
9 minute read
The Benefi ts Of A Better Brush
THE BENEFITS
BRUSH
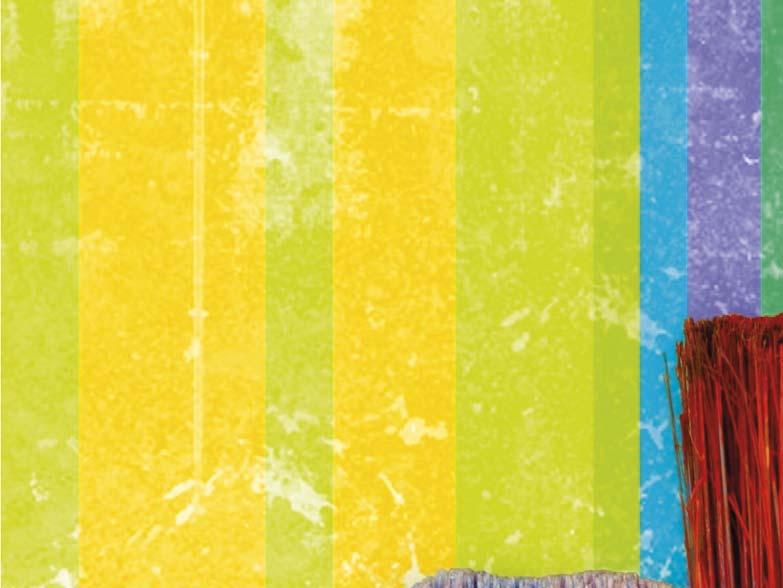
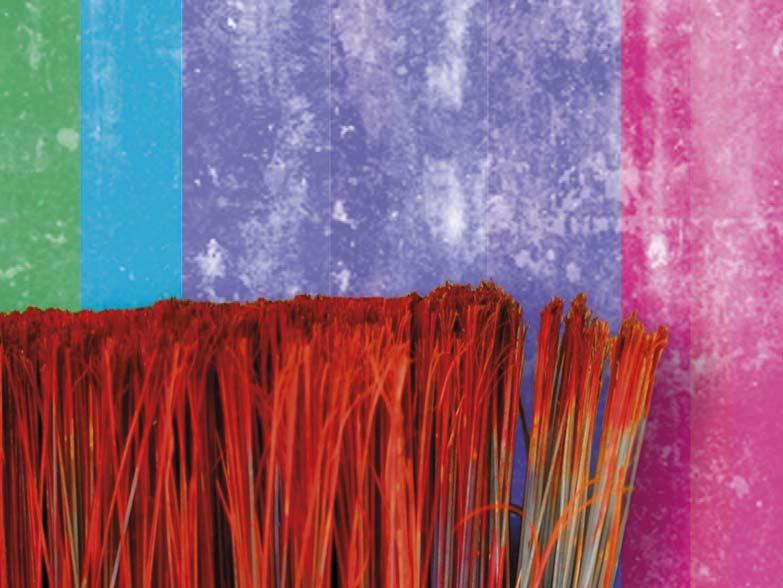
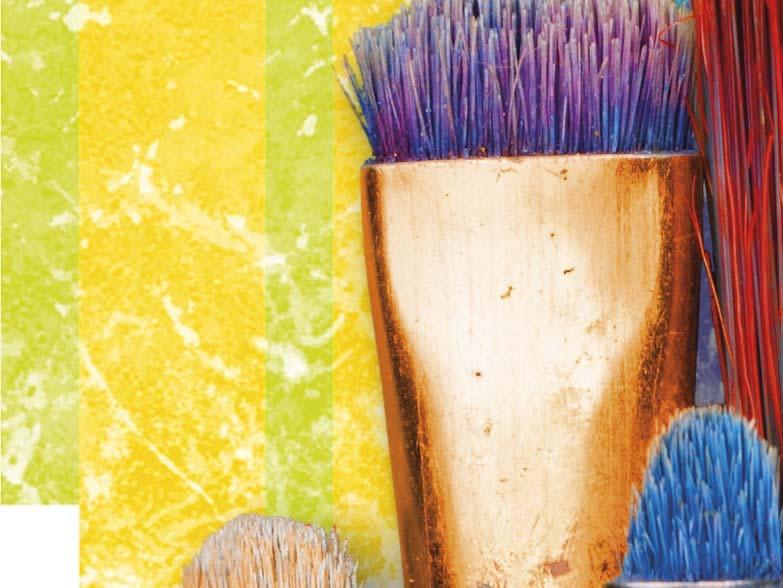
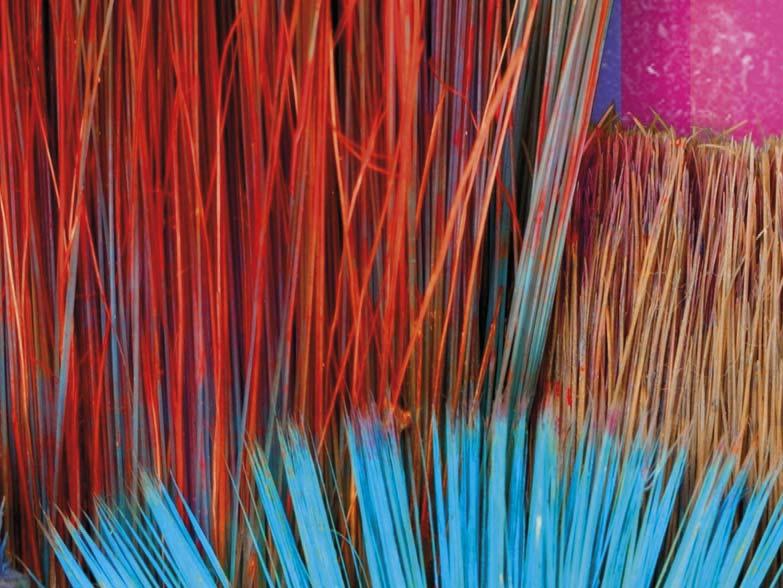

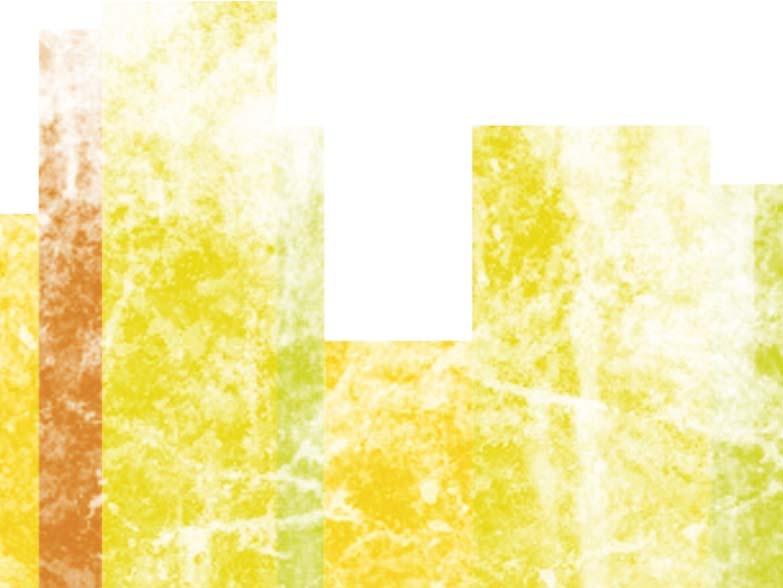
Mathis Menzel, Menzel Elektromotoren, explains why cement producers should forgo brush-lifting devices for slip ring motors in favour of sourcing high-quality, application-specific brushes.
Slip ring motors are great for powering cement mills and crushers. In contrast to squirrel-cage induction motors, they provide the full starting torque from standstill and need no power electronics to get high-inertia applications started. This enables a rugged, long-lasting motor design suited for the most dust-ridden environments at a competitive price. Slip ring motors feature carbon brushes as wear-and-tear parts that typically need to be replaced after a period of several months up to several years, depending on the application. These brushes, composed mostly of graphite and copper, allow the variation of the rotor resistance to achieve high starting torques. After motor startup, the external resistors are switched off. Conventionally, the brushes are in permanent contact with the slip rings. However, by installing short-circuiting and brush-lifting devices, they can be removed after motor startup in order to decrease wear and achieve much longer brush lifetimes. After the motor has reached the nominal speed, the rotor windings must be short-circuited, then the brushes can be lifted. This is intended to reduce maintenance requirements and save costs on brushes.
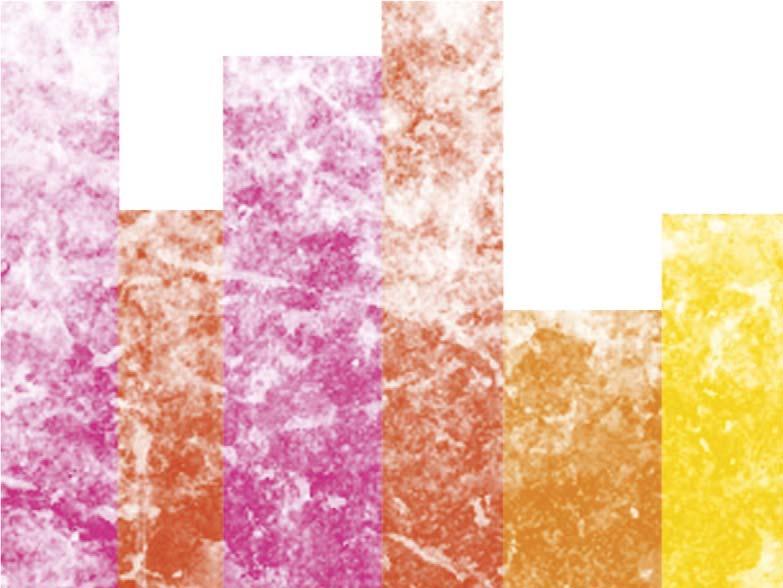


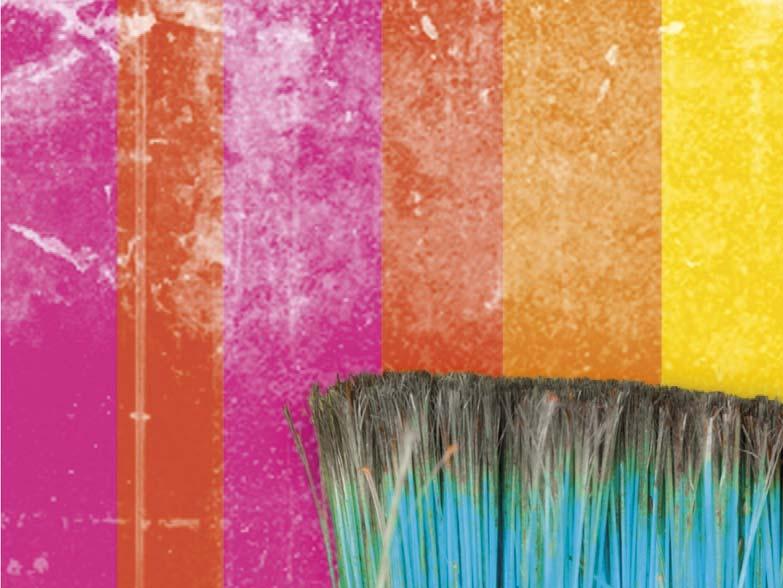
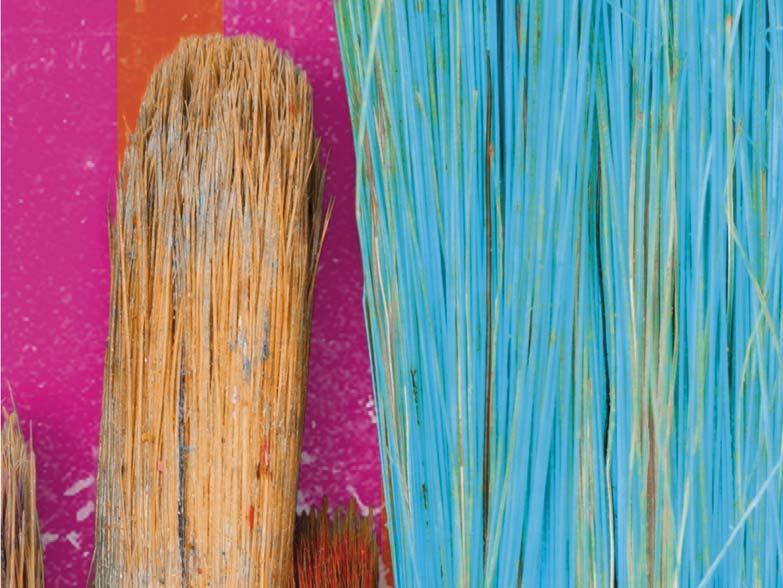
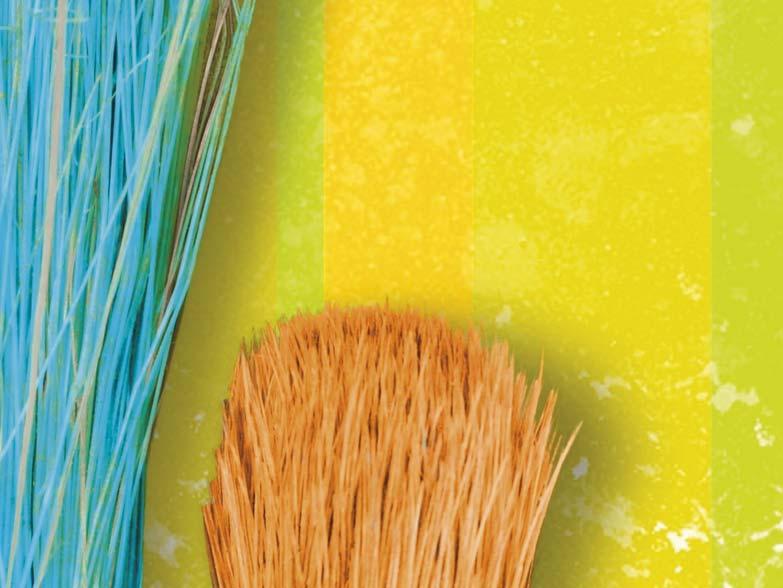
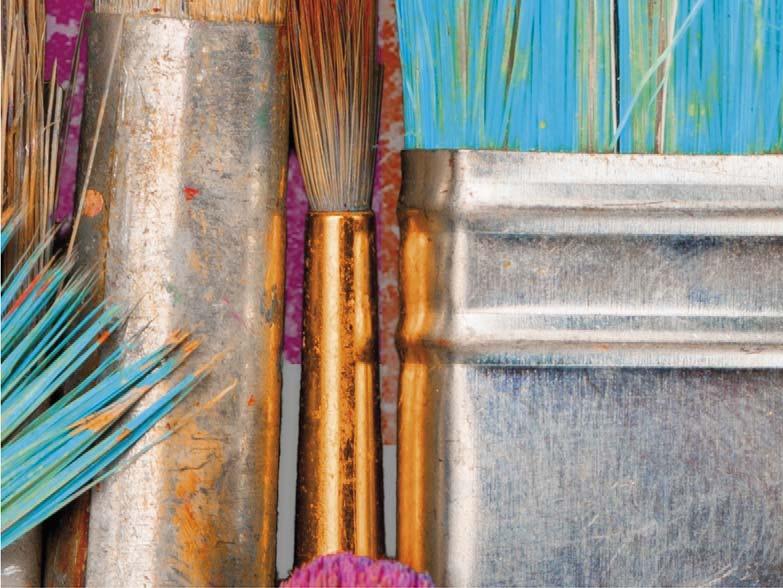
Original target applications
To understand why the question of brush lifting arises at all, it is worthwhile to look at its historical background. In the past, applications for slip ring motors were much wider than today, as they have largely been replaced with squirrel-cage motors. For instance, slip ring motors were also used in applications that did not require high starting torques (like cement mills do) because of their low inrush current. Typical examples for such applications included water pumping stations in remote areas with a weak grid. These motors powered large pumps in practically uninterrupted continuous operation, with just a handful of restarts per year. In those days, brush quality was signifi cantly lower than today, and the brushes wore down quickly. Brush lifting in those circumstances had the advantage that it greatly reduced maintenance requirements – the pump motor could be started up and left running for months on end. It was ideal for remote waterworks that operated mostly unsupervised.
Cost–benefi t assessment
How does this apply to the cement industry?
In the cement industry, the use cases and ambient conditions are completely different. Main mills are typically started up daily in contrast to once every few months. The motors are exposed to vibrations and dust, which exerts a lot of stress on any brush-lifting device. Also, staff are always on hand to check and, if necessary, swap brushes. It appears that the demand for brush-lifting devices in the cement industry is kept alive primarily through active promotion of this solution by a few specifi c motor manufacturers, who see it as a way to distinguish themselves from the competition. Menzel Elektromotoren does not recommend brush lifting for the cement industry because the benefi t of reduced brush wear is too small to justify the additional cost for installing and maintaining the mechanisms.

Figure 1. Sturdy slip ring motors without power electronics are used to drive raw mills.
Figures 2 & 3. Brush lifting requires various moving parts that create additional risks of failure (left). In this design, the mechanism is operated via a chain (right).
Within recent decades, brush quality has improved. Today, high-quality brushes with standing times of one-to-two years per set are available. The price of a customary brush-lifting mechanism will buy brushes for 15 to 20 years. The maintenance effort for regularly checking and exchanging the brushes and cleaning the slip rings is negligible. Plant staff manage this in little time, and servicing can be scheduled to fi t the production plan. In contrast, brush lifting requires complex measures and creates signifi cant additional risks of motor failures. Short circuiting the rotor windings must be very well synchronised between the three phases and with the lifting mechanism. If not, an arc will form between the slip ring body and lifting mechanism upon lifting the brushes, and in many cases, the entire mechanism will be destroyed. Menzel’s experience with repair calls for motors with brush lifting is that in 90% of the cases, the lifting mechanism is the reason for failure. Brush-lifting devices introduce a number of additional moving parts into the slip ring chamber that can wear or jam. Different designs present various weak points. Figures 2 and 3 show a device actuated by a chain drive. This auxiliary drive, which is positioned on top of the slip ring motor itself needs proper maintenance. The hole through which the chain is guided into the slip ring chamber also allows dust and dirt inside. This can lead to scratching of the slip rings and overheating if dirt accumulates. A more modern design as seen in Figure 4 features a levered mechanism. In this case, two auxiliary drives are installed inside the slip

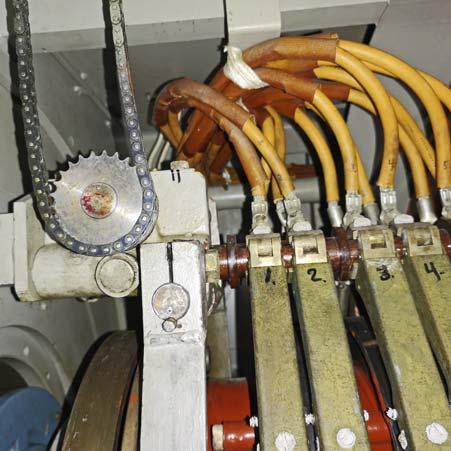
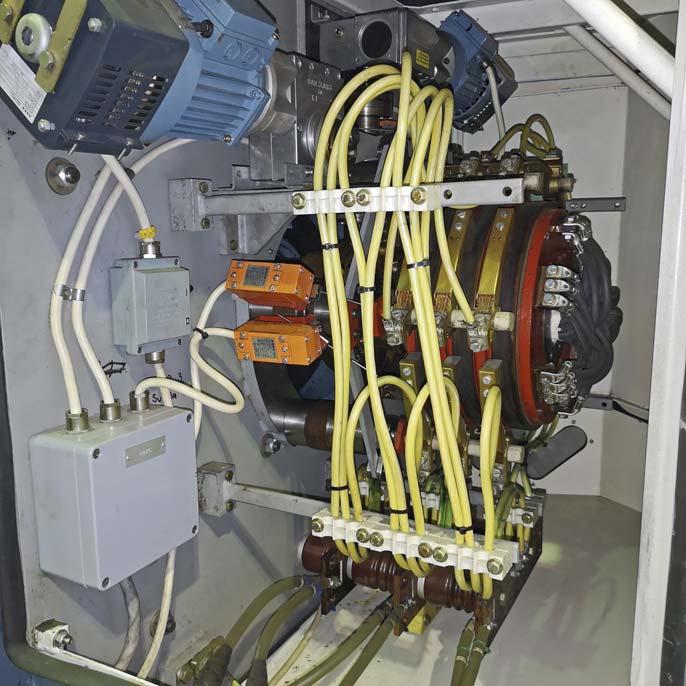
Figure 4. Levered brush-lifting mechanisms and the necessary extra drives take up a lot of space and impair accessibility for maintenance.
Figures 5 & 6. This short-circuiting and brush-lifting device caused total motor damage through a high fault current.
ring compartment, along with several metres of cables as well as various switch boxes. Accessibility for maintenance is made diffi cult.
If brush-lifting devices fail, this results in a complete destruction of the slip ring body and often of the rotor winding, too. Repairs for such a big failure take many weeks and cost almost as much as a new motor.
Figures 5 and 6 show a dismounted short-circuiting and brush-lifting device of a smaller motor, again with a levered mechanism and with an auxiliary drive mounted outside the housing. This device had already caused trouble more than once. Eventually, after 20 years in service, it had blown up, effectively taking the motor out of service until it could be replaced. The device had to short-circuit a current of more than 1000 A. At the same time, the mechanics were subject to dust and vibrations. Eventually, the strain was too much, and there was a high fault current. Repairing or replacing the brush-lifting device would have been prohibitively expensive as well as being too time-consuming. Menzel quoted a motor without brush lifting, which the manufacturer could quickly confi gure for the application. Commissioning was only three weeks after the original motor failure. The customer was happy to be able to limit the machine downtime.
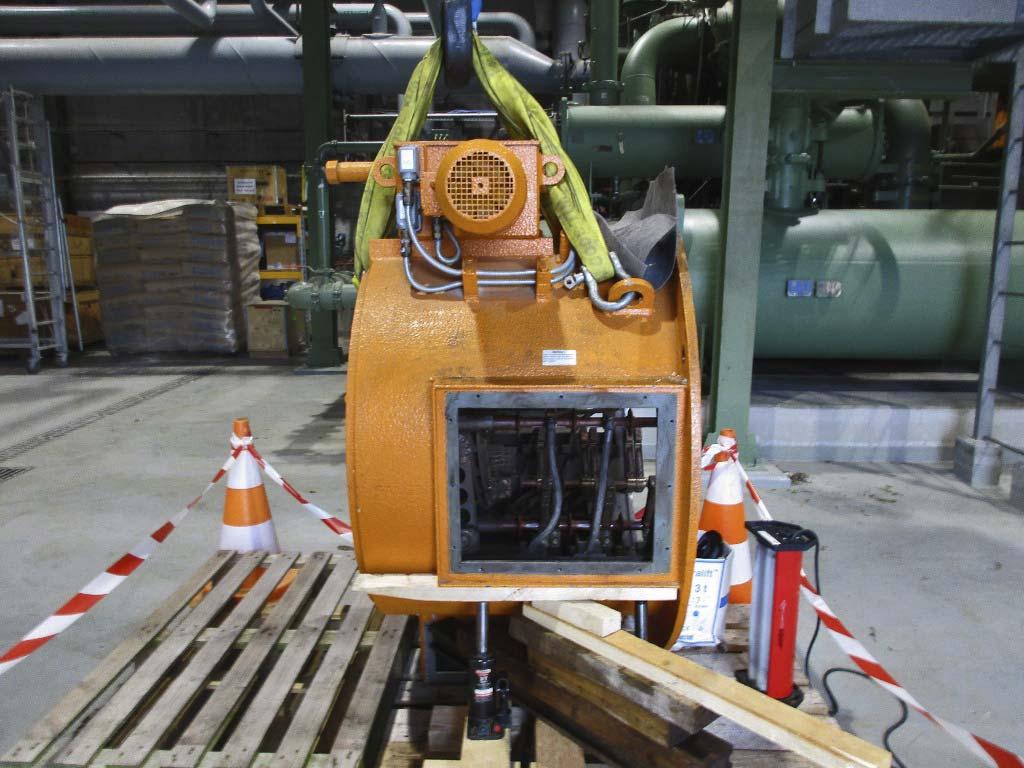

Getting the most out of brushes
Carbon brushes are pressed against the slip rings by springs. They must slide well in the brush holders and have even contact with the slip ring surface. Rocking and tilting brushes can cause sparking and brush fi re with potentially devastating consequences. Brushes should be replaced when they are worn down to half their length because, beyond this point, the pressure will no longer be suffi cient for good current conduction. Customers should always exchange all brushes of one motor at the same time, using only brushes from the same batch to avoid uneven wear. They should generally take care to buy brushes only from reliable sources, such as the original motor supplier, and not fall for poor-quality replacements at supposed bargain prices, which unfailingly have shorter lifespans and often cause costly damage. Motor manufacturers provide information on recommended brush exchange intervals. If in practice brushes wear down much faster than the recommended interval, dedicated analysis of the application by motor experts might show up possible corrective measures that will save money over time and increase the motor’s reliability. Brushes provide the
best performance if the material composition is optimised for the application. Factors to consider include duty types as well as climatic conditions and even the height above sea level. Menzel has built up an signifi cant wealth of knowledge in this fi eld and will happily advise companies on brush selection. The German motor manufacturer regularly also provides customised brushes and has thus improved performance in various cement industry applications. Menzel manufactures large industrial motors – the company has a large stock of motors for all common applications and can also supply motors with brush-lifting devices, but weighs this decision very carefully against the kind of application to avoid unnecessary trouble in the long term. In its own slip ring motor series, Menzel has optimised various design details. The slip ring chamber is positioned between the motor bearings instead of externally. Therefore, the motor bearings can be exchanged without removing the slip ring body, which is often the cause for damaged windings or slip rings. This design does not require hollow motor shafts to connect the rotor windings with the slip ring body. In addition, it enables an overall shorter length of the motors. Since the bearings are situated further apart, the motors are also more vibration-proof. Two large service windows enable comfortable access to the slip ring compartment from both sides.
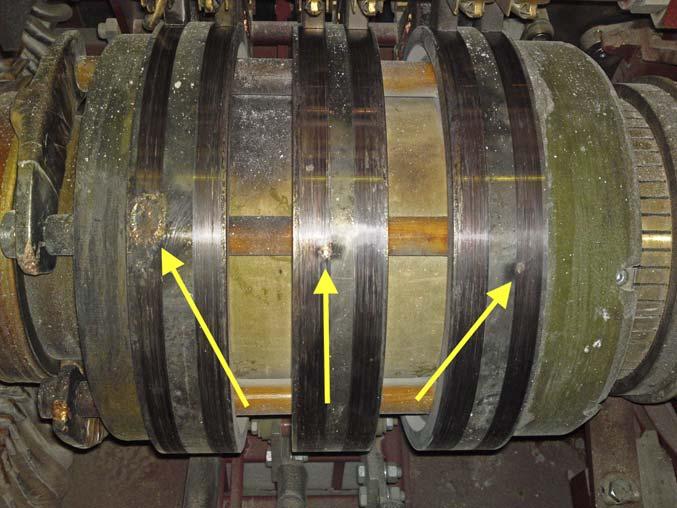
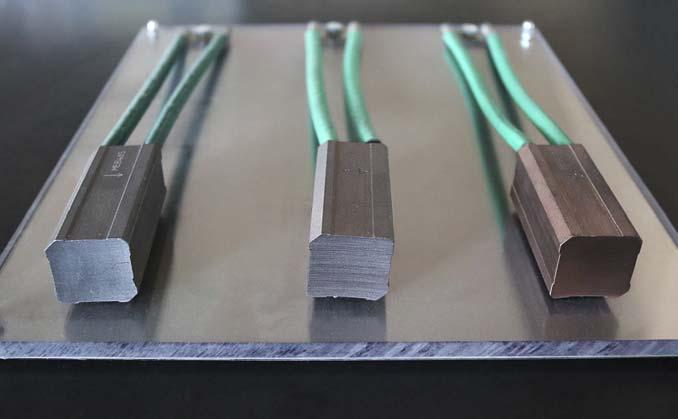
Figure 7. These slip rings show severe damages in multiple places due to a brush-lifting device failure, arcing and fl ashover.
Figure 8. Different, application-specifi c material compositions ensure long brush lifespans in different climatic conditions.
Figure 9. The slip ring compartment in a Menzel-designed motor without brush lifting provides easy maintenance access through two large service windows. Conclusion
Brush lifting avoids brush use, but at a high price. There are high additional costs for correctly installing and maintaining short-circuiting and brush-lifting devices. Especially in cement industry applications, there is no reason to employ brush lifting since the cost-saving potential is small and far outweighed by the risk of causing motor failures. Customers can avoid this risk and ensure higher availability of their motors by sourcing high-quality brushes and regularly servicing them – at comparatively little costs and effort. Optimal application-specifi c brush selection ensures longtime safe operation and minimal lifetime costs.
About the author
Mathis Menzel is the CEO of Menzel Elektromotoren and the grandson of the company’s founder. He has a degree in electrical engineering from the Technical University of Berlin. His university career included studies abroad, including at the University of California, Berkeley. After gathering professional experience in England, France, and Spain, he joined the family-owned company in 2005 as Chief International Sales Manager. In 2007, he joined his parents in the top management. In 2010, he became the company’s sole owner.
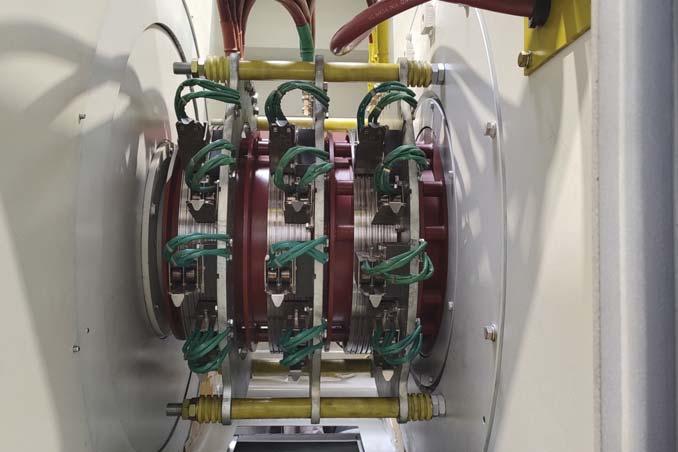