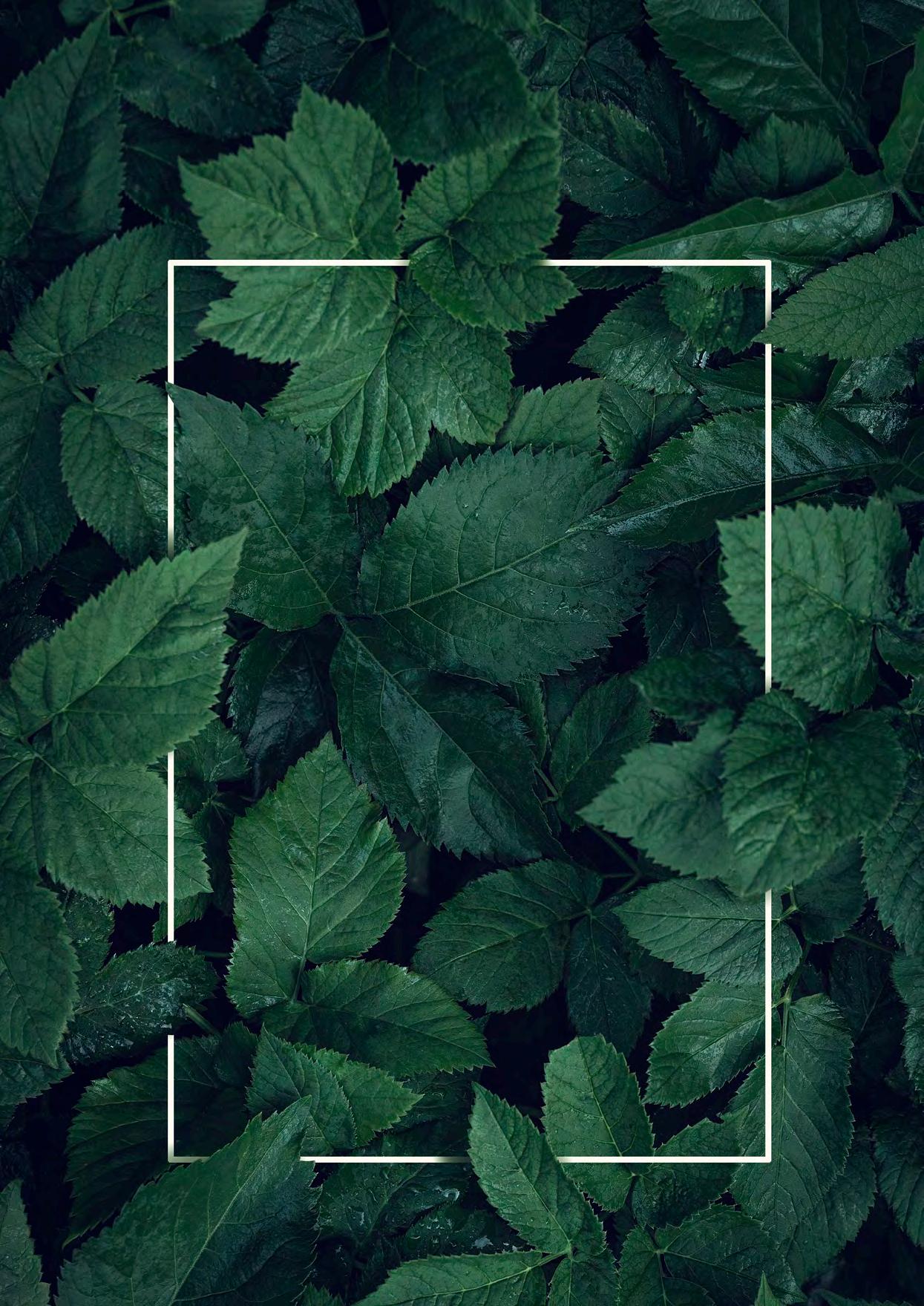
9 minute read
A Little Help From Mother Nature
Jonathan Rogers, Dr. Megan Pearl, Dr. Amir Mahmoudkhani, Tom Swanson, and Corey Petro, Locus Bio-Energy Solutions, USA, review some recent advances in biosurfactant-based saltwater disposal additives and their effects upon water disposal rates, injection pressures, and the carbon footprint of operations.
In its efforts to maximise hydrocarbon recovery from reservoirs, the oil and gas industry must contend with other fluids and solids that inevitably come along for the ride. Produced water presents a particular management challenge at the surface. By some industry estimates, 7.5 barrels of saltwater are produced for every barrel of crude oil, and 260 barrels of water are produced for every million ft3 of natural gas.1
The Permian Basin that spans Texas and New Mexico currently produces 15 million bbl of produced water each day (MMBWPD) – 10 MMBWPD from the Delaware Basin and 5 MMBWPD from the Midland Basin. The Permian’s cumulative produced water volume is expected to rise to 19 MMBWD by 2026.
Some produced water is reused for fracking. But even if operators sourced 100% of their frac water from this source, the volume would only offset 30% of the produced water extracted each day. Some 10 MMBWPD would still need to be disposed of in saltwater disposals (SWDs).
B3 Insight, a water data analysis company, estimates that to handle the anticipated increase in produced water volumes, the Permian Basin will need another 100+ new facilities in the next five years – at a cost of more than US$400 million.
The capacity of an SWD well is calculated as the BWPD injection rate based on a maximum allowable injection pressure. Many SWDs hit their maximum allowable pressures long before they hit the calculated injection volumes. As a result, ‘utilisation’ – actual injection vs calculated capacity – is far below predicted.
Why do SWD wells fall so short in their daily injectable volumes? The water typically contains dissolved salts, solids like iron and scale, paraffin, and asphaltenes, and naturally occurring radioactive materials – all of which create significant disposal challenges for the 170 000 water injection wells across the US.
The solids in produced saltwater can plate out on the reservoir surface during injection, preventing water migration into the rock and increasing back pressure.
In addition, small amounts of hydrocarbon contaminants in the
saltwater can create emulsions in the wellbore, which further reduce injectable volumes. As a result, many disposal wells are operating under predicted injection capacity during a time when increasing hydrocarbon production is feeding a demand for greater water disposal.
Drilling new injection wells is not such a straightforward solution to this disposal challenge. SWD activities are increasingly linked to localised seismic activity in certain parts of the US, prompting regulatory agencies to place new restrictions on the industry. The number of seismic events in Texas has increased dramatically in recent years. According to research from the Bureau of Economic Geology at the University of Texas in Austin, more than 200 earthquakes of magnitude (M) 3 and greater struck the state in 2021 – the majority of them in the Permian Basin. This is more than double the 98 recorded in 2020 and roughly four times the number of M3+ quakes measured in 2019.3 To alleviate seismicity issues, both New Mexico and Texas established Seismic Response Areas (SRAs) in late 2021, which forced operators to reduce saltwater injection rates in seismically active areas. As a result, over 6 million bbl of water from the SRAs must be transported to other locations for disposal.
Better SWD through chemistry
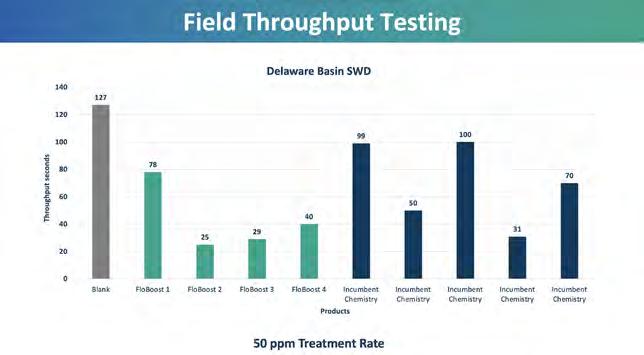
Injection well operators have turned to chemical solutions, such as acid and surfactant combinations, to help increase injectable water volumes by dissolving or mobilising organic and inorganic solids that restrict injection in the disposal reservoir. Many of these conventional solutions only provide short-lived injection improvements and must be coupled with expensive well intervention methods to boost injectivity. FloBoost,™ a new line of biosurfactant-based SWD management additives, were developed to reduce costs and increase efficiency of SWD wells in ways that traditional chemistries cannot. Conventional oilfield surfactants are synthesised from petroleum feedstocks and tend to have higher usage costs and carbon footprints. FloBoost additives share unique physicochemical properties with Locus Bio-Energy Solutions’ other fermentation-produced biosurfactants to improve a range of oilfield operations – at a fraction of the dosage and with minimal environmental impact. Fermentation-produced biosurfactants have unique structures with multiple chemically active sites that allow for improved functionalisation and surface adsorption properties – a contrast to conventional surfactants with a limited number of sites. In both laboratory and field studies, the complex structures of biosurfactants yield interfacial properties that outperform conventional surfactants at extremely low dosage rates. Interfacial tension (IFT) reduction is a key metric of surfactant performance. Biosurfactants outperform surfactants by penetrating and dispersing inorganic and organic solids that choke the injection well. Biosurfactants also possess unique adsorption/desorption characteristics, Figure 1. In rapid filtration tests, FloBoost-treated water samples pass through Millipore delivering long-term wettability alteration filters at an injection rate ten times faster than a nontreated sample. and organic deposit removal – properties that immediately reduce injection pressures and increase water injection volumes. Critical micelle concentration (CMC), which is the concentration at which surfactants self-assemble into micellar structures, is another key performance metric. Many biosurfactants have CMCs of less than 200 ppm, a fraction of the CMC value of most conventional surfactants. As a result, biosurfactants reduce IFTs and alter surface wettability at much lower dosages than many hydrocarbon-based chemistries. Biosurfactants are robust and highly stable at temperatures greater than 300°F. They are also produced from sustainable raw materials, with no live microbes or components that support microbial growth. As a result, these 100% natural, low-carbon Figure 2. At a 50 ppm treatment rate, the FloBoost-treated water samples demonstrated additives minimise a SWD operation’s carbon an improvement of nearly 39% in injection rates compared to the incumbent chemistry. footprint while helping meet ESG goals.
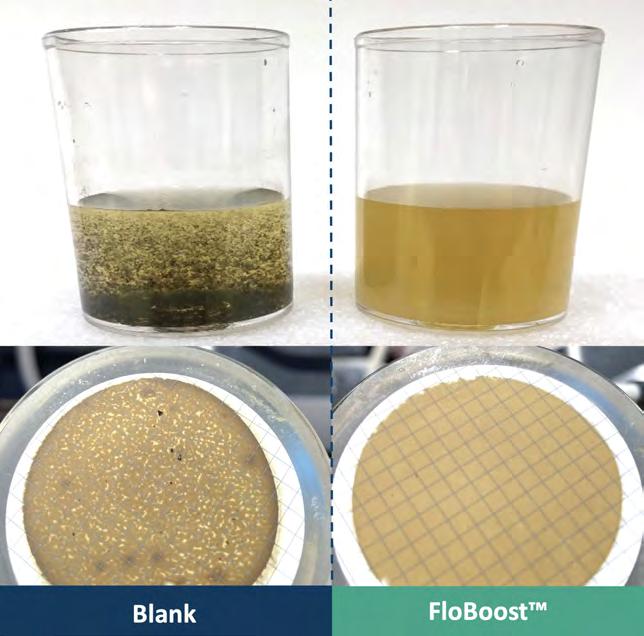
The unique properties discussed above help biosurfactant-based additives address many of the critical challenges facing SWD operators.
Reducing injection pressure
By keeping solids dispersed and suspended in the water, these biosurfactant-based injectivity aids help prevent plugging of rock pores and maximise injection volumes at a given maximum allowable injection pressure, thus maximising the operating capacity of the SWD well. Reducing injection pressure minimises power requirements for injection pumps, offering savings to operators.
In addition to reducing solid deposition, the additives can penetrate and disperse existing filter cakes and increase the effective permeability through these deposits – further increasing injection rates. Finally, by reducing IFT and promoting water wetting of the rock surface, FloBoost additives reduce capillary pressure and promote water flow into the pore space, resulting in deeper penetration into the rock at lower injection pressures.
Minimising emulsions formation and blockage
Although significant effort is made to separate valuable hydrocarbons from saltwater before disposal, no treatment is 100% effective. Even trace amounts of hydrocarbon carryover can create emulsions in the wellbore that reduce water flow into pore spaces, resulting in increased injection pressures and reduced volumes. The biosurfactant-based additives have been shown to effectively break up oil-in-water emulsions and keep oil dispersed in the water, with better efficiency and at lower dosages than synthetic surfactants.
Recovering more skim oil
Biosurfactant-based additives are shown to minimise the frequency of filter changes and allow the operator to recover more sellable skim oil – both of which improve the profitability of SWD operations. The novel additives can also benefit pad remediation efforts in the SWD system by reducing the additional person-hours and chemicals needed to clean tanks and remain in operation.
Providing flexible treatment options
The biosurfactant-based injectivity aids can be applied alone or in combination with acids and other conventional stimulation chemistries, making them a robust and flexible treatment solution in a wide range of downhole environments.
Proving biosurfactant potential in SWDs
While early on in its commercialisation, FloBoost SWD injectivity aids have demonstrated performance benefits within laboratory and in-field testing. The methodologies used allowed for a quick and definitive performance comparison between FloBoost and conventional SWD additives, with repeatable quantitative and qualitative measures.
Lab filtration testing
In rapid filtration tests in the lab, a series of high-solids Permian SWD water samples – a blank, a FloBoost-treated sample, and an incumbent additive sample – were passed through 0.45-micron Millipore filters at an injection pressure of 15 psi. The injection rate, measured as the time for 100 ml of water sample to pass through the filter, for the blank sample was 3 minutes and 30 seconds (Figure 1). The long injection rate was attributed to the undispersed solids and oily contaminants quickly settling on and clogging the filter.
By contrast, the FloBoost-treated water sample kept solids and oily contaminants well dispersed, which allowed the water to pass through the filter in less than 35 seconds – a 10-times faster injection rate compared to the blank.
In similar rapid filtration tests comparing the biosurfactant-based additive to a traditional injectivity aid, FloBoost-treated water passed through the filter at a 77% faster injection rate. At equivalent concentrations, the FloBoost biosurfactant-based additives outperformed the incumbent product by more than four times, implying that lower dosage rates can be used for lower treatment costs.
A series of filtration tests conducted in the field mirrored the biosurfactant-based additive’s performance improvements in the lab (Figure 2). A blank fluid sample collected from a SWD well in the Delaware basin took 127 seconds to pass through a Millipore filter. Fluid samples treated with the incumbent chemistry had an average injection rate of 70 seconds, while the biosurfactant-treated samples delivered an average injection rate of only 43 seconds, a nearly 39% improvement.
Field performance
FloBoost was used in a New Mexico SWD well that was injecting 10 – 11 000 BWPD. The injection pressure was 1200 psi. The produced saltwater contained oil, iron, and scale. In previous treatments, acid and surfactants were added to the high-pressure side of the H Pump. No decrease in pressure was observed with any previous treatments. A batch dosage of 250 ppm of FloBoost was used over two days. Within those two days, injection pressure reduced 12% from 1200 psi to 1060. The injection volumes were maintained at 11 000 –12 000 BWPD.
Conclusions
As produced water volumes increase and SWD wells become more difficult to manage, operators will need cost-effective solutions to inject more water without increasing injection pressures. Biosurfactant-based SWD management additives offer a proven solution by achieving maximum injection volumes for a given maximum allowable injection pressure. Reducing injection pressure optimises power usage by injection pumps, and increases operational efficiency while significantly lowering energy costs in the field. With their combined ability to reduce disposal costs while also lowering an SWD facility’s carbon footprint, biosurfactant-based additives are ideally positioned to become the injectivity aid of choice for SWD operations.
References
1. JOHN KEMP, “Water is the biggest output of U.S. oil and gas wells,”
Reuters, https://www.reuters.com/article/us-usa-shale-waterkemp/water-is-the-biggest-output-of-u-s-oil-and-gas-wells-kempidUSKCN0J223P20141118 2. KYLIE WRIGHT, et al. “The great saltwater flood in the Permian Basin,”
World Oil, July 2022. https://www.worldoil.com/magazine/2022/july-2022/ special-focus-permian-basin-technology-shale-technology/the-greatsaltwater-flood-in-the-permian-basin/ 3. ERIN DOUGLAS, “Earthquakes in Texas doubled in 2021. Scientists cite years of oil companies injecting sludgy water underground,” The Texas
Tribune, 8 Feb 2022. https://www.texastribune.org/2022/02/08/westtexas-earthquakes-fracking/