
10 minute read
Alloy application
Technology for pipeline operators
Join attendees from: INTECSEA, PLUSPETROL, SAIPEM, CENOVUS, TC ENERGY, PETROBRAS, PLAINS MIDSTREAM CANADA, FLUOR, TOTAL, WINTERSHALL DEA AG, BP, CENAGAS, OMV, SAUDI ARAMCO, WOOD, WORLEY, HALLIBURTON, REPSOL, NATIONAL GRID, CONOCOPHILLIPS, SHELL, ENTERPRISE PRODUCTS, DCP MIDSTREAM
An online conference focusing on operational technology, servicing and maintenance for oil and gas pipelines 20th October 2021 - 14:00 (BST)
With speakers from:
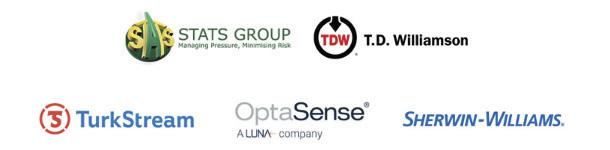

monitor threats along pipeline routes and transmission lines.
Ensuring the future safety of pipelines globally The transportation of hydrocarbons involves a complex network of pipelines that are designed to be fast and efficient. The above discussed factors only prove this fact; it requires meticulous planning, surveying and monitoring as the probability of leakages and pollution stands high during pipeline deployment.
SuperVision is committed to enhance the monitoring of pipeline routes and pipeline construction to prevent pipeline incidents and ensure safe supply of energy.
Bibliography
1. ADEGBOYE, M. A., FUNG, W.K., & KARNIK, A. (4 June 2019). Recent Adances in Pipeline Monitoring and Oil Leakage Detection Technologies: Principles and Approaches. Sensors, 11, 2548. https://www.ncbi.nlm.nih.gov/pmc/ articles/PMC6603558/ abgerufen 2. APPEN. (14 April 2020). What is Training data? https://appen.com/blog/ training-data/ abgerufen 3. BARBOSA, P. (June 2021). Monitoring Pipelines to Protect Against Theft, Leaks. Pipeline and Gas Journal. https://pgjonline.com/magazine/2021/ june-2021-vol-248-no-6/features/monitoring-pipelines-to-protect-againsttheft-leaks abgerufen 4. CDIAC. (2019). Annual CO2 emissions per country. Our World in Data: https://ourworldindata.org/grapher/annual-co2-emissions-per-country abgerufen 5. DELGADO, M. R., & MENDOZA, O. B. (2017). A comparison between leak location methods based on the negative pressure wave. 14th International Conference on Electrical Engineering, Computing Science and Automatic Control (CCE) (S. 1-6). Mexico City: IEEE. 6. Global CO2 Emissions set to Surge in 2021 Post-Covid Economic Rebound. (20 April 2021). Von Yale Environment 360 Digest: https://e360.yale.edu/digest/ global-co2-emissions-set-to-surge-in-2021-in-post-covid-economic-rebound abgerufen 7. HARVEY, F. (31 May 2021). Greenhouse Gas emissions. The Guardian: https:// www.theguardian.com/environment/2021/may/31/eus-greenhouse-gasemissions-fell-in-2019-data-shows abgerufen 8. HILSENBEK, H. (1 December 2020). Mit KI Pipelines effectiv überwachen und instand halten. B_I medien: https://bi-medien.de/fachzeitschriften/ umweltbau/leitungsbau/mit-ki-pipelines-effektiv-ueberwachen-und-instandhalten abgerufen 9. HOARAU, Q., GINOLHAC, G., ATTO, A. M., & NICOLAS, J. (2017). Robust adaptive detection of buried pipes using GPR. Signal Process, 293 - 305. 10. IEA. (2021). Global Energy Review. Paris: IEA. https://www.iea.org/reports/ global-energy-review-2021 abgerufen 11. INNOTER. (2021) https://innoter.com/en/articles/monitoring-the-condition-ofpipelinesb-ased-on-satellite-imagery/ abgerufen 12. LIM, K., WONG, L., CHIU, W. K., & KODIKARA, J. (2016). Distributed fibre optic sensors for monitoring pressure and stiffness in out-of-round pipes. Structural Control Health Monitoring, 303 - 314. 13. MANEKIYA, M., & ARULMOZHIVARMAN, P. (2016). Leakage detection and estimates using IR thermography. 2016 International Conference on Communication and Signal Processing (ICCSP) (S. 1516-1519). Melmaruvathur: IEEE. 14. MENG, L., YUXING, L., WUCHANG, W., & JUNTAO, E. (2014). Experimental study on leak detection and location for gas pipeline based on acoustic method. J.Loss Prev. Process Ind., 74 - 88. 15. MENGPIN, G., & FRIEDRICH, J. (6 February 2020). 4 Charts Explain Greenhouse Gas Emissions by Country and Sectors. World Resources Institute: https:// www.wri.org/insights/4-charts-explain-greenhouse-gas-emissions-countriesand-sectors abgerufen 16. ROBERTS, C. (4 August 2019). How Satellite Technology is Helping to Keep Pipelines Safe. Submar: https://submar.com/how-satellite-technology-ishelping-to-keep-pipelines-safe/ abgerufen 17. TURNER, N. C. (1991). Hardware and Software Techniques for Pipeline Integrity and Leak Detection Monitoring. Soc.Pet.Eng, 139 - 148. https://doi. org/10.2118/23044-MS abgerufen 18. XU, L., ZHAO, Y., & BAI, X. (2020). Leakage Monitoring Technology of Oil Pipeline and Its Application. IOP Conference Series: Earth and Environmental Science. 440. Resources and Geological Engineering. 19. ZHANG, S., GAO, T., XU, H., & WANG, Z. (2009). Study on New Methods of Improving the Accuracy of Leak Detection and Location of Natural Gas Pipeline. Proceedings of International Conference on Measuring Technology and Mechatronics Automation, 360 - 363.
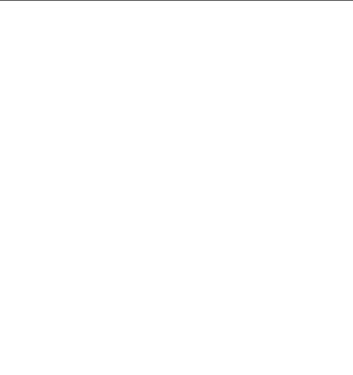
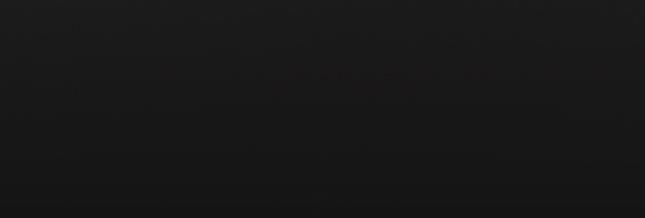
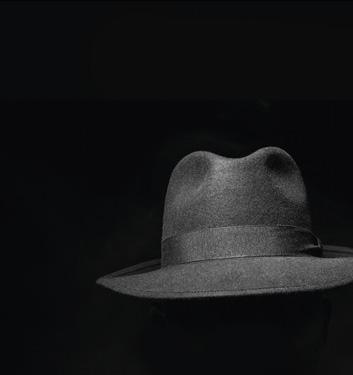
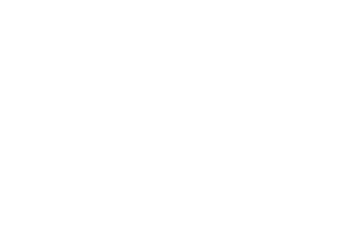


Accurate • Tough • reliable
THE LEADING BRAND OF HOLIDAY DETECTION EQUIPMENT SINCE 1953
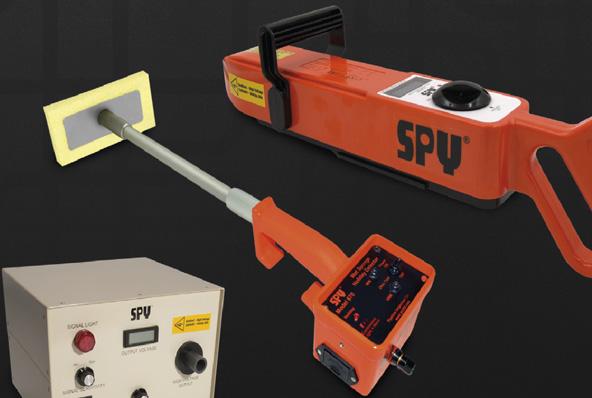

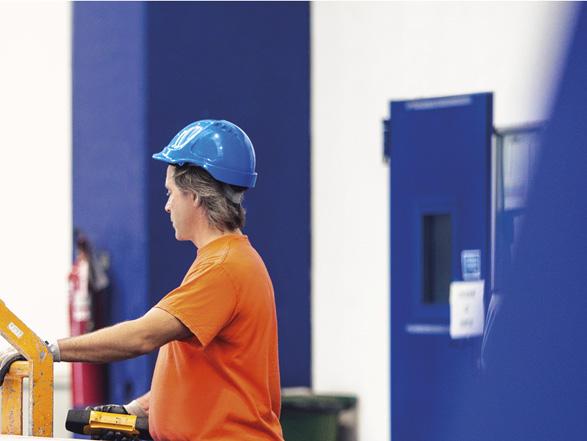

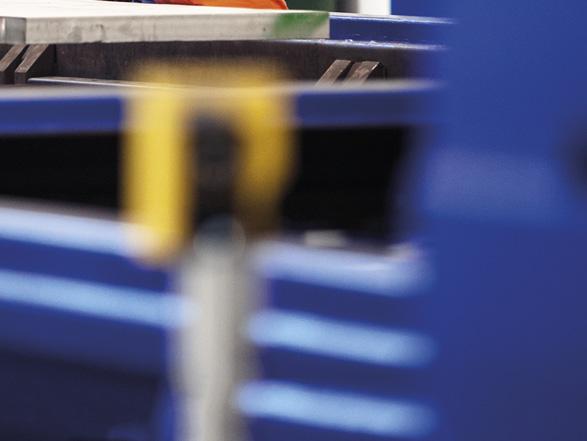
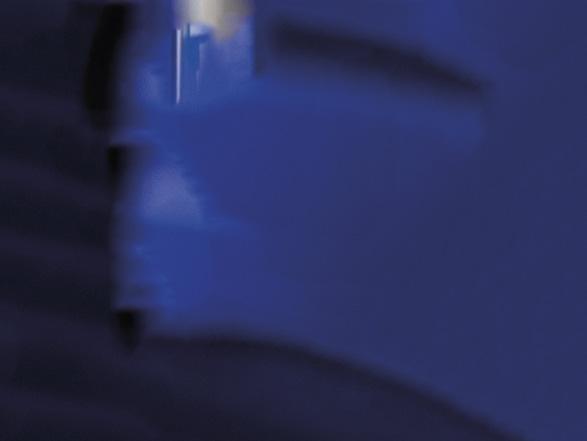
Rodrigo Signorelli, Outokumpu, Brazil, discusses the material challenges for engineers when specifying flowlines and risers, and shares insight into pipeline technologies and the role of corrosion resistant alloys (CRA).
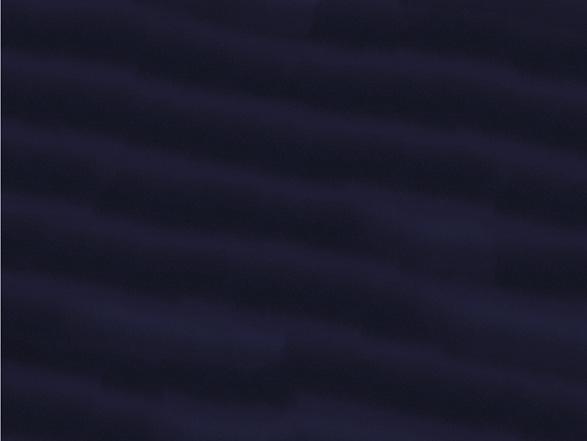
In the field, corrosion resistance provides safety, long life, process continuity, and control of risk. However, purchasing priorities vary widely depending on the application, the environment, and the preferences of the end customer and its supply chain partners. Engineers typically start thinking about pipeline materials early in the project cycle when they need to produce budget estimates for risers, flowlines, jumpers, and fluid transfer lines. They need CRAs in the form of strip, coil and plate for fabrication into flexible pipes, tubes for umbilicals, mechanically lined pipe (MLP), and clad pipe.
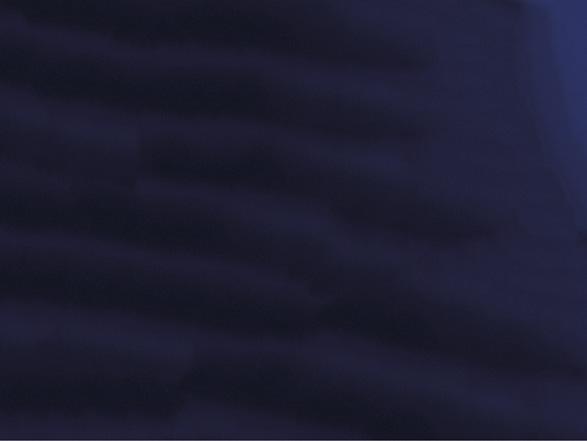

Competing flowline technologies When it comes to flowlines, clad pipes, MLP, and flexible pipe can all be used to transport oil and gas from the seabed to the oil platform. Each has its own pros and cons and the choice between them often comes down to the preferences and standard specifications of the oil and gas operator.
All three rely on CRAs to protect the flow from corrosion. In the case of MLP and clad pipe, the strength relies on carbon steel, whereas the manufacturers of flexible pipes rely on duplex stainless steels strength to avoid pipe collapse in deep waters.
The approach makes a lot of economic sense. Clad pipes and MLP cost around half the price of pipes manufactured entirely from CRA and flexible pipes save costs in the field as they are relatively straightforward to lay.
Clad pipe Engineers specify clad pipe when they want to minimise risk in high pressure and high temperature applications. It provides security thanks to a metallurgical bond formed between the CRA and the carbon steel shell. This eliminates the potential for a void forming between the two layers, which product could seep into, initiating corrosion and leading to failure.
One route to market for clad pipe is via specialist plate manufacturers. They purchase alloys as quarto plate around 10 - 30 mm thick. They match this with a thicker carbon steel backing plate and pass the two plates together multiple times through their mill.
The intense pressure and heat of rolling creates a composite plate of around 15 - 70 mm thickness with the all-important metallurgical bond between the layers.
Explosion bonding is an alternative process to manufacture clad plates. It offers high flexibility with respect to possible material combinations. This method is mainly used for high clad plate thicknesses and small batch sizes.
Clad pipes can also be produced by weld overlay. The corrosion resistant metal layer is deposited on the inner surface of a carbon steel pipe by using CRA welding wire or welding strip.
Tube and pipe mills take delivery of these plates to form into pipe and fittings. These are combined into packages to meet the specifications of the engineering, procurement and construction (EPC) companies that deliver projects on behalf of the end customer.
Mechanically lined pipe While it is similar to clad pipe, MLP is less costly. The most common manufacturing process involves inserting a CRA liner pipe into an outer carbon steel pipe (pipe-in-pipe solution). The liner is then hydraulically or mechanically expanded inside the outer pipe and later held in place by the mechanical forces of the shrinking fit. The liner pipe is seal welded to the outer backing steel pipe at both ends to avoid moisture ingress between the backing steel and the liner pipe.
Other methods make use of heating the outer pipe or using an adhesive layer to strengthen the bond between the two layers. In another process, a spinning mandrel creates the bonding between the inner CRA pipe and the outer backing steel pipe.
Flexible pipe Engineers use flexible pipes either as flowlines to transport oil and gas along the seabed or when they need a riser to transport product up to the surface. It can handle dynamic movements from the action of the tide and waves, and is delivered in long lengths and requires less jointing than the standard 12 m lengths of solid pipe.
CRAs form a carcass to protect the pipe against corrosion from the fluid it carries and collapse due to the high external pressure. It comes in the form of strips 25 mm to 200 mm wide and up to 4 mm thick, depending on the specification and the diameter of the pipe.
Flexible pipe manufacturers form this strip into special profiles that interlock in a spiral to form a long flexible tube. They add multiple additional layers to provide
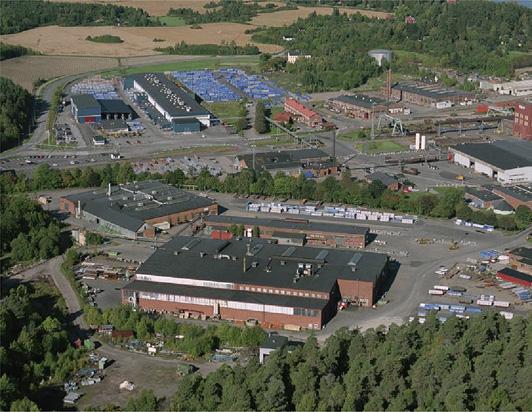
Figure 2. Nyby is one of Outokumpu’s mills that are certified to produce material for the oil and gas industry.
Figure 3. Production of strip for flexible pipe and umbilicals.
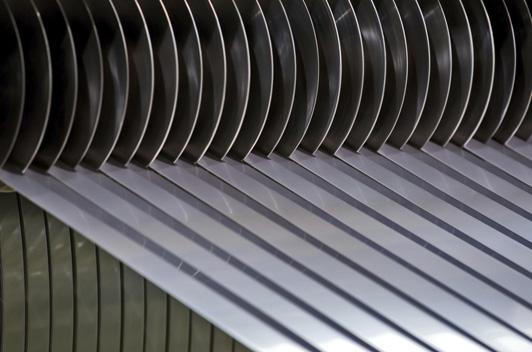
mechanical strength and flexibility, with each manufacturer taking its own approach to the number and design of the layers and their arrangement in the overall cross section.
When it comes to flexible pipe, consistent mechanical dimensions are essential for the strips. This ensures the profiles are manufactured consistently and will lock together as intended. Variation in the thickness, width or flatness of the strip material could impact the integrity of the carcass, posing risk to safety and environmental security.
With risks like these, traceability is extremely important to oil and gas operators. It helps them control risk. Many stainless steel producers can supply the right grades – but few can consistently produce identical mechanical and dimensional properties.
To help us achieve this, customers provide extensive specifications and certifications that combine the technical requirements of the oil company as the end customer with those set by the flexible pipe producer. Technicians use these to produce material to very fine tolerances and mechanical specifications.
Welded pipe gaining ground for umbilicals Another interesting trend over the last five years is that engineers have been turning to longitudinally welded stainless steel tube instead of seamless tube for umbilicals.
Umbilicals are packaged subsea lines to carry multiple services such as flow lines, water, chemical feeds, power and data cables, as well as hydraulic fluid or pneumatic air lines.
Traditionally, only seamless stainless steel tube was used for umbilicals. However, seamless tube is costly and only available in short lengths that need regular buttwelded joints. Manufacturers carry out ultrasonic testing of the entire tube and X-ray qualification of the butt welds as non-destructive testing to qualify tubes before installation in the field.
In comparison, longitudinally welded tubes only need butt welded joints at the end of each strip. This gives them higher mechanical strength and for some applications, it may be possible to reduce the thickness of tubes, saving weight and material.
When supplying for umbilicals, tube fabricators order CRA up to 5 mm thick and at least 25 mm wide, depending on the diameter of the pipe. They deliver the welded tube to umbilical manufacturers, who create the packaged bundle of lines and cables required for the project.
Certifications The most challenging aspect of delivering material for oil and gas projects, and particularly for flexible pipe and umbilicals, is meeting the specifications, standards, qualifications and certifications for each project. Requirements include ASTM and EN standards, qualification bodies such as Norsok and the BS EN 10204 standard that covers traceability and certification by independent third party auditors.
Oil and gas companies all have their own specifications and company standards, as do the fabricators and EPC companies in the supply chain. The industry also demands complete consistency of mechanical properties and dimensions, within very tight tolerances.
When combined, these create a stringent and unique set of specifications for each project. It’s only possible
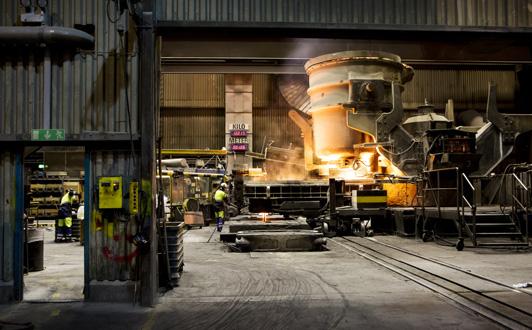
Figure 4. Stainless steel melt shop.
Figure 5. Specialist mills combine corrosion resistant alloy in quarto plates with carbon steel backing plates for clad pipe.
Figure 6. Cold rolling produces sheet coil to precise dimensional tolerances.
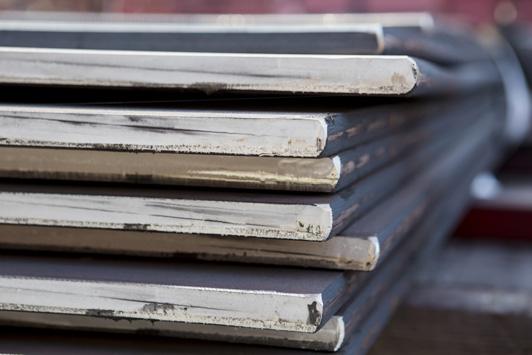
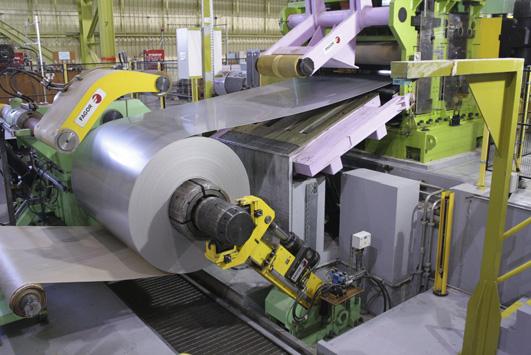