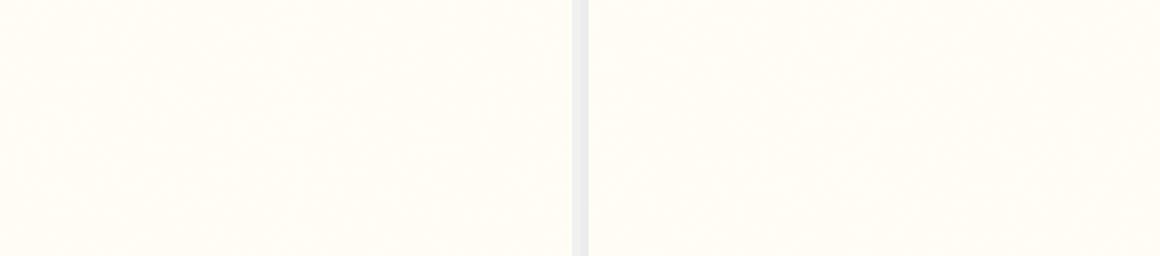
8 minute read
Grabbing Gains
Carolina Vargas and Peter Simons, TOMRA Mining, Germany, explain how methodical testing can show phosphate producers how much silica can be removed from their feed materials to improve yields and lower production costs.


GRABBING GAINS GRABBING GAINS
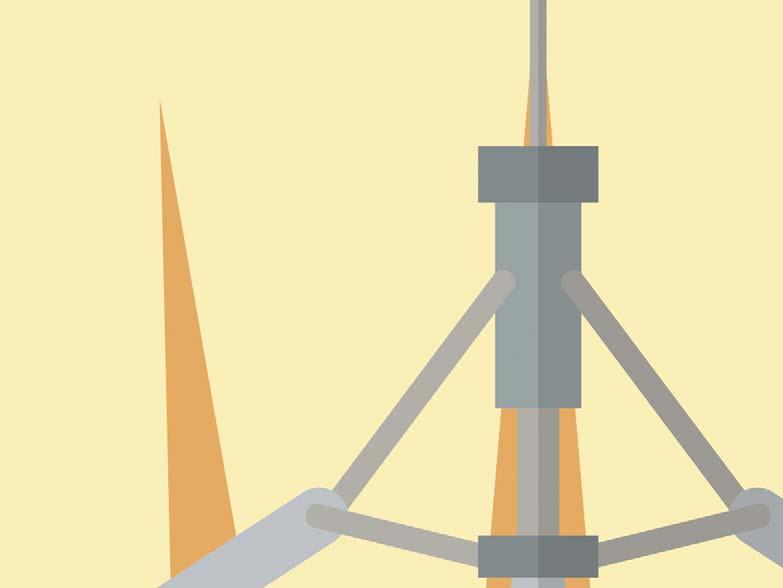

hen producing phosphates for fertilizers, one of the greatest challenges is to reduce the silica content of the mined materials. Though there are several technical solutions, the most effi cient and environmentally friendly is sensor-based sorting. Today’s X-ray transmission (XRT) sorting technology is capable of removing 95% or more of unwanted high-siliceous particles, such as chert and fl intstone, from feed materials. This benefi ts the downstream process by reducing the need for water and chemicals and decreasing maintenance costs. In addition, phosphate recovery rates with single-step sorting are more than 92%, and with double-step sorting recovery rates as high as 99% are reachable.

Figure 1. Example of phosphate (left) and high-siliceous particles (right). The sizing is 25 – 75 mm.
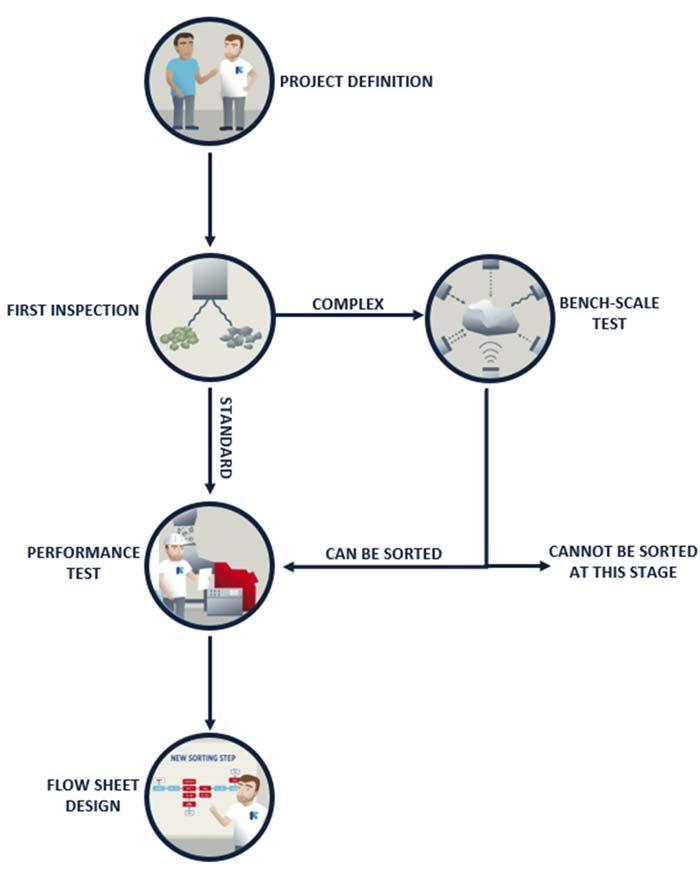
Figure 2. Test work steps.
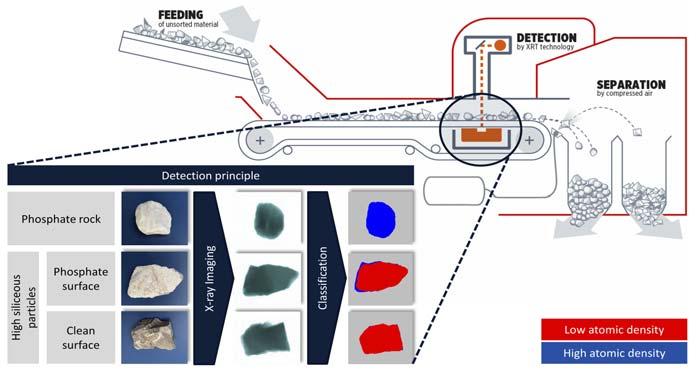
Figure 3. Sorting and detection principle of TOMRA X-ray technology in phosphate application.
Feed materials can vary signifi cantly from one deposit to another, and phosphate producers naturally prefer to see fi rst-hand exactly what can be achieved with their own materials before investing in any sorting machinery. For these reasons, TOMRA works with phosphate producers to demonstrate what is possible through a series of methodical tests.
First steps towards proving results
In the fi rst step, the phosphate producer is requested to answer a few questions covering working conditions, challenges and operational objectives. This information is used by TOMRA’s application department to determine the most suitable testing procedure.
Before the fi rst inspection, the application engineers will already have a good idea which sorting technologies are likely to work best. At this stage, the phosphate producer is required to provide reference sample sets. These typically include a reference sample of product, middlings (neither clean mineral product nor reject/tailings) and waste with 10 – 30 rocks each. These samples are tested with different sorting technologies to establish which is most appropriate for a larger test. Figure 1 shows a ‘product’ and ‘waste’ reference sample for a phosphate application.
If the results of the fi rst inspection are positive, a large-scale test – known as a performance test – is recommended as the next step. This simulates a real process fl ow and determines sorter performance and throughput. The performance test is conducted at one of TOMRA’s four test and demonstration centres solely focused on mining, each of which provides different testing possibilities. There are test centres in Germany, Australia, South Africa and Russia.
During this test, a large mass of sample – typically about 3000 kg of each material type and size fraction – is fed into a full-scale sorter at defi ned capacity. This is an opportunity to test different sorting parameters, such as throughputs and sorting algorithms, with realistic and representative quantities of materials.
After the performance test, the sorted samples are chemically assayed by an independent laboratory. When assessing a phosphate application there is usually also hand-sorting analysis at the laboratory, which gives direct key performance indicators such as removal effi ciency of high-siliceous particles and phosphate recovery. With the laboratory results, the next steps are mapped out in a fl owsheet that takes into account the producer’s working practices and budget (Figure 2).
In some exceptional cases, the phosphate producer might ask for the performance test to be followed up by another, larger-scale test with something like 100 – 120 t of infeed material. This tends to be requested on those occasions when the producer would like the test data affi rmed with even larger quantities of feed materials, and/or needs to further test downstream processes such as crushing, grinding and fl otation.
Seeing is believing
The XRT technology enables the removal of high-siliceous particles, and consequently the reduction of silica in phosphates, by seeing differences in the atomic density of each single particle on the processing line (Figure 3). Phosphate ore has a higher atomic density than high-siliceous particles because of its signifi cantly higher concentration of calcium oxide (up to 55%,
atomic number 20) and lower concentration of silicon dioxide (below 1%, atomic number 14). In fact, silicon dioxide is almost the only component of high-siliceous particles.
These differences are revealed to the sorting machine in the images of the material stream that it captures and instantly classifi es. Figure 4 shows how phosphate ore and high-siliceous particles look different in X-ray and classifi ed images. XRT scans such as these are used during tests and plant optimisation to fi ne-tune sorting algorithms. These algorithms are also tested and, if necessary, further refi ned in accordance with the producer’s feedback.
Using the company’s XRT technology, unsorted material is evenly fed via a screen feeder or vibration feeder over a transition chute onto a conveyor belt. An X-ray tube creates broad-band radiation that penetrates the material and provides spectral absorption information. The transmitted radiation is measured by a highly sensitive X-ray camera with DUOLINE® sensor technology, using two independent sensor lines with different spectral sensitivities. The data supplied by this camera is analysed using a proprietary high-speed X-ray processing unit. Each single particle is classifi ed as having high or low atomic density, regardless of the material thickness or dust and dirt on the surface.
To see theory put into practice, one of the most important steps in the entire testing and evaluation process is the phosphate producer’s visit to the test centre for the performance test. Here, setting up the sorter to achieve an optimum test result is an interactive process involving both TOMRA and the producer (Figure 5).
During the tests, thousands of single particles are scanned individually, evaluated and precisely ejected by air jets within just milliseconds. This is different from traditional dense media sorting (DMS), as it examines each individual particle and detects even very small differences in atomic density. After observing the tests, the producers realise XRT technology is much more high-tech. This provides phosphate producers with signifi cant scope to alter software parameters in order to optimise sorter setup. The technology can also remove more than 95% of high-siliceous particles in the phosphate ore and provides stable sorting performance even at high throughputs.
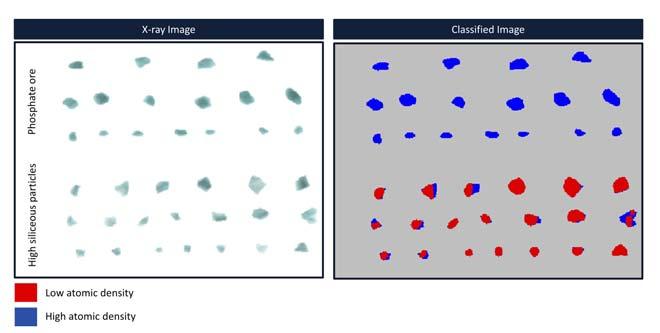
Figure 4. X-ray and processed images showing phosphates versus high-siliceous particles.
Figure 5. Sorter optimisation tailored to customers’ needs.
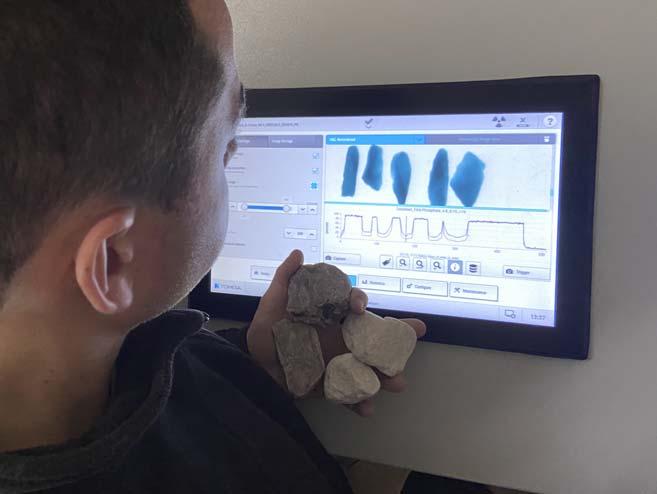
Live demonstrations during the pandemic
For customers who are unable to visit a test centre because of travel restrictions arising from the COVID-19 pandemic, TOMRA organises live online demonstrations of the tests. These are run the same way they would be if the customer were on the premises to witness the test-run in person. Live pictures from the test are streamed from two or three cameras and the machine’s control screen, and viewers are encouraged to direct one of the cameras to look at the aspects of the test they are particularly interested in seeing in more detail. The engineers explain every action and control input they are taking, while the viewers can ask questions. Because the streamed images are recorded, the customer can later share them with other stakeholders in the decision-making process.
Real-world results
A good example of how tests translate into real-world results has been seen at the Wa’ad Al Shamal plant in Saudi Arabia, a joint venture where the leading partner is the Ma’aden Wa’ad Al Shamal Phosphate Co. (MWSPC). A representative sample of 120 t was transported from this plant to Germany in order to conduct performance tests in a particle size range between 9 and 150 mm. Afterwards, the sorted fractions were sent to an independent laboratory for chemical assaying and further test work (e.g. fl otation tests). The XRT sorting results were impressive, and the investors decided on having nine TOMRA XRT sorters for material between 9 and 100 mm, which are removing high-siliceous particles at a throughput of about 1800 tph.
The economic and environmental benefi ts being achieved at this plant are signifi cant. On average, silica content is reduced from 20% to less than 2%, which in turn reduces the costs of crushing by about 75%. Milling costs are also reduced by about 45%. This has the additional advantage of serious reduction of maintenance requirements and downtime in the downstream process.
Effective removal of high-siliceous particles also made it possible from the very beginning to reduce the size of the fl otation plant at Wa’ad Al Shamal by 40%, saving millions of dollars in construction costs and about US$10 million a year for fl otation reagents. Additionally, the consumption of water – in a region where this natural resource is scarce – has been reduced by 45%.
Achieving these valuable improvements at Wa’ad Al Shamal, as well at other plants, would not have been possible without fi rst conducting thorough preliminary tests. What starts with a small grab sample of material can lead to great economic and environmental gains in the processing of phosphates for fertilizers.