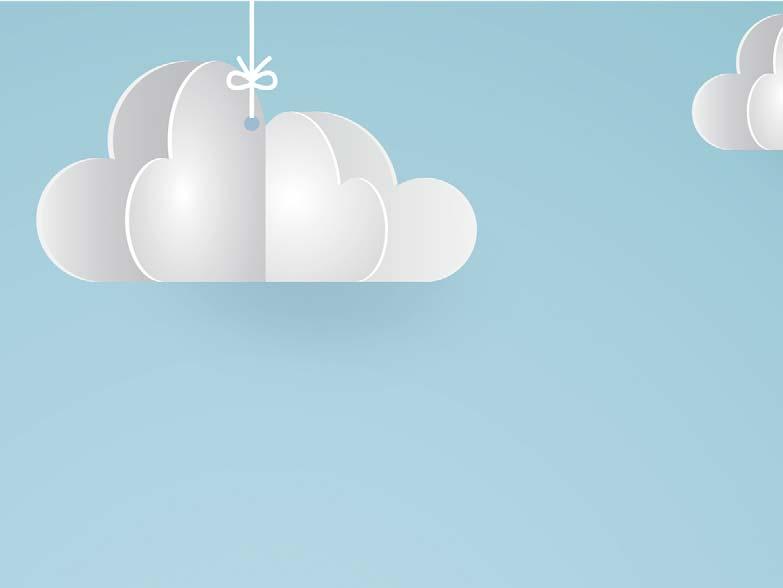
6 minute read
Following The Trends
Barbara Cucchiella and Wilfried Dirkx,
Stamicarbon, the Netherlands, discuss trends in finishing technologies, including larger capacities, lower costs and higher efficiencies.
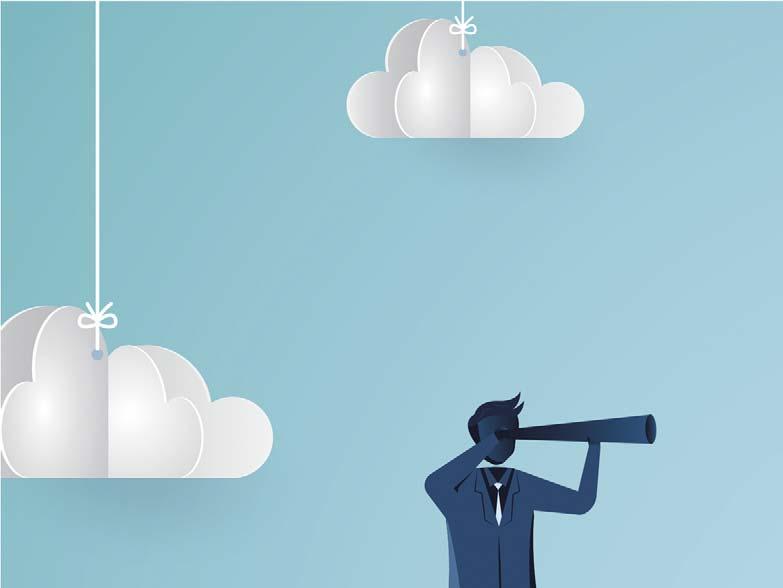

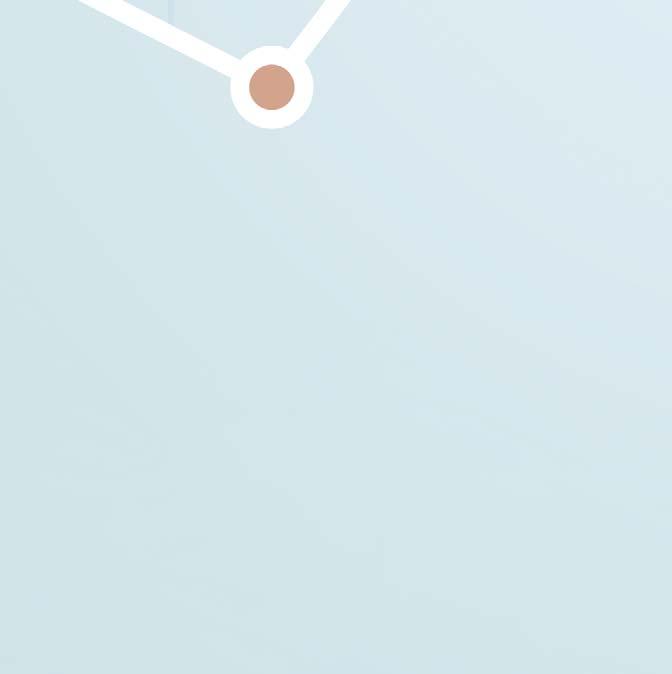
FOLLOWING FOLLOWING THE TRENDS THE TRENDS
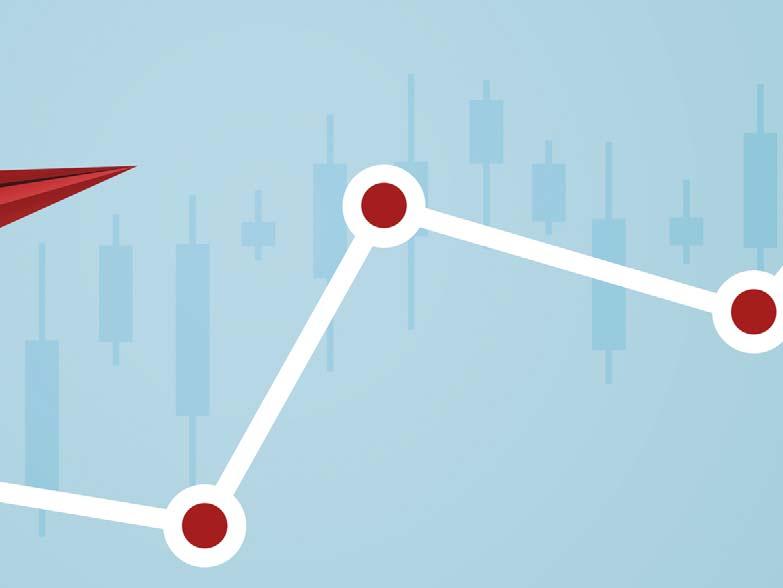
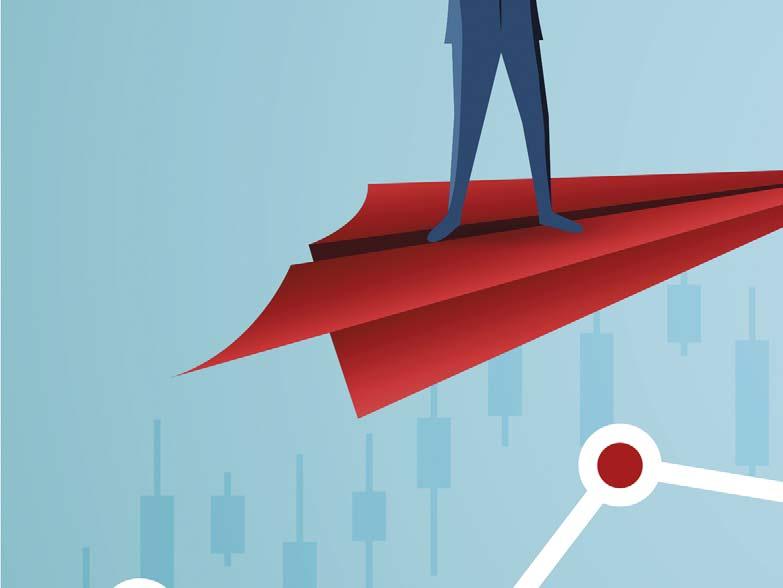
As urea melt plants grow in capacity, so does the need for fi nishing technologies with higher capacities. Although new technology developments have taken place more in granulation than in prilling, the latter is certainly still relevant but will not be discussed in this article.
Stamicarbon, the innovation and licensing company of the Maire Tecnimont Group, has practical experience with both fi nishing technologies, which serve different markets. The decision to go for granulated product instead of prilled product is mainly driven by the interest in export production.
Granules offer a higher strength and better handling and shipping capabilities compared to prilled product, so the construction of urea granulation plants can be found in countries with low feedstock cost areas and options to export the granulated urea product.
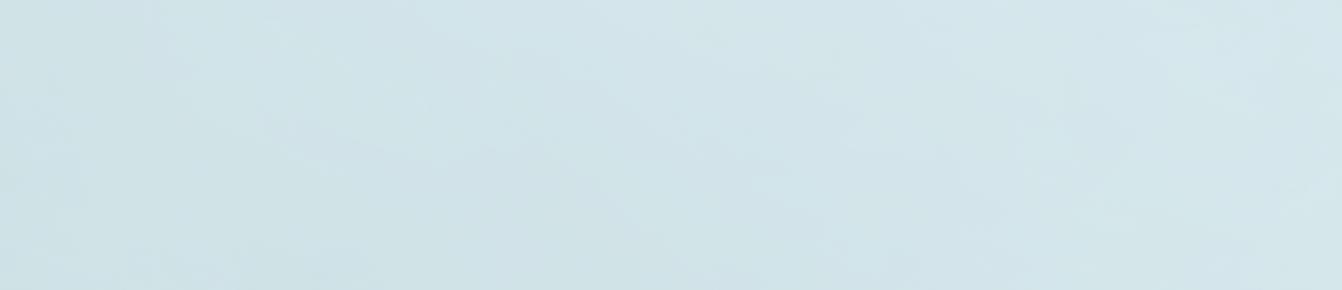
Initial granulation design
After the initial development activities in granulation technology conducted in the 1970s, the fi rst test facility was contracted in 1998 in Belarus, where a small granulation unit of 280 tpd was completely converted to the Stamicarbon LAUNCHTM FINISH Granulation Design. Further scaling up took place in Canada, where two existing granulation lines of 625 tpd were converted to the company’s design. The fi rst grassroot plant with a capacity of 2000 tpd was started up in June 2006 in Egypt. From then on, almost 20 plants with different capacities have been licensed, designed and put into operation.

Compared to other fl uidised bed granulation processes, the Stamicarbon design shows considerable OPEX savings due to a reduced formaldehyde content in the fi nal product and a low dust formation, which results in a granulation plant that can be operated for 2 – 3 months without any interruption for cleaning. The company’s largest granulation plant with its standard design is the Pardis III plant in Assaluyeh, Iran, contracted in 2011 and started up in August 2018. The name plate capacity is 3250 tpd with a capability to operate at 110% capacity and a turndown ratio of 60% of the name plant capacity. Despite the large scale, an on-stream time of more than two months was achieved during the summer period. The plant meets the expectations of the client and operates in diffi cult ambient conditions.
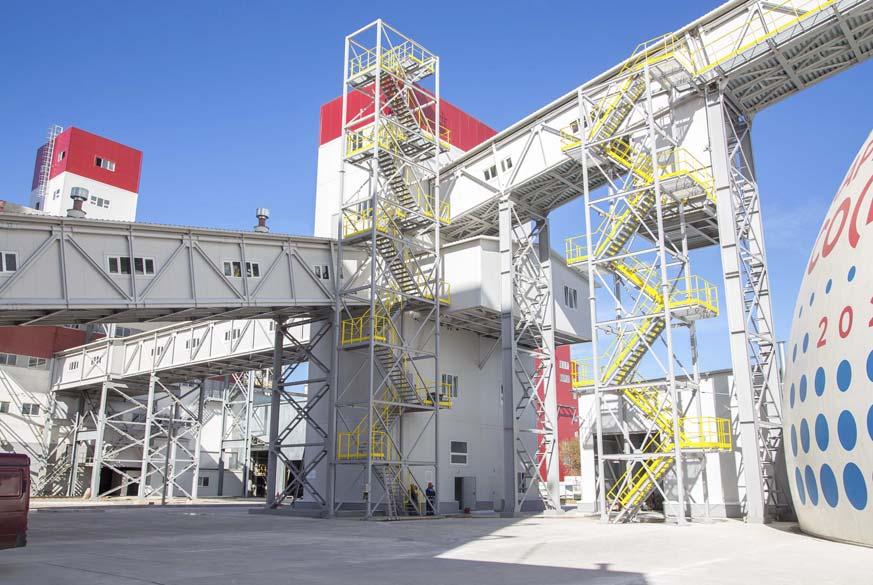
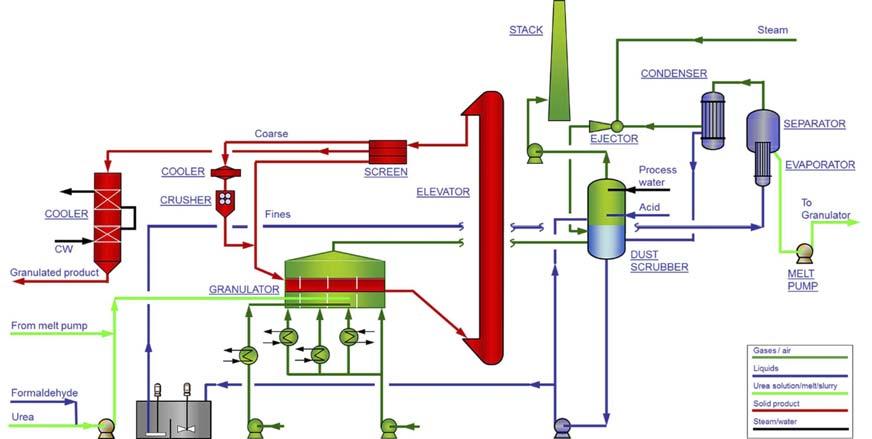
Figure 1. Process flow diagram of the company’s Optimized Granulation Design.
Figure 2. Acron’s granulation plant in Russia.
Figure 3. Stamicarbon’s urea granulation design timeline.
Improved granulation design
In 2008, Stamicarbon introduced its Optimized Granulation Design (Figure 1). The design is characterised by a minimal number of equipment items and a reduction of CAPEX and OPEX costs, while keeping its original performance and high on-stream times.
The cost saving in power consumption is approximately 20% and is mainly due to the omission of three major fl uidisation fans. The fl uid bed granulator cooler was omitted by increasing the length of the cooling zone in the original granulator, and the fl uid bed product cooler was replaced by a solids fl ow cooler. In addition, the respective granulator cooler scrubber with all necessary pumps and fan were omitted as well. The produced granules are cooled down further in the fourth compartment of the granulator, so only a small crusher feed cooler (fl uidised bed cooler) for cooling down the coarse product is foreseen as a separate fl uid bed cooler.
Process description
The urea melt is still fed to the granulator as per the standard Stamicarbon design. However, it differs from the previous design in the last compartment, where the granulated product is cooled down to a lower temperature. After passing the lump screen, the product is directly lifted with a bucket elevator to the classifi cation equipment. The complete solid product fl ows via gravity fl ow through the main screens. The coarse product is fed to the crusher after cooling to a temperature of 70˚C. The crushed product and the fi ne recycle fl ow are combined and recycled into the fi rst compartment of the granulator as so-called seeds. The on-specifi cation end-product in the outlet of the main screens is cooled to storage temperature in a solid fl ow cooler that makes use of cooling water instead of cooling air. The dust-loaded air
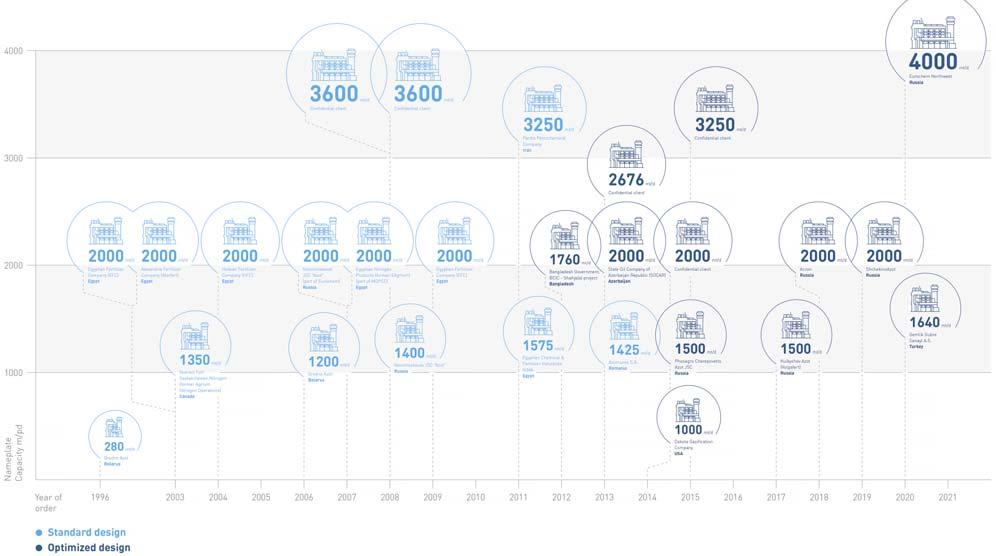
from the granulator, coarse cooler and all the de-dusting points is collected and fed to a single granulator scrubber.
Furthermore, to reduce the amount of fl uidisation cooling air, a water injection system is provided in the discharge of the fl uidisation air fan. This feature is only operated on exceptionally hot days, in order to increase the relative humidity and to reduce the total air consumption as well.
The reduction of equipment items resulted in a signifi cant reduction of the granulation plant footprint and the overall capital cost of the plant. The total CAPEX cost reduction is not only achieved by eliminating equipment, but there are also savings in transportation (shipping) costs, cost of insurance, effect of reduced footprint and construction. Less operational equipment will also result in a reduction in maintenance costs and OPEX savings.
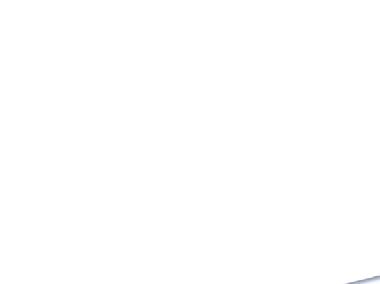
Operational experience
The fi rst granulation plant with this new design was a 1760 tpd plant for Shahjalal in Bangladesh, commissioned in 2015. It started up smoothly and the plant still operates reliably, with minimal operator attention required. The power consumption meets expectations and is 20% lower than in the conventional design, while the maintenance costs have been reduced signifi cantly.
The product exceeds the standard commercial quality, even at formaldehyde levels lower than 0.3% in very humid ambient conditions.
Additional practical experience with this optimised granulation design has been gained with fi ve other plants in operation, varying in capacity from 1000 – 2676 tpd, while there are six other plants under construction. The latest granulation plant that went into operation, in 2020, is a plant operated by Acron in Russia, with a capacity of 2000 tpd (Figure 2).
Scaling up capacity
Over the last decade, the company has seen a rapid increase in the design capacity for granulation plants (Figure 3). All operational granulation plants – although with different product requirements, different ambient conditions, different emissions and with different confi gurations – have met the set performance guarantees.
Recent practical experiences with Stamicarbon granulation plants with capacities above 3000 tpd are positive, meeting the overall and on-stream factor expectations of clients. The next milestone will be the new plant of EuroChem Northwest in Kingisepp, Russia, with a single line capacity of 4000 tpd, which the company is currently designing and is expected to become operational in 2023. This granulation plant will also be equipped with the MicroMistTM Venturi scrubber, meeting the lowest applicable emission standards.
Conclusion

The company’s investigations into the possibility of further scaling up the granulation design over 5000 tpd concluded that there are no actual impediments, provided that a few additional measures are implemented to anticipate the risks of scaling up. Furthermore, a single line of 5000 tpd is estimated to have 30% less CAPEX (on total investment costs) than two lines with a rate of 2500 tpd each.
We understand your processes.
We are familiar with the processes of the chemical industry. With gas-tight designs, high-quality material combinations and proven technology, Venti Oelde offers an all-round reliable solution for every operation.