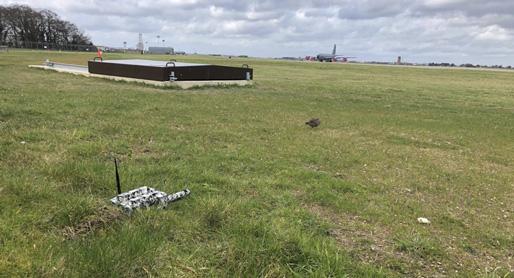
11 minute read
The buzz around drones
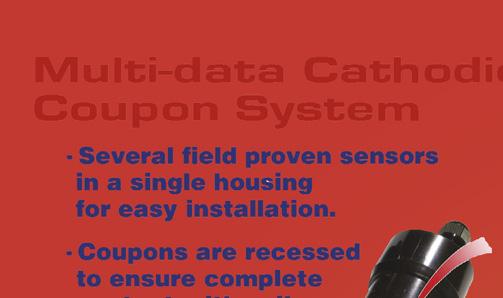

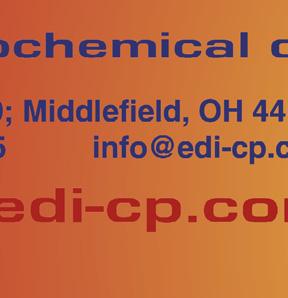
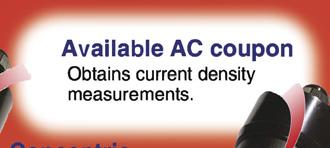
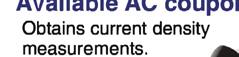
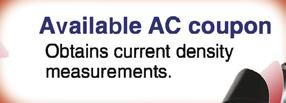
PigView Web allows the user to track real-time pig location online. Users can import pipeline survey data (Figure 2), configure SMS and email notifications, and group all pig passage information from deployed AGMs with surveyed locations so that pig tracking reports are produced instantly at the completion of a run. Users and clients can be notified in real-time of pig launch, pig receipt, pig passage information and even updates on pig speed.
In addition, a real-time data stream and analysis window is part of the PigView Web package. By enabling a streaming session to a deployed AGM (Figure 3) the user can track a pig over the internet as though they were located on site with a handheld receiver and geophone. Real-time graphs of the raw electromagnetic signal, raw geophone waveforms, processed signal strength, and a spectrogram display of received electromagnetic power vs frequency vs time are given. Real-time geophone audio is also provided and streamed into the web browser, enabling the remote user to listen to the acoustics of a passing pig.
Reliable detection In a recent application in the UK, the value of the multi-sensor detection system within the APEX system was truly realised. Upon launching a cleaning pig, the operator confessed to not installing the EM transmitter within the pig, meaning that only tracking by magnets and geophone would be possible. As the majority of the pipeline was buried in depths greater than 2 m, the geophone would be the primary method for detection. With traditional tracking this would have meant that the teams would need to be deployed to listen locally for pig passages. APEX, however, provides the facility to stream this audio live through the web based software, meaning fully autonomous pig tracking could still be performed.
Enhanced safety As discussed previously, the conventional method of pig tracking is to set up tracking locations and move down the pipeline with the pig. This
Figure 4. APEX deployed at a remote location.
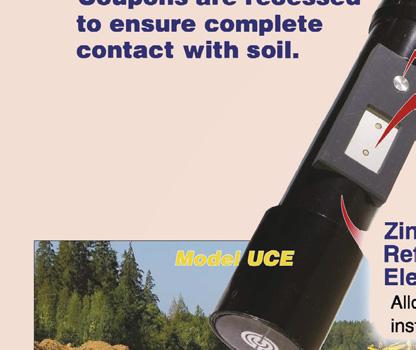
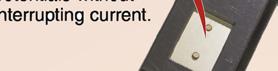

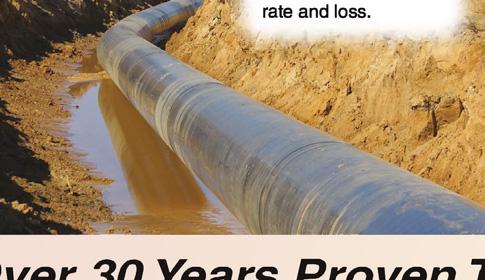


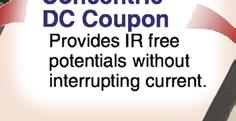
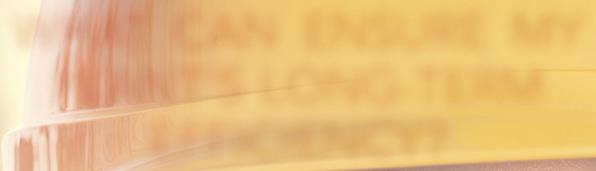
WHAT CAN ENSURE MY PLANT‘S LONG-TERM EFFICIENCY?


EXPERIENCE!
The know-how of more than 60 years in valve manufacturing empowers Böhmer to build Ball Valves that help successfully for the long term.
1/8 TO 56 INCH OIL, GAS, STEAM, CHEMICALS & SPECIAL APPLICATIONS UP TO 800 BAR
Length of pig run Recent projects have had pigging runs spanning over a several days, meaning that both day/night shift crews are required to track the pig. Long hours and working in the dark present safety challenges.

Pig speed For some pipelines, speed control of the pig is unpredictable or subject to change. Therefore, sometimes resulting in the tracking team having to ‘chase the pig’ in order to catch up – which can lead to safety incidents.
Tracking location Onshore pipelines can traverse remote locations, leading to these sites being more difficult to access and reducing the time the pig tracking team has to get into position (Figure 4).
Utilising the APEX system, the risks outlined above can be significantly reduced by tracking the pig remotely. The pig tracking technicians are only on site when the pigging run is ‘offline’ to deploy the equipment, therefore minimising risk associated with ‘pig chasing’ and also 24 hour working.
Reduced costs Using traditional pig tracking methods that utilise teams of technicians can be expensive and can introduce risk. During remote tracking runs that utilise APEX, a technician is only required to deploy and collect the equipment. The management of the pig run itself is performed online by a single user. All of this results in a reduction of: ) Manpower and therefore cost.
) Vehicles required to transport technicians.
) Environmental footprint.
When using remote tracking methods, the cost savings are not only reflected in reduced technician hours, but also in terms of reduced costs relating to reducing travel, etc. It also eliminates the need for long field shifts and night shifts, making it the safe alternative to traditional tracking. While many pipeline companies still use traditional methods, bestin-class integrity programmes are now leveraging remote pig tracking to reduce cost and increase safety.
Internet based pig tracking The use of Propipe’s APEX internet based pig tracking system has been proven to reduce the costs and risks associated with deployment of pig tracking teams on projects. Furthermore, the live streaming of data has resulted in more accurate and reliable tracking of pigs. When considering projects with long pigging runs or multiple pigging runs concurrently, then the system provides a significant advantage. There may be occasions when traditional methods can still be employed but the future of pig tracking is certainly internet based and APEX is leading the way.


Morgan Sledd, Stark Solutions, USA, explores a range of closure technologies suitable for different pipeline applications.
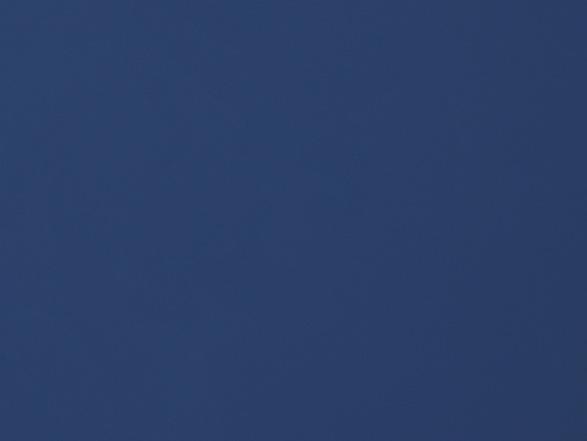
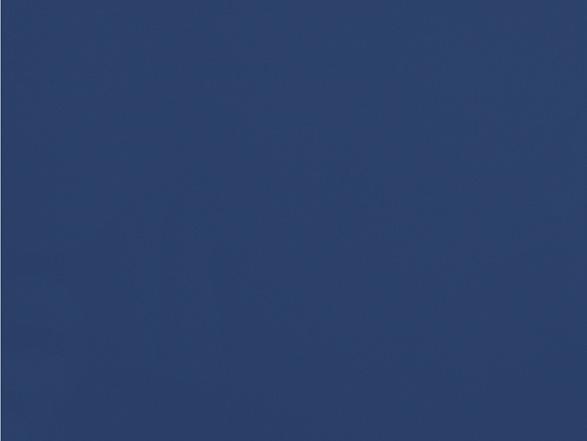
The pigging and tracking of inspection tools in pipelines have a variety of technologies and options. These options start, and end, with how to get the tools in and out the pipelines. Quick opening closures can be chosen and configured to help work with the pipeline operators’ needs.
The first way to optimise the process is to choose the right closure for the application. The main types of closures include threaded, clamp ring, and internal door. Each type has its own strengths and selecting the correct type can play a part in keeping the pigging operation safe and efficient for everyone involved.
Threaded closures like Stark Solutions S-500 are easily identified by the fact the door (commonly called the cap) screws on to the mating portion welded to the pipe (commonly called the hub). The appearance of the cap and hub vary, but generally come with an o-ring seal and some sort of hinging to hold the cap’s weight, when the weight becomes a safety issue. Like most closures, they come with a warning device to prevent the cap from being opened while the closure is under pressure, keeping the operator safe from accidental or unintended pressure release. These closures can be used in applications sized from 2 in. (DN50) through 52 in. (DN1300), in a variety of pressure ranges from full vacuum all the way up to 3705psi (25.5MPag) operating pressure. As the units increase in size, a variety of options become available. These include additional port openings for valves or sensors, as well as the ability to be specified in horizontal, vertical, or inclined applications.
The ease of operation, and the intuitive nature of the opening and closing operations have helped to contribute to the popularity of this type of closure over the many years it’s been in the industry. Also helpful is the often cost-effective nature of this closure’s design, as it has only two pressure parts. These parts are typically low weight as well, compared to the other closure types, making them a favourite in applications where overall project weight is a consideration. Either the cap only, or both components (cap and hub) can be provided with ASME BPVC Section VIII, Div.1 U-stamp should the application require it. While this closure therefore has a very robust design, the threading and unthreading of the unit does require that it is properly maintained with each opening, including greasing of the threads. While this style of closure doesn’t lend itself to stainless steel construction, as the threading and unthreading can gall or damage the threads, with proper preventative operational steps, stainless or alloy materials can be entertained and discussed for quote.
Clamp ring closures have a clamp that holds the hub and door components together, as seen on the Stark Solutions S-2000. Once the safety device is properly operated, these
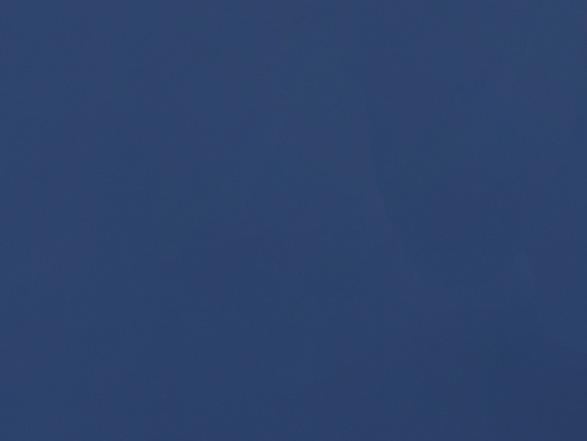
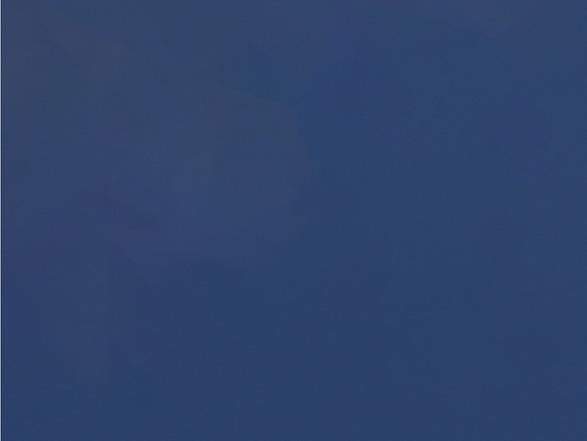
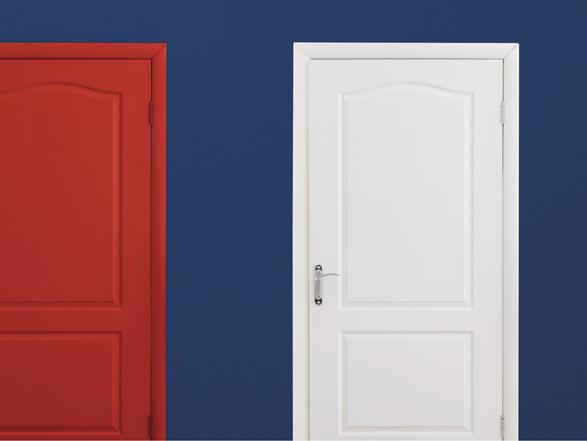
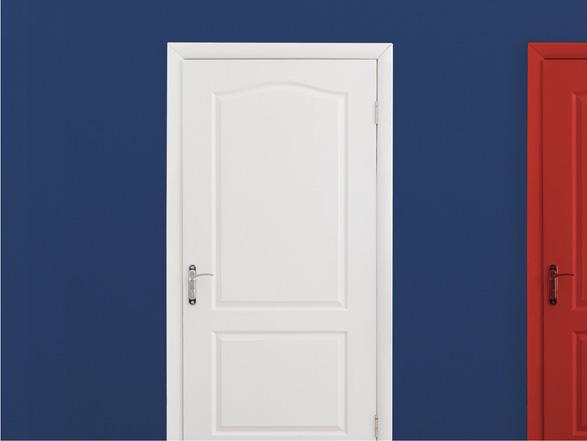
closures often have rapid opening and closing times due to simple latch mechanisms providing the clamping and unclamping action. These closures also have an o-ring seal, allowing for many o-ring materials to be chosen, depending on what the application requires. This closure has a large cross section o-ring to help achieve sealing when the surfaces have small amounts of surface corrosion or pitting. Most often built to ASME B31.8, B31.4, and B31.3 pipeline requirements as a standard, the ability to U-stamp the door exists, as well as the option to have a fully stamped closure should the application require it. These closures are most used in horizontal applications but have been seen in some specialty vertical applications as well. Since they are side hinged, the closure hinging direction needs to be specified. Starting at 4 in. (DN100) in nominal size, and going up to 48 in. (DN1200), the variety of sizes makes them a good choice for most pigging applications. These closures are readily available for pressures ranging from full vacuum to 2220psi (15.3MPag). Having a flat door face, these designs will be heavier than the threaded closures on a size-to-size comparison, but typically have an easier-to-operate singe pivot point hinge that makes opening simpler, and adjustments easy. The flat door provides a large surface for additional port options, and also keeps the overall length of the closure shorter than a threaded closure. Due to the nature of the heavier steel, and the three pressure retaining components (hub, door, clamp), this closure type is generally more expensive than the threaded closure. Unlike the threaded closure, there is no rubbing of components together during the opening and closing cycles, so all acceptable metal varieties can be considered in the quoting process, and most maintenance steps are done externally (no thread greasing).
Internal door closures, of which the Stark Solutions S-3000 is one, are characterised by a door that is inserted into the hub, and then a ring or series of ring-segments expand to prevent the door from being removed. Due to the nature of the closure, the doors are slightly smaller than the clamp ring products, but the hubs are larger. The safety devices on these closures are generally an integral part of the ring expanding/ collapsing mechanism to ensure that the ring can’t be disengaged without being made aware of any residual internal pressure. A great benefit to this design is that if the operation mechanism fails, the closure will not open due to the ring still being expanded in place. This is often referred to as a fail-safe design. To handle the weight of the door and ring, the hinging is usually more robust. The hinging on these units also typically have more than one pivot point, allowing the door to be controlled more easily while being inserted into the hub. The internal door closures are offered with o-ring seals that work well with full vacuum and pressures up to 2220psi (15.3MPag) or with lip seals that work better in higher pressure applications. These closures are ideal in applications where frequent use and high pressures are common.
The flat doors provide much the same advantages as the clamp product do with regard to being able to add additional ports. These closures also benefit the job when corrosion resistant materials are requested, as they are robust enough to have weld overlay added easily or can be made completely from the specialty materials. Due to their robustness, these closures are often the heaviest, when compared to the threaded or clamp ring. This design does scale very well, allowing sizes ranging from 6 in. (DN150) up to 84 in. (DN2100) and beyond in pressure from full vacuum to 3705psi (25.5MPag). While they are often seen on filter vessels, these closures also work very well on launcher and receiver lines and can be provided with U-stamped doors or a fully stamped closure.
All three closures can be offered already welded onto a flange from the factory, and all can be hydrotested at the factory if required. As standard closures usually are provided with a weld bevel and are welded onto a larger assembly, it’s considered best and most cost effective for the fabricator to perform the hydrotest. Additionally, since the closure is typically welded, customer specific paint jobs are recommended to be done after fabrication but can be done by the factory if required. The reason for this is that the welding process, as well as various handling processes, usually damage the coating. Hydrotesting and special coatings make more sense if the closures are shipping from the manufacturer already welded to a flange of course.
Each closure has its own strengths and operational conditions that should be considered when choosing what closure is to be used. It is always recommended to contact the supplier if there are questions, or custom requests, and Stark Solutions has inside and outside sales staff, along with dedicated engineering support, ready to help answer questions or quote to meet project requirements.
Figure 1. From left to right: Stark Solutions’ S-500 Threaded Closure, S-2000 Clamp Ring Closure, S-3000 Internal Door Closure.