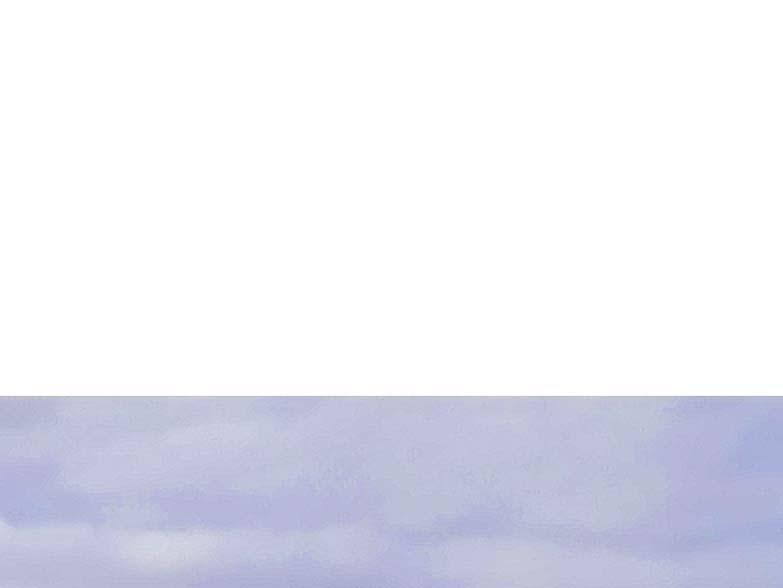
9 minute read
California Crushing
Sathish Krishnamoorthy,FLSmidth, outlines how a new heavy-duty roller breaker helped to eliminate clinker crusher blockages at CalPortland’s Oro Grande plant.
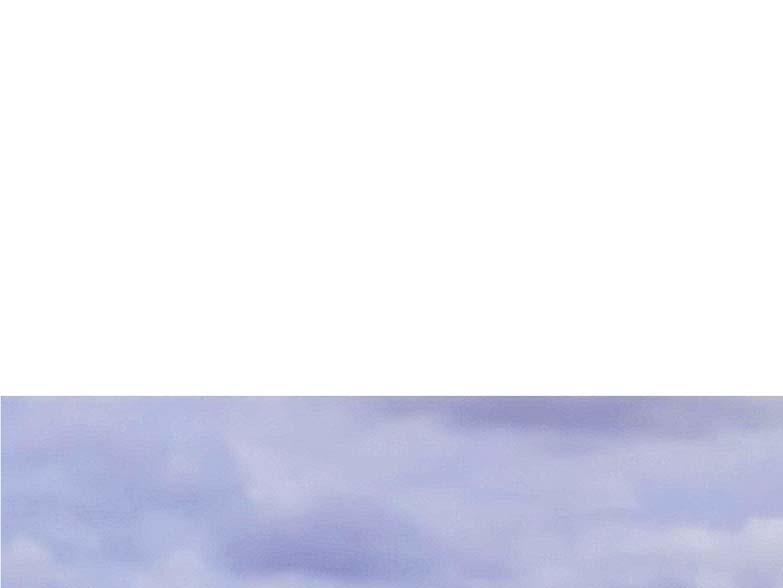
Californi crushin


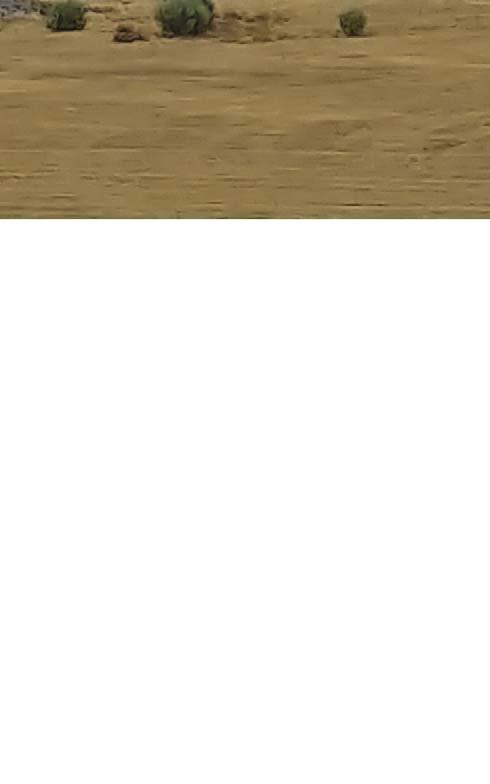
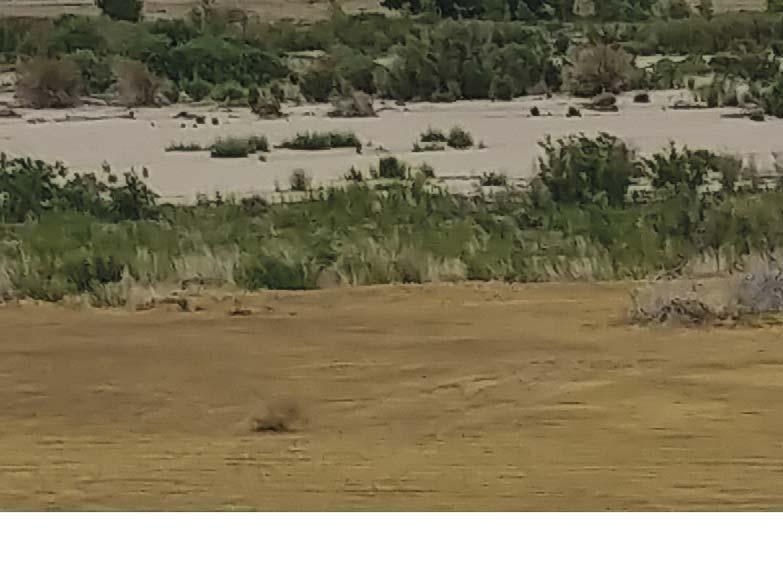
CalPortland was experiencing problems with the clinker crusher at its Oro Grande plant in California. A couple of times a year, a big boulder would come through the cooler and block the hammer crusher, forcing the plant to shut down both the cooler and kiln in order to clear it. As a plant producing 6600 tpd of clinker, the lost production time was costly – sometimes amounting to millions of dollars over a calendar year, not to mention the safety risks involved with entering the cooler. On top of that, the hammer crusher needed regular maintenance to replace wear parts and it was using a lot of power. The plant needed an alternative solution.
However, CalPortland’s clinker crusher problems were solved by a new Heavy-duty Roller Breaker (HRB), supplied and installed by FLSmidth. The company’s one-stop-shop service was able to save the customer time and money, ensuring the successful completion of the project within the scheduled shutdown.
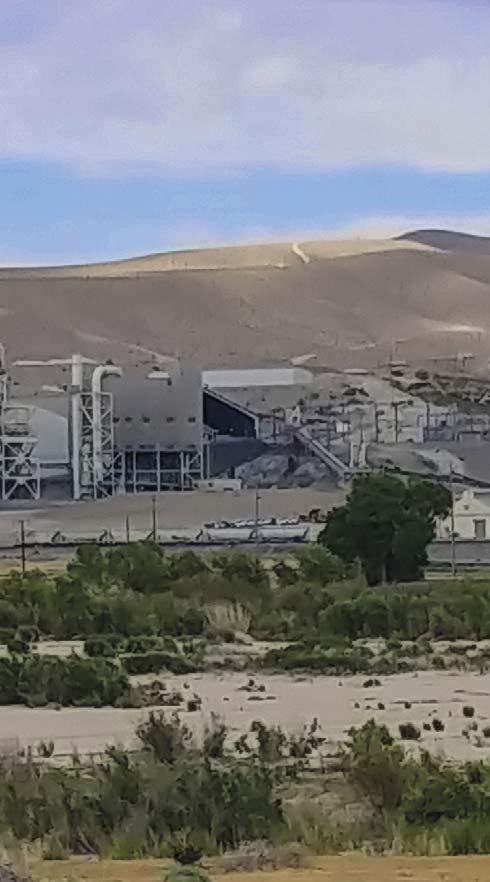

How it works: Heavy-duty Roller Breaker (HRB).
Sub-25 mm clinker falls through the gaps between the transport rollers, while the bigger lumps are conveyed forwards onto the crusher rollers. The fi rst of these is the ‘dropped roller’, which sits slightly below the horizontal plane of the other rollers. This one rotates clockwise, while the fi nal crusher roller rotates counter-clockwise, pulling the oversized clinker into the nip where it is crushed between the teeth of the cast wear segments.
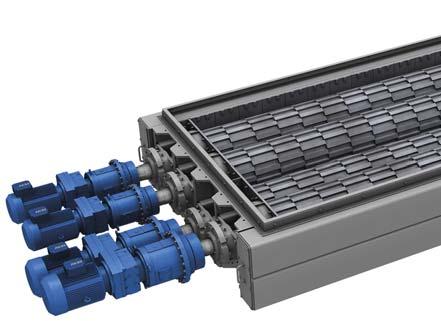
The HRB can handle clinker boulders up to 1.5 m in size.

A signifi cant improvement for health and safety. No boulder too big
The plant had been in talks with a couple of suppliers about their problem for a while but eventually decided on a Heavy-duty Roller Breaker (HRB) from FLSmidth.
“Our sister plant is already using the HRB from FLSmidth with great success, so we were confi dent in the technology. In particular, the differentiator compared to competitor models is what we call the ‘dropped roller’ for the fi rst crushing roll, which gives that extra grip and effi ciency when crushing the largest clinker lumps,” explained Kyle Smith, Chief Project Engineer/Project Manager, CalPortland.
The HRB can handle clinker boulders up to 1.5 m. It features a series of transport and crushing rollers that allow the right sized materials to pass through and crush larger materials down to a pre-set size. For Oro Grande, the HRB 414 was chosen to fi t within the cooler width. This model consists of two transport rollers and two crushing rollers that are electrically driven.
A low maintenance solution
HRBs deliver an effective, low-wear crushing process due to their lower speeds of operation at 6 – 8 rpm – a slow, persistent grind. In contrast, hammer crushers use a striking motion that sends bits of clinker fl ying around the crusher, causing wear. In a HRB, if the load gets too high, the crusher rollers reverse, stop, then resume their usual motion, repeating the process until the blockage is cleared. Instead of very high annual maintenance costs of up to US$100 000 to maintain the hammer crusher (including labour and parts), the cast wear segments have an expected life of at least fi ve years with very minimal maintenance – a signifi cant saving. Additionally, workers do not have to go into the cooler to clear it – a vast improvement for health and safety.
Power consumption is also much lower, at around 100 HP compared to 150 HP installed with a hammer crusher. Not only is this a cost-saver, but it is also in keeping with CalPortland’s ENERGY STAR partner status.
Saving energy is a priority for CalPortland, and the company is always looking for ways to make its plants more energy effi cient, and more sustainable. The power savings were a motivator for the company with this project, as was the anticipation of fewer kiln stops, which have a signifi cant environmental impact on top of the monetary cost.
Installation
Installation of the HRB was scheduled for the plant’s annual maintenance stop in January 2021.
“These types of projects are commonly contracted out to local teams. However, we decided to have FLSmidth Sioux City – our in-house service and installation team – take on everything except the electrical installation,” explained Sathish Krishnamoorthy, Head of Service Sales – NAMER Cement. “We know the equipment best, so it makes sense for us to take ownership of the installation process, providing a one-stop solution for our customer. Also, we wanted to be on-hand in case of any questions or problems during installation.”
This was despite all the restrictions related to the pandemic.
“We were very impressed by the way they handled everything,” said Kyle. “They were diligent, safety-conscious, and mindful of our need to get the plant back online as soon as possible. It was really good to have such a strong FLSmidth presence onsite for the installation.”
During preparations for this project, CalPortland had also been in talks with FLSmidth about purchasing a KilnLoq® inlet probe with hot/wet measuring capability.
“As well as being more robust, the KilnLoq gives the plant a much better oxygen, CO reading that can then be used to optimise the kiln, by balancing the air fl ow split between kiln/calciner, which will also help to reduce fuel consumption,” explained Sathish. “It’s a relatively small project that can have a very big impact.”
Since the FLSmidth crew was already onsite, the company offered to install the KilnLoq at the same time as the HRB, saving money on bringing in additional crews.
CalPortland was impressed with the results of both projects. Crucially, these projects were completed on time and within the company’s limited shutdown window, thanks to FLSmidth’s commitment to the deadline and the collaboration between FLSmidth and the CalPortland team. The HRB started up at the end of January and in March, CalPortland saw a boulder come through that would certainly have blocked the old hammer crusher, forcing them to shut down the cooler and the kiln. The company has experienced record numbers in its uptime and believes that the two projects have been instrumental in this.
About the author
Sathish Krishnamoorthy is the Head of Sales Support and Services at FLSmidth, North America.
How it works: KilnLoq laser gas analysis system.
The system measures gases such as CO, NO, SO2, CO2, HCl and O2 at the kiln inlet, enabling kiln operators to optimise fuel consumption and clinker quality. The KilnLoq also features the unique One Pipe design for easy cleaning and very low maintenance, ensuring maximum uptime.

In-house service and installation team.
The KilnLoq HW Laser Gas Analysis system.
Installation of the HRB 414 was completed within the shutdown window.
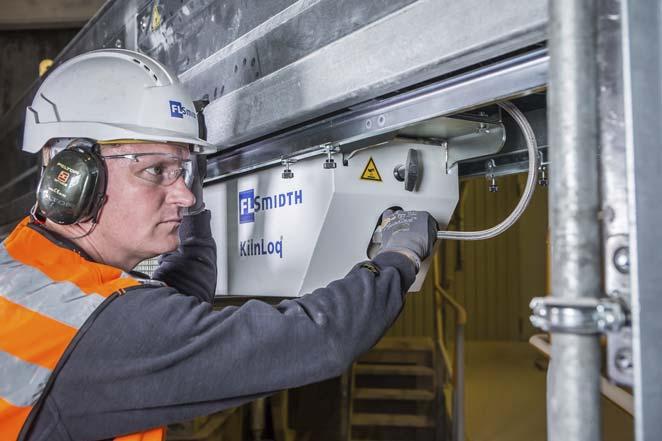
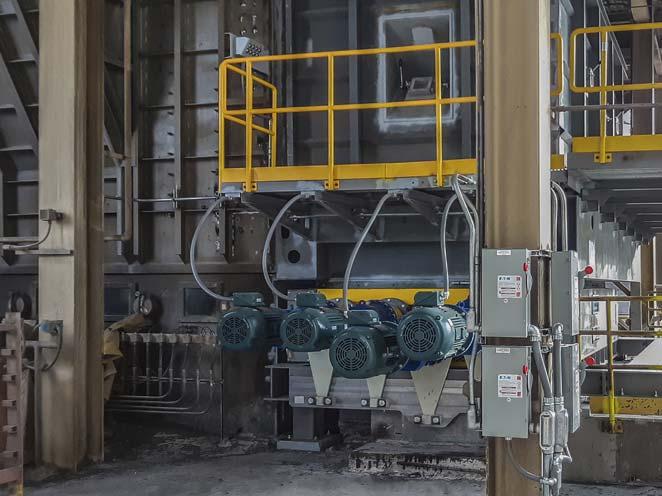

High capacity split roller bearing set to transform industry
Global bearings innovator, Bowman International, has launched to market a split roller bearing with substantially higher radial and axial load capacities. Ideal for applications such as screw conveyors, the new Bowman Advanced Split Roller Bearing offers up to 75% higher radial load capacity and up to a 1000% increase in axial load capacity in both directions.
Ian Breeze, Technical Director for Bowman, comments on the signifi cance of this innovation: “For the fi rst time, plant builders and maintenance engineers working in the cement industry can specify a split roller bearing that does not rely on race lips alone to accommodate axial force in high-load applications. The new Bowman Advanced Split Roller Bearing comprises two independent 3D-printed axial bearings designed to accommodate greater loads, improving system performance with less maintenance and reduced unplanned machine failure. “In fact, compared to other market-leading split bearings, the Bowman Advanced Split Roller Bearing increases bearing L10 life by up to 500%.”
Further enhancing the performance of this revolutionary split roller bearing is a patented triple labyrinth extended seal which not only offers a tighter seal than other split bearings, but also reduces the need for costly removal, machining or replacement of worn shafts. Instead, engineers can simply fi t an extended seal onto an undamaged part of the shaft, without compromising performance and without the need for extended downtime.
Thanks to its high thrust capacity and increased radial load capacity, this bearing can be specifi ed to replace solid spherical roller bearings in rotating machinery, delivering up to ten times faster bearing change times than previously possible for these applications. “When space is limited, engineers often need to disconnect the coupling and move other equipment, such as motors, gearboxes or pumps, out of the way before they can slide solid bearings off the shaft for replacement or maintenance,” explains Ian.
“Split roller bearings can be assembled radially around the shaft, eliminating these additional logistical challenges and making maintenance and replacement a lot faster and more cost-effective. To further enhance time and cost savings, the Bowman Advanced Split Roller Bearing uses the rollers to lock the two cage halves together, eradicating the use of small and easy to lose clips and other locking components.”
Alongside the signifi cant increase in radial and axial load capacity, this new bearing design offers a range of additional installation and performance benefi ts, such as larger diameter screw sizes to accommodate increased capabilities for the clamp rings, cartridges and pedestals and roller pockets with cavities to hold the grease against the rollers.
As part of the Advanced Split Roller Bearing portfolio, Bowman offers a range of dimensionally interchangeable retrofi t products that fi t directly into the existing bearing housings, even from competing bearing brands, to quickly and cost-effectively improve radial and axial load capacities. There is a choice of additional IoT-specifi c functionalities available and bespoke adaptations can be accommodated within fast lead times.
Ian concludes: “Bowman is a proud innovator of bearing solutions that solve real industry issues. We are the fi rst manufacturer to create a split roller bearing capable of increasing the lifespan and performance of high-axial systems and thanks to the production benefi ts of 3D printing, we have been able to deliver this product to market at a price point up to 20% lower than other leading split bearings.”
For more information on Bowman’s new Advanced Split Roller Bearings, search ‘Bowman split bearings’ online.
Advertisement Feature