
7 minute read
Opting For Optimisation
OPTING FOR

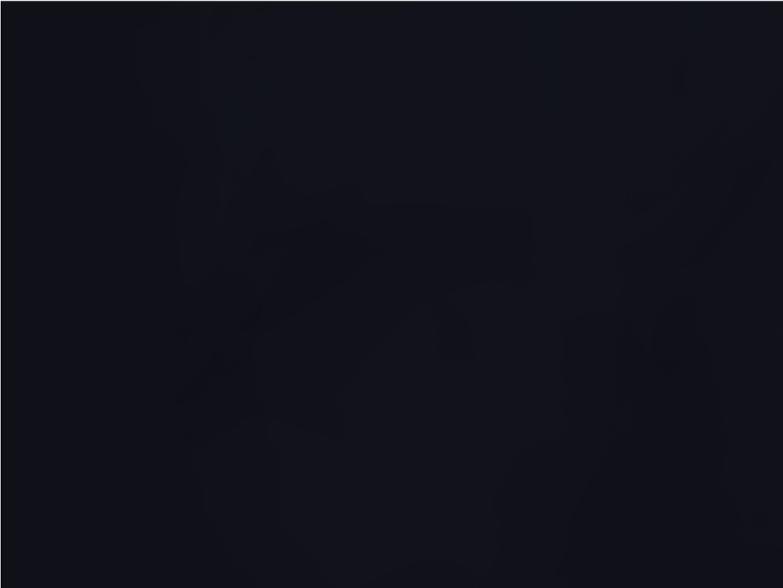
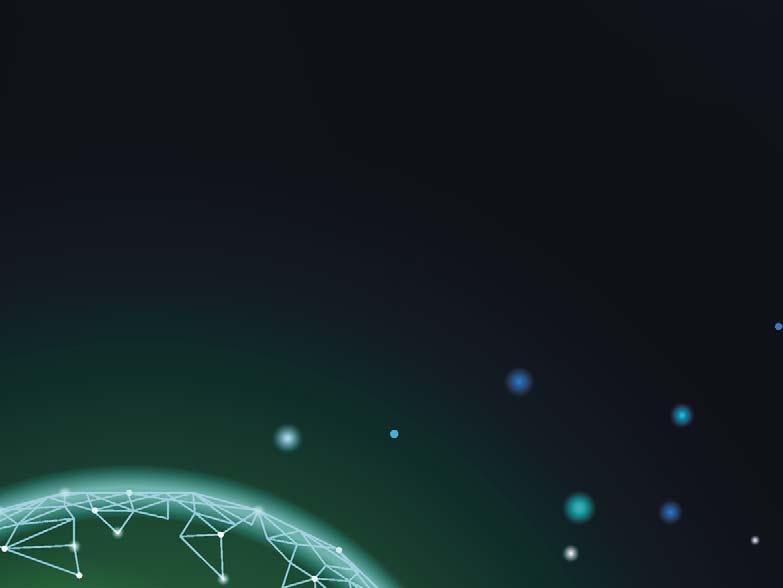
Marco Rovetta, CTP Team, considers how cement producers could work towards achieving carbon neutrality, starting with the optimisation of existing plant equipment.
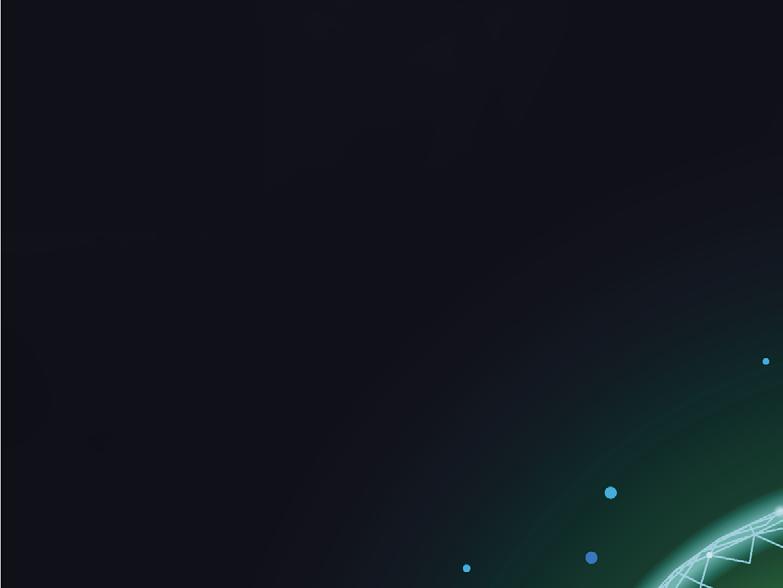
Reducing the cement industry’s carbon footprint involves two challenges – optimising the efficiency of equipment and recycling wasted energy which, in the cement industry, is concentrated in the excess heat from the manufacturing process.
The primary actions to reduce industrial emissions and protect the environment began around 50 years ago, and technologies were developed that, seen with today’s eyes, have had a considerable impact on the balance of the environmental sustainability of the cement plant.
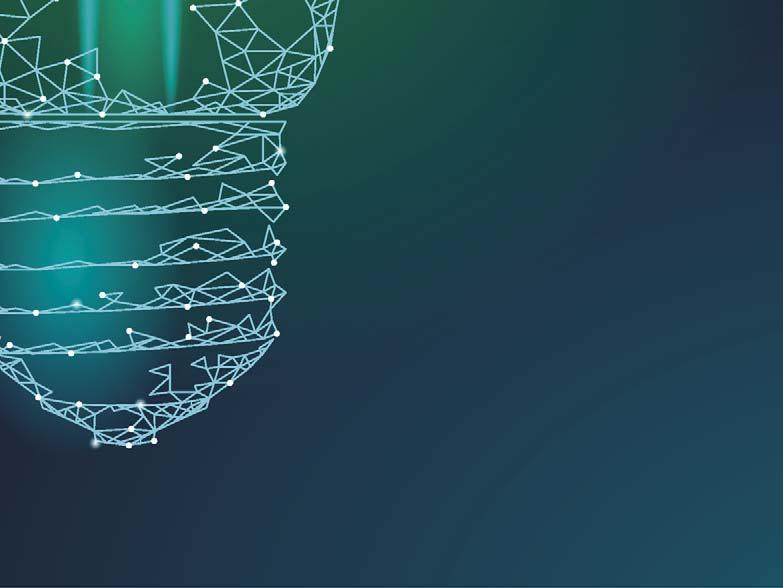


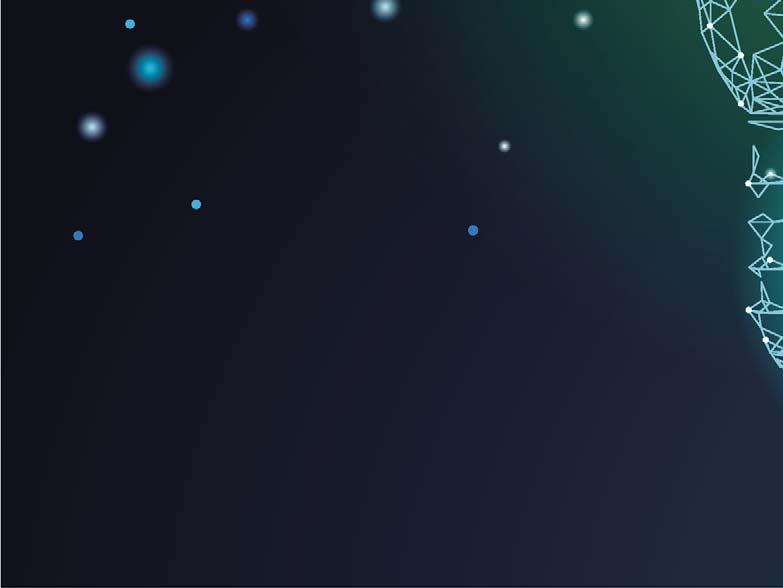
In addition to the reduction of the energy used in filters and gas cleaning through the optimisation of the equipment, a further step towards the optimisation of the environmental footprint of the cement industry is the reuse of the residual heat from the process in suitable WHR systems.
Environmental sensibility
Starting in 1970, the constant improvement of environmental sensibility has brought about a wide range of pollution control systems. The importance of these systems is nowadays very relevant in cement production.
Such importance is underlined by the fact that pollution control devices have reserved a considerable space in the BREF documentation, the official document used as a reference for preventing and/or minimising emissions and impacts on the environment in the EU.
In the frame of the sustainability of industrial processes, today a new challenge for cement producers lies in taking action to combat climate change, which is predominantly caused by greenhouse gas emissions (GHG) such as CO2.
Together with the adoption of new technologies applied to the production process, cement producers must also consider optimising energy usage in existing equipment.
Unfortunately, most emissions control equipment is energy consuming to some degree and in some cases, could have a considerable impact on GHG emissions and production costs as well.
Where possible, the installation of a Waste Heat Recovery system is a useful tool to recover residual heat from the process, and play an active role in the balance of the environmental footprint of the cement plant in terms of GHG generation.
Energy demand in a bag fi lter
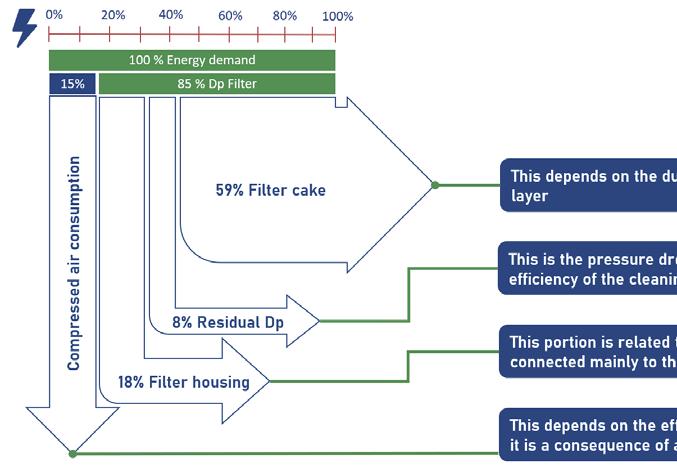
In a bag filter, energy is used to face the pressure drop created by the flow of gas passing through equipment. The only means of controlling a filter’s pressure drop is the cleaning of the bags, adjusted according to a certain frequency. It is possible to distinguish a number of times that bags must be cleaned in order to maintain a certain filter’s pressure drop, of which Figure 1. The optimised operating condition is placed at the minimum value cleaning frequency of the total fi lter consumption curve. is inversely proportional. The cleaning system works using compressed air and it is possible to define the amount of energy used for cleaning in order to maintain a certain pressure drop. As mentioned, the pressure drop is the result of the gas passing through the filter and through Figure 2. Each component of the total amount of the energy used in a bag this, some energy is fi lter is infl uenced by factors that need to be managed with a proper fi lter proportionally used design. in the fan as well.
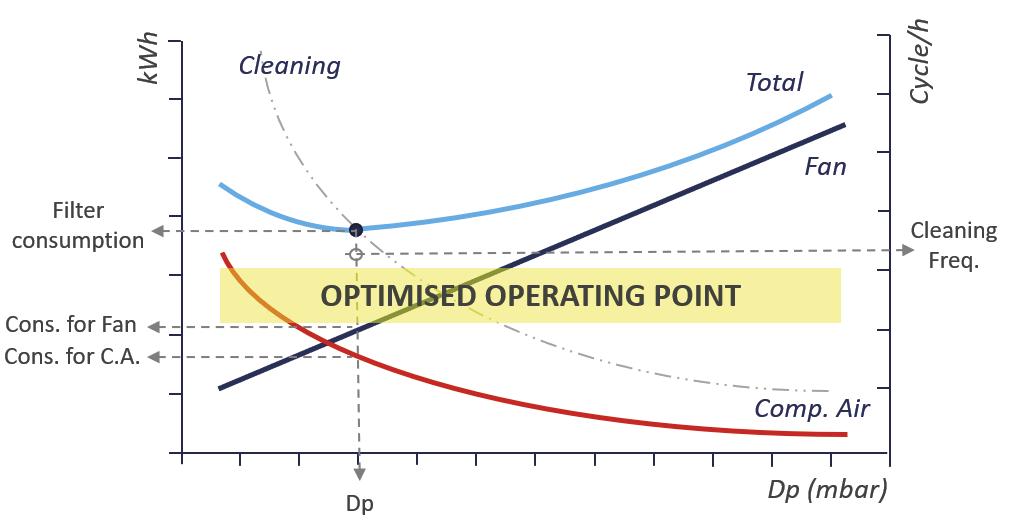
Overall, the energy used for filtration is the sum of the amount spent in cleaning and fan energy. It is possible to find the optimised operating conditions placed at minimum value of the total filter consumption curves.
Considering 100% of the filter consumption: 15% of filter energy consumption can be assigned to the production of the compressed air for cleaning, while the remaining 85% is used to let the gas pass through the filter. This portion includes resistance due to the filter housing (18%) and the residual pressure drop of the bag (8%). The biggest portion is caused by the dust cake at 59%.
Each component of the total amount of energy used is influenced by factors that need to be managed with a proper filter design.
The pressure drop of the filter cake depends on the amount of dust on the bag’s surface and its distribution and density affect the cake’s porosity. The residual pressure drop is related to the resistance of the bag felt without dust, provided that the cleaning system is capable of completely eliminating the dust cake. The residual pressure drop is related to the characteristics of the material used for the bag. The pressure drop due to the filter’s housing is dependent on the layout adopted. The amount of compressed air is a consequence of the sum of all the above factors and can control the cake pressure drop only.
In order to help cement producers in the modernisation and decarbonisation of the plants, CTP Team focus on providing assistance for the optimisation of existing equipment and high skilled maintenance service.
The approach of the ‘OTP’ division
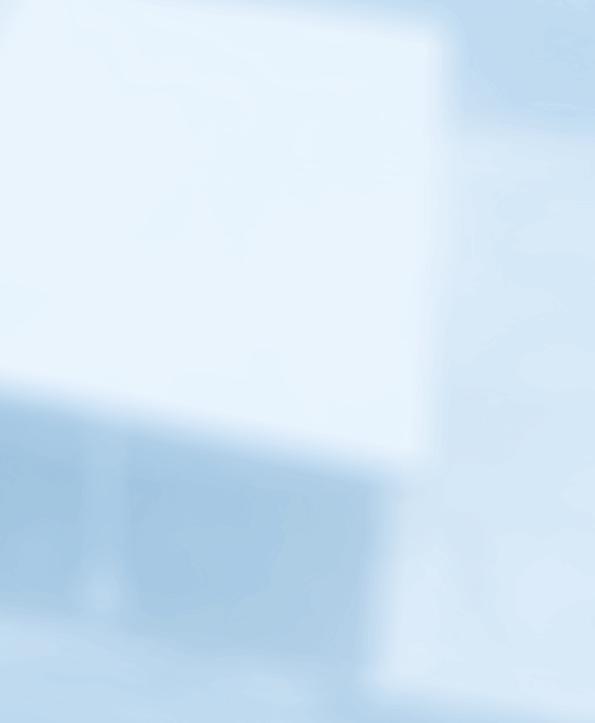
OTP stands for ‘Optimisation Technology Performances’. The OTP division is specialised in the optimisation of bag filters and waste heat recovery systems, valuing reliability, quality and savings.
The OTP technical approach is based upon deep process analysis and equipment validation, identification of critical points, and development of solutions to improve the existing equipment and solve plant problems to meet client expectations.
CTP Team is also focused on the design of pollution control equipment, and the company is ready to do its part in tackling climate change challenges, optimising energy use in dust or pollutant abatement, without forgetting its main task.
Fast. Fair. Flexible.
Think bigger – with InterCem.
From individual components to upgrades to complete plants, InterCem provides customized solutions for operators and investors of cement plants all over the world. InterCem is therefore also the right partner for you when it comes to planning, detailed engineering, project management of greenfi eld projects and conversion/modernization of production plants. Contact us: The InterCem professionals will also fi nd the right solution for your requirements.
The installation of a Waste Heat Recovery system can provide an effective contribution towards balancing the environmental footprint of the cement factory, as well as a concrete support in the energy transition from high to low carbon energy.
The first action for cement plants to take is the optimisation of existing systems in terms of energy efficiency. Then, the installation of a WHR system allows for the production of clean energy without additional greenhouse gases.
One step towards carbon neutrality
An emission controls system combined with Waste Heat Recovery technology has the potential to keep emissions levels under control at the stack, increasing plant energy efficiency. The internal energy production by WHR can significantly reduce electrical costs.
CTP recently partnered with CTN for the installation of two Waste Heat Recovery systems in Sonmez and Cimko Narli in Turkey. The Waste Heat Recovery boiler designed by CTP captures waste heat from the clinker cooler in Cimko Narli and from both clinker cooler and kiln preheater at Sonmez cement.
The WHR based on the Organic Rankine Cycle produces clean energy – the internal power generation system operates without the use of water, a precious natural resource, and saves thousands of tons of equivalent CO2 emissions each year.
Recently, CTP has been awarded a contract for new Waste Heat Recovery systems to be installed in the Outão Cement factory, Portugal. The project will consist of several new developments to provide a highly customised solution to feed a double-loop system (thermal oil and organic), to recover waste heat and produce electricity from three different sources – the kiln preheater and clinker cooler of the existing 4000 tpd cement unit N°9 and a new solar field, that SECIL will install near to the production line.
Two renewables combined
For the Portuguese project, waste heat and solar energy will be combined to produce the electricity needed to partially cover the internal consumption of the Outão Cement factory.
Reducing the environmental footprint of the cement industry is a challenging goal. The challenge is twofold – achieving carbon neutrality without burdening the overall process. A beneficial approach is to focus more on the total exploitation of all the resources potentially available from the process itself.
About the author
Marco Rovetwta is a Mechanical Engineer with over 30 years of experience in the cement industry, especially in emissions control systems. He is a product innovation manager at the CTP Team, leading the continuous improvement of new products and looking for new technologies with the highest performance and best available techniques.
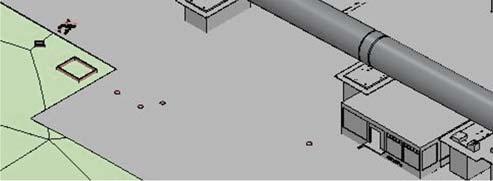
