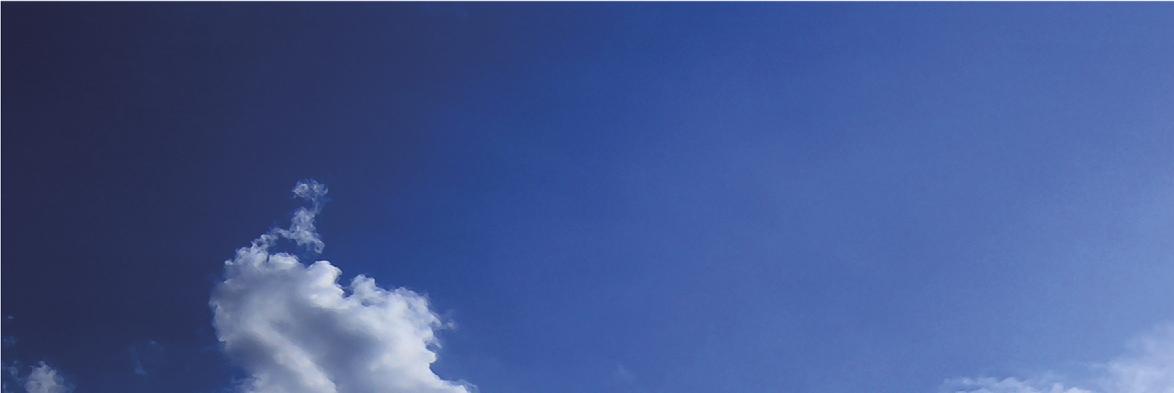
7 minute read
India: Striving For Sustainability
INDIA:

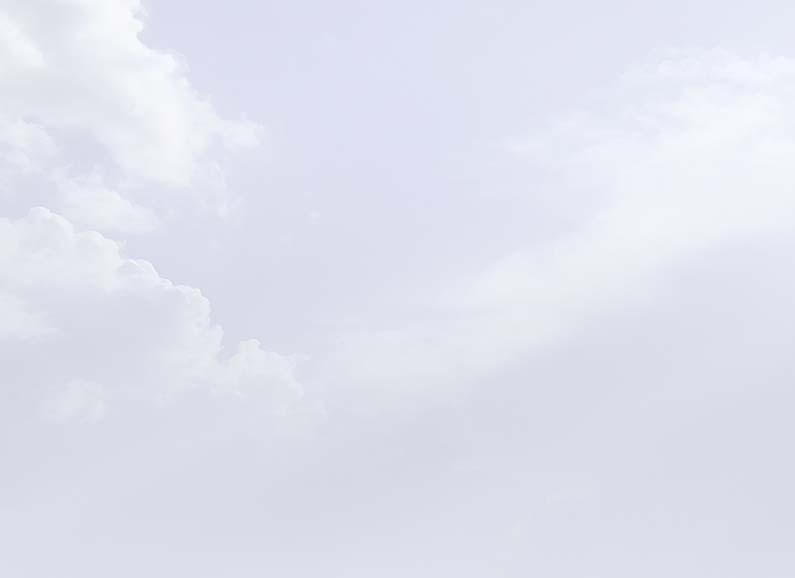
STRIVING FOR STRIVING FOR SUSTAINABILITY SUSTAINABILITY
Dr. S. B. Hegde describes the major strides the Indian cement industry has recently taken towards achieving sustainability and a circular economy.
India’s vision is to become a superpower and to have a robust economy which is primarily dependent on the growth of its industrial sector, with cement being the most produced commodity. In India, the major cement consuming sectors include housing and real estate (65%), infrastructure (25%), and commercial and industrial development (10%).
From 2018 – 2019, India had an annual cement consumption of 337 million t and this is expected to increase up to 550 million t by 2025. This increase is attributed to various developmental schemes launched by the Government of India, including the Smart City Mission, Housing for All, Bharatmala Pariyojana, Pradhan Mantri Gram Sadak Yojana, Urban Transport Metro Rail Projects, etc. Aided by suitable government foreign policies, several foreign players such as Holcim, HeidelbergCement, and Vicat have invested in the country in the recent past. The per capita consumption of cement in India is 240 kg, which is well below the global consumption of 530 kg (DIPP, 2020). This signifi es that there is a huge economic opportunity to cater to the unmet demand in future.
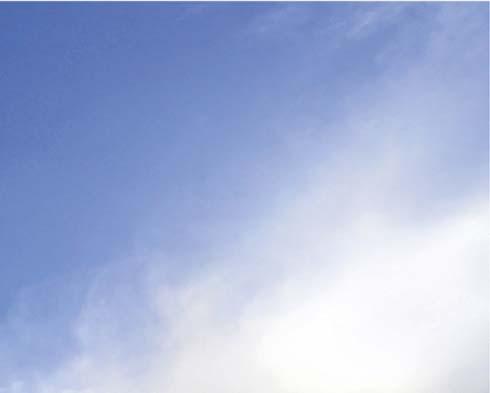
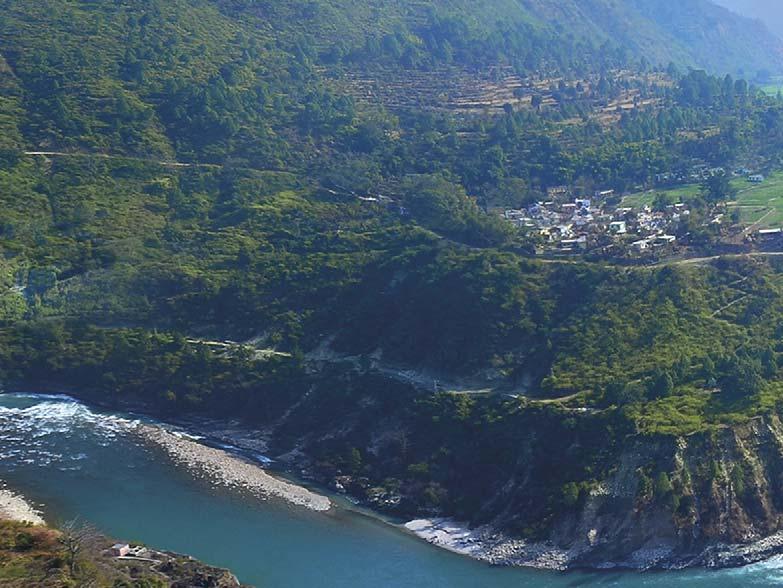

Signifi cant improvements in plant operational parameters
Average ‘specifi c heat consumption’ and average ‘specifi c energy consumption’ in the Indian cement industry is 3.1 GJ/t of clinker and 80 kWh/t of cement, respectively, which is less than the global average of 3.5 GJ/t of clinker and 91 kWh/t of cement, respectively. Regarding the energy effi ciency (EE) lever, many energy-effi cient technologies have already been implemented in the cement industry, leaving little potential for decarbonisation. Additionally, to realise the leftover potential in EE, various technologies like waste heat recovery (WHR), installation of highly energy effi cient coolers, grinding systems, and the use of variable frequency drives (VFD) in process fans etc., are being implemented in integrated plants.
Progress in sustainability
The Indian cement industry is considered one of the best performing industries across various industrial sectors in terms of energy consumption, quality control and assurance, and environmental sustainability, and is adaptive in terms of venturing into new technological options. Some of the recent major strides of the Indian cement industry include the reduction of the CO2 emission factor from 1.12 t of CO2/t of cement in 1996 to 0.670 t of CO2/t of cement in 2017, and enhanced blended cement production from 68% in 2010 to 73% of total cement production in 2017.
Thermal Substitution Rate (TSR) refers to a partial replacement of conventional fuel by alternative fuels in terms of thermal energy requirement, and is calculated as a percentage of heat supplied by alternative fuel from the total heat requirement for pyro-processing in a cement plant. TSR has recently improved to 4% compared to a dismal 1% only 3 – 4 years back. From the TSR level of 4% in 2016 (0.6% in 2010), the Indian cement industry hopes to achieve 25% TSR by 2025 and 30% by 2030. Cement plants have adopted technologies to meet the new emission norms for particulate matter (PM) and NOx emissions.
Plants have installed highly effi cient bag fi lters, electrostatic precipitators (ESPs), and hybrid fi lters to control dust emissions. For NOx reduction, plants have installed secondary control measures like Selective Non-Catalytic Reduction (SNCR). Plants have also installed continuous emissions monitoring systems as per the guidelines of the Central Pollution Control Board. The Indian cement sector is considered an energy effi cient sector, mainly due to the modern technology being implemented in the plants as well as effi cient monitoring of the plants’ performances on a daily basis, focusing on energy savings and CO2 emissions reduction. India’s cement industry growth in next decade looks promising.
The Indian cement industry and potential for a circular economy
The cement industry’s contribution to a circular economy mainly falls under two categories i.e. circular supply chain, and recovery and recycling.
Circular supply chain
The Indian cement industry is playing a key role in contributing towards a circular economy by enhancing the applications of renewable energy for electrical power generation. The renewable energy installed capacity (wind and solar) in cement plants has increased by more than 40% to 276 MW from 2010 to 2017. Of this, 42 MW is solar power, while off-site wind installations account for 234 MW. One cement company has undertaken the target of switching over to renewable energy for 100% of all electrical energy needs by 2030.
Recovery and recycling
It has been established that different types of wastes/byproducts of other industries available worldwide can be utilised as alternative fuels and raw materials for cement production. Moreover, production of blended cements, composite cements and utilising performance improvers in cement also support a circular economy. Use of fl y ash and granulated blast furnace slag (GBFS) in the production of blended cements i.e., Portland Pozzolana Cement (PPC) and Portland Slag Cement (PSC) is also benefi cial for conservation of natural resources, lowering the clinker factor in cement and reducing CO2 emissions along with environmental sustainability.
In the coming years, a circular economy will gain further momentum in the Indian cement industry by utilising gypsum generated from FGD in TPP, consumption of non-recyclable plastic waste, production of high-volume fl y ash cement, utilising steel slag, the reduction of the clinker factor by alternative raw materials, and increasing TSR by the use of AFs.
Usage of alternate fuels
The opportunities for cement manufacturers to start burning alternative fuels are many, but it is a gradual process. Process knowledge is critical when starting up the use of alternative fuels because even the slightest change to one part of the process could create havoc. Many technological aides are available for plants from technology suppliers like Pfi ster, with an Alternative Fuels Starter Kit that comes with a complete package of equipment for materials handling, and dosing and burning, and is designed for using a wide range of alternative fuels like biomass and refuse-derived fuel (RDF). The enhancement of the thermal substitution rate will require adequate pre-processing infrastructure for RDF, both in terms of quality and quantity that will make it suitable for use in cement plants. One of the alternatives to improving the quality of locally generated RDF would be to
blend RDF (which typically achieves an energy value of 1500 kcal/kg) with a better form of RDF known as Solid Recovered Fuel (SRF), which is made from commercial and industrial waste.
Current research towards CO2 emissions reduction
Of late, signifi cant research has been undertaken to develop low carbon cement alternatives like LC3, geopolymer binders, belite rich cements, and other novel cement formulations. Out of these options, LC3 and geopolymer concrete have signifi cant potential for emissions reduction and are in the fi nal stages of development in India.
With the use of circular economy principles (like use of SCMs, and utilisation of construction and demolition waste through technologies like the ‘Smart Crusher’) and design optimisation techniques (like bubble deck/voided concrete slab systems, confi ned masonry, and use of timber) the demand for cement can be optimised in upcoming construction activities.
The way forward
Reducing clinker content and alternate raw materials
It is inevitable that the cement industry will make certain amendments in its current standards in order to accommodate a higher amount of secondary cementitious materials (SCMs) and also opt for new standards in order to accommodate newer cement formulations. These changes in standards would help reduce the clinker component of cement, allowing not only for CO2 abatement but also for mineral conservation.
Further reduction of the clinker factor and the use of alternative raw materials are key in reducing the environmental footprint of the cement industry. To put it into perspective, if it was possible to reduce the CO2 emissions from cement production by just one percentage point, it would be the equivalent of removing the fossil fuel used to provide 258 million households with electricity annually or replacing the use of fossil fuel with 19 000 wind turbines!
Carbon capture and sequestration
Carbon capture systems must target process emissions and combustion emissions. These systems have two categories:
Post-combustion technologies aim to separate CO2 from exhaust gases and typically rely on chemical CO2 absorption (for example, by amines). Oxyfuel technologies react fuel with pure oxygen instead of air, generating a purer stream of CO2, and also can capture process CO2.

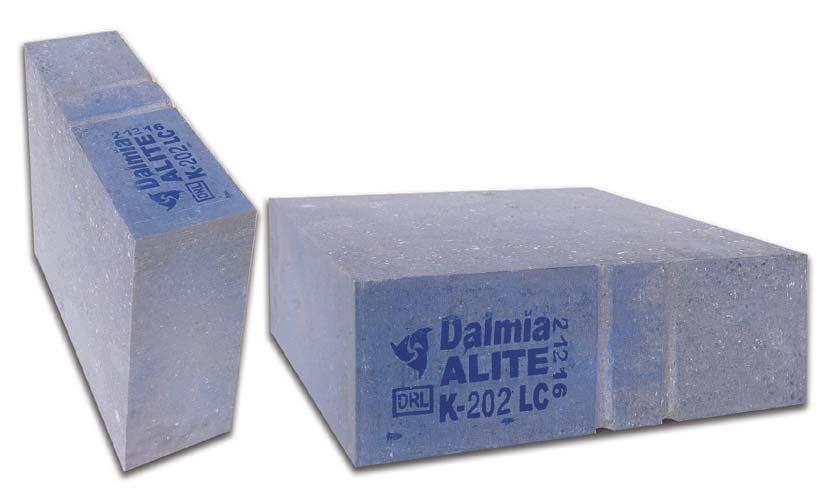
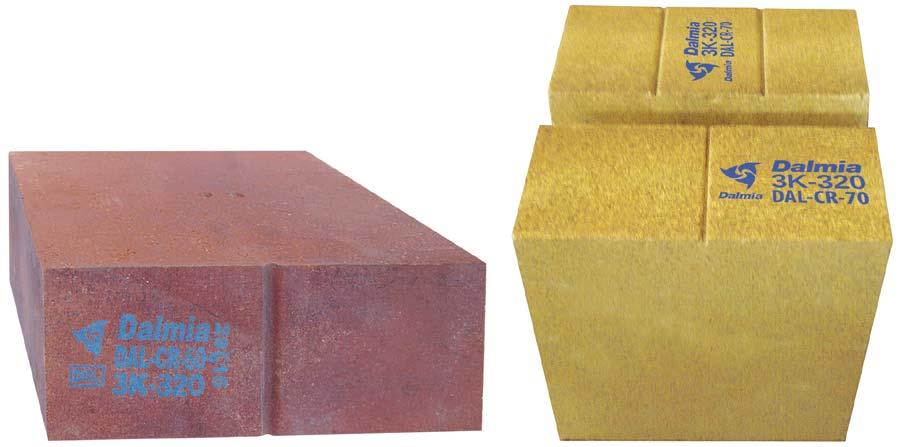
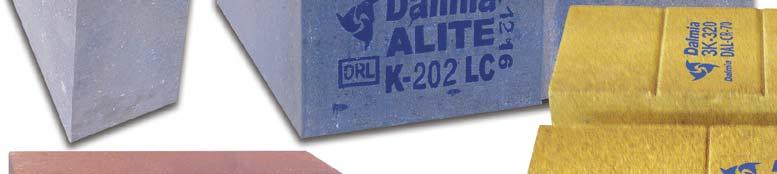