
6 minute read
Advanced platform for pig tracking
several of these technologies on a single tool ensures the best data alignment while also minimising the number of inspection runs. Specifically, running a combination of DEF, MFL, LFM, SMFL and XYZ – referred to as a multiple dataset (MDS) tool (Figure 2) – then contrasting the results against EMAT (Figure 3) or an alternative crack detection technology improves the characterisation of interacting threats and enables the prioritisation of remedial action.
Once the pipeline enters hydrogen service, routine inspection remains essential to integrity. Minimising the effect of hydrogen on sensitive ILI tools requires significant design changes, including: ) New magnet assemblies to prevent hydrogen intrusion (Figure 1).
) New sealing approach to protect the sensitive electronics and batteries within the pressure vessels of the tool.
) New MFL brushes to support the magnetiser and couple the magnetic flux to the pipe wall.
) A complete reengineering of all high-strength steel components that were in previous designs, including the tool’s body-to-body coupling system.
Table 1. Summary of defects considered important for hydrogen service, and the suggested inline inspection technology to find them
Deflect class Tool technology Defect detection
Mill/ manufacturing defects
Construction defects
Mechanical properties
Mechanical damage DEF - MFL - LFM - SMFL - EMAT/UTCD Many mill/manufacturing defects can be hydrogen-susceptible, including laminations, voids, seam weld defects and spalling. Most can be found by combining DEF, MFL, LFM and SMFL, although there are exceptions that will also require a crack detection technology such as EMAT/UTCD.
DEF - MFL - LFM - SMFL During construction, it’s possible to introduce defects such as dents, gouges, scratches, spalling, wrinkles, ripples, grinding marks and weld strikes. Though not all of these are injurious for gas service, they can present issues for hydrogen. Combined DEF, MFL, LFM and SMFL will catch most.
DEF - MFL - LFM - SMFL Prior to hydrogen service it is necessary to assess each pipe spool for hydrogen susceptibility as well as for anything that is not as per installed or different (rogue). A combination run of DEF, MFL, LFM and SMFL is a good way to achieve this.
DEF - MFL - LFM - SMFL - EMAT/UTCD Mechanical damage in hydrogen pipelines is more critical due to the nature of material changes that make dents more susceptible to cracking. A combination of DEF, MFL, LFM and SMFL and EMAT/UTCD is the best detection solution. Re-rounded dents are also more critical where plastic strain exists; this is something conventional DEF and MFL might miss.
Corrosion MFL - SMFL Although metal loss is important, the shape and class of corrosion is more critical. That’s because long, narrow and sharp corrosion is more susceptible to crack formation due to hydrogen embrittlement.
Trapped hydrogen DEF - MFL - LFM - SMFL - EMAT/UTCD Trapped hydrogen occurs in areas such as mill defects. DEF, MFL, LFM, SMFL and EMAT/ UTCD combined will be able to see defects such as laminations and seam weld anomalies where hydrogen can collect.
Hard spots DEF - MFL - LFM - SMFL Combined MFL, SMFL and LFM has already proven the best tool for hard spot detection. It can produce a hardness map permitting prioritization of hard spots in the pipeline.
Blisters DEF - MFL - LFM - SMFL - EMAT/UTCD Blisters may form as shallow geometric anomalies but then segregate as they get larger. Although geometry tools (e.g., DEF) might be early indicators, combining with DEF, MFL, SMFL, LFM and EMAT/UTCD will determine the extent of damage.
Hydrogen embrittlement DEF - MFL - LFM - SMFL - EMAT/UTCD Hydrogen embrittlement may be seen by the LFM through the change in magnetic response as the steel changes properties. Magnetic technology may also be able to view crack-like features. Pure crack detection combined with DEF, MFL, LFM, SMFL and EMAT/UTCD will provide the whole picture.
Environmental assisted cracking DEF - MFL - LFM - SMFL - EMAT/UTCD EMAT is already being used for crack detection; it will be able to see hydrogen induced cracking (HIC).
Fatigue EMAT/UTCD EMAT/UTCD is already capable of finding fatigue cracks, making it the best solution for cyclic cracking. Given that fatigue in hydrogen grows 10 times faster than cracks in natural gas, frequent repeat runs are required to assess the formation of new cracks.
High bending strains
XYZ mapping IMU included on other tool platforms will also be a mandatory requirement to assess line movement, thermal effects and other loadings inducing strain. High strain = high stress = higher potential for crack initiation and growth. High axial strains Axial Strain/Stress Sensor The primary strain in pipelines is in the hoop direction. This can be easily calculated. and IMU can determine bending strains. However, hydrogen does not care about strain direction, so high axial strains may be much more of an issue, especially combined with girth weld material impact of welding.
TECHNICAL DATA: - ROPS-FOPS CABIN - HYDROSTATIC TRANSMISSION ELECTRONIC TRACTION CONTROLS - FLAT BED * - FRONT OR REAR CRANE * - DUMP BED * - 360° ROTATING DUMP BED * - BOTTLE HOLDER * - PIPE CARRIER (ONLY ON THE SFTs)*


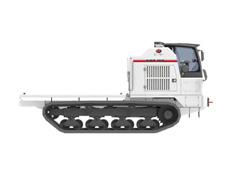
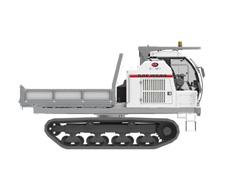
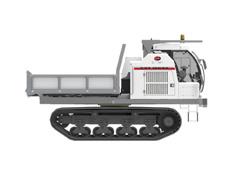

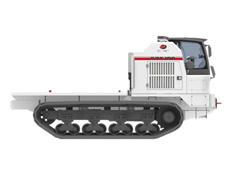


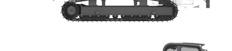

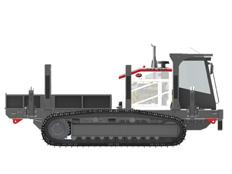
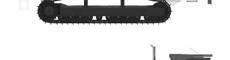
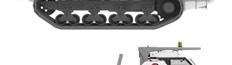
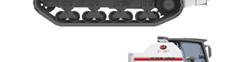
* POSSIBLE CONFIGURATIONS
SRT 155
SRT 180
SRT 250
SRT 155 RD
SRT 180 RD
SFT 105
SFT 155
SFT 180
SFT 350
SCAIP is the original manufacturer of our product line designed over the years and owner of the related know-how. Any other machine that may have a similar design but is not produced by us does not have the same technical features as our products. SCAIP does not give any guarantee on machines produced by third parties.
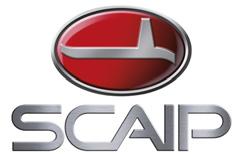