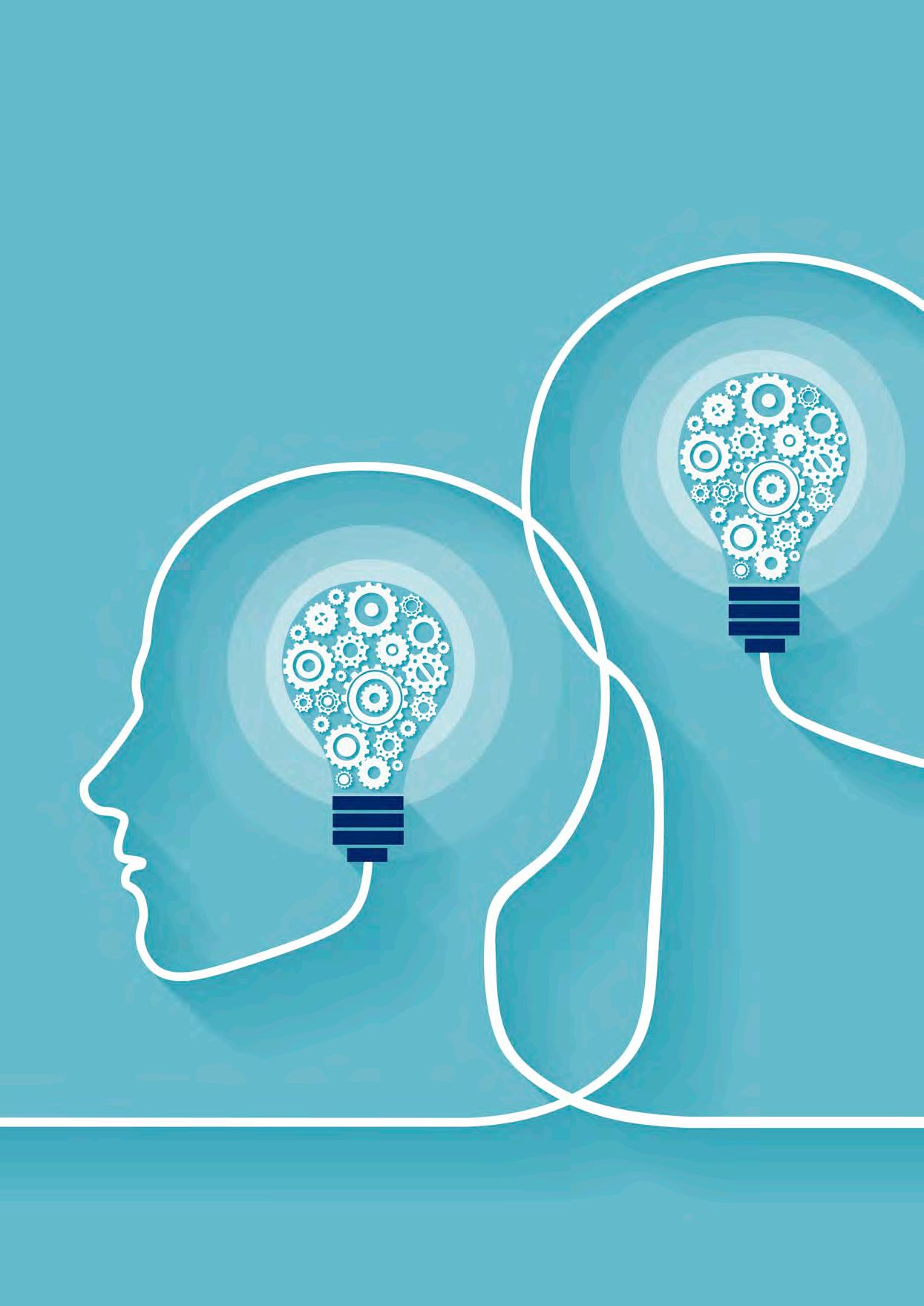
10 minute read
Innovations For Emissions Management
Lenus King, TETRA Technologies Inc., USA, details several innovations for emissions management in the upstream oil and gas sector.
he global energy transition and emissions management together constitute a journey. To meet the world’s rising energy needs throughout this journey, energy producers will be presented with many challenges requiring adaptation and innovation. Though alternative forms of energy seem to dominate the thinking around the transition, the oil and gas industry will remain a pioneering leader and vital contributor to our energy needs.
The use of fossil fuels for heating, medicine and other applications dates back to antiquity in the regions around the Caspian, Black, and Aegean seas. However, only in the past century and a half have they served the whole world, not only as a primary means of fuelling everything from gas lighting and heating to transportation and industry, but also as key components in products that define modern living – from soaps and solvents, to plastics and pharmaceuticals.
Today, however, with growing concerns surrounding environmental conservation, carbon emissions, and a warming planet, the expectation is that the oil and gas sector should adopt more sustainable practices and reduce emissions.
TETRA Technologies is an oil and gas services company with a diverse portfolio supporting the energy transition, and the company has made sustainability integral to its business.

Carbon capture to reduce CO emissions 2
TETRA has made agreements with Texas-based CarbonFree, a global carbon capture company with patented technologies that capture carbon dioxide (CO2) and mineralise emissions to yield commercial products. Carbon-Free’s SkyCycleTM is a unique technology that uses calcium chloride in its conversion process.
TETRA works with calcium chloride chemistry, producing various formulations of the compoundfor use across a wide range of industrial, agricultural, and food and beverage applications. The company is collaborating with CarbonFree to support its calcium chloride needs for the SkyCycle.
Zinc-bromine flow batteries
A crucial component of the energy transition is large-scale energy storage. One type of technology in this regard is the zinc-bromine flow battery, which is typically a large rechargeable battery system with an electrolyte of aqueous, high-purity zinc-bromide-based solution that exploits the reaction between zinc and bromine to store and deliver electric power. Its primary use is large-scale, high-capacity energy storage for solar and wind applications, providing reliability when darkness or low wind conditions interrupt power generation.
The performance and life of zinc-bromine batteries depends on the quality of the electrolyte; impurities of any kind can compromise battery capacity, operation and longevity. Aware of this, TETRA leveraged its processes and expertise in chemistry to develop TETRA PureFlow® ultra-pure zinc bromide – a pure compound derived from elemental zinc and bromine, for use in zinc-bromine batteries. The company is now supplying TETRA PureFlow to battery manufacturers, and can also produce aqueous zinc-bromide electrolyte to customer specifications.
Zinc-bromine battery technology is a greener alternative to the costlier lithium-ion battery. Its water-based electrolyte makes it less prone to overheating and fire than its lithium-ion cousin. Additionally, unlike the solvent-based electrolyte of lithium batteries, which can become a hazardous waste when the battery reaches its end of useful life, a zinc-bromine electrolyte can be recycled for reuse in either another batch of electrolyte or in an oil and gas operation, reducing the need for disposal. In other words, zinc-bromine technology yields a greener battery and a renewable form of energy.
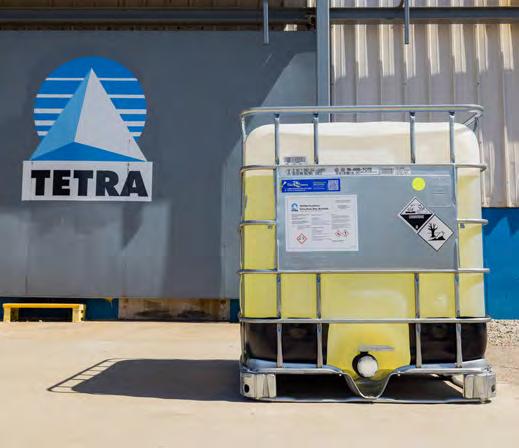
Figure 1. TETRA’s ultra-pure zinc bromide used in zinc-bromine batteries.
Figure 2. Steel lay-flat hose being deployed using TETRA’s rapid deployment and retrieval system.

Calcium bromide mercury removal
Although mercury is a vital element in medicine, dentistry, electronics, and measuring instruments, it is also a pollutant. Gaseous mercury is released when coal is burned, and coal remains a common fuel for power plants around the world. If mercury finds its way into aqueous ecosystems – ponds, lakes, streams, rivers, seas – it can form the highly-toxic methylmercury, which can then be absorbed by plankton and thus enter the food chain. This toxin adversely affects the nervous, immune, and enzyme systems of animals – including humans.
Both bromine and calcium chloride play a crucial role in eliminating the release of mercury emissions into the environment. Calcium bromide and calcium chloride are very effective at oxidising gaseous elemental mercury, which at combustion temperatures is otherwise difficult to capture. Using the bromine or calcium chloride compounds in pollution abatement equipment greatly enhances the removal of mercury from the flue gas of coal-fired power plants, helping to prevent mercury emissions. TETRA manufactures both calcium bromide and calcium chloride in both liquid and solid form.
Environmentally-friendly completion fluids
The deeper one drills, the higher the pressure grows. As offshore development entails increasingly deeper wells, in many cases the density of completion fluids needs to be increased to control reservoir pressure. In the past, this was accomplished by using zinc-based brines, but because zinc is classified as a marine pollutant in many parts of the world, expanding offshore activity led to environmental measures that severely restricted the use of these brines in the Gulf of Mexico, and outright banned them in the North Sea. Operators switched to cesium formate brines for the requisite densities, but due to the limited availability of cesium, the cost of these brines became prohibitive for applications requiring large volumes.
Operators needed an affordable, dense, environmentally-friendly brine made from readily-available ingredients, capable of withstanding harsh downhole conditions and the deepwater cold (e.g. not crystalising). To meet this demand, TETRA’s scientists developed TETRA CS Neptune® completion fluid – a high-density, zinc-free, formate-free, solids-free fluid. After several applications, the brand expanded to a suite of fluids – high-density, extra-high-density, monovalent, divalent – that are all customised specifically for each application. They are compatible with elastomers, pose low corrosion risk, perform at low temperatures and high pressures without crystallisation, and can be formulated as low-solids reservoir drill-in fluids.
Additionally, these fluids are cost-effective and environmentally-friendly, which render them feasible
A greener marine cleanout
As with completion fluid chemistry, wellbore cleanout systems have become more environmentally-friendly. These systems are used ahead of the completion phase to displace the solids-laden drilling fluid and leave the wellbore clean, water-wet and, crucially, free of solids. The presence of solids during completion can lead to the cracking and corrosion of metal tubing and, worst of all, damage the geological formation, which would diminish production.
In the past, a typical deepwater displacement of synthetic-based mud entailed a spacer-train of chemicals, and was then (if an indirect displacement) followed by large volumes of seawater, and subsequently the completion fluid. A direct displacement omits the middle step involving sea water. Either way, the use of harsh chemicals was unsustainable.
TETRA set out to develop a greener direct displacement system using natural, non-toxic, bio-based ingredients that would also be highly effective at removing the drilling mud and yielding a clean wellbore for the completion phase. The result of the company’s research and development yielded the TETRA Advanced Displacement System (TADSTM) – a greener alternative with high efficacy at low dosage, without harsh chemicals, that efficiently displaces synthetic-based and oil-based drilling muds.
Reducing oil and grease contaminants
When environmentally-benign completion fluids such as calcium chloride are not reclaimed for later reuse, they can be discharged into the sea (provided that they are not contaminated with oil and grease). TETRA developed its TETRA OilFix™ filtration service for such cases. The two-step service first entails the application of TETRA O-Lok CTM to remove oil and grease during diatomaceous-earth filtration. It then demands the use of a portable infrared spectrophotometer to determine oil and grease levels before and after filtration. Highlighting the service’s effectiveness is a case in Ghana.
Case study: Ghana
The operator’s deepwater operations were plagued with contamination of the completion fluids by the oil-based drilling mud. Transitioning from calcium chloride completion fluid to sodium bromide, the company sought a means to reduce contamination of the new fluid so that it could be reclaimed for reuse and of the previous fluid so it could be safely discharged into the ocean. Filtering some 36 300 bbl of fluid, the treatment reduced oil and grease contaminants by an average of 82.4%, with a peak of 86%, rendering the calcium chloride fluid environmentally-safe for discharge, and saving the customer time and money.
A better bromide and fluid reclamation
Bromine is widely used in oil and gas applications, specifically to formulate calcium bromide, sodium bromide, and zinc bromide – clear brine fluids used in the completion phase of a well’s development. TETRA produces bromide fluids at its plant in West Memphis, Arkansas, US, and distributes them through global service centres.
The company develops processes for manufacturing bromide-based brines, including one for enabling the use of elemental bromine, and another for enabling the use of elemental zinc in the manufacturing process. Using these processes to produce zinc bromide – instead of the more common method with bromic acid and zinc oxide – the company produces a pure product using less energy and producing fewer emissions. TETRA also reclaims bromide brines used in completion and workover applications for later reuse.
For some years now, zinc has been labelled a priority pollutant, with its use in offshore operations either banned or severely restricted. TETRA has a process for fluid reclamation that is more efficient than a number of methods that produce large volumes of waste. Additionally, any zinc bromide that cannot be reclaimed and treated at a service centre for reuse can be sent back to the West Memphis plant for remanufacture, thereby reducing the need for disposal.
Water transfer and treatment
Hydraulic fracturing has drasticly changed the oil and gas industry. Using water and sand-proppant to crack the formation has enhanced production by an order of magnitude. However, not only is the use of increasingly-scarce freshwater for fracking unsustainable (especially in desert regions and during periods of prolonged drought), but fracking also yields high levels of produced water, which is compatible with the reservoir fluids but cannot be used for fracking – in most cases.
Operators are now turning to recycling produced water for frac use. With treatment facilities centrally positioned to serve multiple frac sites, the water is transferred using pumps and piping, which is more efficient and greener than trucking it back and forth. However, a pipeline spanning up to three miles with dozens of pipe joints can be prone to leaking, and delivering reams of pipe sections requires an undesirable number of truck trips.
TETRA engineers designed a lay-flat hose – a double-jacketed, high-pressure, flexible hose for water transfer. With longer sections and positive-lock couplings, the system reduces the risk of leaks. Moreover, the hose is rapidly put in place and later removed using the company’s rapid deployment and retrieval system, which reduces the number of trucks required for piping operations. This also results in lower emissions.
Automating water management
Automating the transfer, treatment, storage and delivery of water is infinitely more efficient than conducting these operations manually. Automation reduces onsite personnel and the associated safety risks, and leverages advanced computing technology to ensure precision in treatment, pressure, pump performance, and storage levels, which lessens environmental risks. Moreover, an automated system enables users to control and monitor operations from afar, and generate metrics and data that can then be used to fine tune processes.
The TETRA BlueLinxTM automated control system’s nerve centre is a cloud-based dashboard connected by cellular or satellite link to the field equipment sensors, providing real-time access to readings of inlet and outlet pressures, fluid composition, water conductivity, storage levels, pump-engine operation, and equipment status and performance.
The efficiency of the TETRA BlueLinx system also reduces emissions, firstly, by reducing personnel trips to and from the site, and secondly, by precisely controlling pump engines for maximum efficiency and minimal fuel needs. The system also reduces the potential for human error and environmental spills.