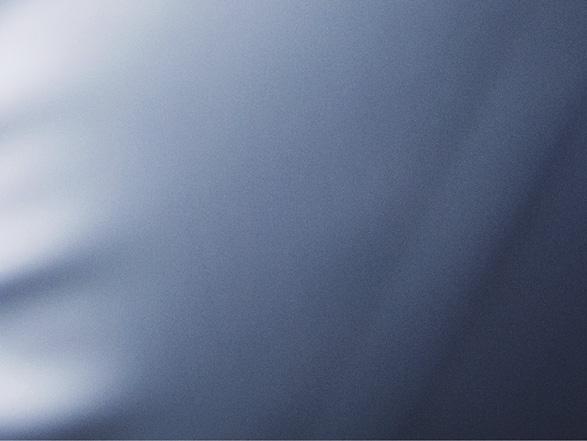
9 minute read
The why, when and how of calibration
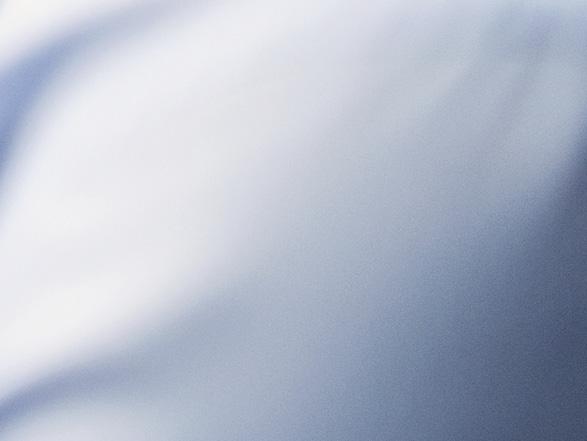
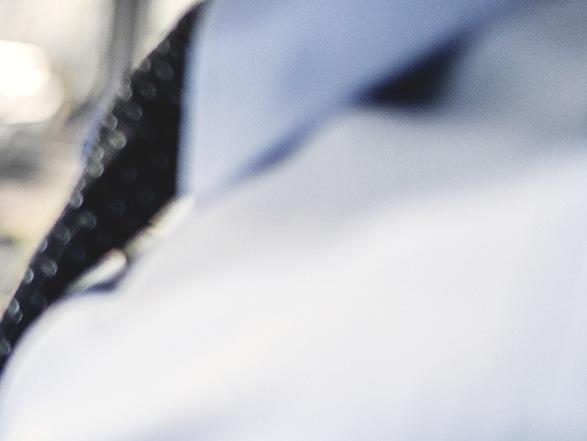
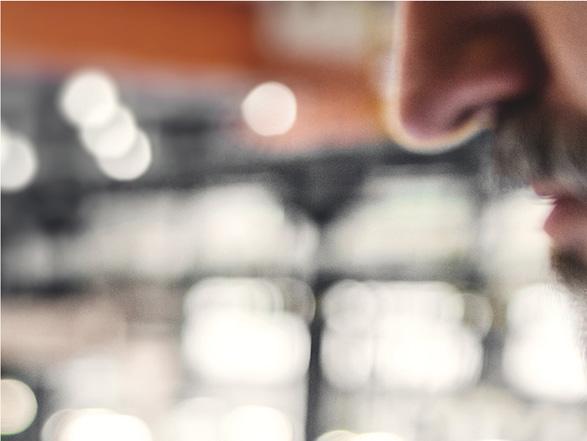
Stephen Gibbons, Global Market Manager for Continuous Gas Analysers for ABB Measurement & Analytics, explains the developments in process gas analyser technology that are helping governments and companies worldwide to keep emissions to air under tight control.
One of the interesting aspects of the COVID19 pandemic has been its impact on industrial emissions. As lockdowns and other measures led to factories closing and transportation grinding to a halt, emissions levels worldwide fell significantly. While this reduction is likely to have only been temporary, it has led to a realisation of just how much impact emissions from activities such as industry and transport can have on air quality, and, more importantly, what should be done to rein them in.
Even before the pandemic, legislation was already in motion to find ways to cut emissions. The Paris Agreement in 2015, for example, set a global target for countries to significantly reduce their industrial emissions to air to help limit global temperature increases to 1.5˚C. Many industrialised nations have already made significant progress in tackling their emissions, while developing nations are also increasingly demonstrating their ability to achieve growth while minimising their environmental impact.
Globally, regulations are being tightened, requiring polluting facilities and plants to install Continuous Emission Monitoring Systems (CEMS) to ensure compliance. The European Union (EU), for example, has introduced its Medium Combustion Plant Directive (MCPD) to bridge the gap
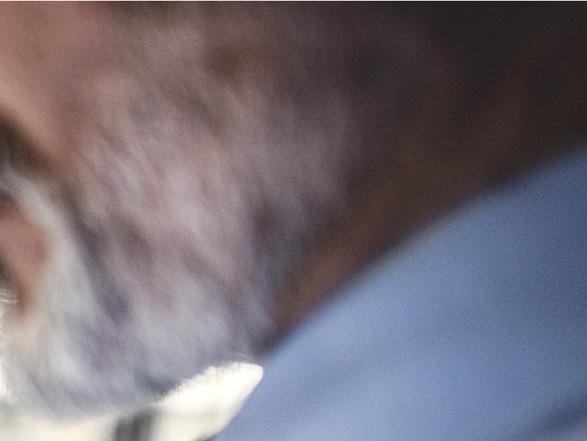
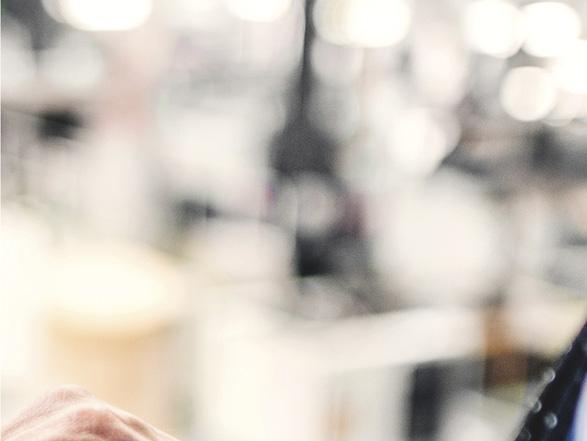
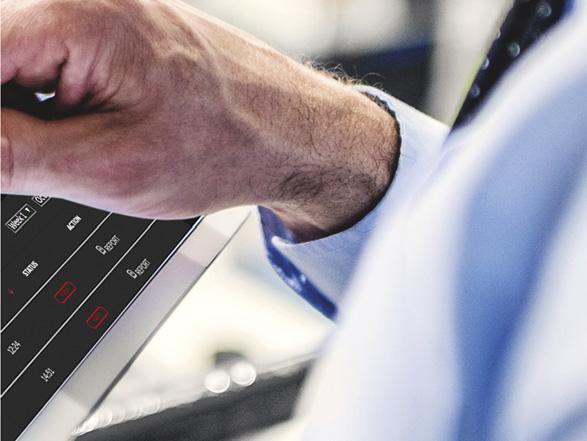
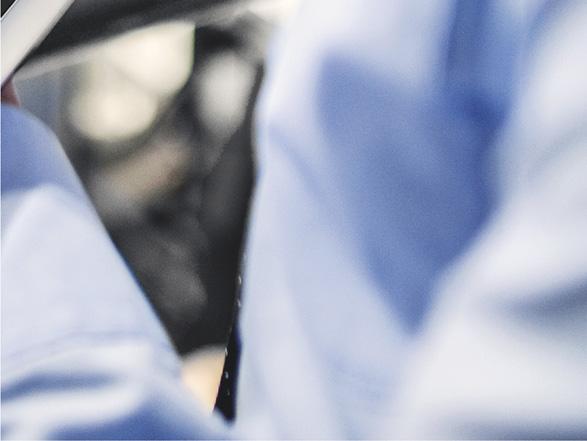
between large combustion plants and smaller appliances like boilers. The Directive is designed to control emissions of sulfur dioxide (SO2), nitrogen oxides (NOX) and dust and applies to approximately 143 000 plants with a rated thermal input equal to or greater than 1 Megawatt thermal (MWth) and less than 50 MWth.
The EU is also bringing large combustion plants for solid fuels such as biomass into line with waste incineration plants. The latest Industrial Emissions Directive (IED) adds further CEMS gas analysis requirements, including mercury, hydrogen chloride, hydrogen fluoride, carbon monoxide, ammonia and total Volatile Organic Compounds (VOCs).
Other parts of the world are also following suit. The US has introduced various measures to reduce emissions from oil and gas pipelines, including the PIPES Act, which includes a provision for operators to monitor emissions from gas distribution systems. In India, many industries such as metal processing, oil and pesticides production have been required to invest in CEMS solutions to monitor particulates, ammonia, sulfur dioxide, oxides of nitrogen, chlorine, hydrogen chloride and carbon monoxide, amongst others.
A wide range of solutions When it comes to CEMS solutions, users can select from a diverse choice of technologies. Options range from simpler systems for natural gas fired boilers to measure carbon monoxide, carbon dioxide and oxides of nitrogen through to highly sophisticated multiple component systems measuring exotic pollutants such as hydrogen fluoride, hydrogen chloride and ammonia. This broad range of options allows emissions to be accurately measured in a wide variety of industrial applications, including power generation and waste incineration, metals and minerals, refineries and chemicals, pulp and paper and marine.
When it comes to measuring stack emissions, operators have a choice of techniques.
Extractive techniques Commonly used for measuring gases, extractive techniques consist of two main methods. Heated extraction involves extracting the sample gas from the stack using a sample probe, heated line, gas conditioning equipment and a heated sample pump. Before analysis, condensate is usually removed from the sample and the temperature is reduced to protect the analysers, commonly referred to as ‘cold/ dry’ measurement.
The alternative is to keep the gas hot all the way through the system, known as ‘hot/wet’. The sample must arrive at the analyser inlet in a representative state that reflects conditions in the stack. The design of the sampling system must also protect against any sample loss or degradation. Typically, multi-gas analysers are used with this method but can be combined with single-component analysers.
In-situ measurement In-situ analysers are directly mounted at the measurement point. Most in-situ systems use infrared measurement techniques. While in-situ analysers can be installed directly on the stack with no sample handling, around 80 - 90% of plants worldwide have a strong preference for extractive methods, which tend to offer a lower cost of ownership.
In comparison to in-situ measurement, extracting a sample means only the probe is in contact with the gas and not any delicate optical components. After conditioning, a clean and dry sample is presented to the analyser. The system can then be installed in an air-conditioned cabinet or shelter, protecting against potentially harsh ambient conditions.
Also, whereas in-situ devices are usually limited to one or two components, multiple components can be measured simultaneously using a sequence of sensors in an extractive system, requiring less holes in the stack.
With the analyser system usually installed at ground level in a clean and accessible environment, maintenance is much more convenient too, with components easy to work on and remove, and test gas cylinders available nearby to easily calibrate the devices.
Another popular technique is cross-duct analysers. These analysers project IR or UV (ultraviolet) energy across the stack and detect the change in energy state of the gas molecules as they absorb this energy at characteristic wavelengths. Most cross-duct systems measure one to two gases over a range of wavelengths. Furthermore, as there is no contact with the target gases, they can require less maintenance and operator involvement.
One drawback is that cross-duct systems can be more complicated to calibrate, although this can sometimes be

Figure 2. ACF5000 hot/wet extractive system.
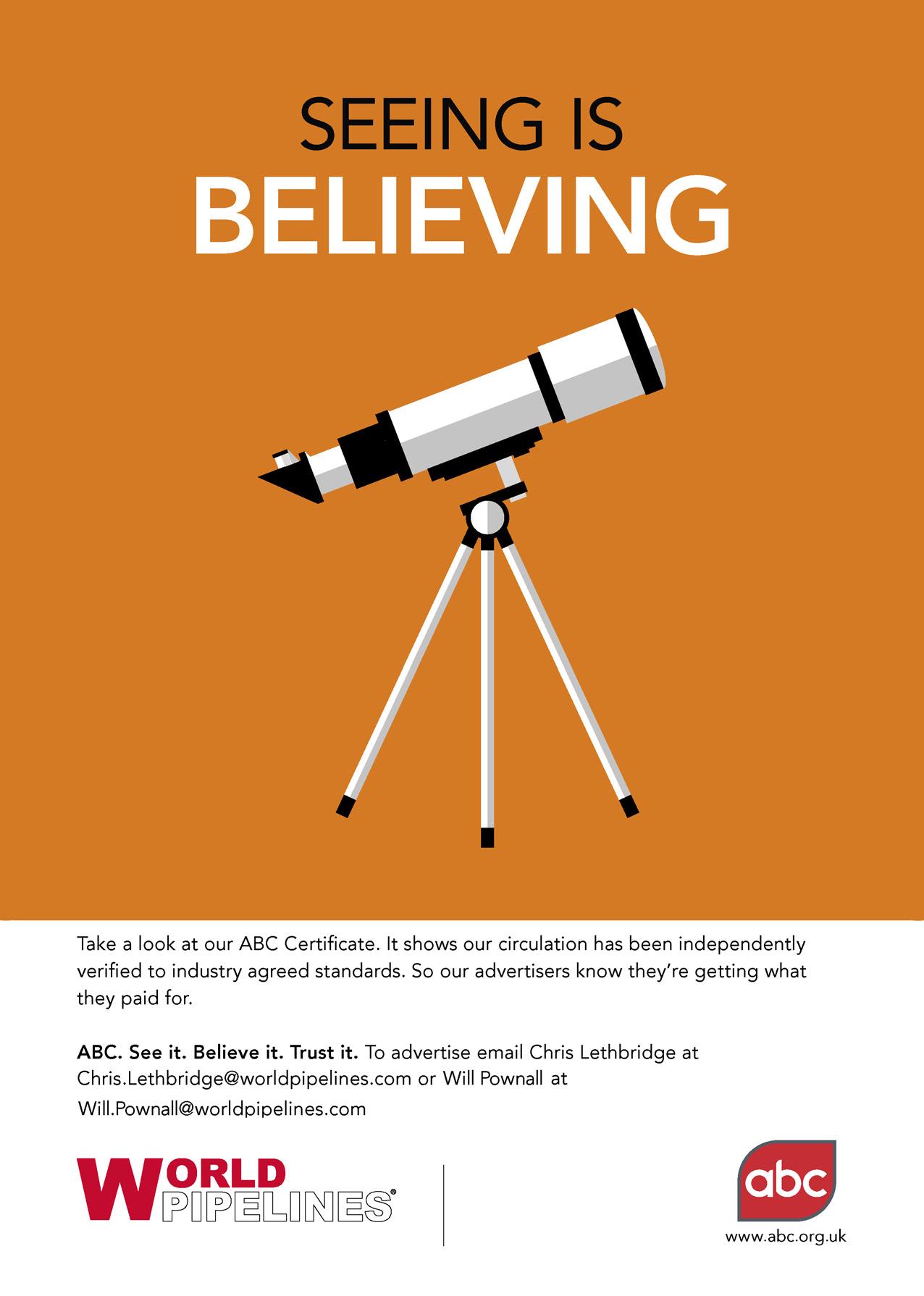
overcome using an automatic calibration system that can demonstrate accurate and reliable calibration checking.
Maximising performance Several criteria determine the choice of CEMS for a particular monitoring application. In the UK, for example, the CEMS must be MCERTS certified for the determinands specified in the IED and must also be certified for a measurement range that is suitable for the application.1
The operator must also ensure that any CEMS being considered will not have its performance degraded by any specific site conditions and that the intended CEMS is proven on comparable installations.
All CEMS must allow the performance of zero, span and linearity tests following installation, while new, extractive CEMs must have a facility for leak checks. Particulate monitors may be sensitive to factors such as changes in flowrate, as well as particle size and shape. Operators with a need for particulate monitoring should determine whether stack conditions could degrade the monitoring data.
Some substances, for example organic pollutants such as dioxins, and inorganic pollutants such as mercury, can exist in both gaseous and particulate forms simultaneously. The monitoring method must therefore be able to sample the selected phase or both phases, as needed.
As well as choosing the right technology, facilities needing to monitor air emissions must ensure the right conditions exist and that correct procedures are adhered to. A major factor is the variability of the emissions. In general, greater variability means increasing the frequency of monitoring, an area where CEMS wins over more intermittent, periodic monitoring techniques. CEMS are the correct choice where emissions levels vary so significantly that intermittent sampling would lead to unrepresentative results or too many samples would be needed.
An appropriate data recording system must also be in place. Instrument-based methods such as CEMS provide real-time data, which must be recorded to allow interpretation and reporting. A variety of systems can be used for onsite storage, from the most basic, such as a simple chart recorder, through to automatic data loggers that can send emissions data to a remote central processing unit.
Trends and expectations In the past, systems that monitored a single gas were popular with many CEMS users, who believed they were less complex than systems that can measure multiple gases and so less prone to failure. This situation has now changed, as the requirement for more plants to monitor a greater range of gases has increased. One technology that is becoming increasingly popular as a result is FTIR spectroscopy, a technique that can measure multiple gases without the need for frequent calibration.
For example, the most recent Chinese ‘Blue Sky’ legislation demands the measurement of particulate matter, carbon monoxide, chlorine, oxides of nitrogen, sulfur dioxide, hydrogen chloride, and ammonia, amongst others. Most of these can be monitored with modern FTIR gas analysers with appropriate data processing software. Systems that can measure multiple components reduce the cost of ownership, with fewer detection elements and less equipment to maintain and calibrate.
Calibration is a significant cost for CEMS operators, accounting for some 24% of operating expenses. It is needed for all types of gas analysers but the frequency of calibration can be much higher in some types than for others, while the effort and costs involved can also vary widely depending on the approach. For example, the cost of calibration gas cylinders is often underestimated, while the US EPA regulations demand daily calibration.
One solution is to use internal gas filled cells. Proven to cut calibration costs by up to 95%, these cells are filled with a test gas of known concentration and are sealed to prevent them leaking, allowing them to offer a stable sample against which to test instrumentation performance. They are also accepted as a viable alternative to flowing test gas, meeting the requirements of both EN 14181 and US EPA 40 CFR part 60 regulations.
An alternative is to use internal validation cells, which use films or cells for all FTIR components. Particularly suited to FTIR based CEMS, these cells conduct automated drift checks by rotating into the optical path to check precision and drift of all FTIR components.
Digital solutions are also making their way into CEMS applications. The ABB AbilityTM range of digital solutions, for example, enable operators to ensure regulatory compliance, reduce complexity and get the most from their CAPEX investments. These innovations include remote assistance. Allowing rapid problem solving, this solution cuts costs and downtime and reduces the training needs of staff. Remote Insights is a solution that makes maintenance safer and more effective, while features such as dynamic QR codes allow the user to share diagnostic information to enable remote trouble shooting.
Another development is remote condition monitoring using real-time data. ABB’s condition monitoring system, for example, enables emissions equipment condition data to be relayed to its service experts for analysis. By allowing potential issues to be identified in advance, the risk of unplanned outages and downtime is reduced, providing system uptimes of 98% or more and enabling users to ensure continued compliance with availability requirements through optimum performance.
Conclusion As the world increasingly returns to normal, there is a need to ensure that emissions can be maintained within sustainable limits, with reductions made wherever possible. With new technologies that are more capable and accurate than ever and the support of vendors offering digital services to keep CEMS operational, the mission of keeping your emissions within limits is becoming increasingly manageable.
References
1. https://assets.publishing.service.gov.uk/government/uploads/system/uploads/ attachment_data/file/730225/TGN_M20_Quality_assurance_of_continuous_ emission_monitoring_systems.pdf 2. https://assets.publishing.service.gov.uk/government/uploads/system/uploads/ attachment_data/file/725557/Performance_Standards_and_Test_Procedures_ for_Continuous_Emission_Monitoring_Systems.pdf