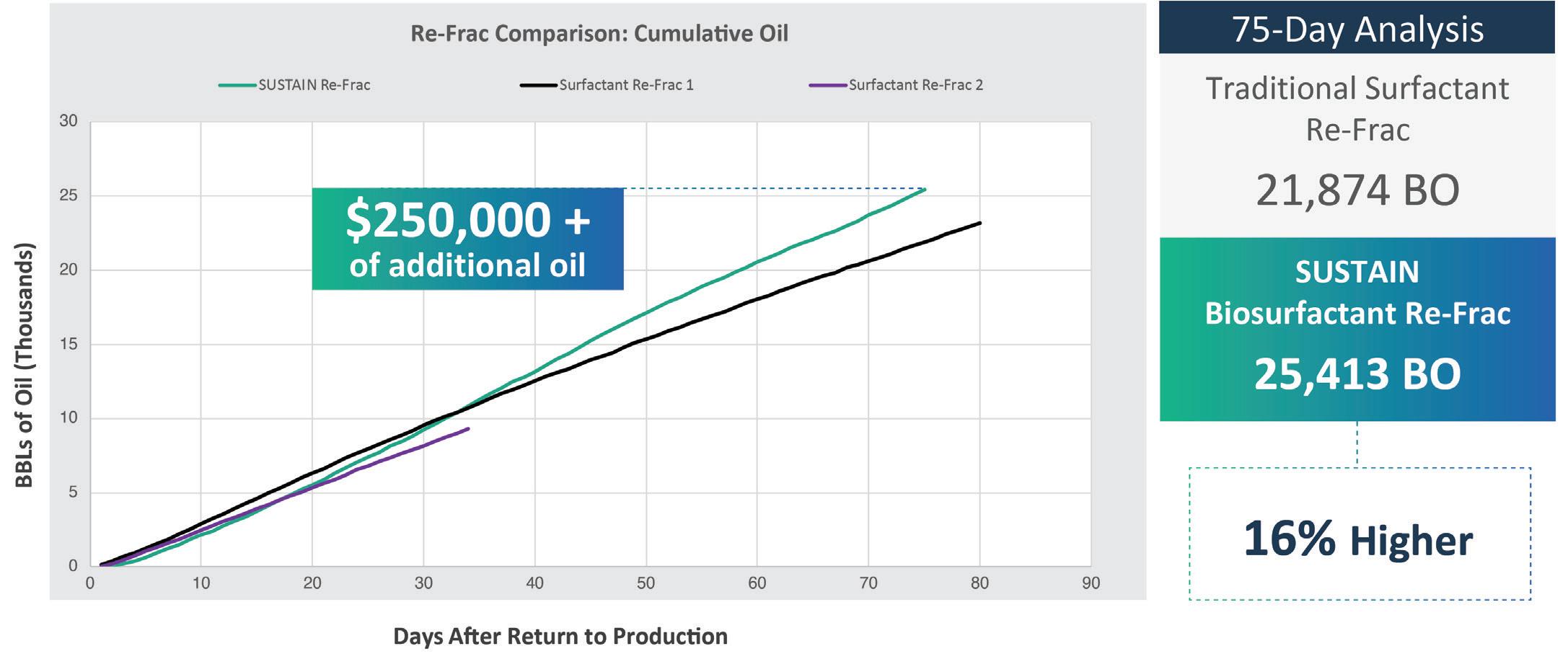
Figure 5. In a re-frac operation in the Bakken Shale, the use of the biosurfactant resulted in greater oil production and higher revenue compared to a re-frac job using a traditional surfactant.