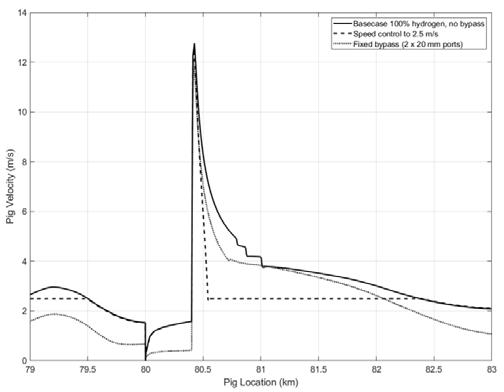
21 minute read
Game changing surface software
Figure 7. Modest fixed bypass can result in a large percentage bypass by flow. Pigs need to seal well for use in hydrogen – to guard against leakage and stalling. The ability to control the pig velocity may be possible with active bypass control (using a control valve and feedback loop).
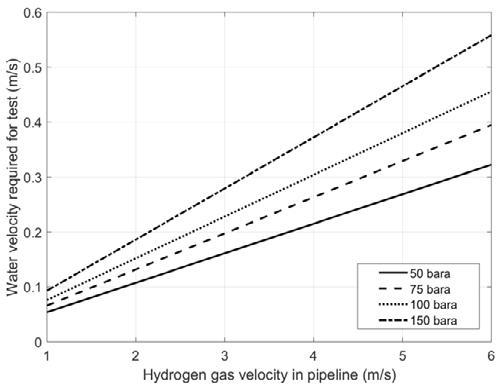
Figure 8. Curve for equivalent water velocity for test against actual expected pigging velocity in the pipeline. For instance, if the pig is expected to move at 3 m/s in a 100 bara hydrogen line, then the tests should be performed at 0.3 m/s or less.
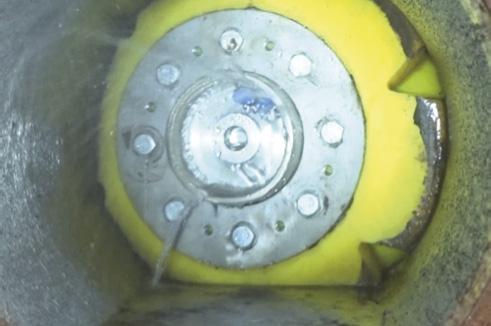
Figure 9. Still from video of open-ended test showing pig negotiating a bend and leakage through the pig body and bolts. This leakage would be difficult to measure using a flowmeter and pig signallers due to errors. Where:
Figure 8 provides an example.
Any leakage paths through the pig body during the tests can be eliminated using silicone sealant and capping off bolts once the final pig configuration is determined.
Testing should be performed open ended to get a clear view of the front of the pig and assess visually any leakage. The aim should be for no visual leakage (with bypass blocked to assess any leakage). Open ended tests require that any air is vented from the pig launcher prior to commencing the tests. If this is done, then the pig should be under control and can be assessed by photographs, visually and using a video camera.
Wear of sealing discs and components may be a root cause of leakage which may not be apparent until the pig is run in the line. Since the hydrogen is expected to be dry and not provide any lubrication for the seals, then this is another aspect that needs to be considered.
Summary Initial output from a review of pigging in hydrogen pipelines shows that pig motion can be more difficult to control because of the low gas density. Minimum operating pressures may have to be higher or use of tools with lower pig DP and changes in DP (a ‘lighter touch’) would be advantageous.
The consequence of increasing hydrogen content produces peak velocity excursions up to three time that of a 100% hydrocarbon line equivalent. This can damage to the tool or the pipeline. An assessment of velocity must be included in any risk evaluation. Higher pressures can aid the situation but may not be possible. Bypass has the potential for reducing tool speed as the lighter hydrogen gas can pass through the pig efficiently. This makes speed control a possibility even on low friction tools.
This indicates another problem that needs to be considered carefully. Low density means that gas can leak past the tool and cause the pig to stall in the line. Any bypass through the pig must be carefully engineered and other possible leakage paths eliminated. Testing at low velocity and open ended with water is an effective method to understand the problem and make the pig work as required. Other factors such as wear and material selection required to be understood but are not included in this paper.
Vwater, test = Equivalent test velocity using water drive.
Vhydrogen, pipeline = Expected flow velocity in the hydrogen pipeline. ρgas = Density of hydrogen in the pipeline. ρwater = Density of water.
References
1. ‘Injecting hydrogen into the gas network’, a literature search, UK Health and Safety Executive, RR1047, 2015. 2. ‘HyDeploy: The UK’s First Hydrogen Blending Deployment Project’, Journal of Clean Energy, Vol. 3 Issue 2, June 2019. 3. BARKER, T., TD Williamson, ‘Inline Inspection Tool Design and Assessment of Hydrogen Pipelines’, PPSA Seminar 2020. 4. HASSANPOURYOUZBAND, A., JOONAKI, E., EDLMANN, K., HEINEMANN, N., YANG, J., ‘Thermodynamic and transport properties of hydrogen containing streams’, Nature.com.

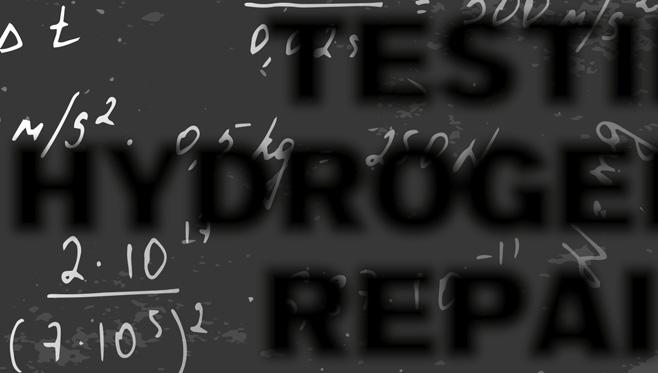
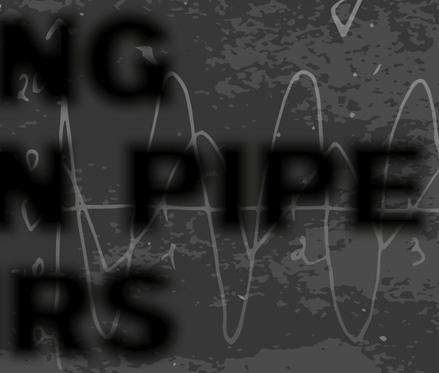
In the second of a two part series, Harri Williams, University of Edinburgh, Derek Muckle, Radius Systems Ltd, and Angus McIntosh, SGN, discuss the assessment of polyethylene systems used for hydrogen gas distribution.
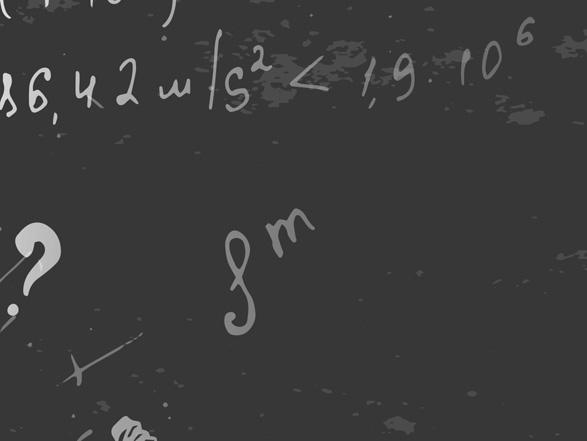
In the following article, the results from testing repairability and leak tightness of polyethylene (PE) systems are reported. The investigation provides evidence to support the quantitative risk assessment on the suitability of connecting fittings and welding practices for use in the distribution of hydrogen gas. The construction of a bespoke leak tightness testing facility within a laboratory environment has allowed the safe testing of sample products using pressurised hydrogen gas. Results demonstrate evidence that contemporary PE materials exposed to hydrogen can be repaired, altered and diverted (with connecting joints) with normal industry practices, ensuring the lifetime expectation of at least 50 years is upheld. The work was scoped and funded by SGN, a UK gas distribution company who supplies gas to over 5.9 million customers. The work is essential to support the case for safety for the first of a kind H100 project from SGN who seek to deliver hydrogen produced by renewable energy to 300 homes in Fife, Scotland.
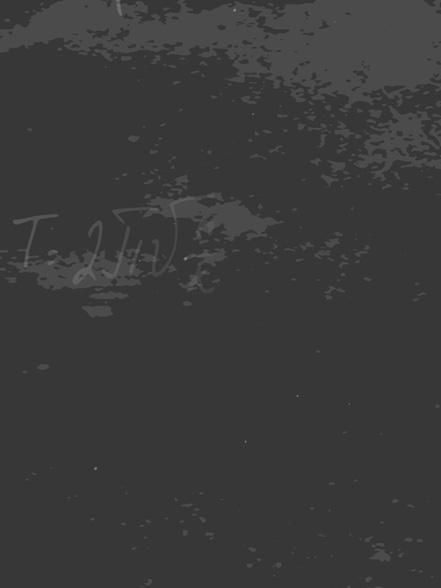
Leak tightness The UK gas distribution networks are currently replacing old ageing metallic gas mains and services to PE as part of the Iron Mains Risk Reduction Replacement Programme. Therefore, ensuring hydrogen gas can be distributed safely with no
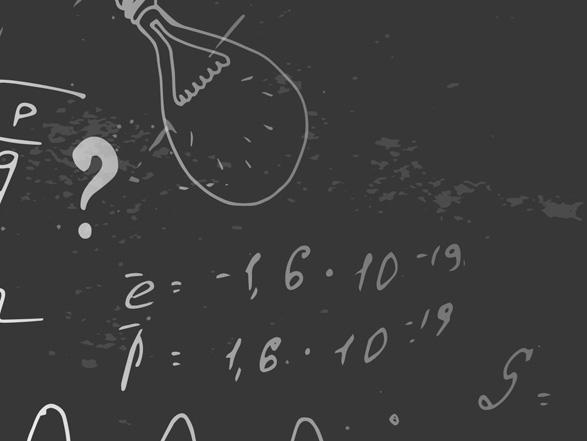
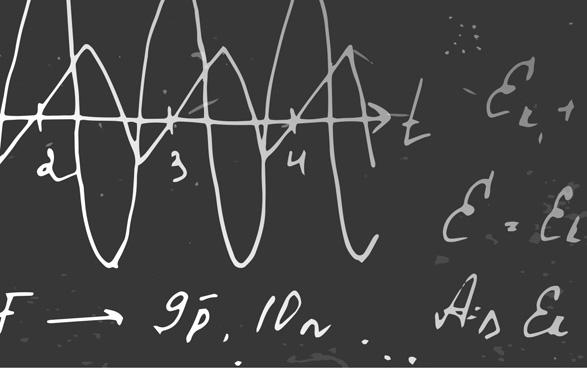
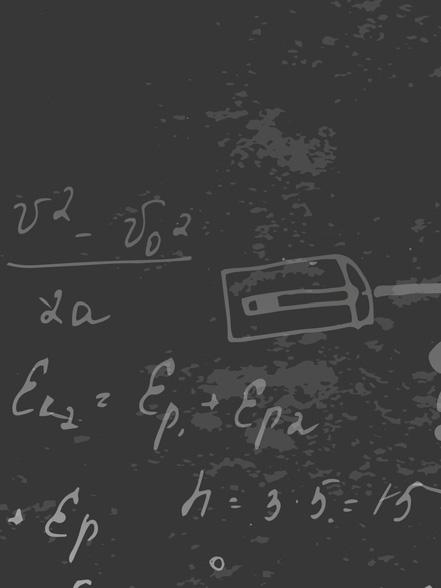
adverse effects to contemporary PE materials, connections and fusion types is paramount to decarbonisation of the gas network and ultimately a ‘net-zero’ future. Due to the physical properties of hydrogen being different to methane (the main constituent of natural gas), leak tightness with joints and fittings needs to be investigated. Electrofusion tapping tee saddles (Figure 1) are used to connect the gas distribution main to the service pipe connected to habitable dwellings. They are the most frequently occurring type joints to be proximal to habitable dwellings and therefore pose the most likely prospect to exhibit a leak. An elastomeric sealing ring (present below the top screw cap) (Figure 1) is the primary means of providing a seal from the top of the fitting. The fitting is described in the gas industry specification GIS/PL2-4, which also describes the fittings long term stability for leak tightness. Testing will demonstrate the leak tightness of the fitting with regards to hydrogen gas.
Future connections by welding Polyethylene pipes will undergo alterations and repairs throughout their operational lifetime due to property developments, network diversions and expansions. They will therefore likely be subject to flow-stopping techniques and welding operations. Connecting techniques must be adequately sealing without damaging the structural characteristics of the original PE material. The ability of PE material to perform future connections and repairs using electrofusion welding techniques after the long-term exposure to hydrogen gas was assessed. During repair or connection-welding the primary risks considered were: ) The risk of ignition, charring or blistering of the PE material as a consequence of prior hydrogen saturation. This would pose a direct health and safety risk to the field operative as well as risk damaging PE materials and connections.
) The absorption of hydrogen into PE pipes over time has the potential to react when future repairs or connections are made. This has been observed during the transportation and subsequent absorption of liquid propane gas (LPG). During subsequent repair, the PE pipe has been shown to swell in the area of welding, due to the reaction of the absorbed gas constituents. This phenomenon has been shown to create defects and resulting areas of slow crack growth development within the welds and connecting areas. This process is regarded as one of the most likely modes of failure within
PE pipelines and therefore testing these practices is vital for future asset management.
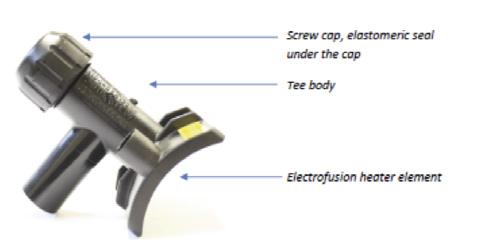
Figure 1. Electrofusion tapping tee saddle fitting. Methods of assessment
Leak tightness Leak tightness testing of the tapping tee fittings is conducted on the fitting closure cap (Figure 1). Leak tightness testing has been conducted in accordance with GIS/PL2-4 leak tightness testing. Three tapping tee cap specimens manufactured by Radius Systems Ltd have been selected from a single production batch. Tapping tee fittings are first installed in accordance with Radius Systems installation instructions. Tapping tee caps are then tightened to a maximum torque of 4 N.m. The fittings are internally pressurised with air at 4 bar for a period of 24 hours. A leak is detected by immersing the fittings at a depth not exceeding 250 mm in a water bath. Any leak, defined as ‘the appearance of a bubble or steam of bubbles from the cap’ is captured with a tube positioned over the bubble source. Leakage volumes are then calculated. Specimens are maintained at a temperature of 23˚C throughout the testing procedure. Tests are then repeated using hydrogen as the pressurising gas. Tapping tee caps are tightened to a torque of 4 N.m and 6 N.m with all other experimental procedures remaining the same. To conduct these tests using hydrogen, a bespoke system has been designed for the tests to be conducted safely in a laboratory environment.
Repairability 63 SDR 11 PE80 pipes were exposed and saturated with hydrogen to replicate the PE conditions in a real-life installation scenario. Industry standard welding techniques such as tapping tee and electrofusion socket fittings for pipe-to-pipe connections were then performed in accordance with supplier installation instructions at laboratory temperatures of 23˚C. A squeeze off operation was held for 1 hour at a temperature of 0˚C (+0/- 5). Reference specimens (not exposed to hydrogen) were also prepared to provide a benchmark for the results. All processes and materials were chosen to represent industry norms in 2018.
Stress resistance cracking was then preformed upon the samples to determine if absorbed gas constituents had been introduced into the welding zone, potentially compromising the 50-year asset lifetime expectation. Samples were exposed to accelerated aging techniques by immersion in an 80˚C water bath, in accordance with industry specifications GIS/PL2-2. To gauge short term performance, squeeze off, tapping tee and coupler connection samples were tested at a hoop stress (the tangential stress at the internal wall of the pipe) of 4.5MPa for 165 hours. Tapping tee and coupler connections were also tested at 4.0MPa for 1000 hours, replicating the conditions for the asset lifetime. Samples were then inspected using X-Ray non-destructive examination techniques and dye penetrating techniques.
Preliminary findings
Leak tightness During the first round of testing, pressurising the tapping tee fittings with air at 4 bar pressure showed no evidence of leaking within a 24-hour test period. When repeating the test with hydrogen, all samples showed a leakage volume of approximately 25 mm of hydrogen over a 24 hour test period. The test is designed to
determine the long-term resistance to creep relaxation of the PE fitting. The 4 N.m of torque used to tighten the tapping tee caps represents the minimum torque likely to be applied by field operatives. This level of torque is considered a conservative number, with the minimum amount of torque applied by field operatives likely to be 1.5 times higher (calculated through ad hoc testing). When increasing the cap tightness to approximately 6 N.m of torque, no leakage was evident over the 24 hour test period. Given the hydraulic properties of hydrogen and observed greater mobility, it is evident that manufacturers testing leak tightness should not use compressed air, but either hydrogen or an inert gas with comparable flow characteristics to that of hydrogen. Modifying assembly procedures to ensure a minimum tightening torque of 6 N.m (accuracy provided by the use of a torque wrench) provides a means of evidencing leak tightness for hydrogen.
Further safety factors are applied in testing when considering the pipe operation pressure. The majority of gas distribution assets operate at pressures of less than 2 bar, with many operating at 75 millibar or less. Reduced service pressures are calculated to significantly reduce leakage rates.
Short term leak tightness for hydrogen was observed when the cap tightness was increased to a closing torque of 6 N.m. The next stage of assessment is currently underway; the above test is repeated at this new minimum torque tightness (6 N.m.) to determine whether the initially leak tight fitting will subsequently develop a leak due to relaxation of the fitting components over time. To ensure a lifetime expectation of 50 years, the tapping tee fittings are currently being assessed for evidence of leaking due to relaxation over a test period of 2500 hours. This test period is expected to conclude in 3Q21. Repairability Applying electrofusion welding techniques to hydrogen infused PE80 piping showed no observable evidence of combustion, charring or blistering. Accelerated ageing techniques performed on hydrogen infused fitting assemblages showed no defects had been observed within the samples which had been tested to a 50 year service period. No failure due to slow crack production was observed within any samples. Conclusion The construction of a bespoke laboratory leak tightness testing facility has allowed for the accurate detection of hydrogen leakage from tapping tee fittings over a 24 hour test period. Hydrogen appears to have a greater affinity to leakage compare to air. Design solutions such as increasing the level of torque applied to tapping tee caps is shown to improve leak tightness. This will be achieved by the utilisation of torque wrenches. These design solutions will be applied to hydrogen specific training programmes and installation instructions. Testing performed within this study gives confidence in the ability of hydrogen infused PE piping to receive reliable repairs, alterations and diversions. The results show that no safety concerns have been identified with regards to electrofusion welding and damage and defects to pipe fitting. There is evidence shown within this study that pipe alterations through electrofusion welding will not damage the long-term lifetime expectancy of the PE material. Visit vermeer.com/thetrenchereffect to learn more.
Trench walls so straight you can hang a picture The trencher effect
What’s the trencher effect? One machine that can outwork multiple excavators while digging pristine trenches and creating its own backfill. Want optimal performance and trenches? Get a trencher.
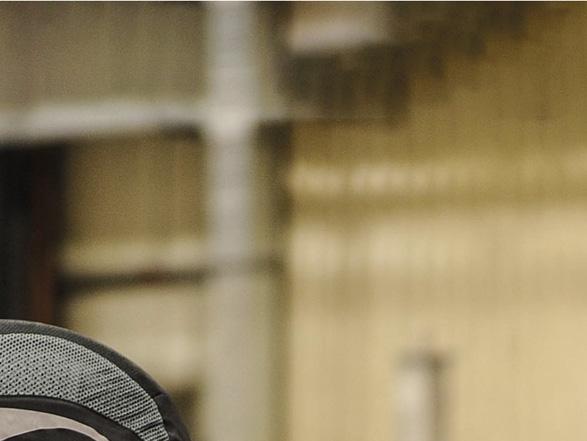
Figure 1. With just a few taps of the screen, all saved readings from the gauge are instantly transferred to the app and synced with no need for manual data entry – just choose which zone the readings are from and the app does the rest.
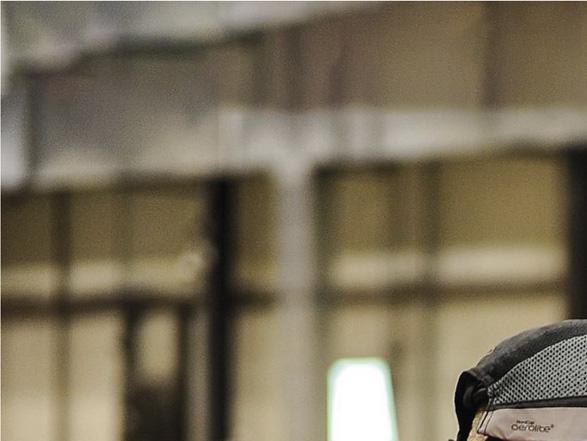
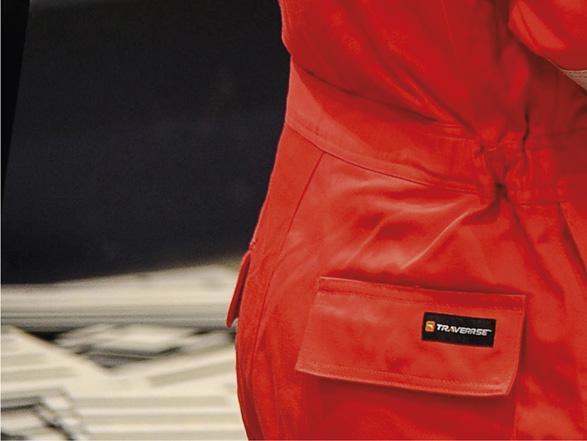
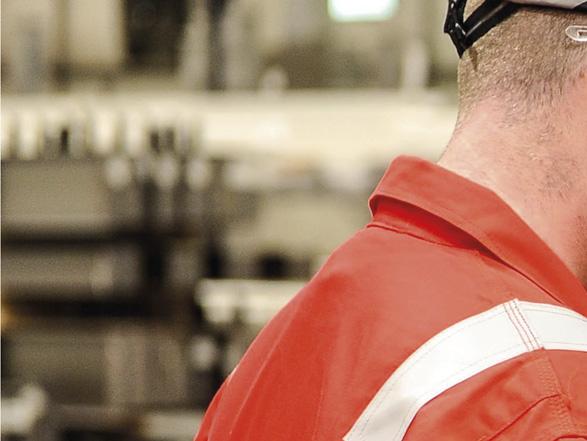
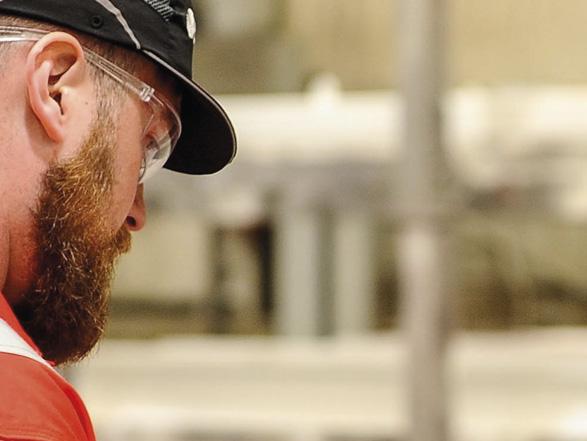
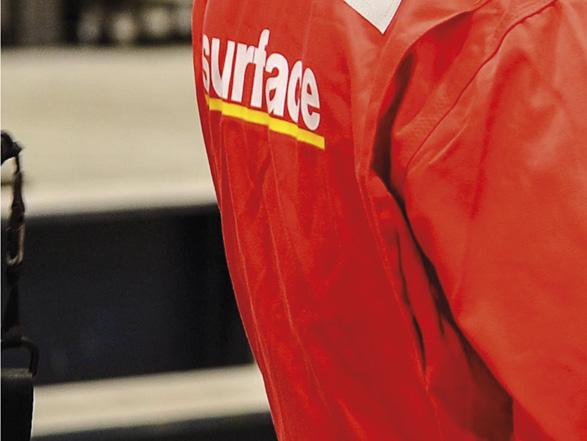
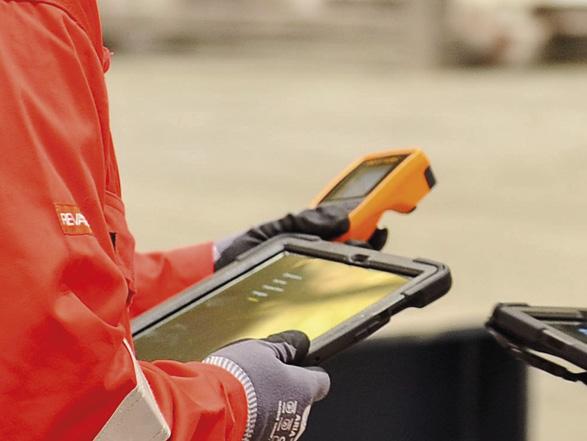
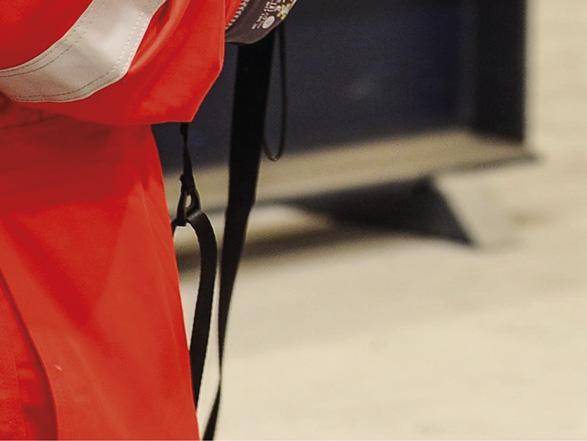
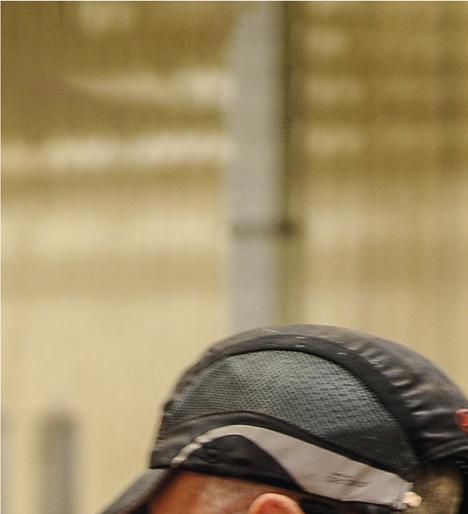
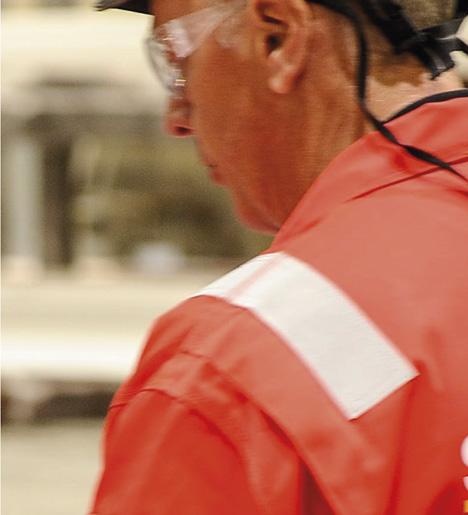
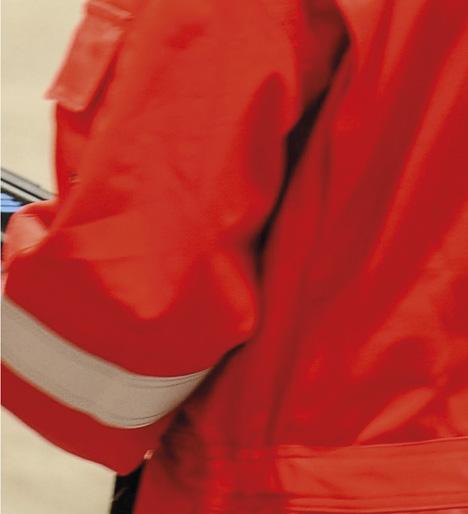
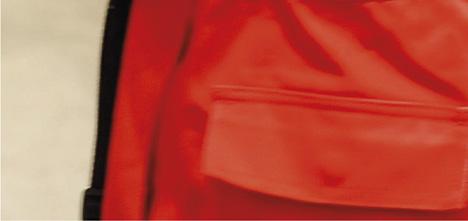
Surface Corrosion Consultants Ltd, Northern Ireland, UK, on changing the face of corrosion and inspection management, via new web-based technology.
Leading the way in web-based technology for the management of corrosion is specialist firm Surface Corrosion Consultants Ltd. The Belfast headquartered company, which specialises in comprehensive paint inspection, NDT inspection and corrosion prevention, has unveiled its innovative new app – Surface Asset Management (SAM) – that is set to transform how coating condition surveys and painting campaigns are recorded and managed. The groundbreaking SAM software is an easy to use, digital inspection application that streamlines all aspects of NDT management and coating inspection. The user friendly, highly intuitive programme can be applied across a range of industries including oil and gas, subsea, renewables, marine, transport and infrastructure as well as wider industrial sectors. The revolutionary software can also manage new build projects providing full cradle to grave traceability. SAM is a fresh and unique approach to corrosion prevention and has been designed by corrosion specialists for corrosion specialists. The technology has been developed with simplicity and efficiency at the forefront of its design. The software removes duplication of tasks and creates a single point of access to monitor corrosion and manage the execution of coating systems, passive fire protection and insulation instalment.
A gap in the market The pioneering technology was developed in 2017 after a team of specialists at Surface Corrosion quickly realised the majority of service providers and major operators are still managing their corrosion protection using sub-contractors and colossal spreadsheets. Recording of maintenance campaigns was inefficient, often documented by creation of
hard copy reports, which proved almost impossible to track and monitor.
The team of entrepreneurs identified a clear gap in the market for a digital solution for recording and saving inspection report data in real-time.
Rab Grainger, Surface Corrosion Consultants’ Technical Director, says: “Working with steel fabricators, it was obvious that there was a gap. We use SAM as a matter of course for all the recording of surface preparation and coatings; it is fundamental to our business.
“SAM surveys are succinct and to the point and provide a snapshot of each asset at the push of a button.
“SAM removes the lengthy process of manual data input and our intuitive software has a fundamental role to play in the future of the energy and construction industries.
Survey data needs to be concise, easy to understand, as well as simple to manage and monitor. With SAM, reporting is instantaneous. Continuing with a philosophy of keeping things simple, the inspection of any fabricated steelwork with SAM is one continuous process. Keeping it simple In the constant drive for efficiency, the app now interfaces directly to Elcometer gauges that are Bluetooth enabled. Using a tablet and Bluetooth technology the coatings inspector and technician digitally records all inspection requirements from NDT onwards including MPI, UT, Visual, environmental readings, DFTs, images and much more in real-time onsite. Reports generated can be adapted and edited to suit the user’s specific requirements. With just a few taps of the screen, all saved readings from the gauge are instantly transferred to the app and synced with no need for manual data entry – just choose which zone the readings are from and the app does the rest. There is no man in the middle to navigate.
Every piece of inspection data collected via the web or tablet is instantly saved to secure servers. SAM creates skilfully formatted and concise documentation that is available anytime to download or send direct from the desktop or tablet.
Some of the work the app covers include: ) Conditional surveys.
) Campaign and scope management.
) Survey and inspection reviews.
) Analysis and reporting.
) Critical repair management.
Speed and efficiency SAM is available on Android and iOS devices for use in fabrication halls. The user interface is simple to use with clearly defined menus. The app offers data entry efficiency and by using an interactive online system, it reduces the amount of time inspectors spend sitting behind a desk painstakingly inputting data.
SAM offers real power in speed and efficiency in four key ways: ) PROTECT – SAM helps to preserve assets. Delivering an expert corrosion and inspection management web-based solution.
) INSPECT – SAM captures MPI, visual and UT survey data in real-time. Full documentation and a snapshot of an assets’ corrosion is available immediately at the push of a button.
) RECORD – Survey data is concise, easy to understand, and simple to manage and monitor. With SAM, reporting is instantaneous.
) CONTROL – SAM provides complete control of data for maintenance planning and scheduling. Clients have optimum control of budgets ensuring funds are correctly allocated where required.
The future of surface corrosion The benefits of SAM versus traditional methods are: ) Subcontractors use the system ensuring data is always updated and owned by the owner/operator.
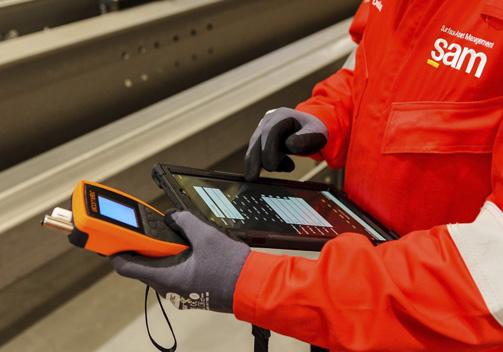
Figure 2. Using a tablet and Bluetooth technology, the coatings inspector and technician digitally records all inspection requirements from NDT onwards including MPI, UT, Visual, environmental readings, DFTs, images and much more in realtime onsite.
Figure 3. SAM accurately estimates how much material you will need for every project, zone or even single items as well as estimating costs for projects.
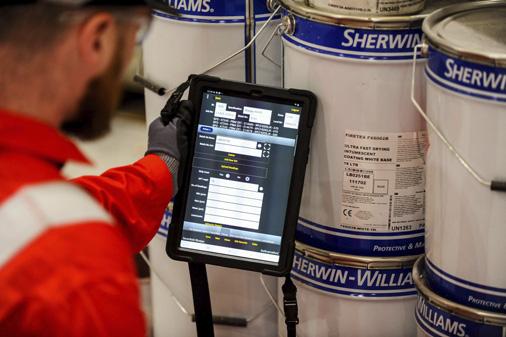
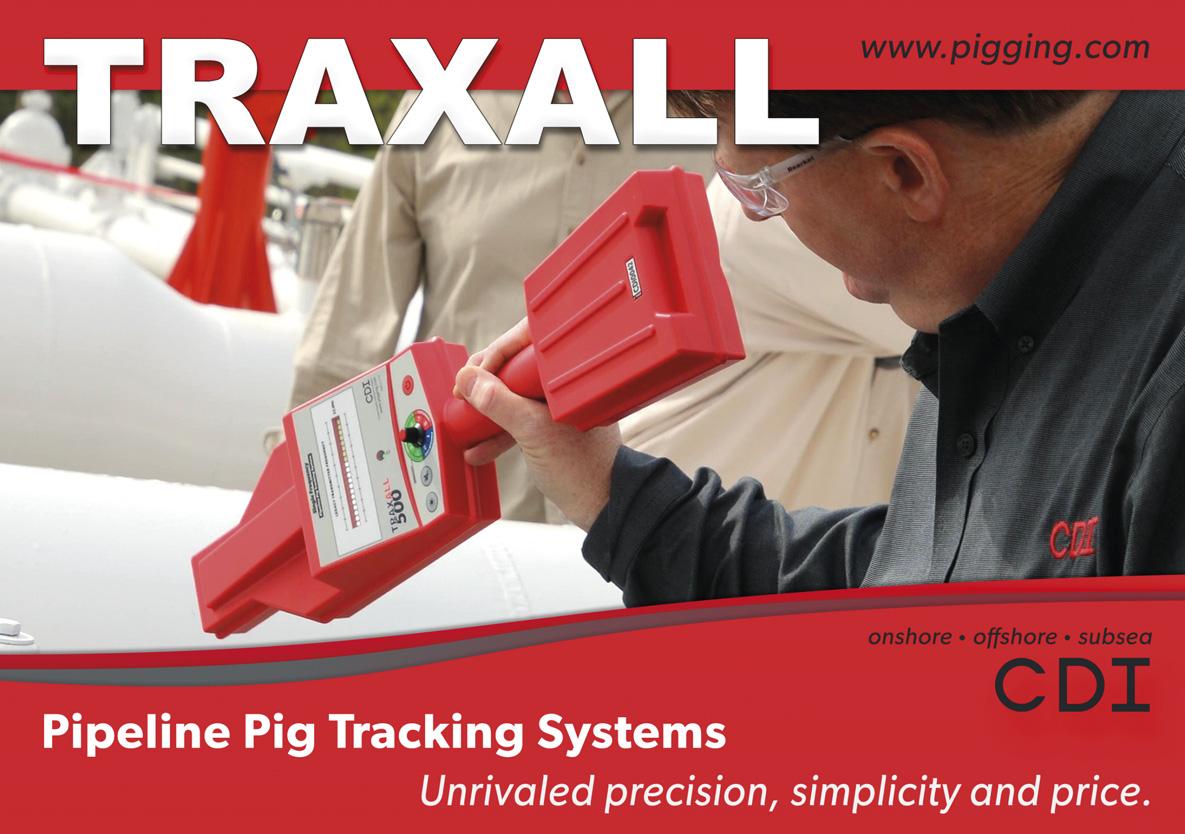
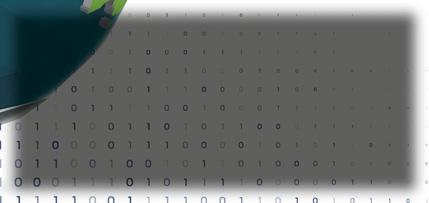
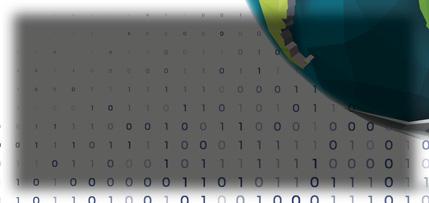
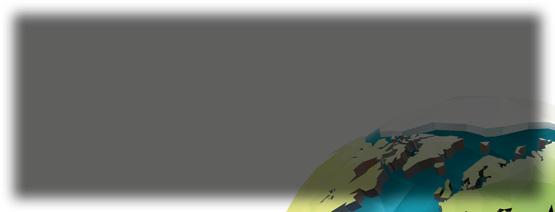
The print issue is distributed to a global audience of industry professionals (verifi ed by ABC). Register to receive a print copy here: worldpipelines.com.magazine/worldpipelines/register
Prefer to read the issue online? The digital fl ipbook version is available here: worldpipelines.com/ magazine/world-pipelines Download the World Pipelines app for Android (Google Play) or iOS (App Store) to access World Pipelines from your mobile device.
Wherever you are, World Pipelines is with you.
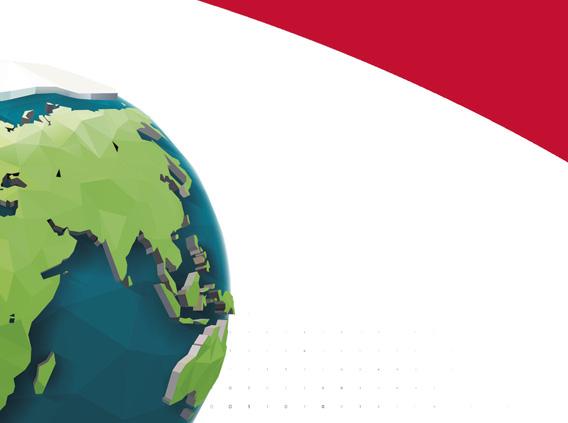

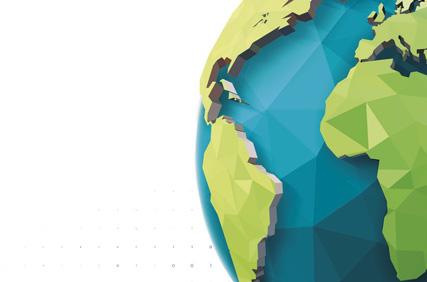
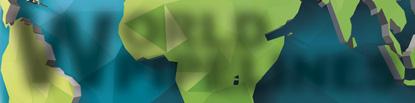
ADVERTISERS’ DIRECTORY
Advertiser Page
ABC
41
AGRU
API
Böhmer
CDI
45
2
36
55
DeFelsko
47
EDI
Energy Global
Fotech
Girard Industries
IPLOCA
Lincoln Electric
MONTI
Pigs Unlimited International Ltd
Pipecare
Pipeline Inspection Company
Propipe
Qapqa
ROSEN Group
SCAIP S.p.A.
Stark Solutions
Vermeer
35
19
4
42
28
11
OFC, 13
17
IBC
27
41
OBC
IFC
Bound insert
17
51
Vietz
Winn & Coales International Ltd
World Pipelines
23
7
31, 55 ) SAM is designed to be managed by you or your designated company. The cutting-edge app can be customised to manage your specific requirements, fully aligned to your processes and procedures.
) Easy user accessibility: immediate information from anywhere that has a suitable internet connection.
) You benefit by having complete control of data for maintenance planning and scheduling.
) Optimum control of budget by ensuring funds are correctly allocated where required.
) Simple user-friendly interface – via PC or tablet.
Data management and monitoring SAM automatically generates dashboards providing insights, intelligence and overviews of all data collected during surveys allowing the user to view scopes in detail and see a clear picture of the critical path ahead. The app can also be used to set priorities which gives the operator the chance to set their own critical repair threshold for the surveyed items. Furthermore, the manning levels can be scrutinised with ease to help assemble the most effective team balance on any project.
Data accuracy is assured as data is recorded directly within the device and instantly imported offering improved assurance and accuracy.
Rab explains: “SAM is tailored to each individual customer requirement and each user has their own clearly defined roles and responsibilities. Every change made within SAM is timestamped to a known user. The correctly qualified person is then able to verify compliance within their expertise.”
The software offers the added benefit of historical data storage to ensure the client’s third-party inspector can confirm each stage in the process or simply verify compliance by load at the end of production.
SAM logs coating product, blast media, and all other essential variables for successful and concise reports. The software can generate reports based on user defined selections by asset, zone, structure type, RE values, planned year, dates and items not yet included offering clients the chance to get a better handle on their data.
Additionally, the app can accurately estimate how much material you will need for every project, zone or even single items as well as estimating costs for projects.
“SAM really is the most versatile and innovative software available on the market today with regards to NDT management and coating inspection. It is a game changer for the future of the management of corrosion in the oil and gas and construction industries.”
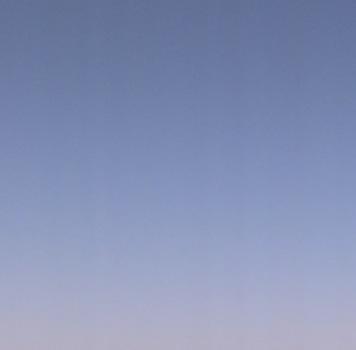
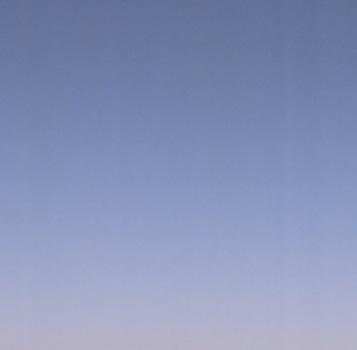
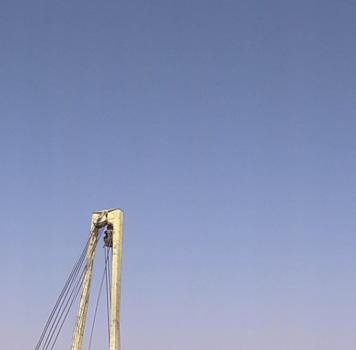
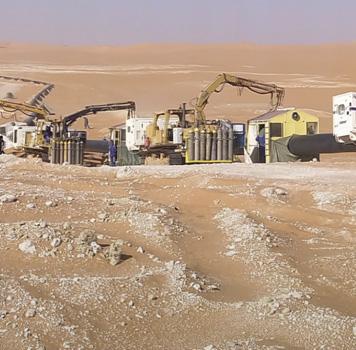
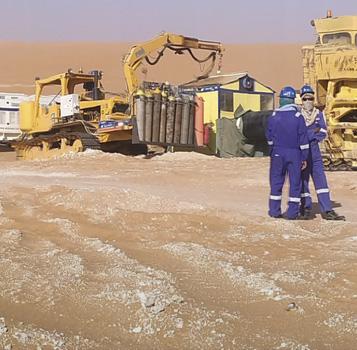
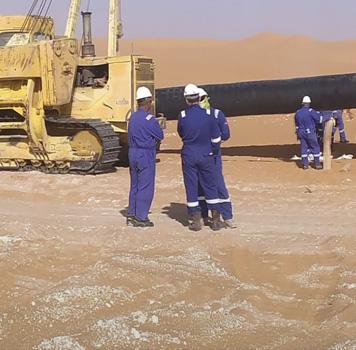
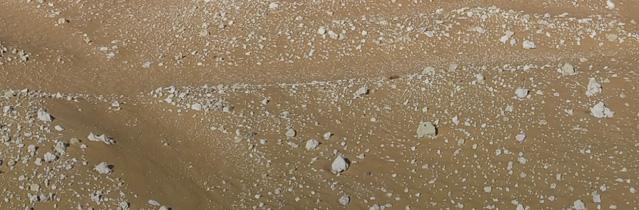
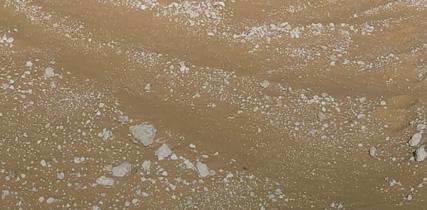
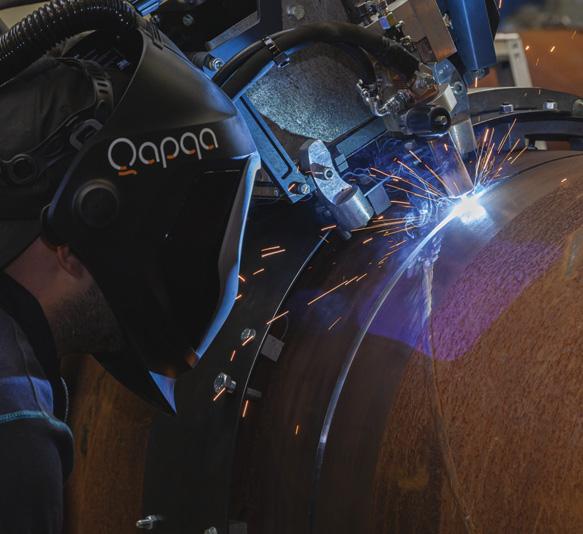